
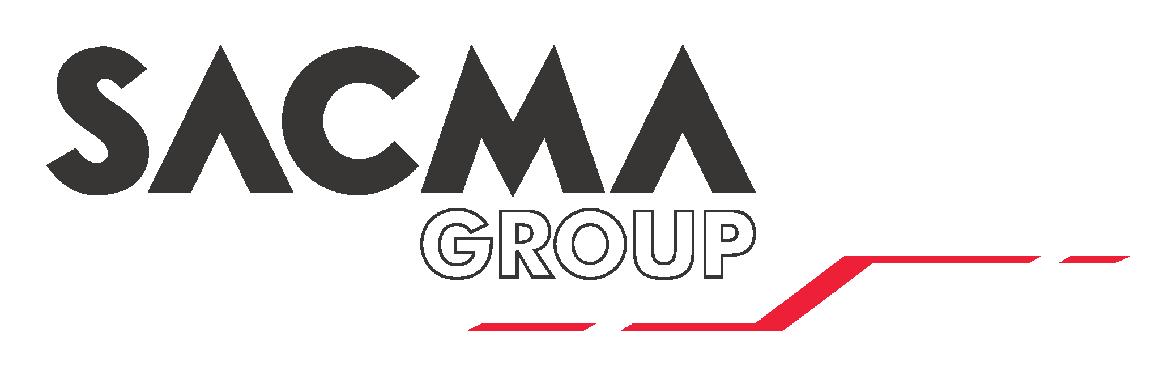
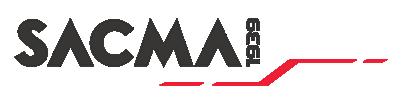
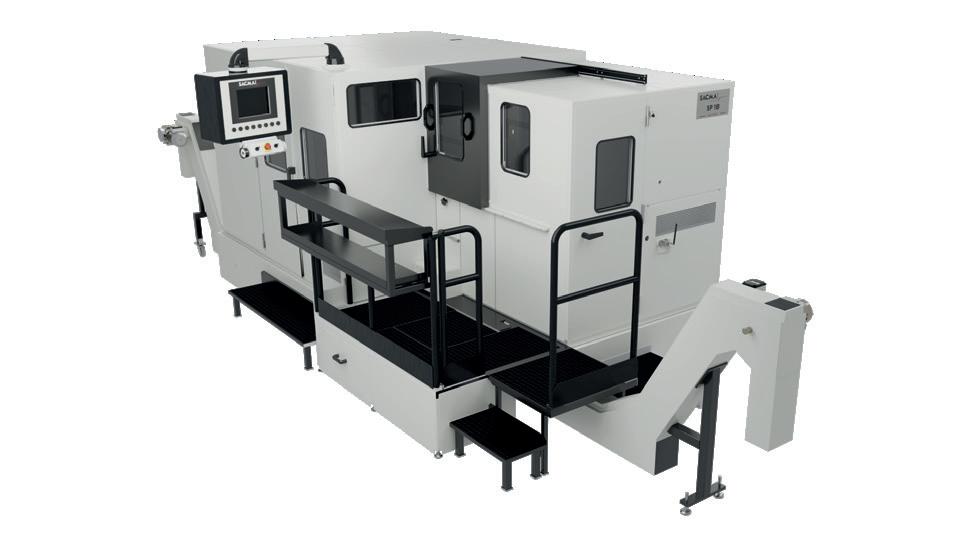
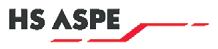
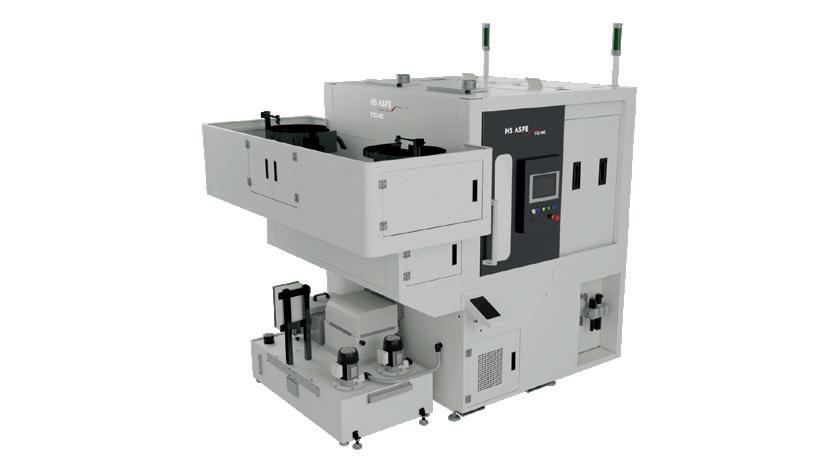

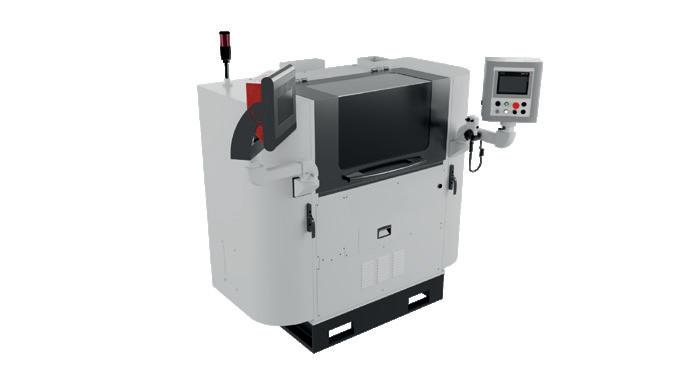
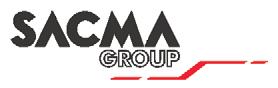
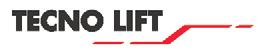
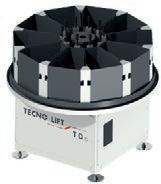
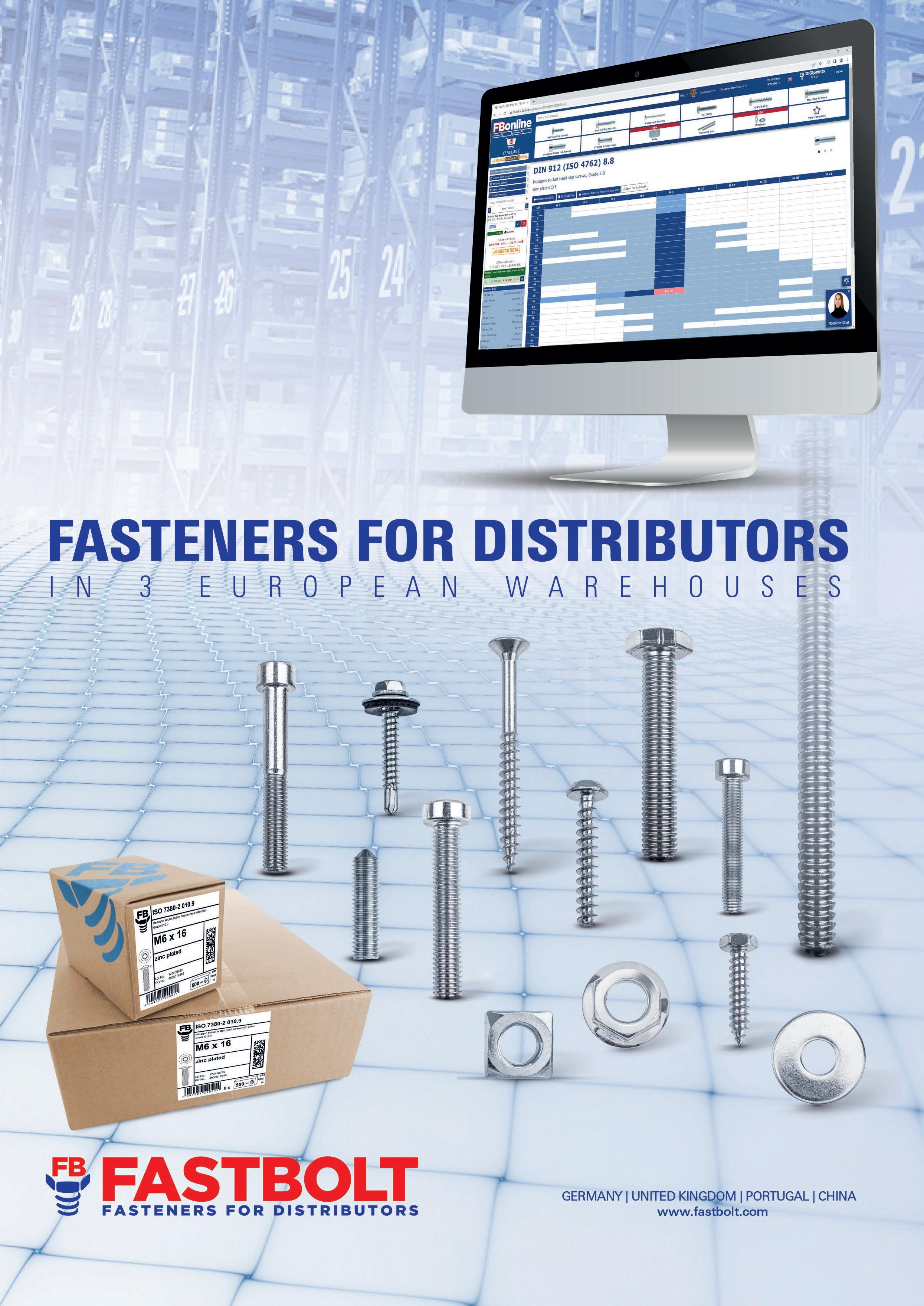
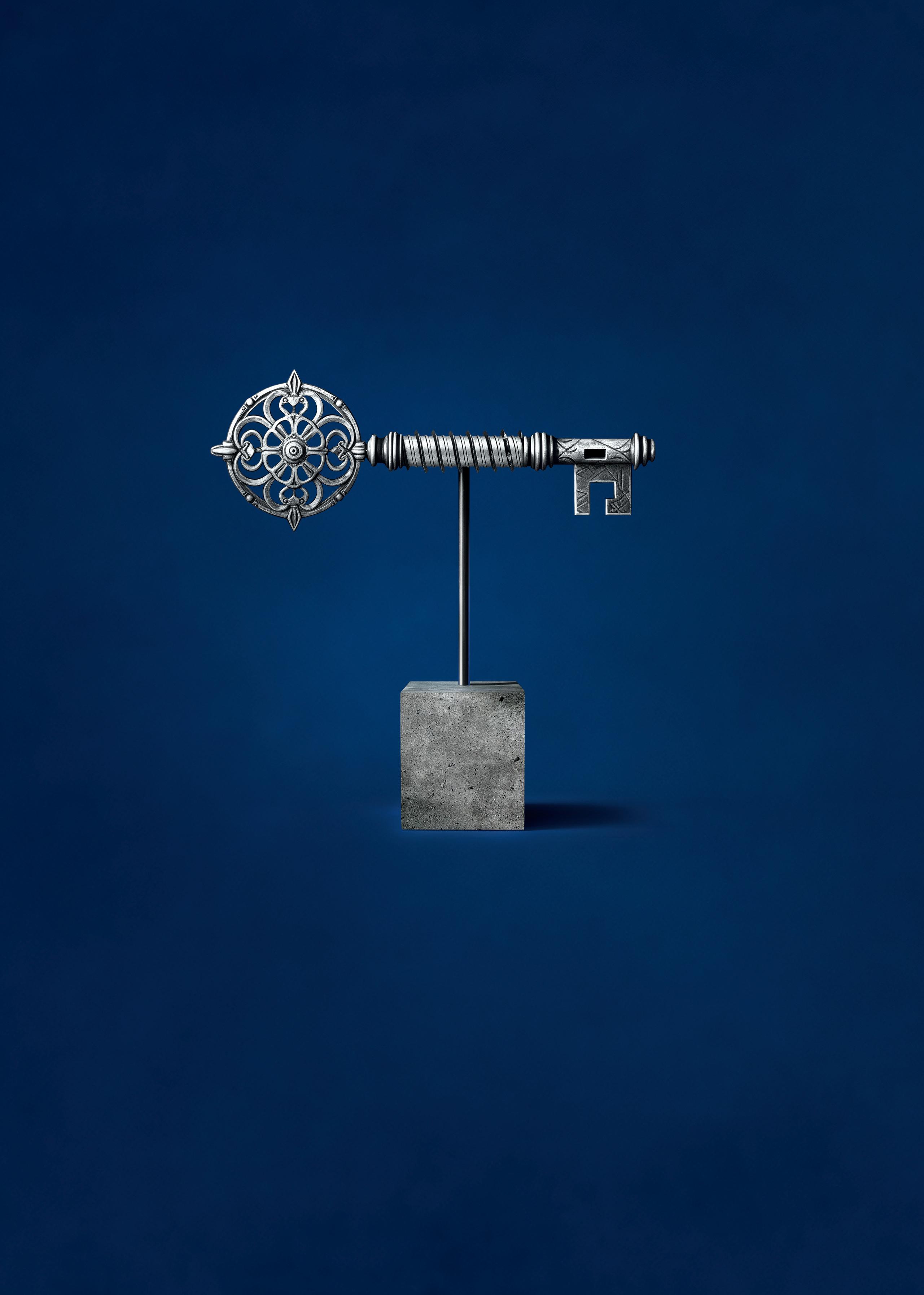
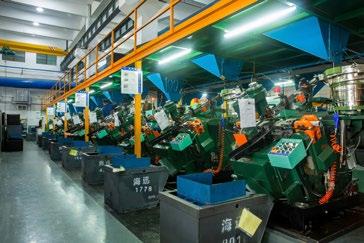

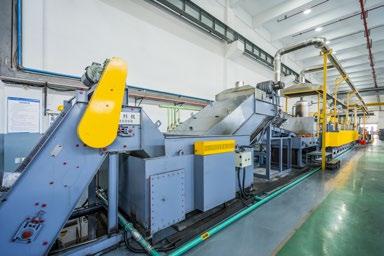
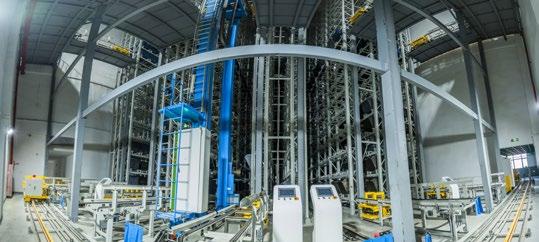
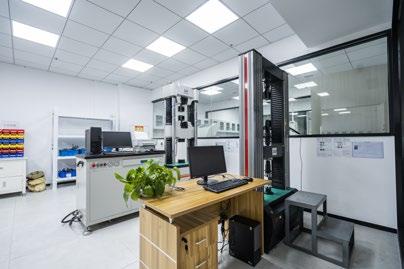
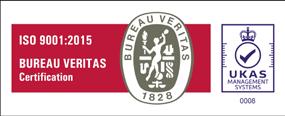

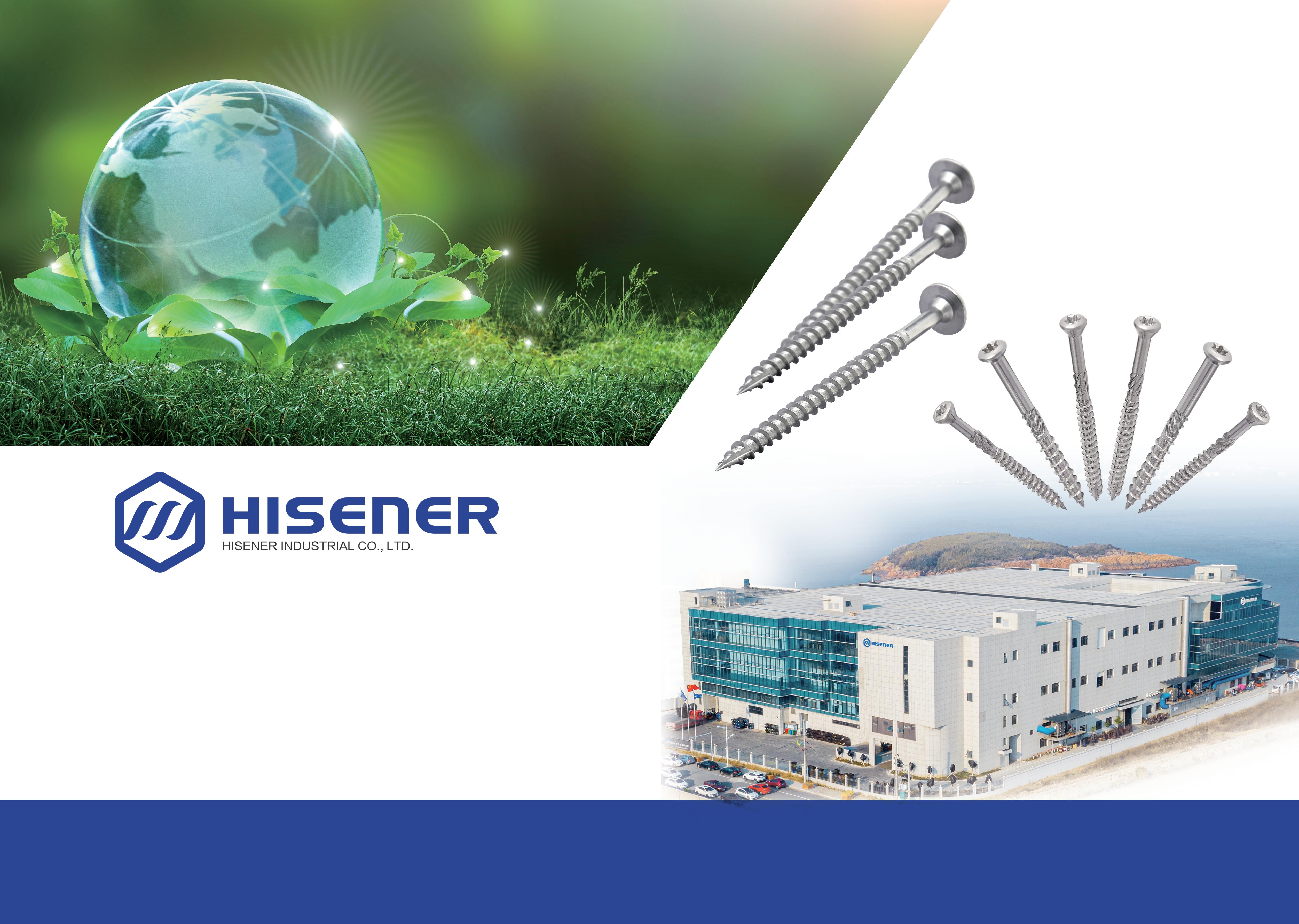
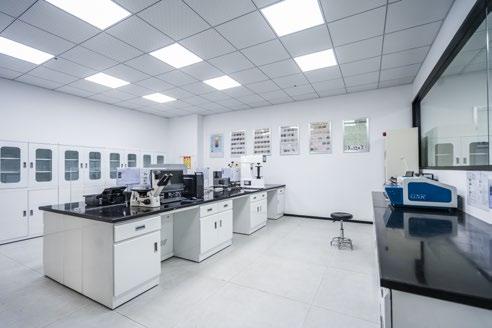
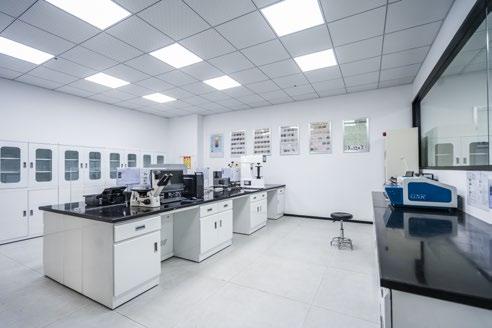
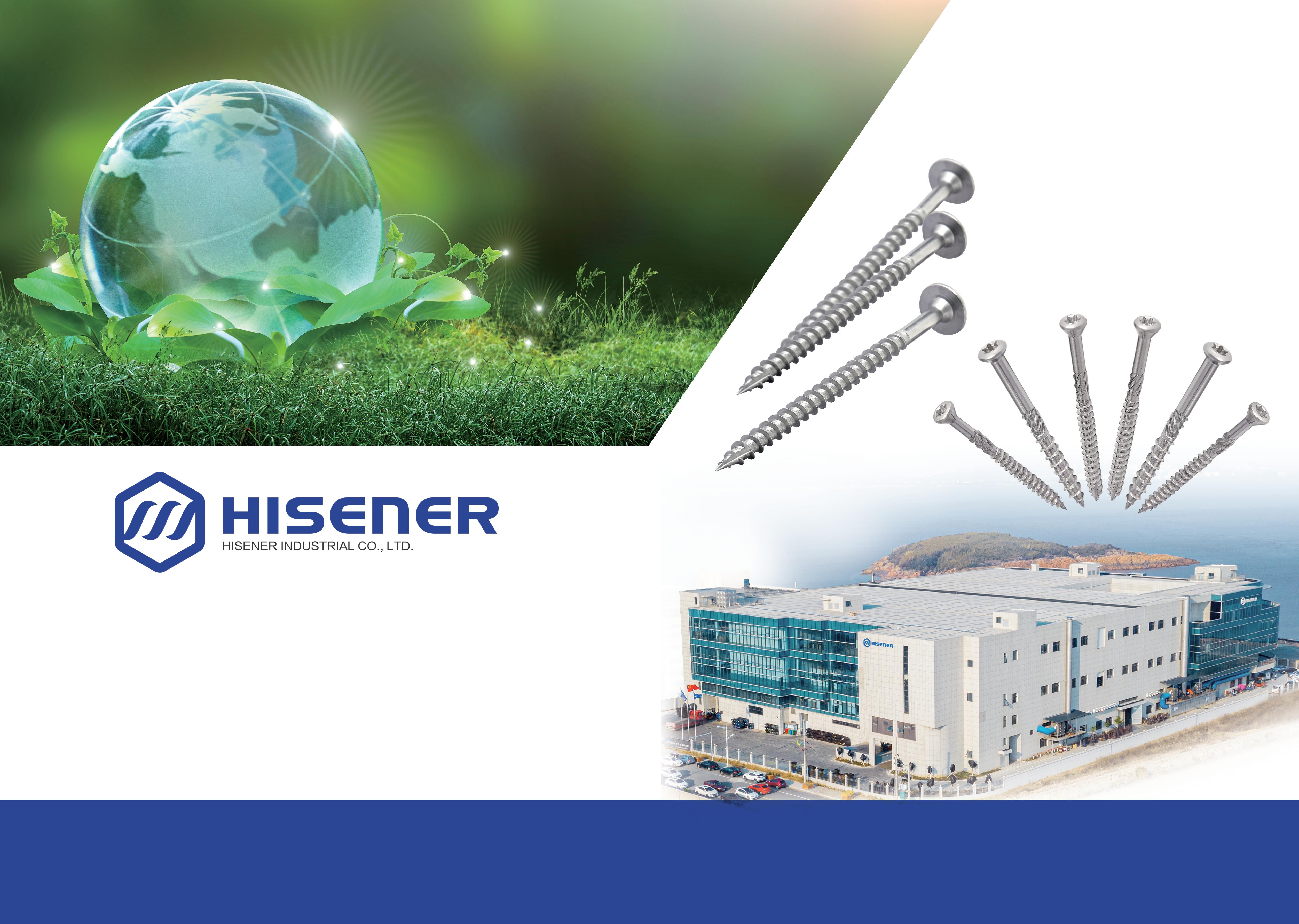
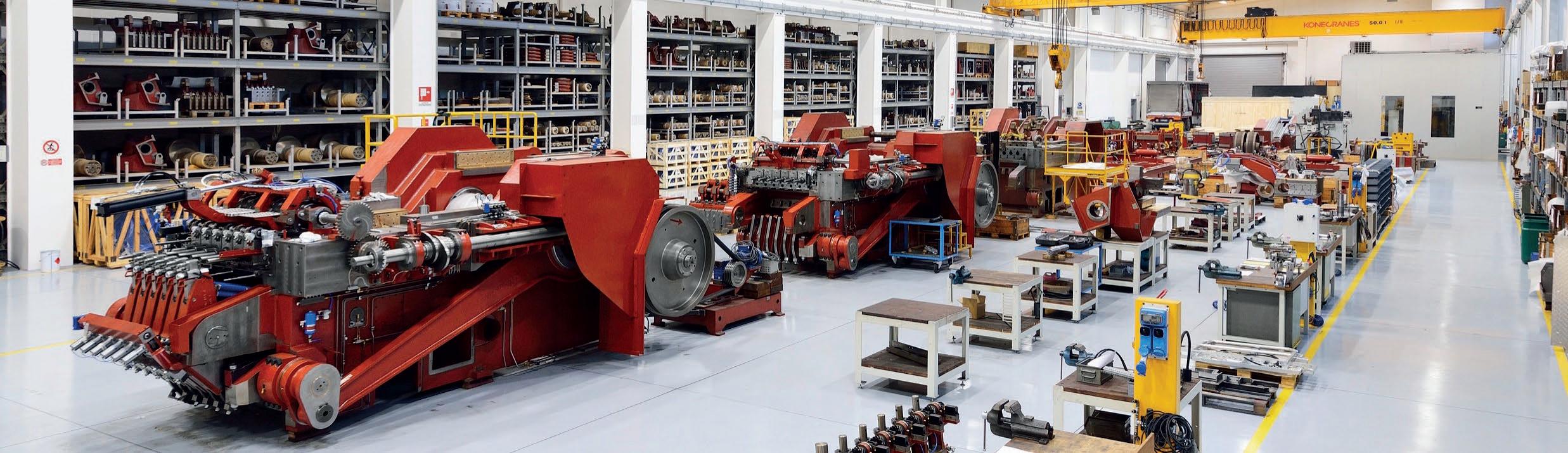
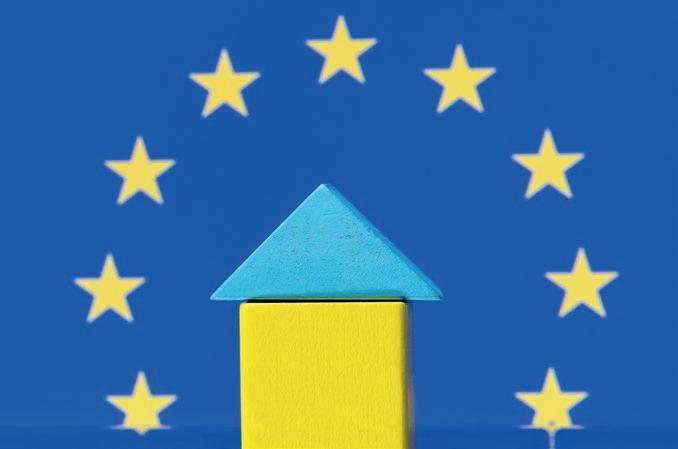
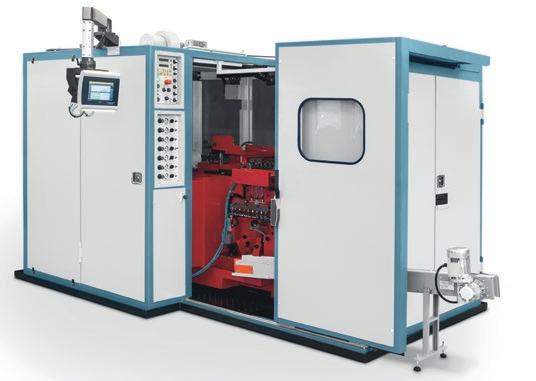
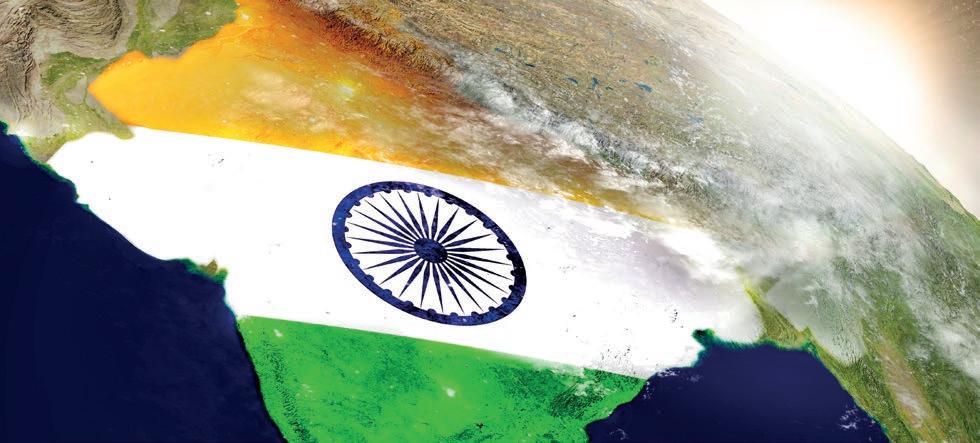
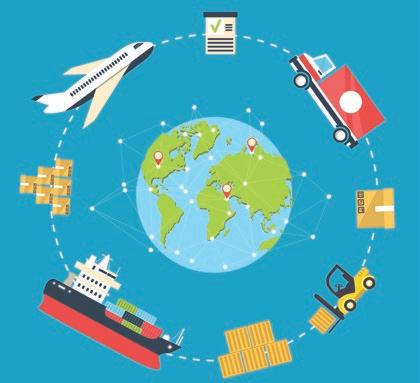
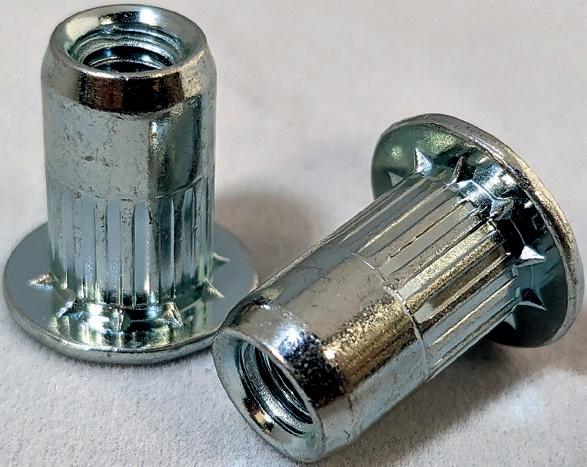
Are you facing challenges developing your application? We offer a tailored solution with lightweight design, more clamping force and smaller fasteners.
KAMAX experts challenge your drawing, analyze your problem and review your application. Our dedicated Application Engineering team is always at your side.
What you need is what we have: bolt design, lab validation, simulation of assembly conditions, supply of test parts as well as high-quality production and shipping of your fastener solution – anywhere in the world.
www.kamax.com
Purchasing additional machinery is always a big investment, but can often be an essential part of a business taking the next step in its development. With automation, digitisation, sustainability and Artificial Intelligence key topics within the market, plus the upcoming wire® Düsseldorf show, we felt it was a perfect time to put a spotlight on the latest developments within fastener machinery.
In our special Fastener Machinery Spotlight feature, we look to provide a unique insight into key areas within the fastener machinery sector, as well as give visitors to the wire® Düsseldorf show, due to take place from 15 th – 19th April, the opportunity to see what they can expect from exhibitors at the show.
The feature includes articles on every aspect of the fastener production process – heading and forging, tooling and dies, threading and secondary operations, turning and milling, heat treatment, as well as inspection and packaging – ensuring that readers will find the latest news on whatever machinery they are looking to update.
Our Cover Story also concentrates on a fastener machinery expert – the world-renowned manufacturer of multi-station cold forming machines for high-precision metal components and fasteners – SACMA Group. The article focuses on how the Italian manufacturer has used a commitment to quality, modularity, excellence, reliability, customer centricity, continuous improvement, innovation, team working, and employee engagement, as its core values to make it the business it is today.
Part of the Mack Brooks Group
www.fastenerandfixing.com
Published by
Managing Director Jamie Mitchell jamie.mitchell@verulammedia.com
Content Director
Will Lowry
will.lowry@verulammedia.com
Deputy Editor Claire Aldridge claire.aldridge@verulammedia.com
Within the Manufacturing Technology section, we also have a great article from Peter Standring, technical secretary, Industrial Metalforming Technologies, who asks the question ‘why heading and forging’ and looks at how even today heading and forging holds secrets that can be easily overlooked.
In addition to sourcing new machinery, a key factor for a lot of readers currently is looking at new suppliers, especially with the global tensions currently around the world. With that in mind, we have an exclusive Made In India feature that not only looks at the current economic situation within India and the Indian fastener market, but also showcases some of the key Indian fastener manufacturers and the steps they have been taking to ensure they can support both existing and new customers going forward in order to take advantage of the opportunity within the market.
To add to this, we have articles from our usual contributing authors – Barbara Sorgato in Construction Fixings and Jason Bader in Management + Systems. We also have special insight articles on Fabory UK, PennEngineering®, Apex Stainless, Remaches Tudela and International Hi-Tech Consulting Srl, as well as features on structural steel and cladding fasteners, rivets and rivet nuts, plus so much more.
Assistant Editor Rebecca England rebecca.england@verulammedia.com
Sales Director Mac Rahman mac.rahman@verulammedia.com
Business Development Manager –Italy
Emiliano Pagliaroli emiliano.pagliaroli@verulammedia.com
Business Development Manager –DACH & Europe Chantal Ridings chantal.ridings@verulammedia.com
Production & Design Manager Lee Duskwick lee.duskwick@verulammedia.com
Bulten AB has reported net sales amounting to SEK 5.757 billion (€510.7 million) for the financial year 2023, an increase of 28.7% on the same period the previous year (2022: SEK 4.474 billion). Operating earnings (EBIT) totalled SEK 230 million (2022: SEK 180 million), equating to an operating margin of 4%.
Adjusted operating earnings
totalled SEK 243 million (2022: SEK 284 million), equating to an adjusted operating margin of 4.2%. Operating earnings were charged with the transaction costs of SEK 13 million – attributable to the acquisition of Exim, an Asian distributor of fasteners and other components.The corresponding period of the previous year was adjusted by approximately SEK 104 million –where SEK 93 million was related to ‘winding up’ costs for Bulten’s operation in Russia.
Based in Singapore, Exim has annual sales in the region of SG$40 million (SEK 320 million). The acquisition affords Bulten a good platform to grow in new sectors, where the distribution stage is a pivotal sales channel.
“2023 was the year when Bulten laid the foundation for future expansion
opportunities in the distribution stage, as well as micro screw sales, through acquisitions and establishing new operations. It was also a year of very high sales, which unfortunately resulted in capacity challenges and also had a negative impact on operating profit, both in Q4 and for the year as a whole,” explains Bulten.
After five years as Bulten’s CEO and president, Anders Nyström departed the company in early February, to pursue “other challenges”. A process to recruit a new CEO and president is underway, having been initiated by the board of directors.
Departing, Anders said: “It has been a privilege to lead and develop Bulten together with the board of directors and all professional employees. My decision to leave has not been
easy, but I feel that the time is right for me to take on new challenges after these five years as CEO of the Group.”
Chairman of the Board Ulf Liljedahl added: “Through his leadership and commitment, Anders has played an important role in successfully developing Bulten AB and taking the company to its current position. During Anders’ time as CEO, the company has experienced strong growth at the same time as the market has been in a period of change. On behalf of the board of directors, I would like to express my thanks to Anders for his valuable contribution during these years and wish him all the best in the future.”
Current Board Member Christina Hallin has been appointed interim CEO and president and will act as such until a replacement has been found for the position.
Despite the tense global economic and political situation, Würth Group was able to grow again, even though the difficult conditions had an impact on its operating result.
Würth Group reported annual sales of more than €20 billion for the first time in its corporate history, according to its preliminary financial statements on the 2023 fiscal year. Adjusted for currencies, sales growth came out at 3.5%. The operating result is expected to remain below last year’s result at €1.4 billion (2022: €1.6 billion), the second best result in the history of the Group.
“Given the cooling global economy, we are satisfied with the past fiscal year. The sales mark of €20 billion is a special milestone for us, as it shows we were able to double our sales volume over the past nine years,” says Robert Friedmann, chairman of the central management board of Würth Group. “Last year, the Group’s heterogeneous structure across different industries and regions, and our business model, were once again the basis of our success. The construction sector, an important industry for Würth Group, showed a slow sales development, which could be compensated for by other strategic business units, such as the Electrical Wholesale unit.”
The ongoing conflict between China, Taiwan, and the USA; the wars in Ukraine, and the Middle East; inflation driven cost increases –especially for energy and raw materials; and high lending rates; all hampered demand in the construction industry, which also had a negative impact on the result.
“Achieving these results in such an environment shows that our more than four million customers greatly appreciate our products and services. They trust us and that is our most important objective. The Würth Group has proven in the past that it can overcome major challenges successfully. The solidarity of our employees and the support of the family, especially by Prof Reinhold Würth and Bettina Würth, give us the necessary stability,” emphasises Robert Friedmann.
In an economically challenging market environment, marked by a strong Swiss franc, Bossard Group achieved sales of CHF 1.069 billion (€1.113 billion) in the financial year 2023 (2022: CHF 1.153 billion) – representing a decrease of 7.4% (in local currency: -2.6%).
Bossard explains that the positive business momentum that continued into the first quarter of 2023 normalised over the course of the year. Normalisation of incoming orders in the course of customer inventory reductions seamlessly transitioned to weaker customer demand. Economic indicators also deteriorated as the year progressed. However, thanks to stable demand in parts of the growth industries, and the gratifying performance of Smart Factory services, Bossard was still able to strengthen its market position in all three market regions.
In Europe, Bossard posted a drop in sales of 6.1% to CHF 586.4 million (in local currency: -3.5%). This result was a consequence of the economic slowdown and normalisation of demand, as well as the stronger Swiss franc. Despite tough economic conditions, the electromobility and railway sectors showed positive accents. In an environment marked by inflation and a shortage of skilled labour, Bossard’s Smart Factory services drew even more attention from customers.
After a phase of double-digit growth rates, demand in America also began to normalise over the course of the year. While sales increased by 3.6% in local currency, sales in Swiss francs declined by 2.6% to CHF 301.5 million. The successful expansion of the customer base over recent years was particularly evident in the positive development of the focus industry of
electromobility. Bossard Ontario Inc, in Canada, which was consolidated since 1 st December 2022, contributed to the sales performance.
Sales in Asia declined by 17.8% to CHF 181.1 million (in local currency: -9%). Particularly in this market region the appreciation of the Swiss franc was significant. Apart from the gratifying development in India, the overall demand momentum in Asia was restrained. Especially in China, where only slight growth momentum was felt after Covid-19 restrictions were lifted. In India, Bossard benefited from nearshoring trends, a dynamic start-up landscape, as well as infrastructure projects in the focus industry of railway.
“At this point in time, it is difficult to forecast how the challenging economic environment will evolve over the coming quarters,” reports Bossard. “Based on current market observations, we expect restrained development in demand in the first half of 2024, along with a continued rise in wage levels. However, even this market environment holds opportunities for growth. The stronger trend toward nearshoring and the digitalisation of processes to increase efficiency, and productivity, should further strengthen demand for our Smart Factory services – in a current environment marked by cost and wage inflation. We continue to stand by our medium term financial goals previously communicated and the consistent implementation of Strategy 200.”
NORMA Group has presented its preliminary figures for the financial year 2023 and the fourth quarter of 2023. With slightly lower sales, the company achieved stable profitability and strong cash flow.
CEO Guido Grandi comments: “We achieved a sound result in 2023 in a challenging environment. We enhanced the efficiency of our operating business more; mitigated the effects of inflation related cost increases; and attracted new customers for our innovative joining technology. In the second half of the year, our improvement measures took effect, so that we achieved a significant increase in earnings in the fourth quarter compared to the previous year. Overall, we achieved a stable margin and considerably increased cash flow.”
Preliminary, unaudited figures put NORMA Group sales in the financial year 2023 at €1.223 billion. Compared to the previous year, the company achieved organic growth of 0.7%. Negative currency effects, however, slowed sales growth by 2.4%. Overall, Group sales were down slightly, declining 1.6% compared to the previous year (2022: €1.243 billion).
Net operating cash flow improved significantly compared to the previous year, reaching €87.3 million (2022: €65.3 million). The primary driver of the strong cash inflow was the lower (trade) working capital, as a result of consistent liquidity management and optimised inventory management.
According to preliminary figures, sales in the period from October to December 2023 fell organically by 1.7% compared to the same quarter of the previous year. This is partly due to a temporary reduction in order ‘call offs’ in the USA following widespread strikes at US vehicle manufacturers in the fall of 2023. Negative currency effects also reduced growth in the fourth quarter by 3.4%. Overall, Group sales dipped 5.1% compared to the same quarter of the previous year to €286.7 million (Q4 2022: €302.1 million).
Guido adds: “Our development expertise combined with our global presence makes us a strong partner for our customers in different markets and countries. I am confident that we will be able to generate further profitable growth in our three strategic business units of Water Management, Industry Applications and Mobility & New Energy. With our ‘Step Up’ improvement programme, we have laid an important foundation in this regard and have already seen initial successes.”
Thanks to Böllhoff Group’s broad product range and international orientation, it was able to achieve an annual turnover of €809 million in 2023 – representing an increase of around 3.3% over the previous year (2022: €783 million).
Michael W Böllhoff, co-CEO at Böllhoff Group, comments: “Despite difficult market conditions worldwide, we were able to achieve moderate growth for our group of companies. This is essentially due to our broad product and service portfolio, as well as our international company network – with our own locations in 26 countries on 5 continents.”
Co-CEO Wilhelm A Böllhoff adds: “It is especially noteworthy that Germany did not contribute to this growth. There is a pressing need for improvements of the much discussed framework conditions in our country, as well a need for more courage, confidence and trust in our own and overall economic strength, also when it comes to creating innovations.”
In 2023, the most important drivers of growth for Böllhoff Group’s sales were India, Mexico and Turkey. For the first time in many years, China did not contribute to growth, largely due to currency impacts.
Looking at Böllhoff’s individual customer groups, past investments in the expansion of the aviation business had a particularly positive effect. Since 2021, the Group has acquired two French manufacturers of special fasteners for aerospace – SNEP SA based in Montbrison, in June 2021, and Gillis Aerospace from Dieupentale, in June 2022.
Demand from the automotive industry, however, remained subdued, characterised by uncertainty in view of the ongoing structural changes in the industry.
Böllhoff Group underlines that the outlook for 2024 is difficult and uncertainty remains high. Many markets are in transition and companies in Böllhoff Group’s customer segments are reducing capacity in some cases or relocating them to other countries.
“We are therefore continuing to work on improving our productivity and processes, in order to remain an all round competent partner for joining technology for our customers,” says Michael W Böllhoff.
“We are also continuing to invest in the company, despite the difficult overall economic conditions – in 2024 this means topics related to digitalisation, as well as in the training and further education of our employees,” adds Wilhelm A Böllhoff.
SFS Group achieved its defined growth targets despite a difficult economic environment in the financial year 2023. Third-party sales of CHF 3.090 billion (€3.217 billion) were generated – a strong increase of 12.6% against the prior year period that was underpinned by robust organic growth of 2.1%. Consolidation effects stemming from the inclusion of Hoffmann as 1st May 2022, accounted for 14.6% of the sales growth.
Geopolitical and macroeconomic developments had a major impact on SFS Group’s activities in 2023. Key leading economic indicators deteriorated considerably over the course of the year. Many customers reduced their inventories as a result of the normalisation of supply chains, after Covid-19 related disruptions, aggravating the situation further.
The Engineered Components segment deftly used the seasonal ‘ramp up’ of components for use in mobile devices in the second half of 2023 to boost the results of the first half year. Demand in the segment’s other end markets remained unchanged overall during the course of the year, whereat Automotive and Medical saw very dynamic organic growth. The segment generated sales of CHF 987.7 million (2022: CHF 1.028 billion).
The Fastening Systems segment achieved a solid result in a weakened market environment with partially high-levels of inventory along the entire value chain – generating sales of CHF 615.3 million (2022: CHF 644.9 million).
After a strong first half of the year, the Distribution & Logistics segment experienced deteriorating market demand during the course of the year. This resulted in a decline in order intake, which was partially offset by the high order backlog. The segment generated sales of CHF 1.487 billion (2022: CHF 1.073 billion). Consolidation effects stemming from the inclusion of Hoffmann accounted for CHF 400.6 million of sales.
With sales growth of 9% in local currencies, Hilti Group reports that it outperformed the market with a total 2023 turnover of CHF 6.5 billion (€6.767 billion). In Swiss francs, growth reached 2.7%, reflecting a significantly negative currency impact.
At a regional level, Europe managed to close the year with sales growth of 8.7% in local currencies, primarily driven by the strong contribution from southern Europe. The Americas region grew by 9.1%, while Asia/Pacific was at 13.8%. China recovered slowly from Covid-19 lockdowns, while the rest of the region achieved solid growth rates. The ongoing war in Ukraine had an impact on the entire EEMEA region (eastern Europe, Middle East and Africa), resulting in growth of 3.1%. The continuous appreciation of the Swiss franc against all major currencies resulted in a negative impact of 6.3% on sales.
“Despite the ongoing economic and geopolitical uncertainties, we grew at a high single digit rate in local currencies and, with that, outperformed our industry. We expect a further softening of the environment in 2024 but are well equipped to face this challenge and confident to continue our growth,” reports Jahangir Doongaji, CEO at Hilti Group.
For 2024, Hilti Group expects a mid-single digit sales growth in local currencies with a significantly negative currency impact in Swiss francs.
Spanish-based Smartfix has announced Carlos Jiménez as its new CEO, as well as a host of modernisation initiatives that include incorporating a new logo, an updated catalogue and an enhanced website.
Smartfix Tecnologia & Innovacion S.L has a customer centric philosophy as the core of its business model and says it takes pride in ensuring a seamless customer experience. From an intuitive ordering process to responsive customer support, every interaction reflects the company’s commitment to provide excellent service.
New CEO Carlos Jiménez, who has taken over from company founder Jose Juan, explains: “We are committed to preserving the values that have defined Smartfix over the years. Quality manufacturing and distribution of blind rivets and self-clinching fasteners are not just a product line, but a legacy we are dedicated to preserving under new leadership.”
In 2023, Smartfix experienced significant domestic growth, solidifying its position in the Spanish market. Looking forward, the company intends to build on this success and establish its global presence in order to meet the needs of customers worldwide. “The goal is to complement established domestic growth by expanding Smartfix’s presence and influence in the international market, fostering new partnerships,” underlines Carlos. “The modernisation initiatives we have introduced – new logo, updated catalogue and enhanced website –have been carefully selected in order to deliver a contemporary and user-friendly experience for the customers, all while preserving the essential quality of our business.”
US-headquartered Simpson Strong-Tie has acquired Swiss roofing and façade fastener manufacturer, PMJ-tec AG, which specialises in A2, A4 and other high grade, corrosion resistant, stainless steel products.
Founded in 1975, PMJ-tec has its main office and factory in Switzerland, as well as warehouses and sales offices in Germany and the Netherlands. Its products, including bi-metal fasteners, carbon steel fasteners, and drainpipe couplers, are engineered with over 45 years of expertise in the construction fixing industry. They’re also manufactured in compliance with rigorous internal and external standards.
Fabio Di Clemente, director EU strategy at Simpson Strong-Tie, said: “PMJ-tec is known not only for its superior quality products, but also for its commitment to clients and service, as well as its innovation oriented culture – all of which makes it a perfect match for Simpson Strong-Tie. This acquisition introduces bi-metal fasteners to our product portfolio, which is of great strategic importance to us.”
Investment AB Latour has, through its wholly owned subsidiary Nord-Lock Group, acquired Precision Bolting Ltd (PBL) and Condor Machinery Ltd – both based in Edmonton, Canada, with a combined total revenue of around CA$7 million (€4.77 million).
Precision Bolting is a Nord-Lock Group distributor in northwestern Canada and Condor is a niche manufacturer of specialised metal components – a combination that adds great value for customers served. The companies will strengthen Nord-Lock Group’s position in Canada and contribute to the Group’s global offer within the mining segment in particular.
Nord-Lock Group comments: “We want to give our warmest welcome to all PBL and Condor employees. We have been able to get to know the companies well over the years and are impressed with
what they have achieved. We are convinced that the companies’ strengths will contribute greatly to the overall Nord-Lock Group offering and that in turn we will continue to support the companies’ ongoing growth going forward.”
Ken Gamroth and Brent Morgensen, CEOs at PBL and Condor, added: ”We have worked closely with Nord-Lock Group for many years and see this as a natural next step for the development of PBL and Condor. Together with Nord-Lock Group, and its strong market position, we are looking forward to continuing this growth journey together.”
DRIVER BTI
DUAL THREAD
FLOORBOARD
DESIGNED FOR FAST AND SECURE INSTALLATION OF FLOORING AND TO ELIMINATE SQUEAKY BOARDS.
DRIVER B
DUAL THREAD
TONGUE AND GROOVE SCREWS
A SPECIALISED SCREW FOR A SECURE AND HIDDEN FIXING IN TONGUE AND GROOVE INSTALLATIONS.
MULTIPURPOSE EXTERIOR FLOORBOARD TONGUE & GROOVE
TWO LONGER LENGTHS NOW ALSO AVAILABLE IN THE RANGE 220MM AND 240MM
PROFIL®, a leading innovator in automotive fastening solutions, has announced it has moved to new, larger offices in Italy – signalling a significant step in the company’s growth strategy. The expansive facility, strategically located on the outskirts of Milan, not only serves as a testament to PROFIL®’s commitment to excellence but also introduces a suite of capabilities aimed at providing comprehensive solutions to its customers.
The new offices feature cutting edge amenities, showcasing PROFIL®’s dedication to advancing its services – including on-site testing and prototyping capabilities, allowing for ‘real time’ evaluation and refinement of Mechanically Attached Fastening (MAF) solutions. With pre-installation services, clients can also experience a seamless integration of PROFIL® products into their systems, ensuring optimal performance.
In addition to these capabilities, PROFIL® has established a dedicated research and development centre within the new facility, poised to drive innovation and allow PROFIL® to stay at the forefront of fastening technology and meet the evolving needs of industries across the board.
Founded in 1994, MEKR´S offers a diverse range of fasteners and anchor equipment from its warehouse located in the Czech Republic. As the company continues to prioritise its focus on the export market, it remains committed to delivering innovative solutions and exceptional service not only to international clientele but also to the Czech market.
MEKR’S dual commitment underscores the company’s dedication to providing top quality products and unparalleled customer satisfaction across all regions it serves.
“In the ever evolving realm of fastener solutions, we have distinguished ourselves through our unwavering dedication to excellence, strong export orientation and exceptional customer service,” states MEKR’S s.r.o.
As a prominent wholesaler in the industry, MEKR´S has made significant advancements, driven by its innovative strategies, efficient operations and expansion of storage capabilities. For instance, its current warehouse expansion project, scheduled for completion in 2024, will add an additional 7,500 pallet spaces to the existing capacity of 15,000 pallets.
“With a steadfast focus on quality, dependability, and customer satisfaction, we have established a prominent presence in both local and international markets,” underlines MEKR’S. “Looking forward, our company remains committed to fostering innovation, cultivating strategic partnerships and exploring new avenues for growth.”
One area of particular interest for MEKR´S is the digitisation of internal systems, including the integration of AI and the automation of logistical processes. “This forwardthinking approach reflects our ongoing commitment to staying at the forefront of industry trends and delivering unparalleled value to our customers,” concludes the company.
One of the key highlights of PROFIL®’s new location is the state of the art warehousing infrastructure that houses a comprehensive stock of fasteners. This strategic move ensures customers have immediate access to an extensive inventory, streamlining logistics and reducing lead times.
Christian Pozzi, head of PROFIL® Italy, comments on the expansion:
“Our move to these larger offices represents a pivotal moment for PROFIL®. This facility empowers us to offer an unparalleled suite of capabilities, from on-site testing and prototyping to pre-installation services. The addition of our dedicated R&D centre reflects our commitment to continuous innovation, and the expansive warehousing underscores our dedication to providing swift and efficient solutions for our customers.”
In response to an increased demand for its large diameter springs, Lesjöfors Group has invested over €1 million to purchase an additional hot coiling line. This investment not only doubles its hot coiling production, but also sees the return of the hot coiling manufacturing process in the town of Lesjöfors, Sweden.
In the last three years, Lesjöfors Group has grown from a €250 million company to a €365 million company – with Lesjöfors springs used in applications across a variety of sectors such as energy, rail, mining and power generation. As heavy springs are a key component within these major global industries, it’s fitting that this investment has involved parties from all over the world.
The line was purchased from South Africa, bespoke refining elements have been added with specialist additions from China, and personnel have skill shared across these countries, as well as the UK, Finland and Sweden.
Ola Tengroth, CEO at Lesjöfors Group, reports: “Our heavy springs product range –the larger, wire size market – has been rapidly expanding across our portfolio. This latest investment is in direct response to customer demand, enhancing our hot coiling capacity and capabilities in-line with market growth – ensuring we continue to deliver the quality turnaround times and customer service we excel at.”
NEVIB, the trade association representing Dutch fastener importers, has celebrated its 10 th anniversary with the announcement of a new president – Arnoud Booij, director and owner of ASF Fischer B.V.
The NEVIB association was created 10 years ago by a group of visionary Dutch fastener importers, with the intention of setting up a body to jointly address the many challenges facing the industry. One founding member was former president Robert Klaassen, who was a driving force behind the association’s rise to become the strong organisation it is today. Thanks to his efforts, NEVIB is now the official trade association for the Dutch import trade in fasteners, recognised by governments, the European industry association, EFDA, and all other stakeholders.
Board changes at NEVIB, also announced at the anniversary meeting, include Bart Veldhuizen (from Hoenderdaal) joining the board of directors as a new member, with Vincent van Dijk remaining NEVIB’s secretary general.
Fastenal Europe has presented the ‘Best OEM Wholesaler’ award to F.REYHER Nchfg GmbH & Co KG in recognition of its achievements as a top supplier.
This award is presented in a Europe wide vote to honour top suppliers of fastener and fixing technology. The US company Fastenal is a renowned manufacturer and distributor of fasteners in the field of standard and special parts and is one of the world’s largest industrial suppliers. Its European subsidiary, Fastenal Europe, is also growing with two distribution centres, two production facilities and 75 locations throughout Europe.
Michael Martsch, vice-president of REYHER export sales (pictured on the right of the picture), comments: “We are incredibly proud of the work that everyone here has done. The award as a top supplier and the associated recognition are the result of our joint efforts. REYHER and Fastenal Europe are looking forward to continuing their good collaboration in 2024.”
With over 130 years of experience, REYHER supplies customers from industry and trade worldwide. More than 960 employees at the central location in Hamburg, Germany, ensure a reliable supply of fasteners and C-parts – with individual, flexible solutions, as well as a daily delivery availability of over 99%.
The Fastener Sector of the Confederation of British Metalforming (CBM) has announced the much aniticpated return of the CBM ‘Mini-Expo’ – unleashing an opportunity for UK fastener manufacturers to showcase their capabilities.
Set to take place on 4 th September 2024, at the esteemed National Metalforming Centre in West Bromwich, UK, this one day extravaganza is geared towards providing a comprehensive platform for UK fastener and precision component manufacturers to explore the latest advancements in fastener manufacturing equipment, technologies and services.
The CBM ‘Mini-Expo’ promises an immersive experience, featuring approximately twenty leading UK-based suppliers showcasing an array of manufacturing equipment and technologies. Attendees can explore offerings in cold heading and thread rolling machinery, process
monitoring systems, tooling and dies, coating systems, inspection and test equipment, lubricants, as well as wire and rod materials. Additionally, exhibitors specialising in heat treatment, coating and threadlocking applicators, testing and inspection, and simulation software, will be present – creating a diverse landscape for industry professionals.
“For companies interested in showcasing their products and services at the CBM ‘Mini-Expo’ please contact us for further information and to secure your exhibition space,” highlights the CBM. “You don’t want to miss this great opportunity to immerse yourself in the future of fastener manufacturing.”
Continuous growth and investments saw Spanish lathe maker CMZ deliver 549 lathes during the 2023 financial year, achieving an unprecedented turnover of €110 million – exceeding its strategic plan and beating its previous turnover record.
With a clear target of achieving a €100 million turnover by end of 2024, the company invested in technology and facilities to meet high market demand. However, at the end of the financial year 2023 CMZ had not only exceeded forecasts by 10% but had done so a year early.
CMZ Machine Tool Manufacturer S.L is responsible for product lifecycle from beginning to end, with the company owning the technical support service for all its lathes and aftersales service. In the financial year 2023, the technical support service achieved a €10 million turnover from over 3,600 interventions and delivering 6,747 spare parts. The company’s technical customer hotline, manned by CMZ engineers, also handled a total of 15,000 calls.
Sales of CNC lathes accounted for around €100 million. Of those sales, 75% were exports, the company’s six European subsidiaries and its own wide network of distributors enabled supply to both the domestic market and the ‘old continent’. Almost 10% of sales were to demanding international markets such as the USA and Turkey, which the company believes has great potential for future business.
In addition, in early 2023, CMZ launched the renewed online tool holder shop, CMZ Store, which had processed around 700 orders by the end of last year – with an average ticket
price of €1,645. Thereby enabling the company to provide support and streamline the entire purchase process for its lathes.
2023 also saw the opening of CMZ’s sixth European subsidiary, CMZ Denmark, strengthening its international expansion plan. The Danish market’s potential enables CMZ to increase its market share and offer a more customer friendly, direct service.
To handle last year’s investments in production equipment, over 40,000m 2 of usable space was made available for manufacturing and marketing CNC lathes,
including the opening of CMZ Denmark, and the new Precitorm– cylindrical parts machining plant in Elorrio – which triples the old plant’s surface area. The company points out that by investing in facilities with the latest technology and centres, high market demand can be met with a product in which more than 80% of components are made at its own facilities.
CMZ is now planning to focus on increasing production capacity to 800 CNC lathes a year and aims to open a US subsidiary in late 2024.
While the National Transportation Safety Board (NTSB) works to establish whether the door plug that blew out in mid-air, on a 5 th January Alaska Airlines flight, was outfitted with the four bolts that prevent it from vertical movement, it’s becoming clear where the responsibility lies.
Dominic Gates from the Seattle Times reported: “The door plug that blew off the Max 9 was removed for repair, then reinstalled improperly by Boeing mechanics at the Renton assembly plant. That leaves Boeing primarily at fault for the accident, rather than its supplier, Spirit AeroSystems.”
Boeing issued a bulletin to its suppliers to ensure bolts are properly torqued, after multiple airlines reported loose fasteners during inspections of the grounded 737 Max 9, according to a 17 th January memo.
The aerospace manufacturer said that it is “imperative” that suppliers meet quality requirements, according to the memo, which was issued weeks after an accident when a panel ripped off a 737 Max 9 jet in mid-air.
The Federal Aviation Administration (FAA) grounded 171 Max 9 planes with the same door panel configuration.
“Ensure that work instructions are mistake-proof and quality is continuously monitored – particularly torqueing requirements,” the memo stated. The bulletin suggested that suppliers document torque requirements on work instructions, require mechanics to record how much torque is applied when fastening components, and ensure tools are calibrated, so bolts are properly tightened.
Ben Minicucci, CEO at Alaska Airlines, said the airline found “some loose bolts on many” Max 9s during inspections. Other airlines reported
similar findings, and the NTSB is currently conducting destructive testing of the door plug. While investigators have yet been unable to establish whether the plug was outfitted with the four bolts that prevent it from vertical movement, it is too early to say whether the root cause was missing or wrongly installed bolts, according to NTSB chair, Jennifer Homendy, who said: “We’re also looking at the seal. We’re looking at whether there was any sort of structural flexing of the aircraft? It may not be bolts.”
Homendy’s comments come days after the FAA announced that it will increase oversight of Boeing and audit production of the 737 Max 9 jet liner. It will determine whether Boeing, and its suppliers, followed approved, quality procedures. The FAA also said it’s reconsidering its long-standing practice of relying on aircraft manufacturer employees to perform some safety analysis of planes.
The catastrophic failure occurred when a door plug blew off a new Alaska Airlines Boeing 737 Max 9 at 16,000 feet, imperilling 171 passengers and six crew members. Four ‘stop’ bolts should have prevented the door plug from moving upward and coming off the plane. But the bolts were not on the recovered door plug, and investigators are trying to determine whether they were even installed. “We don’t know if they were there, or if, again, they came out during the violent explosive decompression event,” Homendy stated.
A fastener company’s adoption of Artificial Intelligence can be important in hiring younger employees who want a “forward thinking company,” Panellist Lonni Kieffer, of SmartCert, pointed out during a National Fastener Distributors Association panel on ‘Using the Power of AI and automation to make your business more efficient’.
Panellist Rosa Hearn, of Brighton-Best International, declared: “It’s here, AI is knowledge feed and we have been feeding it for years.” Any postings to Facebook or Google are now somewhere in AI, Hearn explained – advising checking what AI knows about your company already. “Be careful what you put into ChatGPT,” she cautioned. She cited the incident of a Samsung engineer posting new proprietary information and “now those company secrets are in the public domain”.
Can AI make you a better salesperson? AI can learn about Rosa’s style from Facebook, LinkedIn and emails and be told to write a ‘personal’ email to a customer.
“Is it good enough to give the customer the ‘fuzzy wuzzies’? Hearn asked. “Time will tell.”
AI “doesn’t know how to say ‘I don’t know,’” Hearn pointed out.
Lonni Kieffer, co-founder of SmartCert, said AI isn’t really new if you think of consumer use of thermostats, GPS, online shopping and social media. Those have been moved from paper to digital and “these tools are all meant to provide efficiencies”. It is also part of “continuous learning” needed in “upscaling workers”.
Kieffer sees SmartCert’s job as a “technology partner” helping to “make life easier”. AI can read documents on your behalf, eliminate human error that you have with manual entry and create searchable data. Older emails are “fraught with peril”, Kieffer said.
“AI is going to get smarter yet,” Kieffer predicted.
The global market for industrial fasteners, which totalled US$89.7 billion in 2022, is projected to reach US$124.9 billion (€115.3 billion) by 2030, growing at a CAGR of 4.2% over the analysis period 2022 – 2030, according to a new report by Global Industry Analysts Inc.
Metal, one of the segments analysed in the report, is projected to record 4.1% CAGR and reach US$110.4 billion by the end of the decade, while growth in the plastic segment is estimated at 5.5% CAGR.
China is forecast to reach a projected market size of US$24.9 billion by 2030, trailing a CAGR of 5.6% over the 8 year period. Other noteworthy geographic markets, include Japan and Canada, each forecast to grow at 2.9% and 3.5%, respectively. Within Europe, Germany is forecast to grow at approximately 3.1% CAGR.
According to the report: “The global economic outlook is improving and growth recovery, albeit on the lower side, is expected for this year and the next. The US, although witnessing slowing GDP growth in response to tight monetary and financial conditions, has nevertheless overcome the recession threat.
Easing of headline inflation in the Euro area is helping boost real incomes and is contributing to pick up in economic activity. China is expected to see strong increases in GDP in the coming year as the pandemic threat recedes and the government sheds its zero-Covid policy. With optimistic GDP projections, India remains on course to emerge into a US$ trillion economy by 2030, surpassing Japan and Germany.”
“The upturn, however, remains fragile,” the report stated, “and a number of interlocking challenges continue to run in parallel, such as continued uncertainty around the war in Ukraine; slower than expected decline in global headline inflation; continuation of food and fuel inflation as a persistent economic problem for most developing countries; and still high retail inflation and its impact on consumer confidence and spending”.
The report continued: “Countries and their governments are showing signs of weathering these challenges, which helps lift market sentiments. As governments continue to combat inflation to get it down to more economically conformable levels, by raising interest rates, new job creation will slow down, and impact economic activity. A
stricter regulatory environment and pressure to mainstream climate change into economic decisions will compound the complexity of challenges faced.”
“Although corporate investments can likely be held back by inflation worries and weaker demand, rise of new technologies will partially reverse this prevailing investment sentiment. The rise of generative AI; applied AI; industrialising machine learning; next generation software development; Web3; Cloud and edge computing; quantum technologies; electrification and renewables; as well as climate technologies beyond electrification and renewables; will open up the global investment landscape. These technologies hold the potential to drive sizable growth and value to global GDP in the coming years.”
The FIN Fastener Stock Index roared back in 2023, growing 44.3% in value, compared to an 18.3% gain by an index of related industrial stocks, and this in a rocky economic year that eventually produced a ‘recovery’ in US industrial fastener demand.
Three of the thirteen companies tracked by GlobalFastenerNews.com’s FINdex achieved significant growth during the year: Simpson Manufacturing, for example, soared 123%, defying broader market adversity with continued earnings growth; Park-Ohio, for its part, also finished strong, gaining 120% in stock value during the year; and Carpenter Technology saw its shares rise 91%.
Over the year, the FINdex achieved strong growth in three of the four quarters, including a 17.2% increase in the final three months of 2023. During the first nine months, the FINdex gained 23%, compared to a 5.6% increase by an index of related industrial stocks.
In 2022, the FINdex lost 11.5%, besting a 15.5% decline by an index of related industrial stocks.
In order to assist domestic Taiwanese enterprises to reduce carbon emissions and create a fair, safe and transparent carbon credit trading system, Taiwan Carbon Solution Exchange, (TCX), jointly invested in by the Taiwan Stock Exchange and the National Development Fund of the Executive Yuan of Taiwan, officially launched its International Carbon Credit Trading Platform at the end of 2023.
Unlike other countries with carbon credit trading platforms that operate on a for profit business model, and in order to avoid market speculation, the buyers on Taiwan’s new platform are limited to domestic legal entities and only allowed to hold, cancel and transfer carbon credits. Sellers must be foreign, or domestic legal entities, with the carbon credits’ trading and payments processed in the form of advance receipts, with credits sold according to quotations; the unit of transaction is 1 tonne of CO 2 equivalent, traded in US dollars. The platform is not open to the general public.
For the sellers’ part, they are specifically required to meet the relevant standards for carbon credits (e.g the carbon credit issuer should be accredited by TCX), the vintage of the carbon credits should be within five years and the carbon credit projects should satisfy at least three of the UN’s Sustainable Development Goals, amongst other things.
TCX hopes that through the establishment of this platform, it can effectively match supply and demand, create incentives for enterprises to reduce carbon emissions, as well as further promote the development of low carbon production technologies and innovative industries.
Source: Fastener WorldWire rod prices are on the move and, according to Taiwan China Steel Corporation’s (CSC) latest reports, the global steel industry has hovered low for a year and a half and stockpile in the downstream is at a relative low, reports Fastener World.
This suggests that steel price and supply is bound to go higher in the first quarter of 2024. Taiwan CSC says that by taking the rise in steel refining material cost and international steel prices into account, led to it raising the wire rod price in January to cope with increased material costs.
It said the first quarter price for 2024 has, therefore, been reflected in accordance with the status of downstream industries.
For wire rod, encompassing low/mid/high carbon, cold headed, and low alloy steel, a price adjustment, (NT$ per tonne), of plus NT$800 has been necessary, while for automotive materials, a price adjustment of plus NT$500 has been made for the quarter.
The Directorate General of Trade Remedies (DGTR), a division of the Commerce Ministry in India, has launched an anti-dumping investigation into the import of fasteners from China. This action was prompted by both sectors’ associations, which reported substantial harm to their respective industries due to a significant influx of these goods from China at dumped prices.
Indian producers have made representations before the authority claiming that prima facie evidence exists, indicating the injury suffered by the domestic industry because of the dumped imports. The associations have highlighted a significant rise in both the absolute and relative volume of these imports from China. The DGTR has expressed its contentment with the accuracy and sufficiency of the information presented in the representations.
The DGTR said that in light of the well-substantiated representations submitted by Indian producers of the specified goods, and after a thorough assessment of the prima facie evidence provided therein regarding the dumping of these goods from the subject country, as well as the resulting harm to the domestic industry, the authority has initiated an anti-dumping investigation.
Source: Chinafastener.com
At the end of last year, the Taiwan Industrial Fasteners Institute (TIFI) held the 19th (4th round) member representatives meeting and the 10th (9th round) joint meeting of the board of directors and supervisors at HI-LAI Arena in Kaohsiung, Taiwan.
During the meeting Tu-Chin Tsai, chairman at TIFI, commented:
“I’d like to thank all fastener industry professionals and seniors for their support to TIFI and thank Taiwan CSC for its great assistance to the Taiwan fastener industry. Thanks to the efforts of all of you, the output value of the Taiwan fastener industry reached NT$200 billion in 2022. However, we would like to remind our friends – who are mainly engaged in the European and American markets –to pay more attention to the current ESG, energy saving and carbon reduction, CBAM, and changes in the international regional situations, and to think carefully before making any major investments. This will mean we can continue to maintain a leading edge in the future in the competition from the same industries in Vietnam, China, Indonesia, and Thailand, etc.”
At the meeting Min-Hsiung Liu, vice-president (commercial division) at Taiwan CSC, also spoke: “At present, the global market has shown an improvement. According to the recent statistics of TIFI, the export volume of Taiwanese fasteners from January to November in
2023 reached more than 1.1 million tonnes. Although the export volume declined by 16.3% in a single month, compared with the average 25% decline in January to November, it has been converged. The internal survey of Taiwan CSC also shows that the orders from small screws customers have shown an increase of about 20%, and those from wire drawing customers have shown an increase of about 20% – 30%. We’re confident that the fastener industry will gradually improve. With regard to carbon neutrality, Taiwan CSC will also assist in conducting carbon inventories and will work together towards low carbon/digital/supply chain transformation, and work towards high value added products.”
As part of the meeting Chairman Tsai also announced that after the Taiwan International Fastener Show, which is scheduled to take place on 5 th – 7 th June 2024, TIFI will hold a member representatives meeting again to re-elect the board of directors, supervisors, permanent directors and supervisors, supervisors convener and the new chairman.
Source: Fastener WorldBocast has announced at a technical exchange meeting for new product releases that zirconia ceramic fasteners would soon enter mass production after eight months of technical research, reports Chinafastener.com.
It is understood that the R&D team of Bocast, under the guidance and collaboration of Professor Xiong Yan from the school of materials at Hubei University of Technology, overcame multiple technical difficulties – such as cracking and sintering deformation in the development of zirconia ceramic fasteners –and achieved ‘one time’ moulding of the final product form through mould design.
Zirconia ceramic fasteners solve the non-conductive, non-resistant to high temperature and strong acid and alkali problems of non-metallic fasteners. They can be widely used in electronics, shipbuilding, medical, aerospace and other fields, with an annual total market demand of over 400 million pieces.
The railway industrial product ‘variable-tooth-type anti-loosening nut’, developed and produced by Qifeng Precision Industry, has passed the trial detection of relevant units in the railway system and has been recognised to the technical standard of Q/CR 484-2015.
The successful research and development of this product will promote the application in the railway transportation field and meet the safety requirements of railway construction and maintenance.
The anti-loosening nut developed and produced by Qifeng Precision Industry has excellent resistance to transverse vibration; can effectively solve the problem of thread loosening; and can be applied to a number of industries such as aerospace, shipbuilding, railway transportation, agricultural machinery and others.
Source: Chinafastener.com
Chinafastener.com reports that the plate and strip plant of Northeast Light Alloy has successfully rolled a certain high magnesium aluminum alloy fastener, laying a solid foundation for rolling more high magnesium content alloys in the future.
During the production debugging stage, after multiple rounds of debugging and production failures, the manufacturer’s debugging personnel confirmed that this machine did not have the ability to produce such high magnesium rods. However, the plate and strip plant, with an unyielding spirit, established a special group composed of equipment technical experts and pooled their efforts to tackle the production work of this fastener, even when the equipment manufacturer’s personnel had all left.
Once again, the Anuário do Parafuso – an annual fastener Brazilian buyer’s guide, distributed to the same readers of Revista do Parafuso –was published, with this year being the 10 th edition. To mark the occasion a comparison was published comparing the fastener sector in 2014 and the fastener sector in 2023.
Firstly, it is important to clarify that Brazil has more than 211 million habitants, 4.5% above the 202 million in 2014. Ten years ago, there were around 450 local fastener manufacturers, with 18% less in 2023 at just 372.
From December 2022 to November 2023, the local steel production was 31.15 million tonnes, around 8% below the 33.89 million tonnes produced in 2014. On the other side, the local petroleum production jumped more than 71%, from 2.1 million per day in 2014 to 3.6 million last year.
During January to December 2023 Brazil imported 189,900 tonnes of fasteners at a total value of US$977 million (FOB price of US$ 5.15 per kg) This is 4.34% above the 182,000 tonnes imported in 2014, and 1.5% up on the total value of US$962 million (FOB price US$5.28 per kg).
Brazilian fastener exports reached 30,700 tonnes for 2023, at a total value of US$182 million (FOB price at US$5.92 per kg), which is 18.5% above the 2014 export volume of 25,000 tonnes and 28% up on the US$131 million total value in 2014 (FOR price was US$ 5.16 per kg).
An interesting comparison is between automotive vehicles, in which the motorcycle sector produced 1.573 million units in 2023, the best historic result, superior to the 1.517 million units in 2014. If passenger cars, buses, and trucks, had experienced a similar increase then Brazil, maybe, could be back on the front cover of The Economist Magazine, as happened in November 2009. However, 2023 closed with 2.324 million units produced (121,133 buses and trucks), more than a 35% decrease compared to the 3.151 million (172,902 buses and trucks) in 2014.
Belenus celebrates its 20th anniversary in 2024, having established itself as the biggest Brazilian fastener manufacturer of nuts, bolts, and special parts.
The history of the business started at 1960, when João Lucas, an ex-taxi driver, became a fastener resale manager. In 1978 he opened his own resale company, having at his side João Marcos Lucas, his son. Under João Marcos, the company experienced a meteoric trajectory and prosperity. In 2004, Sergio Lucas the son of João Marcos Lucas, was already at his side and he created a new company named Belenus – starting a new era as a fastener manufacturer.
During the last two decades the rise and growth of Belenus has changed the landscape of the Brazilian fastener market. Beyond fastener production, the company continued to grow and became a group with operations in other sectors, such as distribution of hardware, tools, and various types of equipment, as well as parts for solar energy installations.
Today, Belenus has around 1,700 employees across the different divisions of the group and has a production capacity to process 10,000 tonnes per month at its fastener manufacturing unit.
In the recent Janus Perspective within Fastener + Fixing Magazine (Issue 145, page 86), it was stated that 2.359 million cars (among passengers and commercials cars, buses and trucks) were produced, but this was just an estimate from ANFAVEA –the local Brazilian automotive manufacturing association. The actual figure produced in 2023 was 2.324 million.
A commitment to quality, modularity, excellence, reliability, customer centricity, continuous improvement, innovation, team working, and employee engagement, are the core values that have been defining SACMA Group since 1939 –making it the world leading manufacturer of multi-station cold forming machines for high-precision metal components and fasteners.
At its headquarters in Limbiate, north of Milan, Italy, the 60,000m 2 plant is the beating heart of SACMA Group.
Here, through an insourced, fully vertically integrated and modular production system, the company machines mechanical parts with the highest standards for precision and raw material quality. Each workpiece is then assembled in-house and becomes part of either a SACMA multi-station cold forming machine or an Ingramatic flat die thread roller.
“These machines then share the same destiny – accompanying customers for the next half century in their workshops, rewarding them with the highest output possible – three shifts per day,” states SACMA Group.
In the last 15 years, SACMA has also been dedicating its efforts in extending its product portfolio through strategic acquisitions and product innovation. The result is what SACMA Group is today – an industrial ecosystem for the fastener and cold forming industry that is able to offer cutting edge technologies from process design through to 3D simulation, such as multi-station cold forming equipment (SACMA), flat die thread rollers (Ingramatic) all the way to dedicated CNC machines for secondary operations after forming and threading (HS ASPE). In addition, anything that goes in between these steps requires stable, high efficiency loading and moving systems and for this SACMA Group supplies reliable solutions through Tecno Lift.
Our business model is focusing on proposing everything possible to support our customers to manufacture fasteners at the lowest cost possible, with the best quality…”
“Our business model is focusing on proposing everything possible to support our customers to manufacture fasteners at the lowest cost possible, with the best quality, thanks to our machineries and ancillaries,” underlines SACMA Group. “Our target is to provide premium machineries to manufacture parts and help the new generation of technicians to work safely, whilst respecting conditions regarding sustainable, which are today’s mandatory key factors. We also invest more than 10% of our sales turnover every year in machineries and buildings to further improve our productivity and to be more efficient.”
SACMA Group adds: “Each entity of the group also has its own R&D, manufacturing department and assembly lines. We strongly believe that it is better to grow in supplying more kinds of machineries, with different entities such as our four brands, than to make more machinery. By proceeding like that we have perfect control of the quality of our products to please the worldwide market.”
SACMA Group is focused on different key markets everywhere in the world and will be busy supplying machines to the worldwide fastener market for both 2024 and 2025. “This is mainly due to the reshoring strategy companies are operating since the Covid-19 period, as well as the increasing demand for machines to supply more fasteners to the automotive market –supported by the EV sector’s growing production,” reports SACMA Group. “We have also seen a lower demand for machines from the construction market, due to the decrease in this sector – impacted by the higher interest rates. However, heavy construction is still demanding bigger sized machines for structural bolt production in order to support the large-scale public works confirmed by different countries around the world.”
The aerospace market has also demonstrated a dynamic trend allowing SACMA Group to supply more Ingramatic and SACMA warm forming machines, and also HS ASPE drilling/tapping machines, to run parts with special materials such as titanium, waspaloy, A286 and inconel. The electrics and general industry fields have also been very active with a lot of requests for smaller machine sizes.
“End users have a high appreciation of SACMA machines, considering them to be well designed, well manufactured, powerful, adaptable
for making special parts, flexible for making long or short parts, as well as being fast and reliable whilst providing low cost production,” underlines SACMA Group. “Our modular system is the best warranty for customers to standardise their process, tooling design and friendly user experience. We have more than 20 million spare parts in stock –making our Group the most trustworthy supplier of machineries. This last advantage allows our customers to have our machine always in condition to manufacture parts without any interruption.”
Another aspect that has enabled SACMA to stand out within the market is the tendency of customers to invest in combined machines that have multi-operation all in one machine. “This provides the best solution for high productivity requirements, consolidation of production methods, floor space usage and workflow in a fastener manufacturing environment. It also makes the production of our customers much more sustainable, which is today a strategical necessity,” underlines SACMA Group. “We are a unique manufacturer able to provide all these solutions, SACMA can provide combined headers with heading, pointing and threading stations; Ingramatic provides the combined threaders with washer assembly, rotative threading and flat dies threading stations; and HS ASPE provides combined secondary operation machines with drilling, chamfering and tapping stations ‘all in One’.”
In total, SACMA Group boasts more than 80 machine models including presses, rolling machines, chamfering machines, tapping machines, drilling machines, lathes, transfer and multi-spindle machines, as well as workpiece handling systems – with a worldwide installed base of around 10,000 machines. “For this reason, we are finalising the construction of a building at our headquarters in Limbiate, Italy, that will be dedicated to the service and assistance activities in order to perform additional support to customers,” highlights SACMA Group. “In addition, we have just finalised the new extension at Tecno Lift to increase its capacity – as the company has been increasing its sales turnover by 15% – 20% every year.”
Other investments within the group include the SACMA Vimercate division completing the installation of an FMS line with four horizontal CNC machines – completely equipped with fully automatic loading systems to run parts 24 hours. “This line includes the most advanced features to run our components with a higher quality in a shorter time –helping us to significantly increase productivity,” points out SACMA Group. “In order to facilitate the management of the supply chain, we have also made large investments into vertical storage system in all of our factories – to have a better control of our stock and suppliers.”
With technology continuously advancing at an unprecedented rate, SACMA Group believes it is crucial that it stays at the forefront of the
At SACMA Group we are able to provide a full service to integrate more machines, with different technologies, in order to make a fully integrated cell…”
sector when it comes to implementing new solutions. “As a business we cannot allow ourselves to fall behind, which is why our skilled R&D engineers are committed to hunting down the industry’s most valuable technological innovations,” mentions SACMA Group. “However, it’s not just about discovering them. It’s also about envisioning how they can be integrated into our production processes, machinery, and activities as a whole, as we strive for continuous improvement.”
After selecting and designing an innovative solution, SACMA Group also has a laboratory that is dedicated to testing a solution for at
least two years. “This is the only way to guarantee perfect functioning before looking to apply the solution to our machines and according to our serial production strategy,” explains SACMA Group. “We also have an innovative service to develop new activities or new products through our S-Tooling department, which is where we co-engineer with our customers from the drawing of the part to the industrialised project.”
In addition to staying at the forefront of innovation, SACMA Group also looks to stay ahead when it comes to some of the key topics impacting global markets, for instance sustainability. “For sure sustainability is a topic that we are focusing on and we will need to continue to work on it going forward,” reports SACMA Group. “We believe that we are only at the beginning of what will be a long process when it comes to sustainability. This is because many machines will need to be replaced by new ones that consume less and can make netshape parts in one step – such as with our combined headers, combined threaders and combined machining machines. This series of machinery is also developed with mechatronic solutions to make them energy efficient.”
Internally SACMA Group has also taken steps and made investments when it comes to sustainability. “We have already invested in photovoltaic solar panels and this year all of our companies will be self-sufficient using green energy for the heating, air conditioning and electricity for all of our offices,” mentions SACMA Group. “We will also publish our first sustainability report by June 2024. We believe sustainability is a crucial topic and we want to have the best conditions to be the most sustainable manufacturer of machineries – having a perfect vertical integration of our process, made 100% internally in our factories, as well as using only raw material sourced in Italy.”
Another area in which SACMA Group has taken significant steps is in regard to Industry 4.0 and digitisation, with the Group already offering different options to customers. “We have created new options for all of our machines to integrate with Industry 4.0, which can be customised based on the customer’s level of digitalisation,” highlights SACMA Group. “From a ‘simple’ option to the ‘full advanced’ option, customers can access a range of data, such as machine alarm statistics, energy consumption in kWh, as well as compressed air consumption in cubic metres, for each order. We also have the SACMA 4.0 web App, which can be viewed on a PC. In addition to the information described above, customers can access the electrical, hydraulic and pneumatic diagrams, which can also be consulted from a tablet or smartphone via QR code on the machine.”
To add to Industry 4.0, and digitisation, SACMA Group is also working on how automation can help provide benefits to both the Group and its customers. “Automation has an important role in helping the technicians to work on the forming machines in order to facilitate their work and we believe automation is an opportunity to make the machines user-friendly,” explains SACMA Group. “That is why we have developed a new HMI program to manage the automation of the machine set-up. From the touchscreen panel, according to the machine model, it is now possible to set-up the entire machine. For example, for bigger SACMA formers, the S-Transfer is available to have the machine fully automatic. Speaking about secondary operation machines, HS ASPE can implement robots to load and unload tools and/or parts. Tecno Lift can also supply automatic devices to create fully integrated cells with more machines connected with loaders and conveyors.”
SACMA Group concludes: “It is clear that the fastener industry is looking to simplify processes with new machines that can help to reduce the overall number involved in making more parts, whilst also requiring less operators and using more automation to help improve the flow of the parts, with attention also given to sustainability. At SACMA Group we are able to provide a full service to integrate more machines, with different technologies, in order to make a fully integrated cell that truly meets and exceeds the needs of every customer.”
www.sacmagroup.com
For over 35 years, Marco Pizzi has developed expertise and knowledge in the mechanical sector, specifically in the field of fasteners. Now he has finally embarked on the path of translating his managerial experience into entrepreneurship through International Hi-Tech Consulting.
Founded as a communication and technical/commercial consulting agency, International Hi-Tech Consulting Srl (IHTC) designs and provides turnkey equipment, as well as a support service in Italy for their set-up. “We represent the best brands of fastener machinery on the market, including Nedschroef Machinery, Doss Visual Solution Srl, Tramev Srl, Tecnopress Srl, CMS Costruzione Macchine Speciali, Allways Precision Inc, Omig Srl, as well as many others,” explains Marco Pizzi. “We work alongside our clients, offering the best services and guidance, as well as ensuring that they are not just purchasing specific machines or products but are being well guided and supported so that the entire process and investment can become operational within the expected timeframe and with the promised performance.”
Marco adds: “We position ourselves proactively in the market, listening to the needs and desires of our customers and presenting them with a range of proposals and solutions. We don’t operate as traditional agents or representatives; instead, we prioritise offering technical solutions. We sit alongside our clients, helping them evaluate not just a brochure but thoroughly studying, assessing and advising on the best
project and solution for their needs. This is what we do, and it’s what our clients expect from us.”
Within the organisation, IHTC also has designers, process engineers, industrial experts, and capable managers, all dedicated to delivering the best results. “We leverage the expertise of the world’s best industrial partners. The combination of these forces, extensive global experience, and, most importantly, a spirit of innovation and result oriented research, leads us to position ourselves as the best partners in service of the customer,” underlines Marco.
With the current market subject to multiple challenges, including significant fluctuations in costs; immediate and drastic increases and decreases in demand; as well as uncertainties and confusion in supply and demand; Marco believes that innovation is the only want to stay ahead. “This doesn’t just mean purchasing new machinery; it entails studying innovative strategies, reorganising structures, as well as enhancing skills, and response times, to not only maintain relevant positions in the market but also effectively manage external factors and, consequently, costs. At IHTC we offer this kind of service, supporting technological proposals without imposing or limiting the project. This may even involve guiding companies through change with our consultancy, and then the client choosing to entrust the purchase of machinery to third parties. Our objective is broad ranging, aligning with our mission to provide the best solution for achieving the goal.”
We position ourselves proactively in the market, listening to the needs and desires of our customers and presenting them with a range of proposals and solutions.”
With IHTC already securing several significant projects, Marco is looking forward to meeting both existing and new customers at wire® Düssledorf to further consolidate IHTC’s strategy and position. “We plan to participate at the wire® show (hall 16, stand G62) with a stand filled with innovations, information, proposals, and above all, a spirit of collaboration and joy. Because work should be a joy, not a pain. We look forward to welcoming customers in Düsseldorf to meet our team.”
In addition to IHTC, Marco has also established two other companies –BELOWTHELINE Srl and SMARP Advisor Srl – with each division working closely with one another to provide support and services based on the project.
Marco explains: “ BELOWTHELINE is a communication and marketing agency that – leveraging a team of communication, marketing, and 3D video creation graduates – utilises cutting edge techniques and technologies to assist clients in promoting their products and services. Currently heading this division is my son, Alessandro Pizzi, who holds a BA in creative technologies from one of the most renowned and prestigious Italian universities, La Nuova Accademia delle Belle Arti (NABA) in Milan.”
SMARP Advisor serves as the Group’s holding company, exclusively dedicated to overseeing and executing extraordinary operations in the financial and industrial sectors. “We have already successfully executed several mandates for the sale and, in some cases, the identification of Italian and foreign companies, including three European fastener manufacturing companies,” points out Marco. “Our team, with decades of experience, specialises in management, analysis and organisation – complemented by an international legal office operating in Europe and the USA. We can support entrepreneurs and groups in one of the most critical phases of a company’s life and development – from analysis and search to negotiation – identifying the best partner, project, and valuation, whilst guiding them through every stage of due diligence to closing.”
Marco adds: “Our knowledge of the global market, excellent reputation, and understanding of industrial processes, position us at the forefront of this sector – providing support and satisfaction to both financial stakeholders (such as private equity and investment funds) and purely industrial entities.”
UK-based Apex Stainless is looking forward to 2024 as it plans to increase the use of data within the business, thanks to a new ERP system that will help unlock more efficiency gains, as well as deliver a better customer experience.
Over recent years Apex Stainless has taken several steps in various functions within the company in order to use data to help deliver business benefits and gains. The new ERP system is the next step in this process and the company hopes it will act as a catalyst for the business going forward.
“After 32 years, we decided in 2023 that it was the right time to change our ERP system,” explains David Vahter, managing director at Apex Stainless Fasteners Ltd. “From the very first day of setting up the system we were able to sell, distribute and invoice. Whilst, as one might expect, it took a while to settle into the new system, after only a few weeks we were already back at the service levels we expect.”
David continues: “We are convinced that we can use data to help further streamline the business and we achieve this through a combination of improved performance within our operations and through the delivery of new digitised services. For example, orders are now completely paperless, which is also an important step forward in our drive to achieve a sustainable future.”
Finding those wins for the company, and its customers, is going to be a key focus in 2024 for Apex Stainless, especially after the challenges of the previous year. “I think it is fair to say that the market leading up to 2023 was quite turbulent and while we saw supply stabilising during the year, due to a lower underlying demand, there were still several other macroeconomic challenges we needed to manage,” reports David. “Inflation, low unemployment and high interest rates were on top of the agenda in most countries. The cost of running a business today is far from pre-pandemic levels, which I think will continue to be a defining factor over the coming years for many businesses.”
David points out that 2023 was also the year to prepare for the introduction of new compliance directives, such as Russian Sanctions and CBAM, and in both cases BREXIT was a complicating factor. “In some aspects, we are pushing paper like never before and the importance of data is proving more and more crucial when it comes to these new regulations and directives. Compliance is certainly an area that is requiring more attention by businesses. For some of our customers the burden of compliance will open up a few questions in terms of their own supplier base, which is why it is important we are able to show that we are at the forefront of managing this topic.”
Looking forward, David also believes there is an opportunity for the business through nearshoring, with the various challenges within the world leading to uncertainty within markets. “Russia’s illegal invasion of Ukraine does not seem like it will be resolved anytime soon, with the consequences of the war having now reached the Far East supply side with the introduction of UK notice NTI2953 and EU regulation 833/2014
In this aspect, businesses like Apex, can add real significant value to our customers…”
(11th package). In 2024 there will also be the presidential elections in the USA, which have the potential to create more uncertainty. US politics under Biden have been characterised with a move away from China as one of its main trading allies. It is clear from the outside that when China’s ambition changed to producing more sophisticated products, they became more of a threat for the US than just a trading partner of low cost goods. With China being a more prominent figure in the East, and South China Sea, as well as the controversy around Taiwan, one can perhaps foresee more upcoming political tensions.”
David continues: “These topics matter because cash flow, lead times and compliance will all be big considerations for businesses in 2024 and beyond, with companies looking at their suppliers. In this aspect, businesses like Apex can add real significant value to our customers by offering them stock on a short lead time, with sound payment terms and without the need to reassure a certain compliance across a large number of parts and suppliers. Through the foundations that are already in place, as well as the ongoing investments into our operations, we are very excited to see where it takes the business in the next few years, because it has the potential to be highly transformative for us.”
www.apexstainless.com
Empowering
Remaches Tudela continues to forge its path as one of the leaders in the fastener industry, combining the best of tradition and innovation –with a history spanning three generations and an unwavering commitment to quality and innovation. Here we speak to Isaac Ciordia, CEO at Remaches Tudela S.L, who explores the key aspects that have driven the company’s sustained success.
Remaches Tudela has been a key player within the fastener industry for decades, what do you think has been the key to staying ahead of the curve?
“Our strength lies in our unique combination of tradition and the avant garde. Over the years, we have maintained an unwavering focus on the quality of our products, using the latest technology available to constantly improve. Adapting to technological advances has been essential. However, we have never lost sight of the craftsmanship and know-how accumulated over three generations.
This generational continuity has been an invaluable asset. We are proud to pass on, from one generation to the next, the commitment to quality, business ethics and respect for our customers. This heritage has given us a unique perspective that combines accumulated experience with an open mind to innovation, allowing us to offer products that fuse the best of the past and the present.”
How has investment in technology led to a improvement in the quality of Remaches Tudela’s products?
“Our constant investment in technology has been a fundamental pillar. The introduction of state of the art machinery has allowed us to increase the precision in the manufacture of our rivets – guaranteeing quality standards that exceed market expectations. This not only translates into durable products, but also into solutions that meet the highest safety standards.”
Can you share with our readers any recent project or development that highlights the innovative capacity of Remaches Tudela?
“We have recently launched a rivet line that incorporates cutting edge technologies, improving the strength and durability of our products. In addition, we have implemented more efficient production processes – reducing our environmental impact and reaffirming our commitment to sustainability. These advances reflect our constant effort to exceed market expectations.
Remaches Tudela continues to forge its path as a leader in the fastener industry, combining the best of tradition and innovation. Our focus on quality, technological advances and know-how passed down from generation to generation positions us as an undisputed benchmark in the sector.”
www.remachestudela.com
We are proud to pass on from one generation to the next, the commitment to quality, business ethics and respect for our customers.”
Fastener shortages are a critical issue in the manufacturing sector, causing significant production delays and impacting overall efficiency. As a manufacturer, it’s essential to understand the triggers of these shortages and implement strategic solutions to navigate these challenges effectively. This guide explores the causes of fastener shortages and provides practical solutions, with a special focus on Fabory Logic’s smart logistics and inventory solutions.
Fabory is a leading specialist in fastening solutions and related products, offering a vast catalogue that includes over 150,000 fasteners and a comprehensive range of tools, industrial supplies and safety products – to meet the needs of various industries, including construction, machine building, petrochemical and more. With a rich history of more than 75 years, Fabory has established itself as a trusted provider of quality products, supporting customers with innovative logistics and digital solutions to streamline purchasing processes and optimise inventory management.
The manufacturing industry often faces the brunt of fastener shortages. These shortages can stem from various factors such as supply chain disruptions, increased demand or logistical challenges. It’s vital for manufacturers to identify these triggers early to mitigate their impact on production schedules.
To combat these challenges, Fabory Logic offers innovative solutions –with an approach that includes RFID technology, weight scale cabinets, as well as Pick and Put to Light systems. Each of these solutions are designed to streamline inventory management and ensure a consistent supply of fasteners.
Fabory Logic’s RFID solution provides ‘real time’ inventory tracking, helping manufacturers monitor fastener stock levels efficiently. This technology is crucial in preventing shortages by ensuring timely restocking and reducing the risk of production halts. Another innovative solution is the weight scale cabinets, which use precise weight
measurements to monitor inventory levels, offering an accurate and automated way to keep track of fastener usage and availability.
Finally, the Pick and Put to Light system streamlines the picking process, reducing errors and saving time. This system is particularly effective in fast paced manufacturing environments where speed and accuracy are paramount.
Implementing Fabory Logic’s smart solutions requires a strategic approach. It’s not just about installing new systems, it’s about integrating them into existing processes seamlessly. This begins with assessment and planning and by analysing the current inventory and supply chain processes, as well as identifying the key areas where Fabory Logic solutions can bring the most impact.
The next step involves training and integration to guarantee employees are well trained on the system. It is only through proper integration into the existing workflow that company’s are able to maximise the benefits of Fabory Logic’s solutions. After this, it is a case of continuously monitoring the performance of the solutions and making any adaptions if required. This continuous improvement will help in maintaining efficiency and avoiding future shortages.
The final step in navigating production delays due to fastener shortages is future-proofing manufacturing processes. This involves
adopting a proactive approach to supply chain management and inventory control, such as:
1. Predictive analysis: Use data analytics to predict future trends in fastener demand and supply. This will allow you to make informed decisions and stay ahead of potential shortages.
2. Long-term relationships with suppliers: Build strong relationships with suppliers. A reliable partnership can help ensure a steady supply of fasteners.
3. Leveraging technology for efficiency: Continuously explore and invest in new technologies that can improve inventory management and supply chain efficiency.
By implementing these strategies, and leveraging Fabory Logic’s smart logistics and inventory solutions, manufacturers can significantly reduce the risk of production delays caused by fastener shortages. These approaches not only address current challenges but also prepare businesses for future disruptions.
Operational resilience is key in combating the effects of fastener shortages. This involves building a robust framework that can withstand supply chain disruptions and maintain production consistency. For instance, companies should look to adapt production schedules to account for potential delays in fastener supplies. Flexibility in scheduling can help minimise the impact of shortages. Optimising inventory levels using advanced tools is also a key step as it helps to balance the need for sufficient stock, while avoiding excess that ties up capital. Finally, cross-training staff to handle multiple roles ensures that operations can continue smoothly even when faced with unexpected shortages.
The manufacturing industry is constantly evolving and staying ahead requires businesses to adapt to these changes. Understanding industry trends and aligning strategies accordingly is essential. That is why companies should monitor market trends related to fasteners, including tracking changes in prices, emerging technologies and new suppliers. It is also vital to continuously invest in R&D to find alternative materials or fastening methods that could reduce dependence on traditional fasteners. Finally, businesses need to work on building and developing a resilient supply chain that can quickly adapt to changes, whether it’s switching suppliers or adjusting transport routes.
The key to successfully navigating production delays due to fastener shortages also lies in adopting a holistic approach. This involves a combination of immediate tactical solutions and strategic planning. Manufacturers must not only respond to current challenges but also anticipate future trends and prepare accordingly.
By integrating Fabory Logic’s smart logistics solutions into operations, manufacturers can significantly improve inventory management – reducing the risk of shortages. However, this should be complemented with broader strategies that enhance overall operational resilience and adaptability.
It’s about creating a balance between being reactive to immediate challenges and being proactive in planning for the future. This balance is crucial for maintaining uninterrupted production lines and ensuring the long-term sustainability of manufacturing operations. The key is proactivity and continuous innovation, ensuring that manufacturing processes stay efficient, reliable and ahead of the curve.
PEM® UK has announced the opening of its physical offices in Burnley, signalling a renewed commitment to the UK market. This revitalised space not only serves as a testament to PEM® UK’s dedication but also introduces on-site warehouses featuring a comprehensive stock of fasteners.
In addition to these enhancements, PEM ® UK is thrilled to unveil the expansion of its sales team, reaffirming its motto: ‘We are where you are’. “We are excited to open our doors in the UK, offering more than just a physical presence. Our on-site warehouses, with a diverse inventory, coupled with the expansion of our sales team, underscore our commitment to being a reliable partner for businesses in the region,” explains Mary Ann Fleming, president of PennEngineering® EMEA.
PEM ® UK explains that its warehouse will streamline logistics, providing customers with prompt access to the entire portfolio of PEM®fasteners and PEMEdge services. The expansion of the sales team also ensures that PEM® UK is readily available and accessible to understand and meet the unique needs of its UK customers.
“Through an engineering first mindset, and collaboration with customers, PEM ® helps solve the biggest fastening challenges. We offer design engineered custom solutions; the industry’s most expansive library of standard solutions; advanced engineering and technical services; and a global manufacturing and support presence,” comments Mary Ann Fleming.
As part of the PennEngineering® portfolio, PEM ® UK also offers the full product line of Sherex Fastening Solutions® including rivet nuts, clinch nuts, threaded inserts, Disc-Lock® and TEC Series®wedge-locking products, as well as fastener installation systems – used by many Fortune 500 OEMs to strengthen attachment points while decreasing assembly times and waste.
www.pemnet.com
In the current climate of heightened environmental responsibility, PEM® has also underlined its readiness for the Carbon Border Adjustment Mechanism (CBAM) regulation. Therefore, by choosing PEM® products, customers are not only assured of the highest quality and reliability, but are also contributing to a sustainable and environmentally responsible future.
CBAM is a climate measure designed to address the risk of carbon leakage, ensuring equivalent carbon pricing for imports and domestic (EU) products subjected to carbon costs under the EU ETS.
Mary Ann Fleming, president of PennEngineering® EMEA, states: “At PEM® Europe, we embrace CBAM as an opportunity to further our dedication to sustainable production, fostering innovation and contributing to a cleaner future for generations to come.”
In a market driven by quality and sustainability, the choice to invest in products ‘Made in Europe’ brings advantages often overlooked, as well as preventing any exposure to the CBAM duty.
European fasteners and installation equipment, renowned for craftsmanship and superior standards, offer meticulous attention to detail and a commitment to durability.
Notably, these European products adhere to strict ethical and environmental guidelines, promoting safety and eco-friendly production methods. Supporting European manufacturing not only boosts local economies, and preserves jobs, but also fosters innovation and champions sustainability efforts, aligning with eco-conscious consumer priorities.
“One key advantage lies in the transparency of sourcing and manufacturing processes within Europe, for Europe. This transparency not only enhances consumer confidence but also reduces carbon footprints due to shorter transportation distances. This aspect is particularly significant as it aligns with concerns about climate change and any CBAM duty,” concludes Mary Ann Fleming.
www.pemnet.com
The EN Eurocodes are a series of ten European Standards, EN 1990 – EN 1999, providing a common approach for the design of buildings and other civil engineering works and construction products. They are adopted by several Member States as the National Building Codes and are the recommended reference for technical specifications in European public contracts.
In 2012, the European Commission issued the Mandate M/515 for a detailed work programme for amending existing Eurocodes and extending the scope of structural Eurocodes. The work of the second generation of Eurocodes is almost ready, formal votes will be concluded by early 2026 and the definitive text in the official language versions (English, German and French) will be distributed no later than 30 th March 2026. Member States are due to implement Eurocodes by 30th September 2027 by publication of an identical national standard or by endorsement. The actual Eurocodes, and any related national standards conflicting with the new generation Eurocodes, have to be withdrawn by 30th March 2028. This explains the attention and the involvement of many experts in the drafting of Eurocodes.
The key developments of the new Eurocodes include improving the practical use of Eurocodes for day-to-day calculations; introducing requirements for the assessment, reuse and retrofitting of existing structures; as well as the strengthening of requirements for robustness.
Focusing on the timber sector, Eurocode 5 ‘Design of timber structures’ faced a number of challenges, such as the tremendous development of timber structures in the last 30 years; the development of timber concrete composite structures; the need of harmonisation within the whole Eurocode family; the interface with product standards and European Assessment Documents (EADs); as well as the alternative design methods developed outside of Eurocodes.
In fact, the chapter on connections has seen a variety of new connection types covered by product standards stuck in the pipeline of the standardisation blockage or dealt by EADs. Some product standards
Member States are due to implement Eurocodes by 30th September 2027 by publication of an identical national standard or by endorsement.”
and some EADs, in view of the revision of Eurocodes, dealt with topics such as seismic provisions, durability, sustainability, and related design –somehow anticipating the Eurocodes.
The amended versions of the Eurocodes were then taking on board these aspects, developing them further – as in the case of durability, addressed first in the standard on timber connectors EN 14592:2020 and developed in a more articulated way in Eurocode 5.
Moreover, the Eurocodes also had to reflect several concepts of the new Construction Products Regulation – whose final text is now available – such as installation (execution), sustainability (reuse and retrofitting) and harmonised zone (accessible only via harmonised standards and not anymore via European Technical Assessments).
All these changes generated intensive discussions of both technical and general nature in all Eurocodes. In its enquiry phase, which is the phase where Member States are allowed to comment on the final text, Eurocode 5 alone received in total 7,130 comments, 1,397 of which were on the chapter ‘connections’.
Imagine the stress in the management group who is now seeking for consensus on the most disputed comments. Some of the comments that addressed specific concerns of manufacturers of European timber connectors included:
Manufacturers expressed concerns, and basically opposed, the introduction of screw categories in the Eurocode. The fear is that woodscrews could become a sort of metric product.
At a more technical level, manufacturers expressed concerns on the new formulation for slip modulus of screws, which penalises significantly connections featuring a high-density timber member, and on the value 7.5 given for screws.
In the new Eurocode 5, the use of specific ETA values as an alternative to calculation methods in Eurocodes is allowed only if these are referred to and addressed by the Eurocodes on a case by case basis.
The Eurocode management made it clear that users who apply other information than (a) default values specified in the Eurocode itself for the calculation or (b) the properties and values specified in the relevant, by the Eurocodes referred documents, are exceeding the scope of the design standard. They are, in fact, outside of Eurocodes’ jurisdiction. Hence, responsibility for the applicability of those used values is then
transferred to the user. Manufacturers that did not manage to include alternative ETA values in the Eurocodes are now concerned this may undermine their ETAs and may manifest costs to reissue them.
The introduction of very specific execution rules, which can be seen as forcing users to adopt procedures that are not usual in some member states. One must remember that construction is a very conservative branch, based on local building traditions.
The introduction of seismic provisions for timber fasteners, which were introduced in Eurocode 5 and then transferred to Eurocode 8. Although seismic design is mandatory for certain Member States, it is sometimes seen as a hidden barrier to trade by manufacturers from Member States that are not familiar with the requirements requested by this design (e.g ductility).
Manufacturers of timber fasteners are meeting to discuss and share their analysis and efforts to try to influence some last minutes changes.
It will be important to see how the new design code will be implemented in the related harmonised standards and what will happen with the many ETAs on timber products. This topic is very much depending to the content of the new CPR, which now requires an in-depth analysis and guidance to help manufacturers and users understand what is going to change in the next few years.
www.ecap-sme.org
DIV Group states that its factory in Knin, Croatia, is the largest standard bolts factory in Europe, which can supply products to the demanding European market as well as to Africa, the Middle East and America. “Although there was a certain stagnation in a part of our primary EU market, export growth of 12% continued at the beginning of 2024 due to the expansion of business in other markets – with the business cooperating with partners in over 40 countries around the world,” reports DIV Group. “Through our long-term investments in more environmentally friendly production; adaptations to new EU regulations; expanding production capacities; and opening new markets; we have been able to achieve record exports in the last two years. We have also created prerequisites for new export records in the years to come.”
DIV Group’s product portfolio includes various metric fasteners according to DIN or ISO standards such as DIN 931, DIN 933, DIN 912, DIN 6921, DIN 7990 and inch fasteners according to ASTM and ASME standards. In addition to standard fasteners, a large part of the business is custom-made products and OEM products – with special surface treatment requirements. DIV Group has also implemented and maintains updated quality assurance systems that meet the requirements of international standards such as ISO 9001, ISO 50001, ISO 45001 and ISO 14001.
At DIV Group, great attention is paid to a corporate social responsibility in order to improve the business’ and community’s quality of life. “We strive to be responsible towards the workers, the local community and the environment. We are a proud partner of Resolution Earth, the largest environmental project in Croatia, with the aim of raising awareness of environmental protection and preservation,” explains DIV Group.
Recognising innovation as the basis of competitiveness on the international market, as well as the importance of a systematic approach to the development of innovative products, as well as the improvement of production and business processes, DIV Group has already initiated and implemented numerous projects to help increase energy efficiency, which have been co-financed by the European Structural Funds.
“The project to increase the efficiency of energy used in the production process, and the transition to renewable energy sources in
Croatian manufacturer DIV Group has confirmed that the last two years have been record breaking due to the volume of exported fastener products it has sold – with the company achieving over 40,000 tonnes of exports.
our production facilities, contributed to the achievement of our global goals of sustainable development,” reports DIV Group. “The main activity of the fastener factory is the production of fasteners, where the technology used during the production process generates waste heat, which the cooling system releases into the atmosphere. By switching to a heat pump system, with the aim of utilising waste heat, we can help reduce emissions into the environment, which consequently results in a reduced consumption of electricity.”
Projects to increase energy efficiency in the DIV fastener factory –by building a photovoltaic power station with a capacity of 6,500kW –and in the production plant of Brodosplit Shipyard – by building a photovoltaic power station with a capacity of 8,100 kW – will also help it reduce the need to purchase electricity, with prices having skyrocketed.
“Many companies promise efficiency, but our desire for continuous improvement allows us to identify opportunities and design solutions for even the highest demands of our customers, with the support of local and state administration, strategic geographical position, experience in restructuring, investment in research and development and adaptation to new EU regulations,” concludes DIV Group.
www.divgroup.eu
Fan safety in football stadiums has come a long way in recent decades, yet collapses and accidents still occur. When Bernhard Baumhus was tasked with building a stand for German football club SC Paderborn 07, it was integral to the design to find an optimal bolting solution.
Back in 2019 Paderborn’s home ground – the Benteler Arena –needed to be upgraded and expanded by some 2,000 seats to a 15,000 capacity. Steel construction company Bernhard Baumhus GmbH got the assignment and was only given three weeks over the pre-season to complete a new grandstand. As with all modern football stadiums, safety is paramount with strict regulations ensuring spectators are protected against fire or collapsing stands.
While German football fans’ tendency to jump up and down in unison can create an incredible match day atmosphere, it also adds extra strain to stadium structures. Bernhard Baumhus’ engineers calculated that during a match the new stand would be subjected to around six vibrations per second. If not properly secured, the consequent dynamic load could cause bolts to loosen.
A falling bolt or nut can lead to severe injuries for the spectators. If the load bearing capacity of the structure is affected, the consequences can be even more catastrophic.
Such accidents are unfortunately not uncommon in world football. As recently as January 2020, the roof of a stadium in St Petersburg, Russia, collapsed killing a construction worker. In 2019, a large section of the roof of AZ Alkmaar’s stadium in the Netherlands collapsed due to strong winds, fortunately not injuring anyone as the stadium was empty at the time.
Bolted connections are always critical in steel construction. They can either be bolted or welded, but with changes in production methods and automated processes for drilling holes, bolting has become more widespread. There are also different types of fasteners, however, after exploring the various options available and witnessing a Junker test conducted by Nord-Lock, Bernhard Baumhus elected to use Nord-Lock steel construction (SC) wedge-locking washers as they were the only washers that could be used for all common bolted connection in steel construction.
The proven Nord-Lock principle prevents the bolt from coming loose and the Nord-Lock SC-washer pairs have special chamfers on the inner diameter, on both sides, to ensure an optimal contact surface between the bolt and the washer. Therefore, the washers can’t be installed upside down. The bolt is also secured using a plus tension and not friction.
Bernhard Baumhus was confident that the SC-washers would be able to withstand vibrations and prevent loosening. Another significant advantage was that independent institutions have approved Nord-Lock washers for their use and effectiveness in construction applications. This led to different national technical approvals and European Technical Assessments (ETAs).
Nord-Lock points out that even if SC-washers are used together with HV sets, it is possible to replace the original washers and still comply with the current legal framework. No significant design changes need to be made.
“Designed to fit both HV and HR bolts and nuts, Nord-Lock Steel Construction (SC) washers are approved for use with HV sets and can be used as a direct replacement for standard plain chamfered washers (EN 14399-6),” explains Nord-Lock Group. “The washers are quick to install and remove using standard tools and the locking function is not affected by lubrications – helping to prevent any loosening caused by vibration and dynamic loads.”
Nord-Lock adds: “Today, building and construction companies throughout Europe can rest assured that using Nord-Lock securing washers means they, by default, comply with the European Union’s rigorous safety and quality requirements as Nord-Lock can also offer securing washers with CE Marking.”
www.nord-lock.com
Now with 5% cobalt for stainless steel for even longer tool life. The new ULTIMATECUT Countersink 4S - with four unequally divided cutting edges for unique performance. Available in dimensions from Ø 10.4 to 40.0 mm. Make a decision for a perfect surface. Visit us at ruko.de
As part of its continued commitment and investment to product development and testing, Lindapter has had its Type FL beam flange clamp successfully and independently fire rated for up to 120 minutes.
Following independent fire testing by built environment test organisation, BRE Global Ltd (UKAS 0578), the Type FL beam flange clamp is now a fire rated connection system for securing building services infrastructure to structural, or secondary, beams without drilling or welding.
Such internal service infrastructure includes fire protection, sprinkler, and acoustics systems, HVAC equipment, as well as mechanical, electrical, piping and sanitation systems and fittings. Lindapter explains the beam flange clamp is the only such product to be fire rated and also FM and VdS approved, all resulting from the company’s keen focus on safety and reliability.
BRE tested the products under tension whilst subjecting them to standard fire exposure in accordance with ISO 834 and ASTM E-119, for a duration of two hours. Its test report, P123815-1002 Issue: 1, verifies load limits for 120 minute fire rating. To achieve this rating, product types FL210D/T, FL312D/T and FL412D/FL410T were subjected to load limits of 0.5kN, 0.65kN and 0.7kN, respectively, at 1,049°C for the 120 minute BRE test. This rating now offers contractors, specifiers and construction professionals additional data that can bolster their confidence when using the Type FL beam flange clamp.
Lindapter’s Type FL also satisfies the requirements of performance class A1 (non-combustible), for ‘Reaction to Fire’ characteristics, in accordance with EC directive 96/603/EC.
pgb-Europe has published a comprehensive new catalogue for structural steel construction fasteners, as well as highlighting its new range of L-anchors and complete anchor chairs.
Downloadable from the pgb website, the new catalogue features the company’s complete range of 8.8 grade SB bolts in-line with EN 15048 requirements, as well as detailing pgb’s extensive range of both zinc plated and hot dip galvanised assemblies, sizes M10 to M36, with both partial and full thread.
In addition, as with the company’s HR type products, which meet EN 14399-3 standards, pgb-Europe’s EN 14399-4 type HV preloaded bolts are also now available as a set, with each package containing bolts, nuts, and washers, with additional nuts and washers available separately.
The catalogue also highlights L-anchors and complete anchor chairs, which are new members to pgb’s portfolio.
In railway bridge construction, the decision to change a fastener system can improve the whole reliability of a construction. In 2016 a freight train fell into the Tolten River, in Chile, after the railway bridge collapsed. In 2020, J. LANFRANCO & Cie supplied over 37,000 ESL self-locking nuts for the restoration project.
ESL self-locking nuts were selected due to the harsh environment factors – earthquakes, forest fires, floods, etc – as well as the constant vibration and movements of the Tolten Bridge, which could potentially loosen traditional nuts over time – once again putting the safety of the bridge at risk. ESL self-locking nuts are able to withstand high loads and stresses for structural integrity and vibration damping and can guarantee resistance to variable environmental conditions and dynamic load.
Four types of nuts were used during this restoration project –ESL ⅝ inch nuts, ESL1½ inch nuts, ESL ¾ inch nuts and ESL ⅝ inch nuts, all in CL8 steel.
Another benefit to ESL self-locking nuts is at the bridge installation phase. In bridge construction the decision can be made to weld different parts together to save money and material weight. This leads to a lot of planning and special operations, such as road closures, transportation, etc, to get the bridge in place. The ESL self-locking nuts enabled the bridge to be brought to the site in parts and assembled, speeding up the operation and also allowing the nuts to be reused if necessary.
“Over the past five decades, our company has established itself as a major player in the field of safe fasteners. Our commitment to innovation and quality has enabled us to provide reliable solutions, such as our self-locking nuts, for such important renovation projects,” proudly commented J. LANFRANCO & Cie.
Owlett-Jaton’s product range is vast and includes products from over thirty market leading manufacturers, including Lindapter. Stocking over 200 of its most popular lines, it is recognised as an official supplier of Lindapter products.
Lindapter’s range of high-quality products is designed to provide a solution for a multitude of structural steel applications, including steel-to-steel, structural hollow section, steel flooring, composite decking, building services, as well as lifting and rigging. Lindapter’s products provide many advantages; they can be installed with standard hand tools allowing for faster construction, as well as being a cost-effective alternative to on-site drilling or welding. In turn, this reduces labour costs, whilst helping to preserve steelwork integrity and protective coatings.
Distributors can order Lindapter products from Owlett-Jaton in small quantities, improving efficiency and enhancing customer service levels with their customers. Owlett-Jaton’s service offering includes free next day delivery across the majority of the UK mainland, with no minimum order charges accounting for the majority of business. The company is the UK and Ireland’s leading wholesale supplier of fasteners, fixings, and associated products, to the distributor and merchant trade.
The relationship that Owlett-Jaton enjoys with Lindapter has been in place for many years and the companies work closely to continually deliver the highest level of service to customers, including in-depth technical support and advice.
With a network of Owlett-Jaton sales offices spanning the UK, supported by area sales managers and merchandising teams, customers have access to experienced staff, whilst online ordering provides visibility to pricing, stock availability and more.
www.owlett-jaton.com
THE ORIGINAL: MULTI-MONTI SCREW ANCHORS
Here Nimeka de Silva, head of marketing at BUMAX AB, reflects on the role that stainless steel plays in the construction industry; the impact stainless steel will have on the construction industry in the future; and what solutions BUMAX® can provide in this ever changing industry sector.
Almost every industry sector is now under pressure to continually evaluate their impact on the environment and consider opportunities to develop more sustainable industry practices. The construction industry is no exception to this, especially given the ever increasing need for both public and private infrastructure. In light of these pressures, there is a growing appreciation for the long-term gains from designing infrastructure with longer lifespans, reduced ongoing maintenance and a high proportion of recyclability at the end of life. This is not only from the perspective of sustainability but there is now also a convincing commercial argument. As governmental and societal focus increases, new policies and industry measures continue to be introduced, bringing additional challenges for developers, architects and engineers. This is where stainless steel materials can offer considerable advantages.
Stainless steels are some of the world’s most sustainable engineering materials, given their resilience to environmental conditions, durability, low maintenance and high-levels of recyclability. There are over two hundred recognised grades of stainless steel, all with different properties and varying capabilities. For construction applications, austenitic and duplex stainless grades offer the biggest potential, given their combination of strength, ductility, corrosion resistance and manufacturability. Properly considered, they can not only help designers maximise the reliability and lifespan of assets but also reduce the ongoing (and often costly) maintenance required.
Stainless steel materials have been widely used in industrial structures for some time, however barriers to more widespread adoption of stainless steel in general construction have typically been due to a lack of knowledge, design guidance and standards, component manufacturing and fabrication experience – when compared with carbon steel. There is also a higher upfront investment needed with stainless steel. The total lifecycle cost profile is certainly different to that of carbon steel, where the higher cost efficiencies of stainless steel are realised during the life of the asset, rather than in the initial construction. However, perceptions, experience and economics are
starting to change, making a far stronger case for the increased use of stainless steel within the built environment.
BUMAX ® has built up considerable experience in stainless steel structural bolting over a number of years. As a Swedish manufacturer, specialising in high strength stainless steel bolts, our expertise in this area has led to involvement on many technically challenging construction projects, ranging from bridge construction, tunnelling, building façades, to structural applications in the nuclear industry.
BUMAX® offers a standard stock range of high strength fasteners in different stainless materials. In addition to this, a sizeable proportion of BUMAX® ’s business is project related. The company’s technical and global sales engineering teams are able to offer application support for designers and specifiers, to develop bespoke manufactured solutions.
The company’s stainless steel structural bolting falls into two categories. Firstly, non-preloaded bolting intended for bearing connections acting in tension and/or shear. The second is for more specialist pre-loaded bolt assemblies, intended for slip-critical connections.
BUMAX® non-preloaded structural bolts are based on the BUMAX® 88 product grade, tested, certified and supplied CE marked in accordance with EN 15048. BUMAX® 88 is a premium A4/316L stainless material benefiting from higher molybdenum content. It not only offers the advantage of being mechanically equivalent in strength to 8.8 carbon steel bolts (stronger than A4-80 bolts) but with the additional benefit of higher corrosion resistance than common grades of A4/316 material. BUMAX® 88 can be suitable for use in a wide range of environments, with a non-preloaded structural bolt range that includes hex head bolts, set screws and socket head cap screw assemblies in diameters from M12 – M36 for steel construction applications and from M5 upwards for aluminium construction.
Pre-loaded structural bolting in stainless steel is more involved, as there are currently no standards that govern the use of stainless steel bolts in such applications. However, there is progress being made in this area to develop guidance (and eventually standards) on the use of stainless steel in pre-loaded bolting applications. Within Europe, allowance is currently given in Eurocode 3: ‘Design of Steel
Structures – Supplementary Rules for Stainless Steel’, which states that acceptability of high strength stainless steel bolts for slip-resistant connections should be demonstrated through project specific testing.
In the US, guidance is now provided on the use of austenitic and duplex stainless bolts by the American Institute of Steel Construction (ANSI/AISC) – 370 ‘Specification for Structural Stainless Steel Buildings’. Precipitation hardened martensitic grades of stainless steel have also referenced and have historically been used in the US due to their high strength, however they do not benefit from the same levels of corrosion resistance, ductility or impact strength as austenitic or duplex stainless grades and they are not covered for use in slip critical connections.
BUMAX® is able to offer pre-loaded structural bolting solutions for slip critical connections in both austenitic stainless grades (BUMAX® 88 and 109) and higher performance duplex and super duplex stainless grades (BUMAX® DX or SDX). This provides engineers with three levels of corrosion resistance depending on the environmental conditions, catering for structures located in-land that are exposed to the elements, right through to the harshest offshore conditions. There is also a choice of two strength classes – 88 and 109, equivalent in strength to 8.8 and 10.9. This gives engineers added design flexibility, depending on the structural requirements of the application.
BUMAX®’s product range includes hex head bolts and fully threaded set screws, in diameters ranging from M10 – M24. Technical support by BUMAX ® is provided to specifiers at the early stages of project design to determine appropriate selection, before conducting project specific testing to confirm suitability, as well as the correct design and installation parameters.
To help architects and structural engineers achieve more sustainable designs, BUMAX ® has gone through the process of obtaining an Environmental Product Declaration (EPD) on BUMAX® 88 and 109. An EPD is based on a Life Cycle Assessment (LCA) of the product,
providing specifiers with valuable data on the environmental impact of a product being used within the construction design. On top of the general sustainability benefits of stainless steel materials, BUMAX® has the added advantage of utilising the majority of its raw material from close proximity to its factory in central Sweden and employing manufacturing practices that are continually assessed to keep environmental impact as low as possible.
It is likely that stainless steel will play a more pivotal role within construction engineering in the coming years. Stainless steel materials provide an array of benefits from high corrosion resistance, increased durability, minimal maintenance and very high-levels of recyclability at its end of life, which makes a strong case for being able to support the challenge of improving sustainability in the built environment. With strong experience to date, and an exceptional range of high performance products and manufacturing capability, BUMAX® is committed to doing its part in the continued development of engineering capabilities and sustainability within the construction industry.
Samac Fixings has announced the expansion of its acclaimed Performance range with the introduction of new screw lengths, specifically designed to comply with the updated UK building regulations for roof insulation.
Part ‘L’ of the UK building regulations now mandates a minimum roof insulation level of 0.18 W/mK for all new build homes and extensions. This significant update necessitated the use of thicker insulation materials to meet the new standard, thereby creating a need for longer screws in the construction process.
Understanding this industry shift, Samac Fixings has responded proactively by adding 6mm x 220mm and 6mm x 240mm screw lengths to its performance range. These new sizes are meticulously engineered to travel through the increased thickness of the latest insulation materials, ensuring compliance with the updated regulations while maintaining Samac’s hallmark of quality and reliability.
The longer screws are not just a regulatory response; they are a crucial component in maintaining the structural integrity of roof insulation. Shorter screws may fail to reach the framing behind thick insulation, potentially leading to reduced stability and sagging over time. The Performance range’s extended screws provide a more secure grip and penetrate the full depth of the insulation, offering proper support and preventing damage. Moreover, these longer screws distribute pressure more evenly across the insulation layer. This feature is critical for maintaining the stability of the insulation over time, ensuring that buildings remain energy efficient and compliant with the latest standards.
UK fastener and fixing supplier for the construction industry, Aptus, has become a signatory of the Anti-Copying in Design (ACID) IP Charter, to make a stand to protect original and innovative product design in the face of illicit copying.
Aptus Fastener Systems Ltd has helped pioneer a number of advanced products over its 30 year history including its timberfix ® 360 and pro-struct ® screws that employ proprietary design features and deliver major benefits in areas such as speed, ease of use, durability and fixing performance. However, the company’s success also means it is occasionally copied, making it important that users have the reassurance of knowing they are benefiting from the ‘real deal’ and not an inferior imitation.
Stewart Taylor, managing director at Aptus, explains: “Signing up to the ACID IP Charter reflects that commitment to authenticity and demonstrates our support of the need to protect intellectual property and prevent design theft. We are aware of instances where screws have been marketed and sold as being part of the timberfix ® 360 range, when they’re not.”
He adds: “Whilst imitation might be the sincerest form of flattery, we are concerned about the possibility of users being misled. By becoming a signatory of the ACID IP Charter, we hope to combat that.”
For almost 25 years, ACID has been a positive force for change, working to raise awareness and to encourage respect for intellectual property amongst both individuals and organisations. The ACID IP Charter is a code of conduct and a statement of intent. Its signatories agree to uphold the values of ACID, to advocate product design originality, and to avoid practices, such as copying and IP infringement.
CELO has received a European Technical Assessment (ETA – 22/0613) for its FORCE ONE direct impact nailing system, ensuring the safety, reliability and quality of the company’s direct impact fixing products, as well as offering reassurance to customers worldwide.
The ETA certification highlights the high standard of performance and safety embedded within the FORCE ONE gas nailing system, as well as confirming the technical applicability, suitability and compliance of the system for various applications. The nailing system, which includes nailing accessories, XHA nails, as well as the FORCE ONE gas nailer, enables construction professionals to streamline their workflow and save time and money compared to traditional installation methods.
For their part, the XHA nails have been thoroughly tested and approved to ensure consistent and reliable performance across diverse projects, and are designed to seamlessly integrate with the FORCE ONE gas nailer, as well as offer exceptional strength, durability and precision.
The nailer has been designed for a variety of applications such as electrical installations, including cables, pipes, and tubes, as well as different base materials ranging from hard materials like concrete, to soft materials like wood.
In addition to the ETA, the company’s wide range of nailing accessories, made of A1 steel, hold a fire approval rating, further emphasising their safety and reliability.
Following an agreement with the European Organisation of Technical Assessments, here is a list of recent ETAs published in the last two months on the EOTA website.
It is important to note that existing ETAs may be amended or withdrawn so this list should not be considered definitive. For further information and a full list of valid ETAs visit EOTA’s website. If you have recently received an ETA, and would like to have it included in our table, please email us the full details at editor@verulammedia.com www.eota.eu
ETA NUMBER TRADE NAME COMPANY
Bonded anchors for use in autoclaved aerated concrete slabs
Bonded fasteners for use in concrete
ETA - 23/0914 Mungo MIT-V+
MUNGO Befestigungstechnik AG
ETA - 23/0917 Mungo MIT-VE+ MUNGO Befestigungstechnik AG
ETA - 23/0921 Chemical Stud +
PROMANTE S.A.
ETA - 23/0922 ANCLATEC EPOXI bonded anchor BASTHER HISPANIA, S.L
ETA - 23/1005 2K Anker Fix 2K Anker Fix Winter 2K Anker Fix Sommer WS INSEBO GmbH
ETA - 23/1023 Bremick PURE EPOXY 500 SEISMIC C2 585ml CART Bremick PTY Ltd Australia
Bremick PTY Ltd Australia
ETA - 24/0025 Bremick vinylester resin styrene free bonded anchor
ETA - 24/0063 2KPS EX100-31 Series 2K Polymer Systems Ltd
ETA - 24/0073 PROFAST Injection system V-PRO 70 for concrete
ETA - 24/0078 MERCOLA ANCHOR ADHESIVE PS1
ETA - 24/0080 MERCOLA ANCHOR EXTRA SEISMIC C1 C2
ETA - 24/0081 MERCOLA ANCHOR ADHESIVE PS2
PROFAST Ankersystemen B.V
EVOCHEM S.A
EVOCHEM S.A
EVOCHEM S.A
ETA - 24/0075 PROFAST Injection system V-PRO 70 for (hollow) masonry PROFAST Ankersystemen B.V
ETA - 24/0082 MERCOLA ANCHOR ADHESIVE PS2 EVOCHEM S.A
Mechanical fasteners for use in concrete
ETA - 23/0981 Hoogo Torque-controlled expansion anchor Suzhou Hoogo Construction Auxiliary Co., Ltd
ETA - 24/0005 BAZ2, BAZ2 SC, BAZ2 ZN, BAZ2 SH, BAZ2 A4 CELO Befestigungssysteme GmbH
ETA - 24/0042 Screw Anchor Mark 2 ALLFASTENERS PTY LTD
ETA - 24/0051 ARVEX SS concrete screw ARVEX GROBELNY Sp. Z.o.o
ETA - 24/0091 WA-Z, WA-AT, WA-A2, WA-A4 Bizline SAS
Metal injection anchors for use in masonry
ETA - 23/0915 Mungo MIT-V+ MUNGO Befestigungstechnik AG
ETA - 23/0918 Mungo MIT-VE+ MUNGO Befestigungstechnik AG
ETA - 24/0026 Bremick vinylester resin styrene free bonded anchor for masonry Bremick PTY Ltd Australia
Hex Bolts / Screws 8.8 / 10.9 / 12.9 m30-m42
DIN 933 / 931
ISO 4017 / 4014
Dowel Pin m6-HRC 58-62 DIA 3mm to 30mm
DIN 6325
DIN 7979D / ISO 8735
ISO 8734 / 2338
DIN 7
Socket Products m4-m30 ( 8.8/ 10.9 / 12.9 )
DIN 912 / ISO 4762 / ISO 14579
DIN 7991 / ISO 16642 / ISO 14581
DIN 7984 / DIN 6912
ISO 7380-1 / 7380-2
ISO 7379 / F9 H8
Plug’s 5.8
DIN 906
DIN 908
DIN 910
Dog Points Type A/B
DIN 561
DIN 564
DIN 479
Fit Bolt 8.8 / 10.9 m8-m30
DIN 609 / 610
Here Abhijat Sanghvi, president of the Fastener Association of India (FAI), discusses the latest developments within the Indian economy and fastener market; the opportunities and challenges companies face; as well as how the FAI looks to support its members.
How is the Indian economy currently performing and how has it performed over the last 2 or 3 years? What are the prospects for the future?
“The Indian economy is estimated to grow at 7.3% for the financial year 2024-25. This would be the third year in the row when the GDP would be more than 7%. Many global agencies have also revised India’s growth projection upwards. Three successive years of high growth shows the resilience of the Indian economy and the bedrock of high growth is strong private consumption. Investment is consolidating in the economy as high public CapEx crowds in private investment, which is beginning to set-up additional plants and acquire new machinery to address rising capacity utilisation. In the last few years, India’s GDP grew even as there was an impact of several major reforms, such as bankruptcy law, GST implementation, Real Estate Regulation Act (RERA) and demonetisation, which paid off in the long run.
From the 9th largest economy a decade back, India has now become the 5 th largest economy with a nominal GDP of US$3.4 trillion. India’s GDP is likely to touch US$5 trillion over the next four years and will overtake Japan and Germany to become the third largest economy by 2027. Potentially, India stands to be nearly a US$10 trillion market by 2030.”
How are Indian fastener manufacturers performing? What developments have happened within the Indian fastener market?
“Fasteners are a product range that is consumed across a wide spectrum of industries. Hence, the performance of fastener manufacturers directly correlates with demand from industries such as automotive, construction, aerospace, electronics, general engineering and many others. Economic factors, such as GDP growth, infrastructure projects, and consumer spending, directly affect demand for fasteners. With the positive global outlook for India and it’s growth story, there is continuous upward growth expected in fastener consumption domestically. Globally, with growing resistance in the west to Chinese fasteners, and the unpredictability around the geopolitical situation relating to Taiwan and China, India stands to gain with many more international buyers seriously considering or having already commenced sourcing from India. This means the business environment around the Indian fastener industry is extremely bullish on both the domestic and international front.”
What opportunities and challenges do you believe lie ahead for the remainder of 2024/25 for Indian fastener manufacturers?
“Mandatory certification of all Indian fastener manufacturers by the Bureau of Indian Standards (BIS) has been welcomed by the industry. However, the process is cumbersome, expensive and time-consuming. FAI has explained the limitations of the industry to comply with these
norms to the government, as we are hopeful the process will be simplified, whilst at the same time not diluting the quality norms.
Minimum Import Price (MIP) for most fasteners has also been set, which offsets any dumping of fasteners and is a good protective measure for the industry to have a level playing field in the domestic markets. Opportunities for exports will also be growing continuously, having already mentioned the possibility of India becoming a focus country given the tensions between China and Taiwan.
A big challenge for a lot of Indian fastener manufacturers is in upgrading technologies and capacities regularly – so that they are in sync with the global demand – although many Indian companies have undoubtedly already risen to the task. “
What are the advantages to the business of becoming part of FAI? How does the FAI work with members?
“The FAI is the only pan India industry association that has succeeded progressively in bringing cohesiveness to the Indian fastener industry. We are making bigger strides each year with more members embracing the vision that FAI has for the industry. Conducting industry seminars and networking meetings; tying up with government agencies for Indian pavilions at international trade shows; publication and circulation of India’s only fastener magazine ‘Fastener India’; promoting platforms for business opportunities; dispute redressal among member companies; participation in all major fastener trade shows – both domestic and international; representation of the industry with government ministries and agencies for critical issues – a current case in point being Bureau of Indian Standards (BIS) certification for all manufacturers as a mandatory norm for which industry concerns are addressed, etc. We encourage all fastener companies from India to be a part of the association where the advantages of being a part of the Indian fastener community under FAI are invaluable.”
www.fastenindia.in
In 1979 Mr Romesh Vig embarked on a mission to redefine fastening solutions, establishing MPS Fasteners with a vision for precision and reliability. Since then, the company has evolved and expanded its product portfolio, as well as influence within different markets, to become a leading fastener manufacturer.
Today, MPS Fasteners boasts a staggering range of high-tensile fasteners, numbering 5,000 variants. These fasteners cover a diameter spectrum from 4mm to 48mm, with lengths reaching up to 400mm. The wide variety of grades available, including 8.8, 10, 10.9, 12.9, and 14.9, positions MPS Fasteners as the ‘go to’ source for high performance fastening solutions.
“This expansive range is unparalleled in India, showcasing our dedication to meeting the diverse needs of our clientele,” states Mr Vig, founder and owner of MPS Fasteners.
From automotive to construction, the company’s capabilities in manufacturing fasteners are unrivalled – with a comprehensive range that includes bolts, nuts, screws, hexagon socket heads, countersunk screws, flange button head cap screws, dowel pins, hex head flange bolts, shoulder bolts, socket plugs, hex plugs, engine mounting studs, straight adaptors and many others.
Furthermore, under Mr Vig’s guidance, MPS Fasteners has played a pivotal role in advancing cold forging technology for fastener manufacturing. “By harnessing the power of cold forging we have been able to produce fasteners with superior strength, durability and dimensional accuracy,” highlights Mr Vig. “This technological leap has not only optimised production processes but has also contributed to reducing material waste and environmental impact.”
Through Mr Vig’s vision and continuous research and development efforts, MPS Fasteners also remains at the forefront of innovation, striving to redefine the boundaries of what is possible in the fastener industry. “As a pioneer in both socket screw technology and cold forging, we continue to shape the future of fastening solutions –setting new standards of excellence along the way,” mentions Mr Vig.
MPS Fasteners is proud of its role in pioneering groundbreaking innovations within the fastener industry. “Among our many achievements stands the remarkable contribution of being the first engineering firm in India to develop socket screws (DIN 912). This milestone not only showcased our commitment to technological advancement but also solidified our position as a trailblazer in the field,” points out Mr Vig. “The introduction of socket screws also brought about a significant paradigm shift, offering enhanced performance and reliability compared to traditional fastening methods. This innovation not only met the evolving demands of various industries but also set a new standard for precision engineering in India.”
A core strength of MPS Fasteners also lies in its precision engineering capabilities. By utilising advanced machining techniques, the company can achieve unparalleled accuracy in the production of its fasteners. This precision is crucial, ensuring the reliability and integrity of the products, especially in critical applications where performance is non-negotiable.
To uphold its reputation for excellence and quality, MPS Fasteners also employs rigorous quality control measures at every stage of the manufacturing process. From the initial inspection of materials to the final product testing, the company adheres to international quality standards – ensuring that each fastener not only meets but often exceeds customer expectations.
In order to stay at the forefront of technological advancements, MPS Fasteners has also looked to embrace Industry 4.0, with the introduction of innovative ‘smart’ fasteners. “The quality of any fastening solution is inherently linked to the manufacturing process. That is why we take pride in our state of the art manufacturing facilities, equipped with cutting-edge technology,” explains Mr Vig. “This, coupled with a team of skilled professionals dedicated to precision engineering, ensures the delivery of products that meet the highest standards.”
MPS Fasteners has been relentless in its pursuit of excellence in the manufacturing of bolts, fasteners and nuts. With a firm commitment to quality and innovation, the company has expanded its operations and introduced groundbreaking advancements in bolt technology.
“Innovation lies at the core of our approach to bolt manufacturing and we have continually researched and developed new material, as well as designs, to enhance the
performance and reliability of the products,” states Mr Vig. “From high-tensile bolts for heavy-duty applications to corrosion resistant fasteners for harsh environments, MPS Fasteners offers a comprehensive range of solutions to meet diverse customer needs.”
Furthermore, MPS Fasteners has expanded its product portfolio to included specialised bolts and fasteners for emerging industries, such as renewable energy and electric vehicles. This forwarding thinking approach has positioned the company as a trusted partner for customers seeking innovative solutions in rapidly evolving markets.
MPS Fasteners plays a vital role in the automotive and construction sectors, providing high performance solutions that enhance reliability and safety in critical applications. “In the automotive industry, where structural integrity and safety are paramount, our products have consistently outperformed competitors, contributing significantly to the reliability and safety of vehicles,” underlines Mr Vig. “In the construction industry, where reliability is also key, we have become synonymous with providing durable and dependable fastening solutions. Our products have played a pivotal role in numerous construction projects, ensuring the structural integrity of infrastructure.”
In an era where sustainability is paramount, MPS Fasteners has also looked to prioritise the use of recyclable materials in its fasteners. This not only aligns with environmental goals but also reflects a commitment to responsible sourcing and manufacturing. The company’s manufacturing facilities are also designed with sustainability in mind, incorporating technologies that help minimise energy consumption. “This commitment to reducing environmental impact underscores our dedication to a greener and more sustainable future,” points
out Mr Vig. “Our commitment to green energy is evident in MPS Fasteners’ 500KW roof top solar panels, offsetting nearly 100,000lbs of CO2 – helping contribute to a greener and more responsible future.”
MPS Fasteners success is based on Mr Vig’s life journey, and work experience, from automotive components to global leadership in high-tensile fasteners – all whilst exemplifying resilience, innovation and exemplary leadership in the fastener industry.
In fact, Mr Vig’s exceptional leadership and contributions to the industry have garnered widespread recognition, as evidenced by a plethora of prestigious awards bestowed upon him. Notably, his achievements extend to securing the coveted 1 st position in the MSME category at the CII National Competitiveness Summit. Recognitions such as the Bharat Vikas Awards and Rashtriya Ekta Awards also celebrate his multifaceted contributions to society. Mr Vig has also been honoured with a prestigious lifetime achievement award by Shri Nitin Gadkari, with Mr Vig becoming known as the ‘Fastener Man of India’. Such accolades not only underscore Mr Vig’s outstanding professional accomplishments but also serve as a testament to his unwavering dedication to excellence and innovation in the corporate realm.
Under Mr Vig’s guidance, MPS Fasteners has also received numerous accolades, solidifying its position as an industry leader that is committed to excellence and innovation and validates MPS Fasteners’ prowess and significant contributions to the fastening industry.
“MPS Fasteners’ legacy is characterised by precision, innovation and a commitment to societal and environmental responsibility,” concludes Mr Vig. “From pioneering precision engineering to championing sustainability and social causes, MPS Fasteners continues to lead the way in the fastener industry, leaving an indelible mark on the global stage.”
www.mpsfasteners.com
Mohindra Fasteners is a world-class manufacturer of socket products, and specials, and has a vision of becoming a preferred partner for fasteners, fastening systems and machining components globally.
Mohindra Fasteners Ltd (MFL) commenced its commercial production in 1997 and is now able to manufacture a wide range of fasteners from its three manufacturing locations based in Rohtak, Haryana, in the National Capital region of Delhi. All three locations are company owned and are spread over 10 acres of land – approximately 40,000m 2
MFL’s wide product portfolio includes industrial fasteners such as bolts, studs, screws and special fasteners as per customer’s requirement, which are produced by cold forging up to size M27 (equivalent to 1 inch in diameter). The company can also offer products in various metallurgical grades, dimensions, as well as different kinds of surface finish – conforming to EHV/ROHS norms. Additionally, with the help of its in-house hot forging presses, MFL can cater to bigger and odd size requirements (up to M60 or 2.5 inches in diameter) for customers in various industries.
MFL also has a range of in-house secondary operations machines that includes CNC based machining, horizontal and vertical milling, as well as grinding and drilling machines, that give it an edge in controlling product quality. To add to this vast capability, the company also has in-house operations such as a tool room, wire treatment, an automatic zinc plating line, a semi-automatic product phosphate line, and PLC and SCADA controlled continuous heat treatment lines – which ensure consistent quality in different material and property grades.
Thanks to its vast production capabilities MFL is able to manufacture a wide range of standard parts, including hexagon socket countersunk head cap screws (CSK) and hexagon socket button head screws (button) in metric and inch sizes, button head with flange, hexalobular socket button head, as well as hexalobular socket button flange. Other products include hexagon socket head shoulder screws, hexagon socket low head cap screws, socket head cap screws (long lengths), internal drive pipe plugs, as well as conical thread plugs with conical and cylindrical threads in different head shapes/headless, plus parallel pins of hardened steel (dowel pins) and parallel pins with internal thread of hardened steel (pull out pins).
Under the specials category, MFL can offer parts that are forged and machined, any secondary operations, as well as parts totally machined from the raw material stage, from the diameter range M6 (¼ inch) to M60 (2½ inch) in carbon steel, alloy steel, stainless steel, spring steel and brass for various applications.
To go alongside its vast product and machining capabilities, MFL has also achieved various international standards, including ISO 9001:2015, IATF 16949:2016, ISO 14001:2015, and ISO 45001:2018. Additionally, the company is also CQI 9 certified, with its heat treatment operations externally audited and certified as per guidelines laid out by the North America based Automotive Industry Action Group (AIAG).
MFL’s in-house laboratory is also certified by the National Accreditation Board for Testing and Calibration Laboratories (NABL) in accordance with ISO/IEC 17025:2017 (equivalent to A2LA).
“We have satisfied customers in 25 countries around the world – with two-thirds of our production going to the European and North American markets for more than two decades,” explains MFL. “We have been an approved supplier
for the German railways (Deutsche Bahn) for more than five years and we have been consistently supplying German and other rail companies through vendor partners since the confirmation of the approval.”
The company is also looking to supply similar or extended products to the Indian rail sector based on its experience with German rail products. “The government of India’s initiative of ‘Make in India’ has provided us with newer opportunities in the Indian and overseas markets. Our country’s reliability, based on a stable and a democratically elected government, has given us many opportunities in the overseas markets owing to changing geopolitical equations,” underlines MFL. “This will benefit our strategy of growing further along with our partners, with our CAGR consistently over 6% during the last five years.”
MFL also supplies to the Indian automotive market, including various two-wheeler/passenger car and heavy truck segments –spanning both direct OEMs, as well as tier 1 and 2 suppliers. “We are a reliable and a serious manufacturer of standards and special fasteners and can support customers around the world,” concludes MFL. “We are also a socially responsible company that is currently working towards reducing carbon emissions as the perameters being laid out under the Carbon Border Adjustment Mechanism regulation, better known as CBAM. We are confident we can meet the needs and requirements of customers and we are looking to become long-term partners in progress.” www.mohindra.asia
Gala Precision Engineering states it was born with the intent and need to create a world-class manufacturing facility in India that resembles the quality and standards of global excellence. With perseverance and a commitment to excellence, the company began to carve its niche in the precision engineering sector.
Located in Mumbai, India, Gala Precision Engineering Ltd stands as a testament to India’s ongoing narrative of technical brilliance. Far more than just a manufacturing firm, Gala Precision is a leader in the field of precision engineering. The company’s product line is diverse and sophisticated, including high-tensile fasteners, technically advanced disc springs, and Gallock wedge lock washers. Each product is crafted with an understanding of the challenges faced in modern industries, particularly those focusing on renewable energy, industrial machinery and mobility solutions.
At the core of Gala Precision’s philosophy is a persistent pursuit of quality, guided by stringent international standards. The company’s commitment to excellence is demonstrated in its adherence to multiple global standards including the German DIN standards, known for their rigor and precision. This dedication extends to its quality certifications, including ISO 9001 and IATF 16949, as well as APQP certification for supplying to wind turbine manufacturers –underscoring a global benchmark in manufacturing and quality control. Such standards are not mere accolades but reflect Gala Precision’s unwavering dedication to delivering products that meet the highest levels of reliability and performance.
Gala Precision’s influence also extends far beyond the shores of India. As Asia’s leading exporter of disc springs, and one of the fastest growing fastener manufacturers, the company’s presence is felt across the globe – with more than 175 global active customers in more than 25 countries. This international footprint is a testament to Gala Precision’s ability to understand and meet the diverse needs of a
...with perseverance and a commitment to excellence, Gala Precision began to carve its niche in the precision engineering sector.”
The company’s product line is diverse and sophisticated, including high-tensile fasteners, technically advanced disc springs, and the innovative Gallock wedge lock washers.”
washers have risen to prominence, with the company reporting they have become the ‘go to’ option for global fastener distributors, as well as Original Equipment Manufacturers (OEMs). Adding to these significant achievements, Gala Precision’s high-tensile fasteners are now a
for the wind energy sector is a testament to its commitment to both technological innovation and environmental stewardship.
Similarly, the hydro energy industry relies heavily on precision engineering for efficient and safe operations – making Gala Precision’s springs and fasteners indispensable in hydroelectric plants. They facilitate precise turbine control, effective vibration dampening and ensure robust structural integrity. These products are meticulously designed to meet the unique demands of hydroelectric systems, ensuring uninterrupted energy generation. As the hydro energy sector continues to grow, the demand for such specialised, high-quality components is anticipated to rise – highlighting Gala Precision’s crucial role in supporting this essential renewable energy sector. The company’s focus on delivering high performance, durable solutions positions it as a key player in fostering the development of sustainable energy sources.
Other markets Gala Precision is involved in include the electrical equipment industry – where growth is propelled not just by market expansion but also by the sophistication of engineering applications. Within the electrical and automation sector, springs and fasteners fulfil critical functions that ensure seamless and reliable operations, driving optimal performance and safety. From securing electrical connections to supporting vital components, these specialised elements are indispensable to the success of these industries. As the market is projected to grow significantly, the demand for such high-precision and durable components is set to rise, positioning Gala Precision’s products as key enablers of industry advancement.
The company’s springs and fasteners assume a pivotal role in the electrical and automation industry by guaranteeing secure electrical connections, facilitating mounting and assembly, as well as providing protection against environmental factors. Additionally, they dampen vibrations, making them instrumental
in the efficient and dependable operation of electrical and automation systems. By using top quality materials, adherence to rigorous standards, and a commitment to continuous innovation, these components fuel the progress of the electrical and automation field, enabling groundbreaking technological advancements that shape the modern world.
Gala Precision’s journey is marked by remarkable milestones and a vision for future growth. The company’s foray into supplying compression springs for European metro rails, and entering the automotive transmission segment in India, highlight its diverse capabilities and adaptive strategies. Looking ahead, Gala Precision is focused on continuous innovation, expanding its global presence and maintaining its leadership in the precision engineering sector.
www.galagroup.com
Looking ahead, Gala Precision is focused on continuous innovation, expanding its global presence, as well as maintaining its leadership in the precision engineering sector.”
Gala Precision is embarking on an exciting new chapter with the establishment of a state of the art facility in Chennai – India’s hub for wind energy manufacturing. This strategic move is set to broaden the company’s product offerings – positioning it as a comprehensive solutions provider in the renewable energy sector.
The Chennai plant will specialise in producing high-tensile bolts and other essential fasteners, streamlining Gala Precision’s ambition to be a ‘one stop solution’ for its clients. This expansion not only strengthens Gala Precision’s footprint across India but also complements its existing manufacturing sites.
Strategically located, the new facility positions Gala Precision in close proximity to key customers in the region, including leading wind turbine producers such as Vestas, Nordex, and Enercon, all of which are scaling up their operations in the southern part of India. The Chennai plant is a significant leap forward for the company, enabling the introduction of an innovative line of hexagonal high-tensile bolts, specifically designed for wind towers and nacelles. Additionally, the plant will house advanced inspection and coating facilities, including automated spray-based zinc flake coatings, a crucial technology in the wind energy industry.
This expansion aligns seamlessly with the Indian government’s ambitious goals for alternative energy production. Aiming for a staggering 450GW of renewable energy by 2030, with wind energy poised to play a major role, India’s potential in this sector is estimated at around 302GW. The government’s initiatives to tap into this potential resonate with Gala Precision’s objectives.
Gala Precision’s journey towards becoming a key player in renewable energy extends beyond wind turbines. The company’s expertise in precision engineering caters to a diverse range of industries, including industrial, railway and automotive sectors. With a commitment to quality and innovation, the company continues to provide essential fasteners and springs to OEMs and distributors worldwide, underlining its versatility and global reach in the realm of precision engineering.
Gala Precision Engineering Ltd stands as a paragon of Indian engineering, blending traditional wisdom with modern innovation. The company’s journey from Mumbai to a global leader in precision engineering solutions is a testament to its commitment to quality, sustainability and innovation. The company embodies a vision for a sustainable future, powered by engineering excellence. As it continues to innovate and expand, Gala Precision carries forward India’s rich legacy of engineering, contributing significantly to various industries worldwide and paving the way for a brighter, greener future.
With a focus on quality, reliability, and customer satisfaction, KOVA Fasteners has carved a niche for itself as an Indian fastener manufacturer –achieving significant milestones and garnering recognition for its achievements.
Located in Ludhiana, Punjab, and operating from a 70,000 square foot (6,500m 2) facility, KOVA offers a wide range of products, including hex head bolts, socket head cap screws, agricultural fasteners, structural bolting, hardened washers, load indicator washers, wedge anchors, nuts and washers –supported by fast delivery and a global presence.
The company is able to provide this vast portfolio as its production facility includes an in-house cold forming section and thread rolling machines, as well as processes including heat treatment, coatings, plating, final inspection, as well as packing and logistics. “As a business we have always invested in buying the best technology to make high-quality fasteners,” states Rishi Gupta, managing director at KOVA Fasteners Pvt Ltd. “Thanks to this policy we have state of the art boltmakers and nut formers within our machinery portfolio, which have been imported from the best brands around the world. The same goes for heat treatment lines and also plating lines.”
KOVA has also recently bought land for a new facility, which it says will be 10 times bigger than the current facility. “The new plant will be a second unit and will help us service customer requirements faster and at more competitive prices,” points out Rishi. “We are already planning to start construction of ‘Plant 2’ and by early 2025 it will be fully operational.”
In addition to the new plant, KOVA will also continue to invest in more high-speed lines to improve product quality and also cost efficiency. “Quality is a very important factor in fasteners and being an industry leader means we always have to maintain all the checks and balances
India can take the lead as Asia’s ‘go to’ destination for fastener manufacturing capabilities.”
DIN 7337
GROOVED RIVET
ISO 4034
HEXAGON NUT
ISO 4014
DIN 8140
WIRE THREADED INSERT
DIN 927
SLOTTED SHOULDER SCREW
DIN 7603
SEALING RINGS
ISO 1580
SLOTTED PAN HEAD SCREWS
DIN 2093
DISC SPRINGS
ISO 15481
SELF DRILLING SCREW
DIN 7500
THREAD ROLLING SCREWS
ISO 1051A RIVET FLAT ROUND HEAD
ISO 14589
MULTIGRIP RIVET
DIN 917
HEXAGON CAP NUTS, LOW TYPE
ISO 4034
HEXAGON NUTSPRODUCT GRADE C
DIN 525
STUD BOLTS METRIC THREAD
ISO 15048
STRUCTURAL ASSEMBLY SET
DIN 546
SLOTTED ROUND NUT
ISO 4766
SLOTTED SET SCREWS WITH FLAT POINT
HEXAGON HEAD BOLTS WITH SHANK SEARCH BY DIN & ISO
DIN 1444
CLEVIS PINS WITH HEAD
ISO 14579
HEXALOBULAR SOCKET HEAD CAP SCREWS
DIN 438
ISO 4033
HEXAGON NUTSSTYLE 2
DIN 94
SPLIT PINS
SLOTTED SET SCREWS WITH CUP POINT
ISO 4036
HEXAGON THIN NUTS (UNCHAMFERED)
ISO 4017
HEXAGON HEAD SCREWS WITH FULL THREAD
DIN 6325
PARALLEL PINS, HARDENED
ISO 14583
HEXALOBULAR SOCKET PAN HEAD SCREWS
DIN 912
HEXAGON SOCKET HEAD CAP SCREWS
ISO 299 NUT FOR T-SLOTS
DIN 431
HEXAGON PIPE NUT
DIN 432
EXTERNAL TAB WASHER
ISO 1379
HEXAGON HEAD TAPPING SCREW
DIN 137
CURVED SPRING WASHER
ISO 1207
SLOTTED CHEESE HEAD SCREWS
DIN 787 BOLT FOR T-SLOTS
ISO 21670
SQUARE WELD NUTS
DIN 6923
HEXAGON NUTS WITH FLANGE
ISO 7045
DIN 929
SQUARE WELD NUTS
ISO 7416
HIGH STRENGTH STRUCTURAL WASHER
DIN 935
HEXAGON SLOTTED AND CASTLE NUTS
ISO 10513
PREVAILING TORQUE TYPE ALL-METAL HIGH NUTS
HEXALOBULAR CHEESE HEAD
DIN 404 SLOTTED CAPSTAN SCREW
ISO 14589 RIVET MUSHROOM HEAD
DIN 571
HEXAGON HEAD WOODS SCREWS
DIN 906
HEXAGON SOCKET PIPE PLUGS
ISO 7906
HELICAL COMPRESSION SPRING
DIN 439
HEXAGON THIN NUTS (CHAMFERED)
ISO 8748
COILED SPRING PINS - HEAVYDUTY
ISO 7091
PLAIN WASHER100 HV
DIN 976
STUD FOR T-SLOT NUTS
ISO 8746
GROOOVED PIN WITH ROUND HEAD
DIN 908
HEXAGON SOCKET SCREW PLUGS
required to ensure that all fasteners made at KOVA pass the necessary customer testing, especially in product applications,” mentions Rishi.
The true strength of KOVA lies in its highly skilled and dedicated workforce, which constantly strives for excellence. “The most unique reason for our success and our products is not only the machines, but the people who are running those machines,” asserts Rishi. “Each and every employee who works at KOVA is trained again and again to deliver the best product quality at each and every stage of manufacturing.”
Rishi adds: “Since the beginning of production at KOVA, most of the employees who joined the company from the start are still working with us. They have pledged to dedicate their lives to KOVA and make it a world-renowned brand. Each and every day they come to the factory with great motivation, positivity, faith and dedication to work for a better future for KOVA and all its team members.”
In addition to its employees, KOVA is also committed to forming strong relations with its customers, suppliers and even competitors. “At every stage, we try to improve our commitment to all stakeholders at KOVA. We try to become better than yesterday and I hope in this way we will keep on improving ourselves to deliver the best product and the best company to our employees and also to our customers,” states Rishi.
KOVA is predominantly involved in the export of standard fasteners all over Europe and the USA – with customers in more than 40 countries worldwide. “This accounts for around 75% of our business share; the rest goes to Indian customers in the farm sector and industrial hardware segment,” mentions Rishi. “As a company we have a strategy in place that targets almost equal share of turnover in each of these big markets. Each market is growing very rapidly and we believe there is an opportunity for us as a business – due to geopolitical reasons creating a shift towards India for global companies who buy large volume of fasteners. I believe that in the next five to ten years there is a real opportunity for Indian fastener manufacturers to become truly global players within the fastener industry and that India can take the lead as Asia’s ‘go to’ destination for fastener manufacturing capabilities.”
As the automotive industry undergoes a shift towards Electric Vehicles (EVs), KOVA also recognises the potential business opportunities in this emerging market. While acknowledging that the complete transition to EVs may take the next seven to ten years, at least, Rishi believes there is strong potential within the EV market. “It’s too early to say if the EV sector is causing any disruption in the traditional technology at the moment. However, in the long run, surely EV will pick up. At the moment, the EV industry still has to standardise the products and do a lot of engineering, particularly in the field of fasteners.”
The new plant will be a second unit and will help us service customer requirements faster and at more competitive prices.”
Rishi continues: “Most of the two-wheeler EVs are a complete kit that is imported from China, with all the fasteners too. I believe it is going to change very soon as those fasteners are not standardised and might cause a lot of challenges in the field trials and post failures. I feel there will be a lot of design improvements in fasteners for EVs, especially in the two-wheeler segment.”
Other key topics KOVA will continue to focus on include the company’s commitment to sustainability and continuous improvement – reflecting its determination to remain relevant in a rapidly changing industry. “Fasteners are a product that will be in high demand in the coming years and more and more engineering activities around the world are now taking place in India. This makes the fastener business more sustainable and opportunities for growth are surely there for top fastener brands like KOVA,” emphasises Rishi. “Our aim is to continue at the forefront of the industry, driven by our commitment to quality, customer satisfaction and continual innovation. We envision sustained growth and broader horizons and aim to reach a turnover of US$50 million (€46.3 million) within the next three to four years, indicating an ambitious goal of more than doubling the current turnover of US$15 million for the financial year 2023. We shall not rest on our laurels, but instead will continue to lead the way and aim to shape the future of the industry.”
www.kova.in
Astrotech Steels manufactures and distributes specialised steel products, including engineered fasteners, concrete accessories, coated wire and other products that primarily cater to the industrial and construction sectors.
Based in Chennai, Astrotech Steels’ state of the art manufacturing facility is equipped with precision machinery, which is consistently used in producing quality products. “All our manufacturing equipment has been selected after a thorough due diligence of various types of machines available across the globe,” explains Astrotech Steels Pvt Ltd. “We therefore have high-end machines for every stage of manufacturing. We also provide high impetus on sourcing the right quality of raw material and consumables to manufacture our products.”
Astrotech Steels’ manufacturing operation is also totally integrated from wire drawing to finished product and shipment – all based in one single location – which helps it to better control its processes and operations. “Our entire operation is also governed by stringent inspection/quality assurance systems to ensure consistency in quality throughout the operation – with continuous process improvement.”
All the process functions are also governed by an effective ERP system, thereby enabling the company to maintain accurate and ‘real time’ data in all areas of operation. There is also a quality testing laboratory within the plant to carry out all relevant inspection tests. Astrotech Steels also has an in-house R&D team that works in close coordination with customers to successfully develop new products and meet constantly evolving product and packaging requirements –helping the company to continuously reinvent itself and stay ahead of the competition.
Astrotech Steels’ manufacturing operation is also totally integrated from wire drawing to finished product and shipment.”
“As a business we have insisted in a culture of total quality management, thereby empowering every employee to be constantly vigilant in maintaining the quality levels,” points out Astrotech Steels. “All of the company’s key employees have many years of experience and there is as continuous training programme that every employee undergoes on a regular basis. We also have an effective review and appraisal programme that encourages all employees to continuously keep upgrading their skill sets – in order to maintain high-levels of performance.”
This dedication to its production and employees has enabled the company to create a customer base that is spread across the globe, including customers in the USA, Canada, the UK, Australia, South Korea, India, South America, Africa, UAE, Europe and even Sri Lanka. “We are located in one of the top industrial hubs in India, with close proximity to major sea ports that have excellent connectivity to many major ports of the world,” explains Astrotech Steels. “Our state of the art manufacturing operation, unblemished reputation, unique geographic location, highly skilled work force, wide product capabilities, and esteemed service, help us to cater to different markets across the globe and also enables us to process and deliver the goods within shorter lead times.”
www.astrotechsteels.com
Established in 2006, Strut Support Systems has a rich history of providing high-quality solutions in the field of metal framing – evolving from humble beginnings to become a prominent player within the sector. Here the Indian manufacturer discusses how it is committed to continued growth, sustainability and delivering excellence to customers.
What is it that Strut Support Systems offers customers? What are the key factors that enable the company to stand out from competitors?
“At Strut Support Systems (SSS), we take pride in offering our customers a comprehensive range of high-quality products, including fasteners, strut channels and brackets – prioritising precision in every aspect of our manufacturing process in order to ensure our products meet the highest standards of quality and reliability.
Thanks to our global reach, we are able to serve customers worldwide, offering them access to our superior products and expertise. In addition, our customer-centric approach involves understanding our customers’ unique requirements and providing customised solutions that address their specific challenges. Our streamlined production processes and efficient supply chain management help ensure that our customers receive their orders promptly and reliably. Plus, our knowledgeable and responsive team is always ready to assist customers – providing them with the support they need throughout their partnership with SSS.”
What are the types of products Strut Support Systems is able to manufacture and how do you guarantee the quality of the products?
“Our product portfolio reflects our dedication to providing comprehensive solutions for various industries, meeting the demands of projects with precision and reliability. That is why we specialise in manufacturing a diverse range of products.
Ensuring the highest quality is also at the core of our operations, which is why we implement rigorous quality control measures throughout the manufacturing process. From the selection of raw materials to the final inspection of finished products, we adhere to industry standards and conduct thorough testing to guarantee the durability, performance and compliance of our products. Our commitment to quality extends beyond meeting industry benchmarks; and as a business we strive to exceed expectations. That is why we have established quality management
systems that are continuously monitored and improved to adapt to evolving standards and customer needs.
As a forward-thinking company, we are always exploring opportunities to enhance our product portfolio and manufacturing capabilities. Our commitment to innovation drives us to stay ahead of industry trends and technological advancements.
Going forward, we have plans to expand our product offerings in response to the dynamic needs of our customers and emerging market demands. This growth strategy involves investing in research and development, exploring new materials and manufacturing processes, as well as collaborating with industry partners to ensure that we continue to provide cutting-edge solutions.”
“We believe in providing comprehensive solutions to our customers beyond our core product offerings. This includes customisation services, as we understand that each project has unique requirements. Our experienced team works closely with customers to tailor products to their specific dimensions, materials and finishes. Our in-house team of experts is also available to offer technical support and guidance, whether it’s selecting the right fasteners for a particular application or providing installation advice.
We recognise the importance of a reliable and efficient supply chain and as a business we look to work closely with customers to streamline their procurement process, offering flexible delivery schedules and inventory management solutions to meet their project timelines. We also offer training sessions and workshops to help customers better understand our products, their applications, as well as best practices for installation.
We understand that fastening solutions can be complex, which is why we collaborate closely with customers to identify challenges and develop tailored solutions. Our team is adept at problem solving, ensuring that the fastening solutions we provide align perfectly with the unique needs of each project.
To work with customers in finding fastening solutions, we begin by engaging in a detailed consultation to understand the specific requirements, constraints and challenges of the project. Our team then conducts a thorough analysis of the project’s needs, considering factors such as load bearing requirements, environmental conditions, as well as material compatibility. Based on the information gathered, we provide tailored recommendations for fastening solutions, taking into account the best suited products from our portfolio or proposing custom solutions when necessary. Throughout the collaboration, we maintain open and continuous communication with our customers, ensuring that their feedback is incorporated into the final solution.”
customers. In recent years, we have made significant investments in specific areas or initiatives, including technology and automation, research and development, environmental sustainability, supply chain optimisation, employee training and development, operational efficiency, innovation and product development, as well as customer satisfaction.
Firstly, having recognised the transformative impact of technology in our industry, we have invested in state of the art technologies and automation solutions that have not only streamlined our manufacturing processes but also improved efficiency, reduced lead times, as well as enhanced overall quality – enabling us to fulfil orders more quickly and with higher precision.
What are the key markets for Strut Support Systems and how have these markets developed recently?
“We operate in diverse markets, catering to the unique needs of various industries, including construction, automotive and aerospace. Each of these markets has experienced distinctive developments, challenges and opportunities recently. For instance, the construction industry has been a cornerstone for our products. Despite facing challenges such as fluctuating material costs, and regulatory changes, we have observed steady growth in the sector – driven by increased infrastructure projects globally. The demand for durable and high performance fastening solutions remains strong, aligning with our commitment to quality.
Thanks to this commitment to quality, innovation, and customer-centric solutions, we are well positioned to navigate these challenges and capitalise on opportunities in our key markets. We remain vigilant, adaptive and dedicated to maintaining our position as a trusted partner in these dynamic industries.”
What investments has Strut Support Systems recently made? Why did you decide to make these investments and what are the advantages to the business and its customers?
“At SSS, we recognise the importance of strategic investments to enhance our capabilities, drive innovation and better serve our
At SSS we also understand the importance of a robust and agile supply chain, which is why we have made investments directed towards optimising our supply chain processes. This helps ensure a timely and reliable delivery of our products to customers, even in the face of global challenges or disruptions.
We have also placed a strong emphasis on research and development, with recent investments signifying our commitment to staying at the forefront of the industry, such as introducing new products, improving existing products, as well as addressing emerging challenges.
Finally, our team is our greatest asset, which is why we have invested in comprehensive training and development programmes to empower our employees. These initiatives enhance their skills, keep them updated on industry best practices, as well as foster a culture of continuous improvement.
Thanks to our well trained team, streamlined supply chain processes, as well as other key investments, we are able to provide an improved customer experience – with faster deliveries, reliable service and innovative products enhancing overall customer satisfaction.”
Sustainability is a key topic within the European fastener market, what steps has Strut Support Systems taken in regard to sustainability?
“Sustainability is a paramount consideration at SSS and we recognise the increasing importance of environmental responsibility within the fastener market – particularly in regions like Europe.
That is why as a business we have looked to prioritise the use of environmentally friendly and sustainable materials in our
manufacturing processes. This includes responsibly sourced raw materials and an ongoing commitment to identifying and adopting eco-friendly alternatives. SSS has also invested in energy efficient technologies to minimise our environmental footprint and we continually assess and enhance our manufacturing processes to reduce energy consumption and improve overall efficiency.
Our company also actively works towards minimising waste generation. We have implemented recycling programmes within our facilities and collaborate with suppliers to reduce packaging waste. Additionally, we explore opportunities to repurpose or recycle materials used in our production processes.
We have also aligned our operations with internationally recognised environmental standards and certifications. We adhere to and seek certifications that validate our commitment to sustainable practices, providing assurance to our customers and stakeholders.
Innovation is also a driving force behind our sustainability efforts and we continuously explore and look to implement innovative technologies and materials that help lower the environmental impact. This includes the development of fasteners designed for longevity, reusability and recyclability.
Finally, our company actively engages with stakeholders, including customers, suppliers, and industry partners, to foster a shared commitment to sustainability. Collaborative efforts help us identify new opportunities and best practices to further enhance our environmental performance.
We believe in transparency about our sustainability efforts and provide regular updates on our sustainability initiatives, progress and performance. We are committed to open communication with our stakeholders about our environmental stewardship.”
What are the advantages of being an Indian fastener manufacturer? What are the benefits to customers and why should they look to partner with Strut Support Systems?
“As an Indian fastener manufacturer, we bring several distinct advantages to the table – providing unique benefits to our customers. India is known for its cost-effective manufacturing capabilities and at SSS we leverage this advantage to provide high-quality fasteners at competitive prices, offering cost-effective solutions for our customers without compromising on quality.
India also boasts a skilled and technically proficient workforce, which is why our team is composed of experienced professionals who contribute to the precision engineering and quality manufacturing of our products. Being a versatile fastener manufacturer, we are able to offer a diverse product portfolio that allows customers to source multiple components from a single, reliable supplier – streamlining their procurement process.
We also understand the importance of customisation and work closely with our customers to tailor solutions that meet their specific requirements, whether it’s custom dimensions, materials or finishes.”
“As we look ahead, several trends are shaping the future of fastener manufacturing. The integration of digital technologies, automation, and data analytics in manufacturing processes, is a prominent trend. That is why we are investing in Industry 4.0 technologies to enhance efficiency, reduce lead times, as well as offer more customised solutions to our customers.
The global emphasis on sustainability, which we have just mentioned, is also a driving force in the fastener industry. We are committed to eco-friendly practices, exploring sustainable materials and adopting manufacturing processes that minimise environmental impact. This aligns with the increasing demand for sustainable solutions in the market.
Customers are also increasingly seeking customised fastening solutions that meet their specific project requirements, which is why we are enhancing our capabilities to provide tailored products – working closely with customers to understand their needs and delivering solutions that go beyond ‘off the shelf’ offerings. The demand for fasteners with advanced materials and coatings is on the rise, driven by factors such as increased durability and corrosion resistance. We are staying at the forefront of material science, exploring innovative materials and coatings to offer high performance fasteners that meet evolving industry standards.
The importance of a resilient global supply chain has also been underscored by recent events. We are actively diversifying and optimising our supply chain to ensure a reliable and agile response to market dynamics and potential disruptions.
Collaboration is becoming increasingly vital in the fastener industry and at SSS we are fostering partnerships with customers, suppliers, and research institutions, to drive innovation, share expertise and collectively address challenges in the market.”
www.strutindia.com
India is a country the world is looking up to with rapt attention and renewed respect – with it poised to catapult itself into scaling heights – unfathomable only a decade ago. The next twenty-five years promise to be the most transformative Indian history has ever witnessed, with the potential to become a US$40 trillion economy by 2047 – but this path to the future holds both daunting and rewarding challenges ahead.
Industrial grade fasteners witnessed a valued business of US$88.43 billion (€81.8 million) in 2021 and the next ten years hold promise to see a rise at a CAGR of 4.5%. The sector is staring at strong influences by a steadfastly growing demand for industrial fasteners in the automotive and aerospace industries – backed up by significant developments in the construction industry, such as increased infrastructure building and spending amidst a growing population.
Technological advancements are also being used to manufacture cutting edge lightweight products used in multiple industrial applications. This is leading to a surge in the demand for hybrid fasteners, which combine injection moulded plastic components with metal elements, driven by these advancements.
Riding on a rock solid foundation, Precise Fasteners is an ISO 9001:2015 certified ferrous and non-ferrous fastener supplyer that has been established for over 55 years. The business manufactures and supplies more than 10,000 varieties of premium quality fasteners and is proud to be amongst the chosen few companies that can provide high-end industrial fasteners for practically every engineering need and application.
At the helm
Founded in 1967 by Prakash Shah, Precise Fasteners Pvt Ltd started as a modest trading business that slowly and steadily made inroads into multiple reputed clients. Joined by his son Parag Shah in 1990, the business quickly took giant leaps towards expansion. Initially the company set-up a modest manufacturing facility, which was gradually expanded and today Precise Fasteners holds a stake in different manufacturing facilities in and around Mumbai, Maharashtra.
India’s Ministry of Micro, Small and Medium Enterprises even named Precise Fasteners as one of the Top
The business manufactures and supplies more than 10,000 varieties of premium quality fasteners…”
100 SMEs and the company has accumulated several accolades and awards in its quest to excel. Precise Fasteners has also raised the stock of the company thanks to its products and professionalism, which has proved to be a strong combination.
Today, Precise Fasteners caters to more than 500 clients in India and overseas. It can also boast of being on the approved vendor list with some significant government departments, including Indian Railways, BHEL, HAL, GAIL, BEML and ISRO. Within the private industry, Precise Fasteners proudly caters to conglomerates including ABB, Reliance, Godrej, L&T, Nilkamal, as well as TATA Steel among others – across various industry segments. Presently exporting to fifteen countries, the company is also actively participating in overseas exhibitions across Europe and the USA –helping it to stay in sync with developments and trends across the globe.
Although a substantial portion of fasteners are standard, Precise Fasteners takes pride in specialising in non-standard/customised/
made to engineering specification fasteners and has created several essential and critical components. The company can offer various types of products, such as machine screws, socket products, woodscrews, hex wrenches, self-tapping and drilling screws, bolts, rivets, pressure lugs, nuts, headless screws, star lock washers, bearings and much more.
The company’s USP lies in offering high-grade fasteners, which last for decades without any need for replacement. As a business it can also assist clients with the design process thanks to its expertise and provide solutions that making it easier for customers to assemble their products. The company can also offer multiple types of plating/finishing with SST (salt spray test) withstanding a rigorous 2,000 hours of testing.
Precise Fasteners also offers clients the convenience of a VMI and two bin system in addition to comprehensive fastener solutions. The company lays a strict emphasis with on time deliveries and does not commit to delivery schedules that cannot be maintained. Trying to rush deliveries only hampers quality, affects the delivery itself and ultimately impacts the trust and faith the client has in the business. Clients need timely supplies in the right quality, which is the calling card for Precise Fasteners – especially with the experience it has within the business.
This is underlined by the company’s production, which goes through the rigors of comprehensive quality checks at every stage –from raw material to final product – by a very capable QA team. The administrative team ensures individual client requirements are addressed and adhered to in accordance to purchase order terms, with the shipment and logistics team adapting to individual client packing norms and ever changing needs.
Emerging from relatively humble beginnings, Precise Fasteners has earned its reputation as one of the biggest and most dependable players in the industry through sheer grit and toil. The ability to foresee and implement upcoming market trends on the basis of growth in infrastructure, and implementation of policies, is what enables the business to stand out from the crowd. For instance, the company has developed a complete range of fasteners for the EV segment and can cater to the two, three and four wheeler segment. The huge boost in the construction industry also
Precise Fasteners has earned its reputation as one of the biggest and most dependable players in the industry through sheer grit and toil.”
saw a whole new approach towards building faÇ ades – providing all related fasteners instantly to the façade companies. Precise Fasteners also has clients across multiple industries including rail, furniture, oil & gas, solar power, amongst others.
The number of uses for fasteners is on a rapid incline and due to this Precise Fasteners is optimistic about future growth. It is expanding its network and is in the process of setting up offices across India. It is also setting up another manufacturing unit with IATF approval in the first half of 2024. Simultaneously, it is creating an exhaustive showroom, which will act as a walk through exhibition for clients to address their needs and requirements. Plus, every aspect of the business is constantly monitored and upgraded in accordance with emerging technology and demands.
www.fastenerindia.com
From 16th – 19th January, the halls of the Basel Trade Fair were the meeting place for 615 exhibitors and partners presenting the latest products, technologies and innovations in the construction industry.
Across 85,000m 2 of exhibition space, 52,486 visitors enjoyed ‘Shaping change together’ at the multi industry trade fair offering opportunities for product experiences, information exchange and networking on a variety of platforms.
Every two years, Swissbau welcomes various specialists from the construction industry, such as architecture, planning, investment as well as crafts and operations. For the first time, the exhibition took place across four days – with exhibitors praising the quality of discussions and the increased willingness to place orders at the trade fair.
“The positive feedback from exhibitors, partners and visitors confirms that we are constantly developing new, effective offerings for Swissbau,” says Rudolf Pfander, trade fair manager at Swissbau. “This year, newly created marketplaces as meeting areas with short presentations, as well as the new ‘Swissbau Inside’ design stage inspired both the specialist audience and also the private construction enthusiasts.”
Circular economy, energy, digitalisation and living space were the key themes at this year’s Swissbau and represent the major challenges of the industry. Rudolf Pfander highlights: “An efficient trade fair visit is not just about maintaining contacts and personally presenting products. It is becoming increasingly important to use the day for individually selected events and exchanges with leading experts. This is a great added value for employers and employees when visiting Swissbau. I am very pleased that our unique mix of exhibition and further training is so highly valued by the specialist audience.”
Swissbau will take place once again from 20th – 23 rd January 2026 in Basel.
Messe München has announced that from 2025, the next trade fair for architecture, materials and systems, BAU, will be shortened from six to five days, taking place in Munich from 13 th – 17 th January.
In around ten months, the world’s leading trade fair for architecture, materials and systems will return to its usual winter slot, from Monday to Friday. BAU in Munich will be the international meeting place for architects, engineers, investors, retailers, and tradespeople. The focus will be on solutions and products for the future of construction.
“The last event was a resounding success. The exhibitors and visitors were full of praise for BAU in the survey. In our discussions with the key accounts during the trade fair, however, it became increasingly apparent that the companies would welcome a shorter fair,” explains Dr Reinhard Pfeiffer, CEO of Messe München.
Dieter Schäfer, long-standing chairman of the BAU advisory board and board of trustees points out: “At our recent meetings with Messe München, we took a critical look at this issue together with Messe München and received a similar opinion from the large majority of our members.” Friday will remain a full trade show day with the same opening hours as on all other trade show days.
Just under a year before the trade fair is due to start, the registration figures for exhibitors and exhibition space are on par with BAU 2023. It means that BAU 2025 will once again be booked out and achieve full occupancy of the 18 halls. To date, a host of companies have already confirmed their participation at BAU 2025.
“With this clear commitment to BAU, the leading companies are sending a clear signal to the market despite the somewhat difficult situation. As a result, we are convinced that BAU 2025 will provide fresh impetus for the industry,” comments Dr Reinhard Pfeiffer.
Next year’s key topics at BAU include urban/rural/neighborhood transformation, resource conservation, resilient and climate friendly construction in the face of natural disasters or pandemics, boosting productivity through modular construction and cost-effective construction with the use of robotics and Artificial Intelligence.
From 23 rd – 26th April this year, the most up to date technologies from the fields of vision technology, image processing, sensor technology, as well as measuring and test technology, will be presented in Stuttgart for the 36th edition of Control.
Control showcases various types of measuring technology that is relevant for all industries and the 2024 edition aims to build on the success of Control 2023, which served as a highly inspiring platform for its visitors.
“We’re currently able to confirm very strong booking levels, with 43% of the exhibitors coming from outside of Germany. We’re once again expecting impressive, trailblazing solutions for quality assurance and an expanded range of topics,” comments Fabian Krüger, control project manager at P.E Schall, organisers of the exhibition.
Quality assurance has become increasingly important in many industries and sectors, a sentiment which is reflected at the Control trade fair. “Quality assurance solutions are used in industrial production, in all operational processes, in non industrial fields of application, in medical technology as well as in defence applications,” explains Fabian. “Measurement, testing, inspection, evaluation, documentation –end-to-end solutions for these functions are required everywhere
because more and more data is being captured, analysed, linked and fed back to the respective systems in order to achieve transparency and consistency. This is why software and intelligent evaluation algorithms are playing an increasingly important role.”
Control brings quality assurance experts from all over the world together on an equal footing and is regarded as a unique meeting place for professionals. An intensive exchange of expertise takes place at the event, which is highly valued by exhibitors and expert visitors alike. Solution suppliers come together directly with quality managers, engineers and production experts involved in routine daily operations.
“Quality inspection and quality assurance are highly interesting topics that impact all industries,” highlights Bettina Schall, managing director of P.E Schall. “This event demonstrates just how rapidly technology is developing. Control’s user-oriented trade fair format features the presentation of top technologies, outstanding expertise, direct practical relevance and high-levels of internationalism.”
An extensive programme of activities will make Construmat 2024 the ideal forum for debate and knowledge in the construction industry, focusing on sustainability and innovation as major themes.
From 21 st – 23rd May, the Fira de Barcelona Gran Via venue will host the 23 rd edition of Construmat where innovation, sustainability, industrialised construction, wood and concrete construction will be major talking points, through conferences to masterclasses, forums and talks.
In this sense, it is worth noting the celebration of the Sustainable Building Congress, a congress that will have
50 presentations, 15 round tables and 120 speakers, which aims to highlight the initiatives developed to minimise the environmental impact of construction activity and promote more sustainable and responsible construction. Decarbonisation and the circular economy, digital solutions and technologies, as well as industrial construction systems will also be major themes of this congress, highlighting the best practices and sector innovations.
Show organisers have also highlighted a 50% increase in exhibition space in comparison to the last edition.
A new edition of the prestigious Construmat Awards, curated by the Mies van der Rohe Foundation and incorporating the public award for the first time, completes the programme of Construmat 2024 activities.
With less than a month to go until the Düsseldorf fairgrounds opens its doors for wire® 2024, the international trade fair has announced record numbers – with 1,464 exhibitors from 62 countries signed up to present the latest technologies and products from the wire and cable industry.
Taking place from 15 th – 19 th April, over 67,400m 2 has been sold in exhibition halls 9 to 17, surpassing the current record from 2018, when 1,441 exhibitors from 53 countries occupied a net area of around 65,000m 2
Strong exhibitor growth within Europe comes from Turkey, Italy, Austria, Spain, Switzerland, Sweden and the Benelux countries. Overseas exhibitors from India, South Korea, Taiwan, China and the USA are also increasingly travelling to Düsseldorf.
From machinery and equipment for wire manufacturing, wire processing and finishing, spring and fastener technologies and their finished products, auxiliary materials and process technology tools through to glass fibre, all aspects of the wire industry will be on show.
Fastener and spring making technologies, as well as their finished products will be housed in hall 16 where the entire value chain for fasteners and springs can be found. Exhibitors will include companies from raw materials, machinery and equipment to fasteners, connectors and industrial springs.
Fastener companies exhibiting include CAN-ENG Furnaces International Ltd, Carlo Salvi SpA, Dimac Srl, ENKOTEC A/S, Hatebur Umformmaschinen AG, Marposs GmbH, Nakashimada Engineering Works Ltd, National Machinery LLC, SACMA Limbiate SpA, San Shing Fastech Corp, Talleres Saspi S.A, WAFIOS Umformtechnik GmbH, as well as Weighpack B.V.
“This is a great result and a clear signal to us that wire® Düsseldorf continues to be the international number one trade fair for the wire and cable industry,” says Daniel Ryfisch, director wire, tube and flow technologies at Messe Düsseldorf.
For the first time, the innovations showcased by the industry players in the exhibition halls will be accompanied by an extensive programme of supporting events tuned to the market, on all five trade fair days.
This includes a premiere for wire® and Tube, on the forum stage of hall 1 ‘Buyers’ Day’ will present everything revolving around Due Diligence Supply Chain Acts, sourcing and logistics, transparently compiled and presented by the Federal Association of Materials Management, Purchasing and Logistics (Bundesverband Materialwirtschaft, Einkauf und Logistik).
At the BDS Forum (hall 1 A47) the Federal Association of the German Steel Trade (Bundesverband Deutscher Stahlhandel) will provide information on global trends in the steel trade. Here, experts will analyse the impact of current economic policy trends. Steel traders will also discuss sourcing and sales markets, economic framework conditions and the mega themes digitalisation and AI.
With
Nedschroef Machinery will be exhibiting at wire® Düsseldorf and has a number of new products and innovations that it will be demonstrating to visitors throughout the five days of the show.
Based in Herentals, Belgium, Nedschroef Machinery – part of Nedschroef Group – provides metal parts manufacturers with premium forming machines and tooling solutions. “We can design or configure industrial machinery for the production of a wide variety of metal parts, including fasteners,” explains Dries Paulussen, operations manager at Nedschroef Machinery. “Across the globe our cold and warm metal forming machines are renowned for their durability, efficiency, and versatility, as well as flexibility due to their modular design.”
Nedschroef Machinery’s portfolio includes conventional mechanical cam-operated machines, as well as servo-driven machines. This includes multi-station cold and warm forming machines, straightening machines, as well as cutting machines.
“Our multi-station machines come with a range of standard features and have a modular set up,” points out Dries. “This enables our customers to equip their machine with exactly the features they need to meet their own specific requirements. For the latest multi-die and multi-station machine models we have also incorporated direct drive servo motors, which can be used for a variety of purposes. These high performance, programmable motors offer unparalleled advantages in terms of accuracy, productivity, reproducibility, as well as flexibility in forming abilities and production volumes.”
As part of its Herentals site, Nedschroef Machinery has a testing department, which includes three demonstration machines – along with two cold formers and a straightening machine – so that it can test solutions for customers in-house and see if they are feasible via cold forming technology, as well as helping to understand what tooling concepts may need to be used.
“A big part of the business is our ability to design and deliver tailored precision tools for use in cold and warm forming machinery. With our
comprehensive tooling resources, including five in-house tooling engineers, we can make the tools needed to produce both basic and complex metal parts,” underlines Dries. “A lot of the projects we work on start from the tooling and whether it is possible to make a particular part. It is once this has been clarified that we are then able to work on what machines are the most suitable to produce the parts. We do this by working closely with customers to find out exactly what they need within their projects – so that we can ensure the machines are able to meet these requirements.”
Nedschroef Machinery also has its own milling department in Belgium, where it can produce critical parts for its machines, as well as support customers when there is a requirement for quick turnaround for specific products. “After what has happened in the market over recent years, with the number of external challenges, it is vital that as a business you have control over your critical parts,” states Dries.
“Of course, we work with partners for certain parts, but these are predominately products that are easier to source when required. Our milling department is focused on those parts that are not as easy to source and have significant delivery times but are still very important for the functioning of the machines – which is why we need to have the option of in-house production.”
Nedschroef is globally renowned for crafting durable, innovative machines. We continually push the boundaries of cold forming, striving for manufacturing excellence. Pioneering servo technology in cold forming machines, we’re now enhancing production efficiency and digitization. Explore our state-of-the-art Human Machine Interfaces (HMIs) and Smart Machine Assistance, along with our progress in Digital Twin technology, revolutionizing machinery management.
Join us at the WIRE to delve into our advancements. Let’s discuss our latest updates and innovations together.
New website
Launches a few days before the WIRE!
Meet us at WIRE2024
Düsseldorf | April 15 – 19 | Hal 16 | Stand A22
Dries adds: “Thanks to the investments within the milling department, we also have extra capacity for service, which means that when customers need a part quickly we are able to produce it, which is another value added service.”
To go alongside its machinery and tooling capabilities, Nedschroef Machinery is also able to provide a global service to its customers – with operations in the three key markets. “In Belgium we produce and design the machines, as well as service them for the whole of Europe. We also have a service centre in Detroit, USA, and another one in Kunshan, China,” mentions Dries. “The challenges of recent years has led to the policy of ‘local to local’ becoming more of a factor, so it is very important to have people locally and to provide the correct service to customers. That is why we have recently started a joint venture in China to produce machines ‘local to local’ and why, in the coming years, we will expand our service centre in Detroit – both of which will enable us to further support our customers.”
Nedschroef Machinery has established itself within the market through its innovation and for supplying good, reliable machines – some of which that have been running for over 40 years and still producing high-quality products. “We are known for our innovation and that is why it is one of our key business strategies and something we are always focusing on,” explains Dries. “Currently, the innovative topics we are concentrating on include how we produce efficient machines that do not require skilled operators; as well as how we enable customers to produce smaller batch sizes cost effectively. By introducing these innovations, we will be able to further support customers and help make their production more efficient.”
Nedschroef Machinery will once again be exhibiting at wire® Düsseldorf and will be showcasing a selection of these innovations including new Human Machine Interfaces (HMI) and data logging capabilities; additional machine features that will make them easier to operate; as well as a new website to help customers find the solutions they need.
“The new HMI and data logging platform are focused on helping the operator with easier set-up – thanks to visual tools for setting up the machines – as well as helping with faster problem solving, by providing extra information on how to quickly solve any issues,” reports Dries. “We also have hybrid technologies that we will promote during the wire® exhibition. This is where we take the classical mechanical machines and we add servo-driven technology. This helps make existing machines more efficient, as well as gives customers the possibility of producing even more complex parts on their machines. It also provides extra insight, reduces set-up time and means less maintenance is required.”
An example of this is the NC feeding unit from Nedschroef Machinery, which can be retrofitted onto machines. “This really gives the customer extra functionality – the feeding length is much more
stable and setting up is easier,” adds Dries. “At our booth we will display an old style wire feed with feed rolls, a mechanical linear wire feed and a state of the art NC linear wire feed, so visitors can compare what they can change from their old machines and the benefits of the new technology.”
Dries continues: “We are also showcasing the NC transfer, which can be used for making complex parts, as it enables forming inside the punch. Normally you can only form inside the die, but with NC transfer you can also form inside the punch, which will be a big advantage for customers.”
Another new development that will be displayed at the show is a new design for Nedschroef Machinery’s website, which will include extra features to make it easier for customers to select machines and services they would like to use. “The website has been modernised with the aim of letting customers know our technologies and what we can offer as a company,” highlights Dries. “The new site will also make it easier and faster for them to get in contact with our service department.”
Dries adds: “We are very excited to be at the wire® Düsseldorf show. There is certainly room nowadays for digital meetings, especially since everything with Covid-19, but there will always be a need for physical meetings, as they are so productive and help in creating longer lasting partnerships. We always have valuable discussions at the wire® show, as it is talking directly to customers about their markets and needs. We try to be as close to the customer as possible, so that we can help solve their problems, because if our customers are successful then that will help us to be successful.”
“Nedschroef is globally renowned for crafting durable, innovative machines,” concludes Dries. “We continually push the boundaries of cold forming, striving for manufacturing excellence. Pioneering servo technology in cold forming machines, we’re also dedicated to Industry 4.0, enhancing production efficiency and digitisation. Nedschroef, we build machines that perform!”
www.nedschroefmachinery.com
SACMA Group will be attending wire® Düsseldorf 2024, hall 16 stand D44, and as always will be welcoming all the actors of the forming world to its always appreciated booth dedicated to its four brands – SACMA, Ingramatic, HS ASPE, and Tecno Lift – as well as the most important innovations from within the Group.
Firstly, SACMA will present its series of combined machine model SP18, as it has been updated with a new soundproof enclosure, a new wire feeder with direct drive motor, new HMI software and new transfer unit. This combined header can produce fasteners and screws for the automotive, construction, electric/electronic and white good industries – starting from the wire. SACMA states that this is the best solution for high productivity requirements, consolidation of production methods, floor space utilisation and work flow in the fastener manufacturing process – by having the forming, chamfering and thread rolling all in one machine. The machine is also equipped with the latest technologies available on the market, such as direct drive motors and ultimate software to facilitate the operators to make quick changeover easily and safely.
to permit a shorter commissioning time. All these features ensure quick changeover, space saving, precision, ergonomics, as well as low production costs thanks to its construction design.
The Ingramatic division is today the worldwide leading company for designing and manufacturing cold and warm thread rolling machines. The well known modular I-Thread machine line provides many innovative features, such as the starter units driven by torque motor motion, which will be displayed at wire® Düsseldorf with the 2024 RP120 (TR1/W1015).
Ingramatic points out that the 2024 RP120 (TR1/W1015) is the best compromise between rigidity and high-tech features – making it the most competitive thread rolling machine for building, construction, electronic, furniture, appliance and automotive fasteners, with the capability to run up to 600ppm.
Features of the machine include the control of the introduction system, obtained by a torque motor, and the introducer stroke being adjustable by the operator panel or by means of the electronic handwheel without any manual adjustment, ensuring speed and accuracy of production changeover. The blanks are also separated at the feed point by an innovative stop system that positions the workpiece on three points before it is placed between the dies.
Ingramatic also supplies a monobloc soundproof enclosure that guarantees the operator’s safety and noise reduction. The enclosure rests directly on the base to ensure that all the liquids circulating in the machine are contained and collected – making the RP120 ecofriendly. A special design has also been made for RP120 in order to make the machine very compact and to reduce the space requirements and
The brand HS ASPE is the division of the Group providing secondary operation machines to run pre-formed parts with a range of technologies, including tapping machines, combined machines, transfer machines and multi spindle turning machines.
At wire® Düsseldorf HS ASPE will show the new generation of combined machine model DT12, which is able to run parts up to M12. Drilling and tapping combined machines are used to execute complementary operations in addition to the tapping. Operations like drilling, boring, facing, as well as chamfering, are so performed, sequentially or in overlapping, exploiting the single positioning/clamping of the part under process. That way the output rate is strongly increased. A top performer machine can be gifted with 2-3-4 working units.
Finally, Tecno Lift is the company of the Group in charge of the design and the manufacturing of all ancillaries to load, feed and convey parts to all of SACMA Group’s machines. Every machine that will be displayed on the stand at the show will be equipped with Tecno Lift solutions, which are available for other application or existing machines already installed at the customers.
“We will be pleased to welcome visitors at wire® Düsseldorf 2024, hall 16, stand D44, to show and explain all the new technologies and the capacity to support all the customers around the world,” reports SACMA Group.
www.sacmagroup.com
April 15-19 | Hall 16 / D44
Düsseldorf, Germany
Our combined headers All In One improve drastically your sustainability.
All In One = Optimum Footprint
Energy saving : the installed power of multiple processes, to produce screws and bolts, consisting of header, pointer, washing machine, roller and parts conveyors, is well over double of the installed power of the Sacma combined header, suitable to execute the same operations.
Floor space saving : All In One making the production space 4 times less than traditional lines of manufacture, consisting of multiple machines.
Clean Factory : from wire to the finished product within a single sealed machine, simpler and efficient.
WIP reduction : the WIP requirement of blanks between different operations is cancelled, and deletion of inter process washing operations provides an improved environmental foot print.
Employees care : health and safety is vastly improved using only one machine, having operations within a single machine footprint, thus avoiding wasteful travel between multiple processes and machines.
Sustainable supplier : Sacma is one of the most sustainable manufacturers of forming machines in the world having the production of components integrated in our factories ? Come to visit us !
One of the biggest frustrations nail producers face is downtime, from box changes to locating and fixing issues. That is why the latest version of the ENKOline, from ENKOTEC, is designed to minimise downtime and reduce labour intensity.
When placed in an in-line configuration with the ENKOveyor magnetic conveyor, ENKOroll thread rolling machine, as well as the ENKOveyor Smart Belt conveyor, the ENKOline functions as a complete end-to-end nail production solution. Equipped with the ENKOsmart software platform – an advanced system of interconnected applied sensor technology that allows the individual machines in the line to communicate with each other –the new ENKOline offers a range of advantages such as automatic nail transportation, a reduced footprint and auto-stop/start capabilities.
For example, when the ENKOveyor Smart Belt conveyor senses the nail box at the end of the line is almost full, it will send a signal to put the thread roller into idle mode, which will in turn send a signal to the magnetic conveyor in front of the thread roller and the nail machine, causing them to stop. This allows the operator to change the box without having to shut down the whole line. As soon as the ENKOveyor senses that the box has been changed, it will send a signal to the other machines to resume their normal production, automatically starting up the line again.
This saves valuable time and makes it possible for one operator to manage multiple ENKOlines at the same time – significantly increasing production efficiency in comparison to other in-line or batch production set-ups. The ENKOline can also be arranged in a number of configurations to suit floorspace and needs – including a range of collating solutions, which will be demonstrated by ENKOTEC at the upcoming wire® Düsseldorf show.
The advanced sensors, and ENKOsmart software platform, also enables users to monitor nail production and collect data about the machine’s performance, such as precision quality control and intelligent error tracking, which can be viewed on an interactive touchscreen –making it easy to spot opportunities for improvement.
If an error should occur, the sensors can accurately identify it and report it on the touchscreen interface. This means repairs can begin straight away, eliminating the downtime usually needed to discover the cause of the
problem. The screen also features a digital manual and intuitive video guides to make maintenance and repairs as quick and easy as possible.
The ENKOsmart system also delivers a solution to one of the most frustrating issues in any production industry – waiting for support. It provides a unique opportunity for remote connectivity, which facilitates ‘real time’ troubleshooting and support from a team of expert service engineers at ENKOTEC HQ. This significantly reduces downtime as many issues can be resolved remotely with specialist guidance – getting the machines up and running again as quickly as possible.
www.enkotec.com
Boost efficiency and increase production capacity with the ENKOlinethe world’s most autonomous in-line nail manufacturing system.
Join the Fourth Industrial Revolution and reduce labour intensity with IIoT-enabled machinery featuring:
Advanced Sensor Technology
Auto-Stop/Start Capabilities
Interactive Touch-Screens
Intuitive Digital Manuals
Meet us at:
Hall 16
Booth D40
Remote Support to keep your business ahead of the competition! www.enkotec.com
Once again SASPI will be attending the wire® Düsseldorf show and will be full of energy and excitement to highlight all of its latest features and technology, after what has been a very successful 2023.
On the SASPI stand visitors will find machines including the company’s latest secondary operation machine. This machine´s main characteristic is the lack of cams, with every single movement easily adjustable and configurable to customer needs.
“The new secondary operation machine will start as a pointing, drilling or broaching machine but its potential is beyond these processes,” underlines SASPI. “This user-friendly machine introduces a brand new technology with all the experience and features of the well know SASPI MPA secondary operation machine.”
Also on the stand, SASPI will showcase its new GV2-10 flat die thread rolling machine – equipped with an induction heating unit for warm/hot rolling. The machine is fully motorised and connected, with a patented die block adjustment – together with other motorisations and automatic
At wire® 2024 Manassero Machines will, as always, be available for its customers in hall 16, stand A54, close to two companies that it represents –Nakashimada and National Machinery.
Personnel on the Manassero stand will include Marco, Filippo and Niccolò Manassero, who are hoping to have a five die progressive SACMA header – SP260 on the stand as well. “Time is tight so it is yet to be confirmed but our plans are to display the SP260, which is a new and very interesting machine that we just purchased for stock,” explains Marco Manassero, owner of Manassero & C Srl.
During the show, Manassero will remind its customers about its new partnerships with National Machinery in Portugal and Spain, as well as RMG in Italy. “In addition to these relationships we have for a long time partnered with Nakashimada for southern European countries and RMG for eastern countries,” mentions Marco.
On its stand Manassero will also have all the necessary video material to show more than 200 second hand fastener machines, which are hosted in its two warehouses near Torino in Italy. To add to this there will also be brochures, cold forged parts, as well as everything else necessary to address any questions visitors may have regarding the cold forming process and machinery.
“After wire® Düsseldorf we also plan to have our own open house in our facility with two new RMG wire drawers,” mentions Marco. “Plus, there will be a ‘space saver’ machine, which is the ideal machine to cope with lack of room in the plant, and another machine will be a SMART flat die thread roller. All these machines will remain on display in our warehouse for future visitors, enabling customers to feel the quality and the technology of these two well known brands first-hand.”
www.manassero.eu
die-match – making this machine the easiest and quickest machine to set-up.
“The new GV2-10 flat die thread rolling machine combines the highest technology of the market with the well known SASPI strength of making a highly reliable machine,” states the company. “Whilst this type of rolling is mainly used for aerospace fasteners, it could be used for other applications too and we are excited to speak to visitors about its capabilities.”
“These two machines won’t be the only news from SASPI, we have so much more to talk about during the show and that is why we invite all visitors to our stand in hall 16,” concludes SASPI.
www.saspi.es
For Mayes & Warwick, a specialist manufacturer of thread rolling dies and fastener rolling solutions, wire® 2024 in Düsseldorf is more than just an event – it’s the heart of the company’s exhibition calendar.
For 30 years Mayes & Warwick has made invaluable connections and created business partnerships lasting decades during the show. For the company not exhibiting would be inconceivable; it’s an integral part of its development.
Boasting a rich heritage in precision engineering, Mayes & Warwick takes pride in showcasing its extensive product selection, which has remained at the forefront of fastener production for over 100 years. Combined with its expertise in die design, consultancy, quick turnaround, and supporting its clients’ production, Mayes & Warwick remains a leader in its field.
“Our flagship products are flat thread rolling dies,” states Mayes & Warwick. “With licenses to manufacture rolling dies for renowned brands such as Taptite®, Remform®, MAThread®, Delta, ALtracs®, and more, we lead the market in this field. Furthermore, our machine screw roll dies offer versatility – capable of producing various thread styles, including Metric, Unified, BA and BSW.”
Backed by a skilled team and cutting edge machinery, Mayes & Warwick serves the needs of manufacturers of lock bolts, rivets, special profiles, and self-tapping screws. However, its product range doesn’t stop there, it extends to knurl wheels, holders, and circular and planetary thread rolls – establishing it as a comprehensive solution for fastener production.
www.mayesandwarwick.com
Hall 16 / F58 Hall 16 / A54More than ever, a simple overview of process key figures is an important data basis for production, which is why EWMenn – the technology leader that has been shaping the industry for over 111 years – has continued its reputation for new solutions regarding the production of threaded and profiled parts, with the development of digital iQ-machine assistants.
With the digital iQ-machine assistants, EWMenn reports that it is supporting its customers in the optimal production of threaded or profiled parts. The digital iQ-machine assistants are characterised by simple operation, fast and repeatable set-up, as well as by an overview of effectiveness and resources used.
“Effective set-up and high quantities, with consistently excellent quality and minimal use of resources, are the drivers of the developments,” explains Hendrik Scharf, technical director at EWMenn GmbH & Co KG.
In the current series, all machines also have the Prevent & Support feature as standard for a long service life and high value preservation through regular maintenance. Upcoming maintenance work is conveniently displayed and visually explained to the operator. Completed maintenance work can also be easily confirmed. A transparent overview is always ensured for maintenance thanks to the archiving and display of maintenance work carried out.
If the machine is equipped with linear motorised positioning of the feedfinger, in short an LMP-Feedfinger, the LMP Assist function is also included as standard. With this function, the machine operator is effectively guided on the machine touch panel to a setting that ensures precise, fast and gentle insertion of the blanks.
To add to this there is also the iQ-Setup Assist, this function enables an even more precise and faster preparation of the machine. Almost without tools, the system allows product specific settings to be adopted by push-button. Articles and their specific settings can be saved in the database and are continuously compared. The machine operator is effectively supported during the set-up process by displaying the target and actual values. Transparent work processes are also ensured. Digital
displays, for example on the die basket, provide directional information and visualise the set values – user-friendly with signal colours. Process optimisations can be implemented very easily with this system and deviations from article specific set-up parameters that have already been made are always indicated.
Today more than ever, a simple overview of process key figures is an important data basis for the production. The EWMenn iQ-machine assistants have been developed specifically for this purpose.
For instance, the iQ-OEE Monitor creates a bundled performance overview of the overall equipment effectiveness. The degree of utilisation, quality factor and performance factor are displayed. This function is therefore ideal for evaluating equipment effectiveness and for technological process evaluation. Data from the latest machine generation can also be easily transmitted to a company network in conjunction with a compatible data collection system via an OPC UA interface that can be configured on request.
The iQ-Energy Monitor provides a further central overview of the current and total electrical and pneumatic energy consumption during the machine operation. This machine assistant evaluates the energy consumption per article, batch or operating time, as needed, to make costs more calculable or to make the product specific footprint recordable.
The displayed and bundled performance overview is therefore ideally suited for a technological and process-based evaluation, so that process optimisations can be identified and energy saving potentials can be deduced in terms of sustainability support.
www.ewmenn.de
ASAHI OKUMA AT810 (2 machines) 8x100 mm 200 ppm 7 5 tons 1992
NATIONAL 34 6 5x55 mm 200 ppm IAC sound enclosure 1985
KLOSE LP200-10 10x 200 mm, 90 ppm, 14 tons 1999 unused since 2005
SALVI 243 (4 machines) 5x25 mm, 350ppm, bushing cutoff, sound encl 1990
CHUN ZU CBF83L 10x115mm, 140ppm, 25HP, 14 tons 2000
NATIONAL 500 (3 machines) 14x50 mm 100 ppm Universal Transfer TKO 1986
MULTIPRESS MP510S 12x100mm 50-200ppm 16 tons 2000
NATIONAL 625 S3 LS 19/16x100 mm, 150 ppm, 24 tons, sound enclosure 1988
SALVI 476/SV (2 machines) 4 76x45 mm 450 ppm sound encl 1980 & 1983
NATIONAL M56 HS (3 machines) 6x30mm 350ppm 1970 1978 & 1981
SACMA SP21 (2 machines) 8x80mm, 200ppm 1974 & 1985
KLOSE DPL8 8x200 mm, 40-50 ppm 1980
HILGELAND CH3L (3 machines) 10x150 mm, 100 ppm 1978, 1980 & 1984
FENG PEI FW-40C-255 13x255mm PKO 40-50ppm 30HP 1999 CE
CHUN ZU CH20S 20x150mm 35ppm 250 tons load 23 tons 2014 CE
E W MENN GW52 (2 machines) M6x80/40mm 600ppm 1980 & 1987
E W MENN GW83L (3 mach ) 4/12x150/105mm 260 ppm vib bowl 1984 1985 1990
ORT RP75 max parts diameter 140mm 70 tons 30 kW 1996 CE RMG 1214 Wire Drawer - 22mm capstan 1100mm 21 m/min motor 40 HP 2006
CAN-ENG is continuously working on enhancing the design and development of its modern mesh belt heat treatment systems, which are specifically designed for the fastener industry – ensuring it works closely with its partners to continuously improve upon the system’s performance attributes while also delivering the lowest cost of ownership.
To this end, CAN-ENG Furnaces International Ltd has been active in developing its mesh belt systems to help reduce the overall carbon footprint and decarbonising fastener heat treating processes. This has largely been achieved through improved waste heat and atmosphere recuperation; integration of ultra efficient combustion technologies; as well as electrical and alternative fuel heating systems. In addition to improved heating technologies, CAN-ENG also had several systems commissioned recently with its Energy Reduction System (ERS™) – comprising of several new technologies that allow for waste atmosphere gas energy recovery. It has been measured that the ERS™ integration can reduce the systems energy requirements by up to 30%.
Further development in soft handling and part damage avoidance of safety critical fasteners, while also reducing the opportunity for part mixing, continue to be a focus of CAN-ENG. For instance, its mesh belt furnace external loading system provides a significant benefit compared to cast link furnace loading systems. Mesh belt loading systems allow for open line of sight and reduced part drop heights, which prevents the opportunity for parts to wander on the belt as they are loaded. This is in contrast when compared to cast link loading systems, which may use aggressive shaker pans or long vertical drop chutes to load product onto the cast conveyor – resulting in a greater likelihood for product to wander on the belt during loading.
These mesh belt features allow for the processing of fasteners from M3 to M35 diameters, up to 200mm long and at up to 3,300kg/hr capacity. Modern manufacturers of screws, bolts and nuts today find this size range flexibility to be very attractive in a rapidly changing environment.
“We have recognised that these features are garnering the interest of manufacturers worldwide, as we have seen significant development in interest from manufacturers outside of North America, which has been our traditional market,” explains CAN-ENG. “This interest is the driving force in us taking part in the wire® Düsseldorf show. These developments, as well as others, will be presented during the show and will give us the opportunity to share these with our existing and future partners.”
Demand for products and services have been mainly attributed to the developments in the electric vehicle market. “Our continuous focus on technologies of the future has enabled our talented engineers to find new ways of leveraging existing designs to facilitate the thermal needs of the electric vehicle market,” explains CAN-ENG. “This includes bainitic structure heat treatment (Austemper) systems for high-tensile strength fasteners required by electric vehicles, drive motor and module core (electrical steel) annealing, lightweight structural component heat treatment systems and most noticeably electric battery material thermal processing furnaces.”
www.can-eng.com
National Machinery will be participating at the 2024 wire® show with its stand featuring three machine demonstrations – the FXH2 Lightning machine, the DTi model 3105 wire drawer and the SMART NG20 threader.
National Machinery explains that the first machine, the FXH2 Lightning machine, is a double stroke header that is lightning fast, as it can produce up to 400 parts per minute. “As producers look to make more parts regionally through reshoring, this fast and efficient machine helps make that vision a reality,” states the company. “The header is able to produce a TORX® countersunk screw that starts with 5.6mm diameter wire.”
This wire is drawn to size by a DTi model 3105 wire drawer, which will also be on the stand – with a key feature its ability to take up minimal space while providing the perfect final diameter. National Machinery explains that after the headed part has been produced on the FXH2 Lighnting machine, it is sent to a SMART NG20 threader – the final machine demonstration at the wire® show. “The SMART machine then rolls four features in one pass with a ring, thread, groove and point all added,” points out National Machinery. “The SMART threader is servo driven for full torque at any speed and energy savings are possible with efficient use of power by the servo.”
Set-up is also easy with the auto set-up feature and die match adjustment is now available as automated, which National Machinery points out can create huge savings for production efficiency and operator set-up.
“Check out our stand to also see customer support upgrades and learn how National can make sure your existing machines keep running with great uptime.”
During the show, National Machinery will also celebrate 150 years of business and is keen for customers to mark their calendars and keep an eye out for details of the Open House that is planned to take place the week of 16 th September at the headquarters in Tiffin, OH, USA.
www.nationalmachinery.com
Established in 1996, Doss Visual Solution Srl specialises in the research, design and production of machinery for the visual and dimensional quality control of various components –becoming the ‘go to’ partner for optical inspection systems in all industrial sectors.
Since the beginning, Doss has focused on cutting-edge technology, innovation, and professionalism, as its core values. It is within these values that it continues to invest – in order to shape the future, one that is increasingly being characterised by collaboration with clients, whom the company views as strategic partners in the design and development of high performance solutions.
“With our internal technical and feasibility office; proven and modular solutions; as well as 360° approach to maintenance (from planned routine maintenance to remote assistance worldwide); we are able to ensure a complete and satisfied experience to our customers,” states Doss.
wire® Düsseldorf will be an opportunity for the company to present its vision and strategy for the fasteners market – made up of automation, Artificial Intelligence algorithms, machine integration, as well as development of sophisticated control functions.
A key focus at the show will be the DS PRO, the latest generation automatic visual inspection system that takes advantage of multi-shot technology to identify defects. An automatic single table inspection machine, the DS PRO is the pioneer of Doss’ new generation of artificial vision systems.
Hall 16 / G62
“Thanks to the use of special anti-reflective technical glass, the quality of images captured by the cameras above and below is the same. The fully automatic lens changing system also provides the benefits of fixed-field optics and the flexibility of multiple framed fields,” points out Doss. “The automatic lifting system that all stations are equipped with also allows for quick cleaning or replacement of the table. A webcam is also available to assist with remote support.”
With DS MIND, Doss also welcomes the use of Artificial Intelligence in the world of automated visual inspection and opens the door to a series of new opportunities that the company believes will revolutionise production processes – such as the ease of use, documents from the control panel, ticketing directly into the machine, remote management, multi-level management, as well as total traceability of performed activities.
“We believe that collaborating with partners in the technology and IT sectors is essential for developing cutting-edge solutions that are capable of overcoming the ever evolving challenges the market is subject to,” concludes Doss. “This is why we choose International Hi-Tech Consulting Srl as our main partner in order to provide fastener customers with even more innovative solutions to enhance their operation.”
www.doss.it
Videx Machine Engineering has been manufacturing machinery for U bolts, anchor bolts and eye bolts since 1973. The machines work from wire coil and perform all operations fully automatically.
Today’s market demands are small production batches, requiring short changeover times and operator friendly tooling. With that in mind, Videx has recently added the new line of VAS-DBQ machines that mean customers will no longer have to make bending dies for each part. The new machines are supplied with a floating bending die that covers the entire range of round and square bottom U bolts, enabling customers to make new sizes of U bolts in minutes.
The VAS-DBQ models are equipped with a positive stripper system for the bending station, allowing the operators to run the machines at the fastest possible speed without risking parts jamming. The new Videx operator consoles also now include many of the instructions and messages that were previously included in the operator’s manual. Plus, the new computerised system makes the machine operation easier, intuitive and more operator friendly, enabling easily translation and altering of text to everyone’s language.
All new 2024 Videx models will be serviced by remote through a laptop that Videx will supply. The laptop includes all the software and drivers of the machine, including a remote access program that will be used by Videx engineers to service the machines.
The modular design of the machines enables Videx to add cold forming operations, such as heading and extrusion, as well as material removing operations, including chamfer cutting (pointing), chamfer rolling, form rolling, knurling, extrusion of the ends prior to thread rolling, collaring, heading, grooving, drilling, bending and flattening.
www.videx-machine.com
Founded in 1979, Tecno Impianti Srl is celebrating 45 years as one of the leading European suppliers of wire drawing machines, and uncoilers/pre-feeders, for the fastener industry.
Tecno Impianti’s main machine range is its in-line wire drawers, which can be installed before cold headers, as well as chain, straightening and cutting machines for resizing the wire to a desired final diameter.
Over the last 45 years Tecno Impianti states it has manufactured and sold over 2,500 inline wire drawers, with wire diameters ranging from 1mm up to 37mm.
The Italian company has also created a wide range of products for the fastener sector, including vertical uncoilers that can be supplied with or without motor, for uncoiling
spools or wire carriers; power driven horizontal uncoilers that can be utilised for uncoiling medium-big diameter wires and feed them directly into a cold header or wire drawer, in a pre-straightened form; as well as pre-feeders that are needed for bringing the wire from vertical uncoilers to cold headers or wire drawers.
Other products available from Tecno Impianti include coil-to-coil wire drawing bull-blocks, which can be used for big productions of drawn wire and are supplied in different sizes and configurations –horizontal and vertical. With these machines the drawn wire can be taken up on wire carriers or under the form of bound coils.
Tecno Impianti can also supply wire pointing machines, which are needed for making the point to the wire head before the drawing operation. These machines are available with two or four rolling cylinders and can be installed on fixed base or on carriage. Plus, it can offer hydraulic push-pointers, which can be used instead of a rolling type unit to execute the wire pointing operation on big diameter wires – providing a safe and quick alternative that can be installed ahead of in-line wire drawers or wire drawing bull-blocks.
Tecno Impianti Srl also supplies machines to customers working in other sectors of the wire industry, such as wire drawing machines for production of CO 2 wire and redrawing of galvanised wire; cold rolling lines for production of smooth or ribbed wire for electro-welded mesh coilers; as well as vertical and horizontal spoolers.
“At the wire® Düsseldorf 2024 show, we will exhibit the power driven uncoiler model AP40 for maximum diameter 40mm, in-line wire drawer model SKP16 for maximum diameter 16mm – complete with Industry 4.0 features – and wire pointing machine model AT16-B for maximum diameter 16mm,” reports Roberto Gnecchi, owner and CEO at Tecno Impianti. “The entire Tecno Impianti staff will be pleased to welcome visitors to our stand, in hall 16, stand G43, to show and explain our new technology for the fastener industry.”
www.tecnoimpianti-italy.com
At wire® Düsseldorf, WAFIOS Umformtechnik will be showing for the first time the new HC 6-80A rotor press with a direct connection to an EWMenn AF 61 thread rolling machine – using the patented PTS (Pneumatic Transport System).
WAFIOS Umformtechnik explains that forming machines with an integrated thread rolling unit, also known as combination machines, have recently made a comeback. However, the advantage of this type of machine, which allows production from the wire to the finished screw, with a small footprint, unfortunately also has considerable disadvantages. First and foremost, low flexibility, especially when changing over to a different range of parts at short notice.
This gave the experts at WAFIOS Umformtechnik the idea of linking the newly developed HC 6-80A to an AF 61 thread rolling machine using the patented PTS, which was presented for the first time at the wire® 2022 show and is the central connection between the two machines – making the linking compact and flexible.
During production, the blanks pressed on the rotor press are removed directly from the die and transported via a pipe system out of the press to the desired location. In this case, directly into the feed rail of the roller.
Manufacturers of cold formed parts who have converted to the new PTS report several
advantages, including the prevention of parts being mixed after changeover to another part type; as well as the avoidance of oil carry over – with the parts coming out of the machine almost ‘oil free’, which often eliminates the need for an additional parts washing operation. This is what makes direct connection to the rolling machine possible in the first place.
In addition, energy is saved for the conveyor belts, demagnetisers, and centrifuges, that are no longer required. One user was also able to reduce the amount of oil to be disposed of by up to 85%, thereby extending maintenance intervals. Compared to a normal ejection chute with a blast air nozzle, the same user was able to reduce compressed air consumption by over 30%. The PTS also helps fastener manufacturers to make significant progress in the increasingly important area of sustainability.
WAFIOS Umformtechnik also underlines that the new HC 6-80A itself is a further development of its proven rotor technology and also has a number of innovations included, such as the maximum length for screw blanks and other cold formed parts being increased for the first time to a previously not possible 80mm. Plus, there is a completely redesigned drive with clutch/ brake combination. “In concrete terms, this means that the user has much more direct power during jogging operation because the clutch only engages when the engine is revving up and the machine has reached sufficient flywheel mass,” explains WAFIOS Umformtechnik. “For the first time one of our machines has also been equipped with the iQ Energy Monitoring function, which enables precise media consumption measurement and thus makes a further contribution to saving energy.”
The major advantage of WAFIOS Umformtechnik rotor technology, which has been tried and tested for decades, is its high-speed, which is unique in the double blow world. The company underlines that the newly developed HC 6-80A is no exception – producing 80mm long parts at speeds of up to 380 pieces per minute. “With this innovative direct connection between cold former, PTS and thread rolling machine, the WAFIOS Group is making its contribution to greater sustainability and competitiveness in the fastener industry,” states WAFIOS Umformtechnik.
www.wafios-umformtechnik.de
The high performance AF 61 thread and profile rolling machine from EWMenn will also be presented on the joint exhibition stand –the machine manufacturer is also part of the WAFIOS Group.
80 mm parts with up to 380 pcs/min.
Linked to the thread roller without conveyor belt: The PTS extracts the parts right into the AF 61 rail
iQ Setup Assist + iQ Energy
Monitoring: smart setting + consumption control
The new HC 6-80A rotor press:
• Up to 80 mm part length with up to 380 pcs/min.
• Modern clutch-brake combination: Full torque in jogging mode.
• Pneumatic parts extraction directly at the rotor via patented PTS: The clean and flexible transport solution without conveyor belts.
We are also showing:
• The completely newly developed HN 4-80 nail machine.
• The new HT 5-40 double-blow press with oscillating tool holder.
• An example of a perfect retrofit with the HC 5-60 rotor press.
WAFIOS Umformtechnik GmbH
Im Rehsiepen 35
42369 Wuppertal, Germany
Fon +49 202 4668-0
sales@wafios-umformtechnik.de www.wafios-umformtechnik.de
Precision Parts Forming Machinery
join the best:
15. - 19. April 2024 in Düsseldorf
Hall 10 / Stand F40
With an aim to design and develop innovative solutions for the 100% inspection and sorting of fasteners and special parts, Dimac has also ensured that its MCV machines are ‘born to last’.
Afundamental aspect of all Dimac’s MCV machines are the robust design for enduring performance. “We’ve engineered our machines by using high-quality materials and a modular, scalable approach to reduce stress on mechanical components,” explains Dimac Srl. “The result is long-term reliability and lower maintenance costs.”
The Italian company has also looked to use advanced technologies to ensure lasting reliability. “We’ve embraced innovation with components such as industrial grade fanless computers, IP54 panels, plus closed-circuit air conditioners,” points out Dimac. “This means that we invest more upfront, but the outcome is superior durability and reliability over time.”
Dimac also ensures that its software platform is continually evolving to ensure stability and error-free operation. Each improvement is closely monitored for continuous and reliable performance.
Beyond meeting requirements, Dimac is also committed to sustainability. “We offer durable products, combating planned obsolescence and contributing to consumer wellbeing,” reports Dimac. “We also allocate significant resources to research, new solutions and
As the countdown to the highly anticipated wire® show in Düsseldorf, Germany, begins, industry leaders are gearing up to showcase their latest advancements and innovations. Among them is Carlo Salvi, a company with a rich history of excellence spanning 85 years.
In 2024 Carlo Salvi not only celebrates its impressive milestone but is also poised to unveil groundbreaking developments alongside its esteemed partner, Hatebur, at the wire® show.
Co-exhibiting with Hatebur, Carlo Salvi will present an array of exciting offerings aimed at revolutionising the wire industry. One of the highlights of the exhibition will be Hatebur Group’s newly renovated virtual showroom, providing attendees with an immersive experience to explore the two companies’ complete product range. This innovative approach underscores Carlo Salvi and Hatebur’s commitment to leveraging technology to enhance customer engagement and satisfaction.
Additionally, attendees will have the chance to witness the unveiling of the CS 663 LF, the latest evolution of Carlo Salvi’s most known CS 663 machine. With its revolutionary linear wire feed system, the CS 663 LF promises improved performance and efficiency – setting a new standard for excellence in wire production. Visitors will have the opportunity to see the machine in action and learn first-hand about the advanced technology behind it.
Complementing Carlo Salvi’s offerings, Hatebur will showcase its automatic servo-transfer unit, a state of the art solution that raises the bar for the entire Hatebur Group. “With its precision engineering and innovative design, the automatic servo-transfer unit represents the pinnacle of reliability and performance in the industry,” states the company.
Throughout the exhibition, Carlo Salvi and Hatebur’s team of expert technicians will also be on hand to provide insights, answer questions, and demonstrate the capabilities of the latest offerings. Their wealth of knowledge and dedication to customer satisfaction ensure that every visitor will receive personalised attention and guidance.
As Hatebur Group looks ahead to the rest of 2024, the company is excited to announce a series of upcoming developments and milestones that promise to further enhance its position as an industry leader. With a legacy built on innovation, quality, and customer satisfaction, the Group remains at the forefront of the wire industry, poised to shape its future for years to come.
“Join us at wire® 2024 as we celebrate 85 years of excellence and innovation at Carlo Salvi. Don’t miss this opportunity to experience the future of wire production first-hand and discover why both Carlo Salvi and Hatebur continue to set the standard for excellence in the industry,” concludes Hatebur Group.
www.carlosalvi.com
San Shing Fastech Corp, a fastener manufacturer with 58 years of experience, has announced the integration of Artificial Intelligence (AI) into its self-developed optical sorting machines.
San Shing has been investing in AI for over two years, and this year, with the maturity of AI technology, the company has started testing AI in practical production. “Under the quality requirement of zero defects per million for automotive fasteners, Automated Optical Inspection (AOI) has become an essential inspection process. Through testing, we have discovered a numbers of positive effects,” explains San Shing.
One of the main positives from AI is the improved convenience and reduced reliance on manual labour. By defining only the defective features, AI can automatically perform the optimal configuration by logging good and defective products into separate folders or selecting the defective features. This eliminates the need for tedious parameter settings and repetitive pre-production tests. It also simplifies the machine configuration process and reduces the operating time for personnel.
Another positive is the enhanced stability in inspections, allowing for slight deformations and contamination of fasteners. “Fastener products are often subject to deformations and may contain oil or dust due to processes like forging. In traditional Designed Rule Check (DRC) methods, there is a risk of false rejections leading to waste when inspecting fastener images. However, AI has demonstrated the ability to identify the features of good and defective products, making it more suitable for inspecting fasteners with slight variations in appearance and optical environments affected by oil contamination.”
Currently, the final testing of AI is underway at San Shing’s sorting facility. In addition to the sorting machines, San Shing has also updated its in-house nut former, and tapping machine, to meet Industry 4.0 and the latest CE safety requirements.
www.sanshing.com.tw
US-based RMG (formerly Rockford Manufacturing Group) has recently made several investments within its business to improve its own production, as well as better serve customers, including new CNC machines, a new machine rebuild programme option for customers, plus a new brand image and website.
RMG designs and builds equipment to uncoil, draw, straighten and cut, coiled wire to a length. Its solutions can be found in countless manufacturing processes that begin with coiled wire – where it provides a critical step in production to ensure wire is ready to be manufactured into a usable component or finished product.
“We have a long history of providing equipment to the automotive, aerospace, concrete/construction, industrial, wire forming, and consumer product industries – where customers benefit greatly from the experience of our sales and engineering professionals,” explains RMG. “Our teams continually work with a sense of urgency to provide comprehensive and unmatched support –from equipment design, to delivery, to genuine replacement parts and service. Companies that demand durable, high performance wire processing equipment rely on us to deliver on that promise worldwide – not only with quality products and outstanding customer support, but with competitive prices and lead times.”
Hall 16 / J48
In order to continue to provide a first class service to its customers, RMG has also made several investments, including a rebranding process that produced a new look; a new website that incorporates this new look and makes it easier for customers to find RMG and its products; plus the company has updated and renovated
its plant to improve efficiencies and throughput, as well as adding new horizontal CNC machines to improve production.
“At RMG we look to put our customers first by providing programmes and solutions that enable them to further improve the production processes and capabilities,” underlines RMG. “This includes things such as a new machine rebuild programme, as well as technical advances such as Industry 4.0 – giving customers innovative solutions that reduce downtime and the ability to be more efficient. We also offer services, such as machine financing, which gives our customers the ability to get the equipment they need.”
At wire® Düsseldorf RMG will have two of its most popular machines on display, the model 500 spacesaver wire drawer –capable of drawing up to 8mm – and the model 89 wire drawer – for up to 13mm diameter material. “Both machines will display the latest technical advances, such as our Industry 4.0 technology for data collection and maintenance scheduling. Plus, our new Quick Change wire relaxer assemblies will be on display, which reduce set-up time and enable operators to safely change wire relaxer rolls with no special tools required.”
www.rmgwire.com
From straighten and cut to wire drawers to pay-offs and all points in-between, RMG machines are preparing coiled wire for countless manufacturing processes - with less scrap, quicker changeovers, Industry 4.0, and expert support every step of the way.
RMG also produces over 90% of its manufactured components in-house to tightly control the quality of our machines.
Since 1979 Italian-based TLM has been operating on the world market, producing a host of thread rolling machines for the fastener industry – becoming a qualified partner who can offer expertise, technical support, as well as timely responses and providing flexibility to customers.
TLM can offer a wide range of equipment, including machines for threading screws and bolts, machines for chamfering or for screw tips, machines for assembling washers and screws, as well as special machines for making deformations on screws. “We design and produce dedicated machines, in-line with the specifications of customer companies, striving to fulfil all requirements or individual requests,” explains TLM Srl.
TLM’s product portfolio includes a wide range of solutions, including flat die thread rolling machines from micro diameter 1mm up to 30mm, with mechanic introduction system and grinded monoblock head structure, for best precision and stability. The company also offers rotary thread rolling machines (roll and segment) from diameter 4mm up to 20mm; five models of chamfering machines from 3mm up to 22mm; as well as washer assembly stations (single or double) with three sized carousels with a diameter of 150mm, 200mm and 300mm – for micro washers up to 60mm.
To add to this, TLM can also supply combi machines, such as threader and pointer; threader, pointer and washer assembly station; as well as flat die machine and rotary machine for threading of two different diameters in a single line sequence.
Other solutions include bushes assembly stations, loading systems for screws, bolts and washers, stud loading and orientating systems,
overhaul of flat die machines and rotary machines, as well as, finally, applications of automations designed for the customers.
www.tlmweb.it
The terms heading and forging relating to the manufacture of fasteners seem such humble subjects and yet, what appears as obvious and self-evident – as something practised by ‘smiths’ for millennia – can also hold secrets that can easily be overlooked. It is these underlying aspects of heading and forging that this article seeks to address.
As everyone knows, forging changes the shape of a workpiece. Heading is simply one specific application of forging. But, what to forge?
Nodules of gold – a malleable shiny pebble to early humans – or iron rich meteorites. Being found on the ground, these were probably the first materials to be worked by forging between two hard stone surfaces. Chemistry kicked in when fire produced metallic elements, which were discovered accidentally from smelted ore. It is from such serendipitous beginnings that the world we inhabit was built.
Industrialisation created a demand for ‘things’ and once a competitive process was developed, any number of the same ‘things’
could be produced. In the case of metals, flat strip/plate was rolled, as were lengths of material having the same cross section –round, square, ‘T’, ‘H’, ‘I’, etc. Such products were desirable and necessary for building ships, railways, electrical wiring and cables, etc. However, they required further processing to be made into the multi-functional metal components found in every aspect of commercial, business and public life.
The reason, because most single item metal objects have non-constant cross sections. Changing constant cross sections produced by primary processing (rolling) introduced a requirement for secondary and tertiary processing methods for example, forging using machines. Where, for centuries,
‘smiths’ used their own strength to achieve shape change, industrialisation gave rise to the machine that naturally increased the forces that could be applied.
Until the introduction of electronics, and the subsequent development of digitisation, all powerful human groupings relied for their weapons of war/defence on the ability to ‘forge’ metals. Swords and spears gave way to big guns and battleships. Throughout centuries, those having the skills and abilities (the metalworkers) to provide the people in power with the reason for their power, ensured that they always dined at the top table. Somewhat surprisingly, global political issues have shown that non-electronic weapons, and the means for their mass production, are still required today.
Three basic ‘machine’ forging methods are used: Open and closed die (both hot) and cold (which is almost always closed die).
Hot forging is carried out to reduce the forging force required. By raising the temperature of a workpiece (particularly a complex alloy) it is possible to change its crystal structure so that it is easier to deform. The forming force and workpiece deformation generates internal friction within the workpiece. In complex alloys, it is necessary to ensure that the heat transfer from the workpiece to the tools is balanced by the energy from the forging operation, which is entering the workpiece. Cooling or overheating of the work during forging can lead to defects. For some hot forgings, the cooling rate also determines the final grain structure of the
to use a multi-stage forging operation.
This is because unlike a casting process where the workpiece material is fluid and can flow into a mould, direct stresses on the die walls – produced with a solid workpiece –restrict material flow. This can be overcome using a series of intermediate blows or tooling stations, which in effect, incrementally rather than continuously change the workpiece shape.
Because the process is ‘hot’, the final ‘as forged’ shape will be larger than the functional accuracy needed for assembly. This is subsequently achieved by final machining.
Cold forging takes place ‘below’ the temperature at which the workpiece crystal structure changes. For this reason, the workpiece material is generally required to be available in its most ductile (soft) state. Materials that have ‘free machining’ properties should not be used for cold forging since these are designed to produce the characteristics of brittle fracture needed for creating small chips. Some ductile materials can be ‘warm’ forged, which also reduces the forging force but does not change the crystal structure.
In all metalforming operations, the workpiece strain produced by changing its shape will introduce strain hardening. In hot working operations, and at normal forming speeds, the effects of strain hardening are removed by the elevated temperature. Too high a forming speed and temperature can produce cracking at shear boundaries inside the material – a defect known as ‘hot shortness’.
In cold/warm working, the effect of strain hardening increases the properties (strength)
Where products having complex geometries are required, it is often necessary to use a multi-stage forging operation.”
of the formed (as forged) material. The degree to which a workpiece can be formed is determined by the difference between the strain at which the material yields and that at which it fails. The stress/strain behaviour of common window or bottle glass at failure would show little evidence of permanent strain (ductility). This behaviour would be similar to a grey cast iron – and for that matter an elastic band! Whereas, a nylon rod subjected to a large tensile strain would go on and on extending without catastrophic failure.
So, whilst the material a workpiece is made from must naturally fulfil its specified design criteria, its selection, depending on the manufacturing process used to make a component, is of equal importance. Machinability is enhanced using ‘free cutting materials’ (small chips make for easier swarf removal) but it cannot improve the material
© SACMA Group
properties. The yield (percentage of material in the final product relative to that used in its manufacture) is basically a measure of waste –on aerospace parts, and due to large-scale machining, the yield can be as low as 5%.
Hot forging naturally requires energy to heat a workpiece to affect the necessary microstructural transition prior to it being worked. Although it is not possible to improve the material properties through strain hardening, it is possible to obtain a modification in the structure through preferential material flow and controlled cooling. The high temperature can have an effect on the material ‘yield’ depending on the atmosphere control and accuracy of the process.
Cold forging – as in fastener production –can produce very high ‘yields’ of the material employed. The forming processes can also improve the material properties through cold working (thread rolling provides a major benefit over machining).
As always, the variables involved in cost-effective manufacture are determined by the number of parts required. Small batches are conditional on available stock, equipment, set-up times, etc; as in direct costs. Indirect costs, although important, tend to be considered as overheads.
Medium size batches, whilst fewer in number, offer manufacturers an option of grouping families of products into those requiring similar manufacturing options. Having a more consistent throughput allows greater investment possibilities for the achievement of cost-effective production efficiencies.
Guaranteed large-scale production makes it possible to invest in dedicated facilities and with the correct set-up, the most cost-effective methods of mass production available.
Since most screw type fasteners have heads, this operation has been selected to illustrate some aspects of the foregoing. Heads can be virtually any shape – spherical, as in ball joints, or wedges – as well as have axial symmetry or off-set geometries. For the sake of simplicity, the example chosen here will be a conventional symmetric/concentric hexagonal form. This can be hot, open die forged between flat parallel dies and then trimmed in a die or by machining. The thickness and diameter of the head will be determined by the volume of the upstand of the workpiece (usually cut from rod) above the lower die. The aspect ratio of upstanding height relative to the workpiece diameter (H/D) is limited by the ‘buckling’ ratio. As the bulk of the workpiece is captured in one of the tools, this ratio can be increased if the opposing tool is shaped to prevent the work from sliding off its axis under compression. However, even if both ends of the upstanding workpiece are captured, the ‘slenderness’ ratio predicted by the Euler Critical Buckling Load will still pertain.
Assuming that’ buckling’ is not an issue, deformation of the upstand will take place by the centre core of the material being forced radially out from the axis. As the tools close, the captured part experiences no flow – whilst the outer surface of material above is caused to move outward and downward to be squeezed pancake fashion on the tool surface. At the free end where the material may not be captured, the frictional conditions existing between the work and tool will determine the shape of the deformation. Low friction will allow radial flow. ‘Stiction’ (total friction) will cause the material to behave in the same way as that at the captured end. Since all deformation occurs by shear, it is the movement of internal elements of material along shear boundaries that generates friction and shape change. Introduce boundaries – as in die walls –and the increase in external friction will naturally impact on the flow characteristics within the deforming material. It is for this reason that preforming (multi-stage tooling) is of such importance in obtaining a product that has complex geometry.
Hot closed die forging of a hexagonal head generally requires a two-stage operation. The first would be preforming the head of a circular rod in a conic tool. Shaped like a truncated wizard’s hat, this distributes the material to create the base pancake shape first. A second operation with the conic head inside a hexagonally shaped tool can then be used to complete the forming operation.
Cold forging is carried out in a similar manner but usually on smaller components produced from coiled wire. This is drawn, to ‘size’ the diameter, and then sheared to length. Depending on the type of machine used and the component being formed, the heading operation can be carried out in much the same manner as described above.
As in hot forging, given suitable workpiece material and equipment, the range and complexity of the component geometries that can be forged is determined by the skill and metal former’s imagination. This capability is significantly enhanced at the product design stage by the use of numerical simulation software. It should always be recognised that having design control provides significantly greater opportunities for cost savings in manufacture than is the case when a product is already defined.
A first class example of the opportunities to be gained when ‘free thinking’, was presented in Stuttgart at the New Developments in Forging Technology by H. Gensert of SIEBER Forming Solutions in 2009 [1]. In his paper, Gensert proposed using three piece segmented tooling to laterally
For those clever enough to identify the need for special products, techniques like these represent pure gold.”
form solid or hollow fully finished components cold, on a conventional press as outlined in Figure One. His ideas involved using billets with preformed shapes to allow for the flow of excess material to ensure it did not interfere with the closure of the tooling segments. The shapes produced included conventional threads (without the misshaped crest often found on rolled threads); non continuous threads of virtually any shape – either with longitudinal and or radial discontinuities; also, constantly or variably changing geometries as in the polygonal shape of self-tapping screws. For those clever enough to identify the need for special products, techniques like these represent pure gold.
Press action
a) Direct action of segmented tools on solid or hollow workpiece
b) Indirect action where the axial force of the press creates lateral movement of the forming tools
Figure One: Illustration of press and tool action in lateral forming (after Gensert)[1]
Today, the term ‘tech’ is assumed to be everything IT generated. It is worth noting that the future of future generations will be determined by how they manage the ‘finite’ resources of the planet and the technologies that use them. Goods made from a single source material offer ease of recycling but rarely display the properties required to be fully functional. Coating with diamond for enhanced cutting; gold for electrical conductivity or display; as well as plastic, paint or preservatives for protection; are all necessary but create problems with recycling. Where multi-functional materials are required for specific applications, these could be best applied (where possible) by use of easy to assemble and disassemble products. As always, such things are made possible by the use of fasteners and if adopted for the future – future fasteners.
All technology requires a ‘window of opportunity’ in order for it to succeed. Given the global driving force to combat the effects of climate change, the type of technology suggested in Gensert’s paper 1, and others like it, could become a significant element in terms of forging a future.
References
[1] H. Gensert, SIEBER Forming Solutions, Formed Threads, International Conference on ‘New Developments in Forging Technology’, Stuttgart, Germany, May 2009, pp 135 – 141. (Edited M. Liewald, IFU, University of Stuttgart). ISBN 978-3-88355-375-7.
Today the variety and the quantity of metal fasteners produced by cold forming of wire rod is impressive. Almost all screws, bolts, and nuts, are made with that technology, but it’s not just these products. The name of the process evokes itself with the capacity to form a lot of special parts, solid or hollow, with a complex shape, to be used in the most important industry fields, automotive first.
Cold forming is not the simple heading of its debut in the early 1950s, it now involves more sophisticated multiple die presses, dedicated materials, accurate tooling, and it has become possible to produce parts that only a few decades ago no one could imagine obtaining from wire.
If we add the advantages coming from a high productivity, optimal use of raw material, as well as consistency of precision, the success and the spread of this technology appears logical and motivated.
There is another important point in favour, especially these days, and that is the topic of sustainability – with cold forming only requiring a modest energy intake and having a minimal scrap rate. At SACMA, we are always working to build, in a sustainable way, sustainable machines for the most sustainable technology. To do that, we chose solutions requiring low energy consumption; we increase our own production of renewable energy; and we select our supply chain accordingly.
The core activity of SACMA Group is to design and build machinery for the cold forming process – a complete line of presses and rollers to fulfil the needs of the modern industry, including ancillary equipment and machines for secondary operations.
Our mission is to offer to the producers of cold formed parts the best possible equipment with effective solutions, keeping at the same time the well known robustness and reliability of SACMA machines.
Looking to the most innovative solutions recently introduced, I would like to start with the mechatronics application. In our machines there are more and more functions activated by servomotors: Wire feeder, stock gauge, die kick out, transfer, starter, etc. The purpose is to make the set-up of the machines easier, intuitive, and quicker, with more safety for the operator – because reducing their manual interventions allows us to activate and control the operations directly by HMI. We started to introduce those
Hall 16 / D44
presses, where the advantage for the operators is more consistent, and gradually we are also implementing in the small machines.
Ever focusing on the user’s needs, and the work environment, we have also redesigned the machine cabins, integrating inside them all the items, such as the main motor and the lubrication unit, which were previously external. The result of this activity is a more compact machine, less floor consuming and emitting a lower noise level. Also, any oil dropping is eliminated, helping to keep the work room clean and healthy. We have also improved the ergonomics with more comfortable doors and internal spaces for the interventions. The action plan is already in progress, with the target to fit all the machine models within the next year.
Coming now to functions more connected with cold forming, SACMA continues to develop and propose solutions with a scope to enlarge the potential of this technology. It’s known that complicated parts, made with alloyed steels, cannot be formed in one shot, even through more forming stations. The material, stressed by a too high deformation rate, starts to crack. To avoid that, you must proceed with an intermediate heat treatment to regenerate the metallographic structure. The production process then becomes articulated and involves more machines.
That is why SACMA has introduced re-feeding equipment, allowing the operator to apply the two steps process in the same machine, at the same time. Another solution for extended deformation sequences is the device for feeding pre-formed parts in the cut off station. By having a 6 die press, it should be possible to execute a deformation in 12 steps, with an annealing/coating operation in between, all done starting from a standard machine.
To extend the borders of cold forming, SACMA is constantly involved in improving its own warm forming (WF) machines. This warm forming technology is very near to cold forming – the same base machines and same concept of tools – it is only the special equipment for making them suitable to work at temperature and helping enlarge the deformability of difficult materials, such as stainless steels, titanium alloys and nickel superalloys that is different.
SACMA recently presented a complete line of WF part formers, split into different models according to the operating temperature – WF300, WF500, and WF900 – which can work respectively up to 300°C, up to 500°C and up to 900°C, based on the parts and the materials to be produced. The program predicts all the machines sizes and, thanks to the SACMA Modular Design Concept, all the machine models could be involved. Also, Ingramatic offers a complete line of WF rollers, for instance for threading aerospace fasteners.
We love to build top class machines and we like to see the satisfaction of our customers.”
An interesting function that can be integrated in all our machines is the thermoregulation of the die box and the cooling oil tank. When the tolerances of the part become tight, a stable temperature of tools and coolant is the priority. The TR unit is positioned nearby the machine, to heat up the die box and the oil at machine start. Afterwards, during the production, it cools down, keeping them inside the desired range of temperature. Thermoregulation means precision and consistent reduction of NC parts. That function can be implemented in the WF machines, and it is effective for the cold formers too.
The combined machines have been a key product for SACMA since the first one, an SP27 that is still active at an Italian customer, left the Limbiate factory in 1974. The machines are an ‘all in one’ production centre that includes forming, pointing and thread rolling. At SACMA we ensure they have a compact layout, feature quick ‘plug in’ and include high efficiency and energy recovering. These are some of the most effective and sustainable solutions to produce threaded fasteners and are suitable for products in the range from M3 to M24. We are also constantly innovating and improving them through our engineers –focusing on ease of use, quick tool changeover and energy consumption.
For instance, already within the SACMA portfolio we have the SP59, in two versions – normal and short stroke. This is a 6 die combined press, extending the range of products to the more complicated special parts. We are also planning on introducing the SP39 and after that the SP29. Considering the WF equipment available, the flexibility in terms of feasible products from SACMA is without comparison.
Also on the subject of combined machines, SACMA is proposing the new KSP12, a fully redesigned successor of the iconic KSP11 – a one die two blow header with thread rolling, suitable for production of screws, self-tapping and metric, from diameter 3mm to 8mm. The machine was enthusiastically accepted by our loyal existing customers and by new customers too. The world preview occurred during the last wire® Düsseldorf shows, and the next step is to present a new version for ultrashort and small head screws.
Being aware that the best machines for high performance also need the best tools, SACMA has recently introduced for its customers the S-Tooling division. For this, in a structural way, we have created a department, where skilled and experienced engineers develop and design the tools for new complex parts requested by the market. They are supported by the most up to date and innovative instruments for the FEM simulation, to issue the perfect deformation sequence and the construction drawings of each tool. The successful feedback we are receiving from our customers is encouraging us to increase the capacity of this department with new hardware and resources.
Another theme dear to us is the service after market, including technical assistance and spare parts, which help keep the machines always in the best condition. Our products are designed and built to be durable and our customers are expecting a long productive life. The availability of spares, even for machines born 40 years ago and more, is crucial. That is why we are prepared with a large inventory in our warehouse of parts, ready to be delivered – minimsing machine downtimes. All our branches and agencies, beyond the commercial activity, can give technical assistance. In the Limbiate headquarters we are also boosting up the service with young resources and new structures.
To fulfil the requirements of Industry 4.0, SACMA can also offer different packages to implement the machine data, at increasing levels, inside the network of the customer. Moreover, we have started to investigate Artificial Intelligence (AI) fields – how to obtain additional information and how to make quick and useful instructions for the operators when it comes to set-up and ordinary maintenance.
85 years on from its foundation and SACMA Group still strives, day-by-day, to improve with its own innovative products, not only the SACMA presses but also the Ingramatic rollers, as well as the feeding and unloading equipment of Tecno Lift and the tapping and turning machines of HS ASPE. We are always looking to offer our customers from the fasteners and cold forming industry a wider range of machines and services, making them more successful in the global market. Of course, we do that because it’s our business, but especially because of the passion pushing us. We love to build top class machines and we like to see the satisfaction of our customers.
With the growing interest in reshoring and making components locally, both in Europe and across the world, as well as the growing importance of sustainability within the cold forming process, National Machinery states its machine portfolio can meet the needs of customers.
Amongst the solutions from National Machinery is the FXH Lightning, a double stroke single die header that is available in two sizes, which provides more uptime, fast changeovers and effective ergonomics. “Customers get more uptime from National dependability, quick tool changing, easy adjustments and simple maintenance,” mentions National Machinery. “The FXH also includes a unique slide guiding system, precise linear feed, fine adjustment of kick and feed – while running along with rigid punch rocker locking – to produce consistent quality parts.”
National Machinery points out that the precision linear feed system is so accurate that there is no need for a stock gauge. Plus, there are no parts to change for most wire sizes and feed length adjustment only takes seconds with the automated adjustment. It also eliminates over feeding and feed roll slipping that can damage the wire.
Other features include the motorised adjustment of feed and kick allowing the operator to perform other tasks while the machine is adjusting. In addition, the mechanism adjusts to preset values and fine adjustments can be made while running. To add to this, the die block cap clamps just the die, not the quill, and removes quickly for die change;
there is no wedge to affect the close tolerance slide guiding system; and the quick clamp quill position is repeatable requiring no in-machine alignment.
In addition, the transfer can be pre-set on a fixture outside the machine and the transfer bar is adjustable to the transfer fixture for quick and repeatable changeover. Both punches also mount on the oscillating punch rocker, and mechanical locking and precise slide alignment during both forming blows results in exceptional concentricity and tool life. Finally, the thick wall punch holders extend punch holder life.
Hall 16 / A44
“Localisation is a great way to support sustainability to minimise logistics and inventory,” explains National Machinery. “The small footprint of the machine, in combination with the production speeds of up to 470 parts per minute, make for an efficient use of space and the ‘lightning fast’ speed of the header can make it a key factor in localisation for lots of customers.”
www.nationalmachinery.com
Founded in 1989, RLS Tooling has become a leading rolling die manufacturer with a reputation for supplying competitively priced quality tooling, delivering on time to a global market, thanks to its ability to constantly update its machines, processes, systems, training, as well as listening to customers’ needs.
RLS makes a full range of flat dies for standard, special and licenced thread forms and holds a range of flat thread rolling dies in stock, with Metric threads, help customers receive a faster delivery. The company also manufactures a range of circular thread rolls for the most common two roll machines – up to a maximum of 315mm diameter – and can manufacture rolls for the Fette three roll system, as well as bespoke dies to customers’ sample fasteners or drawings.
“We can also help customers who are looking for a return on their investment in tooling, by regrinding flat and cylindrical tooling purchased from ourselves or others,” mentions RLS Tooling Ltd. “The possibility to regrind redundant thread rolling tools by replacing the original thread profile with a new one – to be able to roll other parts – is a win-win situation. Its costs are effective and also good for the environment.”
RLS also holds licences to manufacture the full range of Taptite® and Remform® thread forming screw dies. These are popular with big assembly lines due to the cost savings made by not having to tap the thread before assembly. The company also holds a licence to manufacture dies for MAThread® screws, which are used widely for automatic assembly lines due to their high resistance to cross threading.
“We also manufacture Excalibur Screwbolt® dies that are used for special bolts to be driven into concrete without the need for using plugs,” points out RLS. “We can use a range of materials such as D2, HSS, and powder metallurgy type, depending on applications, all of which can be coated for increased tool life. We would recommend using our HP1 for rolling the tougher stainless steels and our HP2 for rolling 12.9 grade. We are a customer focused supplier that believes in forging long-term relationships with our customers that is beneficial to both parties.”
www.rlstooling.co.uk
The new TECH 1 application machine from Tecnologic 3® is the perfect companion to apply each type of solvent or water-based products for fasteners – granting outstanding performances with an average production of 20,000 standard screws per hour.
Based in Gorgonzola (Mi), Italy, Tecnologic 3® is a key player within the manufacturing and applying of adhesive products and sealants – using systems, processes and technology designed internally and patented all over the world. The new TECH 1 application machine is a full system enabling an improved application – helping to reduce the impact on the environment whilst getting the best performance in terms of efficiency and productivity.
The new TECH 1 application machine, which includes a new process that is fully patented, also underlines Tecnologic 3® ’s innovative capabilities, with it including a host of new features – such as a new PLC able to manage all operations with maximum speed; a new high performance Pro camera to check online quality; a new automatic reject system; display units for integrated operation; the ability to program directly on the device; a huge display and editing of message text/variables on the device; as well as what Tecnologic 3® says is a game changing application system for groundbreaking performances.
Technical assistance and dedicated service will also guide Tecnologic 3® customers into all the initial phases of the project, until the production start-up.
“The new TECH 1 machine embodies perfectly how tradition becomes innovation,” states Tecnologic 3®. “Continous creative and technological research has allowed us to once again launch an exciting new Italian innovation onto the national and international markets.”
The innovative spirit at Tecnologic 3® is further underlined with the recent launch of two new products to complete the range and offer its customers the best in terms of performance and quality.
Firstly the company has introduced Tecnologic 16, which it states is the most effective and innovative cold applied coating process developed to prevent adhesion of weld splashes and accumulation of paint. It can be applied on both soft and hard metals, as well as plastics – providing the integrity of a top coat and physical properties of material.
The second innovation is Tecnologic 40, a hybrid self-locking and sealant agent based on water and technologically advanced resins. It can be applied on soft and hard metal and helps prevent surface damages.It also prevents loosening through vibration and provides a slight sealing capability through mechanical braking. Finally, it is distributed over threads – eliminating the engagement gap and exerting long-lasting resistance to loosening and vibrations.
“Like all our products, both Tecnologic 16 and Tecnologic 40 are waterbased, helping to reduce the environmental impact,” reports Tecnologic 3® “Our range of machines, products, and application process, are like a perfect circle to help and support worldwide fastener companies and applicators in supporting their clients with the best reactive and non-reactive coatings the industry can offer, with full respect of the environment.”
www.tecnologic3.it
Mechanical testing plays a major role in research, product design and quality control. Tests can be conducted using a wide range of static and dynamic materials testing machines, which engineers frequently use during product development. Mechanical testing incorporates a wide range of techniques, from common tensile and compression tests, to flexural, or torsional, characterisation. Testing may also occur under ambient, or non-ambient conditions, with widely varied temperatures and environmental conditions.
Tensile testing is a destructive test process that provides information about the tensile strength, yield strength and ductility of a material. It measures the force required to break a test specimen and the extent to which the specimen stretches, or elongates, to that breaking point. Universal materials testing machines, capable of conducting static, or monotonic, tests in tension, or compression, play a vital role in product development and quality control of materials and components. The ability of such equipment to provide ‘raw data’, which can be used by design engineers, is essential in the development of new products.
The manufacturing sector faces tough global competition and, for this reason, the use of computer-based development methods continues to grow. However, these simulation methods must be accompanied by real mechanical tests in the various development phases, to determine the important material data.
Many materials and components are required to have a defined fatigue strength, which must be verified to ensure fitness for purpose. These fatigue tests can be accommodated in a servo-hydraulic test machine, but are more quickly and economically performed using high-frequency, resonance pulsators. Whichever test method is used, consideration must be given to special gripping arrangements, in order to satisfactorily complete fatigue tests on a wide range of sample types and sizes.
The operating principle of the high-frequency resonance pulsator is based on the concept of a mechanical resonator with electro-magnetic drive. The mean force is applied by moving the upper crosshead with a lead-screw drive. Due to their design, these machines have been used in the past, solely as dynamic materials testing machines, to determine durability with regard to fatigue life and fatigue limit, for example for fatigue testing to DIN 50100 (S-N curve), under tensile, compression, pulsating and alternating loads.
The new generation of machines can be used as both dynamic and fully fledged static materials testing machines, which can accommodate test loads of up to 1,000kN. Typical applications are material fatigue tests and durability tests on standardised specimens and components, e.g piston rods, crankshafts, and fasteners, as well as production and quality control of components exposed to dynamic loads during their anticipated service lives.
Servo-hydraulic testing machines have universal application for materials and component testing under pulsating, or alternating, loads –with constant amplitude, or pseudorandom, signals. Servo-hydraulic
testing machines may be used in static, dynamic or fatigue testing applications. They operate through a closed loop system consisting of a bi-directional hydraulic actuator linked to the test specimen; a servo valve and controller for adjusting actuator position, velocity and force; a load frame with an hydraulic power source; and an electrical feedback loop enabling the test variables to be controlled using position and load transducers. Although they require infrastructure for both electrical and hydraulic connections, servo-hydraulic testing machines can be a cost-effective, static testing choice, at very high forces, or if a high testing speed is required.
Elevated temperature tensile testing is a reliable process used to evaluate the behaviour of metallic materials when subjected to a combination of high temperature and tensile forces. High temperature, tensile testing procedures are performed routinely in many industries for assessing high performance steel, and other metals, that will be exposed to high temperatures while in service. In applications such as engine design, the material behaviour under increased temperatures, up to approximately 1,600°C and higher, is of vital importance.
The Charpy impact test, establishes the relationship of ductile-to-brittle transition in absorbed energy at a series of test temperatures. Since a variety of metals undergo a transition from ductile behaviour at higher temperatures, to brittle behaviour at lower temperatures, the Charpy test is now specified for a range of steel products, including steel hull plates used in shipbuilding, pressure vessels in nuclear plants, and forgings for electric power plant components.
The Charpy test is usually performed using precisely machined specimens, typically measuring 10mm x 10mm x 55mm, with a 2mm deep V-notch in the middle of one of the specimen faces. Specimens are usually tested over a range of sub-ambient and elevated temperatures. Once a specimen reaches the required test temperature, it is quickly located onto a special fixture in the pendulum impact tester, with the notch oriented vertically. Following the release of the test machine pendulum, the specimen is struck by the tup attached to the swinging pendulum of appropriate design and mass. On impact, the specimen breaks at its notched cross-section and the upward, return swing of the pendulum is then used to determine the amount of energy absorbed in the process.
Indentation hardness tests are used in mechanical engineering to determine the hardness of a material to deformation. Several such tests exist, wherein the examined material is indented until an impression is formed; these tests can be performed on a macroscopic, or microscopic, scale. There are three commonly used hardness testing methods: Rockwell, Vickers and Brinell.
The Rockwell scale is a hardness scale based on indentation hardness of a material. The Rockwell test measures the depth of penetration of an
indenter under a large load, compared with the penetration made by a preload. There are different scales, denoted by a single letter, that use different loads, or indenters.
The Vickers hardness test was developed as an alternative to the Brinell method, to measure the hardness of materials. The Vickers test is often easier to use than other hardness testing methods, as the required calculations are independent of the size of the indenter and the indenter can be used for all materials, irrespective of hardness. The Vickers test has one of the widest scales among hardness tests and the unit of hardness given by the test is known as the Vickers Pyramid Number.
The Brinell hardness test method is used to determine Brinell hardness. Most commonly, it is used to test materials that have a structure that is too coarse, or that have a surface that is too rough, to be tested using another test method, e.g. castings and forgings. Brinell testing often uses a very high-test load, (3,000kgf), and a 10mm diameter indenter, so that the resulting indentation averages out most surface and sub-surface inconsistencies.
Today’s state of the art hardness testing machines can be used in the widest range of applications. They use innovative mechatronic technology for high-precision testing, particularly for quality assurance, production line testing and in the laboratory.
Mechanical testing helps verify that the product meets the stipulated industry standards and regulations, ensuring its quality and reliability. It helps optimise the material selection process by identifying the most suitable material for a particular application, based on its mechanical properties.
Kistler Group has introduced a new cerTEST inspection system for standards compliant torque tool testing, effectively a fastening simulator that collects exact and highly reproducible data.
Kistler’s new way of fast, precise and standards compliant fastening simulation, analyses the capabilities of torque tools with up to four integrated simulators, and over a 0.2Nm to 500Nm torque range. The system is designed for mobile testing in shift operation and is equipped with a built-in rechargeable battery with a run time of up to 16 hours. The corresponding user-friendly CEUS software solution guides users through the test, while also taking care of documentation.
Whether for the automotive industry, aviation or robotics, bolted joints have to withstand high forces and adverse conditions. This is why quality assurance of fastening processes starts with the tools used. Torque tools, such as cordless, rotary and impulse nut runners, are subject to internationally recognised standards, such as VDI/VDE 2645 Sheet 2, VDI/ VDE 2647, and/or DIN EN ISO 5393. To comply with these norms, users must verify their machines’ capability through regular tests.
That’s where the new cerTEST inspection system comes in, enabling users to check their tools safely and in compliance with given standards. The long-lasting, rechargeable battery enables certification directly on the assembly line. The system, with four slots for customisable fastening simulators, can have additional fastening simulators connected externally, if required, enabling tests of up to 6,000Nm to be conducted.
This allows for quick and efficient machine capability tests of electric, pneumatic and hydraulic tools, as well as impulse nut runners. It also means torque tools can be removed from the production environment and inspected without any special preparation. The tools are simply adapted to the corresponding fastening simulator for inspection, with the software selecting the appropriate simulator, depending on the torque parameters.
measures the torque and the angle of rotation of the tool; the simulator can also collect data on the speed achieved during inspection. A colour-coded evaluation of the tested object is available via the software, and on the simulator, immediately after the test procedure. As alluded to at the start, the whole inspection set-up, and the high resolution measurement electronics, ensure minimal measurement uncertainties and optimised reproducibility of all measured values.
As for the collected data, this is displayed directly on the wide screen of the cerTEST device. With the help of Kistler’s CEUS software, users can introduce individual limits, specifications and tolerances into the evaluation, thereby ensuring standards compliant inspection, as well as being able to implement their own stricter specifications.
The web-based CEUS program not only guides users through the measurement, step by step, but also saves different measurement settings. This means that users have to specify the measurement parameters for the tested torque tools only once. The software also creates an individual measurement history for each tool and automatically saves inspection records, making them quickly available when required.
www.kistler.com/reliability
The security of bolts used in airplanes, cars or trains are vital for our safety. Regular calibrations of torque wrenches ensure that every bolt is perfectly in place. To make the calibration process easier, Kistler has developed the small, flexible and user-friendly caliTEST-B device for precise calibration that does not affect ongoing operations. Thanks to interchangeable sensors, the application of caliTEST-B ranges from 0.2 to 1,000 N·m in accordance with DIN EN ISO 6789.
www.kistler.com/reliability
At a recent peer collaboration community event, there was a discussion on the subject of personalisation and the use of AI. This got me thinking about how the concept of personalisation could touch all aspects of a wholesale distribution company. While I could not speak to the vast possibilities in this short article, I will touch on a few that might generate further thought and discussion in organisations.
Personalisation in a business environment refers to creating tailored experiences for customers by leveraging data and analytics to understand preferences, behaviour and needs. The idea is to deliver custom content, recommendations, interaction, and services, that make the customer feel special. A former client of mine was a master at this. His company tagline was: ‘We are experts in your business’. He would find small niche customer segments and then create entire marketing campaigns focused on the products used in that environment. As you can imagine, he became wildly successful by making the customer feel special.
Let’s start simple. Everyone loves to hear their first name. In a business context, we need to make sure that our customers feel really welcome in our place of business. Whether they walk in the door, make a phone call, send us an email, or go to our website, we want them to feel welcome.
Phone etiquette is a dying art. When I was manning the phones in my early days, I was coached to say: ‘Thank you for calling Acme, this is Jason, how can I help you?’ every single time. Four things were conveyed in that sentence. (A) Thanking the customer for calling our business (B) The name of the company they called (C) Who they are speaking to (D) their request is going to be taken seriously. A client of mine has been so concerned with the decline in professional phone etiquette, that they have hired a firm to record and score their phone interactions.
Just because it isn’t face-to-face, doesn’t mean that you can’t make it personal.”
The scoring has led to several ‘coaching moments’ with some of the team members. The CEO shared with me that the recordings have been painful to listen to, but they are giving him the ammunition to seek improvement.
Another simple area to address is email communication. For many, abbreviation and speed has pushed us away from basic customer service. I recall reading a post from some self-proclaimed expert stating that we are all wasting time typing people’s names when addressing them in an email. Cue the rolling of the eyes. Are you so poor at time management that you can’t take the two seconds required to include someone’s first name? Just because it isn’t face-to-face, doesn’t mean that you can’t make it personal.
When we get a new customer on the books, how do we onboard them? How do we make them feel like they made a fantastic decision by choosing us as a supplier? Our sales team worked really hard to get the new customer to sign an application, the organisation needs to work equally hard in making that first interaction amazing. I had one client create a welcome ‘lunch box’ to send to the new customer. I have known others that have the CEO/president send a personalised welcome letter. First impressions matter. My old AR mentor, Abe Walking Bear Sanchez, would recommend that the credit manager reach out to a customer on their first transaction and walk them through the invoice. At this time, they would gather information about preferred email addresses, payable contacts, when they cut checks, and much more about the organisation. He truly believed that the credit management function was more about enhancing customer relationships than the collecting of money. Sadly, most of us don’t reach out to the payables team until the first invoice is overdue.
Is VMI (Vendor Managed Inventory) a form of personalisation?
I would argue that it is. When we set a managed stock room, we are focused on a specific group of products that are uniquely tailored to the needs of the customer. We monitor the levels and replenish as needed. How much more personal can you get? I would highly encourage all distributors to have an active VMI program as an addition to their customer service offering.
The best way to really get personal with a customer is to give them the impression that they are the most important customer on your books. With the thousands of companies you serve, there is no way that your associates can rely on their mental bandwidth to satisfy this goal. This is where a solid CRM comes into play. These systems are way more sophisticated than the old digital rolodex. Yes, you can keep all that personal data; but when you start to incorporate sales data into the mix, this is where we can get really personal. Imagine a system that alerts you immediately when a customer stops buying an item or the pattern shifts. Your associate can give the impression that they are truly on top of the account. Furthermore, imagine systems that tell your associate to suggest items that might be appealing to your customer. Again, it’s the impression you give.
Before I ‘run out of tarmac’ here, I want to touch on personalisation in the eCommerce realm. How do we make people feel special here? When your eCommerce strategy is based on customer login, you have some great opportunities to personalise the experience. Because you are capturing the login, you can tailor the appearance based on the trade type. By narrowing the focus down to functional role of the person logging in, we can offer different views based on the areas they would most likely want to visit.
For example, an accounts payable person would probably like to have easy access to open invoices, delivery verification or discounts taken. A superintendent might want to see new product offerings, tutorials, schematics or other application content. A purchasing associate might be interested in pricing downloads, frequently bought items, or freight policies. The idea is to personalise the experience of the customer entering your place of business.
As selling organisations, distributors are in the relationship building business. Personalisation is in our DNA. We gather information and provide products and services that fit the needs of the customers we are hoping to serve. Unfortunately, in our rush to become digital masters and efficiency experts, we may have strayed from this core tenant. The digital world is not face-to-face, except perhaps on Zoom or Microsoft Teams. As we move to these mediums, we must always keep the personal interaction thought in our mind and work hard to not lose that connection with those that write the checks.
www.thedistributionteam.com
Jason Bader is a holistic distribution advisor who is passionate about helping business owners solve challenges, generate wealth and achieve personal goals. He can be found speaking at several industry events throughout the year, providing executive coaching services to private clients and letting his thoughts be known in an industry publication or two. In 2019, he launched his first podcast, Distribution Talk. Episodes can be found at www.distributiontalk.com and most podcast applications. He can be reached via email at jason@distributionteam.com
When your eCommerce strategy is based on customer login, you have some great opportunities to personalise the experience.”
S&P Software Consulting + Solutions GmbH, part of the S&P Group, has been advising the international construction products industry for more than three decades with regard to the development and sustainable operation of design software.
The S&P Group was founded in 1991 as an engineering office by four university lecturers from Leipzig Technical University in Germany. Over the past 30 years, it has developed into a group of companies with more than 400 employees in 10 locations. The range of services available covers all phases of construction planning and supervision, as well as the development of software solutions on behalf of the international construction products industry.
In December 2000, due to the considerably increasing demand for professional software solutions, S&P Software Consulting + Solutions GmbH was created as an independent company within the S&P Group –taking over all consulting and development activities related to customer specific design software. All of S&P Software’s solutions are tailored to the specific requirements of each customer – there are no standard software solutions that it makes available to the market.
As part of S&P Software’s portfolio, it offers solutions in the areas of fastening technology, timber connection technology, mounting
S&P Software Consulting + Solutions GmbH is specialized in developing construction, dimensioning and product software –available in over 30 languages and 60 countries
DESIGN SOFTWARE FOR ANCHORING STRUCTURAL TIMBERS
rail technology, solar substructures, structural reinforcements and lightweight metal construction. “Since our development teams consist not only of software developers but also of civil engineers, we not only understand the creation of software, but above all know the structural engineering requirements of users for user-friendly and intuitively operable state of the art software,” explains Dr Ing Mirko Neumann, managing partner at S&P Software Consulting + Solutions. “Thanks to our close links with universities, colleges, as well as research and testing institutes, we are able to provide our customers with the highest level of technical and content related advice.”
Software solutions from S&P Software are always developed on behalf of the respective customer and in close cooperation with them. Each software product is tailored to the corresponding individual requirements and developed precisely on the basis of this requirement profile. “As different as the respective boundary parameters are – from the exclusive use of the software in the building product manufacturer’s company; the use by planners, engineers, and fitters; for use in individual construction projects; the adaptation of the software for distribution in the private label business; through to the use in the process of developing new building products – the software is tailored to the individual customer’s requirements,” states Mirko.
With over 20 years of experience, we make our in-depth expertise available to all our partners. Our software ensures acceptance reliability, increasing use and frequency of our partners’ products as well as dimensioning in accordance with national and international technical regulations. We have also been ISO 9001 certified since 2015. From the basic calculation kernel to the user interface – we provide customized programs tailored to your requirements.
S&P Software Consulting + Solutions GmbH
Rathenaustraße 54, 04179 Leipzig, Germany +49 341 442 460 • info@sup-scs.de www.sup-gruppe.com • www.sup-scs.de
In addition to its diverse expertise in the field of structural engineering, and the development of state of the art software solutions, S&P Software supports the construction products industry in the development of new products and design procedures, as well as in approval procedures and ultimately in the ongoing support of the developed software solutions through hosting, maintenance and servicing.
“Within the construction sector we have been working on several areas that we believe will be key topics for the market. For instance, the design of anchors has been undergoing permanent expansion for decades,” reports Mirko. “A whole series of experts and expert groups (in which we are also involved) are constantly working on improving the design approaches and verification procedures. From our point of view, the topics that are of particular interest include verification of the stiffness of the anchor plate, fatigue design, extension of the design for round and triangular anchor arrangements, design in the case of interaction between several anchor plates, as well as the harmonisation of anchor theory and rebar theory. These topics are very complex and are sometimes the subject of controversial debate, so it remains exciting to us as a business.”
Mirko concludes: “S&P Software, like the entire S&P Group, is growing significantly, contrary to the general economic trend in Germany. In terms of software development for a global market, there are growth opportunities not only in the area of fastening technology, but in all areas of structural engineering. That is why we will continue to develop these topics to create value for ourselves and, above all, for our customers.”
www.sup-scs.de
STAFA is one of the biggest suppliers of threaded rods in Europe and stocks DIN 976-1 in 1000, 2000 and 3000 mm lengths. Grades 4.8, 8.8, 10.9 and 12.9 are permanently available. In addition to plain products, we also stock threaded rods and pieces in zinc plated (4.8, 8.8, 10.9) and hot-dip galvanised (4.8, 8.8). On request, we also supply our threaded rods with a certificate EN 10204/3.1.
Recently we have expanded our stock of threaded rods with multiple fixed lengths. In addition, we are always able to fulfil customer requests for fixed lengths in our in-house sawing department. There is no limitation in order size, even small batches are possible. The deburring of the sawn threaded ends is always included.
Aegis Software, a global provider of Manufacturing Operations Management Software (MOM/MES), and Arch Systems®, provider of data and analytics for manufacturing operations, are working together towards digitising continuous improvement of factory operations.
The partnership between Aegis and Arch delivers an Artificial Intelligence (AI) co-pilot, now available in 22 countries worldwide, to guide users toward the right actions during the manufacturing process. If desired, users can also implement these actions automatically via FactoryLogix® on the shop floor.
Manufacturing excellence relies on proactively identifying issues and implementing corrective action. Effective identification requires analytics fuelled by maximum breadth and depth of data and corrective actions rely on revealing insights within those analytics, and then ensuring action is taken on the shop floor. How quickly a manufacturer moves from issue identification to action, and the effectiveness of those actions, is what separates the industry leaders.
By augmenting Arch data sources with both the contextualised product design and human operator interaction data provided by Aegis’ FactoryLogix®, the Arch Insight Engine becomes even more powerful in suggesting targeted operational and process improvements. The results of those actions are then available for both
Arch and Aegis systems to assess the efficacy of the corrective action. In utilising this system of AI, a greater scope of data is possible, thus allowing improvement of the manufacturing process.
“ArchFX customers today achieve unprecedented levels of understanding and actionable intelligence to improve their factories. This partnership will enable our mutual customers to fully detect and align patterns and trends in their data, leading to specific actions for improvement. This is just the start of the novel value this approach can offer,” says Andrew Scheuermann, CEO of Arch Systems®
“Our technology concept is clear – to power autonomously improving operations, a unique and fundamental aspect of Industry 4.0. This partnership satisfies a need we’ve heard from the market as digitalisation becomes more prevalent in manufacturing. That is – ‘how do I better leverage all this data I have from my process to make my operation more successful?’ This solution brings to market an AI co-pilot able to go beyond data and analytics to actually drive operational improvement – either via factory operators or directly via MES,” adds Jason Spera, CEO at Aegis Software.
Mecalux has recently launched a new range of Autonomous Mobile Robots (AMRs) including its 3D Automated Pallet Shuttle system and its DOM software for distributed order management.
Autonomous Mobile Robots are vehicles designed to transport loads between two points independently. They navigate the warehouse freely based on dynamic routes generated by intelligent software. This software optimises the movements of the AMRs, assigning the perfect route for each task. Through the use of state of the art sensors and scanners, AMRs are capable of identifying and evading obstacles. They can operate safely in collaborative environments alongside other machines as well as people.
Mecalux’s AMRs are highly versatile devices that integrate seamlessly into all types of warehouses, requiring neither modifications nor existing infrastructure. The series’ different models make up a versatile set that can handle a wide variety of loads, from boxes, trays, bins, totes and packages to shelving and pallets. Implementing AMRs expedites and streamlines internal flows of goods in multiple intralogistics operations, boosting warehouse productivity and efficiency. Mecalux’s latest innovation, the AMR 600, is capable of moving loads of up to 600kg.
Also new is the company’s latest innovation in integrated warehouse management software – the DOM system. This programme optimises distributed order management for omnichannel businesses with multiple logistics facilities, shops and sales channels. Equipped with the most recent developments in data analytics and Artificial Intelligence, the DOM software integrates and syncs the various supply chain stakeholders, such as warehouses, shops, marketplaces, ERP systems, 3PL providers, carriers and call centres.
Mecalux’s new automated high-density storage solutions for pallets and boxes, the 3D Automated Pallet Shuttle, features a multi-directional shuttle car that moves inside the storage channels and can change levels. Mecalux S.A insists it stands as the ultimate solution for achieving maximum compacting of goods, productivity and flexibility in pallet storage systems. Meanwhile, the Shuttle System streamlines the entries and exits of boxes, thus expediting order picking.
ART. 9015 bi-metal thin sheet screws
with double-thread/fine thread are made of A2 stainless steel and therefore guarantee high corrosion resistance and processing safety. Thanks to the hardened carbon steel tip, the screws are ideal for fastening aluminum and steel components to aluminum or steel profiles – without any pre-drilling!
We are the specialist in high-quality fasteners made from stainless highgrade steel and special materials. We are used to extreme conditions and face the toughest challenges on a daily basis.
We never lose sight of our aim to give the customer just what they want. And we always offer that little bit extra.
So,
Available with or without pre-mounted A2 stainless steel sealing washer.
Exclusively at TOBSTEEL the fixing of pre-drilled aluminium components is also covered by the ETA!
Rudolf-Diesel-Straße 8 | D-74613 Öhringen
At the ‘Production meets Robotics’ event, experts from Würth Industrie Service GmbH & Co KG showed how productivity and efficiency can be increased with the help of innovative technologies, automation and robotics. On 8th February 2024, more than 30 participants gathered at the Würth Industrial Park – one of the most advanced logistics centres for industrial supply in Europe.
In light of Industry 4.0, companies have to deal with changing markets. It is no longer just automation and digitalisation that are keeping the industrial sector engaged. Integrated connection, Artificial Intelligence, cyber-physical systems, collaboration, robotics, big data and many other market trends are shaping and moulding the logistics of tomorrow. This makes it all the more important to rethink existing processes and design the future developments together with customers and technology partners.
At the event, production and process owners, supply chain managers and general managers from a wide range of industries discussed which specific approach could be used to achieve a new level of added value along the entire supply chain in the age of Industry 4.0. The event focused mainly on exchanging experiences, opportunities and risks as well as on visions, technologies and innovations with the aim of presenting concrete ideas, concepts, measures and successful first-hand practical examples.
After introductory words, Stefan Reuss, general manager IT and digital solutions at Würth Industrie Service, held a joint presentation with Erkut Yesiltepe, head of national sales at Würth Industrie Service, which focussed on the C-parts expert’s visions for the future. What will the C-parts management of tomorrow look like and how can automated, connected systems contribute to the autonomous management of parts? In further discussions, the speakers presented their views from the point of view of technological progress. Ralf Bär, CEO of BÄR Automation GmbH, and Sandra Kientsch, vice-president sales and marketing at IDEALworks GmbH, also focussed on possible future directions in changing production structures with a keynote speech on ‘Fundamentals for adaptability in production and logistics’ based on the guiding principle of always being ‘one step ahead’ through innovation and strategic partnerships.
There is no doubt that digital, connected systems ensure excellent progress and pave the way towards Industry 4.0. The participants of ‘Production meets Robotics’ were able to gain a personal impression of the implementation of automation and innovation during a tour of
the Würth Industrie Service logistics centre. They were also shown the 65,000m 2 of storage and logistics space as well as the construction progress of the new high-bay warehouse.
Interested visitors were given an insight into the interplay between the 480 employees and IT systems involved, as well as transport management, which ensures that goods get from A to B every day. Self-learning robots, professional camera inspection systems, driverless transport systems, high-bay and shuttle warehouses are used for perfectly coordinating the processes.
The development of the company is not only visible through the structural measures within logistics but is also depicted in the world of Würth Industrie Service – a room ‘to touch’. During a guided tour, the participants were able to gain a clear picture of the company and a closer insight into C-parts management, including product and system solutions for the manufacturing industry.
What will the C-parts management of tomorrow look like and how can automated, connected systems contribute to the autonomous management of parts?”
METRIC & IMPERIAL SPECIAL FASTENERS
Huge Range of Metric & Imperial Blanks
Grades 4.6, 8.8, 10.9, 12.9; R, S, T, V, SAE8
UK’s largest stocks of BSF & BSW
Special Head Shapes
Most Materials including Exotics
Excellent Prices & Delivery
Over 150 years’ experience in UK MANUFACTURING
sales@smithbullough.com www.smithbullough.com Your
Tel: 01942 520250
SCHNORR® products are always the first choice when metal is being used to meet requirements of movementcushioning - securing through force and form.
Original SCHNORR® Safet y Washers:
• Highly vibration-resistant
• Twofold effect from one component
• E x tensive range
Original SCHNORR® disc springs:
• Various applications
• Best price -per formance ratio
• Customized solutions
Please
Schnorr GmbH
Stuttgarter Str. 37
71069 Sindelfingen, Germany
Phone: +49 7031 302-0
Fax: +49 7031 382-600
mail@schnorr.de
www.schnorr-group.com
tailor-made
Global supply chain solutions provider Blue Yonder is introducing its first set of interoperable solutions across the entire supply chain – from planning to warehouse, transportation and commerce –providing its customers with increased productivity, reduced waste, as well as more resilient supply chains.
As manufacturers, logistics companies, suppliers and retailers look to build greater resilience and mitigate market volatility in their supply chain, they are often hampered by a variety of challenges. These include siloed business processes and communications breakdowns, lack of visibility, disconnected solutions, burdensome workflows across planning, transportation, warehouse, eCommerce, as well as last mile fulfillment. This can lead to inventory waste, high costs, loss of sales, slow responsiveness, lack of resilience and more.
With its move towards end-to-end interoperability, Blue Yonder is looking to solve these supply chain challenges with coordination, streamlined planning and execution management across the end-to-end ecosystem. This includes orchestrating sourcing, production, logistics and network strategies in a single operating system to shorten lead times, improve service levels, optimise operational efficiencies, maximise demand and reduce cost.
As well as this, users are able to align predicted customer demand, network capacity, warehouse capacity, labour capacity, and transportation scheduling prior to sourcing or allocating goods for seamless inventory flow and reduced overhead. Users are also able to build logistics loads that factor in ‘real time’ on-shelf inventory to balance customer demand and waste, generating maximum revenue and margin.
Blue Yonder’s interoperable solutions connect processes, systems, and data seamlessly across Blue Yonder’s supply chain planning and execution solutions, providing a smarter, more scalable, ‘real time’ digital twin to streamline and accelerate enterprise wide decision making. The solutions also offer the end-to-end visibility needed to understand how decisions or actions impact adjacent teams so businesses can work synchronously toward a unified goal.
Deeply embedding Artificial Intelligence (AI) and machine learning (ML) is also featured within the systems to drive decisioning, recommendations, and actions to support a future of autonomous supply chains. The result is more agile, coordinated decision making that reduces costs, increases revenue and improves customer loyalty.
This is the largest product update in the company’s history. “Today’s supply chains are operated by a fragmented ecosystem of legacy solutions, with many being stitched together over time with custom configurations and code,” says Duncan Angove, CEO at Blue Yonder. “While many supply chain solution providers claim to offer end-to-end capabilities, it is typically confined to planning or execution spaces where they’ve integrated their own product suites. Blue Yonder is
...we are redefining end-to-end supply chains and establishing a new category of solutions...”
changing that. With this release, we are redefining end-to-end supply chains and establishing a new category of solutions with interoperable capabilities aligned with our vision to create the supply chain operating system for the world.”
The interoperable solutions are made possible as a result of a number of strategic investments by the company, including its Luminate® Cognitive Platform, as well as its Platform Data Cloud. Blue Yonder’s Platform Data Cloud, powered by Snowflake® , makes it easy to deliver the right data, at the right location, at the right time by bringing together all the required data to run the supply chain in a centralised location. By combining Blue Yonder’s supply chain technology and IP with Snowflake® ’s powerful capabilities, Blue Yonder is reducing the cost, complexity and time required to transform data for its customers, while enabling interoperability between applications and collaboration across Clouds.
“For years, the supply chain industry has had a data problem – there’s too much of it, it’s scattered across disparate solutions, and sharing has become so risky that some organisations have simply come to avoid it. By partnering with Blue Yonder, Snowflake® is helping joint customers address these challenges by centralising data into a single source of truth, reducing the latency in decision making, and making sharing secure, fast and easy,” says Tim Long, global head of manufacturing, Snowflake®
“Together, we’re enabling data, system and business process interoperability by connecting Blue Yonder’s entire end-to-end supply chain portfolio to Blue Yonder’s Platform Data Cloud. Now, Blue Yonder’s solutions can deliver scale and performance that allow customers to significantly accelerate time to value, unlock team productivity, and drive greater resilience.”
Sealing socket head cap screws for tight space applications are used across a range of sectors including electronics, automotive and industrial machinery sectors, particularly where strength, economics and reliability are key considerations.
Available from APM Hexseal, the screws feature a barrel shaped head with a recessed hexagonal drive, with the head being dimensionally smaller than most other standard screws, making them ideal for confined areas of installation. They have also been designed for use in tight spaces and applications where aesthetics might be important, with a sleek design offering a clean appearance, with no protrusions.
The socket head cap screws can also achieve the same, or greater, clamping force as a standard screw and are suited to applications in other areas, such as in the manufacture of excavation equipment, in the energy generation sector, as well as in machining, tool and die, and furniture manufacturing sectors.
Other key advantages of using socket head screws, to those already mentioned, include fewer screws being required for the application, which results in lower component costs. This, in turn, also means fewer holes need to be drilled and tapped, leading to lower manufacturing costs. There will also be an expected end product overall weight reduction, due to the lower component count.
The screw’s socket head features a customised groove under the head, with an O-ring inserted. This creates a reliable seal and protects even the most sensitive systems and components. The product is available with a variety of O-ring materials and is said to provide the same high performing seal as other APM Hexseal products.
www.apmhexseal.com
As flexible electronics manufacturers push traditional boundaries, such as functionality and design flexibility in consumer electronics, Panacol and Hönle UV Technology have successfully developed turnkey solutions, comprising multi-functional adhesives and UV curing equipment, that can be tailored for novel photovoltaic and flexible electronic applications.
The new UV and UV-LED curable adhesives for Organic Photovoltaic (OPV) applications were developed for laminating barrier foils. They provide higher resistance to environmental stresses, have an improved compatibility with PV material, as well as exhibit a low water vapour transmission rate.
Being UV-curable, these adhesives offer high throughput processes, including roll-to-roll, that can be run with greater efficiency, thereby reducing total cost of ownership. The adhesives characteristics, such as flow properties, can be modified in this context to suit the application process, perfectly according to Panacol.
Flexible and bendable UV adhesives have also been created for more traditional applications that are now being performed on flex circuits, including new underfills for die attach/die bonding, as well as structural adhesives being used for component edge bonding.
All UV adhesives from Panacol can be cured with high intensity UV and/or UV-LED curing systems from Hönle, which match the wavelengths of the Panacol photoinitiators exactly. Their light footprint options range from 3mm diameter spot units to linear LED arrays that can exceed one metre in length, making it the perfect choice for smaller and larger irradiation areas.
As for some of the latest conductive adhesives from Panacol, these are being used to secure flexible resistors and create flexible electrical connections in solar cells, touch sensors and wearable devices. They include a one component, silver filled conductive adhesive that adheres effectively to plastics, including polyimide, PC, PVC, ABS, and FR4 boards. When fully cured, the adhesive is very flexible with high peel strength, making it suitable for use in applications subject to vibration, oscillation or rapid temperature changes. One of its major advantages is its ease of handling and storage, where only refrigeration is required.
Master Bond UV23FLDC-80TK is a moderate viscosity, cationic type system that offers both UV light and heat curing mechanisms. It cures readily within 20 – 30 seconds when exposed to a UV light source emitting a wavelength of 320Nm – 365Nm.
The adhesive can also undergo a secondary heat curing for shadowed areas, typically curing in 60 – 90 minutes at 80°C – 85°C.
The system’s adaptability to varying depths and applications, such as encapsulation and bonding, enhances its versatility.
UV23FLDC-80TK has a viscosity of 25,000 cps – 50,000 cps and is highly thixotropic, which is advantageous for applications where minimal flow is required. It has a low tensile modulus of 250 psi – 500 psi, and a high elongation of 90% – 100% at room temperature. Its toughness and flexibility allow it to withstand rigorous
thermal cycling, making it well suited for applications where low stress is critical. The system features excellent electrical insulation with a volume resistivity exceeding 1,014 ohm-cm.
UV23FLDC-80TK is not susceptible to oxygen inhibition. It bonds well to metals, glass, ceramics, and many plastics, including but not limited to acrylics and polycarbonates. It has a service temperature ranging from -80°F to +300°F (-62.2°C – 148.9°C). It is available in a wide range of packaging options, including syringes, ½ pint, pint, quart and gallon containers.
PEM ® fasteners have played an important role for the overall application of a Danish satellite orbiting Earth, launched by students in a collaboration across several universities.
Last year in spring 2023, a Danish satellite was launched by a rocket from the Vandenberg Space Force Base in California, USA. Featured onboard were components by PennEngineering® in the form of PEM ® press fasteners – supplied by the Danish sales and engineering house Hans Buch A/S.
The satellite with PEM® press fasteners is called DISCO-1 and is the first of a series of satellites in the DISCO programme – established in a never seen collaboration by students from four different Danish universities.
The satellite is built by the company Space Inventors, which Hans Buch assisted in identifying the advantages of using the press fasteners over many other fastening solutions.
The total weight was decisive for the satellite’s properties. Rasmus Pedersen, director and CCO of the industry division at Hans Buch, explains: “It was essential for the design of the satellite that the weight could be
kept down without compromising on quality. Our PEM® press fasteners played a crucial role.”
The PEM ® press fasteners used were the self-clinching nuts CLA™-M2-2 in aluminium. They were mounted on a milled aluminium bracket that was anodised to increase the corrosion resistance. Overall, the PEM ® press fasteners enabled an application consisting of aluminium plates with a thickness of just 2mm. This was made possible without compromising on the durability and whilst still ensuring the products could handle the harsh conditions during the rocket launch and while orbiting the Earth from space.
The satellite measures 10cm x 10cm x 10cm, weighs just approximately 1kg, and is the first of a series of satellites that will help researchers understand climate changes in Greenland. DISCO-2 is planned for launch in the summer of 2024.
“We are excited and we are proud to contribute to the successful creation of the
first DISCO satellite, and we have avidly followed the launch of the satellite. The DISCO program aims, among other things, to attract young talent to the Danish space sector, which is growing strongly, and thus, demands an increase in workforce. We are delighted that the project aims to inspire young, technical talents to choose the space sector as a field of expertise and future career. It is great for a company like Hans Buch to be a small part of,” concludes Rasmus.
www.pemnet.com
In Formula E, adhesives are exposed to extreme loads. For instance, a high performance electric motor with an output of 350kW can propel the 854kg race cars to 100km/h in 2.8 seconds. The current generation can reach top speeds of up to 320km/h, which can put a huge strain on all the parts – that’s why the TAG Heuer Porsche Formula E Team relies on Loctite® products.
Through its Loctite® brand, the company has formed a close partnership with the TAG Heuer Porsche Formula E Team, a collaboration that began in 2021 – when Henkel appplication engineer, Martin Christall, met the team to identify possible points of use where Loctite® could further improve the performance and reliability of the team’s electric race car.
The biggest challenge was that, in Formula E, the chassis, battery, aerodynamics and front suspension are the same for all teams. This means only a certain amount of leeway is possible when it comes to incorporating a team’s own technologies and components, such as the engine, transmission, rear suspension and control systems.
Martin recalls the day the company managed to win the team over with one of its first demonstrations. “The design of the car’s front motor raised some assembly challenges for the team. Loctite 9466 adhesive worked amazingly on the first try. This created trust and was a good basis for our further collaboration project.”
Today, the teams work closely together to get even more out of the cars of the future, with the TAG Heuer Porsche Formula E Team improving season on season, with its best ever placing of 4 th in the 2023 season. Their shared goal is to develop even better ways of using Loctite® products, while also testing new solutions that enhance the car’s performance, speed
for a host of key applications, from suspension bearings, gearbox housing parts,
products can be used in a host of areas.
EJOT UK is supporting the 2023 Collaborate to Innovate (C2I) Awards dedicated to recognising and celebrating the very best examples of engineering innovation achieved through a collaborative approach.
The fastening systems manufacturer is sponsoring the ‘Automotive’ category, a market sector the company serves in the UK and globally through its extensive range of advanced fastening systems and its ability to co-develop new joining technologies.
The ethos of the C2I Awards aligns perfectly with EJOT UK’s collaborative approach to R&D and customer support. Working closely with OEMs and component manufacturers makes it possible for EJOT to design the most effective fastening solutions required to address the challenges of today and in the future. Hence why collaboration is central to its continuous new product development programmes.
Some fastening systems that EJOT has developed collaboratively with customers have actually facilitated industry wide change, such as the EVO PT screw. This evolution to the Delta PT screw continues to raise the bar through its unique threadforming zone that provides a virtually constant torque over multiple installation depths within a single assembly.
Another fastening gamechanger was the EJOT ALtracs Plus self-tapping screw for light metal. This has enabled customers to achieve production cost savings and component optimisation goals across a wide range of joining applications, and today different variants of the
screw are being deployed in a number of key areas of EV (electric vehicle) technology, most notably battery assemblies.
Steve Wynn, UK sales manager for industrial fastening solutions at EJOT, said: “Collaboration is key to developing the best solutions to today’s engineering challenges, particularly in the automotive industry where the transition from conventional internal combustion engine (ICE) powered vehicles to hybrid and electric technologies, has succeeded by bringing together the best minds from across the sector and applying fresh ideas. EJOT has always advocated co-development to achieve optimised fastening solutions and we have seen numerous customers realise the benefits in the long-term.”
When a nut is tightened by applying a torque, the bolt is stretched and a tensile force in the bolt, known as the preload, is created resisting this stretching. In response to this preload, a clamp force on the joint is generated – a clamp force that is vital in many instances for the joint’s structural integrity.
Since the preload itself is difficult to measure, and there is no low cost and effective method, the torque being applied to the fastener is used instead to assess if it has been sufficiently tightened. The relationship between the torque being applied and the bolt preload is linear. That is, when you plot out the relationship between the two by measuring both, you get a straight line as shown in Figure One.
So, for any particular bolt, if you double the applied torque you will also double the preload – this is assuming that the bolt material doesn’t yield or the thread starts to strip. This linear behaviour forms the basis of the torque calculation processes. For example, the simple K factor approach in which the formula (T = F x D x K) where T is the torque, D is the bolt diameter and K is the nut factor, otherwise known as the torque coefficient.
For a given bolt diameter and coating condition, ‘K’ is assumed to be a constant and so the formula is essentially that torque (T) is proportional to preload (F). This is a straight line relationship between the applied
torque and the preload. The same reasoning can be shown to apply to the long form version of the torque tension equation that uses friction coefficients instead of the ‘K’ factor.
At Bolt Science we have conducted thousands of torque tension tests. Occasionally, we come across the situation where the graph of torque against preload is not linear, instead the graph is a curve, as demonstrated in Figure Two. The graph of torque against preload may curve upwards, or downwards, depending upon circumstances.
In this instance, if the torque is now doubled, the preload can be greater than double, as in the case when the curve gradient is decreasing, or less than double, in the case when the curve gradient is increasing. The causes of non-linear torque-tension relationships are discussed in a recently published training presentation on the Bolting Technology for Engineers and Designers online course. Further details about the course are available at: www.boltscience.com/pages/training1.htm
NORMA Group’s cooling systems are helping to save weight and improve vehicle efficiency with a tailor-made design for an Indian SUV manufacturer and its all electric fleet.
Together with the customer’s engineering team, NORMA’s product development engineers have designed a solution using plastic lines for the cooling system instead of rubber hoses. This switch in material and design choice allows for a significant weight reduction of the cooling water system – equating to approximately 20% – 25%. From 2024 to 2030, around 700,000 vehicles are due to be equipped in the scope of this order.
Thermal management is an essential aspect of energy management in electric vehicles and helps to optimise battery performance and extend battery life. NORMA’s line systems are used for the thermal management of the power electronics system and help to ensure the optimal operating temperatures of the vehicle.
“Our products and engineering services for the innovative SUV series underline NORMA Group’s contribution to global technology progress,” says Guido Grandi, CEO of NORMA Group. “eMobility will likely remain the mega trend for the automotive industry for years to come, and we will continue to serve our customers with innovative products and services for all electric, hybrid, fuel cell or hydrogen vehicles. This collaboration is a good example of our strategy to work closely with OEMs and deliver tailored solutions for their innovations.”
From mid-2024 NORMA will also deliver cooling water systems for the power electronics system as part of the same customer’s new battery electric vehicle (BEV) platform.
Founded in Italy in 2001 by German national Herbert Schruff, BBA Srl is a manufacturer and designer of rivet nuts and rivet nut studs, with a clear focus on rivet nut innovations, such as its patented BCT® (Bulge Control Technology) rivet nut design.
Standard rivet nuts are a tried and tested means of providing a riveted (permanent) threaded fixing point to thin sheet metals. However, as application requirements increasingly evolve, standard rivet nuts are not suitable options. Where this is the case, BBA’s BCT ® takes rivet nuts beyond known capabilities and achieves new performance heights.
BCT ® is a revolutionary technology comprising of weakening points positioned on the shank of a rivet nut or rivet nut stud. These weakening points precisely predetermine where the bulge will start forming, independent of the application material. The bulge always forms from behind the sheet, pulling it up onto the sheet (clamping it) and therefore avoiding radial expansion on the side walls of the hole. These features mean that rivet nuts and rivet nut studs using BCT ® can offer new and exciting application solutions.
BCT ® Controlled is a range of rivet nuts and rivet nut studs for use in composite and plastic materials, where traditional rivet nuts risk deforming or cracking the application material. As BCT ® Controlled places no radial force on the walls of the hole, the rivet nut may be installed very near to the edge of the application without risk of cracking the material. As the bulge formation is independent of the application material, BCT ® Controlled is also suitable for use in applications where conditions mean that irregular or oversized holes may be present.
BCT® Ultra is a range that achieves the maximum tightening torque loads of Class 12.9 bolts. As the entire product is made from a higher tensile steel of 600MPa (versus 330 MPa for standard rivet nuts) not only the thread is stronger, but the entire product is stronger, thus the bulge is able to maintain the pretension of the mating bolt and offer a very low and consistent torque angle. The BCT® Ultra range is available in rivet nut and rivet nut stud options and offers an alternative to welded nuts and welded studs, avoiding the issues associated with the welding process and is often used as a repair solution for failed welded products. Furthermore, this range is routinely used as an electrical grounding solution and particularly for use on non-metal sheet applications where welding is not possible.
Also available, the BCT ® Micro range is fundamentally a BCT ® Ultra but physically smaller with less threads and therefore can be installed into application spaces too small for standard rivet nuts to fit into. The high strength nature of BCT® Micro means that despite its smaller size, the product still yields thread strength compatible for use with Class 8.8 bolts and their recommended tightening torques, thereby providing load bearing threads in restricted spaces.
Another innovation is the BCT ® Nail Nut, specifically designed where high torque to turn performance is required in application materials that are softer than steel. This includes most grades of aluminium, plastics and composite materials. To increase torque performance in such materials, hexagon holes are used in conjunction
with hexagon bodied rivet nuts. In such cases, the failure mode is generally the sheet material that often deforms around the rivet nut body at relatively low torque levels. With the BCT ® Nail Nut, 4 teeth protruding from under the head of the rivet nut (or stud) are pressed into the surface of the soft sheet material during the installation process. The teeth penetrate into the softer sheet material creating a locking feature that provides outstanding anti-torque to turn resistance. To maximise anti-torque to turn rotation, BCT® Nail Nut can be deployed together with a hexagon or knurled body on the rivet nut too.
Finally, BCT ® Floating is an innovative way to address alignment issues and provide gap compensation. The rivet nut is only partially installed into a slotted hole. As there is no radial expansion in the hole,
BCT ® Floating is then free to travel the length of the slot and cannot ‘fall out’ as it is retained by the partially formed bulge. Later, when the bolt of the mating component is presented to the rivet nut, the bolt can be used to position the BCT® Floating so that it is perpendicular to the bolt. As the bolt is then torqued further, it completes the installation of the BCT® Floating and then tightens the component to the rivet nut to the desired application tightening torque.
Given that all of BBA’s products are manufactured in Italy, whether a standard rivet nut or an enhanced BCT® rivet nut is required, the customer is assured that by choosing BBA as a partner, their supply chain is as secure as possible. Coupled with the fact that BBA remains 100% family owned, the company is able to offer its customers branded products that are backed by the quality, performance, reliability and dependability you would expect from a leading European manufacturer.
www.bbafasteners.com
Here Sherex Fastening Solutions®, a PennEngineering® company and global specialist in engineered fasteners, tooling, and automation, discusses the benefits of combining a compression limiter with a rivet nut to create a compression limiting rivet nut, as well as how its Optisert® round body rivet nut performs comparably versus a half hex body rivet nut.
Compression limiters fill a gap for a metal on metal load transfer as to not deform the material. So when the fastener, such as a screw or bolt, is tightened, the compression limiter is compressed between the fastener head and the metal parts being joined for a compact assembly.
Compression limiters are typically integrated with a fastener, such as a rivet nut, to provide metal to metal transfer of forces during the joint assembly. However, there is an even simpler solution available – combining a compression limiter with a rivet nut to create a compression limiting rivet nut. A compression limiting rivet nut integrates both a rivet nut and a compression limiter into a single piece with a unique part number.
This offers several advantages as it is a single component instead of two separate parts, streamlining assembly time and simplifying the ordering process for purchasers, as they only need to consider one part. It is also cost-effective as a compression limiter and a rivet nut combined would likely cost more than a specially designed compression limiting rivet nut.
With a compression limiting rivet nut, it pretty much acts as a rivet nut with a bigger shoulder or spacer combined on top of the rivet nut. When the compression limiting rivet nut installs, it installs into the base material, but the spacer or compression limiter then sits above it as to not distort the material sitting on top.
Like all compression limiters made and designed by Sherex, they are all unique to the application and the same applies with these compression limiting rivet nuts. They are very popular in automotive applications with pretty much limitless designs – round body, hex body, underhead seals, knurls, etc. Sherex engineering works with the application design engineers to come up with a design that will surpass performance expectations while also being the most cost-effective solution compared to other fastening options.
So, if considering a compression limiter, a compression limiting rivet nut might be a better solution that delivers the same performance with less parts.
Sherex has been working for over five years on a round body rivet nut that can perform comparably versus a half hex body rivet nut. Rivet nut best practice is to still recommend a full hex body rivet nut if you can make a hex hole – especially in harder material like steel and stainless steel. However, if a round hole is the only hole that can be produced, especially in softer materials like plastic, fiberglass, and aluminium, Optisert®’s performance is recommended.
“We’ve had over five years of product development to get the performance where we want it,” says Sherex Engineering Manager John Knechtges. “We’ve done similar wedgehead, knurled rivet nuts as specials for projects, but this standard part has unmatched performance. We’re really proud.”
Optisert® spin out performance in aluminium is closer to the performance of a full hex rivet nut than a normal, round body CAL rivet nut, and actally greater than a half hex rivet nut.
With knurls underneath the flange that bite into the material, resistance to spin out is very extraordinary. Spin out occurs when the rivet nut spins into the hole it’s installed into. Spin out would potentially occur in applications that experience heavy vibration or in applications that experience a lot of strain force.
For industries that are continuously looking for lightweighting options, such as the automotive and heavy truck sectors, Optisert® is an ideal option for a threaded insert fastener. Optisert® also comes in a closed end option with a seal that comes standard. The seal does not compromise grip and helps keep dust and water out of the base material.
www.sherex.com/uk
Six ranges, comprising over eighty lines of rivet nuts, have been launched by Jaton Riveting Products (JRP) – a leading brand from Owlett-Jaton.
JRP, a dedicated riveting brand, offers an extensive range of quality blind rivets, rivet nuts, and tooling. With over 1,200 lines already in the range, the offering is substantial.
The new rivet nuts added are in addition to the circa 230 rivet nut lines already in the range. They include reduced head round knurled body closed, reduced head part hexagon body closed, flat head round JK split nut open, flat head round PN heavy-duty split open, flat head US round knurled body open, as well as reduced head US round knurled body open. These are available in aluminium, steel zinc and Clr Tri8/Tri3, A2 stainless steel, and A4 stainless steel.
The addition of multiple ranges of closed body rivet nuts provides more options for manufacturers looking for a sealed end, which will prevent water ingress. Two new rivet nut setting tools have also been added to aid in setting the JK nuts.
The complete JRP range is supported by a full technical resource. The technical team at JRP is on hand to offer technical advice and suggest the best solution in design and application problem solving. The team provides the technical knowledge needed to support the range and help their customers to support end users.
www.owlett-jaton.com
“We want to make it as easy as possible for customers to add the JRP line to their portfolio. That is why we work closely with manufacturers to guarantee quality,” comments Warren Keeley, technical support specialist at JRP. “Growing the JRP range is essential for continued success. Work has already started on our next launch and we hope to see it in the market later this year. We are also in the process of developing an exciting piece of software that will be unique in the marketplace and provide customers with an additional layer of support. Keep an eye out for the 1 st April launch.”
Speed rivet technology permits the installation of 50 – 60 rivets in a very short time, like a self-feeding concept.Fixi points out this technology allows a 60% – 71% increase in installation when compared to standard blind rivets.
Available in aluminium, steel and stainless steel – with standard or countersunk head and coloured type – the most requested diameters are 3.2mm, 4mm and 4.8mm but other sizes can be requested.
Coming in May 2024, the new line of riveters for industrial use from Fixi consists of four tools covering all blind rivet installation applications from 2.4mm until 6.4mm, including structural rivets. Special attention has been paid to the safety, speed of installation and weight of the new tools to enable industrial workers to work more efficiently.
These two lines complete Fixi’s wide range of blind rivets, threaded inserts, self-clinching fasteners, fasteners for plastic, wire inserts, inserts for tubes and inserts for stones and solid surfaces, as well as the related tools to install.
“2024 is the year of looking to the future with optimism and the desire to continue developing and growing together with specialised distributors in our niche market – fundamental for every solution of fixing,” comments the company. “Fixi is ready, with the technical, quality, commercial and logistics departments to collaborate .”
www.fixi.it
Completely independent of gas cartridges, power cords, and hoses, the new pneumatic cordless nailers from PREBENA Wilfried Bornemann GmbH & Co KG can be used anywhere, offering complete working freedom.
Consisting of three models – the PKT-8-RKP100 round head strip nailer, the cordless nailer PKT-8-RHC40 and the VITAS 100-AKKU small compressor – the new PKT-HYBRID range has a very compact design and has enormous shooting power.
The first of the tools, the PKT-8-RKP100 is suitable for paperbound round head strip nails (Type RKP) up to 100mm in length, as well as processing paperbound half-head nails (D-head) Type PR also up to 100mm in length.
The newest member of the PKT-HYBRID family is the cordless nailer PKT-8-RHC40 for hard surfaces such as steel, concrete and
weather independent and can be used indoors and outdoors.
The devices are ‘Made in Germany’ and easy to operate via the touch display and feature an adjustable single or contact triggering, as well as a quick charging system to enable fast work.
The battery tool programme is rounded off by a small compressor – VITAS 100-AKKU –with a five litre tank and a drywall screwdriver 6A-MGS55 for collated screws up to 55mm.
PREBENA belongs to the Cordless Based on the powerful Metabo LiHD
At Hafren Fasteners, security is not just about functionality; it’s also about seamlessly integrating security measures into a particular environment. This is important in applications such as façades where a screw head, painted in the colours of the façade, blends harmoniously into its surroundings, making an otherwise unwanted feature almost invisible. This is where the company’s new offering of security fasteners with powder coated heads comes into its own.
Powder coating is a dry finishing technique where a fine, electrostatically charged powder, composed of pigment, resin, and additives, is applied to a surface. The electrostatic charge ensures the powder adheres to the object. Next, the coated item is baked in an oven, allowing the powder to melt and fuse into a resilient and appealing finish.
Widely employed for both protection and decoration, powder coating is commonly used for enhancing the durability and aesthetics of various metal items. It’s also the most popular form for colouring heads, as it’s more environmentally friendly, produces less waste, and provides a more uniform and durable finish, which is more resistant to weathering, scratching, chipping, chemicals, and fading, than traditional wet paint techniques.
Hafren powder coats are available in a vast range of colours using a wide variety of RAL and British Standard paints, such as gloss, satin, and matt finishes, but also using special RAL designs, metallic finishes and textured paints. Its extensive colour matching ensures any security fasteners seamlessly integrate into the application surroundings, maintaining a sleek and cohesive aesthetic – whether a customer wants fasteners to discreetly blend into a background, or stand out as a design feature.
Whilst security is paramount, the company believes it shouldn’t come at the expense of design. As a result, its painted heads service allows for a secure application without compromising on appearances. Should a specifier seek to integrate subtle security measures without drawing undue attention, Hafren’s powder coating service offers a solution, seamlessly blending security measures with an overall design –helping to achieve effective asset protection without compromising aesthetics. The process is also versatile, offering any colour for any parts, so that customers can enjoy the benefits of high-quality, reliable fasteners, while still achieving excellent colour coordination for specific requirements.
The powder coating service can be applied to all of Hafren’s wide range of security fasteners, offering great versatility for any application. Whether securing high-value assets, safeguarding property, or simply adding an extra layer of protection to premises, the company’s fasteners can be tailored to suit any specific needs. They can also make a statement, beyond simply blending in; by choosing bold and vibrant colours to showcase a commitment to security, or by matching them to a company’s branding for a cohesive look – the possibilities are endless.
In summary, the key benefits of this powder coating service include customisation; with a wide range of colours and finishes to choose from to match surroundings, or to make a statement, seamlessly blending security into the environment and application for a discreet and polished look; durability, with the powder coating treatment helping to enhance fastener longevity by adding a further layer of protection against weathering; and versatility, with any stock parts being matched with any colour, thereby opening up a world of possibilities.
Hafren believes that security should be effective and elegant, which is why its powder coated heads service offers the perfect combination of security, functionality, and style, giving peace of mind that comes with enhanced security, yet without sacrificing the appearance of any particular application’s environment.
The thread-lock FS Vario-Lock ® from Flaig + Hommel GmbH is a screw thread-lock that allows variable positioning, extreme flexibility and versatility in securing screw threads.
The braking torque, based on the DIN EN ISO 2320 standard, can be defined individually according to customer requirements. Any special thread can be implemented at the time of manufacturing special purpose screws and bolts with external thread, as well as for any customer specific screw types.
The locking effect is achieved through parallel displacement of the thread flanks at 360° of the screw thread. The thread play is eliminated from the screw joints at this point in the counter thread, which results in a locking effect. The thread grips the counter thread flanks firmly. The Vario-Lock ® thread flank acts like a spring, producing the locking torque as specified by DIN 2320.
HIGH LEVEL OF PRODUCTIVITY
Power and efficiency in assembly lines
QUALITY IN RIVETING
Thanks to quick adjustment of force and stroke
EASY MAINTENANCE
With quick change of mandrels and nosepieces
ERGONOMICS AND COMFORT
Thanks to its low weight and ergonomic grip
QUICK INSTALL
Automatic threading and unscrewing with pressure
Bäcker GmbH & Co KG, has added new locking systems and security solutions to its product portfolio, under its new PlacoLock® brand, in order to adapt to changing customer requirements and with future orientated growth in mind.
The new range comprises of compression and twist locks, edge protection and sealing profiles, as well as various other locking systems. The products are used in sectors such as mechanical and plant engineering, vehicle construction, IT and telecommunications, as well as shipbuilding.
The compression latches, with pressure locking, are ideal for sealing cabinets, compartments, or pull-outs. They allow the clamping force to be adjusted when closing and tightening hinge parts, which eliminates vibrations from doors, lids and drawers during machine operation. In addition, the latches are also used when opening insulated and pressurised doors, to ensure safe decompression.
The new brand’s quarter turn latches are aimed at a range of applications with their simple rotary movement of 90° to 180°, they ensure secure locking of cabinets, gates, or other locking
mechanisms. Some of the locks come with conventional key inserts, others are operated with a tool spanner.
The new PlacoLock® brand’s edge protection and sealing profiles are used to protect the unprocessed edges of sheets and panels, preventing cavities at the edges of the material, or to cover sharp edges to prevent cuts and injury. The edge protectors are also equipped with a sealing profile to insulate doors, flaps, lids and other hinged parts. Installation is straightforward and is carried out by
Precision engineered component manufacturer, SPIROL , has introduced its new CL6000 series of lightweight, precision machined, compression limiters.
Lead-free and made of aluminium, the new compression limiters have been designed to reinforce high stress joints in plastic assemblies, where bolts are used to connect two components and where they protect the plastic from excessive compression by absorbing the load when the bolt is tightened to the recommended torque. This ensures the durability and reliability of the joint throughout the product’s lifespan.
SPIROL points out that the CL6000 compression limiters are machined from 2024 grade aluminium, which provides the best combination of strength, corrosion resistance, machineability and cost, but which also makes them 40% stronger and ⅓ of the weight of the same compression limiter made from brass.
When it comes to applications that require extra bearing surface for the mating component, another product, the CL6100 headed compression limiter has also been launched, with all of the features of the CL6000, but with the addition of a head. Similarly, for applications that require a galvanic alternative to aluminium, SPIROL has introduced its new CL8000 brass, precision machined, compression limiters, along with the corresponding CL8100 headed brass version.
SPIROL’s different standard types of compression limiters are intended to meet specific application requirements and assembly methods, which is why the current/legacy series CL600 and CL800 limiter lines are being replaced with the enhanced CL6000 and CL8000. The new products offer benefits that include: Precision through enhanced control of critical features and better geometric dimensioning and tolerancing, making this series ideal for highly automated, or moulded assembly processes; retention as a result of superior knurl formation and control, which result in more consistent and robust retention performance in post mould, assembly processes; and a wider product range, with the larger selection of standard products meeting expansive application requirements and preferences.
The new, standard, precision machined, compression limiters are available in a wide range of standard sizes, in both aluminium and brass, and in headed and non-headed configurations.
SPIROL’s engineering team can also help determine the most appropriate compression limiter for a specific project, offering complimentary design assistance and technical support.
www.spirol.com
Stainless steel
We produce normal A2, A4 And A8 (MATERIAL : 1.4529)
Carbon steel
Our EU ADD rate is 39.6%, TARIC CODE C845
Size:M3-M10
Length:13-400mm
Add: Huiqiao Rd #1121, Langxia Street, Yuyao, Zhejiang, China
Tel: + 86 - 574 - 87162804 Fax: +86-574-6200 8290
Http:// www.alfirste.cn E-mail: 760@chinanchor.com
In the quest to develop a sector wide software tool for the harmonised Product Carbon Footprint (PCF) calculation for the adhesive and tapes industry, it has been agreed that Sphera, a specialised provider of sustainability software consulting services, will work in close cooperation with Afera to finalise the raw material clusters and build the database required to set-up the tool.
During a number of successful workshops and together with the German Adhesives Association, IVK, Afera has been taking part in key discussions to find industry specific processes, raw material clusters, and data requirements, needed to develop the new PCF tool for adhesive tape manufacturers.
In addition to the PCF tool, Sphera will also provide Afera members with a manual on how to use the new tool, as well as a detailed description of the methodology used for PCF calculation, including the assumptions made and how Together for Sustainability (TfS) guidelines apply to adhesive tapes.
Over the course of the workshop series, several important agreements were reached, on calculation methodology, scope, functional units, parameters, data and timeline. Calculation methodology, for example, is to be based on ISO standard 14067:2018: ‘Greenhouse Gases –Carbon Footprint of Products’ through an expansion of the TfS PCF guideline. The functional unit was agreed as CO 2 equivalent per square
metre of tape, with a conversion factor taking surface area and mass into account. The timeline sees data collection during H1 2024 and draft tool delivery (MVP) during Q3 2024.
Pablo Englebienne, Afera regulatory affairs and sustainability manager, said: “We made a lot of progress during the last scoping workshops in Düsseldorf, Germany. All the key aspects have been agreed upon. We can now focus on filling in the details for the raw materials and the manufacturing processes. Fortunately, earlier discussions and data from prior projects can pave the way for a swift development of the tool, so that we can have a version before the end of 2024, as was intended.”
Access to the eventual online platform will be made available to tape manufacturer members, with an access fee. The common goal is to ensure that member companies can soon determine PCF values for adhesives and tapes in a straightforward, harmonised, affordable manner. This will allow businesses to meet future legal requirements, as well as the demands of the supply chain.
Especially Long Size
OEM Project
Solar Panel Fasteners
Non-standard Customized Chipboard Screws
NEW RELEASE OF ETA-CE CERTIFIED SCREWS FOR CRACKED CONCRETE
Enhancement of certifications in seismic zones
New range with reduced embedment for a wider choice of applications
New coatings for enhanced durability and usage in extreme environments
Improved load performance and reduced edge distances and spacings
The CE marking is everywhere. But it’s only now that you’ll find it on one type of securing washers.