How about a little extra?
Linking a system to three different CNC machines and having it loaded automatically. With the aim of making everything easier, increasing capacity and process reliability? Yes, exactly!
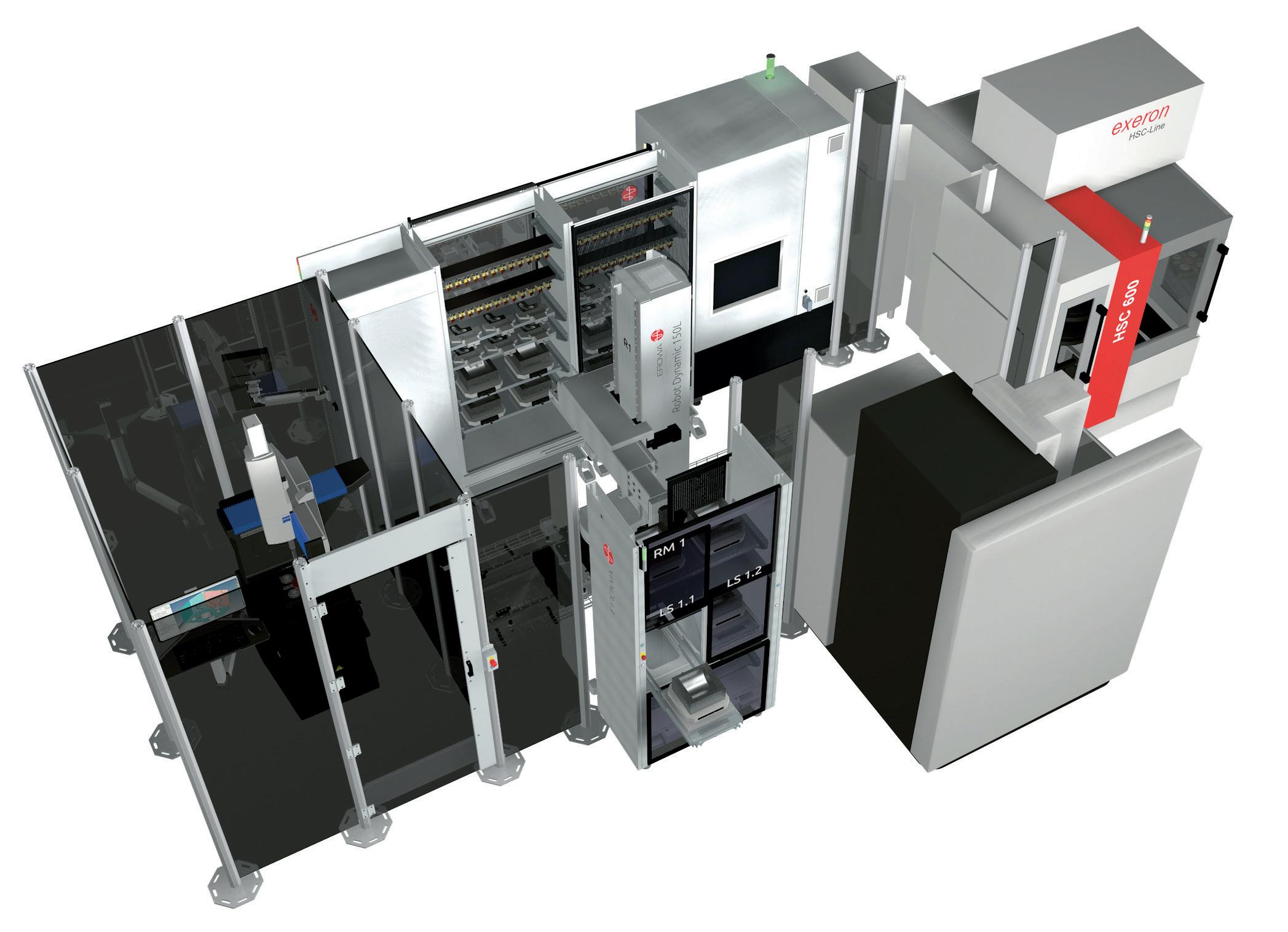

That is Mayweg
The full-service partner in tool and mold manufacturing. From consulting and design engineering to delivery of fully assembled and tested subassemblies, Mayweg GmbH is a system supplier for plastic parts. Every day, 150 employees work together with customers to develop optimal solutions. These customers come from the electrical engineering, electronics, automotive, construction components, sanitary ware and medical technology industries.
Considerations
Christopher Seeboth, Head of Manufacturing in the Tool Design division, and his team are constantly striving to achieve shorter throughput times and higher machine utilization, with repeatable quality and less strain on personnel. To achieve this, the specialists at Mayweg, EROWA, and Exeron joined forces to develop a solution.
The cornerstones
Lower throughput times
In today‘s world, where „right now“ is often already too late, it is inconceivable that workpieces coming from one production step have to sit idle until the machine is ready for the next step. The throughput has to be organized in such a way that waiting times are avoided as much as possible.
Higher machine utilization
One clear advantage of lowering throughput times is a better (higher) utilization of the individual machines in the process. These integrated systems must be extremely robust when 24/7 production is needed all of a sudden.
Database as the foundation
Process interruptions can be avoided only if all manufacturing decisions are made on the same data basis. That is exactly our intention with the database of the JMS 4.0 process control system.
High availability

All well and good, you say? Yes, and when the entire system is available, things get really interesting in production scheduling. Being able to plan with 24/7 production frees up previously unknown capacities. It is extremely important to make sure that these hours are actually available. The reliability of the system is therefore one of the guiding criteria in the assessment.
Easy operation
Everyone knows that the highly interlinked processes in tool and mold manufacturing are extremely complex. This is exactly where the full strength of the JMS 4.0 process control system comes into play. Complex processes require appropriate computing power and the right software, which must be easy for the machine operator to use.
The heart of the matter
The in-depth discussions on taking the step towards automation revealed one thing above all: Everything has to be standardized, starting with the tooling system for the workpieces and electrodes, continuing with the datum points on the machines and finally the part designations, CAD parameters, and complete work processes. The question arises as to whether all this is actually necessary and why the same could not be achieved with just a little more flexibility.
The answer is obvious, though: If a computer is really going to help, it can only do so when the conditions are logical. These conditions can be highly complex, but the variables have to be
calculable. The result: The tooling system defines the datum point (to the nearest 2 µm), the programmed starting points on the machines are fixed, the pallets can be clearly identified by means of RFID chips, and all data pertaining to the order are provided in a central database. Under these conditions, the process control system can generate the optimum production processes, even with continuously changing priorities, delivery dates, or changes in the CAD data.
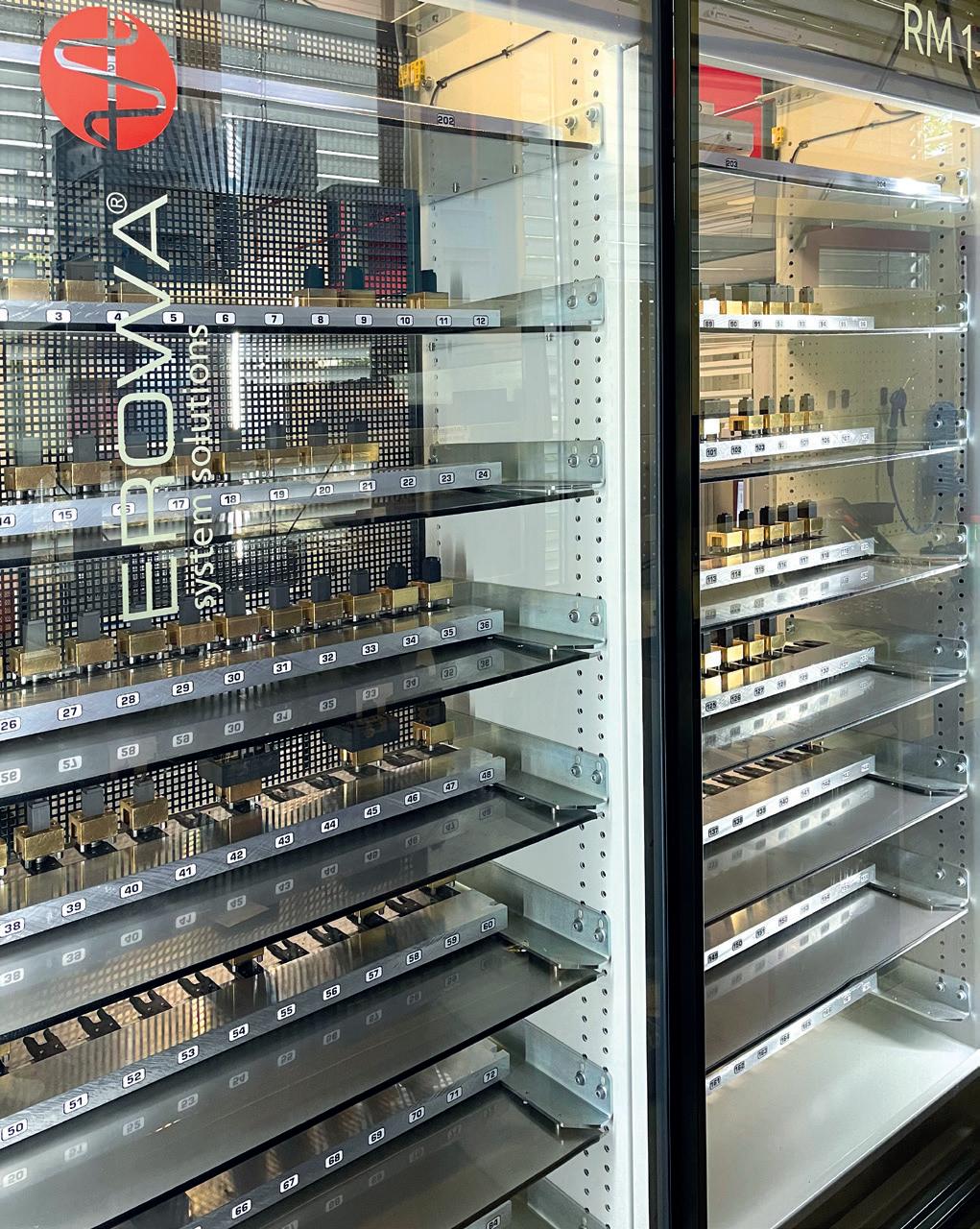
Installation and testing

EROWA automation systems consist of standard components. Installation of the mechanical parts is standardized accordingly. The maintenance technicians are highly experienced and can install and commission entire lines within a week. The process control system is a little different. Embedding it into the existing IT environment requires very high configurability.
„Everything“ is possible, therefore the challenge lies in finding the right settings. Or, as Mr. Seeboth puts it: „I can sum up the test phase in one word: intensive.“ In the end, however, a fully functioning production line was put into operation.
What does 24/7 mean in practice?

Firstly, it is important to emphasize that the new cell really is available 24 hours a day, 7 days a week, in single-shift operation. Mr. Seeboth points out that, despite all the organizational measures that were introduced, not all hours can actually be used productively. When it comes to precision, there are no compromises. All the machines in the system are re-calibrated and cleaned once a day. The HSC milling machine produces quite a lot of swarf, and anyone who has experienced this knows that HSC swarf gets everywhere during machining.
A number of CNC programs are run during the 24-hour period. Currently four people work on the whole system, including three CAM programmers who look after the milling machine and also after the other systems (measuring, washing, EDM machining), while a fourth person is being trained at the same time. This means that any normal absences do not affect productivity. A new job profile has been created at Mayweg: the cell manager. It is a demanding job, but some initial discussions
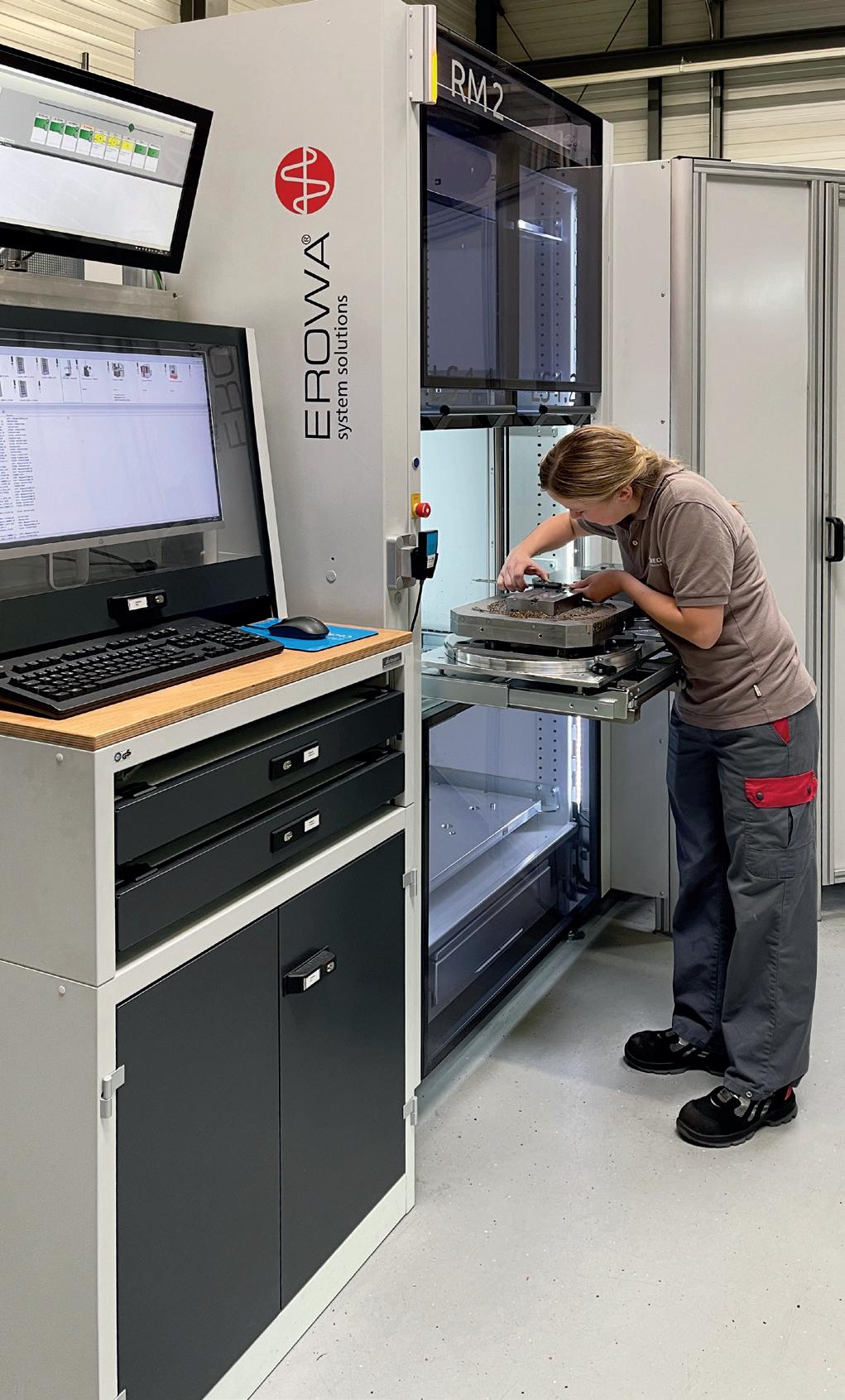
with candidates have shown that it is also a good reason for innovative people to train as specialists. The company may seem like a minor player, but if it can stand out with attractive jobs, then that is certainly a competitive advantage.
Organizing and structuring
The production throughput times have been greatly reduced. That is the main requirement for the system. As experience increases, everyone involved is starting to see more opportunities for optimization. The much-cited OEE factor can now be refined and optimized further. And, of course, EROWA is on hand to provide after-sales advice and support.
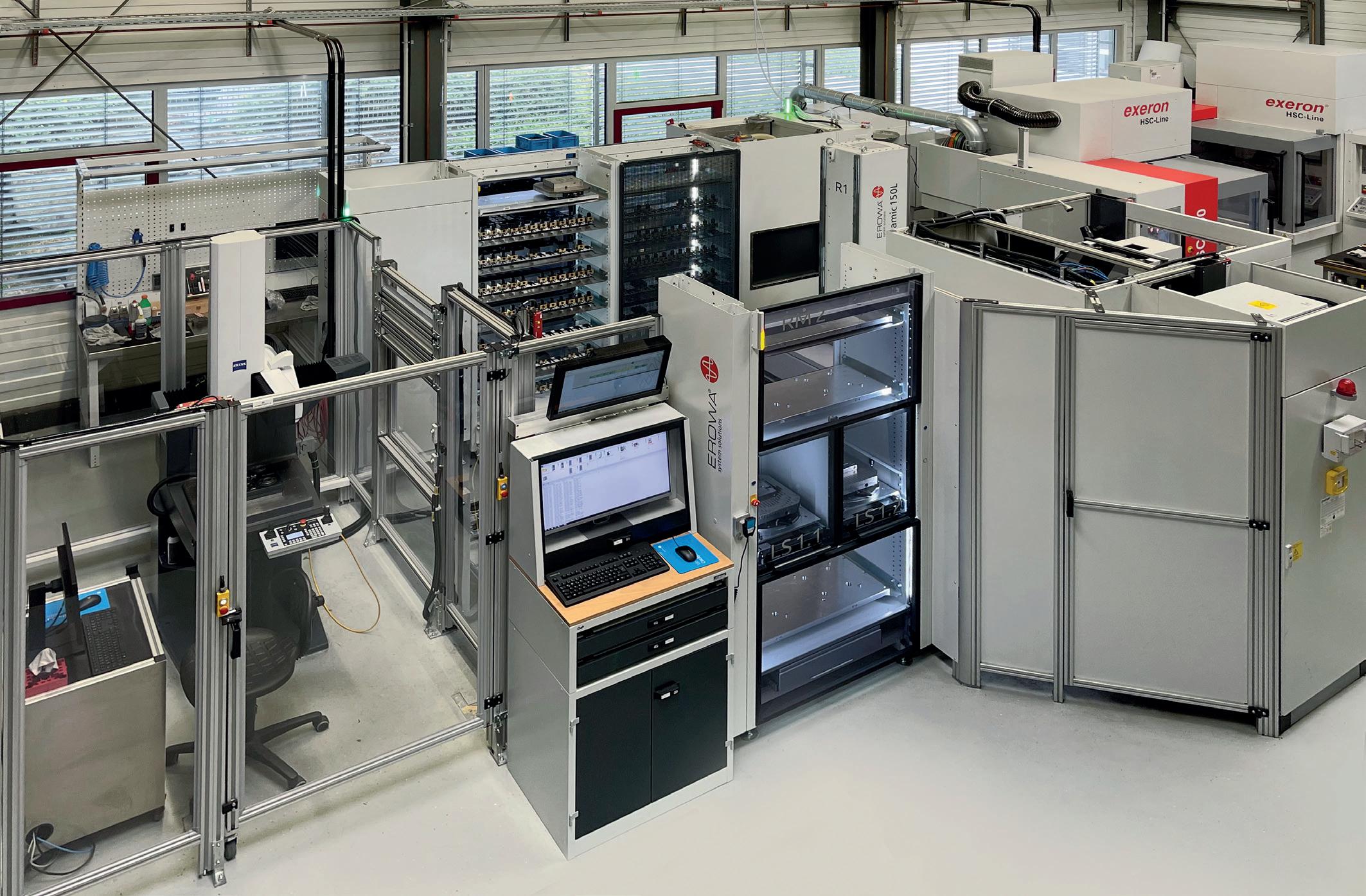
Facts
The ERD 150L including loading station automates the following machines:
• Exeron HSC 600
• Exeron EDM 312
• Zeiss Duramax
• EROWA RoboSpa
Mayweg GmbH
Daimlerstrasse 7
D-58553 Halver
info@mayweg-gmbh.de
www.mayweg-gmbh.de
EROWA AG
Knutwilerstrasse 3
CH-6233 Büron
info@erowa.com
www.erowa.com
CERTA Systems GmbH

Rossendorfer-Strasse 1
D-90556 Cadolzburg

info@certa-systems.com
www.certa-systems.com