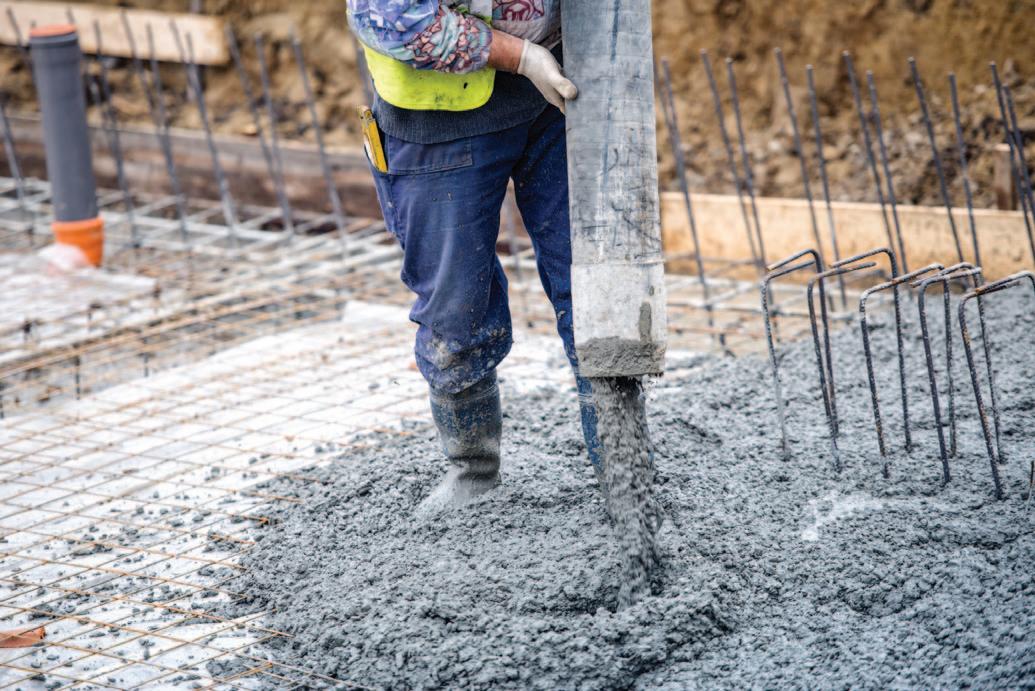
16 minute read
CEMENT TRADE: BELLWETHER OF WORLD ECONOMY
building infrastructure depends heavily on cement
Despite high cement production capacity, both China and India depend on clinker and limestone imports
A symbiotic relationship exists between the volumes of seaborne trade in cementitious materials and how the world economy — particularly in emerging nations such as China and India and developing countries — fares at a given point, writes Kunal Bose. This is because in their pursuit of building infrastructure and providing housing to the masses, large volumes of cement and steel will come for use.
Even while China has a towering presence in cement manufacturing capacity and production as it has in steel and aluminium, it leads other countries in import of clinker made from processing of limestone for use in making cement. The China Cement Association (CCA) informs that while cement production in China has continued to stay high, the country is accessing growing amounts of clinker from abroad, particularly Vietnam, which with cement output of 100mt (million tonnes) ranks third in global pegging after China and India.
According to analysts, China’s 2020 clinker imports at 33.4mt registering a 47% year-on-year leap are a pointer to two compulsions: first, clinker production based on burning of fossil fuel coal is a major emitter of greenhouse gases (GHG) and, therefore, a subject of concern for the Chinese ministry of ecology and environment. Second, besides conservation of local limestone resource leading to reduction of GHG emissions at the point of mining, Beijing wants the industry to be committed to permanently shut down the ageing clinker units, all energy guzzlers. Incidentally, as much as 60% of Chinese imports of clinker are from Vietnam.
That there could be uneasiness in Beijing about such overwhelming dependence on Vietnam for clinker imports is a given. Uneasiness in political relationship and also the fact strict state control obtains in Vietnam further add to Beijing concern. In this context, CCI has dropped hints of China fixing standards for clinker imports linking to verification of
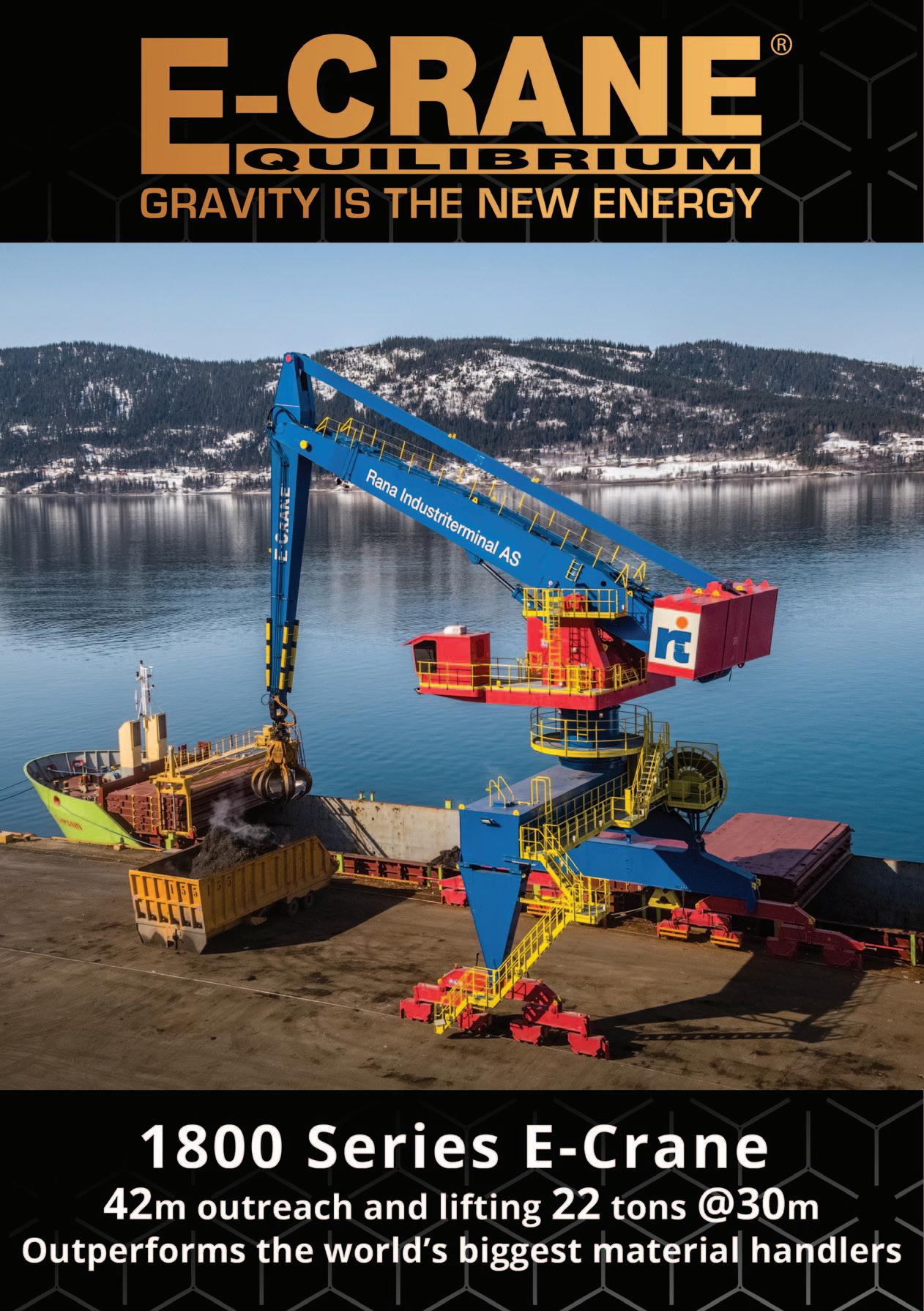
carbon dioxide (CO2) emissions and product quality. Cement machinery manufacturers, particularly in Europe, are concerned that the Chinese move on clinker import screening will favour the export surplus countries where Chinamade machinery is in use. Whatever it is, the fact is Vietnam has rich deposits of limestone, both in terms of size and quality. According to a recent study of clinkermaking raw material (limestone) deposits in Vietnam and Korea, the material is found over 50,000 to 60,000km2 of the former nation or 20% of its territory. The report says of the 351 limestone deposits in Vietnam, 274 sites have undergone investigation revealing reserves of 12.557bn tonnes and resource of 32.180bn tonnes. This apart, the country is fairly richly endowed with dolomite, with reserves of 124mt and resource of 2.676bn tonnes. (Dolomite seen mainly as a refractory material also finds application in cement.) Indonesia too is sitting on huge limestone deposit. Jamaica, known more for its bauxite exports has limestone deposits of 150bn tonnes of which 50bn tonnes are deemed recoverable at this stage. Calcium carbonate concentration in much of Jamaican bauxite being 95% to 98%, the resource there will be much coveted. Almost every country owning the material in large volume wants local value addition to clinker rather than export the raw material itself. Here too sub-nationalism is at work. Then limestone lends itself to seaborne trade ideally over short distances because of its bulk and low value.
India, which is the world’s second largest in terms of cement capacity and has a share of around 8% of global production of the binding material is too an importer of clinker and also of cement. The principal source of Indian import of clinker is Iran and of cement United Arab Emirates, Pakistan, Vietnam, Japan and Bangladesh. However, revenues from and volume of exports are far in excess of imports. For example, during 2020 out of India’s total cement imports of 2.2mt, UAE had a share of 691,000 tonnes. That year Iran supplied 522,000 tonnes of clinker to India. India mainly exports cement to Sri Lanka, Nepal, the USA, the UK and Maldives.
Incidentally, South India Cement Manufacturers Association (SICMA) wants New Delhi to impose customs levy to an extent that will discourage imports of clinker and cement. Asked about the logic supporting the demand, a spokesperson for SICMA says: “We are facing cement duty barriers in a number of markets where we are traditional exporters. You know, the country’s cement capacity is distributed regionally and south Indian plants have a predominant share of 40% of that. Similarly, the major portion of Indian limestone resource is found in the south. Put a higher duty on imports. But at the same time facilitate movement of clinker and cement produced in the south to other parts of the country through telescopic railway freight.”
An Indian cement industry official says that over the years Chinese cement machinery and equipment manufacturers have invested heavily in research & development resulting in “significant improvement in product quality, coming quite close to what are all available from European suppliers.” He further says: “The gap between European and Chinese machinery in terms of efficiency and durability is hardly 10%. But China is already making some machines that are as good as the ones available anywhere else in the world.”
Machines in employment in India with a long tradition in cement making are very largely from European manufacturers such as Copenhagen headquartered FL Smidth and Loesche GmbH. But the rapid emergence of China as a supplier of quality machinery at competitive prices has made cement clinker and grinding units in India to start placing orders with Chinese equipment suppliers. The Chinese cement making capacity may not grow further. But what has already started happening, as the world earlier saw in cases of steel, aluminium and coal, is that cement plants of old vintage emitting unacceptable levels of GHG will soon start to be replaced with new units under a state order. For securing such orders, European machinery suppliers will be engaged in fierce competition with their Chinese peers.
Besides India, cement capacity growth will be occurring in some south and southeast Asian countries, West Asia, Africa and Latin America where also machinery manufacturers of European and Chinese origin will be locked in competition to secure orders. More and more countries are demanding of industries to bring down GHG emissions. Cement, which has a share of nearly 8% of global GHG emissions, is naturally an important correctional target of governments from China to India to Western European countries. This is also the case with steel which pollutes the global environment in a slightly bigger way than cement.
The question is how does the cement
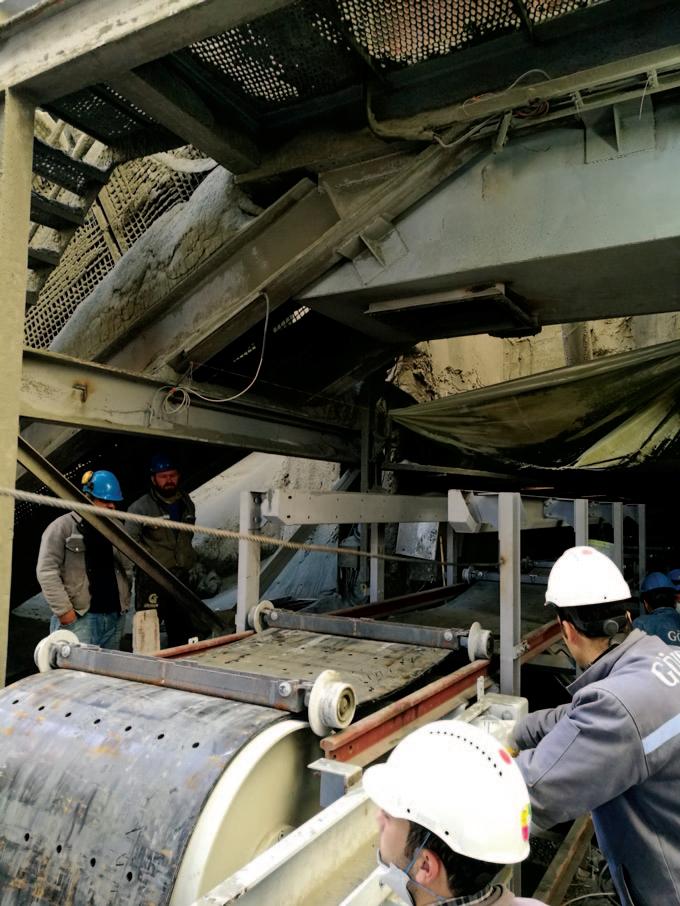
industry go about the goal of net zero GHG emissions? International Energy Agency (IEA) says the direct CO2 intensity of global cement production increased 1.8% a year during 2015–20. This calls for 3% annual cut in emissions till at least 2030 to be on track with net zero emissions target by 2050. The key strategies to arrive at that goal, IEA says, will be to “improve energy efficiency, switch to lower-carbon fuels, promote material efficiency (that is, to reduce the clinker-to-cement ratio and total demand) and advancing process and technology innovations such as carbon capture and storage (CCS).” (Incidentally, during 2015–20, the global clinker-tocement ratio is estimated to have increased at an average of 1.6% per year, reaching an estimated 0.72 in 2020. Unquestionably, this rise was the main reason for the increase in direct CO2 intensity of cement production over the period.)
The last of IEA recommendations underpins the need for machinery manufacturers to produce more advanced plants with better energy efficiency and much less emission of GHG. The quality of machines to be available in future in terms of environment friendliness will depend on their investment in R&D, where considerable government support, including liberal financial incentive will be needed. Expect the ongoing competition between European and Chinese cement machinery makers to now also focus on making plant and machinery that will have increasingly high standards of environmental friendliness. A few Chinese mills have installed CCS units at a very high capital cost. But they are not able to recover the resulting incremental production cost from cement sales. The cost consideration is standing in the way of CCS system gaining popularity in the industry.
An official of a leading Indian cement group says: “This kind of competition works to our advantage. Most of the leading cement companies are setting up either clinker units or grinding plants or both at the same time to grow capacity. We are advantageously placed to drive hard bargain with machinery manufacturers whose margins may come under some kind of pressure. Recent major price inflation of metals, particularly steel, will, however, force machinery makers to pass on the incremental cost to us.”
Foreign groups such LafargeHolcim acquired majority ownership of two major Indian cement companies, namely, ACC and Ambuja Cement with combined capacity of 65.90mt and Heidelberg Cement that opened its India chapter with acquired capacity of 3mt in 2006 has by now more than doubled capacity through organic and inorganic routes. In fact, the Indian cement sector with considerable growth potential is holding major attraction for foreign groups. Indian Brand Equity Foundation says in a report that between April 2000 and September 2021, foreign direct investment (FDI) in cement and gypsum products in India was $5.24bn. Going by the forecast of rating agency ICRA, cement in India will have new capacity of 80mt by 2024 and that will be most impressive since the start of the millennium. This is driven by government-directed high spending on infrastructure and housing in which the private sector is a keen participant. ICRA further says rural housing demand and push to infrastructure projects had likely lifted Indian cement production by 12% during the financial year ended March 2022.
According to the country’s Cement Manufacturers Association (CMA), India has built capacity of 545mt, 99% of which is dry process based. Over the years, the Indian cement industry has seen some remarkable capacity consolidation initiatives, heralded mostly by Ultratech Cement, part of KM Birla Group, which also owns leading aluminium maker Hindalco. Experts say, capacity consolidation work is largely over with Ultratech, a serial buyer of assets, being counted among world leaders in terms of size, operational excellence and profitability (EBITDA basis.) The demand for assets is still very much there, but nothing any longer is coming on the block. In the circumstances, industry leaders are concentrating on optimizing the operating assets and also embarking on organic growth. For example, chairman of Ambuja Cement Narotam Sekhsaria says: “As part of our growth strategy, we are investing in cement grinding expansion plan of 7mt across locations, including in a greenfield project at Barh in Bihar. This will help us move closer to our target of achieving 50mt capacity (currently 31.45mt) in the near future.” As well as Ultratech and LafargeHolcim, some others such as Shree Cement, Dalmia Bharat, Birla Corporation, JK Cement and Ramco have made significant contribution to capacity consolidation.
Interestingly, now a buzz is getting increasingly stronger that LafargeHolcim, the world’s largest in global pecking order in the industry, is considering exiting Indian cement business, wholesale. As the Swiss company is “gauging interest of potential buyers” in India and abroad about acquiring its two subsidiaries — Ambuja Cement and ACC — it may already be engaged in preliminary talks with JSW Group and Adani Group. But why should LafargeHolcim want to leave India after its highly successful journey over 17 years? It may have got to do with its move to diversify away from its core cement and aggregate business to focus more on building technology as it swears by sustainability. The Swiss Group has in recent times sold assets in Brazil and Zimbabwe and using the proceeds to retire debts and diversify through acquisitions, outside traditional cement in roofing and building products.
Well established on the home turf, Ultratech (the biggest in India with capacity of 120mt) has a strong presence in UAE, Bahrain and Sri Lanka. In the meantime, Shree Cement acquired UAE based 4m tonne Union Cement Company (UCC) in 2018 at an enterprise value of $305.24. UCC located close to the Saqr port is strategically placed to sell cement in Gulf Cooperation Countries, Africa and south Asia. An industry official says: “Technologically and also financially some Indian groups have the required muscle to indulge in their kind of wanderlust. But their focus will be mainly on building capacity in India where cement will be much in demand from infrastructure, construction and house building sectors.” Since its acquisition of Union Cement, Shree Cement has commissioned at Ras Al


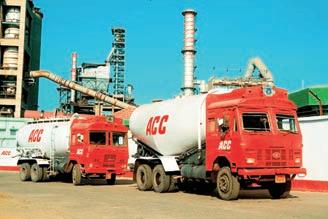
Khaimah in UAE one of the world’s largest kilns with daily capacity of 14,500 tonnes. In the meantime, Beijing wants the cement industry to be cleaned up of “ageing, energy intensive and polluting” capacity, ideally in the next three years. Accordingly, CCA has identified 210 kilns with capacity of less than 2,000tpd [tonnes per day] (or 3.2% of industry total capacity) and 125 kilns of less than 2,500tpd (4.3% of capacity) to be taken off the production line. The combined clinker making capacity of the two sets of kilns is 134mt, which is equivalent to cement production capacity of 210mt. CCA says all these plants earmarked to be taken down were built in 1990s before a major wave of technological breakthroughs in cement making emerged. As China is on the path of replacing polluting capacity with energy efficient advanced plants, it has also decided to go the Western way to push the country’s nearly 3,400 cement units to use in an increasingly bigger way alternative fuels such as solid municipal waste, used tyres and methane from landfill.
China generates annually over 300mt of municipal waste and Beijing wants cement mills to use all of that as a fuel alternative to coal. But China’s progress in alternative fuel ratios at 3% pales into insignificance compared to 20% to 30% obtaining in many other countries. Germany’s advance in this area approaching 70% is the most impressive. Indian cement makers are yet to make a meaningful beginning in using non-fossil fuels to cut GHG emissions. In most places, including China and India, the focus remains on reducing clinker to cement ratio, helped to a major extent by increasing consumer uptake of blended cement. Because of this, the world will experience from here stronger growth in cement blended with industry by-products fly ash and slag and grey cement in general and more modest growth in clinker and white cement. CW Research says in a report that the combination of production rationalization and a regime of increasingly stricter environmental regulations will have a bearing on local supply of cement in China in future years. (Incidentally China had a share 2.5bn tonnes of cement in 2021 total world output of 4.4bn tonnes.) That will give a push to its imports, mostly from Asia Pacific region. The research agency further says following the post Covid-19 general economic rebound, the volume of seaborne trade in cementitious materials will climb to 192mt by 2026. In this the combined share of clinker and grey cement will be almost 85%. The growth in seaborne trade will be mostly on the back of China.
Impending election in Brazil ‘opens the taps’ and causes cement surge
The Brazilian cement industry has experienced a revolution in the past couple of years, writes Patrick Knight. The industry’s 96 plants are set to sell 64.8mt (million tonnes) this year, compared with only 52.3mt sold last year. This was the sixth year when sales average about 50mt. Brazil sold a record 71.2mt in 2014.
The structure of the industry has changed entirely in the past few years as well. This year only 11 companies will make cement, while in 2019, 24 such companies operated. This year, companies will operate 96 mills, compared with the 30 operating in 2000. The industry is composed of 100 plants.
The industry is dominated by three giants: v Votorantim, the world’s fourth largest cement maker, made 22mt in its plants last year. Votorantim’s cement sells in nine countries, the US, Canada, Spain,
Bolivia & Uruguay in South America,
Turkey, as well as Morocco & Tunisia in
North Africa. v The merged Lafarge/Holcim, Brazil’s second largest cement maker, also has 22 plants. v In third place is Intercement, owned by Brazil’s largest construction company, Odebrecht, which has 19 plants. Odebrecht is strong in the region, having plants in Argentina,
Bolivia, Uruguay, and Paraguay. Only one company, Apode, has more than a dozen plants. Brennand and Lisa each have four plants. Four companies, Ciplan, Nacional, Itambe & Cecil have only one plant.
The main reason for the sudden resurgence of demand for cement in Brazil, (40% of which is sold in 50kg bags to small consumers, who use it to improve their ‘self built’ homes) is that Brazil’s controversial President Jair Bolsonaro, is standing for election in September this year. Until a few months ago, it seemed virtually certain that Bolsonaro would be soundly beaten by his long term rival, the two term ex-president, ‘Lula’ da Silva. But the gap has narrowed greatly in the past few weeks. Bolsonaro has adopted the tactic usual to politicians. He has opened the taps. Previously cash-
CEMENT PRODUCTION IN BRAZIL
.
Year
2022 (est) 2021 2020 2019 2018 2017 2016 2015 2014 2013 2012
Source: Cement Industry Association.
tonnes
64.8 52.3 50.1 54.4 52.7 53.8 57.6 64.4 71.2 71.2 69.3 strapped local adminstrations, have seen funds start to flow in freely. Work has started on delayed projects connected with infrastructure. Brazil has embarked on a major new rail building programme, with thousands of kilometres of new track being laid. New ports and airports are being built, new roads are being built. A major new housebuilding programme has been started. All this means, of course, a huge upsurge in demand for cement.
It is perhaps surprising that this surge in demand for cement comes at a time when the Brazilian economy is stagnating. The country’s GDP growth has been negative for several years. Inflation is soaring, unemployment up. The situation has been saved by the boom in exports. Because of the war in Ukraine, the prices of all grains, notably soya and maize, are booming. Demand for, and prices of, bulk goods, notably iron ore, bauxite, alumina, copper, and nickel are up.
Many industries are suffering, notably the motor industry. Others, such as the buoyant pulp and paper industry are doing very well. Several very large new mills are under construction, as sales to China, now by far Brazil’s leading export market, not only for pulp and paper, but also for iron ore, and above all, crude oil, of which Brazil has now become a major exports. With crude prices so high, oil exports, along with those for grains and iron ore, are a major contributor for Brazil’s export earnings. DCi