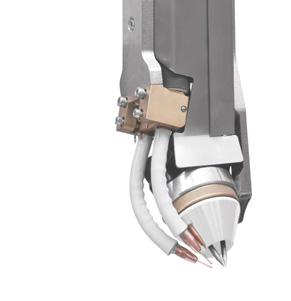
5 minute read
COVER STORIES & SPECIALS The Future of Welding
The Future of Welding
OGI sits down with welding specialist Fronius International GmbH to talk about the exciting developments in automated welding and what this could mean for the industry. Fronius describes how high performance cladding processes enables faster welding speeds which equals customers saving substantial amounts on labor and shielding gas costs. We’ll also touch on the increasing digitization of processes, and how remote maintenance and systems analysis can be achieved through the Internet. Real time process visualization is now possible and Fronius continues to impress the welding world with its component editor and the 3D display. All this along with Fronius’ robotic welding developments makes for an exciting future for the industry.
Advertisement
OGI: What are the different areas of the oil and gas industry that Fronius Welding Automation operates in? Fronius: The line of business Welding Automation mainly operates in the upstream field. Typical components welded with automated cladding systems are components like wet trees, jumpers, manifolds, or risers. However, generally speaking, the fully digital Fronius welding machines find use in all sectors of the oil- and gas industry. OGI: What are the challenges associated with cladding (overlay welding)? Fronius: The parts mentioned above, like valves and pipelines, have to be protected against abrasion and corrosion. Overlay welding has become an established practice in this industry. The technological development for achieving high-quality overlay welds is impressive, whereby the open arc cladding processes have gained considerable importance. Economic efficiency, universality in handling, accurate and straightforward adjustment of welding parameters, and suitability both in the workshop and on-site – those are the reasons for the use of sophisticated open arc overlay welding processes. GTAW* hot wire cladding is one of the most reliable and approved methods. Its main principle is based on the combination of
Sophisticated ETR Ultimate “Endless Torch Rotation” cladding system.
a high-quality welding process and an efficiency increase by using an inductively heated filler wire. For economical production and high clad layer quality, intelligent welding systems such as our Compact Cladding Cell or Endless Torch Rotation System must offer optimized welding processes and advanced process control. OGI: What possibilities does highperformance cladding offer? Fronius: GTAW hot wire cladding offers, besides high quality, relatively low welding speed, which often causes capacity problems in production. With SpeedClad Twin and High-Performance Pipe Cladding, Fronius established two high-performance cladding processes, which raise the welding speed significantly without losing any quality compared to the standard GTAW cladding process. Using two tungsten cathodes combined with two preheated welding wires to create one molten pool, causes less penetration while enabling faster welding speeds and a much higher deposition rate. Maximum productivity is guaranteed,
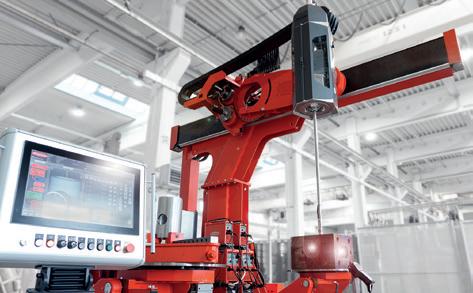
especially when welding larger components. Fronius high-performance cladding offers a low dilution rate and, in this way, excellent cladding results. Customers save substantially on labor and shielding gas costs. The welding speeds depend on the application but can reach up to 170 cm/min. OGI: What solutions do you offer for joint welding? Fronius: For pipeline welding in workshops, Fronius Welding Automation offers the welding carriage FlexTrack 45 Pro. It is a compact welding carriage that provides highquality weld seams on different rail shapes. In combination with flexible rails, operators can join curved parts such as piping components. It is also possible to use ready-made ring systems that cover defined radii from 254 to 1,778 millimeters. Magnetic or vacuum bridges, or feet, form the connection between pipe and rail. The innovative remote control operates the FlexTrack 45 Pro. In addition to the welding and oscillation mode, the user can load, change, and save parameters such as travel speed and direction or oscillation speed and travel via a numerical touch display. Besides, in conjunction with the TPS/i power source, remote maintenance and system analysis is possible via the Internet.
OGI: Can the oil and gas industry expect new Cladding Systems from Fronius, and what advantages will they offer? Fronius: Fronius Welding Automation has renewed its popular Compact Cladding Cell. In the past, it already scored points with its space-saving dimensions, intuitive parameter input, flexibility in component geometries, or optional high-performance cladding. Compared to this former system, the new system convinces first and foremost with the futureoriented HMI-T21 system control. In addition to its 21-inch operating panel, multi-user management, remote maintenance capability, and real-time process visualization, it also impresses the welding world with its component editor, including a 3D display. Ergonomics was another focus of improvements: In the new Compact Cladding Cell, operators can fix torches in just a few easy steps and change wire spools at handle
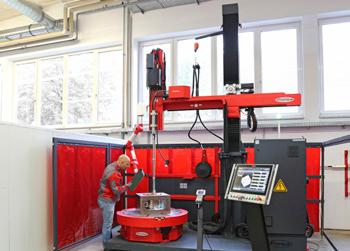
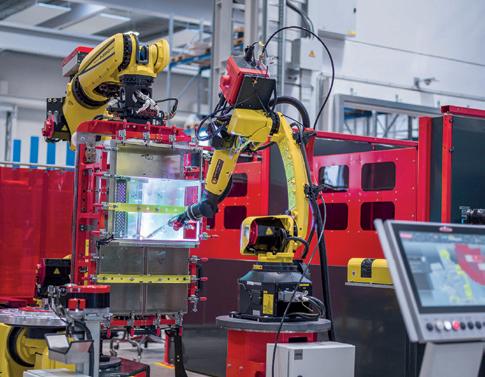
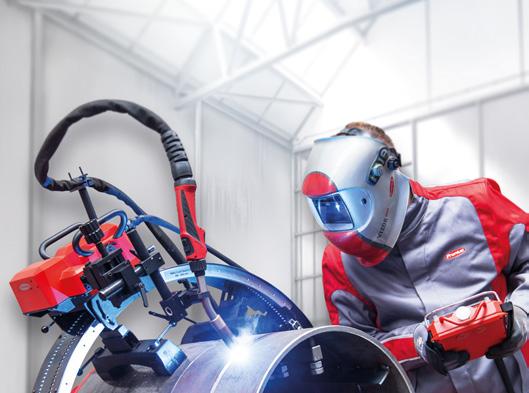
Photos.
Above: FlexTrack 45 Pro welding carriage.
Left: Fronius Compact Cladding Cell – new generation.
Below: Fronius HTW “Handling-to-Welding” robotic welding cell is welding an inverter housing. height. Moreover rail extensions offer easy handling of the welding machines. OGI: What is Fronius Welding Automation doing regarding robotic welding? Is it a topic for cladding too? Fronius: The Fronius Welding Automation department is working on several systems in the robotic field. At the moment, we are establishing a prototyping center to support the industry in the prototyping area. Our gain is to be a reliable partner by welding prototypes and first pre-series combined with measurement and documentation. To carry out feasibility studies and welding trials will be part of the cooperation with our customers. One further goal is to develop a robotic platform, based on handling and welding robots. It will offer intelligent planning, control, and monitoring of all workflows, from simulation to final welding results. The intelligently chosen modularity of robotic welding cells will offer many options for our customers. It will enable the system to weld components of different geometries and materials. Also cladding applications could be a possibility. In addition to various peripheral features such as gripper deposit systems, contact tube changing stations, component locks, or automated rack systems, different welding processes such as MIG-MAG, CMT, TIG, ArcTig, or Plasma will be available. OGI: Thank you for your time. •
If you would like to know more about the solutions discussed in this article please contact: FRONIUS INTERNATIONAL GMBH W: www.fronius.com E: sales.automation.int@fronius.com T: Phone: +43 7242 241 0