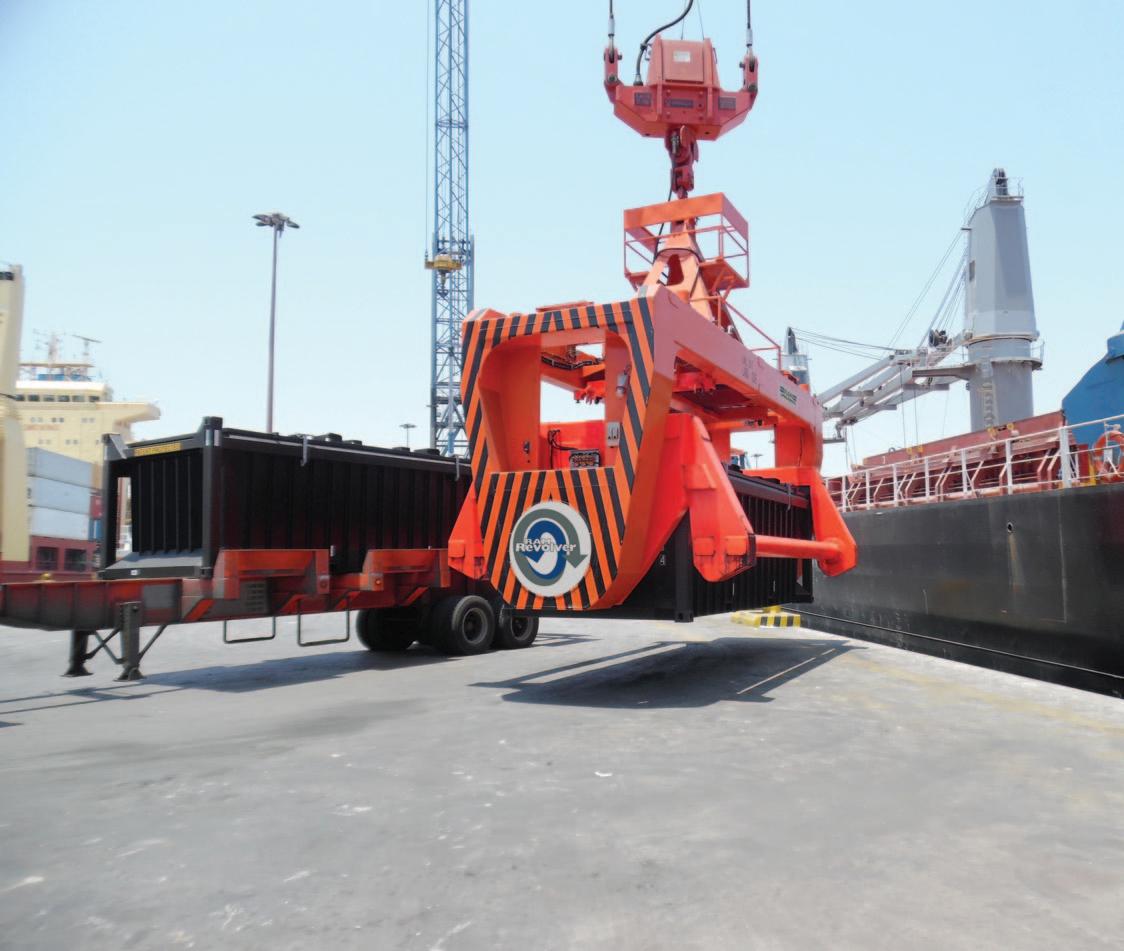
24 minute read
BIGGING UP BOXED BULK: CONTAINERIZED BULK HANDLING SYSTEMS MORE POPULAR THAN EVER
Bigging up boxed bulk
containerized bulk handling systems more popular than ever
Louise Dodds-Ely
RAM Spreaders’ Revolver® proves its worth
Containerized bulk handling (CBH) is increasing in popularity. Traditional bulk loading requires large amount of investment in engineering, design and construction, implementation and maintenance. Some bulk terminals cost more than $100 million to set up.
RAM Spreaders is continuing to develop its popular Revolver® system, which makes it possible to transport bulk product easily using containers. The system works by loading bulk directly to a hopper by grab, and loading the cargo to a container, which is then sealed. (Another method of loading the container is to use a digger.). The container can then be transported and stored, with no need for undercoverage storage facilities. The Revolver® spreader is used to discharge the container — whether into a hopper, or vessel hold, or other.
The RAM Revolver® picks up and rotates the commodity through 360° using open-top containers with sealed lids as a form of loading, transportation, storage and unloading.
The Revolver® has been designed for flexibility to interchange with either a Reachstacker or a bridge crane, with other Revolver® models available for mobile harbour cranes, ship-to-shore cranes and ship crane use.
The CBH process is simple and effective, efficient and most of all, clean and friendly to the environment at a very low cost. The Revolver® CBH can handle all dry bulk commodities such as grains, mineral sands, soya, wood chip, copper concentrate, iron ore, coal and scrap metal.
RAM Revolver® has a SWL of between 35t for ship, bridge and reachstack application. 38t SWL for ship-to-shore

Innovative revolving container technology now in use at DP World Fraser Surrey, Canada
In May last year, DP World and New Gold Inc. announced the signing of a long-term agreement to facilitate the export of copper concentrate through DP World Fraser Surrey using rotating containers
This long-term agreement with mining company New Gold Inc. facilitates the export of copper concentrate through DP World Fraser Surrey using rotating containers — a specialized revolving head technology — with the rotating equipment coming from RAM Spreaders.
New Gold is excited to be partnering with DP World Fraser Surrey, a world class marine terminal and Intermodal Solutions Group (ISG). New Gold is the first mining company in North America to use the ISG rotating containers system, from mine to vessel. New Gold recognizes that keeping bulk products contained, from mine to ship, benefits the environment and significantly reduces or eliminates the risk of dust loss that comes with bulk handling.
DP World Fraser Surrey is the first marine terminal in Western Canada to begin exporting dry bulk cargo by using rotating containers. This revolutionary new export method begins an era of exporting dry bulk commodities in a more environmentally responsible manner. This method allows fully sealed containers to be rotated 180° within the hold of the vessel to unload the contents rather than using the traditional bulk shiploader. A mobile dust-suppression unit is fitted around the rim of each vessel hatch, emitting water mist to mitigate dust levels.
As a result, there is no product damage or loss and the risk of environmental contamination during transport and loading is dramatically reduced.
In addition to concentrates, the ‘rotainer’ technology can be used with sulphur, wood pellets, fertilizer and grains.
DP World (Canada) Inc. CEO & GM, Maksim Mihic, noted: “I am delighted to partner with New Gold Inc. to enable trade in a more efficient way, and with significant environmental benefits. The rotating container is an innovative solution that will improve the competitiveness of Canadian exports in the global markets.”
DP World’s continued investment into Fraser Surrey has created a world class marine terminal. The agreement with New Gold and the early-2022 start-up of this model for exporting cargo forms a new standard in marine shipping, enabling smarter trade and creating a better future for all. The RAM Spreader seen operating at DP World Fraser Surrey in April 2022.
cranes and 45t for mobile harbour crane application. All equipment except the ship crane revolver, which has an on-board power unit, takes power from the crane supply.
Over the years, RAM has shown how the Revolver® can smoothly integrate into any port or logistics type at low costs — that being pit to ship, shed to ship, ship to hopper, etc.
There are a couple of challenges that must be overcome when handling bulk in containers. The first is the issue of working with ships’ gear. Many of RAM Spreaders’ customers want to use ships’ gear, but the tare weight of equipment makes this difficult. Another challenge is that the cost of fully containerizing cargo can be expensive.
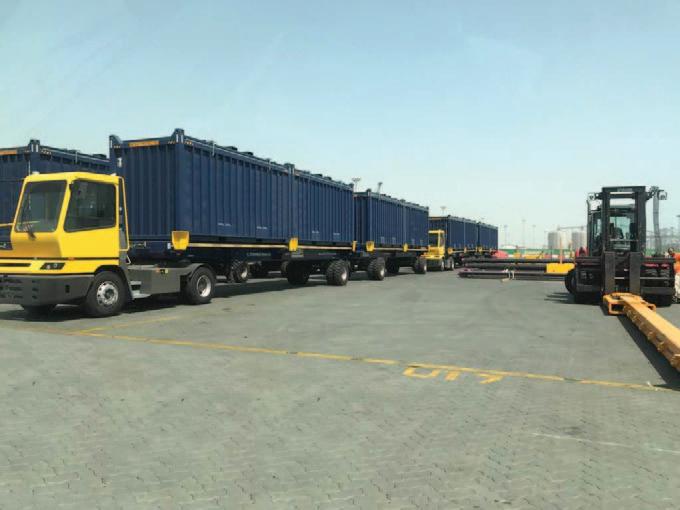

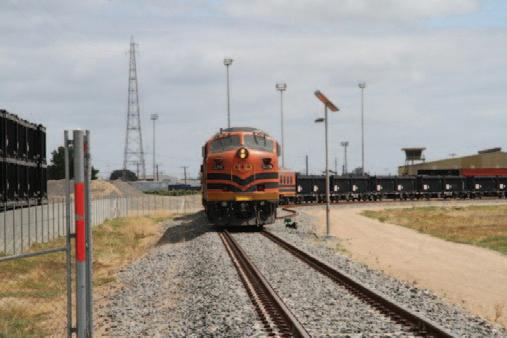
However, these challenges are offset by the significant advantages of moving bulk in containers. These include: v Clean & green: no dust is generated or exposed to the environment as containers are sealed shut. When unloading, the rotating spreader removes the lid semi-autonomously and then gently rotates at the bottom of the hatch. v Multiple types of commodities can be stored in close proximity without the risk of cross-contamination or environmental impact. v Product protection: as containers are sealed shut until unloading, the system prevents loss of commodity or product quality being degraded. v Flexibility: over the years, RAM has shown how the Revolver® can smoothly integrate into any port or logistics type at low costs — that being pit to ship, shed to ship, ship to hopper, etc. v Fast contingency: the bulk handling system has the ability to stockpile the commodity for the arrival of the ship.
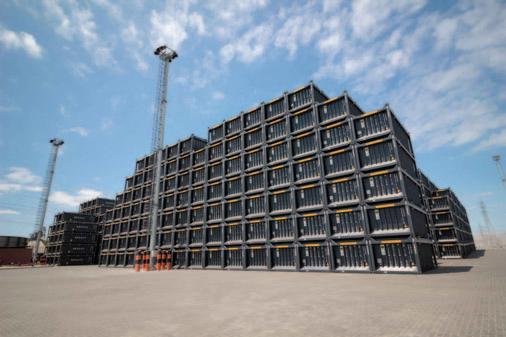


v Boxing clever: the traditional method of stockpiling bulk demands more consideration when planning — from storage facilities, environmental concerns to cross contamination. Containerizing bulk means using existing infrastructures. A container ized system uses up the storage capacity per square metre, as the commodity is stored in a cuboid formation rather than a conical or cone formation.
DUST CONTROL VITAL As mentioned above, containerization of commodities, containerization of commodities results in a dust free environment as the commodity is transported in sealed containers and only sees the light of day immediately before being tipped into the ships hold (or hopper if it is bridge crane/reach stacker for handling facilities or exporting from shed to ship). To ensure maximum dust suppression, a dry fog system is placed around the ship’s hold to suppress the dust plume when unloading the commodity into the ship’s hold.
CUSTOMER BASE Customers for the RAM Revolver® range from mining companies, bulk handling facilities, ports and terminals and inland terminals. The original concept for RAM CBH was aimed at the export market, but in recent years, the RAM CBH has increased in popularity with inland terminals and bulk handling facilities. These customers require bulk to be moved between locations without the need for multiple handling and without environmental impact and loss of commodity from multiple handling points.
LID LIFTING SYSTEM This is the mechanism on Revolver® that lifts the lid from the container immediately prior to Revolver® rotating the container through 360°, tipping the commodity.
LOW-DENSITY BULK SOLUTION RAM Spreaders has also developed a highvolume Revolver® for low-density bulk, to add to its extensive range of container handling solutions. With a growth in biomass and other low density dry bulk materials, RAM has been investigating ways to maximize the efficiency of loading with its customers. Essential to the investigation process and the feedback it received, was the need and ability to load large volumes (>100m3) per cycle. After consulting with customers RAM developed a solution with the ‘Revolver® – Container’ combination being able to handle this level of load rate, by introducing a high volume container capable of achieving a higher volume load capacity.
This new innovation allows the Revolver® to handle large volumes and enable customers to get the very best load rates available. With a maximum volume of standard open top containers being limited, it ultimately restricts its efficiency. So you
Lid lifting system and (inset) placing a lid on a truck-mounted container.

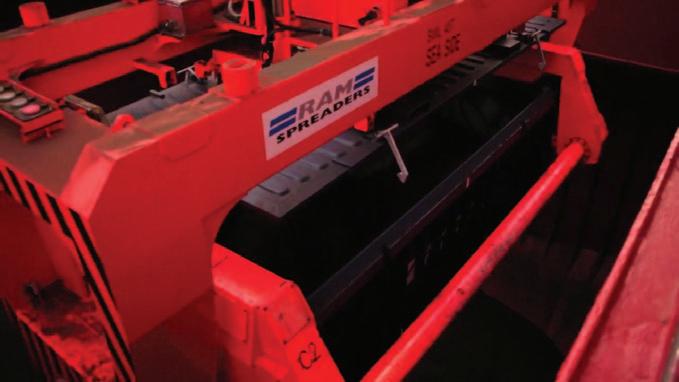
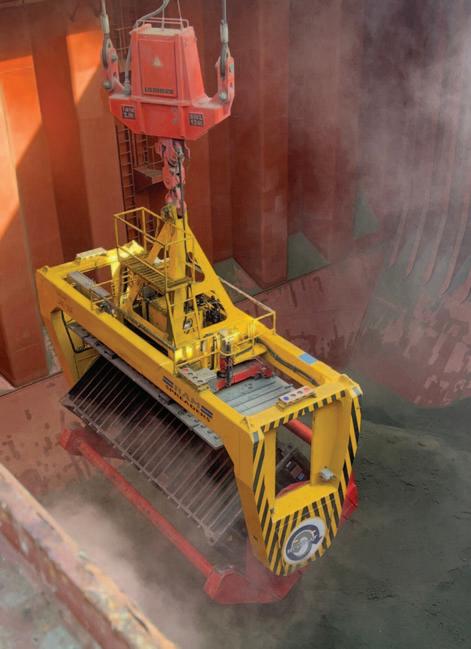
Lid lifting system in operation.
would think to increase the volume, you would have to introduce an out-of-gauge container, which would be expensive to build and to ship.
To solve this problem, RAM developed a two-tier container, which is an ‘in-gauge’ design solution for shipping but out-ofgauge for operations. So for the customer it will increase efficiency but still remain cost effective.
The design and construction of the high volume ‘in-gauge’ container is innovative and very easy to introduce into the containerized bulk handling process.
CASE STUDIES RAM Revolvers® are in use at a wide range of facilities. Notable contracts for the system include: v CODELCO: the largest copper producing company in the world. The copper concentrate is loaded and sealed into special ISO twenty foot containers at the mine; it is then transported to the port’s yard, stored like any other container and then loaded right into the vessel’s hatch with existing terminal equipment. The only new equipment is the purposedesigned revolver from RAM
Spreaders. The CBH process is simple and effective, efficient and most of all, clean and friendly to the environment at a very low cost. The copper is not exposed to the environment, even when it is released at the bottom of the vessel’s hatch by the revolver spreader. v Riga Universal Terminal Ltd (RUT): as part of its ongoing development of the terminal, and in order to increase the effectiveness of cargo handling, RUT introduced the use of the RAM Revolver® for handling wood pellets on large dry bulk ships. The Port of Riga was the first port in Europe to use the system. Pellets are delivered from warehouse to pier in special-purpose open-top 20-foot containers. Using a portal-frame container lift equipped with a Revolver®, the entire contents of a container are delivered onto the ship by turning the container over into the holds.
Said Atis Šulte, RUT Trade and Business Development Director: “The main benefit from introducing the new technology is significant optimization of terminal expenses and increase in performance. Now, we can perform dry bulk handling operations involving a significantly smaller number of machinery and human resources. Savings on resources amount to almost 50%. By introducing containerized cargo handling, we have become more competitive and can better adjust to customer requirements. Following the general tendency in cargo carriage, dry bulk ships handled at our terminal are becoming even larger. By means of the new technology, we are able to ensure fast and effective loading of large ships. By applying the new technology, we are able to load dry bulk and containers at the same pier, using one portal-frame lift. It allows us to quickly organize our work in the terminal and quickly handle any type of ship.”
Says RAM Spreaders Head of Sales & Marketing Cameron Hay, “Being the first Revolver in Europe, the CBH system is world’s best practice for environment; and we can see in Riga that it increases productivity as well”.
Port Elizabeth Container Terminal
v
(PECT), South Africa: following the introduction of containerized bulk handling at PECT, Transnet Port Terminals (TPT) placed a repeat order with RAM Spreaders for four units of the RAM Revolver® bulk handling spreader. TPT handles large volumes of bulk exports annually at PECT, and turned to RAM Spreaders for its CBH needs. The terminal invested in four units of RAM Revolver®, to help it service its base of customers better. Speaking in 2019 at the handing over ceremony of the
Revolvers, RAM Spreaders
Cameron Hay commented “Since the first order of Revolvers® in
Port Elizabeth more than five years ago the CBH system has grown significantly. These new revolvers will allow TPT to ensure environmental compliance.” PECT is located near to the main town of Port Elizabeth and like all cities dust is a sensitive issue. The CBH system, using a hatch misting system is the greenest loading system in the world with zero fugitive dust emissions. v Peru minerals contract: working with international mining consultants Ausenco, RAM
Spreaders designed and supplied its CBH system, which loads bulk ore into containers and uses standard trucks, trains & cranes to
v handle the material through the supply chain. The CBH system seals the valuable material in the container at the mine and doesn’t see daylight until emptied into the ship’s hold. The containers are filled with valuable ore at the mine and then the modular system is transferred simply through the supply chain with no doublehandling or material loss. The RAM Revolver® was designed to be flexible in application, so that it could be changed to handle a number of loading or container handling situations. The system can be interchanged between reachstacker, bridge crane in the warehouse, or port crane for direct shiploading. This flexibility allowed the system to work straight away in the ‘ramp up’ phase of the project before all of the infrastructure was ready. Port of Poti, Georgia: at the Port of Poti, to reduce spillage and wastage before being transported to the terminal, copper concentrate is loaded into reinforced open top containers covered by a tarpaulin in a closed warehouse. The use of the RAM Revolver® has improved efficiency and improved the environmental impact of these operations. There is a clear cost and time saving. At the terminal, the revolving spreader attaches to a mobile harbour crane as a regular spreader does. The suspended spreader turns the container upside down and deposits the contents at the bottom of the vessel’s hold. As the product is loaded into the vessel, a hatch-mounted misting system prevents the copper dust from being blown away. The spreader means that the copper concentrate avoids spillage, dusting and water contamination.
STAYING COMPETITIVE RAM Spreaders retains a highly competitive position in the market by having different designs to suit the application of the customer’s equipment
It also works closely with potential clients to show how the CBH system can flexibly integrate into their port infrastructure (in a small-time frame and without unnecessary costs) to boost productivity.
Moreover, to solidify its relationship with customers, RAM Spreaders aims to provide exceptional customer care before and after delivery. Its support services are there to provide help and guidance throughout the service life of the machine.
TECHNOLOGIES RAM SMAG Lifting Technologies has been manufacturing spreaders since 1972 for nearly 50 years. The head office is based in Germany and the company is an integral part of Group SMAG.
RAM & PEINER SMAG provide the full range of crane lifting attachments from, spreaders, tandem headblock, grabs, RAM Revolver, tilting spreaders, pipe handling spreaders.
RAM SMAG Lifting Technologies is a global company with offices in Germany, Singapore, UK, India, China. It benefits from a global network of local sales & service representatives. RAM carries out all design/manufacturing in-house and does not subcontract.
Quality systems in place include: ISO 9001, ISO14001, ISO18001, ISO 3834-2, EN1090-2.
The company is currently celebrating over ten years of RAM CBH success, with the very first commercially available Revolver still in operation today. This is testament to the hard work and determination of not only RAM, but also its customers, who believe in, and rely on, the product gaining great success and reducing their environmental impact using RAM CBH.
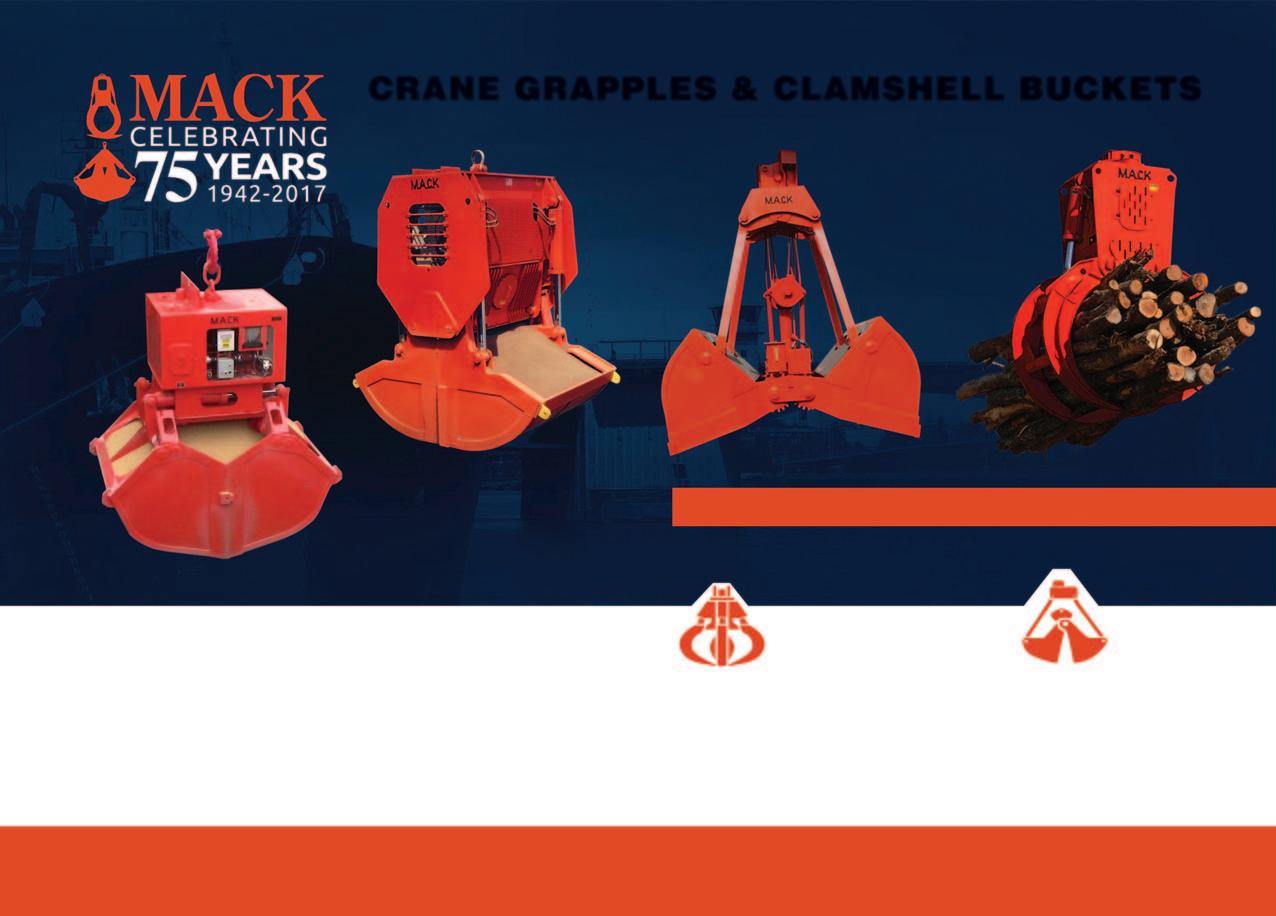
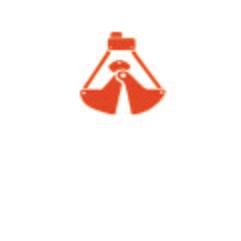
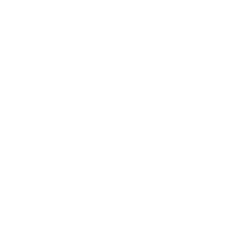

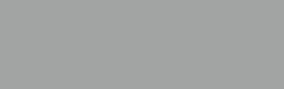

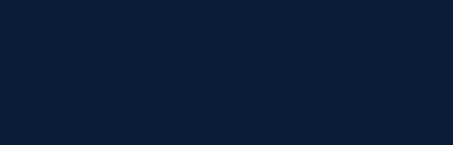

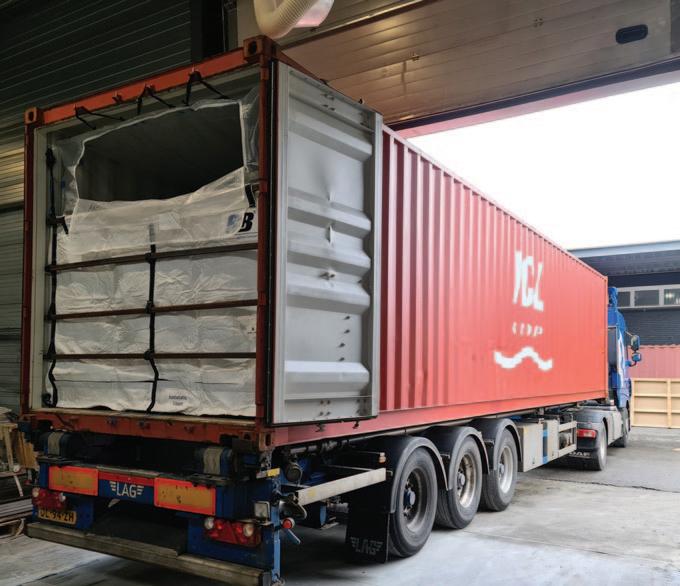
BulkTechPack International BV is an independent supplier of dry bulk container liners, for the dry bulk industry, specialized bulk container operators and container shipping lines.
The company’s innovative container liner designs are recognized for their functionality, quality and are utilized by companies large and small within the food, feed, chemical, mineral and agricultural industries.
With over 30 years of experience within the business, BulkTechPack International facilitates its clients with a unique service for containerized dry bulk opportunities, with reference to packaging, handling and technologies.
To protect free flowing dry bulk commodities during intermodal transport, it is essential bulk container liners are used. The liner protects against contamination and safeguard the integrity of the dry bulk commodities carried, such as dry granular, pellet or powder products.
BulkTechPack International’s dry bulk container liners are manufactured from food grade, virgin LLDPE film or in woven PP/HDPE fabric, depending on the commodity and clients requirements.
Manufactured and tested in a ISO9001, FSSC22000 and BRC quality assured production facility.
The main challenge within the containerized bulk process is to map out all aspects from start to finish. In a dry bulk door-to-door supply chain, the process is covered by several people on a variety of
PE film 40ft container liner, fitted and ready for loading. Loading salt with 20ft bulk liner.
continents.
It is therefore very important, in addition to selling container liners, to also guide and assist customers with on-site training and instructions for fitting, loading and the unloading process.
The main advantage of using dry bulk container liners is the fact that it is possible to increase the loading capacity of each container and decrease the costs of packaging, handling and recycling, compared to the use of bags or FIBCs.
Liners are thus extremely effective for transportation, but also perfect to use as intermediate dry bulk storage on site or close by in port areas and depots, creating a rolling stock.
Bulk container liners can be used for all free flowing granular, pellets, flakes and powder products.
BulkTechPack International’s main clients are within the food and feed industry, where commodities such as sugar, corn, salt, rice, malt, coffee beans, grain,
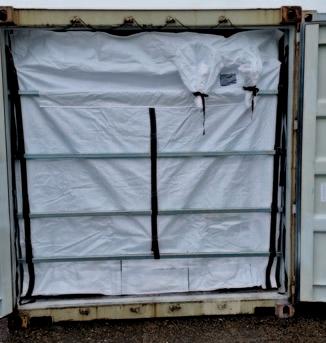
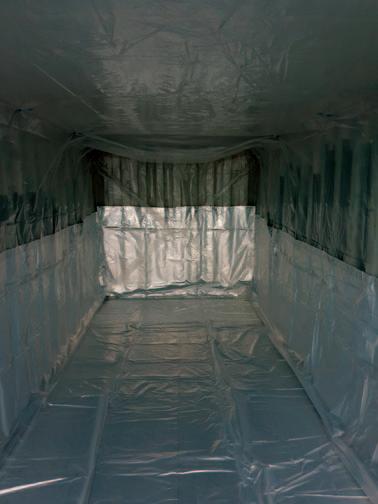
PP woven 20ft container liner, fitted and ready for loading. Interior view of a 20ft container, lined with a PE film sugar liner, with M-Pet barrier material.

flour, animal feed etc. are transported within bulk container liners globally.
In the last ten years, BulkTechPack International has also seen an enormous rise in volumes within the chemical and mineral industry, with the bulk transport of PE resins, PET, PP resin, PVC, fertilizers, asbestos, nylons, carbon black, feldspar etc.
The major benefits described do ensure that once the customers have embraced this form of bulk transport, they want to continue and expand. The concept offers great opportunities to sell free-flowing commodities in bulk, safely and sustainably, in a global market.
As the world starts to recover from the worst of the Covid-19 pandemic, Container Rotation Systems (CRS) is enjoying success, with the award of contracts for a number of new domestic projects both on the West and East Coast of Australia.
The recent global increase in the demand for mineral sands and rare earths has seen a number of projects finally get to the point of production. These types of commodities are well suited for transport via sealed container systems.
LYNAS, WESTERN AUSTRALIA One such project currently entering the world stage is the new Lynas facility in Kalgoorlie, Western Australia. This project has inbound and outbound products with both transport legs requiring road transport, and is therefore well suited for containerization.
To meet the special process require ments CRS developed a special Rotainer® Eurospec 360PC. This unit, specifically for portal cranes (360° multi-direction rotation) will handle the container inside Lynas’s state-of-the-art environmentally sound processing facility, Kalgoorlie, Western Australia. This new unit was purposely developed for portal (gantry) crane operation with a very slow, programmable rotation speed for slow, controlled feed into the hopper system
Lynas chose CRS above other suppliers as CRS can provide the complete container rotation solution such as the container rotators, bulk ore open top containers and lid handling equipment.
Lynas preferred the CRS innovative bulk ore container, branded as ‘Rotorcon®’ (rotatable container) due to the unique shape of the internal tub that is well suited for sticky materials with the ability to ‘selfclean’ to reduce carry back. Lynas found comfort with CRS expertise in supplying the compete container rotation solution.
Lynas chose CRS as the complete container rotation system supplier due to its industry experience combined with the fact the complete system can be manufactured, tested and precommissioned on site at the CRS, state of the art, 3,000m2 manufacturing facility located in Sydney, Australia.
TRONOX, BROKEN HILL Minerals sands is experiencing strong regional growth. Tronox, Broken Hill is in the process of major plant upgrades with new mines coming one line, increases in tonnes processed required a change in the logistics management.
Tronox, which has its own fleet of several thousand bulk ore containers, engaged CRS to supply Rotainer Eurospec 38RS’s (reach stacker) with automated lid lifting to handle its inbound containers. These containers will feed the plant with raw product; once processed, it will then be re-containerized for shipment to processing pants on the West Coast of Australia.
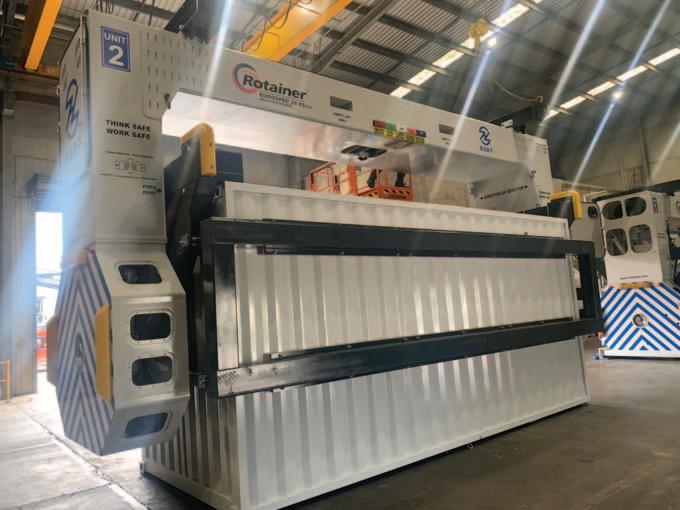
Lynas chose CRS as it can provide the complete container rotation solution such as the container rotators, bulk ore open top containers and lid handling equipment.
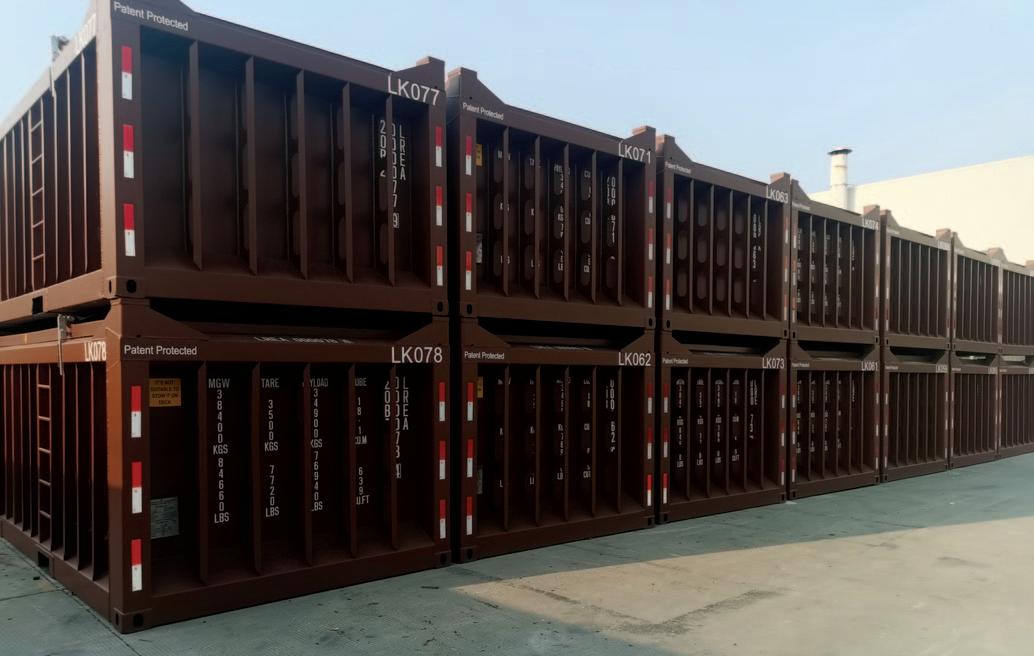
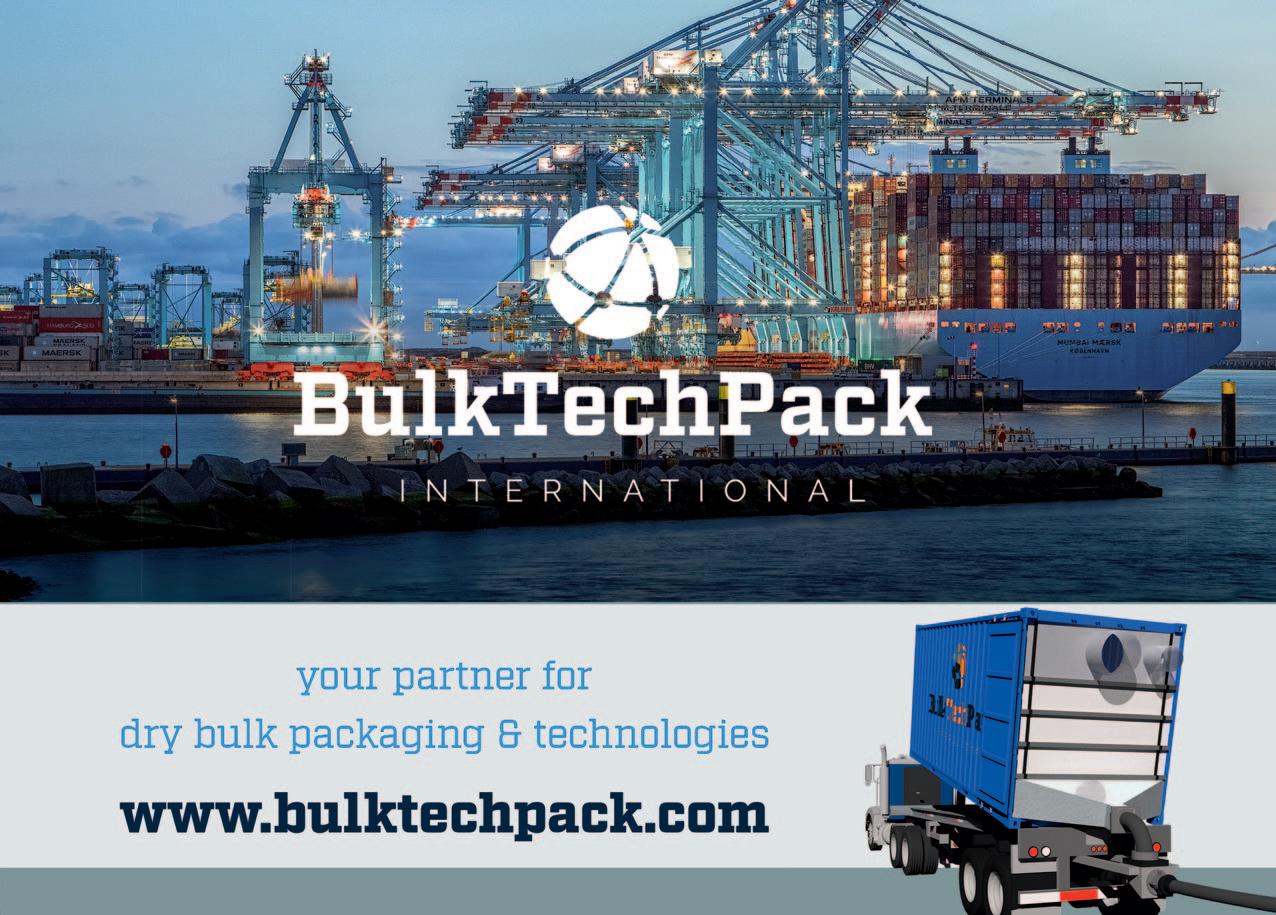

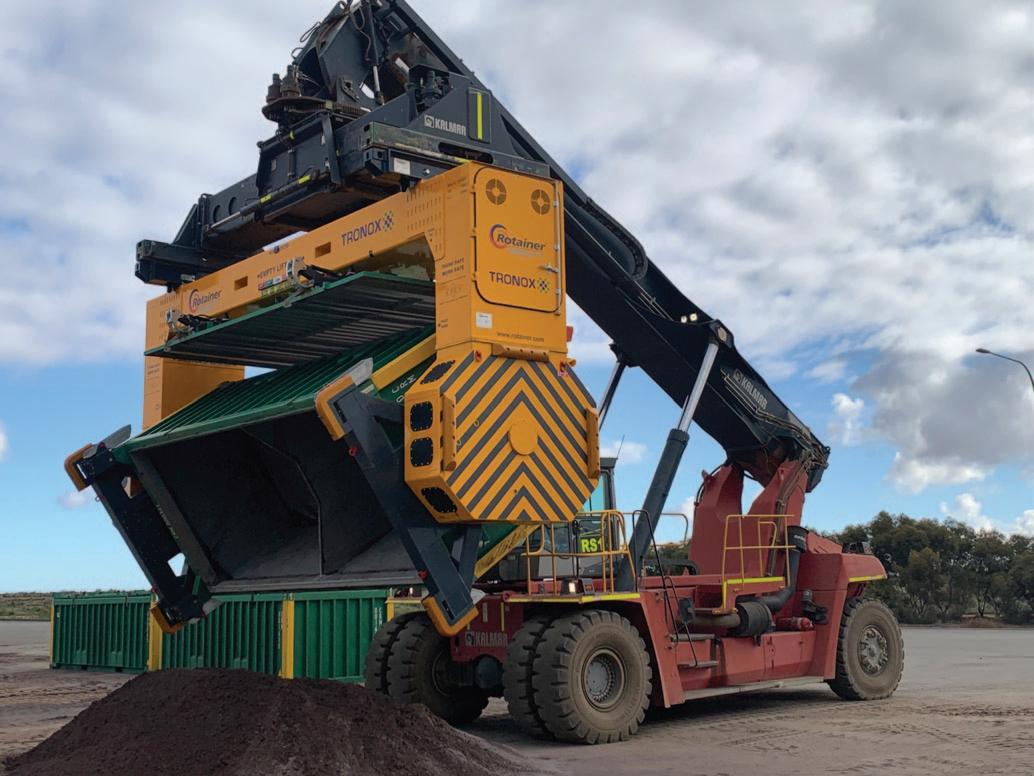
Moving millions of tonnes of containerized bulk commodities from outback New South Wales to process plants located in Western Australia is no easy feat.
Aurizon, Australia’s largest rail freight operators provided the logistic solution Tronox required to move the large volumes of containers from East to West.
To enhance this operation CRS was commissioned to provide additional Rotainer Eurospec 38RS’s for the unloading process.
ABOUT CRS
CRS is Australia’s largest supplier of container rotators and is proud to be at the forefront of container rotation solutions, with its equipment operating in over 20 installations globally.
CRS’s ongoing R&D regime continues to see an increase in the company’s product portfolio such as its Patented Tiltainer®, end tipping for standard general-purpose containers. The CSS (Container Support System), for container side wall support suitable for uncertified open top containers, and the Maxebeam system for maximum product delivery are both Patent Pending.

When the word ‘logistics’ is mentioned, most people think of movement of parts and unit items in containers or in packed crates, writes B Velan, Scorpio Engineering India. Many truck owners call themselves ‘logistics’ companies to keep with their interpretation of the word to mean truck movement. The true gamut of logistics is enormous in its impact and its importance in the final product price or even a country’s GDP is often grossly underestimated.
One area of logistics that even industry professionals are often unaware of, or do not give due importance to, is the movement and distribution of dry bulk materials such as cement, fertilizer, chemicals, petrochemicals, foodgrains, minerals etc. Almost every aspect of everyday life and the contents of every home have products that have begun life as dry powders. Paint and glass are common examples. Both begin life as powders. Glass is made from sand, paints are made from minerals and chemicals. Synthetic blended clothes are made from pellets of plastic. Mobile phones come from plastic pellets and chips. Bathroom fixtures like washbasins and toilets come from ceramic powders and grains. Floor tiles come from the same origins. Detergents and beauty products come from chemical powders and mixtures. All this means an enormous amount of dry bulk materials have to be moved across the country from origin to user destination, from factories making these bulk materials to factories using them in their production processes.
The most common method of moving these materials is in bags. We are familiar with the cement bags we see in everyday life. We are familiar with bags of pulses and grain in the local ‘kirana’ stores (or cornershops). We are familiar with bags packed on the backs of trucks we overtake. All these are of 30 to 50kg weight. They are filled in factories by bag filling machines and are stitched closed automatically. There are also bags that can carry 1,000kg of powders called jumbo bags or big bags or FIBCs (flexible intermediate bulk containers).
To move large amounts of bulk materials, we will need a very large number of bags either of the smaller or larger sizes. The handling of these bags poses major environmental and health problems. In India, most handling is still by manual labour and the lack of legislation that has ‘teeth’ is a major factor in this practice still being continued. As an example, the number of
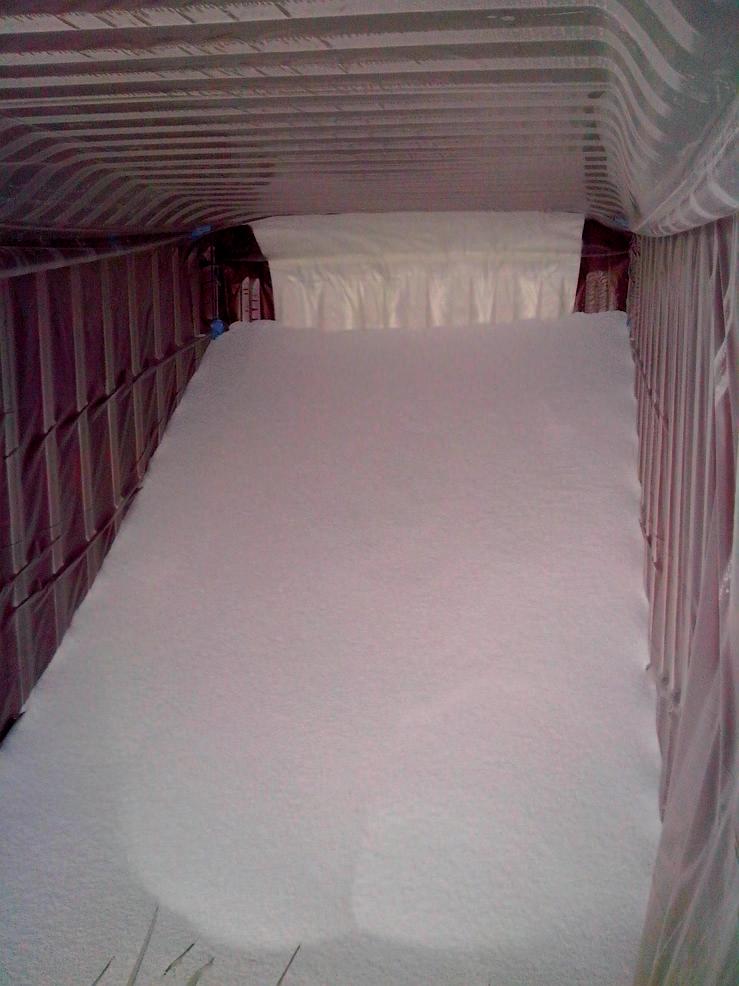
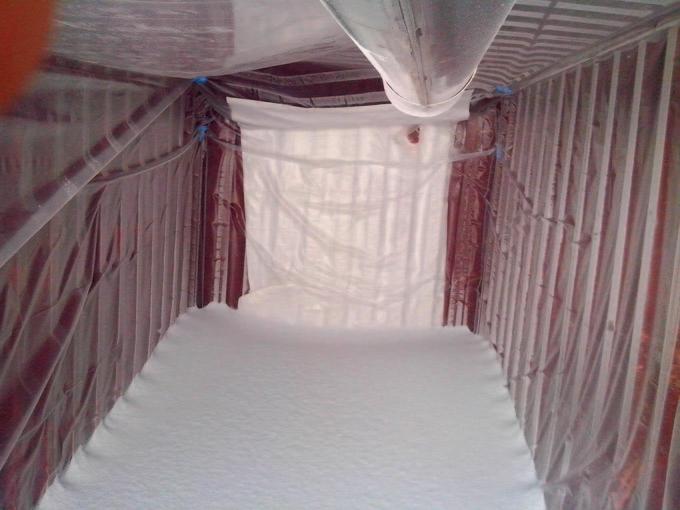


50kg bags that a typical factory producing say 40,000 tonnes of detergent powder a year needs to handle (which includes opening the bags and disposing of the empty bags) is about 800,000. If raw materials are being received every fortnight, this means 30,000 bags every 15 days. Multiply this by about 100, being the total number of such factories that a country like India may have, and you have quite a ‘bagful’!
The best way to move the material that these bags hold will be by bulk, meaning that there are no bags. If it were possible to just fill a typical Tata truck with bulk material (like the sand trucks you see on the roads) and move it across the country, you can avoid bags but at the cost of major pollution. And how do you empty and store the material? The use of lined containers from companies such as Scorpio Engineering is one solution to avoid the filling and handling of bags. This concept is relatively well established in the developing countries but has not yet taken off in India. This is primarily because of the lack of knowledge and information as to what these systems entail. A description of this system is given below.
Liners are special plastic ‘inserts’ that are placed inside standard containers. They have provision for hooking to the internal hooks in the container and also have a bulkhead at the door end of the container.
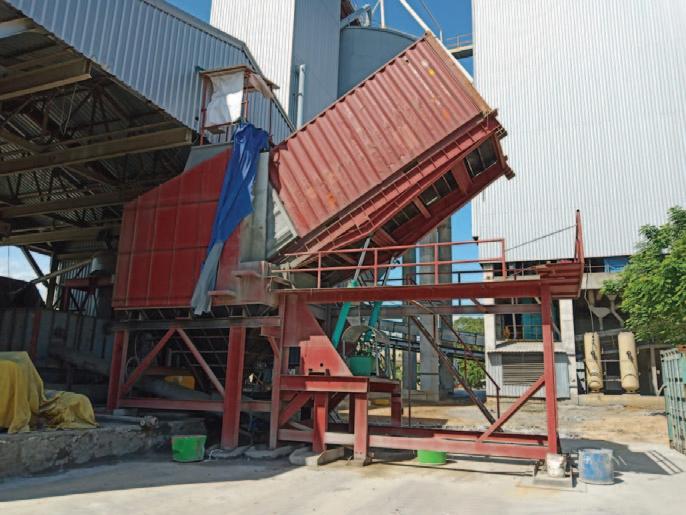

These bulkheads are part of the liner and will be generally made of a heavy synthetic material or wood and are integrated into the liner construction. The bulkhead has one or more entry holes at the top and a discharge spout or opening across the bulkhead at the bottom.
To fill the liner once it is installed inside the container, a variety of methods are available. Depending on the nature of the bulk material, the product can be ‘blown’ inside, conveyed inside by a belt or screw conveyor or the container can be tilted in a container tilt unit. Once the container is filled, the bulkhead openings are shut, doors closed and the container is transported to the destination by road just as any other container movement.
On reaching the destination, however, provision must be available for the container to be lifted off the truck and tilted again with the door side facing down. The bulkhead openings at the bottom are flexibly connected to a pneumatic conveying system which simply blows the product to a silo. The tilt of the container can be varied to suit the product and in the case of difficult to flow materials, the container liner has built in aeration and corner inflatable pockets to ensure full emptying. The container tilt unit is generally hydraulically operated but a new design specifically tailored for Indian conditions uses mechanical lift and tilt systems which are simple and ‘idiot proof’. This is especially significant because of the rampant use of unskilled and uneducated labour for such work in most plants which are also unable to get talented people due to remotely located plants with no infrastructure. DCi
3200T | Tilting Crane Spreader
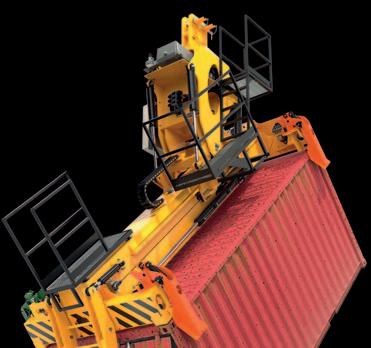
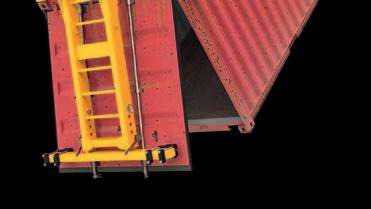
One of our hard-working spreaders
Dedicated crane spreader with tilting function for bulk material handling. Meet the rest of the team at elme.com
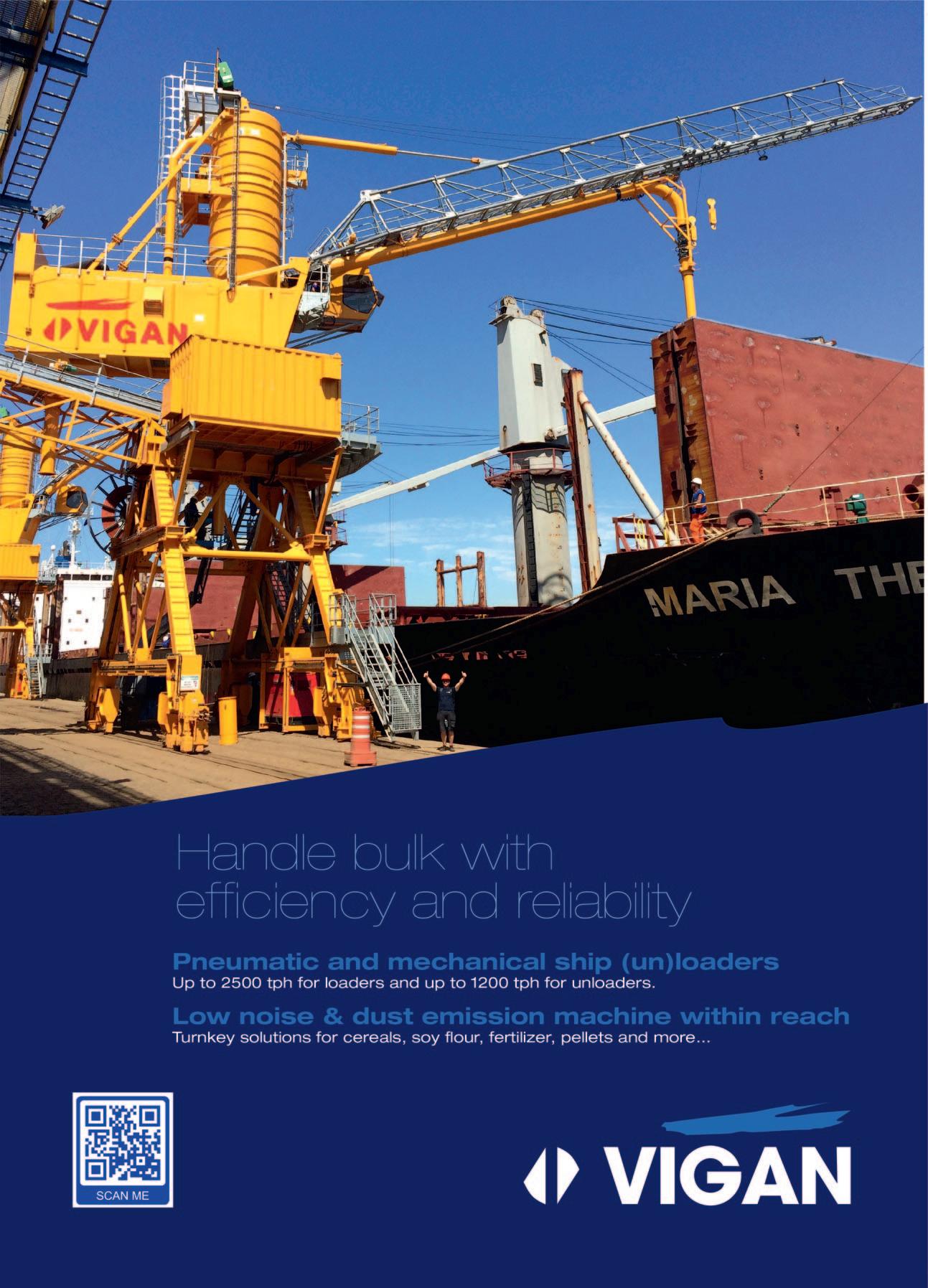