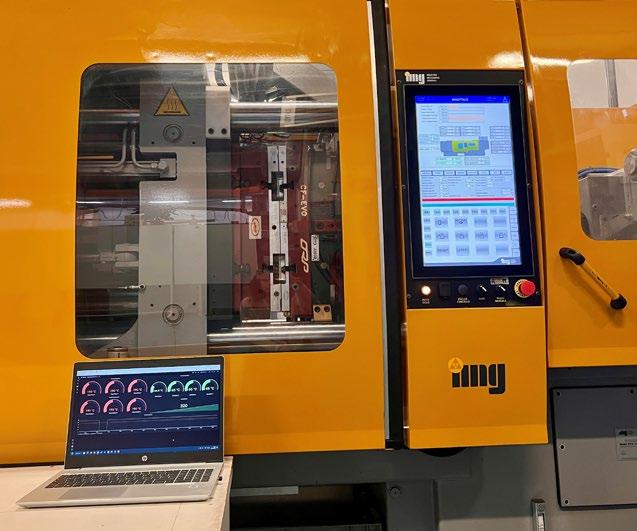
4 minute read
PRESSE A COMPRESSIONE PER GOMMA • RUBBER COMPRESSION PRESSES
l’indirizzo indirizzo IP assegnatole. Successivamente, è stata interrogata utilizzando il protocollo OPC-UA. La prima richiesta è stata l’elenco delle variabili disponibili. Questo è un grande vantaggio legato all’OPC-UA: si richiede alla macchina l’elenco e poi si scelgono i parametri rilevanti da gestire, con la possibilità di aggiungerne in futuro, con il sorgere di nuove esigenze (ad esempio la tracciatura al 100% dei parametri di produzione).
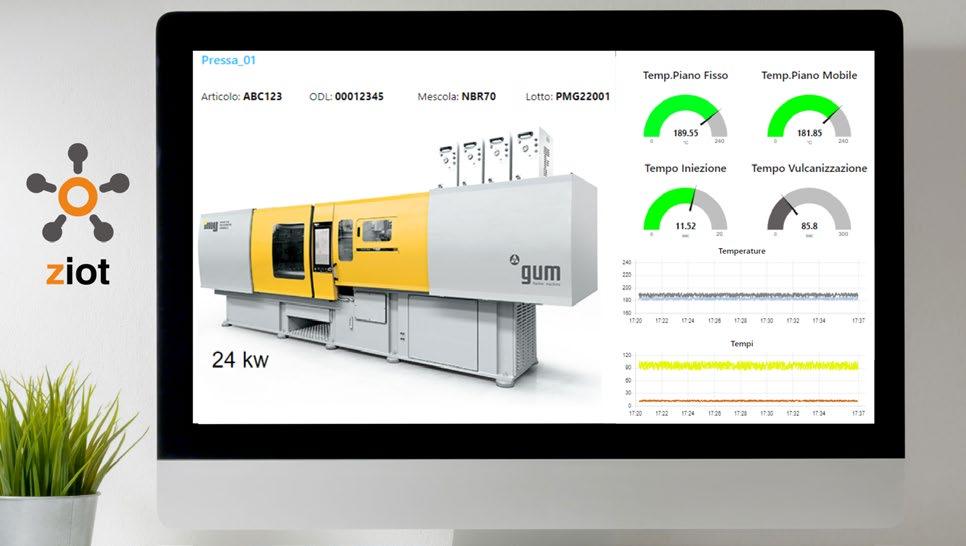
L a pressa IMG rende disponibili tutti i principali parametri relativi a temperature e tempi di ciclo, sia quelli impostati sia quelli rilevati in tempo reale. Dopo aver scelto le variabili significative per il nostro test, Z-IoT è stato configurato per leggerle e memorizzarle nel suo database NO-SQL, adatto a gestire le enormi quantità di dati generati dal processo di stampaggio.
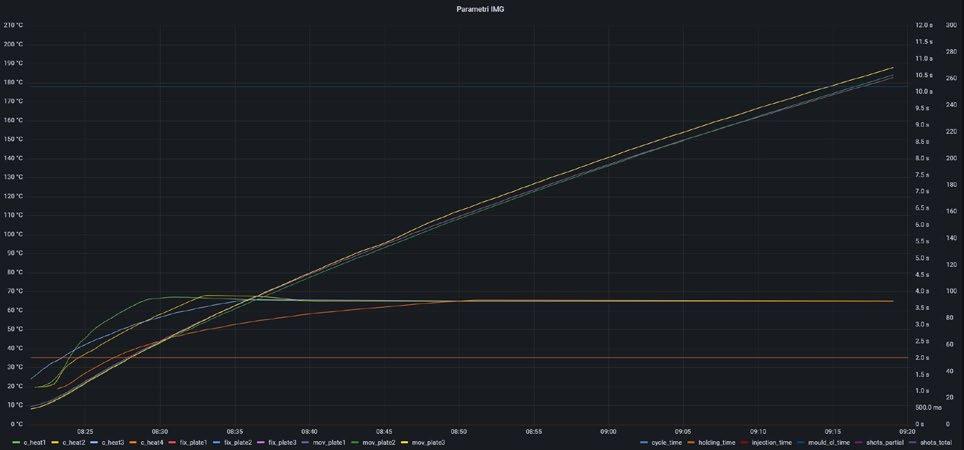
D a quel momento, tutte le grandezze sono visibili nei grafici di Z-IoT, facilmente interpretabili dagli operatori. In questo modo è possibile verificare e confermare la coerenza dei valori letti.
I noltre, dato che Z-IoT registra in continuo i dati, è semplice rilevare il tempo necessario a riscaldare lo stampo. D opo aver definito i parametri da gestire, è stata predisposta la dashboard per visualizzare lo stato della pressa in modo chiaro e intuitivo. Z-IoT consente di realizzare facilmente schermate personalizzate per mostrare le informazioni relative a una o più macchine su un PC o su un grande schermo Andon, con l’indicazione visiva e sonora di allarmi, fermi macchina e altre situazioni anomale. Poiché Z-IoT si connette anche al database di magazzino e produzione tramite i propri connettori SQL, può accedere ai dati degli ordini di lavorazione e utilizzarli per indicare l’avanzamento della produzione, con il numero di pezzi già prodotti e quelli ancora da produrre. Se i dati sono disponibili nel sistema gestionale, la dashboard può indicare anche eventuali ritardi o rallentamenti nella produzione. U n esempio tipico di Andon è la visualizzazione dell’OEE (Overall Equipment Efficiency), che si può ottenere correlando i dati relativi al calendario di produzione con quelli relativi all’operatività e ai fermi macchina e mostrandoli nella dashboard di Z-IoT.
REQUISITI PER LE AGEVOLAZIONI TRANSIZIONE 4.0 RISPETTATI
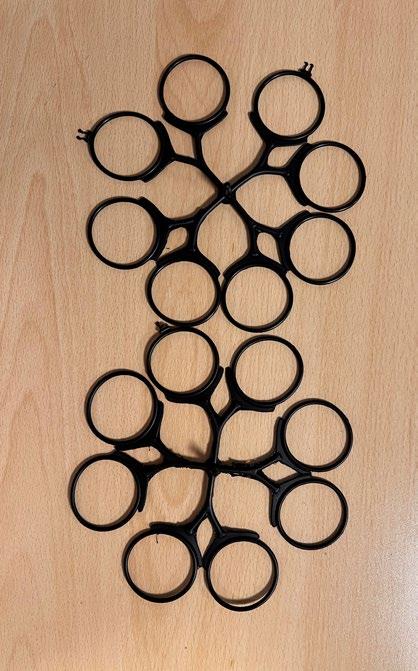
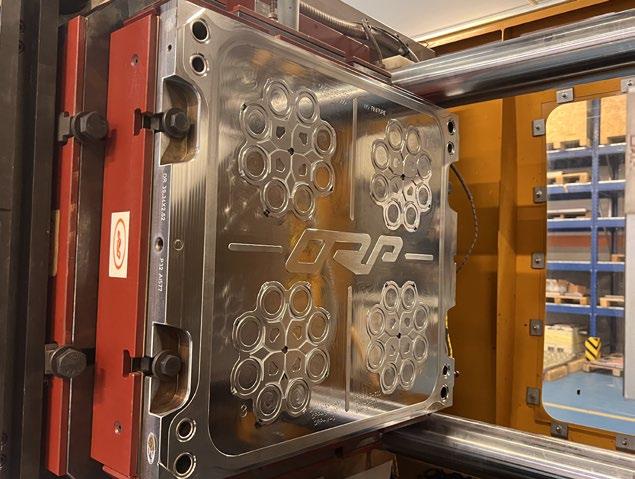
C ome già accennato, Z-IoT si connette ai più diffusi database SQL: Microsoft SQL Server, PostgreSQL e MySQL, per trasferire dati da OPCUA a database e viceversa. In questo modo è possibile soddisfare i requisiti di bidirezionalità per accedere alle agevolazioni previste dalla Transizione 4.0.
N el caso specifico della pressa IMG, si possono trasmettere i dati relativi all’ordine di lavoro, alle quantità da produrre e ad altri parametri. I dati, provenienti dal gestionale aziendale o inseriti direttamente in Z-IoT, sono visualizzati sul pannello operatore della pressa e vengono utilizzati nel conteggio dei pezzi da produrre.
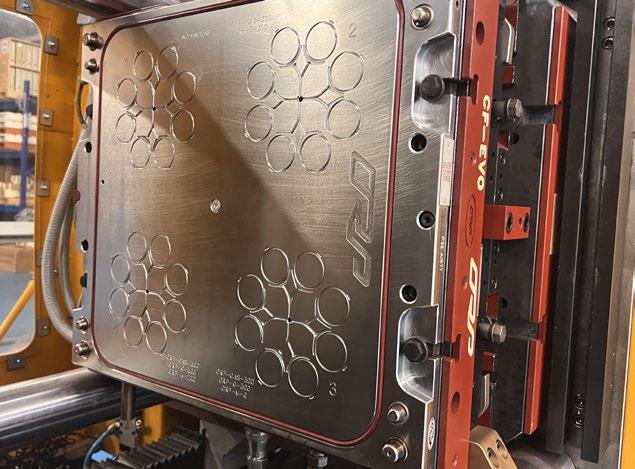
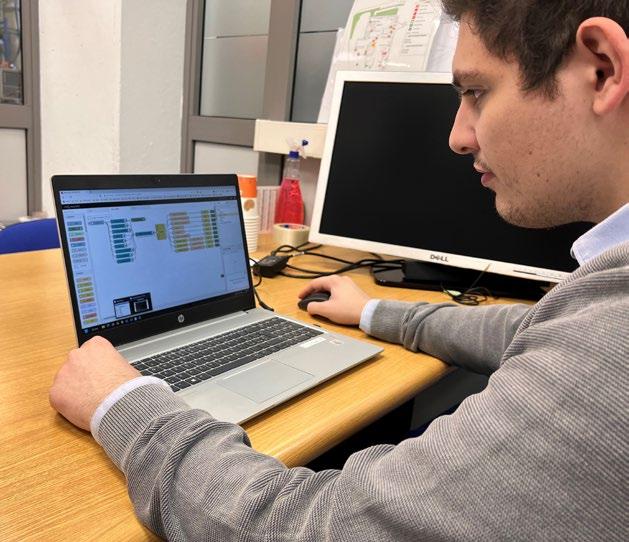
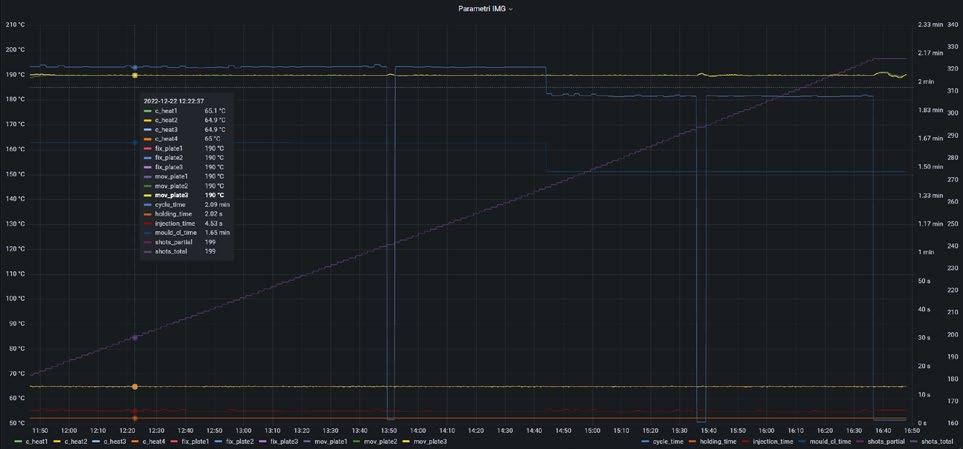
D opo le fasi preparatorie, è iniziato lo stampaggio: è stato utilizzato uno stampo a 32 impronte abbinato ad un canale freddo con 4 ugelli, prodotto da ORP Stampi specificamente per prove, valutazioni e dimostrazioni.
L a pressa ha eseguito oltre 300 stampate in automatico e Z-IoT ha registrato le temperature e i tempi di ognuna di esse. Il sistema registra in continuo i parametri della pressa durante le fasi di attrezzaggio, di riscaldamento, di messa a punto e di stampaggio in produzione, il tutto senza intervento dell’operatore.
È possibile rivedere in seguito i dati registrati, con una sorta di “replay” delle operazioni svolte in un intervallo di tempo, per valutare e verificare gli effetti che la variazione di impostazioni e settaggi ha sulla qualità dei prodotti stampati.
CONCLUSIONI
I n conclusione, da questa esperien - za sono emerse indicazioni utili per effettuare l’interconnessione:
• L a pressa (IMG)
L a normativa di “Transizione 4.0” prevede che al fine della deducibilità il bene sia interconnettibile e interconnesso mediante l’utilizzo di standard di indirizzamento internazionalmente riconosciuti (es. indiriz - zo IP). È fondamentale quindi chiarire con il produttore, al momento dell’ordine, tutti i dettagli relativi alle modalità di interconnessione al proprio sistema informativo. Ad esempio: la pressa supporta nativamente i protocolli necessari oppure ha bisogno di hardware e/o software aggiuntivo? Questo per evitare im - previsti al momento della messa in servizio.
• I l protocollo (OPC-UA)
I ndiscutibilmente, l’OPC-UA è uno tra i migliori protocolli per l’interconnessione di una pressa: non vincola il cliente all’acquisto di software specifico del produttore, consente di connettere macchine eterogenee e, se il partner prescelto per il progetto ha una competenza specifica, la sua implementazione è semplice e immediata. È il protocollo consigliato da richiedere al momento dell’ordine di una nuova macchina o in fase di revamping di una macchina esistente. È importante richiedere che sia effettivamente installato e attivo sulla macchina e non ci siano parti opzionali o da acquistare in seguito
• L a soluzione per l’interconnessione (Z-IoT)
L’interconnessione è da considerare un progetto che dovrebbe com - prendere tutte le macchine, affrontando le difficoltà legate alle loro differenze tecnologiche. In questo scenario, molto comune nelle PMI del settore, Z-IoT si candida ad essere l’hub che raccoglie e rende disponibili i dati di tutte le macchine vecchie e nuove, grazie alla sua flessibilità e al supporto di molti protocolli, come MODBUS, MQTT e OPC-UA. • I l partner per la digitalizzazione (ZLab)
L’approccio tradizionale all’interconnessione ha un grande limite legato alla frammentazione delle competenze: di solito, gli esperti di automazione sono diversi da quelli dei sistemi informativi, quindi il dialogo tra il mondo dei PLC e quello dei sistemi gestionali non è scontato: spesso è necessa rio il supporto di un terzo soggetto con la funzione di mediatore, con il rischio di possibili difficoltà e incomprensioni che inevitabilmente si traducono in aumento dei costi, delusione delle aspettative e ritardi nell’implementazione.
P er superare questa situazione, ZLab ha arricchito la propria consolidata esperienza gestionale, sviluppando le competenze necessarie ad affrontare autonomamente i progetti di interconnessione, dialogando direttamente con i fornitori delle macchine e accompagnando il cliente in tutte le fasi del progetto, sin da quelle iniziali.
Z -Lab si propone quindi come partner per la digitalizzazione dell’azienda, dalla gestione del magazzino alla contabilità, dalla vendita alla produzione, fino all’interconnessione 4.0 tra le macchine e il sistema informativo aziendale.
Q uesta esperienza è stata possibile grazie alle relazioni create e sviluppate tra le aziende che hanno partecipato. Z-Lab è a disposizione di tutte le aziende del settore interessate a ripetere l’esperienza. u
Giuseppe Cantalupo