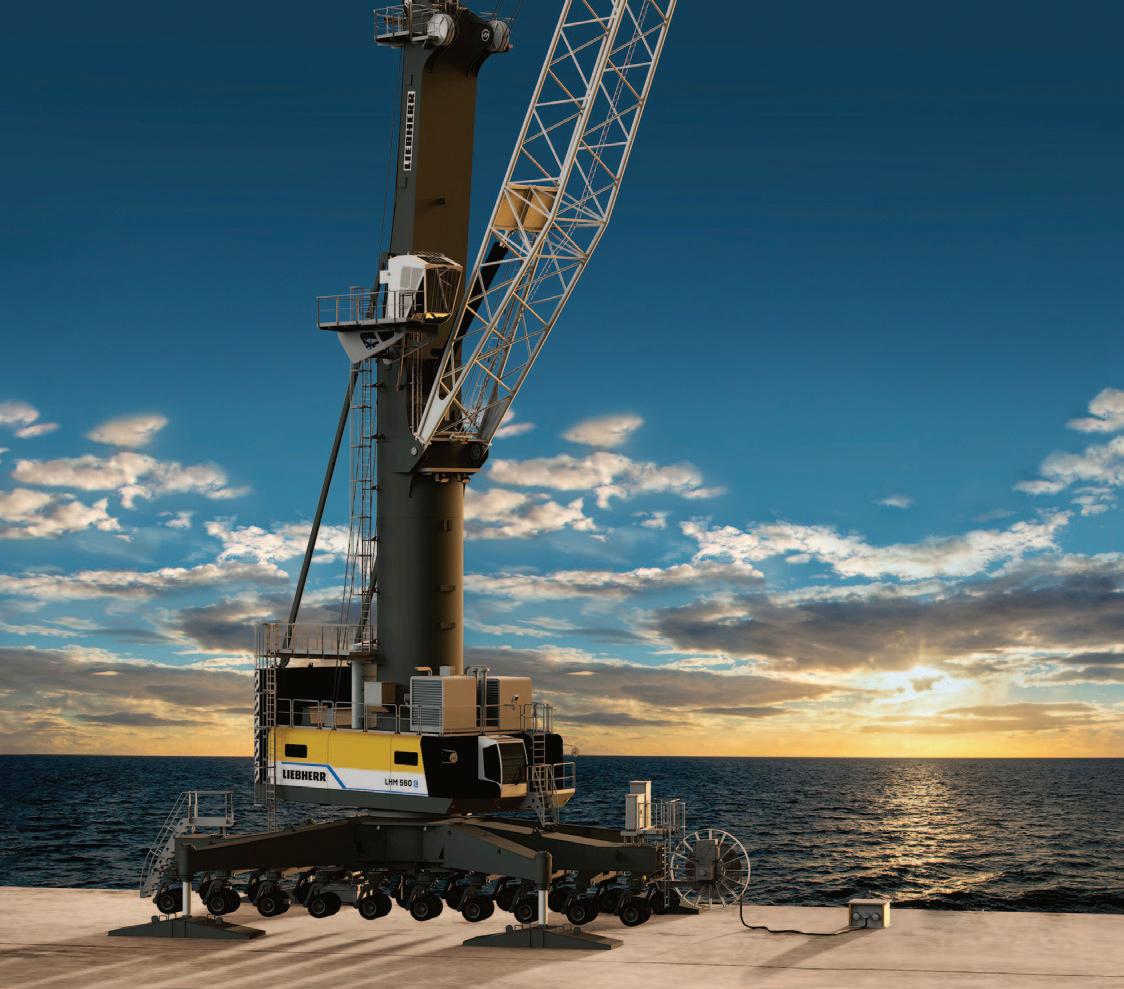
23 minute read
HOW TO TRAIN YOUR CRANE : CRANE TECHNOLOGIES, -DRIVES, -CONTROLS & COMPONENTS
The new LHM crane series is further characterized by a new control and sensor technology, new design, an advanced Pactronic hybrid system and an ergonomically improved operator’s cab.
How to train your crane
crane technologies, -drives, -controls & components
Jay Venter
The new Liebherr mobile harbour crane: ready for the future
The Liebherr mobile harbour crane series gets ready for the future: the new LHM is more digital, more efficient and impresses with a modern exterior design. A new crane control system, advanced sensor integration and digital information transmission enable future assistance and partial automation systems. In addition, the Liebherr Pactronic hybrid system and the operator’s cab have been improved to meet customer needs.
With its new mobile harbour crane, Liebherr presents groundbreaking technical developments and updates that make the LHM product series fit for the future. The decisive innovation is the implementation of the ‘Master V’ crane control system. Together with an even more efficient software architecture, this forms the basis for integrating future assistance and partial automation systems into the crane in the long term. Overall, the crane will become much more digital, networked, and smarter.
The position of the outrigger system is now monitored by sensors and thus part of the internal data processing. The use of a new outrigger base in the field only requires a software update by Liebherr and thus offers more flexibility. Another practical advantage is the variable use of digital IP cameras for better monitoring of the crane interior as well as the external crane environment. The new crane control is supplied by an independent power circuit. This means that the crane can be continuously monitored by cameras and efficiently protected without the crane ignition being activated.
NEW HYBRID SYSTEM — PACTRONIC 2.0 The Liebherr Pactronic 2.0 hybrid system represents the second generation of a hydraulic drive system using hybrid technology. An accumulator serves as an energy storage and provides support when needed by supplying additional, temporarily stored power. The second generation of the Pactronic offers the operator a choice of two operating modes, depending on the current work situation:
BOOST MODE
In this mode, the Pactronic 2.0 acts as a significant power amplifier. Lifting speeds are significantly increased — without the aid of a larger or even additional engine for more power. This massively increases the efficiency of the crane. The LHM together with a Pactronic 2.0 hybrid system provides a reduced cargo-handling time and achieves the same performance parameters as a comparable device with two main units.
GREEN MODE
This mode is designed to save fuel or power consumption and to reduce CO2 emissions. During the lifting process, the

The second generation of the Pactronic offers the operator a choice of two operating modes, depending on the current work situation. ENGINEERING & EQUIPMENT
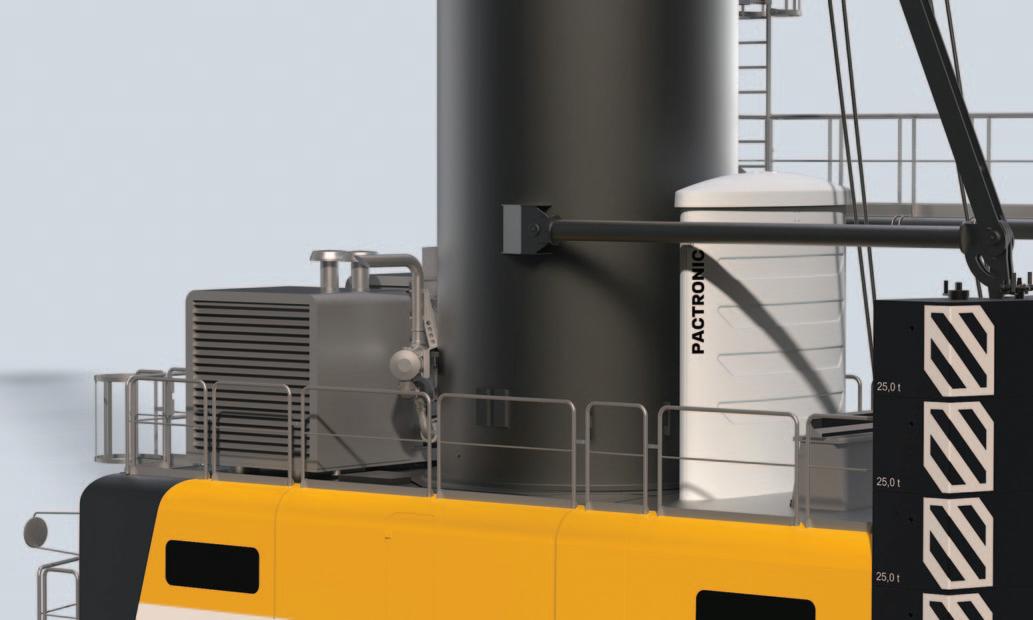
Pactronic supports the main unit to such an extent that less power is required by the main drive, despite the lifting speeds remaining the same. As a result, absolute fuel or power consumption and emissions are reduced.
The second-generation Pactronic is thus even more closely aligned to the actual needs of the user. By setting the individual lifting height, the power output of the Pactronic is adjusted accordingly. The additional energy of the Pactronic is distributed over the entire lifting process. It is also important to note that the new Pactronic reacts to changes in the outside temperature and the accompanying change in pressure in the reservoir, thus further increasing the efficiency of the system.
NEW MARITIME CABIN The redesign of the LHM operator’s cab focuses on the crane operator. Thanks to the new coupling of control lever and armrest, not only does the driver’s comfort increase, but the control of the crane also becomes even more precise and safe. With the new integrated touch panel, all crane functions can be selected clearly and intuitively, which greatly simplifies the operation of the crane. An integrated bottle cooler provides cool drinks — even on warm days.
A revised air-conditioning concept significantly increases the well-being of the operator, whether air-conditioning or heating. It also ensures that fogged windows are quickly dehumidified, thus providing a clear view and more safety.
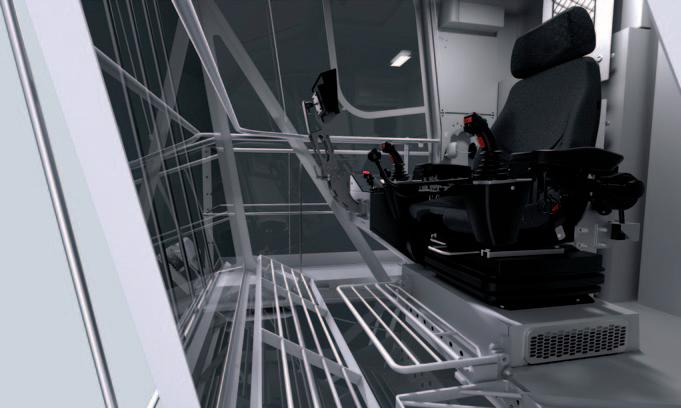
INNOVATION HAS NEVER LOOKED SO GOOD The colour compositions of the latest LHM generation combine the classic Liebherr yellow with new accents in black, grey, and white. The agile-looking design reflects how long-standing tradition and corporate values combine with advanced technologies. The modern colour scheme gives the machines a distinctive look and instant recognition. The blue accent in the colour composition and also the blue Esymbol next to the crane type, give all alternatively powered machines a distinctive look. This allows all future LHM customers to directly communicate advanced and environmentally friendly crane technology to their stakeholders.
Thanks to the new coupling of control lever and armrest, not only does the driver’s comfort increase, but the control of the crane also becomes even more precise and safe.
ABOUT LIEBHERR-MCCTEC ROSTOCK GMBH Liebherr-MCCtec Rostock GmbH is a major European manufacturer of maritime handling solutions. The product range includes ship, mobile harbour and offshore cranes. Reachstackers and components for container cranes are also included.
ABOUT THE LIEBHERR GROUP The Liebherr Group is a family-run technology company with a broadly diversified product range. The company is one of the world’s largest manufacturers of construction machinery, but also offers high-quality, user-oriented products and services in many other areas. Today, the group comprises more than 140 companies on all continents, employs around 48,000 people and generated a consolidated total turnover of more than €10.3 billion in 2020. Since its foundation in 1949 in Kirchdorf an der Iller in southern Germany, Liebherr has pursued the goal of convincing its customers with sophisticated solutions and contributing to technological progress.
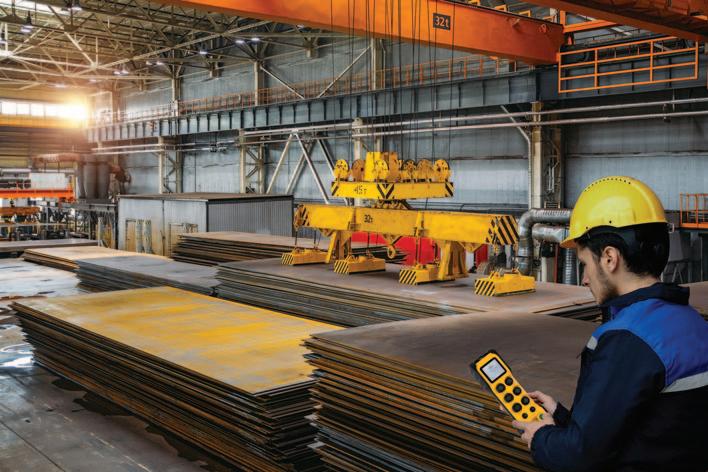
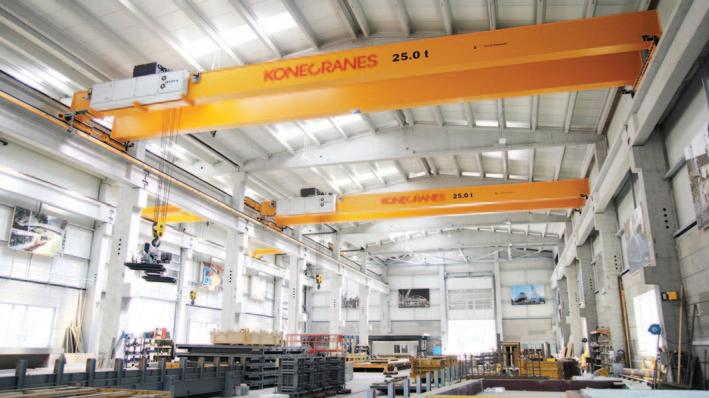
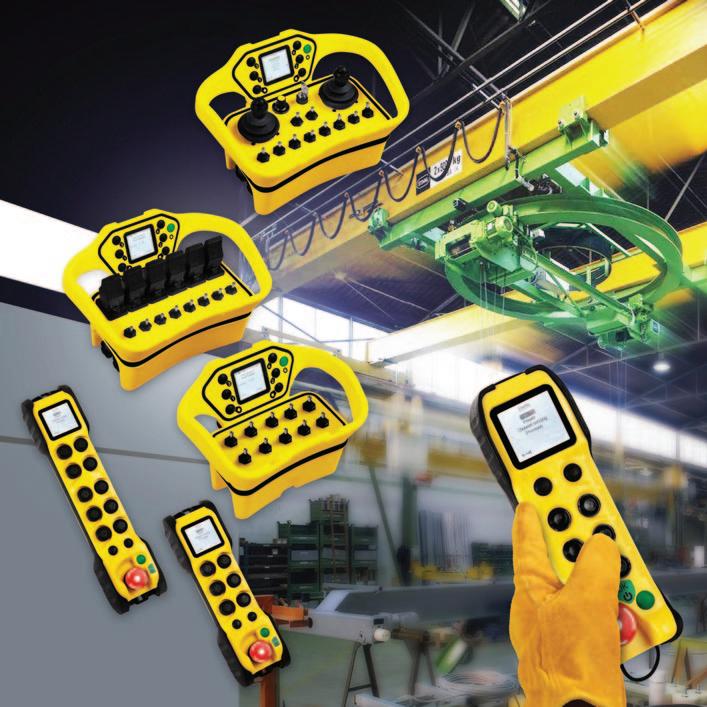
In industry, mobility and safety play an equally central role. With remote controls, mobile machines such as cranes can be safely operated and monitored from a distance. The radio remote controls of the Jay series from Conductix-Wampfler offer safe communication in ideal interaction with solutions for energy and data transmission systems. The radio remote controls are certified for even the harshest environments. Thanks to the ATEX range, the series can also be used in potentially explosive environments and is compatible with most industrial automation networks.
The Jay range was developed at Conductix-Wampfler’s French Centre of Excellence for radio remote controls near Grenoble. The site benefits from its proximity to various electronics suppliers, research and educational institutions and technology parks. It also has extensive expertise in the field of electronics, real-time software, and industrial safety technology. “In addition to our experience in the field of radio technology and safety, our know-how results from in-depth knowledge of our customers’ applications,” explains Philippe Vialette, Product Manager Jay Radio Remote Controls at ConductixWampfler. Starting with standard products and features, ConductixWampfler develops solutions that fit customers’ specific applications and operating environments. “Having worked with many customers over many years, we are familiar with a wide range of hazardous environments. And we are absolutely experienced in integrating a radio transmission system into all types of electrical or electronic architectures,” emphasizes Vialette. This applies to standard cranes as well as to special crane types.
RELIABLE FUNCTIONS FOR EMERGENCIES All Jay radio solutions are designed with safety, ease of use and absolute reliability in mind. The Machinery Directive 2006/42/EC establishes a uniform level of protection for accident prevention for machinery placed on the market in the European Union. The directive emphasizes a comprehensive risk assessment of the machine, which includes a detailed risk analysis. This involves assessing the probability and severity of possible dangerous failures. Jay radio remote controls from Conductix-Wampfler offer safe communication in ideal interaction with solutions for energy and data transmission.
To increase safety, infrared photocells can be fitted to the cranes and the remote control. This not only reliably selects the right machine, but also ensures that operation takes place from a safe zone.
The different series of the Jay radio remote controls from Conductix-Wampfler.
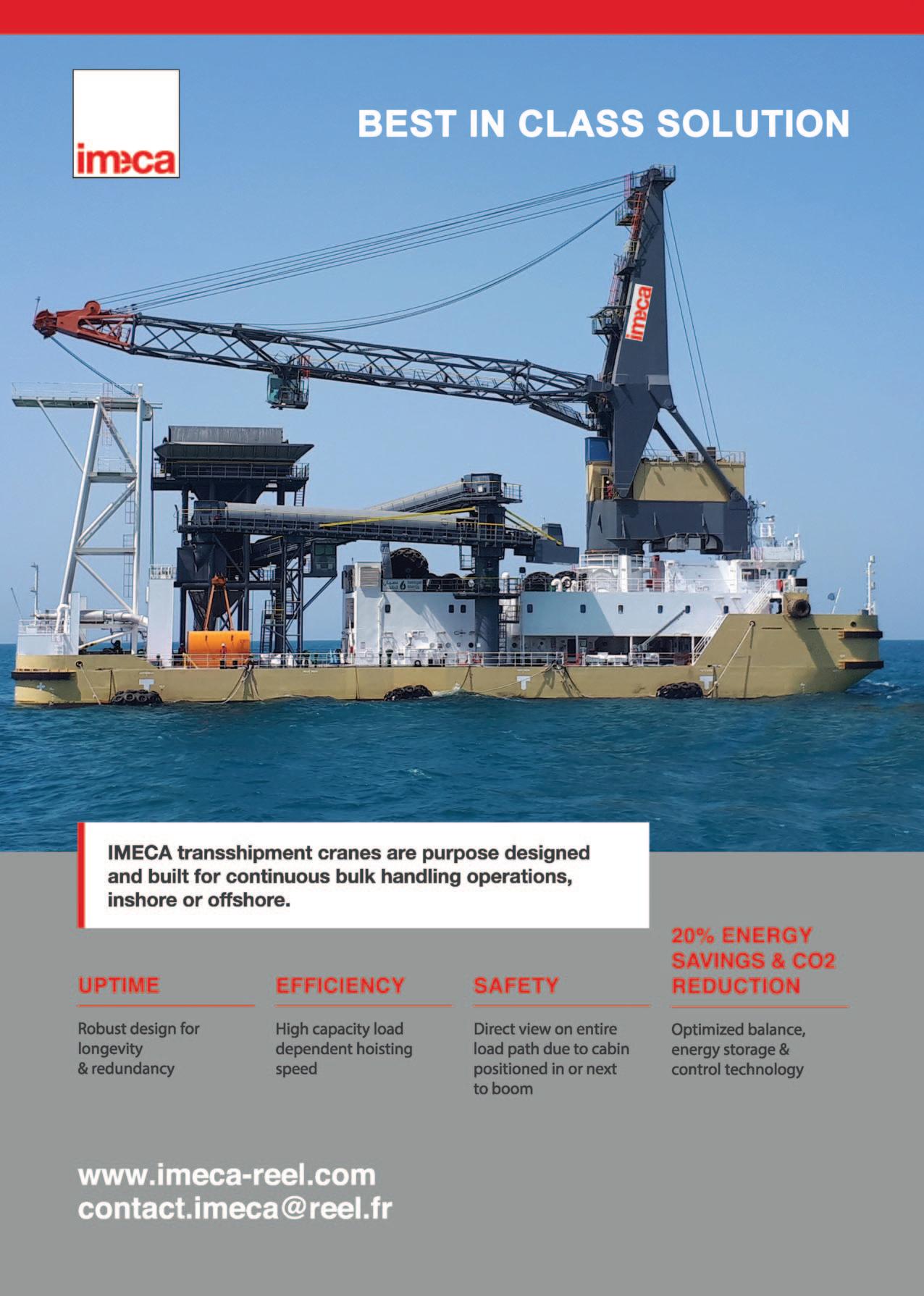
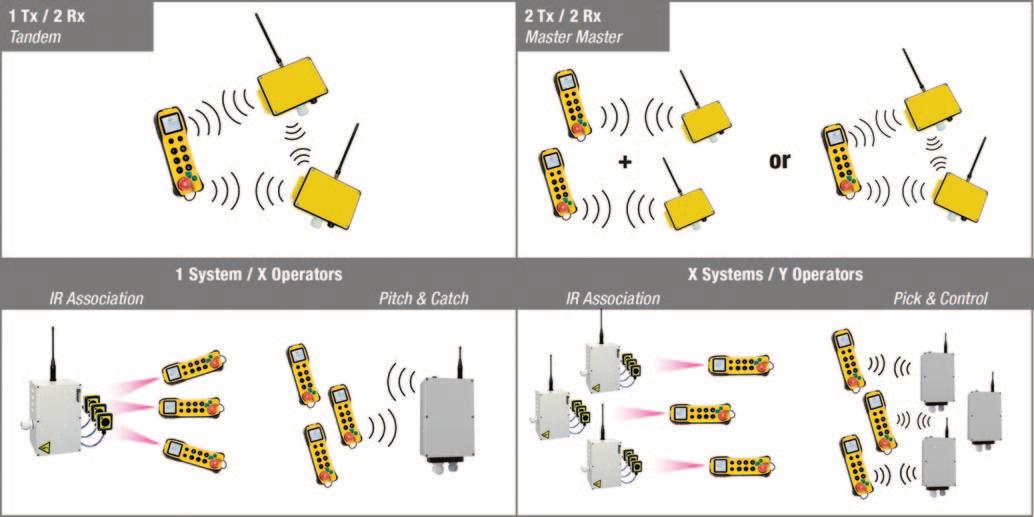
Some common configurations of the Jay radio remote controls from Conductix-Wampfler.
On this basis, a SIL or PL safety level is then set for the crane’s control system.
SIL means Safety Integrity Level and is used to reduce the existing risk of an installation to an acceptable level, i.e. a tolerable risk. This standard increases functional safety and is divided into four levels. The determination of the required SIL level results from the possible measure of damages, the duration of stay of the personnel, the probability of occurrence of a dangerous situation and the possibilities to avoid damage. The Performance Level (PL) is the central safety standard that describes the ability of safety-related parts of control systems to perform a safety function under foreseeable conditions. “The first requirement is an emergency stop that can be triggered in dangerous situations. For standard crane applications, a SIL 2 - PLd rating is specified, while for the most critical applications, a higher level SIL 3 - PLe applies. In addition to the emergency switch, joysticks and command buttons on the remote control can also be assigned safety functions,” explains Vialette. In this way, any release of the command button or joystick stops the movement with proven reliability. For example, cranes with electromagnets or crucibles may require SIL 1 - PLc - category 2 certified push buttons on the remote control. They ensure that unintentional release of the load is not possible.
To further increase safety, infrared photocells can be fitted to the cranes and the remote control. This not only reliably selects the correct machine, but also ensures that operation is from a safe zone. Wireless control and the associated ability to move away from the danger zone of suspended loads make wireless solutions an inherently safer option than pendant controls. In environments where an explosive atmosphere may form - whether due to the presence of flammable gases or the accumulation of airborne dust Conductix-Wampfler offers special ATEX or IECeX certified radio remote controls to avoid any risk of ignition sparks.
INTERFACE FOR INDUSTRIAL AUTOMATION SYSTEMS The radio remote controls of the Advanced Control series from ConductixWampfler can be connected to the most common automation systems via industrial buses such as Profinet, EtherCAT, Ethernet/IP, CANopen, DeviceNet, and others, thereby establishing comprehensive communication. A 2-way radio connection between transmitters and receivers enables the transmission of feedback signals to the subordinate control system. In turn, screens of the transmitters can be used as mobile terminals to display information or warnings to the operators. Also for automatic process cranes, the radio control connected to the PLC is a very useful tool for the commissioning, adjustment and maintenance phases. It allows to take over the manual control of the process step by step or at reduced speed. In this way, maintenance personnel optimize efficiency and safety at the same time.
A major challenge in the industrial environment is to ensure smooth radio communication under all conditions. This can be of the highest safety relevance in an emergency and must not be disturbed by environmental influences. “Obstacles, distance between transmitter and receiver and environmental phenomena such as weather, dust or air pollution affect the propagation of radio waves, can deflect them or even interrupt them. This can have serious consequences such as operational failures or loss of safety if an emergency stop is not executed,” Vialette points out. Conductix-Wampfler has therefore designed its radio remote controls with a wide range of antenna models to adapt to any environment. In addition, the signal strength and the radio ratio in the operating zone are detected at all times. For environments with many physical obstacles, such as densely loaded warehouses, repeaters can reliably amplify the frequency.
WIDE RANGE OF SERVICES FOR VERSATILE REQUIREMENTS The interconnection of several cranes in a synchronized sequence is common practice, especially when handling large parts. The latest generation of radio remote controls therefore offers customized solutions to efficiently control the interaction between several operators and cranes. Here, too, infrared sensors bring additional functional possibilities and safety features. Conductix-Wampfler’s broad product portfolio and high level of system expertise enables customized combination solutions of energy and data transmission systems such as conductor rails, festoon systems or cable reels with radio remote controls for a wide range of systems and applications.
VIGAN’s successful commissioning of two NIV600tph ship-unloaders at Transnet Port Terminal
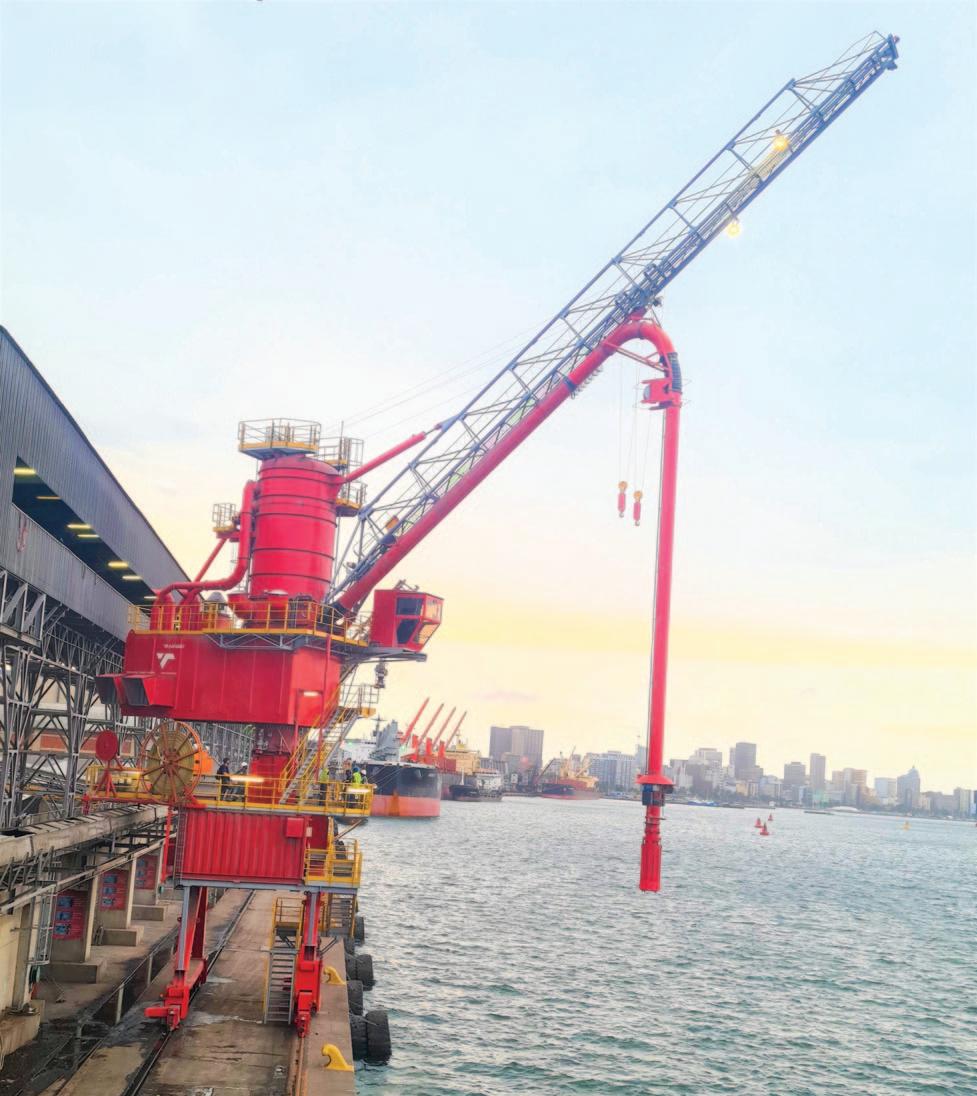
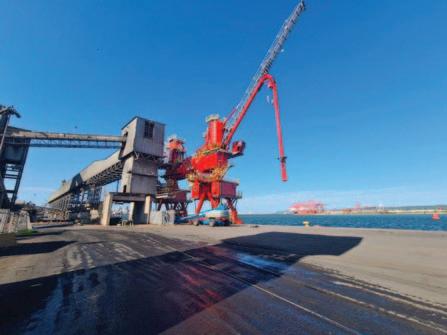
Once again, Transnet Port Terminal (South Africa) has decided to continue to trust VIGAN Engineering’s ship-unloaders.
After using two NIV300tph (tonnes per hour) ship-unloaders for more than 20 years, Transnet decided to double its capacity to cope with the increase in its activities.
The process started during the Covid-19 crisis and the relationship of trust between the two parties was strong enough, despite travel restrictions, to manage the project together efficiently and successfully from a distance.
With these new VIGAN ship-unloaders, Transnet reinforces its role in the unloading of grain in South Africa.
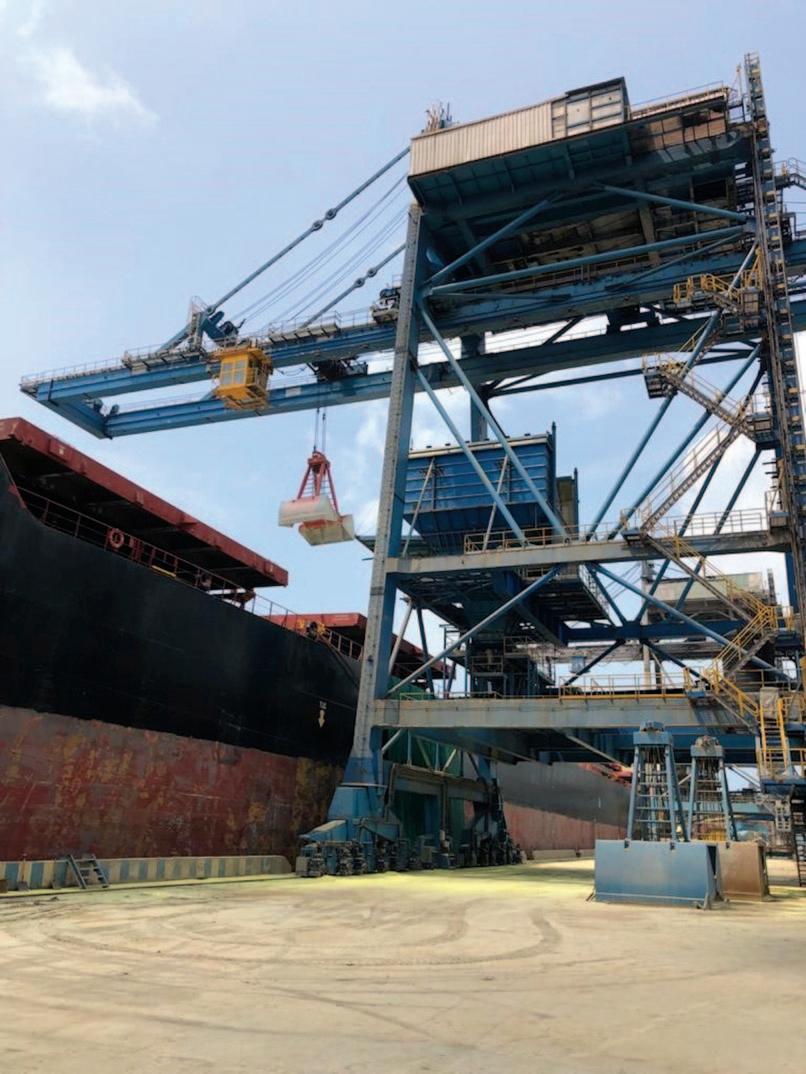
Port cranes have a difficult and demanding job, unloading thousands of tonnes of goods from ships around the clock. This is particularly true of a TRF Limited grab and loader crane operating at Paradip Port on the East Coast of India. The crane helps to supply raw materials to one of the largest fertilizer and chemical manufacturing facilities in India. To ensure reliable braking performance for the crane, TRF approached Stromag to provide a complete system package.
CRANE NEEDED The Indian Farmers Fertilizer Cooperative Limited (IFFCO) operates the manufacturing facility in Paradip. Founded in October 2005, the plant produces two million tonnes of fertilizer every year as well as 7,000 tonnes of sulphuric acid and 2,650 tonnes of phosphoric acid daily. These large-scale operations require a vast quantity of raw materials, which are delivered by ship via the deep seaport at Paradip. When IFFCO took over the plant, it was clear a large clamshell bucket port crane was required to ensure efficient offloading of the bulk raw materials.
TRF Limited, a TATA enterprise which manufactures a range of handling and processing equipment for multiple industries, was approached by IFFCO to deliver the crane. TRF commissioned Stromag in India to provide a suitable braking system for the hoist and bucket clamping mechanisms.
Stromag is a global manufacturer of braking systems for a wide variety of crane designs, with its systems operational on port cranes worldwide. A major brand of Altra Industrial Motion Corp., Stromag can deliver complete braking system packages. The business has a proven track record working with crane OEMs, which ensured it could deliver brakes exactly to the TRF specification.
SAFEGUARDING CRANE UPTIME Akshay Gore, Senior Engineer Customer Care & Sales at Stromag, explains: “The crane was designed to provide an unloading capacity of up to 1,500 tonnes per hour. To achieve the quantities required by IFFCO, the crane operates between 18 to 24 hours a day. Of course, this means that our braking system needs to provide exceptional reliability.” “Crane downtime is very undesirable for IFFCO. Any pause in unloading reduces the supply of raw materials to the plant, compromising productivity. A failure in the braking system due to it not opening or closing could result in a five-hour repair at the very minimum. At Paradip, this translates to around 7,500 tonnes of lost raw material supply. Furthermore, extra costs would be due to ship operators for any delays; valued on an hourly basis. This would be on top of the cost of carrying out maintenance work.”
PUTTING THE BRAKES ON To support the crane’s bucket hoisting and clamping mechanism, Stromag provided TRF with 1TX-A and 3TB-R spring applied, hydraulically released caliper brakes — both Type T service brake variants. These were combined with two types of SVK400 disc couplings, one with a 705mm diameter disc and another with a 550mm diameter.
Stromag Type T service
Demanding job, unloading thousands of tonnes of goods from ships around the clock. This is particularly true of a TRF Limited grab and loader crane operating at Paradip Port on the East Coast of India.
Stromag provided 1TX-A and 3TB-R spring applied, hydraulically released caliper brakes - both Type T service brake variants.
brakes are designed to provide consistent braking force over an entire service life. This ensures that any slippage is avoided, performance is maintained and that the braking torque value doesn’t decrease below acceptable levels.
Braking force is provided by a highquality spring pack, which is subjected to rigorous internal testing by Stromag to ensure reliability over hundreds of thousands of cycles and a high number of duty cycles per hour. Furthermore, an integrated hydraulic system to release the brake reduces the risks of leakage from external piping, maximizing reliability and ensuring a compact design. The arrangement of the brake arms in a V shape provides huge braking force within a reduced footprint. Each brake for the crane was specified with an additional performance margin so that it could operate with extra assurance over a long period.
The SVK400 disc couplings feature a ventilated disc to provide improved thermal capacity. Designed to compensate for torque shocks and peaks, the SVK400 is optimized to be a perfect match for the braking system.

THE BENEFITS OF A COMPLETE SYSTEM “We are a provider of complete braking systems, which unlocks benefits for our customers,” Gore explains. “A perfect match between brake and disc ensures an optimum friction coefficient of the brake friction material and the surface of the disc. This ensures correct and stable brake torque, providing consistent braking performance and exceptional reliability.
The TRF crane at Paradip harbor also benefits from localized maintenance support. Stromag has a large presence in India, with a manufacturing plant located in Pune, Maharashtra. The facility features its own design and hydraulics teams, as well as highly trained service technicians to provide installation, commissioning and maintenance services.
Gore concludes: “By providing a complete braking package, we could ensure consistent braking performance for the TRF crane at Paradip harbor despite high duty demands. This was incredibly beneficial, allowing IFFCO to secure its supply of raw materials and safeguard productivity. With routine maintenance and one replacement of the brake linings, the crane braking system has operated trouble free for 16 years.”
These brakes were combined with two types of SVK400 disc couplings, one with a 705mm diameter disc and another with a 550mm diameter.
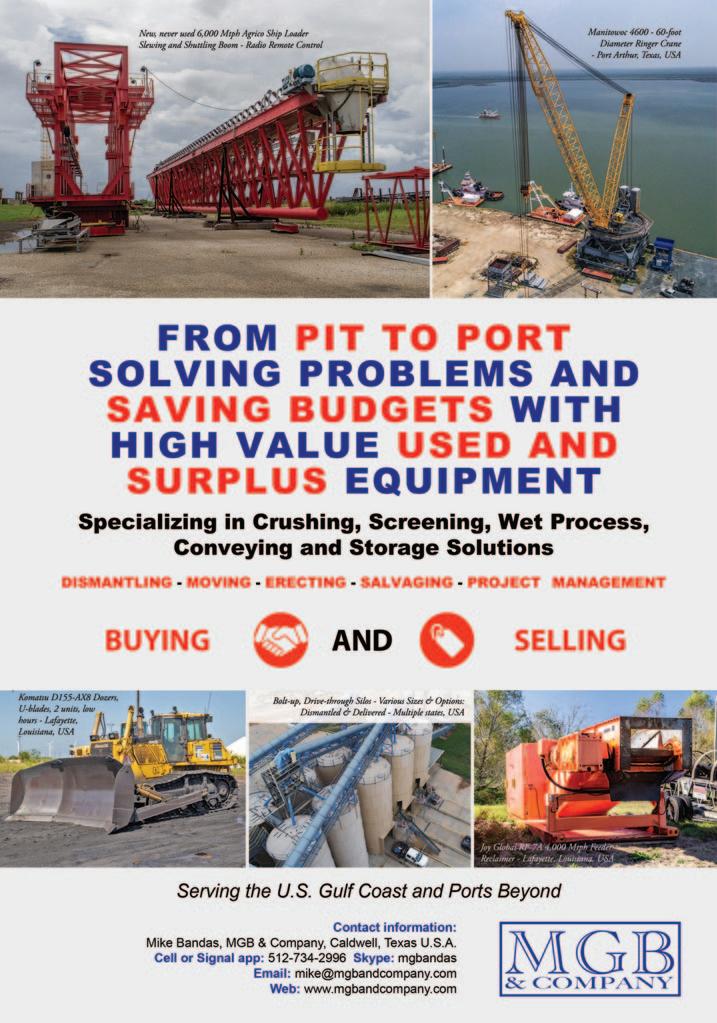
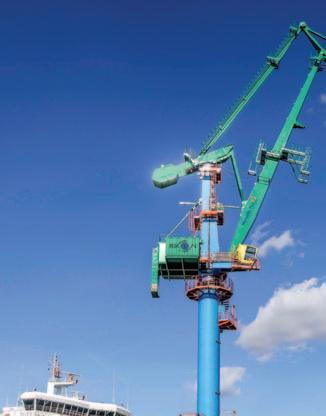
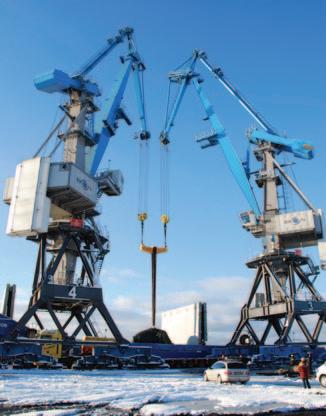
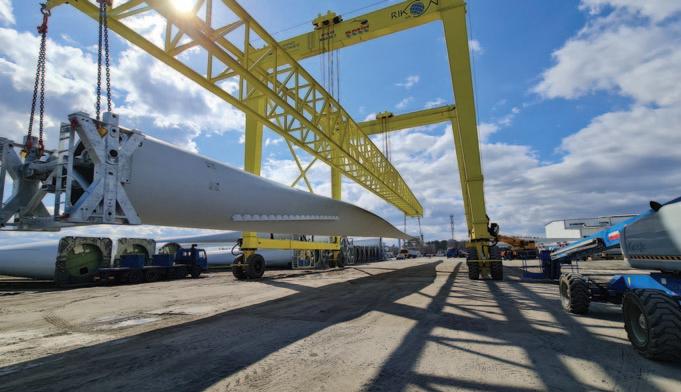
AS RIKON (Riga, Latvia) has been in the lifting and transport market for 60 years and offers design, production, assembly, installation and transportation services of level luffing cranes (double jib and one jib), gantry cranes, mobile harbour cranes, steel structural elements of lifting cranes, electrical boxes for cranes and for vessels. Moreover, the company also manufactures cargo gripping devices like grabs and spreaders.
The company has its own know-how and wide experience in the field of manufacture of lifting and transshipping machinery for ports, shipyards and industrial enterprises. All works, from planning, designing and manufacturing to installation and commissioning are carried out by the company itself. The works are supported by a reliable service.
AS RIKON is located in the territory of Riga Freeport. It has a highly developed infrastructure which consists of a railway branch line, roads, 130 metre-long quay, crane runways and engineering networks.
A serious modernization of the factory was carried out with the installation of new Italian and Finnish equipment, which in turn, attracted world-renowned manufacturers to work with the factory.
The factory is located on an area of 21,000m2, where there are well-equipped plants with an area of 10,000m2. The factory’s lifting equipment is capable of handling cargoes of up to 50t inside the plants and up to 70t outside the plants.
The factory uses modern metal processing and welding equipment, including universal metal cutting machines, computer-controlled plasma and gas cutting devices, including sheet metal bending press with capacities up to 350t and matrix length up to 6m.
The application of almost half a century experience in manufacture of port machinery forms an important precondition for solving the problems of a customer. The production and service of the AS RIKON comply with the standards ISO 9001:2009.
AS RIKON’s competitiveness in the market is facilitated by investing in testing and development of new innovative solutions.
“A modern lifting equipment is a complex technological structure ‘with eyes and brains’. Its work is controlled and regulated not only by humans, but also by IT solutions and countless sophisticated sensor systems, which provide for smooth and safe handling. Our ability to adapt, create innovative solutions and a quality product is our competitive advantage,” said Mihails Baškankovs, Commercial Director of AS RIKON.
The cranes created by AS RIKON are able to operate and safely perform their functions in both Arctic and tropical climates. Cranes designed to work in the Arctic shall be able to perform safely even at –50°C, so they are made of highstrength steel and metal alloys, while special painting technologies are used in warmer and wetter climates. Every manufactured part, every weld is subjected to careful quality control and certification procedure.
RECENT SUCCESSES v On 6 2022, AS RIKON signed a contract with First Dry Port Terminal in Uzbekistan for one gantry crane, 41 tonnes under spreader; v Earlier in June 2022, AS RIKON signed a contract with one of the biggest
Spanish government companies, ADIF, which operates all of Spain’s railways, for two gantry cranes, 41 tonnes under spreader; At the end of 2021 the company
Level luffing crane supplied to Great Port Of Marseille. AS RIKON cranes in Riga.
Special electro-hydraulic RTG crane supplied to LM WIND POWER, Poland.
v
v
v signed a contract with Port Of Brcko, Bosnia and Herzegovina for the supply of a 27 tonne double jib level luffing crane; At the end of 2021 AS RIKON supplied a level luffing crane to the biggest French port Great Port Of Marseille. The crane takes part in the repair and painting of cruise vessels. The crane has a smart anti-collision system installed, which takes into account not only the position of the cranes on the tracks, but also the crane’s degree of rotation, boom outreach, etc. The RIKON specialists also modernized the existing old crane of Great Port Of Marseille; Mid-2021 AS RIKON supplied a special electro-hydraulic RTG crane to LM WIND POWER, Poland, (part of General Electric, USA). The crane is equipped with special traverse, the length is 70 metres and the weight is 40 tonnes and handles wind turbine blades.
ENGINEERING & EQUIPMENT Works on more than 1,000 metres: igus develops the world’s first driven e-chain system for long travels
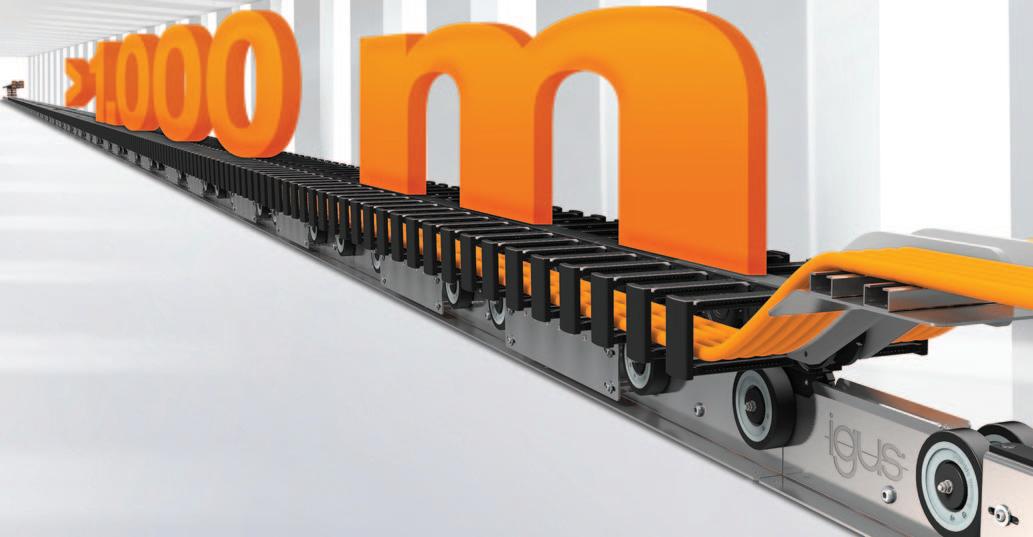
High dynamics and long service life: the igus drive-chain is the world’s first powered e-chain system for long travels (1,000 metres and more). (Source: igus GmbH)
DRIVE-CHAIN IMPRESSES WITH MAXIMUM DYNAMICS AND LONG SERVICE LIFE, WHILE SAVING UP TO SIX TONNES OF WEIGHT Almost no limits on long travels, high dynamics, long running times — these are the characteristics that distinguish the innovative igus drive-chain. The world’s first energy chain with its own drive ensures significantly longer running times on extremely long travels because hardly any push/pull forces act on it. Across the globe, rail-mounted automated stacking cranes (ASCs) in ports are just one of the applications that benefit.
Forty years ago, container ships were tiny compared to today’s vessels. They held an average of 1,000 containers. Today, giants in the Triple-E class carry almost 24,000 containers — and that number is rising. These sizes pose challenges for ports, which must continuously expand their infrastructure, including the ASCs that load containers onto lorries and trains. The huge overhead cranes now travel on rails for distances of several hundred metres and more. In many cases, the motor cables follow the movement of the ASC cranes.
“At lengths of over 1,000 metres, enormous push/pull forces act on the echains,” says Jörg Ottersbach, Head of the e-chains Business Unit at igus. “To prevent this load and further optimize energy supply system service life in extreme applications, we are the first developer in the world to develop an energy chain with its own drive.”
E-CHAINS USE THEIR OWN DRIVE TO FOLLOW ASC MOVEMENT The drive-chain design concept works as follows: drive boards are mounted on the outer radius and drive the e-chain in the lower run. The bottom rail has motordriven friction wheels on the sides and rollers on the top. When the crane sets off, the friction wheels also start their motors. The lower run travels along the rail in a synchronized movement, during which hardly any push/pull forces from the moving end act on the chain links. “This gives us a minimal load, low wear and long service life on travels of 1,000 metres and more,” says Ottersbach. igus is also already working on an alternative drive concept that replaces friction wheels with linear drives.
E-CHAINS WITH DRIVES ARE AN ALTERNATIVE TO STEEL CABLE DRUMS Self-powered energy supply systems are an economical alternative to traditional systems that have been used in ASCs for decades: steel cable drums that wind and unwind motor cables — often in two directions when the fixed point of the cable is in the middle of the travel. The problem is that when the crane approaches this fixed point, it has to brake to allow the cable guidance system to pivot. This takes time, which is critical at a period when ports must continuously increase productivity. Motor drums also weigh four to six tonnes, which considerably increases the crane’s energy consumption. “Since the drive-chain travels on the rail without interruption, ASCs no longer need to brake near the fixed point in the middle. They can thus work more productively,” says Ottersbach. “At the same time, the e-chain system increases neither the overall weight nor the system drive power required to move it. The lower weight allows speeds of 6m/s even on long travels. These are significant advantages, benefiting more and more port operators around the world.”
ABOUT IGUS igus GmbH develops and produces motion plastics. These lubrication-free, highperformance polymers improve technology and reduce costs wherever things move. In energy supplies, highly flexible cables, plain and linear bearings as well as lead screw technology made of tribo-polymers, igus is the worldwide market leader. The family-run company based in Cologne, Germany, is represented in 35 countries and employs 4,900 people across the globe. In 2021, igus generated a turnover of €961 million. Research in the industry’s largest test laboratories constantly yields innovations and more security for users. 234,000 articles are available from stock and the service life can be calculated online. In recent years, the company has expanded by creating internal startups, e.g. for ball bearings, robot drives, 3D printing, the RBTX platform for Lean Robotics and intelligent “smart plastics” for Industry 4.0.