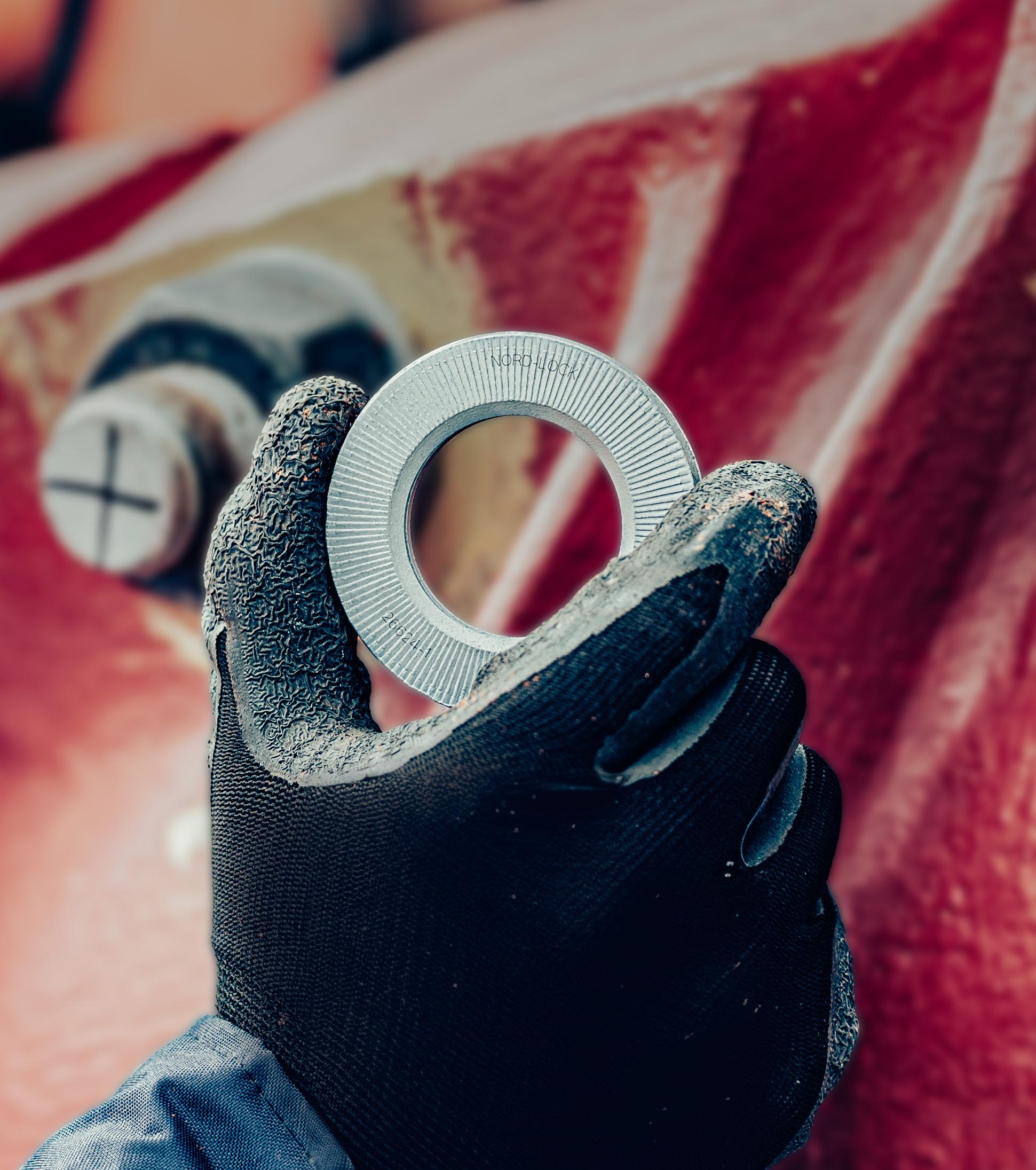
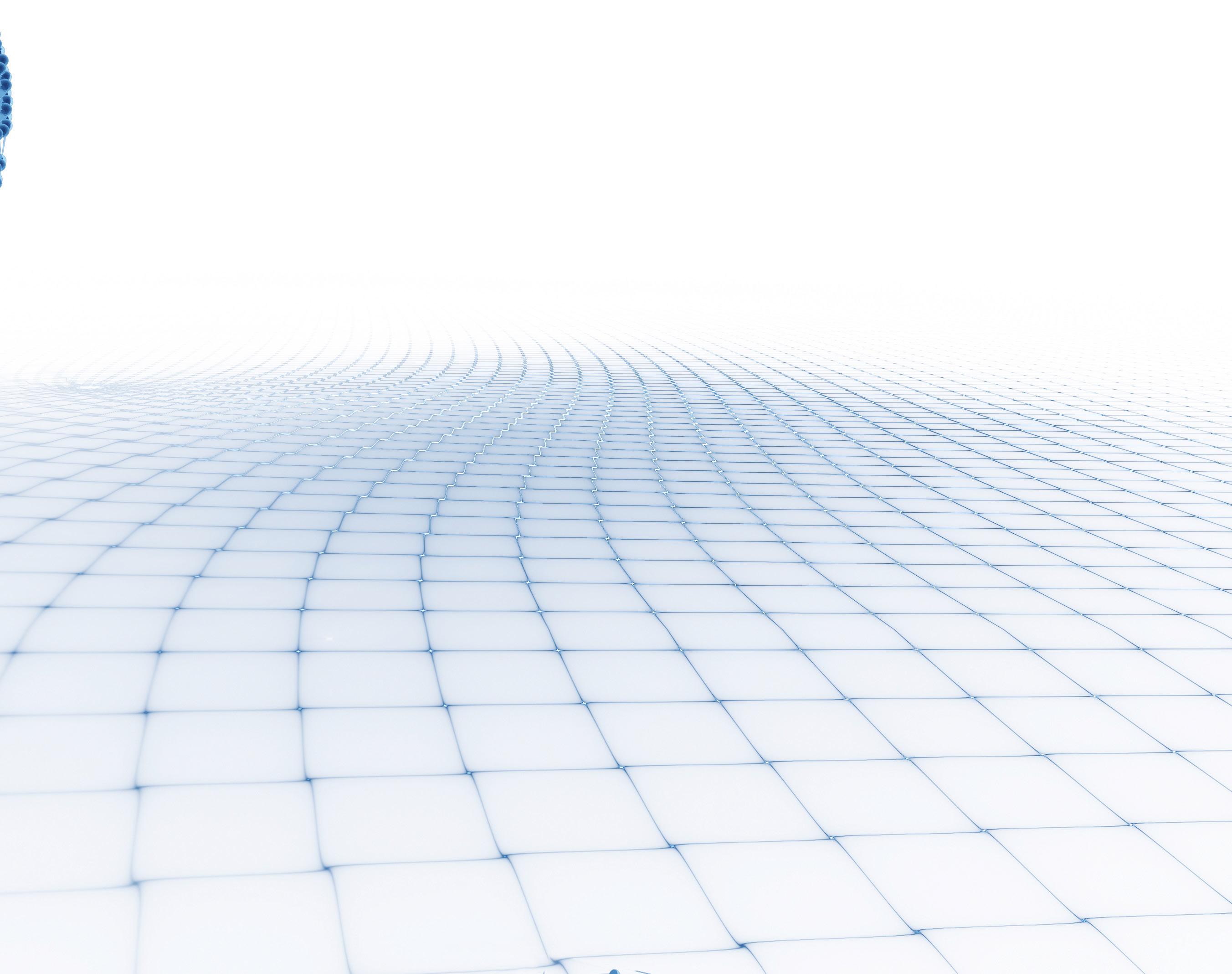
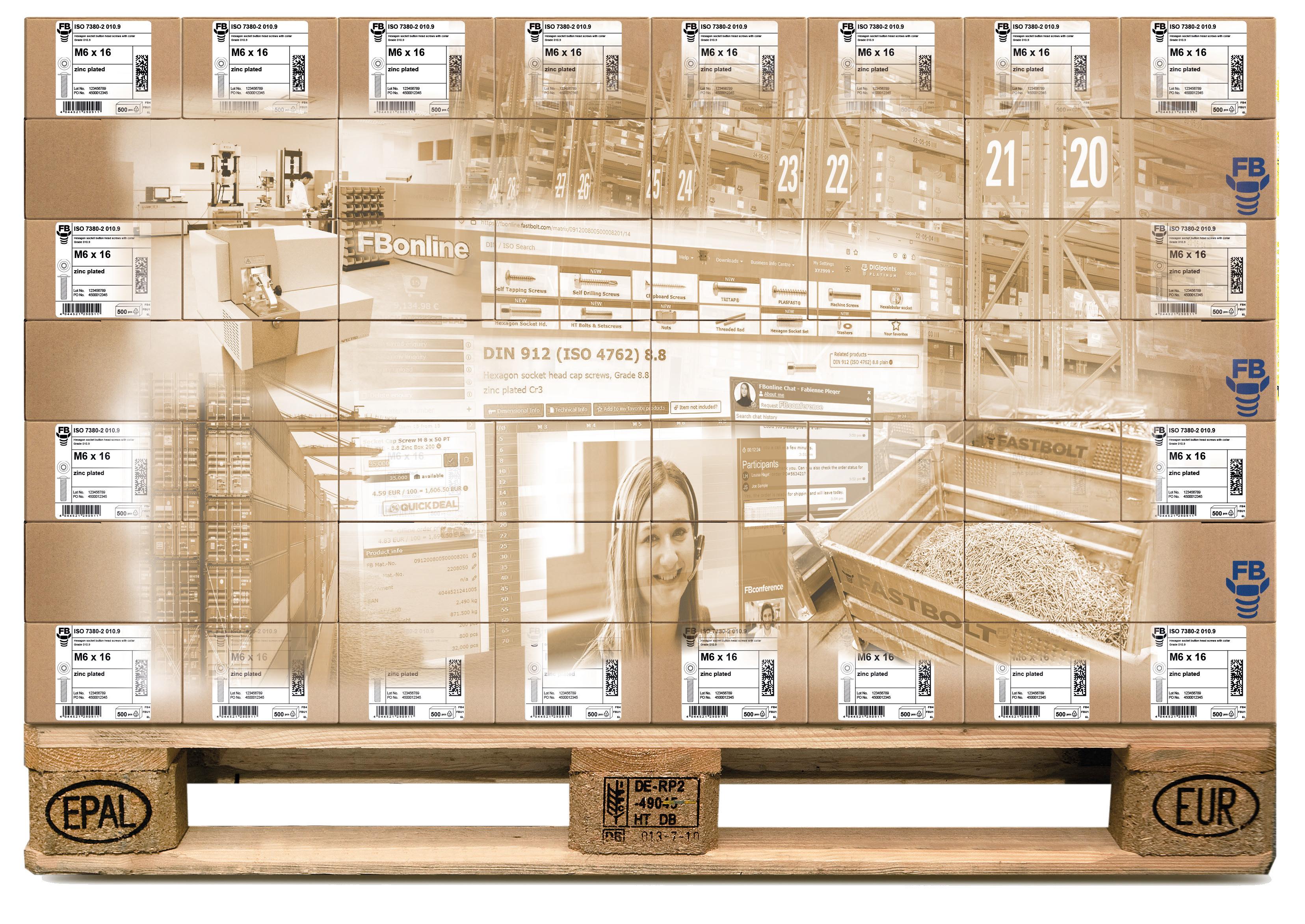

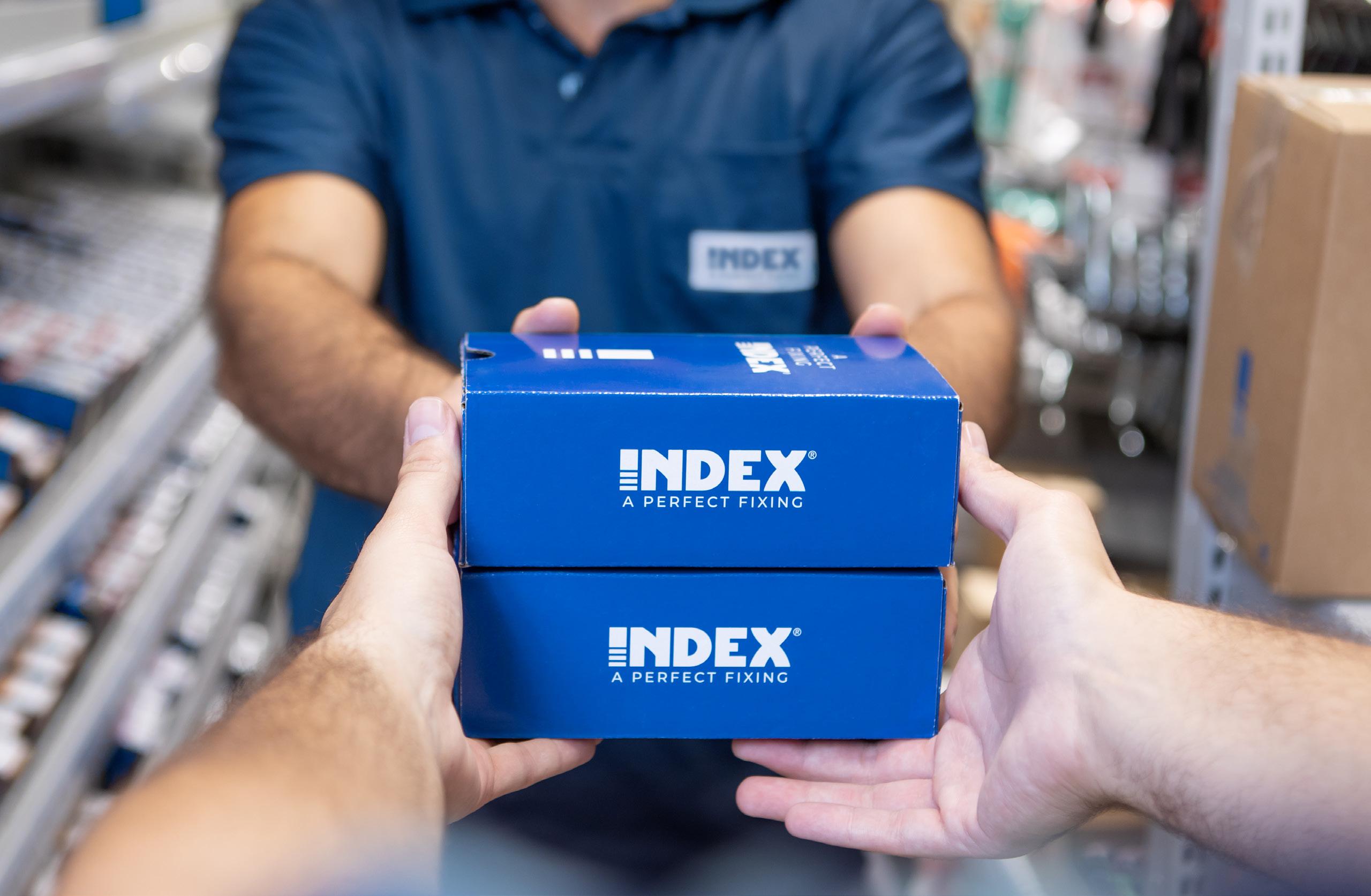
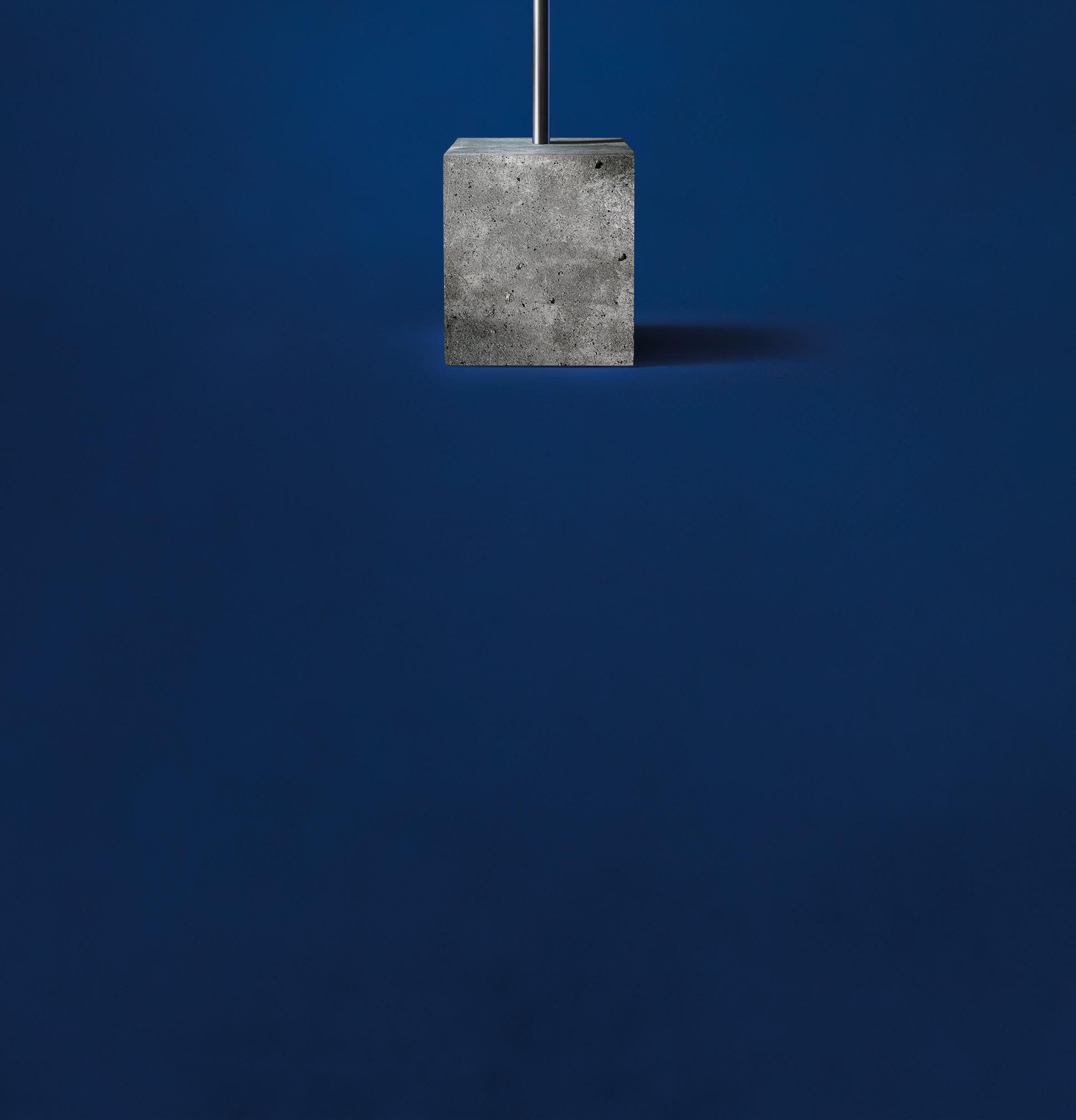
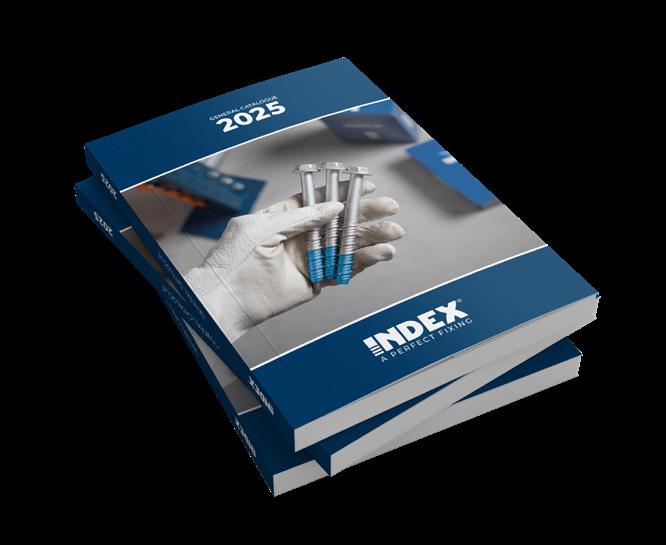



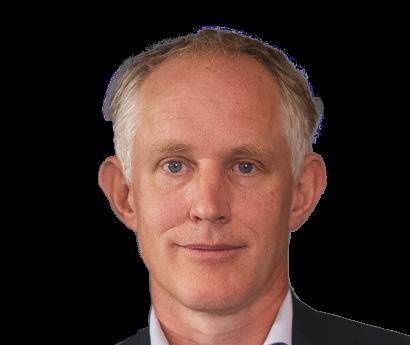
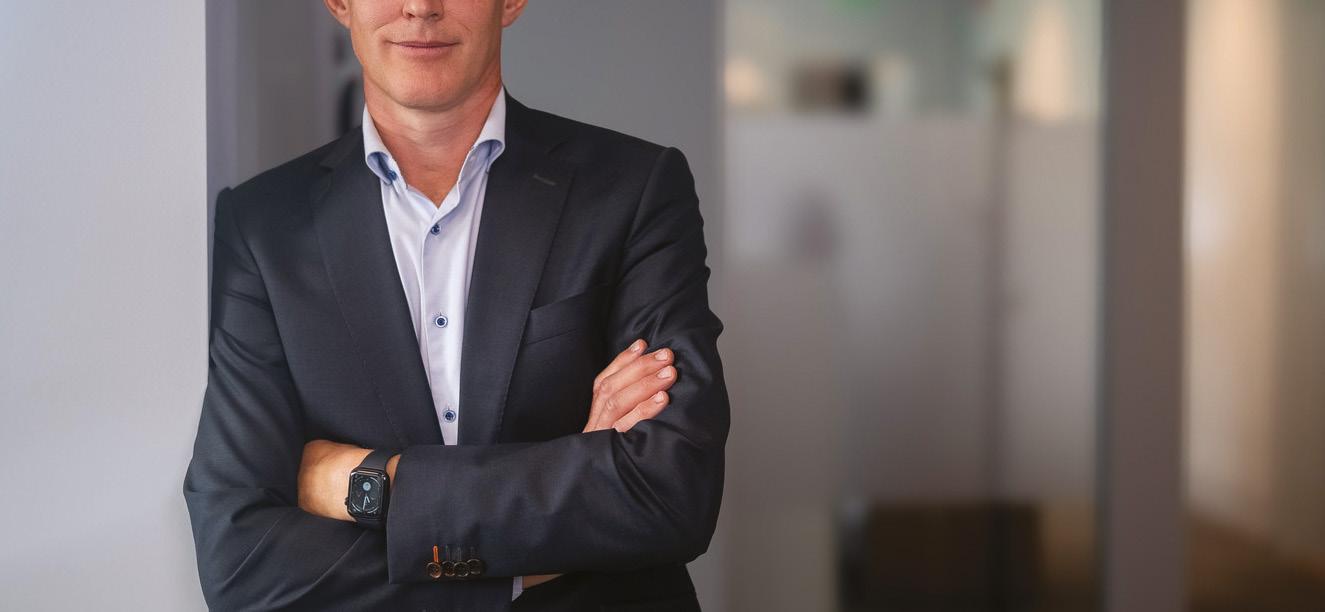
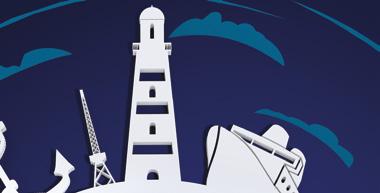

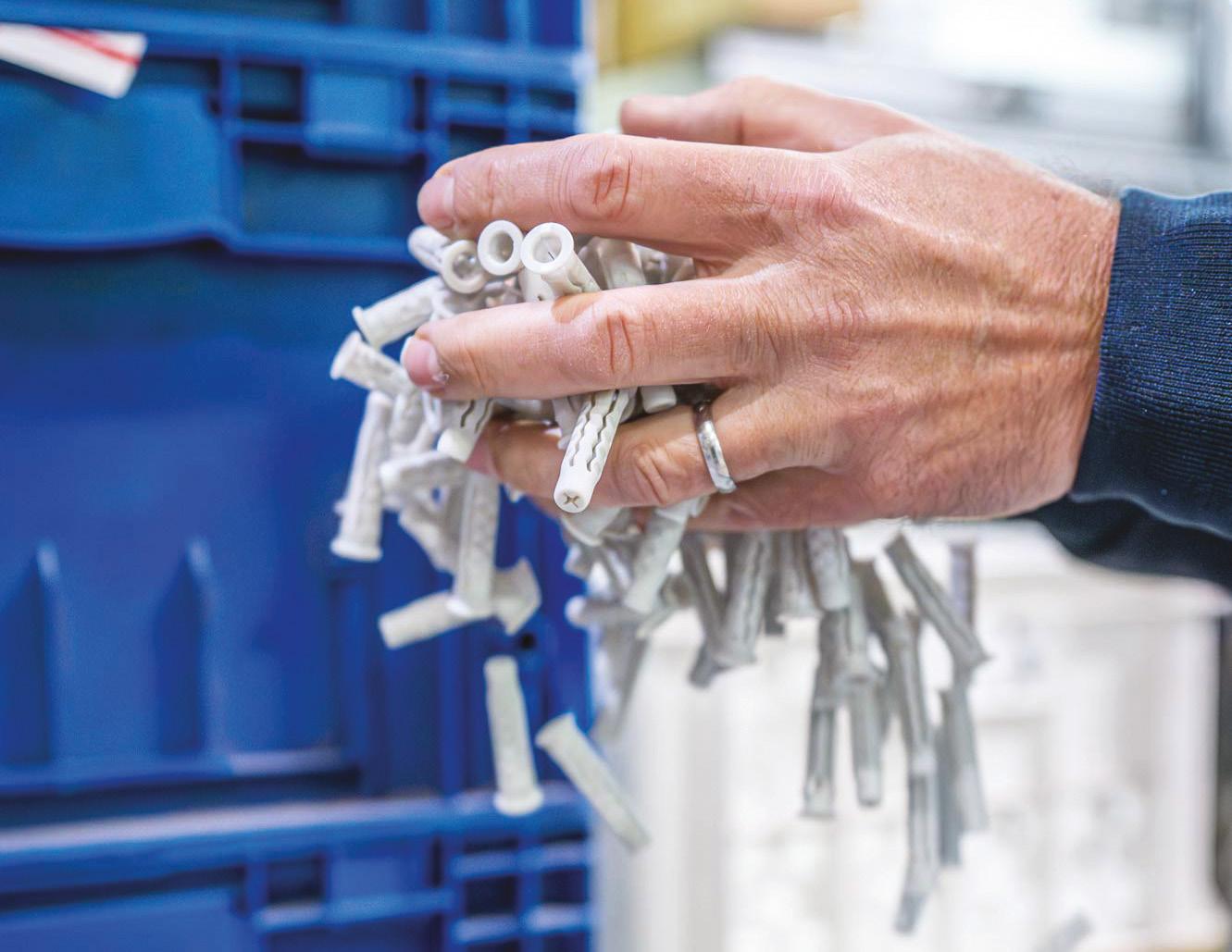

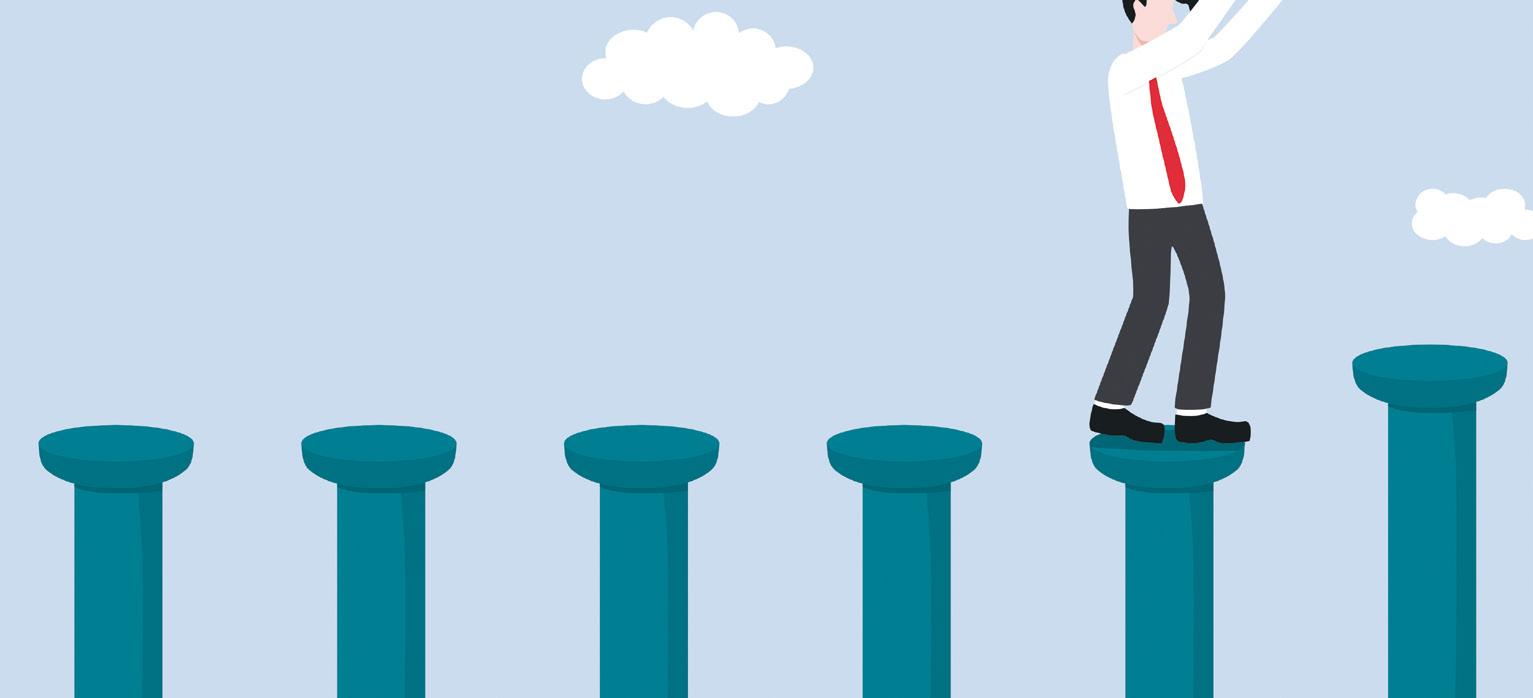
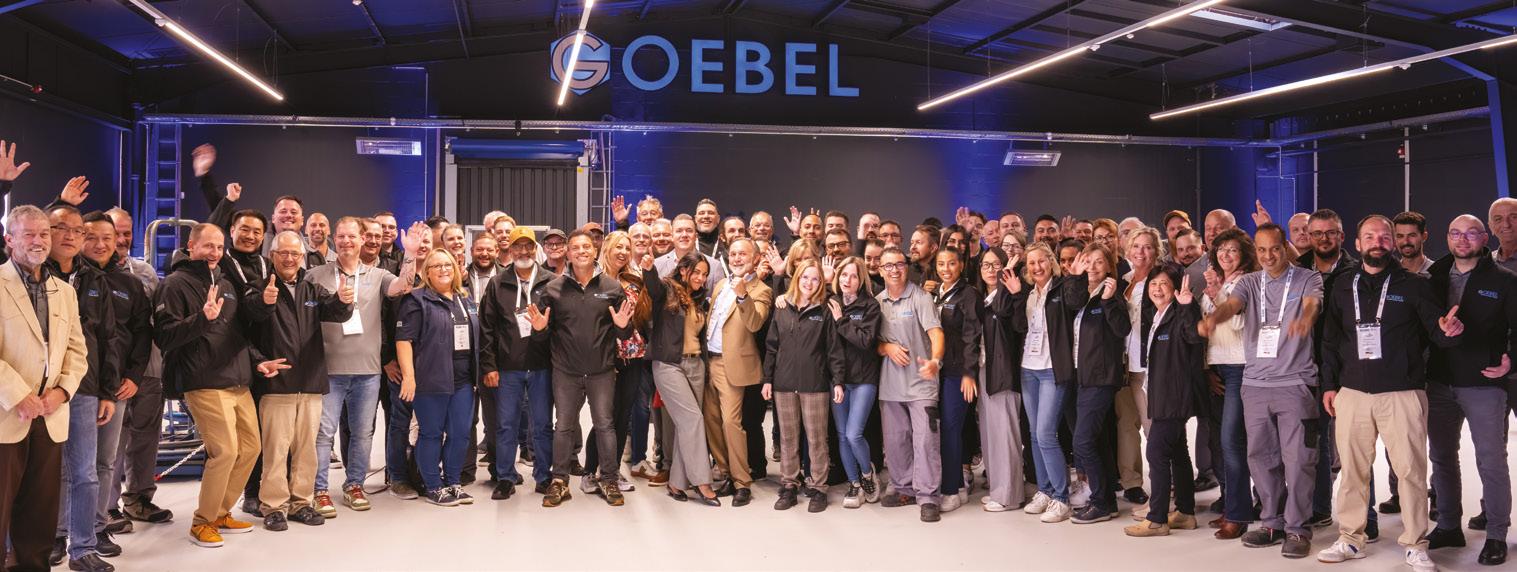
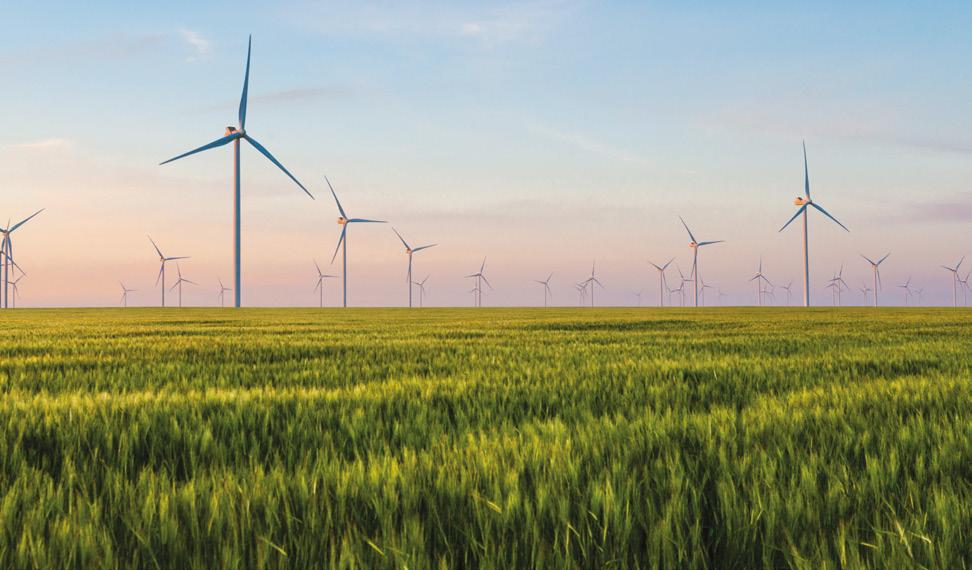
When speed and accuracy are vital, only PEM® and Haeger® deliver maximum efficiency for the most critical fastener applications. Our first-time-right solution eliminates downtime, boosts productivity, and empowers fabricators to work smarter.
LEARN MORE
This is the 150th issue of Fastener + Fixing Magazine and we are very proud to have reached such a milestone and provided breaking news and analysis on the fastener sector for over 25 years. We have established ourselves as the ‘go to’ news source within the industry and we promise to go on providing the intelligence and insight that helps inform our global readership.
Some more big news at Fastener + Fixing Magazine is that Claire Aldridge has been promoted to editor, so it will be the last time you see my (older than I would like to admit) photo on this page. Claire has been with the magazine for 12 years and has been a key part of the success and growth of the Fastener + Fixing brand, ensuring we supply the insight that we are renowned for within the industry.
I will still very much be part of the magazine and my role as content director will be to look at the strategy of the publication, and different media channels, as well as where we can provide even further analysis when it comes to the fastener and fixing industry – ensuring we focus on the topics and issues our readership want to read.
With all that in mind, I will leave it to Claire to give you a breakdown of what to expect in this special 150 th issue.
Claire Aldridge, editor
www.fastenerandfixing.com
Published by
Managing Director
Jamie Mitchell jamie.mitchell@verulammedia.com
Content Director
Will Lowry will.lowry@verulammedia.com
Editor Claire Aldridge claire.aldridge@verulammedia.com
Will Lowry, content director
Fastener + Fixing Magazine has continuously grown over the last 150 issues, thanks to a simple commitment – to keep the fastener industry better informed. In a special timeline feature, we underline some of the highlights in our journey, as well as the exclusive articles we have published to help further support our readers.
T hat commitment is even more evident in this issue, with an article in our News section on the European Commission’s decision to launch a new anti-dumping investigation, as well as an article from Alexander Kolodzik, secretary general of the European Fastener Distributor Association, who outlines how the association is continuing to help its members meet the challenges of the Carbon Border Adjustment Mechanism (CBAM) regulation.
Our Cover Story is an exclusive interview with Nord-Lock Group’s new CEO Daniel Westberg, who discusses the Group’s recent reorganisation period, as well as how Nord-Lock is actively trying to accelerate growth through investments, internal initiatives and acquisitions.
We also have a special ‘Made in eastern Europe’ feature that gives an in-depth look at the latest developments from eastern European fastener manufacturers, with an underlining theme of investments and a focus on sustainability.
Finally, we have a special ‘sealants + adhesives’ feature in Construction Fixings, a ‘renewable energy’ feature in Application Technology, an ‘inspection + packing’ feature in Manufacturing Technology, as well as a ‘tapes + adhesives’ feature in Products – it really is a busy issue.
Assistant Editor
Rebecca England rebecca.england@verulammedia.com
Sales Director Mac Rahman mac.rahman@verulammedia.com
Business Development Manager –Italy
Emiliano Pagliaroli emiliano.pagliaroli@verulammedia.com
Business Development Manager –DACH & Europe
Chantal Ridings chantal.ridings@verulammedia.com
Production & Design Manager Lee Duskwick lee.duskwick@verulammedia.com
Fastener + Fixing Magazine is a dedicated, trade–only publication which is circulated freely throughout the European trade.
Disclaimer
The Publisher cannot be held responsible or, in any way, liable for errors or omissions, during input or printing of any material supplied or contained herein although the utmost care is taken to ensure that information contained is accurate and up to date. The Publisher also cannot be held liable for any claims made by advertisers or in contributions from individuals or companies submitted for inclusion within this publication. The opinions expressed are not necessarily those of the Editor or Verulam Media.
Copyright Entire contents copyright © Verulam Media Ltd 2024. No part of this publication may be reproduced, stored in a retrieval system, or transmitted in any form or by any means without the prior permission of the publisher.
Annual subscription (6 issues) to non–trade and outside EU is €200.00 Verulam Media Limited, Office 3, 17 Holywell Hill, St Albans AL1 IDT Tel: +44 (0) 1727 743 882 Find us online:
The European Commission has given notice of the initiation of an anti-dumping proceeding, concerning imports of screws without heads, originating in the People’s Republic of China.
Published on 17 th October 2024, the product subject to this investigation is screws and bolts, with or without their nuts and washers, without heads, of iron or steel other than stainless steel, regardless of tensile strength – excluding coach screws and other woodscrews, screw hooks and screw rings, self-tapping screws, as well as screws and bolts for fixing railway track construction material.
The notice reports: “The European Commission has received a complaint pursuant to Article 5 of Regulation (EU) 2016/1036 of the European Parliament and of the Council of 8 th June 2016 on protection against dumped imports from countries not members of the European Union, alleging that imports of screws without heads, originating in the People’s Republic of China, are being dumped and are thereby causing injury to the Union industry.”
“The product allegedly being dumped is the product under investigation, originating in the People’s Republic of China, currently classified under CN codes 7318 15 42 and 7318 15 48. The CN code is given for information only
and without prejudice to a subsequent change in the tariff classification.”
“The investigation of dumping and injury will cover the period from 1 st July 2023 to 30th June 2024 (‘the investigation period’).
The examination of trends relevant for the assessment of injury will cover the period from 1 st January 2021 to the end of the investigation period (‘the period considered’).”
The full notice can be viewed online.
LISI Group achieved sales of €1.323 billion for the first nine months of 2024, up 8.6% compared to 2023, with LISI AEROSPACE up 20.7% on the same period and LISI AUTOMOTIVE and LISI MEDICAL finishing down 4.6% and 0.6% respectively.
LISI AEROSPACE sales totalled €742.2 million in the first nine months of 2024. The ‘Fasteners’ segment continued to benefit from the ramp up in single aisle aircraft production rates, and from strong demand for maintenance services linked to the sustained traffic in the commercial aircraft fleet. Third quarter sales rose by 26.8% in Europe and 22% in the United States, despite an unfavourable currency effect.
The resilience of the global commercial aeronautics market is reflected in high order levels, particularly at Airbus. Nevertheless, production rate increase ambitions have been postponed due to tensions throughout the aeronautical supply chain. The strike at Boeing since early September has halted assembly of the B737 MAX –around 38 aircraft per month. Although this stoppage has not yet had a significant impact on LISI AEROSPACE in the third quarter, it will weigh on general demand.
LISI AUTOMOTIVE division sales came to €447.2 million in the first nine months of 2024, down 4.6% on the same period in
2023. This takes into account the accelerated decline in sales in the third quarter, down 9.1% compared with the same period last year, particularly noticeable among OEMs.
LISI MEDICAL division sales came to €134.3 million in the first nine months of 2024. They were virtually stable, down 0.6% compared with the same period in 2023.
LISI AEROSPACE has appointed Equity Energies to deliver bespoke energy management and decarbonisation solutions to further advance its net zero progress in the UK.
Through its consultancy offer, and proprietary technology, Equity Energies will develop and deliver a tailored energy management strategy and net zero pathway, helping the business meet the growing demand for emissions reductions while accelerating its decarbonisation through energy efficiency and waste reduction.
www.achill-fasteners.com
Bulten Group has reported net sales amounted to SEK 1.33 billion (€1.3 billion) for the third quarter of 2024, a decrease of 3.3% on the same period the previous year. Adjusted operating earnings totalled SEK 91 million (€7.8 million), equating to an adjusted operating margin of 6.8%.
Christina Hallin, interim president and CEO, highlights: “The reported operating earnings for the third quarter are an improvement on the corresponding quarter of 2023 and on the previous quarter this year. This is a clear sign that our efforts over the past year to stabilise and streamline production, combined with a focus on reducing our costs, are paying off. The operating margin has improved during Q3, which is generally a weaker quarter as there are fewer days of production. The margin has been positively impacted by non recurring items, including insurance compensation relating to machinery in Poland. Our long-term ambition to have an operating margin of 8% remains, although this will be difficult to achieve for 2024 as a whole.”
She continues: “There has been a slight decline in demand for fasteners from vehicle manufacturers in all markets during the quarter. The falling demand is largely due to a decrease in vehicle sales, but also
to the fact that some of our larger customers are shifting platforms, thus affecting their Q3 2024 net sales production volumes in the short term.”
“In addition, there are other disruptions in OEM supply chains, which impact on our sales volumes. Although the market is not growing at the same rate as before, we now have an operation that is more stable and flexible, which is able to handle large fluctuations. The fall in demand gives us the opportunity to review our customer base and focus on customers and segments where we see better margins. It also enables us to review our customer contracts and phase out any unprofitable ones, something we have been doing during the quarter. We have also begun to reduce working hours in a couple of factories and we are working on a number of minor structural issues, including a review of some of our joint ventures. We cannot rule out additional structural changes moving forward, if they are necessary to further improve profitability levels,” concludes Christina.
Bufab Group has reported that in the third quarter its net sales declined by 9.2% to SEK 1.8 billion (2023: SEK 2.07 billion), with organic growth down 2.6%.
Demand in the quarter remained cautious, with continued large variations between different industries and regions. Similar to previous quarters, the strongest developments were noted in energy and defence. Organic growth amounted to -2.6%, indicating an improvement to the previous quarter (-6.6%). The region Asia-Pacific showed a new trend with organic growth of a strong 13.2%, driven by particularly strong growth in China.
Erik Lundén, president and CEO at Bufab, comments: “We have continued our efforts to strengthen the gross margin, which increased by 1.6% in the quarter to an all time high of 30.6%. The gradual strengthening over the past few quarters is a result of the long-term work that began in 2023 to improve our customer and product mix, develop our value creation for customers, as well as achieve purchasing savings.”
“The adjusted operating margin was in-line with last year, amounting to 12.7% (2023: 12.6%), which is a stable level given the challenging market conditions. Our dedicated work with cost control throughout the organisation have yielded the expected results, primarily due to staff reductions, but also reduced overhead costs. At the same time, we continue to invest in driving growth and improving profitability in the long-term and have continued to invest in our customer offering during the quarter.”
He continues: “Uncertainty regarding the general economic outlook remains, but we see indications of improved demand from general industry, likely not until the first half of 2025. At the same time, a weaker economy creates favourable conditions for a strong player such as Bufab to take new market shares. This, together with our focused work on strengthening our gross margin and on cost savings, will put us in a strong position once the market rebounds.”
With over 20 years of experience from management, sales, strategy, business development, and international business, in several global manufacturing companies, Martin Dahlgren has become the new managing director of BUMAX Sweden AB.
Martin joins BUMAX from a position as head of linear motion Asia Pacific at motion technology group Schaeffler and has a broad range of experience in developing and leading OEM brands across the EMEA and APAC regions, through various managerial positions with companies including Ewellix, SKF Group, Thule Group and Volvo Cars. Martin also holds a degree from Chalmers University of Technology, with further studies at London Business School and China Europe International Business School.
He comments: “I am thrilled to join the global leader in fastener technology. BUMAX is such an innovative company, whose high strength stainless steel fasteners help many companies to unlock new design capabilities, improve the performance and durability of its products, while supporting industry sustainability goals.”
Berardi Group, a portfolio company of H.I.G Capital, has completed the acquisition of Italian-based Fixi Srl – a distributor of fastening systems offering a wide range of products such as rivets, threaded inserts, self-clinching fasteners, welding studs and related professional equipment.
With depots in Veneto, Emilia Romagna, Marche, and Abruzzo, Fixi serves over 2,000 industrial customers in Italy and across Europe. The transaction represents a significant step in Berardi’s growth strategy, aiming to enrich the range of products and services offered to its customers through strategic acquisitions of distributors specialised in high potential product categories.
The acquisition will strengthen Berardi’s position as a national leader in the fastening systems category, a segment in strong growth for its customers. It will also improve the geographic coverage and service in Italy and throughout Europe, to the benefit of its customers.
“The partnership with Fixi is a step of enormous importance in the growth path that we have outlined for our Group, which will enable us to
have a greater geographical presence and to provide our customers with a product portfolio and a range of services suited to their every need,” underlines Giovanni Berardi, chairman of Berardi, and Mauro Pasini, CEO at Berardi Group.
Maurizio and Alessandro Mora, majority shareholders and CEOs of Fixi, added: “We are excited about our new partnership with Berardi, the undisputed leader in the distribution of industrial components in Italy. Our history and shared culture of excellence, innovation and maximum attention to our customers and employees enables us to fully leverage our specialist skills in fastening systems and seize new growth opportunities that will enable us to accelerate the development of the business.”
NORMA Group achieved a sound level of profitability in the third quarter of 2024 despite a difficult market environment. Group sales in the third quarter were down 7.9% over the prior year to €273.6 million (2023: €297.1 million)
NORMA reports that business with joining technology for vehicles – Mobility & New Energy, suffered under a weak global automotive industry with low production figures for cars and trucks. Sales in the Water Management sector, on the other hand, remained stable at a high-level. The Industry Applications business unit was especially impacted by the persistently weak economy in large parts of Europe and in China.
In the Americas region, sales in the third quarter fell by 1.2% year-on-year to €131.3 million due to negative currency effects in
connection with the US dollar (Q3 2023: €132.9 million). Adjusted for currency effects, sales development was slightly positive (up 0.1%).
In the EMEA region sales amounted to €108 million in the third quarter of 2024, down 9.4% on the prior year figure (Q3 2023: €119.3 million).
In the Asia-Pacific region, third quarter sales were down 23.9% to €34.2 million (Q3 2023: €45 million). Currency effects had a slightly positive impact here. Business with customers in the Chinese automotive industry (Mobility & New Energy) declined significantly.
Hilti Group reported sales growth of 1.9% in local currencies over the first eight months of the 2024 business year. Consistently negative currency effects impacted sales and resulted in a decrease of 1.1% in Swiss francs compared to the same period last year. The operating result grew by 4.9% to CHF 489 million (€520 million).
Business development over the first eight months of 2024 was largely influenced by a challenging market in central and northern Europe (up 0.2% in Europe in local currencies). In the Americas, Hilti Group recorded a slight increase of 1.2%. In Asia-Pacific the company was able to grow by 5.5%, while the EMEA region continued to grow strongly, at 11%.
“We expect the market environment to continue to vary strongly, from negative in our home market of central Europe to positive in Asia-Pacific and the Middle East. With our business model, we can successfully navigate these uncertain times,” explains Jahangir Doongaji, CEO at Hilti Group.
Hilti recognised as carbon management leader
Hilti Group has achieved a Gold rating in the EcoVadis assessment for the fourth consecutive year, placing the company in the top 2% of over 130,000 companies evaluated across all industries worldwide and in the top 1% in the industry segment.
EcoVadis has once again declared Hilti to be a ‘leader in carbon management’ and a ‘company with a best-in-class greenhouse gas management system and strong ambitions for decarbonisation’. This outstanding rating is also based on Hilti’s commitment to the Science Based Targets initiative (SBTi), which aims for a significant carbon footprint reduction by 2032 and net zero emissions by 2050.
“We are honoured to see our efforts in sustainability once again recognised,” says Jahangir Doongaji. “We will continue to diligently work on our initiatives to be our customers’ best partner for sustainability.”
On 1 st January 2025, Marc Schaad, the longstanding CTO, will take over operational management of Kistler Group from Rolf Sonderegger, who has led the group as CEO for 22 years.
Marc Schaad is a mechanical engineer and graduate of the Swiss Federal Institute of Technology Zurich (ETH). In his current role, he has played a crucial part in Kistler Group’s ongoing development. He has been responsible for research and development, has headed a business unit and, at the beginning of 2024, he added strategic product management to his remit. Thanks to his wide-ranging experience in these key areas, Marc Schaad is excellently qualified to continue Kistler Group’s successful development.
Marc Schaad comments: “Kistler’s DNA and values remain unchanged: A family run company with a long-term strategic vision that focuses on cutting edge technology to meet the challenges of today’s and tomorrow’s customers. I look forward to continuing this success story with a highly motivated Kistler team.”
Under the leadership of Rolf Sonderegger, Kistler Group has evolved from a component manufacturer into a global provider of complete measurement technology solutions for highly dynamic applications. The company was founded at Winterthur, Switzerland, in 1959 by Hans Conrad Sonderegger (Rolf Sonderegger’s father) and Walter P Kistler. In 2002, Rolf Sonderegger assumed overall responsibility as CEO and delegate of the board of directors, acquiring Walter P. Kistler’s shares at the same time. Driven by a targeted growth strategy and strategic acquisitions, the company has achieved sustainable growth of over 500% and created more than 1,500 jobs.
Joint administrators from BDO have completed a sale of two divisions of The Electrolytic Plating Company Limited (EPC) to Wolverhampton Electro Plating Limited, part of the Anochrome Group of Companies.
Kerry Bailey and Lee Causer of BDO were appointed as joint administrators of EPC – an electrolytic plating, high performance surface coatings and metal finishing business –on 5 th September 2024. A sale of two divisions, and certain assets of the business, was completed immediately following their appointment to Wolverhampton Electro Plating Limited.
The remaining business has ceased to trade and certain employees have been made redundant. Kerry Bailey, one of the joint administrators, said: “The Electrolytic Plating Company Limited has traded for over a century, but it has had to navigate a number of financial challenges, particularly since the Covid-19 crisis. We are delighted that the sale of the two divisions and certain assets will see the business continue, securing the continued employment for the divisional employees. Regrettably, the administration has also resulted in a number of redundancies and the administrators are supporting affected staff members with their statutory redundancy claims. We are now taking steps to maximise the remaining assets of EPC for the benefit of creditors, in-line with our duties.”
“As the years have gone by, we have worked together to surmount half a dozen crises, overcome various setbacks and celebrate some extraordinary successes. Growth has been the keynote in 19 out of the last 22 financial years – years that have been magnificent and thrilling, but always challenging. However, there is a time for everything, so I will be stepping down as CEO at the end of 2024,” outlines Rolf Sonderegger.
Rolf Sonderegger will remain the majority owner of Kistler Group and he will take over as chairman of the board of directors from Valentin Vogt in spring 2027 after a two year sabbatical.
To significantly expand its presence in Germany and eastern Europe, Bossard Group has signed an agreement to acquire Ferdinand Gross Group.
Headquartered in Leinfelden-Echterdingen, Ferdinand Gross is one of the leading distributors of fastening technology in Germany and is celebrating its 160 th anniversary this year. The Group employs around 260 people and also operates in locations in Hungary and Poland.
With the contemplated acquisition of the Ferdinand Gross Group, which expects net sales of around €80 million for the current financial year, Bossard will be able to better serve its customers in Germany and eastern Europe even more comprehensively.
“I eagerly look forward to the upcoming collaboration with our new colleagues. The planned acquisition of the Ferdinand Gross Group not only brings together two companies with a long tradition, but also two strong partners who share common values and business philosophies – in the spirit of ‘Proven Productivity’,” comments Daniel Bossard, CEO of Bossard Group.
We offer a range of socket head cap screws, socket countersunk head screws, socket button head screws, socket sets, socket shoulder screws, taper pressure plugs and socket wrenches. Available in a range of sizes from M1.6 - M30.
Socket Screws Available in
Finish: Self-Colour, Bright Zinc Plated, Galvanised, A2 and A4 Stainless Steel
Grade: 10.9 and 12.9 Steel
Metric and Imperial
Head Type: Button, Button Flange, Cap, Countersunk and Low Head Cap Standard: DIN 912, 7991, ISO 7379, 7380-1, 7380-2, 10642 and ANSI B18.3
Socket Sets Available in
Finish: Self-Colour, Bright Zinc Plated, A2 and A4 Stainless Steel Class: 45H Steel
Point Type: Flat, Cone, Dog, Plain Cup and Knurled Cup Standard: DIN 913, 914, 915 and 916
Products are available for free-next delivery, with low minimum order levels, across the majority of the UK mainland.
On 1 st October 2024, Reinhold Würth, chairman of the supervisory board of the Würth Group, celebrated his 75th work anniversary during a ceremony at Carmen Würth Forum in the German town of Künzelsau.
From a hardware wholesaler with two employees to a global market leader with more than 88,000 employees, family and friends, numerous guests from the worlds of politics, business and the arts, as well as the company management, congratulated Professor Reinhold Würth on this impressive milestone.
“I stand before you, immensely grateful, and in all modesty and humility, knowing that I would never have achieved the success we are seeing today without the hard work and the loyalty of these 88,000 people from all these different cultures, different backgrounds, with different nationalities and different religions,” outlined Professor Würth at the ceremony.
German Chancellor Olaf Scholz also offered his congratulations: “It is thanks to entrepreneurs like Reinhold Würth that Germany has such a strong economy. His entrepreneurial courage and his tireless commitment to the company and its employees are impressive and deserve my respect and admiration. The company’s success is exemplary of one of the most important pillars of Germany as a business location.”
Nord-Lock south-east Asia and Taiwan, part of the Nord-Lock Group – the world’s leading provider of advanced bolting and engineering solutions, has announced the inauguration of its regional office in Q Sentral, located at the heart of the capital’s transportation hub, Kuala Lumpur Sentral.
Nord-Lock Group’s move to relocate its regional office from Singapore to Kuala Lumpur underscores the market leader’s commitment to expand its presence and it will serve as a hub for its operations in the Asia-Pacific region, to better serve its customers and partners.
Norbert Hentschel, head of Asia-Pacific at Nord-Lock Group, explains: “Nord-Lock Group’s investment in this new regional office underscores our long-term vision for growth in Malaysia. Over the years, Malaysia has emerged as a key market for us, offering a skilled workforce, strategic location, as well as a conducive business environment. This relocation strengthens our presence in the region and marks the start of an exciting chapter in Nord-Lock Group’s journey to establish closer relationships with our distributors, strengthen our global presence and deliver excellence to our customers regionally.”
Robert Lejon, deputy head of mission of the embassy of Sweden to Malaysia, who was at the inauguration event, agreed with Norbert Hentschel. “Through safe bolted connections, Nord-Lock Group provides a critical component that holds modern society together, and through its decision to expand and invest, it is also bringing Sweden and Malaysia closer together. This will open more doors for growth in business and cooperation between our nations, providing more job opportunities in both our countries respectively. We are excited about the opportunities this move will bring and look forward to mutual success.”
The Malaysian office will be helmed by Kang Tzee Chang, general manager, Nord-Lock south-east Asia and Taiwan. Kang Tzee Chang comments: “Our new office in Kuala Lumpur represents a significant milestone for Nord-Lock as we continue to expand our footprint in south-east Asia. We are committed to investing in Malaysia, fostering local talent, and contributing to the country’s economic development. This
move is a testament to our belief in the immense potential of the Malaysian market.”
Nord-Lock takes a long-term view of its presence in Malaysia with plans to continue investing in its operations, as well as establishing a regional distribution centre by the end of the year. Kang continues: “Our Malaysian office is staffed by a dynamic and professional workforce with in-depth expertise – our plan is to further expand this established and experienced team.”
Standard and non-standard items
Norm- und Standardteile
DIN, ISO, EN and others / und andere
Special parts and special materials
Sonderteile / Sonderwerkstoffe
The perfect union occurs when everything fits
To expand its European spring supply solutions, Lesjöfors Group has acquired Ressorts Lacroix –a French-based manufacturer of springs and wire parts for customers within the hydraulic, automotive, aerospace and medical sector.
The completion of the purchase of Ressorts Lacroix builds on a strategic growth plan for Europe. Yohan Dutheil, CEO of Ressorts Lacroix, highlights: “Our potential is now limitless and with Lesjöfors as a global parent company, we are able to access new markets and give a greater reach.”
Qingdao Fervi International Trading Co Ltd is the latest addition to the FERVI Group, marking a significant milestone in its global expansion strategy.
Based in Qingdao, one of China’s most vital port cities, this new subsidiary is strategically positioned to enhance logistics and streamline the Group’s ‘go to market’ efforts, reinforcing its commitment to international growth.
The fischer group of companies has acquired a majority stake in its trading partner SEEFELDER GmbH – a specialist retailer for fittings, tools and assembly technology.
With the majority shareholding, fischer is further expanding its product range and services for retailers and will work together with SEEFELDER to develop new product ranges, product innovations and service concepts.
As of 23 rd October 2024, Mungo Befestigungstechnik AG has been acquired by a group of investors with extensive international industrial expertise.
The acquisition also brings changes in Mungo’s executive leadership, with Mr Claude Mion announced as Chief Executive Officer, with a vision to unlock synergies that will reestablish Mungo as one of the most influential global players in the fastening industry.
SFS Group has acquired EPRO d.o.o, a longtime distribution partner for high-end applications to the building envelope in Slovenia, further strengthening the Group’s presence in the Adriatic region.
EPRO is a family run company specialising in the distribution of fasteners, fixings, fall protection systems and accessories for flat roofs, roofing and façade elements. The company generated sales of approximately €4 million in 2023 with about ten employees.
Fastener supplier Rapierstar is supporting a Scottish window and door manufacturer and installer to realise its growth ambitions by keeping its product quality and factory productivity on track.
Precision Windows has always used Rapierstar fasteners to manufacture its PVC-U product range, because the team recognises the value of quality components and profiles in achieving a competitive advantage, including the Veka FS70 fully sculptured and M70 bevelled systems.
As part of the UN Global Compact Leaders Summit, which took place from 24th – 25th September in New York, USA, representatives from Norm Holding presented a waste energy recovery project as part of the SDG Innovation Accelerator for Young Professionals.
The UN Global Compact Leaders Summit aims to bring together opinion leaders and business pioneers in the field of sustainability on the global stage, with the Norm team gathering significant praise for the project proposal on waste energy recovery.
The Norm Holding team included Senior Sustainability Specialist İzel Özgür Tekeli, Method Engineer Elif Yegen, Strategy and Business Development Specialist Berk Akşit, under the leadership of Sustainability and Management Systems Director Muhsin Doğan.
“We place great importance on supporting the transformation and development of society and the business world, especially our customers. While driving this transformation with high value added, high-quality, safe and innovative products, we also support the development of the sectors and regions in which we operate through the responsible investment approach we have adopted,” underlines Mustafa Sabri Doğrusoy, sustainability committee chairman at Norm Holding.
He added: “Sustainability is critical in every department and area of our company, serving as a core focus across all our business processes.
The project presented at the Leaders Summit, developed through the collaboration of our colleagues from sustainability, strategy, and methodology departments, holds special significance as it reminds us once again that sustainability is a responsibility shared by all departments and, indeed, by all of us.”
by Jason Sandefur, editor/publisher, GlobalFastenerNews.com
The global industrial fastener market, valued at US$91.34 billion (€83.9 billion) in 2023, is projected to grow at a CAGR of 3.5% through 2030, according to Maximize Market Research.
The industrial fastener market is witnessing significant trends, including the miniaturisation of fasteners – to meet demand for compact and multifunctional products in industries such as consumer electronics, healthcare and automotive.
Additionally, there is a growing focus on innovative fastening technologies that enhance functional permanence and operational efficiency. The trend towards sustainability is also influencing the market, with a shift towards using environmentally friendly materials and processes in fastener production.
Opportunities are emerging from the increasing demand for lightweight and durable materials, particularly in the automotive and aerospace industries. The push towards electric vehicles and advancements in renewable energy infrastructure also present new avenues for growth.
The adoption of smart manufacturing technologies, and the development of customised fastener solutions for specific applications, are additional opportunities that market players can leverage. The Asia-Pacific region accounts for over 45% of total output. The region’s manufacturing sector is growing rapidly, driven by significant foreign investments and favourable economic conditions.
The seasonally adjusted Fastener Distributor Index (FDI) improved to 53.8 in August (July 47.5), “mainly on a recovery from last month’s abysmal sales reading, much slower supplier deliveries and slightly higher pricing,” wrote R.W. Baird Analyst David Manthey with Quinn Fredrickson.
Sales, supplier deliveries and customer inventories drove the improvement, while employment remained flat. Nearly four in 10 respondents (35%) indicated sales came above seasonal expectations compared to just 22% last month and the 34% average over the past year. An equal amount of respondents said sales were in-line with expectations.
The fastener industry is working with manufacturing customers to seek new ways to reduce vehicle weight – by reducing the number, type and weight of fasteners, Design News reports. In terms of number of parts in a vehicle, fasteners can be up to 50% of the vehicle’s Bill Of Material (BOM).
Reducing the number of fasteners through innovative fastener technology helps manufacturers meet new Corporate Average Fuel Economy (CAFE) standards, requiring an industry wide fleet average of 50.4 mpg for passenger cars and light trucks, by 2026.
There are several ways fastener manufacturers are helping automotive OEMs innovate to improve performance, according to Design News, including:
Optimising production with advanced raw materials to enable manufacturers to produce high performance, cost-effective lighter weight products – with better fuel efficiency and enhanced performance.
Working in an integrated fashion that combines design, analysis and optimisation techniques for lightweighting products, at the request of OEMs.
Redesigning fasteners, moving to lightweight materials, such as going from steel to aluminium, to reduce weight in areas like non-structural rivet applications.
As part of CAFE efforts, the fastener industry is continuing to do its part to introduce methods reducing weight in vehicles by consolidating parts; redesigning and reengineering fasteners; using alternative materials; and generally thinking of new ways to reduce weight and increase performance.
Weidmuller USA recently introduced BOLTcontrol, a monitoring that detects broken bolts or studs in the wind blade root that connects to the hub, alerting operators immediately of any issues.
With BOLTcontrol, broken bolts are held securely in place with detection plates, which prevent consequential damage that would result if pieces fell into the hub and ricocheted as it rotated. By continuously monitoring the rotor blade bolts, BOLTcontrol minimises downtime, reduces repair costs and ensures the safe uninterrupted operation of the turbine.
“The bolted connections between the hub and the rotor blade are constantly subjected to dynamic loads in a wind turbine,” explains Pete Tecos, director of new energy solutions at Weidmuller USA. “Stud and bolt failures have become more common and BOLTcontrol not only alerts operators to blade root fastener failures, but also prevents the fractured components from falling into the hub, thereby avoiding costly damages to the pitch systems and other critical components.”
Primary benefits of BOLTcontrol includes prevention of damage – holds broken bolt securely in place to avoid damage to hub and components; ensures continued operation – improves safety at the turbine site and a reduction of climbs for needed repairs; safe and economical – reduces downtimes and control operation and maintenance costs by continuously monitoring the blade bolts; as well as being quick and easy to retrofit – adaptable and can be customised to different turbine types.
“Using ‘real time’ data at the site, decision making can significantly improve with BOLTcontrol. This helps operators prioritise inspections based on conditions of the blade root connection and be one step ahead of maintenance and service needs.” highlights Pete
R.J Leahy Company Inc, a 96 year old fastener distributor in San Francisco, has closed permanently after filing for Chapter 7 bankruptcy.
The storied company supplied metal fasteners that “held together WWII-era ships, Disneyland art commissions, and historical renovations of restaurants, residences and San Francisco City Hall,” according to the San Francisco Business Times.
Founded in 1928 by Ray Leahy Sr, the company prospered in the growing maritime and military industries by offering non-ferrous fasteners, as well as copper and brass metal products. As those industries faded in the Bay Area, R.J. Leahy supplied fasteners and metal products to contractors, architects, artisans, and metalsmiths, looking for vintage fasteners.
By studying the financial reports from 2021 to 2023 in Commonwealth Magazine Issue 798 (May 2024), Fastener World Magazine has created a table for the top Taiwanese fastener companies in 2024. Units of revenue, profit after tax, and total assets, are in NT$ 100 million.
During its production and sales meeting for Q4 2024, on 3rd September 2024, Taiwan China Steel Corporation (CSC), the largest integrated steel maker in Taiwan, reported on the status of the global economy and Taiwanese fastener industry to more than a hundred business owners and professionals working in the fastener, wire rod, surface treatment and machinery industries.
As part of the briefing, the National Development Council of Taiwan announced that Taiwan’s leading indicators and concurrent indicators continued to rise, showing that the domestic economy maintains a growth trend. As of July, Taiwan’s purchasing managers’ index had exceeded the boom-bust line for three consecutive months and remained in an expansion state. Export orders had achieved positive growth for five consecutive months.
The cumulative export orders value from January to July this year increased by 2.7% compared with the same period last year. The IMF, Taiwan Institute of Economic Research, and other institutions also predicted that Taiwan’s GDP growth rate in 2024 will exceed 3% and be up to as high as 3.9%.
In the first seven months of 2024, Taiwan CSC imported 277,000 tonnes of wire rods from around the world, an increase of 34% from
206,000 tonnes over the same period last year. Among them, 33% of wire rod imports were from Indonesia, 21% from South Korea, 12% from India, 11% from China, 8% from Japan, and 7% from Vietnam. The materials of imported wire rods were mainly low carbon steel (accounting for 50%) and alloy steel (42%).
According to statistics from the Taiwan Industrial Fasteners Institute, the export weight of fastener products in the first seven months of 2024 was 740,100 tonnes, a year-on-year decrease of 2.77%. The average export unit price was US$3.5, an annual decrease of 8.05%. Although Taiwan’s fastener export weight to Germany dropped by 13.31%, the export weight to the USA, Japan and Canada increased by 1.83%, 0.4% and 22.17% respectively. As of the second quarter of 2024, Taiwan’s fastener export weight to the world achieved a
of 1.6%.
Chinese new energy vehicle manufacturer, BYD Company Ltd, expects to sell 50,000 electric vehicles in Mexico this year and aims to achieve a sales target of 100,000 by 2025, with plans to open its first factory in Mexico.
It is reported that the initial production capacity of this new factory will reach an annual output of 150,000 electric vehicles, with potential expansion to an annual output of 300,000 in the future, demonstrating BYD’s confidence in the development prospects of the Mexican market.
Jorge Vallejo, general manager of BYD Mexico, stated that the company expects to announce the location of this factory by the end of this year.
On 10 th October 2024 the Yongnian International Sourcing Fair of Fasteners was successfully held, establishing a deep communication bridge for the fastener industry in Yongnian to access the international market, as well as inject new vitality into the integrated development of regional industrial clusters and high-quality growth in foreign trade.
With the theme of ‘Connecting Global Fastening Force to Build Yongnian Purchasing Festival’, the event attracted industry professionals from around the world. Through a series of carefully planned activities, such as business matchmaking meetings, product exhibitions, and technical exchanges, the event provided a precise matching platform for global fastener enterprises, enabling efficient communication and cooperation between suppliers and buyers.
The event not only broadened the international market horizons of Yongnian’s fastener enterprises, but also provided global buyers with direct access to the latest technologies and high-quality products in China’s fastener industry, further enhancing the international competitiveness of Chinese fasteners.
The successful hosting of the event significantly increased the international reputation and brand influence of Yongnian’s fastener products. Driven by the fair, the synergistic effects within Yongnian’s fastener industrial cluster became more pronounced, actively guiding enterprises towards high-end, intelligent and green development. At the same time, the event also encouraged enterprises to adopt international standards, improve product quality and service levels, as well as promote the transformation of the entire industry towards a higher quality foreign trade development model.
China’s Zhejiang Geely Holding Group Co Ltd has signed a cooperation agreement with Vietnamese enterprise Tasco, planning to construct a joint venture automotive assembly plant in Thai Binh Province, Vietnam.
The total investment for this joint venture project is expected to be approximately US$168 million, (€156 million) with Geely contributing 36% of the capital.
I nitial annual production capacity of the joint venture is expected to be 75,000 vehicles, primarily assembling models under the Lynk & Co and Geely brands, with potential expansion to other brands in the future. The new plant is expected to commence construction in the first half of 2025, with the first batch of vehicles anticipated for delivery in early 2026. Meanwhile, Tasco’s subsidiary, Tasco Auto, will become the official dealer for the Geely brand.
In the first half of 2024, Geely’s cumulative export sales reached 197,428 vehicles, marking an increase of over 67% compared to the previous year. Based on this strong market performance, Geely has revised its annual sales target for 2024 to 2 million vehicles. The collaboration with Tasco will undoubtedly further propel Geely’s strategic layout and development in the international market.
By Fasteners India
Super Screws Pvt Ltd, one of the leading Indian bolt manufacturers, has announced the signing of a Memorandum of Understanding (MoU) with Mitsuchi Corporation, an Japanese-based provider of custom fasteners for automotive components in Japan.
The MoU aims to establish a joint venture for setting up a new plant in India focused on the manufacturing and sale of special cold forged parts. The joint venture highlights Super Screws’ intent to fulfil the rising needs of local Japanese companies and the burgeoning Indian market.
SK Kapoor, chairman at Super Screws, comments: “Super Screws has always been in pursuit of new and advanced technologies. This new partnership strengthens the engineering competence of the company and accelerates the localisation and manufacturing of cold forged parts for the Indian market and global exports.”
Reiterating similar sentiments, Samrat Kapoor, director at Super Screws, highlighted key offerings from both the parties. He mentioned Super Screws’ expertise in value focused engineering, manufacturing processes, and customer connections, as well as Mitsuchi’s technical know-how, global experience, and future technology access and how they create a formidable platform for success and growth in India.
Sundram Fasteners has reported its standalone net profit for the first quarter of 2024 increased by 17% year-on-year to INR 131.64 crore (€14 million) compared to the INR 112.78 crore during the same period of the last fiscal year. Profit before tax reached the highest for the company, reaching INR 177 crore for the period, an increase of 17.4% on the previous year.
Earnings before interest, depreciation, and taxes (EBITDA) for the quarter were INR 223 crore, and the margin was at 17%. Gross margins showed an enhancement due to growth in exports, comparatively sound commodity prices and a favourable product mix. Operations revenue even grew to a record INR 1,310.33 crore, up 7.7% from the previous year. Domestic sales were up by INR 855.75 crore, which was a slight increase from the previous year. Exports surged by 21.5% to INR 422.65 crore.
Preethi Krishna, the eldest daughter of Suresh Krishna, chairman at Sundram Fasteners, is planning to sell a part of her stake in the holding company. Preethi’s stake will be acquired by her father Suresh Krishna, mother Usha Krishna, and sisters Arathi Krishna and Arundathi Krishna, further consolidating their control in the holding company.
To finance this transaction, the four family members propose to offer INR 400 crore (€44 million) of Sundram Fasteners shares to institutional investors, including those from the Middle East.
After the proposed transaction, Preethi will be left with a 14% – 15% stake in the holding company, from the present 20%, whereas her family members would continue to hold 20% each in the company. Currently, the holding company owns 48% of the stock in Sundram Fasteners and has a market capitalisation of INR 28,000 crore. The sale involves a block deal of 1.5% of Sundram Fasteners shares to foreign investors.
Sérgio Milatias, editor, Revista do Parafuso, www.revistadoparafuso.com.br
Böllhoff Brazil – headquartered in Jundiaí town, São Paulo State,since 1964 – recently celebrated its 60th anniversary, with the celebrations dedicated to local employees and executives.
Guests to the celebration also included global directors CFO Thomas Pixa and co-CEO Wilhelm Böllhoff, who spoke Portuguese to the attendees. A manufacturer of a wide range of mechanical fastening elements, with strong ties to customers in the automotive sector, as a leading fastener provider, Böllhoff Brazil’s 60th celebration was a good ‘rehearsal’ for the larger Böllhoff Group who will achieve the impressive 150 year milestone in 2027, with a big celebration planned.
Fontana Gruppo recently celebrated 10 years in Brazil, with several key guests attending the ceremony, including Fabrizio Fontana and Salvatore De Giorgi – board member and COO of Fontana Gruppo respectively – who travelled from Italy to take part in the celebration.
The ceremony opened with brief speeches from Fabrizio and Salvatore, followed by Fernanda Bueno (interim development secretary of Atibaia). Presentations by Nei Teodoro (general director at LATAM general) and Hailton Alcantara (commercial director) concluded the formal part of the event. The event wrapped up on a high note with a tour of the factory, a cocktail party and a special gift for all the guests – a commemorative book celebrating the Group’s 70th anniversary.
As one of the leading global players in the fastener manufacturing industry, with over 70 years of experience, the Fontana Gruppo consolidated its presence in Brazil back in 2014. It further solidified its presence by acquiring eleven Acument industrial units located in the USA, Mexico and Brazil. Since then, all operations, including the two facilities of Acument Brasil, have been fully integrated under the Italian group’s control.
Founded in 1943 in São Paulo, originally under the name Mapri, the company has built a reputation for adhering to the highest quality standards in the supply of fastening systems, particularly for the Brazilian automotive sector (cars, trucks, buses, agricultural and road machinery, as well as motorcycles).
Under Fontana’s leadership, the company further strengthened its position by expanding its industrial park – with the introduction of robust multi-stage presses and thread rolling machines, along with numerous other investments, such as in laboratories, inspection systems, heat treatments and various other aspects of ‘Made in Brazil’ production.
Since it was acquired by Primat Curtis Group in 2022, Prosdac – the Brazilian anti-corrosive coatings service company – has looked to continue to develop and take the next step in its growth through strategic investments.
Located in Jundiaí Town, São Paulo State, Prosdac has been receiving robust investment from Primat Curtis since the acquisition, including the purchase of a neighbouring warehouse – increasing its total area to 10,000m². Other investments included the introduction of a new painting line with an overhead conveyor, two new finishing lines with a new state of the art oven, and a big investment in its people, such as the introduction of the English language into daily operations, especially after the new Brazilian Operations Director Danny Thompson joined the business.
“I have been in automotive Tier 1 companies my entire career, almost 23 years now,” underlines Danny.
“I have worked in many divisions inside industries, such as interior, exterior, stamping, injection moulding, blow moulding, paint and paint systems, as well as full on assembly, which includes headliners, consoles, door panels, glove box and digital instrument panels. This gives me excellent experience that I can use for Prosdac.”
You joined Nord-Lock Group three months ago, what insights and perspectives do you bring with you? Tell us a little more about your career history.
“I spent the first 20 years of my career within the SKF Group, where I held various positions in departments such as sales, manufacturing, business development and acquisitions. Looking at the customer ecosystems, there are many similarities between SKF and Nord-Lock Group and what I’ve learned during my time at SKF is valuable. This includes insights related to manufacturing, where I can leverage my experience in high volume bearing production and apply it to the high volume manufacturing of Nord-Lock washers.
For the past eight years, I served as CEO at Ewellix, a global automation company with around 1,300 employees. Ewellix supplies components and subsystems and manages high mix, low volume production, which is similar to how the Nord-Lock Group technology brands Superbolt®, Boltight® and Expander® operate. However, learning never stops, and I continue to experience new and exciting things every day here at Nord-Lock Group.”
What are your initial impressions of Nord-Lock Group and the fastener market in general?
“There’s plenty to be excited about when it comes to the fastener market and Nord-Lock Group’s position. The fastener market is a large and offers numerous high potential opportunities to grow our business.
On 1st August 2024, after a period of reorganisation, Daniel Westberg became Chief Executive Officer at Nord-Lock Group. We caught up with Daniel to discuss what this means for customers and how, as the global leader in bolting and engineering solutions, Nord-Lock is committed to delivering what its customers’ need, when they need it.
As the leader in the fastening industry, NordLock Group is well positioned to pursue opportunities, particularly through our business unit Nord-Lock, which offers an outstanding product portfolio of wedge-locking washers – creating exceptional customer value across a wide range of applications.
The tensioning side of Nord-Lock Group is quite engineering intensive and when coupled with an extensive global distribution network, it translates into impressive capabilities for supplying both standardised and customised solutions that serve the needs of our customers.
Nord-Lock’s network of partnerships and distributors is another aspect that excites me about Nord-Lock Group’s position in the fastening industry. As a crucial component of the company’s success, I am committed to continuing to cultivate and expand these mutually beneficial partnerships.
What Nord-Lock Group has managed to achieve in terms of product quality, on-time deliveries, and short lead times, is something that I’ve been really impressed with. It’s nothing less than world class and creates significant value for our customers. This value is both direct, for example, by enabling customers to carry less inventory, and indirect, by avoiding costs related to replanning and dealing with quality issues. We are also known for our exceptional experience and expertise, which our customers can rely on no matter where they are located in the world. Add to this the internal process control, and years of performance in every mechanical and industrial application imaginable, and there is certainly a great deal of substance behind the unique lifetime warranty that Nord-Lock Group offers.”
Last year Nord-Lock Group went through a period of reorganisation to become more customer driven – why was this decision made and what are the benefits to customers?
“An organisational set-up with three business units, each having end-to-end responsibility for delivering what their customers need, makes a lot of sense. This is because getting Nord-Lock washers to our customers through a distributor is quite different from engineering a tensioning solution for large industrial applications –together with an OEM. With our decentralised, customer first set-up, we can excel in all of our business processes while ensuring that our customers’ needs permeate the entire
organisation at all levels. Reassuringly, I’ve already been part of quite a few customer meetings, and based on the positive feedback we receive, our organisational customer first approach is certainly working.”
How has 2024 progressed for Nord-Lock Group and how do you see the next twelve months developing?
“Nord-Lock Group is growing and we are actively trying to accelerate that growth. Fortunately, we have several ways to achieve this, such as leveraging internal initiatives, making investments, or acquiring businesses that fit into our business model.
However, we are not immune to the effects of the year’s long trend of weaker industrial demand. I do want to stress, though, that we are well aware of, and prepared for, potential business climates ahead and the challenges they can bring. In any case, I am fully confident that with our customer first philosophy, and competent team of co-workers, we will have what it takes to navigate uncertain times and still deliver what our customers need, when they need it.
We can do this thanks to Nord-Lock Group’s dedicated sales teams, in about 25 countries, each with an extensive partner network. By combining the benefits of being close to our customers with an extensive global reach, we can support and collaborate with customers in every region of the world.
I believe that at this moment, we are at a low point in terms of demand. After the turbulent years brought by the Covid-19 pandemic, inventories are back to normal levels. I also expect industrial demand to start growing again during 2025 as interest rates drop in Europe and North America, as well as with the increase in stimulus we see in
Nord-Lock Group is growing and we are actively trying to accelerate that growth.”
China. So, from our side, we’re ready to meet such growing demand for our products with maintained short lead times and virtually 100% on time deliveries. All of this brings me to a positive future outlook and I believe that 2025 will be another positive year for Nord-Lock Group.”
Sustainability continues to grow in importance within markets. What steps has Nord-Lock Group taken on this topic and how do you see this area developing? Have you seen demands from customers in regards to sustainability?
“As the dangers of our changing climate become increasingly noticeable, Nord-Lock Group takes this very seriously. As one
of the larger companies in the industry, we acknowledge our position to achieve real positive impact, which we strive to do in several ways. Firstly, we have a responsibility to engage our co-workers so that their knowledge, curiosity and entrepreneurship can contribute to our company’s sustainability transformation, as well as that of our entire industry.
Secondly, we commit ourselves to a comprehensive sustainability programme that addresses not only environmental sustainability issues, but also business ethics and social sustainability. With our Code of Conduct for business partners, we ensure that these partners are aligned with our values. We have also committed to the Science Based Targets initiative to reduce emissions in-line with the Paris Agreement, which will entail investments and changes to our own operations, as well as awareness and mitigation of emissions related to our suppliers and other partners in the value chain.
In regards to customer demands changing, the short answer is yes. Compared to only two years ago, our partners and customers now want more information about exactly how we work with sustainability. Many of our bigger accounts also define specific thresholds for sustainability performance in their tendering processes, and if we don’t manage to meet their standards, we’re no longer a viable option for them. We must show that we not only take environmental issues, human rights and a sustainable supply chain seriously, but also that we have focused initiatives in place committing us to net zero carbon emissions by 2040.
Moving forward, we will see more customers wanting to know the environmental impact of specific products. Given the challenges of raw material shortages and climate change, the use of circulated or carbon free steel will grow. So, life cycle analysis to determine our products’ environmental footprint will be a bigger focus of ours, both because our customers demand it and in order to make a positive contribution to the sustainability of our industry. We believe all of these developments are overwhelmingly positive and well needed.”
www.nord-lock.com
By Alexander Kolodzik, secretary general, European Fastener Distributor Association
It has now been a year since the European fastener industry found itself in the CBAM transition period and the sector is struggling with the challenges of the EU Carbon Border Adjustment Mechanism –with the reporting requirements for EU importers of fasteners increasing once again for Q3 of 2024.
The further complication for Q3 onwards is that EU importers can no longer use the European Commission’s default values for direct and indirect emissions for their quarterly report in the CBAM transition register. Instead, they must report the actual values of the emissions generated during the production of the imported fasteners. This poses major challenges not only for European fastener distributors, but for all participants
The further complication for Q3 onwards is that EU importers can no longer use the European Commission’s default values for direct and indirect emissions for their quarterly report in the CBAM transition register.”
in the supply chains – from any intermediaries to the manufacturers of the fasteners, as well as the suppliers of the raw materials used to produce the fasteners. According to CBAM, all parties are required to provide EU importers with data on emission values and other data so that EU importers can fulfil their legal reporting obligations according to CBAM. However, this is a huge endeavour that requires tremendous efforts from all parties involved.
The European Fastener Distributor Association (EFDA) is making every effort to ensure European fastener distributors, and their business partners around the world, can meet these challenges as effectively as possible. It is clear that the EU CBAM regulation has been prepared too hastily and poorly, which is why the mechanism is completely inadequate and, in particular, unsuitable for downstream products such as fasteners, which have complex supply chains and thousands of parties involved around the world. It is also obvious that EU importers under CBAM are at a severe disadvantage compared to EU manufacturers of fasteners under the European Trading System (ETS), especially from 2026 when EU importers must buy CBAM certificates per tonne of emissions embedded in the imported goods. For this reason, EFDA is advocating for fasteners to be excluded from the scope of CBAM. However, that is not the issue at hand in this article.
Currently CBAM still applies to EU fastener importers and as an association we are doing everything we can to support our members. That is why EFDA, with its members from the national member associations and companies, has set-up an EFDA CBAM Working Group –with a group of experts from distributor companies in various European countries. This team is doing an excellent job, which enables us to keep our industry informed about many aspects of CBAM and provide them with some useful documents and tools.
From the outset, we have kept our members informed about CBAM in webinars that we conducted together with the steel expert Andreas Schneider from StahlmarktConsult. We have also provided them with shorter and more detailed briefing documents that they can use to inform their suppliers that they, too, are affected by CBAM and how. This also applies to the many intermediaries who have to provide EU importers with CBAM data from the manufacturers they used to purchase the goods, an extremely difficult task.
Suppliers need to understand CBAM in order to obtain the data to be reported. This is a huge challenge for all parties involved, but especially for small and medium-sized companies around the world. The communication template created by the European Commission is far too extensive and complex for suppliers to use to report the required data to their customers in Europe. EFDA therefore created its own template very early on, which requests the necessary data in a clear and user-friendly way. Despite all our efforts, the number of suppliers that returned the template with specific emission values was only 12% a few months ago.
Since specific emissions data must be reported from the third quarter of 2024, the EFDA CBAM Working Group, together with the consultancy Carboneer, has added an EFDA Calculator to the EFDA Template. The EFDA Calculator makes it easier for fastener manufacturers to calculate the data to be supplied for direct and indirect emissions. A new ‘EFDA guide for non-EU suppliers of fasteners subject to CBAM’ also provides
information on the main hurdles of CBAM and highlights the most important aspects when completing the EFDA template. The EFDA guide has been prepared by Carbooner and the expertise of the members of the EFDA CBAM Working Group. We have also created a tutorial that guides users step by step through the EFDA template. Initial reports from our members confirm that the quantity and quality of the data reported by suppliers has increased since then.
Nevertheless, it remains extremely difficult to obtain the required information from all suppliers. EFDA and its member associations and companies will therefore continue to work to ensure that the enormous burden that CBAM places on our industry is lifted.
www.efda-fastenerdistributors.org
EU importers under CBAM are at a severe disadvantage compared to EU manufacturers of fasteners under the European Trading System (ETS), especially from 2026 when EU importers must buy CBAM certificates per tonne of emissions embedded in the imported goods…”
Are you facing challenges developing your application? We offer a tailored solution with lightweight design, more clamping force and smaller fasteners.
KAMAX experts challenge your drawing, analyze your problem and review your application. Our dedicated Application Engineering team is always at your side.
What you need is what we have: bolt design, lab validation, simulation of assembly conditions, supply of test parts as well as high-quality production and shipping of your fastener solution – anywhere in the world.
As a business driven by the need to optimise customer satisfaction, Owlett-Jaton is continually looking to invest when it sees an opportunity to improve the service it offers to its customers and make cost savings. The installation of its vertical storing storage systems are a prime example, as they support the UK wholesaler’s mission to offer customers an extensive ‘one stop shop’ for fasteners and fixings.
Investing over GB£500,000, Owlett-Jaton has installed nine Modula vertical lift storage machines at its Staffordshire warehouse. These machines have enabled Owlett-Jaton to expand its product range; improve picking speed and accuracy; create a safer working environment; and become more cost efficient at the same time.
Each machine has over 60 trays with a weight capacity of 750kg per tray and each tray can be adapted to hold up to 50 different products. The choice of products depends on pack type, size, weight and pick frequency, with Owlett-Jaton now able to store and pick over 6,500 products in an area that previously only allowed for 450 products. This additional capacity enabled the launch of a 1,000+ strong range of rivets under the JRP brand and the consolidation of over 5,000 products from a second warehouse, bringing all picking activity under one roof and consolidating company stockholding.
Part of Owlett-Jaton’s customer offering is the ability to place orders up to 17:30 – with customers receiving delivery the next working day. With over 7,000 lines per day being picked, this creates a period of intense activity between the order cut-off and the timing of the last trailer leaving for the carrier hub at 22:00. The vertical storage systems allow for much higher picking rates to be achieved, with a good operator being able to pick over 200 lines per hour, compared to around 40 lines per hour in conventional picking.
This additional speed is invaluable in keeping to the tight deadlines created in meeting the next day promise to customers. The vertical storage systems operate by bringing the product to the picker and have an inbuilt laser pointer system to identify which products are to be picked, thus reducing the potential for errors, particularly important at such high picking rates.
The health, safety and wellbeing of its staff is of paramount importance to Owlett-Jaton, and by installing the Modula machines a number of health and safety benefits were also realised. The first was that picking from the machines is done at waist height, with the product being brought to the operator. This eliminates the need for much of the
bending and stretching, which was needed previously. Given the heavy weight of many fastener products, this reduces the risk of strains and other injuries in the workplace.
A second major benefit was realised as the vertical storage systems have enabled the creation of a large pedestrian only, vehicle-free zone in the warehouse, reducing the risk of staff being hit and hurt by one of the forklift trucks or order picking machines. The machine picking also provides another different job in the warehouse and facilitates the rotation of staff between roles, lessening the risk of repetitive strain injuries.
Financially the Modula machines have also proven to be a sound investment. The higher picking rates achieved have enabled a reduction in headcount, which, even after all maintenance costs were factored in, enabled the machines to pay for themselves in under three years.
Replenishment of the Modula machines is done during the night shift via system generated replenishments at a time when there is no scheduled picking of customer orders. The team replenish the machines with approximately five days’ worth of stock. The mix of products in the machines is kept under constant review – with the aim to optimise the right balance between exploiting the picking rates that can be achieved, and the amount of stock that needs to be held to ensure stock is always available to pick. The sheer volume of some of the faster moving lines keeps them in pallet-based picking locations, as keeping them stocked in the Modula machines would prove a challenge.
Owlett-Jaton’s entire warehouse has changed many times over the last 75 years. Modern warehouses with narrow aisle multi-level pallet racking are increasingly becoming the norm, but the addition of modern picking automation is groundbreaking in the UK fastener and fixing wholesale industry – with Owlett-Jaton planning additional vertical storage systems in the future.
www.owlett-jaton.com
Lederer has confirmed current Managing Director Peter Henke will retire at the end of 2024, with Sebastian Ovenhausen, current managing director at NORMTEC Montage- und Befestigungstechnik GmbH –acquired by Lederer in 2021 – taking the role from January 2025.
Peter Henke has been a key part of Lederer for 32 years – playing a fundamental role in the company’s growth and success.
“Peter really has been a major player in our business and has always been ambitious and loyal to Lederer – handling the company as if it was his own,” explains Volker Lederer, also managing director at Lederer GmbH. “Over the years we have created an optimal relationship and worked together very constructively, and in a trustful way, which has led to Lederer being successful. I am very happy and honoured that he worked for us for such a long time and brought us to the position we are in today – especially in the end user railway sector, which in many ways was his ‘baby’ and is now a strong market for us. He has certainly helped us push forward and grow as a company and I wish him a happy retirement.”
With Peter retiring, Lederer has decided to appoint Sebastian Ovenhausen, current managing director of NORMTEC, as the new managing director. Acquired by Lederer four years ago, NORMTEC is also a distributor for stainless fasteners – partnered with effective and cost efficient logistic processes, whilst also guaranteeing high availability and precise delivery times.
“Sebastian has demonstrated his capabilities and leadership at NORMTEC and he will play a key role in the generational change of the management team at Lederer,” underlines Volker. “As a business we are looking to bring in the next generation of employees – putting them into more and more responsible positions within the management team, so we can guarantee our long-term success and continue to move the company forward.”
As a business we are looking to bring in the next generation of employees –putting them into more and more responsible positions within the management team, so we can guarantee the long-term success of Lederer…”
Volker adds: “Almost everything for NORMTEC customers will stay the same, in most cases even keeping the same contact person. It will only be those customers who buy from both companies where we will create one contact point.”
By integrating NORMTEC fully into Lederer it will also generate
With Sebastian becoming managing director of Lederer, it has also been decided that it is the right time to fully integrate NORMTEC into the Lederer brand. “NORMTEC is very similar to Lederer, but on a smaller scale, and with Sebastian becoming managing director sales, it was decided it would be more efficient to integrate NORMTEC fully into Lederer and provide both companies with new opportunities to grow going forward,” highlights Volker. “For example, the range of NORMTEC is relatively small, but we can add the Lederer range to the offering, meaning NORMTEC customers can get access to even more products.”
opportunities for Lederer. “With its end user business NORMTEC does some very special things, which could prove beneficial to Lederer and help us move further into new markets over the coming years,” mentions Volker. “The end user market is already proving a successful sector for us and we have established a reputation as a reliable supplier of stainless steel fasteners, especially within the railway market. Our position within the railway sector is very strong and the rail sector in the coming years will continue to grow, not only in Europe but around the world. As already mentioned, Peter Henke had a lot to do with our success in this area and we are keen to continue to grow the market.”
A prime example of Lederer’s success in the end user rail sector is its partnership with a global rail customer – who recently announced plans to establish a new branch on the east coast of the USA, with Lederer given the opportunity to tender for the business, for which it was successful. “As part of this tender process it was necessary for us to establish a branch in the USA and to be able to serve the customer directly,” explains Volker. “That is why we have set-up a branch close to the client. Whilst we already have customers in the US, this is the first time we have our own physical location, making it a big step for us.”
Volker continues: “Our first objective for Lederer USA is to serve the rail customer in question and ensure we are providing a first-class service. Once this is successful, we can think about possibly expanding our business within the US, but this a second or even third step for us currently. The main focus will be our key rail customer and guaranteeing a complete service.”
With the new management structure and generational shift; the addition of the US operation; as well as ongoing growth targets; Lederer is looking to reaffirm its organisation and structure in order to go on providing the products and service its customers have come to rely on. “At Lederer we realise the importance of continuously moving forward and growing as a business, which is why we have focused on our management team, the markets we supply, as well as the products and
services we deliver to customers,” concludes Volker. “We also make sure we are flexible as a business, so we can react quickly to the challenges of the market, such as freight costs, exchange rates, etc, whilst continuing to provide our customers with the products and services that have enabled us to become one of the leading companies within the stainless steel fastener sector.”
www.lederer-world.com
As part of the tender process it was necessary for Lederer to establish a branch in the USA, so it can serve its customer directly.”
Supplying over 175 customers in more than 25 countries, Indian manufacturer Gala Precision Engineering states it is embarking on a transformative journey of expansion, with an ongoing commitment to quality, as well as embracing sustainability, which promises to offer exceptional value to its global clientele.
As part of this journey, Gala Precision has launched its Initial Public Offering (IPO), a strategic move designed to fuel innovation, expand production capacity and enhance its global footprint. The capital raised is being invested in two key areas – expanding its existing Indian facility in Wada and establishing a new, state of the art manufacturing plant in Chennai.
The Chennai plant represents a significant milestone for the company. Strategically located to serve key markets more efficiently, this expansion brings Gala Precision closer to its customers in southern India and enhances connectivity to global markets such as Europe and the USA. This proximity reduces lead times and improves logistics, making it easier for customers to receive products faster and engage in collaborative projects.
Being closer to its customers also enables Gala Precision to better understand its customers’ specific needs and challenges, as well as deliver customised products that meet exacting specifications. This customer centric approach fosters long-term relationships – built on trust and mutual success.
At the heart of Gala Precision’s operations lies an unwavering commitment to quality. Gala Precision Engineering manufactures high-tensile fasteners and technical springs with unmatched precision and quality, adhering to stringent testing standards to ensure every product meets and exceeds customer expectations. Gala Precision is proud to be ISO and IATF certified, reflecting its dedication to maintaining the highest quality management systems in manufacturing.
Gala Precision specialises in supplying critical components to sectors such as renewable energy, industrial applications and automotive. By diversifying its product range, the company meets the evolving needs of various industries – including the renewable energy sector. Gala Precision’s products are vital for constructing and maintaining wind turbines and solar panels. The high-tensile fasteners and technical springs are designed to withstand harsh environmental conditions, ensuring the longevity and efficiency of renewable energy installations.
Additionally, the company holds the APQP4Wind certification, showcasing its expertise and reliability in supplying components to the wind energy sector. This certification underscores Gala Precision’s commitment to supporting renewable energy initiatives by providing products meeting the industry’s rigorous demands.
In addition, the company provides components essential for machinery, infrastructure, and equipment, ensuring reliability and performance across global industrial operations. As well as this, in the automotive sector, Gala Precision supplies fasteners and springs critical for vehicle safety and performance. Adhering to stringent quality standards, the business meets the high demands of automotive and railway manufacturers, contributing to advancements in mobility.
Gala Precision’s expansion is not just about increasing capacity; it’s about embracing sustainability and innovation to drive the industry forward. The company recognises the importance of environmental responsibility and integrates sustainable practices throughout its operations.
By investing in research and development, Gala Precision is exploring new materials and manufacturing processes that reduce environmental impact without compromising on quality. This commitment aligns with the global shift towards eco-friendly practices, positioning the business as a leader in responsible manufacturing.
Gala Precision’s bold expansion through its IPO, and the establishment of the new Chennai plant, marks a significant step forward for the fastener manufacturer. By manufacturing high-tensile fasteners and technical springs, adhering to stringent testing standards, and holding prestigious certifications, it is setting new benchmarks for quality and reliability.
Supplying a diverse range of sectors, Gala Precision is not only meeting the demands of today’s market but is also anticipating the needs of the future. Its commitment to sustainability, innovation, and precision engineering, positions it as a leader poised to shape the industry’s trajectory.
www.galagroup.com
Celebrating its successful transition from rivet distributor to German rivet manufacturer –GOEBEL Group became the setting for the first ever World Riveting Congress 2024 (WRC2024) in September – where attendees from around the globe, including Fastener + Fixing Magazine, were able to witness the first production batch of GOEBEL rivets.
Taking place from 28 th – 29 th September at its European headquarters in Ekrath, near Düsseldorf, the WRC2024 saw participants and representatives from 19 countries attend expert presentations – delving into the latest developments in blind rivets and riveting machines.
Marcel Goebel, managing director at Goebel Group, explained: “WRC2024 was the first event of its kind, anywhere in the world and the idea behind it is simple – we wanted to bring together buyers, distributors, engineers, and industrial customers, from all over the world to educate, share knowledge, as well as discover the latest trends and innovations in the industry.”
Marcel continued: “The journey to ‘Made in Germany’ started back in 2020 when we had to fight supply chain disruptions because of the Covid-19 pandemic. These delays were frustrating, so I decided to do something about it – I bought some machines from a manufacturer in Spain and our journey to a manufacturer began. It’s been scary, but exciting, and I’m still in the process of learning – wire is not wire, tooling is not tooling and oil is not oil – but I am very proud of the cold forming team we’ve created in Ekrath and the WRC2024 was the culmination of the dedication and hard work of the whole GOEBEL family.”
The journey to ‘Made in Germany’ started back in 2020 when we had to fight supply chain disruptions because of the Covid-19 pandemic. These delays were frustrating, so I decided to do something about it...”
The twelve expert presentations, given in both German and English, included technical lectures from Joachim Kruger, head of sales cold forming and stamping at Marposs Group, on process monitoring process data and digitalisation solutions for the riveting industry. Joachim outlined how rivet companies can use data to optimise production, the benefits of process monitoring, as well as how production companies can identify ‘weak points’ in order to improve. During his presentation, Joachim also switched live to videos of GOEBEL’s blind rivet production, which is successfully utilising Marposs process monitoring.
Another innovative technology adopted in GOEBEL’s new facility is SmartCert. WRC2024 attendees were able to attend a technical lecture from SmartCert Owners Lyndon and Lotti Lattie on how the technology can be used for batch traceability and documentation. Lyndon highlighted: “As a forward-thinking company, GOEBEL has been an early adopter of SmartCert and is embracing innovation across the entire organisation. In the supply chain, suppliers want more control over the way they receive documents, the quality of these, as well as how quickly they receive them. Our technology is focused on making the
fastener industry more competitive and efficient, so companies can focus on what they do best and not worry about sending documentation and certificates in a certain way – which is also largely customer dependant –instead the information is already there.”
GOEBEL’s newly designed packaging has a QR code that enables suppliers to scan and receive all relevant certifications and documentation straight away – in whatever format they desire. This QR code can also be updated in ‘real time’, even once the products have been shipped.
Lyndon concluded: “Launched in the fastener industry back in 2021, SmartCert is expanding to a variety of industries – any industry that requires traceability. As market trends develop, such as CBAM, as well as other global carbon footprint initiatives, we are excited by where this technology will take us.”
With CBAM a topic on everybody’s minds, attendees were also able to attend a technical lecture from Bettina Mertgen, partner – customs, excise taxes and foreign trade law at Deloitte Legal Rechtsanwaltsgesellschaft GmbH – a German company specialising in offering competent advice in all fields of national and international business law. Bettina explained the CBAM regulation in more detail, as well as covering how the regulation is currently impacting fastener companies.
Bettina also highlighted various key topics within the European fastener industry including the ESG Supply Chain Act, known as the Corporate Sustainability Due Diligence Directive (CS3D), which requires companies to be more transparent about their sustainability efforts and to address human rights and environmental impacts.
Bettina explained: “Germany has led the way in respect to mandatory supply chain due diligence obligations. The CS3D stipulates comprehensive supply chain due diligence obligations including establishing a risk management system, performing risk analyses,
implementing preventive and remedial measures, as well as a grievance mechanism and documentation and reporting obligations. Most recently, the Council and the European Parliament reached a provisional agreement during the trilogue negotiations, aiming to enhance the protection of the environment and human rights in the EU and globally. The result was that the CS3D was adopted and entered into force in early 2024 with a transition period into national law ahead.”
Bettina also gave attendees a look at other legal requirements that she believed would become more prominent in the future and have an impact on the industry – such as the topic of plastic taxation, with single use plastics directive regulations starting to be implemented across the European Union.
In addition, the extensive lecture programme featured technical lectures from Elias Goebel and Jennifer Diecks from GOEBEL on cold forming, simulation, project implementation and circular steel. With over 50 years’ experience between them, the GOEBEL colleagues outlined tool design and simulation and how it goes hand-in-hand with Marposs process monitoring, as well as what steps GOEBEL is taking to improve the overall quality of its products. Philipp Hülsemann, owner at Rotover Lackiertechnik GmbH, also gave a technical lecture on the coloured painting of rivets, there was also a technical presentation by GOEBEL’s QS management – Cem Bakar and Kevin Amar – on ‘corrosion protection and surface protection’.
There were also three technical lectures from the Fraunhofer Institute, with Mark Dörre, fastener engineer, mechanical joining technology group leader, defining the static calculation of blind rivets and standards; as well as Christian Denkert, industry contact in the field of rail and vehicle construction, highlighting blind rivet nut standards and applications.
In addition, the third technical lecture from Fraunhofer Institute was from Alexander Holch, from the large structures in production engineering division, who focused on the advantages and benefits to GOEBEL’s G-GRIP ® lockbolt system. The patented full stainless steel lockbolt system, now has the German DIBt approval, making it a powerful alternative to welding or regular screw connections.
Marcel Goebel highlighted: “Whilst travelling in Canada a few years ago, I was told that ‘nobody in the world can make a stainless steel lockbolt system’. I took this as a challenge and opportunity – and G-GRIP ® was born. Developed for applications where an extensive grip range is needed, and a consistent flush pin break to the collar is favourable, the G-GRIP ® is the new and improved standard. Essentially, the G-GRIP® extensive grip range and various sizes can replace up to 14 sizes of the classic 6 groove locking fastener system.”
To give attendees an ‘up close example’, a Kenworth Truck was brought from Canada to the WRC2024 to showcase the G-GRIP®’s use in restoring the Kenworth W900B’s trailer walls, with a GO-LB1 cordless lockbolt battery tool, with brushless motor, used to secure the rivets.
As well as the extensive conference programme, attendees also had a factory tour where guests had the opportunity to experience GOEBEL’s new production facility and gain a true insight into the ‘Made in Germany’ manufacturing process, with both Marcel and Elias Goebel proudly showcasing the new facility’s adherence to the highest standards of quality and precision. Attendees were able to observe the entire production process, from material selection to final assembly, and celebrate the start of GOEBEL’s own production ‘Made in Germany’.
To further help celebrate, Todor Gajanovic – a Sheet Metal Workshop video streamer, used the first production batch of blind rivets to create the GOEBEL logo from sheet metal, supported by an UltraCut laser machine from Marcel Schwartmanns, which will be displayed in the production hall. Guests were also presented with their very own rivet from GOEBEL’s first production batch to take home.
Also taking place during the event was the ‘Riveting World Showroom’ where attendees were able to get ‘hands on’ with some of the latest innovations and products from GOEBEL and its partners. This included MTG Hartmut Thiele GmbH with its rapid fastening systems. Through 40 years experience, the company has
developed speed fastening technology, making it possible to use up to 200 speed rivets on mandrels for single use – with wire lengths between 400mm and 1,110mm – without having to change the mandrel.
The ‘Riveting World Showroom’ also included GOEBEL’s latest innovation – the GO-GB1 lightweight tool. Presented by Mike Derenne, sales engineer at GOEBEL Fasteners Inc, the GO-GB1 was introduced to the sound of the iconic ‘ghostbusters’ theme tune thanks to its 36V battery backpack. Available across the market soon, the GO-GB1 can set GO-LOCKs and lockbolts up to ⅜inches (9.8mm) and has a pulling force of 40kN.
Celebrations also continued into the evening with over 300 guests at the evening party at Dr Thompson in Düsseldorf – where guests were thanked by Marcel and his family, who were already anticipating doing it all again, as well as Lord Mayor Christopher Schultz, who expressed how grateful he is with GOEBEL’s choice of location and thanked the company for “bringing manufacturing back to Germany”.
Marcel Goebel concluded: “As we look to the future, we need to invest in more machinery and take responsibility in terms of both sustainability and the environment. One of our main goals when we started the ‘Made in Germany’ dream was to manufacture in a sustainable way and I’m proud of the steps we’re taking to achieve this. We look forward to setting new impulses in riveting technology and working together to shape the innovative and environmentally friendly future of this important industry.”
www.goebel-group.com
To celebrate the 150th issue of Fastener + Fixing Magazine we have created a timeline to showcase how we have grown to become the global multi-platform publication we are today, as well as highlighting some of the breaking news and insights we have exclusively published to keep our readership better informed.
Fastener + Fixing Review launches, dedicated to the UK fastener industry.
First Fastener + Fixing Search business directory launched.
Name changed to Fastener + Fixing Europe to reflect the growing European readership.
Our 10 year anniversary and a name change to Fastener + Fixing Magazine to reflect our global readership.
127, 2021
Verulam Media becomes publisher of Fastener + Fixing Magazine.
Launch of Fastener + Fixing Magazine’s social media sites. We now boast 15,000 followers.
ISSUE 73
First industry renowned Janus Perspective feature.
On 4th September 2024 the Confederation of British Metalforming (CBM) staged its second Fastener Mini-Expo at the National Metalforming Centre, West Bromwich. Aimed at providing an informative networking opportunity for the UK fastener manufacturing sector, all respondents to a post-expo survey felt the event was good or excellent, with 83% recommending it to industry colleagues.
The one day event involved twenty-seven exhibitors, encompassing leading European steel and machinery manufacturers, inspection, process monitoring and simulation systems, tooling and heat treatment specialists, as well as lubricant and energy suppliers, including Brankamp MARPOSS, Carlo Salvi, SASPI, RLS Tooling, Regg Inspection, Condat Lubricants, Hariton Machinery Company, TR Fastenings, Vision Engineering and voestalpine. The Mini-Expo was also supported by Fastener + Fixing Magazine and CBM associates Croner HR and Crowe UK.
A highlight of the event was a fascinating in-depth presentation from voestalpine, exploring both the opportunities and challenges of transitioning to green steel production.
The CBM Fastener Mini-Expo originated in 2019, but plans for further editions were stymied by the Covid-19 pandemic, until a successful relaunch this year. That was at the initiative of CBM Fastener Specialist Derek Barnes, with the able support of the Confederation’s Media and Communications Administrator Rachael Bromley.
Reflecting on the event, Derek said: “The CBM set out to create a dedicated trade fair for fastener and precision component manufacturing companies, giving them access to key providers in the supply chain but also bringing them together as a community for a great networking opportunity. We chose exhibitors that were diverse in their products and services and offered state of the art technologies that add value to the manufacturing industry.”
Explaining the selection of voestalpine as the day’s keynote speaker, Derek explained: “We decided to have a single keynote speaker and the presentation by voestalpine on green steel was not only extremely relevant but also very insightful. It created an excellent focal point for attendees and exhibitors, with discussions continuing over the buffet lunch provided by the CBM.”
The National Metalforming Centre is the CBM’s headquarters and events venue, conveniently located in the heart of the West Midlands, close to the M5 and M6 motorway network. For Derek Barnes, as well as showcasing the capabilities of the NMC as a welcoming and effective venue, hosting the Expo there “allowed us to create a really good, relaxed atmosphere, appreciated by all”. He noted: “It’s fair to say that the day was a total success with both
exhibitors and attendees enjoying the event. Having re-established the value of the Mini-Expo, now we can start planning next year’s event.”
Derek was far from alone in his assessment of the day. One exhibitor noted that it had received three times as many positive enquiries than it had at big exhibitions. All bar one exhibitor confirmed they would be pleased to exhibit again.
There was unanimous approval for the voestalpine presentation, which was described by one attendee as “very good and useful”. The presentation, led by Dr Walter Berger, voestalpine’s director of innovation –who flew in with his team especially for the event, provided a detailed and scrupulously honest commentary on both the opportunities and challenges of transitioning to green steel production.
Overall assessments of the Mini-Expo included comments describing it as “well organised and well attended”, with positive feedback on the range of featured exhibitors, as well as special praise for a “lovely lunch”. 91% of respondents to the post event survey were pleased with the variety of exhibitor stands, with a similar percentage approving the time efficient schedule – some felt the event might be even more focused closing sooner after the keynote presentation and lunch. Others, however, clearly valued the networking time. Every respondent concurred that the National Metalforming Centre was a good location, although there was a feeling that, if this year’s success drove greater demand, as seems likely, space might become a challenge.
commented: “CBM was delighted to host so many fastener sector participants, both as exhibitors and attendees. It was particularly pleasing to see ‘standing room only’ for an excellent presentation from voestalpine. It was also great to hear how attendees were engaging with the exhibitors and each other. It was important to Derek that the Mini-Expo should be a successful networking, as well as informative, event and it certainly delivered on both scores. It was also a measure of the range of support that CBM provides its members that attendees valued the presence of Croner HR and Crowe UK, as well as our Policy Advisor Phil Matten, who was clearly being ‘collared’ on various pressing regulatory issues, particularly steel safeguarding and CBAM.”
The CBM stages informative TTG webinars on fastener manufacturing technology and holds regular online forging and fastener meetings, which deliver the latest on market and regulatory developments.
The webinars also include personal updates from President Steve Morley on CBM’s lobbying with government departments on key concerns for the entire metal manufacturing sector.
Fastener Fair Italy underlined its status as a major international event for fastener professionals, with the two day show seeing a continuous stream of visitors from across Europe – leading to the strengthening of relationships, discovery of the latest innovations, as well as insights into market trends.
Now in its fourth edition, Fastener Fair Italy –taking place in hall 3 of the CityLife – Allianz MiCo in Milan – included over 190 exhibitors, from 18 countries, with a strong presence from Italy, Germany, Turkey, China and Taiwan. This strong international exhibitor presence led to a comprehensive overview of the global market and enabled visitors to explore a whole host of products – ranging from screws to bolts, anchoring systems to safety devices, as well as assembly technology to production machinery.
Throughout the hall there were also several eye-catching stands that attracted a significant number of visitors across both days of the show, this included Fastbolt Schraubengroßhandels GmbH, Lederer GmbH, Ambrovit SpA, Bralo SA, Böllhoff Group, Berardi Group, Mecavit Srl, INDEX® – A PERFECT FIXING, CHAVESBAO, VIPA Srl, VITAL Srl, as well as FM Metal Fasteners Group SpA. Francesco Quaranta, operations director at FM Metal Fasteners Group, confirmed that he was very pleased with the show. “FM Metal Fasteners Group had an excellent fair, in-line with our expectations. We successfully achieved our strategic objectives – consolidating key relationships with existing clients; presenting significant innovations; meeting new interesting suppliers; as well as establishing contacts with new international clients.”
A main focus for FM Metal Fasteners Group during the show was to present its B2B eCommerce platform, which features cutting-edge web-oriented technology that surpasses industry standards in terms of user experience. The company also wanted to strengthen relationships with partners, clients and suppliers through its Partnership Programme. “This programme facilitates the sharing of industry information and updates; provides comprehensive support for distributors and users; and integrates a digital approach alongside traditional sales methods –catering more to new generations,” underlined Francesco.
Italian fastener distributor VITAL also reported a successful show, with the event exceeding its expectations. “We participated in the 2022 edition, and we can affirm that at this year’s edition of Fastener Fair Italy there was more excitement and greater participation, perhaps driven by the increased presence of Asian exhibitors, who always attract attention from international visitors,” explained Luca Bernasconi, shareholder and purchase manager at VITAL Srl. “We exhibited in order to create opportunities to meet with active customers and discuss ongoing or potential business. We certainly achieved this goal, thanks to the informal atmosphere and our ability to offer lunches and breakfasts at our stand, which created a friendly and relaxed environment to discuss business.”
Another company that reported meeting its objectives during the show was washer manufacturer Growermetal. “The show went well, we received visits from recognised industry players, partners and potential
clients. There was great engagement and we received positive feedback on our stand and products,” highlighted Michela Mauri, marketing manager at Growermetal SpA. “Our main objectives were to increase brand visibility, connect with existing clients and generate new leads. I’m pleased to say we successfully met these objectives, as we made several valuable connections and gained significant interest.”
Leading Italian screw and bolt manufacturer Bontempi Vibo only booked its stand at the last minute, but was pleased it did after two very busy exhibition days. “The show went very well, as we met existing and potential customers – with everybody interested in the new ranges we presented during the show,” explained Vittoriano Calomeni, general manager at Bontempi Vibo SpA. “We organised this show at the very last moment, as we thought it was better to invest primarily for the Fastener Fair Global show in Stuttgart, Germany, next year. However, the market pushed us to be at Fastener Fair Italy, so we could show our new strategic plan for 2023 to 2028, as well as showcase all the new product families we have added to our already outstanding range, which covers M2.5 to M64. We are very satisfied with the results of the show and we think we achieved all the goals we had prior to the event.”
At the time of going to print the official visitor numbers had not been released by the organisers, but once released will be reported on www.fastenerandfixing.com. The next edition of Fastener Fair Italy will take place from 7 th – 8th October 2026, once again at the CityLife – Allianz MiCo in Milan, Italy.
info@eco-italia.com • www.eco-italia.com
The 7 th edition of the international trade fair for fastener and fixing technology – FASTENER POLAND® has concluded successfully with 75% of exhibitors coming from foreign countries –helping to cement the show’s importance within the fastener industry calendar.
Taking place at EXPO Kraków from 25 th – 26th September, FASTENER POLAND® saw 153 exhibitors from 18 countries participate. In addition to Polish suppliers, manufacturers and distributors from Belgium, the Czech Republic, Denmark, France, Spain, India, Malta, Germany, Switzerland, Turkey, Taiwan, Great Britain, Italy, China and the USA presented their products. For the first time in Kraków, this year’s show also saw manufacturers from Pakistan and the United Arab Emirates present their products.
The statistics of visitors were equally international. Of the 2,856 guests, 46% came to Kraków from abroad. Europe was most represented by industrialists from Germany, the Czech Republic, Slovakia, Ukraine and Romania, but there were also contractors from the furthest corners of the world, such as Jordan, Japan, Kuwait and Israel.
As well as the international presence, the show also underlined Poland’s strategic position in the fastener market. “The demand for specialised fasteners, in terms of quality and standards, is constantly growing. This is probably influenced by the most technologically advanced industrial sectors. Polish suppliers have specialised in supplying high-quality fasteners and Poland is the third largest supplier of fasteners in the European Union, after Germany and Italy. Its location, and well developed transport infrastructure, guarantee uninterrupted supply chains to the furthest corners of the continent. Although labour costs are also rising, Poland still offers competitive prices compared to
other European countries. All these factors make Poland an ideal place for investment in the fastener industry,” highlighted show organisers.
This was also confirmed by Timo Scholle from Achilles Seibert GmbH: “Customers from eastern Europe are becoming increasingly important to us, especially from Poland, our developing market. We decided to exhibit here, in Kraków, because specific customers come to the trade fair. This was our first time at FASTENER POLAND® and it was very well organised and a successful show.”
For the first time, this year’s show also included a Meeting Zone dedicated to companies that are beginning their adventure with participation in fairs and those that have not planned this form of promotion in this year’s budget. In a dedicated area, with a small financial outlay, traders had the opportunity to present their offer and obtain orders. This project was enthusiastically received and will certainly be continued reported show organisers.
The next edition of FASTENER POLAND ® will take place on 15 th – 16th October 2025.
Preventing and adapting to the consequences of climate change in the face of extreme weather events is a task for society as a whole. That’s why BAU 2025 is focusing on climate friendly construction, with companies presenting possible solutions in Munich, Germany, from 13 th – 17 th January 2025.
Climate friendly construction is an approach to planning, constructing and operating the built environment in such a way that it has the least possible negative impact on the climate, while at the same time being resilient to climate change. The need for action is high particularly in densely populated areas, as the high-level of sealing and materials used exacerbate the urban heat island effect. BAU 2025 is a platform for exchanging ideas on forward-looking concepts, structural engineering solutions, and innovative building products, in order to work together on designing sustainable, climate friendly solutions.
Fastener exhibitors already confirmed include Adolf Würth GmbH & Co KG, adunox GmbH, AKIFIX SpA, BESSEY Tool GmbH & Co KG, BEVER GmbH, CELO Befestigungssysteme GmbH, DL Chemicals, Eurotec GmbH, fischerwerke GmbH & Co KG, FIXINGGROUP GmbH, KEIL Befestigungstechnik GmbH, Kinfast Hardware Co Ltd, KLIMAS Sp z.o.o, Kyocera Senco Germany GmbH, PREBENA Wilfried Bornemann GmbH & Co KG, REISSER-
Schraubentechnik GmbH, Rotho Blaas GmbH, Sika Deutschland GmbH, Simpson Strong-Tie GmbH, Soudal NV, Tecfi SpA, INDEX ® –
A PERFECT FIXING, as well as Trutek Fasteners Polska Sp z.o.o.
“The construction industry is under pressure to drastically reduce carbon emissions and resource consumption. But that’s not all. Adapting to the consequences of climate change is also a transformational task that impacts the entire value chain. Our projects must make do with less energy and resources, and at the same time, achieve more – a truly Herculean task,” comments Dr Thomas Welter, federal managing director of the Association of German Architects (BDA).
The organisers of BAU concludes: “Climate friendly construction is an interdisciplinary task. That means that sharing knowledge, methods and approaches across traditional disciplinary boundaries is necessary in order to effectively meet the complex challenges of climate change. We are looking forward to companies discussing and presenting their solutions at BAU 2025.”
For the 2025 Fastener Fair Global show, Fastener + Fixing Magazine will, once again, sponsor the Route to Fastener Innovation Competition. Here we take a look back at a couple of the show’s previous winners and why the competition continues to be a key platform for innovations and new technologies in the fastener industry.
The Route to Fastener Innovation Competition is an exclusive competition for exhibitors that enables visitors to discover and evaluate what’s new in fastening technologies – putting the spotlight firmly on innovative products and services. After a record number of entries in the 2023 competition, first place was ultimately given to Scell-it UK, with its patented E-007 power tool designed to install hollow wall anchors.
“Winning the Route to Fastener Innovation (RTFI) award validated the E-007’s innovative nature and demonstrated its potential to disrupt the market. The E-007 represented a significant advancement in the fastener industry, offering a more efficient and userfriendly solution for setting hollow wall anchors,” highlights Dean Stonehouse, marketing manager at Scell-it UK. “By entering the competition, we aimed to showcase the innovation and benefits of the product to a wider audience, including potential customers, industry experts and investors. The award provided significant exposure, increased brand awareness and generated interest from potential customers and partners.”
Dean adds: “The E-007 has gained attention from both existing and new customers and the competition helped to establish the tool as a leading product in its category. We have seen increased sales
and positive feedback from customers who appreciate the tool’s efficiency and ease of use. The RTFI competition has proven to be a valuable platform for showcasing innovation and driving market adoption.”
Second place was awarded to Growermetal SpA for its Grower SpheraTech ® Developed by the company’s R&D department, SpheraTech® is based on the combination of a spherical top washer and a conical seat washer, ensuring a safe locking function on non-parallel surfaces, as well as avoiding damage or breakages to the bolted joint connection –caused by the bending of the head or the shank of the screw.
The RTFI competition has proven to be a valuable platform for showcasing innovation and driving market adoption.”
“The award demonstrated our commitment to innovation and sustainability and helped us gain visibility in the industry, enabling us to reach new audiences and reinforce our position as leaders in the field,” reports Growermetal SpA. “Entering products into the competition offers numerous benefits for companies. First and foremost, it provides an excellent opportunity to showcase innovation and differentiate products in a competitive market. Additionally, participating in such a prestigious competition helps validate the quality and uniqueness of products, giving credibility with customers and stakeholders. Finally, the feedback and exposure from the competition can serve as valuable insight, driving future improvements and innovation. The feedback we received has inspired Growermetal to develop new brands and as a result, we’re excited to present another new brand during the 2025 competition, continuing our commitment to innovation.”
Entering a product not only presents the potential to be heralded as a 2025 Fastener Technology Innovator, it also provides visitors with a great incentive to visit stands at Fastener Fair Global – to see the product, evaluate it, and to find out more information about it.
Every entrant will be previewed in the January - February issue of Fastener + Fixing Magazine and will also be highlighted in certain Fastener Fair Global visitor information. In addition, every exhibitor that enters will be provided with a special logo for their stand highlighting the company is an entrant.
For the full rules and details on how to enter your product in the competition, please visit www.tinyurl.com/bdhhctea
Stuttgart, Germany
25 Mar – 27 Mar 2025
www.fastenerfairglobal.com
The international exhibition for the fastener and fixing industry.
The Big 5
Dubai, UAE
26 Nov – 29 Nov 2024
www.thebig5.ae
An event covering every critical phase of the construction cycle.
bauma China
Shanghai, China
26 Nov – 29 Nov 2024
www.bauma-china.com
Construction and mining machinery trade fair.
International Hardware Fair India
New Delhi, India
6 Dec – 8 Dec 2024
www.hardwarefair-india.com
An international event solely focused on the hardware and DIY sector.
BAU
Munich, Germany
13 Jan – 17 Jan 2025
www.bau-muenchen.com
Trade fair for architecture, materials and systems.
BUDMA - International Construction Fair
Poznań, Poland
11 Feb – 14 Feb 2025
www.budma.pl
The meeting place for manufacturers and distributors in the construction industry.
The smarter E India
Gujarat, India
12 Feb – 14 Feb 2025
www.thesmartere.in
India’s hub for future energy solutions and technologies.
BouwBeurs
Utrecht, Netherlands
3 Feb – 7 Feb 2025
www.bouwbeurslive.nl
Trade fair dedicated to the Dutch construction industry.
Southern Manufacturing & Electronics
Farnborough, UK
4 Feb – 6 Feb 2025
www.southern-manufacturing-electronics.com
Industrial exhibition for new technology in machinery, production equipment as well as tooling and components.
Schraubtec Stuttgart
Stuttgart, Germany 19 Feb 2025
www.schraubtec.com
The regional trade fair for screw connections.
Asia-Pacific Sourcing
Köln, Germany
11 Mar – 13 Mar 2025
www.asia-pacificsourcing.de
European platform for import and export between the West and Asia.
National Hardware Show
Las Vegas, USA
18 Mar – 20 Mar 2025
www.nationalhardwareshow.com
Connects retailers, dealers, wholesalers, distributors and manufacturers to the marketplace.
BYGGERI
Fredericia, Denmark
18 Mar – 21 Mar 2025
www.byggerimessen.dk
Scandinavia’s trade fair for construction products.
An in-depth look at the latest developments from EASTERN EUROPEAN manufacturers
Next year, Klimas will celebrate its 35 th anniversary as one of the largest manufacturers of construction fasteners in central and eastern Europe. Ahead of this milestone, we speak to President Wojciech Klimas about how the company has grown to produce up to 30 million screws a day, as well as how it is investing heavily in its product range for wooden construction, as wood becomes the ‘material of the future’.
Established in 1990 by Joanna and Wojciech Klimas, Klimas initially operated in local markets, but has grown to export its products to 70 countries worldwide. Klimas is able to supply a variety of screws and fasteners for wooden constructions, such as high-quality woodscrews, carpentry screws, construction screws for the roof truss, wood fasteners for fixing roofing and wall thermal insulation to wooden substrates. In addition the company is able to supply terrace screws for floors and terraces, as well as three dimensional carpentry connectors such as wood angles, carpentry nails, plugs and decorative rosettes.
Wojciech Klimas underlines: “Being in the construction industry for so many years, I always felt that wood construction would grow in strength, which could be related to environmental
protection requirements, but also to the growing awareness of investors. Woodscrews will always hold a special place in our hearts, with our products used in a variety of applications and environments around the world.”
This includes a wooden mountain chalet in Mount Assiniboine at an altitude of more than 2,000m above sea level in Canada, as well as a 27 storey building of arcaded glulam beams in Singapore, or the unusual Marmormolen wood complex on Copenhagen’s waterfront.
“By all means, this is the direction the world is heading – wood is the material of the future, especially glulam, which enables frame structures to be erected quicker than ever before. This type of construction carries economic advantages, such as the lack of need to store the material on the construction site and the speed of the project – as the structure is assembled from ready made elements already on-site. An equally important issue is the sustainable nature of wood and thus the reduction of the carbon footprint in the construction process of a given building. Investors are increasingly understanding that this kind of responsibility is their duty to the environment. However, despite this recognition, few European companies produce woodscrews because of the complex technology needed to manufacture quality products,” explains Wojciech.
Klimas’ four integrated production facilities located in Kuźnica Kiedrzyńska and Wanaty near Częstochowa, are equipped with Industry 4.0 technologies with over 100 injection moulding machines; 200 presses and rollers; a tool shop with advanced machining centres; a high storage warehouse; as well as a modern quality control department – to meet the highest requirements of both domestic and foreign markets.
Klimas’ production process is independent from start to finish. From the coiling of the wire to the process of packaging and distribution of various finished, hardened and coated screws, to provide customers with an uninterrupted supply chain – regardless of the dynamically changing circumstances of the European and global economies.
“The last few years have shown global manufacturers that all it takes is for one piece to be missing from each plant’s logistical jigsaw puzzle and the entire supply chain suffers. Through the crises of Covid-19 and the armed conflict in neighbouring Ukraine, Klimas came through without much perturbation, which I believe is largely down to our production independence,” comments Wojciech.
“Challenges in recent years have also been joined by those related to ecology and sustainability. At Klimas, we were fully aware several years ago that the world would move towards sustainability, so we acted then to stay ‘one step ahead’ by recovering heat used from production to heat buildings, as well as having a vehicle fleet consisting largely of hybrid cars. Going forward we will look to invest further with the planet in mind,” adds Wojciech.
After more than three decades, Klimas continues to focus on development and innovation, which is apparent in its patented products. This includes the Klimas’ SQ Ceramic coating – a chromiumfree and environmentally safe multi-layer corrosion protection – or the milling tip, which speeds up work with woodscrews by up to 40%, saving not only contractors’ time, but also tool batteries.
“When it comes to innovation, I set the technological bar high enough so our products are among the most innovative on the market, despite the constant challenges and technology moving forward at a tremendous pace. To ensure we are a global leader, we must continue to keep up with these ever changing needs and requirements by striving to be the best, as well as focusing on quality and innovation,” highlights Wojciech.
After more than three decades, Klimas continues to focus on development and innovation”
In order to further guarantee quality, Klimas has its own in-house laboratory, research and development centre, as well as testing area for inspecting manufactured products. Specialist equipment, including a logistical measuring microscope and X-ray spectrophotometer, make it possible to check the entire batch of a product after production, before packing. The company tests parameters such as length, core diameter, thread diameter, head size, drive design, thread pitch and length, drill bit and others. Screws that pass the test are sent for packing, while those found to be out of standard are rejected.
“In order to meet the expectations of all markets, we must be sure our products are of the highest quality, as well as carry the appropriate European safety certifications. This includes European Technical Assessments and, in the case of some mechanical anchors, also seismic testing, which ensures customers safe products from a trustworthy, reliable manufacturer,” proudly states Wojciech.
“Thirty-five years is a lot and is often a whole professional life, however when compared on the scale of European manufacturing companies, Klimas is a relatively young brand. That is why I am proud that Klimas still competes boldly with the biggest players on the continent, as well as having successfully entered Asian markets including India, Sri Lanka and Nepal,” comments Wojciech.
He concludes: “I am inspired by the actions of many companies, sometimes competing ones, because I realise how much effort and sacrifices these successes cost. You need to have some humility in life to be able to appreciate your opponent, even more so if you have been in this industry for years and know how much daily work it takes to achieve a high position in it. For a family owned company to achieve such prominence in business, it takes not only knowledge and persistence, but also a commitment to values and with them a sense of security and customer confidence, which has given Klimas a place as a leader in European construction fastener manufacturing, which we hope to maintain for many years to come.”
www.klimas.com
With a recent move to Mielec in the south of Poland, Trutek™ Fasteners Polska, is serving its local and European customers with more precision than ever before, through high-quality products, technical support and expertise, as well as a focus on new product development.
Trutek ™ currently manufactures and offers a wide range of fixings including ETA certified insulation anchors, frame anchors, as well as plastic plugs and hammer screws. The company also prides itself on offering products that meet strict European and international standards, guaranteeing high safety and performance, as well as products approved for use in critical infrastructure and demanding environments.
Having recently opened a UK warehouse, as well as having key partners in Europe and the Middle east region, Trutek ™ also has plans to supply the US and South American markets and, in addition, add new products to its wide range.
Some of its latest product additions include a range of concrete screwbolts with increased loading for equivalent expansion anchors, which are fully adjustable – the fixings can be taken out after installation, adjusted and reinstalled with no loss to loadings, in both crack and non cracked concrete. There has also been recent developments in Trutek ™’s gas and PAT range, with battery nailers in development – planned for launch in 2025. ETA certified anchors are currently also in testing with the aim to attain more approvals in 2025.
“We see the future of construction to be transformed by advancements in technology, sustainability and regulatory processes. With the rise of smart building materials, 3D printing, and automation, construction methods will become more efficient –reducing time and costs while enhancing precision. This is why it’s crucial for Trutek ™ to constantly invest in new products, approvals, and research, to further its expertise – which is how DesignFiX was born,” comments Ben Beardon, operations manager at Trutek ™ Fasteners.
DesignFiX is Trutek’s anchor programme to simplify complex calculations, ensuring precise anchor selection in-line with European Technical Assessments (ETAs) and international standards. With its intuitive interface, DesignFiX enhances efficiency and confidence in choosing reliable fastening solutions, making it an essential tool for modern construction projects.
Trutek’s customer-centric approach includes flexible, on time delivery and customised solutions for unique project needs.”
“Our DesignFiX software provides customers with tailored, efficient anchoring solutions backed by expert technical support and a personalised service,” highlights Ben.
This personalised service includes helping customers choose the right products for their specific needs, providing on-site consultations, as well as design assistance and calculation services to ensure that the fastening systems are optimal for the project. Additionally, Trutek’s customer-centric approach includes flexible, on time delivery and customised solutions for unique project needs.
“Eastern European production is known for blending skilled craftsmanship with advanced technology, to ensure reliable, durable products meet rigorous European standards. We envision ourself as a leading provider of innovative fastening solutions globally, continuing to expand our product range and market reach,” states Ben.
Looking ahead with a continuous focus on research and development, Trutek ™ plans to introduce more eco-friendly and technologically advanced products, supporting the growing demand for sustainable construction practices. Additionally, Trutek ™ is further enhancing customer relationships by taking part in key market exhibitions such as Fastener Fair Global in March 2025 –where the company will be showcasing its new crack approved anchor range, PAT and gas tools, as well as launching a new range of 20V cordless tools, to ensure the company remains at the forefront of the construction fastening industry.
www.trutekfasteners.eu
Amidst custom restrictions, anti-dumping duties and CBAM regulations, European production is becoming increasingly vital, which is why pgb-Polska – the production branch for pgb-Europe – is undergoing a number of investments in technology and infrastructure at its production facility in Zabrze, Poland, to offer shorter lead times, higher quality control, as well as greater flexibility.
Krzysztof Biskup, general manager at pgb-Polska Sp z.o.o, explains: “The shift to source from Europe is enhancing the significance of European manufacturers and helping to drive the competitiveness of the region’s fastening industry. The label ‘Made in eastern Europe’ is increasingly synonymous with quality, affordability and flexibility, with eastern European manufacturers known for their ability to adapt quickly to changing market conditions, while maintaining high standards of production. These attributes, combined with cost efficiencies, make eastern European products highly competitive on the global stage.”
With a large warehouse and production facility in Zabrze, pgb-Polska is able to supply and replenish deliveries to global customers from the warehouses of its parent company pgb-Europe, headquartered in Melle, Belgium. This means customers can benefit from a truly global outlook, with strong sales activity in the Middle East, central Asia and North Africa – with particular emphasis on the European market.
“With the added advantage of utilising our global network, pgb-Polska is able to focus
on investment and innovation, which are the cornerstones of our business philosophy,” reports Krzysztof. “By continually investing in the latest technologies, we stay ahead of the curve, enabling us to lower production costs while boosting efficiency and productivity. This enables us to introduce cutting edge solutions that cater to the ever
changing needs of our customers, ensuring that we deliver both quality and value in every product.”
A recent investment includes an advanced automatic box packing system that was introduced in Zabrze, enabling a significant shift in speed and productivity. pgb-Polska has also enhanced its production capabilities by acquiring several new machines and expanding its central material supply system, which ensures efficiency at every step. Additionally, the company is embracing sustainability with the installation of energy measurement systems and photovoltaic panels to lower its carbon footprint, with further expansions planned.
The company’s commitment to sustainability has also seen a change to some of its product processes. “Recently we started with the process for an Environmental Product Declaration (EPD) on our plastic anchors, which will provide transparency about our product’s environmental impact and support our customers in complying with regulations and certifications, as well as ensure the quality of our wide range of products,” highlights Krzysztof.
pgb-Polska’s diverse range of anchoring products is distributed under the patented SMART brand, with a full range of woodscrews offered through the pfs+ and HAPAX brands, with rigorous certifications and regular audits ensuring the highest possible product quality.
Krzysztof outlines: “We take pride in offering one of the most comprehensive ranges of plastic and metal fixings on the market, designed to meet the needs of diverse industries – from construction to furniture manufacturing. We have been promoting and offering our own products for years under the SMART brand, which has proven to be a high-quality range of products for our customers.”
Krzysztof continues: “Quality isn’t just a value for us – it’s the backbone of everything we do. However what really sets us apart is our holistic approach to customer service. From prompt delivery and a complete product portfolio to thoughtfully designed packaging and robust technical support, we ensure that our clients receive an experience and service that goes beyond the product itself.”
As part of this service, pgb-Polska has recently launched an entirely new packaging model featuring new graphics to elevate the visual identity of its products. In addition, the company has also introduced customised private label packaging, enabling customers to personalise boxes with their own branding, offering tailored
packaging solutions to meet customers’ diverse needs.
The company has also recently introduced a variety of innovative fixings, including insulation plugs with long expansion zones, specialised anchors for aerated concrete and sandwich panel screws, as well as a new line of C4 coated screws – under the HAPAX brand. “All our latest investments not only streamline our operations but improve our product offering, which ensures pgb remains competitive in a growing market, while catering to both current and future customer demands,”
We take pride in offering one of the most comprehensive ranges of plastic and metal fixings on the market, designed to meet the needs of diverse industries –from construction to furniture manufacturing.”
states Krzysztof. “As we look ahead, automation is a key driver of our future growth strategy. It plays an essential role in improving operational efficiency and reducing costs, so I expect it to become even more integral to pgb’s processes, enabling us to stay competitive and continue delivering value to our clients. The goal with pgb-Polska is to continue to put ourselves at the top of the list of high-quality plastic anchor producers, by continuing to excel in both products and added services, as well as being a sustainable partner for existing and future customers.”
www.pgb-polska.com
With a wealth of experience and a track record of thousands of successful implementations, we are your experts for heat-treating technology. We don't just offer solutions – we craft them, aligning with our customer's unique needs and exceeding expectations. We are your heat treatment partners.
Check out our solutions for the fastener market:
Mesh Belt – The furnace designed for heat treatment and thermo-chemical treatment of small parts in the temperature range from 840°C to 955°C.
Rotary Retort – A solution designed to improve production and maintain the consistent heat treating and quench performance required for high-performance small parts like bearings and fasteners.
VECTOR® High Pressure Gas Quench – The single-chamber vacuum furnace that offers a wide variety of heat-treating process options.
Our service team offers consistent worldwide technical assistance aided by remote services. Count on us for seamless operation and support, wherever you are.
st Your 1 choice partner in solutions for heat treatment!
For the last seven years TOP KRAFT SK has been on an intensive investment journey of modernising and strengthening its production capacity, which will conclude at the end of 2024 with the completion of a new production facility in Myjava, Slovakia.
Active on the Slovakian market for more than 23 years, TOP KRAFT is a family owned company specialising in anchoring and fixing technology. Headquartered in Myjava, to the west of Slovakia and close to the Czech Republic border, TOP KRAFT ’s manufacturing is focused on its nylon plastic anchor range, which includes the Nail plug NP – available in diameters 6mm and 8mm and lengths from 35mm – 160mm; façade dowels FI – available in diameter 8mm and 10mm and lengths from 70mm to 50mm; the expansion plug KR – available in diameters from 6mm – 12mm; knotter dowels PX –available in diameters of 6mm – 12mm; as well as the Plug P anchor – available in diameters of 6mm – 14mm. Each product can be used for a variety of different materials including concrete, clay brick, hollow brick, aerated concrete and stone. TOP KRAFT also specialises in roof telescopes and moulds in diameters 4.8mm, 6.3mm, and 8mm, in lengths from 65mm to 525mm.
“Here in Slovakia and specifically in our region, the production of plastic products has a long-standing tradition,” explains TOP KRAFT. “This is why the decision was made to further strengthen our production capacity through investments in new machinery to modernise and replace old machines; with more economical, responsible, electric or hybrid machines; new moulds for existing products to further enhance quality; as well as the development of new products.”
These new products include façade anchors and new types of frame dowels, offered alongside its plastic anchors range. TOP KRAFT can also supply universal screws with collar for wood, metal and plastic, large flat head screws, drywall screws, plastic frame fixings, steel dowels, mechanical anchors, injection resins, a complete range of brackets and beams, threaded bar, as well as a host of tool accessories.
Plans to further expand its product portfolio include for a façade anchor range, where TOP KRAFT has just completed prototype tests and is in the stages of producing a new series of moulds, as well as working on an ETA certification for the product.
“We are very proud of our production capabilities and when combined with our complete production portfolio we are able to meet a wide range of customers’ needs,” points out TOP KRAFT. “We’re also able to differentiate ourselves from others by having a fixed maximum production capacity and by focusing on the quality of the products, which we think can be lacking in mass production. Production in Europe has clear advantages at this moment in time with all the challenges of the market. We are significantly faster and more flexible and our price is competitive – which is why it’s so important for TOP KRAFT to continue to invest in our products and services.”
As part of this service, TOP KRAFT is able to work closely with its customers to advise and recommend the best technical solution for a
project. “We know how important a one-on-one approach to our every customer is. That’s why we go the extra mile for our customers – at no additional cost. We put emphasis on sales and aftersales service and our sales and technical representatives are ready to assist customers 24/7.”
This includes tensile tests with the use of high-quality machines, accompanied with exam protocols and providing tile layouts with a round stamp, through collaboration with a civil engineering expert office, as well as the ability to produce products in private labels, based on the requirements of customers.
“Being able to provide customers with these services is another advantage we have as a smaller, family business. Another is our flexibility and, as customer demands change, TOP KRAFT must continue to adapt to meet these new requirements. More recently there is now a focus on sustainability – but not just from the environment side, from the social side too,” states the company.
TOP KRAFT is able to answer these needs by striving for maximal social responsibility, not only towards customers and employees, but also by providing work positions for people with physical impairments, support for youth sports and committing to smaller charity projects.
“With the last seven years being dedicated to the modernisation and strengthening of our production structure, as we look ahead to the future, we’d like to see new and existing customers continuing to recognise TOP KRAFT as a great partner for long-term cooperation that is able to provide high-quality, reliable and innovative products for all construction projects.”
www.topkraft.eu
Priemyselná 9 05 0 /1 , 9 0 7 0 1 Myjava
+42 1 3 4 6 2 1 42 41 I topkraf t@topkraf t .sk www.topkraf t .sk
Through investments in technology, research and development, as well as sustainability, Euromac International is committed to meeting customer needs to continue as a ‘go to’ supplier for chemical dozing solutions.
Headquartered in Gdynia, Poland, Euromac International is one of the leading manufacturers of foam guns and applicator guns for construction industry chemicals, specialising in caulking guns, foaming guns and spray guns, with the company recently introducing the production of 30% PCR PU foam guns. A few years ago, Euromac also further expanded its offering, based on customer feedback, to include bespoke procured tools, waterproofing solutions and construction accessories. The first quarter of 2025 will also see the release of a new versatile caulking gun model to serve a variety of cartridge types for adhesives and sealants.
A core part of Euromac’s business is its ability to provide private label and customised products as per clients requests, making sure the tools have an innovative design, are ergonomic, have a quick turnaround time, as well as have the right technical solutions. Euromac also offers customers optimal support in designing their own brand of tools and packaging, with a high-quality machine for pad printing a logo on the tools also available.
“By working closely with our customers, and nurturing business relationships, Euromac is committed to becoming a ‘one stop shop’ for chemical applicators. Thanks to our extensive product range, and twenty years of experience within the industry, there is very little we cannot deliver in terms of product customisation. We can also support clients at every stage of the concept – including the design – sharing our expertise and know-how to deliver the perfect solution based on our customers’ needs,” explains Euromac.
As customer needs continue to evolve, Euromac is adapting with new services, such as product storage solutions, enabling customers to keep their products in Euromac facilities across Poland and have ‘staggered’ deliveries – as and when required. As well as this, Euromac offers a bespoke procurement service, quick delivery and professional sales team support, enhancing its long-lasting relationships with both customers and suppliers globally – with US offices established recently in order to reach new markets.
“As a European supplier, adapting to meet customer needs and streamlining operations is vital,” states Euromac. As Asian manufacturers begin to offer higher standards, we must continue to use our expertise and know-how to showcase our strengths. With our in-depth knowledge and expertise, we are able to monitor market trends and able to identify sustainability and ‘green solutions’ as a key focus in our key markets.”
The company continues: “As a result, sustainability has been at the centre of our operations for quite some time and we are proud to already be serving market leaders in the field of environmental adhesive solutions. Alongside them we have developed our mind set around a more sustainable way of operation, with an investment in green energy to power our operations. We have also achieved ISO 14001 and have successfully joined the TFS – Together For Sustainability initiative.”
TFS – Together For Sustainability is a prestigious standard that focuses on ensuring the highest quality of services in the field of construction chemistry. The TFS certificate is awarded only to those companies that meet rigorous standards of quality, efficiency and innovation in the construction industry. TFS brings together the largest producers of construction chemicals from around the world, creating a platform for the exchange of best practices and the latest technological solutions, with participation proof of Euromac’s ability to maintain the highest standards and its commitment to delivering top quality products and services.
Euromac concludes: “As we look ahead, we want to continue our commitment to more sustainable operations with a new state of the art logistics and warehouse facility planned for the second half of 2025. We are also committed to looking at new ways to attract talent in our industry – something that is fundamental for our continued growth. By investing in people and growing our pool of talent we can continue to be customer focused and deliver great customer experience.”
www.euromac.com.pl
By working closely with customers and nurturing
With over 23 years’ experience as a distributor of woodscrews, electrical materials, tools and screw products, Slovenia-based LOGIN BV has completed its transition to a woodscrew and roof mesh manufacturer, with the introduction of its new TEROX brand.
Driven by a desire to produce high-quality products in Europe and ensure competitive prices, LOGIN BV began investment in its own production line for woodscrews in 2023. The company explains: “Through our years of experience in the construction industry we came to know what customers wanted and knew we could meet these requirements. As the growth in popularity of wooden building construction continues to gain pace, the development and innovations in the fastening technologies need to also keep up. That’s why we are confident the TEROX construction screws and roof mesh can change the way wooden houses are built and help optimise work processes to make wood construction stronger – one screw at a time.”
The TEROX construction screw is designed to make framing and wood house production stronger and faster. Made of high-quality carbon steel, TEROX construction screws are specially designed to increase holding power and reduce the risk of wood splitting,
a unique tip geometry to prevent wood from splitting. Available in special dimensions, the TEROX screws also have a pending ETA certification, proving their reliability and efficiency.
Also manufactured in Slovenia as part of the TEROX brand is the TEROX eaves mesh – a two-tone aluminium eaves mesh for protecting and enhancing the appearance of eaves. The TEROX eaves mesh is UV resistant with a high-quality and aesthetically pleasing appearance that won’t fade, curl or lose its shape over time. It is available in two colours – rich brown (RAL8017) and sleek anthracite (RAL7016) – making it a great choice for ensuring the longevity and beauty of eaves.
The company can also offer customers many different packaging options for the products, at the customer’s request. “Our strength lies in the flexibility of our production. Yes, ‘Made in eastern Europe’ stands for quality, but it also stands for flexibility. We are open to developing different dimensions and shapes of TEROX screws for our customers and we have the capacity to do that,” mentions LOGIN.
The company continues: “We want our TEROX brand to be synonymous with quality and so carry out daily controls in production and in all subsequent procedures. Customers want a competent partner who can provide quality products, in a much shorter time than if ordered from the Far East and that’s our advantage. The TEROX brand also brings production closer to customers, thereby ensuring fast delivery of products, as well as being accessible and adaptable to our customers’ ever changing needs.”
As part of these needs, LOGIN is also focusing on sustainability. During the build of the new production
Through our years of experience in the construction industry we came to know what customers wanted and knew we could meet these requirements.”
We want our TEROX brand to be synonymous with quality and so carry out daily controls in production and in all subsequent procedures.”
plant, a solar power plant was implemented to reduce the cost of electricity and make the plant more sustainable. As well as this, the company has ensured its products and packaging can be reused and recycled. “Our main market is the EU and with that comes the global trend of sustainability. With the global political market very uncertain, it is imperative to be as independent as possible from imports in the future. As a European screw manufacturer, we must strive to be able to supply as many of our own products at a competitive price, with every product raising the level of quality even higher,” concludes the company. “We will continue to develop our production of woodscrews and expand our production programme under our TEROX brand, with the goal to invest in new premises – where we can develop and become one of the leading manufacturers in our field.”
www.terox.si
By Barbara Sorgato, secretary general, European Consortium of Anchor Producers
Whilst waiting for the publication of the final text of the revised Construction Products Regulation (CPR), company experts are testing the effects of the new law on their products based on the last available draft, approved by the European Council and parliament.
The first test is done in the framework of the ‘so called’ CPR Acquis, which consists of rewriting the legal basis (Standardisation Request) for future harmonised standards (hENs). Rewriting the legal bases means not only including everything that has been done so far in terms of harmonised standards, but also what one would like to harmonise in the future.
For fasteners, the test bed is that of timber connectors. The two main standards on timber connectors are the harmonised standards hEN 14592 and hEN 14545, both under revision. To bridge the gap between the blockage of the publication of standards under the current CPR – a blockage due largely to the lack of an appropriate legal basis – and the evolution of new connectors, in the last few years new European Technical Assessments (ETAs) have popped up on the market. Some of these ETAs overlap with revisions of existing standards, others cover new products. Experts are now trying to put things in order and have a solid legal basis for future harmonised technical specifications. They need to do it soon, because the next Standardisation Request in the pipeline of the CPR Acquis, whose work are expected to begin at the end of 2024, is on timber products and ancillaries.
Companies also need to be aware that some things have also changed at a design level. The design prescriptions given in ETAs are not taken on board automatically by the new generation of the Eurocodes. Some of them are, some of them are not. CEN and EOTA have also agreed that conflicting design rules are no longer allowed and will require action by EOTA.
Here we are talking about standardisation, i.e harmonised standards, and not ETAs. In the revised CPR, in fact, ETAs are defined as ‘outside of the harmonised zone’. Does the industry wish to have CE Marking inside the harmonised zone? Then it needs to make sure that issued ETAs are taken on board in the new legal basis of the CPR Acquis, so they can become standards in the near future.
What ‘outside of the harmonised zone’ means is not explained in the revised CPR. The answer given to the questions posed by the experts of the European industry, anxious about the future of their investment in ETAs, is based on the opposite of the definition of the harmonised zone –Member States cannot impose extra national regulations on products inside of the harmonised zone. On the contrary, in the case of technical specifications outside the harmonised area (i.e ETAs), Member States may require additional requests such as national certifications – for instance if they consider that an ETA does not meet the required characteristics/ thresholds and levels for products placed in the market in those states. The sense of this is that, whilst European Assessment Documents allow for the assessment and sale of unique innovative products, these products might cause different requirements in different countries.
This does not mean that a CE Marking based on ETA is no longer valid, it is still valid but it just might not be enough – depending on each single Member State. What this does mean is that if a company wants to make sure their product circulates freely in the European zone, without any further additions and requests, they will have to go for a harmonised standard.
Bonded-in rods (BIR) are connectors used in timber, consisting of a bonding agent used in combination with a rod. Today, BIR are covered by an ETA and one of the two BIR components, the bonding agent, is covered by a non-harmonised test standard. The experts of the industry realised that, under the new CPR, this product will have no harmonised CE Marking, unless it is included now in the legal basis. So, they decided to give it a try and considered including BIR in it, in view of the starting works of the CPR Acquis for timber products and ancillaries.
As convenor of CEN TC 124 WG4 ‘Timber connectors, I am part of the discussion within the CEN standardisation framework and would like to report here some bits of the debate.
By addressing the possible standardisation of BIR, critical issues have emerged that impact the entire world of fasteners. BIR is a connector and consists of a bonding agent and a rod/rebar. However, EADs covering bonded products call them BIR or injection anchors, whilst standardisation addresses only its component (adhesive, glue, bonding agent). Basically, when BIRs are used in free installation in job sites – and not coming out of the factory already glued in timber blocks –in the concrete world they are called ‘injection anchor’ or ‘bonded anchor’. Instead, as the worlds of wood and concrete live on different planets and use different terms, in the wood world BIR are called ‘bonded-in rods (former glued-in rods)’ and their bonding agent is called ‘glue’ or ‘adhesive’.
It is not only about terminology, the test standard on the bonding agent for BIR was drafted by a technical committee dealing with adhesives. In the concrete world, adhesives are addressed for repair purposes only and focus rather on the adhesive properties, whilst injection anchors are covered by ETAs deriving from a previous ETAG, developed by experts addressing the product ‘fastener’ –
focusing on the structural behaviour of the system ‘bonding agent plus a certain rod and a certain concrete’.
It seems to me that with the use of mixed wood-concrete structures increasing, due to them being a very good solution in terms of sustainable construction, connectors are going to be used more and more in free installation and coexisting in mixed structures with other post-installed fasteners. That is why the CE Marking approach of fasteners used in wood, in concrete, in masonry, stones, and other base materials, should aim at a common approach and terminology.
During the CPR Acquis work, Member States expressed the wish to handle fasteners in a separate group, which is in the pipeline for standardisation. We do not know if this group will put together timber and concrete, but it seems to me that a first step in this direction has already been done. Finally, it seems to me that, because post-installed fasteners are due to be standardised in the coming years, the industry is taking the chance to test the challenges and the practical implications of the standardisation of a bonded fastener, to be prepared for a possible future transition from ETA to hENs.
www.ecap-sme.org
It seems to me that with the use of mixed wood-concrete structures increasing, due to them being a very good solution in terms of sustainable construction, connectors are going to be used more and more in free installation…”
With UK Building Safety Minister Rushanara Ali announcing in a statement to parliament, in September, plans to halt the scrappage of CE Marking, Chris Middleton, general manager at the Construction Fixings Association (CFA), outlines why the extension will benefit the whole of the UK construction industry.
UKCA (UK Conformity Assessed) Marking came into effect on the 1 st January 2021, however it became clear very quickly that it was impossible to facilitate the change over from CE Marking in this timeframe. Therefore the deadline was increased to January 2023 and then June 2025. In September, the UK government announced the continued acceptance of CE Marking past 30th June 2025 deadline.
Acceptance of CE Marking going forward is welcomed across the whole of the construction products industry. CE Marking has become not just a European conformity mark but a mark that’s accepted globally. For the UK to compete in our own market, and in export markets, we need to achieve and exceed these standards to meet current and future construction standards with regards to performance, sustainability and environmental credentials.
At the CFA we represent the leading fixing manufacturers, with our full members including EJOT, fischer, Hilti, Rawlplug, Simpson Strong-Tie, SPIT and Würth – all international companies that spend millions of pounds complying with European and international standards. At a time when we are looking to the construction industry to boost the UK economy, it seems ridiculous to inflict extra costs on the sector when in reality it does nothing to improve the quality of the product.
The continued use of CE Marking will give reassurance to engineers and designers with regards to concrete anchors, concrete screws and self-drilling and self-tapping fasteners, as well as systems having gained the European Technical Assessments’ (ETAs) 3 rd party certification and the associated CE conformity mark.
The continued use of CE Marking will give reassurance to engineers and designers…”
ETAs and CE Marking provides consistency of technical information and conformity, when used on existing, current and certainly for future projects. The valuable information provides engineers, consultants, designers, OEMs and installation specialists the confidence in the data and calculations produced from these documents. ETAs are essential in providing technical performance data to meet the higher demands of the Building Safety Act and the Building Safety regulator.
Products that gained the UKTA voluntary assessment will also be compliant and run hand in hand with the ETAs documentation. Manufacturers who only hold a UKTA for their products will also be accepted with the associated UKCA conformity mark, as the performance data of both documents are derived from the same EOTA European Assessment Document (EAD).
At the CFA we welcome the acceptance of the CE Marking extension and trust common sense will prevail.
www.the-cfa.co.uk
200+ companies listed
400+ product categories users (last 12 months)
When it comes to construction, manufacturing, and maintenance, the choice of materials and bonding techniques can significantly impact the durability and performance of a project. With over 50 years of experience, UK sealant manufacturer Hodgson Sealants offers a comprehensive range of sealants and adhesives as superior alternatives to traditional fastening methods.
In an age where efficiency, weight optimisation and aesthetics are paramount in engineering and design, traditional mechanical fasteners such as screws, bolts and rivets are no longer the automatic choice for joining materials. Sealants and adhesives are highly versatile, innovative solutions that are transforming modern construction and manufacturing by redefining approaches to structural integrity and assembly.
“For many years, mechanical fasteners have been at the forefront of bonding techniques – and it’s easy to see why. They are trusted, easy to install bonding methods, which require no curing time and create minimal mess. They are also simple to remove and replace, requiring little training, which makes them a popular choice across various industries,” outlines Kevin Nickolay, national sales manager at Hodgson Sealants.
Hodgson Sealants offers a wide range of high performance sealants and adhesives tailored for construction and industrial applications. Its silicone and hybrid sealants provide weatherproofing for windows, doors, roofing and façades, while its industrial grade products create durable, flexible bonds in sectors such as vehicle conversion, automotive, marine and leisure.
Kevin continues: “Sealants and adhesives offer a range of benefits that go far beyond simply holding materials together. One of their most valuable features is the ability to create airtight and watertight bonds, protecting surfaces from environmental exposure and preventing rust – critical in high moisture or outdoor environments. By sealing joints effectively, they mitigate the risk of corrosion, extending the lifespan of structures in harsh conditions.”
Additionally, some sealants are acoustically rated, which can help reduce sound transmission, making them a smart choice for joints in sound sensitive applications. These sealants form airtight, flexible barriers that block noise leakage through gaps and joints, and absorb and dampen vibrations, making them ideal for sound sensitive applications, such as buildings, studios and vehicles.
Fire rated sealants are also a key part of Hodgson’s portfolio, protecting the integrity of fire compartments in buildings and offering critical safety during emergencies. The company’s acrylic and hybrid sealants are ideal for sealing cracks, joints and gaps in residential and commercial properties, with the added benefit of paintability for maintenance projects.
Kevin explains: “With innovative sealants and adhesives entering the market – providing strong competition to traditional, mechanical methods – it’s crucial for product designers to carefully consider the bonding system early in the new product development process, as it can impact the project’s performance, weight and cost. Expert guidance can be invaluable in selecting the right bonding method for optimal results.”
He adds: “One of the key strengths of adhesives lies in their ability to distribute stress evenly across a bonded surface, where mechanical fasteners concentrate force on specific points. This uniform stress distribution not only extends the lifespan of bonded components, but also makes structures more resilient to vibrations and dynamic loads, minimising fatigue and failure over time.”
“Sealants and adhesives are not only technically superior in certain respects, they also simplify manufacturing processes. Without the need for pre-drilled holes or exacting alignments required for fasteners, assembly becomes faster and less labour intensive. Plus, they eliminate the unsightly appearance of screws or rivets, giving products a cleaner, sleeker look,” comments Kevin. “Since adhesive joints can be smaller and thinner than traditional fastenings, they contribute to lighter products, too. This streamlined approach is one of the key reasons why industries focused on weight and efficiency have widely adopted adhesive technology.”
Another critical advantage is the versatility of adhesives when it comes to bonding dissimilar materials. Whether joining metal to plastic, glass to composites or even wood, adhesives offer solutions where mechanical fasteners often struggle. “This ability to work across different materials opens up new design possibilities and enables performance to be prioritised without being limited by material compatibility. Moreover, the dual function of sealing and bonding provides additional protection against moisture, air and contaminants, making adhesives a top choice for applications that demand both strength and durability,” highlights Kevin.
He concludes: “Although there is still space for traditional fixing systems, as engineering priorities evolve, it’s clear that sealants and adhesives are taking a more prominent role. With their capacity for stress reduction, weight savings, and seamless assembly, they are quietly transforming the fastener and fixing industry.”
Stafa is one of the renowned wholesalers in Europe for HV bolts, nuts, and washers. We have a large stock of structural bolts which meet the international standards.
Preloaded bolt/nut/washer assemblies
Certified according to EN 14399-4-6 / 10.9 K1 (nut lubricated with MoS2)
Hot dip galvanized according to ISO 10684
TUV Certified
Certificates according to EN 10204/3.1 available
With a commitment to innovation and ongoing product development, Bond It is continuing to pioneer sealants, adhesives and building chemicals with its Incredibond adhesive and Gripbond Pro sealant –manufactured in its UK-based manufacturing facility.
Incredibond, a fibre reinforced adhesive, can be used to stick almost any material to any substrate, but is also instant grab and offers exceptional levels of bond strength, which, Bond It reports, is higher than most other hybrid polymer adhesive and sealant on the market. Thanks to its strength, Incredibond can be used as an effective and quick, easy to use alternative to mechanical fixings, such as screws and nails. It’s also suitable for both interior and exterior applications, as well as solvent-free. This latter feature means that as it cures it is low odour and does not emit any potentially harmful Volatile Organic Compounds (VOCs).
Another product that rivals Incredibond for levels of innovation is Gripbond Pro. This unique sealant and adhesive employs cutting edge hybrid polymer technology, with an advanced formulation that helps to remove application barriers faced by conventional products. For example, it can be applied in the rain and even underwater, is resistant to petrol and chemicals, and can perform across temperatures ranging from -40°C to 100°C. Gripbond Pro also remains permanently flexible, making it the perfect choice for joints and surfaces where movement may occur.
Gripbond Pro’s many other benefits include versatility – it is suitable for interior and exterior use and can be used with most substrates. This includes stone, concrete, mirrors with an acetone resistant backing, natural stone, marble, gypsum board, polycarbonates, polystyrene, PVC, many plastics, ceramics, copper, lead, zinc, aluminium, stainless steel, wood and glass. In addition, Gripbond Pro is high strength, non-staining, can be painted over with water-based paints and, like Incredibond, is solvent-free.
Bond It also continues to use innovation to meet changes in market trends, such as offering a growing number of more sustainable
solutions. These solutions include Bond It Breeze Block Foam, which can help to enhance a building’s thermal efficiency. This specialist and independently tested, airtight, multi-purpose, gun grade polyurethane foam is ideally suited for use as a gap filler on construction joints – where movement is likely, for example around windows and doors.
Phil Charles, commercial director at Bond It, states: “Bond It is no stranger to innovation. Not content to simply be one of the UK’s largest independent manufacturers of sealants, adhesives and building chemicals, we’re also committed to being one of its most innovative. As a business, we will continue to challenge convention and to explore new ideas and approaches to keep our operations, our stockists, and those who use our products, at the very forefront of what’s possible with sealants, adhesives and building chemicals.”
Responding to global consumer needs by significantly expanding the potential for decoration and redecoration, Henkel has launched an innovative adhesive solution under its ‘No More Nails’ category.
Pattex No More Nails Stick & Peel is a removable construction adhesive that strikes the perfect balance between strength and removability of an adhesive, offering the same initial tack as regular permanent construction adhesives, but is translucent and flexible enough to be peeled off in just one piece with no traces on the surface.
The product can be applied quickly, easily and cleanly – users only need to open the tube and apply in dots to the object. The user then presses the object to the wall in a twisting motion and holds it in place.
Pattex No More Nails Stick & Peel also has instant grab and can be loaded with weight after 24 hours.
Pattex No More Nails Stick & Peel will be launched step by step across 2024 and beyond under different local brands such as Rubson, UniBond, Resistol, and LOCTITE® , and has been available in stores since Q2 in Italy, France, Greece and Benelux and will be followed by Germany, Austria, Iberica, the UK, Scandinavia and Mexico during the second half of 2024. In 2025 Henkel also plans to launch the product in the USA and across eastern Europe.
Z.I.
DuPont Performance Building Solutions has recently introduced Great Stuff™ wide spray foam sealant, a new broad coverage spray foam ideal for air sealing seams, joints, large gaps, irregular surfaces and hard to reach spaces.
Designed for fast application, this one component foam sealant expands up to one inch, creating a durable, airtight and weather resistant seal, adhering to both vertical and horizontal surfaces without sagging. With a simple, hassle free formula that requires no complex set-up Great Stuff ™ wide spray can streamline the sealing process, helping to save both time and money.
“We’re excited to expand and strengthen the Great Stuff ™ portfolio with the launch of our new wide spray foam sealant,” says Melissa Helpinstill, global business director for DuPont Performance Building Solutions. “In a category of its own, Great Stuff ™ wide spray is an innovative product developed in response to customer feedback, offering a quicker, easier way to seal wide gaps and tight spaces compared to bead foam. Its lightweight shake and spray design makes
covering large areas effortless, helping users complete even the toughest jobs with greater efficiency.”
The all in one Great Stuff kit includes two cans of Great Stuff wide spray, as well as four nozzles –enabling users to tackle a variety of challenging applications. These are two white cone nozzles, spraying up to four inches wide for more precise sealing in tight spaces, as well as two blue fan nozzles, spraying up to 6 inches wide for broad coverage from a distance.
With its new line of six Parasilico AX alkoxy-based silicone sealants, Belgian manufacturer of high-quality sealants and adhesives DL Chemicals states it is launching the ‘silicone sealants of the future’.
Offering many advantages, the Parasilico AX product line is MEKO-free and is characterised by very low VOC (Volatile Organic Compounds) emissions. The high-quality sealants also offer excellent adhesion to most common materials; fast skin formation and curing; high elasticity; and have an unlimited colour choice available.
The six products in the range include the Parasilico AX Construct T –a universal alkoxy silicone for all connection and movement joints in construction; the Parasilico AX Easy Seal T – a neutral alkoxy curing silicone sealant that is, due to its high viscosity and body, particularly easy to apply and finish; as well as the Parasilico AX Easy Seal Sanitary T – another neutral alkoxy curing silicone sealant that has been developed for sealing in damp areas and for grouting tiles.
The three remaining products in the range are the Parasilico AX Sanitary T neutral alkoxy curing silicone sealant – excellently suitable for applications in high-humidity and sanitary areas, as well as for cold rooms; the Parasilico AX Standard LMN T neutral alkoxy curing silicone sealant for all connection joints and façade joints; and finally the Parasilico AX Plastics T neutral alkoxy curing silicone sealant for sealing plastic surfaces, polycarbonate and PMMA.
The new sealants are also packaged in Post Consumer Recycled (PCR) cartridges consisting of 100% recycled material.
Following an agreement with the European Organisation of Technical Assessments, here is a list of recent ETAs published in the last two months on the EOTA website.
It is important to note that existing ETAs may be amended or withdrawn so this list should not be considered definitive.
For further information and a full list of valid ETAs visit EOTA’s website. If you have recently received an ETA, and would like to have it included in our table, please email us the full details at editor@verulammedia.com www.eota.eu
24/0814 VINYL MAX VR 300 HELIX CHEM ErgoHelix A Karavas S.A
24/0851 PCT-CF-PE100 and PCT-CF-PE600 injection system for concrete N/A
24/0860 PCT-CF-CH200 bonded anchor Precontech (Hangzhou) Rail Transit Technology Co Ltd
24/0872 MO-PSU Index – Técnicas Expansivas S.L
24/0885 V-CHEM 1 Kingfisher International Products B.V
24/0902 P-CHEM 1 Kingfisher International Products B.V
24/0914 Chemfix 100 and Chemfix 600 injection system for concrete Singh Ram Impex
24/0935 Masonmate Drop In Anchor DWS, DWSL, DWSS, DWEA4 Dormole Ltd
24/0955 RAMSET AnkaScrew Tapcon Xtrem ITW Australia (Ramset)
24/0970 Injection System CTU CS – P 100 EB Ithalat Taahhut Insaat Malzemeleri San Tic Ltd Şti
24/0974 Injection System CTU CS-V 500 EB Ithalat Taahhut Insaat Malzemeleri San Tic Ltd Şti
24/1023 LX-SUPER POLYFIXER PESF N/A
24/1024 LX-SUPER POLYFIXER EASF N/A
Injection anchors for use in masonry
24/0828 TITAN TIES POLYESTER ANCHOR RESIN N/A
24/0884 P-CHEM 1
24/0886 V-CHEM 1
Kingfisher International Products B.V
Kingfisher International Products B.V
24/0912 REPOL CONEXY GEFIX SNC
Fastenings for metal
24/0830 MOTOTEK Bi-Metal Screws:
Bi-Metal 4.5xL A2+Carbon steel
Bi-Metal 5.5xL A2+Carbon steel
Bi-Metal 6.0xL A2+Carbon steel
Zhejiang New Shengda Fastener Co Ltd
With more than 10,000 references, the new INDEX® – A PERFECT FIXING catalogue not only includes innovations in the current lines, but also incorporates new ranges and products designed to meet the needs of key sectors within the world of fastening and installation systems.
New innovations include an expansion of INDEX® ’s range of anchors for direct fixing to concrete, with added versions in stainless steel A4 bimetal, which offer high resistance to both corrosion and wear during installation, as well as new references and finishes for existing models.
Also incorporated in the catalogue are new accessories ideal for work in agricultural fields, such as the rubber anchor, the macaroni and the wire connector tensioner. Other additions include a new range of metal shock anchors, a family of metric screws according to ISO 7380, bimetal drill bit screws available in A4 stainless steel, as well as solutions for the installation of solar panels.
“The commitment of INDEX®, as a manufacturer and reference in the world of fastening, is to offer a range of products that combine innovation, resistance, and versatility, always maintaining quality and safety as one of its main priorities through various approvals,” comments the company.
The new catalogue can now be downloaded online.
www.indexfix.com
ART. 9015 bi-metal thin sheet screws
with double-thread/ fine thread are made of A2 stainless steel and therefore guarantee high corrosion resistance and processing safety. Thanks to the hardened carbon steel tip, the screws are ideal for fastening aluminum and steel components to aluminum or steel profiles – without any pre-drilling! Available with or without pre-mounted A2 stainless steel sealing washer.
Exclusively at TOBSTEEL the fixing of pre-drilled aluminium components is also covered by the ETA! We are the specialist in high-quality fasteners made from stainless highgrade steel and special materials. We are used to extreme conditions and face the toughest challenges on a daily basis.
We never lose sight of our aim to give the customer just what they want. And we always offer that little bit extra.
In the construction and manufacturing sectors, safety, reliability and high-quality are paramount, particularly when it comes to fixings – with European Technical Assessments (ETAs) playing a critical role in ensuring these standards are met. As a leading specialist construction fixings supplier, JCP Fixings deems ETAs vital –irrespective of how complex, time-consuming and costly the process may be.
Issued by independent technical assessment bodies, an ETA demonstrates that a fixing has been rigorously tested, confirms its quality, and provides reassurance that it will meet or surpass the highest standards of safety, durability, and performance, which are commonly expected by the market.
It will also help to provide grounds when deciding whether the product is used on construction projects, both big and small. Engineers, contractors and distributors can rely on ETA certified products, confident they will perform as required in demanding environments.
Products with an ETA can obtain a CE Marking, which signifies the product meets safety, health and environmental protection requirements. For these products, third parties continuously inspect the manufacturing process. This will guarantee every product batch or series produced is identical in quality and performance to the one that was originally tested and certified.
As a leading specialist construction fixings supplier, JCP Fixings has committed to obtaining and maintaining ETAs for over twenty-five of its structural ranges and supplies a wide variety of approved products from chemical anchors to mechanical metal fixings.
The technical information included within the ETA covers aspects such as mechanical properties and performance of products, durability, installation instructions and safety measures. With recent changes in regulations, and an increased awareness concerning the importance of fixings to safety, an ETA can also assist in determining the correct fixings selection. The Anchor Calculation Program (ACP) that is provided for free on JCP’s website has gathered all technical information of ETA approvals within the JCP range, which helps specifiers to easily carry out calculations based on the design standards under static, quasi-static and seismic actions, as well as fire
JCP will continue to have products tested to achieve ETA certification, which will ensure it remains at the forefront of the construction fixings industry.”
JCP’s Anchor Calculation Program helps specifiers easily carry out calculations
exposure, and finally select the most suitable anchor for applications.
Mehrdad Mirshokraei, technical manager at JCP, explains: “European Technical Assessments play a vital role in the construction industry, offering all stakeholders significant advantages. As a supplier, JCP will continue to have products tested to achieve ETA certification, which will ensure we remain at the forefront of the construction fixings industry. Currently, we have our throughbolts, ankerbolts, drop-in anchors, heavy-duty anchors, injection resins and nylon frame fixings with ETAs that serve as a mark of distinction, helping products stand out in a competitive market for their quality and reliability.”
In conclusion, an ETA signals that a product has undergone a thorough assessment to meet and maintain consistently high standards of quality and performance. JCP products are available for free next day delivery, with low minimum order levels, across the majority of the UK mainland.
www.jcpfixings.co.uk
In-house
Dynamic
Machine interconnection
Doubling of the production capacity
EJOT has provided more than 6,000 high performance mechanical anchors for the installation of the electrical services and public address (PA) system in one of the UK’s most high profile road tunnel projects.
EJOT and LIEBIG branded HCR (high corrosion resistance) anchors have been supplied for the major civil engineering project by BISON UK, a UK supplier of fixings, support systems and bracketry to the M&E and building engineering services sectors.
Simpson Strong-Tie, a specialist in engineered structural connectors and building solutions, is extending its line of structural fasteners with the launch of the Strong-Drive SWD Double-Threaded™ screw.
The screw’s unique double thread design, with differentiated thread geometries and smooth mid-shank, holds wood members together tightly. It features a black exterior double barrier coating for corrosion resistance and a chisel tip for fast starts, easy driving at any angle and reduced splitting.
Lindapter has launched its brand new brochure featuring approved solutions for Mechanical, Electrical & Plumbing (MEP) building service connections.
As part of product awareness, Lindapter has produced this 28-page brochure to highlight its unique range of approved steelwork connection solutions, intended for anyone involved with the design or installation of building services.
Harrison & Clough, a leading UK distributor of fasteners and fixings, has announced new additions to its range of high-quality fastening solutions.
All showcased in a new 200-page Fastener Solutions brochure, the new additions include new socket cap screws, socket dome screws, full nuts, which have been designed to meet the rigorous demands of industries, including automotive, construction, machinery and a variety of electronics.
Rapierstar has supported the technical team at Cotswold Architectural Products during the development of an innovative multi-functional friction stay to be launched in 2025, as part of its long-term partnership.
Having worked closely with Cotswold for around 20 years, Rapierstar was recently tasked with advising on the most effective fasteners to securely attach Cotswold’s latest friction stay. Celebrating its 50 th anniversary this year, Cotswold was the first company in the UK and Europe to manufacture friction stays back in 1976.
Samac Fixings has introduced a self-adhesive Rooftec Flashing Tape, engineered to deliver exceptional protection against the harshest elements.
Rooftec Flashing Tape is designed to protect structures from weather related damage, providing excellent puncture resistance while the bitumen component delivers the perfect balance of flexibility and adhesion for long-lasting performance without the risk of slumping.
By Markus Ahr, global product manager corrosion protection, MKS Instruments, material solutions division
In recent applications of zinc nickel (ZnNi) its excellent resistance to corrosion is not only its standout feature, it also offers an important advantage that enhances its overall value. This alloy demonstrates higher corrosion protection compared to traditional zinc coatings. In addition to slowing down corrosion generally, zinc nickel also tends to corrode only on the surface. This prevents the deep and extensive corrosion often observed in zinc coatings.
As corrosion occurs, the alloy begins by dissolving zinc locally, forming a protective layer on the steel substrate due to its more negative potential. This localised dissolution appears as a fine white haze. Furthermore, as the zinc concentration decreases locally in the grains, the nickel concentration increases, shifting the potential within the corroded area to a more noble state and preventing further corrosion in that specific location. This exceptional behaviour significantly contributes to the durability of zinc nickel, even when passivate protection is diminished or absent.
As the automotive industry evolves, transitioning from internal combustion engines to electric battery powered cars, zinc nickel coatings have gained prominence. With new players entering the automotive sector and successful Original Equipment Manufacturers (OEMs) increasingly adopting corrosion protection strategies, zinc nickel electroplating has become a crucial technology in corrosion resistance. For instance, leading Chinese OEMs are now plating brake callipers for exports to Europe and the USA with zinc nickel rather than traditional zinc plating.
The transition to electric vehicles requires a number of structural adjustments, such as doubling holders on the vehicle body to accommodate the increased weight. As a result, the use of zinc nickel surfaces on components in underbody areas has become more prevalent. To address weight considerations, carburised fasteners were downsized from M8 to M6, but the overall number of hardened fasteners has increased. These are high strength fasteners that are designed to withstand stronger forces.
Since these M6 fasteners are smaller, more must be used in order to guarantee an equivalent fastener per weight in the plating barrel. This results in a 46% increase of the surface area to be plated, as illustrated in Table One. Consequently, for hardened fasteners and high barrel loads, the minimum required current is also 46% higher compared to that of M8 fasteners. This trend suggests that achieving equivalent productivity to previous systems will be a prerequisite in the years to come. These developments highlight the growing significance of zinc nickel surfaces in contemporary automotive design and manufacture.
x 60
Surface area per fastener, dm2
Weight per fastener
No. of fasteners in 100kg barrel
to be plated per barrel
Minimum required current
A
A
Table One: Comparison of M8 x 60 and M6 x 60 fasteners’ physical attributes for barrel line plating and current requirements
Considering the various advantages of zinc nickel in enhancing the longevity of steel, it is crucial that this technology is aligned with sustainable developments in the electroplating industry. Since 2015, the introduction of Zinni® 220, an acid zinc nickel electroplating process, has provided a viable alternative that yields comparable plating results with exceptional thickness distribution. Despite widespread cost pressures, both tier suppliers and OEMs overwhelmingly favour components and fasteners that undergo alkaline zinc nickel plating. Their recognition of the challenges associated with wastewater treatment for this complex solution underscores this preference. The complexity arises from the need to precisely plate zinc and nickel in the right alloy composition while incorporating 12% – 15% nickel content.
Efficiency and productivity are critical factors in zinc nickel plating, particularly in the context of alkaline zinc nickel processes. These processes require a substantial quantity of strong complexing agents to enable the simultaneous plating of nickel and zinc. However, during the plating process these complexing agents undergo decomposition through anodic oxidation, which not only consumes the agents themselves, but also other essential organic additives like brighteners. The primary concern lies in the resulting decrease in productivity and throughput, which could potentially halt the process for specific parts. This is due to the reduced coverage rate for hardened fasteners in low current density areas (LCD), which makes plating impossible as breakdown products accumulate. As a result of this accumulation, the current efficiency, during processing in a barrel, drops from 80% – 85% to 55% – 65% until the bath stabilises.
Introducing the Atotech CMA Closed Loop System, a game-changing solution for alkaline zinc nickel plating. This revolutionary technology leads the sustainability transition by reducing the disposal and treatment of zinc nickel wastewater by 90%.
Experience exceptional performance and enhanced product quality. Maintain your competitive edge and achieve your sustainability goals faster through higher efficiency, lower energy consumption and savings with the Atotech CMA Closed Loop System.
To find out more about our surface treatment solutions, scan the QR-code to the right.
Efficiency and productivity are critical factors in zinc nickel plating, particularly in the context of alkaline zinc nickel processes.”
To address this issue and create an electrolyte that is free from breakdown products, MKS Atotech has introduced CMAs. Since breakdown products do not form, a new electrolyte will maintain a performance of 80% – 85% in barrel production. These anodes employ a semi-permeable membrane to separate the anode from the electrolyte, ensuring continuous electrolyte management and avoiding any compromise in plating speed or efficiency. The term ‘compact membrane’ refers to the thinnest known membrane box in the electroplating industry, measuring only 65mm compared to the typical range of 120mm – 150mm. This reduction makes the compact membrane compatible with existing plating lines that were previously unsuitable for membrane technology.
The CMA technology employs an acidic solution as an anolyte, facilitating current transport via hydrogen ions through the membrane (Figure One). This approach minimises side effects, distinguishing it from other solutions on the market, which utilise an alkaline solution relying on sodium ions to transport currents through the membrane.
In the past, MKS also employed such alkaline solutions. However, anodic oxidation makes them prone to sludge formation on the anode surface. To maintain optimal anodic efficiency, regular maintenance every 4 to 8 weeks is essential. Moreover, it must be diluted to combat the increasing density of the electrolyte caused by the sodium ions, which negatively impacts cathodic efficiency.
To address these issues, this common technology operates with two drag-out levels. The first level involves part drag-out, which significantly stabilises the density and efficiency. The second level occurs over the membrane itself, allowing negatively charged ions like SO42- and CO32- to be transported directly to the anode. The anolyte must be continuously replaced and the process also generates alkaline zinc nickel contaminated wastewater.
The CMA technology delivers noteworthy enhancements in cathodic current efficiency. In contrast to traditional plating lines not utilising membrane technology, which typically achieve 20% – 30% cathodic current efficiency in rack plating, those incorporating membrane technology demonstrate a substantial improvement of 55% – 65% efficiency. Barrel applications utilising CMA push this efficiency further, reaching 80% – 85%. This process is therefore 25% – 35% more effective when compared to applications without any membrane technology. Furthermore, the implementation of compact membrane anode technology leads to a remarkable 32% reduction in energy consumption. This achievement not only boosts operational efficiency, but also contributes significantly to an improved carbon footprint. These results have been certified by TÜV Rheinland through thorough evaluations conducted on an installed CMA line.
Dealing with wastewater from alkaline zinc nickel processes presents a substantial challenge for customers. Production lines typically generate a considerable volume of wastewater, ranging from 300 to 400 litres per hour in three-cascade rinses following the zinc nickel process steps. This results in a significant accumulation of complexed zinc nickel containing wastewater over the course of one day of production. To address this issue, customers often employ an evaporator to concentrate the rinse water, reducing its volume by one-fifth to one-tenth, while maintaining its high viscosity. The concentrated solution is then outsourced to external waste management facilities. Nevertheless, recycling this concentrated waste is another challenge that customers must contend with.
Considering the various advantages of zinc nickel in enhancing the longevity of steel, it is crucial that this technology is aligned with sustainable developments in the electroplating industry.”
Recognising the environmental impact associated with alkaline zinc nickel electroplating, MKS Atotech initiated the Zero Liquid Discharge project a few years ago. Rather than discarding rinse water, it takes a proactive approach by employing a specialised vacuum evaporator designed to operate at low temperatures. This not only preserves organics in the electrolyte but also reduces energy consumption. The process yields two significant outcomes – the first phase produces pure water with a low conductivity of 0.2 to 0.3 micro-Siemens [µS], which is reused in rinsing after pretreatment and zinc nickel plating. The second phase generates a zinc nickel solution, which is then pumped and dosed back into the electrolyte tank, as seen in Figure Two. This innovative concept resulted in the development of the CMA Closed Loop System, tailored for both rack and barrel plating lines. The technology allows for nearly wastewater-free operations, resulting in substantial reductions in waste generation and effectively lowering the carbon footprint. These benefits have been officially recognised by TÜV Rheinland. It is important to note that the CMA Closed Loop System technology is already protected under the patent EP 4 219 801 A1. The CMA Closed Loop System can also recover and reuse up to 95% of alkaline zinc nickel wastewater, significantly reducing its environmental impact and promoting sustainability in the electroplating process.
Figure Two: Schematic representation of the CMA Closed Loop Circuit System: The vacuum evaporator connects all stages of the zinc nickel process, including both rinses before and after the alkaline zinc nickel process
Our advanced technology represents a Closed Loop System designed to comprehensively address every aspect of the alkaline zinc nickel plating process. The system incorporates Compact Membrane Anodes (CMA), tailor-made chemical additives, a vacuum evaporator, as well as a freezing unit. These components collectively contribute to a substantial reduction in environmental impact, an enhancement in product quality, and an extended lifespan for the electroplating line.
As part of the process, alkaline zinc nickel also produces carbonate when it comes into contact with air during barrel/cathode movement or electrolyte circulation. The integrated freezing unit plays a pivotal role in purifying the electrolyte by eliminating accumulated carbonate and other anions. Particularly crucial in the Closed Loop System, the integrated freezing unit serves as the sole method for removing substances from the Closed Loop while allowing the electrolyte to remain in continuous circulation.
Through close collaboration with one of our customers, we have acquired a valuable dataset that highlights the significant productivity and cost saving potentials associated with the CMA Closed Loop technology. The remarkable improvements in plating performance and the reduction in energy consumption are primarily attributed to the efficacy of the CMA anode.
The customer saw an impressive 24% reduction in energy consumption, including the energy used by the evaporator, in their plating line equipped with the Closed Loop technology. This improvement stems from an enhanced current density, which skyrocketed from 50% in barrel applications to an impressive range of 80% – 85%. These findings underscore the tangible benefits of the CMA Closed Loop technology, demonstrating its ability to optimise energy usage and enhance overall plating efficiency. Table Two and Table Three compare performance parameters of the previous barrel and rack operations without the CMA Closed Loop System and the current operation utilising CMA Closed Loop technology.
Table Three: Comparison of performance parameters in rack plating line with and without CMA Closed Loop installation
parts smoothly without any defect areas. This advantageous feature ensures that no organic film disrupts the passivation process, resulting in impeccable part quality.
The benefits extend beyond operational efficiency and part quality to encompass significant cost savings and sustainability for plating shops. The CMA Closed Loop System achieves an impressive 95% reduction in alkaline zinc nickel wastewater and a corresponding 95% reduction in sludge, underscoring its positive environmental impact and long-term economic viability.
(Commissioning of 1st Closed Loop System)
2023 (Commissioning of 2nd Closed Loop System)
Table Four: Reduction of zinc nickel wastewater and sludge generation during four years of CMA and Closed Loop System installation and operation
The data presents compelling evidence of the Closed Loop System’s ability to recycle a substantial volume of alkaline zinc nickel electrolyte within a production span of one year across two lines, accommodating both rack and barrel processes. Specifically, when focusing on non-consumable components like sodium hydroxide and complexing agents, the system recycled the equivalent of 330,000 litres of electrolyte. Moreover, since zinc and nickel are both easy to recycle, this technology successfully reclaimed a total of 212,000 litres of pure zinc nickel electrolyte. These remarkable savings underscore the resource efficient nature of the CMA Closed Loop System, presenting a substantial contribution to resource conservation.
The adoption of the CMA Closed Loop System presents substantial advantages in rack applications, leading to a remarkable 47% reduction in ampere hours and a corresponding 47% faster plating time. This transformative change increased productivity by almost 100%. A station equipped with the Closed Loop System and CMA membrane technology processed 22.5 racks in one working day. In that same time frame, equipment without the technology was only able to process 12 racks.
Beyond the enhancements in productivity, the CMA Closed Loop System contributes to superior part quality. The purified rinsewater, with a conductivity of 0.25 µS, has a positive impact on part cleanliness –facilitating the formation of a silver or black passivation that covers
The CMA Closed Loop technology goes beyond conserving resources. It also encourages sustainability and facilitates ongoing recycling – while having a positive impact on plating quality and passivate performance. It has historically been very difficult to gain approval for plating parks and new installations that involve alkaline zinc nickel processes. However, the significant wastewater reduction achieved by the CMA Closed Loop System substantially diminishes the ecological footprint of these installations. This breakthrough not only makes the system more environmentally friendly, but also paves the way for its incorporation in new plating lines and parks in the future. www.atotech.com
Established in 1970, Hariton Machinery Co Inc specialises in providing new and used machinery to the global fastener industry, as well as buying surplus equipment, whether that’s a single machine or entire factory – anywhere in the world.
Mark Hariton, owner at Hariton Machinery, underlines:
“We are proud to be the leading dealer of used fastener and cold forming machinery in the world. We have the largest inventory of machines available worldwide and supply customers in Europe and Asia, in South America and of course in North America.”
From its warehouse in Bridgeport, Connecticut, USA, as well as European warehouses in Italy, Germany and the UK, Hariton Machinery supplies assembly machines, bolt making machines, chip wringers, cold headers, conveyors, in-line drawers, drills, feeders, forging presses, hot nut formers, headers, inspection machines, packaging equipment, lathes, pointers, threading machines, as well as wire drawers and more.
Mark highlights: “Customers can be rest assured that our machinery is quality stock. As members of the Machinery Dealers National Association
(MDNA), we adhere to a code of ethics that means any machine sold from our inventory or stock comes with a 30 day unconditional return privilege. If there’s a problem with a machine once it’s received, and we can’t resolve the problem to the customer’s satisfaction, they can return the machine for a total, full refund of the purchase price.”
As well as selling new and used equipment, Hariton Machinery also focuses on buying surplus equipment – from a single machine up to an entire manufacturing facility. Mark explains: “During the past 50 years we have been involved in the outright purchase of a number of small and larger fastener manufacturing facilities. We are willing to make an offer on a single piece of equipment or an entire facility and are immediately available to discuss requirements on a confidential basis. We will go anywhere in the world to inspect and buy surplus machinery – with sales representatives in the USA, Mexico, India, Australia, South Korea, Brazil, Germany, Japan, Thailand, Turkey, Spain and Italy.”
This global presence is also shown through Hariton Machinery’s participation in fastener trade shows across the globe. This includes Fastener Fair Global, wire®, the CBM fastener show, as well as trade fairs in India and Mexico.
Another area of expertise for Hariton Machinery is the appraisal and evaluation of fastener equipment. Mark explains: “This appraisal could be done for you, or your bank, or perhaps a leasing organisation who may be interested in financing the purchase of additional equipment for use in your facility. We presently have two certified and accredited appraisers on hand for any appraisal need.”
Mark concludes: “My wife and I started Hariton Machinery in 1970, which means we have been in constant contact with major manufacturers throughout the world, for over 50 years. It’s this experience and know-how that enables us to offer the best new and used model equipment, as well as maintaining an inventory of hundreds of machines, with more coming in daily. Let’s start the next 50 years together.”
www.haritonmachinery.com
4 Foreign Branches with local after sales staff, 11 Technical Service Centers 24/7 onsite and remote service, Excellence for our customers www.sacmagroup.com
All spare parts available for shipment within 24 hours
At SACMA Group, we put your needs first. We listen carefully to your requirements, ensuring that every solution we provide is tailored to your unique challenges. With our team of experienced engineers, we bring industry-leading expertise to deliver innovative, efficient, and reliable equipment for producing high-precision metal components and fasteners across various industries.
GLOBAL : wherever you are in the world, our dedicated local technical service team is ready to support you. From fast spare parts delivery to service, remote support, overhaul, and training, we ensure your Sacma, Ingramatic, and HS Aspe equipment operates at peak performance, minimizing downtime and maximizing productivity.
LOCAL : We’re in your time zone, we speak your language, and with our global network of Service and Technology Centers, we are available to assist you whenever you need us. On-site repair and maintenance services guarantee that your operations run smoothly, securing your long-term productivity and success. We are
!
National Machinery celebrated 150 years of innovation and excellence in the machinery industry by hosting an open house at its Tiffin, Ohio facility in the USA. The event drew industry professionals, clients and enthusiasts eager to witness the advancements that have propelled National Machinery to the forefront of its field.
Kicking off with a ribbon-cutting ceremony hosted by the local chamber of commerce, the event saw local politicians and dignitaries commend National Machinery’s long-standing commitment to the Tiffin community and its positive impact on the regional economy. US Congressman Bob Latta presented CEO and majority owner Andrew Kalnow with a folded flag that had been flown over the nation’s capital in honour of National Machinery.
Attendees were then treated to an exclusive tour of National Machinery’s state of the art research and development department, showcasing the company’s commitment to innovation and customer support. The tour also highlighted the advanced machining capabilities that have been integral to National Machinery’s success over the decades. Demonstrations featured cutting edge technologies including the FORMAX® Plus, equipped with Industry 4.0 capabilities, and the new FXH Lightning. The interactive sessions allowed participants to experience the seamless integration of a Kuka robot with the FORMAX® XXV machine, alongside the precision of SMART thread rollers. The all new Lean Header & Threader also showcased how efficiency is redefined in today’s manufacturing landscape.
In addition to the facility tour, the open house hosted a series of twelve industry related educational technical seminars. These sessions covered a broad range of topics pertinent to modern manufacturing, including machine inspections and predictive maintenance, new FORMAX® technology, as well as the evolving landscape of online tools for operator training and technical support.
Industry experts from various affiliated companies also led discussions on vital subjects, such as the state of the industrial economic market; facility safety; tooling applications; and the historical evolution of National Machinery itself. Each seminar was designed to equip
The open house fostered a tradeshow-like environment during lunch breaks, allowing guests to network with industry professionals and explore a variety of products and services. Booths were staffed by representatives from National Machinery’s customer support, Cleaning Technologies Group LLC/Ransohoff, SMART Machinery, the Industrial Fastener Institute, Drawing Technologies Inc, CONDAT and Brankamp/S&K. This dynamic setting facilitated valuable discussions and partnerships among attendees, enhancing the sense of community within the industry.
Each afternoon, the event featured a classic car show and rally, adding a unique and nostalgic flair to the festivities. National Machinery has a deep history within the automotive industry and for over 100 years has celebrated with a car show, car rally or a car caravan at major anniversaries. Guests were treated to a display of modern and classic cars from different eras and brands.
With doors opening at 08:00 each day, the open house was meticulously organised to maximise engagement and learning. Attendees also had the opportunity to speak one-on-one with technical experts, deepening their understanding of both National Machinery’s products and the broader industry landscape.
As the event ended, it was clear that National Machinery’s 150 th anniversary open house was not just a celebration of its storied past, but a look forward into a future filled with promise and innovation.
“One of the biggest goals was to hopefully enable participants to leave the event inspired and equipped with new knowledge and connections, ready to tackle the challenges and opportunities that lie ahead in the machinery sector,” explained Andrew Kalnow. “This landmark event exemplified National Machinery’s commitment to its customers, partners, and the industry at large, ensuring that the next chapter of its legacy will be just as impactful as the last. As the company looks forward to the future, it remains dedicated to advancing technology and fostering a collaborative community within the machinery industry.” www.nationalmachinery.com
Turn over for an exclusive interview with Andrew Kalnow, CEO at National Machinery
With National Machinery celebrating its 150th anniversary, we decided to speak to CEO Andrew Kalnow about how the company has developed into a leader in advanced cold forming machinery and the plans the business has to ensure it stays at the forefront of the sector.
National Machinery has just celebrated its 150 th anniversary. Can you tell us about how the company started and what the key points have been in its development?
“National Machinery started in 1874 in Cleveland, Ohio, USA, and moved to its current location in Tiffin in 1882. Meshech Frost, my great grandfather, was attracted to Tiffin because of its advantageous logistics and resources. The factory could be located on a main east/west railway; there was cheap land to build a much larger factory; and Tiffin boasted plentiful skilled labour with its German and Italian immigrant populace.
During those early years National focused on small machines to make bolts, nuts and nails. However, as the automotive industry boomed in the industrial northern states, National seized the opportunity to supply forging equipment to those growing markets. The company then introduced innovations such as the Maxipres vertical press and cold nut formers with rotating transfers. Boltmaker™ equipment up to 1¼ inch was also introduced, which led to National making significant international sales, as well as domestic.
After Word War II, with the Marshall Plan in full force to rebuild Europe, National’s strategy to meet burgeoning demand for cold forming
As a machine builder, National Machinery is not only distinguished by the speed and quality of its machines, but also the strong service and support we offer customers worldwide…”
equipment took a bold turn when it acquired, in 1958, the largest cold forming machine maker in Europe – J.G. Kayser in Nuernberg, Germany.
A totally new factory that approached the size of the Tiffin factory was completed in the early 1960s in Nuernberg and even today the city remains the hub for our European operations.
We also expanded into Japan, in 1973, and we are still located in Nagoya, which is a key access point to the Japanese bearing and automotive markets. Finally, the 1990s ushered in the FORMAX® line that continues to evolve today with new features and models on a regular basis.”
What is the machine portfolio that National Machinery can offer customers today? How does the company guarantee the quality of these machines?
“Our main line of equipment is FORMAX®, which comes in various sizes, die configurations and options – based on customer requirements. Machines can also be specialised based on the part application to make the most ‘net shape’ part possible.
A fundamental part of our machine portfolio is to ensure quality, which is a process that starts with engineering design and control of the bill of material and then flows to our own machining department and suppliers. Once assembly starts, we observe our assembly work
Another key service that we can supply customers is tooling design, whether manufacture or development, thanks to our Met-MAX innovations group..”
instructions and then do a thorough testing validation of each machine. The processes in place to monitor quality are extensive and we truly follow our policy of ‘build and delivery quality’.”
As a global business, what is it that National Machinery can offer customers? What are the key factors that enable you to stand out from competitors?
“As a machine builder, National is not only distinguished by the speed and quality of its machines, but also the strong service and support we offer customers worldwide. We ship to customers all over the world and our key differentiation is that we have regional facilities for local service and support. These local service centres stock inventory based on the installed base of machines in that region. This means that it doesn’t matter if a machine is 50 years old or 5 years old, we can help service and support it.
Our customer support function also includes spare parts, technical service and rebuilding. So, it’s not just spare parts supply, it is also available technical resources to answers questions and then in-plant technicians to provide service as needed. We are also capable of rebuilding all vintages of our machines at our regional locations.
Another key service that we can supply customers is tooling design, whether manufacture or development, thanks to our Met-MAX innovations group, which has the goal of ‘pushing metal to the maximum’. This process development group can help with small or large projects and has a state of the art Tooling Technology Centre to build tooling. It also has multiple development machines in our R&D area that are permanently allocated to support part application development.”
have these markets been developing recently and
“We are involved in many markets, which is done on purpose to both serve a large range of customers and to extend the range of cold forming opportunities. Recently we have been fortunate to be involved in some new part applications related to the automotive EV market and although some parts of the global market have not grown at the rate expected, the hybrid sector can still utilise those components. We are also involved in various small niche industries where we can help an OEM with new product development – so they can produce new products successfully with cold forming.
Robot-for-Changeover, as well as our latest Industry 4.0 features. Our National Online website portal also gives customers access to not just their own specific machine information, but now also includes a FORMAX® operator training video series.
As always for the future the key will be innovation, as well as how to make new and existing formed parts the fastest, and most efficiently, for our customer base. That’s what we have built our company on doing and that is what we plan to continue to do moving forward.”
www.nationalmachinery.com
As for opportunities, those that visited our Tiffin site during our 150th celebration got to see a glimpse of the future. There were numerous brand new machine tools in our machining departments to make parts faster, more efficiently and to tight tolerances. They also saw new FORMAX® machines for small diameter fasteners and parts; specifically the Lean Header & Threader and FXH Lightning. Additionally, we showcased specialised technology such as
Screws, nuts, washers, springs, clamps – fasteners are essential for safe and reliable assembly. In the course of increasing demands on technical cleanliness in industrial production, fasteners also have to meet increasingly higher cleanliness specifications. In order to achieve these specifications reliably, economically, and sustainably, cleaning processes and systems that are optimally adapted to the task at hand are required.
Whether in the automotive and transportation sectors, traditional mechanical and plant engineering, energy technology, the production of construction and agricultural machinery, the manufacture of medical devices for diagnostics and therapy or other industrial sectors, the requirements for component cleanliness have increased enormously in recent years – including fasteners. Even the smallest particles and/ or minimal film residues on the surfaces can impair the results of subsequent processes, such as coating, heat treatment or corrosion protection, and disrupting the long-term, flawless functioning of individual parts or complete systems.
the form of surface energy or surface tension (e.g mN/m = millinewtons per metre). In the case of fasteners for high-tech areas, including high vacuum technology, semiconductor production equipment, and medical technology, individual specifications or factory standards, such as outgassing rates, are usually added.
In order to avoid this, limit values for the particulate and filmic contamination still permitted on the component surface, also known as ‘residual dirt’, are increasingly being defined for fasteners. In terms of particle cleanliness, these can be specifications such as ‘no particles larger than 200 µm’; the maximum number of permissible particles in a size class; or a weight-based (gravimetric) determination of the amount of residual dirt. Specifications for filmic cleanliness are often given in
In addition to the cleanliness specifications to be met, there are various other challenges when cleaning connecting parts. These include different materials such as steel, stainless steel, aluminium, titanium, non-ferrous metals, plastics and composite materials, as well as the sometimes very complex geometries of the parts. In addition, the screws, nuts, and other parts, come into contact with various machining media during the manufacturing process, which generates particles and abrasion. They leave residues on the surface that can accumulate to form a mixture that is difficult to remove or, like some special lubricants (e.g Molycote), is inherently difficult to clean off. Cleaning, which is usually carried out as bulk material, often results in high weights and dense packings. Small fasteners in particular are difficult to clean and dry. High throughputs, short delivery times and sometimes low margins are further aspects.
In order to achieve the required cleanliness in a stable, efficient and sustainable manner, and to master the other challenges economically, comprehensive know-how about the various cleaning technologies, as well as knowledge about the applications and the physical relationships are required. As an experienced full service provider of future oriented solutions for industrial component cleaning and surface treatment, Ecoclean GmbH has both. This guarantees cleaning solutions that are designed and equipped to meet requirements and with which defined cleanliness specifications up to the highest demands in ultra-fine cleaning can be reliably achieved.
Fasteners are usually cleaned as a batch in wet chemical processes. The following factors must be taken into account: Material, size, geometry and weight of the component, type and amount of
For efficient and short cleaning processes, the systems are equipped with various application specific process technologies. This includes high-pressure spraying with a pressure of up to 16 bar for solvent systems, which is used for densely packed batches of bulk goods and complex parts
contamination, downstream process and resulting cleanliness specifications, as well as throughput requirements. On this basis, it can be determined whether the adhering contaminants can be removed most effectively with a water-based cleaner, an environmentally compatible solvent or modified alcohol with lipophilic and hydrophilic properties. This information also makes it possible to define the most suitable process engineering and drying technology. Several cleaning steps are often required due to the different processing media used in the various manufacturing steps, such as pressing, rolling or heat treatment.
Cost efficient and compact chamber systems that work under full vacuum when using solvents, and have appropriate systems for media preparation, are state of the art for cleaning connecting parts. The batch capacity ranges up to lattice boxes. If a large variety of materials, very high throughput requirements, or the cleanliness specifications to be achieved during final cleaning, make the use of a chamber system unfeasible, modular ultrasonic multi-bath immersion systems such as the UCMSmartLine are available. Thanks to modules with integrated electrical and control technology for the cleaning, rinsing, drying, loading and unloading process steps, as well as a flexible transport system, it can be easily adapted to the respective task.
To keep the costs per cleaned component as low as possible, the systems are equipped with various application specific process technologies, for example for spray, high-pressure, immersion, ultrasonic and plasma cleaning, steam degreasing, injection flood washing, Pulsed Pressure Cleaning (PPC) or Ultrasonic Plus and, if required, for passivation/ preservation of the parts. In combination, these processes make it possible to influence both the cleaning result and the cleaning time for specific components. For densely packed bulk material batches and complex components, spray processes and injection flood washing with adjustable pressures of up to 16 bar also ensure significantly improved results and shorter process times for solvent cleaning processes. Pressure change processes such as PPC or Ultrasonic Plus, in conjunction with aqueous or solvent immersion cleaning, enable contaminants to be removed reliably and quickly from small cavities. By combining processes in one cleaning system, that would otherwise require several systems, such as solvent or aqueous batch cleaning with a subsequent low pressure plasma process, the component surface can be prepared effectively and efficiently for subsequent coating, among other things.
If a large variety of materials, high throughput requirements or cleanliness specifications necessitate an ultrasonic multi-bath immersion system, modular solutions with integrated electrical and control technology and a flexible transport system are available.
Whether in a chamber or ultrasonic multi-bath immersion system, the cleaning of fasteners for high-tech applications is often based on validated process parameters, compliance with which must be monitored and documented, such as the ultrasonic frequency and power. The Acoustic Performance Measurement (APM) systems from Ecoclean GmbH provide a solution for this task, with which measurements up to an ultrasonic frequency of 2,000kHz can be carried out inline and reproducibly. Monitoring is carried out using a condenser or laser-acoustic microphone, which is aligned with the surfaces of the ultrasonically equipped cleaning and rinsing tanks of a multi-bath immersion system. The measurements are thus carried out without movement or contact, ensuring the reproducibility of the results. In addition, APM technology makes it possible to detect ultrasonic frequency and sound pressure through ‘walls’. It can therefore also be used in closed cleaning and rinsing tanks, as well as chamber cleaning systems. Analysis, evaluation and storage of the recorded data are carried out by the measuring system software.
The best way to determine which system and process technology is optimal for the respective task, in terms of cleanliness and cost-effectiveness, is to carry out cleaning tests with originally contaminated components. Ecoclean has extensively equipped test centres worldwide for this purpose, which enable tests to be carried out under near-production conditions.
In order to help make inspection processes faster and more efficient, Marposs Group has introduced a new 3D functionality to the Marposs Optoflash, an optical measuring unit that offers ultra fast cycle time – enabling both new level of quality controls and a superior ease of use.
In the fastener industry, quality controls of screws are a crucial activity for operators. While manufacturing operators generally control screws during ‘work in progress’ execution and at end of process, those operators in the supply channel need to guarantee inbound and outbound compliance to the nominal screw specifications.
The high volume production, together with the high variety of screw models, generally results in demanding conditions for any operator in this industry, due to complexity of controls and consumption of time to execute the measurements. Technological innovation plays a key role in making inspection processes faster and more efficient to meet these challenges, which is where the Marposs Optoflash is able to stand out.
Thanks to its multiple and fixed position sensors, Marposs Optoflash can automatically control several different features on a screw in seconds. “The measurement of screws is not generally an easy task, due to the variability of the screw features and its profiles,” explains Marposs. “Nevertheless, on the Optoflash the measuring technical complexity is managed by the software and is not visible to the users. In fact, the Optoflash automatically compensates the variability of the part positioning on the holder and also the possible form errors of the screw.”
In addition to Optoflash’s ability to analyse screws over 360°, and automatically combines several images in order to determine both part optical axis and measurements of the features, the latest product evolution enables 3D part reconstruction and 3D measurements. “By the appropriate synchronisation of its multiple sensors, and by the combination of the
full area images, the 3D software engine of the Optoflash can easily reconstruct the workpiece in a 3D format,” underlines Marposs. “The 3D measurement not only performs better than a traditional 2D projection, but the 3D surface reconstruction enables the possibility of extensive part validation, since the 3D measurements are based on thousands of points from the surface of the workpiece. For this reason, irregular part profiles, interrupted surfaces, or threads, are perfect applications where the Optoflash and its 3D engine gives distinctive performance with respect to the traditional approaches.”
On top of the performance, the 3D functionality of the Optoflash also boosts the ease of use. After each measuring cycle, the workpiece is visualised on the display of the product in 3D format, together with the measurement results from the cycle. The operator can navigate the 3D of the workpiece directly from the touch display of the Optoflash and they can easily review each inspection point by its images or they can immediately identify and locate any incorrect part feature detected during the cycle.
Marposs adds: “The standard measurement toolkit can easily solve any of the most typical measurement problems. These include dimensional, position and form measurements – both in static and dynamic mode. The library also includes thread analysis – maximum and minimum diameter, pitch diameter, pitch value, thread angle, thread linearity, as well as total thread length.”
www.marposs.com
Packaging is a crucial part of a product’s journey from production to the customer’s hands. It plays a vital role in ensuring the protection, quality and presentation of goods. However, even the smallest details can sometimes cause significant problems, leading to costly delays or dissatisfied customers.
Bonotto Packaging Srl states it can help resolve these challenges efficiently and accurately, helping customers avoid issues such as improper box closures; damaged or defective parts included in packaging; or inconsistencies with printing and labelling. “A common issue is the closure of box flaps, where the box may not seal properly, risking the integrity of the product during transport,” points out Bonotto. “This can result in customer complaints, potential returns, or even damage to your brand’s reputation. Another frequent problem is the inclusion of defective parts, such as screws with damaged threads or faulty components, which can lead to customer frustration and negative reviews. Small details like these can have a significant impact, but they can be hard to detect manually.”
Bonotto Packaging understands how essential it is to maintain flawless packaging, which is why it offers cutting edge technology that addresses these issues head on. “Our packaging systems are equipped
with highly accurate camera inspection tools designed to detect even the tiniest of errors. Whether it’s a box with an open flap, a defective screw, or the need to ensure the precision of printed labels and barcodes on boxes or bags, our solutions have you covered,” underlines Bonotto. The company adds: “By utilising our advanced inspection systems, you’ll not only increase operational efficiency but also enhance customer satisfaction. Customers can trust that each package is assembled correctly, each label is clear and accurate, and that no defective parts slip through the cracks. This results in fewer complaints, fewer returns, and a stronger relationship with your customers. We help customers maintain the highest quality standards that your business, and your customers, deserve. With us, you can focus on delivering products, confident that your packaging is in expert hands.”
www.bonottopackaging.com
RAMAC is an Italian company specialised in the design and development of packaging solutions for technical products, using a design approach that focuses on simplicity, intuitiveness and low management costs.
Whether it is screws, furniture fasteners, components or hydraulic parts, RAMAC deploys its personalisation and customisation ability to answer customers’ requests, with the company always looking to improve and develop new solutions for customers’ applications.
A prime example is the BL-04 Hybrid, a packaging machine designed for the packaging of screws, fixings and small metal or plastic parts, which is an extremely versatile and precise machine that enables packaging both in bags and boxes, according to customers’ needs.
The machine features an automatic weigher with five independent vibrating linear channels, which allow a homogeneous and constant separation of the product in the roughing and finishing channels. Depending on the selected production order, the weighed product is sent to the bag packaging machine or to the boxes line.
“To pack in bags, customers can combine a packaging machine, with various types amongst our range, depending on their needs. For packaging in boxes, however, customers can use a semi-automatic system or a fully automatic line with box forming, up to the automatic closing of the lid and palletisation,” explains RAMAC. “We are dedicated to the 100% Italian production of packaging machines for technical items and thanks to our innovative BL-04 Hybrid machine, which offers wide versatility, customers can double the possibility of packaging in boxes or bags.”
The newest development in SKAKO Vibration’s portfolio of products is its semi-automatic packaging machine, optimising its compact weighing and packing system, which can fill different kinds of carton boxes and plastic or steel returnable boxes ( KLTs).
SKAKO’s semi-automatic packaging machine is especially suited for short and medium size productions, as it is easy to operate and reprogramme. The machine also features a compact, single floor design, which allows it to be placed with a limited foot print – without the need for extra ceiling height. The machine also has an open construction, which makes the process both accessible and easily monitored. This is important for the fastener and automotive industry, which usually operates with many different items, thus has the need to be able to switch from one to another, without the risk of getting them mixed.
“We have been manufacturing light to medium duty vibratory feeders and screens since 1963 and the hardware industry is a significant and growing part of our business, especially feeding, weighing and dosing equipment for heat treatment lines,”
explains SKAKO Vibration AS. “Therefore the semi-automatic system for the packing industry fits perfectly and our know-how could be used.”
The system consists of a vibrating storage feeder, a vibrating feeder, a chute system with accumulation possibility, a table with integrated load cells and an integrated sample/check weighing platform. It can be configured in different sizes and supplied with a lift and tip unit. The lift tipper can be configured according to the customer’s specific container/containers.
“Furnace feeding systems are a very important part of many industrial processes, for instance the full automatic and weight guaranteed feeding of belt, annealing and tempering furnaces; discharge of industrial washing and drying machines; as well as the feeding and discharge of industrial electroplating and surface treatment lines,”
underlines SKAKO Vibration. “Thanks to our semi-automatic packaging machine, customers get controlled, automatic and weight guaranteed feeding of bulk material –ensuring a steady product quality, optimised efficiency of the downstream equipment to be fed, as well as reproducible and traceable production parameters.”
A manufacturer of high precision aerospace fasteners in Kansas, USA, has recently purchased a VisionLab-150, 3D measuring system from General Inspection LLC to measure its full product range - up to 150mm in length and 50mm in diameter.
VisionLab-150 will also help to streamline the manufacturer’s inspection process by reduced inspection times, and improving quality through fast, accurate and complete dimensional data reporting.
This system is equipped with SurfaceView for 360⁰ visual defect detection, End-View to inspect head markings and measure broach features, and Upper Tooling/Bit Kit that measures recess depth and recess concentricity.
“The VisionLab system is a versatile, accurate and fast inspection machine designed to handle a wide range of applications. For time savings, traceability, and removing human error, VisionLab creates customised, detailed reports with graphs and data charts – saved in CSV or Excel formats or seamlessly uploaded to 3rd party SPC packages,” concludes General Inspection.
Heat treatment expert AICHELIN Group has expanded its product range to include innovative industrial vacuum furnaces and technologies. These modern, flexible and environmentally friendly solutions are sold, designed and produced by the joint venture company AICHELIN ST Vacuum GmbH, which was founded in May.
The innovative vacuum furnaces offer the usual high AICHELIN quality and clear advantages for companies in industries such as aerospace, the energy sector, tool and mould making, the automotive industry, medical technology and contract heat treatment – with the modular design enabling customer-specific solutions for various heat treatment requirements.
“By expanding our portfolio, we are completing our offering in industrial heat treatment. Our vacuum furnaces combine technological innovation with sustainability. This allows us to support our customers in optimising their production processes and reducing their ecological footprint at the same time,” reports Christian Grosspointner, CEO of the AICHELIN Group.
The new technology solutions are characterised by precise process control, energy-efficient design and user-friendly operation. Fast heating and cooling times considerably reduce cycle times, which leads to a significant increase in process efficiency. The furnaces are versatile and can be used for the heat treatment of various materials for hardening, brazing and sintering.
The energy efficient processes also help to reduce the carbon footprint – while providing solutions to the challenges of modern manufacturing. This combination enables industrial companies to increase their production quality, optimise processes, significantly lower operating costs and reduce emissions at the same time. Companies also benefit from short delivery times and the global AICHELIN sales and service network.
INNOVATION AND DIGITIZATION OF FORMING PROCESSES FOR INDUSTRY 4.0
The post-process data evaluation offers the possibility to analyze and evaluate the entire process data for the first time. Important conclusions can be found about process variation, setting of monitoring limits and recognition of process influences during the whole production run. The knowledge acquired is helpful in determining the optimum process parameters and provides detailed conclusions about tool wear.
By Peter Standring, technical secretary, Industrial Metalforming Technologies
No genuine forward progress can be made without first obtaining a clear understanding of the knowledge required to make it. Getting to the bottom of a problem means just that –because without sound foundations, nothing substantial can be constructed.
For example, chemistry is based on the identification of basic elements, without knowledge of which the world we currently inhabit could not exist. Likewise, physicists believed they had established the smallest possible unit of an ‘element’ when they discovered the atom. Yet, the quantum world of sub-atomic particles has revealed that on a human scale, there are more zeros needed going smaller than required to reach the edge of our expanding universe.
This is why we can never hope to obtain perfection! Of course, peering into a mist like this is simply a recognition of our collective human ignorance but fear not, we can get by quite well by employing the knowledge we do possess. If ‘perfection’ is beyond our grasp, let us change the requirement to ‘fit for purpose’ and from our existing achievements we can certainly obtain that.
When used in a marketing context, the word ‘quality’ is often a euphemism for ‘hype’. Quality, time, performance, life, etc, all are seeking to use the term to exceed the norm. However, if the norm is ‘fit for purpose’ why do those in the market seek to enhance their product by giving it an unnecessary epithet?
Being commodity products, fasteners do not generally have to attract the eye or become a ‘trend’ item. They need to carry no more than an internationally recognised, acceptable and traceable means of identification. Anything more would simply mean unnecessary embellishment and extra cost. In the world of fasteners ‘quality’ is taken as read and simply implies that the item meets and satisfies all the required standards. However, in an imperfect world, the question then becomes, what level of defects does the purchaser accept?
If ‘perfection’ is beyond our grasp, let us change the requirement to ‘fit for purpose’ and from our existing achievements we can certainly obtain that.”
In almost every issue of Fastener + Fixing Magazine, the range of fastener geometries and their apparent complexity seem to increase. This is probably not true as over the years, specialisation, standardisation, and rationalisation, of both the sector and its products have created significant conversion. Notwithstanding, the changes in the various fastener markets and the opening of new ones, plus the continuous challenge to achieve more with less, has undoubtedly made fastener geometry more complex. Special heads requiring special tools – for both security and brand – as well as multi-functional bodies/ threads, which include the capabilities of both cutting and fastening, are currently available. Dual purpose applications requiring different material properties, which can only be achieved in a single product by a combination of dissimilar materials. These all increase the number of attributes in the part and with them, the need for assessment.
In every fastener, the attributes associated with it include tolerances –dimensional (length, etc), geometric (roundness, etc), material (properties), as well as surface finishing (coatings). As shown in Figure One, depending on the ‘standards’ to be met, these will also include destructive/non-destructive testing of samples per batch; full documentation of input material; plus all fully audited processing of the parts (equipment used/calibration, etc), heat treatment and inspection. Within the EU, and possibly elsewhere, this will also include information required for the Carbon Border Adjustment Mechanism (CBAM) regulation.
In every fastener, the attributes associated with it include tolerances – dimensional (length, etc), geometric (roundness, etc), material (properties), as well as surface finishing (coatings).”
Figure One: Idealised closed loop of fastener design, manufacture and application
In the production of threaded fasteners from rod or wire, it is relatively easy, using off the shelf equipment, to obtain both dimensional and geometric measurements once a part has been made. Although this may be a necessary part of a batch inspection process, on its own, it is wholly inappropriate for mass manufacture. Clearly, off the machine sampling is a post-process operation – therefore any part found to be out of specification will need the process to be stopped and checks made to determine, how, when and why the process went out of control.
This is why in-process sensors, both recording and control, are an absolute essential to gain knowledge over the process route. All component dimensions have both an upper and lower limit – the specified tolerance of the designed feature. The wider this tolerance, the less accurate/expensive the equipment needed to make the part.
As a tool, that is making a part, wears the part dimension approaches a limit and the sensor informs the machine setter of the changing situation. If left unattended, the system will automatically switch off once the tolerance (action) limit is reached. Such information has been listed for many years in the International Tolerance (IT) Grades Table Chart ISO 286-1. IT grades 01 – 18 underline the measuring tools, fits required and manufacturing methods available. IT 01 represents the tightest tolerance grade.
When a machine is initially set-up it is generally arranged to make the part to the particular tolerance level (upper or lower), which will enable tool wear to change the dimension within the tolerance band. A hole will get smaller and a cylinder larger as a manufacturing tool wears. Continuously recording these dimensions sequentially and then visual plotting the output will indicate that the process is under control. To ensure the upper and lower tolerance limits are not breached, other tolerance bounds are produced to lie inside them. These are termed ‘warning limits’. The statistical data obtained from such systems enable statistical process control (SPC) to be obtained, which in turn provides
automatic control over the manufacturing process. Also, it provides direct online information of the ‘trends’ in performance of the equipment, materials, settings, etc.
Dimensional measurements are basically two dimensional. Geometric attributes on the other hand refer to a component’s surface features. These include cylindricity (roundness), flatness, parallelism (between two opposing faces), squareness (between adjacent faces), eccentricity (radial departure from a common axis), etc. Geometric Dimensioning and Tolerancing (GD&T) is significantly more complex than dimensional tolerancing and whilst there exist a number of standards, such as ASME and ISO, there are differences between them.
The whole concept is based on the establishment of a theoretical datum from which all measurements are determined. This can be a surface or a point, plane or an axis, which provides the reference on which everything else is based. For example, in the case of flatness, it is assumed that a second ‘theoretical’ surface exists, displaced away from the ‘datum’, by the distance of the tolerance boundary. For a component to be deemed ‘within tolerance’, its surface must lie between these two imaginary planes.
Of course, it is perfectly possible that the datum surface may lie between the tolerance limits. This is the case where surface roughness can be determined using the technique of Centre Line Average (CLA). Here, the measuring stylus is drawn across a surface and the resulting distribution of recorded ‘peaks and valleys’ used to determine the CLA value of surface roughness. Other visual and statistical methods for determining surface roughness also exist.
It should always be recognised by design engineers that whilst geometric attributes may be key to the functionality of a part/assembly, their careless, or misunderstood use can cause serious manufacturing problems and cost to the fastener manufacturer. For example, if a
sophisticated heat treatment regime marginally changed the helix angle of a threaded component – giving rise to varying thickness (distributed mass) – would that matter if its ‘fitness for purpose’ was unaffected. It might, if the person who designed the part included an unnecessary geometric tolerance, which was now exceeded.
Existing fastener specifications relating to material requirements and their audit trail are well established – that is until a Regulatory Body decides on improvements. However, where more multifunctional, multi material, multi design features are incorporated to obtain more for less, the need for performance testing increases. Simple tensile, torque and hardness testing are of course necessary but if the fastener is to be used in hostile environments, under many different loading conditions and possibly in maintenance excluded areas until end of life, then discerning customers will require suitable guarantees of satisfaction.
Accelerated testing is well established as a practical tool for a wide range of products, but in a fast moving world of solving someone else’s problems, as they emerge, is this an extra burden that fastener manufacturers should reasonably be expected to shoulder?
As fastener specialisation increases, the desire to do more with less falls increasingly on the fastener/assembly interface. It is also a fact of life that all fastener users, if given a choice of having to use a fastener or not use a fastener, would choose the latter. Fortunately, despite the development of 3D printing and adhesives, for both the fastener manufacturer and distributors, the need for fasteners is unlikely to change any time soon.
However, the requirement for fasteners to meet the demands of new and emerging market sectors has, in less than one working lifetime, transitioned amazingly from pre-electronic ironmongery, through space travel to climate change.
Regarding climate change, two camps exist, those who want to ensure what we are doing to the planet is controllable, and others who don’t. In reality, it’s the folks who put up the signs who determine the speed limit not drivers. The signs on climate change have been put up and are continuously being added to. In short, if you want your goods to flow from here to there, you too must abide by them.
End of life, recyclability, ease/cost of disposal are all natural targets for the legislators to enhance the quality of life of the only place in this universe where people can live.
Clever, multifunctional designs, incorporating multifunctional materials, may offer OEMs great opportunities for lightweighting, extreme service conditions, and reduced assembly inventories, but they may also provide easy targets for those seeking to improve the desired quality of life for all. This is not just a consideration relating to the product, but it also involves all aspects of fastener manufacture –including its supply chain partners.
On ancient maps showing strange and often uncharted lands, it was not uncommon to find illustrations of two headed people and inscriptions stating: ‘Here be dragons’.
Given the rapidly changing world in which we live today, it might not be too long before the fear of global pestilence, flooding, drought and air quality could produce a world not dissimilar to us than those found on ancient maps. The future is simply unknown territory and without a map, who can say what strange things might lurk there.
The ubiquitous nature of fasteners, and the fact that they were probably mankind’s first technical achievement, places them at the leading edge of our voyage of discovery into the future. For this reason, the development of fasteners and the reasons why they are the way they are will be known first by those who make and use them.
The electrical contact resistance between two fastener components is a key quality parameter, especially when the bolted joints carry electrical current. If the resistance is too high, heat is generated between the elements. In response to this problem, Kistler has introduced the OhmBox to its ANALYSE friction coefficient test stand to measure electrical resistance while fastening is actually in progress.
With the help of the Kelvin method, users of the new OhmBox can precisely record the electrical contact resistance during the fastening process and correlate it with other parameters, such as applied torque.
To do this, the user connects two measurement tips as close as possible to the bolted joint. The OhmBox then constantly emits current, and the highly sensitive measuring system registers the voltage loss through the electrical contact resistance – even down to the microohm range. In this way, the user can accurately determine the level of electrical resistance during tightening and slackening. To prevent distortion of measured values by external influences, the bolted joint under test can be fully isolated in the test set-up.
The testXpert® software from Kistler records the entire testing procedure, with online user defined data visualisation. In the software, the electrical contact resistance can then be displayed together with other measured values, such as the applied torque over the angle or time axis. This enables developers to determine and verify the optimum combination of parameters quickly and reliably – giving them a valid basis for meeting quality requirements and comparing different materials.
Kistler points out the OhmBox can supplement an ANALYSE system that is already in operation, or can be combined with a new system with additional, individually selectable modules for friction coefficient, tightening torque or preloading force. Following a straightforward set-up procedure carried out by Kistler experts, manufacturers can then design and implement a diverse range of test scenarios – thus ensuring that their bolted joints remain safe and reliable, even when carrying electrical current.
www.kistler.com/reliability
With the WAFERinspect AOI measuring system, Confovis GmbH is expanding its WAFERinspect product range with an AOI tool, which combines defect inspection, defect review, as well as 2D and 3D measurements in a single system.
For defect detection, the Confovis WAFERinspect AOI uses current computer architecture to compare golden samples in the memory with the current defect scan in ‘real time’. Defect detection reaches a speed of up to 25 FPS because access times to the SSD hard disk as a limiting parameter are eliminated. Compared to currently established standard systems, the Confovis system enables a considerably higher resolution at the same process time, whereby even the smallest defects of a size down to 0.1µ/px are detected on various surfaces and process steps in front end or back end. Depending on the application, the entire wafer or individual chips can be taught as a ‘golden sample’ for a die-by-die or reticle-by-reticle defect scan. The classification of the defects does not have to be carried out during set-up but can be carried out afterwards and separately based on the defects found.
Defect detection and classification has been implemented together with Confovis’ partner NeuroCheck, a supplier of industrial image processing. A multi-stage process, which is also very robust compared with changes in contrast values, is used. An essential advantage of the NeuroCheck defect detection software is flexible adaptation of the inspection programs to changes in the production process, so that modifications are not necessary. Instead, analysis tools can be enhanced as a function block in the program flow, which enables simple iterative adaptation of the test programs to the defects to be found via the GUI. In addition, all changes – including classifier training – can be carried out offline and locally on the user’s premises. This means it is not necessary to transfer sensitive data to a Cloud to extend defect detection.
The new OhmBox ohmmeter from Kistler allows to determine and document the electrical resistance between two or more fastener components during the fastening process quickly and reliably. In this way, developers ensure minimal heat generation when bolted joints carry electrical current – and ensure their safety in e-mobility.
The OhmBox complements the ANALYSE fastener test stand product range and can be combined, amongst others, with the module for measuring tightening torques.
www.kistler.com/reliability
As the fastener industry continues to grow and evolve, SmartCert – a specialist in certification management –is leading the charge in transforming how suppliers and manufacturers handle the complexities of certification management with its cutting edge platform to manage certification processes.
Introducing the platform to the fastener industry at the prestigious Goebel World Riveting Congress 2024 in Germany, SmartCert showcased how the AI-powered platform is set to transform supply chain operations – offering suppliers and manufacturers a groundbreaking way to manage certification processes. With AI-driven precision, SmartCert brings new levels of visibility to certificate management, ensuring that certifications stay attached to parts throughout the entire supply chain process. This ensures quality and compliance, ultimately minimising errors and reducing inefficiencies.
SmartCert is able to centralise supply chain management into a single, easy to use platform
that enables users to manage processes, vendors, and certifications, from one unified source of truth, resulting in a streamlined workflow and enhanced communication across the board.
“Our goal with SmartCert is to simplify and optimise the entire certification process,” explains Lonni Kieffer, co-founder of SmartCert. “By keeping certifications with parts, we are empowering suppliers and manufacturers to improve compliance, reduce manual errors, and create a transparent, collaborative environment.”
The platform’s AI-powered tools enable ‘real time’ collaboration and consolidate all communications in one place, ensuring critical information is always accessible. Additionally, the platform enables users to generate certifications and review them against industry specifications. “The ability to seamlessly integrate certificates with parts, while managing everything from processes to vendors in a single platform, is poised to set a new standard for the industry,” concludes Lonni
www.smartcert.tech
Kerridge Commercial Systems (KCS), a global provider of enterprise resource planning (ERP) and business management software for distribution, servicing and rental businesses, has completed the acquisition of Vigo Software.
Vigo designs, builds and hosts Warehouse Management Systems (WMS) and Transport Management Systems (TMS) for its customers across the UK and Ireland. Vigo’s solutions help businesses reduce transport costs through efficient loading, plan delivery routes, meet transportation deadlines and enhancing customer experience through transparent on time delivery.
With the combined Vigo-KCS solution, customers can expect to see improved stock visibility, capture logistics operational efficiencies and enhanced client service and communication. Vigo also offers ‘real time’ driver mobile Apps with features such as route scheduling and electronic proof of delivery. This complements KCS’ growing suite of logistics and field service solutions.
John Vickers, managing director of Vigo, highlights: “Our combination represents an opportunity to provide greater value to our customers in terms of accelerating the pace at which we bring innovation and supply chain efficiency enhancing technology. For our team, this represents an exciting opportunity to grow together with the larger global organisation that is KCS.”
Ian Bendelow, CEO of KCS, concludes: “We are excited to welcome Vigo Software to KCS. This acquisition represents a significant milestone in our journey to empower businesses to achieve significant improvements in the stocking and shipping of goods to their customers. With this acquisition we underscore KCS’ commitment to innovation, best in class industry specific functionality and providing market leading solutions to the logistics market globally.”
S m a r t C e r t ' s K
Centralized dashboard
24/7 access to certs
Streamlined collaboration
Stronger and faster processes
Discover who’s joining the revolution
Follow SmartCert on LinkedIn to see industry leaders embracing our network
Ready to transform your business?
Visit smartcert tech or scan the QR code
Consulting + Solutions GmbH is specialized in developing construction, dimensioning and product software –available in over 30 languages and 60 countries
DESIGN SOFTWARE FOR ANCHORING STRUCTURAL TIMBERS
SOLAR SUBSTRUCTURES
REINFORCED CONCRETE
With over 20 years of experience, we make our in-depth expertise available to all our partners. Our software ensures acceptance reliability, increasing use and frequency of our partners’ products as well as dimensioning in accordance with national and international technical regulations. We have also been ISO 9001 certified since 2015. From the basic calculation kernel to the user interface – we provide customized programs tailored to your requirements. INSTALLATION
S&P Software Consulting + Solutions GmbH Rathenaustraße 54, 04179 Leipzig, Germany +49 341 442 460 • info@sup-scs.de www.sup-gruppe.com www.sup-scs.de
Across almost all aspects of manufacturing, businesses are eliminating paperwork to boost efficiencies. In this article, Kiran Soni, managing director of inventory management specialist RGIS, explains how to calculate the hidden costs of an in-house stocktake, as well as the challenges companies may face when relying on pen and paper inventory management.
The annual stocktake is often a source of workforce grumbling, viewed as a necessary chore. But it also might be costing a lot more than realised. As with any other aspect of manufacturing, we need to fully understand this issue before we can make an informed decision on how to address it. Questions to consider include how much human resource it requires and whether it diverts resources from other areas of the business.
When calculating the hidden costs of an in-house stock take, it is important to account for all factors. The first question to consider is, how much human resource is required? This will vary significantly depending on the size and complexity of the warehouse.
For example, a small operation might only have a few hundred Stock Keeping Units (SKUs), whereas a more complex or larger company can easily keep more than 10,000 SKUs on the shelves. To complete an inventory check successfully, people are needed to manually count parts and collate the information, as well as someone to compare the findings with inventory records.
Often, the warehouse team cannot manage a full stocktake on their own, meaning people are brought in from the production cells or assembly lines; or office staff from departments such as purchasing and accounts. If considering this approach, there are two ways these costs can be measured.
Firstly, how much does it cost to pay a production or office worker to carry out an inventory check? Secondly, what impact does diverting these people away from their day jobs have on productivity and efficiency –even on sales targets? Even if a stocktake is scheduled to coincide with an annual shutdown, there is still a cost involved. Workers are being paid to come in while the rest of their colleagues are on annual leave.
The third question is harder to quantify but is equally important. Are those workers taking part in the stock take capable and motivated? Disgruntled colleagues from the assembly lines will be less effective, taking longer to complete tasks. Similarly, those with little experience of inventory checks have a higher risk of making mistakes which will impact the accuracy of results. For example, not everyone in the stocktake team may have the expertise to identify a damaged or mislabelled part.
Many manufacturing facilities still rely on pen and paper inventory management. Of course, they keep digital records of inventory, such as spreadsheets; but the stock take itself is still recorded the old fashioned way. This presents a further risk of inaccurate results, as written records
of stocktakes are open to human error during the count as well as transposing the data into a digital format.
Above all, manually recording the data requires a significant amount of resources. It can lead to inefficient counting techniques, meaning the actual counting of SKUs takes a lot longer. Working out the size, scale and location of discrepancies between the count and the inventory records can be a laborious exercise that is also at risk of the same human errors. In addition, you can only understand issues on variances after the fact. In a pen and paper stocktake, there is no mechanism by which management can gain oversight and insight until the entire process is complete.
One way to ensure better results is to implement a barcode system. These are of course common in retail but less so in manufacturing and while introducing barcodes for all SKUs can significantly improve the speed and accuracy of a stock take, there are significant downsides.
Rolling out a barcode system across the entire warehouse requires a huge investment in time and money. It requires the diversion from day jobs described above, along with all the inherent risks from using inexperienced or unmotivated workers and requires a pause in production that comes at a price.
There is a way to avoid all these costs and challenges – outsourcing the annual stocktake to a third party. Inventory management specialists such as RGIS can help companies make significant savings on stock takes. Put simply, trained, experienced auditors work faster, meaning it can complete a stock check in far fewer days.
In addition, breakthroughs in technology mean that some providers can now offer the speed and accuracy of a stocktake using a barcode system without the cost and hassle of implementing barcodes. RGIS Vision is an advanced industrial solution that goes beyond barcode scanning to speed up stocktaking and inventory checks by eliminating paperwork and manual data entry. It can scan part numbers, product codes and barcodes, enabling auditors to achieve faster and more accurate results than a manual in-house stocktake.
In the past, managers could only complete the variance checks once they had collated all the paperwork from a stocktake. Using RGIS Vision means auditors can send management a line-by-line variance report as it completes the count on each parts bin. This saves a significant amount of administrative time after the stocktake and provides companies with much quicker insights.
RENEWABLE ENERGY FEATURE
Prioritising quality in wind turbine manufacturing is crucial, especially with the fasteners that hold everything together. While they may seem small, fasteners play a significant role in ensuring the safety of workers and the longevity of equipment. Here, Scott Hayfield, inside sales manager technical, quality and engineering specialist at Fabory UK, looks at the role of high-quality fasteners in ensuring worker safety.
Keeping people safe – even in extreme weather conditions –is vital when it comes to wind turbine manufacturing. As part of that, the role of fasteners is critical, with the safety of a team depending on the strength and reliability of these fixings. When high above the ground, balancing on a platform surrounded by moving parts, the last thing a team wants to worry about is whether a bolt is up to standard.
Fasteners are the heroes that hold the whole structure together; they prevent catastrophic failures that can lead to dangerous situations. Quality fasteners are engineered to meet the rigorous demands of the wind industry, ensuring that each component performs well under pressure.
It is therefore crucial to prioritise using high-quality fasteners for effective risk management. Investing in reliable fastening solutions significantly reduces the potential for failure, thereby ensuring the safety of workers and protecting company investment. By choosing fasteners that meet rigorous standards, such as those certified through APQP4Wind, a non-profit association which provides quality assurance to the wind industry, businesses are fulfilling requirements and actively creating a safer working environment.
This approach is about safeguarding operations for the future and minimising the risk of costly downtime or accidents. It reflects a culture that prioritises safety and quality, acknowledging that even the most minor component can significantly impact a project.
Understanding the consequences of using low quality fasteners is paramount in
When high above the ground, balancing on a platform surrounded by moving parts, the last thing a team wants to worry about is whether a bolt is up to standard.”
practical manufacturing. These low quality fasteners can lead to increased maintenance costs, downtime and
or worse. There are strict checks such as the Production Parts Approval Process (PPAP), to confidently assure customers that each fastener meets the requirements.
Frontline workers depend on the quality of the materials and fasteners used in their equipment. The industry has already witnessed the devastating effects of disregarding safety standards – just a few questionable choices regarding fastening could lead to catastrophic failures.
By closely adhering to regulations and investing in high-quality fasteners, companies such as Fabory UK are promoting a proactive approach to safety that benefits everyone involved. With an extensive portfolio of over 120,000 fasteners, Fabory UK prides itself on offering tailored fastener solutions for diverse
Specialinsert®, since 1974 in the world of fasteners, thanks to the experience matured and to the continuous research, today it is able to supply the most innovative fastening systems.
The sustainable S50ROS cable tie is made from polypropylene, featuring a significantly reduced CO₂ footprint compared to standard cable ties made from other materials. It offers high tensile strength of 185N, chemical resistance, and is ideal for sensitive, smooth cables as it prevents lateral movement thanks to its anti-slip design.
Perfect for various applications and supporting the circular economy, the S50ROS is a high-performance cable tie – tied to your sustainability goals.
The cable ties in the T- and OS-Series are also available in 100% post-industrial recycled (PIR) polyamide, designed to meet both performance and sustainability standards. Made from heat-stabilised, high-impact modified polyamide 6.6 (PA66HIRHS), they offer exceptional durability without requiring moisture conditioning.
Available in various sizes and with tensile strengths ranging from 80N to 535N, these ties ensure reliable performance while reducing CO2 emissions compared to those made from virgin PA66. Ideal for industries like automotive and electrical installation.
Solar installations are a fundamental part of the transition to a more sustainable future, which is why INDEX® – A PERFECT FIXING offers specific solutions for the fast safe assembly of both industrial and residential installations, with its coplanar and triangular systems, designed to withstand adverse weather conditions, as well as guarantee stability and durability.
INDEX® recommends its coplanar system for sloped roofs, where solar panels are to be installed parallel to the surface. In these installations, the panels follow the natural line of the roof, which simplifies their installation and thus reduces installation times, as well as labour and material costs. The coplanar system allows for an aesthetically pleasing finish while making the most of the space. For tiled roofs, users can opt to perforate the tiles or include a safety roof hook to avoid drilling.
Fixings included in the coplanar system for tiled roofs include safety roof hooks to fix the structure in place without the need to perforate the tiles; adjustable accessory kits, used with double threaded screws or threaded rods, sealing washers and other elements according to the type of structure; ‘L-shaped’ flanges, acting as a joining point between the double threaded screws and the aluminium profiles; as well as connectors to join the fixing structure to the aluminium profiles. Also included in the coplanar system are aluminium joints for joining INDEX®’s PSE-C aluminium profiles through a central cavity; fast fixing staples to fix the photovoltaic modules to the profile using pressure; as well as aluminium guides to be installed as a support for the staples at each end of the row of panels.
In addition, for applications with flat or slightly inclined roofs where the natural angle does not offer the optimum inclination to capture energy, INDEX ® offers its triangular systems. These systems enable users to adjust the inclination of the panels, which maximises the solar exposure and increases the energy efficiency of the installation.
Key components of the triangular system include adjustable triangles made of steel and aluminium, which enable users to adjust the inclination of the solar panels; butylene watertight tape – to ensure the watertightness between the surface of the roof and the profile or guide; INDEXTRUT perforated guide made of steel with Atlantis® C4-M coating, as well as thin sheet screws recommended for the fixing of profiles,
which are self-drilling and have anti-rust protection.Also available are adjustable accessories – including assembly plates and double threaded screws for installation with a chemical anchor; fast fixing screws to provide additional fixing points on INDEX ® ’s GP-XS steel guide; EMP-XS solar connectors to join the GP-XS guides through its central channel without interfering with their functions; as well as fast fixing staples that fix the solar panels to the profile by means of pressure.
To further enhance its offering in the renewable energy sector, INDEX ® has launched the INDEX ® solar fixing App, designed to select products and provide information and calculations to the user for the necessary fixings needed for the installation of solar panels. Optimised for any type of surface or environment and available in several languages, the App can reliably provide calculations valid for any type of panel and orientation.
www.indexfix.com
LEADİNG THE İNDUSTRY FOR 29 YEARS, KALELİLER SERVES FROM TÜRKİYE TO THE WORLD. JOİN US FOR RELİABLE CONNECTİVİTY SOLUTİONS AND LET'S ACHİEVE SUCCESS TOGETHER!
NORM Coating’s latest innovation, an alkali zinc coating developed to meet the growing demands of the renewable energy sector, has been specially designed for solar panel fasteners and other renewable energy components.
As the renewable energy industry expands, so does the need for durable, long-lasting solutions that can withstand harsh environmental conditions. NORM Coating addresses these challenges with its cutting edge coating technology that offers protection against corrosion while delivering extended product longevity in the most demanding environments. Its self-renewable property ensures that mechanical damage does not compromise performance of the application. With solar energy systems exposed to various environmental stressors such as rain, wind and temperature fluctuations, NORM Coating’s alkali zinc coating features a homogeneous, bright appearance that helps protect solar panel fasteners from these elements, ensuring continuous and efficient energy production over time. The coating also
features the innovative ability to self-repair minor mechanical damages to ensure consistent protection even in harsh conditions. This unique property extends the service life of fasteners used in solar panels and other renewable energy installations, reducing maintenance costs and improving overall reliability.
NORM highlights that its latest innovation provides a minimum of 600 hours corrosion resistance with its thick passivation layer and, when combined with a special top coat, can achieve resistance that exceeds 10 cycles in atmospheric cycle tests, ensuring long-term durability in outdoor environments. Additionally, the coating is free of harmful Cr+6, thus aligning with the sustainability goals of the renewable energy sector.
www.normcoating.com
As the global market looks at the negative impact manufacturing can have on the environment, due to toxic gasses and chemicals released into the atmosphere, APM Hexseal is providing fastening solutions to eco-conscious companies, that are switching to green manufacturing to lessen their environmental impact.
Designed to protect sensitive electronics from the elements, APM Hexseal’s products are ideal for green energy solutions including solar, wind and hydropower applications due to their resilience in harsh weather conditions. This means the products are more durable and do not need to be replaced as often, as well as being easy to recycle and reuse – producing far less waste.
This includes APM’s sealing boots, which can be used to protect switches on solar and wind farms. The boots provide added protection to ensure the electronic and mechanical switches used to control the systems are protected from environmental hazards and continue to function, which increases efficiency while minimising the risk of down time and failure.
Wind and solar farms, weather buoys and clean energy generation stations, all rely heavily on systems that must function flawlessly, even in remote locations that are often exposed to difficult and hazardous environmental elements. Using APM’s sealing screws, nuts or washers to protect the openings in the enclosures and housings, prevents these contaminants from penetrating the box and damaging the internal components. This simple step helps to maintain the functionality of the system and keep the power on.
As well as keeping unwanted liquid and moisture out, self-sealing boots and fasteners from APM also help to protect the environment from hazardous materials. This is due to their ability to prevent substances from leaking out of devices or instruments, ensuring toxic materials are effectively sealed inside. This means the risk of leakage into fragile ecosystems is mitigated.
APM Hexseal products are also an ideal solution for businesses looking to improve sustainability and move towards green manufacturing practices. However, these solutions aren’t limited to renewable energy, with many other industries benefitting
Green manufacturing has secured its place as the future of manufacturing...”
including in applications in agricultural machinery, food dispensing and processing equipment, as well as in the marine industry –where mission critical equipment is continuously submerged in highly salinated water. These sealing solutions not only protect vital equipment and technologies from corrosion and damage, but also create a robust seal to protect vulnerable environments from contamination by preventing fluid and gas leakages.
Another industry that benefits from these products is in the medical sector. Lifesaving
devices require extra levels of protection from environmental hazards to increase service life and comply with FDA regulations. After each use, these instruments must undergo rigorous and thorough cleaning with sanitising chemicals. Durable sealing solutions from APM Hexseal help to extend the working life of these critical devices by protecting the sensitive electronics – decreasing manufacturing costs and promoting sustainability.
“Since 1947 APM Hexseal has put environmental sustainability at the forefront of its innovations, with efforts to develop sealing solutions that extend the life of electronics in wide ranging industries, under the harshest conditions. Green manufacturing has secured its place as the future of manufacturing and for good reason – going green provides numerous benefits to manufacturers, from cost savings and reduced environmental impact to increased performance and product longevity. With a full line of reusable, self-sealing switch boots and fasteners APM has a sealing solution ideal for any application,” concludes the company.
www.apmhexseal.com
In recent years, the sudden rise in demand for Electric Vehicles (EVs) has caused significant challenges for fastener manufacturers, pushing the need for innovative solutions. Growermetal aims to meet these growing demands with the launch of its Grower OhmLock® conical washer, designed for use in EV battery packs.
Grower OhmLock® strikes a balance between electrical conductivity and corrosion resistance. Crafted from quenched and tempered carbon steel, the washer features two sides with distinct geometries – the top surface has knurling, while the underside includes inner sharp protrusions. This dual-sided design makes it particularly effective for fastening the battery pack to the vehicle chassis, as well as for car underbody applications, where exposure to weather conditions and high-levels of vibration pose significant challenges.
“Grower OhmLock ® was engineered in partnership with Brugola OEB with the goal to avoid oxidation and loosening over time in the bolted joint connections for EV battery packs. Its geometry secures the components without damaging paint coatings, while minimising the risk of external corrosion. The result is a product that prevents failures or malfunctions, ensures a smooth and uninterrupted power flow, as well as maintains low electrical resistance,” explains Paolo Cattaneo, CEO of Growermetal SpA.
He continues: “Grower OhmLock® is the result of extensive research and collaboration across our development team and one of our important automotive bolt maker customers.”
Whilst the launch of the Grower OhmLock® is a major milestone for Growermetal this year, there have also been other important
achievements. To enable an expansion of its international services, the business has broadened its sales network by opening a new office in Germany in October – Growermetal Germany GmbH.
“The fact that Growermetal sells an important percentage of its goods to German customers was the deciding factor in opening a branch here,” explains Klaus Vogt, general manager of Growermetal Germany GmbH. “The proximity to our customers throughout Europe can thus be improved and there will be a central contact person in the future.”
With participation in important European trade shows, combined with a rooted presence in the US and South American markets, this achievement aims to strengthen Growermetal’s support to European customers, with a focus on the German, Swiss and Austrian areas. Klaus continues: “Thanks to a network that has been built up over many years, we are able to speak to the right contacts and thus find out what the market demands. In order to develop suitable products, it is important to stay in dialogue and be present at the right events.”
The opening is also strategical in making partners aware of the company’s solutions and offering. “The fasteners we produce are world leaders in many ways, but if the market is not aware of our solutions, we cannot solve their fastening problems. The basic goal is to further make the Growermetal brand known in Germany and Europe. To do this, we will first intensify relationships with our existing customers and inform them about new products, approvals and everything important,” concludes Klaus.
www.growermetal.com
In many industrial sectors, the use of composite materials and thin sheet metal represents a challenge when it comes to fastening. This is due to the thickness of these materials, a thickness which is often not suitable for threading and can’t easily support traditional fasteners or inserts. This challenge has prompted J. LANFRANCO & Cie to design a range of fasteners specially designed for these applications.
Thin materials and composites are becoming an increasingly common component in modern manufacturing, especial in industries where high strength and lightweight materials are now the most desirable, such as the automotive, rail and aerospace industries. J. LANFRANCO’s modular fixtures with unidirectional and multidirectional movement capabilities offer a highly efficient and cost-effective alternative to traditional methods when securing thin sheet metal or composites to metal structures. These solutions remove the need for costly processes such as laser cutting or complex machining, while providing precision fastening with tolerances as tight as 0.5mm. This not only ensures precision, but also significantly reduces overall manufacturing costs.
Manufactured from various materials, including stainless steel, steel and aluminium, the main innovation of these fasteners lies in the polyvalence of the profiles. Designed with J. LANFRANCO’s
+ Hommel GmbH Verbindungselemente
Heerstraße 1 D-78554 Aldingen
Tel.: +49 (0) 74 24 / 9 62-0 info@flaig-hommel.de www.flaig-hommel.de
self-locking nuts with double superposed slots, these profiles are available in two configurations; unidirectional movement, which offers a predefined range of movement, or multidirectional movement; which allows flexibility, with the fixture capable of 12mm movement in all directions on a given surface. Such a design offers a secure fastening solution for applications requiring complex assemblies, without compromising the structural integrity or precision of the assembly.
The fasteners can be installed quickly and efficiently using simple riveting techniques, without the need for welding or other labour, offering an advantage in industries where labour costs are high. Additionally, these products can be adapted for each application to meet the specific needs of customers.
It’s not difficult to draw a parallel between the words ‘adhesives’ and ‘adhesion’. Yet, it still causes confusion. Here, Thomas Besley, content manager at Forgeway, outlines what adhesion is, why it’s one of the first steps to ensure a strong bond, as well as analyses why some materials are so difficult to bond.
Adhesion is the bond between two different materials at the interface. In the context of adhesives, it is the bond between the adhesive itself and the substrate.
Multiple factors can impact adhesion – surface energy, contaminants and adhesive type all play a significant role in the strength of adhesion. There are also several different types of adhesion. Mechanical adhesion is where materials are joined together by interlocking. Voids or pores are filled and the material ‘hooks’ itself onto the adherend. It isn’t always an adhesive that forms mechanical bonds. Velcro and sewing are also examples of mechanical adhesion on a much larger scale.
Chemical adhesion is the strongest form of adhesion and it occurs when there is either an intramolecular or intermolecular interaction between the substrate and the adhesive. Intermolecular attractions are between one molecule and another, whereas intramolecular attractions are the forces within the molecule. In terms of strength, intramolecular
Strong adhesion doesn’t necessarily mean a strong bond. Multiple factors decide a strong bond.”
attractions are the strongest, but intermolecular attractions can be strong when there are a large number of them. The most common intramolecular bonds are ionic and covalent bonding. Examples of intermolecular interactions include hydrogen bonds and van der Waals.
There are also other types of adhesion – electrostatic and diffusive adhesion. However, these are rarely associated with adhesives and bonding as we know it.
Typically, the adhesives used to create a bonded joint will need to form a chemical bond. This type of adhesion is the strongest and most durable. Mechanical adhesion is also able to create strong durable joints. Dispersive adhesion is the aim for bonded joints that need to be removable.
The correlation between adhesion and bonding is obvious. The stronger the adhesion, the stronger the bond; right? This isn’t always the case. Strong adhesion doesn’t necessarily mean a strong bond. Multiple factors decide a strong bond.
Nonetheless, a strong adhesion between the adhesive and the substrate will form the foundation of a strong bond and to get a strong chemical adhesion is more important still.
To begin with, the material’s surface plays a big role in adhesion. Contamination can create a barrier between the adhesive and the substrate. It’s important to remove any contamination to ensure a strong bond. Abrasion can help remove contamination. It can also create pits and grooves on the surface to add an element of mechanical adhesion. But, as we explain in a separate article, abrasion isn’t always consistent.
There are several other methods of surface preparation you can use to remove contamination. Abrasion is usually the ‘go to’ method. Even if it isn’t always the best. Regardless of contamination and abrasion, there’s one thing that ultimately determines a material’s ability to form a strong bond – surface energy.
Surface energy is what determines a material’s tendency to attract or repel a liquid and surface energy is measured in millijoules per square metre. Materials with lower surface energy repel liquid and make it difficult for the liquid to ‘wet’. The ‘wettability’ of a surface describes how well a liquid spreads.
When the surface energy is low, it makes it very difficult for things to adhere to. It’s ideal for items that you don’t want things to stick to. It’s not so ideal if you want to stick things to the material.
An adhesive needs to have a lower surface energy than the material so it can wet out and form an effective bond. Some plastic types have very low surface energy, such as PTFE (Teflon), polyethylene.
In summary, three main things will affect the ‘bondability’ of a material; contamination, abrasion and surface energy. The surface energy of the material will be the deciding factor. But don’t forget the effect contamination and abrasion can have too.
Now that the science behind adhesion is understood, it’s time to analyse how good adhesion can be ensured. Understanding how adhesion works is a good start. That knowledge needs to be applied when analysing an application. When it comes to selecting an adhesive, different adhesive chemistries will be compatible with different materials.
For example, epoxy adhesives bond very well to metal and polyurethane adhesives will form strong bonds with wood. Acrylic adhesives have good adhesion to plastics. Some adhesives are also not compatible with certain materials. Most adhesives will struggle to bond low surface energy plastics. But apart from that, some methyl methacrylate or acrylic adhesives aren’t compatible with wood due to the curing mechanism. It is also difficult to bond over the top of silicone or silicone coated materials.
Multiple factors can impact adhesion – surface energy, contaminants and adhesive type all play a significant role in the strength of adhesion.”
Whilst an educated guess can be made on whether an adhesive and substrate are compatible, there is never a guarantee. Testing each material is essential.
It’s also worth remembering that although some materials are generally easy to bond, different grades or different brands of metal will not have the same properties. This variation means you can’t be complacent when using materials from different suppliers. When a material change is made, the adhesive must be compatible before you use it in production.
We’ve seen examples where a recreational vehicle manufacturer changed their supplier of Glass Reinforced Plastic (GRP). The company didn’t test the adhesive on the new GRP. After all, isn’t all GRP the same? The new grade of GRP had a very inconsistent surface. Although this didn’t affect the performance of the GRP, it did affect the adhesion. In some areas, it formed a strong bond. In other areas, the GRP hadn’t fully cured, leaving an incompatible surface for the adhesive. Simple surface preparation fixed the issue for the company, however, it learnt the lesson that not all materials are made equal.
Ultimately all the predictive methods in the world can be used, but the best way to ensure an adhesive and substrate are compatible is to test and there are several simple testing methods for checking the adhesion.
Strong adhesion is the foundation of a strong bond. But it won’t guarantee the bond will remain strong for long. The argument of adhesion vs cohesion is an important consideration at this point. From an adhesive and bonding perspective, adhesion is the strength of the bond between the adhesive and the material. Cohesion is the internal strength of the adhesive.
Other factors such as durability, impact resistance and heat resistance are just a few factors to be considered. It’s at this point that companies can get stuck. They aren’t sure how to choose the right adhesive and don’t know if the adhesive will survive in ‘real life’ conditions.
At Forgeway we’ve helped companies in this exact situation for over 25 years, finding the right adhesive following four simple steps. We know that the first step in finding the right adhesive is to ensure the materials are understood. Understanding the materials will help know whether it can form a strong adhesion, as well as the science behind it. Strong adhesion will help form the foundations of a strong bond.
Rising CO 2 emissions, stricter regulations and increased consumer expectations has led to bio-based materials and low temperature adhesives becoming the ideal choice for sustainable packaging. Henkel Adhesive Technologies has combined both technologies with the new Technomelt Supra 079 Eco Cool.
Combining 49% directly bio-based raw materials with 30%
ISSC-certified mass-balanced material, Technomelt Supra 079
Eco Cool is a bio-based product for folding cartons, trays and wraparound packaging at a processing temperature that is up to 40°C lower than application temperature, allowing for lower energy consumption, as well as a reduced risk to burns and reduced exposure to vapours and volatile substances.
With the Supra Cool range, Henkel offers a portfolio of hot melts that lead to lower energy consumption thanks to reduced application temperatures. While the Supra Eco range uses bio-based materials for a more sustainable packaging design, by combining both technologies in the latest development, users can optimise the sustainability of packaging at two points in the value chain – raw materials and processing.
Like many non bio-based adhesives in the Henkel portfolio, the adhesive is compatible with the paper recycling process and is certified by Institut cyclos-HTP, which has developed a scientifically based catalogue of requirements and assessments for testing and verifying the recyclability of packaging and goods.
“With Technomelt Supra 079 Eco Cool, we are addressing several trends and challenges in the packaging industry,” highlights Nele Gering, sustainability manager Europe at Henkel Consumer Goods Adhesives. “Increasing regulations and consumer preferences for
TAPES + ADHESIVES FEATURE
sustainable packaging practices and materials are putting pressure on companies to innovate in the area of sustainable packaging design. Technomelt Supra 079 Eco Cool is particularly suited to responsible companies by reducing CO 2 emissions, improving process efficiency and is fully compatible with the paper recycling process.”
With the Product Carbon Footprint (PCF) being one of the most established methods for determining the climate impact of a product, Afera, the European Adhesive Tape Association, and IVK, the German Adhesives Association have developed a web-based tool for PCF calculation of both adhesives and adhesive tapes using an aligned, straightforward, affordable method.
Unveiled in Thessaloniki at Afera’s 67 th Annual Conference, the TACK – Tapes and Adhesives Calculation Kit – has been developed through a collaboration with Sphera, a specialised provider of sustainability consulting services and is in the final stages of development for B2B utilisation by adhesive tape manufacturers, converters and raw materials suppliers who are either Afera or IVK members.
PCF sums up the total greenhouse gas emissions generated by a product over the various stages of its lifecycle and is becoming increasingly important within the tape and adhesive industry for estimating the environmental impact of all types of adhesive tapes – in particular, a ‘cradle to grave’ (entire lifecycle) or ‘cradle to gate’ (defined life cycle phase) assessment of PCF. This is all based on the Life Cycle Assessment (LCA) approach, which includes factors such as the raw materials, manufacturing, distribution and end of life stages for B2B reporting.
Experts will be able to work with the pre-customised, web-based interface which can also be linked to corporate ERP systems. Users have the option to input primary data from suppliers or utilise a high-quality secondary data set curated from Sphera’s LCA database. TACK’s current database for adhesive tapes consists of 74 raw materials incorporated into adhesive tapes, as well as 17 recipes for generic adhesives and release coatings, totalling 91 entries.
TACK is currently in the modelling and preparation stage of development, after which it will be reviewed, adjusted and then validated by DEKRA, a specialist in the field of testing, inspection and certification in Q1 2025.
With over 130 years of experience, REYHER is one of Europe´s leading trading companies for fasteners and fixing technology worldwide.
An innovative and patented fastener engineered for an almost flat and smooth surface features a grooved conical underside to prevent ‘self-loosening’.
SCHNORR® is an international leader in engineering and producing safet y washers and disc springs for automotive, aerospace and mechanical applications
Original SCHNORR® safet y washers:
• Highly vibration-resistant
• Twofold effect from one component
• E x tensive range
Original SCHNORR® disc springs:
• Various applications
• Best price -per formance ratio
• Customized solutions
Please contac t us Together we will find your tailor-made solution.
Schnorr GmbH
Stuttgar ter Str. 37
71069 Sindelfingen, Germany
Phone: +49 (0) 7031 302-0
Fax: +49 (0) 7031 382600
mail@schnorr.de www.schnorr.de
Methyl Methacrylate Adhesives (MMAs) offer strength, toughness, and ease of use when bonding metals, plastics and composites. Their properties and processing benefits mean they are suitable to trial for many applications. Compared with alternatives such as epoxies and polyurethanes (PUs), the benefits and properties of MMAs are perhaps less well known. Here Ben Swanson, joint managing director at adhesives specialist Intertronics, shares an overview of this useful adhesive technology.
Astructural adhesive is one that cures into a material capable of holding two or more substrates together, bearing the forces involved for the lifetime of the project, such as shock, vibration, chemical exposure, temperature fluctuations, or other destructive/ weakening agents. Common structural adhesives are epoxies, PUs, UV curing adhesives, MMAs and arguably cyanoacrylate adhesives.
MMAs are two part reactive acrylic adhesives that include a resin and an activator. Mixing them together causes a free radical reaction that enables fast curing at room temperature. Additives may include elastomeric tougheners and impact modifiers. They are typically available in two mix ratios, 1:1 and 10:1. The 1:1 adhesives generally have higher strength than the 10:1 products, but the 10:1 adhesives have higher elongation and so more flexibility.
MMAs are excellent for bonding metals such as steel, stainless steel, aluminium, thermoset composites, both carbon fibre and glass fibre reinforced, as well as thermoplastics including acrylics, ABS, polycarbonates, PVC and other engineered plastics. They are favourable in applications where speed, strength, toughness and environmental resistance are important, because they bond to a wide range of substrates and have choices of cure speed, they are seen as quite versatile.
MMAs fully cure and reach their full strength at room temperature, due to the fast exothermic reaction that forms them. Their cure is less susceptible to ambient conditions like temperature and humidity than other adhesives. Critically, the time between mix/application and fixture strength, sometimes called green strength or handling strength, is short, reducing work in progress and enabling faster throughput – a key processing advantage. To suit different process requirements, MMAs are available with a range of working times from 5 minutes up to 120 minutes, and fixture times from 6 minutes up to 4 hours.
Typically, less surface preparation is required when using MMAs to bond composites, metals and plastics than when using other adhesives, as the chemistry is able to cut through some surface contamination. A solvent wipe to remove any light oils on metals or composites, or a dry wipe on plastics, may be all that is required with an MMA, although some
projects will require the use of a solvent wipe or abrasion. Some MMA products are available that bond metal without the need for a primer, which creates a leaner process, removes the risk of error and can improve health and safety.
MMAs are readily and commonly available in two part cartridges from 50ml to 490ml in size, and can be supplied in bulk for larger volume applications. They are applied through static mixing nozzles, which comfortably give the adhesives an adequate mix.
Important properties for a structural adhesive are strength, toughness and flexibility. When bonding dissimilar materials, such as a rigid metal with a flexible plastic, flexibility in the adhesive is particularly important. Generally, when compared with epoxy technologies, MMAs are less brittle, less prone to cracking, offer non-critical mix ratios, large gap fills, and a flexible choice of cure speed. When compared with polyurethanes, MMAs offer high bond strength, good impact resistance, large gap fills less environmental sensitivity, good chemical and environmental resistance, fast cure speed and reduced health risks (no isocyanate). In metal bonding, for example, MMAs have become a popular choice over epoxies, as they are easier to use and cure faster, whilst having enough bond strength for many applications.
There is some disadvantages however. MMAs have lower operating temperature ranges than, say, epoxy adhesives. In some cases, where there is larger adhesive mass or thicker bond lines, understanding of the exothermic heat produced during fast cure is required to avoid potential substrate discolouration or distortion.
It is important to note that there is no perfect or universal adhesive and the benefits and disadvantages of each chemistry should be weighed up against the demands of the application and processing environment. Overall, MMAs bring many process and technical advantages to applications in a range of industries and may be a good candidate to trial when reviewing structural adhesive chemistries.
Bülte has expanded its product range with a new line of self-adhesive cover caps, designed to provide both aesthetic appeal and practical functionality.
An ideal solution for furniture manufactures, carpenters and specialists in vehicle fittings, these self-adhesive cover caps are made from premium melamine and offer a sleek, uniform finish while protecting screws, eccentric fittings and dowels from dust, rust and wear, ensuring long-lasting durability.
The cover caps are available in two standard sizes in diameters of 14mm and 20mm, as well as other sizes upon request. Available in a wide variety of decors, these caps seamlessly blend with popular wood, melamine and laminate surfaces from manufacturers of wood-based materials.
One of the key benefits is easy application, as the self-adhesive backing with acrylic glue ensures quick and hassle-free installation without the need for additional tools or glue. Their versatility and broad range of finishes make them an ideal fit for a variety of interior design and furnishing needs.
Master Bond has introduced EP21ARHTND-2, a two part epoxy adhesive, designed to withstand prolonged exposure to a wide range of chemicals, as well as being optimised to resist acids.
EP21ARHTND-2 is capable of curing at room temperature to optimise its acid resistance properties, however Master Bond recommends an overnight cure schedule at ambient temperatures, followed by a heat cure of 150°F – 200°F (65.5°C – 93.3°C) for 2 – 4 hours or longer.
This epoxy is a reliable electrical insulator with a volume resistivity greater than 1014 ohm-cm at 75°F (23.8°C), and dielectric strength of 440 volts/mil at 75°F. Other noteworthy properties include a tensile strength of 9,000 psi – 10,000 psi, and a Shore D hardness of 75 – 85. EP21ARHTND-2 also provides good heat resistance and is serviceable from -60°F to 400°F (-51.1°C – 204.4°C).
EP21ARHTND-2 does not contain solvents and is RoHS compliant. The product bonds well to metals, ceramics, composites, rubbers and plastics. It features a smooth paste-like consistency and will not flow, or sag once applied, making it ideal for bonding and sealing applications. The epoxy is available for use in ½ pint, pint, quart and gallon container kits.
Master Bond also offers speciality packaging in 50ml double barrel cartridges, which not only eliminates the need for manual measuring as well as mixing, but also enables the possibility of manual or automated dispensing.
Developed with 60% bio-based materials using a patented synthesis process, the new Bostik Super Glue Ultra+ from Bostik, marks a significant advancement in the adhesive industry, combining high performance with a strong commitment to sustainability.
Designed for a wide range of repair applications, Bostik highlights its Super Glue Ultra+ offers exceptional strength, durability and resistance to extreme conditions such as heat and water. Its bio-based formula ensures that consumers must no longer compromise between performance and sustainability.
In addition to the advanced formula, the new adhesive comes packaged in recycled and recyclable cardboard blisters and will soon be available in tubes made from recycled aluminium, emphasising Bostik’s commitment to sustainability by reducing waste and adopting circular economy practices.
The launch of Super Glue Ultra+ is a key milestone for Bostik, a global specialist in adhesives and sealant solutions and part of Arkema, and is the result of Arkema’s unique positioning in speciality chemicals, leveraging a bio-based raw material derived from castor oil and a newly patented synthesis route for cyanoacrylates developed by R&D teams. This cutting edge formulation not only demonstrates its commitment to innovation and sustainability but also reflects the company’s extensive research and development capabilities.
TAPES + ADHESIVES FEATURE
IPS Adhesives, a global manufacturer of structural and surfacing products, has acquired a range of adhesives based on acrylate and Methyl Methacrylate (MMA) technology from global sealing company L&L Products.
IPS Adhesives will rebrand the former L&L product numbers A-K321 and A-K322 as SCIGRIP ® products and they will continue to be available in Europe, with reduced lead times in the coming months.
While L&L Products demonstrated significant technical success in developing advanced acrylate/ MMA formulations, this acquisition enables L&L to focus on the development and commercialisation of unique adhesives, sealants, reinforcements and acoustic technologies that provide innovative problem solving solutions for the automotive and transportation markets, as well as diversifying its business to enter new markets.
Scott McDowell, president at IPS Adhesives underlines: “This acquisition accelerates our ability to create and deliver even more high performance solutions to our customers across Europe and North America. We’re passionate about enabling customers to bond in new ways, as demonstrated by our recent launch of a groundbreaking low surface energy adhesive. The combination of our technical expertise with L&L’s current MMA portfolio and pipeline products further enhances our ability to solve problems and innovate for customers.”
TAPES + ADHESIVES FEATURE
tesa® has opened a new, state of the art customer solution centre and office space in Bangkok, Thailand.
This strategic expansion marks a significant step for tesa® to further expand its presence and customer relationships in south-east Asia, following the inauguration of a new production facility in Haiphong, Vietnam last year, as well as the opening of a new office in Hanoi earlier this year. The new customer solution centre in Bangkok now represents another important milestone on this journey.
The centre features advanced simulation and testing capabilities and is specifically geared towards customers and partners from the automotive, electronics and printing industries. Visitors can test applications with specialised equipment on a total area of 850m 2 , including a 100m 2 laboratory unit including an oven and a climate chamber.
Andreas Gunnestrand, regional manager at tesa® AsiaPacific, explains: “Our investments in the new customer solution centre and the new office space in Bangkok underscore our commitment to the south-east Asian market. We want to work even more closely with our customers on-site, offer tailored solutions for our products and be able to respond even faster to individual requirements. We are once again emphasising our strategy of always being close to the market and our customers, which is crucial for success in this dynamic region.”
TAPES + ADHESIVES FEATURE
Panacol’s newly developed conductive adhesive, Elecolit® 3648, reliably creates long-lasting, flexible electrical connections, making it an ideal solution for bonding electrical components.
Adhering well to plastics, including PI, PC, PVC, ABS and FR4, Elecolit® 3648 can be cured at 80°C within a few minutes. At higher temperatures the adhesive can be hardened within seconds as a ‘snap cure’ adhesive. Thanks to its one component system, eliminating the need for mixing prior to application, Elecolit ® 3648 can also simplify manufacturing processes and can be dispensed by conventional dispensing equipment, by jetting or screen printing.
Elecolit® 3648 offers flexibility in application and can efficiently secure flexible resistors and create flexible electrical connections to lead the generated electricity from the conductive tracks to the end device. This adhesive is also effective in touch sensors or wearable devices where flexibility is a desired feature, making Elecolit® 3648 an ideal solution for replacing solder joints in applications subjected to vibration, oscillation or rapid temperature changes.
HEICO Group is introducing three new innovations – HEICO-TEC ® expansion bolts for rotating flange and coupling bolt connections, HEICO-LOCK® reaction washers for reaction-free assembly of large bolted joints, as well as the HEICO-ONE safety washer to its comprehensive portfolio of tensioning technology and bolt security solutions.
Launched earlier this year, HEICO-TEC ® expansion bolts include three base types: Suitable for non-threaded boreholes, threaded blind boreholes and through-holes. This means the product line is engineered to meet specific application needs and can be tailored to individual customer requirements. A wide range of customisation options are also available, including options for the HEICO-TEC ® tensioning element, an option for using elastic HEICO-TEC ® reaction nuts to ensure optimal joint longevity, as well as additional option to protect bolted joints against self-loosening.
The HEICO-TEC ® expansion bolts offer an ideal solution for connecting large drive flanges or couplings, replacing the traditional fitted bolts found in gearboxes and shafts used in wind turbines, hydroelectric turbines, gas turbines and other drive systems. They feature a unique conical design which enables precise alignment of components and adaptation to boreholes through radial expansion, eliminating the need for costly and time-consuming reworking of boreholes and fitted bolts.
As well as the expansion bolts, HEICO is also introducing the new HEICO-LOCK ® reaction washers that, like all products in the HEICO-LOCK® range, are based on the proven wedge-locking principle. The HEICO-LOCK ® reaction washers provide secure bolt locking but also allow large, bolted joints to be tightened quickly and safely by using conventional high torque wrenches, without the need for reaction arms.
HEICO’s reaction washers consist of a two washer system with radial ribs on the outer surfaces and opposing wedge-shaped inner surfaces. The gear-like contour of the larger washer at the bottom enables safe, reaction arm-free tightening with commonly available powered torque tools, which
prevents potentially damaging bending during the tightening process. The Group also offers compatible dual sockets, which are adaptable to torque tools from nearly all leading manufacturers.
To facilitate the use of HEICO-LOCK ® reaction washers in through-bolt connections, without the need for time-consuming countering or holding on the passive side, HEICO has also developed a friction-based back-up washer featuring wave-like locking ribs on both sides. The HEICO-ONE safety washer complements the reaction washers by being placed on the passive side between the nut or bolt head and the bearing surface, preventing the passive-side bolt or nut from rotating during tightening on the active side, while also protecting the bolted joint against self-loosening.
“With the launch of these new products, we are expanding HEICO Group’s already comprehensive portfolio, providing our customers with innovative, tailored solutions and optimisation potential,” explains Sven Heggemann, sales engineer at HEICO Group. “We are confident this expansion will not only offer substantial value to our existing customers but will also significantly drive growth in new markets and customer segments.”
www.heico-group.com
Designed with a fresh design and intuitive navigation to improve the user experience of its customers, BRALO SA has launched its new corporate and product website, helping to highlight its commitment to excellence and innovation in the industrial sector.
BRALO’s new website has been optimised to guarantee fluid and simple navigation, enabling users to find what they need easily with the fewest clicks. Enriched with detailed content on various products and their applications, the website also offers technical specifications, competitive advantages, as well as videos and manuals of products. Interactive tools such as product configurators and repair and warranty registration forms are also on offer to facilitate contact with customers. The technical library on the website’s predecessor has been updated, providing a more visual resource that enables users to find the document needed.
BRALO also delves into the practical applications of its products in key sectors such as renewable energy, automotive, construction, HVAC and industries in general, with the new website offering specific solutions for each application. With a responsive design that adapts to any device, the website facilitates access to information at any time and place, ensuring an optimal user experience on both mobile and desktop devices. The website is published in Spanish, English and French, with other languages to be incorporated later to meet the needs of customers in global markets. Also available on the website are details of the company’s internal processes, actions for sustainability, as well as the vision and mission of BRALO. www.bralo.com
By Dr Bill Eccles, Bolt Science Ltd
Joint bearing pressure is the pressure acting on the joint as a result of bolts being tightened. If the contact pressure is too high, plastic collapse of the surface can occur. This in itself may not be an issue, but when such plasticity occurs after the tightening is completed, the bolt preload will reduce. As a consequence, joint integrity can arise such as self-loosening and fatigue.
The issue of excessive bearing pressure is likely to be encountered when softer joint materials are being used such as aluminium, as well as when mild steel instead of hardened washers are used. The strength of aluminium is usually less than half of the bolting materials typically used. As a consequence, without having something present to increase the contact area, such as flanged fasteners or hardened washers, the surface is likely to collapse when the bolt is fully tightened.
Historically, in mechanical engineering mild steel washers have been frequently used. Such washers indent and deform when the bolt is fully tightened, with some of this deformation occurring after the tightening is completed. This has been the cause of issues including accidents resulting from the preload being reduced to a level causing the bolts to loosen.
For decades bolts have had strength grades or property classes. Relatively recently was an ISO standard introduced for property classes for washers. ISO 898 Part 3 (mechanical properties of fasteners made of carbon steel and alloy steel) was introduced in 2018. This states that a 200HV washer is recommended for an 8.8 bolt, 300HV for a 10.9 bolt and 380HV for a 12.9 bolt. It also uses the wording, “shall not be used for certain washer-bolt combinations”. For example, a 100HV washer shall not be used with 8.8 or higher grade bolts. Since standards contribute to what is deemed to be ‘state of the art’, an application using soft washers with higher strength bolts that are fully tightened, can’t be regarded as ‘state of the art’.
I remember on a training course once, someone countering the argument about hard washers being needed based upon their experience. The company had been using mild steel washers for a long time in an application without any issues arising. One reason why the permissible bearing pressure should not be exceeded is that the preload loss becomes unpredictable and cannot be accounted for in joint calculations. The preload losses sustained by the use of such soft washers in their application may be such as not to cause any issue.
In other joints, such as those having a short grip length and those more highly loaded, the use of such soft washers may well result in large preload losses resulting in joint failure. The point being
Without having something present to increase the contact area… the surface is likely to collapse when the bolt is fully tightened.”
Accordingly, it is a wise choice to limit the bearing stress to the capabilities of the joint material.
The issue of surface collapse when a soft metal is used under a fully tightened bolt or nut raises the question of the suitability and advisability of the use of tab washers in high performance joints. A tab washer is a thin, soft metal plate that is fitted under a nut or bolt prior to tightening. Once tightening is completed, a corner of the plate is folded or hammered over onto one of the flats of the hexagon of the nut or bolt. By necessity for its function, the tab washer metal must be soft so that it can be deformed without fracturing. The warning about excessive bearing pressure will apply and it will not be possible to provide limits at the design stage, or on how much preload loss will result from plastic deformation of the surface following tightening. It could however be established from tests, but the modern approach is to predict at the design stage whether the joint is fit for purpose. Accordingly, Bolt Science doesn’t recommend the use of tab washers due to the uncertainty of what preload losses are going to be experienced.
Tab washers are used to prevent rotation of a tightened bolt or nut. You would think this would be a fool proof way of preventing rotation. Surprisingly, the soft nature of the washer can work against it. On a Junker test, the off torque that is attempting to undo the bolt is of such a magnitude that it can cause the tab to be forced away from the hexagon flat so that the bolt rotates, and the preload lost. On the tests completed by Bolt Science, double tabbing (having two tabs against different sides of the hexagon faces) such movement
www.boltscience.com
JRP (Jaton Riveting Products), the dedicated riveting range from Owlett-Jaton, has extensively increased its portfolio by adding over 80 sizes of rivet nuts, along with two new rivet nut setting tools.
Six new ranges are now available in steel zinc, ClrTri3, ClrTri8, with two new ranges also available in A2 and A4 stainless steel. Additionally, two ranges feature a closed design, making them ideal for manufacturers seeking a sealed end that protects from liquid and debris.
The new range from JRP includes the reduced head round knurled body closed blind rivet nut – for use when a ‘flush fit’ or a moisture/pressure-tight seal is required; a reduced head part hexagon body closed blind rivet nut – used when a higher torque loading is needed, as well as a ‘flush fit’ or moisture/ pressure-tight seal is required; and a flat head round JK split nut open blind rivet nut which is ideal for use in soft or brittle materials. The legs of the flat head round JK split nut open blind rivet nut expand on the blindside of the parent material to provide a load-bearing footprint.
As part of the range expansion, two new rivet nut hand tools, consisting of a wrench and pliers have also been introduced to use specifically with the flat head round JK split open blind rivet nut.
Also featured in the new release is the flat head round PN heavy-duty split nut which is ideal for use in composites, plastics, GRP and thin sheet metals where very high pull-out forces are required, as well as the flat head US round knurled body open blind rivet nut for use in oversized holes due to its larger body diameter than other types of rivet nuts. A thin wall also allows for a larger grip range.
distributors to gain business they previously couldn’t,” comments Warren Keeley, technical consultant at JRP.
JRP also offers the reduced head US round knurled body open blind rivet nut, which is similar to the flat head version but ideal where a ‘flush fit’ is required without the need for a countersunk hole.
“With feedback from our customer base, we have listened to demand for products that are required for use in our growing market share in the electronics, rail, automotive and agricultural sectors especially. The confidence in the quality of the JRP brand along with its easy colour-coded packaging with full batch traceability, has helped
JRP has also recently invested in a new online comparison product finder, exclusively designed to assist customers in finding the exact JRP riveting product needed. The unique tool is an easy to use online converter accessed via the company website – the user simply enters an alternative supplier code into the box and it returns the JRP equivalent. The tool can be used across the whole JRP range of rivets, rivet nuts and tools.
www.jrprivets.co.uk
BÄCKER, a German-based manufacturer of plastic solutions in industrial fastening and connection technology, has expanded its production capacities with the acquisition of state of the art injection moulding tools enabling the company to add new lengths, as well as new lens screw, to its product portfolio.
Meeting the growing demands of its customers, plastic screws according to DIN 933 and DIN 912 in size M12 are now available in lengths of 20mm, 25mm, 30mm, 35mm, 40mm, 50mm, 60mm, 70mm and 80mm.
Additionally, screws according to DIN 933 in size M16 in lengths of 20mm, 30mm, 40mm, and 70mm, as well as screws according to DIN 913 from M5 to M10, are now available in larger quantities and with faster delivery. This production optimisation allows BÄCKER GmbH & Co KG to pass the resulting cost benefits directly to its customers, further strengthening its market competitiveness.
The injection moudling tools have also enabled BÄCKER to introduce a range of lens screws with TORX® drive in M3 to M8 and in lengths up to a maximum of 50mm. This investment highlights BÄCKER’s commitment to continuously investing in cutting edge technologies to meet the growing demands of the market while maintaining the highest quality and precision in production.
“For over 45 years, we have been a reliable partner in the production of high-quality plastic screws. This strategic investment in our production capabilities ensures we will continue to offer our customers premium products at competitive prices,” explains Marco Dornseifer, managing director of BÄCKER.
www.baecker.eu
At EuroBlech 2024, Sherex Fastening Solutions® and Haeger®, both part of the PennEngineering® family, demonstrated a Sherex® rivet nut installation using a Haeger® insertion machine. This demonstration highlights the growing synergy between the PennEngineering® brands, offering customers an integrated solution for fastener installation that reduces overall installation costs.
Demonstrating how Haeger® insertion machines can install a broad range of PEM ® fasteners, now including Sherex rivet nuts, this expanded capability is a major advantage for manufacturers seeking to streamline processes and minimise machine downtime.
“This marks a significant milestone for PennEngineering®,” states Mary Ann Fleming, president of PennEngineering Europe. “By adding the expertise of rivet nut installation on Haeger® machines, we will offer customers greater flexibility, enabling them to select the optimal fasteners for their applications while keeping installation costs low.”
For Haeger®, the ability to install rivet nuts will further enhance the versatility of its fastener insertion systems. Customers already using Haeger® machines will be able to broaden the range of fasteners they install, reducing the need for additional equipment and tools. This upgrade will also provide more precise installation control, improving production efficiency.
“Haeger® machines offer unmatched accuracy in force and distance control,” explains Mary Ann. “Combined with advanced programming and tooling capabilities, this will enable customers to install rivet nuts with greater precision than traditional hand tools, leading to a superior finished product.”
With this new development, PennEngineering® will continue its mission of driving innovation, offering fastener solutions and advanced installation technologies that improve operational efficiency for manufacturers around the globe. www.pemnet.com
Made to be efficient, safe and versatile, the new PPHSeries hydraulic pin puller kits from Enerpac provide a safe and easy way to remove joint pins.
Excessive damage to joint pins can result in extra costs and lead to longer downtime. The new complete and versatile kits feature unique and innovative components that enable a single operator to remove a multitude of joint pin sizes. By unleashing the power of hydraulic force, dangerous practices such as torching, cutting and hammering are eliminated, and components are captured and held securely within the synchronous locking jaws, which enables precision and minimal damage.
With a pulling capacity of 40 to 67 metric tonnes, the PPH-Series pin puller provides a safer and more efficient removal of joint pins up to 302mm long. It uses a powerful, Enerpac hydraulic cylinder to extract pins with precision and minimal damage, enabling a single operator to remove a multitude of joint pin sizes easily.
Supplied in a portable, wheeled carry case, the PPH-Series pin puller kits, PPH40 and PPH66, are ideal for mastering a diverse range of pin pulling tasks. Each set includes three stacking and locking patented C-Sleeves, with the option of adding an extra two sleeves for longer pins up to 508mm long. The C-shape design creates a fitment around the flag of heavy machinery pins, providing a precise and safe pin removal. Improving operator safety, each kit contains a shackle for lifting via a crane or lifting system. The column sections have multiple hoist points, designed to give the user more control over the balance of the tool while it is suspended. The kit also contains a quick nut for fast attachment to threaded rods, with alternative thread sizes available to purchase separately.
With existing solutions using regular threaded nuts, which require time to run down the rod and cannot be used on damaged treads, the PPH-Series kits are engineered to streamline even on the most demanding pin pulling projects. The innovative split quick nut makes it easier and faster to manipulate damaged threads. The easy one handed closure is quick to assemble around a rod and avoids running the nut over damaged threads.
Designed with its customers in mind to streamline business process management, PSM CELADA Fasteners, a UK-based distributor of fastener solutions, quick lock systems and assembly tools, has launched its new online Customer Area.
This newly enhanced portal is an easy to use, intuitive platform, offering a refreshed interface that serves as a virtual dashboard.
It gives customers a comprehensive overview of their entire order history and, with just a click, users can access a variety of information needed from quotes and orders to invoices, technical documents and quality certifications.
To further enhance direct communication with customers, PSM CELADA Fasteners is always on hand to resolve any issues. Customers can submit support requests directly to the service team via a dedicated section of the platform.
The updated Customer Area is part of PSM CELADA Fasteners’ long-standing commitment to staying close to the market and being the ideal partner for clients’ project needs.
“With this new Customer Area, PSM CELADA Fasteners is better equipped to support customers throughout the post purchase journey, addressing their needs through a platform designed to streamline and accelerate business processes, making professional life easier,” explains PSM CELADA Fasteners. “The introduction of increasingly user-friendly, intuitive and responsive tools demonstrates our commitment to simplifying work management and providing a smoother, more sustainable customer experience. Driven by a continuous pursuit of quality, innovation and efficiency, we are consistently striving to meet the highest standards of excellence, with a focus on constant improvement.”
UK-based TensionPro, an expert in bolt tensioning technology, has developed a new semi-automated tensioning system, QUANTUM smart tensioner, equipped with a digitally controlled pump unit connected to an electro hydraulic tensioning tool to deliver greater
By providing crucial data necessary for correct and accurate loading of critical bolts, TensionPro explains the QUANTUM smart tensioner offers its users ultimate tensioning control, with features such as an electronically controlled pump with digital LCD and integral PCB to control the pump, store preset programs and records of the crucial completed bolt tightening data. Presets specific to each bolt or application are pre-programmed into the system prior to use, so the entire tensioning procedure can be completed with the press of just three buttons located on the tensioning tool. This semi-automated process ensures repeatable and accurate loading of each bolt.
Simple to use and completely versatile, the smart tensioner can be configured for use on OEM factory assembly lines, for both onshore and offshore construction and installation, or for ongoing maintenance projects. The system is ideal for wind turbine generator applications, ensuring speed, control and safety when working on the monopile to transition piece, foundation bolts, tower bolts, blade bolts and gearbox. Additionally, the tensioner can be used with or without a Lift & Move trolley depending upon application space and bolt sizes.
Richard Outram, sales director at TensionPro outlines: “We are very excited to launch our QUANTUM smart tensioner. The system is highly versatile and can be adapted to a wide range of applications. It can be configured with different sized trolleys and tensioning tools depending on the bolt size and flange geometry. QUANTUM is also easy for one technician to operate alone, or where a large quantity of bolts are being tightened, multiple units and technicians can work simultaneously. By improving the accuracy and repeatability of the bolt tensioning process, QUANTUM makes an important contribution to asset integrity and operator safety.”
TR Fastenings, part of the Trifast Plc group of companies, has relaunched its patented EPW self-extruding thread-forming screw, engineered to significantly cut assembly time and cost.
Arevolutionary fastening solution, the TR EPW creates its own internal thread in thin sheet metal and suits a wide variety of applications, including the HVAC, automotive, electronics, medical and telecoms industries.
Unlike traditional flow drill products, the EPW screw can be easily installed by hand with a cordless drill, making it extremely convenient and versatile. EPW works by aligning to the pilot hole in the sheet metal, forming an extruded collar and creating a robust thread profile before tightening and clamping securely, all in one easy step.
The thread-forming screw can be installed manually or via robotic systems. With a reusable design, thanks to fixtures that are easy to disassembly, EPW can be easily removed and reused for a strong and long-lasting joint. Featuring high vibration resistance and high radial compression on the screw shank, a superior hold and a secure assembly can be ensured. The lightweight design also makes the screw an ideal solution for many industries currently facing the lightweighting trend.
Designed, developed and patented by TR Fastenings, the EPW is a high strength fastener manufactured in TR’s own factory in Italy and is available across global markets in a range of materials, sizes and head styles. Surface coatings include standard zinc plating, high corrosion zinc nickel and organic zinc flake.
The EPW offers cost-effective solutions to users, thanks to its versatility of use, ease of installation and its reliability. It can be used for a variety of materials, including steel measuring 0.4mm to 1mm in thickness and aluminium measure (0.4mm to 1.5mm in thickness, complementing an already comprehensive product range that includes self-clinch fasteners, blind rivets, welding products and more.
Enrico De Angelis, research and development at TR Italy comments: “The EPW screw represents a significant commitment on our part to provide the finest possible product designs allied to the very best in quality, functionality and versatility. Relaunching this fastener now is perfect timing as customers are coming to us for more cost-effective solutions for thin sheet metal. The success that we feel this product will bring is due to a culmination of factors, including of course the investment that TR has made.”
MEKR’S, a Czech wholesaler of fasteners and anchor equipment, is making waves in the fastener sector with a strong focus on export. Renowned for its high-quality screws, bolts, nuts and washers, the company has successfully expanded its global footprint by catering to diverse regional demands.
To support its growth, MEKR´S is investing heavily in warehousing capacity and advanced technology to provide customers with a fast service. This year, the company increased warehouse capacity by 7,500 pallet spaces, an improvement designed to make managing inventory easier. The company is also implementing Artificial Intelligence into its systems, enabling MEKR’S to speed up order processing, thus leading to faster deliveries and greater efficiency.
By engaging with global clients and experts, MEKR´S aims to stay ahead of emerging trends and continue its trajectory of success.
As MEKR’S prepares for Fastener Fair Global 2025 in Stuttgart, the company sees this prestigious event as an opportunity to strengthen industry connections. “We will be be pleased to welcome visitors to our stand and share the latest innovations from MEKR’S and discuss how our fastening solutions can meet customers’ needs. It’s a great opportunity to connect and explore potential collaborations,” highlights the company. www.mekrs.cz
Rapid are a proud British Manufacturer of fasteners and turned parts. We manufacture a comprehensive range of standard threaded fasteners in various materials, including steel, stainless steel, brass, and specialty alloys such as INCONEL, DUPLEX, and SUPER DUPLEX.
Our team of experienced fastener engineers are experts in producing custom, precision components tailored to your specifications and technical drawings.
In-house bespoke manufacturing 48 machines across three sites
Full certification Nationwide delivery
DEWALT® has expanded its XR® product line of power tools with the 20V MAX XR® ¾ inch and ½ inch high torque impact wrenches, as well as the 20V MAX XR® ¼ inch quiet hydraulic impact driver.
Specifically designed with features to enable various applications, these new tools provide users with solutions to meet a range of needs from max torque for heavy-duty applications to quiet operation in noise sensitive work environments.
Among E-Z LOK’s range of threaded inserts for metal, plastic and wood, the company offers its E-Z Fin™ brass threaded inserts specifically produced for use in wood.
Providing robust metal threads in soft wood materials, E-Z LOK highlights these threaded inserts enable stress to be distributed over a greater surface area, thus enabling a permanent fastening that minimises the possibility of thread erosion.
Specifically designed for stubborn and high torque crankshaft pulley fixings, the new three counter weighted ½ inch drive sockets from Laser Tools deliver effective torque delivery –on even the tightest of fixings.
With the added weight of these sockets to reduce impact loss, this enables a more effective torque delivery from impact guns and are available in sizes 17mm, 19mm and 21mm.
Rivit’s extensive catalogue includes the structural rivets Lockriv and Magnariv, together with riveting tools specifically designed for their application, such as the 500 Series.
Suitable for sectors which are especially susceptible to vibration, both the Lockriv and Magnariv exhibit high shear strength and tensile strength and are available in aluminium, zinc plated steel and AISI 304 stainless steel, in diameters 4.8mm, 6.4mm and 7.8mm.
NSK has created MT-Frix™, a low friction ball screw designed to be mounted on the linear drive units of machine tools – an application which requires a high-level of accuracy.
Tested using NSK’s analytical technology to clarify the contact condition between the ball and groove inside the ball screw, the company has reported a “significant reduction in dynamic friction torque and heat generation for more machine tool accuracy”.
With both quality and durability in mind, GEDORE has introduced the R33003043 43 piece torsion bit set to withstand even the most challenging screwdriving jobs.
The set includes a magnetic ratchet bit screwdriver that can be converted into a pistol grip at the press of a button, alongside ¼ inch torsion bits in slotted, PH, PZ, TORX® and hexagon profiles, in lengths ranging from 25mm, 50mm and 90mm.
Special stainless steel washer
For insulating panels on timber frames
Deep-drawn outer edge
For increased rigidity
Stainless steel material
Suitable for all types of environments and atmospheres
Extra-large contact surface
For optimum load distribution on the insulating element (low density)
Flared hole (insulation side)
For full integration of the countersunk wood screw head
Suitable for all orientations of the insulating element
Horizontal, vertical, inclined, etc.
3 Bis rue du Faubourg de Couzon 42152 L’Horme | France +33 (0)4 77 73 35 43
www.acton.fr export@acton.fr
SPECIALISTS IN U-BOLTS, ACCREDITED TO ISO 9001: 2015 QUALITY MANAGEMENT SYSTEM.
We have a vast array of stock itemsmanufactured in-house - to BS3974 & Light Pattern. Available in HDSG, BZP and 316 (A4) Stainless Steel. We also stock a range of N-Bolts and can manufacture a variety of other bolts including:
Hook-Bolts, J Bolts, Sq. U-bolts, Sq. Hook Bolts, L-Bolts and C- Bolts.
STANDARD & BESPOKE SIZES, IN METRIC OR IMPERIAL
MANUFACTURING SIZE RANGE:
• M6 – M24 (Metric Coarse)
• 5/16” – 3/4” (Imperial – BSW & UNC) MATERIAL SPEC. RANGE:
• Drawn Mild Steel Rod (Gr 4.6)
• ASTM A193 B7/ A320 L7 (Gr 8 –High Tensile)
• 316 (A4) & 304 (A2) Stainless Steels
3 Star Rivet 153
310 Express 172
Abbey Clamps 15
Achilles Seibert GmbH 11
Acton 178
Advance Spare 167
Albert Pasvahl GmbH + Co 9
Alexander Paal GmbH 39
Ambrovit 13
Apex 177
APM Hexseal 145
Aramid Technologies, Inc (SmartCert) 135
Astrotech Steels Private Ltd 137
Atotech Deutschland GmbH & Co. KG 107
Bäcker GmbH & Co. KG 169
BBA Fasteners Srl 129
Beijing Jinzhaobo High Strength Fastener Co Ltd 177
Bendfast 178
Berardi Group 21
Berdan Bolt 35
Bonotto Packaging Srl 123
Bossong 95
Bralo 164
Brighton Best International 171
Brugola OEB Industriale SpA 47
CAMCAR Innovations™ (Geniune TORX®) 43
CAMCAR Innovations™ (TORX® Ttap) 173
Canali Srl 65
CEIA 121
Cetin Civata 23
Chavesbao 21
Colombo Special Fasteners 103
Construction Anchors Co Ltd 161
Dell’Era Ermanno E Figlio Srl 157
Don Quichotte B.V 165
DS Fasteners 163
E.CO. Srl 65
Euromac International Sp. z.o.o 85
Fastbolt 2
FastFixSearch.com 91
Fastener + Fixing Magazine 77
Fastener Fair Global 69
Fixi Srl 15
Flaig + Hommel GmbH Verbindungselemente 148
Fong Prean Industrial Co Ltd 173
Fürniss GmbH 127
G & B Fissaggi Srl 98
Gala Precision Engineering 49
GOEBEL GmbH 51
Graewe GmbH & Co. KG 169
Growermetal 63
Hafren Fasteners Ltd 147
Haiyan Jiamei Hardware Manufacturing And Tech Co 31
Halfmann Schrauben GmbH 105
Hariton Machinery Company Inc 112
HAŠPL a.s. 85
HEICO Befestigungstechnik GmbH 163
Hellermann Tyton GmbH 139
Hisener 4, 5
Hobson Engineering Pty Ltd 97
3
Inoxdadi 65
Jiangsu Yongyi Fastener Co 29
Jiaxing Kinfast
157
Enhancement of certifications in seismic zones
New range with reduced embedment for a wider choice of applications
New coatings for enhanced durability and usage in extreme environments
Improved load performance and reduced edge distances and spacings
We already know our wedge-locking washers are the go-to bolting solution when safety really matters, and adding the CE-marking makes the list of benefits even longer. This means that independent, third-party bodies ensure the highest quality performance, while you enjoy a seamless process of complying with EU regulations.