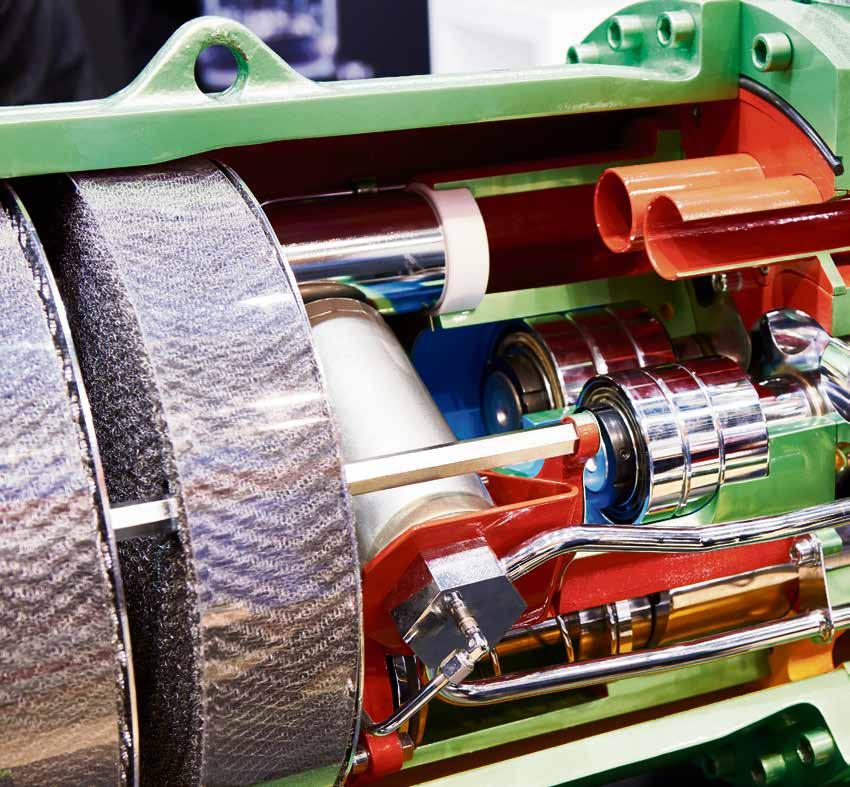
9 minute read
VİDALI KOMPRESÖR KABİNLERİNİN SOĞUTMA PERFORMANSININ İYİLEŞTİRİLMESİ
from Air World Türkiye_Sayı 15
by Eda
Ali GÜRBÜZ Teknik & Ar-Ge Müdürü Sarmak Makina Kompresör
VolkAn GEZGİnCİ Bakım & Kalite Kontrol Mühendisi Sarmak Makina Kompresör
Advertisement
Birçok sanayi sektöründe kullanılan vidalı hava kompresörleri ve basınçlı hava, gün geçtikçe daha önemli ve etkin bir rol oynamaktadır. Basınçlı havanın kullanımı, bir enerji kaynağı olduğundan; verimli, kaliteli ve devamlı olmalıdır. Bu yüzden, ele alınan vidalı kompresörler her geçen gün daha verimli, kaliteli ve kullanıcı isteklerini karşılayabilir nitelikte üretilmelidir. Buna bağlı olarak üreticiler, kompresör ünitesini en optimum hale getirerek, kurulacak basınçlı hava sistemini geliştirmektedir. Proseslere enerji sağlayan kompresörlerin kalitesi ve kesintisiz basınçlı hava üretebilmesi, sayısız yan dalları olan üretimlere büyük katkılar sağlayacak ve zincirleme olarak son kullanıcıya kadar ulaşacaktır.
Bu projede, gerekli ölçümlerin yapılabilmesi, HAD (Hesaplamalı Akışkanlar Dinamiği) analizleriyle karşılaştırılabilmesi ve elde edilen gelişmelerin uygulanabilmesi açısından; 75 kW gücünde gerçek bir kompresör üretilmiştir.
Optimize edilmemiş prototip üzerinden, hız, sıcaklık ve akış değerleri ölçülmüş ve daha sonra HAD analizleri (örneğin ünite içindeki akışların hangi komponentleri nasıl etkilediği ve verimsiz noktalar) yapılarak, prototip üzerinde değiştirme metodu kullanılmıştır.
Prototip üzerinde, sıcaklık sensörleri, hava hız ölçümü, güç analizörü kullanılmış, kompresör ana kumanda kartının verdiği basınç, sıcaklık değerleri değerlendirilmiştir.
Optimizasyon sonrası, prototip yine ISO 1217-Ek C test kabul koşullarına göre test edilmiş ve bahsi geçen parametreler ölçülmüştür.
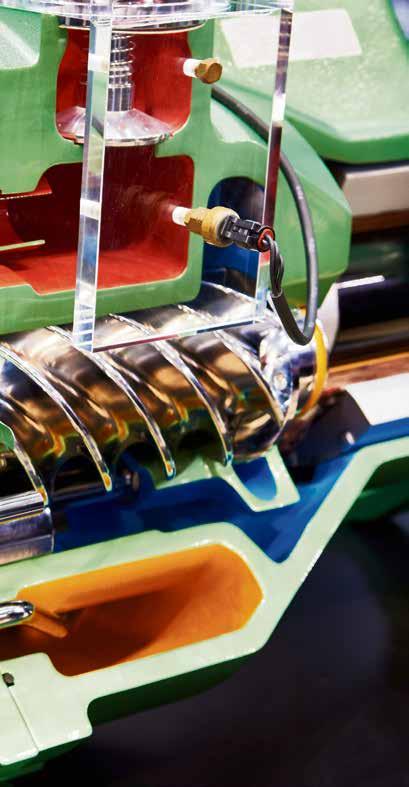
Deney düzeneğinin tanıtılması
Vidalı hava kompresörlerde; basınçlı hava çevrimi, yağ çevrimi ve soğutma çevrimi başlıca çevrimlerdir.
Soğutma çevrimi genel olarak, ‘Hava ile soğutma’ ve ‘Su ile soğutma’ olarak çeşitlendirilmiştir. Su ile soğutma tercih edilirse; basınçlı hava ve kompresör yağı, su ile soğutulabilir (basınçlı hava ve yağ için ayrı ayrı ısı eşanjörlerinin -su soğutmalı- ünite içine yerleştirilmesiyle), fakat kabin içi yine hava ile soğutulmalıdır.
Söz konusu çalışmada ‘hava soğutmalı vidalı kompresörler’ ele alınacaktır, dolayısıyla, basınçlı havanın, yağın ve kabin içinin; atmosferden çekilen hava ile soğutulduğu sistem incelenecektir. (Basınçlı hava ve yağ, farklı radyatörler kullanarak ve bu radyatörler üzerinden yeterli soğutma havası geçirerek soğutulmaktadır).
Yaptığımız projenin amacı; kabin içi yerleşimi optimize ederek ‘verimli bir soğutma’ ve ‘enerji tasarrufu’ sağlamaktır. Bahsettiğimiz hava soğutmalı vidalı kompresörlerde; yukarıda geçen tüm çevrimler kabin içinde yer aldığından; önemli bir denge oluşturulmalıdır.
Özetle denge konusu şu şekilde tarif edilebilir: Yapılan tasarıma göre kabin için soğutması fazla olursa; kurulu fan kapasiteleri sabit olduğundan; kabin içinin fazla soğutulması; kabin içinden gelen geçiş alanlarının fazla tutulması ile mümkün olur. (Bakınız Şekil 1)
Şekil-1 Optimize edilmemiş kabin ve radyatör soğutma
Basınçlı hava ve kompresör yağı gerekli düzeyde soğutulamayabilir. Kabin içi az, basınçlı hava ve yağ fazla soğutulursa (soğutma havası büyük ölçüde radyatörlerden geçirilirse); bu durumda da vida bloğu ve elektrik motoru yeterince soğutulamayabilir. Her iki bölüm (kabin içi ve radyatörler) birden çok soğutulmak istenirse; daha güçlü fanlar ve dolayısıyla fazla enerji maliyeti gerektirir.
Büyük fanların ve fan motorlarının kullanımı, enerji maliyetlerinin artmasının yanında; tasarım zorlukları doğurur. (Örneğin: kabin ölçülerinin çok büyük olması, estetik olmayan, yerleşimi zor ve hantal kabin tasarımı vb.) Aynı zamanda yatırım maliyeti de artar. Radyal fan kullanılıyorsa, yatırım maliyeti artar, kabin içi yerleşim daha zor olur ve/veya fan adeti artabilir. Aksiyal fan kullanılıyorsa; gürültü seviyesi artar ve kabin boyutları büyür.
Dolayısıyla; kompresör iç tasarımı ve soğutma fanları öyle ayarlanmalıdır ki; aşırı büyük fanlara ihtiyaç kalmadan, kabin içindeki elektrik motoru, vida bloğu ve yağ tankını yeterli ölçüde soğutulabilmelidir. Öte yandan, radyatörler üzerinden yeterli soğutma havası geçirilerek basınçlandırmadan dolayı ısınan hava ile kompresör yağı da istenilen düzeyde soğutulabilmelidir. (Bakınız Şekil 2)
Şekil-2 Optimize edilmiş hava ve yağ radyatörlerinin soğutulması
Kabin içi soğutmanın etkisi elektrik motoru için hayati önem taşır. Sıcaklık arttıkça, motor verimi belirgin şekilde düşer ve kullanım ömrü azalır. Motor verimi de enerji kullanımını direkt olarak etkilemektedir.
Kabin içi soğutmanın diğer bir etkisi de, kompresör yağının toplandığı separatör tankının ve yağın soğutulmasıdır. Çünkü, vida bloğunda basınçlandırılan yağ ve basınçlı hava; vida bloğu çıkışında maksimum sıcaklığına ulaşır ve bahsedilen separatör tankında toplanır. Eğer bu tank ve içindeki basınçlı yağ iyi soğutulursa; yağ radyatörünün yükü azaltılır

ve maksimum sıcaklığa ulaşmış kompresör yağı; bu sıcaklıktan kısa sürede kurtulur. Dolayısıyla, yağın deforme olma (örnek: viskosite değişikliği ve/veya fiziksel özelliklerini kaybetme) tehlikesi de bertaraf edilmiş olur. Özellikle mineral kompresör yağları için bu etki çok önemlidir. Aynı zamanda, maksimum sıcaklığa ulaşmış kompresör yağı iyi soğutulamazsa; buharlaşma oranında artış ve buna bağlı olarak yağ separatöründen yeterli oranda ayrışamadan, kullanıcının basınçlı hava sistemine karışma riski vardır. Bu olasılık da; sadece kullanıcının basınçlı hava kalitesini düşürmez; aynı zamanda yağ çevrimindeki azalma nedeniyle, devamlı yağ eklemek gerektirir. Bu ise yüksek maliyetli ve devamlı kontrol gerektiren çalışma koşulları gerektirir.
Firmamızda üretimi yapılan 75 kW gücündeki bir vidalı kompresörün kabin içi mevcut sıcaklık dağılımı ölçülerek kritik noktalar belirlenmiştir. Yapılan detaylı HAD analizleri ölçülen sıcaklık dağılımlarına oldukça benzer sonuçlar vermiştir. Söz konusu olumsuzlukların, bileşenlerin mevcut yerlerini değiştirmeden, farklı karakteristiklere sahip fanlar kullanmadan ve mevcut hava emiş yerlerinin kullanılması ile giderilemeyeceği gözlemlenmiştir.
Yapılan yeni tasarımın, HAD yöntemi kullanılarak gerçekleştirilen akış analizleri ile sınanarak, mevcut olumsuzlukları ortadan kaldırdığı görülmüştür. Bunun üzerine prototip kompresör imal edilmiş, sıcaklık ve güç değerleri ölçülmüştür. Ölçümler, HAD ile elde edilenlere benzer sonuçlar vermiştir. Ayrıca yeni seçilen ve kullanılan fanların toplam gücünün eskisine oranla %23.4 oranında azaldığı görülmüştür.
Sonuç olarak, mevcut kompresöre oranla, daha iyi, değişmeyen ve düşük değerlerde sıcaklık dağılımı ve daha az güç tüketen fanlar ile sağlanmıştır. (Bakınız
Şekil 3)
Şekil-3 Optimize edilmiş kompresör kabin içi soğutma
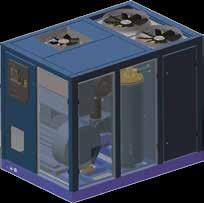
Prototip üzerinde elde edilen bu iyileştirmeler; sadece 75 kW için olmayıp, diğer tüm serilere uygulanabilme özelliğindedir. Vidalı hava kompresörleri, genel olarak, güçlerine göre, belirli gruplarda dizayn edilmektedirler, dolayısıyla; bu projeyle elde edilen
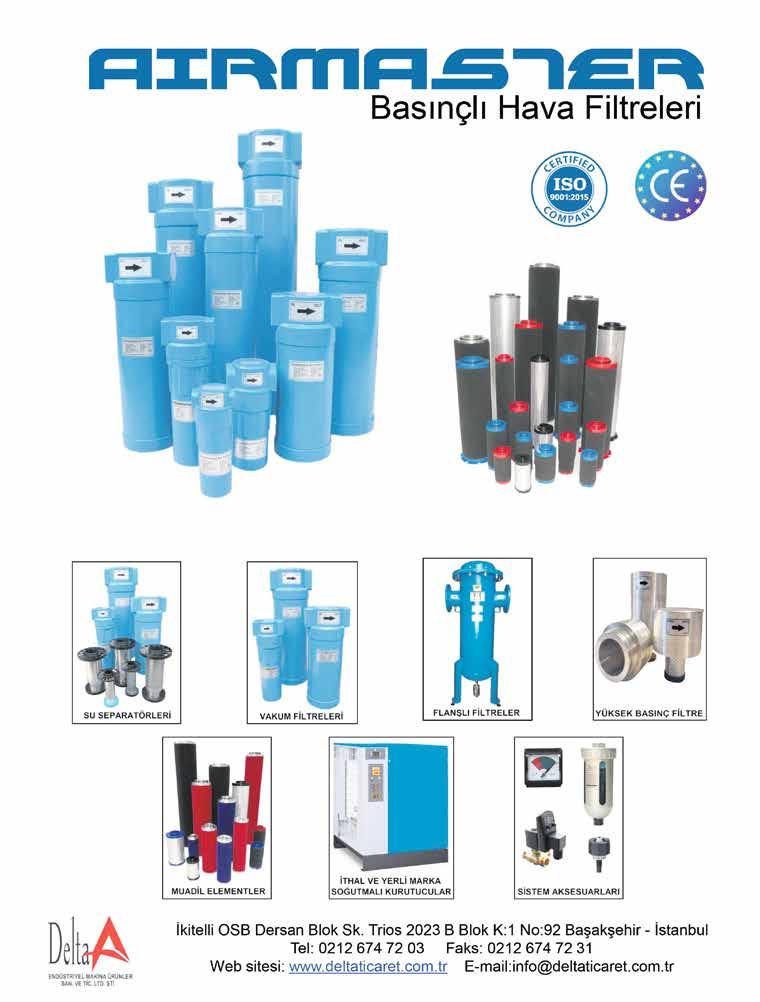
optimizasyon yeteneği, farklı iç yerleşim tasarımına sahip gruplara uygulanabilecektir.
Farklı tasarımlar anlamında sadece büyüyen veya küçülen güçler olarak sınırlandırmak doğru değildir. Kullanıcının çok farklı çalışma ortamları için talep ettiği kompresörler de, yapılacak tasarım değişikliklerini meydana çıkarabilir. Örneğin; aşırı tozlu bir ortam söz konusu ve üretici, kompresör kabin soğutma havası temiz tutabilmek için farklı emiş filtresi (soğutma havası için) kullanmak durumundaysa; bu durumda yine yukarıda bahsedilen gibi bir analiz gerekecektir.
Sonuç
Projenin tüm kapsamı düşünüldüğünde elde edilen somut kazanımlar; herhangi bir ek yatırım yapmadan, mevcut tasarımın optimize edilerek, gerek kabin içi ve gerekse diğer çevrimlerde yer alan basınçlı havanın ve kompresör yağının, optimum soğuması sağlanmıştır.
Üretilen prototiple HAD analizlerinin uyum göstermesi; bu analiz yönteminin, diğer ekipmanlar için de kullanılabilip; fonksiyonlarını daha verimli hale getirebilmeleri (örneğin: daha az basınç düşümü, optimum hava emiş hızı gibi) avantajlarını sağlayacaktır.
ANALİZ 1. DONANIM
Yapılan Hesaplamalı Akışkanlar Dinamiği ( HAD ) analizleri 12 çekirdekli Dell Precision T3610 işlemciye sahip 48 GB RAM’li bilgisayarda gerçekleştirilmiştir. Tarif edilen donanımlar üzerindeki işletim sistemi 64 bit Windows 7 Professional’dır.
2. YAZILIM
Analizler ANSYS / Fluent 15 versiyonunda yapılmıştır.
Yazılımda kullanılan Algoritmalar;
n Basınç Hız ilişkilendirilmesi için SIMPLEC n Ayrıştırmalarda ; Gradient için Green-Gauss Cell Based, Basınç için Standart, Momentumla birlikte enerji ve türbülans denklemleri için Second Order Upwind n Paralel çözücü kullanılmıştır.
3. ANALİTİK ÇALIŞMALAR
Kompresör kabininin havalandırılması amacı ile soğutma havası giriş eleklerinin geometrisini modellemenin kabin çalışmasında kullanılacak sayısal ağ miktarını arttıracağı ve analiz sürelerini uzatacağı ön görülmüştür. Bu nedenle elek geometrisinin giriş debisine bağlı olarak oluşturacağı basınç kaybının Fluent yazılımı içerisinde Porous Jump modeli ile tanımlaması yapılmıştır. Aynı şekilde radyatörler için kullanılan Porous Media sınır şartında Porous Jump sınır şartına benzer bir hesaplama kullanılmıştır.
4. KULLANILAN ELEMAN VE DÜĞÜM NOKTASI, ELEMANLARIN ÖZELLİKLERİ
Sayısal ağ kalite parametrelerinde skewness ideal eleman şeklinden (2 boyutta eşkenar üçgen ve kare, 3 boyutta eşkenar tetrahedral ve küp) bozulmayı ifade eder. Maksimum Skewness değeri için 0.98’den daha büyük değerlerde olan hücrelerin olmamasına, olacaksa kritik bölgelerden uzak ve az sayıda olmasına dikkat edilmiştir. Kompresör makinemizde analiz esnasında oluşturulan sayısal ağdaki minimum skewness değeri 4.00079e-10 iken maksimum skewness değeri 0.8491’dir. Ortalama skewness değeri 0.238 mertebesindedir. (Bakınız Şekil-4)
Şekil-4 Sayısal ağın (mesh) kabin kesitindeki yapısı
5. ANALİZDEN ELDE EDİLEN VERİLER SONUCU PROTOTİPTE YAPILAN İYİLEŞTİRMELER
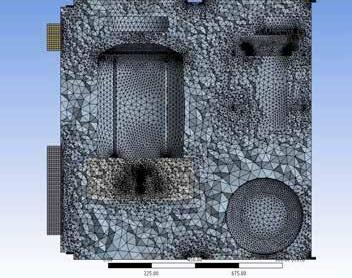
1.
2.
3.
4.
5. İlk tasarımda 2 adet 2.2 kW soğutma fan motoru kullanılırken, yapılan iyileştirmeler sonucu 2 Adet 1.5 kW ve 1 adet 0.37 kw soğutma fan motu kullanılmıştır. Bu sayede soğutma fanlarında toplamda 4.4 kW ‘dan 3.37 kW’a düşülerek % 23.4 enerji tasarrufu sağlanmıştır.
Ana tahrik motorunun eleklerden soğutma havası emişi daha verimli hale getirilmiştir. (Şekil-5 ve Şekil-6)
Kompresör içinde belirlenen kritik 3 noktadan alınan sıcaklık değerleri ile son tasarım ve ilk tasarım kıyaslanmıştır. Alınan sıcaklık değerlerine göre noktasal olarak 8 0C ila 3 0C arasında soğutma sağlanmıştır.
Hava radyatöründen geçen havanın sıcaklığında 0.8 0C soğuma sağlanmıştır. (Şekil-7 ve Şekil-8) Yağ radyatöründe geçen havanın sıcaklığında 3 0C soğuma sağlanmıştır. (Şekil-7 ve Şekil-8)
Şekil-5: İlk tasarım motor soğutma havası emiş
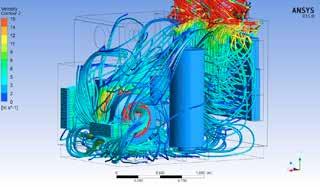
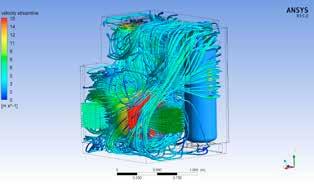
Şekil-6: Son tasarım motor soğutma havası emiş (Optimize edilmiş )

Şekil-7: İlk tasarım radyatör üzeri termal analiz
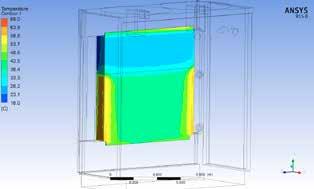
Şekil-8: Son tasarım radyatör üzeri termal analiz (Optimize edilmiş)
Teşekkür
Bu tip projelere destek vererek yüksek düzeyli teknoloji kullanımına olanak sağlayan TÜBİTAK’a, proje aşamalarında katkı sağlayan değerli akademisyen Sn.Prof. Dr.Erkan AYDER’e, danışmanlığına başvurduğumuz değerli akademisyen Sn.Prof.Dr. Hüseyin AKILLI’ya, ANSYS programının kurulup uygulanmasında rol alan Anova firmasına ve projenin dökümantasyonu konusunda destek veren İNOPARK firmasına teşekkürlerimizi bildiririz.
Firmamız Yönetim Kurulu Başkanı Sn. Murat SARACOĞLU ve Başkan Yardımcısı Sn. Aslı SARACOĞLU ÖZER’e ve projenin gerçekleştirilmesinde özverili katkılarda bulunan tüm firma çalışanlarına teşekkür ederiz.
Abstract COOLING PERFORMANCE IMPROVEMENT FOR SCREW COMPRESSORS
Compressed air cycle, oil cycle and cooling cycle are the main cycles in screw compressors. Cooling cycle is divided into ‘air cooling’ and ‘water cooling’ types. If there exists water cooling type; compressed air and oil can be cooled by water; otherwise atmospheric air is used to cool them. To be able to use water as cooling agent; a kind of cooling tower required; but for air cooling type; an additional facility is not required.
Air cooled screw compressor are taken into consideration for our purpose. In air cooled screw compressors; there are two main sections that have to be cooled by air: oil and compressed air radiators (coolers) section and inside of compressor unit: including screw block, electric motor, separator tank and connections. With this project; we have aimed to optimize the cooling procedure for both coolers and inside of the compressor cabin. We have detected that there should be a sensitive balance while cooling the above mentioned sections. Otherwise, some problems can rise due to overheating of oil, compressed air or inside cabin and consequently electric motor & screw block.
Using over-sized cooling fans can cause energy inefficiency, over-sized compressor canopy and higher investment cost. Instead, we preffered to optimize the cooling process by using such ANSYS program which is described as below sections.
A prototype compressor with 75 kW motor power was constructed for this analysis. Detailed CFD (Computational Fluid Dynamics) analysis on prototype has enabled us to decide on the critical points. Consequently, both computer analysis and actual measurements on the physical compressor have matched each other. Obtained values have assessed and suitable modifications are implemented on the prototype.
After optimization; it is realised that not only cooling process optimized, but also a 23.4% of reduction of fan power obtained.
The important result of this project is that; it is also applicable to higher and lower capacity air compressors. Since heat is the most important problem to be eliminated with compressors; efficient cooling is crucial for the whole process.