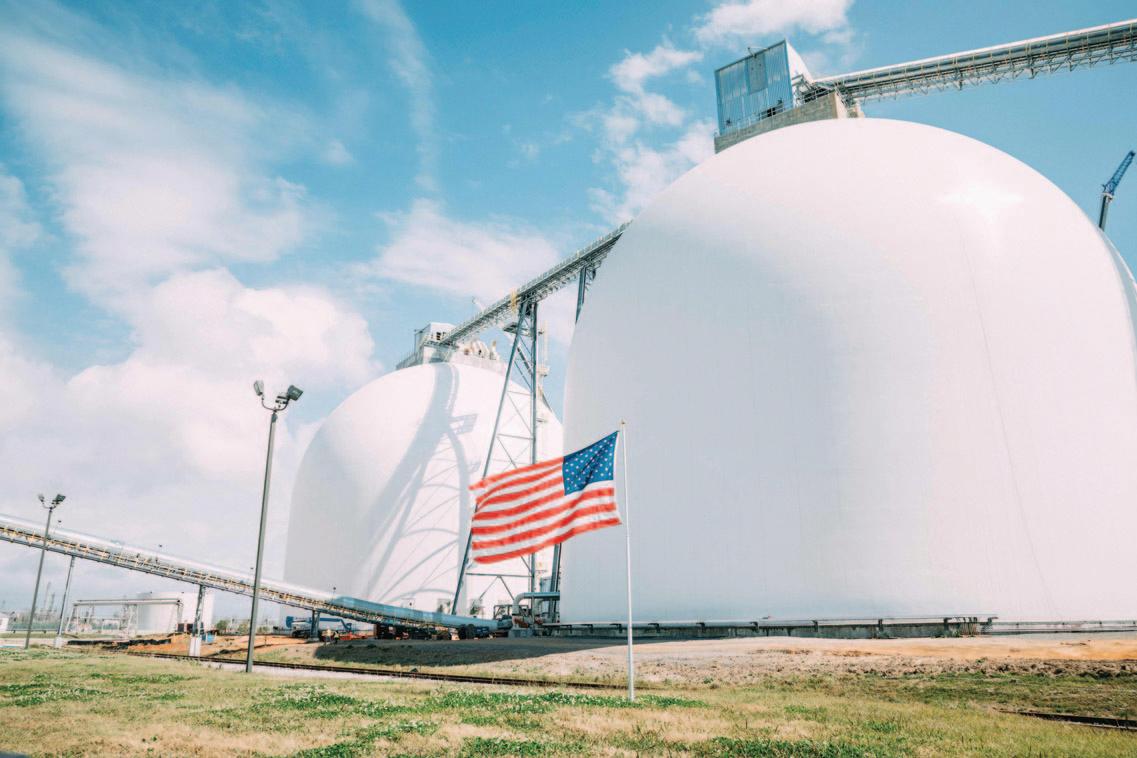
29 minute read
BIOMASS IN BULK: POPULARITY OF ‘GREEN’ SOLUTIONS LIKE BIOMASS CONTINUES TO RISE
Close-up of the exterior of Enviva’s storage domes at the Port of Pascagoula
Biomass in bulk
popularity of ‘green’ solutions like biomass continues to rise
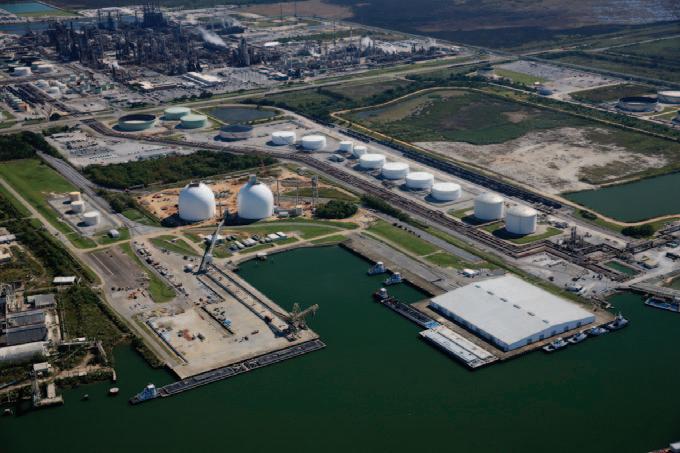
Louise Dodds-Ely
Enviva expands capacity with plans to double production of wood pellets
Enviva’s Port of Pascagoula in Mississippi, USA received its first delivery of pellets from its Lucedale, MS wood pellet production site on 31 March this year, and has been in ‘continuous operation’ since 9 April. The first shipment of pellets will be in Q2 of 2022.
ABOUT THE PORT OF PASCAGOULA At the Port of Pascagoula, through collaboration with the Jackson County Port Authority, Enviva Inc. owns a deepwater marine terminal in the Bayou Casotte Harbor that will serve as the shipment point for pellets manufactured at Enviva’s Lucedale plant and its other plants under development in the Gulf region. The terminal will be capable of receiving product by rail, barge, and truck and supporting Panamax-sized vessels. The facility includes two wood pellet storage domes with 45,000 metric tonnes of storage capacity each.
ABOUT ENVIVA Enviva Inc. is the world’s largest producer of industrial wood pellets, a renewable and sustainable energy source produced by aggregating a natural resource, wood fibre, and processing it into a transportable form, wood pellets. Enviva owns and operates ten plants with a combined production
capacity of approximately 6.2 million MTPY (metric tonnes per year) in Virginia, North Carolina, South Carolina, Georgia, Florida, and Mississippi. Enviva sells most of its wood pellets through long-term take-orpay contracts with creditworthy customers in the UK, the European Union, and Japan, helping to accelerate the energy transition and to decarbonize hard-to-abate sectors like steel, cement, lime, chemicals, and aviation fuels. Enviva exports its wood pellets to global markets through its deepwater marine terminals at the Port of Chesapeake, Virginia, the Port of Wilmington, North Carolina, and the Port of Pascagoula, Mississippi, and from thirdparty deep-water marine terminals in Savannah, Georgia, Mobile, Alabama, and Panama City, Florida.
ENVIVA ANNOUNCES MOU WITH US CUSTOMER, PROVIDES UPDATES TO BUSINESS AND SALES PIPELINE, AND ACCELERATES CAPACITY EXPANSIONS In mid-January this year, Enviva provided a business update announcing a memorandum of understanding (MOU) with Enviva’s first US-based customer, and detailing plans to significantly accelerate its capital expansion timeline due to recent commercial momentum with power and heat generators and with industrials in hard-to-abate sectors. The business update also included preliminary 2021 financial results.
Highlights of the report include: v Plans to accelerate doubling of production capacity over the next five years, including bringing forward plans for a third plant in the Pascagoula,
Mississippi cluster as well as additional plants around Savannah, Georgia and in the mid-Atlantic regions, with capability to build and commission two plants per year, up from one per year; v Signed MOU with Enviva’s first USbased customer, to develop a supply chain strategy to support the customer’s biofuel refining facilities in the Southeast U.S. and potentially
California; v Plans to evaluate building production capacity in California, potentially utilizing fibre in high-hazard zones to mitigate devastating wildfire risk and improve climate benefits of forests in the West; v First shipment of wood pellets to
Germany serving emerging industrial and other adjacent use cases; v Updated customer sales pipeline to more than $40 billion with the addition of the US customer MOU and v results; and Finalized Green Finance Framework and received independent Second Party Opinion (SPO) from S&P Global confirming alignment with green bond and green loan principles.
CONTRACTING UPDATE
Enviva announced the signing of an MOU with a US-based cleantech company to codevelop a supply chain strategy for advanced, low-carbon transportation fuels, including sustainable aviation fuel (SAF), with a focus on the customer’s operations in the US Southeast and potentially California. Under the MOU, the customer’s refining process will convert Enviva’s woody biomass into a drop-in replacement for crude oil used for producing aviation fuel.
Enviva’s current operations and numerous potential development sites in the US Southeast position it to co-develop alongside the SAF refining capacity the customer intends to construct in the region. California is another jurisdiction where Enviva is evaluating plans to build one or more facilities with the intent of utilizing low-grade wood fibre from highhazard zones in the state both to mitigate devastating wildfire risk in the region and tackle the negative effects of climate change globally.
This latest MOU represents not only the second industrial agreement Enviva has recently signed, but also Enviva’s second agreement related to SAF, which underscores the demand momentum for low-carbon transportation fuels.
Enviva recently announced its first shipment to Germany to serve its emerging industrial market (including steel and cement) and other adjacent use cases (such as lime, a key input in cement manufacturing) that are progressing through the phases of design, development, and application, as industrial companies pursue not only their own net-zero goals, but also fulfill the increasing demand for greener products from their own customers.
As of 1 January, 2022, Enviva has a total contracted revenue backlog of over $21 billion. This contracted revenue backlog is complemented by a customer sales pipeline exceeding $40 billion, which includes contracts in various stages of negotiation. Enviva’s customer sales pipeline consists of the US-based MOU, the previously announced J-Power MOU, and other longterm off-take opportunities in traditional markets for biomass-fired power and heat generation in geographies ranging from the UK to the European Union (including emerging opportunities in Germany and Poland), to Asia (including incremental demand in Japan, emerging potential in Taiwan, and maturing opportunities in South Korea), as well as in developing industrial segments across the globe (including steel, cement, lime, chemicals, SAF, and biodiesel). Enviva is negotiating long-term wood pellet supply contracts with several leading industrial companies in each of these difficult-to-abate sectors that are actively and urgently pursing large-scale decarbonization. Over the next 12 months, Enviva expects to progress negotiations and convert several sales pipeline opportunities into binding contracts, including MOUs.
ASSET EXPANSION UPDATE
In response to the increasing pace and scale of commercial progress, Enviva is accelerating its plans to double its production capacity over the next five years, from 6.2 million MTPY to approximately 13 million MTPY. To capitalize on this momentum, Enviva is broadening and deepening its development capabilities and leveraging relationships with key equipment suppliers and construction partners to enable it to build and commission two plants per year, up from its historical rate of one plant per year. Enviva plans to continue utilizing its ‘build and copy’ approach to plant design while increasing the nameplate production capacity of its new plants to approximately 1.1 million MTPY, up roughly 45% from the previous standard of 750,000 metric tonnes per year.
Enviva’s ‘Multi-Plant Expansions’ are expected to be completed by year-end 2022. Enviva also expects its plant in Lucedale, Mississippi, which is the first plant in its Pascagoula cluster, to ramp production throughout 2022, exiting the year at its designed run-rate of 750,000 metric tonnes per year. Additionally, in the first half of 2022, Enviva plans to commence construction of the fully contracted plant in Epes, Alabama, the second plant in the Pascagoula cluster.
Enviva’s business model of fully contracting plants before commencing construction remains unchanged. Given the current pace of contracting with customers, Enviva plans to accelerate the construction of a third wood pellet production plant in its Pascagoula cluster in 2023, along with other proposed plants in the Savannah and mid-Atlantic regions.
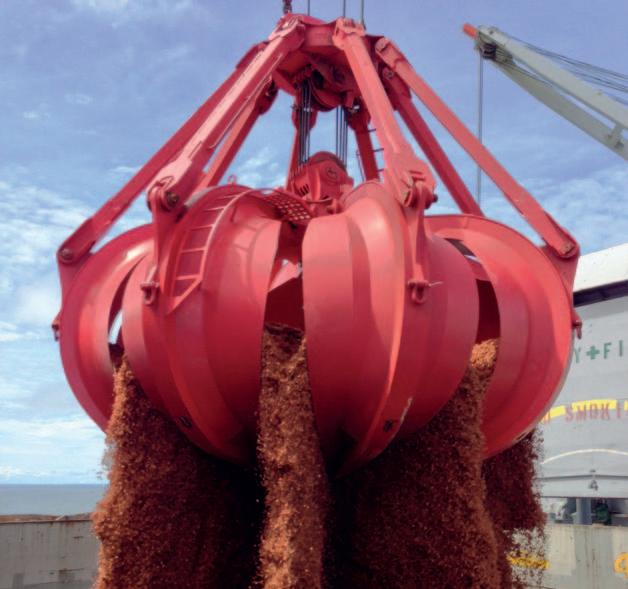


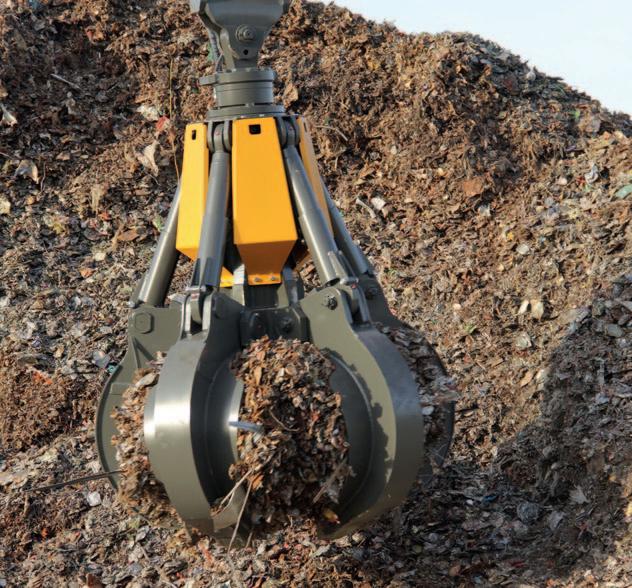
Additionally, it plans to commence and complete the fully-permitted 300,000 metric tonne per year expansion of its Lucedale plant during 2023, which will increase its nameplate production capacity from the current 750,000 metric tonnes per year to approximately one million MTPY.
In 2024, Enviva plans to place both the proposed third and fourth Pascagoula cluster plants in service and begin construction on two additional plants expected to be located in its Savannah, Georgia and Wilmington, North Carolina clusters.
In 2025, Enviva expects all of its Pascagoula cluster plants will be operating at their full run-rate, in addition to having the new Savannah cluster plant in service. It anticipates that construction of its proposed Wilmington cluster plant and Chesapeake cluster plant to be underway.
In 2026, Enviva plans to have both proposed Wilmington and Chesapeake plants in service, with the proposed Savannah plant and Lucedale expansion ramping to full run-rate by the end of the year.
In total, Enviva plans to place six plants in service over the next five years and expects that the construction and commissioning of new plants with a nameplate capacity of 1.1 million MTPY will take up to 18 months, on average, and cost between $200 million and $250 million, with total capital expenditures spanning nine quarters. Each plant is designed to run 24 hours a day, seven days a week, for an average of 350 days per year when accounting for scheduled maintenance days.
ENVIVA ANNOUNCES $250 MILLION INVESTMENT IN NEW PRODUCTION PLANT FOR BOND, MISSISSIPPI TO SERVE GROWING DEMAND FOR RENEWABLE RESOURCES In April this year, Enviva announced it will invest approximately $250 million in Bond, Mississippi to build a new wood pellet production plant. The facility is a key component of the company’s growth strategy to double production capacity from the current 6.2 million MTPY to approximately 13 million MTPY annually over the next five years.
“Markets for our renewable products have been growing rapidly as countries look for new ways to reduce their dependence on coal, natural gas, and other fossil fuels for heat and power generation. Demand from manufacturers driving to reach ‘netzero’ by decarbonizing industrial production of steel, cement, lime, and sustainable aviation fuel is also growing rapidly for us,” said John Keppler, Enviva’s Chairman and CEO. “And in an increasingly volatile geopolitical environment, countries and companies around the world are seeking security of supply from stable partners like the US. This new facility, the community in which it operates, and the tremendous people who support it every day will continue Mississippi’s strong tradition of helping friends across the globe secure energy independence and win the fight against climate change,” he added.
The facility site, directly off Highway 49 in Bond, was selected in close collaboration with Governor Tate Reeves, the Mississippi Development Authority, and Stone County officials.
The plant is fully contracted under longterm take-or-pay supply contracts with customers around the world, providing for durable, positive economic impact to the community. In addition to creating around 100 local jobs with wages projected to be approximately 70% higher than the county average, the Bond plant will generate more than $1 million in taxes per year for the county and school district and deliver over $250 million annually in economic impact in the region. Once operational, the plant will support more than 350 jobs, including those in related industries such as logging and transportation.
The new plant in Stone County joins two other Enviva facilities in Mississippi, one in Amory, which is Enviva’s first production plant in the state, and the company’s most recent manufacturing facility in Lucedale. The company also owns and operates a deep-water marine terminal at the Port of Pascagoula from which pellets are shipped to customers in Europe and Asia. Combined, Enviva’s total investment in the Magnolia State is more than $600 million and supports over 850 direct and indirect jobs in Mississippi.
“We very much appreciate the skilled workforce and great business environment in the state. I want to thank Governor Reeves, his team, and the Stone County community for being such great partners during site selection,” Keppler said.
“Enviva’s decision to invest a quarter of a billion dollars and create 100 new jobs in Mississippi is another tremendous win for our state’s economy. It’s further proof that Mississippi is a prime location for manufacturing. I’m incredibly proud that these wood pellets, produced right here by hardworking and skilled Mississippians, will be distributed and used around the globe. I’d like to thank Chairman and CEO John Keppler and the entire Enviva team for their dedication to our state and all that they have done to bolster Stone County and its residents. We look forward to our continued partnership for many years to come,” said Governor Reeves.
Construction is expected to begin in early 2023, subject to receiving the necessary permits, and is expected to take approximately 18 months. The Bond plant is expected to have a production capacity of more than one million MTPY of wood pellets.
Mississippi has a robust fibre supply basket, and the plant intends to use lowvalue and low-grade softwood and hardwood fibre sustainably sourced within 75 miles of the facility, creating durable markets for local landowners and incentives to keep land as forests. The facility will use state-of-the-art environmental control technology to minimize any impact from the plant’s operation on the community.
“Stone County was founded on the timber industry more than a hundred years ago. Our citizens have long respected the woods and the natural resources they provide. With the announcement of Enviva, we have an opportunity to produce a record number of new jobs because of the plentiful resources in Stone County. Our most important asset, our people, will benefit from the growth we will experience for decades to come,” said Lance Pearson, President of the Stone County Board of Supervisors.
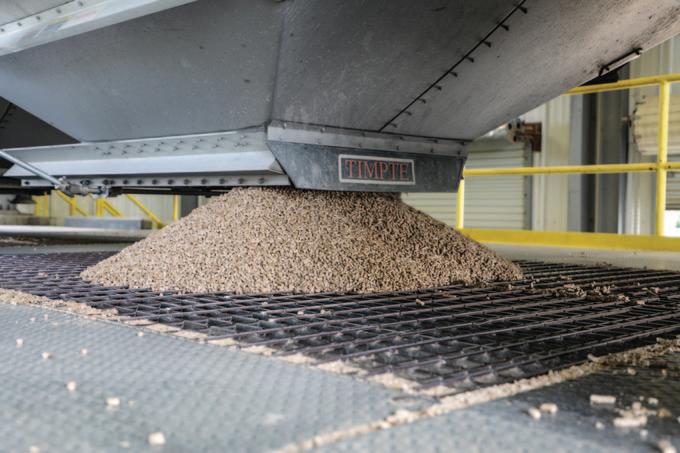
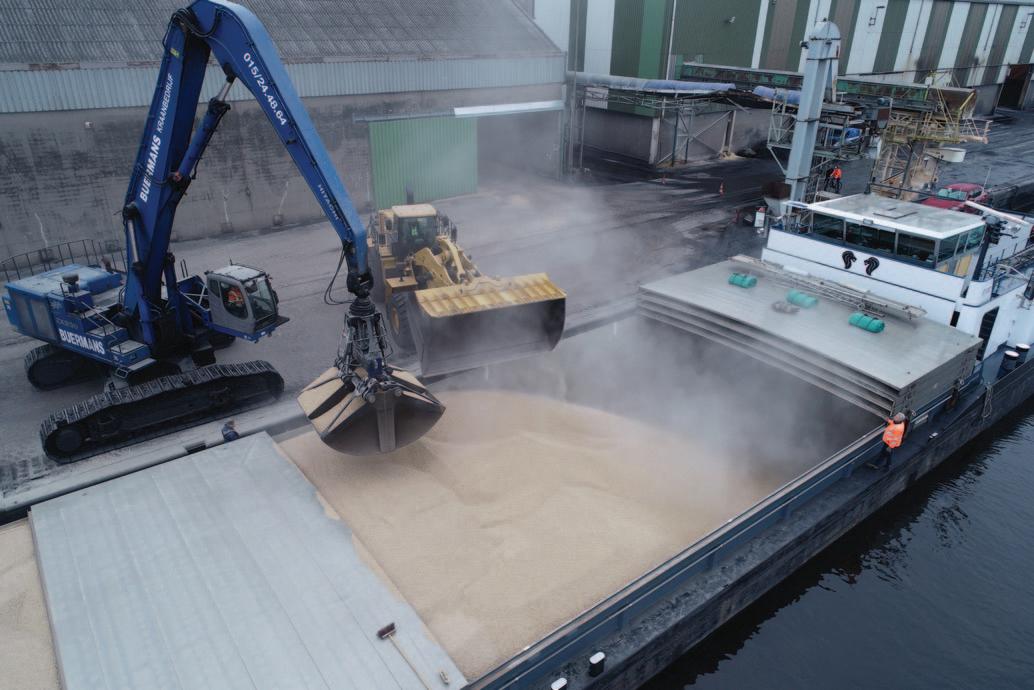
Terval SA founded in 1981 and based in the port of Liège in Belgium, is a company specialized in the trading and processing of coal for the western European industrial market. Terval trades about 2mt (million tonnes) of material a year sourced from all around the world. More than 90% of the volume handled by Terval transits by waterway. The rest is divided between the rail- and roadway. The Port of Liège ranks second after Duisburg among European inland ports. Terval’s trimodal terminal can load up 6,000 tonnes and unload up to 12,000 tonnes of dry bulk daily.
For the last several years, European governments and EU commissions have been strengthening their environmental politics, which tends to force the industry to change its way of thinking by disinvesting itself from fossil fuel. A few years ago, we saw many industrials turn to gas due to its low prices and its lower dependency on logistical issues — low water levels on the major rivers of Western Europe for instance. Nevertheless, over the last months, and due also to the Ukraine war and Europe’s desire to become less dependent on Russian gas imports, this trend appears to be reversing and industrials are returning to coal.
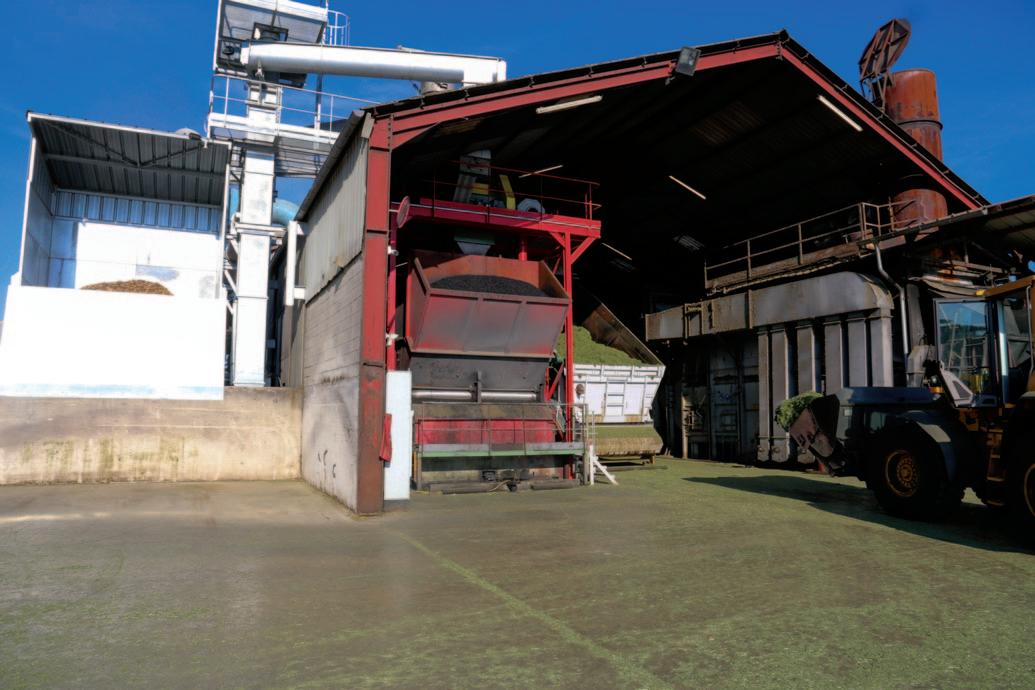
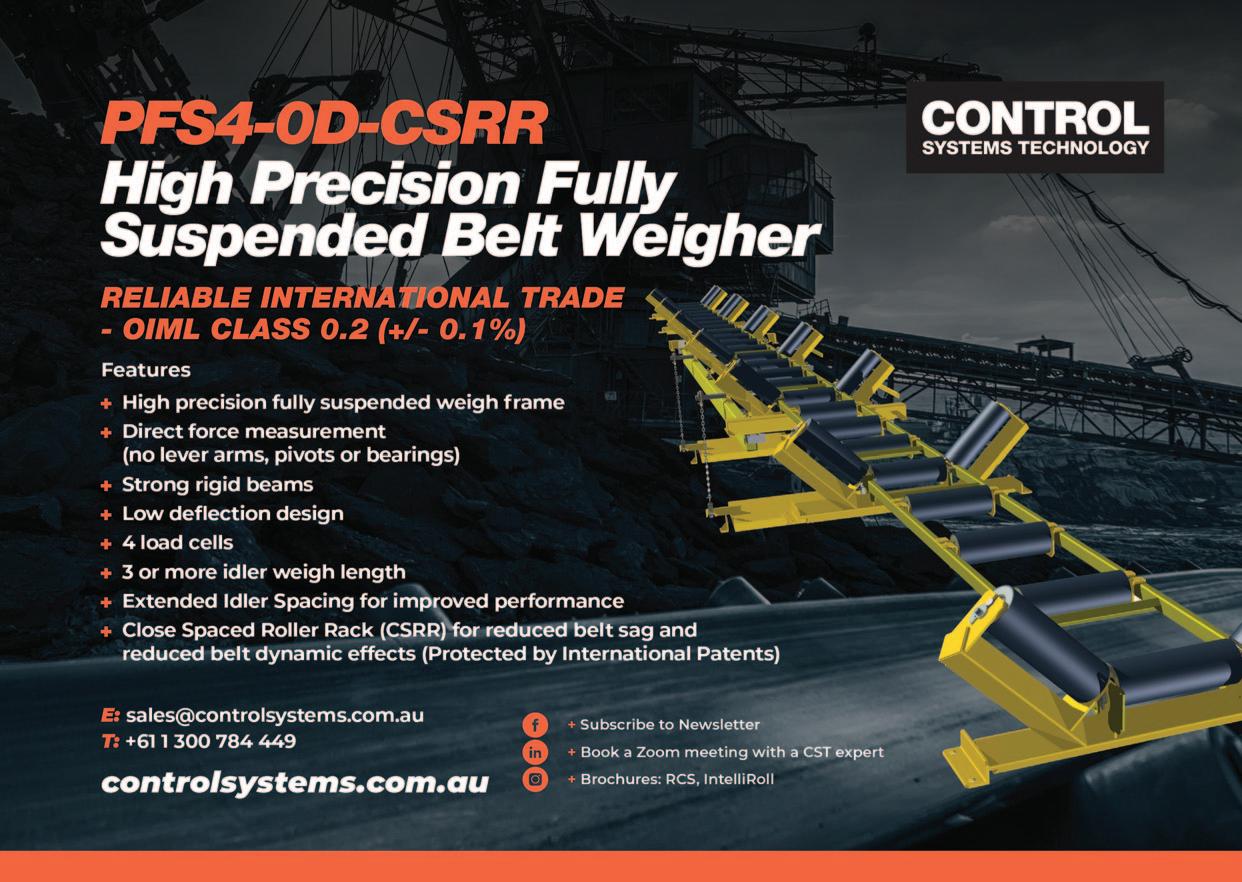

Beyond coal and gas market, there is also a willingness from industry to implement biomass in their energy portfolio. It’s a long-term job that requires a lot of time and resources. Terval, via its French subsidiary Bioval, works directly with its current clients — mainly the sugar industry and the dehydration of lucerne crops in France — in the implementation of biomass projectors to convert their furnaces and coal boilers. The objective is to transition to 100% Biomass-to-Energy. With the technology developed by Bioval, Terval can revamp existing installations, thus minimizing CAPEX costs. Furthermore, generally it is possible to increase evaporation capacity for an existing dehydration plant of ca. 30%. With Bioval’s expertise in the combustion of solid fuels, it helps its customers to
optimize combustion, which represents in general the highest cost factor to them. Also, many different biomass types can be used.
By choosing the Bioval solution, the customer is able for transition of up to 100% biomass, to increase the plant’s capacity and to optimize its combustion. The objective now for Bioval is to broaden the spectrum of customers as well to extend abroad by recruiting new engineers.
Terval has 24,000m² warehouse space, with 3,200m² dedicated to ±10,000 tonnes of woodpellets storage. Since 2020, Terval has been working with the Danish Company CM Biomass, a major market maker in Europe. It organizes, on their behalf the unloading, storage and reloading of wood pellets for industrial end-users. These pellets are originated from European productions and from abroad. A new warehouse project with 3,200m² is under construction and will offer a capacity of between 10,000–18,000 tonnes for pellets or other biomasses.
Terval also trades torrefied wood pellet quality for the industry. This pellet has a brown colour and is water resistant. Therefore, outside storage without damaging the structure/quality of the product is no problem. The manufacturer of this pellet is using a specific technology of vapocracking allowing an outwards transfer of the lignin inside wood molecules.
It is this outwards transfer of the lignin that will give this hydrophobic property to the pellet. It is a brand-new technology and volumes are quite limited so far, but this product will potentially find its way in the biomass market.
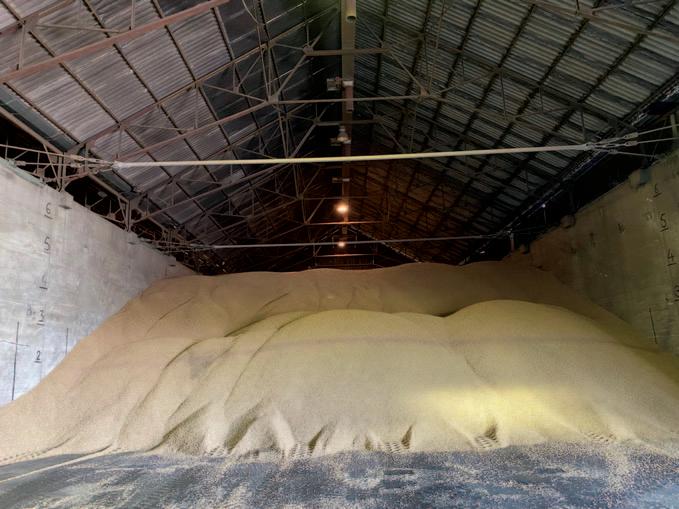
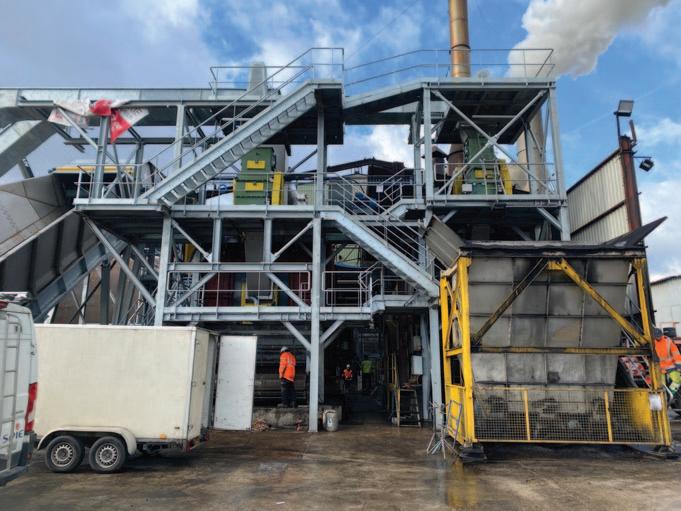
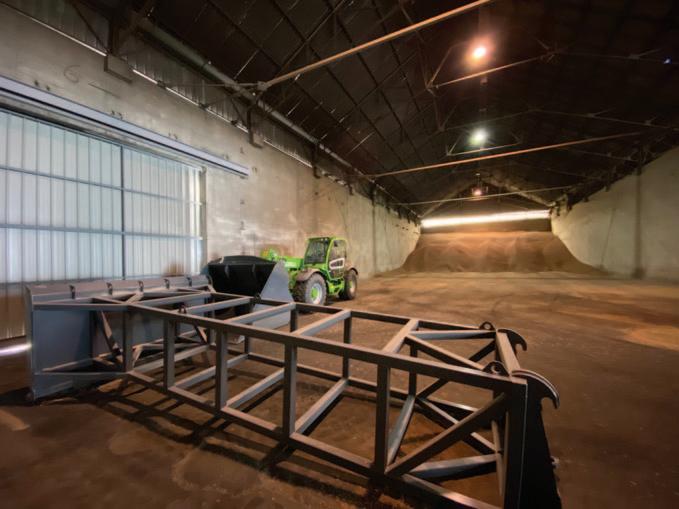
Associated British Port’s (ABP) Port of Immingham is the leading UK port specializing in the latest facilities and equipment to store and handle biomass.
The team at the state-of-the-art Immingham Renewable Fuels Terminal (IRFT) works closely with customers to offer safe, efficient, and cost-effective handling of cargoes.
IRFT has the latest leading-edge handling and storage solutions and is the Europe’s largest biomass handling facility bringing in the bulk energy cargo (wood pellets) to fuel the UK’s leading power plants.
It can discharge and store 200,000 tonnes of wood pellets in eight silos. The facility can handle 6mt (million tonnes) per year with two dedicated continuous ship-unloaders,
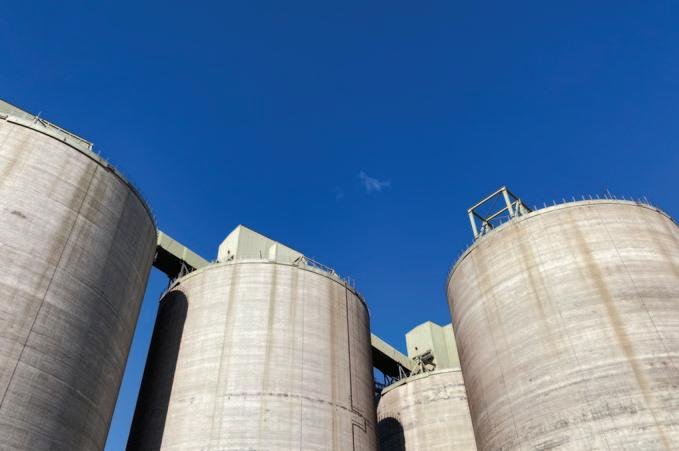
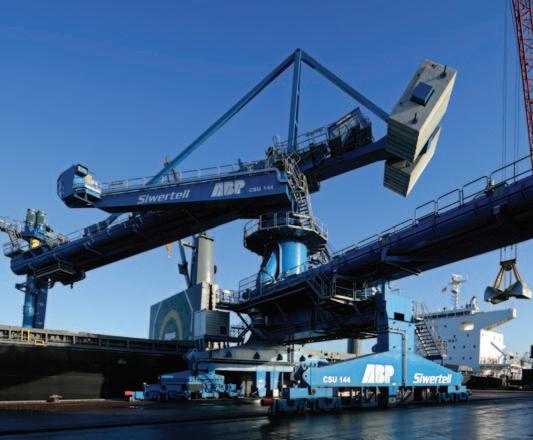
and fully automated enclosed conveyors which transport the biomass to the silos for storage. A reclaim system efficiently delivers high volumes of cargo for onward transit by rail. £150 million has been invested into facilities and equipment at the terminal to ensure it is at the forefront of technology.
The team at IRFT is focused on the continuous improvement of their operation and is always implementing new ways of working that improve the Health and Safety of all terminal users, and the efficiency and productivity of the terminal’s operations.
The Humber port can also handle some of the largest vessels in the world at the Humber International Terminal (HIT), which is ABP’s largest terminal. It benefits from excellent road and rail connectivity to the rest of the UK.
The Port of Immingham in the Humber Estuary is the UK’s largest port by tonnage, handling around 46mt of cargo every year. It forms a critical part of the supply chain for energy production, helping power the nation and helping to cement the Humber as the ‘UK’s Energy Estuary.’
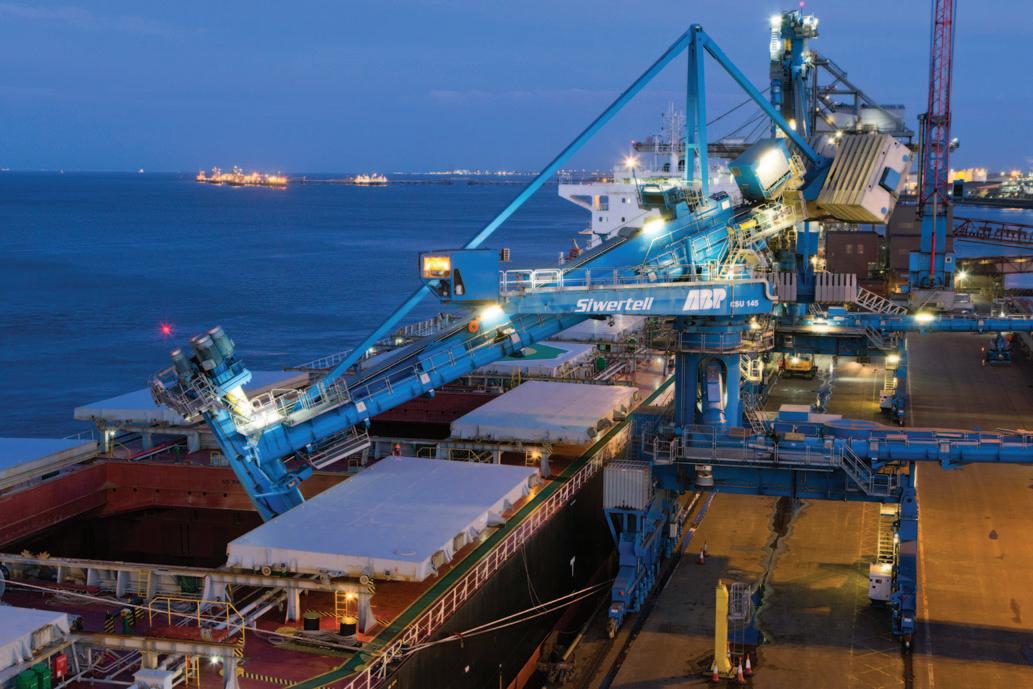
New technology for feeding biomass and MSW feedstocks into high-pressure environments
Biomass is a general term used to describe a variety of materials including wood chips, pellets, sawdust, milled switch grass, corn stover, etc, writes Dr. Jayant Khambekar, Senior Consultant, Jenike & Johanson. From a material storage and handling perspective, these materials can exhibit various handling challenges. Materials such as milled corn stover are very light and often exhibit nesting tendencies that result in discharge issues from hoppers and silos, whereas materials such as woodchips exhibit strong interlocking tendencies. Pellets may undergo attrition and generate dust, which can pose an explosion hazard. Municipal Solids Waste (MSW) is a feedstock which has flow characteristics that are similar to biomass materials. As such, MSW feedstocks also experience similar flow issues during handling. Whether it is gravity-reclaim stockpiles, silos or feed hoppers, or feed-systems to pressurized reactors, unless properly designed, they can experience flow problems such as flow stoppages, limited live storage capacity, feed rate limitation, etc. Similarly, if the feeder and transfer chutes are not designed properly, they can result in flow problems. These problems in the feedstock receiving area can be avoided by properly designing or retrofitting the storage and handling systems.
Even more critical are the problems with feeding material into high-pressure, high-temperature environment. Many technologies for biofuels involve feeding biomass materials into such high-pressure, high-temperature reactors. Delivering feedstock reliably across this pressure barrier is no simple task, especially when the feedstock is difficult to handle materials like biomass and MSW. Many of the existing technologies for feeding materials into high-pressure environment that are based on use of plug-screw-feeders have to overcome challenges with pressure blow back. On the other hand, existing technologies based on lock-hoppers have to overcome challenges with arching/ bridging associated with feeding material into a high pressure environment. Getting a continuous discharge from a typical lockhopper systems can be a problem too as these systems usually work on batch process mode. The success of any such biofuels or waste-to-energy plant depends on reliably feeding the reactor.
To address these problems, Jenike & Johanson (Jenike) has developed a new technology to feed materials like biomass and MSW into high pressure, high-temp erature environ ments. This patent-pending tech nology is focused on reducing consolidation of feedstock during handling, minimizing springback of biomass materials, and providing continuous discharge into pressurized environment using a unique lock-hopper-based system design.
Established in 1966, Jenike is a global technology company which provides solutions for reliable storage and handling of bulk solids. Jenike has more than five decades of experience in designing handling systems for various challenging materials like biomass and MSW. Jenike also has significant experience with designing lock hoppers, since 1980s. Leveraging Jenike’s experience in biomass handling and lockhopper design, it has developed this unique, patent-pending technology that can reliably feed biomass and MSW feedstocks into high-pressure, high-temperature environ ments such as biofuel reactors. The company is excited about this new technology and is happy to discuss it with any interested reader.
Apart from feeding pressurized reactors, Jenike is also uniquely positioned to assist clients with designing/retrofitting feedstock handling systems, right from the receiving area up to the feed-system for the pressurized reactor. For this upstream handling, various solids flow issues can occur.
Problems Jenike solves/avoids: v flow stoppages or erratic flow due to arching and ratholing in silos and feed hoppers; v limited live storage capacity in silos and gravity reclaim stockpiles; v feeder discharge issues; v chute pluggages; v attrition and dust generation during pellet handling; and v solids handling equipment failure investigations.
Bulk solids handling problems are often the major cause of costly downtime and demurrage charges for many facilities, especially during startup! These same flow problems continue plaguing on-going operations by limiting throughput and creating safety and health risks, as well as reducing equipment life, increasing maintenance costs and causing premature equipment failure.
To address these costly problems, Jenike has developed proven ways to design handling equipment that will promote reliable, smooth and unrestricted flow of bulk solids. Bulk solids handling equipment design should not be a trial-and-error approach; Jenike doesn’t guess at material properties, it measures them. The company has the largest and most complete laboratory in the world for characterizing the flow properties of bulk solids under representative environmental conditions. For over 56 years, Jenike has focused on developing first principle theories on bulk solids flow and conveying behaviour.
Jenike’s services include: v licensing technology for feeding material into a pressurized environment; v biomass flowability study; v silo, hopper and stockpile gravityreclaim system design; v feeder design; v transfer chute design; v calculation of material flow induced loads on silo and hopper walls; and v training on solids flow and pneumatic transport
Jenike combines test results and real world project experience, which yields the best solution in terms of reliability and costeffectiveness. Its skilled and experienced engineers provide detailed structural and mechanical design of solids handling equipment, and routinely design silos, hoppers, feeders and transfer chutes.
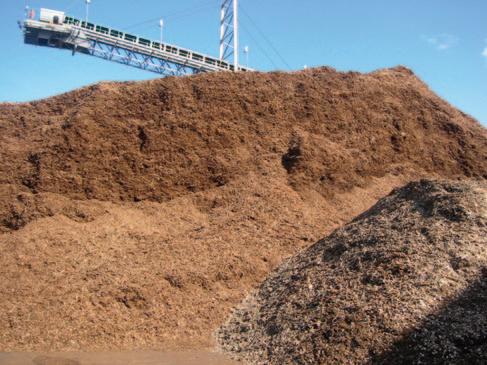
Around the globe, an increasing share of total energy production is generated by biomass powerplants. Biomass has rapidly become an important substitute for other more traditional sources of energy generation such as coal and has become a key part in the energy transition journey.
The largest source of biomass energy is wood and residues from wood. Whether it’s woodchips, pellets or also other types of biomass, then during handling, shredding and/or upgrading a considerable amount of dust is generated. Extended or repeated exposure to fine biomass dust has a negative health effect as biomass dust is a carcinogen, i.e. a substance that promotes carcinogenesis or the formation of cancer.
Furthermore, it is a fact that from biomass handling points — such as power plants or recycling facilities — dust travels for miles and spreads out over the surrounding areas and communities. Apart from the health issues that this causes, there is also a considerable loss of product.
Over the years, dust-control specialist Wuvio has, in close co-operation with a number of important players, developed a range of solutions dealing with biomass dust.
FOAMING In general, the basis for Wuvio’s solutions to combat dust in biomass environments is foaming.
This is a solution used for inline treatment, with increased active duration of up to 30 days if need be. Applied with compressed air, a Wuvio’s dry foam is created with minimal usage of water and consequently low moisture levels, so that the (calorific) value of biomass is not impacted. Ideally Wuvio’s dry foam is applied by using a spray bar with nozzles that spray it into the drop points of the conveyor belt system or shredder.
Furthermore, Wuvio’s foam solution has a number of advantages over the spraying of water, as the product: v can be applied using existing/standard nozzles and sprinklers; v reduces water consumption by 80%; v reduces dust emissions by 90%; v is 100% biodegradable and harmless to the aquatic environment; and v is 100% safe for people and the environment.
EQUIPMENT Wuvio’s focus is to provide a fully integrated solution, which is built to be rugged enough to withstand harsh environments. The key is to have the equipment work for you, so typically Wuvio’s spraying solutions are integrated with system automation to work in conjunction with the production line.
Wuvio offers a variety of spraying equipment: v spraying cannons which can be used for spraying stockpiles — various tank sizes; v automated foam dosing units, spray bars & atomizing systems; and v a full range of automated mixing solutions including buffer tanks and silos.
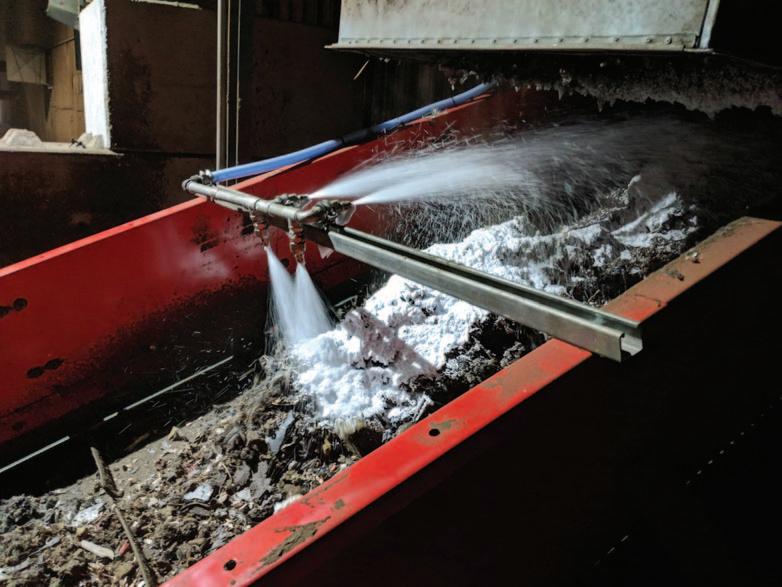

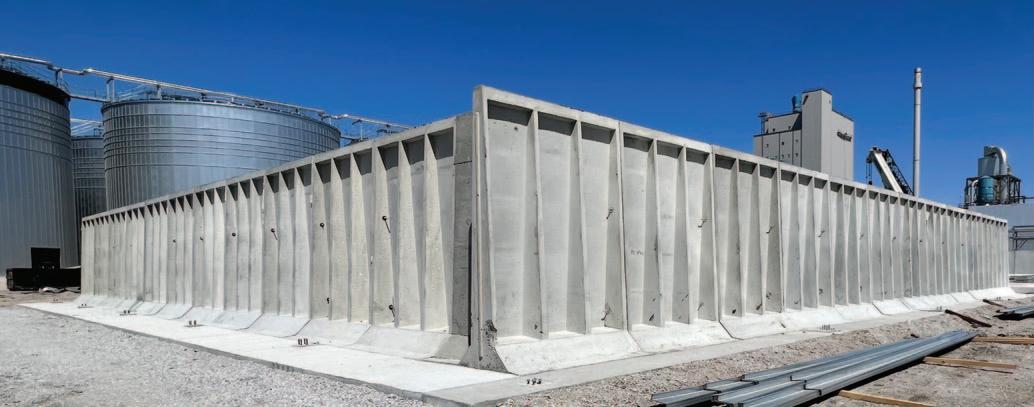
Hanson Silo LP recently completed a biomass storage containment system with its precast concrete 12ft-high storage wall panels. The bunker is storing Humus waste. Essentially, 30 million gallons of human manure is mixed with stover bales to run a digester, and then the final product is sold as a compost fertilizer.
The VERBIO Nevada Biorefinery, located in Nevada, Iowa (USA), is the first industrial scale renewable natural gas (RNG) facility in North America using agricultural residues as its feedstock. The plant is 100% owned by VERBIO North America Holdings Corporation.
RNG production from corn stover began in December 2021 with the completion of Phase I, at a capacity of seven million ethanol gallons equivalent (EGE) per year. Upon completion of Phase II in the fourth quarter of 2022, the site will begin operating as a biorefinery, producing 60 million gallons of corn-based ethanol and an additional 19 million (EGE) of RNG from stillage. The integration of RNG and ethanol production, unique to VERBIO, incorporates advanced operational technology currently practised at the company’s facilities in Germany. The process also yields humus, a soil amendment, and organic fertilizers.
ABOUT PRECAST PANELS It is possible to use every inch of a bulk storage building with precast panel walls along the perimeter. The panels are designed to optimize pile heights and locations to help users load, handle and work more efficiently. There is no wasted space and no wasted material in a custom building designed around a precast panel containment system. v Faster construction: precast concrete panels are fabricated and delivered to
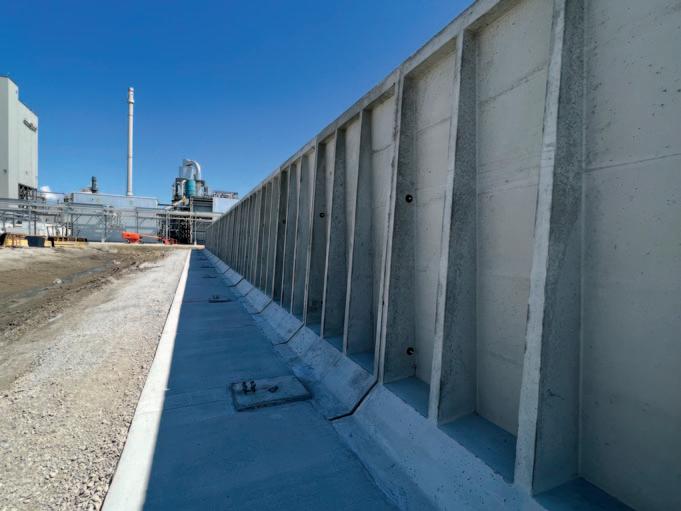
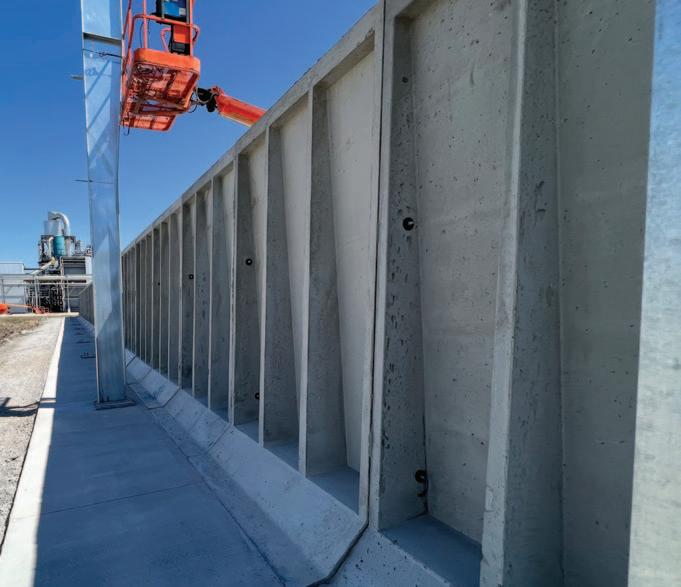
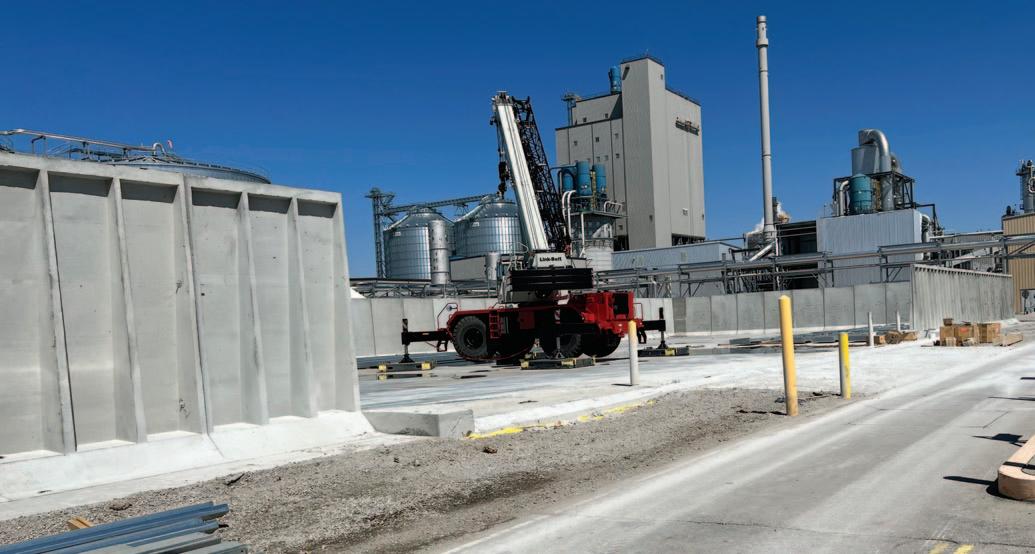
v the site. The panels are assembled and cured in a controlled environment for easy, expedited manufacturing. Because the panels are made offsite, they are not delayed by weather or construction permits. After assembly, the panels are delivered to the building location and set in place, with no footings and no additional curing time. An entire precast panel system can be assembled in just one day. Durability: precast concrete withstands pressure from stored materials, increasing the bulk storage capacity of a fabric building. An experienced building consultant will calculate the size of the precast panels needed based on tonnage and requirements. A custom panel system provides the required storage without wasted materials and labour. Concrete panels withstand constant exposure to corrosive elements and collision. They are not vulnerable to pests and do not serve as feedstock for rodents. The quality of concrete does not deteriorate over time, making them a longer-lasting option for bulk storage. Exceptional value: in addition to the
v
faster construction time, concrete panels allow the building owner flexibility for current and future storage needs. Precast panels are moveable and reconfigurable to store or blend new products. Changing the size and shape of a bin is as easy as moving a few panels and loading the new product in place. Concrete is easy to wash and dry when cycling through materials. And precast panels are portable assets if the building is relocated in the future.
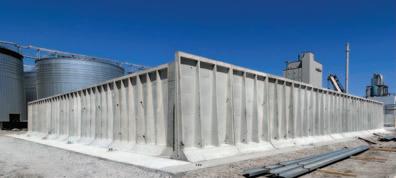

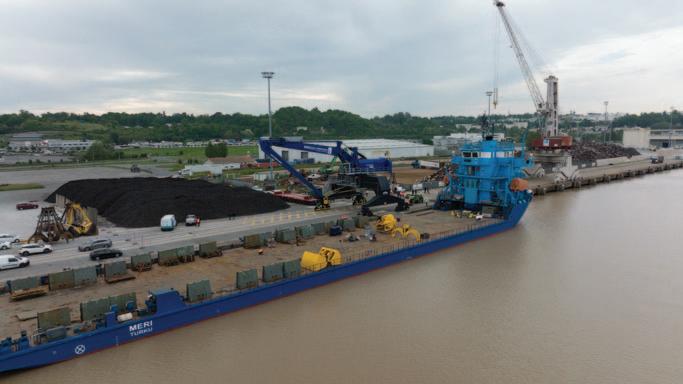
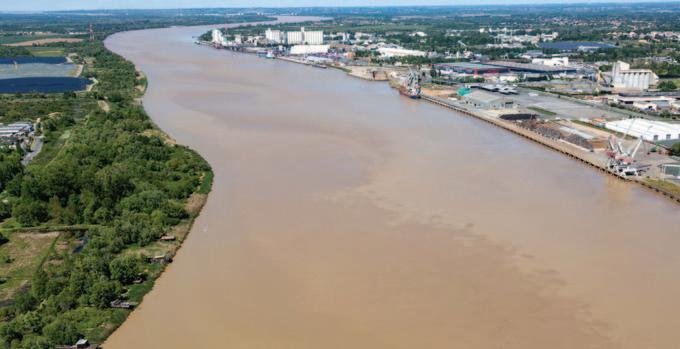
Beyond agricultural bulk, the major bulk challenge for the Port of Bordeaux in France is to recover and develop the volumes generated by all niche dry bulk, by proposing an adapted and quality offer, where storage plays a major role.
Biomass is an energy recovery process that consists of using the calories contained in waste by burning it and recovering the energy thus produced. It is included in the Bordeaux port’s 2021–25 strategic project as one of the processes of the future.
This is why the port is committed to renovating and bringing up to standard the hangars of the Bassens terminal, i.e. hangars 45, 43 and 42bis from the end of 2022.
These investments are an initial response to the needs of the various existing and future industries in the port of Bordeaux and in the hinterland when necessary, particularly all products derived from biomass.
This work will make it possible to expand the classes of products that can be stored in the warehouse and to guarantee better storage and handling conditions for the goods (2022).
The stakes are high because the storage activity, which is essential in the case of volumes generated by biomass, is a link in the logistics chain associated with the goods. The challenge for the shipper is to minimize costs while having a responsive and fluid supply chain.
Mention should also be made of the investments made for Bordeaux Opérations Portuaires (BOP), the Bordeaux port branch specializing in handling. The acquisition of a Mantsinen 300 series crane (the largest model on the shovel crane market) is a strong signal of Bordeaux Port’s ambitions in the dry bulk sector. It is indeed a hydraulic machine intended for multi-bulk operations, which will reinforce the fleet of cranes existing at the port of Bordeaux. The reception of this material handler took place this month in May with commissioning scheduled during June. Fitted with a 14m3 bucket, this newgeneration crane will be able to handle all types of traffic related to the biomass sector with flexibility and efficiency, whatever the vessel.
THE PROSPECTS FOR THE WOOD-ENERGY SECTOR Wood is the first source of renewable energy used in France, where the resource is present in quantity. It represents more than 40% of renewable energy in France. Wood energy is therefore expected to contribute significantly to the French energy and climate objectives (ADEME).
The wood energy sector is growing and demand is increasing, whether for boiler rooms (pellets) or heat production (agricultural greenhouses) or electricity. The sector is organizing itself to improve logistics and become competitive so that maritime flows are possible.
Wood-energy represents 80% of renewable heat. The production of heat is the main outlet of wood energy, wood being used in various forms (logs, briquettes, pellets).
The consumption of pellets in France is essentially national, or in import/export with neighbouring countries for small volumes. Wood biomass of the pellet type is a bulk product of low density adapted to the massive modes.
The ban announced by the Government to install new oil-fired boilers makes the biomass prospects strengthened.
In a context of energy transition, it is of course renewable energies that must answer the call. However, importing pellets from distant regions (e.g. Brazil for Gardanne) does not appear to be a sustainable solution for the Port of Bordeaux.
DEVELOPMENT PROSPECTS New Aquitaine benefits from a significant biomass resource, with the largest cultivated forest in Europe. It does not therefore need to import in the short or medium term.
On the other hand, from the port of Bassens, export/cabotage prospects could exist, to supply the regions of Central France, less well endowed with cultivated forests.
Bordeaux Port already operates 15 to 20kt of chipped wood annually.
In addition, Bordeaux Port signed an agreement with CVE on 1 December 2021, allowing the construction and operation of a methanization unit within the perimeter of the port in the municipalities of Bassens and Ambarès-etLagrave. This territory project, developed within the framework of the PEEPOS (Positive Energy and Economy Port) approach and in a circular economy logic, will allow the production of bio-methane which will be directly injected into the local gas distribution network.
The CVE/Port of Bordeaux project will allow the recovery of up to 25,000 tonnes per year of organic matter from the region, including by-products from port industries and local agri-food companies, organic matter from local communities and agricultural matter produced nearby.
The biomethane produced by the unit will be directly injected into the local network. The unit will produce the equivalent of the consumption of about 3,500 households, i.e. the equivalent of the population of the town of Bassens.
New Mantsinen crane and shredded tyres in the background (photo:© Rosamund Quentin Chaumy).