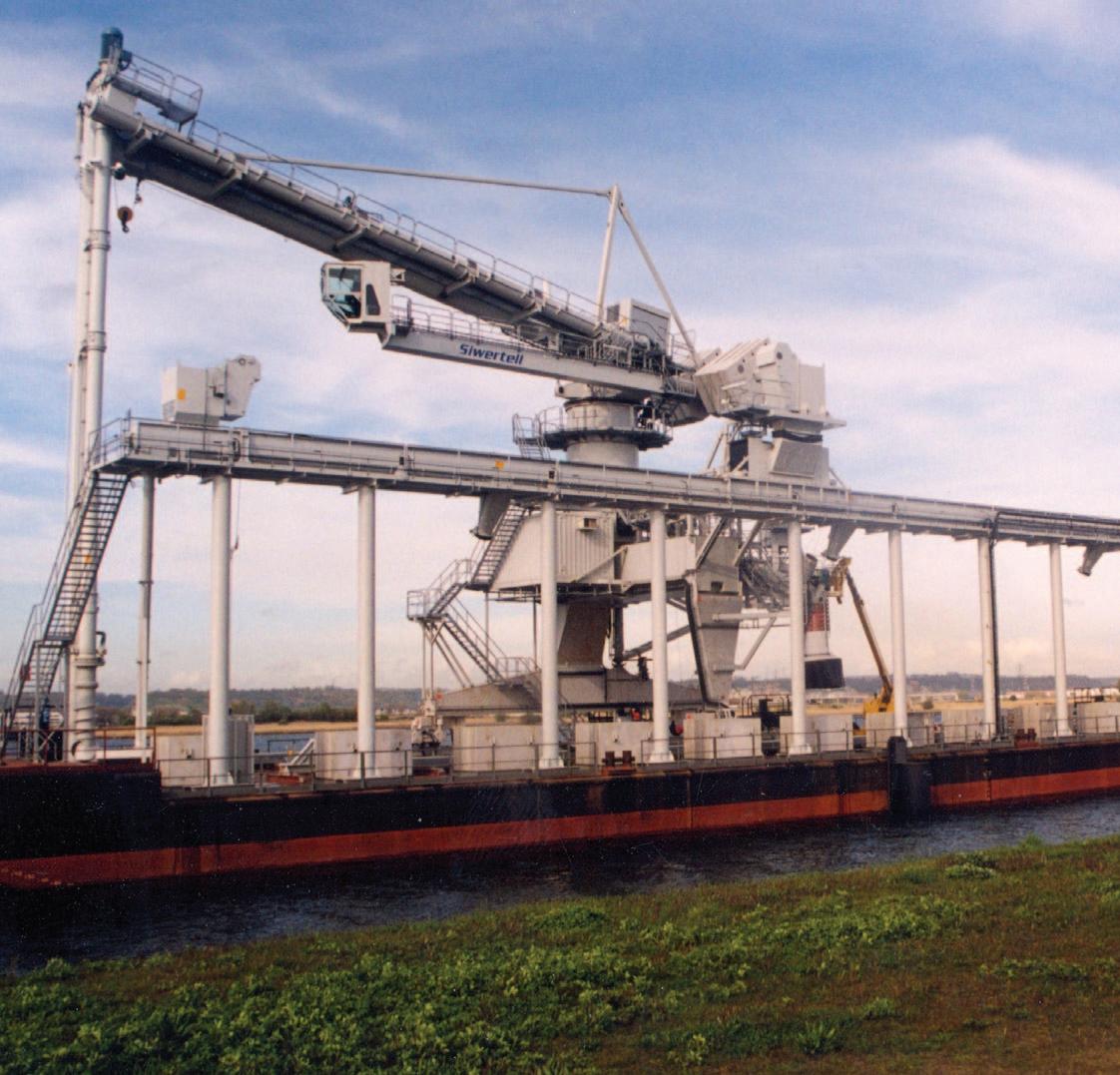
43 minute read
MINIMAL IMPACT: PROTECTING OUR WORLD WITH ENVIRONMENTAL BULK HANDLING
Protecting our world with Environmental Bulk Handling
Jay Venter
Screw conveyors: turning the tide on energy efficiency
ENVIRONMENTAL PROTECTION AND PROTECTION THROUGH-LIFE COSTS Today, hundreds of installations, from industrial facilities and port terminals, to ships, silos, and power plants, benefit from the unique capabilities of our screw conveyors. They offer some of the most outstanding dry bulk material handling attributes on the market. Here are a few highlights:
ENVIRONMENTAL PROTECTION Screw conveyors have very low energy consumption demands and are totally enclosed, protecting the environment by ensuring that dust emissions and spillage are eliminated when conveying all materials. They can handle virtually any dry bulk and are ideal for powdery, dusty cargoes, especially where scrupulously clean operations are essential.
OPERATIONAL FLEXIBILITY Screw conveyors can be supplied with multiple inlets and outlets, allowing for very flexible cargo distribution arrangements. They can be delivered as stand-alone units or as part of complete bulk material handling systems and are available in several diameter sizes to accommodate a wide range of applications, and capacities range from 30 to 1,700m³ per hour.
Screw conveyors operate with the helical flight moving the bulk material forward by rotational action. A vertical screw conveyor can elevate material up to 40m, combining multiple conveyors in a series allows material to be raised to any required height. The same principle holds for horizontal conveyors, which can also be inclined and are reversible.
LOW WEIGHT ADVANTAGES Bruks Siwertell screw conveyors are lightweight with a very small physical footprint. This makes them ideal for jetties with weight restrictions and when installing a conveying system within existing infrastructure. For example, vertical screw conveyors require much less space than a bucket elevator, making them ideal when space is limited.
THROUGH-LIFE COSTS The rigid and heavy-duty construction of our conveyors reduces wear and enables easy maintenance at infrequent intervals. Bruks Siwertell’s screw flights offer some of the industry’s longest service lives.
Longevity of material storage solution from Schenck Process proven in demanding circumstances
Storing and safely handling bulk materials such as grain in harbours — and in bulk handling stockyards — is a challenging prospect and an area where Schenck Process engineers and supplies a unique solution in the form of its MaxiStore® .
SOLVING STORAGE CHALLENGES IN DEMANDING ENVIRONMENT A customer, part of the dry bulk commodities industry, wanted a long-term bulk material storage solution within its limited available space at a harbour. The company contacted Schenck Process for a solution that led to the MaxiStore demonstrating its longevity and starting a relationship lasting over 15 years.
With restricted space within the port, the customer needed to maximize what was available. A traditional loading system uses a high-level conveyor with a tripper supported from the apex of the building roof. Potentially, it could have made for a costly build and resulted in inefficient material loading. Also, controlling the material positioning across the length of the store could have proved difficult for that system.
After establishing that the traditional system wouldn’t solve the customer’s challenges and a more innovative approach was required, the team at Schenck Process proposed the unique MaxiStore system. Based on the combined advantages of proven Redler, en-masse conveyor technology, and an industry-leading approach to the process of store loading, the MaxiStore system used a cranked en-masse chain conveyor within a steel structure to span the building laterally. The machine could move along the length of the store with material fed through the chain conveyor to drop to the floor. It allowed the material to easily be fed to any required storage bay while having the capacity to fill up to the ceiling and along the entire length of the building, optimizing storage volumes for any given space. MaxiStore manages the area safely by minimizing dust that can lead to explosions.

MAXISTORE: DURABLE AND FULLY ADAPTABLE SOLUTION TO CUSTOMER NEEDS Each MaxiStore system can be specifically designed to meet the customer’s exact needs, no matter how complex. By working with the customer to understand the particular requirements, Schenck Process developed a robust system that optimized the storage volume for the limited store size and maximized profit. The result empowered them to work within their conditions and have a storage system that could operate continuously.
The MaxiStore system is made to handle large quantities of animal feed, minerals, and other bulk materials at rates up to 1,000 tonnes per hour. It enables the user to maximize its space while providing better and safer material distribution.
The MaxiStore was proven to provide the most efficient and flexible filling of dry bulk solid materials throughout a storage building.
Schenck Process offers installation and after-sales support — across the entire lifecycle of its process solutions — assuring the customer of the longevity of the systems it designs, manufactures and engineers. With over 100 years of experience in mechanical conveying and storage solutions, the customer benefited from access to a wealth of Schenck Process’s expertise. Maintaining the infrastructure within the harsh marine environment of the port has been crucial to extending the service life of its acquisition, giving it confidence that it had purchased a best-in-industry storage solution.
Having a long-term satisfied customer is a testament to the performance of Schenck Process’s solutions and demonstrates their commitment to developing innovative and efficient automated bulk storage solutions. The system installed 15 years ago is still working 24 hours a day and remains a fundamental part of the customer’s port operation.
SCHENCK PROCESS: Schenck Process is a major global provider of sustainable products, integrated solutions and services in mission critical applications for bulk materials. Headquar tered in Darmstadt, Germany, the group has more than 3,000 employees with a presence in over 20 countries across six continents focused on the food, mining, chemicals and performance materials, and infrastructure and energy market segments.
The product offering includes solution for industrial weighing, feeding, conveying, pulverizing and classification, screening, mixing and blending and associated digital applications.
The group was acquired by Blackstone International in 2017 and generated revenues of nearly €600m for the year ended 31 December 2020.

Iron ore production is expected to rise steadily to reach 2.7Bt by 2025, according to GlobalData’s estimates. In this huge industry energy savings are key to keep production costs within limits and to minimize the ecological footprint of the products. The dust control agent C-Force Industry IPC, developed by Instral B.V. the Netherlands, not only reduces dust, it also gives the pellets and sinter a moisture-repellent layer, which shields the materials from taking up moisture during rainfall. Less ballast water in the pellets means major savings further in the process, both in transport and when the water needs to be removed during the melting process.
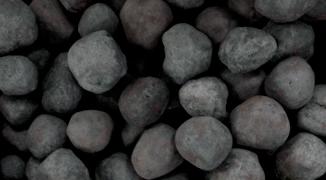
ABSORBING WATER When mined, stored, shipped or otherwise handled, iron ores can get wet from rainfall or moist environments. Since the pellets and sinter are poriferous, they tend to absorb water, leading to several issues such as liquification, leaching and lumping because of frosting. Apart from these problems, excess water in the pellets can also lead to unnecessarily high energy bills, both during transport and in the melting process.
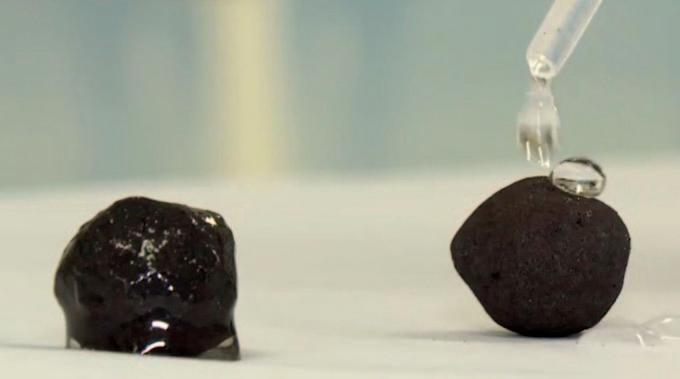
GORETEX QUALITIES The C-Force coating acts as Goretex in our raincoats; it keeps the water from coming in but is breathable at the same time, allowing moist to evaporate from the pellets. Instral B.V. conducted tests with pellets to determine water uptake with or without the C-Force coating. The coating proved to reduces the amount of moisture in bulk pellets significantly.

ENERGY SAVINGS Since the pellets will take up less water during storage and shipment, ballast mass (water) does not have to be shipped to customers, thus providing for a return on investment for the producer of US$0.45/metric tonne on average. The savings for the end-user will be substantial when moisture repellent pellets are being used, as the removal of water costs a lot of energy. Based on the average industrial consumer energy prices of 0.153 $/kWh the savings could amount to US$1.56/metric tonne. On top of that, the end-user will also save on CO2-taxes due to energy savings.
PRACTICAL USE OF C-FORCE Water is used as a carrier to distribute the C-Force® Industry IPC on the surface of the pellets. The coating can easily be applied to huge amounts on pellet stacks using a waterspray cannon or by using spray nozzles (from two sides) when pellets are transported by belts. The latter is most effective, covering all pellets on all sides. C-Force Industry IPC can be applied on cold as well as hot pellets/sinter (–25 to 290ºC) and stays on the pellets all the way into the oven. The C-Force Industry products are non-hazardous and burn ash-less. INSTRAL C-FORCE® INDUSTRY IPC

PROGRAM
BENEFITS
v v v v v v Effective dust control Long-term performance Weatherproof Moisture repellent Easy to apply Environmentally friendly
COST REDUCTION
v v v v v Saving on water use Saving on energy Saving on shipping costs Less production loss Lower cleanup costs

QUARRY MINING LLC (QM) designs, manufactures and installs crushing & screening plants in compliance with European standards, while adhering to the same safety standards and features that you would expect of equipment produced in Europe.
QM is certified for quality management by ISO Certificate 9001:2008 and for environmental management by ISO Certificate 14001:2004 from the German Technical Inspection Association TÜV Rhineland/Germany, and includes the continuous integration of all upgrades. QM is founded and managed by German Nationals but located in the United Arab Emirates. QM can supply high-quality plants at very competitive prices.
Conveyors have been used for material transport in a wide range of applications in mines and quarries. The key factors behind QM’s track record of safe and efficient operation of such conveyor systems is sustainable maintenance and use of high quality parts specifically the rollers, drums and belt; but also the drive and control systems. As operational companies need to ensure maintenance and energy costs are kept as low as possible whilst keeping plant downtime to a minimum, there is always a balancing act which directly impacts the final price per tonne. QM has developed an innovative solution to absorb and reuse excess electrical energy from material transported on downhill conveyor systems, therefore reducing the overall energy cost to zero in addition to generating additional electrical power. This energy saving from QM’s uniquely designed and custom-tailored conveying system enables total transportation costs per tonne to be reduced dramatically.
INTELLIGENT CONVEYING SOLUTIONS “In 2015 we realized a pioneering project of a 3,5km long conveying system,” says Christian Drewes, Deputy General Manager and Technical Manager, Quarry Mining, “with a total capacity of 2 x 4,000tph [tonnes per hour] in one of the largest limestone quarries in the world. It was the first downhill conveying system in the region and with that system our client can reduce the transportation costs per tonne to a minimum and saves a lot of energy. Now, seven years later we are building the third system and it’s going to be commissioned by mid of 2022.”
One of the most important tasks was the partial downhill route of the conveying system. In order to prevent the system from overspeed caused by natural gravitation force, the potential energy has to be ‘pulled out’ of the system. Thus, a control system with an electronic braking system was developed by QM. With that system, it is possible to brake the downhill conveyor electrically and wear-free. In addition, the potential energy of the material is converted into electrical energy, which is then fed back to the grid and can be used for other plants. With this innovative solution, a negative energy balance of the conveying system can be realized.
“This means not only that the material transported is completely energy free, but also that electrical energy can be generated from the transportation.” explains Drewes. In case of power failure,

a special braking system ensures the safe-stop of the entire operation; highest safety standards are employed at all times. Frequency converters are used as a driving unit to ensure smooth start and stop of the >700m-long conveyors.
To generate the electrical power and to keep the belt speed as consistent as possible, a highly complex PLC system is required to control the conveyor at any given time with only a maximum speed difference of 1% for any and all load conditions. Only if these requirements are met will a safe operation of the entire plant be ensured.
As can be seen with the full load in figure 4 (on the right), the energy demand is negative and energy is generated in addition to the material transported. The feedback capacity depends on the height difference between head and tail drum. The larger the height difference, the bigger the energy generation. Power generation increases with the more material that is on the belt because more material will create a higher potential energy and will ‘drive’ the belt more. It is therefore a win-win solution; the higher the quantity of material, the larger the energy savings. Such a system can be realized whenever material needs to be transported downhill. This solution, engineered, designed, manufactured, installed and commissioned by Quarry Mining LLC is a unique, innovative and future-oriented solution provided to the client. It is sustainable, extremely environmentally friendly and reduces the energy costs dramatically.
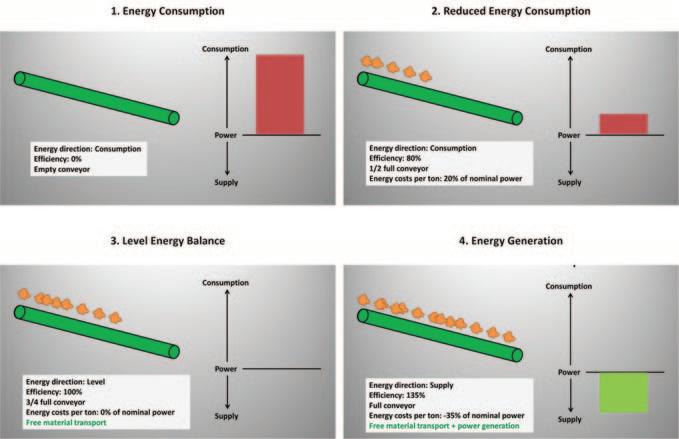
The figures above show the varying load conditions of the conveyor system and the corresponding energy demand.
Chile, the world’s largest copper exporter – a country case study
Chile takes the environment seriously. That’s according to Managing Director for ISG, Garry Pinder.
Chile is the mining logistic , storage and ship loading bench mark for countries who have the environment in mind.
Chile has passed many laws over the years to protect the environment. One law states: “Commodities being moved from the mine site to the port must be in sealed units so there is no product loss or dust problems.”
The ISG system fits that criterion. ISG has successfully implemented its logistic, storage and shiploading system in 70% of the ports in Chile which load copper concentrate. Most of these ports are container ports giving them another string to their bow by now becoming a bimodal port with very little capital expenditure (buying a tippler is the only additional equipment required for a container port).
A new era of bulk loading
Look at the top two items that the green movement protests about with mining logistics: 1) dust control 2) water pollution
Look at the two items mining executives try to minimize: 1) product loss 2) Clean up costs
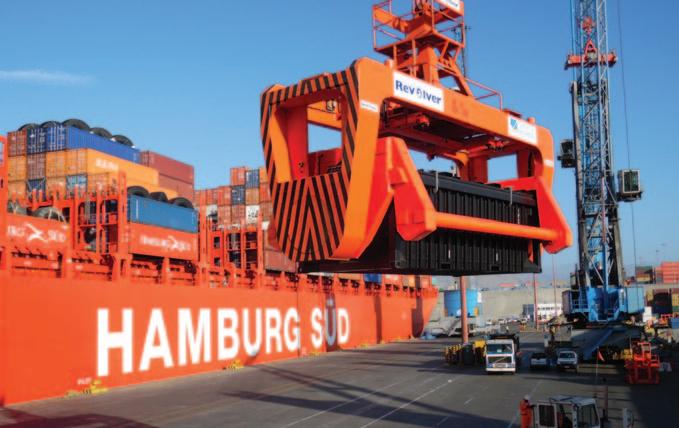
HOW DO YOU PLEASE BOTH PARTIES:
LOGISTICS ISG supplies containers to the miners who load them with their concentrates and move them by either rail or road to the port. The containers all have sealed lids so there is no product loss or unwanted dust, making them an environmental logistical solution.
PORT STORAGE At the port the containers are blockstacked instead of being unloaded into labour-intensive and dust-emitting storage sheds. This makes the system an environmental storage solution and turns container ports into bulk ports.
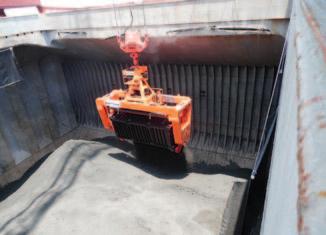
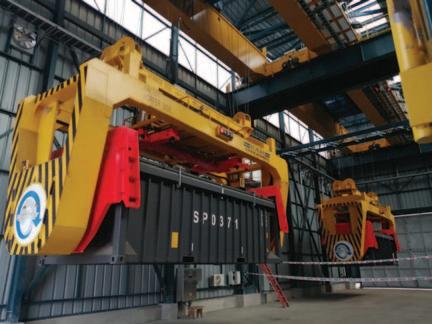
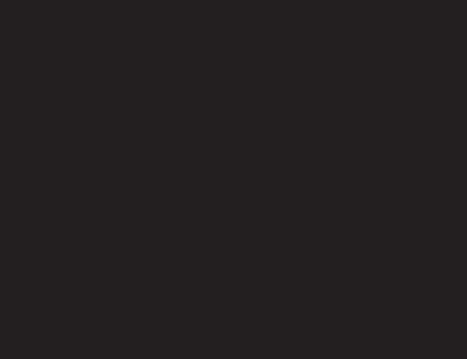
BHP Spence mine loading in the Port of Meijonnes.
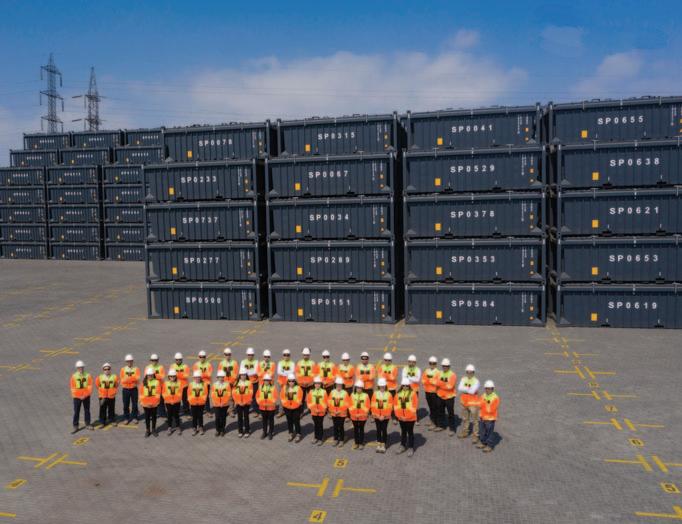
SHIPLOADING When the ship arrives, the containers are taken around to the quay side and with the use of the ISG tippler the containers are lifted into the ships hold and the lid is taken off using the patented ISG lid lifter and the containers are turned 360°, so the product is unloaded.
Depending on the product a misting system is used making the ship loading process an environmental ship loading process.
STANDARDIZATION With 70% of the ports using the same system and same container designs every miner has the option to use various ports to export from in the event of a port closure for various reasons or road or rail blockage.
GLOBAL AWARENESS Other countries are now starting to benchmark Chile with mining ministers talking to mining ministers and many mining companies visiting Chile ports to see the results.
The Port of Mejillones, who load the BHP Spence mine’s copper, lined up to display the ISG containers loaded with copper and awaiting the ship to arrive .
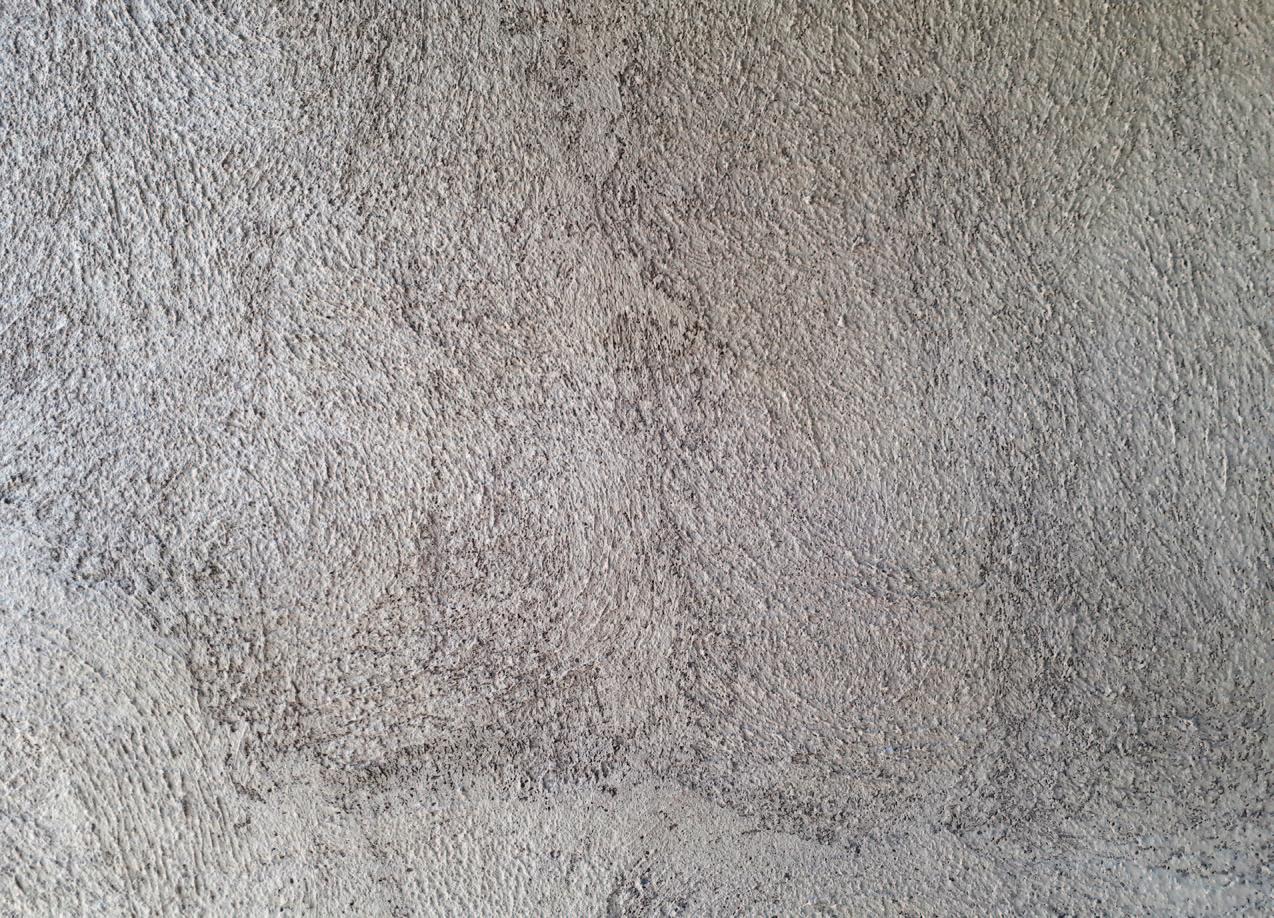
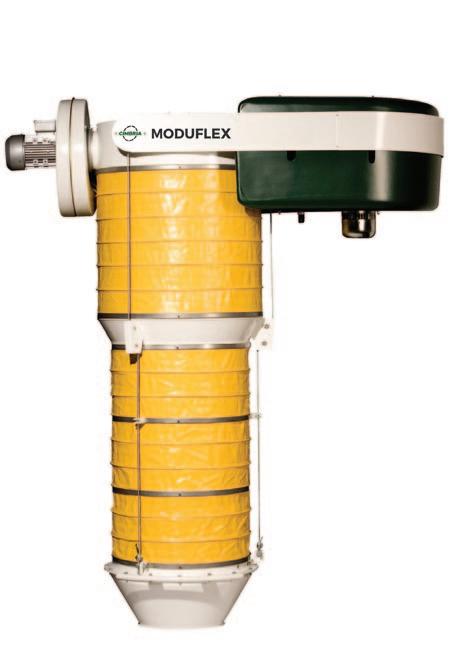
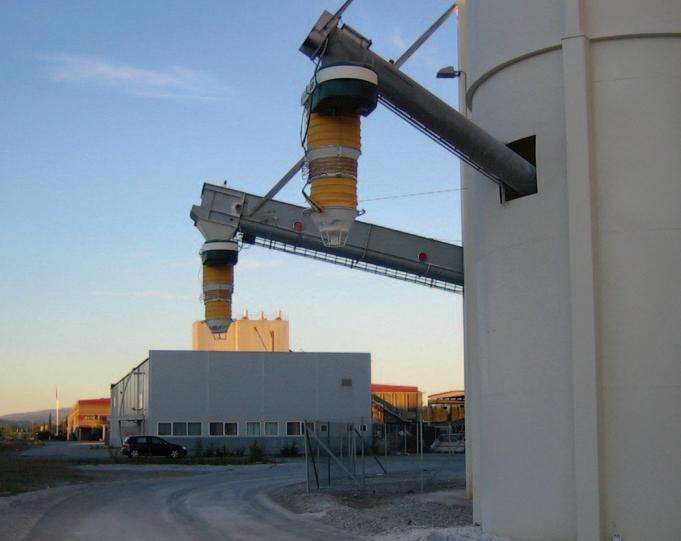
For 75 years, Cimbria — provider of hightech technologies and services applied to conveying of various products — has been serving companies all over the world with specific solutions for bulk handling. The range of products offered to the cement business is named Moduflex and it is made in different lines of loading chutes, especially designed and built to ensure a perfect job in the field of limestone, fly ash, clinker, minerals, where extreme heavyduty resistance and volume handling are mandatory.
With more than 17,000 systems sold to various industries worldwide, including the very high demanding sector of port terminals, Cimbria can profit of the experience and the firm foundation of knowledge which is of constant benefit to customers around the world who invest in bulk loading equipment.
LOADING CHUTES MODUFLEX, STURDY PRODUCTS MADE TO LAST Cleanliness, precision, safety: an authentic mantra when it comes to Moduflex, the Cimbria range of telescopic loading chutes, designed for loading dry bulk materials without any dust escape. The range has been developed to satisfy various business needs, from cement products, to industrial commodities and raw materials or chemicals and can be used permanently or for special needs. The layout of loading chutes can be adapted to tank trucks, open trucks, dumper trucks, rail cars and open/closed containers. The range also features specific solutions for ships, compliant with the port loading needs, and for loading in warehouse and stockpiling, inspired to durability and high capacity.
Indeed, the resistance is the primary feature of the range, made to ensure heavy-duty jobs and the endurance notwithstanding the extremely highvolume loading. The flexible outer chute is made by PVC-clad polyamide and it is suitable for loading not exceeding 70°C. The chloroprene rubber-clad polyamide, with increased wearing qualities and protection against UV light, gives shape to solutions intended to treat products with a temperature arriving up to 130°C. Inlets are provided in mild steel, stainless steel, wear-resistant steel or ceramic inserts for highly abrasive products. Heavy-duty metals are also used for the other components and especially for the outlet skirts and the supporting rings. The internal cones can be specified in nylon, mild steel, stainless steel or resistant steel depending on the usage they are addressed to. Materials, as well as design features, have been studied to solve specific issues related to operations involving different bulk products and means of transport. So the flexibility, together with the maximum sturdiness of the whole project are the real plus of this range built to fit and resist to the hardness of the heaviest works.
LOADING CHUTES MODUFLEX, MODULAR SOLUTIONS FOR EFFICIENT RESULTS The Moduflex range offers many different options specifically developed for the various bulk material applications. A specific range of accessories enhances the great versatility of these slides, which become truly ‘made to measure’ and can be adapted to suit 99% of all known applications within the dry bulk industry, thanks to the various combinations of standard components.
The very best advantage of Moduflex is its modular structure, which ensures the client receives the solution matching his specific purpose. For regular maintenance and in the event of accidental damage, it is only necessary to replace the affected section rather than the entire chute assembly. Besides obvious savings in direct costs, there is another important cost benefit in terms of reduced plant downtime. Furthermore, the base of standard components ensures operators that the Moduflex chutes are always built of well-founded, well-tested technology and entails quick access to standard spare parts, if a breakdown occurs.
The Moduflex loading chutes can cater for capacities up 4,000m3 per hour in the
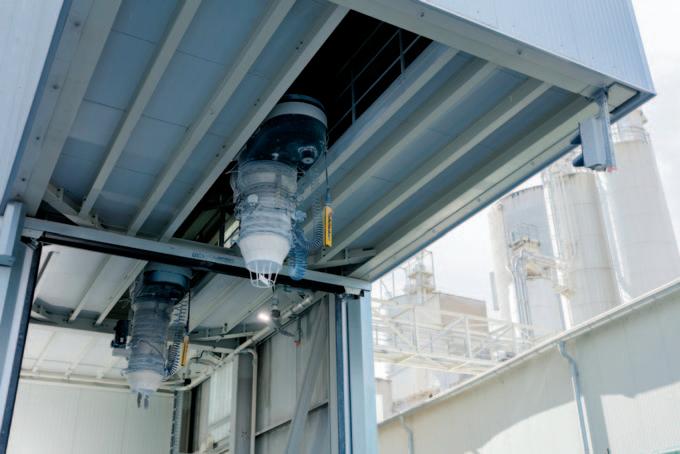
To prevent all risks related to dust, Moduflex is equipped with specific features to avoid dust all through the process.
standard configuration, and a drop of more than 30 metres. This high level of flexibility can only be achieved using a loading chute, and is not possible with alternative loading methods. Systems are produced in sections in two standard modular lengths, 300mm (12 in) and 600mm (24 in) and a range of diameters determined by throughout capacity.
LOADING CHUTES MODUFLEX, DUST-FREE OPERATIONS IN CLOSED SYSTEMS The Cimbria Moduflex range is specifically designed to allow the dust-free loading of bulk products. Every part of the system has been optimized so dust cannot escape from the loading solution in closed environments. This is critical in businesses with an intrinsic risk of creating waste and dust, especially for the impact that dust can have on the quality of the loaded material, as well as on the quality of the surrounding environment and working conditions.
To prevent all risks related to dust, Moduflex is equipped with specific features to avoid dust all through the process. A range of filtration modules is offered with the inlets as an integral part of the chute, which together with a reverse jet air system produces the necessary negative pressure to return all filtered dust into the delivery stream, while the particular design of the cones ensures effective separation of the material stream from the dust-laden upward airflow.
Moduflex is widely used for the loading of tanker trucks and closed railway wagons, a challenging supply due to the number of trucks’ and wagons’ doors. Cimbria Moduflex loaders are designed to cover the hatches with an outlet cone ensuring a dust-free loading. The ‘secret’ lies in the design of outlets that seal the opening and contains the dust inside the container, guaranteeing a safe and clean process for operators. In addition, the loading chutes are equipped with an outlet coupling fitted with three adjustment wire bushes, which are mounted to allow quick adjustments of the outlet, making sure it is in a straight horizontal position.
For port terminals, Moduflex offers applications for the tanker ship loading, which requires a transport arm with the ability to pivot up and down together with the loading, so that the chute remains in a vertical position. The different sizes of ships and the movements caused by the tide, force the precision with the height adjustment, in order to allow the correct flow of the product, minimizing the wear factor on the entrance and on the guide cones of the slide. Furthermore, loading tanker requires a wave compensator at the outlet, to even out the small movements caused by the waves, to have a constant seal between chute outlet and the tanker hatch during loading.

LOADING CHUTES MODUFLEX, SERVICE AND SUPPORT Cimbria is always at the forefront when it comes to optimizing and upgrading bulk loading stations. Smart solutions, often custom-made at first, are regularly added to the standard program after proven success. Thus, customers of Cimbria can always be certain to have purchased a thoroughly tested and documented products.
The vast programme of products is completed with a great emphasis on the consultancy approach ensuring targeted advice, enabling customers to select the very best solution to match both the specific technical and financial conditions. In addition, the after sales reaction to any issues is very quick and efficient thanks to the always-in-stock spare parts.
ABOUT CIMBRIA Cimbria is a global brand of AGCO and is globally respected in the fields of industrial processing, handling and storage of grain and seed, as well as animal feed, foodstuffs and other bulk products. Cimbria works together with its customers to design, engineer manufacture, install and service individual machines, customized systems and complete turnkey installations.
The Cimbria Moduflex range is specifically designed to allow the dust-free loading of bulk products.
ABOUT AGCO:
AGCO is a global expert in the design, manufacture and distribution of agricultural machinery and precision ag technology. AGCO delivers customer value through its differentiated brand portfolio including core brands like Challenger® , Fendt®, GSI®, Massey Ferguson® and Valtra® .
Powered by Fuse® smart farming solutions, AGCO’s full line of equipment and services help farmers sustainably feed our world. Founded in 1990 and headquartered in Duluth, Georgia, USA, AGCO had net sales of $11.1 billion in 2021.
ENGINEERING & EQUIPMENT Sustainability: Bedeschi’s daily mission for the future
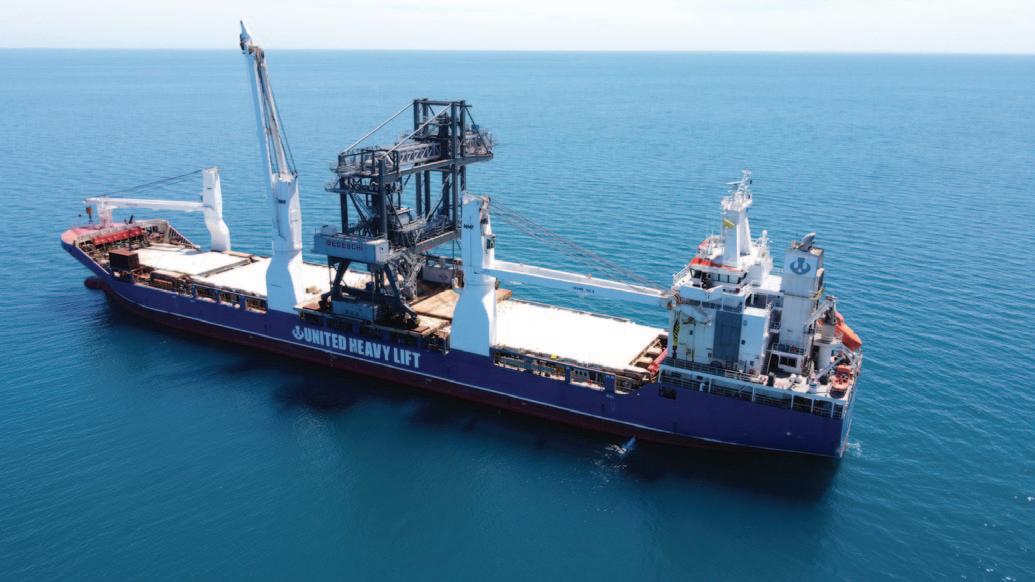
Shiploader for Cargill Australia delivered fully erected.
For Bedeschi sustainability means more than green. In the last hundred years, the company’s major target has been creating value for customers and stakeholders carefully selecting its value chain partners to fit with its vision of sustainable and modern manufacturing.
Bedeschi operates in three main areas: innovative engineering, pollution control and power consumption.
INNOVATIVE ENGINEERING Bedeschi’s business has been increasingly compelled to meet stringent standards reducing emissions and pollution. This is not only true for what is directly generated by operations, but also involves becoming a greener system as a whole. Besides the constraints imposed by the law, the desire to impact as little a possible on earth’s environment can only be translated into facts considering efficiency, seamlessness, dust limitation and sustainability as a single, integrated target rather than unrelated and independent issues. The ability to apply known solutions with a ‘think out of the box’ attitude is the key to achieving the goal. Sustainability is about so much more than controlling dust emissions. Welldesigned and innovative solutions can reduce the overall environmental impact
Renova pipe conveyor for grain.
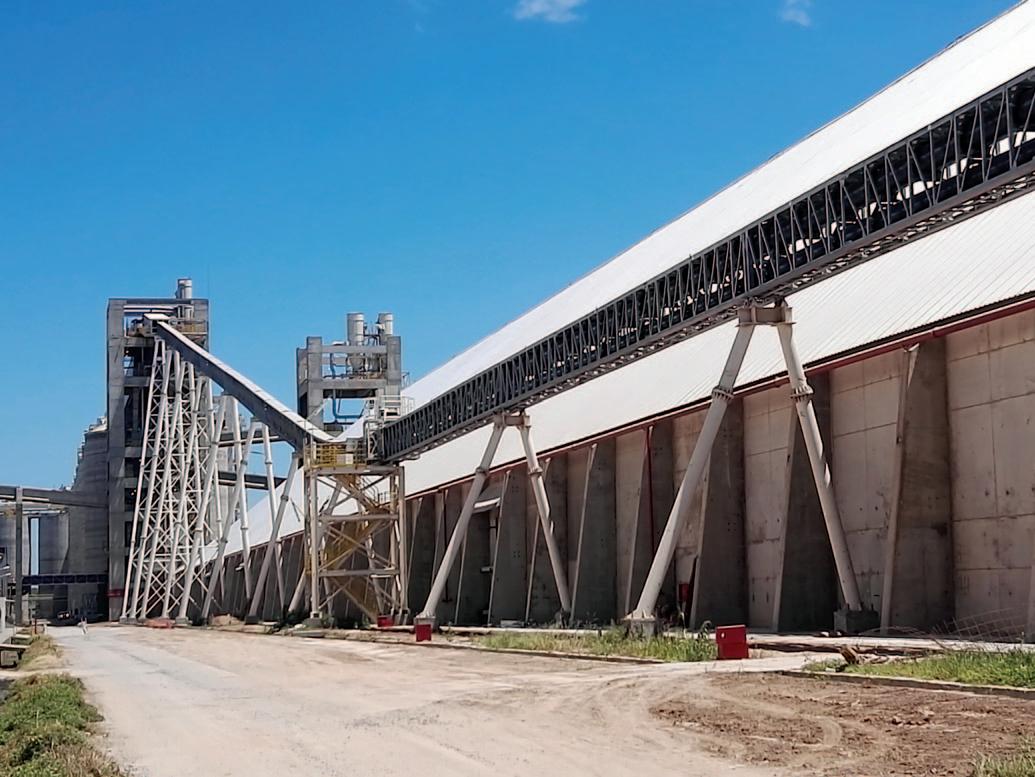
with a more effective port operation and logistics. In Australia, for Cargill, Bedeschi reduced by up to 50% the average mooring time of the vessels, with all the related benefits in term of fuel consumption, noise and gas emissions. With a nominal conveyor capacity of 1,000tph (tonnes per hour), this guarantees an overall efficiency improvement of more than 80% on the entire shiploading operation.
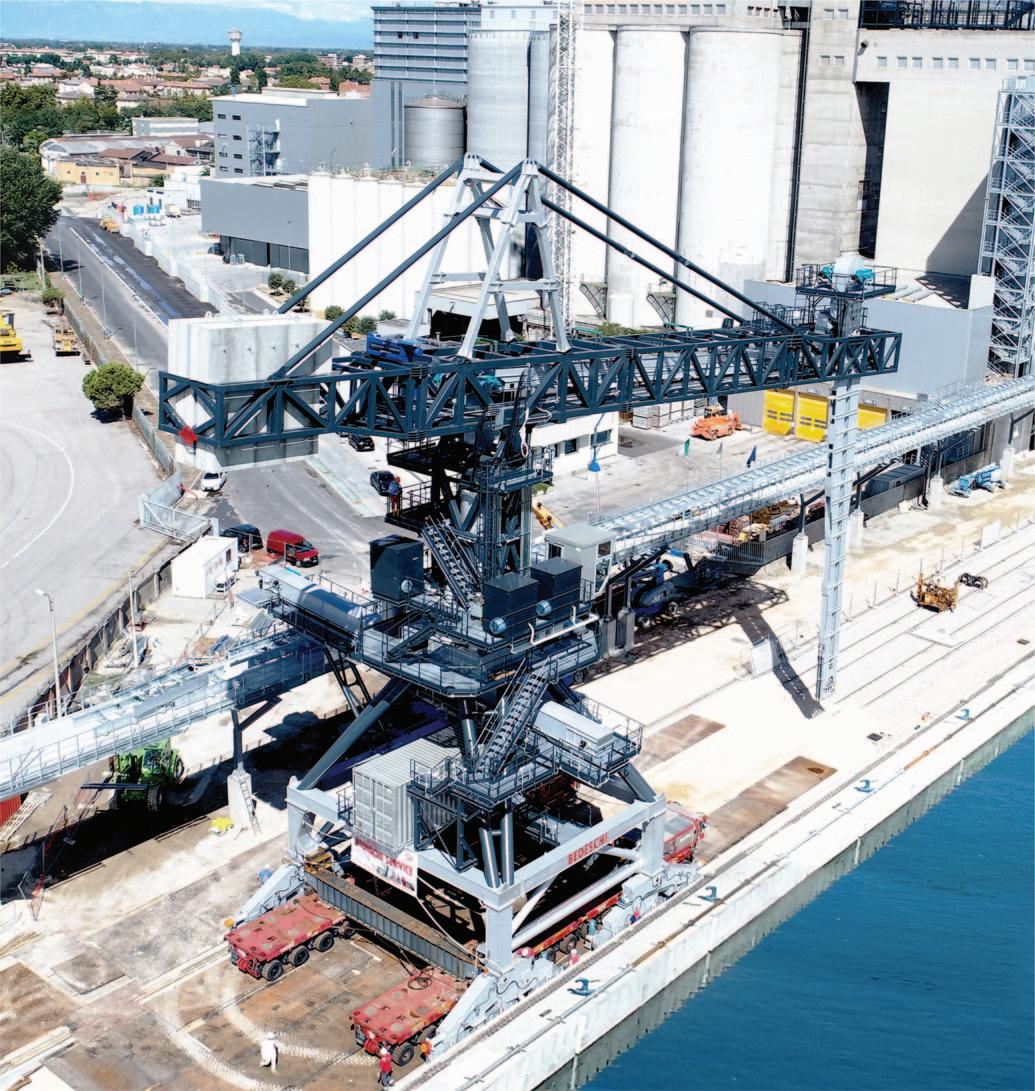
DUST CONTROL The use of completely closed or pipe belt conveyors helps to avoid emissions and spillage of material. Moreover, the PC technology reduces the necessity for dust suppression systems, which in turn means saving the energy usually required to operate dust control units. Also, this system gets rid of all the drops between conveyors that waste energy and are totally useless for the process. Without transfer towers, it saves a lot of steel, foundation works, and erection activities, thus reducing the carbon foot print of the plant and the environmental impact.
Environmentally friendly pipe conveyors are also very useful in the grain sector; one example is the Renova project. This is the first-ever pipe conveyor to be used in Argentina. The system, which was developed as a turnkey mechanical project, was completely engineered and supervised by Bedeschi America. It is one of the largest in Latin America thanks to its capacity of 1,500tph and the length of about 900 metres.
The use of enclosed belt conveyors and/or chain conveyors in ship-unloading or shiploading systems, ensures that the material is handled in a completely sealed volume, all along the conveying path from or towards the ship’s holds. The need for dedusting equipment is reduced to its minimum — and sometimes even eliminated.
The use of eco hoppers and controlled flow chutes are some of the technologies used by Bedeschi to guarantee dust control: these technologies consist of the application of systems to monitor dust production as controlled flow spouts, air cleaning filters and dry fog that use micro drops of nebulized water to keep the surrounding environment clean. Special applications as eco hoppers, combine the design, dust suppression, suction system
Grain ship-unloader with chain elevator and enclosed conveyors on board.
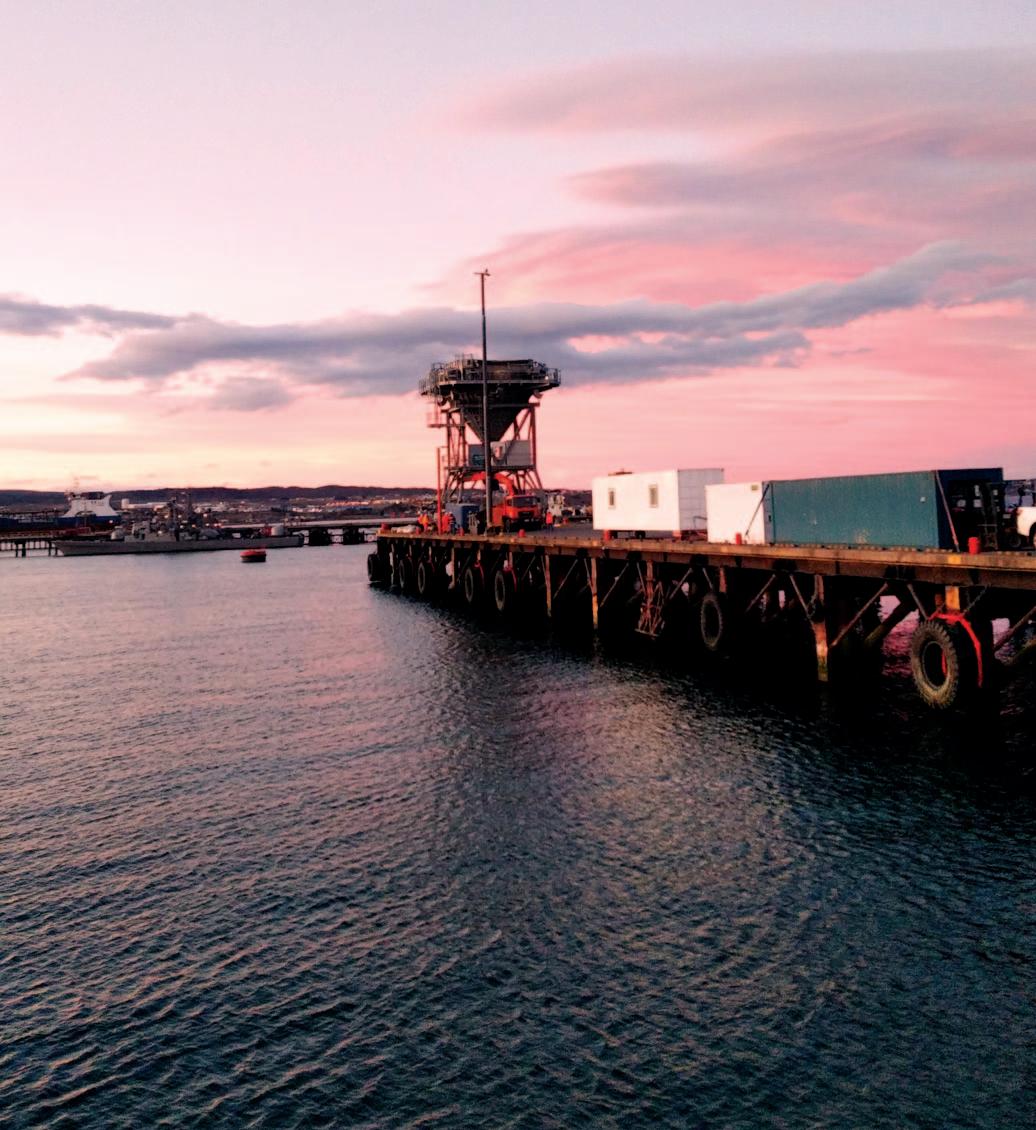
Melon Eco-Hopper.
and CF chute to facilitate dusty material handling through grabs. The use of ecofriendly or even food-grade oil and grease, and system for energy recovery is of great importance.
Bedeschi supplied several dedusting hoppers. To increase efficiency, these can be supplied fully erected and pre-tested. In the case of Melon S.A., Bedeschi supplied a new Eco-Hopper to be operated on the austral port of Punta Arenas, Chile.
The Eco-Hopper is designed for direct unloading of clinker to trucks at a rate of 600tph and is designed to work with 12m3 grabs. The machine is equipped with pulsejet bag filters with high filtration capacity and performance and with low compressed air consumption: an economical and flexible solution to satisfy the stringent environmental standards required.
The Eco-Hopper is designed with a special support structure that allows a solid anchoring of the hopper to the pier structures during unloading operations, but at the same time it allows the machine to be moved by means of SPMTs (selfpropelled modular transporters) when not in use.
This configuration is made necessary by the multi-purpose nature of the Punta Arenas port and due to structural limitations of the existing pier. These operational constraints forced Bedeschi’s engineers to find a winning solution in terms of flexibility of use, weight limitation and structural strength.
POWER CONSUMPTION Last but not least, to offer its customers efficient and innovative solutions for optimizing energy consumption, Bedeschi has developed advanced technologies to meet strict capacity and quality standards, at the same time compatible with Industry 4.0. Multiphysics and DEM Analysis helps to push the design of the machines with positive impact on energy consumption for operation.
Finally, Bedeschi’s R&D department is constantly working to improve the capability of its systems to minimize the environmental impact. This includes dedicated studies on the noise reduction, both by design and by passive insulation, and on light pollution, by means of lighting simulations. These are performed to reduce the overall installed lighting power while, at the same time, having a properly illuminated working area, without disturbing the surroundings.
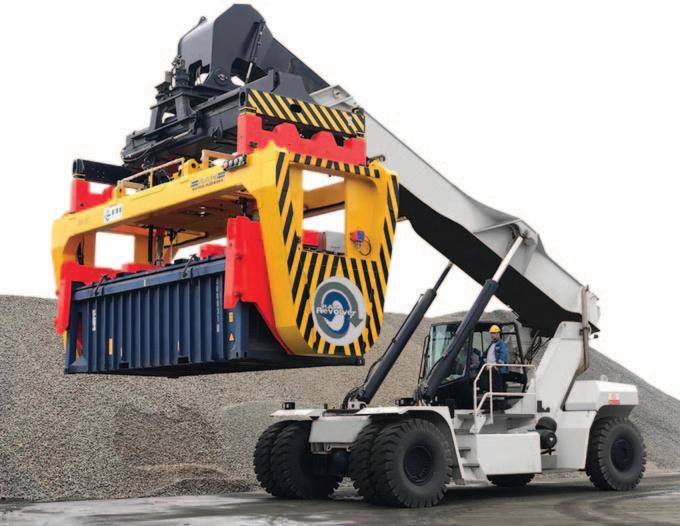
RAM’S REVOLVER ON REACH STACKER REPLACES TABLETOP BULK LOADER AT ETI BAKIR Turkey’s largest mining and metallurgy operations company, Eti Bakir, is turning the tables on its bulk handling with a further order of the Revolver on reachstacker.
Before introducing containerized bulk handling, Eti Bakir used a rotating tabletop frame system to handle pyrite concentrate at their Mazidagi plant in Mardin, Turkey. Consisting of a rotating frame, the tabletop system with open-top containers mounted above a hopper is fed by a reachstacker onto a conveyor belt.
The tabletop system was temporary and proved slow and cumbersome. Following an increase in demand, Eti Bakir had to consider another bulk handling method, as its existing system could not sustain the high-volume levels required.
The team at Eti Bakir looked for a reliable, quick to set up and cost-effective solution, capable of being integrated into their existing handling process, with minimal impact environmentally and with zero loss of commodity when handled.
They had to look no further than Revolver Containerized Bulk Handling (CBH) that is being used for a variety of bulk handling projects around the globe, and is celebrating ten years of success.
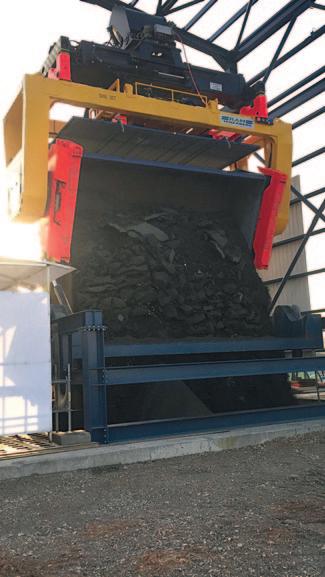
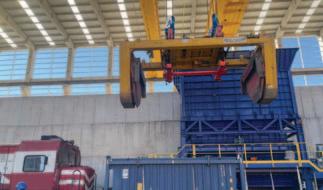
TURNING UP THE VOLUME WITH CBH The benefits of introducing CBH: Eti Bakir is able to utilize their existing hopper/conveyor system with a rotating spreader at its Mazidagi plant, where it handles pyrite. Eti Bakir also uses the same system at its Samsun plant, using two RAM Revolver’s to handle copper concentrate.
LIFE IN THE FAST LANE With cycle times in less than three minutes, compared with 15–20 minutes from the tabletop system, Revolver CBH allows Eti Bakir to increase its product flow to meet demand.
BRIDGING THE GAP As CBH is flexible in its application, Eti Bakir are using the RAM Revolver rotating spreader also on an overhead crane.
This allows CBH to be used at different locations, without the need for expensive infrastructure or storage sheds being built in anticipation of an increase in demand at certain times of the year.
SHIFT FROM PORT TO INLAND BULK After delivering many Revolvers to load bulk to ships direct from boxes, many of RAM’s customers saw the benefit of moving bulk inland with CBH.
CBH is fast and simple, compared to bags or dump trucks. It has virtually zero waste and can flexibly handle any commodity in containers.
ON THE DOUBLE After experiencing the benefit of CBH, Eti Bakir is now considering a spare Revolver for its Mazidagi & Samsun facilities.
“Our revolver customer base has expanded from ship loading to now 50% of orders being inland bulk logistics.” says Cameron Hay, RAM Spreaders.
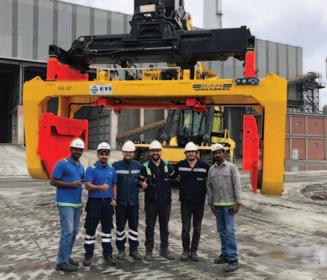
Pictured: RAM & Eti Bakir during commissioning & training at the Eti Bakir Samsun copper facility. ENGINEERING & EQUIPMENT
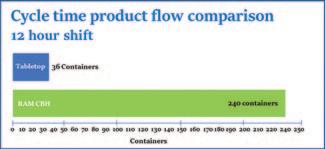
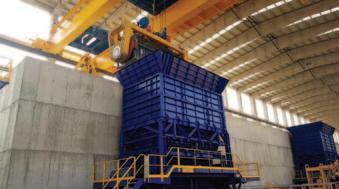


Dust accumulation on rolling components can cause abrasive damage and premature failure. External wear liner and dual self-adjusting seal with belt support. © 2022 Martin Engineering Company
When tonnes of bulk material hit a moving conveyor belt, three things happen: fines scatter in random directions, cargo shifts and dust becomes airborne, writes Daniel Marshall, Product Engineer at Martin Engineering.
The impact creates turbulent air pressure inside the transfer chute that escapes from any available gap, carrying dust and fines with it. A properly designed enclosure will manage bulk solids, allow cargo to settle in the center of the belt and contain most of the dust inside a settling zone enclosure. Well-designed conveyor loading zones also keep walkways clear from spillage and control dust emissions, allowing hazard-free inspections and maintenance.
THE COST OF SPILLAGE If left uncontained, fugitive material in the form of dust and fine particle spillage will increase labor costs for cleanup, foul equipment, potentially encapsulate the belt and pose a serious safety hazard. A dirty and dusty environment also discourages workers from doing regular maintenance on the problem area and negatively affects morale.
Since trips and falls are regularly among the most common workplace accidents, Occupational Safety and Health Administration (OSHA) inspectors are constantly on the lookout for those hazards. Dust levels are also strictly regulated by OSHA, and permit violations are often accompanied by fines and potential downtime.
SEALED CHUTE COMPOSITION A well-designed loading zone typically consists of a combination of components. These include: v An enclosed transfer chute should be long enough to give dust and fines time to settle. v A heavy-duty belt support system absorbs impact, protects the belt and can handle rapidly shifting heavy material. v Closely spaced idlers help avoid sags in the belt that allow gaps where fines can escape and ease material disruption from bouncing. v Externally adjustable or self-adjusting skirting contains fine particles and adapts to fluctuations in the belt plane. v Easily serviced wear liners can be changed from outside the chute without confined space entry. v Dust curtains set strategically throughout the enclosure control airflow and help settle dust. v Dust bags or mounted air cleaners collect tiny, highly active particles. v A sealed tail box protects the tail pulley from the backflow of fines, dust and spillage. v Exit curtains prevent fugitive dust from escaping from the end of the chute.
CASE ST UDY A US power generating facility has drastically reduced dust and spillage from its biomass fuel handling system, helping to prevent fugitive material from reaching nearby homes and businesses. The fuel includes wood from open loop sources (such as waste wood, limbs and agricultural waste) and closed loop sources (dedicated crops of trees), with a goal of averaging 75% of the power generated from biomass fuels.
The material handling system at the site is critical to the plant’s efficiency, but from the time it began operations, controlling dust and spillage was a challenge. Because of the largely residential area in which the facility is located, controlling carryback and spillage were among the top priorities. After a thorough evaluation of the material handling system, Martin Engineering technicians began by installing primary and secondary belt cleaners on all four conveyors.
The primary units on each belt are brush-type cleaners, a unique electricpowered design that provides an effective, cost-efficient solution for residual beltborne material. The secondary units are versatile ‘deflected blade’ designs that feature a gentle pressure to prolong service life and prevent belt damage.
“We installed electric brush cleaners on each conveyor, because they’re very effective on the type of cleated belts used at this facility,” observed the Martin Engineering Territory Manager. “The rotating brush delivers good cleaning performance in difficult applications, including belts with ribs, grooves or chevrons, and belts carrying sticky materials or stringy fibres.”
Part of the problem was that some of the conveyor sections were at steep angles, and with the variable size and moisture content of the fuel, there were always chips that would fall back down. To address the issue, Martin Engineering technicians removed troublesome sections of the conveyor and replaced them with specially-engineered transfer points. They also modified existing transfer points, installing drop chutes to help eliminate dust and transfer chutes with a hood-andspoon design to improve the material flow.
“Reducing the material turbulence during transfers is key to preventing
fugitive dust,” observed a Martin technician. “By managing the material speed and direction, transfer chutes help minimize impact and wear on liners and belts, while containing the dust and spillage that are often generated at transfer points,” he said. “All of the chutes were field-fabricated, which helped us get an exact fit and minimize lead time.”
The transfer chutes employ special geometries that capture and concentrate the material stream as it travels through. Each unit is customized to suit the specific material characteristics and conveyor systems of the individual customer. They provide the dual benefits of minimizing aeration and preventing buildup within the chute, particularly important when dealing with combustible materials.
The installation team also placed electric rotary vibrators in key locations on drop chutes to reduce the potential for plugging. To further ensure control of fugitive material, settling zones were created at the transfer points to slow the air speed, with dust curtains to contain airborne particles.
Finally, skirtboard sealing systems were installed on the sides of the loading zones to contain dust, eliminate spillage and reduce cleanup. The dual-sealing system incorporates a primary seal clamped on the steel skirtboard to keep lumps on the belt and a secondary or ‘outrigger’ strip to capture any fines or dust particles that pass beneath the primary seal. The secondary seal lies gently on the belt and self-adjusts to maintain consistent stripto-belt pressure, despite high-speed material movement and fluctuations in the belt’s line of travel. The unique design incorporates two wear surfaces on a single elastomer sealing strip, installed along the bottom of the skirtboard. When the bottom side of the strip against the belt is worn, the sealing strip is simply flipped over to deliver a second service life.
With the modifications in place, the facility reports significant reductions in spillage and airborne dust. “We’re very pleased with the results we’ve seen in fugitive material control,” said a source close to the project. “We’re now reviewing several other conveyor sections to determine the opportunities for additional dust control measures. Our goal has always been to provide customers with safe, reliable power that’s produced and delivered in an environmentally-responsible manner, and this work is a reflection of that commitment.” A field-fabricated drop chute fitted with a vibrator to improve material flow to the new transfer point.
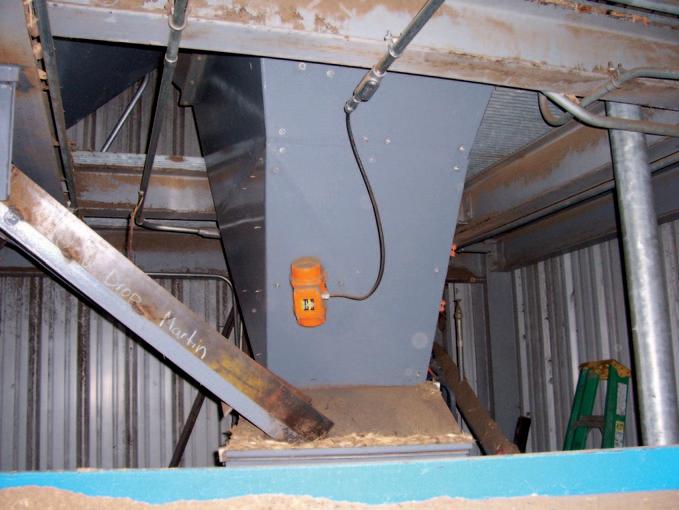
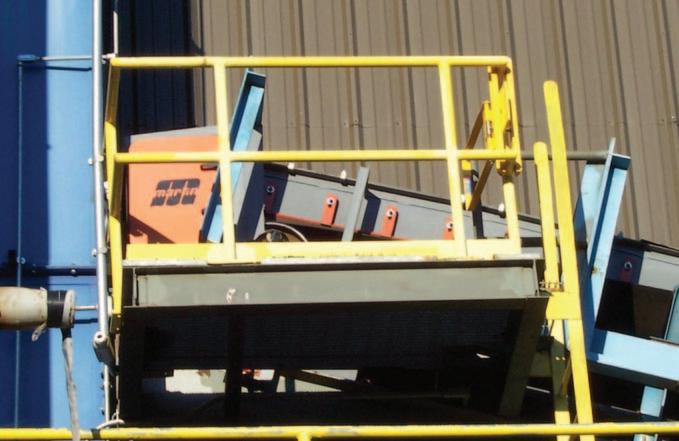
A new head chute and brush cleaner reduced dust by an estimated 95% at the bucket elevator.
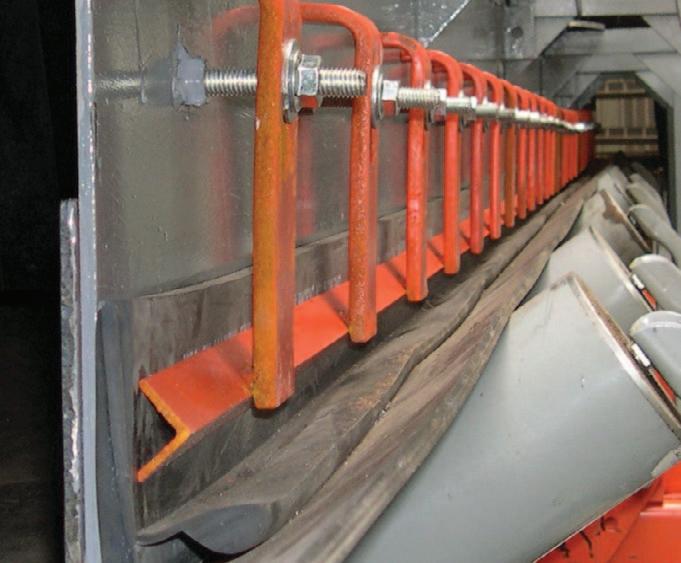

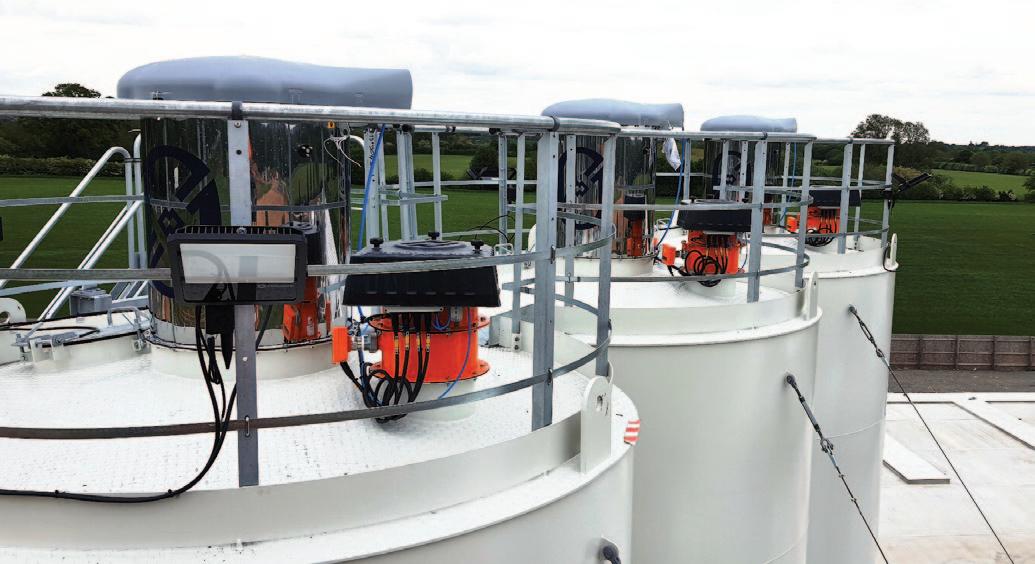
SHIELD LITE 2 IS THE FINAL WORD IN SILO PRESSURE SAFETY Recently having reinforced its reputation as a silo safety expert by collaborating with the Mineral Products Association (MPA) on new guidance for safer pressurized tanker deliveries, Hycontrol Ltd is now proud to announce the launch of the updated SHIELD Lite silo protection system. The revised SPS is smaller than previous versions, with all critical silo-top safety components built-in and pre-wired to provide simpler, easier and lower-cost installation. This design yields safe deliveries straight out of the box, cutting the chance of wiring mistakes. Utilizing purpose- designed pressure monitoring and control equipment, SHIELD Lite meets and exceeds current best practices, including those in the new MPA guidance.
Powder storage silos are used across many industries but are at risk of overpressurization during tanker deliveries. Pressures as low as one psi are enough to rupture a silo or forcibly eject the filter unit from the roof. Besides the physical danger and risk of fatalities from falling equipment, this can cause massive equipment damage and environmental pollution. A comprehensive, failsafe safety and control system is vital to prevent such disastrous outcomes.
SHIELD Lite goes beyond failsafe, providing a fully-automated self-testing safety system that removes the risk of human error from the delivery process by thoroughly monitoring and controlling it. The high-accuracy pressure safety components are preassembled and wired for simple installation. In addition, SHIELD Lite incorporates Hycontrol’s pioneering Ground Level Testing (GLT), whereby a single key-turn activates a full-function test of all the crucial safety components without climbing the silo.
Hycontrol Managing Director Nigel Allen said: “We have insisted for many years that simplicity is the key to safety, so we have made a system that will make a silo safe straight out of the box. With baked-in failsafes like ratio alarms, filter blockage warnings and driver delivery behaviour diagnostics, we can effectively eradicate the risk of human error. We understand that mistakes in maintenance and testing are inevitable. Our philosophy is to accept this and provide a system that monitors and safely alerts you when these errors occur. Safety for staff, contractors and drivers should always be the number one priority. As we say — safe silos are tested every time.”
About Hycontrol: Hycontrol has been at the forefront of level control and silo protection technology for nearly four decades. The company has pioneered failsafe silo pressure safety and groundlevel testing. Hycontrol systems reduce risk, create a safer working environment, and provide the best-engineered solution — without compromise.
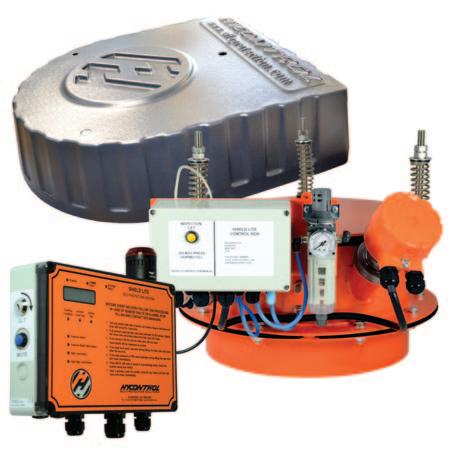
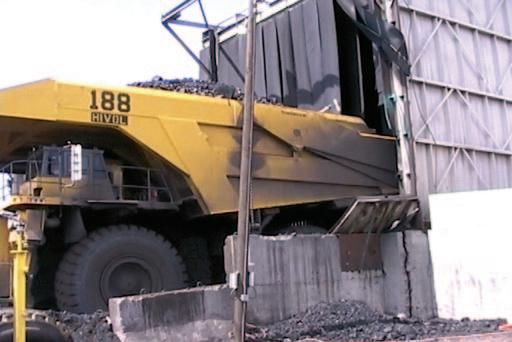
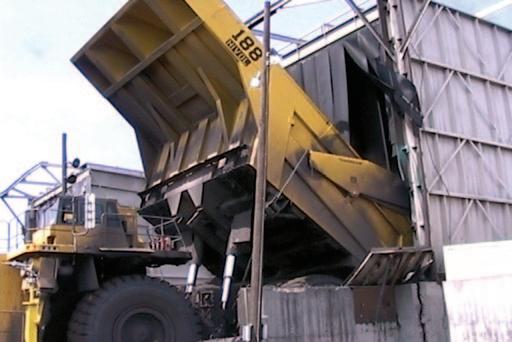
Environmental regulations and scientific research have helped material handling companies to consider airborne dust as a key issue under their operations. This will keep their workers’ health safe, their neighbouring communities dustless and protect our environment, writes Gonzalo Campos Canessa, CEO, The Raring Corp, TRC.
Dust is not easy to control and when it becomes airborne it already polluted the air, so dust must be stop at the source. Although there are different levels of dustiness which basically depends on two main factors: lack of moisture and wind. When bulk material is dry, it is easier that its fine particles become airborne, because it is difficult for them to stay together and to be heavier as a whole bulk. The second factor is how the dirt is exposed to wind. If the dirt is dry and exposed to wind, dust emissions will be seen.
Just focusing on the material handling sources of dust, we can assume that all sources are due to transferring material from one point to another. Within the transfer we can identify wide open transfers (like dump hoppers, open top bins and stockpiles) and those naturally encapsulated (like conveyor belt transfers, fine crushers and screens), where each of them present different levels of complexity when containment has to be implemented. In real life, material handling companies are in the business of moving as much bulk material as they can, and they are reluctant to spend the money required to design ‘dust control friendly’ facilities.
Dust control is a combination of two elements, Passive and Active. The Active dust control systems are those that uses energy to operate, there are several options and suppliers who can take care of this important part which can be done by TRC’s Dust Suppression, Extraction or Scrubbing. Regarding the Passive dust control system, we can say that it is as important as the Active one, and they cannot work apart because of the high interrelationship of passive and active systems. The Passive dust control system is the key element that creates a controlled volume to isolate the point where dust is generated allowing the Active one to do its job. Active systems cannot function without a corresponding passive system –dry fog does not function in open space; dust extraction cannot function without some constraint on the flow of extracted air. If an enclosure is the passive technology, then the larger the enclosure, the tighter it is sealed, the more collection surface is contained within it — the more efficient the passive system and the less the active system will be needed to achieve the goal. If we skimp on passive features, we have to go heavy on active energy and, in some cases, will never achieve the same efficiency.
As an example of the relevance of the passive dust control on truck dumps, I am presenting data collected by the Raring Corporation between 1988 and 2010 and its conclusions. Of the approximately one hundred truck dump dust control systems that has sold between that period, only a handful can be said to work well. 80% of the projects we’ve done use fog and the remainder use only water spray. Twentyfive per cent of the projects that use fog also use water sprays. Only five of the one hundred systems are fully enclosed (stilling shed) and all of those use fog and work very well. A further four are partially enclosed, use fog, and work well. Very few of the open truck dumps using fog have been successful.
When a truck dump that is not covered by a stilling shed but that has a large hopper, includes turning veins to circulate displaced air back into the hopper, and when wind velocity is either naturally below 15km/h or controlled with a Weathersolve windfence (passive dust control), and the dumper orientation is correct with respect to the wind, the dust control can also be efficient.
At the transfer between conveyor belts, we recommend a large passive enclosure with the best possible continuous belt support in the loading zone, dust-tight skirting, a flow control transition from chute to belt that prevents dust from escaping from the back end (or a tail box), enclosure baffles, and three scrubbing zones of dry fog.
Raring Corp has been designing, manufacturing and supplying dust control systems for the last 38 years and it remains convinced that its systems couldn’t be as successful without the Passive Dust Control features.

ENGINEERING & EQUIPMENT Two electric cranes at the Port of Ipswich cut ABP carbon footprint further
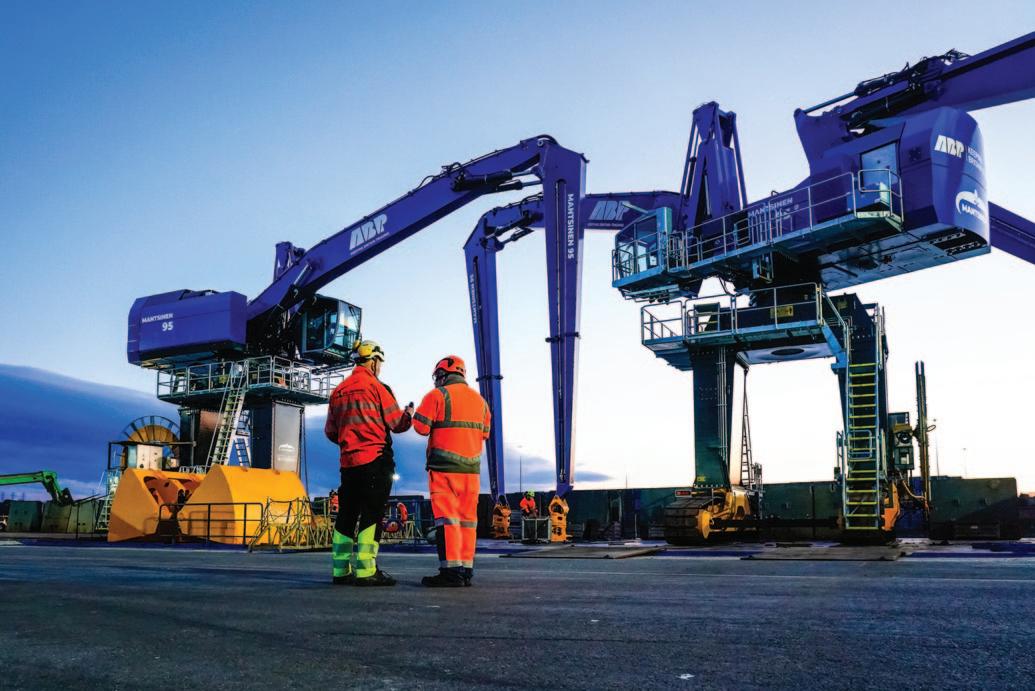
Electric cranes arriving ABP Port of Ipswich.
Associated British Ports (ABP), the UK’s leading ports group, will further reduce its carbon emissions, as two of the very first fully mains-electric powered hydraulic cranes arrive at the Port of Ipswich. These cranes are amongst the first of their kind in the UK and are the latest in a series of bold investments in sustainable measures from ABP, which have contributed to a 36% decrease in greenhouse gas emissions since 2014.
The cranes, Mantsinen model 95ER, have been configured around specific workings of the operations at the Port of Ipswich to optimize efficiencies and further reduce energy consumption. It is estimated that these two electric cranes will save up to 5,275 tonnes of CO2 over their lifetime. To provide perspective, one tonne of CO2 is equivalent to driving a car once around the world (circa 23,000 miles).
ABP has partnered with provider, Cooper Specialised Handling in this pioneering agreement to invest in these multi-million-pound, state of the art cranes that can be powered by the solar energy generated at the port itself. The Port of Ipswich already has ~4,000 solar rooftop solar arrays and has invested in an onsite sub-station to future proof sustainable portside operations, that can accommodate up to four electric powered cranes. The port has also invested in electric vans to minimize the impact of port operations on the environment.
The two cranes will be able to manage a range of material received in the East Anglian Port, which handles over two million tonnes of cargo each year and is the UK’s leading grain export port. Not only will this initiative improve ABP’s green credentials, reducing the port’s CO2 emissions and decreasing energy consumption by up to 40%, but it will also allow for quieter operations and improved air quality.
Paul Ager, Divisional Port Manager said: “ABP is really committed to reducing the Greenhouse Gas emissions arising from port activity. This £4 million investment at the port is the latest development in ABP’s carbon reduction goals tailored to its operations.
The transition to electric machines will not only improve ABP’s cargo handling service to its customers, but will also feed into ABP’s wider policy to reduce CO2 emissions all the way down to zero.
ABOUT ABP EAST ANGLIA With the support of its customers, ABP’s Ports of East Anglia, King’s Lynn, Lowestoft and Ipswich contribute £360 million to the UK economy every year, supporting 3,700 jobs in the region and 5,300 jobs nationally. v ABP’s East Anglia ports handle more than 3 million tonnes of cargo every year Ports in East Anglia handle over 2mt
v
v (million tonnes) of agribulks and 170,000 tonnes of timber annually The Port of Ipswich is the UK’s leading export port for agricultural products
ABOUT ABP
With 21 ports and other transport-related businesses, ABP creates a unique national network capable of handling a vast array of cargo.
The company contributes £7.5 billion to the UK economy every year and supports 119,000 jobs. Its current investment programme promises to further increase its contribution to regional economies around the UK.
ABP:
v Handles over 1.5 million vehicles
v
v
v v
v v every year. Generates around one quarter of the UK’s rail freight. Has 1.4 million square metres of covered storage. Has 1,000 hectares of open storage. Handles around 90mt of cargo each year. Owns 5,000 hectares of port estate. Has 87km of quay.