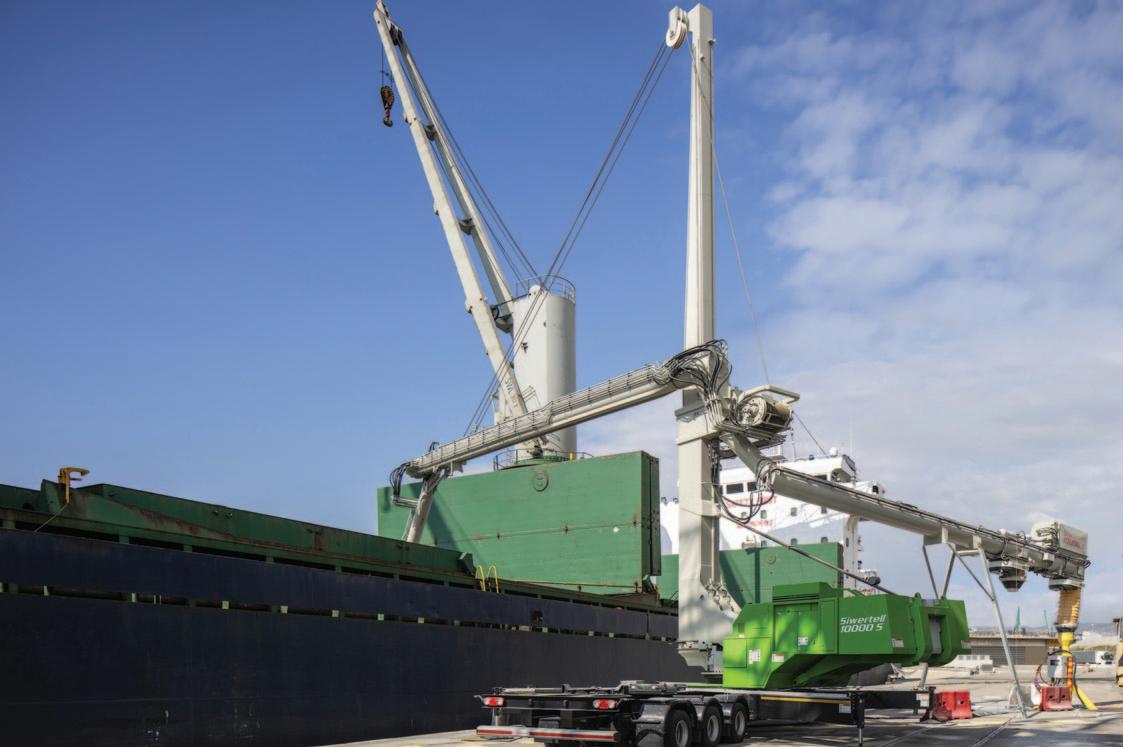
67 minute read
SMOOTH OPERATORS: KEEPING CEMENT MOVING SAFELY AND EFFICIENTLY WITH THE RIGHT EQUIPMENT
Smooth operators
keeping cement moving safely and efficiently with the right equipment
Louise Dodds-Ely
Siwertell road-mobile unloader for dust-free cement handling in Sweden
Bruks Siwertell has received an order from Swecem AB, a subsidiary of Peab Group’s Swerock, for a next-generation Siwertell road-mobile ship-unloader. It will secure environment-friendly, dust-free material handling for the Merit producer and cement purchaser in the port of Helsingborg, Sweden.
“Environmental protection is a key consideration for Swecem’s operations and it adheres to very strict standards,” says Jörgen Ojeda, Sales Director Mobile Unloaders, Bruks Siwertell. “With this in mind, Swecem was looking for a shipunloading solution that could deliver continuously high through-ship capacities, but at the same time, ensure enclosed dry bulk material handling to minimize any environmental impact.
“This is also an important order because it is part of a growing picture that will see all operators taking more sustainable steps,” Ojeda continues. “Sweden has a mounting legislative drive to reduce the environmental impact of the country’s cement industry. However, the same industry has to maintain, and even exceed, current ship unloading capabilities to keep up with growth, posing a potential future gap in supply and demand. Our systems can, and will be, part of this positive change.”
Siwertell road-mobile unloaders deliver totally enclosed material handling from the ship’s hold to the receiving system, which minimizes dust emissions and eliminates spillage entirely. Furthermore, they have a dust filter installed at the top of the loading conveyor, creating negative pressure to minimize fugitive dust at transfer points. The filter automatically returns collected dust to the conveying system.
Road-mobile systems also offer a high degree of flexibility and can move from port to port, requiring minimal infrastructure. They have a worldwide reputation for reliability and efficiency.
“This was certainly a factor in the order, along with good feedback from other Siwertell ship unloader owners” notes Ojeda. “We also could offer a local presence, with offices close by for any through-life service support.”
Swecem’s new Siwertell 10 000 S nextgeneration road-mobile unit will have a continuous cement unloading capacity of 300 tonnes per hour and is able to discharge vessels up to around 10,000dwt. It will be delivered fully assembled to the operator’s import terminal in May 2022.
ENGINEERING & EQUIPMENT BEUMER Customer Support assists cement manufacturer in the modernization of bucket elevators
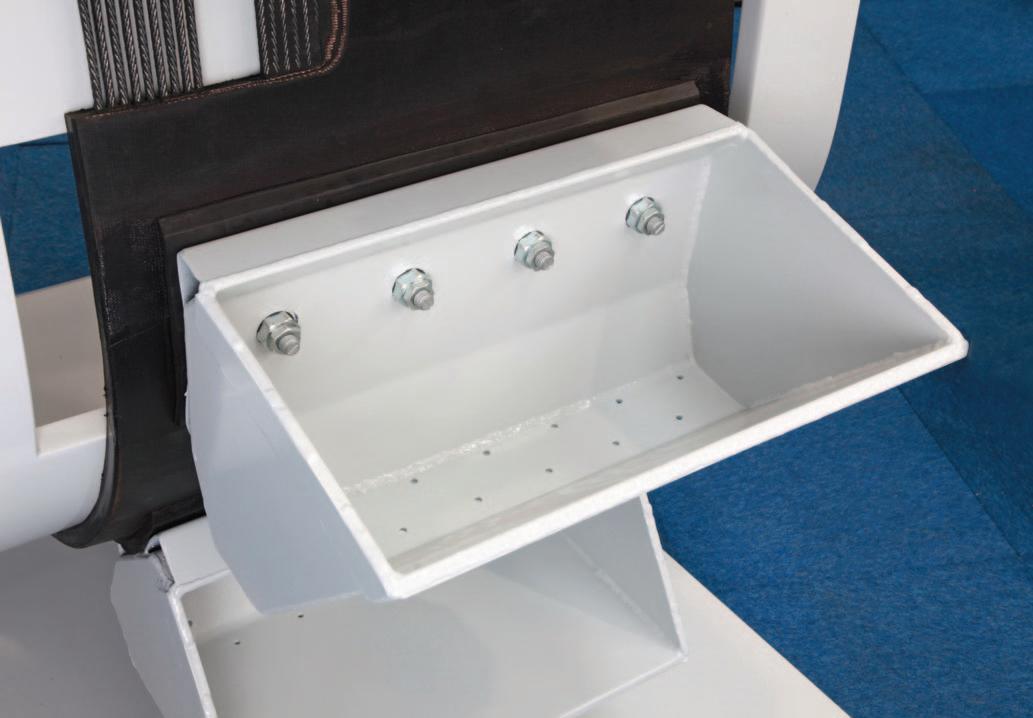
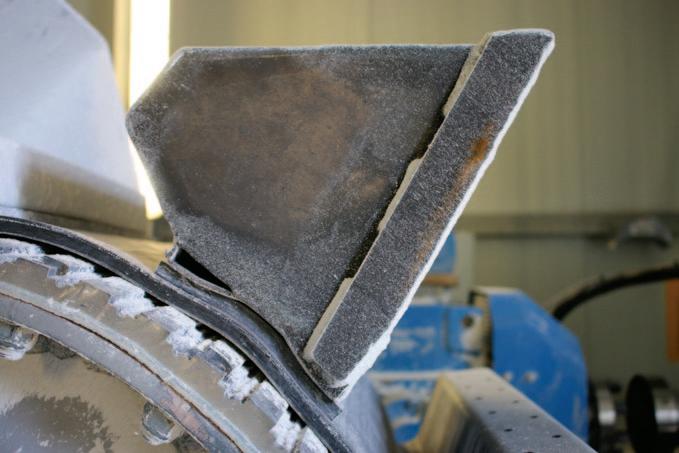
The drive pulleys are equipped with segmented laggings. A steady running of the belt is ensured by the crowned drive pulleys (all photos: BEUMER Group GmbH & Co. KG).
IT DOESN’T ALWAYS HAVE TO BE NEW Outdated technologies often lead to increased maintenance, and that can rapidly become expensive. A cement plant owner faced this problem with his bucket elevators. An analysis carried out by the BEUMER Customer Support team made things clear: it is not necessary to replace the whole systems, but only components. The service experts were able to modernize the bucket elevators and make them more efficient, even if the systems were not from BEUMER.
“Right from the beginning, our three bucket elevators caused problems,” says Frank Baumann, plant manager at a mediumsized cement company based in Erwitte, North Rhine-Westphalia, near Soest, Germany. In 2014, the manufacturer also established a plant in Duisburg. “Here, we produce blast furnace cement, using a central chain bucket elevator as circulation bucket elevator for the vertical mill and two belt bucket elevators for the silo feeding,” describes Baumann. The central chain bucket elevator on the vertical mill was unusually loud right from the beginning and there was also an immense chain vibration of more than 200mm. Although the original supplier made several improve ments, a high level of wear and tear was evident after only a short running time. “We had to service the systems more and more frequently,” says plant manager Baumann. Of course, this was expensive, on the one hand because of the downtimes, and on the other because of the spare parts.
FREQUENT DOWNTIMES, HIGH COSTS Due to the frequent downtimes on the vertical mill circulation bucket elevator, BEUMER Group was contacted in 2018. The system supplier not only supplies bucket elevators and modernizes them if necessary, but also optimizes existing systems of other suppliers. “In cases like this, operators of cement plants are often faced with the question of whether a completely new plant or a possible
No material can penetrate between belt and bucket.
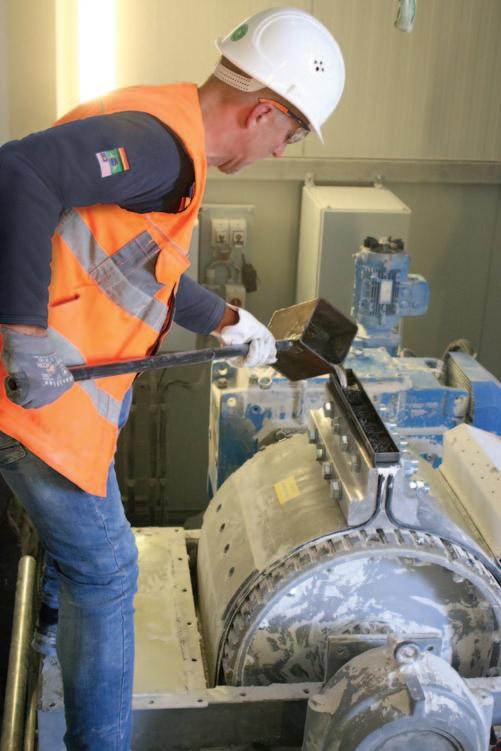
After casting, the junction is cured very quickly. ENGINEERING & EQUIPMENT
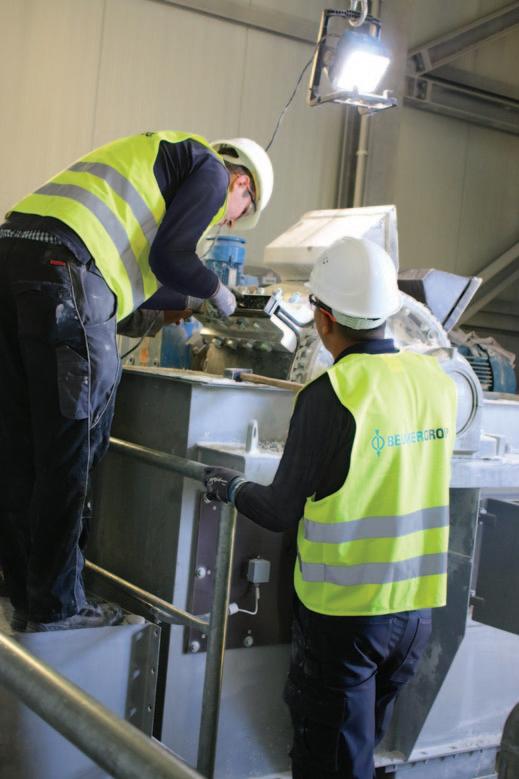
The ends of the steel cords are divided into individual strands in the U-shaped part of the belt clamping connection, twisted and cast with white metal.
conversion would be the more economical and targeted measure,” explains Marina Papenkort, Area Sales Manager in the Customer Support division at BEUMER Group. Because modernization can be worthwhile: “With our customer support, we help our customers to fulfil future performance and technology requirements in a cost-efficient way in the context of modernizations and modifications”, says Papenkort. “Typical challenges of our customers include performance improvements, adaptations to modified process parameters, new materials, optimization of availability and extension of the maintenance cycles, designs easy to maintain as well as reduced noise levels.” In addition, all new developments with regard to Industry 4.0, such as belt monitoring or continuous temperature monitoring, are included in the modifications. BEUMER Group offers everything from one single source, from technical dimensioning to assembly on site. The advantage is to have only one contact and thus to benefit from reduced organizational and co-ordination expenses.
The profitability and especially the availability play a crucial role for customers, because modifications are often an interesting alternative to new constructions. In case of modernization measures, as many components and structures as possible are kept — in many cases also the steel structure. This alone reduces material costs by approximately 25% compared to a new construction. In the case of this company, the bucket elevator head, the chimneys, the drive unit and the bucket elevator boot could be reused. “In addition, the assembly effort is lower, and so the downtime is usually much shorter,” explains Papenkort. This leads to a faster return on investment compared to a new construction.
HEAVY DUTY FOR COARSEGRAINED MATERIAL “We retrofitted the central chain bucket elevator to a high-capacity belt bucket elevator type HD (heavy duty),” reports Papenkort. Belts with wire-free zones, and to which the buckets are fastened, are used for this type of bucket elevators just as with all BEUMER belt bucket elevators. In the case of products from competitors, often the steel cords are cut through when mounting the buckets. Thus the steel cords are no longer covered, which might result in moisture penetration and, as a consequence, lead to corrosion and damaged supporting cords. “That’s not the case with

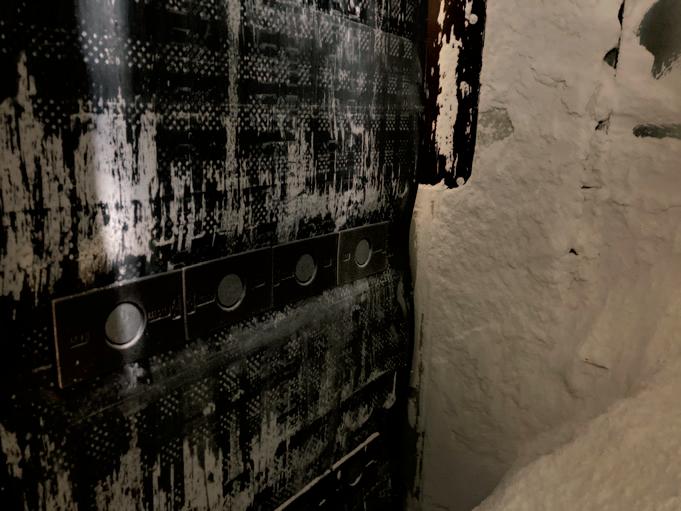
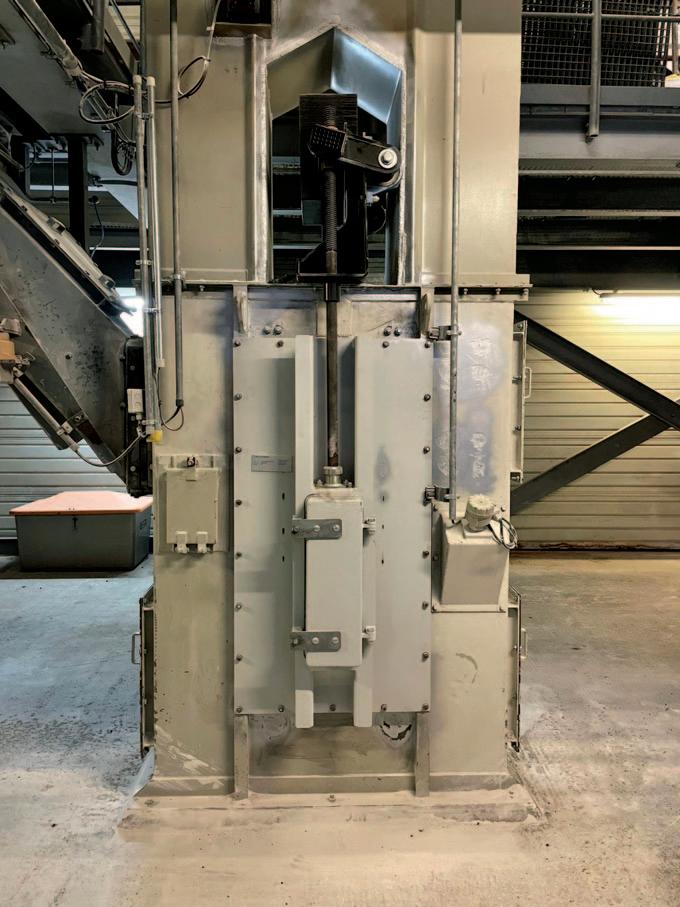
our systems. The tensile strength of the bucket elevator belt is completely kept,” explains Papenkort.
Another important factor is the belt clamping connection: the rubber of the steel cord ends is first removed on all BEUMER steel cord belts. The technicians divide the ends into individual strands in the U-shaped part of the belt clamping connection, twist and cast it with white metal. “Thus, the customer benefits from a huge time advantage,” says Papenkort. “After casting, the junction is completely cured after a very short time and the belt is ready for use”.
FOR STEADY RUNNING OF THE BELT In order to enable the steady running of the belt and to extend the service life in view of the abrasive material, the BEUMER team exchanged the existing segmented laggings of the drive pulley by specially adapted ones equipped with ceramic. These are crowned for a steady straight run. The design, which is easy to maintain, enables to quickly replace the single segments of the segmented lagging through the inspection hatches. Thus, it is no longer necessary to exchange the complete drive pulley. The segmented laggings are rubberized, with linings made of full ceramics or steel. The choice depends on the material conveyed.
The buckets are adapted to the crowned shape of the drive pulley and thus lie flat on, which considerably increases the service life of the belt. Their shape allows for smoother running and therefore less noise generation. Depending on the intended use, the operator receives the buckets in the design that suits him best. They can for example have a rubber bottom or be made of high-quality steel. The proven BEUMER HD technology impresses with a special bucket connection: In order to prevent coarse-grained material from penetrating between bucket and belt, the bucket is provided with an elongated back plate, which can be mounted flush to the bucket elevator belt.
In addition, with the HD technology, the buckets are mounted firmly to the back of the belt with forged segments and screws. “All the screws would have to get lost for a bucket to tear out,” explains Papenkort.
TO KEEP EVERYTHING RUNNING STRAIGHT In order to achieve a permanently correct tensioning of the belt, BEUMER mounted an external parallel take-up device without product contact in Duisburg, which ensures that the take-up pulley is limited to parallel movement. The tension bearing is designed as inner bearing in a completely encapsulated construction. The bearing housings are filled with oil.
“A part of our HD technology is the cage-type foot pulley which is easy to maintain. The bars are hardened due to the abrasive material conveyed and screwed into the cage-type foot pulley to enable a rapid replacement. The take-up pulley is equipped with a double deflection cone, which reliably prevents damage to the belt caused by jammed bulk materials,” explains Papenkort.
SATISFACTION LED TO FOLLOW-UP ORDER “This modification enabled us to increase the availability of our vertical mill circulation bucket elevator and to be more competitive on the long term,” Baumann says happily. “Compared to a new investment, it was possible to reduce our costs and we were operating faster. At the beginning we had to convince ourselves more than once that the retrofitted circulation bucket elevator was in operation, because the noise level had changed drastically and we were not familiar with the smooth running from the previous chain bucket elevator.” The company was so enthusiastic about the retrofitting that it
The parallel takeup device ensures that the take-up pulley is limited to parallel movement. The buckets are mounted with forged segments and screws on the back side of the belt.

With this modernization, the cement manufacturer was able to increase the conveying capacity of the bucket elevators for the cement silo feed. commissioned BEUMER Group to also optimize the other two bucket elevators with regard to the conveying capacity. Also in this case, the operator complained about continuous off-tracking, buckets hitting the shaft casing and difficult maintenance conditions. “In addition, we wanted to further increase the throughput of the mill and were therefore interested in greater flexibility in terms of the conveying capacity of the bucket elevators,” explains Baumann. In 2020, the Customer Support of the system supplier also solved this problem. “We are completely satisfied,” states Baumann. “In the course of the retrofitting, we could also reduce the energy consumption of the bucket elevators.” To avoid caking, the take-up pulley is designed as cage-type foot pulley and is provided with a double deflection cone. For this order, the screwed & hardened version of the cage-type foot pulley has been used.
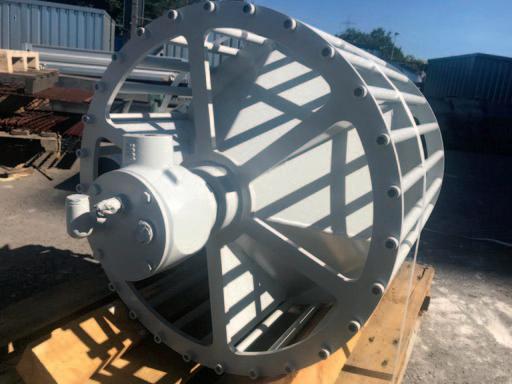
ABOUT BEUMER GROUP
BEUMER Group is an international expert in the manufacture of intralogistics systems for conveying, loading, palletizing, packaging, sortation, and distribution. With 4,500 employees worldwide, BEUMER Group has annual sales of about €950 million. BEUMER Group and its group companies and sales agencies provide their customers with high-quality system solutions and an extensive customer support network around the globe and across a wide range of industries, including bulk materials and piece goods, food/non-food, construction, mail order, post, and airport baggage handling.
Proven technology by an innovative and creative shipbuilder
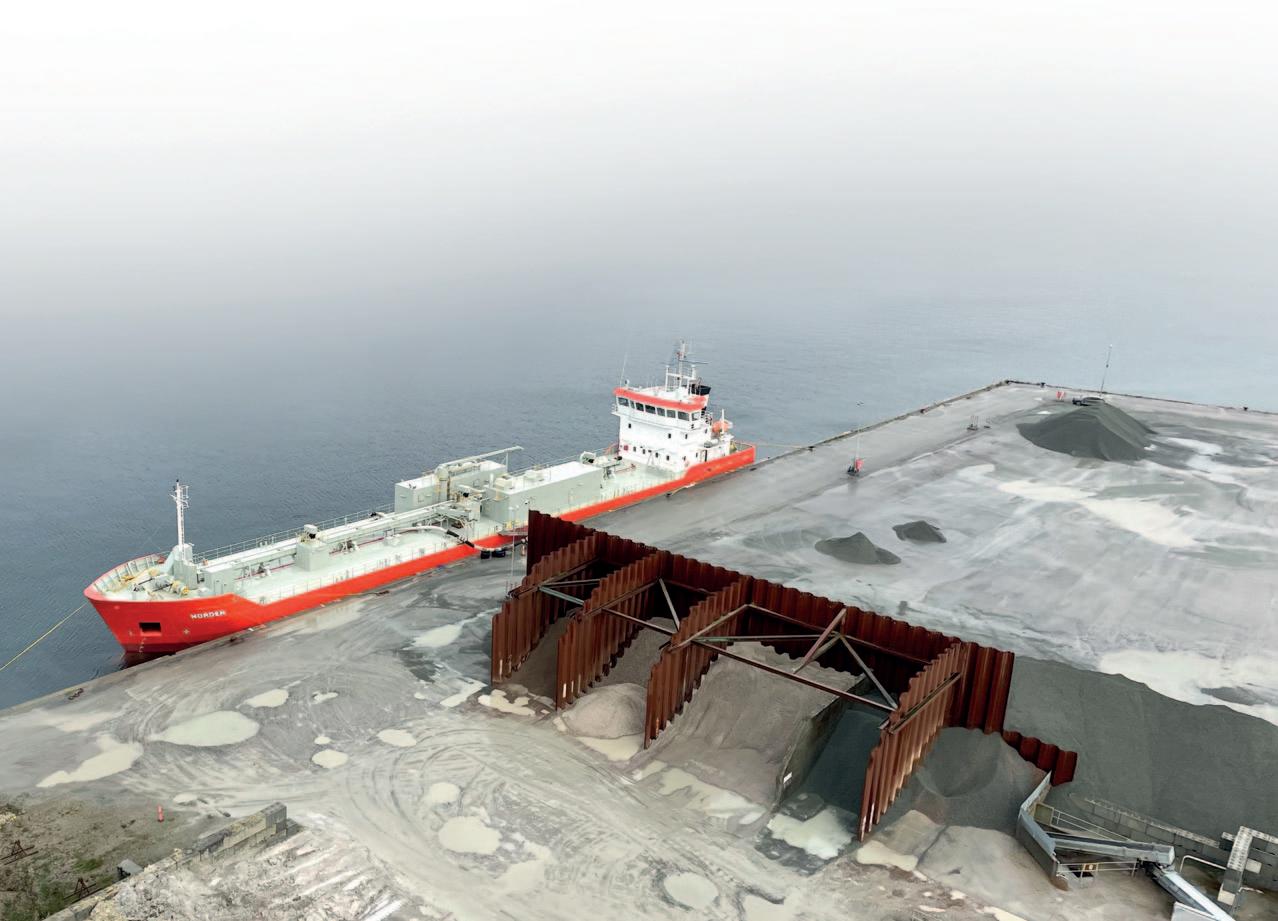
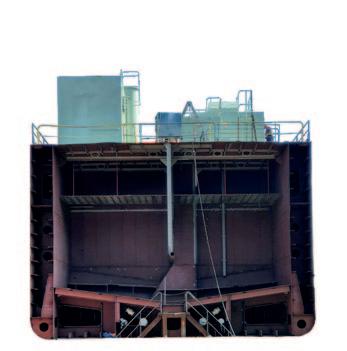
Cement carriers
Optimized ship design for sustainable and safe navigation and efficient cargo hold design for cost-effective cargo handling and maximum cargo intake.
Fast and reliable handling of cement, including transport and storage, is a topic of great interest today. Due to the Covid 19 pandemic, availability was affected by disrupted supply chains and this situation was further aggravated by the war in Ukraine.
Conductix-Wampfler’s expertise in providing robust power and data transmission solutions for all mobile machinery and equipment in the cement industry, is based on many years of working on challenging projects involving material handling at various levels of the supply chain.
Whether handling raw materials or finished products or storage, ConductixWampfler provides reliable, high-quality service that helps customers improve productivity, optimize operations, increase

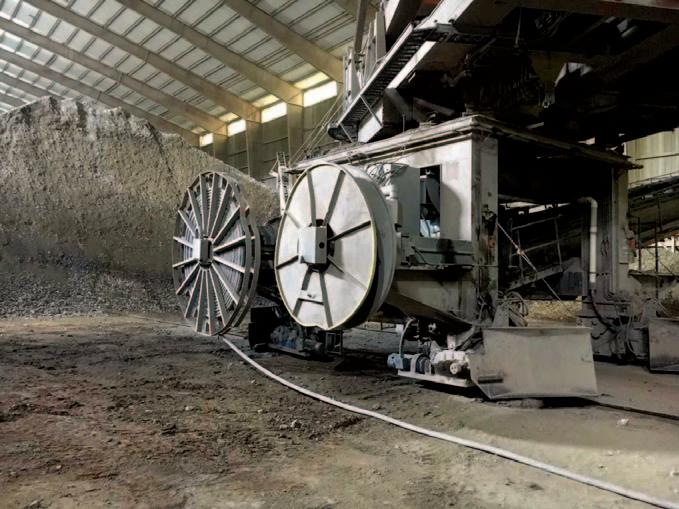

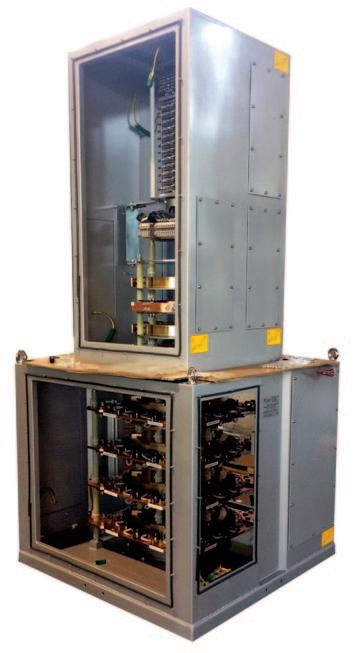
safety, and reduce energy consumption, and comply with the most demanding environmental regulations.
As a full-range supplier ConductixWampfler is an ideal partner for customized solutions for power supply, data transmission and controls that are modularly designed, based on standard components, and comply with nearly all international standards and protocols.
Conductix-Wampfler’s portfolio ranges from spring or motor driven cable and hose reels, cable festoon systems to slip ring assemblies and rotary joints to conductor rail systems, energy storage solutions and safety radio remote controls. The company’s global production footprint and strong sales network including comprehensive, tailor-made aftersales services complete the offer.
Global OEMs such as thyssenkrupp Industrial Solutions AG, AUMUND Group, FLSmidth or Beumer (just to name a few) regularly rely on the company’s support due to local contacts and the extensive technical support.
Motorized Cable Reels with the proven magnetic coupler technology (MAG drive) are often a perfect fit for end-users. It is a modular system developed to be able to design the most technically suitable product for each customer requirement. It is based on a proprietary magnetic coupling technology that uses wear-free permanent magnets that do not require lubrication and act like a torque limiter that protects the cables during operation, thus extending their service life.
The beauty of such a system is that it can be adapted for all harsh environmental conditions: at the seaside, in dusty environments, in very low (and high) ambient temperatures of –40°C (+70°C) with easy maintenance and a reduced set of spare parts.
Slip ring assemblies used on circular storages as well as on shiploaders (or unloaders) have been subjected to rigorous testing and a wide variety of conditions during their development and are extremely efficient thanks to the knowledge and data gathered over the years.
Spring-driven cable reels for overhead reclaimer systems are a further evolution in the development of solutions for cement storage applications. Manufactured in robust all-steel construction with effective corrosion protection and equipped with lifetime sealed bearings and high-performance textured steel springs. Large cement companies such as Lafarge, Holcim, CNBM or CEMEX attach great importance to reliability, availability and innovations and require customized solutions. This is the reason why Conductix-Wampfler is highly appreciated. Qualified employees can design a suitable solution for every customer requirement, which is manufactured and delivered as quickly as possible in specialized locations around the globe and, if required, installed, and commissioned on site by experienced specialists. ConductixWampfler solutions keep customers’ vital business moving.
A tough design for really demanding applications

ENGINEERING & EQUIPMENT Cement plant solves belt drift using highly responsive tracking equipment

Ash Grove Cement plant in Chanute, KS (USA) (© 2022 Ash Grove Cement).
The belt on a conveyor can either gradually inch its way out of alignment or suddenly –without warning – lurch sideways and get shredded against the stringer, writes Cory Goldbeck, Territory Manager, Martin Engineering. In some cases, the belt will realign itself or activate a stop switch, shutting the entire system down. The worst outcome is when the contact between the belt and the stringer causes enough friction to ignite the cargo or belt and convey a fire quickly through the facility. Either way, the general result of belt mistracking is hazardous and expensive.
The Ash Grove Cement plant in Chanute, Kansas has received dozens of safety awards since the facility’s modernization in 2001, and when operators experienced several frustrating involuntary shutdowns and rising costs from drifting belts, prevention-minded managers sought an effective solution.
“Although there was one belt that had a particular issue with tripping the emergency stop switch, mistracking was a problem on several belts from the limestone quarry all the way to the raw mill,” said Danny Wolken, Maintenance Planner at Ash Grove Chanute. “We have different materials converging into a single area, and disruption to the flow affects the productivity of the whole system.”
A LONG HISTORY The Chanute plant has been in operation since 1908, producing high-quality Portland cement. After several modernizations through the decades, the plant now has a production capacity of 1,628,000 tonnes of clinker per year. It also carries the distinction of being the first cement kiln in the U.S. to utilize 20–25% alternative fuels on an annual basis, reducing the use of fossil fuels.
Various materials from the storage
With the discharge so close to the belt entrance, the tracker had to be installed immediately outside (© 2022 Ash Grove Cement).

Figure 1 – Camber can happen in the manufacturing process, and belts should be inspected prior to installation (© 2022 Martin Engineering).

dome are carried approximately 1,150 feet on eight belts to the raw mill for mixing and insertion into the preheater for calcining in the kiln. With an average belt width of 36 inches (914mm) running at ≈375fpm [feet per minute] (1.9mps [metres per second]), the system transports ~500 tph (453mtph [metric tonnes per hour]) of material. The outdoor conveyors are covered to protect cargo from the variable Kansas weather patterns.
OBSTACLES TO EFFICIENCY The belt carrying limestone was of particular concern. After passing through the crusher, four inch-minus (<100mm) aggregate would be loaded onto the conveyor. After leaving the settling zone, the belt had a tendency to crawl up on the side of the idlers. This would disrupt the centred distribution of the material on the belt, causing smaller aggregate to spill along the length of the system until the belt drifted far enough to activate the stop switch, which shut down the conveyor.
Stop switches are sensors that are installed at intervals along the length of the conveyor on both sides of the belt near the outer limit of a safe belt path. The wandering belt pushes a lever arm and activates a switch, which either sets off an alarm or, in Ash Grove’s case, interrupts the conveyor’s power circuit, stopping the system. Costly downtime and lost production make these devices less of a solution to the misalignment and more of an indicator of a severe problem.
The shutdown would have a ripple effect throughout the plant. During the unscheduled downtime, several maintenance workers would drop what they were doing, rush to the area, go through the lock-out/tag-out/blockout/test-out procedure and then manually realign the belt. “This one conveyor hit the stop switch 26 times last year, for a total of 17 hours of downtime,” Wolken explained. “Although the limestone conveyor had the worst problems, issues with tracking stretched across all eight conveyors. That adds up, since we run ten hours a day, seven days a week.”
Along with excessive unscheduled downtime, the belt on the limestone

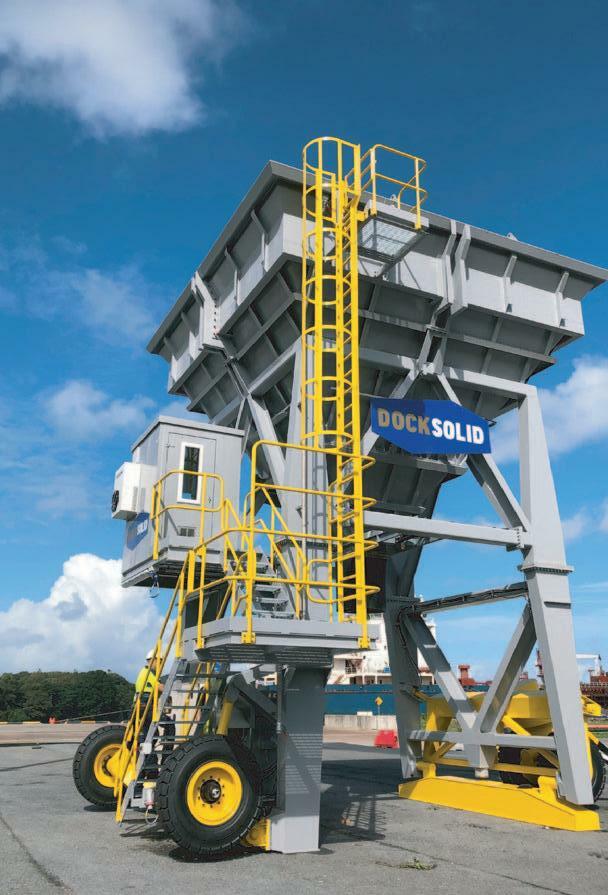
Engineering
BULK HANDLING EQUIPMENT www.buttimer.com
Ireland UK Poland
Buttimer Engineering Cahir Business Park Cahir Co. Tipperary E21 Ireland
BESPOKE BULK PORT EQUIPMENT. FULL RANGE OF HOPPERS AVAILABLE www.docksolid.com
Our DOCKSOLID® hoppers are designed and fabricated in Cahir, Co. Tipperary and are sold under the Docksolid Brand in Ireland, United Kingdom and Poland and branded as Manta in the rest of the world by our partners Terex Prostack www.terex.com/prostack
Ship unloaders
Road mobile ship unloaders
Storage & reclaim
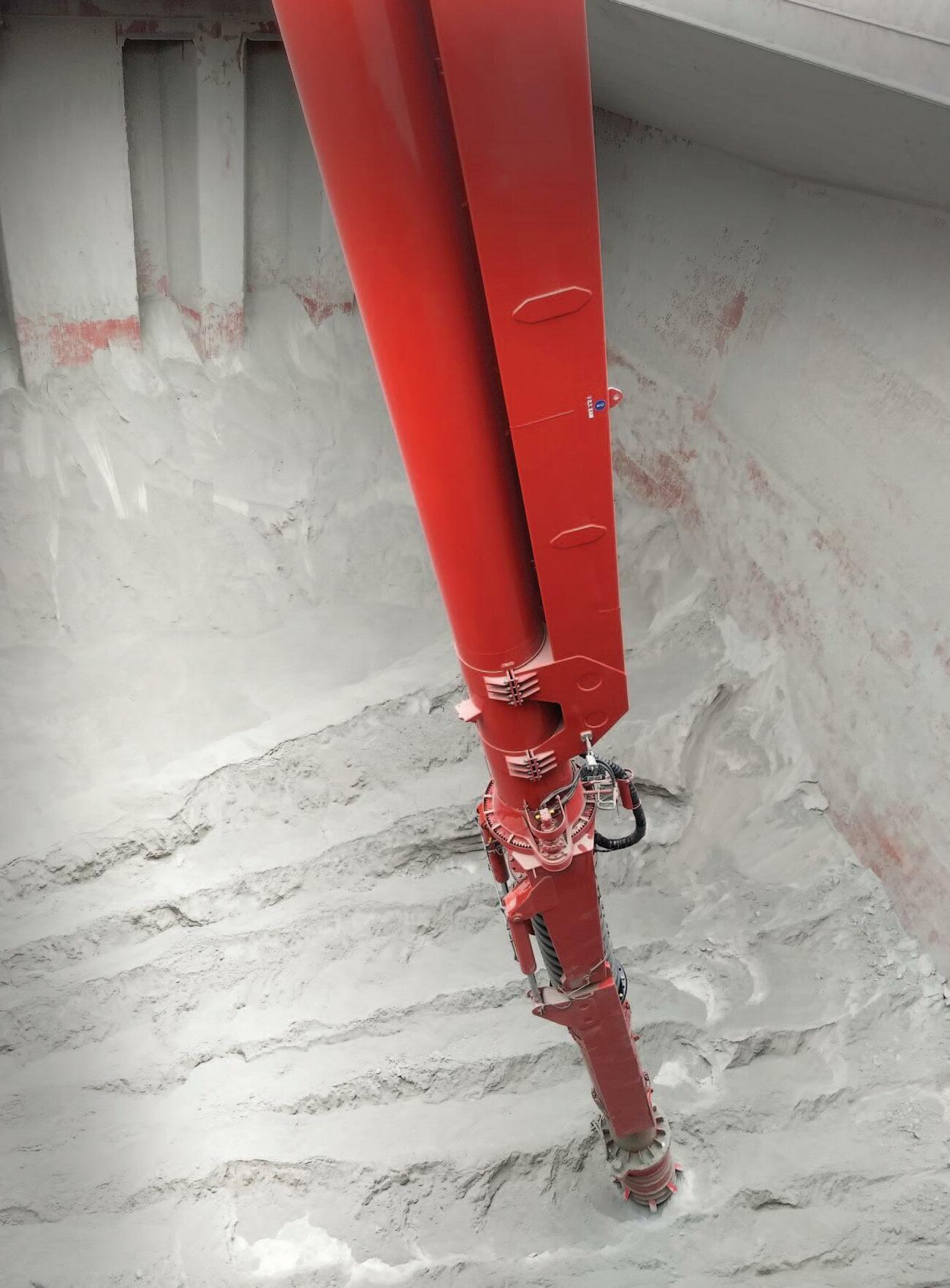
Convey units
Truck loading
Ship loaders
The answer to your bulk handling questions
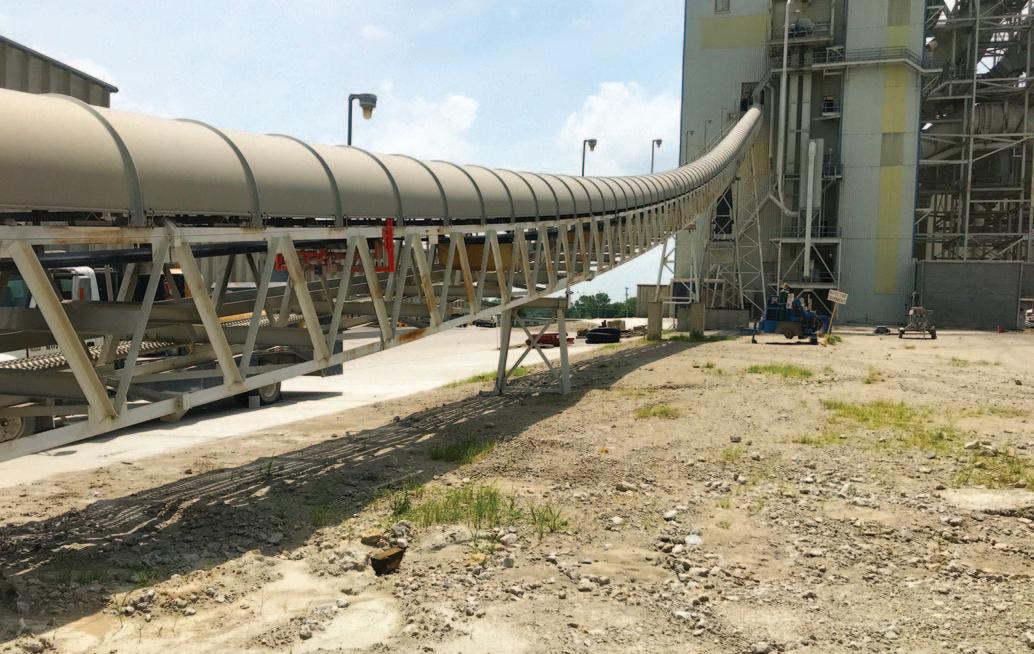
conveyor began to fray from contact with the structural components of the system. Having only been replaced six months earlier, labour, downtime and equipment expense makes belting one of the costliest components of the system. Incidental contact drastically reduces the belt life and can degrade the splice. The belt damage likely contributed to further misalignment and spillage.
Adding to the problem, every 45 days or so several workers dedicated about 50 hours of time to clean under and around the structural supports of the eight systems. This helped mitigate accumulation that could potentially encapsulate the belt and kept the area safe.
“The regular cleaning and the stop switch helped protect workers and saved the system from more serious damage,” Wolken said. “But mistracking was also impacting productivity and the cost of operation, so we needed an alternative.”
SYSTEM DIAGNOSIS With a long-standing relationship of providing quality equipment and service, Martin Engineering was asked to inspect the systems and offer solutions. Technicians walked the belts individually and took detailed notes on the unique causes of mistracking for each system.
“We were already extremely familiar with these conveyor systems, since we also service and install belt cleaners at the plant through our Mr. Blade program,” said Jacob Taylor, Service Technician for Martin Engineering. “We had an idea of where and how the conveyors were having tracking problems. Walking the belt and filling out a detailed checklist helped solidify those assumptions and revealed some specific details we might have missed, so it pays to be thorough.”
First, technicians found that when the belt drifted, cargo shifted downward to one side of the belt, causing it to mistrack further. The material lost surface area and spilled over the edge of the belt. The spillage dropped along the entire length of the system, causing product loss, creating potential workplace safety issues and requiring excessive cleanup.
Second, technicians suspected some potential manufacturing flaws of the belt attached to the limestone conveyor. If the belt isn’t precisely engineered or properly stored, it can bow or camber. [Fig.1] This might have contributed to the tracking and belt damage issues.
Third, the extreme temperatures and high winds common to Kansas can impact belt alignment. Ash Grove enclosed the conveyors specifically for shelter against the prevailing wind, which helped minimize dust emissions and frozen idlers, but changing temperatures can still cause components to expand and contract, with changes in friction and functionality.
Fourth, belt manufacturing issues may have also contributed to the ‘cupping’ observed by the technicians. Commonly seen on the return side of the belt, cupping is when the belt curls on either edge, reducing the surface contact and tension with rollers, causing it to drift. A wider drift area means the belt can be wildly offcourse by the time it encounters tracking equipment, making the force and angle of
The Martin® Tracker™ for the carrying side adjusts to fit the system’s trough angle (© 2022 Martin Engineering). www.drycargomag.com
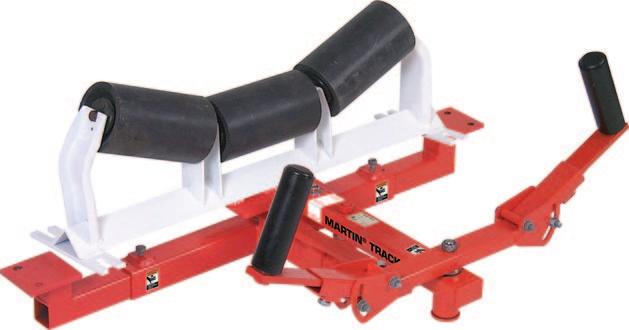
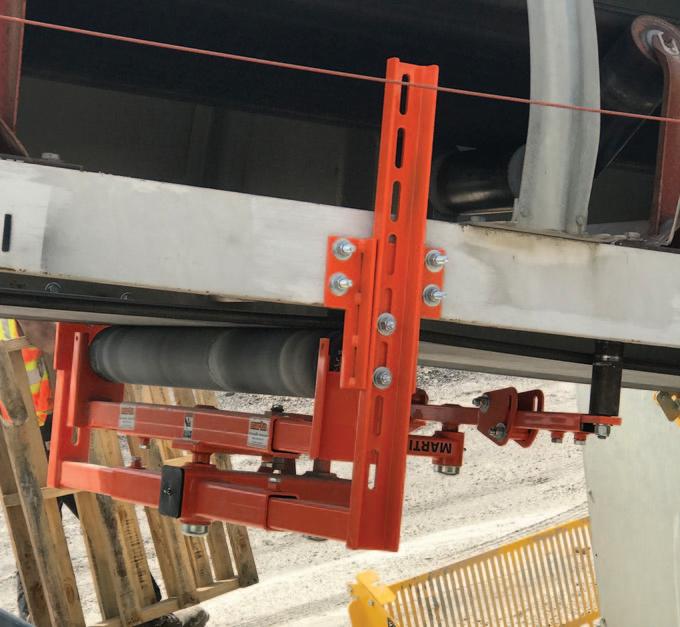

the belt nearly impossible to correct.
Fifth, the existing tracking systems were found to be inadequate. They delivered only minor corrections to discourage belt damage and quite often broke, requiring additional maintenance. Technicians realized that the belt’s return run also needed a solution for the whole system to remain in line.
PREVENTATIVE SOLUTIONS Martin technicians pinpointed the problem areas on each of the conveyor belts and offered an economical solution that utilized modern belt tracking technology where it was needed. “Across the eight conveyors, we recommended installing 28 Martin Trackers,” Taylor said. “Many of the units control the belt return, but there are also upper trackers strategically placed in problem areas.”
Utilizing innovative multiple-pivot, torque-multiplying technology, the Martin® Tracker™ has two sensing arms that extend out to either side of the conveyor with rollers at the tip, which smoothly ride the edges of the belt. The sensing arms detect slight variations in alignment and use the force of the belt to immediately pivot the position of the troughed idlers against the misalignment with equal force, thus returning the belt to its intended path. [Fig.2]
With its sensitivity to misalignment, less opposing force is needed for the equipment to realign the belt. Early detection with a reduced range of drift before correction makes the belt run more efficiently, mitigates spillage and results in longer equipment life.
The lower trackers have a flat roller with a polyurethane coating. Raised slightly above the belt plane, the roller acts partly as support with just enough downward force from the belt for the polyurethane to grip the belt and return it into alignment.
INSTALLATION The installation was performed by two Martin technicians during scheduled downtime. Since edges of the belt on the limestone conveyor had serious damage caused by the mistracking, another team replaced the belt as well. The new belt was thoroughly inspected to ensure that it did not contribute to tracking issues.
Trackers were installed with minimal impact on structural supports except for a few bolt holes. The idler angle of the upper trackers matched the trough angle of the system to ensure a smooth belt path, and the torsion arms were properly aligned with the belt edge. The working grade (standard-duty, heavy-duty or extra heavy duty) of the trackers depended on the thickness and weight of the specific belt. The heavier the belt, the more force is put on the torsion arms and the pivot support, requiring proportional reinforcement. If the unit is not properly matched to the belt weight, it may not be able to adjust quickly enough.
Three critical areas on the conveyor required tracking: the exit of the settling zone, the entrance to the feed mill and along the return path. A lower tracker placed along the belt path and near the loading zone ensures the belt is aligned as it hits the tail pulley to promote centered loading. An upper troughed tracker at the settling zone exit reinforces a straight belt path as it travels the length of the system.
One of the most difficult installations involved the trackers placed at the entrance to the feed mill. Raised off the ground in the weighing tower, the technicians required some extra safety equipment and time to install those units. This was an important step, because a centered belt entering the head pulley ensures that the belt cleaner blade adequately dislodges adhered material from the belt. Specifically positioned to clean the center of the belt where carryback resides, belt drift may cause some of the material to avoid the blade, dropping spillage and fouling rollers along the return path.
Figure 2: a tracker pivots against the mistracking, using the force and weight of the belt to redirect it. The Martin Tracker has minimal impact on the stringer structure (© 2022 Martin Engineering).

The return side Martin Tracker lifts the belt slightly for appropriate contact (© 2022 Martin Engineering).
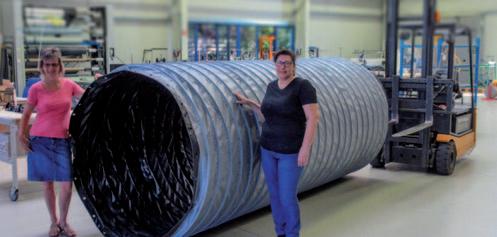
STAYING CENTRED The installation of a new belt helped with testing the tracking system to ensure that the trackers are addressing cargo and transport issues and not belt flaws such as camber or cupping. Initial testing revealed positive results, with the belts remaining centered along the entire length of the system.
“Every time we replace a belt it costs approximately $35,000 in equipment and labour, not counting the loss of production,” Wolken said. “Replacing the belt is not a sustainable solution, so seeing the trackers keep the belt in line was a positive result.”
The belt remained centered from pulley to pulley, drastically reducing the amount of spillage. As with any bulk handling, cleanup is always a factor, but operators pointed out that the time and labour for cleanup were significantly reduced. This improved efficiency and lowered the cost of operation.
Observation over time revealed that the belt remained aligned through changes in weather, and none of the belts have come in contact with the emergency stop switches since the installation. This has resulted in a significant reduction in unscheduled downtime, improved efficiency and eliminated the need for maintenance staff to interrupt their work to get the system running again.
“We trusted that Martin Engineering would be able to offer an affordable solution that could solve our problem, and they really came through,” Wolken concluded. “We like the trackers, so we’re looking into installing them on other systems. They have definitely paid for themselves.”
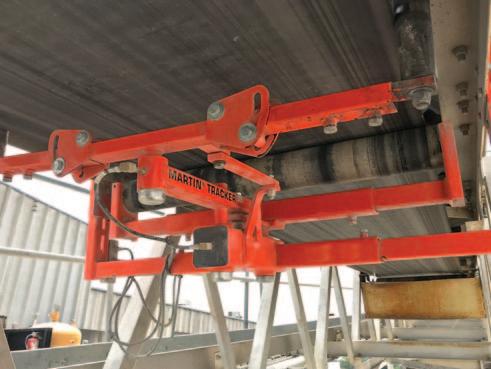
ABOUT MARTIN ENGINEERING Martin Engineering is a global innovator in the bulk material handling industry, developing new solutions to common problems and participating in industry organizations to improve safety and productivity. The company’s series of Foundations books is an internationally recognized resource for safety, maintenance and operations training — with more than 20,000 print copies in circulation around the world. The entire 500+ page volumes can also be downloaded as free PDFs from the Martin web site. Martin Engineering products, sales, service and training are available from 19 factory-owned facilities worldwide, with wholly-owned business units in Australia, Brazil, Chile, China, Colombia, France, Germany, India, Indonesia, Italy, Japan, Mexico, Peru, Spain, South Africa, Turkey, the USA and UK. The firm employs more than 1,000 people, approximately 400 of whom hold advanced degrees.
VERLADESYSTEME FÜR SCHÜTTGÜTER
We make sure that nothing gets lost!
For over 50 years, our loading systems for bulk materials have been synonymous around the world with long-lasting and reliable technology.
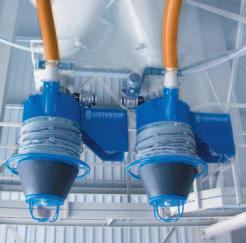
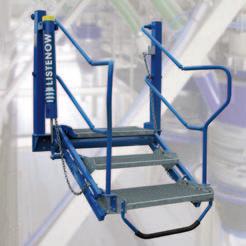
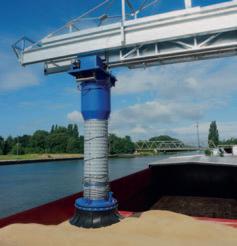
Replacement loading hoses +49 7152 50900
› Bulk loading systems for open and closed loading › Loading with no segregation e.g. with FLOW-stop technology › Dust-free loading › High quality loading hoses e.g. made in wear-resistant PU-flex › Positioning System LIS-pos › First-class service:
Start-up and installation
Revision and repair services
System maintenance, modernisation and upgrading › more informationen at www.listenow.com
LISTENOW GmbH & Co
Dieselstrasse 21 71277 Rutesheim / Germany +49 7152 50900 listenow@listenow.com www.listenow.com
ENGINEERING & EQUIPMENT Cement conveyor belt retrofit with high-performance rollers from Rulmeca
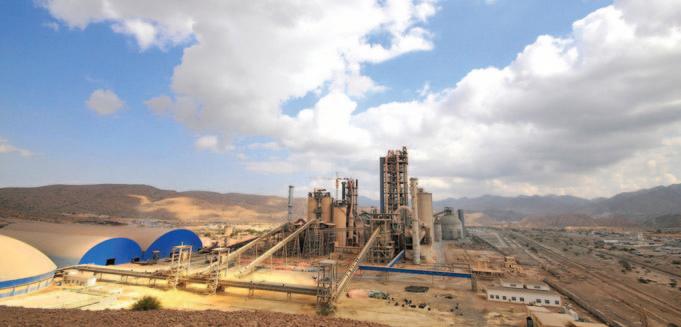
66% INCREASE IN PERFORMANCE THANKS TO BETTER-RUNNING ROLLERS The Oman Cement Company (OCC) SAOG, Muscat, Oman, has upgraded the performance of its 30-year-old conveyor, which transports hot cement powder from the cement mill to the silo, from 150tph (tonnes per hour) to 250tph, write Jens Hagenau, Product Manager and Export Manager (Bulk Material) at Rulmeca in Aschersleben, Germany, and Anil P George, Business Head, UAE – Synergy International FZE. The implementation of this 66% increase in capacity via a retrofit of the existing conveyor (with a horizontal length of 255m and a vertical stroke of almost 44m) was enabled with the use of highperformance rollers from Rulmeca.
The Oman Cement Company symbolizes Oman’s quest for selfsufficiency in its core industries. This company, with ISO 9001 certification, has Oman Cement Company (OCC) conveys hot cement powder with bulk material handling technology from Rulmeca.
The new OCC cement conveyor is a retrofit, using high quality conveyor components from Rulmeca to significantly increase throughput with the existing basic design.
become the backbone of the construction industry in Oman ever since the cement plant was established in 1983. As such, it plays a key role in the development of the country’s infrastructure and provides the necessary resources to support the nation’s self-sufficiency efforts. This has been successfully achieved. The plant is continuously increasing its production capacity, and it currently produces 2.4mt (million metric tonnes) of cement a year. All the raw materials required for its production are indigenous. The limestone deposit, additives, quartzophylites and ferrogenous quartzophylites can be found near the site of the plant. Gypsum, which is
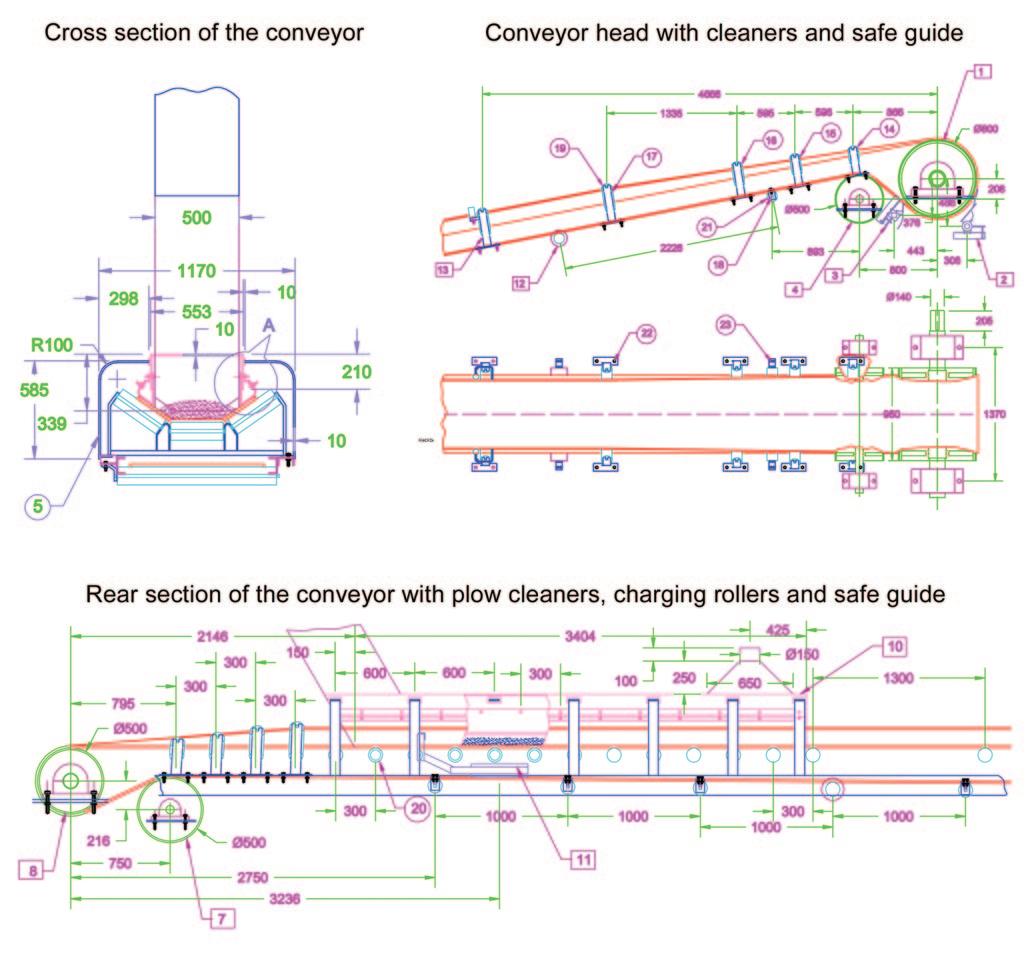
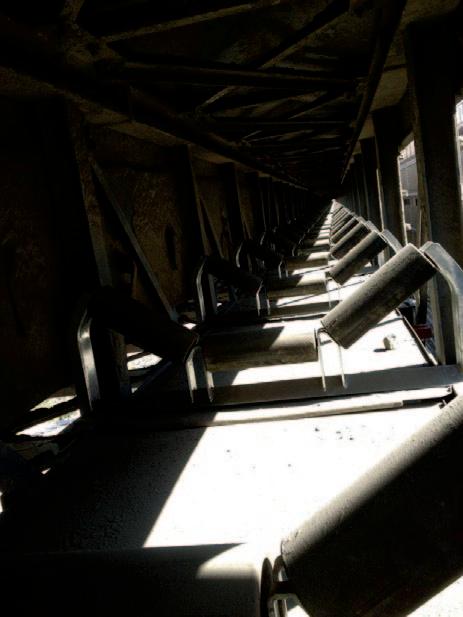

used to slow down the cement setting, is extracted from the mines at Ghaba in Wilayat Adam. Three kilns and four cement grinding mills allow for the flexible production of various types of cement.
As part of increasing the output of the cement mill, the conveying technology used in it (both upstream and downstream) has also had to cope with higher throughput. Some throughput optimization can be achieved with the utilization of existing performance reserves of existing conveyor technology, simply by making the belt run faster. However, in the case of the conveyor responsible for transporting the hot cement powder to the downstream silos, this buffer was no longer sufficient. Considerably more throughput capacity needed to be achieved. Yes, everything could have been torn down, with the construction of a new conveyor. However, with such large conveyors, one tries to preserve the basic frame with its supporting structures, seeing as how its implementation required such high investments. The challenge is therefore to increase throughput via a retrofit at minimum investment cost.
The engineering, procurement, and construction (EPC) specialist Synergy International FZE was commissioned with the concept for the retrofit. Synergy International FZE has been based in the Ras Al å economic hub in the United Arab Emirates since 2005, and has more than 15 years of experience in the markets of the Middle East and North Africa (MENA) as well as in Europe and India. The company specializes in the fields of mechanical power transmission and bulk materials handling (e.g. belt conveyors, industrial chains, gearboxes, fluid coupling systems), as
well as wear management In dusty environments such as the OCC solutions and environmental cement conveyor, the quality of a conveyor solutions (such as dust collection roller has a significant impact on the total cost systems), ball mill optimization, of ownership. steel mill optimization, automated flow control systems, plant assembly, and commissioning. It is thus an ideal partner for OCC. To increase throughput via a retrofit, Synergy International FZE had to use all possible measures to ensure a higher throughput with the existing basic design. As part of this, the conveyor belt was widened by 23% (from 650mm to 800mm). The belt running speed was increased from 1m/s to 1.34m/s (i.e. +34%), and this required rollers which were significantly more resilient. The drive drum was increased from 500mm in diameter to 800mm, to increase grip. As part of this, the power of the drive motor (with fluid coupling and gearbox) was also increased from the existing 55kW to 90kW. Other important elements include Rulmeca’s high-performance idlers,
The technical differences between Rulmeca’s rollers and the competition’s rollers – which easily get hot – in detail.
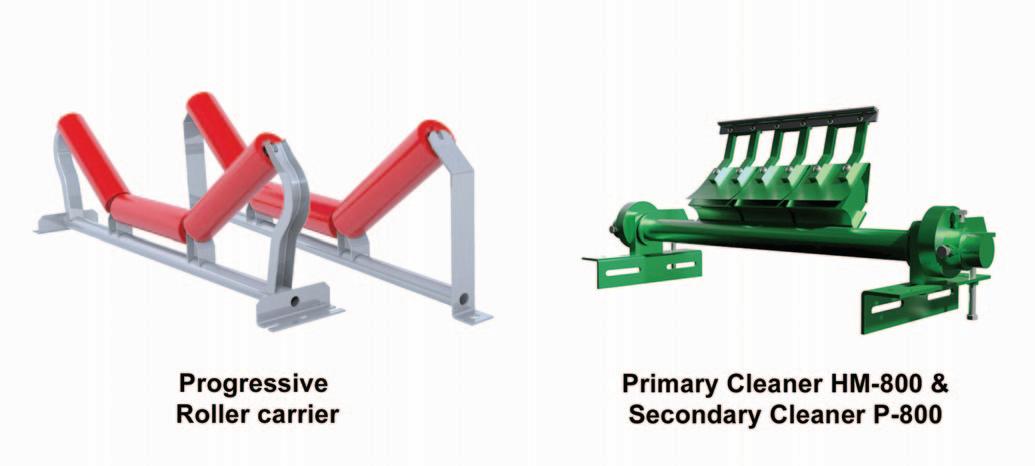
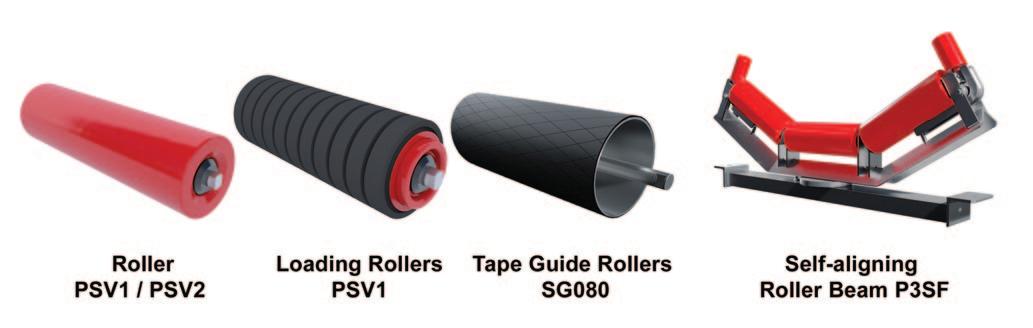
which are crucial for reliable long-term operation of such large conveyors with increased throughput. Compared to simple rollers of inferior quality, they run much more smoothly, and this reduces thermal stress. In addition, they also contribute significantly to lowering overall ownership costs. This is because they have a much longer service life than simple lower-quality rollers, and they also ensure the high reliability of the entire system due to their lower failure rate.
These quality products are manufactured from precision-turned components. Especially hardened steels and other alloys ensure that the conveyor belt rollers function optimally over a long period of time and under the toughest conditions. Various protective measures for the bearings and minimal concentricity tolerances are paramount for the longevity of the bulk material conveyor rollers. Rulmeca achieves maximum precision by balancing each individual roller. It is understandable that this has its price. This investment in quality is all the more worthwhile given the higher speed and greater length of the belt.
However, large conveyors such as OCC’s are not equipped with a single type of idler. Rather, what is required is a very wide variety of components which must be precisely matched to the particular conveying task. Synergy International FZE chose the following components from Rulmeca’s bulk material transportation belt roller range in the design of the OCC conveyor. v PSV1 series rollers (20F, 108N, 323) with a pitch of 1.3m are used on the carrying side. PSV2 series rollers (25F, 108N, 958) with a 3m pitch are used on the return side. Both product series are specially designed for heavyduty continuous operation under high workloads and are characterized by smooth running and minimal maintenance requirements. The rollers of the PSV2 series are designed for higher loads. For better damping of the belt at the
v
v
v loading point, so-called loading rollers (PSV1,20F,63/108NA,323) have also been fitted. These shock-absorbing rollers are fitted with rings designed to absorb the impulse generated by the impact of the material on the belt. On the return side, tape guide rollers of model SG080-30-800-958 are now positioned at three strategic locations. They serve to correct possible belt skew in the return direction and are characterized by the fact that they can centre themselves. On the carrying side, self-centralizing troughing sets with a braking effect (P3SF/70 F14 108 H155) were also applied every 25m: in the event that the belt is misaligned, the selfcentralizing rotation of the troughing sets guides the belt back to the centre.
In addition to these moving parts, Synergy International FZE has also used Rulmeca conveyor roller accessories, thus ensuring the provision of virtually all components from a single source: v A3P1 series transoms (5A-F14-108
H155 Z) are used for smooth belt transition from 10 to 20 and from 30 to 35 degrees of trough angle. v SPT series supports (1478 H70 Z) are used on the return side. v A primary cleaner (HM-800) and a secondary cleaner (P-800) achieve almost 100% cleaning efficiency at the conveyor’s head. A plough cleaner (VLP-800) is also used for rear cleaning.
The retrofit design and component selection was carried out with the use of software by the Australian company Helix Technologies. The modelling was done using SOLID Works (USA) and AutoCAD. Structural analysis is the main tool for ensuring that a structure can withstand the various types of forces that it will be exposed to during its normal operation — this Rulmeca managed with the German software Dulbal. The feed chute has a wear-resistant lining for a longer service life — this was also modelled using Helix software. The project was wholly managed using MS Project. Rulmeca provided corresponding CAD data for its entire range. This allowed Synergy International FZE to provide OCC with a complete package in which all components in use were comprehensively coordinated with each other. Rulmeca always co-operates with local partners on such conveyor technology tasks, so that the end user can be provided with the most comprehensive support possible during the development process and, as a result, may also be able to take care of maintenance tasks quickly and efficiently (should these be necessary at all): Rulmeca’s conveyor belt rollers are designed for maintenance-free operation of at least 30,000 hours. Incidentally, the challenge in the design of the feed chute was to optimize it so that it could not overflow — this was a problem with the previous conveyor in particular — but this bottleneck is now a thing of the past.
ABOUT RULMECA RULMECA GERMANY GmbH is part of the RULMECA Group based in Almè/Italy, which provides materials handling movement technology worldwide. Rulmeca Germany GmbH produces idlers, motorized pulleys, and belt pulleys which meet the highest demands and every application common with unit load and bulk material handling technology, at an ISO-certified location in Aschersleben, Germany, and employs more than 200 people. RULMECA cooperates worldwide with leading equipment manufacturers, development offices, and end users. In addition to the production of conveyor technology components, Rulmeca also offers its customers the service of calculation of conveyor belt elements of complex plants.
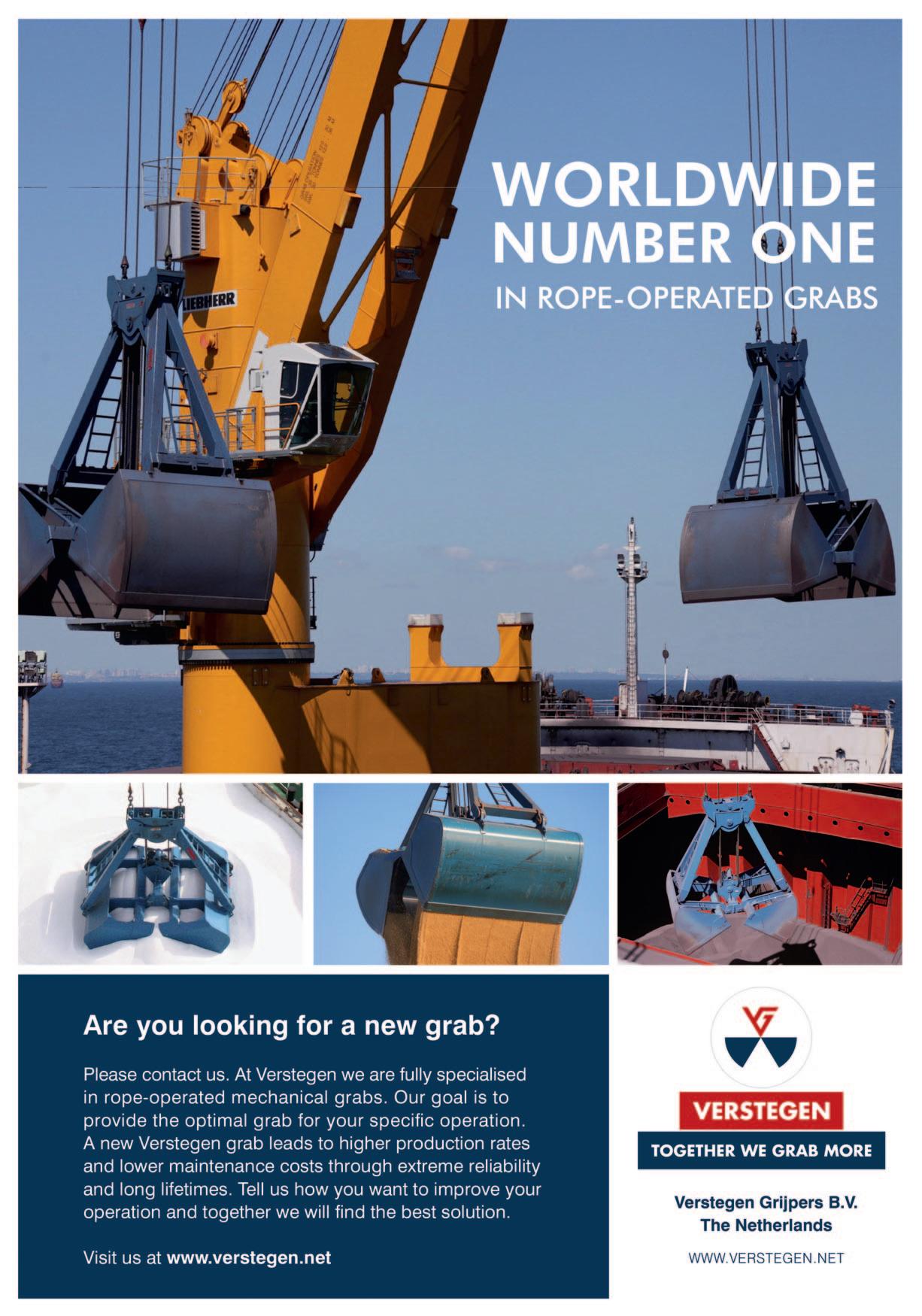

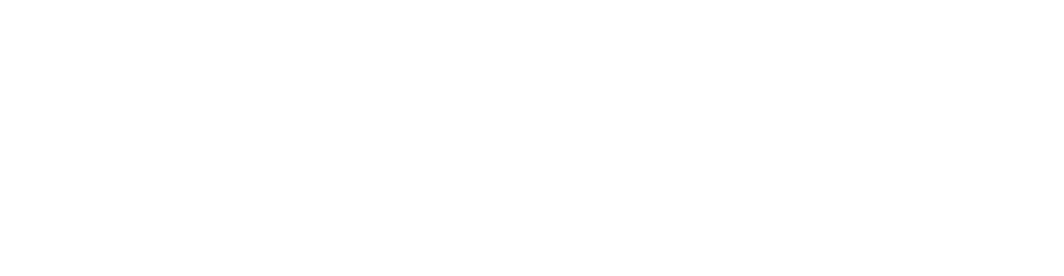
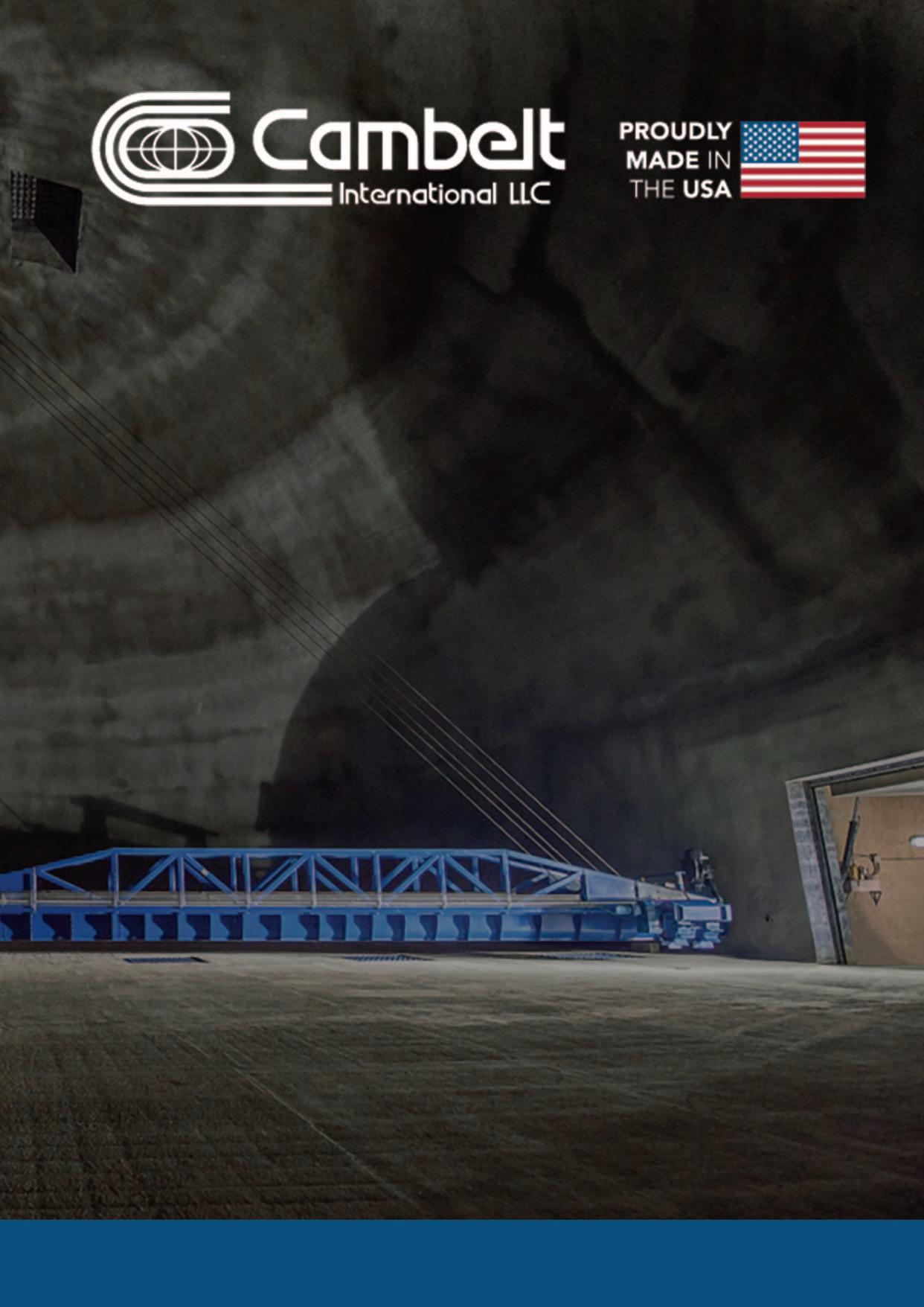

ENGINEERING & EQUIPMENT Sustainability in the bag — high-quality cement bags from Starlinger
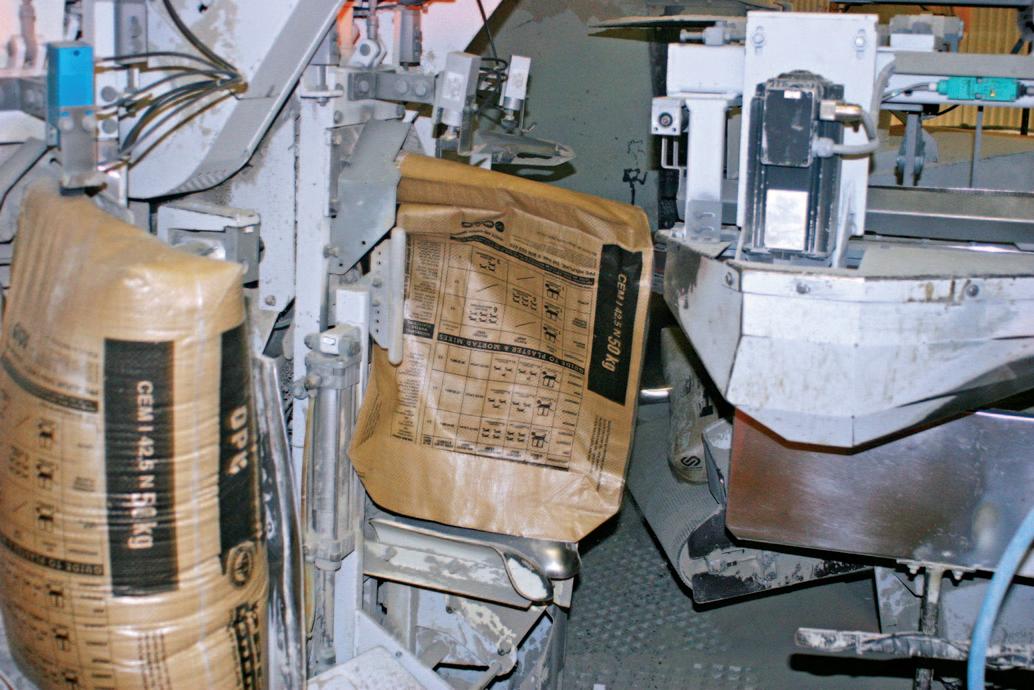
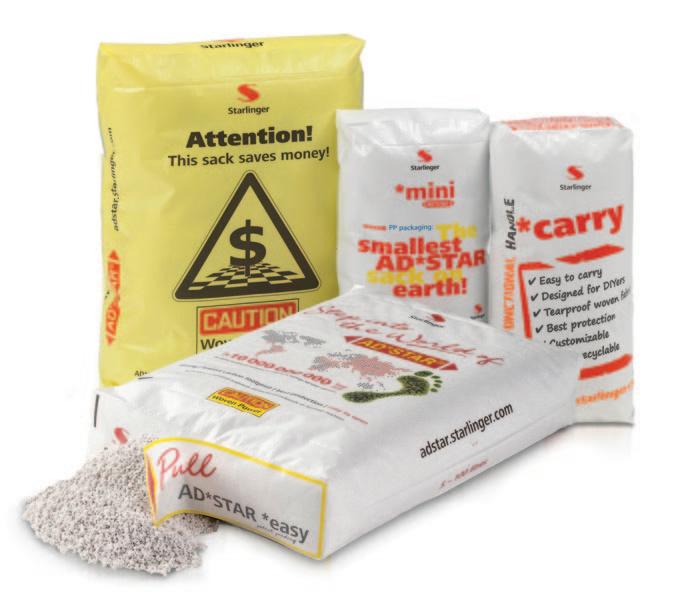
Smooth and clean filling process on high-speed cement filling lines with AD*STAR sacks (all photos: ©Starlinger).
High-quality tear-proof cement sacks save tons of cement and cement packaging that would otherwise go to waste and contaminate the environment, writes Sigrid Eder-Ince, Marketing Manager at Starlinger & Co GmbH. Made of woven polypropylene tape fabric, Starlinger’s AD*STAR block bottom valve sacks are highly resistant to breakage and can help to reduce CO2 emissions in the cement industry.
In the 1990s, Austrian machine manufacturer Starlinger & Co. GmbH, a respected supplier of machinery and complete plants for the production of woven plastic packaging, developed and patented the AD*STAR block bottom valve sack as a tear-proof and highly protective packaging for dry bulk goods. Next to cement, the sacks are used for packaging a wide range of free-flowing goods such as other building materials, fertilizer, chemicals or resin, but also for flour, sugar and animal feed. Currently, more than 17 billion AD*STAR sacks are produced on Starlinger lines installed on five continents every year.
SAVINGS POTENTIAL FOR GREENHOUSE GASES
Note: AD*STAR® is a registered trademark. AD*STAR® sacks are exclusively produced on Starlinger machinery. A Life Cycle Assessment carried out in 2016 and commissioned by Starlinger showed that AD*STAR sacks have lower global warming potential (also known as carbon footprint) than, e.g., paper sacks. A decisive factor for the positive results of AD*STAR sacks in this study are the low breakage rates in the course of the life cycle of the sacks. Due to the special production process, AD*STAR sacks are extremely robust despite their very low weight. The strength and resistance result in breakage rates below 1% during the entire usage phase of the sa cks — i.e. from filling, transport and storage until unpacking of the cement. This means that if AD*STAR sacks are used, less cement is lost and needs to be replaced, and less packaging is
AD*STAR sacks are available in various sizes and with useful features such as handles or easy-open strip.
Starlinger’s AD*STAR conversion lines ensure highly precise sack conversion with a minimum of rejects.
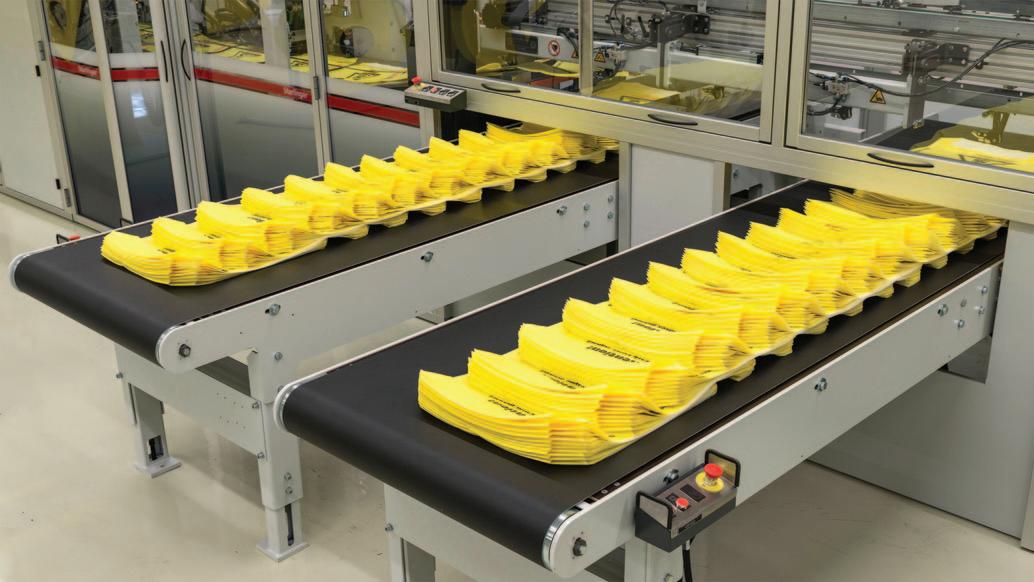
needed — consequently, fewer greenhouse gases are produced. As about 4.1% of the total global CO2 emissions are caused by the cement industry , millions of tonnes of CO2 emitted during cement production could be saved additionally each year by low sack breakage rates.
HIGH-STRENGTH PACKAGING AD*STAR sacks are block bottom valve sacks made from coated polypropylene tape fabric and sealed with a patented hotair method without the use of glue or sewing threads, making them a monomaterial packaging that is easy to recycle. The sack bottom and top are closed in a special conversion process by means of hot air welding. The use of high-strength polypropylene for fabric production and the tight sealing of the sack bottom and top ensure low breakage even during rough handling, dropping, or after contact with water. The precise production process on Starlinger’s AD*STAR sack conversion lines ensures high-quality sacks with minimum size variations. If required, optional microperforation provides aeration without product emission.
THE TECHNOLOGY Starlinger provides the full range of technical equipment together with the know-how needed for the production of AD*STAR sacks: polypropylene tape extrusion lines, tape winders, circular looms for fabric production, coating and printing machinery, as well as the ad*starKON block bottom sack conversion lines. The entire AD*STAR technology has been developed with the focus on high sack quality. This ensures the high strength and durability of AD*STAR sacks, as well as smooth and trouble-free cement filling on the most modern filling lines. Starlinger’s AD*STAR conversion lines cover a broad format range, from a sack capacity of only five litres up to 100 litres.
AD*STAR CEMENT SACKS — ADVANTAGES: v high strength and durability – reducing
CO2 emissions due to low breakage rates; v raw material savings due to the low packaging weight; v easy-to-recycle mono-material packaging solution; v suitable for automated filling, handling and palletizing; v fully automated sack production; v no spillage or leaking because of the polypropylene coating; v adjustable air permeability due to optional micro-perforation — keeps dust formation to a minimum and protects moisture from entering the sack (longer shelf life); v tamper and theft-proof; and v attractive sack design with high-quality print or laminated BOPP film for best brand promotion.
LATEST PRODUCT DEVELOPMENT: AD*STAR *EASY
The new patented easy-open feature allows for quick and easy emptying of AD*STAR cement sacks without the use of mechanical tools. To open the sack, a strip that is welded to the bottom patch of the sack is simply pulled off. This means that woven plastic sacks are now catching up with paper sacks in this regard and greatly facilitate the daily work of end consumers. The development of the AD*STAR *easy sack was prompted by the great demand in the market, which is reflected by the increasing number of conversion lines sold equipped with the easy-open feature.
CONCLUSION AD*STAR sacks offer benefits for the environment and the cement producer: They are economical in the use of raw material, have an extremely low breakage rate, help to reduce CO2, and can be either recycled or reused for other purposes. Each one of these ecological advantages also is an economic benefit for the cement producer. The special characteristics of tape fabric ensure high strength and durability while significantly less raw material is used in the production process. The favourable breakage rates of AD*STAR sacks help to reduce the carbon footprint of the cement industry, saving tons of spilled cement from entering the environment and avoiding replacement cement production.
ABOUT STARLINGER & CO GES.M.B.H. Starlinger is a Vienna-based mechanical engineering company with production sites in Weissenbach and St. Martin, Austria, as well as Schwerin, Germany, and Taicang, China. As a major global supplier of machinery and complete lines for woven plastic bag production, recycling and PET extrusion and refinement, Starlinger & Co Ges.m.b.H. is a synonym for leadership in quality and technology in over 130 countries. Founded in 1835, the familyowned business has been exporting machines worldwide for more than 50 years with an export quota of over 99.5 %.
Sales and service centres in Brazil, China, India, Indonesia, Mexico, Nigeria, Thailand, Russia, South Africa, USA and Uzbekistan ensure quick and professional technical support and service.

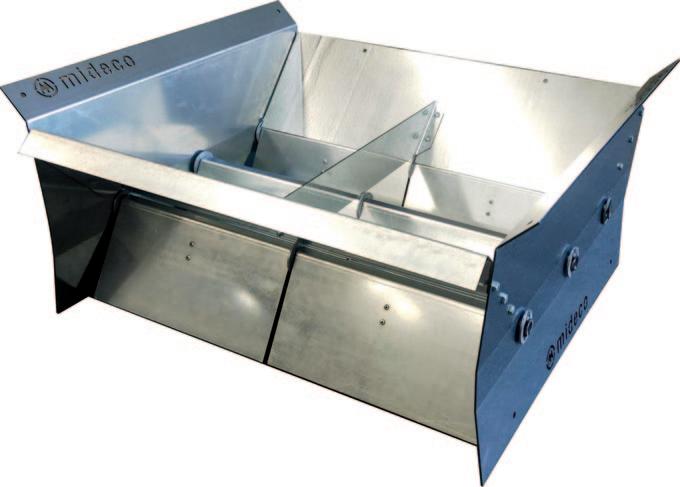
When it comes to providing conveyor belt support — for bulk products including cement and clinker — Kinder Australia has a solution to suit any transfer point regardless of any configuration or application.
These factors can include: v product; v belt width; v duty/belt speed; and v budget.
Rollers alone with spacious gaps, do not give ample support to the critical transfer point. If support is not provided adequately, belt sag can occur — along with detrimental productivity issues such as material spillage and excessive dust. The product loss, equipment damage and downtime issues caused by poor conveyor belt support is inconvenient, unsafe and expensive.
Kinder Australia’s K-Sure® Belt Support System is engineered to provide the support that the transfer point requires.
It utilizes the existing conveyor idler frames and load, carrying the centre conveyor roller. The wing rollers are then replaced by the K-Sure® Belt Support System’s universal adaptor brackets and low friction polymer belt support rails.
The K-Sure® Belt Support System requires no pre-engineering, adjustments or special tools. It is available in a standard two-metre length assembly kit. Other lengths can be modified upon request.
Effectively, it is designed to provide a consistent and stable support for the troughed belt profile by reducing the number of rotating components. K-Sure® Belt Support System eliminates any belt edge sag and therefore increases the effectiveness of the skirting seal.
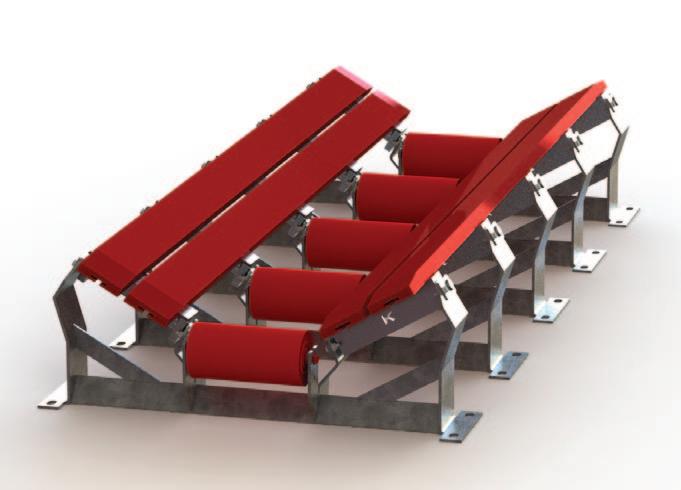
Keeping it clean: Mideco dust-control systems ideal for cement handling
Mideco has been widely known for its prominent role in industrial dust collection for over 60 years. Mideco is an acronym for Mechanical, Industrial, Domestic, Engineering, Company. Established in 1950, it is Australian-owned and operating, with agents in multiple countries, delivering turnkey industrial dust collection solutions across a diverse range of industries to keep thousands of employees healthy and the environment safe.
Mideco works closely with its customers to provide individualized solutions as unique and specific to the requirements of each customer. Its extensive capabilities and track record of global success mean that it can confidently recommend the best dust collection technology for its customers needs, in a range of industries including cement
Burnley Baffles. Bat Booth.
handling. The underlying philosophy here is to achieve solutions that provide mutual benefits both environmentally and financially.
Mideco has extended its commitment to dust elimination around the globe — in countries such as Germany, UK, and South Africa. Its clients range from large multinationals to start-ups, having a common desire for clean air, healthy employees, high-quality, solution-driven, and
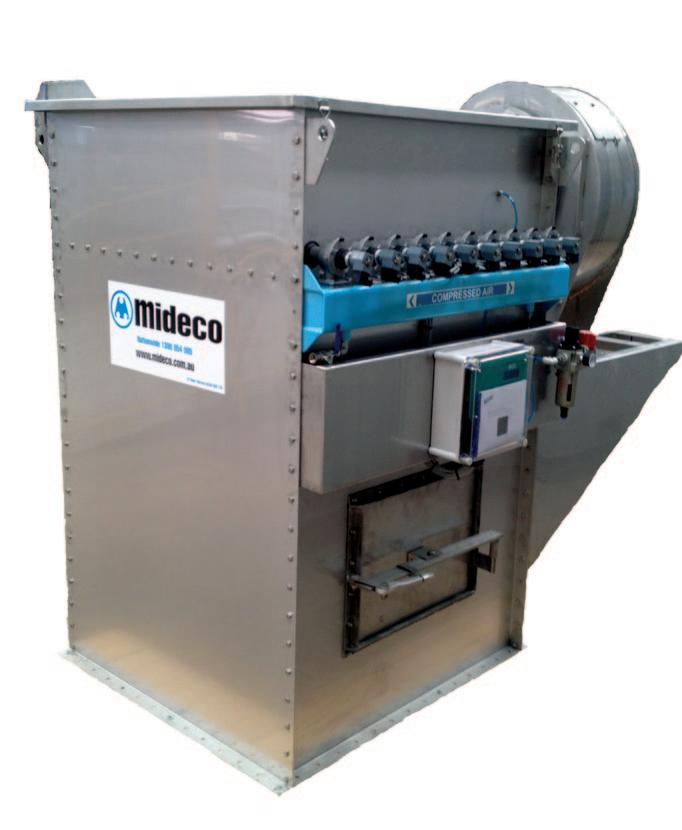
precision-built products that meet the highest standards in health, safety, and the environment. Some of Mideco ‘s clients include Boral, Glencore, Hanson Heidelberg Cement Group, BHP Billiton, Holcim, NSW Government, and many others.
Mideco provides advanced industrial dust collection solutions, at the heart of our de-dusting solutions is the ‘Bat Booth’, which has two variations: Bat Booth Standard and Bat Booth Premium both use the National Institute for Occupational Health & Safety (NIOSH) design. One of the most dreadful health concerns faced by industrial sectors is respiratory illnesses caused by airborne dust silica (silicosis), ‘black lung’ (miner’s lung), pneumonia, and also non-respiratory issues such as heatstroke. Bat Booth helps to keep clean a person’s dusty uniform, which can have dangerous exposure levels to respirable dust. A smarter, sleek, simple and effective variation of Bat Booth Standard is the Bat Booth Premium. It has a medically calibrated infrared sensor to measure the person’s body temperature which can detect early signs of heat stress, a control panel inside the booth which changes colour and displays instructions based on the temperature; all in less than half a second. Both versions use high-volume Economy filters.

Dust collectors.

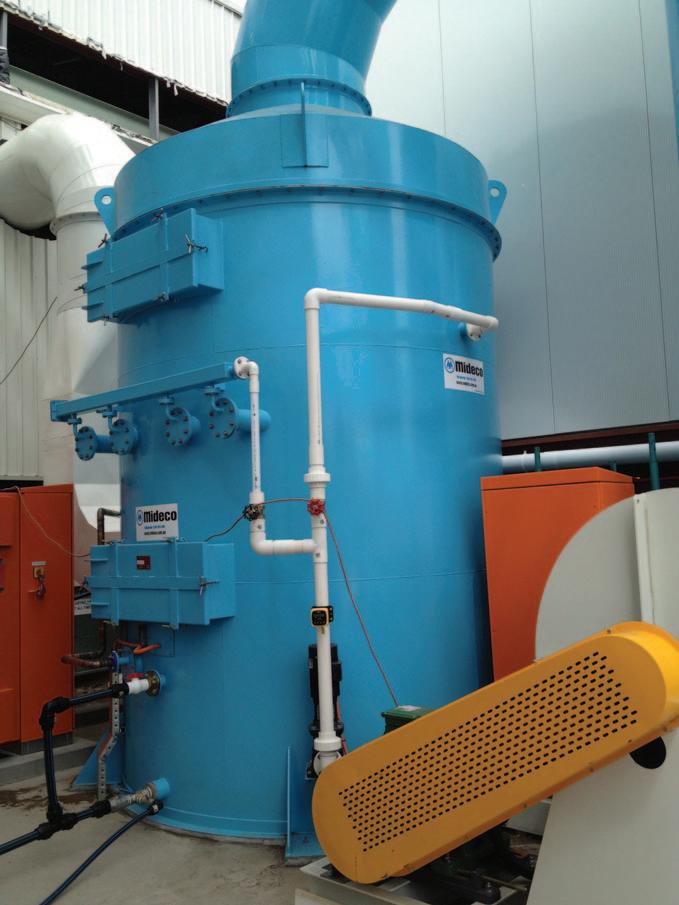
low-pressure compressed air to safely remove dust from the person’s clothing in ten seconds.
Burnley Baffles is an internationally patented dust suppression device to reduce the escape of dust from dump hoppers and chutes handling dry granular raw materials such as grains and ores. A set of Burnley Baffles when applied to a hopper alone can eliminate up to 80% of dust, and on applying a dust collector directly to the hopper can eliminate 100% of dust. They come in five different models depending on the granular material involved: cement and clinker, grain, fertilizer, soda ash, ores, coal, or any other materials. They are a simple yet effective design based on the principles of gravity and air movement. Burnley Baffles are a modular system that fill the open inlet face of a hopper. Each module contains a set of blades that pivot to allow the material flow into the hopper.
The baffles strip the air moving through the hopper off the pieces of grain or ore because the air pressure on all sides of baffles is all but constant. As the air is not heavy enough to open the blades, only the product enters the hopper while the dust is kept below the blades. The competitive advantage of Burnley Baffles is hard to beat as they are easy to install, virtually maintenance free, can be customized to a hopper of any size and is available in various sizes to suit different types of dry granular bulk raw material.
Economy filters are uniquely designed to maximize the filter cloth area while minimizing the space requirements, where these economy filters can be easily used with pulse or shaker cleaning systems. They include the essentials required for effective dust collection and can be customized to suit customer requirements with the addition of maintenance platforms, ladders, gas strut lids and insulation or cladding.
The economy filters can be used on conveyor transfer points, in tight places, low-head room applications, and with offline reverse air heating to manage high moisture applications.
Mideco has developed unparalleled expertise with the use of the latest ultrafine filtration technology using the HEPA After Filters (H13), using reverse air filters in high moisture conditions, and incorporating forward-thinking technology for optimal performance using Mideco’s Tubular Pulse Filters.
Lastly, Mideco’s range of dust scrubbing systems effectively removes harmful exhaust gases before they are released into the environment. In order to meet the requirements of any dust scrubbing application, Mideco can provide customized instrumentation and control systems, alternative materials such as stainless steel, and specialized paint or coating systems. The two kinds of dust scrubbers Mideco offers are Venturi Scrubbers and Peabody Plate Scrubbers.
Mideco has developed and improved its range of products, satisfying the market and aiming its goal of protecting people at their work sites. The company became interested in finding a way to prevent the collective workforce and those close to them from suffering predictable and preventable diseases. In 2006, Mideco patented a diesel fume control system for use in bulk material storage sheds, and received a Bulk Materials Handling Award for Environmental Project of the Year. In 2014, it launched its flagship product, the Bat Booth. Aside from providing services and products to existing and potential customers, Mideco also aims to create a positive social impact. It develops longterm partnerships with its clients and will be there to assist with ongoing support from advising how to purchase the perfect product that fits business requirements, running a training programme, and also for servicing the equipment.
Scrubbing system. Dust collector.
Bedeschi upgrade project: increase the reclaiming capacity of an existing limestone-reclaiming plant

The long co-operation between Colacem and Bedeschi continues with a contract award to Bedeschi. Bedeschi has been contracted for the complete upgrade project for the limestone reclaiming system located in San Cristobal plant, Dominican Republic, and managed by Domicem (part of Colacem Group).
The original stacking and reclaiming equipment, installed by Bedeschi in 2004, allows for clay and limestone handling at the plant: the upgrade of the machine will improve the limestone reclaiming system, increasing its capacity from 200tph (tonnes per hour) to 360tph, the capacity needed to feed the new production line that will be installed at the plant. The system will be renewed from the mechanical and electrical point of view, in order to guarantee the upgrade of all the components so that a completely new system is delivered.
Fully up to the stress test: MUHR’s MBG-600
CEMENT LOADING AS A ‘STRESS TEST’ FOR LOADING UNITS How much a loading unit is capable of becomes clear when it is subjected to a stress test. A prime example of such a test is cement loading: the extremely abrasive loading product requires a special design in terms of material quality and workmanship. Robustness is also essential because product temperatures of up to over 100°C can occur during loading due to residual embers in the silos.
Moreover, cement is so powdery that it recognizes every ‘escape route’. An effusion at the dome opening can be largely prevented by a tight fit of the loading head and a powerful extraction system. But depending on the design of the loader, the suction slows down the product flow unnecessarily — or even creates negative pressure that leads to strong vibrations at the dome opening.
There is a whole range of problems that need to be solved
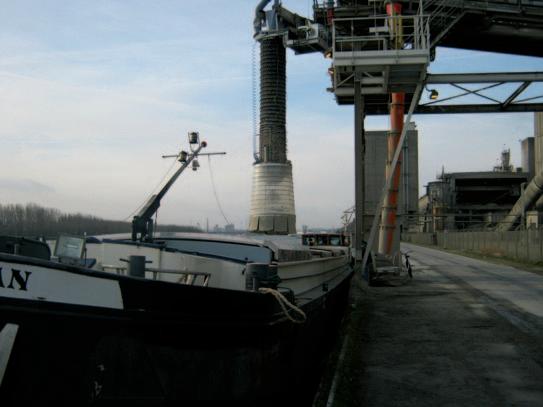
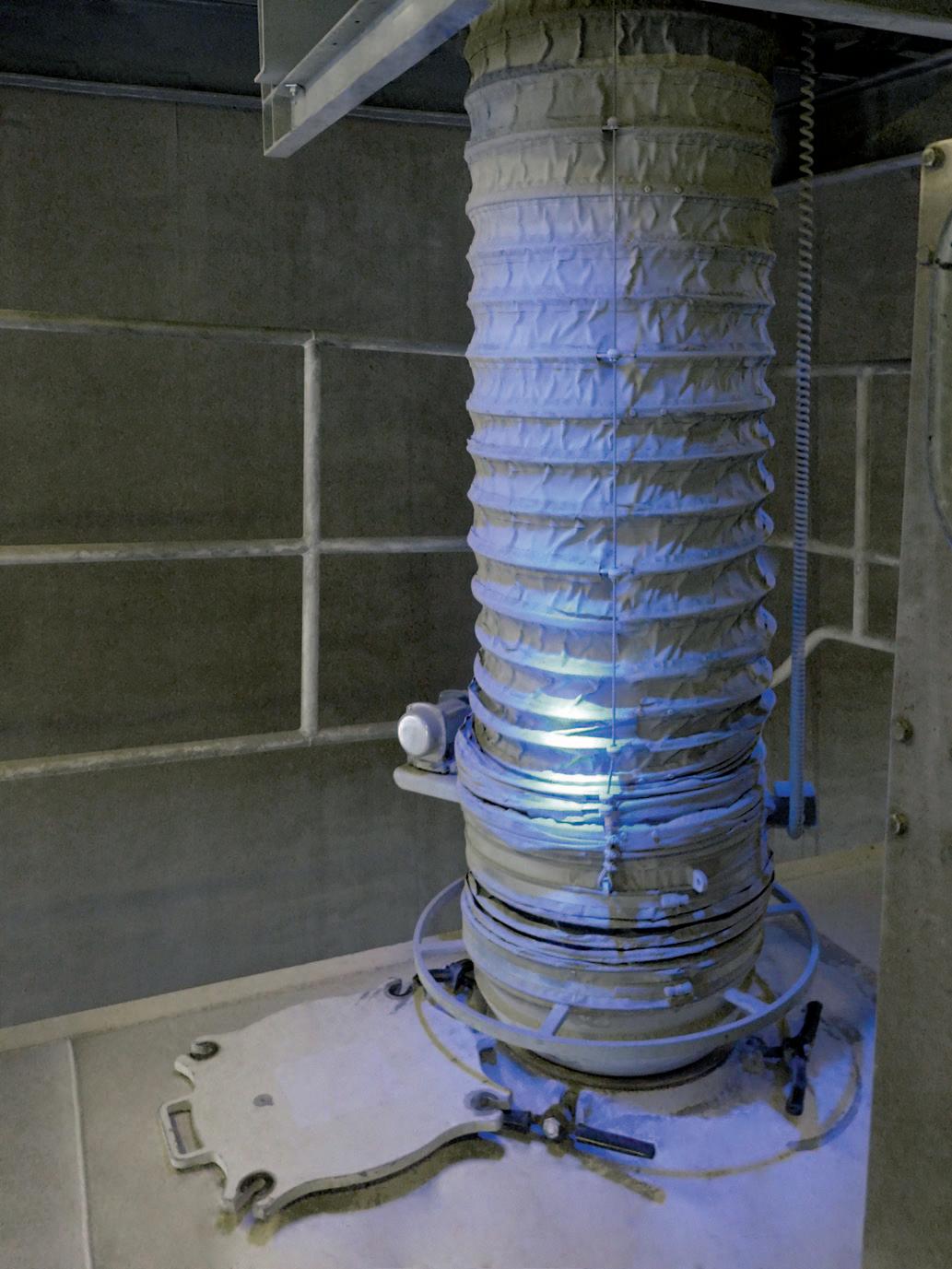

here. The MUHR MBG-600 with double bellows does this, and in the smallest of spaces. The double bellows enables a significantly higher loading speed because automatic pressure equalization is established between the loader and the container, while the rubber cone of the loading head ensures optimum tightness at the dome opening. The high-quality design of the trim allows loading of highly abrasive products even in extreme temperature ranges, making it durable and less susceptible to repairs. Another advantage of the double bellows is that it compresses enormously in its L min and can therefore be used in almost any installation situation: this is an advantage in older cement plants with low ceilings.
DOUBLE BELLOWS: THE FASTEST WAY TO THE GOAL
Traditionally, cement is loaded with a bellows that contains product cones made of an abrasion-resistant material that are inserted into each other. However, products such as cement and also lime, gypsum, anhydrite or dolomite are so fine that some of the loaded material passes through the gaps between the cones into the exhaust air stream of the outer bellows and is carried back upwards. This reduces the ‘efficiency’ of the loading process and the filters are unnecessarily loaded. In addition, the extracted product must be
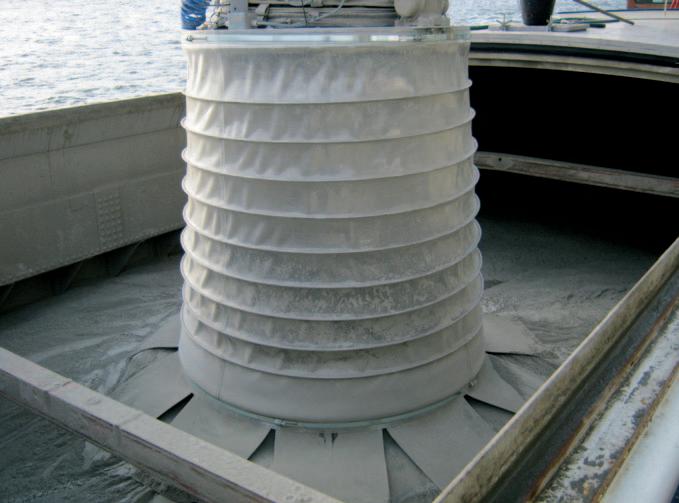
disposed of via a separate organ or returned to the product flow — additional efforts that are associated with financial, time and personnel costs.
In the case of the MUHR double bellows, the product flow in the inner bellows and the outflow of air in the outer bellows are completely separated from each other. Assuming an efficient external filter system on site, the loading performance can be noticeably increased. There is no need for additional peripheral equipment such as separators and rotary valves, and no manpower is required to move separated material. The inner bellows is equipped to withstand the same loads as the solid product cones.
A practical example from a MUHR customer shows how high the optimization potential is: with the MBG-600 loaders introduced in the cement plant, a reduction of the loading time from approximately 15 to approximately eight minutes was achieved. The filling of the trucks could also be optimized through a special design of the loading head: the fill level indicator is located at the highest possible point above the locking cone and only signals when the truck is almost completely filled.
Due to the intensive loading activity, cement loading in silo vehicles requires loaders with maximum robustness and reliability. The product itself and the high loading capacities required by the customer place great demands on the loading and process engineering processes. The MUHR loading system MBG-600 meets these requirements in an excellent way, which is proven by numerous positive customer references.
THE ADVANTAGES OF GERMAN SPECIAL MECHANICAL
ENGINEERING
Muhr is ‘Made in Germany’ in the original sense: all engineering, manufacturing, assembly and acceptance take place at the main site in Brannenburg (which has recently been expanded). The installed components are also purchased on the German market. Quality, workmanship and flexibility go hand in hand: for a special mechanical engineering company like MUHR, it is a matter of course to take special requests into account and respond to a multitude of specific requirements.
Expect all-around excellence
in enclosed, open and combined dry bulk loading chute technology
www.muhr.com
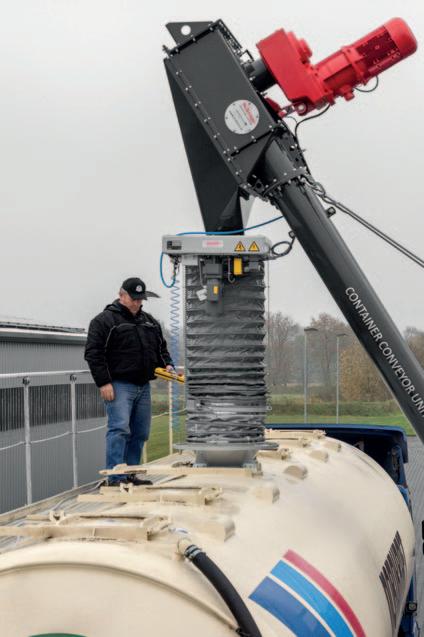
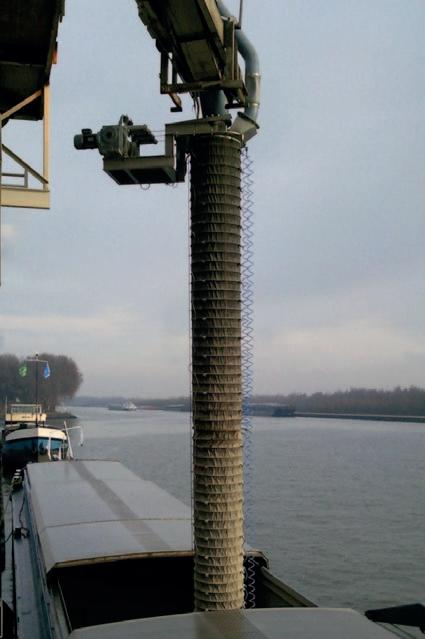
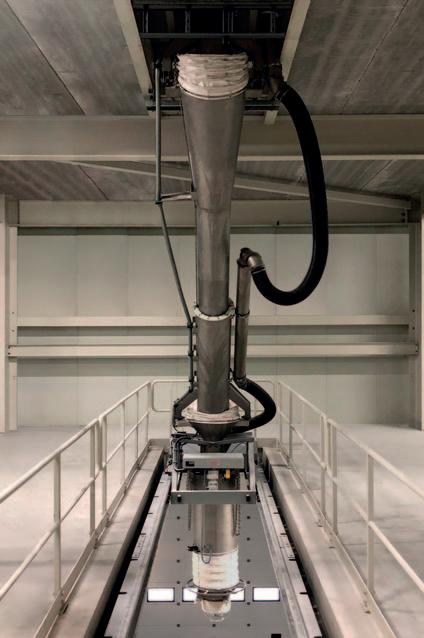
ENGINEERING & EQUIPMENT STANDARD INDUSTRIE improves production performance
Since 1978, Standard Industrie International has been a major engineering and manufacturing group specializing in the handling, storage and transportation of bulk materials. Its innovative solutions help to improve production performance and efficiency, reduce maintenance costs and risks, and ensure a safer working environment. They are regularly used mainly in the cement industry and in more than 60 industries throughout the production process.
THE AIRCHOC® PREVENTS PRODUCTION STOPPAGES DUE TO MATERIAL BUILD-UP The AIRCHOC® air cannon (picture 1) acts preventatively on the material through regular shots. It is an economical solution that uses air only when the shots are activated.
With a wide range of products (tank capacities from four litres to 400 litres), this solution is suitable for many areas of bulk material.
WHAT ARE THE AREAS OF APPLICATION OF THE AIR CANNON IN THE FACTORY? The AIRCHOC® is regularly installed on raw material storage units (sand, powders, flours, grains, wood chips, peat, straw, mulch, etc.). AIRCHOC® can also be found at the end of the process on fly ash or lime silos (Picture 2).
Used in boiler rooms, for example, AIRCHOC® air cannons, placed at the level of heat exchangers, guarantee continuous heat production and allow operators to supply energy without the risk of breakage due to fouling.
STANDARD INDUSTRIE’s technical teams carefully study the blockage factors, the behaviour of the clogged product, the inclinations of the storage unit, the productivity issues, etc... This complete diagnosis makes it possible to establish an optimal installation recommendation according to the environment of use (various risks, high heat zone, corrosiveness, humidity). The recom mended AIRCHOC® solution will also take into account the need for precise orientation of the shot, the number of shots, the diameter of the spigot according to the available pressure, the volume of the tank and the length of the spigot.
Picture 1.
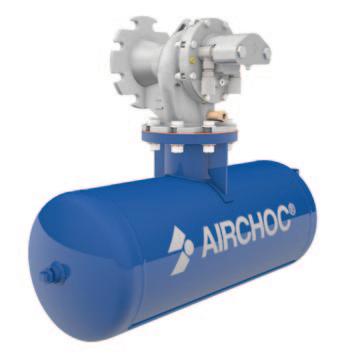
Picture 2.
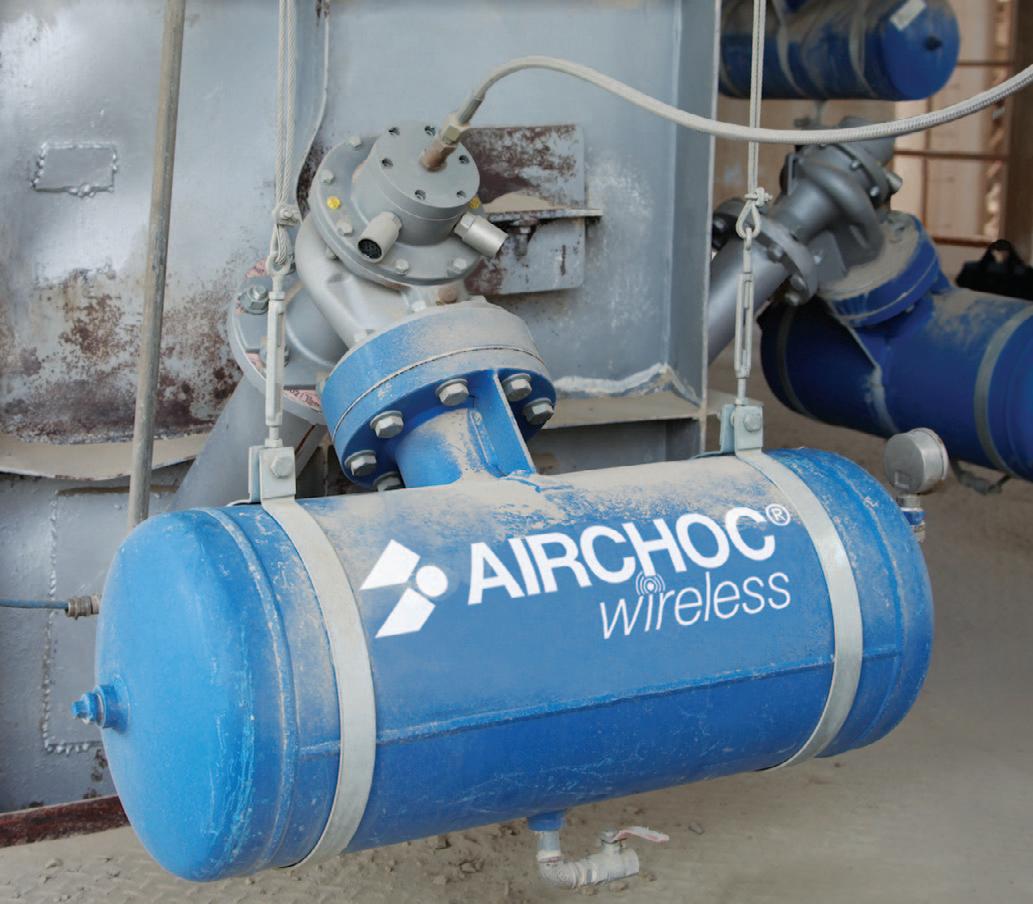
Particularly attentive to the requirements of its customers, STANDARD INDUSTRIE, and in particular the design office team, has spent more than a year testing modifications to its legendary AIRCHOC® air cannon in order to make it even more efficient and economical.
The AIRCHOC® has always had performance, economy and safety features. The latest innovations focus on: v saving compressed air: thanks to a better sealing of the piston and the possibility of shooting using only part of the air contained in the tank. It is also planned to programme jerky shots. v Reliability: due in particular to an improvement in the force of impact of shots from the barrel. (No AEP): no air passes through the piston seal, so no seal wear. v Spare parts: such as the solenoid valve, the valve or the silencers — rationalized and selected for their durability, these new components of the AIRCHOC® simplify its maintenance. In this respect, Standard
Industrie has also created an
AIRCHOC® maintenance kit that avoids the need for long and costly
HOW TO UPGRADE AN EXISTING
AIRCHOC FLEET?
STANDARD INDUSTRIE offers its customers fleet audits to evaluate the needs in terms of equipment renewal and homogeneity. Of course, the transition to the new version of AIRCHOC® guarantees the continuity of supply of compatible spare parts. The conversion of the fleet only concerns AIRCHOC® heads, so the change of tank is not systematic.
EXAMPLES OF A RECENT INSTALLATIONS OF AIRCHOC® SYSTEM IN CEMENT PLANTS: v A cement plant equipped its tower of preheating with 11 AIRCHOC® air cannons in order to eliminate the concretions and to avoid the manual ringing. They have been installed in the riser duct during the kiln shutdown, in addition to the 18 AIRCHOC® acquired (12 air cannons in July 2018 and six air cannons in May 2019) installed in the kiln inlet, smoke chamber and cyclones. This site, which has a 760tph (tonnes per day) 1970 KHD production furnace, uses 80% gas and 20% fuel oil. The AIRCHOC® air cannons are very effective on this type of installation. A different cement plant was looking
v
for a better cleaning of the equipment. The customer noticed in PLC that at the furnace inlet, cyclones and goosenecks equipped with AIRCHOC® air cannons in 2016 for the last ones, have a higher impact force and a better result/speed than those from a competitor, at the outlet, too small. Therefore, he wanted to install the AIRCHOC® at the furnace/cooler outlet. Solution installed: ten AIRCHOC®, DN 150 high temperature, 100 litres with deflectors reinforced baffles, Blowpipe tapping and safety accessories such as guillotine insulators, solenoid valves spares, etc.
CONCLUSION Building on its proven expertise with more than 5,000 customers worldwide, STANDARD INDUSTRIE brings, with its new generation of air cannon, a reliable and long lasting cleaning solution. It can help plants with handling and storage problems optimize the performance of their production tools while reducing their operating and maintenance costs.
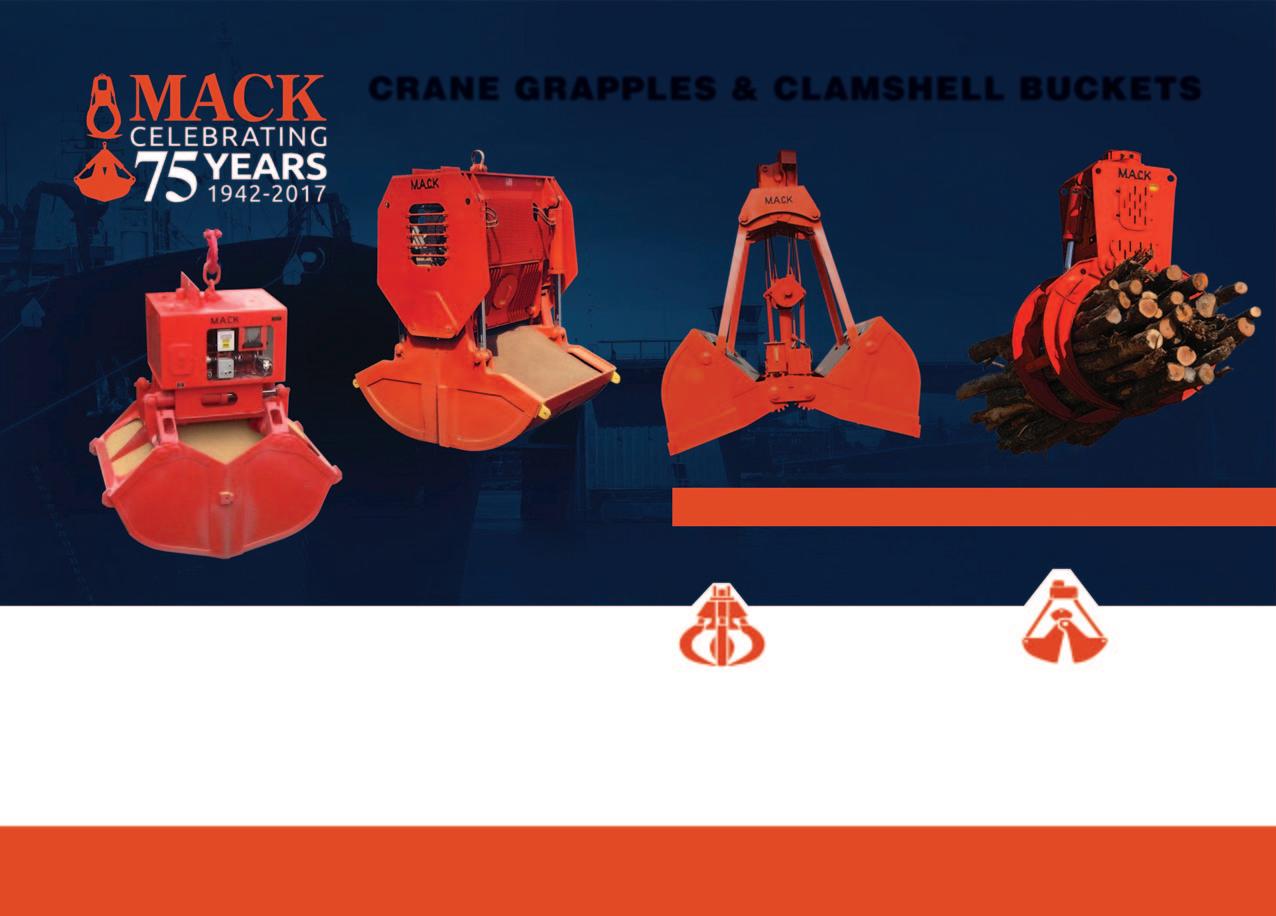
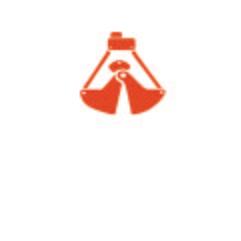
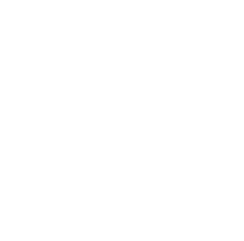

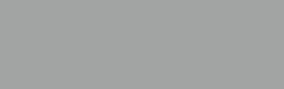

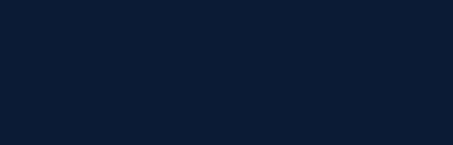
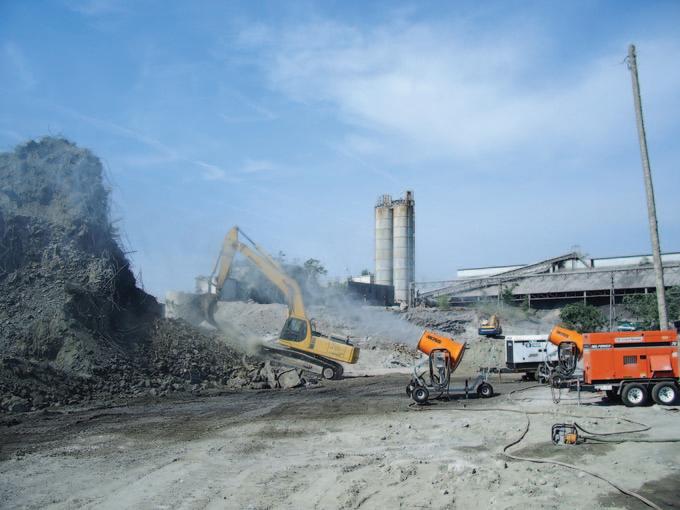
By any measure, preparing for a $320 million site renovation at a cement plant in West Virginia was a huge undertaking. Demolition of 16 storage silos was followed by a massive excavation effort to remove all buried footings, foundations and underground structures, making way for new pilings and foundations. Each of the silos measured 26 feet in diameter, with eleven of the structures 45 feet tall and the other five nearly twice that height. The project also included several additional buildings, ranging from one to three stories and with an average footprint of about 25,000ft2 .
What really complicated this project was the fact that all of the silos were still half- to ¾ full of sand, powdered cement or aggregate. The potential dust volume was staggering, and demolition engineers needed proven high-performance dust suppression as a key element of the company’s site-specific Health & Safety Plan and detailed demolition notice submitted to the West Virginia DEP.
“Without the appropriate control techniques, the emptying and demolition of the silos could have been a dust nightmare,” observed one of the contracting managers. For the health and safety of employees as well as the surrounding community, it was apparent that traditional hoses or sprinklers would not be sufficient to prevent such a large quantity of dust from becoming airborne. In addition to controlling the surface dust, it was critical for the chosen technique to be an effective method of scrubbing solid particles from the air, efficient enough to prevent migration.
“With a Mining Safety & Health Administration representative directly onsite, it was very important that we achieve our goals for dust suppression,” the manager said. After reviewing several control options, the company selected two DustBoss® model DB-60 units as the best method for dust management on the project. The oscillating carriage-mounted machines were outfitted with portable generators for added flexibility, allowing them to be located wherever they were needed most on a given day.
The DB-60 is one of the largest models from BossTek (Peoria, IL), with a throw of more than 200 feet (about 60 metres). When equipped with full oscillation, the unit is able to blanket nearly 125,000ft2 with a powerful dust-trapping mist from a single machine — more than 2.5 football fields.
Critical to the unit’s efficiency is its ability to balance the size, spray pattern and speed of the dust-trapping mist, atomizing the water droplets to the optimum diameter and velocity to deliver maximum dust attraction, while remaining large enough to carry for substantial distances. The DB-60 employs a series of 30 specially designed brass nozzles to atomize water into droplets 50–200 microns in size, the optimum for effective dust particle attraction. Launched by a powerful 25HP (18.6Kw) motor that generates 30,000CFM (nearly 850 cubic metres per minute), the atomized spray has a throw of more than 200 feet (approximately 60 metres) to produce the massive coverage area of more than 2.8 acres.
APPROACHES TO DUST CONTROL Basic spraying techniques such as sprinklers or hand-held hoses can help capture surface dust before it becomes airborne, but they have a tendency to saturate target surfaces, often resulting in standing water that can create additional hazards or damage sensitive cargo. The range of these techniques also tends to be limited, frequently requiring significant staff time to man the hoses or reposition sprinkler heads.
Their greatest drawback, however, is droplet size: water droplets produced from hoses and sprinklers are simply far too large to have any meaningful effect on airborne dust particles. A more effective option is the atomized mist produced by the DustBoss, which relies on the principle of creating tiny droplets of a specific size and delivering them at high velocity over a wide coverage area, inducing collisions with dust particles and driving them to the
The demolition effort included 16 storage silos, each measuring 26 feet in diameter. The greatest attraction between dust particles and water droplets occurs when they are roughly the same size, avoiding a slipstream effect.
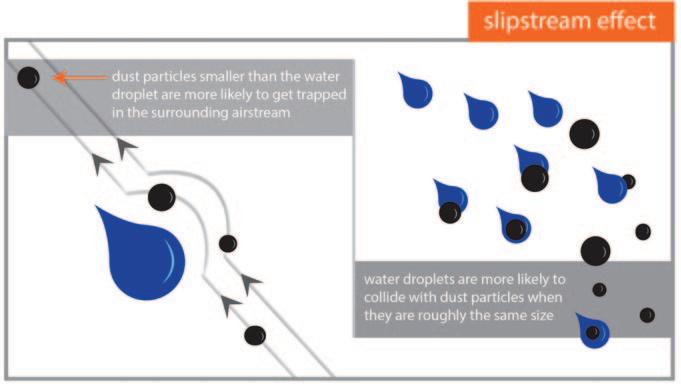
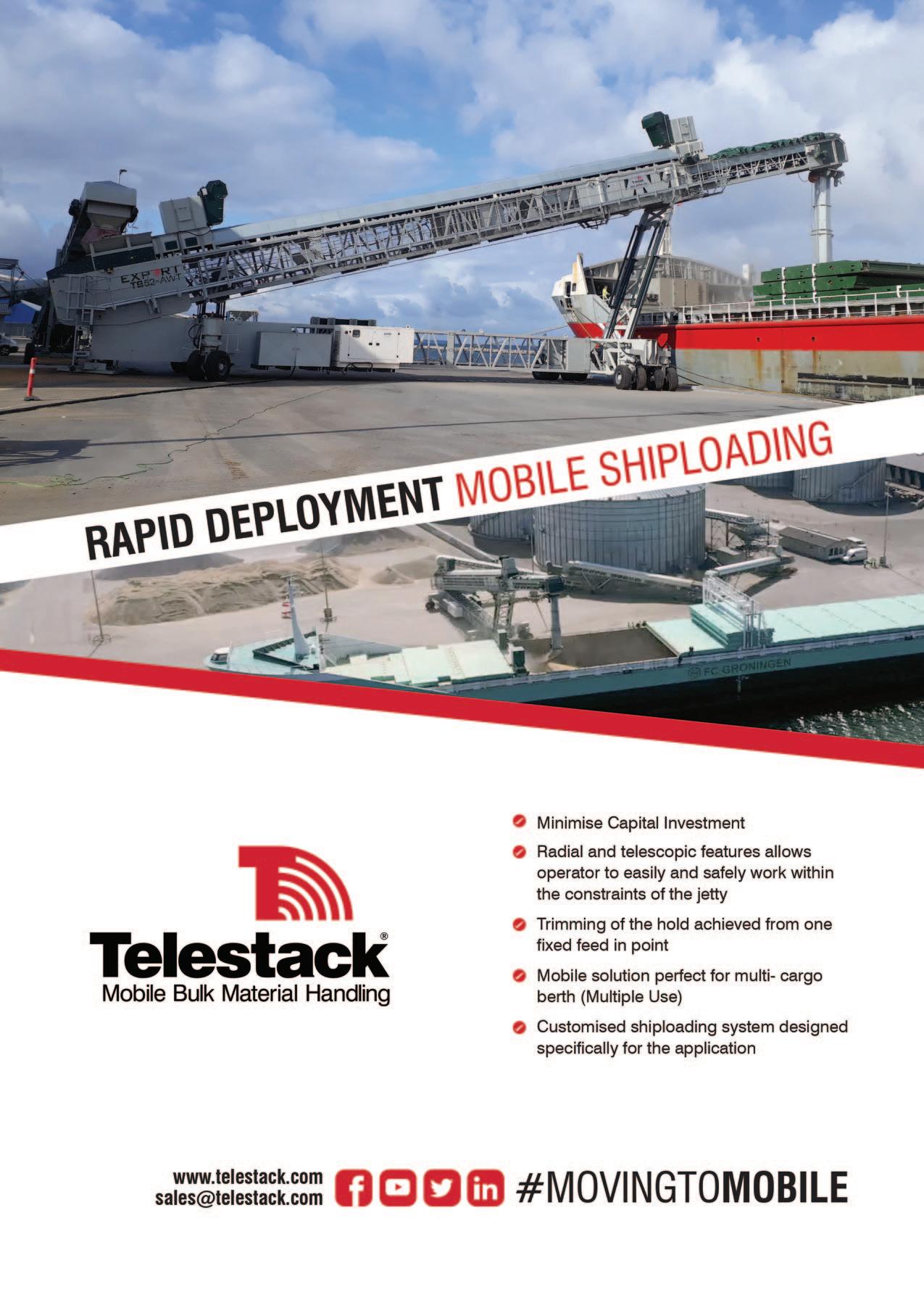
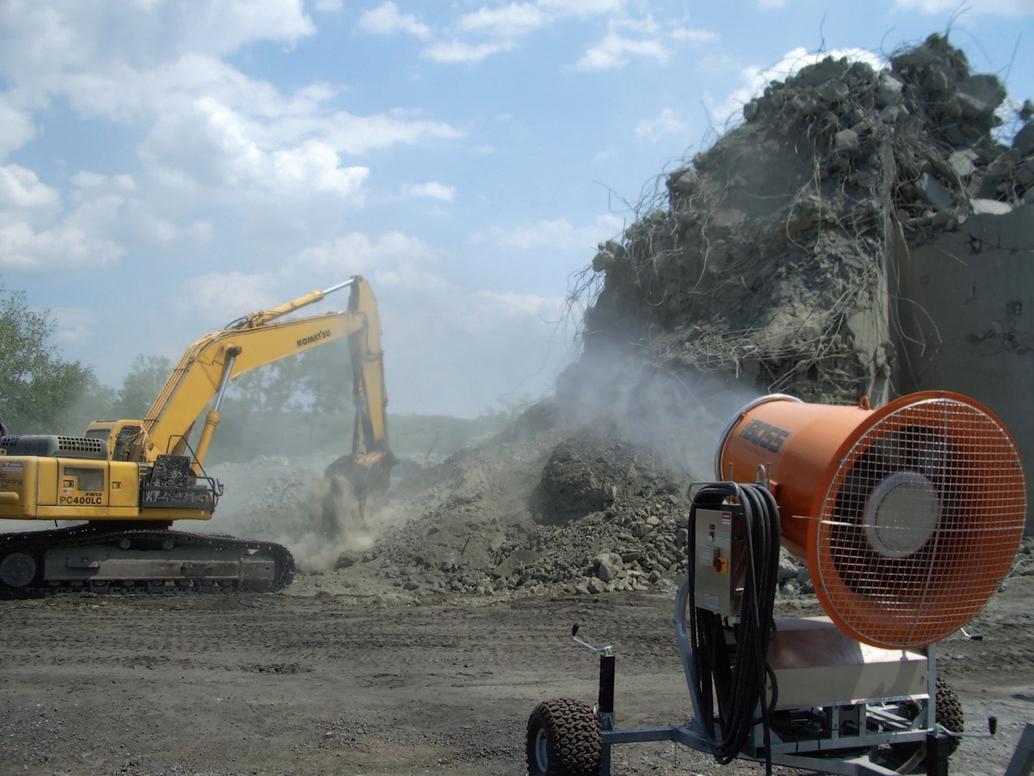
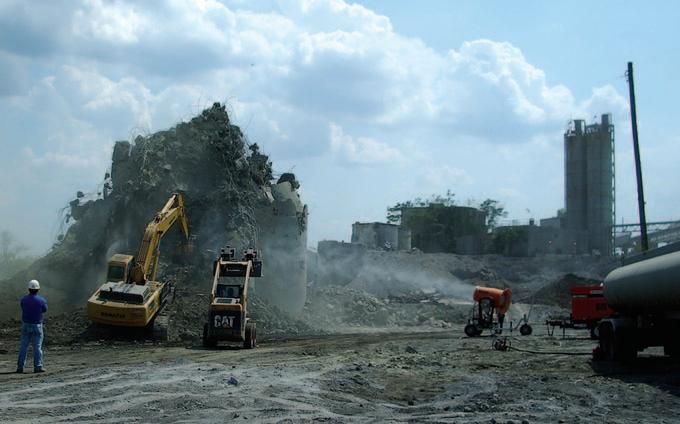
Complicating the project was the fact that all of the silos were still ½ to ¾ full of sand, powdered cement or aggregate.
ground. The method has proven well suited for managing dust from cement, coal, aggregates, and other bulk materials. It’s also one of the few technologies capable of delivering control of both airborne and ground-level dust.
As dust particles and water droplets approach each other, the best chance for a collision is created when they are roughly the same size, avoiding a slipstream effect that can carry them past one another.
THE TAKEDOWN Demolition crews used several different pieces of heavy equipment to demolish the buildings and foundations, including a Komatsu PC 450 LC with a fabricated steel rake attachment, a Komatsu PC 400 LC with concrete pulverizer and a Komatsu 300 with pulverizer. A 200-tonne P&H lattice boom crane took the tall silos down to about 40 feet, so the PC 450 excavator could safely level the structures to grade. The firm also employed a wheel loader with a five yard bucket and a Cat 236 skid steer loader.
The DustBoss equipment was in service primarily when heavy equipment was working. The twin oscillating units were strategically located for the greatest possible coverage, creating a virtual dust barrier between the demolition area and the remaining plant structures, which remained operational during the process.
The concrete silos were constructed with a substantial amount of rebar, with inner I-beams for additional reinforcement. As they were demolished, scrap metal was sorted from the debris and loaded into containers, then sent off-site for recycling. Demolished concrete was placed in a stockpile for crushing, while sand and cement were trucked to separate storage areas. Once the structures were demolished to grade, the contractor proceeded to remove all slabs, foundations and footings, aided by a Komatsu 300 with 8,000 psi hammer, a Komatsu 200 with 5,000 psi hammer and a Cat 963 track loader.
In all, more than 150,000 yards of material was excavated, sorted, transported and stockpiled. The entire four-month project was completed without a single injury or safety incident. “Thanks to the excellent control from the two DustBoss units, we didn’t receive one dustrelated complaint,” the manager added. “We were very pleased with their effectiveness and would definitely use them again on a project of this nature.”
ABOUT BOSSTEK BossTek is an expert in effective dust and odour control solutions for bulk material handling, demolition, rock processing and recycling. The company’s DustBoss® product line helps reduce labour costs vs. manual spraying, freeing up manpower for more important tasks. The automated units also use less water than hoses and sprinklers, with some customers realizing payback in less than six months and netting an annual cost savings of more than $50,000.
Each oscillating DB-60 can blanket nearly 125,000ft2 (1.16 hectares) with dust-trapping mist.
Atomized mist cannon
managing dust in unfavourable weather conditions
The DB-60 Surge is built for versatility and continuous use in punishing outdoor weather conditions.
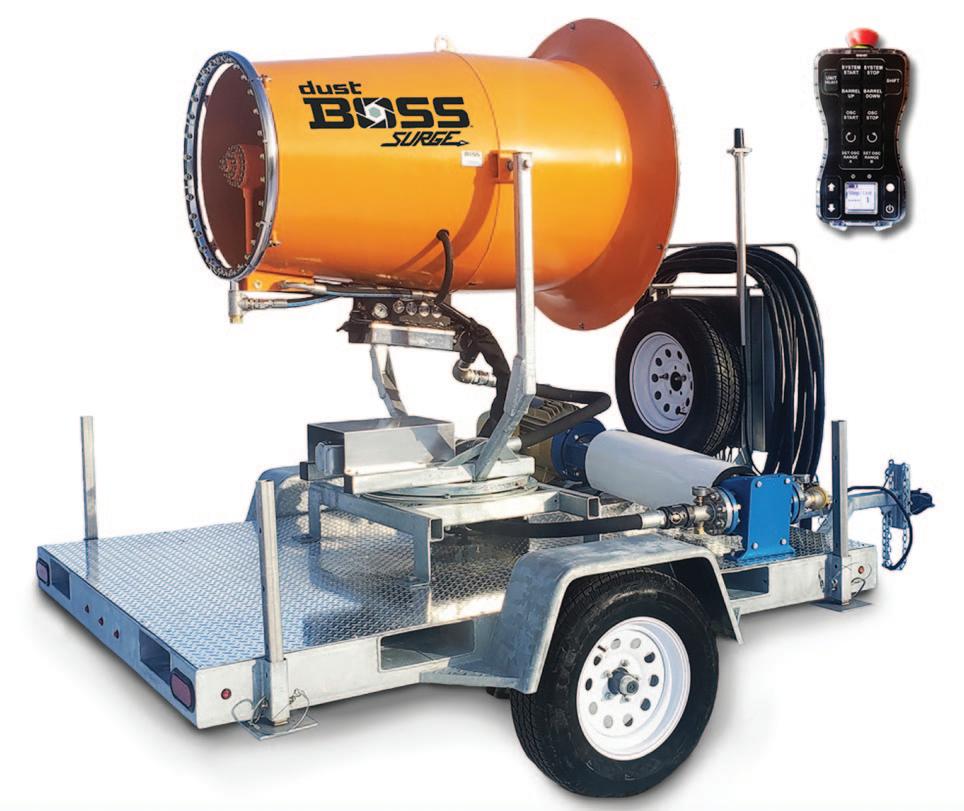
The next advancement in industrial dust suppression has been introduced by a renowned atomized mist technology specialist — a powerful cannon that is designed to fight dust with maximum efficiency. Developed in response to the needs of customers in areas with variable winds, the DustBoss® DB-60 Surge® features water propelled at high velocity from a center nozzle, combined with the industry-proven fan and misting ring system. With three remote-controlled stages and precision oscillation for optimum command over water volume and coverage area, the cannon uses highpowered jets that surge through the wind for over 250 feet (76.2 m) to suppress both surface and airborne dust. The result is effective and versatile dust mitigation in challenging weather for outdoor operations ranging from demolition to bulk material processing and storage.
“Our customers operate in very different circumstances; some with highreach excavators, some in open areas without natural barriers, while others are located in narrow corridors where wind velocity is amplified,” explained BossTek Dust Control Specialist Mike Lewis. “What these customers have in common is the difficulty in controlling fine atomized mist during blustery conditions. So we worked with our industry partners, listened to their feedback and engineered our most versatile and innovative machine to date.”
Lewis recalled that one of the initial drivers behind the new design was a need in the demolition industry. “Several customers described their challenges in suppressing dust during demolition of highrise structures,” he said. “Some of them use attachments that can be mounted on a high-lift boom, but that can bring its own complications. When we started working on a solution, we realized that this technology would also deliver benefits to a wide range of applications in which variable wind conditions can be a problem, such as port facilities, material processing operations and large outdoor storage facilities.”
The DB-60 Surge combines the power of an industrial fan, misting ring and heavyduty barrel with the reach and force of a central high-pressure spray nozzle. The pressurized spray resists wind shear and even uses the force of the wind to further fragment and carry the droplets, enhancing its dust suppression capabilities. This is achieved without the need for the high

Figure 1 – Water volume of each stage.
water output associated with a hydrantdependent hose or industrial sprinkler system.
In high-wind situations, dust is lifted into the atmosphere and carried beyond the site line over long distances, which can lead to permit violations. Operators of bulk storage mounds, demolition sites, ports, recycling material piles, etc. often mitigate particulate emissions using a sprinkler or hose to saturate a material’s surface. The higher the wind, the more water pressure is required to break through the shear, resulting in greater amounts of water filling the surrounding work area — often 300GPM (1,135 lpm) or more.
There are several issues associated with the use of hoses and industrial sprinklers. Hoses typically require manual labour, removing workers from other critical tasks. Moreover, both sprinklers and hand-held hoses contribute to high water bills. Taking compliance and expenses into consideration, the long-term cost of operation for sprinklers and hoses is higher than it might appear.
The DB-60 Surge addresses wind, labour and water usage issues. While striving to stay compliant with dust regulations, operators can now better match the water requirements to the specific application. Fed by a standard 1-½ in. (38 mm) hose with a cam-and-groove quick disconnect coupling, the powerful booster pump delivers as much as 500PSI (27.5BAR) of water pressure to the centre nozzle, with an output of 37–100GPM (140–378 lpm).
Controlled by a three-stage system
The design features three remote-controlled stage and precision oscillation for optimum coverage.
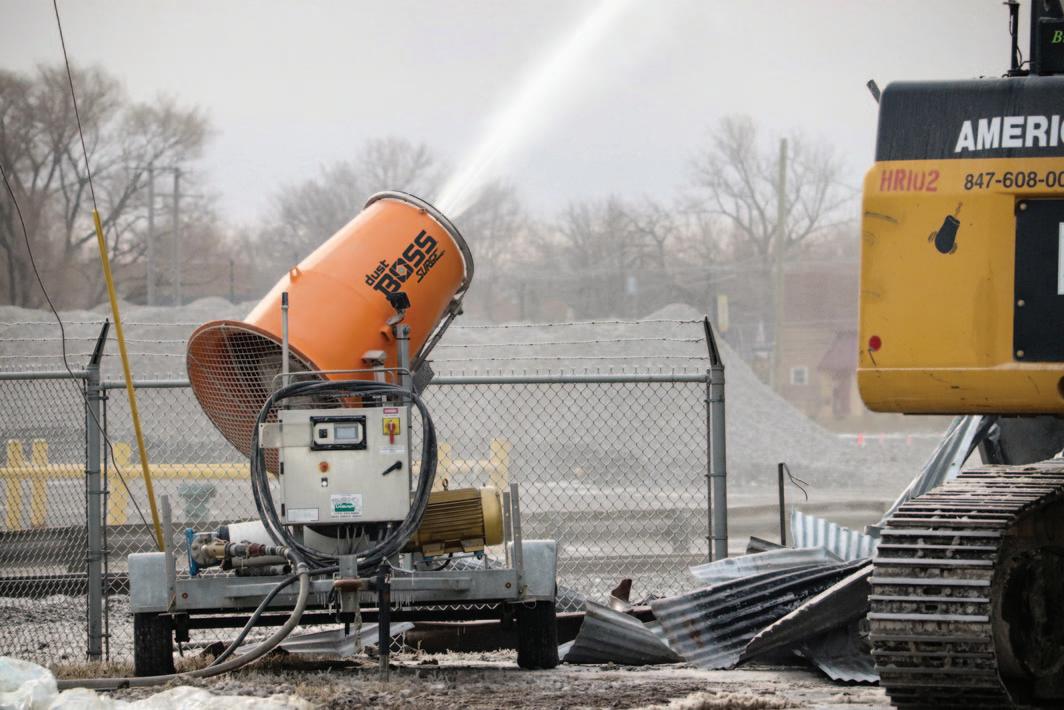
The cannon uses high-powered jets to cut through the wind, suppressing surface dust and airborne particles.
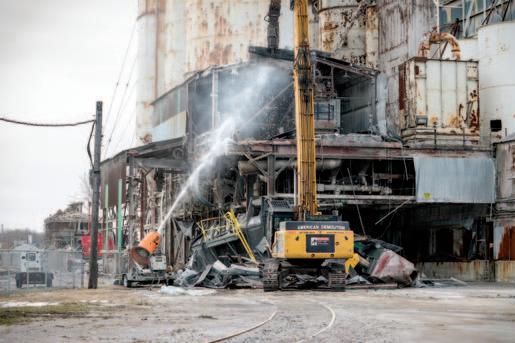
adjusted by a hand-held remote, the first stage is highly effective on moderate days for airborne and surface coverage. It uses the powerful 25HP/30,000CFM (849.5CMM) fan and misting ring to deliver millions of fine atomized mist droplets over a wide area, which collide with tiny dust particles and drag them to the ground. For windy days, stage two features a pressurized stream delivered by the central nozzle. On high wind days, operators can utilize the fan, misting ring and center nozzle for maximum coverage.
The versatility and coverage area is extended with the customizable 359º horizontal oscillation range and 0–50º vertical throw angle. Using the hand-held remote, the operator can raise the spray angle to reach extended heights, directing the 250ft (76m) spray to areas such as high-reach demolition or across the beam of large bulk cargo ships. The oscillation range is easily controlled with the left and right trigger of the remote control to customize the precise desired horizontal range.
Mounted on a heavy-duty roadworthy trailer for towing at highway speeds with a standard ball hitch, it can be placed by a pickup truck, skid steer or lift truck wherever dust suppression is needed. As supplied, the DB-60 Surge can run potable or nonpotable water, as it is equipped with two in-line 30 mesh, 595 micron filters to avoid clogging. One filter is located at the water entry point to the booster pump, another prior to the pipe feeding the central nozzle.
After the initial setup, the DB-60 Surge requires no labour to operate. The remote control has a 1,000ft (305m) range, so operators using heavy machinery from high-reach excavators to front loaders can command the machine without leaving the cab.
Lewis mentioned that other options are already available, including tower mounting and a version of the company’s popular Fusion lineup, which pairs the Surge with a generator to alleviate the need for a nearby power source.
“DustBoss is known for its rugged quality and long equipment life, often described as one of the most reliable and lowmaintenance pieces of equipment on any job site,” he added. “Our three-year or 3,000-hour warranty is evidence of our confidence in the products. The DB-60 Surge is designed with that same philosophy and is built to last.”
ABOUT BOSSTEK BossTek is globally renowned for its dust- and odour-control solutions for the storage and handling of clinker, petcoke, coal, rock and aggregate, as well as controlling air quality during port unloading, recycling and scrap processing, mining, earth moving, and demolition activities. The company’s DustBoss product line utilizes atomized mist technology propelled by powerful fans to capture fugitive particles over a wide area.