
30 minute read
Echoclor Advertorial
from Nafs November 2020
Steve Candito Is Your Ballast Water Management System Compliant: Understanding the AMS BWMS and IMO BWMS Code Requirements By Steve Candito, CEO Ecochlor
Time is running out and shipowners need to understand the latest ballast water management system (BWMS) regulations for their installed systems in regard to the USCG AMS deadlines and IMO BWMS Code Type Approval.
Advertisement
AMS BWMS extensions are expiring
The U.S Coast Guard (USCG) created the Alternative Management System (AMS) program to allow shipowners to move forward with ballast water management system (BWMS) installations while the USCG worked with manufacturers to type approve a wide variety of treatment technologies. The program was a temporary measure to provide five years to develop enough USCG Type Approved BWMS for every vessel type and/or shipping route to satisfy shipowners.
At the time, the new U.S. BWMS guidelines required “newbuild vessels constructed after 1 December 2013 to have an installed BWMS - including AMS accepted - upon delivery and for most retrofits to be D-2 compliant at the first scheduled drydocking after 01 January 2016.” The first USCG BWMS was not type approved until July 2016 (i.e. 6 months after the original deadline). Thus, initially the USCG automatically issued deadline waivers (i.e. extensions to the next scheduled dry dock).
Now, the temporary approval of many of the early AMS BWMS is expiring in 2020. As a result, if the installed AMS BWMS on board the vessel does not have U.S Coast Guard Type Approval then the owner must either file for an extension or install a USCG Type Approved BWMS.
The USCG is allowing some short-term extensions, which are reviewed on a case-by-case basis. These extensions allow shipowners to continue to sail in US waters until the manufacturer can finalize their Type Approval. Typically, extensions have been granted if the BWMS vendor is in the process of testing or are only a few months away from achieving Type Approval.
Another important issue for owners to understand is that if the installed AMS BWMS has since gained USCG Type Approval, it does not automatically mean that the installed system is compliant. All modifications or upgrades required to make the AMS BWMS match the USCG approved system model must be carried out by the end of the five-year AMS period. Many manufacturers are working with owners to make sure that these systems are updated prior to the AMS expiration, including an extension if needed. Owners should also be aware that some first-generation BWMS may require extensive upgrades to become compliant.
Lastly, there are several installed AMS accepted BWMS that are not pursuing Type Approval or it is doubtful they will be able to achieve it. This situation will be very problematic for shipowners wishing to continue trading to the United States and may require a new system installation for the vessel.
Updates in BWMS Code Type Approval vs. G8
Any shipowner who has trade routes outside of the United States and does not have a BWMS on board their vessel will be impacted by the BWMS Code Type Approval if their chosen system is not compliant.
The requirements came into effect on 28 October 2020. According to MEPC.300(72) paragraph 1.5, “Approval of a system is intended to screen out BWMS that would fail to meet the standards prescribed in regulation D-2 of the Convention. Approval of a system, however, does not ensure that a given system will work on all ships or in all situations.” In addition to an updated testing protocol, the BWMS Code Type Approval process has a number of changes, which result in notations on the Type Approval certificate. A few are addressed below.
The first is a section addressing System Operating Parameters that addresses the salinity and temperature of the water the BWMS can treat. Prior to the BWMS Code, manufacturers could test their BWMS in only two different salinities, but received an approval for all three water types – fresh, salt and brackish water. Under the new requirements, manufacturers must test in all three salinities to receive approval for all three. A BWMS that has not been tested in all salinities will have their limitations included within the Type Approval Certificate.
The second change focuses on System Design Limitations (SDLs). The Type Approval Certificate must identify each relevant operational parameter together with the validated low and/or high parameter values. The system’s design capacity is a critical parameter since it must match the vessel’s ballast flow rate. For
example, the Ecochlor system is approved for 50 – 16,200 m3/hr., which is the highest approved flow rate in the industry. This flow rate capacity must be noted on the BWMS Code Type Approval certificate and the vessel may not exceed the flow rate listed in the SDL.
Another SDL example, which is particularly important for UV system approval, are limitations related to turbid or “dirty water”. This factor will be crucial for vessels on trade routes that include muddy rivers like the Mississippi, Amazon and Yangtze. Thus, the vessel owner must ensure that any UV BWMSs SDL encompasses the dirtiest water the vessel is likely to encounter or the BWMS will risk not being approved to operate in certain locations based on the SDL listed on the Type Approval Certificate.
The third factor relates to bypass requirements in the BWMS Code that now requires makers to have “…bypasses or overrides to protect the safety of the ship and personnel…” that are connected to the vessel’s ballast system. These bypass systems must activate an alarm and be recorded by the BWMSs control and monitoring equipment. The crew is also required to record this information within the ballast water record book every time the system is bypassed or an alarm activates.
Lastly, with regard to general monitoring, the system must monitor, record and store sufficient data on the various operating parameters to verify correct operation for the past two years. Alerts must automatically occur when the system is shutdown or when an operational parameter exceeds the approved parameter.
After the BWM Convention ratification there were approximately 83 BWMSs that received approval under the original IMO regulations. When the USCG released their type approval requirements, that were more stringent than the IMO regulations, many manufacturers decided not to continue testing for compliance in U.S. waters. To date, only 36 BWMS have been USCG Type Approved, with several additional systems pending approval. Under the BWMS Code, there are only 19 BWMS that have been approved as of September 2020.
Shipowner Extensions for Noncompliant BWMS
With the imminent deadline, many vessel owners continue to seek extensions. In the past, regulators have been quite lenient by offering vessel compliance date extensions for ballast water management system installs, particularly now due to the Covid-19 pandemic. However, the BWMS Code requirements were widely publicized prior to the pandemic and shipowners were aware of this requirement. Additionally, the AMS five-year window has offered most manufacturers enough time to qualify for USCG Type Approval and allow for any upgrades needed for Compliance by the deadline. Thus, the prospect of further extensions at this time is limited.
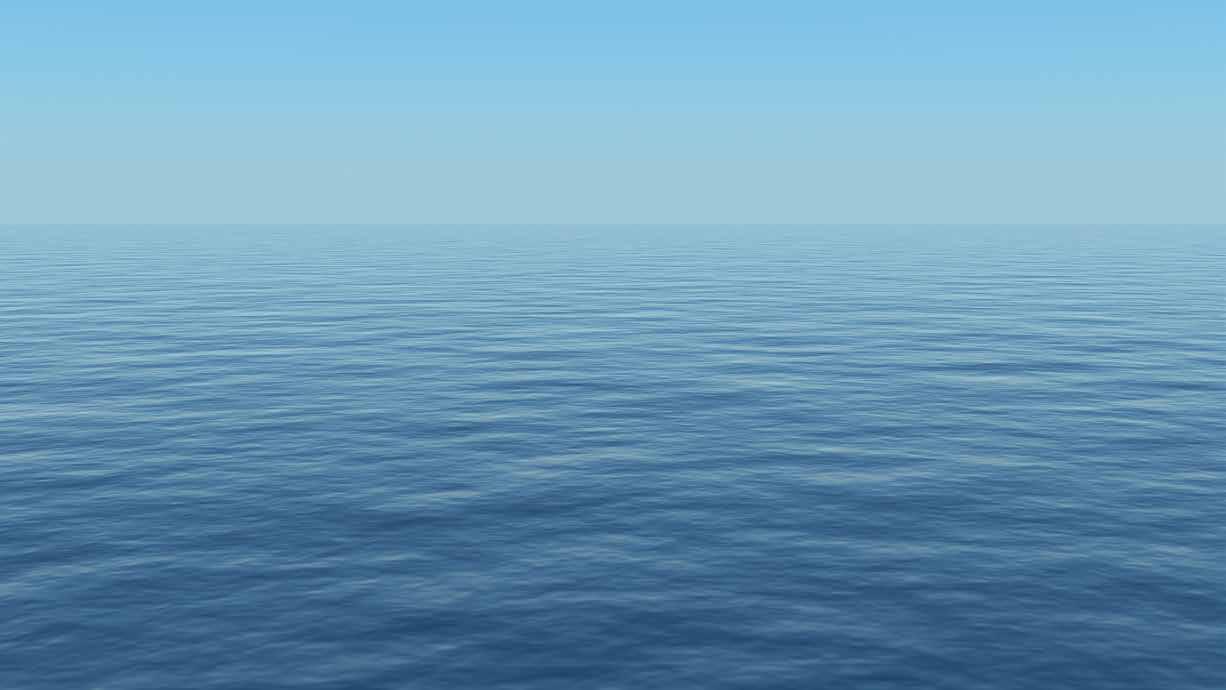
Panos Smyroglou At Ecochlor we are expanding our global Service capabilities
Panos Smyroglou, is Director, Business Development, Ecochlor Inc.
Ecochlor is best known worldwide as a top-tier ballast water management system manufacturer and service provider. The Ecochlor® ballast water management system (BWMS) uses a two-step process to treat ballast water, filtration followed by a chlorine dioxide treatment technology. Chlorine dioxide is a widely used and incredibly powerful biocide. It has been used in a wide variety of landbased treatment applications, including drinking water, municipal waste, food and pulp and paper for over 70 years, and has now been proven for effective onboard treatment of ballast water. Chlorine dioxide offers a number of advantages over other disinfection chemicals and techniques. It is completely effective on all potential aquatic invasive species regardless of turbidity, salinity, or temperature of the incoming ballast water. This allows for a consistent, easy-to-use system for the crew without the uncertainty of its effectiveness when faced with varying water types. Vessels that have routes in challenging
system installation, providing support to the integration and the high employee turnover in shipyards, there is still
waters often look to the Ecochlor BWMS as a solution.
Key advantages of the Ecochlor BWMS is the proven technology. Our system meets or exceed all regulatory requirements from IMO & USCG: International Maritime Organization (IMO) Type Approval – G8 (2011), (2018), BWMS Code (2020) & G9 (2010); and, USCG Type Approval (2017). Benefits include: • Minimal crew involvement during system operation • Small footprint even for vessels with high flow rates • Low power requirements, possibly the lowest in the industry • Treatment efficacy not affected by turbidity, salinity, or temperature • Installation flexibility; Treatment System can be placed in any convenient location as modular components. The Ecochlor System a allows for the flexibility to design a skid-mounted system • No ballast water treatment or neutralization required at discharge • No TRO sensors
Each ship with an Ecochlor system on board is assigned their own “vessel delegate” to ensure a quick response to any issues encountered during ballasting operations. After each ballast operation, the crew sends the Ecochlor vessel delegate a Functional Monitoring Data Sheet (FMDS) via email to analyze. The FMDS provides critical information to the service team, such as the location and date of the last ballasting operation, various operational parameters and, most importantly, monitors the amount of chemicals used during the operation and the amount currently available on board the vessel. This information on the FMDS is then incorporated into a Fleet Status Update Report, allowing for proactive maintenance and support of the Ecochlor® BWMS on board the vessel. Through the FMDS, an Ecochlor Service team member tracks the ship’s chemical usage, and provides logistics and technical support for ents, as well as receiving their positive feedback after the
chemical resupply at ports and harbors around the world.
At Ecochlor, we have undertaken a commitment to serving our clients well beyond BWMS industry expectations and we stand fast in our operations. NAFS: In what ways is Ecochlor working closely with international shipyards as well as the vessel shipowners in order to coordinate and support their ballast water compliance efforts?
P.S.: Ecochlor has expanded after-sale retrofit options to better provide turnkey logistic and installation solutions. This helps to ensure an easier, streamlined retrofit. Ecochlor offers “door to door” service for its equipment delivery through either sea or air transfer. This service simplifies logistics for customers and minimizes delays in ballast water management system (BWMS) parts delivery.
I recommend that our own installation team oversees the engineering firm and shipyard personnel so as to ensure a successful installation. This is of particular importance if the integration engineers or shipyard performing the project have limited or no experience with the retrofit of an Ecochlor system. Installation attendance is provided on a daily basis at a support level of the customer’s choosing. Thus, the Ecochlor team can either oversee the entire installation process, or be onsite to only oversee certain activities as may be required to ensure a streamlined, high-quality installation. Typically, the shipyard is simultaneously working on many projects for multiple vessels. The schedule for each job is very tight and does not allow much time to evaluate every detail of the installation. When projects are rushed, that’s when things can go wrong. Due to tight schedules concern that BWMS retrofits are not receiving the necessary oversight that ensures a successful installation. During the installation, regular and consistent communication between all the participants is critical to a positive outcome. When attending an installation, the Ecochlor Installation Team has daily meetings with the shipyard crew and sends a daily report to Ecochlor’s Engineering Team in the USA, the shipyard superintendent, integration engineers and the shipowner, to show the project progression, as well as highlight any issues that many need to be addressed. This helps to limit the impact of any problems.
NAFS: For Ecochlor, finding the best solution for its cliefforts to provide the very highest standards in support of our clients’
sale, obviously brings considerable satisfaction?
importance of meeting each and every one of our customer’s desired levels of satisfaction. The goal is to provide the customer with a BWMS with proven reliability and easy operation. NanoVapor is an alternative technology for the rapid gas-freeing of fuel tanks and other tanks, which significantly reduces time and costs whilst enhancing crew safety during Additionally, we have moved our Corporate Headquarters to a much larger facility to accommodate a fast-growing team of professionals and company expansion. Extensive feedback shows that crew man entry. Due to the health risk to crew and NAFS: Ecochlor recently presented find the Ecochlor System simple to fire /explosion risk on the vessel, I believe NanoVapor, a very promising product that operate. In part, this is because there that shipowners will appreciate having a will change - according to you - gas-freeis no need for the crew to adjust the safer, environmentally-friendly option for the ing bunker and cargo tanks forever! operating parameters due to changing crew but will also look at the savings gen- Safer, greener, up to 90% less time and water conditions. Our BWMS does not use a TRO sensor or complex power supplies that can interrupt the ballasterated by the up to 90% less time it takes to gas-free tanks! The NanoVapor unit is simple to use and operate along with an onboard twin tool compressor. The TankSafe™ techless expensive. Do think shipowners will be interested in this nanotechnology? ing / deballasting operations when they nology is non-toxic, non-reactive and comP.S.: Being a successful market leader in malfunction and there is no need for pletely safe for humans. Additionally, it is this BWMS sector means that we have neutralization prior to discharge. engineered from renewable materials, read- been able to start increasing additional The first Ecochlor BWMS was installed ily biodegradable and leaves no residue or environmental protection and crew safety in 2001. Since that first installation Eco- hazardous waste product behind for cleanup technologies to our portfolio. In 2019, chlor has not had to make any funda- or disposal. It has been formally designat- Ecochlor launched its global maritime mental changes to the original BWMS ed as a global “Best Practice Standard” by sales alliance with NanoVapor. design. Nevertheless, the company’s Shell Oil for degassing of underground petrol NanoVapor is an alternative technology engineers are always seeking opportu- tanks for maintenance and inspection. for the rapid gas-freeing of fuel tanks and nities to reduce costs while maintaining equipment reliability and other tanks, which significantly reduces time and costs whilst the long-life of the system. enhancing crew safety during man entry. Due to the health risk to Ecochlor’s system reliability comes down to the choices that the crew and fire /explosion risk on the vessel, I believe that shipownengineers make when designing and specifying the system’s ers will appreciate having a safer, environmentally-friendly option components. They make sure that suppliers understand the ship for the crew but will also look at the savings generated by the up operators’ requirements and the nature of the environment that to 90% less time it takes to gas-free tanks! the equipment will be operating in. This way the company can con- The NanoVapor unit is simple to use and operate along with an fidently guarantee that its systems are ‘fit for purpose’ all the way onboard twin tool compressor. The TankSafe™ technology is down to the component level. non-toxic, non-reactive and completely safe for humans. AdditionAlong with offering a reliable system, Ecochlor has gone beyond ally, it is engineered from renewable materials, readily biodegradthe service management of other manufacturers by providing able and leaves no residue or hazardous waste product behind for oversight of every ballast operation of our BWMS on board a ves- cleanup or disposal. sel – our current operational levels are at 98%. NanoVapor’s Vapor Suppression Systems have been successfully applied across the transportation industry, including commercial NAFS: As Ecochlor is growing quickly, it is increasingly obvious aviation, retail underground tanks, and ocean /inland marine. It that the role of well-qualified and well-prepared personnel to has been formally designated as a global “Best Practice Standard” assist, is vital. Could you please tell us a few words about the by Shell Oil for degassing of underground petrol tanks for mainteimportance of your people to support the daily operations to the nance and inspection.
highest level of customer support? NAFS: Please tell us α few words about your cooperation with
P.S.: This year we boosted efforts to expand our global Service Euploia Drydocks and Services? capabilities by hiring a new Vice President of Global Services, Michael Madely. Mr. Madely has over 30 years of experience in P.S.: Ecochlor’s agent in Greece is Euploia. Euploia represents a senior management positions in both Commercial and Techni- number of high-quality maritime product lines and through this cal roles in the maritime industry. At Ecochlor, he will lead and they have been able to assist Ecochlor in reaching out to Greek manage the operation and growth of Global Service Support and shipowners. Charis Valentakis is Euploia’s Managing Director, Chemical Supply Operations to meet the needs of the rapidly bringing more than 30 years of maritime experience in Greece to expanding vessel fleet equipped with Ecochlor’s BWMS. Ecochlor. After six years of collaboration there is a great synergy Under Mr. Madely’s leadership, we have expanded our chemical between the two companies with strong support for the Greek service resupply hubs and spare parts supply network in Singa- clients with both companies. pore along with further plans to develop more locations that align Contact Charis Valentakis, Managing Director at +30 210 with the needs of our client-base. 9400660, greece@ecochlor.com or ecochlor@euploia.com
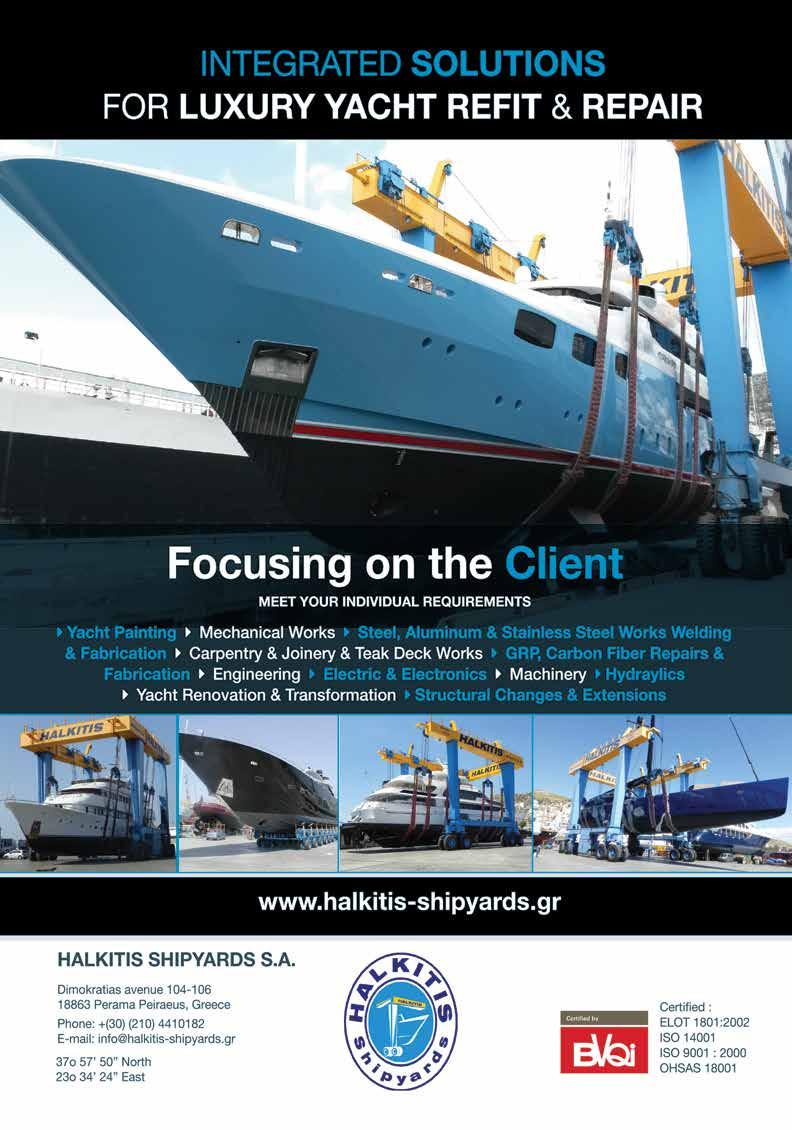
Andrew Marshall Ballast Water Treatment: Chlorine Dioxide is NOT Chlorine Andrew Marshall, is VP of Business Development, Ecochlor
The chemical compound “chlorine dioxide” is often mistaken for chlorine (bleach) but their disinfection capabilities are very different. Understanding these key differences are critical when choosing a ballast water management system (BWMS) for your ship.
Treatment Effectiveness
Chlorine and chlorine dioxide are both oxidizing agents. However, chlorine dioxide is more selective in its reactions, making it effective at lower concentrations, resulting in it having 2.6 times the oxidative power than chlorine! This means that ships need to use almost triple the amount of chlorine to achieve the effectiveness of chlorine dioxide. Chlorine dioxide reacts with living cells by first penetrating the bacterial cell wall and then reacting with the material within the living cell in order to kill the organism. Chlorine dioxide has very limited reactions with organic matter present in ambient water and works exceptionally well where high levels of organic materials (“dirty” or turbid waters) are anticipated to be present. This greatly reduces the formation of disinfection by-products and means that chlorine dioxide treatment effectiveness is not affected by turbidity, salinity or temperature. On the other hand, chlorine reacts with almost any organic material (living and non-living) such as oil, algae, sediments, etc., This means that waters with high levels of organic matter can increase the background oxidant demand for chlorine, leaving less available to treat living organisms in ballast water or requiring an increased chlorine treatment dose. Due to the types of reactions that chlorine has with both organic and inorganic compounds, chlorine has greater potential to form undesirable by-products in the water. These by-products can pose toxicity risks to both aquatic organisms and human health.

Neutralization of Treated Water
The higher levels of chlorine required to treat ballast water comes with limitations as neutralization is required to ensure chlorine can be discharged at a safe level. Because of its highly reactive nature with living organisms and low chemical dose, chlorine dioxide does not require neutralization or re-treatment (as is the case with UV) prior to discharging treated ballast water because it naturally decays to a safe discharge concentration.
Solubility and Disinfection Capacity Influences of pH and Water Temperature
Solubility is another important advantage in the use of chlorine dioxide for water treatment. Chlorine dioxide is 10 times more soluble in water than chlorine, making it faster-acting (especially if the water pH rises), even in cold water conditions. Chlorine dioxide effectively operates in a broader range of pH levels, ranging from 4 - 10, whereas chlorine has an optimum treatment range of 6 - 8.
Conclusion
The chlorine dioxide treatment technology is extremely powerful in low doses and is not affected by varying water conditions, such as turbidity, salt, temperature or pH. Chlorine dioxide is generated as-needed at the point of use making it an extremely safe, cost-effective and far more effective technology for the treatment of ballast water.
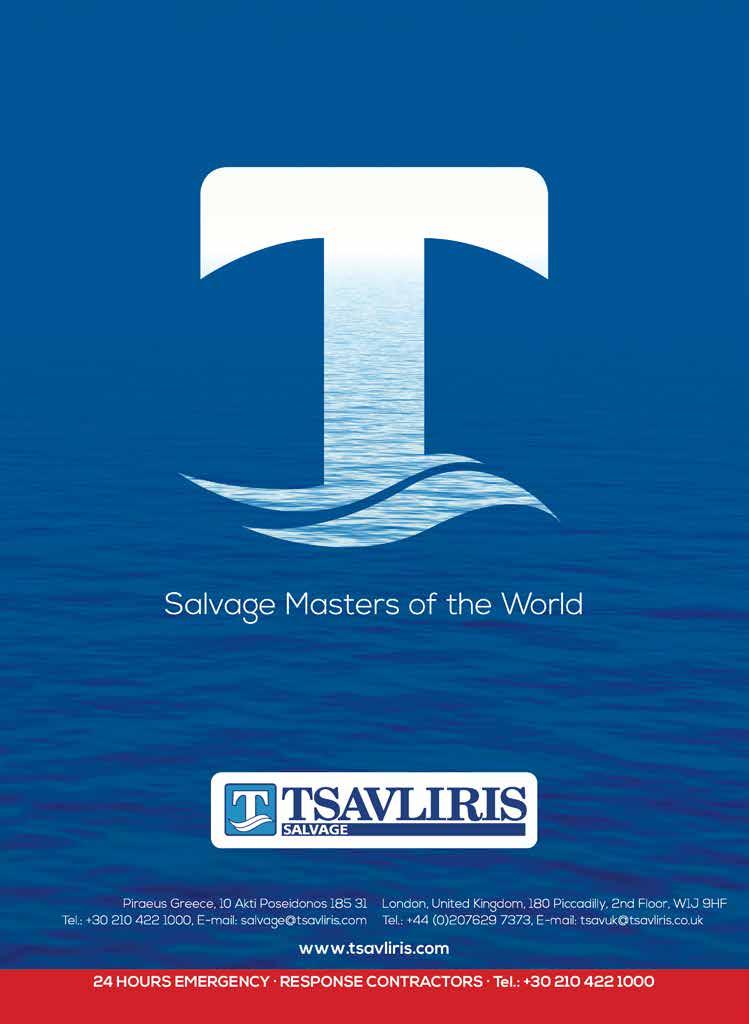
BWMS Coordinating BWMS Retrofit Logistics Can Be Challenging in 2021
Ballast water management system (BWMS) retrofits will face dry-docking schedule issues due to COVID-19 and as drydock projects triple in 2021.
Generator and parts ready for shipyard
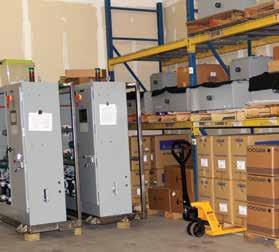
Logistics Team reviewing comprehensive process for an Operations Request

Edwin Michaud, Logistics Coordinator, loading a crate of GRE piping onto our storage racks
This year shipowners and BWMS manufacturers have been faced with many problems when coordinating the logistics of retrofits. This has been due in part to COVID-19. Early in 2020 retrofit schedules were disrupted at many shipyards because of shutdowns and manpower shortages due to mandatory quarantines. Additionally, travel bans affected the delivery of BWMS equipment and prevented manufacturers from ensuring that human resources were available to get things back on track. To minimize disruption to its customers Ecochlor monitored the changing business situation right from the start of the pandemic, and kept in daily contact with suppliers and customers alike to ensure that the impact to clients was minimal. Now, almost a year later, the BWMS retrofit dry-docking schedules are back to normal but that doesn’t mean that it will be “smooth sailing ahead.” BWMS installations are expected to triple in 2021, so it is more important than ever for shipowners to plan their installations. As project schedules are rearranged, lead times for booking slots in shipyards are increasing and the availability of space will likely decrease. Even the most meticulous planner risks ending up with results that are far from satisfactory. Justin Knight, Director of Operations, coordinates the logistics for delivery of all Ecochlor equipment for installation worldwide. One of the challenges he faces is matching up the drydock schedules and shipyard location for the system delivery. Mr. Knight shared, “Ecochlor understands that plans can change. Last-minute notifications regarding changes to drydock schedules or locations can create logistical problems and we always want to ensure that we meet the shipowner’s project schedule.” Looking over the extensive experience Ecochlor has gained over the years - with respect to producing and supplying BWMS for retrofit - Mr. Knight offers some suggestions to make certain that the arrival of BWMS equipment at the shipyard is as trouble-free as possible. He recommends that shipowners: 1. Communicate your dry dock schedule, location and logistic contact to the manufacturer’s installation team as soon as possible. 2. Plan to have the BWMS manufacturer handle shipping of the equipment to allow for seamless transportation and delivery. 3. If picking up the equipment, plan to do so as soon as it is complete and packed. For items held longer than 2 weeks, most manufacturers will need to move the equipment to a storage facility which may generate additional charges and could cause delivery delays when the owner is finally ready to install the equipment. After feedback from shipowners Ecochlor has expanded their after-sale retrofit options to better provide turnkey logistic solutions to allow for an easier, streamlined installation. These options include: • Door to door shipping – provision of ocean or air shipping, customs clearance and equipment storage when required for delayed dry dock schedules. • Installation oversight – provisions of Ecochlor personnel to oversee the Ecochlor System installation and provide support to the integration engineering firm and shipyard personnel to ensure a high-quality installation. Ecochlor recommend that shipowners take advantage of this options, in particular if the integration engineers or shipyard performing the project have limited experience with Ecochlor retrofits. Installation attendance is provided on a daily basis, thus the Ecochlor installation team can oversee the entire installation process, or they can be onsite to oversee certain activities to ensure the system is installed successfully. Additionally, if allowed by Class or the vessel’s Flag state, our commissioning team can be on-hand to review biological efficacy commissioning testing. This provides an experienced set of eyes to view the crew’s system operation as well as the lab during commissioning testing. In the event of a system failure, having an Ecochlor engineer in place to observe the process can be an important resource for the owner in case of a dispute with the testing lab. • Bulk purchasing power – purchase and delivery of the owner-supplied materials required for the installation of the Ecochlor System which includes Alloy 20 and 316L stainless-steel piping. Steve Candito, CEO of Ecochlor believes that every Ecochlor installation is a learning opportunity for the company. He further explained, “our team has been able to draw on a vast amount of experience - more than 19 years and over 180 vessels since our first retrofit - to better prepare for, and continually improve our procedures for any future BWMS installations for our clients.”
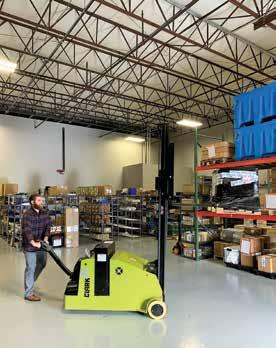
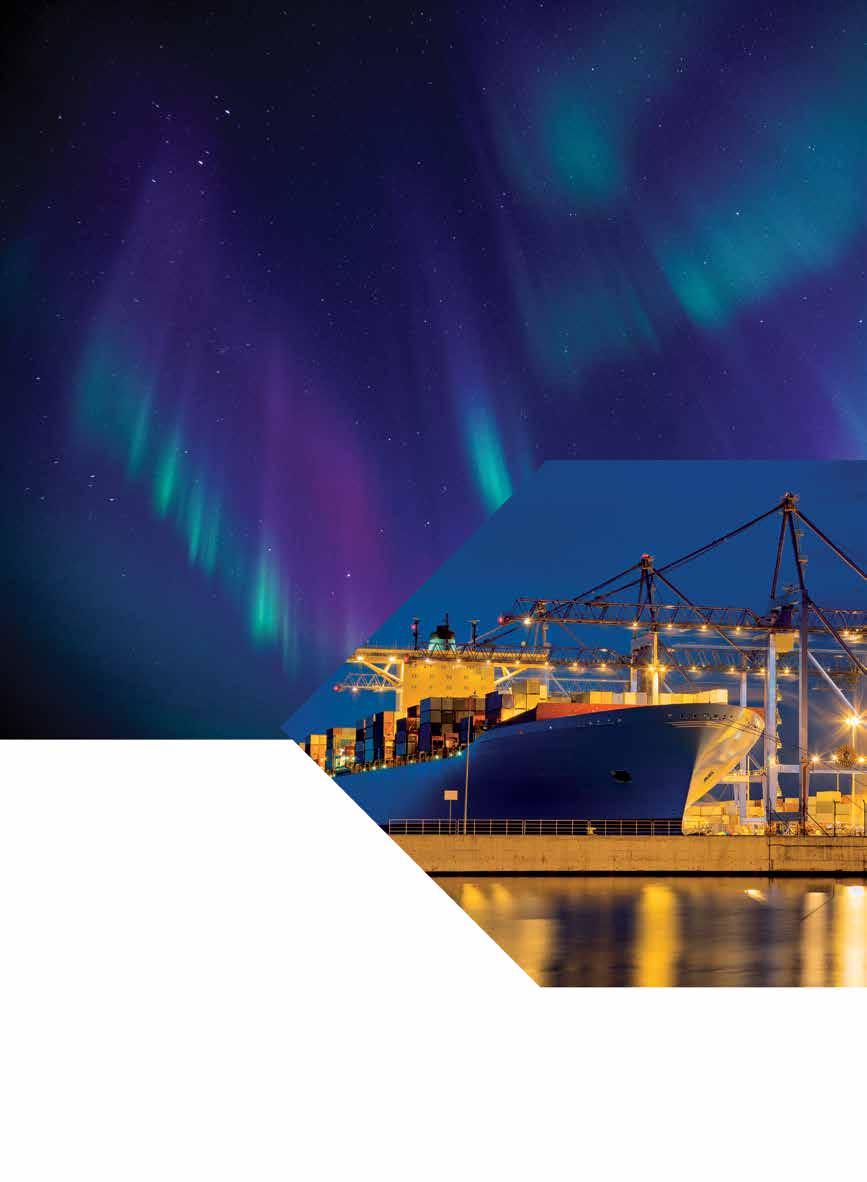
In-house Training in 2019 by Max Hasson, Manager of Service Operations
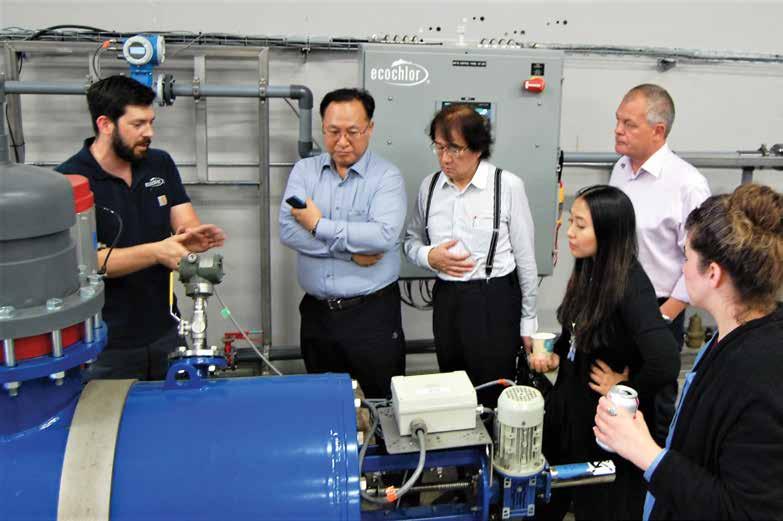
After the Retrofit: Training is one of the Single Most Important Issues to BWMS Compliance
Shipowners have a wide range of views about the importance of crew training on their new ballast water management systems (BWMS). At a minimum, the Chief Engineer, First Officer, and Second Engineer should all be able to run the system and assist any other crew members in its operation. There is a learning curve for each BWMS, some are more complex than others and require more in-depth crew training. This need is especially acute when performance is conditional on understanding the system’s limitations in variable water conditions such as salinity, temperature, and turbidity. Proper training ensures a smoother operation at a lower cost. Depending on the owner’s choice of BWMS manufacturer, there may be a range of training options (beyond commissioning requirements) that are available for crews, including handson training centers, online tutorials and even portable units that simulate system operation.
Ecochlor’s Training Options
Prior to the end of an Ecochlor ballast water management system (BWMS) installation period, the Ecochlor commissioning engineers provide both classroom training as well as hands-on operational training. Classroom training is usually held sometime within the first 15 days of dry dock and runs approximately two hours. The hands-on operational training is typically one of last items completed prior to leaving dry dock. Shipowners are strongly encouraged to allow enough time to complete this training with additional time allowed to compensate for biological testing requirements expected to be enforced, as part of the commissioning certification, by October 2021.
After the shipboard hands-on training at commissioning, Ecochlor can also offer training at the ship’s first full ballast operation, allowing for a more realistic, stressfree learning experience with the engineers on board the vessel. Additionally, Ecochlor provides an interactive training program produced by MARPOL Training Institute, Inc. to each vessel with the system on board. This software training program can be installed on the ship’s computer network or given to an owner’s facility for access on their server during corporate training sessions. At the completion of each training session by the crew member there is a standardized test that provides a record for management to demonstrate that the seafarer has successfully completed the training program.
In addition to the above options, Ecochlor has developed a portable Human Machine Interface (HMI) training kit that allows familiarization with the BWMS operation utilizing process simulation and a full-size HMI panel. Various operating and alarm conditions can be replicated to provide the experience of using an Ecochlor system in a real-world situation as well as a response to normal and abnormal variations in
Ecochlor Training in 2019 with Ecochlor Service Team and AquaMarine Engineers
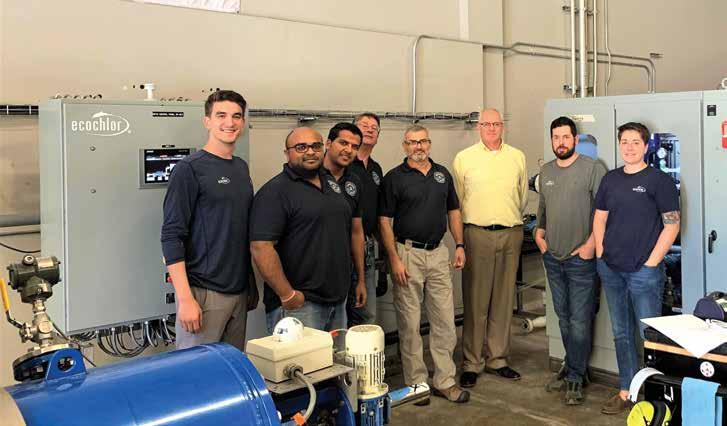
operating conditions. The Ecochlor sales team and service engineers often use this simulator for local onsite training but it is also available to shipowners so they may have in-house capability to continue crew training at their own facilities. Lastly, Ecochlor has a Training Center located in the USA that provides classroom instruction on function, safety, troubleshooting and maintenance of the Ecochlor BWMS. During the hands-on part of the training there is an operating Ecochlor BWMS and wet filter, as well as a dry filter on the premises - allowing for the equipment to be disassembled to view inner workings and functions. Ecochlor encourages shipowners to take advantage of these training resources as it represents an ideal situation for everyone; the crew is better able to assist with the installation and they are more likely to troubleshoot any issues once at sea. Earlier this year, Ecochlor sponsored a crew training for a shipowner that owns a fleet of oil tankers. Manager of Service Operations, Max Hasson explained, “The biggest takeaway [for the crew] was getting a jump on learning about the new equipment that was going to be or was recently installed on the vessel that they sail on. …we all agreed that this was a huge advantage over crews who have no idea what the system is about until they are already on board and then trying to figure out how to operate it. Some of the owner’s technical office staff also attended so that they would have a better understanding of the system to best assist the crews on board whenever they are needed.” “Onsite company-wide training sessions have taken place in Turkey and Greece at ship management company offices,” shared Tyler Harvey, Technical Manager. “This training was offered to both sailors and the technical department personnel giving them the opportunity to ask questions about the Ecochlor BWMS and get familiar with our equipment.” For Ecochlor, crew training also continues post-commissioning with regular periodic BWMS instruction after the system is handed over to the crew. This follow-on training, provided by the Ecochlor Service Team, is offered two times a year during chemical resupply so that new seafarers to the ship can learn the BWMS and existing crew members’ knowledge is refreshed. Continuous training for the crew helps to guarantee continued safe and reliable operation of the BWMS for years to come; the more comprehensive and regular the training offered, the better the operational outcomes.
Training Crucial for an Efficient BWMS
According to Commissioning Testing of Ballast Water Management Systems, a white paper published by SGS Global Marine Services, they noted one major issue during the commissioning test was, “crew members reported receiving limited training in the use of the BWMS. In fact, the commissioning itself was often the only training given to the crew prior to sailing.” Their conclusion was that it is extremely important that the crew is aware of any limitations of the BWMS and safety requirements both for the smooth operation of the system as well as to ensure compliance during port inspections of the system.
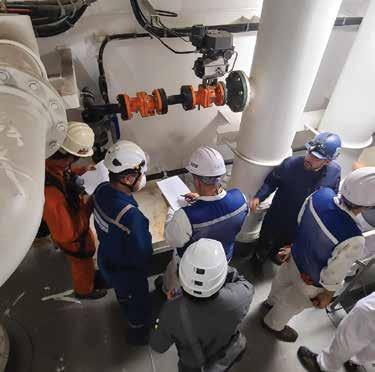
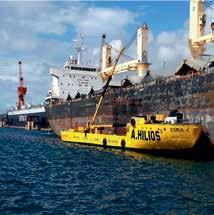
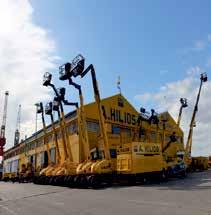
BWTS “Best in Class” BWMS Service and Customer Support
Mick Madley, VP Global Services
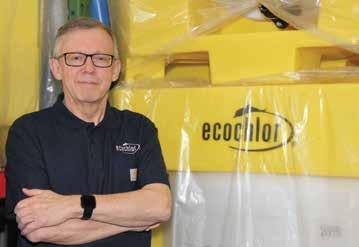
One of Ecochlor’s initiatives in a company-wide expansion has been to invest in hiring the right people at the right time. As part of this initiative, Michael Madely was appointed to serve as VP, Global Services with a focus on bringing a level of service and customer support to Ecochlor’s clients that is “Best in Class” in the maritime industry. “The expansion of our service locations and chemical supply capabilities are intended to provide highly efficient and streamlined service support to our customers. After close consultations with shipowners regarding current and potential vessel operations, we are making sure that we place service and chemical refill capabilities at strategic ports relevant to their trading routes. We currently have our own service engineers located throughout the USA, Europe and Asia, and are continuing to strengthen our in-house team, supported by carefully selected Ecochlor-trained authorized installation and service providers,” explained Mr. Madely. “Currently,” explained Tyler Harvey, Installation Manager, “our Ecochlor engineers in Europe are handling installation project supervision and commissioning across Europe and the Middle East. Our employees in South East Asia and China assist with logistics, mechanical support and commissioning. To provide additional local assistance, Ecochlor is in the process of appointing three new Regional Service Managers in China, Singapore and Europe. To support services in China, Bob Nash was recently selected as the new Installation and Commissioning Manager. He will play a lead role in discussions and negotiations with the shipyards and our customers in the region.” “We have a diverse team at Ecochlor, our recent hires come from different backgrounds than are typically found in a traditional ballast water management system (BWMS) manufacturing and service firm. Our diversity is an asset, giving us different perspectives and unique solutions to any challenge we face,” added Justin Knight, Director of Operations. The first of many planned locations for Ecochlor’s spare parts support network outside the United States has been established in Singapore. The end goal is to have spare parts located in the three major time zones – Asia, Europe and the USA – in order to provide real-time response to the customers’ requirements; facilitating maximum system operation with minimum downtime. Additionally, Ecochlor moved its Corporate Headquarters to a new
Jonathan Perlich, ships spare parts to Singapore
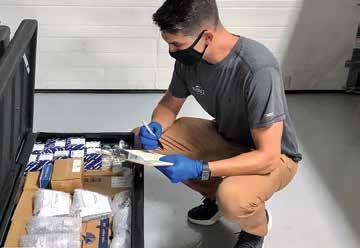
facility in the USA to accommodate their fast-growing team of marine engineering professionals. This new location has provided more
space for the expansion of the engineering department as well as a dedicated training facility that has a full-size BWMS in place for
customer use. Currently, Mr. Madely is directing his focus on expanding Ecochlor’s crew training opportunities. He offered, “across the industry there is a consistent problem with crew training. The original crew is trained to operate the BWMS, but crew onboard the vessel changes frequently and the new seafarer often doesn’t have the necessary training and experience to take over operation of the System.” Ecochlor recognized this as an industry-wide problem and has implemented many training options that are available to their customers. In addition to training at commissioning, the service team can be available to train and assist the crew at their first full ballast operation. An interactive software training program is provided to the ship for use with new crew, which can be installed on the ship’s computer network or used at the owner’s training facility. The training center, located at corporate headquarters in Connecticut, USA, includes classroom education as well as hands-on instruction with a full Ecochlor BWMS replicating real-world situations at sea.
Conclusion
Ecochlor is reshaping the way the industry is thinking about BWMS manufacturers. This mindset is trending from the traditional equipment vendor models to one in which the highest priority is to provide both an easy-to-use, reliable system, but also focuses on having in place robust after-sales services and support. This works toward ensuring compliance for every shipowner that has an Ecochlor system on board their fleet of ships.
CONTACT INFORMATION:
Charis Valentakis, Euploia’s Managing Director at +30 210 9400660 ecochlor@euploia.eu or greece@ecochlor.com In addition, considering the importance of the Greek market, Ecochlor established an office for Europe & the Middle East in Athens, Greece. Contact information is +30 210 7005836 or southerneurope@ ecochlor.com.
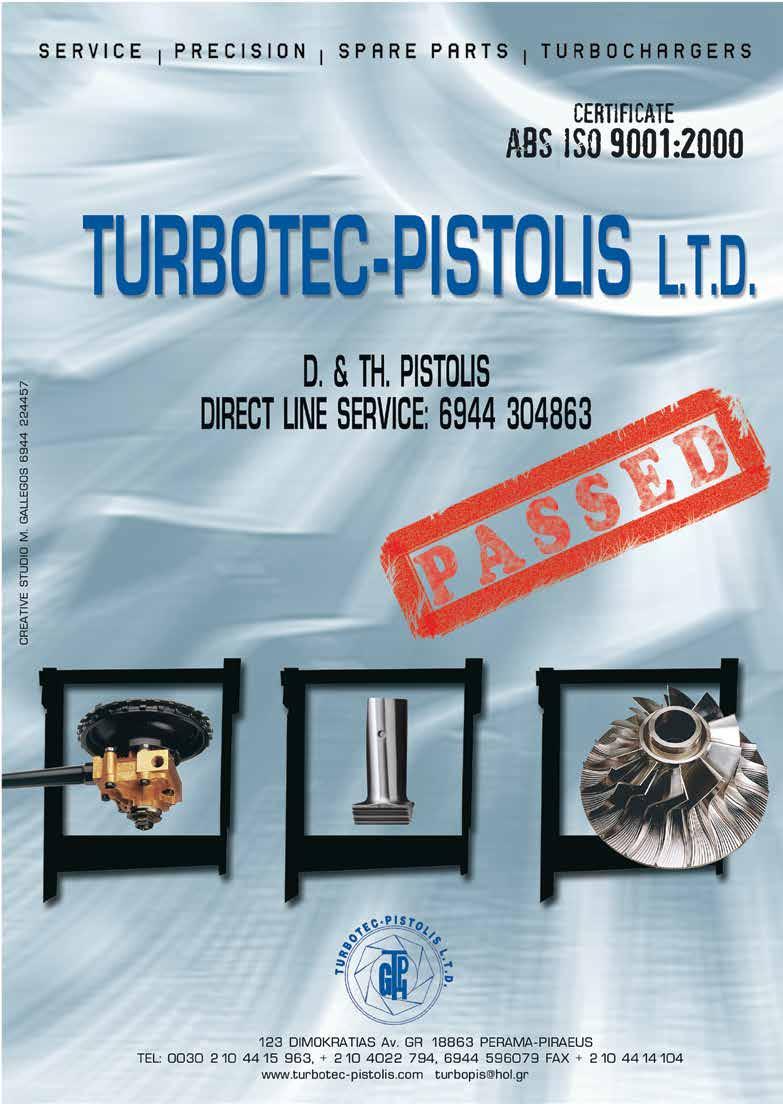