Modular system for the future
Precision mechanics with a purpose
NBF GmbH & Co. KG Feinmechanik in Münster, Germany, has been providing precision technology and precision engineering services since 1988. As a leading company in the development and manufacturing of precision systems and components, NBF has manufacturing expertise in a broad range of industries. NBF customers include companies from the fields of medical technology, optomechanics, laser technology, as well as automotive suppliers and scientific and research institutes.
Systematic automation projects
The ever-present call to shorten delivery lead times inevitably brings up the topic of automation in production processes. This is also the case at NBF, where owner Norbert Bücker handles customer requirements, machine availability, raw material supplies, and general production data on a daily basis. The name EROWA first came up as a provider of forward-looking automation solutions when NBF was evaluating new CNC milling machines. A team including partners from Alzmetall and EROWA was created to systematically work out all the possible configurations.
System requirement:
Shorten lead times
Not just talk about it, but actually do it. The great potential for reducing throughput times lies in the unused off-peak and nighttime hours. While these can be utilized with a multi-shift operation, the cost of doing so is high. And finding the skilled workers this requires is no easy task.
Reducing set-up times
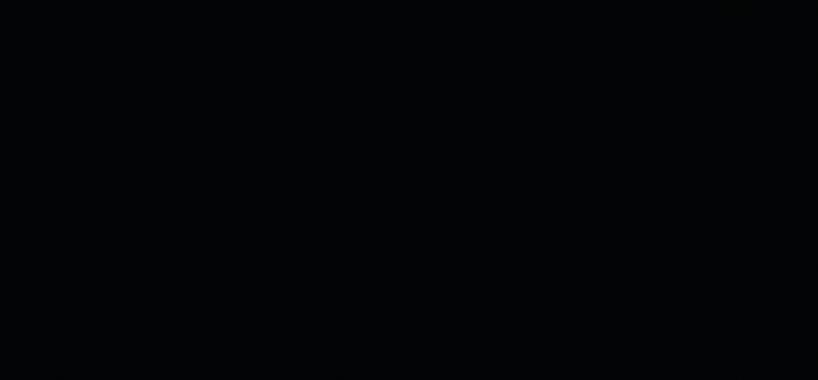
Preparing upcoming jobs on the machine in parallel with “cutting time” is the way to go here.
Flexible response time
When the customer needs the work delivered yesterday, you have to figure out how quickly jobs in the pipeline can be switched around and reprioritized without throwing the entire schedule out the window.
Making 24/7 a reality
A large part of the second (and most definitely the third) shift should run without supervision. And when it is necessary to intervene in the process, a clear message needs to go to the standby workers.
Ease of operation
Automatic machining of small batches is the real art of job preparation, not to mention machine operation. Accordingly, the cell control system must be clear, plausible, and simply structured.
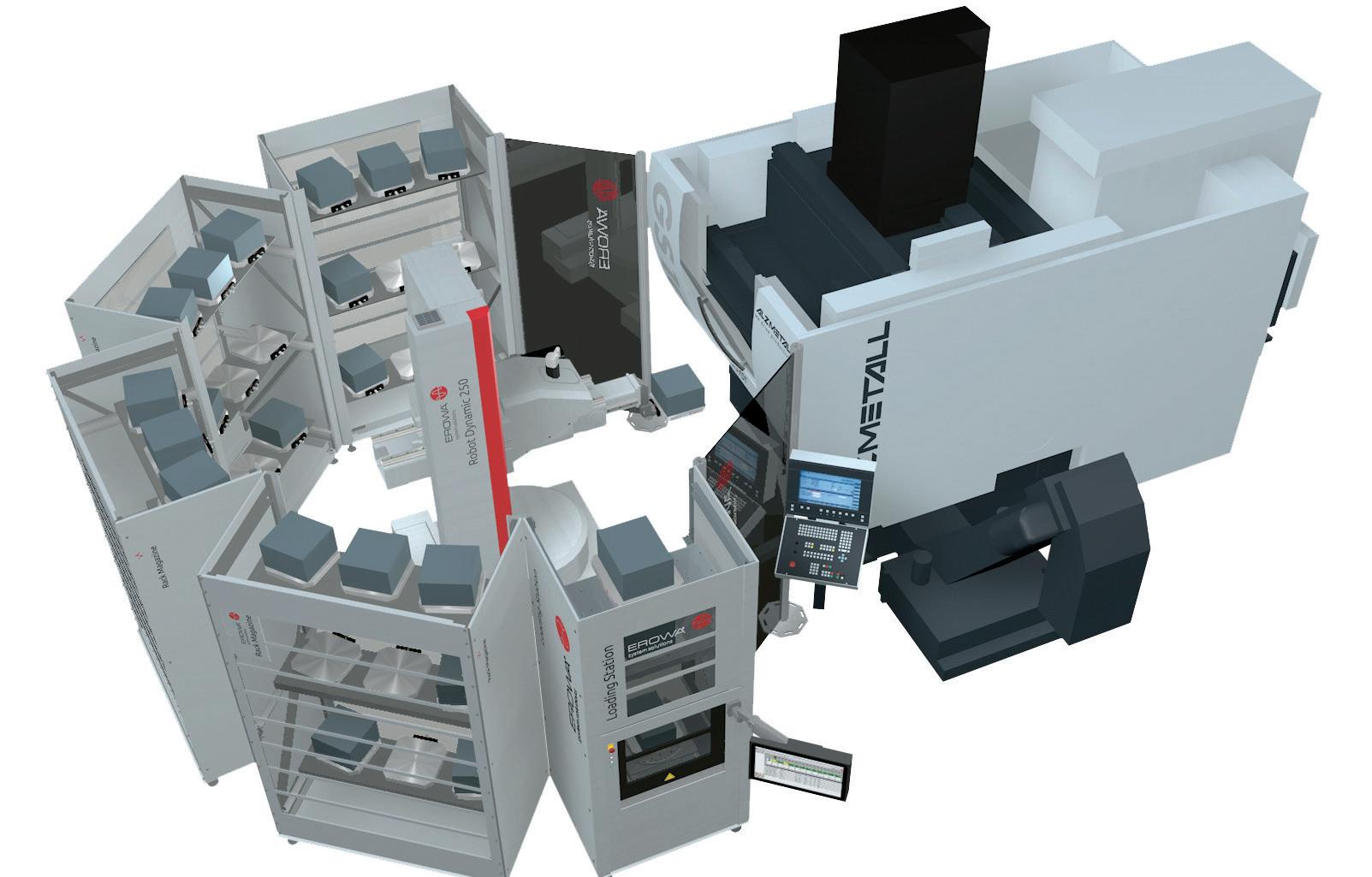

And still work manually
In the staffed shifts also, doing the odd job without any automation at all should be possible.
Method to the modular system
Fully automated production systems almost inevitably come to mind when considering such ambitious requirements. Systems with driverless transport systems that provide the link between individual machines and robots that safely load two, if not more, production lines automatically. Starting right away with a complete system can be extremely challenging, however. This is where the modular capability of the EROWA Robot Dynamic comes in handy. To start off, a single CNC machine can be smartly equipped with automatic loading to get the most out of the machine. Then, the next logical step involves adding a second or third system to the cell.
At NBF, we calculated how may pallets of storage would be required to achieve around-the-clock autonomy based on the specifications. In other words, how long can the production system run without requiring a technician to be present?
The project team
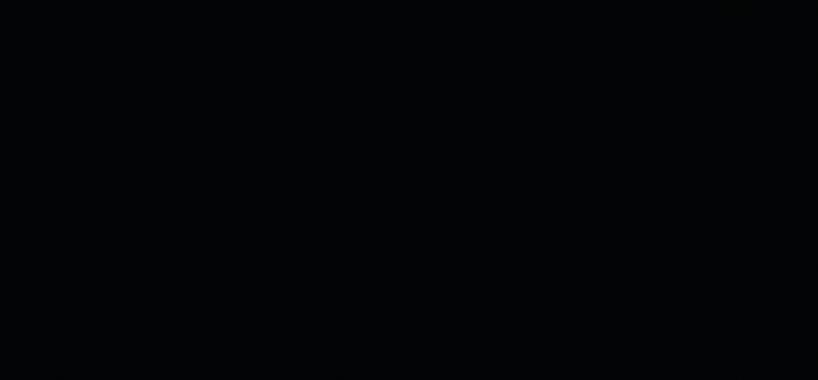
Major tasks are best solved in a team. And the step that NBF was planning – switching from manual machine loading to automatic production – was indeed a major task.
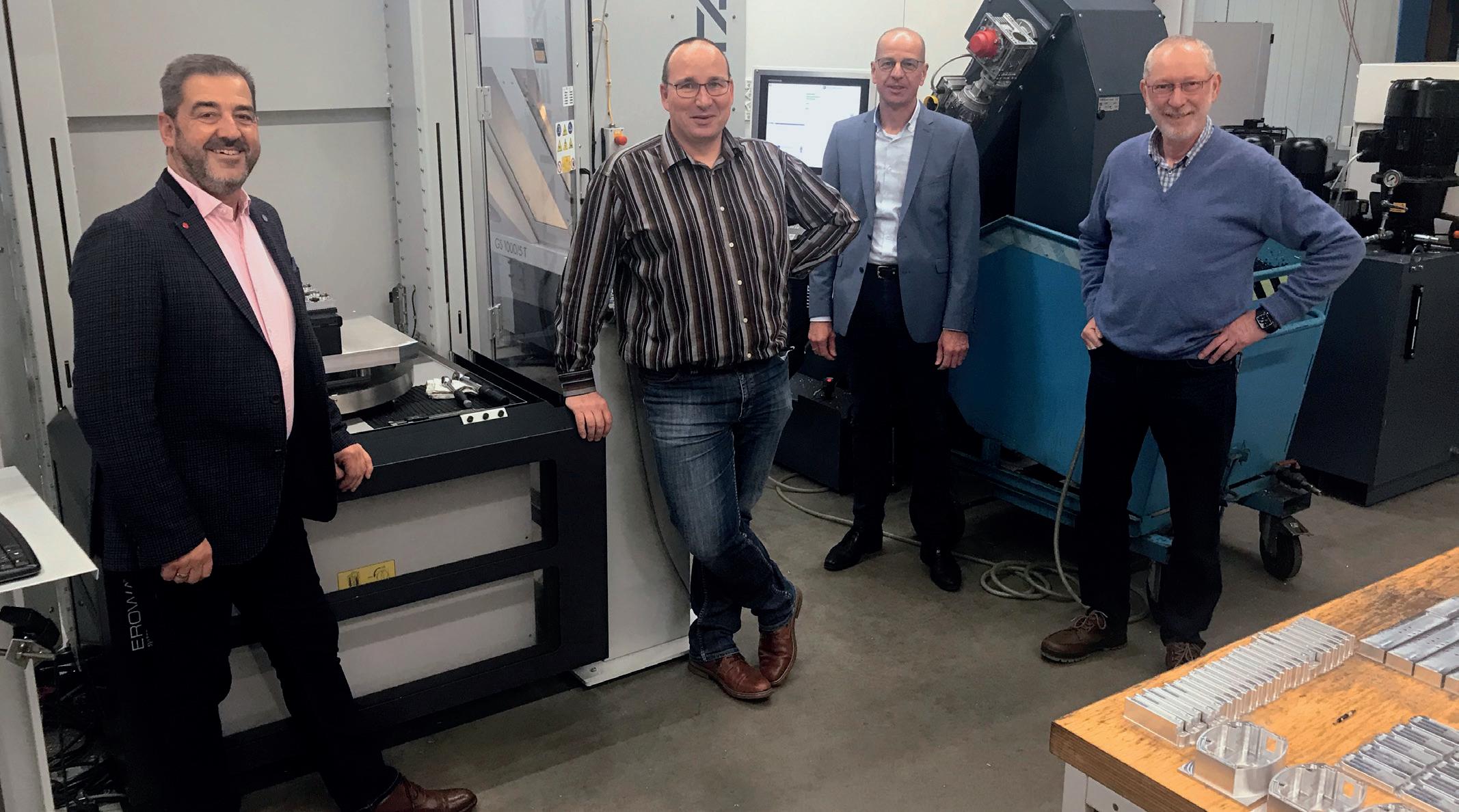

Employees from NBF’s Production and Planning departments were also on board. The outcome of the project was going to optimize their day-to-day operations, after all.
On the machine side, the Alzmetall team was brought in, since deciding on a machine always involves weighing what’s required against what’s doable. EROWA (represented by Michael Horstmann) provided answers to questions about tooling systems, automatic loading of the machine, and the entire process sequence.
The ideas that the NBF crew brought to the table were analyzed to the last detail. Various solutions were considered for the milling machine, the tooling system, and the robot. It soon became clear that the best solution can indeed come from disparate sources working together. Specifically, when specialists from production, machine experts, and experienced process designers all pull together, they come up with a solution that delivers optimum results for the user. Ultimately, the consensus among the team members was that the EROWA Robot Dynamic with four large magazines and one loading station on an Alzmetall GS1000 would meet the requirements. It was a combination with tremendous potential.
Commissioning
EROWA automation systems are made up of standard components. With well over 4000 systems in operation worldwide, it stands to reason that our technicians boast top-level experience.

In addition to the hardware, the JMS 4.0 ProductionLine process control system had to be integrated. Surrounding systems such as ERP and CAD/CAM had to be factored in and connected. There were one or two “hiccups” in this regard until everything worked to satisfaction. But in the end, chapter 2, “Contingencies,” was also concluded. The employees were then trained on the new system, marking the successful completion of the commissioning process.
From machine operator to system manager
Finding skilled workers is hard. And retaining skilled workers is no easier. When it comes to automation, a debate often ensues about the value of employees and the jobs on the machine. We believe that actually working on an automated cell is far more interesting than simply watching the machine do its milling for hours on end. Keeping a manufacturing cell running requires organizational skills, a sound knowledge of the technology being used (at NBF, it’s CNC milling), a knack for hands-on work and, last but not least, a commitment to work as needed. But the second, and possibly third, shift is unattended. A job like this is a challenge for skilled workers and thus a reason to stick with it.
The proof is in the system
An additional 3 to 5 productive hours were gained per calendar day. This was mainly due to the often quoted “main time-parallel setup.” Small production runs with one to two pallets in the main shift were loaded manually but set up outside the machine. This freed up productive time. It also came as no surprise that a single CAM station was no longer sufficient. Not by a long shot. Currently, there are three employees working at two stations to provide enough “fodder” for the entire production cell every day. NBF engineer Mark Harleman, who was instrumental in implementing and supporting the project, remarked after the first few months with the cell: “Our initial experience working with the automated system has been overwhelmingly positive.” There’s even talk now of expanding the complete cell to include two or even more machines.
And the proof is this:
For those who rise to the challenge, the future is straightforward.
NBF – Norbert Bücker GmbH & Co. KG
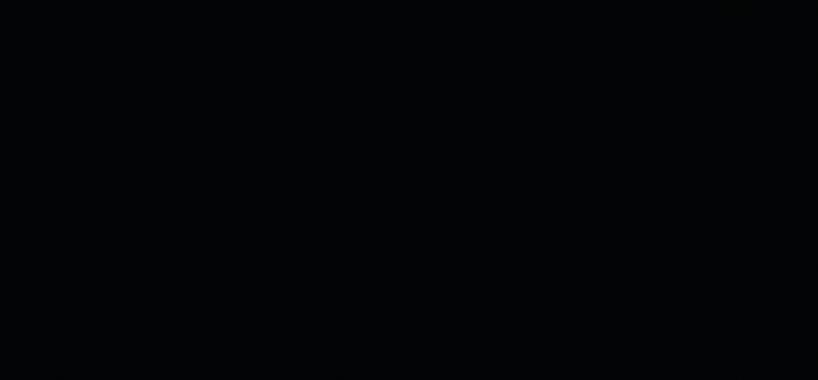
Norbert Bücker
Mark Harlemann
Lise-Meitner-Strasse 19 48161 Münster, Germany Phone: +49 2534/646912 info@nbf-muenster.de www.nbf-muenster.de
EROWA AG
Knutwilerstrasse 3 CH-6233 Büron info@erowa.com www.erowa.com