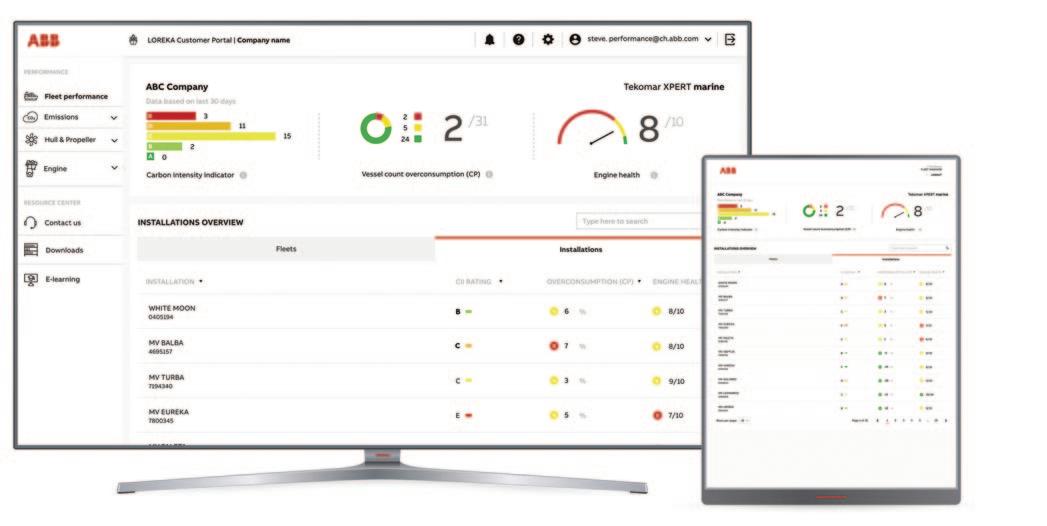
19 minute read
IF-THEN-ELSE: SOFTWARE & AUTOMATION IN BULK HANDLING
Tekomar XPERT marine’s customer portal offers all-inone vessel efficiency and emissions monitoring. ENGINEERING & EQUIPMENT
ABB Ability™ Tekomar XPERT marine is a digital suite delivering powerful insights into vessel performance, as well as CO2 emissions monitoring and reporting
ABB estimates that deeper insights into a vessel’s operational data enabled by Tekomar XPERT marine can provide up to 20% fuel reduction, cutting costs and emissions as a result
The digital marine suite provides easy to use, automated reporting that saves time and increases operational efficiency
ABB Turbocharging has launched Tekomar XPERT marine, a comprehensive digital solution that offers shipowners simplified management of propulsion efficiency and emissions reporting. By enabling potential combined emission savings of up to 20%, this product suite can make a significant contribution to the decarbonization of the shipping industry, which is under regulatory pressure to halve its carbon footprint by 2050.
Tekomar XPERT marine comprises three modules covering the engine, hull and propeller, and emissions. Combined, these modules provide actionable insights into ship performance, based on which shipping companies can make better operating decisions, which lead to notable fuel savings. This, in turn, enables vessels to achieve improved carbon intensity index (CII) ratings. Charter party conformity on emissions reporting is also eased.
Tekomar XPERT’s engine module is already an established solution favoured by many shipping companies and currently optimizes the performance of more than 8,000 engines in operation. The hull and propeller and the emissions modules have now been launched to further extend the solution’s capabilities.
The emissions module enables the CII rating and CO2 emissions to be accurately forecasted, allowing for pre-validated emissions reporting in line with the International Maritime Organization’s (IMO) and the EU’s Monitoring, Reporting & Verification (MRV) requirements. The module has an easy to use, automated reporting function based on electronic logbook data. The actual CII ranking and its simulation is based on the key operating parameters of the vessel, as well as historic data.
The hull and propeller module provides insights into the vessel’s performance in real time. For example, it enables an accurate assessment of de-fouling requirements, which can have a significant positive impact on vessel’s performance –fouling can lead to an overconsumption of fuel of up to 20%. With this level of insights, effective planning of improvement actions is greatly simplified.
“Tekomar XPERT marine raises our digital offering to a new level by adding the hull and propeller, and emission modules to our engine room offering. These combined analytics deliver real customer value through enabling greater efficiencies. For example, fuel savings of up to three tonnes per day can be achieved by optimizing performance of the engines alone, which translates to some nine tonnes of CO2 emissions per day,” said Cristian Corotto, Vice President Digital Customer Solutions ABB Turbocharging. “Just as important is the system’s delivery of information needed to support decision-making related to the optimal timing of cleaning events, and the identification of the root cause of reduced propulsion efficiency. Essentially, with Tekomar XPERT marine customers are ready for the next level of data-driven decision making.”
Results of analyses from all the three modules are immediately available to shipowners and operators, and the solution can be integrated to work with existing data collection systems without the need for installing additional hardware. The expanded digital analytics offering promotes benchmarking, historic tracking and forecasting. Furthermore, the system offers advisory support on all levels, from the engine to the ship’s hull and propeller, as well as its emissions and CII ranking.
Customers can gain 24/7 access via a portal where they can view and benchmark their entire fleets. Operational data can be shared with ABB via C-2-C connectivity, following which ABB will assess, analyse and provide expert operational insights. Tekomar XPERT marine functions across all engines regardless of make, type and age.
ABB’s Process Automation business specializes in automation, electrification and digitalization for the process and hybrid industries. It serves its customers with a broad portfolio of products, systems, and end-to-end solutions, including its distributed control system, software, and lifecycle services, industryspecific products as well as measurement and analytics, marine and turbocharging offerings.
Rockwell Automation, Inc., the world’s largest company dedicated to industrial automation and digital transformation, has been recognized by Ethisphere, a global leader in defining and advancing the standards of ethical business practices, as one of the 2022 World’s Most Ethical Companies.
This is the 14th time Rockwell has been included on this prestigious list which honours companies that demonstrate exceptional leadership and a commitment to business integrity through best-in-class ethics, compliance, and governance practices.
“We’re proud to once again accept this recognition by Ethisphere, which highlights our commitment to ethics and integrity,” said Rockwell Chairman and CEO Blake Moret. “We’re doing extraordinary things for our industrial customers. We approach these challenges with passion because what we do is essential to making the work more productive and more sustainable.”
Ethics and integrity are among Rockwell’s highest scoring drivers of employee engagement, nurtured and cultivated through a robust commitment and a strong ‘speak up’ mindset, including the company’s long-standing Ombuds programme. Rockwell also requires 100% of its Board of Directors, employees, and contractors to complete an Annual Ethics Training, which is updated each year.
“Today, business leaders face their greatest mandate yet to be ethical, accountable, and trusted to drive positive change,” said Ethisphere CEO Timothy Erblich. “We continue to be inspired by the World’s Most Ethical Companies honorees and their dedication to integrity, sustainability, governance, and community.”
Rockwell was one of only 136 honorees recognized spanning 22 countries and 45 industries. Grounded in Ethisphere’s proprietary Ethics Quotient®, the World’s Most Ethical Companies assessment process includes more than 200 questions on culture, environmental and social practices, ethics and compliance activities, governance, diversity, and initiatives to support a strong value chain.
Big appetite for SET Maritime toolkit to enable digital transformation
SET Maritime is pointing the way for digital decision-making in the shipping industry after a surge of downloads of the newly launched Software Evaluation Toolkit (SET) as more supporters seek to come onboard. “This has certainly hit the sweet spot in an industry struggling with digitalization and the level of interest we have seen shows there is a definite need for such a tool in shipping,” says David Levy of Get SET Maritime, a joint initiative of various stakeholders set up to promote it to the wider industry.
There have already been scores of downloads of the free open-source tool –essentially a workbook with benchmarking criteria to evaluate different software vendors — with a high conversion rate of around 36% from visits to the SET Maritime website within a few weeks of the launch.
In addition, three other companies — software suppliers Dataloy and Ports+, and media firm Fathom World — have so far come onboard as supporters, in addition to existing backers Kongsberg Digital, DTN, SEDNA, OrbitMI, Stena Bulk, The Digital Ship, Marine Money and Blue-C.
‘CONFUSING LANDSCAPE’ Fathom World owner Craig Eason says: “The time is right for this toolkit given the myriad number of maritime software vendors out there and the difficulties for shipping companies in making the right selection decisions to procure applications aligned with their business model.”
Levy explains SET Maritime is intended to help companies make the right software decisions to speed up industry adoption of new digital technologies that are necessary to meet decarbonization goals, as well as stimulate cost savings in areas such as fuel efficiency.
“The problem is there are now multiple vendors touting different applications within categories such as voyage management, navigation and cargo & vessel tracking, and this makes the maritime technology landscape very confusing for software buyers,” he says.
“The number of software vendors has tripled to more than 550 in only three years so there are a lot of aggressive vendors looking to capitalize on market demand for digital tools and it is difficult to determine which of these has a relevant product – or just a Powerpoint presentation.”
“Software buyers can become confused over what type of technology is available in relation to what they really need and, consequently, bad choices are made. Ultimately, progress gets slowed down, and money and valuable time are destroyed.”
SCREENING AND ANALYSIS To tackle this pressing industry issue, SET Maritime functions as a screening and analysis tool that enables software buyers to assess up to six different vendors based on criteria such as company profile, solution architecture, and usage and extendibility.
The workbook has a 1–4 scoring system to rank vendors on a checklist according to these criteria and provides a final visualization in the form of a radar chart showing the relative performance of each vendor.
Levy underlines the tool is provided as a blank workbook with no pre-set weighting or prioritization of vendors, so companies do their own scoring and can also customize it according to their individual needs and preferences.
SET Maritime supporter Stena Bulk is already far along in its digitalization journey, and its sustainability and transformation manager Peter Björkborg says: “Digital solutions will play a vital role in the decarbonization of shipping as these can address inefficiencies in both fleets and individual ships. SET Maritime is a key enabler for companies to embark on this transition.”
Kim Evanger, who leads Maritime Partnerships at backer Kongsberg Digital, says: “We see SET Maritime as a liberating tool to make sense of a confusing software landscape for shipowners and facilitate informed decisions on applications to accelerate digitalization of shipping.”
SPREADING THE WORD Get SET Maritime now aims to spread the word to put the toolkit in the hands of technology buyers across the industry, as well as attract new supporters to the cause including classification societies, shipowners, managers and software vendors, according to Levy.
The toolkit is available for download from SET Maritime’s website.
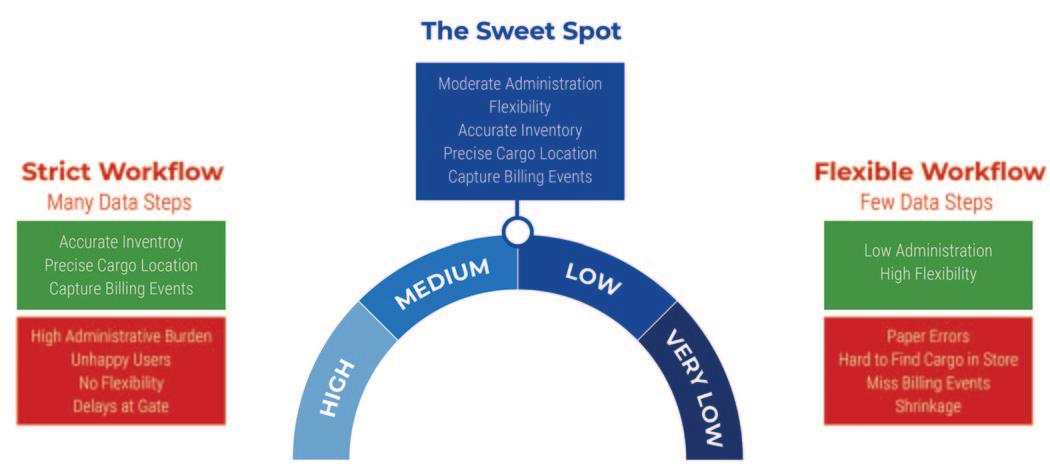
SUMMARY Various factors have led to breakbulk and general cargo terminals having disparate processes, focussed on turning around ships as quickly as possible then mopping up the data capture afterwards, writes David Trueman, Managing Director, TBA Group.
This creates several challenges such as confirming the manifest, recording predamaged cargo, and locating the cargo in the warehouse. However, implementing data capture in the field, which solves these problems, is a significant change management exercise, which can make or break a project. Therefore, a preparedness to customize to find the best balance for every application can be the best approach to guarantee success.
THE PROBLEM When selecting a TOS many terminals try to take a standardized approach, using software developed for other industries and work hard to make it fit to the operational parameters of a breakbulk or general cargo operation. This may work to some extent but rarely does the solution fully deliver the results that drove the initial purchase.
So, what is the real issue? Why does the standardized option fail to deliver in breakbulk and general cargo terminals?
Let’s look at a close relative of the break bulk and general cargo sector — container terminals.
When we consider container operations, we typically have several immovable objects, which force stakeholders down a standardized path to digitization. It is not uncommon to find the following: Standard dimensions of containers
v
v v
v standardize storage rules. Standard EDI messaging. Standard type and position of container numbers facilitates easy reading by OCR systems. The terminal can operate efficiently without needing to know the details of the container contents.
In comparison typical Break Bulk/GC terminals have the following traits: v No standard EDI, just bespoke point to point messaging (if you are lucky) or worse, just a spreadsheet OR even worse, a fax! Cargo manifests especially can be very large, variable in format and unavailable in any usable format. v Cargo comes in many shapes and sizes with multiple storage criteria for example, indoor/outdoor, hazardous/ non-hazardous, limited stack height, multi-tier and changeable ownership structures. v Cargo identification is variable, from colour marks to RFID tags and everything in between but never positioned to make the stevedores life easy. v Cargo may need to be consolidated, de-consolidated, conditioned, repacked, quarantined, FIFO, LIFO.
To further add to the challenge terminals are often in a very competitive environment (you only need a warehouse and a few forklifts to play the game) with short term contracts restricting the possibilities for investment.
A TYPICAL SYSTEM SOLUTION To manage this environment many terminals have implemented software to handle their inventory, often a Warehouse Management System, which addresses the core aspects of stock recording and gate management without ever introducing process improvements or optimization.
This is acceptable to many terminal operators because it also avoids the difficult issue of data capture at the quay during discharge. The upside of this approach is that it allows stevedores to unload cargo in the most expedient way possible, often leaving the checking against the manifest until the cargo is already in the warehouse. The downsides of this approach are numerous: v No real time performance data or progress reporting. v Having to find cargo in the warehouse after unloading. v Not validating the manifest until the vessel has sailed. v Not recording damages at the point of receipt. v Delay in customs clearance. v A large team of back office administrators performing data entry. v The sweet spot in data capture within a bulk terminal falls midway between a strict workflow and a flexible approach.
ESTABLISHING AN OPTIMAL TOS The first ‘must’ is to electronically import the cargo manifest (In a usable form) into the system. If you are not able to solve this problem, you simply can’t overcome the burden of manual data entry. The optimal
answer is EDI (remember there are no standard messages) with an Excel uploader being a less efficient compromise. To establish an effective EDI environment will require effort involving numerous parties. Ideally the TOS has a standard API connector which can be mapped to various customer systems using a tool such as Dell Boomi but customers still have to buy into the investment on their side and work to ensure the data is consistent.
The next must is to decide on an approach to data capture, which allows the terminal to optimize the whole operation, not just the quayside. We talk about finding the Data Capture ‘Sweet Spot’, where the effort required to capture is balanced with the business improvements facilitated by the data.
The sweet spot in data capture within a bulk terminal falls midway between a strict workflow and a flexible approach.
In all process areas the terminal needs to assess the balance between: v Using the TOS’ standard workflows at the cost of changes to working practices. v Adapting the TOS workflows to reach a compromise, which is easier for users to adopt.
Mobile applications are easier to customize than the core product and the cost/risk of customization here can be worthwhile to facilitate buy in.
If union labour is utilized, then data capture on the quayside using mobile devices may be hindered by the Luddite rules of the union. However, if it is possible to scan as the cargo comes off the hook, then grasping the nettle of introducing this process needs to be explained to the stevedoring gangs as the improvements in all areas behind the quayside more than compensate for the extra task.
It is also beneficial to scan cargo into location at the time of placing it rather than placing it first then going to find it later.
Ultimately, if the terminal wishes to minimize double handling, capture all billable events, reduce the back-office burden and establish continuous improvement strategies data capture must move into the operational areas. This will require changes in working practice and therefore Change Management needs to be a key function of an implementation project. Our experience teaches us that following activities will help to support the acceptance of change required for a successful implementation: v The establishment of explicit goals which act as a reference point for all stakeholders during the project. For example: “We are implementing a TOS because we want to know which cargo is left to unload from the ship in real time so that we can update our customers and more accurately predict vessel completion. This will improve our customer service and allow us to win more business.” v Take time at the conceptual stage to understand what needs to change and what must stay the same. Consider customization based on this assessment but be aware that going beyond an 80/20 standard to customized ratio will make the project more difficult. v establish effective integration with their systems. The benefits are mutual, but they will need a budget, so you need to sell the improvements to them. Ensure that you sweat your new TOS asset to deliver the best returns for the business. Understand the business case before you start and test for success.
CONCLUSION Too many terminals fail to maximize their software assets because they set out to find a product to support their ‘as is’ processes without understanding what is possible.
Of course, managing the inventory is important but this alone won’t deliver a strong return on investment.
TOS providers have a key role to play in demonstrating what can be achieved but making a step change in business improvement requires a collaborative approach, advocated by senior management but understood and supported at all levels of the business
ABOUT THE AUTHOR:
David Trueman, a managing director at TBA Group, has over 20 years of experience in delivering solutions to the bulk, breakbulk and general cargo sector. His understanding of the challenges faced within the sector led his organization to develop CommTrac, an awardwinning Terminal Operating System, which has been designed to empower clients to drive optimization strategies, increase operational performance and improve competitiveness.
Dedicated software for bulk terminals – TBA Group advances operational excellence at Saldanha Iron Ore Terminal
In March 2015, Transnet Port Terminals’ Saldanha Iron Ore Terminal (SIOT) in South Africa deployed a sophisticated software solution by TBA Group – CommTrac, to optimize its bulk operations and terminal management. This bulk and general cargo dedicated Terminal Operating System (TOS) is an integrated application linking the outside world and physical infrastructure and allows the SIOT’s operators to support and control all administrative and operational processes. Since the deployment of the CommTrac application, the system has been proven to be stable and reliable in the eight years that it has been running at Saldanha without any downtimes and has increased this bulk terminal’s performance levels significantly.
SIOT is the largest iron ore export facility in Africa and is situated 140km northwest of Cape Town. In 2012, as part of Transnet Port Terminals (TPT)’ Market Demand Strategy to drive economic growth in South Africa, SIOT embarked on a journey to use the latest technology to improve the operational performance of TPT’s terminals.
As South Africa’s only dedicated iron ore terminal, the bulk terminal can handle up to 60 million tonnes of iron ore and accounts for roughly 96% of all iron ore exports from South Africa. TBA’s CommTrac terminal management system was selected to replace their obsolete inhouse system with a state-of-the-art software application.
Fernando Goncalves, the IT manager at SIOT during this project, stated: “We tried to take our former (in-house developed) TOS to the next level by linking and/or integrating with other systems both on the financial and automation side. A business decision by Transnet, was to look at a new terminal operating system and go out to the market with an open tender. CommTrac was then selected to become the ‘new’ TOS for the Iron Ore Bulk Terminal of Saldanha.
“I was involved right from the start with implementation, development, customizat ion, processes, reporting, etc. to the end product that it is today. We did venture into some unknown territory but with the assistance of both Delton and Daubert and
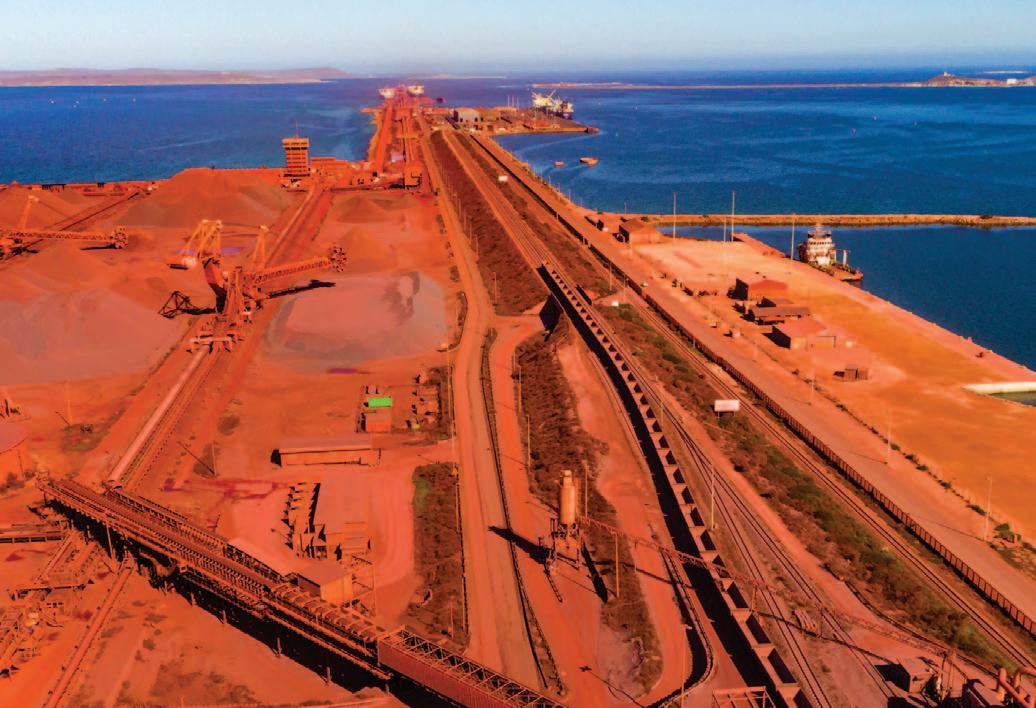
the development team from TBA, we got to where we are today and CommTrac has served us well.”
Alvin Gulzar, Acting TPT ICT Executive Manager stated: “In 2014, TPT had developed a viable General Cargo Operating System (GCOS) in-house which while efficient for breakbulk, automotive, container and skip-handled bulk operations — it was unable to cater for the bulk operation handled by SCADA systems integration. It was important for us to find a technology solution that was, adaptable, created visibility and increased the performance of our bulk terminals nationally. In an open tender to market, we were able to secure CommTrac because they offered a solution that best fit our operation. Their customization offered measurable value, along with dedicating a South African-based support person.”
By installing an integrated application that is linked to the outside world and physical infrastructure, this allows the SIOT’s terminal operators to support and control all administrative and operational processes. CommTrac forms a real-time and near real-time operating system in the layer between high level systems such as ERP and weighing and conveying equipment at a terminal. The software collates and processes information from other systems and automates manual processes where feasible, whilst improving the user experience in being able to perform their function more efficiently.
It provides real time accurate reporting, inventory tonnage position, real time overview of loading and discharge progress and real time overview of delays and variances among many other important functions and insights.
Goncalves said: “Information became available and reliable at a touch of a button, so there was enough data for decisionmaking and data analysis including real-time scale reading which are critical to our vessel loading operations.”
On the question asked what the major changes between the former system and CommTrac are, he mentioned: “Using CommTrac made an impact and one of the successes for Saldanha Iron Ore Terminal is, that users have access to information all the time. It’s accessed in such a way that users cannot change or modify data and therefore, the integrity of data is maintained. Users have the ability to view the data on screen at any given time, as PDF or to download to Excel, providing management information that does assist in operational decision making and improve efficiencies.”
He further added: “In the six to seven years (using CommTrac), I don’t think we’ve had any downtime from CommTrac. So yes, it’s been very reliable.”
Goncalves said: “We’ve gone beyond the off-the-shelf CommTrac that we’ve got. Our SAP link, SCADA tag reading, anticontamination rules, stockpile manage ment, permit system, vessel graphical representation in near-real time, automated scheduled reports, amongst others has contributed to its success.” …. “We did request a lot and TBA was accommodating to reach this point (of success). We intend to do more and look forward to the next version of CommTrac”
David Trueman, Managing Director TBA Doncaster, says: “TBA and TPT have worked well together over the years and that collaborative approach delivers real value to the users. We are proud of the levels of optimization afforded through the use of CommTrac and look forward to many more years working together with ever more powerful iterations of the product.”
ABOUT THE COMPANY TBA Group is a respected international consultancy and software company, that uses in-house simulation and emulation software, to provide integrated and sophisticated solutions to simplify the operations of ports, terminals, and warehouses.
CommTrac is the software for bulk terminal operations, which enables the terminal operator to plan, track and manage in real-time all agribulk, breakbulk, mineral, marine and general cargo, manned/automated assets, and people right across the terminal or terminal network. It provides the tools, control, and management information the operator needs to maximize the operations, profitability, compliance, and growth potential whilst reducing risks.