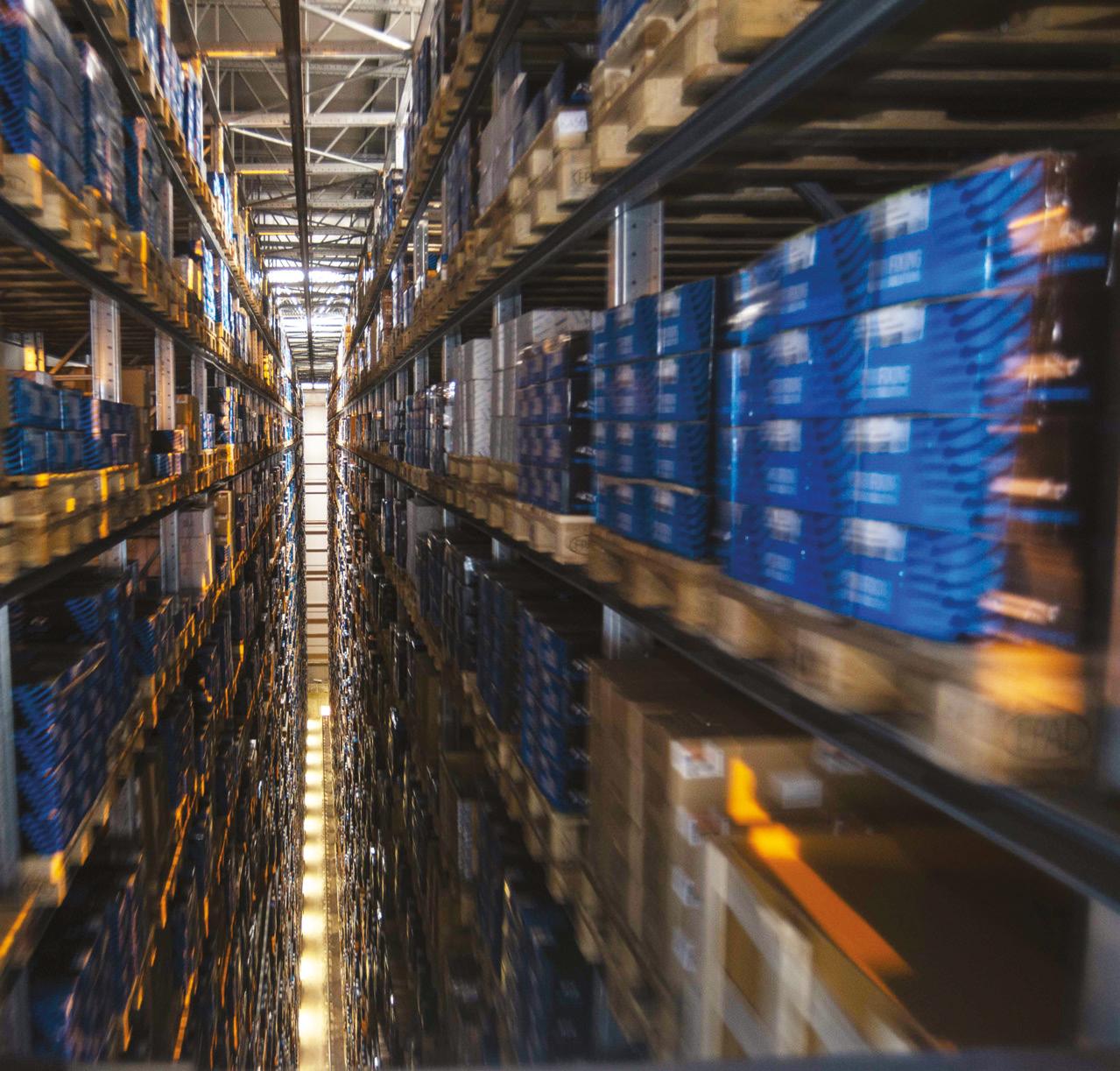
CONNECTING THE GLOBAL FASTENER INDUSTRY
In
Artificial Intelligence and logistics in the fastening sector Made in Italy
Countdown to Stuttgart

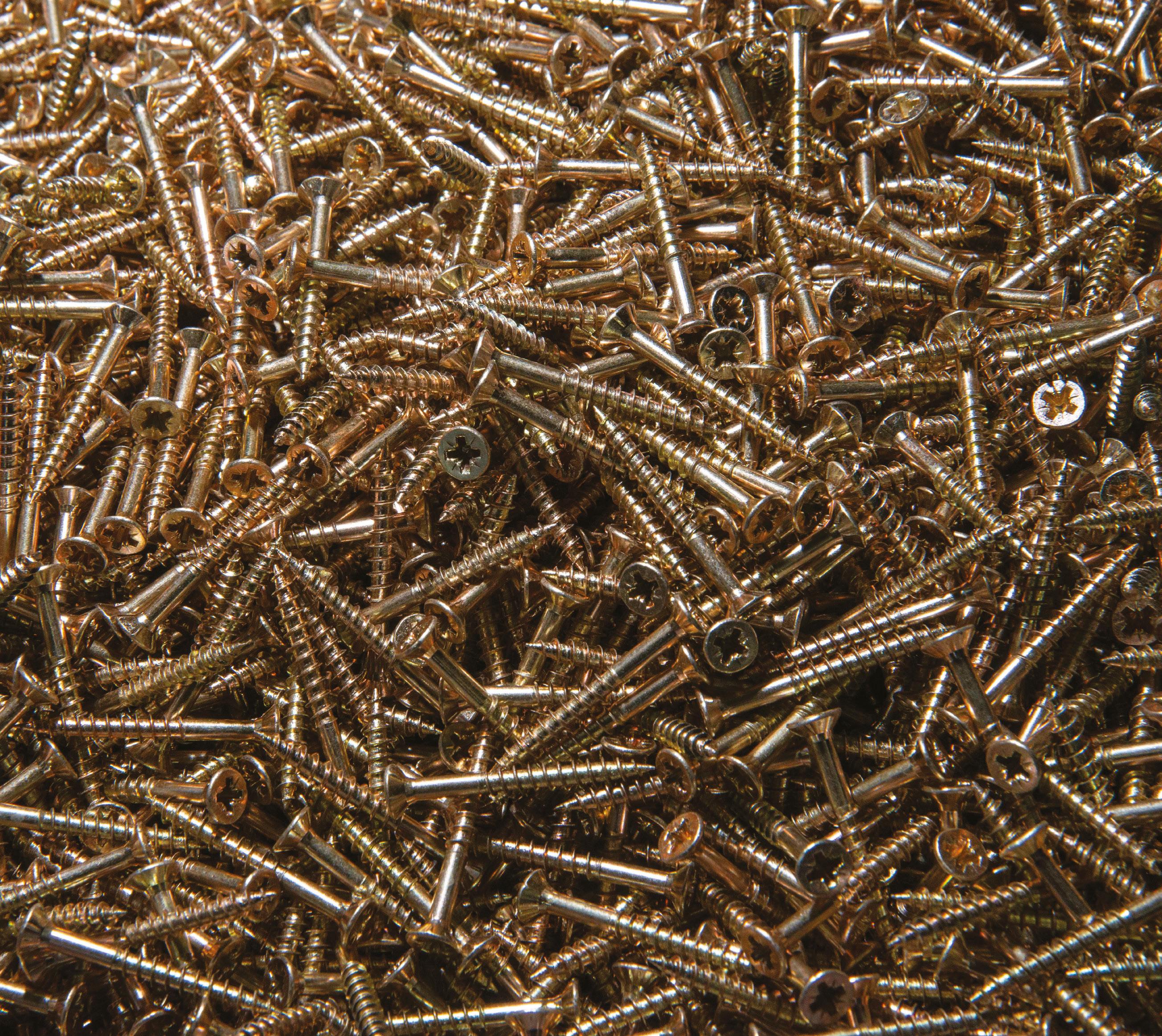
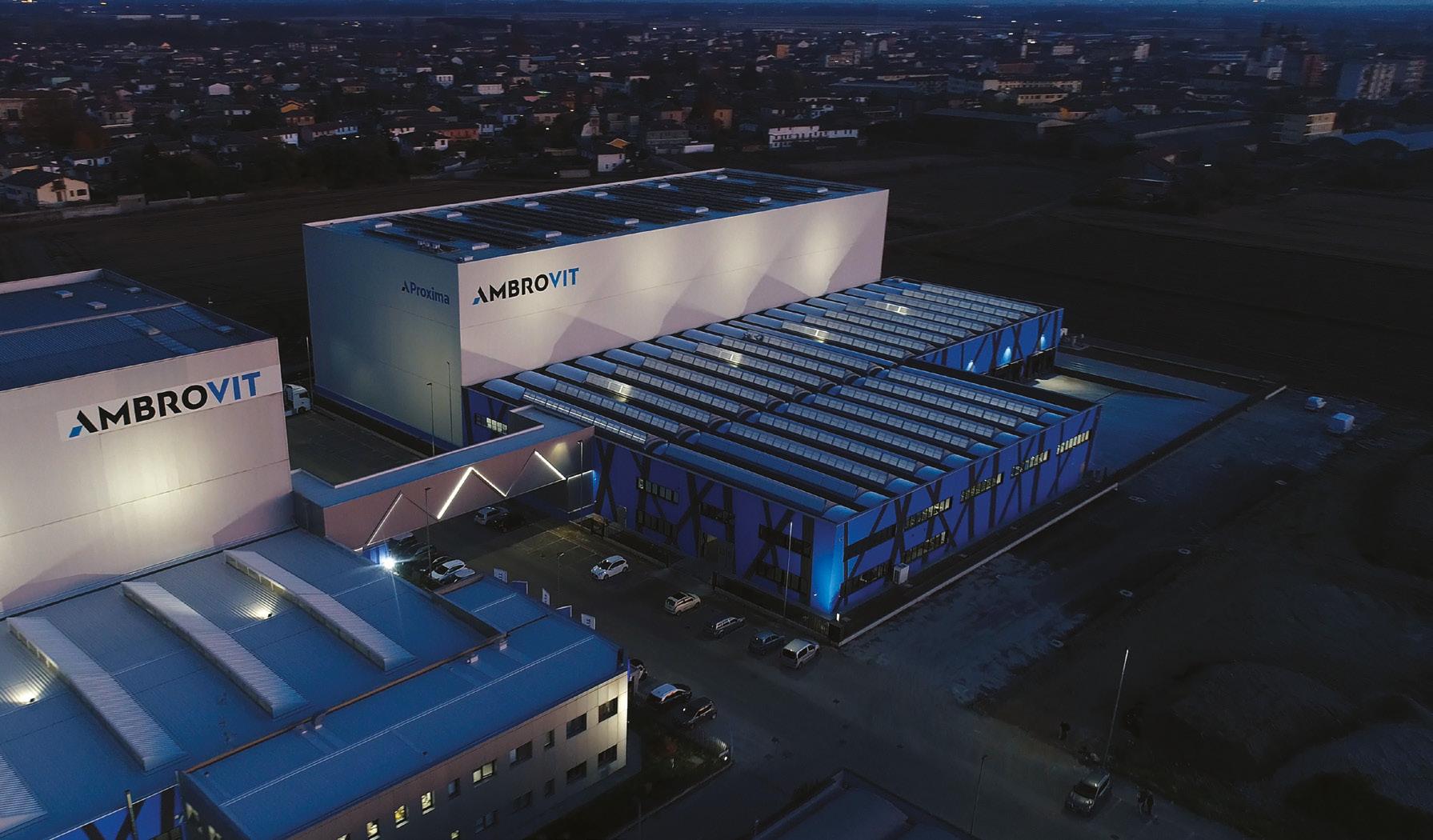
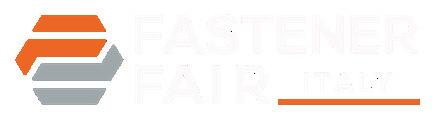
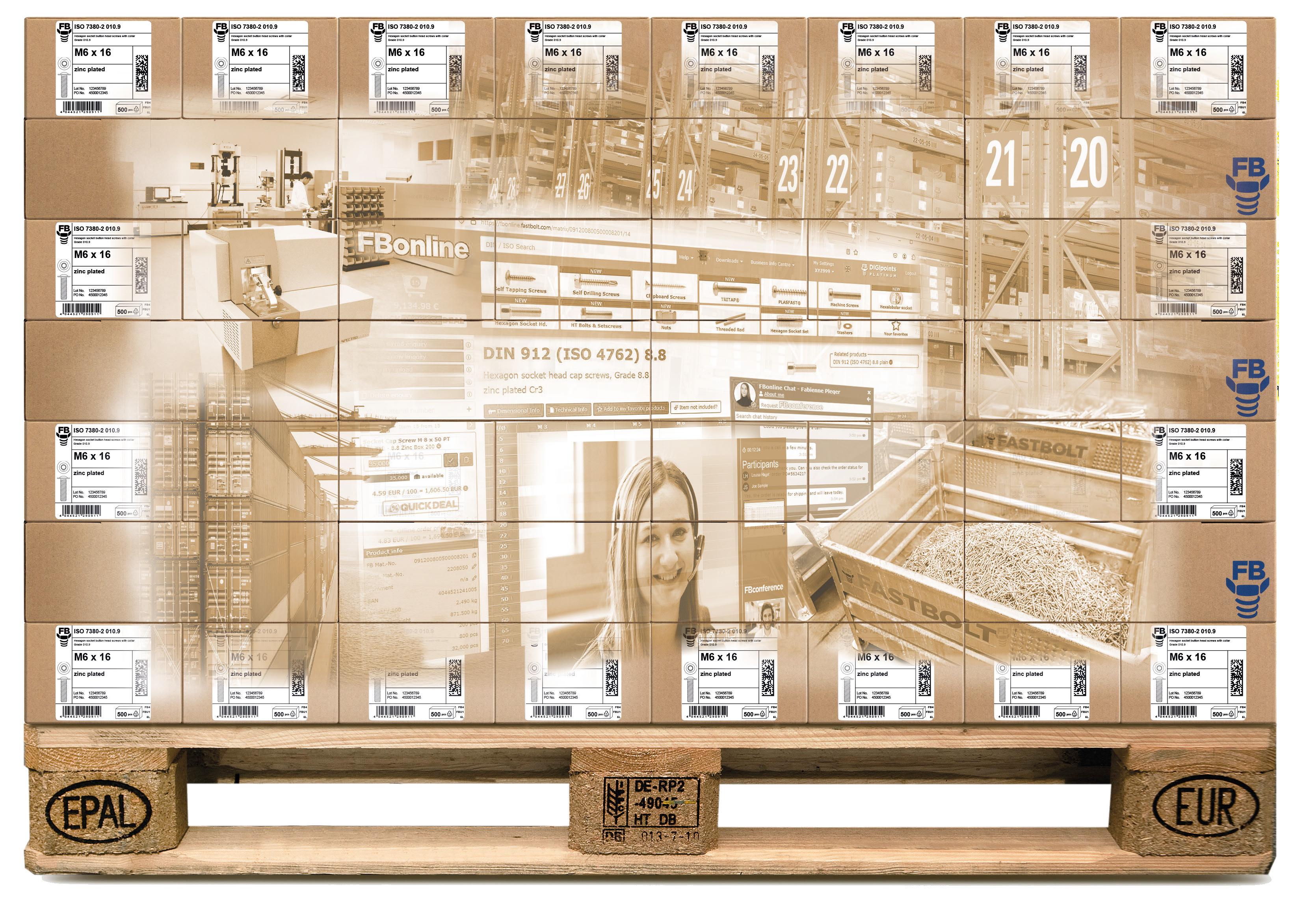
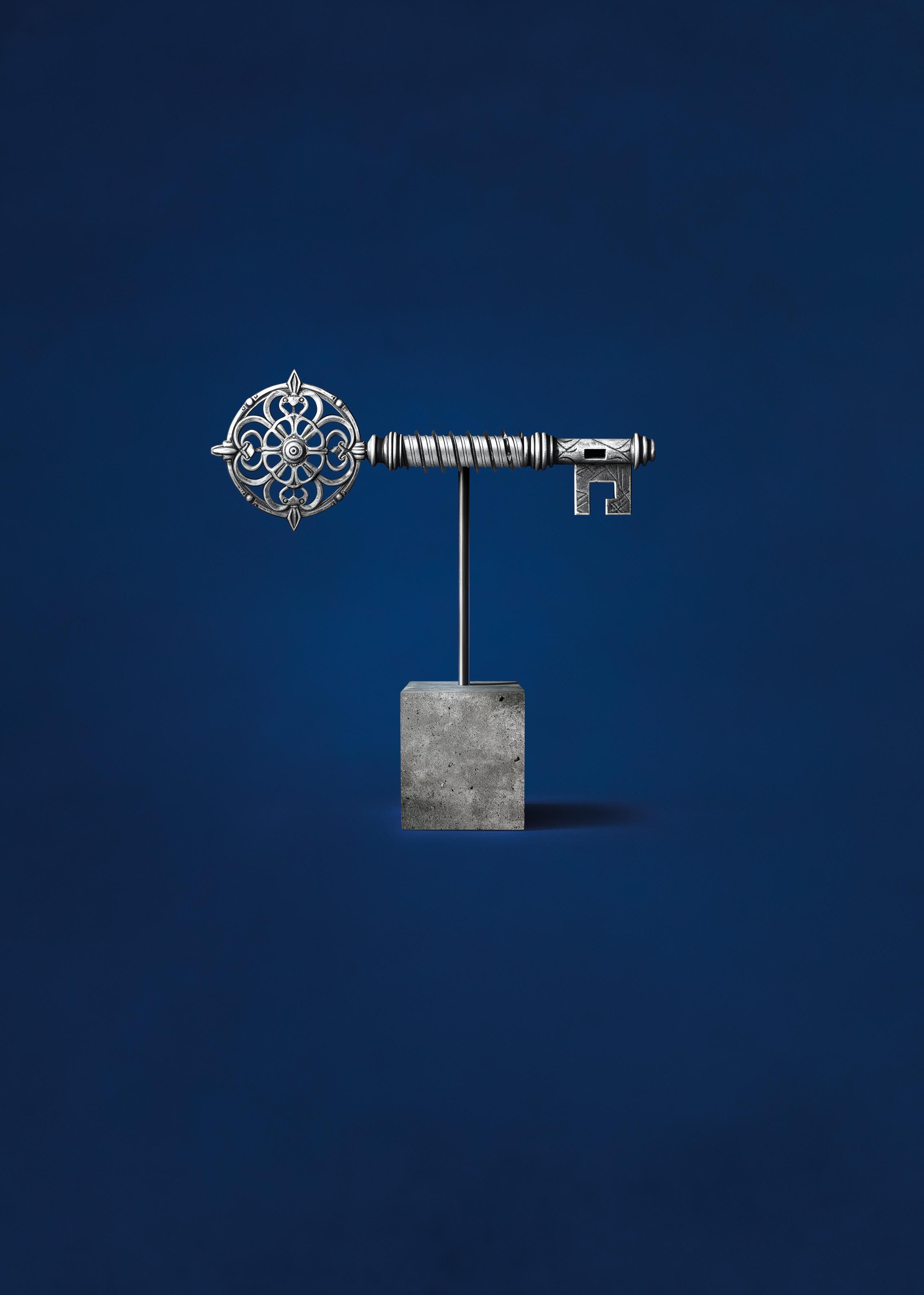
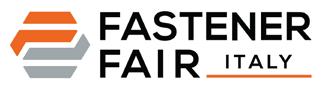
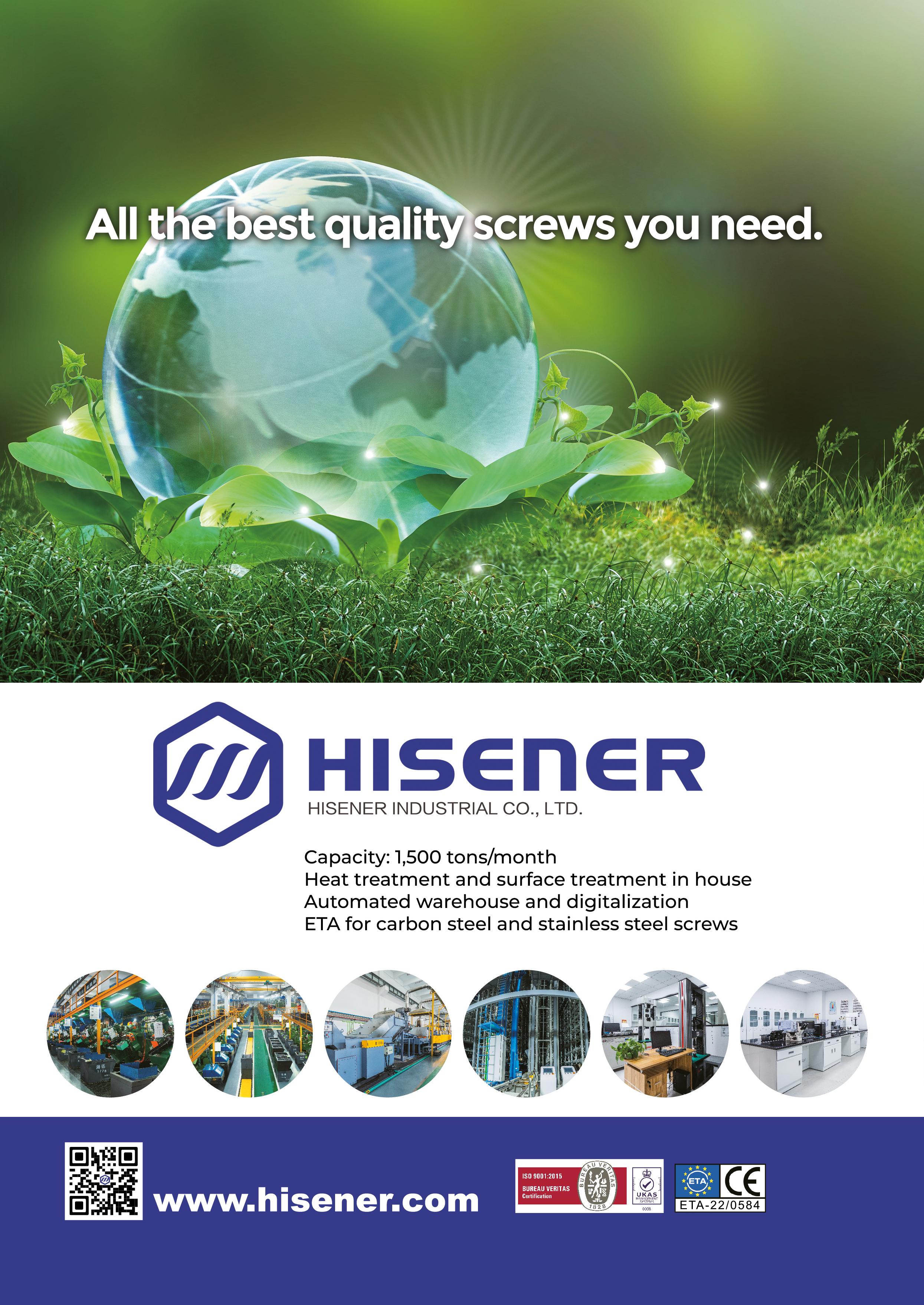
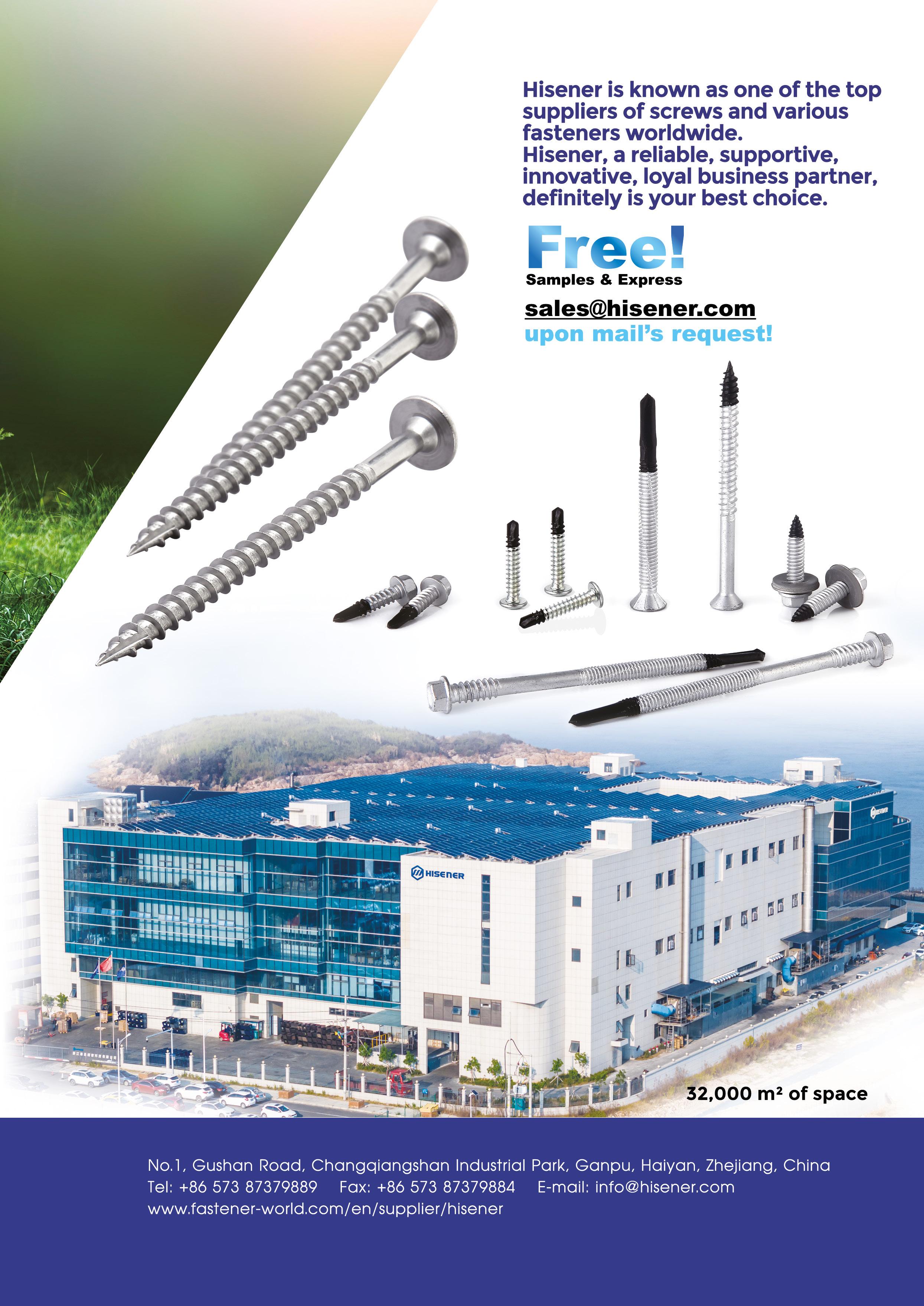
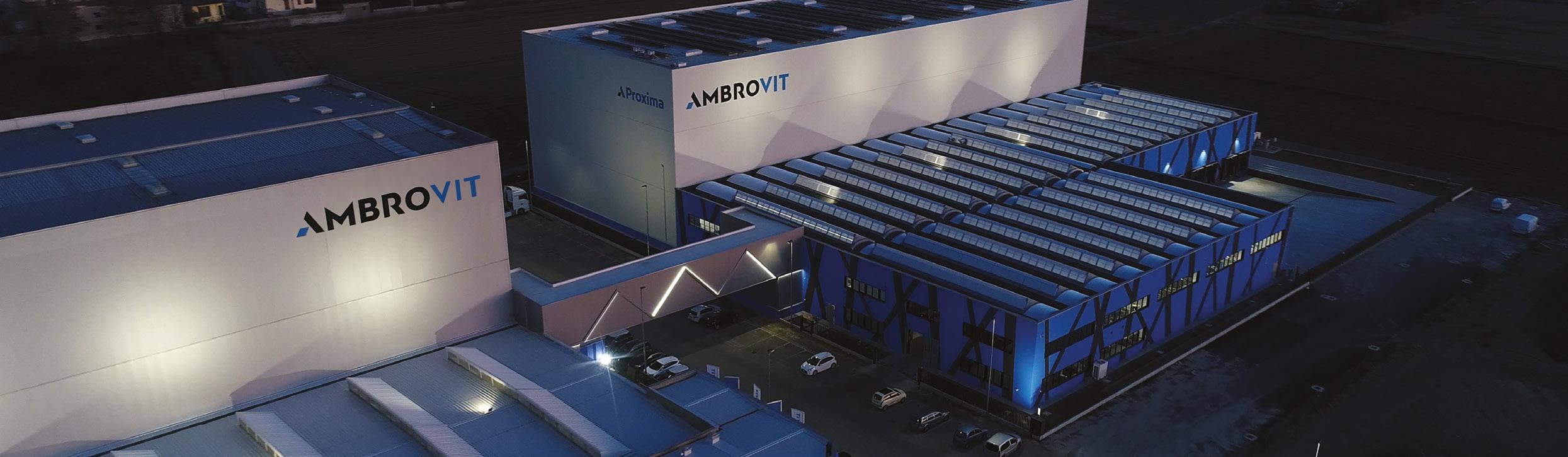


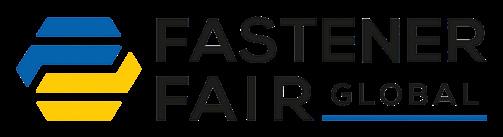
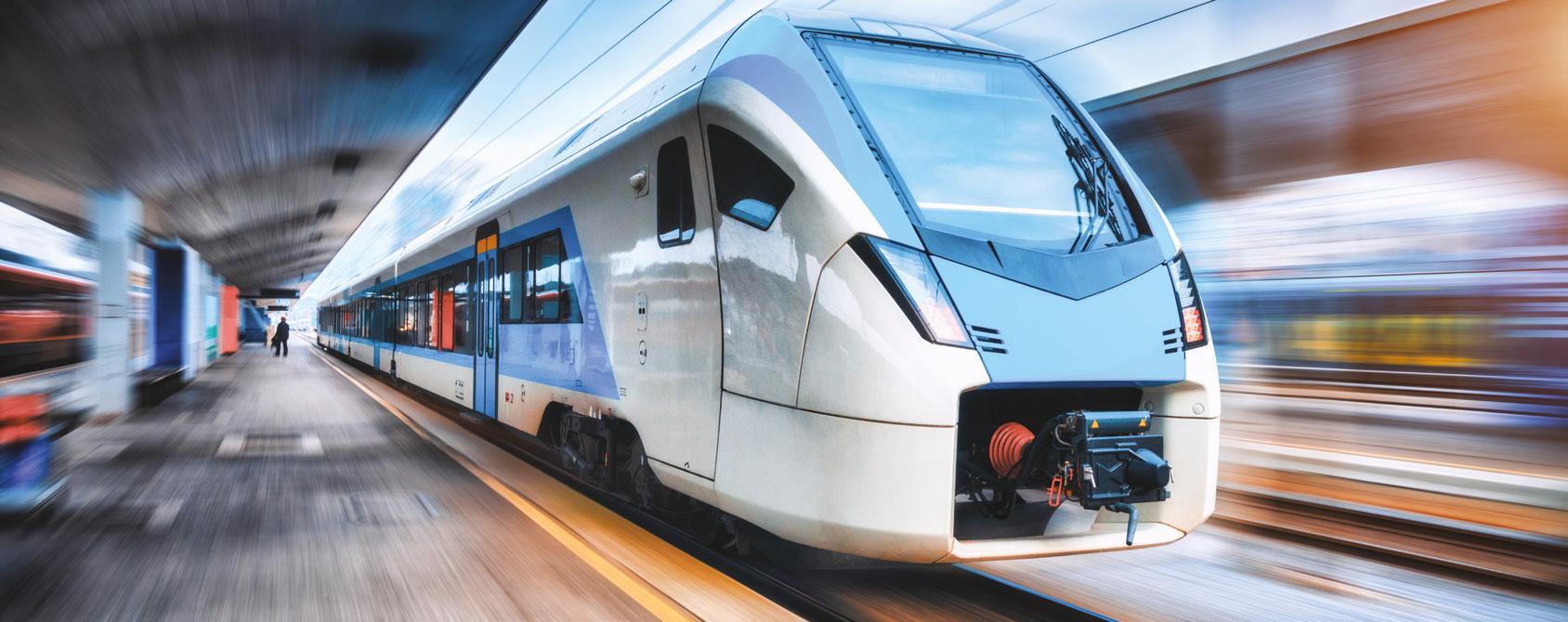
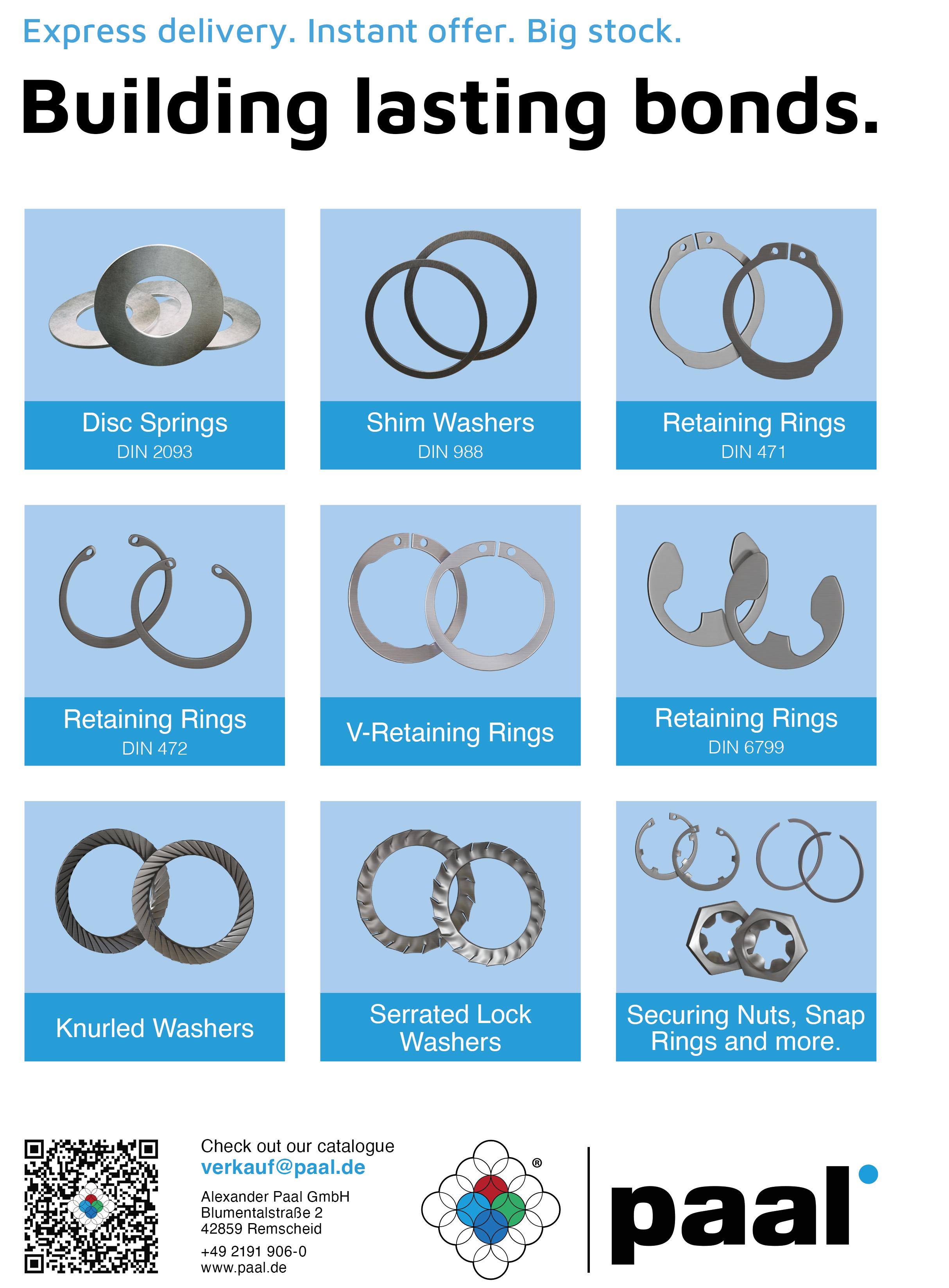
CONNECTING THE GLOBAL FASTENER INDUSTRY
In
Artificial Intelligence and logistics in the fastening sector Made in Italy
Countdown to Stuttgart
Will Lowry, content director, Fastener + Fixing Magazine
As the biggest issue ever in over 25 years, I am confident the September edition of Fastener + Fixing Magazine made a satisfying ‘thud’ when it hit everybody’s desks. Inside there are over 200 pages of jam-packed insights, news and developments across the fastener and fixing sector – especially when it comes to the Italian market.
We have an exceptional ‘Made in Italy’ feature that includes 42 Italian companies, from SMEs to global leaders – producing everything from high strength bolts, automotive fasteners, screws, rivets, nails, mechanical and chemical anchors, retaining rings and washers, threaded rods and tie rods, to precision turned parts, power tools and specials, as well as leading machinery for every step of the fastener manufacturing process.
With the ongoing impact of the Carbon Border Adjustment Mechanism (CBAM) regulation, the feature really does underline the type of products that are available from an EU country with a reputation for the very highest quality.
Alongside our ‘Made in Italy’ feature we have a preview of the upcoming Fastener Fair Italy show, which takes place from 29th – 30th October in hall 3 of CityLife – Allianz MiCo in Milan. We also have an exhibitor list of those companies at the event, as well as a floor plan to help find them during the show.
Another special feature in the exhibition section is focused on Fastener Fair Global, which is just over six months away. In addition to an interview with Liljana Goszdziewski, portfolio director for the European Fastener Fairs, about what visitors and exhibitors can expect from Fastener Fair Global 2025, we also invited key exhibitors to give us their thoughts on why the show is a must attend event and what they have planned.
Other key articles within this edition include our Cover Story, which is focused on Italian wholesaler Ambrovit – who explains how, in the era of Industry 4.0, technological innovation is transforming every sector and logistics is no exception –from operational efficiency to customer service, every area is affected by the ‘revolution’.
As always at Fastener + Fixing Magazine, we like to get out into the market, which is why we will also be exhibiting at the show. So, whether you are a visitor or exhibitor make sure you visit stand 144 to say ‘hello’.
www.fastenerandfixing.com
Published by
Managing Director
Jamie Mitchell jamie.mitchell@verulammedia.com
Content Director
Will Lowry will.lowry@verulammedia.com
Deputy Editor Claire Aldridge claire.aldridge@verulammedia.com
Assistant Editor Rebecca England rebecca.england@verulammedia.com
Sales Director Mac Rahman mac.rahman@verulammedia.com
Business Development Manager –Italy
Emiliano Pagliaroli emiliano.pagliaroli@verulammedia.com
Business Development Manager –DACH & Europe
Chantal Ridings chantal.ridings@verulammedia.com
Production & Design Manager Lee Duskwick lee.duskwick@verulammedia.com
To add to this there are articles from the British & Irish Association of Fastener Distributors on why, one way or another, the impact of CBAM will only continue to intensify for UK and Irish businesses; we have an article on the growth of Fast Trade, which has created a network of distribution and logistics centres in Italy, Spain, France, Germany and Romania, enabling it to experience significant growth in just a few years; plus there is an SME Insight into WOLTERS, a nut producer with over 100 years of production experience, but it’s not just its experience that allows it to position itself as a benchmark for the sector.
Fastener + Fixing Magazine is a dedicated, trade–only publication which is circulated freely throughout the European trade. Disclaimer
The Publisher cannot be held responsible or, in any way, liable for errors or omissions, during input or printing of any material supplied or contained herein although the utmost care is taken to ensure that information contained is accurate and up to date. The Publisher also cannot be held liable for any claims made by advertisers or in contributions from individuals or companies submitted for inclusion within this publication. The opinions expressed are not necessarily those of the Editor or Verulam Media.
Copyright Entire contents copyright © Verulam Media Ltd 2024. No part of this publication may be reproduced, stored in a retrieval system, or transmitted in any form or by any means without the prior permission of the publisher.
Annual subscription (6 issues) to non–trade and outside EU is €200.00 Verulam Media Limited, Office 3, 17 Holywell Hill, St Albans AL1 IDT Tel: +44 (0) 1727 743 882
Find us online:
for free
Find out how
+
The Würth Group reported sales of €10.2 billion in the first half of 2024, which corresponds to a year-over-year decrease of 3.2%, and a minus of 2.6% adjusted for currencies.
The sales volume generated by the German companies of the Würth Group amounted to €4 billion compared to €4.2 billion in the same period last year, with companies outside Germany reporting a slight drop in sales of 1.8% year-over-year. Within Würth Group’s core business, the Auto Division reported positive growth of 4.2%.
At €525 million, the operating result of the Würth Group is down year-over-year (2023: €680 million) as a result of the lower sales volume in the first half of the year.
Over the past twelve months, the Group has also created over 300 jobs in the fields of digitalisation and IT. Currently, the Würth Group has 88,616 employees worldwide, with 44,437 employees working in sales. Around 1,200 employees joined the company through acquisitions.
Robert Friedmann, chairman of the central managing board of the Würth Group highlights: “Our sales development continues to be strongly influenced by the economic situation, which is particularly noticeable in the manufacturing units that supply to the automotive industry, for example. Nevertheless we are sticking to our
countercyclical strategy: We invest when others scale back. We are continuing to expand our sales activities across all channels such as the sales force, shops, and eBusiness, while also investing in IT and promoting digitalisation. The promise of readily available products to our more than four million customers worldwide is our top priority.”
LISI Group achieved sales of €903.6 million in the first half of 2024, up 10% compared to 2023, with LISI AEROSPACE up 21.8% compared to the same period of last year, and LISI AUTOMOTIVE and LISI MEDICAL finishing down 2.5% and 0.8% respectively.
LISI AEROSPACE sales totalled €505 million at the end of the first half of the year. The ‘Fasteners’ segment grew in Europe by 26.2% and 22.9% in the United States on an already high comparison basis in H1 2023. As well as this, the ‘Structural Components’ segment grew by 17.1%.
The good long-term outlook for the global commercial flight of the aeronautical market is reflected in high order levels among manufacturers. The increases in monthly production rates for single aisle aircraft were revised downwards at the end of the half year with no impact on the division. The significant return of long haul orders, as well as the good performance of the helicopter and military market segments, are also supporting demand over the long-term.
LISI AUTOMOTIVE’s sales amounted to €310.6 million. Order intake for new products remains at the high-level of 13.6% of sales over the half year (14.2% in 2023) which equates to €42 million (€45.2 million in 2023). The LISI AUTOMOTIVE division thus confirms its positioning in electromobility and its ability to
quickly adapt its product ranges. These performance results also testify to its increased diversification with Chinese or American OEMs and manufacturers, for braking systems or interior fittings.
The LISI AUTOMOTIVE division is expected to experience a slowdown in demand from its main customers during the second half of the year in a market experiencing profound technological and geographic changes. Added to this is strong pressure on prices across the entire automotive industry with the will to lower the manufacturing costs of electric vehicles. The LISI AUTOMOTIVE division will therefore have to continue to demonstrate discipline and adaptation while ensuring the development and ramp-up of new products resulting from record order intake in recent years.
LISI MEDICAL’s sales amounted to €88.5 million in H1 2024. In addition to this unfavourable comparison basis in the first quarter was a movement to adjust the inventory levels of the division’s main customers and production disrupted by difficulties in sourcing raw materials.
Fastener Fair
25th - 26th September 2024
Booth W10 | Krakow | Poland | www.fastenerpoland.pl
Fastener Fair
29th - 30th October 2024
Booth 1434 | Milan | Italy | www.fastenerfairitaly.com
Achilles Seibert GmbH Philipp-Reis-Straße 3 D-24558 Henstedt-Ulzburg
Phone +49 (0) 41 93 89 55 sales@achill-fasteners.com
www.achill-fasteners.com
Norm Holding has announced that effective from 1 st January 2025, Vice-Chairperson and CEO Nedim Uysal will transition his CEO role to Mahmut Öztürk, head of industry group. Mr Uysal will continue as vice-chairperson, ensuring a smooth transition and continuity in leadership.
Over the past five years, Nedim Uysal has been instrumental in strengthening Norm Holding’s market position. His visionary leadership has led to significant growth, with Norm Holding expanding its operations and revenue to €500 million. Under his guidance, Norm Holding’s branding and marketing efforts have advanced domestically and internationally to 24 companies and 20 production facilities. His focus on sustainability and corporate governance has earned Norm Holding several accolades, including the EcoVadis Silver Medal, TAİDER Northern Star Sustainability Award, and Deloitte Best Managed Companies Award.
Chairperson M Fatih Uysal shared his thoughts on the transition: “Our recent investments have deepened our core activities while enabling growth in new sectors. To meet our evolving needs, we aim for a more agile structure. I extend my heartfelt thanks to Mr Nedim Uysal for his visionary leadership and determination, which have greatly enhanced our business. We are deeply appreciative of his contributions and the significant milestones he has achieved for our company. I am confident that under Mr Mahmut Öztürk’s leadership, marked by responsibility, meticulousness, and disciplined dedication, we will make significant strides toward our innovation and sustainable growth goals. I believe that the valuable contributions of both executives will propel our organisation further in the coming period. I wish the new appointments all the best and success.”
Mahmut Öztürk graduated from Dokuz Eylül University’s faculty of economics and administrative sciences in 1995 and completed the procade master programme at Dokuz Eylül University faculty of business administration in 1997. He started his career at Norm Fasteners as an export officer in 1997, later holding roles in production planning, domestic sales, and automotive sales. From 2006 to 2017, he served as general manager at Norm Fasteners, and since 2017, he has been the head of industry group. In 2024, he graduated from the Harvard Business School advanced management programme.
NORMA Group achieved a robust level of profitability in the second quarter of 2024 despite a difficult market environment, performing in-line with expectations.
Group sales in the second quarter of 2024 were down 5.5% over the prior year to €306.3million (Q2 2023: €324 million). Currency effects had a positive impact of 0.2%. The acquisition of the Italian irrigation specialist Teco, which was completed at the end of February 2024, also contributed 0.2% to sales development.
In the Americas region, sales in the second quarter of 2024 showed a 1.3% year-on-year increase to €146.4 million (Q2 2023: €144.5 million). This includes positive currency effects of 1%. End customer driven business with stormwater drainage and irrigation solutions was the main growth driver – with Water Management growing by 5.9% compared to the same quarter of the previous year.
In the EMEA region, the company generated sales of €122.7 million in the second quarter of 2024, representing a decline of 10.1% compared to the prior year quarter (Q2 2023: €136.6 million). A downturn in the European vehicle industry with lower production figures was reflected in a 13.3% decline in sales in Mobility & New Energy compared to the same period of the previous year. Industry Applications also declined slightly by 3.6% compared to the second quarter of 2023.
In the Asia Pacific region, sales declined by 13.4% year-on-year to €37.2 million in the second quarter (Q2 2023: €42.9 million). This includes a decline of 1.6% due to negative currency effects. The continued hesitant recovery of the Chinese economy and, in particular, the uncertainties in the construction sector had a negative impact on business with joining technology for broad industrial applications (Industry Applications), which shrank by 26.4% compared to the previous year.
Nögel Montagetechnik Vertriebsgesellschaft GmbH has started work on its new 4,200m² facility, aimed for completion by February 2025.
The new facility will house the German manufacturer’s plastic injection and aluminium production, as well as further increasing its warehouse capacity. In 2021, the company increase its stock capacity up to 14,000 pallet spaces to provide a reliable supply to its customers.
Established in 1981, Nögel has developed from a family business into a market leader for the window, construction and industry markets –providing over 45,000 different solutions for applications involving windows, doors, façades and wood construction.
Bossard Group has signed an agreement to acquire the French Aero Negoce International Group (ANI), significantly expanding its market presence in the aerospace industry.
Aero Negoce International SAS, headquartered in Béziers, France, employs 33 people and expects net sales of around €25 million for the current financial year. ANI is a French distributor of fastening solutions and provider of logistics services in the aerospace industry, with further locations in the USA and Malaysia.
“The intended acquisition of ANI is an important step to accelerate our growth strategy in the aerospace industry and strengthens our strategic presence in the Aerospace Valley in France. In addition, we see great market opportunities in the cooperation with Bossard Aerospace Germany, which will further strengthen our position in the European aerospace industry,” says Daniel Bossard, CEO of the Bossard Group.
“We are thrilled about this transaction. Bossard Group’s backing will provide ANI with a great opportunity to continue its growth trajectory while preserving the service oriented ethos that has defined our family business since its inception,” comments Patrick and Nathalie Bianchini, who led ANI in the second generation.
The closing of the transaction is expected within 2024 and is subject to the approval of the regulatory authorities and other customary closing conditions. The acquisition will be financed through the use of existing credit facilities.
The Bossard Holding AG board of directors will elect David Dean as successor to retiring chairman Dr Thomas Schmuckli Zug at the annual general meeting of shareholders on 11th April 2025. David Dean has been a member of the board of directors since 2019 and chairs the compensation committee, as well as being a member of the audit, risk and compliance
committee. Prior to that, he served Bossard Group for 15 years as CEO and seven years as CFO. Thanks to his many years of experience on the board of directors and the executive committee, he is very familiar with Bossard’s strategy, business model and corporate culture, and is therefore optimally prepared to promote the successful further development of the Bossard Group.
The board of Bulten AB has appointed Axel Berntsson as the new President and CEO of Bulten Group –starting no later than 22nd January 2025.
Axel comes most recently from the position as President and CEO of Absolent Air Care Group, which he has held since 2018. Prior to this, he was CEO of the subsidiary Absolent AB for two years. Axel also has experience in senior roles within ESAB and CPS Color, and has worked as a management consultant at Accenture.
“The board is very pleased with the recruitment of Axel Berntsson. He has solid experience from several global industrial companies and has great experience of change management, as well as of creating long-term shareholder value. With his background and leadership, I am convinced that he will successfully develop the company in new customer segments and markets,“ says Ulf Liljedahl, chairman of the board.
“Bulten is a well managed company with a long history and strong position and has a clear growth strategy. I am proud to have the opportunity to lead and further develop the company towards new goals, together with new colleagues,” states Axel Berntsson.
TR Chai Yi Precision Fastenings Manufacturing, now part of the Trifast Plc Group of companies, is celebrating the launch of its Chinese manufacturing facility in the key industrial city of Dongguan, within the Guangdong Province, capitalising on years of increasing demand in the region.
Guangdong is a vibrant world class centre of innovation and technology, providing the perfect place for TR to produce its precision engineered screws to OEM’s and their sub-contractors, whilst leveraging its global scale on a local basis.
The new 2,800m 2 of manufacturing space houses 44 cold forging machines and 36 thread
rolling machines producing 0.6mm to 4mm micro screws and thread forming screws, in steel, stainless and titanium, with an output of around 1 billion pieces per annum.
TR Chai Yi is proud to have achieved the globally recognised ISO 9001 certification demonstrating it meets the stringent criteria required for quality, safety and efficiency standards for its products and services to customers in the region. The accreditation affirms the team is committed to providing the highest level of quality across the organisation and are continually looking at ways to improve.
Jeremy Scholefield, Asia Pacific managing director, explains: “We’re delighted to open this new facility and in such a renowned area,
it’s such a positive move for TR as a Group. Our focus is on producing competitive products and continuing to build a strong capability in China and across the Asia Pacific region to meet market demands. Here in Guangdong, one of our key differentiators is our technical engineering knowledge to produce very precise and often complex components, those that are manufactured to exact measurements and mass produced. This latest investment is key for us, as it highlights TR’s robust development in the region and our commitment to staying close to key customers here.”
The new China plant is the company’s seventh global manufacturing facility with factories now also in Italy, Singapore, Taiwan and Malaysia.
Omer and Ido Wiesenfeld – the 3 rd generation of the Wiesenfeld family – have joined Videx Machine Engineering Ltd to strengthen its design, sales and service departments, as the company gets ready to celebrate its 50 th anniversary.
As well as these new additions to the team, Videx has just completed its three year expansion plan, in which it tripled its engineering staff and doubled its yearly machinery production. This was made possible by converting production departments into assembly halls, while using skilled subcontractors to make the parts that were previously made in-house.
Videx is also continuing to invest in R&D towards the computerisation of all its machines, including automatic thread matching, design of forge lines for short production batches and automation of production lines. These changes became necessary due to lack of skilled operators after the Covid-19 pandemic, as well as the trend to return production lines to Europe and the USA.
Reduced Head Round Knurled Body Closed Blind Rivet Nut
Reduced Head Part Hexagon Body Closed Blind Rivet Nut
Flat Head Round JK Split Body Open Blind Rivet Nut*
Flat Head Round PN Heavy Duty Split Body Open Blind Nut
Flat Head US Round Knurled Body Open Blind Rivet Nut
Reduced Head US Round Knurled Body Open Blind Rivet Nut Over 80 lines of rivet nuts have been added to the range. These
The Lesjöfors Group, specialists in spring and pressing manufacture, has further increased its operations in Europe with the opening of a new manufacturing facility in Poland, as well as the acquisition of both a UK and French spring manufacturer.
The new production site in Marki, Poland, divides the custom-made tension and torsion spring manufacturing specialisms across two dedicated sites and enables the production and assembly of increased spring volumes, in-line with customer demand.
In addition, investments have also been made at its subsidiary Alcomex’s standard stock door spring operation in Pune, India. The investment enables advancements in cutting edge technology, production lines, storage and shipping facilities, as well as expanding capabilities in-line with market predictions for the European and American residential and industrial door spring market.
Lesjöfors Group has also purchased Clifford Springs Ltd, a spring manufacturer based in Redditch, UK, expanding Lesjöfors Group’s parent owned sites to six within England. The aquisition also broadens Lesjöfors Group’s extensive global product offering with Clifford Spring’s seal energising technologies.
Lesjöfors has also signed an agreement to acquire 100% of the shares in Ets Lacroix SAS, a French spring manufacturer supplying mainly compression springs to customers in hydraulics and general
spring manufacturer with high technology specialisation focusing on small to medium-sized
for being a reliable supplier with strong industry know-how and quality.
“Acquisitions are a core part of the Lesjöfors growth strategy, strengthening our brand as a leading spring and pressing supplier. We have over 50 production and technical sales offices in Europe, America and Asia and are actively looking to acquire more spring manufacturers, to extend our capabilities and geographic reach,” underlines Ola Tengroth, CEO at Lesjöfors Group.
TOBSTEEL has celebrated its 20th anniversary at the end of July with all its employees and their families, having established itself as a specialist for stainless steel products and special materials.
Established by owner and managing director Tobias Schäfer on 1 st August 2004, TOBSTEEL started out as a screw distributor for stainless steel fasteners of all kinds. Over the years, the company continued to develop, by carving out a niche for itself and thereby achieving numerous significant milestones.
These include the new premises in Öhringen with an administration building, a logistics building, as well as a storage area of 12,500m². There has also been an increase in the number of employees from three to 103 and the creation of one of the largest stainless steel screw storage areas with fasteners for all five corrosion resistance classes.
This is the speciality of the screw expert, which has specialised in large-scale projects in the construction sector including tunnel construction, pipeline construction, solar technology, timber construction, fence construction, offshore and façade and window technology. TOBSTEEL is now well known in the industry for its technical expertise, quality processes and high stock levels.
The company attaches particular importance to quality – which is highlighted in the bi-metal thin sheet screws with ETA. The bi-metal thin sheet screws with double thread and fine thread were especially developed for use in the PV/solar industry as well as in roof and façade construction, hall construction and metal construction. These screws offer outstanding drilling performance in steel up to a thickness of 2mm and in aluminium up to 4mm – without any pre-drilling. This saves
valuable time and reduces material wear. In addition, the chip reduced screwing ensures a smooth and clean screwing process.
Another significant advantage of the bi-metal thin sheet screws is that the main application, the fastening of pre-drilled aluminium components, is tested exclusively at TOBSTEEL and is also covered by the ETA.
The screw wholesaler has set itself ambitious goals for the future. These include investments in warehouse logistics, the expansion of its market position and further growth in sales. With a clear vision and a strong team, the company is looking confidently towards the coming years.
Standard and non-standard items
Norm- und Standardteile
DIN, ISO, EN and others / und andere
Special parts and special materials
Sonderteile / Sonderwerkstoffe
Olli Köresaar has been appointed the new CEO of Ahlsell Finland and the Baltics. He assumed his new position on the 1 st of September and will be part of Ahlsell’s Group management.
Olli joins the company from Schindler where he held multiple leading roles over 16 years, most recently as CEO UK & Ireland and prior to that as managing director for the Nordics as well as for Finland.
Alloy Wire International’s aviation business has seen a 10% growth of its GB£18 million turnover –with this expected to rise further with post Covid travel volumes increasing.
Supplying the sector for more than 20 years, the business currently produces and ships Nimonic 90, Waspaloy, Haynes 282 and Inconel 600 to customers who then use the materials for fuselage frames, sealing rings and fuel pipes hoses, amongst other things.
ForgeFix has further strengthened its sales team with the appointment of James Blamire, who will oversee both the north and the north-west of England as he aims to further consolidate the business’s UK market by adding value to merchant customers.
James is no stranger to the fixing and fastener industry or the Dormole Group, having joined Harrison & Clough in 2000 as a trainee sales advisor, moving to an external sales representative, senior sales manager and then senior warehouse and distribution manager.
Henkel Adhesives Technologies India Private Limited (Henkel India) has completed Phase III of its manufacturing facility in Kurkumbh, near Pune, Maharashtra.
The Kurkumbh site, which was launched in 2020, serves the growing demand of Indian industries for high performance solutions in adhesives, sealants and surface treatment products. Henkel entered the Indian market in 1996 and is a significant growth driver for the business today.
After more than 30 years of operations in Russia and more than 15 years in Belarus, the Hilti Group has decided to exit both markets.
Since 2022 the Hilti Group has significantly ramped down its operations in, and ceased all exports to, Russia and Belarus. Pending government approval, the Hilti Group will sell all its local operations to the local management. The local entities will be entirely separated from the Hilti Group and operate independently. They will no longer use the Hilti nor the Oglaend brand.
Huntsman Corporation has opened a new innovation centre in Tienen, Belgium, strengthening its research and development (R&D) capabilities and reinforcing its commitment to its customers in the region.
The new 11,000m 2 facility comprises an analytical laboratory; two machine halls; as well as a fully equipped and automated product testing facility. The centre is home to more than 100 scientists and will support the application of Huntsman technologies in key markets.
Swedish premium fastener manufacturer BUMAX AB has announced the recent appointment of Star Stainless Screw Company as its new master distribution partner in the USA.
This announcement marks a notable step forward in BUMAX’s route to market in the USA and is part of the company’s ongoing development strategy for the North America region.
Established in 1950, Star Stainless Screw Company has built an unrivalled reputation throughout the US as an importer and distributor of fastener products in a range of stainless steel and other exotic alloy materials. With a network of distribution centres in strategic locations, the company is well placed to serve its extensive customer base of fastener and industrial component suppliers across the country.
“We at Star Stainless Screw Company are so excited to be partnering with BUMAX. We feel the quality of product from BUMAX, partnered with the reputation Star has for offering the highest of quality of product and service will be a perfect fit. We look forward to our partnership and thank BUMAX for its trust in Star’s excellence in distribution,” comments Tim Roberto, president at Star Stainless Screw Company.
Star Stainless will be responsible for stocking and supplying the extensive BUMAX range of high strength stainless steel products to fastener distributors and industrial product suppliers throughout the USA. This
partnership will significantly improve the availability, accessibility and speed of supply of BUMAX products to customers in the US.
“After a long road, I am happy to see our agreement finalised. A key challenge in the US has always been the geographic size and diversity of the market. Bringing together the expertise of both companies, we can now begin the important work of raising awareness of the advantages of BUMAX high strength stainless steel fasteners in the US market and making our products more readily available throughout the region,” explains Jacob Bergström, segment manager, distribution, at BUMAX.
The Fastener Training Institute (FTI) has announced a new Spanish webinar series, starting in November 2024, which will offer dual access for both English and Spanish speaking attendees.
Jo Morris, marketing director at FTI, explains: “Spanish training has been a goal of ours for years. Removing the language barrier for training is important and it will make the perfect training opportunity for entire teams. It’s critical everyone in our industry has access.”
Each 90 minute webinar will be presented in English by Salim Brahimi, the Industrial Fasteners Institute’s (IFI) director of technology, and translated into Spanish by Carlos Suarez, industrial engineer and quality control specialist at Pernostock Ltda.
“Fastener training and continuing education is important across all job functions in the industry. Whether it’s understanding the basics, learning new trends or becoming confident navigating standards, the Fastener Training Institute has you covered,” underlines Jo Morris.
The Fastener Training Institute is a non profit organisation that provides beginning and advanced training on fastener products, standards and specifications. Its core purpose is to enhance fastener use, reliability and safety with a mission to make industry professionals more knowledgeable about the fastening products they buy, sell, specify or use.
Stanley Black & Decker recently announced its second quarter 2024 financial results with Q2 revenue at US$4 billion (€3.6 billion), down 3% compared to the previous year. The company also experienced 1% organic revenue growth led by DEWALT®, Outdoor Products and Engineered Fastening, which was more than offset by infrastructure divestiture and currency.
Headquartered in the USA, Stanley Black & Decker operates manufacturing facilities globally. The company’s approximately 50,000 diverse and high performing employees produce innovative end user inspired power tools, hand tools, storage, digital jobsite solutions, outdoor and lifestyle products, as well as engineered fasteners, to support the world’s builders, tradespeople and DIYers. The company’s world class portfolio of trusted brands includes DEWALT®, CRAFTSMAN®, STANLEY®, BLACK+DECKER®, and Cub Cadet®.
Donald Allan Junior, president and CEO at Stanley Black & Decker, comments: “We extended our trajectory of solid execution on our operational priorities, which drove gross margin improvement versus the prior year, and strong cash generation in the second quarter. Strength in DEWALT®, outdoor and aerospace fasteners combined to yield organic growth amidst a weak consumer backdrop.”
He continues: “As we look to the back half of 2024, we expect mixed demand trends across our markets. With that in mind, we remain focused on implementing supply chain improvements designed to reshape our cost structure and expand margins – delivering earnings growth and generating strong cash flow. We are continuing to reinvest a portion of the savings to fund new growth investments intended to further strengthen our powerful brands, accelerate innovation and
deploy differentiated market activation to capture compelling long-term opportunities in our industry.”
Donald concludes: “Stanley Black & Decker continues to become a more streamlined business, built on the strength of our people and culture, with an intensified focus on our core market leadership positions. I am confident that by executing our strategy, we are positioning the company to deliver higher levels of organic revenue growth, profitability, and cash flow, to drive strong long-term shareholder returns.”
Patrick D Hallinan, executive vice-president and CFO, reports: “In the first half of 2024 we enhanced gross margins versus the prior year and accelerated working capital improvements, which together with proceeds from the infrastructure divestiture, reduced US$1.2 billion debt and further strengthened our balance sheet. Looking forward, we remain focused on executing our supply chain improvements to further improve gross margin and earnings in the second half of 2024 –and our progress to date supports our improved full year adjusted earnings and free cash flow outlook. We remain confident that our actions to drive toward our target of 35% adjusted gross margins, while funding additional organic revenue growth investments, will continue generating positive results. Our top priorities remain delivering margin expansion, cash generation and balance sheet strength to position the company for long-term growth and value creation.”
by Jason Sandefur, editor/publisher,
The US aerospace fastener market is forecasted to grow at a CAGR of 6.4% through 2034. Valued at US$8.9 billion (€8 billion) in 2024, the market is projected to expand as both commercial and military aircraft get approval, prompting increased demand for fasteners, according to Future Market Insights (FMI).
FMI suggests that commercial flights are becoming even more frequent as more tourists make long distance trips – due to the increasing disposable income of the working class population in developed and developing countries.
By 2034, the market is expected to top US$16.5 billion. FMI points out that one way which market players are expanding the trust placed in their products is by making products able to withstand harsh conditions. Fasteners that provide enhanced protection from corrosion and can operate at high pressure are set to add considerable value to the market.
FMI underlines commercial aerospace leads the application segment, with mechanical commercial aerospace expected to account for 67.5% of the market share in 2024.
India also shows promise for the market, with an estimated CAGR of 9.5% for the forecast period. China and Spain are forecasted to be lucrative countries for the market, with predicted CAGRs of 7.2% and 4.8%, respectively, over the forecast period. The market is expected to register CAGRs of 2.5% and 3.6% in the UK and the USA, respectively.
The FIN Fastener Stock Index fell 10.2% in the second quarter of 2024 amid ongoing weakness in the US manufacturing sector. Manufacturing economic activity contracted in June for the third consecutive month and for the 19th time in the last 20 months, according to the Institute for Supply Management.
The Manufacturing PMI registered 48.5% in June, down a 0.2 percentage point from the 48.7% recorded in May. Facing those headwinds, only two FINdex companies – aerospace suppliers Carpenter Technology Corporation and Howmet Aerospace – achieved stock price gains in the second quarter.
Carpenter Technology’s shares rose 53.5% amid continuing OEM demand strength. “We see no impact (from Boeing’s delivery delays) near term and anticipate no impact longer term,”
Carpenter CEO Tony Thene told investors. “We supply to OEM, MRO, narrowbody, widebody, Boeing, Airbus, whatever it might be.”
The FINdex performed better in the first six months, with strong gains (14.7%) in the opening quarter – lifting it 3% for the period.
Jinn Her Enterprise Co Ltd President Yung-Yu Tsai, formerly the vice-chairman of Taiwan Industrial Fasteners Institute (TIFI), has been voted by the board of directors as TIFI Chairman, taking over from Tu-Chin Tsai.
On the 27 th June at the HI-LAI Banquet in Kaohsiung, the first TIFI general members meeting of 2024 was held, with the vote taking place earlier on the same day. Yung-Yu Tsai, who has been fully involved in TIFI’s affairs and operations commented: “This year TIFI has been busy with CBAM and net zero emission issues, which have increased costs and the economy is not doing well, but this is both a crisis and a turning point for the better. In addition, we would like to thank the Ministry of the Interior (Taiwan), Ministry of Economic Affairs (Taiwan), TAITRA, Chinese National Federation of Industries, MIRDC, Taiwan CSC, and other related organisations, for their counselling and support to the fastener industry, which have enabled the Taiwan fastener industry to continuously enhance its competitiveness in the international market.”
He continued: “We ask all members to continue to support the activities of TIFI, and we hope that with the support of all member manufacturers, directors, and supervisors, TIFI can continue to progress and develop.”
Mexico has successively imposed temporary anti-dumping duties on screws imported from China, helping to increase orders for Taiwanese fastener companies.
Without low price competition from China, Taiwanese fastener companies think the price of Taiwanese screws exported to Mexico can remain at an acceptable level. The total export value is expected to rebound and will benefit the Taiwanese fastener industry.
At the end of last year, Mexico imposed a provisional anti-dumping tax of 8.02% to 48.08% on fasteners imported from China. From 23rd April this year, Mexico imposed a provisional tariff of 35% on bolts and nuts from China for a period of two years. This move has led to an increase in export of Taiwanese fasteners to Mexico.
According to statistics, Taiwan’s fastener export to Mexico in Q1 this year totalled 8,800 tonnes, up 27% year-on-year. In March, the export volume soared to 3,782 tonnes, an annual increase of 47.6% and up 79% from February. However, in terms of export price, it was US$4.16 per kg in Q1 this year, a year-on-year decrease of 5.23%.
Last year, Taiwan’s fastener exports to Mexico totalled 31,500 tonnes, a year-on-year decrease of 5.12%. The export price was US$4.31 per kg, an annual increase of 8.13%. The total export value was US$136 million (€123 million), a year-on-year decrease of 2.31%.
Taiwan CSC held a meeting on 20 th June 2024 for the third quarter steel pricing, where it was pointed out that the global economy has shown a moderate trend of recovery.
Since the third quarter is the off season for industrial demand, and considering the changes in the overall global trade situation, in order to ensure the momentum of downstream order intake, the pricing principle of “following the trend to make suitable pricing and ensure industrial stability” will be adopted.
It was agreed that the quarterly prices for bar steel and wire rod including low carbon, medium-high carbon, cold forged, as well as low alloy, will remain flat, while the prices for automotive materials will be adjusted upward by NT$800 per metric tonne.
Kaohsiung-based Rexlen has purchased a new 3,513m 2 piece of land in the New Bay area of Kaohsiung City, Taiwan.
Located near the Dream Mall, the land has been purchased for NT$1.041 billion (€29.26 million) for building corporate headquarters, enhance corporate identity and optimise the working environment of employees.
On 18th June the opening ceremony of the newly formed China Fastener Exporter Association (CFEA) and High Quality Development Forum of Hardware and Fastener Industry were successfully held in Jiaxing, Zhejiang, China.
So far, CFEA has recruited 42 council members and over 200 members, representing approximately 60% of China’s fastener export share. CFEA plans to expand to around 500 member companies in the next two years, representing over 85% of China’s fastener export share.
Jiang Hui, president of the China Chamber of Commerce of Metals, Minerals & Chemicals Importers and Exporters, delivered a speech analysing the challenges and obstacles faced by the current international trade situation. He elaborated on the original intention of the establishment of CFEA and its future development directions. At the same time, he earnestly hopes that colleagues in the fastener industry will work together to promote the development of China’s fastener industry.
Mr Shen Jiahua, president of the Zhejiang Fastener Industry Association, and founder and chairman of Yuxing Fastener (Jiaxing) Co Ltd, was elected as the first president of CFEA.
Mr Scott McDaniel, president of NFDA, sent a congratulatory message on the establishment of CFEA and looked forward to long-term cooperation. Mr Andreas Bertaggia, president of EFDA, expressed his congratulations on the establishment of CFEA and emphasised the trade relationship between China and Europe is crucial to the fastener industry. However, he also pointed out that the industry is currently facing challenges such as the imposition of antidumping duties and the Carbon Border Adjustment Mechanism (CBAM) regulation. Therefore, he is looking forward to cooperating with CFEA to jointly face these challenges.
The High Quality Development Forum of Hardware and Fastener Industry was also held on the same day. The forum conducted professional discussions on the global economic and trade situations, CBAM interpretation, digitisation of fastener quality management, as well as the import and export situation of fasteners – providing important information for participating enterprises.
In the context of global economic integration, trade ties between China and Russia are continuously strengthening. On 10th July, a business exchange meeting focusing on the Russian market was held at the China Hangzhou International Expo Center.
Hosted by ITE Group, a Russian exhibition organiser, the event aimed to deeply analyse the latest trends in the Russian market and further enhance cooperation between China and Russia in the fields of hardware, welding and fasteners.
In recent years, trade relations between China and Russia have shown robust growth, with bilateral trade volumes continuously rising and repeatedly breaking historical records. The cooperation between China and Russia is deepening, particularly in industrial sectors such as hardware, welding, and fasteners, bringing more business opportunities and market space for enterprises on both sides.
Exhibitions are an important way to promote communication and cooperation between enterprises of the two countries. Among the participating enterprises, companies from Zhejiang are a significant force. Recent data indicates that in 2023, Zhejiang enterprises accounted for 53.8% of Chinese companies participating in the hardware, welding and fastener sectors in Russia, fully demonstrating their strong competitiveness and far reaching influence in the international market.
“China and Russia have already achieved remarkable success in economic and trade cooperation, with the potential for future cooperation being enormous. It is foreseeable that more Chinese enterprises will seize this opportunity to actively enter the Russian market and jointly promote the development of the hardware, welding and fastener industries with Russian enterprises,” said a representative from ITE Group.
According to Russia’s authoritative financial and economic media Kommersant, sales of auto parts from Chinese automotive brands in the first half of 2024 increased by 1.8 times – demonstrating the huge potential of Chinese parts in the Russian market.
Although specific figures were not disclosed, Kommersant stated that several well known Chinese automotive brands, such as Haval, Chery, and the premium sub-brand EXEED, have achieved significant growth. Among them, Haval’s auto parts sales increased by 93% year-on-year, Chery’s by 78%, and EXEED’s by 10 times.
Industry experts have expressed that the demand for Chinese auto parts in Russia will continue to grow. This prediction is based on the crucial fact that Chinese manufacturers now account for up to 60% of the new car market share in Russia.
Between 2019 and 2023 almost US$4.5 billion (€4 billion) of bolts, screws, nuts and similar metal fasteners were imported by Brazil. Considering the US$533.85 million already imported in the first half of 2024, the trend by the end of this year will likely exceed US$1 billion, as it did in 2022.
Going back to 2019, when US$847 million of fasteners were imported in total, China was at the top with a market share of 21%. Over the last five years, plus the first half of 2024, China has further increased its share to 27% – with an average share among fastener purchases in Brazil of 25.33%. Next comes the USA, 16.6%; Germany, 9.71%; Japan, 9.35%; Italy, 7.08%; France, 5%; Taiwan, 4.1%; South Korea, 3.2%; India, 2.3%; and Sweden, 2.2%.
On the other side of the Formosa Strait (Taiwan Strait), Taiwanese exporters are facing a sharp drop in sales to Brazil, falling from 5.4% in 2019 to 3.1% by June 2024. One of the biggest global players in the sector, the Asian nation is betting on the sophistication of its fastener production chain; increasing its capacity to serve more demanding and high-tech industrial sectors – achieving a benchmark position in the market and acting in fine tune with social and environmental demands (ESG, CBAM, etc). This was underlined by the ‘Green Fastening, Precision Attaining’ presentation that was given during the Global Fastener Forum, an event held simultaneously with the recent edition of the Taiwan Fastener Show in June 2024.
By Dr Ricardo M. Castelhano, CEO at JOMARCA
At the end of the first half of 2014, over ten years ago, US$1 was equivalent to R$2.20. Today, the equivalence to a single US dollar is R$4.46 – with it as high as R$5.65 in the first half of the 2024.
With such a difference in the comparison between the US dollar and the Brazilian Real it made me think about how domestic Brazilian production could be at a more competitive level if we had policies more in favour of ‘Made in Brazil’ production. Instead, with the exchange rate at the current level, it’s difficult enough for many within Brazil to keep their ‘heads above water’.
When you look at just fasteners, the importers sold US$1.053 billion to Brazil in 2022; US$977 million in 2023 and US$533 million in the first half of 2024. Imagine for a second an inversion that led us to produce, let’s just say 20% of that in Brazil.
A key factor for fastener production overseas and its continued success is the industrial policies of those countries, especially in the Far East, which work more in the favour of local producers rather than against them. In addition, there is less hostile taxation, simpler paths to financial access, as well as in the acquisition of new and more modern machines, which make all the difference when it comes to productivity.
In any case, the immediate effect of the exchange rate works as a shield to protect local manufacturing, but you can’t count on a ‘glass shield’ that is of limited resistance – but that’s what we have for today.
www.gov.br/mdic
Ford Motor Company’s local production in Brazil lasted 102 years, from 1919 to 2021. However, the iconic brand maintains a development and technology centre in the Camaçari town, Bahia state, and has announced an expansion to add another 1,000 employees.
Currently operating with over 1,500 employees, Ford’s development and technology centre in Brazil is involved in various activities, such as virtual reality laboratories and ‘teardown’ projects, which is the disassembly and analysis of components. Even without local manufacturing activities since 2021, in a recent note on the Ford media portal, the North American company announced a new expansion, which will conclude in 2026, creating a new build space to house another thousand employees –increasing the total number of direct
Here Ambrovit explains how, in the era of Industry 4.0, technological innovation is transforming every sector – with logistics no exception. Companies are seeing Artificial Intelligence (AI) as a handy solution to different problems, permanently changing the way they work. From operational efficiency to customer service, every area is affected by the ‘revolution’.
Today AI is changing the business world thanks to the many functionalities that can be applied to every sector. It is particularly useful, for example, in allowing companies to predict market trends and enabling them to innovate products to remain competitive. Similarly, by analysing data and customer preferences, AI facilitates the customisation of the offer, adapting it to the specific needs and desires of consumers.
In addition, AI is useful in calculating management, security and cybersecurity risks, offering companies strategies to mitigate potential threats. Finally, it can help in assessing sustainability risks, supporting businesses in adopting more sustainable practices and contributing to
a greener future. Thanks to these advances, AI enables companies to improve operational efficiency and maintain a competitive advantage in a rapidly changing market.
On the other hand, there are certain risks associated with the use of AI that companies should be aware of and be able to anticipate. These are mainly critical issues related to the privacy of sensitive data, which can be overcome through transparency of use by companies, but also related to the inevitable changes in the world of work, which can be solved through adequate staff training.
Ambrovit SpA stands out for its ability to innovate while maintaining a strong focus on quality and efficiency. The Proxima and Orion warehouses in Garlasco, linked by a 26m bridge, are equipped with automated storage systems that optimise space and reduce product search times. Thanks to the ‘real time’ monitoring of stock levels, orders are automatically generated when needed, thus improving operational efficiency and supply chain management. For Ambrovit: ‘The future is an incredible adventure’, to be lived with enthusiasm and determination. Besides being a slogan, this motto represents Ambrovit’s positive attitude towards innovation and anticipation of market trends.
“The future is an incredible adventure to be lived with enthusiasm and determination.” Besides being a slogan, this motto represents Ambrovit’s positive attitude towards innovation and anticipation of market trends.
GO EASY ! designed by Ambrovit dedicated to the world of DIY, positions itself in a brand new market with a fresh and affordable image. Designed to make the purchase of screws and bolts easier and more accessible to end consumers and to improve the user experience, GO EASY! guarantees its customers access to the right tools.
This is how GO EASY ! was born, which is a new brand dedicated to the world of DIY – positioning itself in a brand new market with a fresh and affordable image. Designed to make the purchase of screws and bolts easier and more accessible to end consumers, and to improve the user experience, GO EASY! guarantees its customers access to the right tools.
In 2024 Ambrovit launched its new website that continues its ‘we are not numbers’ motto.
The message is clear – despite the great importance the company gives to technological innovations, these will not replace the inestimable value of the human component. In an increasingly technology driven world, Ambrovit’s approach to change represents a path to a more efficient and innovative future. Through the optimisation of logistic processes, and the introduction of customised solutions for DIY, Ambrovit not only embraces change, but drives it – showing how innovation can be successfully integrated into every aspect of business. The future of logistics is here and Ambrovit is at the forefront, ready to seize every opportunity it has to offer. www.ambrovit.it
PennEngineering®, a global leader in innovative fastening solutions, has announced the expansion of its operations located in Galway City, Ireland. This significant extension is set to create 70 new jobs over the next five years, in support of the company’s commitment to growth and community development.
Since 1942, PennEngineering® has enjoyed a sustained reputation as the global leader in the fastening industry. The company’s brands: PEM®, PROFIL®, Sherex®, as well as PennAuto®, are considered the premier manufacturers for self-clinching and other mechanically attached fasteners. In addition to Haeger®, for installation systems and Heyco® for moulded and stamped products.
The €14 million expansion project, which involves the construction of a new building, includes a state of the art technology and training centre, as well as testing laboratories and a customer experience centre that will enhance PennEngineering® ’s capacity to meet the increasing demand for engineering fastening solutions. The new jobs created will span a variety of roles including manufacturing, engineering, training and more, offering diverse opportunities for local talent.
Minister of State for Trade Promotion, Digital and Company Regulation Dara Calleary TD says: “I am pleased to welcome this announcement from PennEngineering®, which will see the creation of 70 jobs as part of a major expansion project. Investments such as this continue to advance Galway’s position, in particular, as a global hub. I wish PennEngineering® every success.”
“We are thrilled to expand our operations in Galway,” adds Mary Ann Fleming, president of PennEngineering® Europe. “This investment reflects our confidence in the potential for growth in the region and our commitment to contributing to the local economy. We look forward to welcoming new members to our team and continuing to innovate in the world of fastening technology. Our on-site manufacturing also continues to expand with the introduction of new products, continuing our 82 year history of product innovation in self-clinch fasteners. Supporting training and development of our people, and job creation, are priorities for us and this expansion is key to this initiative. As part of this growth announcement, we welcomed the board of PennEngineering® on-site for their biannual meeting and wished them well as they strategised for the future of our global company.”
Pete George, CEO of PennEngineering®, states: “Our long-standing partnership with Ireland and the IDA spans over 20 years, and their support has been invaluable in fostering the growth and development of our business in Europe.”
The expansion is expected to be completed by January 2025 and PennEngineering® plans to begin the recruitment process immediately, with job openings to be posted on the company’s website and local job boards.
The expansion project is also supported by the Irish Government through IDA Ireland. Mary Buckley, executive director of IDA Ireland, comments: “PennEngineering® has been in Galway since 2001 and this announcement highlights its ongoing commitment to the West region. The operation is already a recognised centre of excellence within the global organisation and this 4,000m² expansion, and 70 jobs, further enhances its strategic capabilities in Galway. I wish the PennEngineering® team continued success.”
www.pemnet.com
Visit us at EuroBLECH in Hannover this October in Hall 12, Stand H145 to learn more.
Haeger®, a PennEngineering® Brand, has been developing and manufacturing fastener insertion machines and tooling systems for over 80 years. The latest 5th generation Haeger® comes equipped with robot-ready capability and Industry 4.0 solutions, aimed at boosting productivity and maximizing shop-floor efficiency.
www.haeger.com
The name WOLTERS has been linked to the production of nuts for over a century, with the company’s experience forming the basis of its globally valued expertise in fastening technology. However, 100 years of production experience alone is not the only thing that has enabled WOLTERS to position itself as a benchmark for the fastener sector and a leading modern business.
WOLTERS GmbH is a third generation family business, founded in 1921 by the brothers Carl and Hans Wolters. Today the company employs 90 people and commissions over 25,000 tonnes of goods annually. “The basis of our long-term success lies in the combination of traditional production expertise and a broad, deep product range – with over 20,000 different nuts of all common standards,” explains Stephan Vick, CEO at WOLTERS GmbH. “We leave nothing to be desired in terms of materials, standards, strengths and sizes. We also deliver all types of coatings quickly and even in small quantities.”
Thanks to the unique breadth and depth of its range, WOLTERS can respond flexibly to the requirements of trade and industry. Its customer base includes well-known companies from all sectors, be it construction, automotive or mechanical engineering.
“Customers who do not want to compromise on quality and service have been relying on us for many years,” points out Stephan. “This is
because the entire journey of the products, from raw material to the customer, is transparent, documented and thus meets the highest requirements. Thanks to our 100% incoming goods inspection, measurements during production, and exclusive cooperation with certified partners, we are able to guarantee the highest level of quality and stability in our supply chains.”
WOLTERS’ customers can also benefit from individual inventory management, which includes both standard and special parts. “We keep larger quantities of goods in stock for our customers in order to be able to react flexibly to unforeseeable fluctuations in demand,” highlights Stephan. “This strategy has proven successful, especially during the Covid-19 pandemic, when we were able to deliver continuously.”
WOLTERS is also able to develop special solutions together with customers and their development departments. “Our engineers are always on hand to offer advice and support, thus offering real added value. Individual special solutions are in demand not only in logistics, but also in service and development. At WOLTERS, the customer does not speak to a machine, but to a personal consultant who quickly creates a tailor-made offer, regardless of whether it is a 10kg or 10 tonne order.”
Stephan continues: “The sooner our specialists are involved in projects, and new developments, the better we can develop products that meet both technical requirements and are economically optimal. Thanks to our knowledge, and our extensive databases, we are able to simplify complex special solutions and can optimise them through internal processing.”
Thanks to state of the art production and measuring systems, WOLTERS can quickly and easily provide prototypes and prove their suitability for individual requirements. “Our expertise in thread cutting and in the production of customer specific lock nuts is particularly noteworthy – including the manufacture of one piece locking nuts (full metal, steel and stainless steel),” reports Stephan. “We offer threads from M4 to M72 as standard, with larger threads available on request. Our extensive inventory of blanks and taps, along with uncommon and rare dimensions and thread designs, also enables us to respond to unusual customer requests at short notice.”
WOLTERS’ flexibility also enables it to quickly react to customers’ requirements, for instance in the implementation of customer-specific test programs or being able to take into consideration the additional clamping forces that coatings applied after the deformation process can produce. “Our modernised and expanded systems enable us to sort according to customer specifications and meet all requirements,” underlines Stephan.
In recent years, the company has also continuously modernised and expanded its machinery; invested in a large photovoltaic system –so that it is now independent of the public power grid for much of the year; introduced a new ERP system; as well as continued to invest in its employees to ensure they are continuously receiving specialist training, which ultimately benefits customers.
“These investments have created a solid foundation for the future, with a focus on expanding our expertise in the area of standard parts, as well as drawing and special parts,” explains Stephan. “By further building up our technical expertise in the turning and milling sector, we will be able to offer our customers even greater added value in the future.”
PRK Technologies GmbH, part of Indian-based Micron Group of Industries, is a trading enterprise and committed supplier and wholesaler to the fastener sector – with the company taking pride in its ability to offer a diverse and extensive product portfolio that is meticulously produced to cater to a wide spectrum of industries.
Headquartered near Hamburg Airport, in the town of Norderstedt, Germany – with a warehousing facility that has a storage capacity exceeding 2,500 Euro pallets –PRK Technologies states it is able to provide maximum availability of stock at all times, with quick delivery anywhere in Europe.
“We are able to meet all our customers’ requirements by getting parts manufactured around the world, with our fully stocked warehouse enabling us to supply customers as per each delivery schedule,” underlines PRK Technologies. “This reduces the inventory costs for the customers and ensures availability of stocks at all times.”
From automotive to aerospace and construction, PRK Technologies states that its portfolio is unparalleled, with a comprehensive range including bolts, nuts, screws, hexagon socket heads, countersunk screws, flange button head cap screws, dowel pins, hex head flange bolts, shoulder bolts, socket plugs, hex plugs, engine mounting studs, straight adaptors, as well as many other items.
At the core of PRK Technologies’ offering lies a range of high-tensile fasteners – with 5,000 variants covering a diameter spectrum from 4mm to 48mm, with lengths reaching up to 400mm. The wide variety of grades available including 8.8, 10, 10.9, 12.9 and 14.9. “This vast capability positions us as the ‘go to’ source for high performance fastening solutions,” highlights PRK Technologies. “Our expansive range is unparalleled, showcasing our dedication to meeting the diverse needs of our clientele.”
PRK Technologies also sets itself apart by meticulously selecting materials for its fasteners. Considering factors such as strength, durability, and corrosion resistance, the company ensures that its products can withstand the most challenging environments.
“This commitment to material excellence is a cornerstone of PRK Technologies’ approach to quality,” explains the company. “The quality of any fastening solution is inherently linked to the manufacturing process and thanks to our team of skilled professionals, we are able to ensure the delivery of products that meet the highest standards.”
In its unwavering pursuit of excellence, PRK Technologies prioritises adherence to stringent quality standards, as evidenced by its prestigious
certifications. “Our certifications underscore our dedication to sustainable manufacturing practices, ensuring minimal environmental impact throughout our suppliers’ production processes,” points out PRK Technologies. “By adhering to these internationally recognised standards, we not only demonstrate our commitment to excellence, we also instil confidence in our customers – assuring them of reliable and high-quality solutions.”
PRK Technologies ensures that it maintains its compliance with international benchmarks such as ISO 14001:2015 for the manufacture and supply of hot and cold forged high-tensile fasteners, with is commitment to delivering superior products and services further reinforced by certifications to ISO 9001:2015 and ISO 45001:2018 standards.
“These certifications validate our robust quality management systems and our unwavering focus on customer satisfaction and occupational health and safety,” mentions PRK Technologies. “With a steadfast commitment to upholding the highest standards of quality and excellence, we set ourselves apart as a trusted supplier – dedicated to delivering products and services that consistently meet and exceed customers’ expectations.”
Understanding that every client has unique needs, PRK Technologies has also adopted a customer-centric approach, with the company collaborating closely with clients to understand their specific requirements –offering tailored solutions that address customers’ challenges.
“At PRK Technologies we don’t merely sell products, we provide comprehensive technical support to customers. With a track record of excellence, established in India and now extending to Europe, we continue to set new standards for technological innovation and sustainable business practices on a global scale,” states the company. “In an era of rapid technological advancements, the fastening industry is on the cusp of continuous evolution. PRK Technologies, with its commitment to innovation, sustainability, and customer satisfaction, is well positioned to lead this transformation. The company’s future strategies; upcoming product developments; and its vision for staying ahead in the competitive landscape; are poised to set new benchmarks in the industry.”
Owlett-Jaton is the UK and Ireland’s leading wholesale supplier of fasteners, fixings and associated products to the distributor and merchant trade. In addition, whilst working with a network of secondary process partners, Owlett-Jaton can offer its customer base a wide range of secondary processes and added-value services.
Whilst the majority of fastener applications can be met by fasteners produced to recognised standards – ISO, DIN, BS, etc – with a standard coating, there are other applications for which standard products do not meet the needs of the application. They need something more specific – a special. Through its network of secondary partners, Owlett-Jaton can act as customers’ single supplier – providing order and delivery, convenience, efficiency, traceability and peace of mind.
This offering can be broadly split into six categories, all of which can be combined for a comprehensive service – thread patching, machining, bespoke to drawing and sourcing, certification and batch traceability, packing, as well as plating.
The first part of the servive is surface treatment and coating applications, which are primarily designed to reduce degradation significantly, protecting the products from corrosion, which, if not protected, could potentially lead to product failure. Secondly, it may be beneficial for the products to have an aesthetically pleasing finish to either match or contrast against the application.
Owlett-Jaton provides eighteen different coating options, with typical coatings including electroplating, such as bright zinc plating, heat-based options, such as hot dip galvanising and sherardising, or organic zinc flake coatings, such as Geomet®. Coatings may also be applied as additional topcoats to assist with torque tensioning control.
To help increase the prevailing torque and ensure that fasteners are securely locked, Owlett-Jaton also offers a wide range of thread patching. Thread patching can ensure that parts are firmly locked into position after assembly, minimising loss of clamp load due to vibration. Thread patches can also improve sealing in gas, oil and other liquid industry applications.
Another added service is the machining of fasteners – ranging from simple drilling to allow the insertion of locking split pins, or cutting to length and chamfering, through to more complicated modifications such as rethreading and shank diameter reduction.
Depending on the application, there are also times when a unique fastener is required, which needs to comply with a drawing. Working closely with the customer, the Owlett-Jaton Specials team provides a fully bespoke service, ensuring requirements are met. The process includes managing the manufacturing through to fastener testing. A variety of manufacturing processes can be utilised, including
cold forming for high volumes, hot forging for lower volumes of odd sized or extra large fasteners, as well as machining for small volumes.
Additionally, Owlett-Jaton’s non-standard products are individually batch controlled and can be provided with a range of specific certifications. Country of origin and full batch traceability is provided for all special products, with batch traceability maintained from the source and great care taken to ensure it remains identified throughout the secondary process chain.
Special fasteners often end up in demanding applications, resulting in them potentially requiring additional certification. These may include Initial Sample Inspection Reports (ISIR) or Production Part Approval Process (PPAP) – with Owlett-Jaton able to provide ISIR and PPAP up to level 3. A certificate of conformity will certify the goods or services meet the required standard, whilst a 3.1 material inspection certificate will certify the batch of components, or the raw material used.
Products and secondary processes are sourced exclusively from ISO 9001 certified factories, and Owlett-Jaton has a comprehensive product quality assurance programme in place and is also itself ISO 9001 certified.
Finally, once a product returns from a secondary process partner, and the refinishing is complete, Owlett-Jaton can repackage the product in-house to customer specifications. Using brand-free, high-quality, double-walled cardboard boxes and paper tape, products can be packed to customer quantities, up to a maximum weight of 10kg. Labels can be designed to customer requirements with bespoke branding, complete with data containing product codes and descriptions, quantities, barcodes, and batch references – making the product suitable to go to the end user without any rework. The stock can then be held at Owlett-Jaton’s warehouse facility and delivered as and when required on a call-off basis.
“The world of specials is complex and ever-changing. Our dedicated Specials and Subcon teams have many decades of experience in providing products for a wide range of customers and applications. The teams can help with all customer requirements and provide the technical and documentary backup needed to be a reliable partner in this area,” underlines Owlett-Jaton www.owlett-jaton.com
Established in 2020, Fast Trade has experienced significant growth in just a few years – creating a widespread network of distribution and logistic centres in both the EMEA region and the new markets of the Emirates and Morocco, as well as an eCommerce platform dedicated to the B2B market, which exploits all the potential of digital.
Fast Trade, part of the Fontana Gruppo, is able to offer the widest range of both standard and special fastening solutions for multiple sectors, from industry to infrastructure, petrochemical to wind energy. “The wide choice of products in the catalogue combines with the opportunity to take advantage of tailor-made services in the design of dedicated solutions, as well as take advantage of a distribution footprint that covers the entire national territory,” explains Jesus Herrera, CEO at Fast Trade.
In the last few years, Fast Trade’s activity has undergone a strong acceleration thanks to an agreement signed with SIGMA Enterprises LLC, a company specialised in the distribution of industrial products in the United Arab Emirates and in the Gulf Cooperation Council region –belonging to Mazrui International, which is a privately held diversified holding company operating across numerous sectors and asset classes.
In 2023 Fast Trade also acquired ownership of Intermétal, based in Nancy, France, a company specialised in the distribution of screws and small metal parts for industry in general – with the acquisition helping Fast Trade to expand with new product lines and solutions. Furthermore, in 2024 Fast Trade and Mungo Italia Srl became partners with the aim of providing a complete service to a vast clientele throughout Italy. Mungo Italia is a leader in fixing, sealing and thermoacoustic insulation technologies – with the company offering a long series of brands recognised and appreciated by the fixing, sealing and insulation markets. The two companies have already started collaborating on a series of projects and activities, which will also lead to benefits for the respective sales networks.
“Thanks to our links with the Fontana Gruppo, we are also able to develop adhoc projects for customers, working in partnership for the creation of special fasteners for every type of need,” highlights Jesus. “Fast Trade is also in-line with environmental policies, including sustainability. We not only comply with environmental regulatory requirements but we interpret its indications and values with a view to continuous improvement.”
Jesus continues: “To add to this, Fast Trade has a deep knowledge of the specific reference markets and an on-site presence that guarantees speed and continuous assistance. As a business we also have an inventiveness, flexibility, as well as a real empathy with the customer,
plus the ability to take a deep and sincere interest in the customer’s needs, which also makes the difference in business.”
Amongst the many new features this year, Fast Trade has also expanded into the African continent with the acquisition of Technofix Maroc, a Casablanca-based company with over 30 years of experience and the owner of the Fix it brand. Jesus comments: “We are very satisfied with the company, as well as its widespread presence across the territory and the customer/product portfolios it brings as a legacy. With this new incorporation into Fast Trade, we will be ready for upcoming projects in the coming years such as the 2025 Africa Cup of Nations and the 2030 World Cup. We are convinced that this can be an excellent gateway to the broader market of the African continent in countries such as Senegal, Cote d’Ivoire, Gambia, Guinea and Ghana.”
Going forward, Fast Trade has also set itself a target to have an even wider product range within the next five years. “Fast Trade’s business model is scalable for markets, product offerings, solutions – for all the sectors in which it operates,” underlines Jesus. “The company is already one of the most complete operators within the distribution sector and it is looking to consolidate its position. Through the approach we are taking we will become a unique supplier compared to the classic product distributor.”
www.fasttrade.cloud
By Phil Matten, policy advisor, BIAFD
It’s not been an auspicious start for the EU’s Carbon Border Adjustment Mechanism (CBAM), but that genie won’t go back into the bottle. Now, the UK has committed to introduce a similar mechanism by 2027. One way or another the impact of CBAM on UK and Irish businesses will only continue to intensify, so it’s time to take CBAM seriously.
The British & Irish Association of Fastener Distributors’ (BIAFD) position with the UK Government, and through the European Fastener Distributor Association (EFDA) with the European Commission, is that 7318 fasteners have no place in CBAM. They are not included in either UK or EU Emissions Trading Systems and their complex supply chains and processes make obtaining, collating and reporting emissions data an administrative nightmare.
BIAFD is very serious about that request but recognises it will be an uphill battle. So, while hoping for the best, we are very definitely planning for the worst.
CBAM has been top of BIAFD’s agenda for a year now and we are intent on ensuring our members are thoroughly informed and alert. We’ve invited experts to make detailed presentations to record attendance BIAFD meetings; BIAFD representatives sit on an EFDA Working Group – meeting regularly to unravel the complexities of EU reporting and simplify reporting from global supply chains; plus, BIAFD is evaluating software and support systems to help members developing CBAM reports.
We have also made a detailed submission to the consultation on UK CBAM – including the request that fasteners are removed from UK plans – and worked with government officials to provide insights into the complexities of the EU mechanism.
Across the UK and Irish fastener sector there is widespread bafflement about how to comply with the EU CBAM and, more significantly, how to find the resources to cover the administrative burden and costs of doing so. At least there is recognition here that CBAM does have to be addressed. Many, however, still seem to be in denial – believing CBAM will simply go away. That is a real cause for concern, placing those businesses in both commercial and even legal jeopardy.
It didn’t help that EU CBAM was less of a launch and more of a crash. The initial phases demonstrated a massive impact on businesses, presenting major challenges and administrative burdens both to EU importers and to their overseas supply chains.
The EU argues that CBAM is a new concept and that it has provided a two year transitional period for importers and supply chains to adapt. Nevertheless, it is a very steep learning curve. Fewer than 20% of EU companies required to file a CBAM report have so far managed to provide detailed emissions data. Major issues with the EU reporting system, now mostly resolved, certainly didn’t help.
Core issues remain:
Limited awareness amongst EU companies and far less amongst global supply chains.
The complexity of the data required.
Reticence on the part of supply chain companies to provide data.
Concerns over commercial confidentiality.
CBAM has exposed the paucity of tracking and recording emissions in supply chains, compounded by the reticence of some manufacturers and suppliers to share their data. The more complex the supply chain, the greater the stresses and resistance – nowhere more severe than in the complex global supply chains supplying industrial fasteners to the European market.
Unless we are very fortunate and UK and EU authorities accede to the request to exclude fasteners, CBAM is here to stay and will impact every fastener company in the UK and Ireland.
For imports up to the end of June, EU importers could report using default values published by the European Commission. From July, the use of default values is severely restricted and importers must now report detailed emissions data by the October deadline.
Obtaining meaningful data from supply chains is proving a huge challenge. EU importers tried passing on the EU CBAM template – but its complexity has left many UK exporters, let alone those in Asia, bewildered. Even simplifying the data template or working with a credible system provider is limited in overcoming supply chain reticence or lack of comprehension.
The deadline for full reporting compliance is, therefore, very challenging for other than the most straightforward supply chains, where credible data is readily available. Be clear, the European Commission is adamant that detailed emissions data will be required for Q3 of 2024 and that there will be no extension of the use of default values.
By all means, hope for the best but, please, prepare for the worst. Don’t wait – act on CBAM now, to ensure you will not be either legally or commercially penalised. Find out whether the products you export to the EU are in scope. If they are fasteners, as it stands, the answer is emphatically yes. Similarly, if you import fasteners, as it stands, they will come into the scope of the UK mechanism when it is introduced.
Please don’t think, as some do, that the quick answer is to stop exporting to EU customers. Sure, you won’t have to provide data directly to those customers, but it’s almost certain you will have UK customers that do supply into the EU – so you are still likely to be required to provide CBAM data to them.
Add your voice to BIAFD’s and EFDA’s in opposing the inclusion of fasteners in CBAM. Become one of the better informed – access all the information and support BIAFD is providing and will continue to provide its members. Join the British & Irish Association of Fastener Distributors today.
www.biafd.org
As the demand for high performance, precision engineered components increases, manufacturing companies are looking to embrace digital transformation methods. Carlo Salvi is able to meet these needs with its wide range of fastener machinery to enhance production efficiency, improve product quality and reduce lead times.
Carlo Salvi supplies a wide range of machines for different applications in many fields, such as aerospace, automotive and oil and gas, and include cold and warm forming processes. The forming machines include simple one-die two-blow headers, as well as multi-station machines with up to six-die and six punches.
To meet customer demands, the company is upgrading its machinery to incorporate Industry 4.0 capabilities and enable ‘real time’ monitoring and data analysis. Carlo Salvi is also going one step further to ensure its machines are Industry 5.0 compliant, to provide customers with higher precision products, more reliable delivery schedules, as well as the ability to meet ever increasing complex requirements.
Carlo Salvi SpA comments: “There has been a notable shift towards automation and digitalisation in production processes in recent years, aiming to enhance efficiency and quality. The key markets we supply have seen robust growth driven by technological advancements and increased demand for high-quality fasteners. Current challenges include managing supply chain disruptions and adhering to stringent regulatory requirements. Opportunities lie in the increasing trend towards lightweight and high strength materials, where our advanced forming technologies and commitment to innovation can play a crucial role.”
Through its extensive experience, technical expertise, and commitment to quality, Carlo Salvi is also able to offer customers comprehensive support services, including technical consultation, customised product development and aftersales service. “We offer tailored solutions to meet specific customer needs, leveraging advanced technologies and innovative processes. We collaborate closely with customers to understand their specific requirements and provide tailored solutions,” highlights the company.
This cooperation with customers is evident in the constant expansion of Carlo Salvi's product portfolio – which the company is looking to grow further with the addition of a new machine for the construction industry (see page 154 for more).
Carlo Salvi continues: “Geographically our key markets are in Europe, North America and Asia. These markets have shown
Carlo Salvi is going one step further to ensure its machines are Industry 5.0 compliant…”
strong development with increasing industrial activities and demand for precision engineered components – especially in China. On the other hand, challenges include navigating trade policies and local regulations, as well as adapting to regional market demands. However, we see an abundance of opportunities in these regions as we see growth in sectors such as the electric vehicle market and renewable energy industry, which require advanced fastener solutions that we are well equipped to provide. The market has also faced challenges such as rising energy costs and supply chain disruptions. Despite these challenges, the resilience of Italian manufacturers has led to innovations in sustainable practices and materials, positioning the market to meet future demands.”
Looking ahead, sustainability is a core focus at Carlo Salvi as it continues to incorporate eco-friendly practices in its manufacturing processes, as well as reduce waste and use energy efficient technologies. The company has also recently implemented a comprehensive sustainability programme that includes recycling initiatives and sourcing sustainable materials to not only help protect the environment, but also enhance its long-term competitiveness and meet the growing demand for green products.
“Manufacturing companies need to embrace digital transformation, sustainability and agile production methods to remain competitive,” explains Carlo Salvi. “We see our role evolving towards being not just a supplier but a strategic partner in the supply chain. We are committed to continuous innovation, integrating advanced technologies and promoting sustainable practices. By doing so, we aim to enhance our customers’ competitiveness and contribute to a more resilient and efficient supply chain.”
www.carlosalvi.com
Steeped in history and tradition Agrati Group is a worldwide leader in high-quality fastening and component solutions – supplying global automotive markets. Claire Aldridge, deputy editor, visited the company's headquarters in Veduggio, Italy, to find out how the business started as a small mechanical engineering company and has grown to produce 40 million pieces a day.
Established in 1939 in Brianza, Italy, producing woodscrews and carpentry parts, Agrati has grown to become a global organisation with twelve production plants and five logistics centres – exporting products to three continents around the world. These products include high strength bolts in various sizes and geometries; engineered components with complex geometries; nuts – single nuts, cage nuts and weld nuts; as well as licensed screws for metal, sheet metal and plastic joints for the global automotive industry.
“From a little company born in Brianza to a leading global organisation, Agrati’s success is due to a long-standing history, enriched with a passion for high-quality manufacturing, along with a supply chain that’s competitive, high-quality, flexible and adaptable,” comments Paolo Pozzi, CEO at Agrati Group.
Paolo continues: “Over the years our supply chain has grown into what our customers know it for today – strength and reliability. As our customer needs and market demands have changed, this supply chain has had to be adapted accordingly to create a local, short and competitive supply chain, which has only been possible because of the quality machinery, tooling, coatings, and of course raw material suppliers, that are still available to us locally as an Italian manufacturer.”
This locality of key suppliers also stands Agrati in good stead when it comes to its carbon footprint. The company has developed a decarbonisation strategy, with the ambition of reaching carbon neutrality by 2039. The strategy aims to define a clear decarbonisation trajectory, anticipating the milestones set by the Paris Agreement and the EU Green Deal of 2050 carbon neutrality.
In order to reach these ambitious targets and reduce its CO 2 emissions, Agrati is committed to improving the energy efficiency in
Agrati’s success is due to a long-standing history, enriched with a passion for high-quality manufacturing.”
various stages of its production with the purchase and generation of electricity from renewable energy sources, the use of low impact steel, the shift towards hydrogen, as well as the purchase of steel produced from scrap using electric arc furnaces.
“With our carbon strategy we aim to become a decarbonisation leader in the automotive industry. For Agrati, sustainability means treating the Earth as we treat our company – by taking care of it to make it healthy and strong, whilst giving those who come after us a future that can provide value. However, sustainability for Agrati is also about much more than just environmental factors – we are very proud to recognise the three pillars of sustainability,” highlights Paolo.
Paolo adds: “The three pillars of sustainability – environmental, social and economic – have different driving forces across the globe. In Europe, we are seeing a big focus on the environmental aspect but in the Americas, the social and economic factors are far ahead of their time. As a global company it’s important for Agrati to recognise all three pillars as key mechanisms to address future challenges within the fastener market.”
Recently implemented social policies include flexible working time, special work programmes to help accelerate young talent within the company, an employee mental health programme, as well as supporting its employees in local volunteering opportunities. As part of this volunteering drive, Agrati employees also participate annually in corporate volunteering, carrying out various activities with different associations.
AGRATI PERFORMANCE: the new business unit dedicated to developing and providing cutting-edge solutions for the world of racing, sports and supercars.
The mission is to ensure unparalleled reliability and high performance both on the road and on the track.
SCAN TO DISCOVER MORE
Come to discover AGRATI PERFORMANCE at the International Suppliers Fair - IZB 2024. From 22nd to 24th October 2024, Wolfsburg | Germany. AGRATI BOOTH IZB6-6307.
As well as this, Agrati has its own Agrati University for the development of its employees, with 50 trainers worldwide and over 67 courses offered. “We learn by doing, that’s always been the case. Agrati University is the beating heart of our people’s growth and development, becoming a place where knowledge merges with experience and where talents are cultivated and skills honed. It is the engine that fuels the success of our company, preparing it for future challenges and unexpected opportunities,” says Paolo.
Here, employees, and also customers and suppliers, can immerse themselves in tailor-made training paths, guided by expert trainers and/or through interactive digital platforms to enhance existing skills and discover new perspectives, helping to retain the knowledge and expertise in Agrati’s work force.
“Like every manufacturing company, we face the challenges of attracting and retaining skilled workers. With Agrati University we strive to offer our employees knowledge and understanding of the company, as well as the industry. It is important for our people to be able to know what they’re working towards, and what they’re creating, and I am proud that investing in people continues to be one of Agrati’s strengths,” states Paolo.
Agrati University also enables the company to develop completely new talent independently, based on the specific needs of the fastener market. “We promote entrepreneurship in our company by supporting people’s ideas and creativity, as well as providing the skills and
With our carbon strategy we aim to become a decarbonisation leader in the automotive industry.”
competence to innovate and improve our daily and future activities. Our team is trained to achieve better performances,” mentions Paolo.
As testament to its commitment to innovation, Agrati has recently launched a new business unit, Agrati Performance, dedicated to developing, producing and delivering cutting edge solutions for the world of racing, sports and supercars. Under the leadership of Giandomenico Sbaragli, group sales and marketing director at Agrati Group, as well as Walter Mauri, chief innovation officer at Agrati Group, the engineering team will mainly focus on three key areas of work: Performance engineering – offering co-design, calculations and FEM testing; dedicated service management – from prototypes and small batches for racing to mass production; and high performance components – featuring complex geometries and special materials.
“Our mission is to ensure unparalleled reliability and high performance both on the road and on the track. From our expertise in high performance engineering ,and as a Full Service Provider for the most prestigious supercar brands, Agrati Performance is a testament to our passion for automotive excellence,” remarks Paolo.
This passion is further underlined with Agrati’s co-design service, taking place in Agrati Tech Centres (ATCs) across the globe – where a dedicated and integrated team works directly with customers’ engineering and R&D departments to design, test and validate all the joints of new automotive and commercial vehicle components and complete full systems.
Within the ATCs, the co-design projects go through three stages –design, prototyping and testing. At the design stage Agrati manages the analysis of the joint with its working loads to make calculations and designs of the fastening system, integrated by FEM analysis for a complete nonlinear joint calculation. The company also has dedicated
lab tests on components to optimise the calculations and to integrate the database of proprietary software and workstations to find the best tailor-made solution. This stage enables the correct design definition and tightening procedure of the fastening system under investigation.
Agrati then produces small batches of parts in-house, which are used for the validation tests, cutting the cost and improving efficiency of the development with a manufacturing process that is representative of the serial process. Finally, Agrati manages tightening tests on complete systems to validate the tightening procedure to measure the clamping force by ultrasonic devices. The company also studies the effect of dynamic loads on the joint and the clamping force relaxation, as well as investigates the tribological interaction and influence of coatings over materials.
“By understanding the needs and co-developing with our customers, Agrati can improve design methodologies and spread our experience and knowledge in the field of fastening systems. This enables us to be involved with designing not only the fastener but the entire bolted joint system for an automotive application – by specifying materials, sizes, as well as tolerances, which is an added service for our customers,” highlights Paolo
With ATCs Agrati is able to offer its multi-generational deep-rooted experience, further know-how in fastening systems and next generation lab equipment and testing capability to its customers first-hand.
ATCs are equipped with the latest generation machines to measure mechanical strength, fatigue performance, chemical composition, friction coefficients, stiffness, torque and tension correlations, corrosion resistance, cleanliness level and metallurgical analysis.
Another positive to come out of the ATCs was the establishment of TOKBO Srl – a new independent company developed to bring intelligence onto fasteners, making infrastructures digital and thus increasing the level of maintenance and safety of these applications.
The TOKBO system is composed of a network of sensorised structural bolts that allows the detection and monitoring of clamping force, vibration, temperature and inclination. These bolts are connected to each other via gateways. TOKBO has also developed a proprietary solution that enables the digitisation of these threaded joints by remotely
and continuously monitoring the status of the joint with force data and accelerometric status.
The TOKBO system can be applied to both existing and newly built structures and requires four steps – installing the sensors on the threaded joints; connecting the gateway; setting up the system; as well as switching on the network and monitoring. The system can be applied to various types of fastening systems, starting from an M12 diameter, and is already being used across a number of industries including highways, railways and construction.
“TOKBO was born out of technology that Agrati was already using for our own benefit. Our ATC enabled us to look outside the box and apply this existing Agrati technology to new applications. As a result, the TOKBO solution is potentially applicable to multiple environments and we believe there are many opportunities for the technology across a multitude of new industries,” explains Paolo.
Paolo concludes: “Today our investment activities have changed. Instead of looking at the traditional ROI, we are looking at how our investments can reduce our carbon footprint. To be a global leader we must act sooner rather than later. We simply cannot wait until the last moment to invest, become compliant and meet targets. Sustainability is a huge focus for the foreseeable future within our industry and Agrati is ready.”
www.agrati.com
Driven by a need to increase production capacity, Dimac underlines that the motivation for purchasing sorting machines is changing, with a focus on replacing obsolete machines and automating processes. Therefore the Tortona-based company is ensuring its high-quality machines are designed for the future with three new solutions for the defect detection in the thread of screws and bolts.
Guaranteed by rigorous design activity and state of the art hardware and software components, and devices, together with many years of expertise in the mechanical assembly and testing, according to existing regulations and customers’ specifications, Dimac produces nine different automatic 100% inspection and sorting machines for fasteners, as well as three SPC in process control measuring systems.
A fundamental aspect of all Dimac’s machines are the robust design for enduring performance. “We’ve engineered our machines by using high-quality materials and a modular, scalable approach to reduce stress on mechanical components,” explains Dimac Srl. “The result is long-term reliability and lower maintenance costs.”
The Italian company has also looked to use advanced technologies to ensure lasting reliability, such as the new inspection stations for thread defects and surface defect controls. The new advanced solutions also include a linear camera station, multi-camera station and electro-mechanical roller station, now available on mcv sorting machines.
Dimac adds: “External thread inspection in screws and bolts is crucial for ensuring product quality and reducing false rejections, thereby lowering selection costs. Various technologies are employed for this purpose, each with specific characteristics suited to different situations.”
The traditional method for thread inspection is an optical profile control using rotating station and dimensional camera – the control station puts in rotation the piece while the dimensional camera captures multiple images. The profile analysis solution with a rotating station has two main limitations, the piece is not inspected over its entire surface, despite the increased number of captured images, and the rotation entails high machine costs and long selection times. To address these needs, Dimac has developed three advanced inspection stations.
The first solution, a linear camera control station, uses a line surface scanning camera that grabs a line of pixel for each trigger while the piece turns 360 degrees. The grabbed surface lines are then joined together to obtain the unrolled image of the cylindrical side surface of the thread. The surface line scanning camera is triggered by the 360° rotation station’s encoder to cover the entire piece surface and the resolution of the trigger pulses can be set to improve the accuracy of the surface inspection.
The vision software analyses the thread using Dimac AI tools, identifying irregularities such as ‘z-thread’ or foreign hits and dents or excess of surface coating between crests. The high-quality of the acquired side surface image enables the detection of minimal defects, including those quite invisible to the human eye, such as head fine cracks. This method is very accurate but does not perform dimensional measurements, plus its scanning cycle time limits output rates. Dimac therefore recommends this method when high-quality controls are required, such as in aerospace applications.
The second solution is a multi-side camera station equipped with three or four side surface cameras positioned 90° or 120° to one another to look at the threaded shank surface, all around. Although the image quality is lower than the line surface scanning camera version, the multi camera station doesn’t require the piece rotation, enabling high productivity of up to 700 pieces per minute for M6 screws. Dimac AI tools are also used with this station to detect macroscopic defects, such as dents, scratches, open cracks and radial holes.
The third technology, patented by Dimac in 2023, is electro-mechanical inspection using a gauging roller station, where a threaded master roller gauges the thread’s compliance. Designed for M6 screws, a group of two gripping rollers keeps the piece in rotation while the third threaded roller gauges the threaded shank simultaneously. The roller gauge sliding axis movement is checked to stay into a threshold
envelope by a special sensor. Any defect impacting the roller gauging effort to spike out of the envelope is immediately identified, to define the thread quality.
Thanks to a special control algorithm, the system is insensitive to core ovalisation, reducing the rate of pseudo-reject. The output rate is also lower than the other two solutions, but this station ensures the screwability of the conformed parts – making it reliable for fasteners used in automatic assembly lines as it helps to remove small burrs or dirt in the thread.
“We see important opportunities for Dimac to introduce automatic machines for high-speed 100% inspection and sorting fasteners with Artificial Intelligence (AI) features, as well as SPC systems for in-process data collection across all key industries. These markets are facing challenges concerning the continuous improvement of automation in production and control processes, together with data collection and analysis, as well as traceability and efficiency. They are also facing the challenges of eliminating manual sorting operations, which are subject to errors and too expensive,” states Dimac. “At Dimac we can help and our perspective automation can be the driver of the future.”
For instance, Dimac machines are designed to run unattended and be used by unskilled operators because they are user-friendly and intuitive. Furthermore, Dimac also offers periodic metrological verification using the MSA procedure as part of its after sales service, to ensure compliance with quality standards.
Dimac also ensures that its software platform is continually evolving to help guarantee stability and error-free operation. Each improvement is closely monitored for continuous and reliable performance.
As well as these technological investments, Dimac is also committed to sustainability and creating a production site in 2023 that operates entirely on sustainable energy. The site’s roof has solar panels to power
the geothermal energy plant, as well as provide heating and cooling to the building housing a new showroom, along with modern offices for the sales, marketing, service and R&D departments.
In terms of economic sustainability, in 2022 Dimac launched the Pay Per Use project in Italy. This initiative enables 100% inspection and sorting machines to be rented through a variable monthly fee based on the volume of fasteners sorted per month. The project aims to economically sustain sorting operations in low volume production contexts and promotes a circular economy by providing machinery as a service. After the usage period, machines are returned to Dimac and can be rented out to other customers.
Dimac has also recently launched a SPC-Dimac business unit, automating SPC control in production, to enhance its role as a consultant. Dimac is able to assist customers in managing quality control data, maintaining accurate and current control plans, as well as ensuring data validity for immediate use in optimising production processes. The challenge is not about the big data collection but in swiftly making the relevant data accessible and impactful. This approach promises significant future business development, offering benefits such as predictive maintenance, personnel savings, reduced waste and increased production flexibility.
“With a drive for quality getting stronger, we believe that fastener manufacturers should be changing their mentality regarding quality control,” reports Dimac. “Instead of seeing an investment in inspection and sorting machines as an extra cost in the production process, companies should be considering the investment with the same weight as they would production machinery. Dimac’s role is to partner with fastener manufacturers to support investments and supply high-quality, accurate and reliable machines that are ‘born to last’.”
www.dimacsrl.com
» INNOVATIVE CONTROLS » OPEN TO UPGRADES » CONSISTENT IN EXTREME ENVIRONMENTS » SECURE INVESTMENT
OPTICAL / MECHANICAL / NON-DESTRUCTIVE CONTROLS FOR ALL KIND OF
In 2019 Colombo Special Fasteners (CSF) acquired its heat treatment supplier CITT to guarantee the high-quality of its products. Five years on, Deputy Editor Claire Aldridge visited CITT’s brand new production plant in Usmate Velate, on the outskirts of Milan, to see how an investment in a fully automated belt line is helping towards CSF’s goal of 100% energy autonomy.
Established in the 1960s as a manufacturer of small furnaces for the goldsmith sector, CITT Srl now offers heat treatments including hardening, quenching, annealing, normalising and tempering, as well as thermochemical diffusion treatments such as carbonitriding (with and without hardening), carburising and nitriding. Surface finishing treatments are also available including sandblasting and thermal burnishing.
Fully operational at the start of June, the new automated belt line has a washing station with an integrated dephosphating system and has been developed with Industry 4.0 in mind. The production plant also complies with all current environmental and industrial regulations.
The new dephosphating station consists of a washing process before the heat treatment and is carried out using specific alkalinebased products – necessary for degreasing and removing oils, greases, stearates, as well as phosphates used mainly on steel to increase the efficiency of the lubricants required for cold drawing, which is a requirement in many automotive specifications for strength classes ≥10.9 and the ISO 898-1 standard. The new line also includes two new furnaces – a continuous furnace for smaller parts serviced by an automated belt and a static furnace for longer parts – to provide CITT with a wider range of quality services, with everything connected to an internal IT system and geared for Industry 4.0.
CITT is working for others – not just for CSF – and is a reliable heat treatment partner in the fastener industry.”
“In the current market it’s hard to find high-quality heat treatment suppliers. We made the investment in CITT because the loss of a good supplier would have created problems for us,” explains Marco Colombo, CEO at Colombo Special Fasteners (CSF). “CITT is working for others –not just for CSF – and is a reliable heat treatment partner in the fastener industry. At the same time, CSF invested significant resources to the complete renovation of CITT to guarantee a high-quality service, quicker delivery times and more flexibility – contributing to growth, improvement and development. CSF is now able to stand as a partner providing an even more exhaustive service in terms of offer, qualitative performance and timing.”
Founded in 1955 by Piero Colombo, as a factory geared towards the production of standard screws, wire drawing, and resale, CSF now focuses on the development of special parts according to drawing and is able to manufacture cold formed parts from 2.5mm – 30mm in diameter, in a variety of materials such as steel, stainless steel, brass, as well as copper, in lengths of up to 240mm. This includes parts with complex geometries and finishing grades with special threads, machining operations, heat and surface treatments through to careful inspection and sorting.
60% of CSF’s turnover is domestic, with the remaining 40% coming from mainly European markets – something Marco is keen to develop further. “Every day we take actions aimed at generating long-term value for the company and that includes a policy of expanding the countries to which we export. These actions have brought both CITT and CSF into an Industry 4.0 perspective and the next investments from 2025 and
beyond will be in sustainability and energy containment, with the goal to reach 100% energy autonomy,” highlights Marco.
Sustainability for CSF means the constant and concrete commitment to promote a business model aimed at the efficient and strategic management of the resources available. That is why the company’s strategy is made up of small steps that gradually contribute to integrating sustainability into the way it operates – laying the foundations for a real transformation of the company’s culture.
CSF’s sustainability goals include the completion of a new eco-friendly production site in Cisano Bergamasco – with solar panels to help meet the company’s energy needs; a centralised fume extraction system for the benefit of employees and the working environment conditions; implementation of an oil recovery and cleaning plan, as well as waste reduction; digitalisation of the production departments by completely eliminating the use of paper; and finally the promotion of good habits and responsible management of resources in each department, such as reducing water, plastic and paper consumption.
“We want our technology to combine profitability and sustainability, increasing efficiency while reducing costs, waste and impacts. As well as this, we are committed to promoting a good corporate culture, in order to attract and retain skilled people – a challenge we currently face as a manufacturer. CSF therefore offers the opportunity for young people to learn the art of cold forming and grow within the business,” mentions Marco.
He continues: “We need to make sure the CSF environment is a comfortable, attractive and desirable place to work, as it becomes clearer each day that the expectations of potential employees for the company are not just economic but wellbeing too. For this reason, the business
is focusing on the renovations of office buildings in both factories to provide a more stimulating and beautiful environment.”
The new eco-friendly production site in Cisano Bergamasco also houses another of the company’s projects – MASTER FACTORY 4.0. The project means all machinery in the production department is now interconnected to manage and control the production function of the whole plant, as well as the monitoring of machine activity load through the ‘real time’ data collection of headers, thread rollers, sorting machines and CNC centres. Data collected includes quantities produced and related timing; machine stops and related causes; raw material used; rejects and product nonconformities; as well as production efficiency KPI measurement. This enables the company to draft customised reports and have full product traceability.
Marco concludes: “With these investments in new high-quality technology we are laying the foundations for our future. We welcome changes, adapt to them, and shape our proposal according to the real needs of the customers – primarily ensuring their satisfaction. We are open to constantly optimising processes and improving products, aware that any positive change brings corporate wellbeing and new added values for our customers.”
www.colombofasteners.com
www.cittsrl.it
For Leonix Fasteners the last two years have been characterised by notable changes including new investors and investments, marking the beginning of a new phase of growth, in order to develop tailor-made fasteners.
During 2023 the founders of Leonix completed a partnership with new investors, all of whom have extensive experience in the manufacturing and distribution sectors. The main objective of this partnership is to strengthen Leonix’s growth trajectory and expand its geographic presence; diversify its product range; as well as enter new target markets and actively seek complementary acquisitions.
In March 2024, Leonix Fasteners also strengthened its turning milling department with the purchase of an automatic lathe for the secondary operations of pre-formed bespoke parts. The new machine enables Leonix to rework extruded cold formed fasteners in stainless steel, special alloys and also carbon steel. The secondary operation can be made on infinite geometries with a diameter range between 4mm – 20mm.
Leonix explains: “Strengthening this department means Leonix can create grooves, holes, knurling, shank reductions, machining on the tip and on the head and much more. The combination of cold forming and rework offers a cost-effective alternative to the traditional bar turning process, especially as volumes increase, which ensure a more replicable product with excellent mechanical properties at a lower cost. This enables us to become an important point of reference at a European level for this type of product. Our focus is to collaborate more with our customers to understand their needs and develop tailor-made solutions.”
The company, ISO 9001:2015 certified and located in Chiuduno, in the north west of Italy, is able to produce a range of screws in diameters from 4mm to 20mm – in lengths up to 350mm. These screws can also be supplied assembled with washers and with all main thermic and surface treatments (i.e anti-corrosion, lubrication, threadlocking, etc).
Leonix has an integrated in-house production model that covers over 5,000m 2 including a raw material warehouse, a cold forming department – with up to five blocks machines, a modern mechanical workshop, a threading department, turning/milling department, packaging department, as well as a laboratory fully equipped with the most modern control devices for inspecting incoming goods and screws in all production stages.
The company outlines: “The only way to be competitive on the market is to have an efficient production process achieved by extending the use of Industry 4.0 as far as possible to all stages of production. Of course automation can partially fill labour shortage, which is, and will remain, a challenge for the years to come but we work to cultivate a positive perception of manufacturing in order to attract talented young people to join our team. We do this by creating a positive and inclusive working environment that is fundamental to our success and growth as a company.”
As well as the focus on its working environment, Leonix has also recently dedicated its efforts and research to develop a range of machined screws in response to ever changing market needs. “These items are the result of the synergy between the economic competitiveness of the cold forging process and the flexibility and precision of the turning process,” mentions Leonix. “We see a lot of potential in this area and will continue to conduct research into opportunities.”
Our highly experienced team is able to support customers’ in the development of bespoke screws...”
Leonix exports the majority of its products to the European market into a variety of industries including mechanical, building, petrochemical, nuclear, automotive and food.
“Due to being active in many industries, we are seeing that the supply chain continues to suffer significant issues after the Covid-19 pandemic. In 2024 we now also have additional challenges with rising fuel and energy costs, labour shortages, as well as the difficulties of global trade including marine freight cost increases due to tensions in the Red Sea. This has led many of our customers to review procurement policies and to source products in the regions where they are consumed.”
To answer that demand Leonix is responding with extremely fast delivery times, timely responses and excellent technical support.
“Our highly experienced team is able to support customers in the development of bespoke screws starting from a simple draft. Thanks to our know-how, consolidated knowledge of the sectors, as well as the flexibility of our production, we can develop the best combination of geometry, material, mechanical properties and surface treatments to bespoke performances.”
A focus on environmentally friendly production is also pushing companies to look closer to home. Leonix is therefore focusing on obtaining its ISO 14001 certification, which it aims to receive by the end of 2024. The company has also installed a 250kW photovoltaic system, as well as charging stations for electric vehicles for all employees. Leonix also utilises low impact stainless steel and purchases stainless steel produced from scrap.
“We believe that sustainability is our duty and our responsibility. We are constantly adopting the latest technologies for sustainable development and for the reduction of our environmental footprint,” concludes Leonix Fasteners Srl.
www.leonix.it
To deliver exceptional value to its customers, as well as maintain its high-quality standards, Bulloneria del Toce is continuing to invest in advanced technologies, enhance its service capabilities and explore new market opportunities.
With 40 years of experience in the production of carriage bolts, Bulloneria del Toce Srl is active in many industries including agricultural, mechanical, automotive as well as electrical components. The company comments: “Recently these markets have shown positive development with growing demand for high performance and quality solutions. The electrical components industry is benefiting from technological innovation and increasing efficiency needs; with the agricultural and earthmoving sectors experiencing growth due to the adoption of advanced technologies and the expansion of agricultural activities. As a reliable partner we therefore need to drive innovation and maintain our commitment to high-quality standards, enabling us to expand our offerings and strengthen our position in these key markets.”
Bulloneria del Toce currently supplies a wide range of screws, in Classes 4.8 – 12.9 and in materials such as stainless steel and aluminium, with multiple surface treatments to suit different applications, which also comply with DIN standards to meet custom specifications. Through expertise and know-how, the company also works closely with customers to identify and develop tailored fastening solutions.
“By leveraging our technical knowledge and flexibility in production, we can address specific needs and provide customised solutions. Our ability to quickly adapt to special requests and ensure timely deliveries enhances our added services for customers, helping them to find the best fastening solutions,” highlights the company.
Other additional services include producing small special batches with a quick turnaround time and maintaining a stock of standard products.
To ensure the consistent high-quality of its products the business also implements rigorous quality control processes throughout its production, which includes sourcing high grade materials, conducting comprehensive testing and adhering to strict manufacturing standards.
Bulloneria del Toce also recently invested in advanced packaging machinery to enhance the speed and quality of its deliveries. This investment enables the company to accelerate its production times, improve precision, as well as reduce operational costs through automation and efficiency.
“As we look to the future, the fastener market is expected to see increasing competition and to remain competitive companies must focus on enhancing customer service and providing exceptional value. We plan to continue to prioritise responsiveness and improved service quality, faster delivery times, as well as personalised support. By continuously adapting to market demands and investing in innovative solutions, we will strengthen our competitive position and capitalise on emerging opportunities.”
www.bulltoce.com
For over 30 years MICROMETAL Srl has been providing screws almost invisible to the naked eye – as little as 0.3mm in diameter – to a variety of industries worldwide, with a focus on accurate tight tolerances.
Using single spindle sliding head and CNC Swiss-type machines, MICROMETAL produces high-quality small diameter fasteners for industries including eyewear, automotive and electronics – where high precision components are needed.
The company outlines: “Our core business remains precision screws, but in recent years the custom sector has increased significantly, with customised items becoming the most requested by customers. When a customer has problems our technical office works closely with them to understand the product’s use and functionality to create modifications or new choices of materials or treatments, as well as develop new reliable, high-quality products.”
In order to maintain this high-quality, MICROMETAL focuses on the speed and efficiency of its production processes – with new machines including automated quality control for 100% selection. The company also has plans to expand its production area at the beginning of 2025.
“Every year we try to invest in new machines both for
production needs and to update the machine park. In the last two years we have invested nearly €600,000 in new machines in order to satisfy our customers,” comments MICROMETAL.
In 2023 MICROMETAL increased production by 15% compared to the previous year, exceeding 95 million pieces sold. With over 40 years of know-how, quality, and competence, the company is looking to the future to identify new markets and
Established in 1988, OMC – Wirelombardia designs and builds bespoke secondary operation machines for fasteners. Claire Aldridge, deputy editor, visited Olginate to find out how the company’s continuous investment in new projects and technologies is helping to create innovative solutions tailored to customers’ specific needs.
By focusing on flexibility and the specific needs of each individual customer, OMC is able to design and develop custom solutions to guarantee the best technological approach to production, creating tailor-made machines that enable maximum productivity and profitability, engineered primarily for the automotive sector.
OMC is known in the fastener industry for its various production lines including milling, turning and drilling, as well as high performance machines for the controlled calibration of threads –especially after surface coating. The company also produces machines for cold deformation, as well as a vast range of assembly machines.
Over time numerous machine models have been born and evolved to meet customer requirements. This includes the OMC 6 SP CN shank slotting machine with electronic cams for concrete fasteners. With its high productivity, and great versatility, the OMC 6 SP CN is designed for the execution of special milling operations for self scraping
Compact, solid, and sturdy, it is a machine driven by a high precision mechanical movement and, supported by electronic cams connected to the mechanical movements, enables the best machining profile to be assisted by interacting with the touchscreen panel. The machine also features a fast and efficient range change system to minimise production downtime, as well as being machine 4.0 ready on request.
“This fully automatic, high performance machine was created for high productivity to manage production costs and guarantee the best quality of the finished product,” highlights OMC – Wirelombardia Srl.
OMC continues: “The high-quality of our products has always been underlined by the knowledge and professionalism within the company after 37 years. Because of our knowledge of the complete production cycle of individual parts to be assembled, we are able to build effective and efficient machines designed and created ad-hoc to meet the specific production needs for every type of product. By working in a variety of industries we are able to acquire different technologies and transfer them from one sector to another, creating innovative solutions for our customers.”
Another of these innovative solutions includes the recently developed multi-tool cam lathe. The company explains: “Our focus is not just developing new machine models. We have also recently technologically revolutionised existing machine models to satisfy new applications requested by customers. These include the automatic assembler for structural bolts and the drilling machine for banjo screws.”
The OMC 14 DB drilling transfer for banjo bolts is a multi-station transfer with a compact design, specifically designed for the delicate
OMC is able to supply high-quality machines to satisfy the needs of an increasingly sophisticated and complex market...”
drilling operation on banjo screws in the automotive industry. Banjo screws have meticulous qualitative requirements and need to be entirely produced following a process without any flaws. The OMC 14 DB is able to perform precision drilling without any flaws and burrs both inside and outside the holes, guaranteeing 100% quality of the finished product.
Thanks to CNC technology, the production parameters can be adapted for any size and type of material to boost cycle times and the duration of cutting tools. A special monitoring system for tool wear also guarantees the best quality of the finished product and enables cost reduction. The OMC 14 DB also has a loading and unloading system in masked time; a fast tools change system; ‘real time’ monitoring of tool wear status for drilling units; as well as being machine 4.0 ready.
In order to further support its customers, OMC also offers remote and on-site assistance to guarantee a prompt and effective solution, which is supported by specialised technicians able to assist customers across the globe. The company outlines: “OMC machines are used in five continents and over 30 countries all around the world. We strongly believe that we are part of a production chain and to ensure the chain continues to run smoothly we have to adapt and look to the future. The know-how and flexibility of our company, as well as the benefits of being a family-owned business, enables us to face any challenges presented, as well as continue to invest.”
OMC has therefore invested in a new 2,000m 2 piece of land where a brand new production site will be constructed to increase its production capacity and enable the company to grow further, on both a technological and an organic and productive level; to help meet customer demand.
“Investments help us look to the future. We strongly believe that the greatest opportunities come to those best placed in the market, which is why we’re also focusing on sustainability too; to ensure we’re always ‘one step ahead’,” highlights the company. As part of this commitment, OMC recently received a certificate of recognition for 100% use of energy derived from renewable sources to cover all of the electricity needs for the new building. The new site will be equipped with solar and photovoltaic panels, and OMC will also be taking into account the choice of materials, as well as heating and cooling systems, for an optimum, sustainable work environment.
The company concludes: “The development of any idea must be supported by a technical study. The construction of valid and effective machinery starts from a sound idea and an excellent design. Using the most advanced design systems, as well as the best technology and components on the market, OMC is able to supply high-quality machines to satisfy the needs of an increasingly sophisticated and complex market.”
www.wirelombardia.com
Products produced by the OMC 14 DB
New shank slotting machine with electronic cams for CONCRETE FASTENERS
After almost thirty years, Tecfi is changing its brand and evolving by using a renewed and modern look to communicate its brand values –linked to the modernity, innovativeness, dynamism and the Italian heritage of the fixings manufacturer.
With a head office in Pastorano, to the north of Naples, Tecfi SpA is a specialist in the design and manufacturing of fixing systems and general fasteners. The rebranding initiative represents a milestone in the process of growth and innovation at the business, reflecting the company’s evolution and commitment to providing state of the art products to its global customer base.
“This is not a revolution, but an evolution of the brand,” states Tecfi. “Over the years, we have built a reputation for excellence in technological innovation and customer satisfaction. With the continued growth and expansion of our product portfolio – now comprising over 9,000 catalogue items – we have started a process of renewing our brand identity to better align with our values, vision and aspirations for the future.”
The new graphic element brings with it the current trends in visual design, which focus on simplification in all areas of visual communication – with a single primary colour represented by the new pictogram, associated with an evolved and modern text font and elements that recall the ‘Italian soul’ of the company.
As part of the project linked to the change in logo, Tecfi has also developed four brands representing the main product lines in the catalogue, including ‘Anchors for concrete’, ‘Nylon anchors’, ‘Fixing systems for roofing’ and ‘Screws and accessories for wood’. The graphics of the new product logos also have a strong link to the family heritage in terms of recognition with the new company brand.
To add to its rebranding process, Tecfi is also looking to increase its capacity by expanding its production range, which will enable it to produce larger and longer parts in Italy. “To become a strong industrial player within Europe we realised we needed to develop our capabilities as a business,” reports Tecfi. “That is why in 2012 we bought a large piece of land in an excellent logistical location (just off one of the exits of the A1, Italy’s main motorway, between Rome and Naples). On this land, we started to build a large industrial plant, which was completed in 2015 and enabled us to relocate the two
production processes of our company – metal stamping and plastic injection. We were also able to create a third production process, which involves the cold forming of wire and threading. Now, perfectly in-line with our long-term strategic planning, which was defined ten years ago, we are ready to take the next step in upgrading and expanding our production capacity, with a new industrial building of an additional 6,800m2 set to be added.”
The advantage to customers of the new production is that Tecfi will be able to produce more products in Italy and meet extra demand, as well as be more competitive when compared with Asian suppliers. “For customers around the world, who prefer European products, they will have access to a wider range of ‘Made in Italy’ products, even items normally produced only in the Far East,” underlines Tecfi.
Tecfi’s wide range of products includes roofing fixing products (screws, gaskets and accessories), heavy-duty anchors and concrete screws, chemical anchors, windows and frames fixing products (screws, anchors and accessories), insulation anchors, and light anchors, screws, structural and non-structural timber connectors and accessories, as well as general fasteners.
“With the exception of standard products that are manufactured according to the requirements of national/international standards, all our products are designed by the technical area of Tecfi, which actually consists of two laboratories,” mentions the company. “This includes the technical department for design and compliance, as well as the research, development and certification department for regulatory support to product design and certification.”
Both departments include a state of the art assessment laboratory, equipped with the most important certified facilities, which perform tests from the raw material to the finished product – through dimensional, mechanical, metallurgical, corrosion and scanning calorimetry tests. In addition, for the past nine years, Tecfi has equipped a new laboratory with modern facilities for static, dynamic and seismic load tests, for the research and development of anchors for use in cracked concrete and in seismic areas.
“Thanks to this unique technical area, we are able to guarantee our customers the continuous compliance of our products to established specifications, as well as the most updated certification for the safe use of our products in the worldwide construction market. Plus, we can work on continuous improvements to our product range, based on state of the art knowledge and certifications,” points out Tecfi.
From a technical point of view, Tecfi is also able to help designers in choosing the most suitable anchorage for their needs, either by consulting with them in their design or by helping them to use Tecfi’s calculation software for anchors – TADS (Tecfi Anchor
Design Software) – a CAD (Computer Aided Design) software for anchors. This software allows immediate verification of the most common cases of structural anchors, using simple and intuitive ‘real time’ 3D graphics, including seismic design for both C1 and C2 performance category anchors.
Tecfi can also offer a field engineering service, aimed primarily at end users, construction companies and those who use anchoring systems in their work on a daily basis. “The purpose of the on-site intervention is to help end users in the event of particular complications during the technical design and/or construction phase,” explains Tecfi.
“We can also offer a technical training service, thanks to our know-how in the sector, which includes organising theoretical and practical technical training sessions for customers, in order to spread knowledge of the most innovative fixing solutions and the most effective installation techniques. The training can take place at our headquarters or directly at customers’ premises.”
Tecfi is complementing these high-levels of performance and service with an effective logistic/shipping management system, which has always been a strength of the company –with over 8,000m 2 dedicated to warehouses.
“We have a storage capacity of over 20,000 pallets that is capable of managing a stock of seven months for Tecfi manufactured items and over 13 months for those produced by our partners,” highlights Tecfi. “This management requires high-levels of investment in order to guarantee continuous product availability to customers, even in situations of high demand and/or turbulence in the market – with a fulfilment rate in 2023 of 97% of order lines received.”
This is not a revolution, but an evolution of the brand… we have built a reputation for excellence in technological innovation and customer satisfaction.”
Another area that will influence the construction sector, as well as production processes and services, is sustainability requirements – with companies also required, at the same time, to comply with ESG (Environmental, Social, Governance) goals and to be ever faster in studying the different and complex cases that construction technology will face. This will lead to the demand for investment in these directions becoming even more important.
“Only manufacturing companies that are prepared to invest large amounts of resources in these goals will really be up to the demands of the market,” states Tecfi. “Our company has always paid great attention to the impact of its procedures/activities on the environment –with the company ISO 14001 certified since 2004. Furthermore, we have always had an ongoing commitment to our stakeholders in strictly adhering and complying to the idea of Corporate Social Responsibility (CSR), developing a business with a built-in philosophy to ensure that all our business processes are in accordance with national and international ethical standards. We strive to drastically limit the environmental impact of our operations and to provide an equally
professional commitment to consumers, employees, local communities and all other stakeholders.”
Tecfi continues: “This year we began the long and difficult journey of assessing and improving our sustainability position, in order to identify, predict and evaluate the potential ESG (and economic) impacts of our activities. We expect to have our first sustainability report in 2025. To this end, we have established a new department that will deal exclusively with ESG issues and train everyone in the company to improve our position. This approach will also be crucial for our business in the future, as we will soon be required to declare both the environmental and technical performance of our products.”
Tecfi concludes: “Our customers all over the world count on us as an industrial partner based in Europe that has a ‘Made in Italy’ seal for thousands of products. Thanks to our advanced R&D and assessment laboratory, we are able to keep our business and products in-line with the latest technologies within the construction sector. In addition, thanks to our huge stock, we have the ability to ship within 24 – 48 hours in Italy and 48 – 96 hours all over the world from order.”
www.tecfi.it
With a focus on quality, reliability, flexibility, as well as the importance of working closely with its customers, Claire Aldridge, deputy editor, visited Mavita to see how these goals are enabling the company to be a key international fastener supplier for a variety of industry sectors.
Mavita’s production range includes screws and bolts from 2mm – 12mm in diameter and in lengths from 4mm – 120mm in all types of carbon and stainless steel, with the possibility of providing all types of heat, galvanic and anti-unscrewing treatments. The company also cooperates closely with its customers – with 70% of its production range made up of special parts according to customers’ drawings.
Roberta Piccina, export department and commercial manager at Mavita Srl, highlights: “Paramount to our success is the close
relationship between our in-house technical department and the customer. Close cooperation as early as possible in a project is vital as it enables us to fully understand the customers’ needs and develop the best quality product possible. The small/medium size of our company is our strength, as we are able to build long-term relationships, as well as offer flexibility that can’t always be found in larger companies.”
By working closely with the customer, Mavita is also able to offer customers significant economic advantages. “If we are involved with the end customer as soon as possible, we can use our expertise and know-how to suggest cold pressed parts, instead of the turned parts the customer may have originally requested,” proudly states Roberta. It is this flexibility that has enabled Mavita to diversify its product range and expand into new market sectors, with the company now supplying products into the automotive, household appliance, electrical, electronic, mechanical construction, components, naval, building sectors, as well as the main national and European retailers.
“‘Made in Italy’ stands for a brand that represents everything associated with the Italian way of life – such as our history and cultural roots. Our manufacturing vocation is so appreciated throughout the world that globally Italian brands are perceived as a guarantee of quality, authenticity and style. To work with Mavita means to have a trustworthy, flexible supplier that provides quality in terms of both products and added services,” says Roberta.
Roberta continues: “Although quality has always been important in our industry, customer demands and expectations are changing in terms of specifications, cleanliness and now of course our carbon footprint. In order to satisfy our customers’ requirements we must adapt to meet the needs of the present generation without compromising those of the future generation. To reach our sustainable development goals, we have three important objectives – centrality of people, contribution to the ecological transition and sustainable product innovation.”
In order to meet these objectives, Mavita has recently invested in its infrastructure with a renovation of its heating system; investing in upgrading old machines; as well as the introduction of completely recyclable packaging for its products – combining respect for the environment, waste minimisation, packaging functionality and product protection. Furthermore, due to numerous retirements in the last few years, Mavita has experienced a true generational change in its production departments and has therefore invested in training courses for new employees.
“A part of sustainability is the quality of life in and outside the company; health and safety in the workplace; equal opportunities for professional growth and career development; as well as the respect for diversity and customer satisfaction. Our new colleagues have demonstrated they are capable and willing to learn and have improved our production capacity by creating a team capable of developing new projects in less time, and with fresh ideas,” states Roberta.
Roberta concludes: “Mavita has always embodied the fundamental values of ‘Made in Italy’ by putting people at the centre, both employees and customers, and we will continue to do so by maintaining our long-term relationships and building on the trust we’ve become renowned for.” www.mavita.it
Over the last three years Viteria Fusani has made significant investments within its plant and machinery, in order to continue supplying high-quality customised screws to the global market and underline its position as a strong and reliable partner.
Afamily business now in its 3 rd generation, Viteria Fusani is an ISO 9001 and IATF 16949 certified company that is able to supply customised high-quality screws in large quantities, both self-forming and self-tapping, as well as metric screws from M1.6 to M9 in diameter. In order to continue to meet the needs of its customers, and to grow its export potential, Viteria Fusani has made several key investments within the business since the Covid-19 pandemic.
“We have a long experience of producing customised screws and we are open to expanding our range based on clients’ requests,” states Viteria Fusani. “We are noticing that what clients really value at the moment is a reliable and stable working relationship. We are a family-owned business and these values reflect our distinguishing business practices and that is why we are investing in order to continue to provide the service and products our customers expect.”
Some of the key investments that Viteria Fusani has made include the installation of specific software to connect all the manufacturing processes with the management system, to comply with the 4.0 industry standards, as well as introduce a new assembly machine for screws and plastic washers –further developing its production capabilities and product range.
“The way in which we manufacture our screws requires a skilled work force, which means automation is not a major developing factor for our business at the moment,” highlights Viteria Fusani. “We have a very knowledgeable team and to ensure we keep the skills and experience within the business, we have been hiring young employees to work alongside our current more skilled and experienced staff members. This facilitates training, skills building and supports the natural turnover of employees. It also ensures the continuity of quality and customer care that are core values for our company.”
Viteria Fusani adds: “More and more clients are focused on finding reliable suppliers to build stable relationships. They also prefer to buy locally to secure business in view of potential geo-political situations, such as the Ukraine War, the Israel-Hamas conflict, etc. Post Covid-19 many distributors who used to work with Asia have now relocated part of their business closer to home. Thanks to our investments, we are able to meet these needs and provide 360° support, from monitoring order needs and production planning to offering technical support.”
In addition to the investments it has been making, Viteria Fusani has also been continuously updating and implementing initiatives to comply with environmental standards, including climate change and sustainability practices. “Sustainability is very important for our business and we are dedicated to continuously updating and implementing initiatives to comply with environmental standards
and requirements,” underlines Viteria Fusani. “We are a proud Italian company and we are strategically positioned in the heart of Europe, which means we can offer on time delivery with excellent customer service – as well as a friendly and professional approach. Thanks to our precision and cutting edge technology, we always guarantee the highest quality to customers – whilst constantly exploring new possibilities to expand our product range and reach new target markets.”
www.viteriafusani.it
Over the past decade Sariv has evolved from a sole producer of standard blind rivets to specialising in customised non standard parts, with the design and manufacture of custom parts now accounting for 80% of its turnover. The company is hoping to continue this trend and see custom parts account for 90% of its turnover in five years time.
With five distribution companies in eastern Europe –Czech Republic, Poland, Croatia, Slovakia and Russia –as well as through several distributors all around Europe, Sariv works with the most important brands in the market to provide customised solutions designed specifically for customers’ applications.
Sariv Srl explains: “Through working closely with these distributors, we have developed the know-how and development skills to move from the production of standard blind rivets and nuts to a wider portfolio of bespoke fastener solutions, created from scratch. Our increased capability to design dedicated solutions has enabled us to create brand new solutions, such as the new mechanical sealing products for high pressure applications that will be introduced to the market in 2025.”
The company designs and manufactures both standard and customised blind rivets, blind rivet nuts, and cold formed parts, from its Italian premises – where most of the treatments are managed internally, giving full control and guaranteeing the high-quality of its products. Sariv has also been investing heavily in traceability and digitalisation processes to apply the philosophy of Industry 4.0 to its production processes.
Sariv comments: “An automated company, in which all steps are digitised, has infinite production data available. This means all production systems can be optimised making processes more flexible and efficient, enabling the customer to obtain full traceability and ‘real time’ information on the status of processes and product availability, product engineering and customisation, production costs containment, reduction of consumption, as well as quality assurance.”
This quality assurance is important when supplying products to a variety of industries, where the trend for data has never been more prevalent, such as the automotive, construction, building, medical,
household, electronics, machinery and shipbuilding sectors. Sariv comments: “Supplying into a variety of industries means we must manage certain trends and be able to adapt quickly to them and remain a strong, reliable partner. Recently the automotive industry has been weak but our ability and focus on designing custom solutions has meant we have been able to answer customers’ changing needs and requirements with our reliable, high-quality solutions.”
Also key when supplying these sectors are the added quality requirements, which Sariv has answered by achieving IATF 16949, ISO 4001 and ISO 45001 certifications through a number of new initiatives across its production. These include paperless digitisation –electronic archiving of documents drastically reduces the unnecessary consumption of paper; renewable energy – Sariv now uses the energy produced by a photovoltaic system installed above the roof of its factory to partly power its production processes; optimising the shipment of goods to help reduce the pollution caused by means of transport; as well as the use of an innovative washing system that eliminates water from degreasing. The company is also planning additional investments in terms of Industry 5.0 to further reduce its environmental impact and carbon footprint to increase material recycling and energy reduction.
As well as improving its environmental impact, Sariv is also focused on creating a desirable, safe and clean working environment for its workers. “Several investments have been made in the field of automation but this is to support our operators, rather than to make up for a lack of manpower,” explains the company. “We believe it is essential to move operators from alienating and low added value jobs to operations where they can bring value, such as working on continuous improvement of setup operations; improving production and tooling efficiency and tooling lifetime; as well as managing data. Through these commitments, as well as our 30 years’ experience, Sariv is focusing on organic growth and looking ahead to possible collaborations with new products and thereby expanding into new markets.”
www.sariv.it
Ober® conceives, designs and builds every element of its tools at its Cadriano di Granarolo facility to ensure a local and short supply chain, guaranteeing its customers trusted, reliable and innovative products – 100% ‘Made in Italy'.
Customer satisfaction has been Ober®’s primary mission for over 60 years. The company designs and builds a range of portable compressed air tools, pneumatic motors, automated machinery, as well as systems for drilling, grinding, tapping, threading and screwing –including riveting tools with electronic pulling force – from its facility to the north of Bologna.
Through its expertise and knowledge, as well as continuous investments in research and development, Ober® is a trusted supplier of innovative products and services to key sectors including the automotive, construction and industrial sector.
“These key markets demand high-quality products, so we must be able to guarantee quality to our customers. ‘Made in Italy’ carries significant weight globally, representing products that are associated with high-quality and high specialisation. Therefore, when we say ‘Made in Italy’, we mean it – with every tool built in our Cadriano di Granarolo facility. Our quality assurance processes also involve rigorous testing, compliance with industry standards and
Customer satisfaction has been Ober®’s primary mission for over 60 years.”
traceability, as well as continuously evaluating market demands to explore opportunities to expand our product offerings,” highlights Andrea Belletti, general manager at Ober® SpA.
Andrea continues: “The fastening tool market has seen several developments over the past few years, including the increased adoption of digital technologies for supply chain management and a shift towards higher precision and process control fastening tools.
...when we say ‘Made in Italy’, we mean it –with every tool built in our Cadriano di Granarolo facility.”
As well as this, recent developments in the automotive industry have seen an increased demand for lightweight, performing and durable tools, which is why we have created tools specifically for riveting that ensure high-quality, precise results.”
“Future challenges include global supply chain disruptions, the rising threat of cyber attacks, as well as labour shortages that impact costs, production efficiency and increase costs – so we need to make sure we are reacting to these challenges,” mentions Andrea.
Ober® has therefore put a focus on attracting and retaining skilled workers. “Talent management plays a pivotal role in a company’s success, along with state of the art machinery and automation systems. Of course, automation enhances efficiency, reduces labour dependency and ensures consistent quality, but it is our aim to balance automation with retaining skilled workers and upskilling them for new roles,” points out Andrea. “As we look to the future, we must continue to monitor market trends and react accordingly to stay competitive. Manufacturing companies must embrace digitalisation and invest in skilled talent to confirm their role in the supply chain with efficient production, along with flexibility and seamless collaboration with suppliers and customers.”
www.ober.it
With more than 60 years expertise and experience – with a team of seasoned professionals and extensive knowledge, as well as young and motivated staff able to bring new ideas – E.CO is continuing to focus on customisation and reacting quickly to the specific needs of its customers.
Whether it’s a personalised product or a customised service package, E.CO strives to exceed expectations and meet customer requirements with high-quality fasteners and spare parts for various industries, including automotive. However, in recent years the company has noticed an increase in the requests from many other sectors due to a greater demand for a quality European supplier able to ensure continuity in sales, without delays caused by conflicts or other global market challenges.
“Customers can rely on E.CO throughout the entire production phase, from the research of the solution, based on the specific needs of
Customers can rely on E.CO throughout the entire production phase...”
the customer, to the creation of the mould, the production of the item and the packaging – which can also be personalised. As well as this, we are able to offer excellent customer support as we are able to assist customers in six different languages,” underlines E.CO Srl.
“The key factors of our products, as well as those of our company, are flexibility and adaptability. As the fastener market is constantly evolving, we see several trends shaping its future – including the increased demand for clips used in hybrid and electrical vehicles. We have reacted quickly to this with our wide range of products and keep in constant contact with our customers to ensure we can quickly react to market demands. As an Italian manufacturer we are perfectly placed to better understand the market and be the first to react.”
E.CO has also reacted to these market changes with recent investments in new specialised staff, training courses for current staff, as well as investments in new machinery and energy resources including the introduction of solar panels.
“The market is moving towards a respect for the environment, through production systems, materials, and energy sources, which all need to be eco-friendly. Companies that integrate these processes into their day-to-day practices will have a competitive edge and it’s our goal to provide high-quality, sustainable fastening solutions,” comments the company.
In order to do this, E.CO has introduced a number of eco-friendly projects including finding alternative solutions to save energy costs, reducing energy usage and waste in operations, as well as using eco-friendly processes and materials. The company has also utilised automation within several internal manufacturing, packaging and managerial procedures. A new automated IT system recently introduced has also helped to enhance productivity by speeding up workflows and reducing errors.
The company concludes: “We are proud to be identified with ‘Made in Italy’ since this concept has a significant value worldwide of tradition, design, innovation and craftsmanship, guaranteeing authenticity and adherence to Italy’s high-quality standards and raw materials. In five years time we see E.CO as the market leader in the production and distribution of fasteners – with an even wider range of customers and products. By focusing on technological innovation, sustainability and global expansion, we will have a bright future.”
www.eco-italia.com
For Specialinsert, ‘Made in Italy’ means the expert knowledge within a company, as well as the ability to discover, innovate and create, which is why the Italian manufacturer is continually investing in research and development to supply high-quality products worldwide.
Producing mechanical fastening systems for a wide variety of industries, from automotive to white goods, from aerospace to medical, Specialinsert Srl highlights: “The various sectors are realising that even a fastener system can make a difference, so greater quality, even at a higher price, in the long-term saves money and time. Therefore, in order to stay ‘one step ahead’ and answer customers’ needs, we must continue to look for new applications in strategic sectors for our products, as well as look at new trends in innovative materials.”
An example of this is Specialinsert’s range of titanium products, to answer lightweighting needs within the automotive industry. The company also has the ability to customise products, prototype and create solutions from scratch based on customers’ needs. Specialinsert explains: “Because of the level of product customisation we provide, an operator’s ability to equip a machine is fundamental, which is why we are focusing on employee training and development, as well as human resources. Of course automation is a big trend in the fastener industry at the moment and we must not ignore it. Specialinsert uses automated processes where we can guarantee a better way of working, but not as a replacement for manpower.”
In addition to customised products, pre-designing, and prototyping, Specialinsert also has strong pre and post sales services, as well as technical experts able to provide immediate assistance to its customers.
The company states: “As well as the added services we provide customers, Specialinsert’s strengths are in our knowledge, creativity and quality. We see quality as a continuous and structured growth path, which is applied throughout the entire company with UNI EN ISO 9001 and IATF certifications.”
Specialinsert concludes: “For over 50 years Specialinsert has been committed to providing the most innovative fastening systems in every industry and for every use. We have established ourselves as an innovative company that is constantly evolving to develop technologically advanced customised solutions, as well as offering cutting-edge services.”
www.specialinsert.it
Italian quality since 1974
Everyday Specialinsert® stands by railway passengers and employees, guaranteeing their comfort and safety on board.
We design and develop deformation threaded or self-locking inserts, quick release fastening systems, and self-tapping bushes for the railway sector, also
customized solutions. Innovative fasteners for every design requirement.
Contact our specialists to find the right product for your needs.
As the development of new, increasingly high performance materials and their applications become more widespread, Inoxdadi is offering a wide range of products from stainless steel nuts and bolts to brass, aluminium and some special alloys, as well as duplex, superalloys, and titanium, in order to meet customers’ needs.
Founded in 1973 for the production of stainless steel fasteners, Inoxdadi Srl supplies nuts, screws, bolts, washers, threaded rods, mechanical and chemical anchors, as well as other fasteners, in a wide range of ferrous and non-ferrous materials. A special range of solar fasteners is also available ex-stock.
Andrea Togni, export manager at Inoxdadi, explains: “The market is constantly changing and so are customer requirements. Service and stock availability have returned to being key factors after years of price being the only decision parameter – with customers wanting stock available 24/7. Geographic positioning has also returned to being important, due to the many international tensions and extreme weather/natural events. Customers are once again reconsidering the importance of having a local supplier.”
In order to satisfy customers’ ever changing requirements, Inoxdadi is continuing to invest in new machinery to increase its production capabilities. “We felt the need to expand our production range for cold stamped nuts, so that we could satisfy larger and larger slices of the market with products of undisputed quality, through the use of more technologically advanced machines,” Andrea points out. “Today we are able to produce cold pressed nuts up to 36mm across flat – in a variety of materials including the most ‘tough’ alloys, so as to fulfil all the needs of the market.”
Andrea adds: “Our fleet of machines now includes mostly six-station progressive presses. If you think that at the beginning, we had predominately three-station machines, it shows how today we are able to offer a product with high-quality characteristics and a wide variety of geometries. This allows us to compete with top European companies both technologically and in terms of product offerings. Our production sites also meet all standards regarding quality, product and external/ internal factory environment.”
From the quantitative point of view, for future developments, Inoxdadi also plans on building a new production site, for which a building lot adjacent to the current one has already been identified and purchased. Other key factors the company plans to focus on for future growth include
concentrating on product quality and the flexibility of its manufacturing operations, as well as supplementary services associated with sales.
As a company, Inoxdadi has always been attentive to the quality of products, which is the reason it has in-house quantitative departments that include technologically advanced equipment, such as spectrometers, quantometers, testing machines, sorting machines, as well as traditional laboratory machines (hardness testers, profile projectors, etc) – all helping to guarantee the highest quality standards.
“Besides quality, service is also key,” states Andrea. “Our customers come to us for the quality of our production, the high-quality of our products, and the added services we offer. This includes quick deliveries, medium and small deliveries, as well as flexibility. The efficiency and reliability of the production processes, and the high technology used, ensure the constant quality of Inoxdadi products, with complete traceability of the chemical physical characteristics of the products, thanks to the batch and casting numbers shown on each package.”
Thanks to Inoxdadi’s internal optical selection department, customers can be certain of receiving only compliant pieces, as well as the possibility of customised packaging including cartons, boxes, blisters, and the labelling of the products, in order to facilitate the distribution of the articles to the end user.
Finally, with regards to surface and/or heat treatments, Inoxdadi uses highly qualified external resources capable of responding to the many demands of the market. “Our service providers are the result of continuous research that has seen us work side by side with them for the past 51 years,” underlines Andrea. “We also have a quality system certification by DNV, according to the ISO 9001/2015 standard, and TÜV Rheinland ‘U-ZEICHEN’.”
www.inoxdadi.com
After the announcement that Novastone Capital Advisors acquired Mecavit Srl through an Italian special purpose vehicle, we spoke to Sales Director Giuseppe Verdoliva to see what’s in store for the Italian manufacturer and what the future holds.
How will the acquisition benefit Mecavit and its customers?
“Mecavit will continue to be a leading company in the industrial production of fasteners. With a 44 year history, Mecavit has established itself as a trusted name in the fastener manufacturing industry, known for its high-quality products. The company’s growth and reputation have been carefully nurtured by its partners over the years and the sellers will reinvest to ensure the business' continuity and future success.
Nicoletta Nutrito, an engineer and local resident with extensive experience in both national and international industries, will lead the company. Her vision is to maintain Mecavit’s high standards of quality while fostering innovation and growth. Our goal is to prioritise quality, technical expertise, and reliability, while expanding our offerings to new markets.
The Italian fastener market has swiftly adapted post Covid-19, with increased demand facing the post Covid-19 rebound in 2021 – 2022. Now we are starting to see a slowdown mainly due to the crisis in the European automotive sector and the overstock of the past years.
Over the past twenty years, Mecavit has strategically expanded its market share and invested heavily in cutting edge technology. Notably, we have installed photovoltaic panels on the roof to reduce energy costs and support our green initiatives. Additionally, we have implemented a new wire treatment plant to enhance production efficiency. These investments were made to boost our operational capabilities, ensuring that our customers receive high-quality products with improved reliability and performance. Mecavit will continue to collaborate closely with customers, offering co-design services for new components and applications –providing quality lab tailored solutions for our customers’ needs.
As former partners myself and Giorgio Grillini will continue to support the company alongside Mrs Nutrito and we are pleased to pass the management to a professional from our region who not only possesses the
necessary skills but also shares our values and is committed to ensuring growth and continuity.”
What are Mecavit’s key markets and how have they developed recently? What opportunities do you see?
“Mecavit produces standard and special fasteners from carbon steel 8.8, 10.9, 12.9 to stainless steel A2. We specialise in small diameter metric threads from M4 to M14, to DIN 912, DIN 7991, DIN 7984 and ISO 7380 with and without flange.
The automotive sector has always been our core market. However, the recent slowdown has pushed us to diversify our client portfolio, offering high-quality products to European distributors. We see opportunities in continuing to offer unified products manufactured with the same procedures as automotive products to distributors throughout Europe, sometimes to complement imported products. However, there are still very active markets that are now being concentrated on such as the appliances, electronics, construction and automation industries.
Within our key markets geographically across Europe, challenges such as CBAM and rising sea transport costs might prompt importers to shift towards European productions, presenting significant opportunities for us. The new management has therefore introduced fresh strategies to drive innovation as companies adapt to global challenges.”
What have been the challenges in the past two years, what impact have they had on your company and how have you managed the situation?
“Rising energy costs have been a significant challenge for all European producers, especially in Italy and Germany – where they have skyrocketed in a very short time. We mitigated this by installing state of the art solar
panels, which helped control costs and support our green initiatives, as well as align with our commitment to environmental sustainability.
The drive behind sustainability is also a big topic at the moment. Besides our solar panels, we are also focusing on recycling materials and energy conservation by reducing our environmental footprint through the recycling of materials and avoiding energy dispersion. This involves important heat recovery from the tempering oven, which ensures the heating of the entire plant in the winter months by partially recovering the emission of the heat produced into the atmosphere.”
“Mecavit’s dedication to quality, innovation, and sustainability, continues to position it as a leader in the fastener industry, ready to tackle future challenges and seize new opportunities. We aim to solidify our success with continued enthusiasm and dedication and have always positioned ourselves as a true business partner – not just a simple supplier – by fostering long-term customer loyalty and trust.
‘Made in Italy’ signifies superior quality, eco-friendly processes and meticulous craftsmanship, setting Mecavit apart from low cost competitors. Competing on cost while maintaining high standards is our ongoing challenge.”
With advancements in production technologies and materials improving the performance and
Bonotto Packaging Srl offers a comprehensive range of machinery for packaging in the hardware sector, with its product line-up including everything from small semi-automatic machines to fully automated turnkey lines.
“Our portfolio encompasses a wide variety of packaging solutions tailored to meet diverse needs,” explains Bonotto. “We provide machinery that caters to both small scale operations and large-scale automated systems. Whether it’s single machines for specific tasks or complete, integrated packaging lines, we ensure that our solutions cover the full spectrum of requirements in the hardware industry.”
In order to meet the developments within production technologies, the Italian manufacturer has also made significant investments in its marketing and digitalisation. “Our investments in marketing and digitalisation aim to enhance our online presence and streamline
our operations,” states Bonotto. “By adopting advanced digital tools and platforms, we are improving our ability to reach and engage with customers more effectively. This investment allows us to leverage data-driven insights to tailor our marketing strategies and enhance our overall visibility in the market.”
Bonotto has also invested within its customer support, by developing remote support systems and hiring highly specialised technical staff. “These measures enable us to respond promptly to customer inquiries and address their needs more efficiently,” mentions Bonotto. “Our remote support systems facilitate quicker resolutions to technical issues, while our expert team ensures that customers receive the highest level of service and assistance. Overall, these investments are designed to benefit our customers directly, as they are our top priority. By improving our digital capabilities and support services, we aim to provide exceptional value and satisfaction to our clients.”
Another vital aspect of Bonotto’s service is its quality assurance, with all the components of its products ‘Made in Italy’ – reflecting the company’s commitment to high-quality standards. “We are able to guarantee the quality of our machinery through rigorous testing and inspection processes,” underlines Bonotto. “Our equipment undergoes thorough testing and validation, often in the presence of the customer at our facility, to ensure it meets our exacting standards and performs reliably.”
This commitment to quality has seen Bonotto grow its market share, with the company strong in several key geographical markets, including Europe, southeast Asia, and North America. “We are also actively expanding into North Africa and Latin America, with both emerging markets presenting significant growth opportunities – due to their developing industrial sectors and increasing demand for high-quality products,” points out Bonotto. “As a dynamic and customer focused company, we are constantly evolving to better serve our clients. We are also continually expanding our range of solutions to address emerging needs and incorporating the latest technological advancements.”
Thanks to its commitment to ongoing development, and responsiveness to customer feedback, Bonotto is also able to ensure that its product portfolio remains current and comprehensive. “That is why we are able to provide a full range of high-quality packaging machinery for the hardware sector, with a strong focus on reliability and continuous improvement,” points out Bonotto. “Our dedication to evolving our product offerings ensures that we meet the changing needs of our customers.”
Bonotto concludes: “Through the investments and steps we have already taken as a business, we are in a strong position to continue growing – with the aim of becoming a leading reference point in the hardware packaging sector. We are also looking to continue to innovate with advanced packaging solutions and strengthen our relationships with clients worldwide. At the same time, our focus will remain on delivering high-quality, customised products and exceptional customer service, ensuring that we not only meet but exceed the expectations of our clients.”
Dell’Era Giuseppe is a historical Italian family run business, now in its seventh generation, specialising in the manufacture of mechanical industrial fasteners and fixings systems.
Recognised mostly for the production and distribution of UNI ISO 1234 (DIN 94) split pins, Dell’Era Giuseppe is able to supply a wide range of split pins, such as Beta/R-Clips cotter pins (DIN 11024 single and double ring), IEC 372 for insulators, Humpack split pins, linch pins, as well as other bent wire articles to customers’ drawings.
“Since the beginning of the 1900s we have been a company that bends metal wire, especially split pins,” explains Giulio Dell’Era, administrator at Dell’Era Giuseppe. “However, it was the production of split pins that has made us grow the most over the years, and made us a global company. However, we still don’t want to forget our production of stationery items linked to our brand Leone Dell’Era, which is very well known in Italy, as well as our production of straight pins and clips for shirts for the haberdashery market.”
In order to remain competitive within increasingly fierce markets, Dell’Era Giuseppe has always looked at the technological overhaul of its machinery, which is why every year the business invests in the purchase of new production machines or the complete revamping of old machinery –carried out internally.
“We can proudly state that we have an excellent mechanical workshop capable of transforming a limping machine into a technologically advanced and decidedly higher performing machine in terms of production – all clearly in accordance with increasingly stringent safety regulations,” outlines Giulio. “For instance, in 2021, we revamped the entire fleet of straight pin production machines, one of our historic productions for the haberdashery market, as well as several split pin production machines.”
Giulio continues: “We believe that automation is the only real solution to compete on the market today, which is why it is a goal that we are always pursuing. Technology is evolving at a pace that is difficult to follow, but it is our utmost commitment to invest as much as possible in it. Production machines capable of self-diagnosing; fast and fully automatic packaging machines; automated passages from production departments to packaging and stock departments; management software capable of analysing productivity and criticality of a department; managing warehouse stock based on statistical consumption data; these are some of the steps that we have taken as a company in order to continue to grow and meet the needs of our customers.”
Guaranteeing quality is also a vital aspect of the business, with Dell’Era Giuseppe’s operators following extremely procedural quality control processes, with the business also ISO 9001 certified. The company also has its own internal laboratory, which, using measuring and optical instruments, checks the samples coming from production and issues any certificate requested by the customer.
“Through our production, product range, employees, and quality control, we have grown into a global business, with 70% of our production exported to every part of the world – especially split pins that are sold in large tonnages throughout Europe,” points out Giulio. “Our desire is to expand further into markets where we only have a small presence, such as North and South America, Asia and Africa.”
Giulio adds: “Buying from us does not only mean buying a product, but also receiving a complete service – a tailor-made treatment based
on the specific needs of the customer. It is possible to buy any type of standard size, always available in stock for immediate delivery, as well as non-standard. Unlike our competitors, we also produce split pins in any material, such as low/medium carbon steels, stainless steels (AISI 304 and 316), copper, brass, aluminium, as well as other special materials such as duplex."
“We are also able to offer any surface treatment of any thickness, whether white, yellow, black, iridescent, zinc-nickel, lamellar electrolytic zinc plating, tinning or even painting. As well as this, there is the possibility of having different packaging options, so in addition to our resistant classic cardboard boxes, we can supply our products in bulk, with obvious savings for the customer, or in quantities per box –with personalised labels if requested.”
Giulio concludes: “What distinguishes us the most from our competitors is the quality of our products; the high probability of making immediate deliveries; and the possibility of having a direct and friendly relationship. As a business we pride ourselves on always being flexible and ready to find the best solution for our customers’ needs.”
www.delleragiuseppe.com
In order to stay competitive and meet customers’ demands, SIPA has extended its wide product offering to include a new range of gazebo multipurpose plates in 170 different sizes.
Founded in 1989 SIPA Srl was initially based on the production of plates and angles for hardware, with the company progressing to focus on a wide range of other items – before developing steel cutting and plastic moulding services for third parties.
Sipa comments: “We have always looked to grow as a business by adding new products that can provide opportunities in new or existing markets. These new additions underline that we are keen to grow where possible and the new product line allows us to satisfy a greater number of customers – few companies can boast of such a complete assortment,” explains SIPA.
The additions to its product line are made possible by the company’s steel cutting department housing 30 automatic presses, with capabilities from 50 – 250 tonnes for cutting sheet coils. The company also has its own plastic pressing department, which is composed of 11 automatic presses, ranging from 50 tonnes – 430 tonnes – for pressing plastic material from granules. An additional 250 tonne bicolour press also enables the use of two different materials or two different colours simultaneously.
“To add to this, we also have our mechanical workshop that consists of four work centres,
machines, one lathe, one radial drill, one microdrill, one erosion bath and two wire eroders,” points out SIPA. “Thanks to these departments, and the experience of our employees, we are able to develop a mould both for steel and plastic articles – from a simple idea, a sample, or a technical drawing. We can also produce parts using moulds from other firms. Additionally, we provide all the necessary maintenance during and after production, which enables us to supply excellent product quality combined with competitive prices.”
In addition, SIPA also has its own 7,000m 2 warehouse, which includes four automatic packaging lines for boxes and industrial packaging, as well as various manual packaging machines – to satisfy all customer demands. “Having the warehouse puts us in a strong position to handle the various market challenges that arise. For instance, thanks to our stocks of both raw materials and finished products, we have been able to fulfil orders to our customers very quickly,” adds SIPA. “The strength of our company is in the fact we are able to provide a 360° service with an excellent quality/price ratio and a fast delivery service.”
SIPA concludes: “As an Italian manufacturer we are synonymous with quality, service and competence. Furthermore, customers can count on our knowledge and know-how, gained from extensive experience in the markets, to provide the solutions and services customers’ demand. With this in mind, we will continue to consolidate our position as a producer and distributor in the domestic market, as well as look to grow our exports.”
www.sipaitalia.it
As an Italian manufacturer we are synonymous with quality, service and competence.”
Headquarterd in Turin, Italy, G&B Fissaggi is continuing its growth by developing new market opportunities, whilst maintaining the values, reliability and flexibility its customers have come to rely on. G&B Group now has six commercial offices in Europe and thanks to the acquisition of MAREFIX S.L – a Spanish screw producer based in Logroño – is further expanding its product range with the addition of MAREFIX screw products.
Initially specialising in the production of nylon plugs, G&B Fissaggi has been supplying products of the highest quality and certified performance to the European fixing market for over 40 years. Thanks to the flexibility of its production, the company is now a
manufacturer of nylon fixing systems, as well as steel and chemical anchors for many fields including ironmongery, hardware, construction building, engineering , electric, thermo-hydraulic and self service stores.
With the acquisition of MAREFIX, G&B Fissaggi is is able to offer its customers an even
wider range of products. MAREFIX® branded products by G&B Group are now part of a complete line of high-quality, versatile fasteners and accessories for applications on steel, aluminium, wood, and plasterboard, for the hardware and construction sectors. Full details and product specifications are available in G&B’s catalogue in the Geto-Fix screws section.
“Our goal is to continue to guarantee our customers high-level products and services with the highest quality and maximum versatility,” explains Enrico Galeasso, CEO at G&B Fissaggi.
“Our competitive strength will be further consolidated by the seriousness and experience of MAREFIX – a reference point for the screws industry in the Spanish market. We are confident that thanks to this new acquisition, we will be able to satisfy every fastener and screw need, with an increasingly global approach.”
To maintain this global presence, G&B Group has commercial offices in Germany, Spain, Belgium, France, northern Europe and the UK (with a warehouse in Sheffield), as well as its Italian headquarters in Turin, which has recently been expanded by over 3,500m 2 to ensure a large stock of products are readily available. The company has also recently invested in its technical, marketing and sales department to strengthen its knowledge and know-how.
Even during the last two years of market difficulties, due to international crises and rising energy costs, G&B Fissaggi continues to work on the research and development of new products to offer a better service to its customers, both in Italy and in Europe. This includes the introduction of the GETO PLUS TMK SCREWS CE OPT 1 self-threading anchor for structural fixings, with CE Option 1 for applications in seismic areas. With a new thread for fastener installation and high performance, the GETO PLUS TMK SCREWS CE OPT 1 ensures secure fixing, even close to the edges of the support, as well as being suitable for high-loads with the special thread geometry enabling extreme tightness in concrete.
Other recent product innovations include the new GEBOFIX PRO SISMIK CE OPT 1 bonded anchor, as well as the new bonded anchor XTR EXTREME HYBRID CE OPZ 1, both of which are CE Option 1 approved for applications in seismic areas.
Furthermore, G&B Fissaggi has developed the new version of its calculation software G&B Calculation Suite – designed to calculate and identify the most suitable anchor to satisfy all geometric and load conditions.
Alongside its wide product portfolio, the company has also been committed to the very highest quality standards. “The challenges of a growing and highly competitive market such as construction fixing products, within both the Italian and European markets, has led to a thorough and more responsible use of resources in our company in order to achieve and control the total quality in every area of the supply chain –from production to sales, to service, with a growing sensitivity towards the respect of the environment and the use of recyclable packaging,” comments Enrico. “We are very proud of the quality we can provide customers, which is underlined by our production process being certified to DNV ISO 9001.”
www.gebfissaggi.com
Here Jody Brugola, president at Brugola OEB, discusses developments, investments and strategies within the leading Italian manufacturer. He also provides an overview and insight into the wider automotive sector for which his business is synonymous.
In the past two years the fastener market has seen significant evolution. The demand for more sophisticated and customised solutions has increased, driven mainly by the ongoing transition in the automotive world. Fastening components continue to be essential regardless of the type of engine, be it electric, internal combustion or hybrid.
At Brugola OEB we have invested heavily in a strategic expansion plan over recent years, which includes the purchase of new machinery, expansion of production facilities, an increase in human resources, as well as technological investments. These developments have been driven by our desire to continue our growth path. We have a concrete goal to exceed €200 million in revenue whilst continuing to offer our customers excellent and cutting edge products.
Brugola OEB has always been a world leader in the production of critical fasteners for internal combustion engines. In fact, we are able to produce any type of screw or fastening element for the automotive sector, regardless of the type of engine. Every one of our components is designed for high performance applications and the quality of our products is ensured through rigorous controls at all stages of production, from the procurement of raw materials to the final inspection of the finished product. To expand our portfolio, we have also invested in the development of special products that require a high-level of technical know-how and an in-depth knowledge of the automotive market. I see a growing demand for customised and sustainable solutions with a focus on technological innovation. That is why our company plans to continuously invest in research and development to anticipate these trends and offer products that meet new market needs.
Whilst the automotive sector is currently undergoing a significant transition towards electric mobility, our goal remains bringing excellent products to the market – meeting customer demands, as well as providing technologically advanced solutions. To do this we focus on a ‘four-handed’ collaboration with the customer, which involves joint product development – working closely with customers to understand their specific needs and develop tailored solutions. This approach allows us to provide not only products, but also added value through collaborative innovation.
Manufacturing companies need to undergo a significant transformation to remain competitive in the future. A crucial element of this transformation is preserving the skills and know-how acquired over the years. This is essential because, despite technological advancement and automation, human labour remains indispensable in many cases. Finding people willing to work in manufacturing companies is an increasing challenge. Skilled labour is essential in maintaining high standards of quality and innovation. To address this challenge, companies need to invest in continuous training programmes and work closely with technical institutes and universities to attract young talent and train the next generation of skilled workers.
We have a concrete goal to exceed €200 million in revenue whilst continuing to offer our customers excellent and cutting edge products.”
I believe that in our sector, we can always move towards new forms of automation, but the human component will remain a key and fundamental element for the production of fasteners. I do not believe they can be in contrast; on the contrary, automation and new technologies can support creating better working conditions and increasing resource efficiency.
Another key transformation companies will need to make is regarding sustainability, which is already a fundamental pillar for Brugola OEB. For several years we have been committed to a series of projects aimed at improving energy efficiency and offsetting CO 2 emissions. Our goal is ambitious; to achieve carbon neutrality by 2035 and record a 70% reduction in emissions compared to 2019 levels through offsetting and reduction activities.
To do this we are engaged in various initiatives to reduce environmental impact, such as reusing oils used in our production process, as well as reducing plastic and using LED lighting. Additionally, we have been collaborating with Forever Bambù, a European leader in giant bamboo forests in Italy, for several years. Currently, we have purchased six hectares of giant bamboo, which will soon become sixteen hectares. Each hectare has an absorption capacity of 260 tonnes of CO 2
Another area in which we have taken measures is in regard to the increasing energy costs, which have been a major factor in recent years. We have looked to improve energy efficiency, as well as optimise our production process and reduce consumption. In the future, I expect energy costs to remain volatile, so we will continue to invest in sustainable solutions and the optimisation of our production processes.
At Brugola we are proud to be an Italian manufacturer, for us ‘Made in Italy’ represents quality, innovation, and tradition, which reflects our commitment to excellence. Italian manufacturing also stands out for its ability to combine tradition and innovation, a quality that allows us
Another key transformation companies will need to make is regarding sustainability, which is already a fundamental pillar for Brugola OEB.”
to offer unique and high-quality products that set us apart from global competition. Brugola’s story is that of a company that has created a revolutionary and iconic product, known by the name of its inventor, with a precise and important constant – the strong ‘Made in Italy’ identity that has not changed from 1926 to today. Skills, production, know-how and resources have always been 100% ‘Made in Italy’ – with the aim of pursuing excellence through innovation and enhancing our territory.
We are also a company that is going against the trend of the fastener sector, with 2024 a very important year for us. In April 2024, the company ownership returned to 100% Brugola family ownership through the repurchase of minority shares. This is a fundamental milestone both for the company and the family. This is a gesture I felt the duty and desire to accomplish in honour of my father and grandfather, who dedicated passion and commitment to building this company. Of course, we do not intend to stop here. Brugola is always oriented towards progress and we have numerous goals to pursue. Thanks to this operation, which occurred at a strategic moment, we can continue to adhere to our expansion and growth plan with the intent to meet market demand with excellent, innovative and tailored products for our customers – who also benefit from high-quality products, dedicated technical support and customised solutions.
www.brugola.com
Turned parts manufacturer Colombo Giovanni & Figli is entering new markets with the acquisition of one of the largest brass turned parts manufacturers in Italy and Europe – OMMES Srl. Deputy Editor Claire Aldridge visited the company in Samolaco, Italy, to find out how the acquisition is creating important synergies to benefit both company’s customers.
Colombo Giovanni & Figli Srl currently produces high-quality and precision turned parts in steel, special steel, stainless steel, aluminium and other alloys according to customer drawings for the automotive industry, oil and gas, hydraulic, pneumatic, as well as goods and other mechanical appliance industries. Its production department is equipped with the latest generation multi spindles automatic lathes, 6 and 8 spindles with spindle stopper with a workable diameter from 4mm – 52mm, all equipped with automatic bar loaders from Pietro Cucchi SpA. Its turnover is split 50% in Italy and 50% in Europe, particularly in Germany.
Gianluca Colombo, owner of Colombo Giovanni & Figli, explains: “This acquisition of OMMES will enable Colombo to enter the brass market, with OMMES exporting nearly 90% of its production to industries all over the world. As markets change, the current challenge faced by companies is to be present across a number of industries worldwide and adapt quickly to customer requirements. This acquisition enables us to do just that and stay present in our industries, as well as enter new ones.”
OMMES produces 200,000 brass turned parts a day for a variety of industries including electromechanics, electronics, hot water and heating, automotive, valves, industrial machines, as well as compressed air.
Gianluca continues: “'Made in Italy' stands for technology, fair prices, flexibility and most importantly quality, which is taken very seriously at Colombo with online SPCs on all production machines, as well as special cameras to perform 100% sorting. It was important, therefore, that OMMES had a quality guarantee too, in order to align with our values.”
Thanks to modern technology equipping each machine with a touchscreen, it is possible for OMMES to monitor its entire production process, from raw material to finished product. The company also has 25 technologically advanced Shüette machines and uses only high-quality raw material. In recent years, OMMES has invested even further in product quality with a certification programme to guarantee the control of machines, with the company also certified according to ISO 9000 and ISO 14000.
Gianluca concludes: “With this new acquisition, Colombo Giovanni & Figli continues to be a strategic partner and supplier for high-quality turned parts, with a top of the range service focused on growing and improving quality and services to a wider and more diverse market.”
www.colombotorneria.it
As markets change, the current challenge faced by companies is to be present across a number of industries worldwide...”
Bontempi VIBO has launched a new five year strategic plan that, added to the major investments just completed and ongoing within the company, will allow it to double its production capacity by 2028. With this growth focused on maintaining the correct balance between quality, service and price – features that have always been distinctive for VIBO.
Raoul Bontempi, CEO of Bontempi VIBO SpA, explains: “As a company we want to grow and to do this we have to further develop our production and the way we manage each stage of the process. This has led us to make investments in key aspects of our processes and to make strategic acquisitions to increase our product portfolio. With the acquisition of first FRAM and then Mi.Me.Af., our production range has expanded significantly – now ranging from 2.5mm –64mm in diameter and up to 1m in length.’
A prime example of this investment plan is the new heat treatment line at the company’s southern plant. “Two years ago we built a building adjacent to our southern plant
and in the new building we introduced new packaging machinery, as well as adding an electrolytic galvanising line, so that we could also bring this process in-house to be able to reduce production lead times and increase product quality,” mentions Raoul.
Raoul continues: ‘All these investments are not aimed at saving money, but were made to help us save time during the production process and ensure a key aspect of the process, which is crucial in today’s market.”
In addition to the investments undertaken with the third heat treatment line, Bontempi VIBO has also invested in new machinery that has allowed the company to double its screw production from M5 to M12 already this year. “These new machines, which have allowed us
to increase our capacity, have also enabled us to introduce new product ranges,” explains Raoul. “In addition, we have also introduced two-shot stamping machines for smaller screws.”
Raoul adds: “We have also built a new compact warehouse in Calabritto, which will add another 1,000 pallets to our storage capacity. Just a few years ago we doubled our central warehouse to 18,000 pallet spaces, but with the addition of the compact warehouse we can provide a more efficient service to customers – by shipping full truckloads from the south.”
Bontempi VIBO also has further investments planned, including the doubling of its plant in Rodengo-Saiano. “In recent years we have made very important investments and this will continue in the future,” says Vittoriano Calomeni, general manager of Bontempi VIBO. ”By the end of the year we will approve investments to double our in Rodengo-Saiano plant. We will also order a new heat treatment line and some additional moulding machines. At the end of this investment period, we will be able to produce 45,000 tonnes of screws, doubling the production capacity of the last ten years by 2026.”
In addition to its production capacities, Bontempi VIBO has sought to develop its product range to meet customer needs. Pietro Bontempi, head of new business development at Bontempi VIBO, and son of Raoul, focuses on serving new customers and selling the new products that are introduced to the range. “We have such a wide range that sometimes our customers are not fully aware of what we can offer. For example, we are the only manufacturer in Europe to offer standard stainless steel fasteners. We can supply special hot forged screws from diameter
M20 – M64 in diameter – in lengths up to 1m and special items with Mi.Me.Af (which is IATF certified). We are therefore able to supply our product range, standard and special, from M3 – M64.”
Pietro continues: “Another range we are investing in is the production of studs, which was introduced to the company after the integration of the FRAM business. Again, the range is available from diameter M20 – M64 in diameter and we are keen to grow this market in the future. As a company, we are always attentive to customer needs and plan to introduce several more product lines later this year, which will be available in all sizes.”
By further increasing its capabilities and product range, Bontempi VIBO intends to increase the amount of purchases from existing customers and attract new customers. “We want to be the first supplier every bolt distributor in Europe thinks of when they want to buy a bolt. That is our goal,” says Raoul. “We are confident that in the future many European distributors will choose us to avoid the risks associated with imports and other hidden costs (CBAM and other environmental issues). We are a very reliable European supplier for our customers and there will always be a need for reliable European suppliers in the market.”
A key part of Bontempi VIBO ’s business is its philosophy to serve only distribution customers, without reaching the end user. “This is a very important statement for us,” Vittoriano emphasises. “We guarantee our customers that we will never compete with them in the acquisition of an end customer. Some customers have been working with us for more than 60 years and know that we can provide a full range of products and services to meet every need. This allows us to be a partner for the largest distributors.”
“As we have seen from the trade war between China and the USA, with both introducing duties on a wide range of incoming products, it is important that in a global market we all compete on the same level.
We believe that the EU will soon have to start thinking and acting in the same way, and with our investments we are ready to meet the needs of the market.”
After so much investment within the company, it was necessary for Bontempi VIBO to review its business plan, production and future objectives, as well as introduce a reorganisation of its management and sales department.
Paolo Cola, Bontempi VIBO ’s sales director, explains: “Through the continuous process of expanding our product range, we want to satisfy all our customers’ needs for bolts, including all the most popular categories and families. A key aspect in doing this is people, who are one of the most important resources within the company – because it is people who make it possible to achieve success.”
Paolo continues: “With this in mind, we have redesigned Bontempi VIBO’s approach from a managerial point of view. We strongly believe that to reach 45,000 tonnes in the next three years, we need every employee to act like a manager, so we are trying to transform the people we have in the office to act and think like managers. If you give people responsibility, they are happier doing their job; they also know what they have to do and they have the confidence to go and do it.”
Raoul concludes: “All the investments we have made in new buildings, new machinery, new products, and reorganisation, have been made with our own funds. It is my resources, my people, my family, my suppliers and my customers. We are on a journey and we want our employees, suppliers and customers to follow us and have confidence in Bontempi VIBO. We also make no secret of the fact that we always keep our eyes open for a possible takeover.”
www.vibo.com
A prime example of this investment plan is the new heat treatment line at the company’s southern plant.”
This year is an important milestone for Tecno Impianti, marking 45 years of supplying wire drawing machines and uncoilers/ pre-feeders to the fastener industry – accumulating considerable experience in the wire drawing machine sector.
Established in 1979, Tecno Impianti’s main machine range is it’s in-line wire drawers, which can be installed before cold headers, as well as chain, straightening, and cutting machines, for resizing the wire to a desired final diameter. Over the last 45 years, Tecno Impianti has manufactured and sold over 2,500 in-line wire drawers, with wire diameters ranging from 1mm up to 37mm.
The Italian company has also created a wide range of products for the fastener sector, including vertical uncoilers that can be supplied with or without motor, for uncoiling small diameter wire on spools or wire carriers; power driven horizontal uncoilers that can be utilised for uncoiling medium-big diameter wires and feed them directly into a cold header or wire drawer, in a pre-straightened form; as well as pre-feeders that are needed for bringing the wire from vertical uncoilers to cold headers or wire drawers.
“Everything is designed in-house, from the manufacturing of parts or components to the assembly of the machines, guaranteeing a high-quality standard, which Tecno Impianti Srl has become renowned for,” underlines the company. “We have also started to see a trend in our customers wanting more added value brought by new machines, so to answer these needs we recently invested in new designing software so our technical office can offer newer solutions and more complex machines.”
Tecno Impianti also works closely with its customers’ to understand their specific requirements. “To meet with a customer and understand their challenges and needs is so important in order to find the right solution and improving their production. There’s a trend in Europe to utilise old machines and it is our goal to supply machines that work in a safer and more efficient way,” explains the company. Tecno Impianti also supplies machines to the construction industry and to other customers working in the wire industry, such as wire drawing machines for production of CO 2 wire and redrawing of galvanised wire; cold rolling lines for production of smooth or ribbed wire for electro-welded mesh coilers; as well as vertical and horizontal spoolers.
Looking to the future, Tecno Impianti will continue to meet customers’ needs by providing tailor-made solutions. “When customers buy a Tecno Impianti machine, they know that it is coming from a company with years of experience and great passion for what they are doing. It is important, in this fast changing world, that we do not forget where we come from and what our roots are: Quality, innovation and attention to detail,” the company concludes. www.tecnoimpianti-italy.com
In the Italian industrial landscape, a new frontier of innovation is emerging – Industry 5.0. In this context, Fastdev, a software specialist supplying ERP and MES systems to the fastener industry, is developing a revolutionary solution to integrate aspects of 5.0 into its systems that can improve the operational activities of manufacturing companies.
The solution proposed by Fastdev was born from a path started over twenty years ago, aimed at promoting the culture of data and automation in the fastener industry.
Fastdev’s ERP and MES not only addresses manufacturing needs, but also embraces the importance of sustainability and energy efficiency, offering unprecedented competitive advantages and operational improvements. Compared to 4.0, Innovation 5.0 aims to support the development of Italian companies by reducing the overall energy consumption of the production structure by at least 3%; or alternatively guarantee energy savings of at least 5% on the chosen process with a collection and analysis of energy data.
This holistic approach enables companies to monitor the efficiency of their operations in ‘real time’, in order to identify areas for improvement in both energy production and use. With accurate and timely data, manufacturing companies can optimise production processes, reduce waste and improve sustainability.
The ERP and MES systems are also designed to transform the data collected into strategic information, supporting managers in business decisions. With advanced analytics, companies can predict trends, identify improvement opportunities and make informed decisions to improve competitiveness and operational efficiency. The ability to understand and use energy data also enables targeted interventions, reducing costs and environmental impacts, as well as increasing competitive advantage.
Fastdev is not only able to provide cutting edge technological tools, it is also committed to training companies on the importance of data management and reducing energy consumption. Through dedicated training programmes, manufacturing companies can acquire the skills necessary to fully exploit the potential of ERP and MES systems.
As the demand for nails continues to increase post Covid-19, titibi® is focusing on the high-quality and flexibility of its products, as well as its aftersales service, to ensure its customers are in expert hands.
titibi® explains: “In order to meet this demand we have had to equip ourselves by investing in both resources and processes. We have therefore increased production and packaging hours, as well as hired new staff, in order to supply our products quickly.”
For more than 50 years titibi ® has specialised in the production of hardened steel nails, using cutting edge processes to guarantee the highest quality. “We are always attentive to new markets and the possibility of producing something new and innovative. Many of our customers need special nails made according to their design, so it is always a new challenge to be able to create something new and provide a new product,” states titibi®
The company is able to provide these customised solutions thanks to its in-house production facilities where it produces all the spare parts and consumables for its machinery. This enables titibi® to be able to produce components and modify its production quickly, something that its customers have come to rely on.
“Being a manufacturing company is always a challenge – you have to be flexible in order to be competitive, but you must also navigate market trends and geopolitical impacts. One example of this is the cost of electricity, which is now approximately three times higher than it was in 2019. Production processes therefore need to be more efficient to reduce the impact of this
increase – but it will never fully be enough to offset the cost. In addition, raw materials prices have also meant that the price of the final product has risen – forcing us, as well as all manufacturing companies, to adapt the final sales price,” comments titibi®
To help with this competitiveness, titibi® is focusing on automation with automatic production processes reducing human error, reducing lead times, as well as increasing production.
“As a manufacturer, you have to concentrate on the production of the right items, at the right time, as well as constantly innovating to offer something new to satisfy customers’ needs. titibi® is always aiming to create products and equipment that allow operators to speed up fixing times and therefore complete projects in less time,” adds the company.
Examples of this include titibi®’s automatic fastening machines, including the ISOLFIXA wall insulation gas nailer, which titibi® points out enables users to take four times less time than usual fastening systems –easily, safely and effortlessly; as well as the PRIMA concrete nailer, designed with a safeguard grip and magazine capacity of 40 nails.
www.titibi.com
Specialising in the production of chemical anchors since 1962, Bossong SpA is continuing its position as a reference point for chemical anchoring with the introduction of the BCR HYBRID chemical anchor with two ETA accreditations (ETA – 15/0559 and ETA – 24/0016).
Designed to meet the current needs of markets that require fast, universal, multipurpose and environmentally certified products, the BCR HYBRID is a universal bi-component hybrid chemical anchor, without styrene, for medium/heavy loads and applications in concrete and masonry. The product also has CE Marking.
The first ETA (ETA – 15/0559) covers the BCR HYBRID according to EAD-330499 for non-cracked concrete, Option 7, in diameters from M8 – M24, and for bars with improved adhesion from 8mm – 16mm. As well as this, the BCR HYBRID is covered under Option 1 –performance for cracked concrete, for bars M10, M12, M14 and M16.
The product also has seismic qualification according to EAD-330499 and is qualified in seismic category C1 for diameters M12 – M16 and seismic category C2 for M12 diameter.
Approved for fixings with a variable anchorage depth, the BCR HYBRID provides high flexibility to the designer, as well as a maximum anchorage depth of up to twenty times the nominal diameter of the threaded rod – with reduced edge distances enabling its use even in structural elements with limited dimensions. The anchor can be used in dry, wet and flooded concrete, as the hardening reaction of the product even occurs in the presence of water.
The second ETA (ETA – 24/0016) covers the BCR HYBRID according to EAD-330076 for fixings on solid and hollow masonry under static action. Specifically, the product is certified for applications on eight different masonry blocks, including solid masonry
Approved for fixings with a variable anchorage depth, the BCR HYBRID provides high flexibility to the designer...”
blocks, hollow masonry and AAC (autoclaved aerated concrete) blocks.
The threaded rods covered by the certification range from M8 – M16 in diameter, while the plastic cages for use on hollow bricks range from diameter GC 12mm x 60mm for M8 rods to cages GC 15mm x 135mm or GC 20mm x 85mm for threaded bars M10 – M12. Also, for use on solid masonry, there are performances for bars with improved adhesion, with diameters 8mm – 12mm, which follow typical applications of reinforcement on load-bearing masonry, adjustments and reinforcements with reinforced plaster.
The BCR HYBRID product is also undergoing testing to obtain a third ETA-CE certification for applications on solid brick masonry under seismic action. Furthermore,
the product is equipped with an Environmental Product Declaration (EPD), which is currently in high demand – especially in public works and large construction sites where environmental product aspects are strongly considered. Thanks to the absence of styrene, it can also be used in enclosed environments. The resin, due to its high adhesion value and ease of penetration into porosities and voids, also enables secure fixing without expansion and therefore without tension in the base material during installation. The resin and hardener only mix during extrusion by passing the product through the dedicated mixer – no pre-mixing is required. It can also be used as a repair and filling compound.
www.bossong.com
Amidst geopolitical tensions and the challenges of an uncontrollable market, Kilton is helping to ‘bring manufacturing home’ with a focus on quality products and a flexible service.
Since it was founded in 1976, Kilton has produced both standard and special fasteners based on its customers’ needs, especially when it comes to the increasingly varied and challenging applications they face. Kilton Srl explains: “We actively collaborate with companies across all sectors and markets. From technical consultancy to the study of the cost-effectiveness of a process, we work together with our customers to propose credible solutions for a variety of applications. Our passion is responding to customers’ needs and this brings us new opportunities to offer savings in both product management and inventory management.”
Kilton’s flexibility and commitment to meeting the requirements of its customers, regardless of how niche or specialist, has enabled it to stand out from its competitors. “When we started our business there was a lot of competition within the European market and we quickly decided to focus on ad hoc solutions and meeting small quantity requirements. Then, when the market moved towards Asia, we dedicated ourselves to offering niche standard products – available from stock. When customers find themselves without material, such as in 2021/22, they realised the risks of sourcing products from the other side of the world,” underlines Kilton. “By focusing on these areas, as well as developing the services we can provide customers, we have been able to establish ourselves as a highly valued manufacturer based in Europe.”
Kilton’s operations are located in the south of Milan, with the business running across three separate units – covering 5,000m 2. “Today, all of our machinery uses advance systems and we are able to control every process during production to minimise the chances of errors or waste. Thanks to the technical expertise we have within the business, we are able to produce high-quality products that reach design and production standards in compliance with international regulations.”
Kilton continues: “Quality and reliability are keywords for us. We have never cut corners or saved on raw material, equipment or contractors. Kilton is a solid reliable partner that has reached high design and production standards in compliance with Italian and international regulations. For this reason we also have customers beyond the borders of the European market. Having Kilton in your production chain means having a technical partner that is able to offer simple and effective solutions that can be produced and stored within Europe for quick delivery.”
“Saying ‘Made in Italy’ today can sometimes mean ‘assembled in Italy’. For Kilton, ‘Made in Italy’ means 100% ‘Made in Italy’, as well as a belief in our country, our people and in future generations. We are, of course, in the world of robots but specialised labour is still needed to assemble a moulding or threading machine. In our sector, secondary processes have been automated, more for image than for real necessity and it must be remembered that automation also causes the loss of skills and abilities.”
Kilton concludes: “We are looking ahead making sure not to be left behind. Customers need to be able to live without the anxiety of products not arriving for a variety of reasons. Kilton is the solution, with sales and technical staff available to answer every industry need.”
Dell’Era Ermanno e Figlio, an Italian player within the production of cold forged metric screws, has made the reliable and consistent supply of high-quality products its main focus, along with an unwavering commitment to innovation and sustainability.
Established in 1924, and based in Valmadrera, Dell’Era Ermanno e Figlio Srl is a fundamental part of the regional and national industry, embodying the principles of solidity not only in its financial condition, but as an overall approach to business management – providing it with adaptability and proactivity. “In the past two years, the market has been characterised by global challenges, as well as instability and economic uncertainty caused by conflicts and financial weakness,” reports Owner Paolo Dell’Era.
“Throughout this period our business’ resilience and innovation have proved even more essential.”
Dell‘Era’s policy is to combine the right focus on innovation, development, and competitiveness, with sustainability and respect for the environment. The company does this through investments in advanced technologies, as well as the continuous search for eco-friendly solutions and a commitment to corporate social responsibility, which are just some of the aspects that enable the company to stand out in a competitive market.
“As a business we have built solid foundations on which we can thrive, expand, and innovate, despite global economic fluctuations. This has been essential for our continuous economic growth,” explains Paolo.
“An example of this is the recently implemented investments into a new management software for matching all the data involved in the SEMs production system and the OEE performance index.”
As a business we have built
foundations on which the company can thrive, expand and
Another key success of Dell’Era is its higher quality standard levels, with the quality assured by the company’s ISO 9001:2015 and IATF 16949:2016 certified management systems for the automotive industry. In addition, periodic inspections are applied at each production stage, thus ensuring the traceability of each lot. Plus, a laboratory with the most innovative control technologies is used to check processes and products.
“As a business we have also paid attention to our human resources, with the high skill level and expertise of our employees playing an essential role in guaranteeing our product quality, high-quality services and reliable deliveries,” concludes Paolo.
www.delleraviterie.com
With an extensive product portfolio, state of the art coatings, and a constant focus on industry trends, Growermetal aims to meet the evolving demands of railway systems, ensuring safe and efficient operations for customers.
Fasteners are an important part of rail systems, being used both in infrastructures, such as tracks and in the means of transport itself. With the evolution of railway engineering, the demand for precision and reliability has grown, leading to constant research for parts in-line with the highest industry standards.
While the sector is experiencing the development of new technologies, the introduction of more specific materials, and the necessity of lighter and faster trains, means manufacturers of fastening products need to meet these unique requirements and the related challenges.
This is the case for Growermetal SpA, the Italian safety washer manufacturer, which has achieved high-levels of expertise in the creation of solutions for the railway sector. Guided by its 70 year long history, one of the main strengths of the company lies in the balance between its comprehensive production model and its range of designs and geometries, suitable for a great number of uses.
Railway washers are classified into different types and geometries, according to the specific application and function to be performed. Growermetal offers an extensive array of safety washers and coiled spring washers – available in various designs, materials, and dimensions –which can be further optimised with specialised surface treatments and coatings, such as the zinc flake coating DELTA PROTEKT ® KL120.
The latter is particularly suitable for railway applications, even in environments with the presence of water and humidity, for example in railway tunnels, as the washer provides outstanding quality with a complete line of base and top coats available.
In this way, customers from the rail industry can count on high performance and high-quality coatings, with a process performed entirely in-house on a fully automated line – eliminating the risk of hydrogen embrittlement, whilst ensuring the mechanical integrity and longevity of the washers.
Among the solutions offered by Growermetal, single, double or triple coiled spring washers are essential for mitigating dynamic heavy loads resulting from train movements.
The company produces single and double coiled spring washers meeting the UIC 864 standards for European markets and the A.R.E.A. 1967 standards for the USA. These washers are available in stainless steel AISI 316, which is particularly suitable for corrosive environments.
In addition to the wide range of sizes, Growermetal also offers spring washers with ribbed bearing surfaces, in order to improve the product’s fastening performance and eliminate the risk of breakage; as well as many standard coatings including burnishing with light oil film protection, mechanical zinc plating, zinc flake coating DELTA-PROTEKT ®, hot dip galvanisation and other solutions upon customer request.
Introduced in 2019, Grower TenKeep® is a flat washer that results from Growermetal’s investment in research and development. This commitment led to the innovative patented design of the safety washer, characterised by two surfaces of differentiated knurls that create a greater locking performance – even in presence of extreme vibrations and dynamic loads.
While the product prevents the loosening of the bolted joints, at the same time its exclusive geometry ensures the protection of the bearing surface, so that no damage occurs during the tightening and untightening procedures – even on galvanised, painted or soft surfaces.
In addition to single, double and triple coiled spring washers, and to the flagship product Grower TenKeep®, Growermetal's range for railroad tracks includes many other solutions that provide even more flexibility to customers. Among these products there are conical contact washers and conical elastic Sperrkant washers, designed to create an elastic pre-load in a bolted joint connection and reduce the risk of unwanted loosening. The combination of the conical geometry and radial ribs on the washer’s upper surface provides high resistance to loosening of the bolted connection, whilst avoiding damage to the bearing surface. Characteristics that make contact washers the ideal choice for railway and electromechanical applications, where parts are subject to temperature variation or high vibrations.
Conical elastic washers for bolts are another important item to maintain secure assemblies, as they compensate for thermal expansion and contraction, eliminating play. Their elastic properties ensure a reliable connection in dynamic conditions.
Finally, for versatile applications flat washers for bolts come into play, protecting surfaces from damage and enabling a more even distribution of loads, as they increase the load-bearing surface –safeguarding the integrity of the assembly.
Participating in trade shows is a strategic priority for Growermetal, as events offer a platform to showcase its comprehensive range of solutions. One of the most prominent events in the calendar is InnoTrans, the international trade fair for transport technology, held biennially in Berlin, Germany.
"From 24th – 27 th September the Growermetal team will present our product line and services at booth 415, hall 8.2 of the Berlin Exhibition Grounds – with the show a unique opportunity to connect with global industry leaders and extend our dedication to international customers from the railway industry,” highlights Paolo Cattaneo, CEO at Growermetal SpA www.growermetal.com
GROWER TENKEEP®: ONE WASHER TEN KEEP. When extreme vibrations or dynamic loads threaten the performance of bolted joints, the unique design of Grower TenKeep® provides a flawless anti-loosening action.
Its secret? Two surfaces of different geometries, for defined and uniform friction conditions without damaging the bearing surface, even in the most challenging applications.
Mustad has been investing in automation in order to further improve the quality of its products, as well as its productivity, to maintain its unchanged position as a leading manufacturer of quality products and technically advanced screws.
Afamily business with over 100 years of experience, Mustad has seen significant success and growth in the last five years, with both production volumes and turnover growing due to new customers and new markets. “Our success is based on the fact we manufacture 100% of the products we sell,” states Mustad SpA. “We are also able to manufacture a wide range of products for a lot of markets, including automotive, household appliances, electronics, mechanical, wood, as well as aluminium and PVC. In addition, all of our processes are carried out internally in a very strong and integrated way.”
Mustad continues: “For us screws are not just objects but functions, which is why we develop products according to applications or to improve the customer experience – helping to also reduce global fixing costs. For us it is not just about developing products, it is also about investing in training our staff and customers to understand the capabilities of the fasteners, as this helps us underline how the products can be used and sold.”
Mustad exports 40% of its products to more than 30 countries within Europe, as well as in the USA – approaching each market with a strategy of a long-term vision and looking to partner with customers that believe in a long-term cooperation. “Our focus is on the European markets where our products and services can help make a difference to customers,” mentions Mustad. “For instance, we often provide a co-design service to our customers, which is a win-win approach because customers can find solutions or standardise their processes and we can learn about various applications. By focusing on our customers’ needs, we can find the best solution with the best quality/price ratio, whilst delivering solutions that are produced on machines and product lines that are becoming more and more automated.”
The company adds: “Automation for our customers is a strong drive that is developing year by year. This is an advantage for us because for these types of customers the quality of the product, the service level, the stock availability and the very short supply chain are crucial aspects. We also guarantee our products are 100% 'Made in Italy', which ensures a very short supply chain and helps us to be more responsive to customers’ needs.”
“That is why we have ensured our production is highly automated. However, even with automated machines they still need to be set-up before they can work autonomously and with customer requirements increasing every year, the products also need to be checked when being produced. That is why we are so focused on investing in training our operators so they are able to handle these challenges,” reports Mustad. “We must continue to face the market with curiosity to catch opportunities and manage change. Thanks to our investments, we are able to continuously improve our quality, proximity and the development of our capacity.”
www.mustad.it
Our success is based on the fact we manufacture 100% of the products we sell… In addition, all of our processes are carried out internally in a very strong and integrated way.”
- Made in Italy since 1912
- 2 plants with a total production area of over 20,000 m2
- More than 100 heading, threading, pointing and packing machines
- Internal hardening department
- Internal machine tools department
- Millions of pieces produced per day
- Thousands of items in stock
- Highly qualified customer support
- Technical customer service
- ISO 9001 - IATF 16949 certifications
100% MADE IN ITALY
In order to maintain high-levels of quality and a quick, reliable service, Canali is constantly investing in technology and machinery, as well as adapting to meet the needs of customers in a variety of industries.
For over 40 years Canali Srl has been producing threaded rods, sections, tie rods and U-bolts, in large or small batches, to meet the specific production needs of each customer. The company is also able to supply threaded items from customers’ drawings, from M3 – M100 in diameter and in different lengths.
Using the best Italian quenched materials, and best alloys on the market, Canali is able to offer maximum customisation and guarantee 100% ‘Made in Italy’ quality. The quality is further guaranteed by full internal processes and continuous quality checks during each step of production – from the raw material’s arrival to the fastener product’s zinc plating treatment.
640
Due to its wide product range, Canali is active in various industrial sectors from the infrastructure industry to the wind power industry, as well as the construction sector and furniture and furnishings industries. “The current main challenges within these markets is to guarantee accurate deliveries and to be flexible with customers’ demands. Therefore it is our main focus for 2024 to become more stable on the pipe and valves industry, as well as continuing to invest in our equipment and services,” highlights the business.
Recently, Canali invested in a new machine to chamfer its products and maintain the high-quality its customers have come to rely on, as well as focusing on automatic machinery. The company explains: “As well as investing in automatic machinery our goal is to strengthen our labour. As an Italian manufacturer we are facing a number of challenges within our sector because of the lack of skilled workers. We are therefore committed to helping skilled young people enter our industry and offer an attractive work prospect.” Canali therefore works closely with local engineering schools to give students the opportunity to work in the sector as soon as they finish studying.
“Our constant investments in the latest generation of machinery, as well as the investments in our people means that customers can expect expert know-how and high-quality products capable of satisfying even the most sophisticated needs.”
www.canalisrl.it
With the fastener industry’s increasing focus on the networking of all production systems, as well as the evaluation of process data, Marposs Group is offering both software and hardware to customers to fully digitalise their production processes.
Marposs Group’s two product lines, Brankamp and Scwher + Kopka, offer process monitoring devices, MES software and analysis tools for evaluating and storing process data, enabling Marposs to work in close cooperation with its customers to develop new analysis evaluations that are specifically required.
“The current trend is digitalisation and the evaluation of data and the feedback of these results are put into production,” underlines Joachim Krüger, head of sales support forming and stamping at Marposs Group. “The large amount of machine and process data poses a challenge in terms of filtering and analysing it in a systematic manner. However, it does enable operators to be better supported in the set-up process, as well as help tool life to be improved. That is why in recent years we have invested in the development of software and hardware that allows our customers to fully digitalise their production – meaning processes can be analysed downstream and conclusions drawn about tool life, production problems or production breakdowns.”
Marposs monitoring devices are also an integral part of the automation sector, as the units can analyse and store process data and send signals to the machine. Furthermore, data can be sent from the ERP system to the monitoring terminal and back again. This bi-directional function offers customers many possible applications and supports the automation of production.
“In the last five years we have further advanced the automated processes and integration into forming machines – providing machine operators with helpful, reliable information to support the set-up process and troubleshooting,” points out Joachim. “Sensor signals are also increasingly being used automatically as reliable control values for the machine. Networking between production and operating data will also be further integrated and we will work with our customers and partners to drive forward efficient and reliable production processes.”
With subsidiaries in more than 20 countries worldwide, helping ensure customer support from sales and service in the local language, Marposs Group is also able to recognise local trends and the needs of customers at an early stage, so it can combine the highest technical precision, with local customer proximity, to offer customers optimum cooperation.
www.marposs.com
The post-process data evaluation offers the possibility to analyze and evaluate the entire process data for the first time. Important conclusions can be found about process variation, setting of monitoring limits and recognition of process influences during the whole production run. The knowledge acquired is helpful in determining the optimum process parameters and provides detailed conclusions about tool wear.
After a challenging couple of years, BENERI SpA states that business has returned to pre Covid-19 normality – enabling the company to work in a more planned way, as well as creating more time to look ahead to future projects and opportunities.
Back in 2021/2022, post Covid-19, BENERI experienced unexpected and exponential growth, demand reached levels never seen before – with supply struggling to keep up. “Raw materials were in short supply and prices were very high,” explains BENERI. “Since then, the conflict between Russia and Ukraine led to an energy crisis in Europe for gas and electricity – with soaring costs. This created a very difficult period, but we are extremely satisfied because we worked hard to manage these big challenges.”
BENERI continues: “When it comes to last year, we worked partly to satisfy the requests of the previous year, while in the second half of the year the market did witness a clear slowdown in demand, which we expected and in our opinion was ‘physiological’ rather than a true slowdown. However, after a slow start to 2024 it is turning out to be a year in-line with pre Covid-19 business and more importantly a sense of normality has returned to the market, which means we are able to look forward and develop new exciting products and projects. For instance, we have been expanding and consolidating our brand in northern Europe, Asia and the USA.”
With over 60 years of experience BENERI has developed the expertise, knowledge, production, and commitment to quality, that enables it to supply a wide range of retaining rings and washers to the global market.
A family-owned company, BENERI has a wide production capacity, with parts designed and produced in five production units located in Valmadrera (LC), Italy. As a leading manufacturer of standard retaining rings and washers, both in metric and inch dimensions, the company is able to supply products that comply with DIN standards, as well as a variety of special solutions.
“In the last decade, we have invested a lot in quality and have introduced several additional quality checks in each step of the production process to guarantee the highest quality levels for our products,” states BENERI. “We have also ensured we have a huge stock of our product range that can be delivered quickly to customers globally.”
Thanks to its know-how, and constant technical research and investments for the optimisation of the production processes, BENERI is
able to develop new products, including a line of products with standard sizes but with very strict tolerances. “This range of products is created for end users, where the assembly of the rings is made automatically, so that robots can work without line stops,” points out BENERI. “In recent years we have also started several special projects, based on customers’ designs, for different industries including automotive, agriculture and white goods.
A key focus for BENERI going forward will be how the company attracts new talent and employees to the business. “Never before has human capital been as important as it has in recent years, even with the increasingly pressing robotisation and automation of processes,” outlines BENERI. “That is why one of the most important investments we have made recently is improving the working conditions for our workers, as well as ensuring the highest safety in all of our production plants.”
The Italian manufacturer has also placed sustainability as a key topic for the future. “We believe that sustainability is important in several aspects. For this reason, we have decided to work on the production of our first sustainability report, which we will publish shortly and will show without filters the current situation of BENERI, as well as what our objectives are and what goals we will achieve,” points out the company. “This has been a voluntary choice for our business, we had no legislative obligations, but we think this attitude will distinguish our name from competitors worldwide.”
BENERI concludes: “Customers that work with us know they can count on us as a serious and reliable supplier. We have long-term business relationships with our customers and suppliers and we believe that the best way to do business is growing together with our partners.” www.beneri.com
One of these challenges includes the adoption of advanced materials, with a growing demand for lightweight and high strength materials due to the growth of the aerospace and automotive industries – both driving factors in the growth of the specialised fastener market. That is why DOSS designs and manufactures innovative visual inspection systems that are capable of adapting to various production needs in terms of materials to be inspected, defects to be identified, sorting times, as well as logistical requirements.
Since 1995, DOSS has been working with companies that manufacture rubber, silicone, plastic and metal components for the automotive, pharmaceutical, industrial and fashion sectors – helping to satisfy the standard of 100% quality control.
With the trend of digital technologies, DOSS is constantly investing in new technologies to design easy to use, more sustainable machines, as well as introducing Artificial Intelligence (AI) and deep learning to simplify use and optimise processes. Thanks to intelligent sensors and connected devices, it is possible to monitor the status of fasteners in ‘real time’, preventing failures or loosening before problems arise. This digitalisation also allows predictive maintenance, helping to extend the useful life of fasteners and reduce maintenance costs.
The fastener industry is adopting advanced materials and digital technologies to improve the efficiency, safety and durability of fasteners, enabling increasingly sophisticated applications in a wide range of sectors. With innovation guiding every aspect of DOSS, the company is focused on addressing market needs with cutting edge technologies, as well as rising to the challenges new markets present.
DOSS machines are also able to collect and transmit a large set of information, thus contributing to the creation of an advanced business process oriented towards the design/industrialisation of products, as well as the sustainability of products and business processes for an increasingly digital and interconnected factory.
“Italy is the second largest manufacturing industry in Europe and we are going through a delicate period in our history. The digital revolution has changed the way we produce and design products, and services, and now the world economy has the test of sustainability ahead of it, but the challenges are global,” comments DOSS Visual Solution Srl. “If we want to remain at the top of global manufacturing we have to be able to manage increasingly complex logistics systems, control the reliability of supply chains and absorb economic shocks. As well as this, we must be able to react flexibly to increasingly less predictable environmental changes – such as a circular economy and supply chain issues. We also need to be able to react to challenges common to small and large businesses.”
With the transition towards a circular economy, important employment opportunities are opening up considering the transition towards the green economy, which represents a prerequisite for the survival of manufacturing and the digital gap. “Data is a key factor for circular economy, which is why digital transformation must be accelerated in those situations where the path still needs to be completed,” reports DOSS. “Automation and AI have definitively entered the heart of industrial production to improve both the precision and efficiency of operations. For instance, DOSS AI can analyse images and data with accuracy that far exceeds humans, detecting tiny defects that might be missed during manual inspections. Automation also enables processes to be sped up, reducing risks for operators.”
As well as this benefit, DOSS vision algorithms can process and analyse large amounts of data in very short times, significantly accelerating quality control and reducing production downtime. AI models, as well as cobots, can also be trained and reconfigured for different types of products or production lines, making the tools scalable and adaptable to different needs. There is also the benefit of integration with other systems for even more comprehensive quality control.
“The potential of these technologies goes far beyond the automation of repetitive tasks. The ultimate goal is to raise production standards to unprecedented levels, guaranteeing superior quality products. The synergy between human capabilities and AI not only increases efficiency, but also enriches the workplace with new skills and stimulating challenges,” explains DOSS.
An example of this is DOSS ROBOTICS – an automated robot integrated with vision control to automate both visual inspection and the piece handling processes within production. DOSS robots can take parts directly from a customer’s machinery and transfer them to the inspection station – where they are analysed in detail to ensure accurate quality control over the entire surface of the part.
“Now that the world has become smaller and faster, only the ones who will know how to be creative and competent in the development of innovation will be able to exploit multi-sector applications and gain success. The era of competence has begun,” states DOSS.
The company adds: “We have always worked to make our machines increasingly sustainable and reduce the already low energy impact. The transition to a sustainable business model is no easy feat but it is essential for us – with management committed to sustainability, considering it a strategic priority for the business."
As part of this commitment, an analysis of the company’s current situation in terms of sustainability has been planned for 2025 – with the goal to identify areas for improvement, risks and opportunities linked to environmental, as well as social and economic aspects. As part of this goal, DOSS will be informing and educating employees, suppliers, customers and other stakeholders on the importance of sustainability and how the company contributes to it, by implementing a monitoring system to measure progress towards sustainability objectives with annual reports. www.doss.it
As an agile and resilient company BBA is able to rapidly adapt to new opportunities and changes within the market, which puts it in a very strong position, especially after increasing its production capabilities – including adding cold forming machinery to produce components in large diameters and very long lengths.
BBA explains that the investment into expanding its cold forming and tapping possibilities was in response to winning several high volume rivet nut applications, as well as responding to the growing need of customers to use ‘big’ cold formed components. “Due to lightweighting of structures in general, customers are forced to use expensive reinforcing elements that must be inserted and welded into the structures to provide areas of local strength within it,” explains Paul Hanratty, managing director at BBA Srl. “Our new cold forming capabilities mean we can make cost-effective reinforcing elements that crucially can be riveted anywhere into a structure, unlike welded solutions, offering huge process cost savings and increasing customers design flexibility.”
A specialist in rivet nut and rivet nut stud manufacture, BBA has a reputation for manufacturing innovating solutions, with the company producing the patented Bulge Control Technology (BCT) rivet nuts, which it says are perfect for achieving high strength performance or where applications use fragile or delicate sheet materials that are challenging to fasten. “As a technical innovator and cold forming specialist, we can deploy our resources to make similar products that have entirely different application uses,” underlines Paul.
In addition to the Italian market, BBA has already committed to investing in increasing its sales exposure in Germany, eastern Europe and the USA – with its activity partly funded by the Italian state. “We are entirely grateful for the support from the Italian government and our efforts in these different markets is now coming to fruition,” mentions Paul. “We are seeing significant growth in real terms, including in our project pipelines and exposure to new potential customers. Next on our horizon is the Korean Peninsula, where we are actively developing some new exciting applications.”
BBA is already supplying some large volume applications in the European automotive sector – with the company able to meet the stringent quality levels required. “In most cases, our customers are
installing our parts using semi or fully automated systems,” points out Paul. “These machines do not suffer variation in the rivet nuts they install and stop every time a part that is not dimensionally correct is presented, as well as for those that do not conform to the pre-determined setting curve, which proves our products are able to achieve the highest level of quality.”
Paul continues: “We can achieve this level of quality thanks to us religiously adopting an ethos of continuous improvement. In addition, our ability to design and build our own production machines in-house, together with machine tools, means we understand our capabilities very well. Knowing where our strengths and weaknesses are in the manufacturing process, we are well prepared to address the issue or ensure appropriate process controls are in place to detect such issues.”
As a European manufacturer BBA is clear that it needs to differentiate itself from other businesses by remaining committed to technology, innovation, quality and service. “Adding value to the customer is fundamental and therefore developing brand awareness and customer loyalty is critical. We believe that for the engineered fastener market, the trend of customers seeking to secure their supply chain by sourcing from European manufacturers, versus purchasing parts that originate in the Far East, is strengthening, and for good reason – such as long transit times, availability of shipping containers, the shipping costs, as well as potential for delay when sourcing from the Far East. These can be mitigated to some extent by maintaining higher levels of stock, but that too is costly and risky. However, political volatility, such as the potential of trade tariffs, embargoes, and ultimately the potential of conflict, are significantly less easy to cope with. The issues in the Middle East, South China Sea, Korean Peninsula, and Taiwan, could easily result in serious disruptions of fastener supply. To this end, it would be irresponsible of larger fastener consumers and distributors to not have established a robust European sourcing policy.”
Paul concludes: “BBA is often regarded by customers as a fastener consultant supporting those who are seeking advice not only on rivet nut applications but for general engineered fastening solutions. Overall, we aim to add value to our customers’ businesses and can work together on solutions. We offer real technical innovation, providing customers with problem solving solutions and product performance often beyond expectation. By adding value to our customers, and making them stronger, we benefit hopefully with long-term relationships that provide stability and consistency for all concerned.”
www.bbafasteners.com
Since becoming part of Bontempi VIBO, Mi.Me.Af. has gone through a period of restructuring and major investments – with the latest development in its strategic reorganisation the decision to move from end users to distributors as its main market.
Specialising in the production of customised fasteners, Mi.Me.Af. was founded in 1952 and its growth over the years has been based on continuous efforts to meet customers’ demands for quality and customisation. The company’s expansion has been constant even when the market has experienced moments of stagnation, with the decision to specialise in the production of custom designed parts, and the accuracy of bespoke products, a key factor in overcoming any turbulence in the various sectors.
In 2021, Mi.Me.Af. was acquired by Bontempi VIBO as part of its industrial growth strategy. “When we acquired Mi.Me.Af., we started a restructuring process to rebuild part of our internal organisation, in particular sales, accounting and the quality department," explains Raoul Bontempi, CEO of Bontempi VIBO and president of Mi.Me.Af.. "As part of this process, we have also renewed our production machinery to help modernise processes and make them more efficient.”
A more recent development was Mi.Me.Af.’s decision to move from end users to distributors as its target market. “Bontempi VIBO has always been clear in its policy of only supplying distributors and we wanted to be transparent with our customers, which is why we are going through this process,” Raoul points out. “We want our distributor customers to be confident that when they work with us they are building a long-term partnership.”
With a capacity of 4,000 tonnes per year, focusing on special parts from M3 to M12, as well as having obtained a number of certifications, including IATF 16949, Mi.Me.Af. is intent on capitalising on the company’s recent developments and attracting new customers and business, as well as continuing to work with Bontempi VIBO and its customers.
“By focusing on distribution, we can have a better connection with Bontempi VIBO and this allows our parent company to provide customers with both standard and special products, which will be a great advantage for customers,” Raoul reports. “By working with Bontempi VIBO we can provide all the fasteners a customer needs, thus reducing the costs associated with working with numerous suppliers. We are also able to collaborate with customers and provide expertise if we feel there are better options. We have a great deal of experience in the production
of fasteners and our technical department can support customers in all their needs or, if required, follow specifications or drawings.”
In order to provide a first-class service to its customers, Mi.Me.Af.’s production has been optimised to improve the production flow and includes state of the art machinery – enabling the company to expand the range of available formats and develop new products, while maintaining the highest quality. Mi.Me.Af. has also revamped its sorting department with the introduction of six optical sorting machines, so that it can offer customers 100% sorting and guarantee the highest quality.
“We have made a lot of changes at Mi.Me.Af. and we are excited to work with companies to find solutions to their needs for special and customised fasteners, as well as offering a full service of standard and special parts in cooperation with Bontempi VIBO,” concludes Raoul. www.mimeaf.it
With over 40 years of experience in the sector, Atlantic Man Srl is a reliable partner in the field of fastening solutions – providing a comprehensive range of products capable of securely connecting a wide variety of industrial systems.
Based in Castelnovo di Sotto, Italy, the company has implemented an automated in-house production facility, which is constantly evolving to guarantee the highest quality, competitiveness and precision of each component.
Despite its deep Italian roots, Atlantic Man embraces a clear European and international vision, exporting its products worldwide and adapting to the different needs of local markets. “We are aware of the necessity to comply with national and international regulations and standards to ensure the conformity of our fastening systems,” states the business. “For this reason, we constantly invest in research and development to manufacture solutions capable of meeting the increasingly complex needs of our customers.”
This combination of Italian manufacturing tradition and technological innovation enable Atlantic Man to offer reliable and durable products for multiple contexts and applications, while also contributing to the reduction of environmental impacts. “Sustainability
With a clear vision and a constant commitment to excellence, Atlantic Man is ready to face future challenges...”
is at the core of our corporate philosophy. We have adopted eco-friendly production processes and implemented an ISO 14001 certified environmental management system to reduce the impact of our activities and contribute to a greener future,” highlights the company.
Atlantic Man not only offers high-quality fastening solutions at competitive prices but also distinguishes itself with precise and punctual service, aimed at complete customer satisfaction. “We are committed to providing increasingly personalised support. For example, we can produce hoses and heavy-duty clamps according to specific designs and are equipping ourselves to offer a laser marking service on each individual piece manufactured,” underlines the business.
With a clear vision and a constant commitment to excellence, Atlantic Man is ready to face future challenges and consolidate its position in the fastening systems sector. “We strive to anticipate market needs by offering innovative and reliable solutions, maintaining a dynamic and flexible approach to ensure our customers’ complete satisfaction.” clamps.atlanticgroup.it
CEIA has been designing and manufacturing no contact induction heating devices for metal treatment for more than 50 years. As customer demands for greater quality products continue to increase, the company is seeing a willingness to invest to guarantee greater production efficiency.
CEIA SpA highlights: “Thanks to 100% control of our production process, we can guarantee maximum quality, flexibility and efficiency. In fact, the uniqueness of CEIA’s production is being able to directly manage and control every aspect of our production –from the development and assembly of the electronic boards used in our systems; software development; to the creation of the mechanical carpentry; and the final assembly and testing of the generators.”
dimensions, can be easily integrated inside forging machines for the warm forming of titanium, nickel or steel during the production of fasteners.
CEIA’s unique technological solutions enable the manufacturing of power equipment with compact sizes, extremely high energy efficiency and long-term reliability. CEIA produces high and medium frequency induction heating systems, with a complete range of generators that have variable power from 2kW – 200kW, and working frequency up to 1,800kHz, as well as control units and optical pyrometers for temperature measurement.
The company’s induction heating systems can be used across many different applications including heat treatment – CEIA generators perfectly adapt to hardening applications, surfacing hardening and annealing. The area and the heating depth depend on the coil geometry and the exposure time to the magnetic field. As well as warm forming, CEIA induction generators, thanks to the extremely compact
The company's systems can all be integrated into automated production processes in order to guarantee highly efficient products to minimise operating costs for customers. Thanks to the remarkable experience, and the continuous technological research, all CEIA induction generators, control units and optical pyrometers are certified and calibrated to grant the customer a repeatable result and high-quality control.
CEIA explains: “We don’t just sell a product, but we offer a service guaranteed by our organisational structure at a global level, in Europe, America and Asia. Our goal is to further strengthen our presence by increasing the number of retailers who can work directly with CEIA USA, as well as developing new partners in the Asian market to have assistance closer to end customers. Our priority is to develop longlasting collaboration with all customers.”
“‘Made in Italy’ is synonymous with professionalism, quality and efficiency, and it is important that global customers continue to recognise these characteristics in all CEIA products.”
www.ceia-power.com
Over the past two years the fastener industry has seen a significant surge in sustainability innovations. TECNOLOGIC 3® is therefore committing to its environmental responsibility by phasing out high CO 2 emitting products and investing in its eco-friendly products.
In order to achieve this goal
TECNOLOGIC 3® has invested in low emission machinery; technologies to minimise high impact materials; as well as in further reducing its carbon emissions by replacing high CO 2 emitting products in favour of environmentally friendly and healthier alternatives.
This includes its commitment to water-based products for an eco-sustainable and ‘reduced impact’ product. Through innovative chemistry, specific industrial production, and advanced applications, TECNOLOGIC 3® is an undisputed player in the market for reactive and non-reactive coatings for fasteners dedicated to automotive and other industries. These water-based solutions have the ability to reduce the impact on the environment that the extensive use of solvents is having on the planet. In addition to the environmental benefits gained, the water-based solution is also physiologically and toxicologically harmless.
“In addition, all water-based formulated products promote significant cost and energy reductions and allow the use of products, and application systems, to help reduce the impact on the environment and living things,” underlines the company.
TECNOLOGIC 3® is able to tailor products using customisation processes to transform every request into an innovation opportunity, as well as turning research and development into a cycle of experimentation and learning, which yields field-tested solutions in its laboratories.
With its own in-house research laboratory that supports all development activities on products – ensuring complete dominance in application, development and technology –a specialised team strives to innovate and offer continuous support to the activities of more than 300 different customers. Market demands and new industry perspectives, such as specific performance and eco-compatibility, are the guidelines in the design and implementation of new products and preparations, which the R&D centre processes in three stages – laboratory research, application
development, as well as testing and certification by relevant bodies.
TECNOLOGIC 3® is able to tailor products using customisation processes to transform every request into an innovation opportunity...”
This not only ensures product effectiveness but also drives the continuous evolution of company expertise – a mindset that has been a hallmark of TECNOLOGIC 3® since its inception. This ethos also extends to employee care, currently addressed through a welfare bonus scheme and supplementary health care – with potential for future enhancements.
TECNOLOGIC 3® concludes: “Future goals include strengthening our position by expanding into non-European markets, such as America. This presents an opportunity to export our Italian and European vision of product and process sustainability, promoting a business approach that TECNOLOGIC 3® deeply values. Moreover, it offers the chance to gain insights into new challenges that, while currently peripheral, could become pivotal for both the company’s and industry’s future.”
www.tecnologic3.it
A commitment to quality, modularity, excellence, reliability, customer centricity, continuous improvement, and innovation, are the core values that have been defining SACMA Group since 1939. The past two years have also seen a period of investment for the Group – with an expansion of its product offering, across all of its brands, to meet customers’ needs.
SACMA Group encompasses five interconnected production sites; 300 employees worldwide; five international branches with local aftersales staff in the USA, China, Taiwan, Germany and Brazil; as well as 24 agencies. With over 85 years of history, SACMA guarantees 24/7 on-site and remote service with 11 technical service centres providing excellence for its customers.
At its Italian plants in Limbiate, Vimercate and Castelenuovo Scrivia, through an insourced and modular production system, the factories manufacture mechanical parts with the highest standards for precision and raw material quality – due to the large majority of forging, casting and raw materials coming from Italy to respect the sustainability charter. Each workpiece is then assembled in-house and becomes part of either a SACMA multi-station forming machine; an Ingramatic flat die thread roller; an HS ASPE tapping machine; or moved by Tecno Lift products to customers’ workshops.
Active worldwide in western Europe, eastern Europe, the Americas and Asia, SACMA Group has invested heavily over the past few years to be closer to the customers buying its equipment. SACMA Group explains: “Sales are currently prevalent in America and India, where many new
SACMA Group is spreading its technologies around the world and reaching new and emerging customers.”
important projects are requiring new machineries. European countries are now in restructuration due to the inflation rate and the low level automotive market, but this could change quickly if politicians released the restrictions for the sales of thermic engines, unlocking the declining automotive market. SACMA Group has registered a large amount of purchase orders for the next 18 months, with some assembly lines sold out up to 2027 – something that has never happened before. This is a demonstration of how SACMA Group is spreading its technologies around the world and reaching new and emerging customers.”
In order to further meet customers’ needs, SACMA Group is investing heavily in the machines it offers. As combined machines now represent more than 50% of SACMA Group sales, the brand has introduced the new SP18 and SP28 combined header machines. These machines enable customers to produce fasteners and screws for the automotive, construction, electric/electronic and white good industries – starting from the wire. SACMA states that this is the best solution for high productivity requirements; consolidation of production methods; floor space utilisation; and workflow in the fastener manufacturing process –by having the forming, chamfering and thread rolling all in one machine.
The machine is also equipped with the latest technologies available on the market, such as direct drive motors and software to facilitate the operators in making changeover quickly, easily and safely.
Since this technology is extremely profitable in terms of layout and sustainability, some customers requested a combined six die header, resulting in the SP39 combined header machine with a six die forming station, pointing station and threading station.
As well as this, the KSP12 – a one die two blow combined machine with the threading operation integrated into the machine – is now supplied all over the world, enabling customers to reduce the layout of any kind of multiple machine lines. SACMA Group has recently dedicated one extra assembly line to the KSP12 in order to satisfy customer demand.
With the focus of strong standardisation of fasteners in the automotive market, Ingramatic is also investing in its product offering with the new Rotative Rolling ‘RR’ standalone machine. The ‘RR’ is a combined thread rolling machine with a modular solution consisting of the installation of a rotative rolling station just before the flat dies threading station to run the complex parts in one shot. The ‘RR’ machine will be available in three different sizes and can be sold as a station or standalone. Ingramatic is also further looking to the future with the commitment to double its building space by 2025 to increase its capacity to assemble more threaders.
As well as these future building plans, Tecno Lift is also investing in infrastructure with the extension of its plant to create more room
to build ancillaries equipment to move fasteners. The plant now has two buildings with the first dedicated to laser cutting, bending, and welding, and the second housing the assembly line with vibrating hoppers, conveyors, elevators and bean tilting units.
As a further symbol of Italian excellence, HS ASPE, a brand for dedicated CNC machines for secondary operations after forming and threading, has introduced the T10-VT – a brand new tapping machine with a vertical architecture to run parts from M3 to M10, with four spindles at the maximum production speed of 200ppm. The machine has been designed to improve customers’ workshop layouts by reducing space and improving ergonomics.
SACMA Group is now focusing on the sustainability of the fastener production process by introducing options to its machines to help customers exchange consumption and CO 2 emissions, with different levels of process data digitisation made available.
These include an ‘Industry 4.0 Advanced’ level consisting of a Siemens® IOT server in the electrical cabinet for the remote reading of code and commenting of the part in production, with the possibility of writing the quantity of pieces to be produced in the two pre-sets. Technical documentation such as electrical, hydraulic, pneumatic plans and operator manuals are also integrated into the machine and are available through QR code on a tablet or smartphone.
In addition, the ‘Industry 5.0 SC Energy’ level equips the machine with a device monitoring the consumption of power and compressed air, in order to identify the opportunities to improve the energy efficiency, with economical, environmental and operative benefits. The figures are also available directly from the device itself or for download. Other functions include tracking of air pressure, temperature, humidity, as well as a shut-off valve to eliminate air consumption during machine stops.
To conclude its period of investment, and in order to provide customers a full service to exceed their needs, SACMA is focusing further on sustainability with the increase of its photovoltaic solar panels for its five factories, with more than 2,270kW, as well as a new generation of compressors and heaters to reduce its CO 2 footprint. In addition, SACMA Group has invested in new systems to guarantee the safety of its employees working in the manufacturing and assembly division with new factory layouts, new safety guards and new modular platforms. www.sacmagroup.com
Fastener Fair Italy 2024, now in its fourth edition, promises to be a major event for fastener professionals – with the event representing a key appointment for the entire industry – offering visitors a dynamic environment in which to consolidate relationships, discover the latest innovations and gain insights into market trends.
Taking place from 29 th – 30 th October in hall 3 of CityLife –Allianz MiCo in Milan, Fastener Fair Italy is designed to offer visitors a comprehensive and enriching experience, enabling them to explore a wide range of products and services presented by the companies at the fair. The strong participation of exhibitors and the robust representation of international companies confirm the strategic importance of the sector for the global economy.
The fastener market is strategic in many manufacturing sectors, such as automotive, aerospace, manufacturing and construction. In Italy, this sector is on the upswing, supported by a projected average annual growth rate of 2.3% for the next five years and an expected value of sales of around US$2 billion in 2025. The internationalisation of markets also represents a great opportunity for commercial expansion for the entire industry.
Confirming the importance of the event, there are already 190 exhibiting companies from 18 countries, with a strong presence from Italy, Germany, Turkey, China and Taiwan. It is precisely this variety of international attendance that ensures a comprehensive overview of the global market, enabling the professionals involved to discover the latest innovations and technologies in the field of fastening systems. This contributes to an environment rich in stimuli and opportunities, where visitors can discover innovations and know-how from various geographical and industrial backgrounds.
During the show visitors will be able to explore products ranging from screws to bolts, from anchoring systems to safety devices, from assembly technology to production machinery. This wide range of products is divided into thematic areas to facilitate the meeting of supply and demand, making the visit more efficient and targeted to the specific needs of the attending professionals.
One of the central themes of Fastener Fair Italy 2024 will also be innovation, with a focus on cutting edge solutions that improve the efficiency, quality and sustainability of manufacturing and installation processes. Visitors will be able to discover intelligent fastening systems, made with advanced materials and additive manufacturing technologies, capable of meeting the specific needs of various industries.
In addition, sustainability will be a key topic, with many companies presenting eco-friendly solutions to reduce the environmental impact of their products and production processes. Visitors will have the
opportunity to explore how the fastener industry is contributing to the transition to a greener economy by discovering best practices and sustainable innovations.
Fastener Fair Italy 2024 is not only a showcase for products and services, but also a unique opportunity for networking and training. Visitors will be able to participate in B2B meetings, which offer the opportunity to establish direct contacts and initiate business negotiations. These meetings are designed to optimise the time available and focus efforts on the most promising opportunities.
Online registration for free access to the event is already open at www.fastenerfairitaly. com/it-it/tickets.html , offering industry professionals the opportunity to prepare for two intense and opportunity packed days in Milan.
www.fastenerfairitaly.com
A.D. PRECISION FORGINGS PVT LTD 550
A.I.F.M. - ASSOCIAZIONE ITALIANA
FINITURE DEI METALLI 214
ACHILLES SEIBERT GMBH 1434
AICHELIN GES.M.B.H. 1028
AMBROVIT SPA 620
ANNIBALE VITERIE SPA 1540
AOZHAN INDUSTRIAL CO LTD 346
ARCOSTEEL 320
ARSER SRL 419
ASIL CIVATA SAN. VE TIC. A.S. 335
ATOTECH ITALIA SRL 520
B.A - BONOMI ACCIAI SRL 120
BERARDI BULLONERIE SRL 430
BERTOLONI & BOTTURI SRL 515
BETA UTENSILI SPA 500
BETTER FASTENERS (SHANGHAI ) CO LTD 344
BIRLIK BAGLANTI ELEMANLARI SAN. VE TIC. LTD. STI. 1250
BÖLLHOFF SRL 330
BONFATTI FILETTATURE SRL 260
BONOTTO PACKAGING 730
BONVINI ELETTROGALVANICA SRL 1042
BRALO ITALIA 840
BULLONERIA DEL TOCE SRL 353
BULLONERIA USORINI SRL 449
BULL-VIT SRL 1120
CANALI SRL 640
CAPITAL BOLTS AND HARDWARES 1213
CARLO SALVI SPA 740
CARUTTI SRL 1028
CEIA S.P.A. 1440
ÇETIN CIVATA SAN. VE TIC. A.Ş. 1130
CHAVESBAO (CHAVES BILBAO S.L. ) 530
CHIREK FASTENER CORPORATION 1012
CHITE ENTERPRISES CO LTD 1210
CHUN YU WORKS & CO LTD 1017
COLDMATIC FORGE / KALOTI 920
COLOMBO EZIO & C SRL 660
COLOMBO SEVERO E FIGLIO
ERMANNO SNC 1441
CORBETTA ERMANNO SRL 553
CORNWALL ENTERPRISE CO LTD 1015
DATAGEST SRL 1428
DELL'ERA ERMANNO & F. SRL 1030
DELL'ORO DI DELL'ORO DAVIDE ( EXPOMETALS.NET ) 1640
DFV AUTOMAZIONI 940
DIMAC SRL 600
DIV GROUP LTD 1449
E.CO. SRL 1253
E.W. MENN GMBH & CO KG 1028
ECOZINC SRL 1040
EFP INDUSTRIE 960
EUROFIX SRL FASTENING SYSTEMS 410
EUROPRESSVIT SRL 945
EVEREST METAL INDUSTRIES 318
EVERFAST DIS TICARET A.S 130
EZEL CIVATA SANAYI VE TICARET A.Ş. 1036
F.R.L. SRL 1030
FACCHI FRANCO & C. SNC 1020
FASTBOLT
SCHRAUBENGROSSHANDELS GMBH 1243
FASTDEV SRL 720
FASTEN FIX CO LTD 243
FASTENER + FIXING MAGAZINE 144
FENG YI TITANIUM FASTENERS ( FENG YI STEEL CO LTD 453
FESTON S.N.C. DI FESTI GIUSEPPE & C. 361
FILET SRL 455
FIXI SRL 555
FLAIG + HOMMEL GMBH
VERBINDUNGSELEMENTE 703
FM METAL FASTENERS GROUP SPA 1330
FOSFANTARTIGLIO L.E.I. SPA 1223
FRIGERIO ETTORE SPA 1030
G.V. GOBBI SRL 310 GALLY SPA 418
GAMMA OFFICINE MECCANICHE SRL 1450
GANDINI FASTENERS SRL 1050
GENERAL INSPECTION LLC 118
GESI ITALIA GMBH 1220
GIDIEMME S.A.S. 1645
GIUSSANI RAPID SRL 640
GROWERMETAL SPA 850
HAIYAN GUANGDA HARDWARE CO LTD 1313
HAIYAN HUASHENG FASTENERS CO LTD 1316
HAIYAN SANSHUN TRADING CO LTD 1314
HAIYAN SHANGJIA HARDWARE CO LTD 244
HAIYAN YIHUI HARDWARE TECHNOLOGY CO LTD 1317
HARYANA FASTENERS 415
HEICO ITALIA S.R.L. A SOCIO UNICO 561
HICCOM GMBH 810
HISENER INDUSTRIAL CO LTD 1312
IK INTERKLIMAT SPA 447
IMANPACK PACKAGING & ECO
MEAPFORNI SRL 328
MECAVIT SRL 420
MECCANICHE MORANDI SRL 855
METALLURGICA LOCATELLI SPA 655
MEVI ITALIA SRL 610
MICROMETAL SRL 547
MILANI ENRICO SRL 835
MINSAVIT SR 1455
MITOS SRL 760
MITTER FASTENERS 1218
MOLLIFICIO LUIGI CODEGA SRL 148
MUBEA TELLERFEDERN GMBH 1350
NIBRO B.V. 1357
NINGBO NANJUBAOGE FASTENER
MANUFACTURING CO LTD 347
NORD-LOCK SRL SOCIO UNICO 1254
NUOVA RIVETTERIA BOLOGNESE SRL 1535
OFFICINA MECCANICA PISCETTA SRL 518
OFFICINE RIVA SPA 820
OMEGA CIVATA SAN TIC A.S. 1320
P SYSTEMS SRL 1200
PGB EUROPE 755
PILONI SRL 1030
PRESSVIT SRL 1328
PRK TECHNOLOGIES GMBH 1136
PROFIROLL TECHNOLOGIES GMBH 1425
R+FK SCHULTE KG 510
RAACO GERMANY HANDELS GMBH 138
RAPITECH SRL 1030
RAY FU ENTERPRISE CO LTD 1018
ROHTAS FASTNERS PVT LTD 319
ROMEO COBALCHINI SRL 440
ROTEC B.V. 560
ROTOR CLIP S.R.O. 435
SABE FORNI SRL 1054
SALCA SRL 861
SANTECH FASTENER TECHNOLOGIES 1550
SENSO VISION SYSTEMS PVT LTD 700
SERTEL VIDA METAL A.Ş. 1325
SHANGHAI FAST-FIX RIVET CORPORATION 342
SHANGHAI SEA SONG CO LTD 340
SHANGRAO CITY YIWEN FASTENER CO LTD 345
SOLMEC SRL 750
SPROUT TOOLING CO LTD 1550
SSAMH PRECISION TOOLS PVT LTD 311 ST SBAVATURA TERMICA SRL 603
STRUBL GMBH & CO KG 615
SUZHOU YNK FASTENER CO LTD 341 TANCO CONSULTING & TRADING JSC
TECNOLOGIC 3 635 THE MAGNI GROUP INC 1046
U.D.I.B UNIONE
Milan, Italy
29 Oct – 30 Oct 2024
www.fastenerfairitaly.com
Italy’s essential showcase for fastener and fixing technology.
Kraków, Poland
25 Sept – 26 Sept 2024
www.fastenerpoland.pl
International trade fair for fastener and fixing technology.
wire China
Shanghai, China
25 Sep – 28 Sep 2024
www.wirechina.net
Wire and cable exhibition, including fastener manufacturing technology.
UK Construction Week
Birmingham, UK
1 Oct – 3 Oct 2024
www.ukconstructionweek.com
The UK’s largest construction event.
Motek
Stuttgart, Germany
8 Oct – 11 Oct 2024
www.motek-messe.de
Trade fair for assembly and handling technology.
Hanover, Germany
22 Oct – 25 Oct 2024
www.euro-blech.de
Sheet metal working technology exhibition.
Taiwan Hardware Show
Taichung, Taiwan
23 Oct – 25 Oct 2024
www.hardwareshow.com.tw
Hardware tools, fasteners and building material show in Asia.
Dresden, Germany
6 Nov 2024
www.schraubtec.com/dresden
German regional trade fairs for screw connections.
Amsterdam, The Netherlands
19 Nov – 21 Nov 2024
www.metstrade.com
Large international B2B exhibition for the marine industry.
The Big 5
Dubai
26 Nov – 29 Nov 2024
www.thebig5.ae
An event for the construction industry acting as the gateway between east and west.
Stuttgart, Germany
3 Dec – 5 Dec 2024
www.adhesivesandbondingexpo-europe.com
Trade fair and conference for industrial bonding products and manufacturing.
New Delhi, India
6 Dec – 8 Dec 2024
www.hardwarefair-india.com
International fair for the hardware and DIY sector.
Munich, Germany
13 Jan – 17 Jan 2025
www.bau-muenchen.com
German trade fair for architecture, materials and systems.
Stafa is one of the renowned wholesalers in Europe for HV bolts, nuts, and washers. We have a large stock of structural bolts which meet the international standards.
Preloaded bolt/nut/washer assemblies
Certified according to EN 14399-4-6 / 10.9 K1 (nut lubricated with MoS2)
Hot dip galvanized according to ISO 10684
TUV Certified
Certificates according to EN 10204/3.1 available
For seven years FASTENER POLAND® has been a key forum for exchanging experiences; learning about new products; and building lasting business relationships in the fastener industry. The fastener sector is now looking ahead to the next event, taking place from 25 th – 26th September at EXPO Kraków.
In addition to Polish suppliers, the list of exhibitors includes 150 exhibitors from all over the world, including companies from the Czech Republic, Denmark, Spain, India, Malta, Germany, Pakistan, Turkey, Taiwan, Italy, China and the United Arab Emirates.
Among the exhibitors already confirmed are: SKAKO Vibration AS, NOEGEL Poland, EKATEC GmbH, TORK Bağlanti Elemanlari, Fastbolt Schraubengroßhandels GmbH, TOGE Dübel GmbH & Co KG, UNBRAKO – Deepak Fasteners Ltd, MEKR´S sro, Achilles Seibert GmbH, pgb-Polska, Inoxdadi Srl, TFC Ltd, Nord-Lock Poland Ltd, BRALO CZ sro, VIPA SpA, DROMET Ltd and many more.
The most modern industrial fasteners and fixings will be presented from screws, through to rivets nuts, pins and wedges, as well as construction fasteners, such as anchors, concrete screws, façade and insulation fasteners, plus advanced assembly and installation systems –with a presentation of the latest riveting devices, screwdrivers and screwdriving systems or mounting brackets, as well as connector production technologies and devices for their storage and distribution.
As well as this, during FASTENER POLAND® there will be expert speeches, training and demonstrations on key industry topics, including
environmental issues such as carbon fees and sustainable development; increased quality and normative requirements; shortened supply chains; technological progress; as well as the rising prices of materials.
Guest registration has been very popular for professionals from construction and industry, who use fasteners to produce products. This is why the fair will be accompanied by a special zone of fasteners for construction, which will enable specialists in the insulation industry, installers of air conditioning, ventilation and refrigeration systems, façade fitters, scaffolding manufacturers, and contractors of industrial and warehouse halls, to establish contacts with suppliers.
With online registration open, everyone who registers will receive a free ID card allowing them to visit the fair and participate in the accompanying programme. Detailed information and registration can be found online.
www.fastenerpoland.pl
Organised by Koelnmesse and the China National Hardware Association, this year’s China International Hardware Show (CIHS) will see more than 2,800 exhibitors cover over 120,000m 2 at the Shanghai New International Expo Centre from 21 st – 23rd October 2024.
CIHS is a one stop B2B platform for industry experts, buyers, visionary leaders and DIY enthusiasts to tap into the thriving Chinese hardware market, as well as professionals seeking to explore new business opportunities.
Renowned brands such as GreatStar, TDC, Wera Werkzeuge, WEDO TOOLS GmbH, Rosver Srl, and Great Wall Precision Industrial Co Ltd, from Germany, Italy, ASEAN, Asia Pacific countries, and China, will be showcasing products, unveiling new offerings and sharing valuable market insights – while establishing extensive networks with global professional buyers.
CIHS 2024 will showcase a comprehensive range of products and solutions, including tools, abrasives, fastening technologies, building hardware, locks, equipment and accessories. It aims to propel the collective development of dual circulation in both the Chinese and global hardware markets, addressing the challenges of a new stage in industrial innovation.
Aiming to provide a rewarding and comprehensive exhibition experience for all visitors, CIHS 2024 offers diverse customised trade activities tailored to the specific needs of professional buyers, industry leaders and hardware enthusiasts. An upgraded hosted buyer programme also encompasses business matchmaking sessions, delegation tours and recommended booth visits. These differentiated solutions are designed to cater to the specific procurement requirements of global buyers across a wide range of product categories and distribution channels.
CIHS 2024 will continue to contribute value added resources in market expansion, network exploration, as well as the latest products and innovative technologies for both supply and demand in the global hardware industry.
Afera, the European Adhesive Tape Association, will be holding its 67 th annual conference themed ‘Taping our future’ at the Hyatt Regency in Thessaloniki, Greece, from 25 th – 27 th September 2024.
The premier event for the European tape industry typically attracts more than 150 participants from 15 countries – across Europe, Asia, the USA and Middle East – for critical networking and deep diving into the hottest tape business issues. Programme and registration information can be found online and Afera has already seen markedly increased rates of early registration and sponsorship.
“What those in our business are looking for is market intelligence, information and advice on regulatory and sustainability matters, as well as tips on the latest tape applications and technologies,” underlines Astrid Lejeune, secretary general of Afera. “Our team scrutinised past participant feedback and has formulated a programme we feel is the best fit for the needs of the business owners and decision makers of our 120 member companies, who represent 80% of European tape manufacturers in volume produced.”
Afera’s annual conference will feature three separately themed working sessions including market data and trends, regulatory affairs and sustainability, as well as current tape applications and technology highlights. Social activities have also been planned to frame and enhance each day’s schedule, such as a ‘five senses’ tour of Thessaloniki and long networking
coffee breaks and organised conference lunches, drinks and dinners on each day.
“We are thrilled to unveil our detailed programme for Afera’s 67 th annual conference, which promises three different days packed with engaging seminars, insightful discussions and great networking experiences for both commodity and speciality tape industry professionals,” highlights Evert Smit, president of Afera and director scouting for sustainability, technology and innovation at Lohmann GmbH & Co KG.
Evert continues: “Attendees get the opportunity to improve their business performance by delving into market data and trends; exploring economic indicators and prospects; navigating regulatory landscapes; uncovering the expectations of notable end users; as well as discovering the latest innovations in product development and company management – all with a focus on sustainability.”
Organised in a different European city each year, and with a new layout and content, Afera’s annual conference is attended by company delegates representing businesses along the adhesive tape industry value chain including primarily manufacturers of tapes; raw materials, machine and packaging suppliers; converters of tapes; research institutions; national tape organisations and other international counterparts.
Here Liljana Goszdziewski, portfolio director for the European Fastener Fairs, gives an insight into what visitors and exhibitors can expect from Fastener Fair Global, which will take place from 25 th – 27 th March 2025 in Stuttgart, Germany.
Fastener Fair Global 2023 was a record breaking event. How will Fastener Fair Global 2025 raise the bar even further?
“Fastener Fair Global 2023 was a tremendous success, breaking records and setting new benchmarks in the fastener industry. For professionals in manufacturing, distribution, and engineering, it was a golden opportunity to network, learn and showcase innovations.
Fastener Fair Global 2025 promises to be an event like no other, building on the success of 2023 and raising the bar even higher. With over 800 exhibitors already having booked a spot in Stuttgart, new features such as the Hand Tool Pavilion, plus the Innovation and Sustainability Pavilion, as well as three days of valuable networking opportunities, mean the show is a must attend for anyone in the fastener industry.”
You mention the Hand Tool Pavilion and the Innovation and Sustainability Pavilion. What will these new areas bring to the show?
“The Hand Tool Pavilion and Innovation and Sustainability Pavilion are exciting additions to the 2025 show and will provide platforms for showcasing cutting edge technologies, products and processes.
The Hand Tool Pavilion will be dedicated to exhibitors specialising in hand tools, allowing them to present the latest innovations and connect with potential customers and partners. Attendees can look forward to seeing demonstrations of the newest tools on the market, learning about advancements in technologies and discovering how these tools can improve operations.
In an era where sustainability is more important than ever, the Innovation and Sustainability Pavilion will highlight products and processes that promote environmental responsibility within the fastener industry. Exhibitors will have the opportunity to present innovations and attendees can gain insights into sustainable practices and technologies. Additionally, Fastener + Fixing Magazine will host the Route to Fastener Innovation Award, recognising the most groundbreaking advancements in the field.”
How are exhibitor bookings going? What is the breakdown of exhibitors at the show?
“Exhibitor sign up for Fastener Fair Global 2025 is progressing at an impressive pace, with 95% of the available space already sold out. This high-level of commitment from exhibitors underscores the event’s significance within the industry. Major players such as Ambrovit SpA, Schäfer + Peters GmbH, Lederer GmbH, Fastbolt Schraubgroßhandels GmbH, FM Metal Fasteners Group SpA, Norm Civata San ve Tic AS, INOXMARE Srl, Alexander Paal GmbH, Stafa Group, Tecfi SpA, Böllhoff,
F.REYHER Nchfg. GmbH & Co KG, MKT Metall-Kunststoff-Technik GmbH & Co KG, pgb Europe N.V, Growermetal SpA, Würth Industrie Service GmbH & Co KG, and WASI GmbH, have all secured spots, ensuring a diverse and comprehensive showcase.
The wide range of exhibitors reflects the comprehensive nature of Fastener Fair Global, making it a must attend event for anyone involved in the fastener industry. The participation of these industry leaders guarantees that attendees will have access to the latest products, technologies, and innovations, providing valuable opportunities for learning and networking.”
“Fastener Fair Global stands out from other fastener related shows in several ways. Firstly, its comprehensive coverage of the whole industry and its wide range of exhibitors from both Europe and further afield. This diversity ensures that visitors can find solutions and innovations relevant to their specific needs.
The introduction of the Innovation and Sustainability Pavilion highlights Fastener Fair Global’s commitment to showcasing cutting edge technologies and promoting sustainable practices. Fastener + Fixing Magazine’s Route to Fastener Innovation Award also celebrates the most significant advancements in the fastener industry.
By exhibiting at Fastener Fair Global, companies can showcase products and innovations to a targeted audience of industry professionals – leading to new business opportunities, partnerships and increased brand recognition.
For those companies interested in exhibiting at Fastener Fair Global 2025, there is still an opportunity to secure a spot. While 95% of the space is already sold, the remaining 5% offers a chance for new exhibitors to join this prestigious event. To apply for an exhibitor spot, visit the Fastener Fair Global website and get in touch with the team.”
www.fastenerfairglobal.com
Fastener Fair Global is just over six months away and exhibitors are already looking forward to the leading trade fair and how they can optimise their presence. With that in mind, we invited a selection of companies to give an insight on why they think Fastener Fair Global 2025 will be one of the best shows yet.
Fastener Fair Global is the well established highlight of the global fastener exhibition calendar. It attracts visitors from all over the world and therefore it is only natural that Fastbolt was one of the first exhibitors at the initial show back in 2005.
Due to our exclusive focus on selling our range of high-quality fasteners to distributors only, Fastener Fair Global gives us the opportunity to meet a high percentage of our existing international customer base. At the same time, we have always been able to establish lots of new relationships through the exhibition.
While the vast majority of our business is nowadays digitalised, the exhibition still plays an important role in offering a physical meeting point. For us the three days in Stuttgart are always extremely busy as we also –besides our existing and potential customers – meet a good number of our worldwide suppliers on our booth.
In current times of complex market situations, and ongoing regulatory changes, it is absolutely essential to take every opportunity to closely communicate with suppliers on the one hand and customers on the other hand. Stuttgart is an ideal venue to catch up on open topics and to initiate new opportunities for the future.
During next year’s show, we will also take the opportunity to update visitors about the building extension of our German central warehouse, as well as the planned introduction of an automated small parts warehouse. Through this new increased stock capacity, we are also planning some very exciting stock range extensions. At the same time, we will also highlight the continued investment into systems and equipment to further improve the efficiency, and stability, of our quality management, trading processes and logistics.
Fastener Fair Global is still some months away, but we are definitely looking forward to presenting our company, product range and stock capacity developments to our trading partners worldwide. The show will also be a good opportunity to discuss changes within the market. Currently we are seeing lots of things developing and the import trade of standard fasteners is going through some important changes. This creates risks and opportunities at the same time for our business. We hope that the overall economic development in Europe, and the world, will improve by Stuttgart in March 2025 – so that our industry can go through this time of changes with solid demand and a positive outlook for the future.
www.fastbolt.com
•
•
•
•
•
We are looking forward to exhibiting at Fastener Fair Global and believe it is one of the most important fairs within the sector – with the show providing the opportunity to meet new potential customers and build long-term relationships.
Fastener Fair Global attracts visitors from all over the world, as well as being the perfect opportunity to meet up with existing customers who are not located near our offices, which is why our team of experts will be on hand to answer questions; provide personalised consultations; and explore how we can tailor our solutions to meet the specific needs of each customer.
At the show, as in previous years, we will present our complete capabilities. We have such a wide range of products and services that we really want to make sure we can help our customers as much as possible. From HV to customised threaded rods; from universal screws to hook anchors; our assortment covers most types of fasteners. Additionally, creating special parts, based on specified drawings, is possible.
Our goal is to provide a comprehensive understanding of how STAFA can be a valuable partner in the projects of our potential customers, offering reliable products of high-quality alongside exceptional customer service.
Fastener Fair Global is more than just an exhibition for us; it’s a chance to engage with the global fastener community, exchange ideas, as well as stay at the forefront of industry trends. For instance, so far 2024 has gone well for us as a business, but there are some challenges that have impacted us, as well as the entire industry, including the Carbon Border Adjustment Mechanism (CBAM) regulation and the increasing prices of sea freight. That is why one of our main focuses
for 2024/25 is decreasing our carbon footprint and ensuring that we, as a company, do our best to improve processes wherever we can. This involves investing in more sustainable materials; optimising our supply chain to reduce emissions; and adopting energy efficient technologies. We are committed to not only meeting regulatory requirements but also setting a benchmark for environmental responsibility in our industry. By continuously innovating and striving for sustainability, we aim to contribute positively to the global effort against climate change –whilst maintaining the highest standards of quality and service for our customers.
We are also currently busy developing a new and improved webshop to ensure customers have the best possible user experience. By combining the robust features of a B2B platform, with the user-friendly look and feel of a B2C platform, we are creating an intuitive interface that is easy to use for every customer. This new platform will feature streamlined navigation, as well as enhanced search capabilities to meet the specific needs of our diverse customer base. Our goal is to provide a seamless and efficient online shopping experience that reflects our commitment to innovation and customer satisfaction. Stay tuned for the launch, as we are confident this new platform will significantly enhance the way our customers interact with our products and services.
www.stafa.nl
Fastener Fair Global is a reference point for all the professionals, manufacturers, and distributors, specialising in fixing systems and fasteners in Europe, the Middle East, Africa and Asia. The history behind this show; the strong support from all the main players in the sector; and the high-quality of the audience; makes this show very attractive for us.
That is why having a presence at the show is a must, as it is a good opportunity to get in contact with our current partners and new potential distributors. It also allows us to present the new products developed during recent months and the improvements we have made to continue to level up our quality and performance.
During the show all our visitors will receive a good overview of our commitment to the sector in developing the best product range, not only on product variety, but also on the best performance compared with competitors.
Our commitment to the service level and efficiency for our customers, along the entire supply chain, will also be present on our booth. This is underlined by us working really hard on the development and putting into service all our resources on digitalisation, online services, B2B eTools, as well as B2C eTools, which help our customers with their sales to customers.
As a business we have also been working hard during the last few years to increase our value to the customers. That is why at Fastener Fair Global 2025 we will show new products, improvements on current products and certifications, as well as a lot of new tools that, we are sure, will make INDEX – A PERFECT FIXING one of the best manufacturers and distributors in the world – offering the best package to the market.
Thanks to the steps we have been taking we have seen good results for the first half of 2024, besides all the difficulties in the world, with a
reasonable increase in market share. We have also managed to keep our stock level stable and provided a good service to customers. Our expectations for the second half is to keep on growing with the same energy, increase the market share and our service levels – to do this we have put a lot of effort into reinforcing our stock and our team. We will also continue to help our partners by providing the best products with the most competitive proposal and best service.
We are a team of people who add value to our customers by offering global solutions as a supplier of semi-finished metal products, screws and fastening systems. Relying on a strong corporate culture, we focus our efforts on delivering a differentiated customer experience; whilst developing new markets, countries, sectors and channels. We can do this thanks to our investments in new products, services, resources, and technology, which helps ensure the competitiveness, reliability and security of our business. www.indexfix.com
For us Fastener Fair Global is the main event for the fastener sector. We always see a lot of familiar faces, as well as meeting new people and companies. During the show you get a good look and feel for what is happening in the market and in which direction it is heading.
We have a history of exhibiting at Fastener Fair Global and we were even present at the very first Stuttgart show, which took place at the old exhibition grounds – close to the city centre. For the 2025 edition visitors to the Don Quichotte stand can expect a warm welcome, along with our famous Dutch hospitality. Of course, our main fixings and fasteners will be on display and our international sales team will be there to answer questions or enquiries – along with an abundance of good coffee and typical Dutch snacks.
As a business we are known for our product innovations and our strategy has more or less shifted to products for electrical installation, which might not be the first products that come to your mind when visiting this particular show, but are more and more distributed by the same type of customers as the ones who are already selling fasteners. These products will still be on display at the show as there are usually customers visiting who are interested in these types of products, alongside the standard fixings and fasteners. It also helps that the Eltefa, a German fair for the electrical sector, is running at the same time, on the same grounds as the Fastener Fair.
During the show we will also talk to visitors about the investments we have made in our production efficiency, including packaging machines, as well as investments in logistics and more sustainable production and packaging – resulting in less energy waste, energy regeneration, as well as more green energy – with a goal to significantly decrease our carbon footprint every year.
Whilst 2024 started slowly, it does seem to be picking up pace and we believe by the end of the year we will be on par with 2023. However, we expect the pace that is building to continue to pick up through the beginning of 2025, which means the market should be in an interesting position come March 2025 and the Fastener Fair Global show.
www.don-quichotte.com
When it comes to the question of whether to exhibit at Fastener Fair Global 2025 there was only one answer for us at Lederer –‘Of course!’ It is one of, if not the most important show within the fastener and fixing sector.
At Lederer we are currently in the first phases of planning for the show and considering how we will design our trade fair appearance in Stuttgart. Of course, there will be news on the latest developments within the business. Of course, we will have all of our important contacts from sales, purchasing and management to meet and chat with visitors. We will also be co-exhibiting with Fastbolt once again. and will have our always famous hospitality that warmly welcomes visitors and guests – again with our longstanding cocktail and catering partners, who ensure a particularly relaxed atmosphere for conversation. Finally, we will have a great quality time during the show, as well as at our aftershow parties on the Tuesday and Wednesday evenings. www.lederer-world.com
Fastener Fair Global is a ‘hot spot’ for technicians, sourcing and more importantly high-class exhibitors – making it the perfect venue to exchange information. No matter if current, or former employees, customers, or vendors, there’s the saying ‘once fasteners, always fasteners’, which makes the show the perfect place to present our new products and innovations to the fastener community.
One of the key aspects for us as a business during the show is to ensure we have ‘open ears’. We‘re going to listen to the challenges of our visitors, to be able to provide the best solution possible – no matter whether it‘s a technical or a logistical solution. Our speciality is working closely together with customers to challenge their applications and make them better with our highly experienced team. By doing this, we can ensure we always find the perfect tool in the KAMAX toolbox for each customer.
At the show we will also be showcasing all the new developments in our product portfolio. These include our long and narrow KXpanded bolts, with up to 600mm length for battery packs, fuel cell stacks, as well as eMotors, which help replace inefficient long threaded rods. We will also be showcasing our KXtreme innovation with ultra high-tensile
strength (up to 1,700 MPa) and maximum ductility – enabling us to increase the preload force of a fastener by up to 45%.
We are also currently defining a standard portfolio for our ultra high-tensile strength KXtreme fasteners. This will enable us to deliver smaller quantities more quickly and make this innovation available to more customers. Of course, we will continue to customise our ultra high strength fasteners to meet all needs of our customers. At the same time, we are concentrating on combining KXtreme with the KXprotect coating. This will enable us to achieve even greater resistance to hydrogen induced stress corrosion cracking than already established solutions.
www.kamax.com
If you like cars you know that Monte Carlo is a must for Formula 1 or Indianapolis for the Indy 500; if you are a fan of painting, you must visit the Louvre in Paris or Prado in Madrid; and when it comes to fasteners there is no doubt that Fastener Fair Global is a mandatory meeting point every two years in Stuttgart, Germany.
This fair is a worldwide event where almost all fastening solutions companies are present. For us at BRALO, it is a fair where quality and innovation are shown, which is why we always look to showcase our products and innovations. That is why at Fastener Fair Global 2025 we will be unveiling a new range of pneumatic tools, with the launch the result of a long period of reflection, research and design. The outcome is truly remarkable and we believe these tools will bring many improvements to the market –supported by a reliable, robust, fast and durable machine.
At BRALO we are continuously up to date and developing new products, in order to guarantee the best response in class to our
customers. That is why we are customising fastening and engineered solutions constantly – as it is one of our strengths.
During the last Fastener Fair Global in 2023, we presented our new battery tool family both for rivets and rivet nuts, with the BT-20 professional battery tool a finalist in the Route to Fastener Innovation Competition – thanks to its power, speed and versatility.
At the show in March our booth will also be designed to attract and engage visitors efficiently – with the BRALO team well prepared to handle enquiries and provide personalised attention. In fact, the country managers of BRALO’s nine European subsidiaries will all be involved.
www.bralo.com
Thanks to its dedication to excellence, Posirol has earned the trust and loyalty of leading brands across Europe – with the company able to produce metal fixing bands that can be used for attaching objects, regardless of shape, in numerous applications.
Established in 2011, Posirol Oy – located in Rauma, the fourth oldest city in Finland, on the eastern shore of the Bothnian Sea – is able to produce a wide range of perforated bands and steel straps, both under its own name, as well as under customers’ own brands.
“We are proud to be the producer behind the success of some of the leading brands within the fixings sector and look forward to continuing to provide them with our fixing band,” states Kim Komaro, CEO at Posirol. “Our partners are happy to work with us because we offer private labels, a wide range of fixing bands and plenty of packing options.”
Used for the securing, supporting and strapping of cables, pipework, ducting, guttering, fencing, lighting, trunking, and general repairs, Posirol’s fixing bands are ideal for all suspension applications and many more superficial installations. The fixing bands are available in galvanised steel, different stainless steel grades, as well as aluminium, and can be produced in a plastic coated band in a variety of colours. The bands are available in 3m, 10m and 25m as a standard length, but the company can also make custom sizes. Plus, Posirol has one of the biggest ranges of hole patters on the market.
“A key factor is that we can offer customers a private labelling service, which has been designed to provide clients with a strategic advantage in the marketplace. We are also constantly implementing advanced technology and regularly improving our products and the efficiency of our operations,” explains Marin Marinov, business development at Posirol. “As a business we are also focused on the adoption of more automation and robotics, and smart manufacturing systems, to enhance our productivity and quality. That is why our strategy is to implement even more automation in our production processes in future to increase efficiency, decrease costs and reduce errors.”
To guarantee the quality of its products, Posirol sources raw materials from reputable suppliers and conducts thorough testing of incoming materials – making inspections at various stages of production to catch and correct defects early – as well as performing tensile strength tests, and other mechanical tests, to ensure product durability and performance.
“We also assess how our products perform under various environmental conditions such as humidity, temperature, corrosion and fire, to ensure the very best quality for our customers,” mentions Marin.
In order to meet the needs of its customers, Posirol introduced a new eco-friendly solution in 2023 – the Eco-Pack cassette – which is an innovative patented packaging that uses significantly less plastic compared to a traditional cassette, making it a more environmentally friendly option. In addition to its ecological benefits, the Eco-Pack is designed to be durable and reliable, ensuring that Posirol’s fixing bands arrive at their destination in perfect condition. “The Eco-Pack cassette is easy to store, transport and use on the construction site,” comments Marin. “It protects users’ hands when they pull the band out and the Eco-Pack cassettes can be reused or recycled after the band is removed.”
Kim concludes: “Our customers know that by partnering with Posirol they get a unique combination of high-quality products, expert knowledge, delivery security and outstanding customer service. We already export to more than 30 countries worldwide, including in Europe, the Middle East, as well as Asia, and we are looking to continue to grow as a business in the future.”
www.posirol.com
Staht has recently made several strategic investments to enhance its product offering including the introduction of Staht® Connect, a software platform that integrates with Staht’s testing equipment – with the aim to modernise testing workflows and ensure data is easily accessible and securely stored.
Staht specialises in manufacturing digital pull testing equipment, including 60kN and 25kN models, designed for various industries requiring the precise and reliable testing of mechanical fastenings amongst other parts. Alongside the hardware, Staht has developed the Staht® Connect App, available for both Android and iOS, which integrates with the digital pull testers to provide ‘real time’ data monitoring, analysis and reporting capabilities.
Staht® Connect is a digital SaaS platform that consists of a suite of software applications, including the development of mobile and web applications, which has the ability to capture geo-located feeds of data from measurement sensors on testing devices. Once recorded digitally, this data is transmitted via a mobile device connected to a Cloud platform; and then to back-end monitoring and reporting workflows for onward presentation and processing.
Staht® Connect can capture intricate pull test data in ‘real time’, with live photo and video capability, as well as providing the ability to analyse the results...”
“The aim of Staht® Connect is to modernise testing workflows, ensuring data is easily accessible and securely stored, which helps enhance operational efficiency,” points out Rob Hirst, managing director at Staht Ltd. “The software platform will also help us on our mission to dramatically optimise working practices within the construction industry’s safety testing – by reducing manual processes, on-site attendance and associated logistical considerations.”
The Staht digital pull tester App is included as standard, with a free lifetime subscription – with no monthly payments or extra charges.
“Staht® Connect is adaptable to a wide range of specific business logic requirements and can offer customisable workflows, as well as test and report fields,” highlights Rob. “Configurable to kN and LBf, Staht® Connect can capture intricate pull test data in ‘real time’, with live photo and video capability, as well as providing the ability to analyse the results from within the App, including a ‘real time’ on-screen data graph. Staht® Connect also features Bluetooth connectivity to ensure Cloud data storage is quick and easy.”
Staht® Connect enables users to share the tests with colleagues and customers, by a simply pressing of a button, as well as the option to upload the data to the Staht® Connect web dashboard, which is supported on all major desktop browsers – providing ‘real time’ data streams, analysis tools and reporting functionality for back office teams.
To add to this, Staht® Connect adds quality assurances, with every Staht product guaranteed through several rigorous measures. “Each product undergoes extensive testing to ensure reliability and accuracy. This includes both in-house testing, external FEA testing and field testing during the R&D phase,” mentions Rob. “Our products are also designed to meet the relevant industry standards and regulations, ensuring compliance with safety and quality benchmarks.”
Rob concludes: “Staht® Connect is just another example of our continuous improvement approach, where we incorporate feedback from customers, and technological advancements, into product development. When this is added to our commitment to sourcing high-quality materials and implementing advanced manufacturing techniques, which helps us maintain our strict quality control throughout the production process, we are able to deliver the highest quality products and a complete service to every customer.”
www.staht.com
JCP, Owlett-Jaton’s speciality fixing division, has expanded its portfolio with over 30 new product lines, including new European Technical Assessments, demonstrating its commitment to the ever changing demands of the construction sector, as well as the needs of its customers.
JCP’s heavy-duty anchor portfolio now includes ETA certified (ETA – 20/0727) pan head bi-metal ankerbolts, drop-in anchors and lipped drop-in anchors, reassuring contractors about reliability and quality, particularly when safety and compliance are critical. The two new ranges of bright zinc plated drop-in anchors have been launched as a cost-effective alternative to the existing popular ETA drop-in anchor range, bringing the total number of options to eight – six of which are ETA certified.
A bi-metal masonry screw has also been added to the heavy-duty anchor range and is available in three sizes. The high-quality masonry screw speeds up installation time, enables thread cutting and avoids corrosion.
Along with the new range additions, two of the current ETA ankerbolt lines (ETA – 15/0040) have been extended, providing customers with a wider variety of size options. This brings the JCP
pgb-Europe has added four different types of ETA certified (ETA – 24/0064) sandwich panel screws to its wide range – each with a unique design depending on the application.
Featuring a 19mm EPDM sealing washer, these screws have self-drilling or self-tapping capabilities and are made of hardened steel with a C3 coating, making them very durable in demanding environments. Each screw is clearly marked with the drill point size, which is related to the drilling capacity of the screws. The panel screws come in four different types; SWPS-3 – drill point type 3 with a drilling capacity up to 6mm maximum; SWPS-5 –drill point type 5 with a drilling capacity up to 12mm maximum; SWPS-7 – drill point type 7 with a drilling capacity up to 20mm maximum; and the SWPS-C – for applications in wood or concrete with a special point and high-low thread. pgb-Europe highlights: “An ETA is an important technical document that enables manufacturers to affix CE Marking to innovative construction products that are not covered by a harmonised European Norm (hEN). The CE Marking ensures that products meet EU safety, health and environmental protection requirements.” www.pgb-europe.com
range of ankerbolts to over 100 lines, with various head and finish options available.
The range of self-drilling screws has also grown significantly over the last three years, becoming a popular choice for customers. For example, a woodfix high-thread screw for timber in BZP has been introduced in five sizes and is ideal for fastening composite panels to wood. There is also a new fibre cement screw for timber, which offers an alternative to the existing fibre cement screws for steel. Finally, line extensions have been added to the range of metalfix wafer head self-drilling screws.
The chemical anchors range has also seen the introduction of an additional 410ml injection tool with improved features for the professional installer. As well as the injection tool, three new plastic coated fixing bands are now available and come in three colours – black, white and red – giving customers ten fixing band lines to select from. www.jcpfixings.co.uk
Woodies® Ultimate screws from A.S.F Fischer B.V, are renowned for their high-quality and reliability in the construction sector, with an ETA certification (ETA – 17/0286) confirming they meet stringent European standards for safety, performance and durability.
Available in a number of ranges, including the Shield Outdoor range with ep5 coating, the screws ensure a longer lifespan and better resistance to corrosion. Woodies® Ultimate Shield Outdoor is available in various types of screws including waferhead, countersunk head – full and partial thread – decking screws, as well as hinge screws. They are also available in Blackline to match black surfaces. Additionally, the screws have an optimised thread design to provide a secure anchorage –making them versatile and reliable in use. All Woodies® Ultimate Shield screws also have CE Marking and are RoHS and chrome 6 free.
“Thanks to the relevant certificates, in particular the ETA certification, users can trust that Woodies® screws consistently perform well – even under challenging conditions. The certification not only offers peace of mind but also confirms the technical superiority of the screws,” comments A.S.F Fischer. “In a market where quality and safety are paramount, Woodies® Ultimate screws stand out by adhering to the ETA, making them a preferred choice for professionals who do not want to compromise.”
Following an agreement with the European Organisation of Technical Assessments, here is a list of recent ETAs published in the last two months on the EOTA website.
It is important to note that existing ETAs may be amended or withdrawn so this list should not be considered definitive. For further information and a full list of valid ETAs visit EOTA’s website. If you have recently received an ETA, and would like to have it included in our table, please email us the full details at editor@verulammedia.com
ETA NUMBER TRADE NAME COMPANY
Mechanical fasteners for use in concrete
www.eota.eu
Bonded fasteners for use in concrete
ETA - 24/0567 Akfix C920 Epoxy Acrylate Styrene Free Chemical Anchor
ETA - 24/0568 J-FIX POLYESTER RESIN
ETA - 24/0570 J-FIX VINYLESTER RESIN
Akkim Yapı Kimyasalları AS
Hexstone Ltd T/A JCP
Construction Products
Hexstone Ltd T/A JCP
Construction Products
ETA - 24/0571 CFM PS Trutek Fasteners Polska Sp z o.o
ETA - 24/0572 TCM V Trutek Fasteners Polska Sp z o.o
ETA - 24/0573 ROX GU Chemical Anchor Teknik Alet AS
ETA - 24/0654 Sismacast EP Bonded anchor UNICALCE SpA
ETA - 24/0657 FORTE PRESA IBRIDO/HYBRID 9.3 SARATOGA INT SFORZA SpA
ETA - 24/0683 AnchorMark POLY SF Anchormark PTY Ltd
ETA - 24/0722 FORFIX 1 BMF SPRL
ETA - 24/0759 EMS Dubell F.1311 PE Chemical Anchor METSAN ENDÜSTRIYEL YAPISTIRICILAR TIC AS
Injection anchors for use in masonry
ETA - 24/0684 AnchorMark POLY SF Anchormark PTY Ltd
Bonded anchors for use in concrete
ETA - 24/0658 FORTE PRESA IBRIDO/HYBRID 9.3 SARATOGA INT. SFORZA SpA
Screws and threaded rods for use in timber constructions
ETA - 24/0711 PanelFix Schrauben, HapaFix Schrauben, SopaFix Schrauben INTRA-TEC GmbH
Fastenings for metal
ETA - 24/0547 Fastening Screws JT, JZ and JF for fastening of wall brackets EJOT SE & Co KG
ETA - 24/0546 G&B Fissaggi concrete screw GETO PLUS TMKI CE1 G&B Fissaggi Srl
ETA - 24/0731 Torque-controlled expansion anchor Bremick PTY Ltd Australia
Linear joint and gap seals
ETA - 24/0611 Fireguard A+ 566 Dana Lim AS
ETA - 24/0613 Fireguard GR570 Dana Lim AS
ETA - 24/0661 FireFree F766 Fugeforsegler Scandi Supply AS
ETA - 24/0754 Rawlplug RFR ACRYLIC Rawlplug SA
Fasteners for external wall claddings
ETA - 24/0591 TUA Trutek Fasteners Polska Sp z o.o
ETA - 24/0556 Cladding kit type URBAN T Zürcher Ziegeleien AG
ETA - 24/0678 Cladding kit type URBAN UL Zürcher Ziegeleien AG
Systems for post-installed rebar connections
ETA - 24/0655 Sismacast EP for rebar connections UNICALCE SpA
ETICS with renderings
ETA - 24/0621 ISOLK8 ECO Isolkappa Italia Srl
ETA - 24/0626 KlimaExpert ETA Kerakoll SpA
Three dimensional nailing plates
ETA - 24/0542 OBI Angle Brackets and Hold Downs OBI Group Sourcing GmbH
INDEX® – A PERFECT FIXING has taken over the full production of its TN4S nylon plugs, reaffirming its commitment to quality and innovation in the fastening industry.
This strategic decision enables INDEX® - A PERFECT FIXING to be in control of every stage of the production process, ensuring that its high-quality standards are reflected in every part.
This evolution not only guarantees the durability and performance of the products but also allows fast adaptability to market demands, thanks to the efficient implementation of continuous improvements in the production process.
This progress underlines INDEX® - A PERFECT FIXING ’s commitment to excellence and innovation, reinforcing its position as an expert manufacturer of fastening systems. www.indexfix.com
At the Pol’and’Rock Festival in Czaplinek, Klimas Wkręt-met has created the largest painting in Poland made of screws, together with the participants of one of the biggest music events in the country.
Back in April, the manufacturer also surprised with a splendid opening of the exhibition ‘Screwed Art’, during which it presented twelve paintings, also made of screws. By using different lengths of screws the paintings become spatial and three dimensional. The play of light on the heads makes these spaces come alive and the very interpretations of classic works of world and Polish painting, of which there are already more than twenty in the author’s KLIMAS art gallery, can be rediscovered.
At the Pol’and’Rock Festival the brand went a step further and in the same unorthodox technique decided to make the largest screw mosaic in the country, involving thousands of people in the effort. The record breaking painting made of KMWHT branded woodscrews is 16m 2,depicting eight characteristic buildings from around the world, including the Leaning Tower of Pisa, London’s Big Ben, the Syndey Opera House and India’s Taj Mahal, among others, against a colourful background.
Everything went according to plan and the brand celebrated the successful completion of the project with festival attendees. The last ten screws were screwed in to the accompaniment of a countdown, applause rang out and glittering confetti was sprinkled. There was much to celebrate, as all indications are that the Klimas brand set a Polish record in these unusual festival circumstances.
www.klimas.com
www.don-quichotte.com
ForgeFix has further strengthened its sales team with the appointment of James Blamire, who will oversee both the north and the north-west of England – as he aims to further consolidate the business’s UK market.
Speaking on his new appointment, James commented: “I’ve joined ForgeFix at an exciting time and I plan to position the company in the best possible stead for its promising future plans. As such, my aim is to hone my current skills and take helm of the north and north-west sales region by fostering those strong client relationships that makes ForgeFix the value added supplier it is.”
Head of Sales Paul Simpson added: “James has fitted in great with our sales team and has already started making significant contributions. I look forward to seeing what we can achieve together.”
In response to customer feedback, Scell-it UK has streamlined its offering to introduce two cutting edge, new formula and new look resins – the Universal all in one resin and the High Load resin for tougher applications.
Scell-it UK’s Universal resin is an all-round general purpose polyester styrene-free resin, suitable for a variety of applications, and has an ETA (Option 7) for uncracked concrete. The High Load vinylester resin is designed to conquer demanding construction challenges – suitable for high load applications and has an Option 1 ETA for uncracked and cracked concrete.
EuroTec states that its Lifting Anchor and Lifting Anchor Mini help ensure efficiency and safety in timber construction, thanks to the safer lifting of components, of varying sizes, as well as improved handling to simplify assembly processes.
The Lifting Anchor Mini is specially designed for lighter loads in timber construction and is characterised by its easy handling in glulam and CLT. Its collar on the top edge prevents it from slipping through the drill hole, ensuring safe handling during the lifting process. The Lifting Anchor offers similar advantages as the mini version, but is designed for heavier loads. It is often used to lift and transport larger, prefabricated wall modules in timber construction and is also reusable thanks to its screw fixing.
Heavy-duty chemical fixings by fischer have been used to anchor safety hooks into the cliff face of Mägdeberg, a mountain with a height of 654.2m located in the middle of the southern German Hegau landscape of volcanoes and ruins, in order to restore a climbing crag.
To restore the Mägdeberg climbing crag, compound hooks that sit flush against the rock were used together with the fischer two component FIS V Plus injection mortar, which is quick and easy to use and provides a high-level of safety in extreme conditions – now including securing climbing hooks in high, steep mountains.
Taiwanese screw manufacturer Fong Prean has introduced MSword screws, which have been specifically designed for hardwood-to-hardwood applications and feature sword points and unique thread – meaning no pre-drilling is required on heavy-duty wood.
Fong Prean Industrial Co Ltd points out that the MSword screws are perfect for various decking materials, including hardwood and composite. Made from stainless steel, they also present high corrosion resistance, which makes them ideal for outdoor use. The MS head design enhances stability and ensures a perfect countersunk finish without burrs. Available in sizes from M3 to M8, and lengths from 25mm – 400mm, Fong Prean can also provide customised specifications to meet customers’ project demands.
LIGNOLOC® wooden nails for structural timber construction have been granted a European Technical Assessment (ETA) and can now be used in loadbearing timber constructions throughout the EU – especially timber-to-timber or panel-to-timber connections.
Created by Raimund Beck KG, LIGNOLOC ® ’s approval applies to the nails without a head and enables the planning, design and execution of load-bearing connections in timber frame construction. The provisions made are based on an assumed intended working life of the LIGNOLOC ® nails of 50 years.
Through strategic acquisitions SurTec Group has established itself as a comprehensive partner for the global fastener industry, with the Group able to offer a unique technical consulting service, as well as a complete portfolio of products, for any possible function a coating can provide on a blank fastener.
Belonging to the Freudenberg Group, SurTec develops, manufactures and distributes chemical specialities for surface treatment worldwide. In 2022 the Group acquired omniTECHNIK and precote® USA, including the precote® products for locking, sealing and clamping. In addition, SurTec also inherited the anti-friction coatings (bonded coatings) from sister companies OKS Spezialschmierstoffe GmbH and Klüber Lubrication.
Thanks to its full product portfolio, global reach, and the experience within the business, SurTec is able to work with design engineers and guarantee they get the ‘best in class’ technical consulting and products for their requirements – for every type of sector and market.
“If an engineer needs a new screw design to ensure a certain corrosion protection, plus a guaranteed locking function on the thread; a sealing function under the head; as well as a friction control for the installation torque; they need to approach three or even four different companies in order to get the right products – with no guarantee the coatings will work together,” points out Dr Sebastian Thau, global product manager, functional coatings at SurTec Group. “By working with SurTec, the
engineer can find the best system solution, such as SurTec 717 and SurTec 556 RT for corrosion protection, a SurTec Coat for friction control, precote® 85 for thread locking and precote® 15 for underhead sealing. We are able to meet all their needs, helping to save time and money, as well as ensure the highest quality products with a first-class service.”
“Thanks to these recent acquisitions, the SurTec portfolio covers the full range of surface treatments required, with the five fields of applications including functional coatings, functional and decorative electroplating, metal pre-treatment and industrial parts cleaning,” states Dr Jens Krömer, global sales and marketing manager at SurTec Group.
“The set-up with precote® as a brand of SurTec also further strengthens our strong position on the market. Both SurTec and precote® are well known on the market for outstanding technical service and we have kept the specialised teams for each product line, whilst also cooperating closely together in customer projects and F&E projects. In addition, we have a new global expert team for anti-friction coatings as well.”
Headquartered in Bensheim, Germany, SurTec Group is represented in more than 40 countries with its own subsidiaries and global partner network. “With modern and sustainable developments, and global technical centres, SurTec is leading the way within the sector – using decades of experience to develop environmentally sustainable and high performance finishing processes,” reports Dr Jens Krömer. “We are also certified to the international standard ISO 9001 (quality management), as well as according to OHSAS 18001 or ISO 45001 and ISO 14001 – underlining the important business objectives of occupational health and safety, as well as environmental sustainability and resource conservation.”
Corrosion protection
Reduced friction:
One time installation
Multi time use
Anti rattle & squeaking
Reduced stick-slip
Wear resistance
Conductivity
Locking function
Sealing function
Clamping function
SurTec International GmbH
Neuhofstraße 9 |64625 Bensheim info@surtec.com | www.SurTec.com
As specialists in functional coatings, we combine expertise in the coating and finishing segment of metals (especially fasteners such as screws, etc.) and plastics.
With SurTec, our customers receive a go-to expert for essential fastener functions.
We are part of SurTec, supplier of chemical specialities for surface treatment
SurTec is a group of companies within Freudenberg, a familiyowned, renowned, German-based, and globally operating business.
Featuring revolutionary potential in the production of parts with a shank length up to 165mm, and the ability to feed wire lengths up to 200mm, the new CS 004 machine – available from Carlo Salvi from October 2024 – completes the Italian manufacturer’s range of double stroke headers.
With the possibility of forming parts with head diameters of 22mm, the new CS 004 stands out as a versatile and powerful solution for a wide range of applications. With a maximum production speed of 180ppm, the header delivers an impressive mix of performance and precision.
This new machine not only ensures high versatility in the production of long parts, but also stands out for its flexibility and precision. The header has been designed to deliver accurate and repeatable results, enabling fastener manufacturers to efficiently obtain high-quality products. Furthermore, with the CS 004, Carlo Salvi SpA aims to become a key player in the construction industry.
740
The ability to produce parts with new extended lengths, together with the possibility of forming wire with a diameter ranging from 4mm to 10mm, positions this machine as the essential ally for manufacturers looking for efficiency, versatility, and quality, in forming essential parts for the construction industry.
The new header has been designed with a series of innovations that further enhance its performance and reliability, ensuring superior results and a positive impact on overall productivity.
One distinctive feature of the CS 004 is the revolutionary part transfer system. The phase positioning based on the length of the piece has become more ergonomic and faster, thanks to a cam placed in the operator’s area, whose access and adjustment is simplified by loosening two screws. This innovation not only improves the efficiency of the production process but also represents Carlo Salvi’s clear commitment to workplace ergonomics.
Another revolutionary feature of the new CS 004 is the condition monitoring system. Strategically positioned sensors constantly monitor the machine temperature, preventing seizures and major damages that
The CS 004 marks a commitment to innovation that will redefine the landscape of precision part manufacturing machines.”
could cause significant machine downtime. The use of digital pressure switches in the lubrication circuits enables the ‘real time’ monitoring of the lubricant pressure, preventing damage to hydraulic pumps and mechanical components. Moreover, all this data can be integrated with Industry 4.0 technology, placing the machine on the front line of the fourth industrial revolution.
The CS 004 also stands out for its brand new oil tank with a recovery pump for collecting any accidental spills. This eco-friendly solution prevents the outflow of oil on the floor, avoiding possible leaks into the ground and confirming Carlo Salvi’s commitment to transitioning to more sustainable practices.
The parts conveying system with oil recovery has also been improved to ensure greater efficiency. Moreover, fume extraction directly from the collection funnel prevents oily films and vapours in the operators’ area and contributes towards maintaining a safer workspace.
As well as this, the CS 004 comes with a bedframe already prepared for the installation of two types of inductor coils in the die holder and cartridge right in the bedframe, providing the versatility of cold and warm forging as standard, which meets various production requirements.
Finally, the position of the wire straightening unit outside the machine, with an ergonomic platform for all adjustments and maintenance on the wire inlet side, emphasises the company’s focus on practicality and ergonomics. Carlo Salvi underlines: “The CS 004 will be ready for its market debut by the end of October 2024. This means that companies seeking cutting edge precision part production should prepare for a new standard of performance, versatility, and reliability, which promises to change the way the production of fastening systems is conceived.”
“The CS 004 marks a commitment to innovation that will redefine the landscape of precision part manufacturing machines. The machine is on its way, and Carlo Salvi is ready to lead the industry to new standards of excellence. We eagerly await the beginning of this new era.”
www.carlosalvi.com
TXAS’: Two-section thread replaces full thread!
Greenhouse gases investigation : 2023 Carbon footprint : 2023
Videx Machine Engineering Ltd has completed its range of fully automatic lines with the addition of a line for large diameter U-bolts and long straight studs, from straight bars or from coils.
Designed to work automatically without operator intervention, with coil or bar raw material, the new lines will cut to length from straight bars or coil; chamfer both ends; carry out thread rolling on both ends at the same time; as well as bend to shape.
The difference to traditional machines is the Smart-Transfer, which controls all the machines in the line. The Smart-Transfer dictates the line speed and controls the free flow of material from one machine to the other, stopping the line in case of any fault. The supervisor only needs to handle the feeding of the coils or bars and the discharge of the finished parts.
The new lines are available up to M27 high-tensile and will soon be available up to M33. The parts feed into the chamfer station, the thread
With a philosophy to not discard anything, TLM Srl is specialising in a comprehensive reconditioning process for TLM machines, or those from other manufacturers, to update, modernise and make older machines more efficient.
Recently, the Italian manufacturer acquired a very old thread rolling machine from a client, one of the first built by TLM and completely overhauled and modernised it by updating its transmission. Today, this thread roller is hard to distinguish from a new machine, having been transformed into a combined machine by adding a state of the art pointing machine at the rear.
TLM explains: “We examine the condition of the machinery and evaluate with our clients the most cost-effective actions to undertake. This model of thread rolling machine upgrade ensures savings on purchase costs, easier adjustment and includes a specific warranty. The result is clearly visible – a thread roller that looks new, with the versatility of a combined machine.”
rolling station and the bending station are fully controlled by sensors that make sure the parts always feed parallel. The machines are fully protected from improper feed, thus avoiding occasional failures and resulting in higher feed rates and longer die life.
The new lines are equipped with quick change features, taking the guess work away from the operator, as well as enabling efficient production in small batches of 200 – 500 pieces. The new lines can also manufacture long studs up to 6m long, with threads on both ends. Extrusion of the bar ends and other secondary operations, such as facing and drilling, can also be supported by adding stations.
www.videx-machine.com
CAN-ENG Furnaces International Ltd has been awarded two contracts for its high capacity line of mesh belt heat treatment systems, for the processing of high volume, speciality automotive components.
Including oil quench hardening and salt quench austempering capabilities, the two systems being supplied were chosen by both clients to replace existing systems that could not meet the growing demands of customers.
The new treatment systems feature low energy consumption, reduced part mixing, reduced part damage and part distortion potential, as well as high uptime productivity when compared to conventional conveyor furnace designs.
These systems are currently being commissioned and include a mesh belt furnace system, oil quench and salt quench systems, post quench wash systems, CAN-ENG PET™ SCADA system and integrated controls. These contracts represent the continued interest in CAN-ENG’s mesh belt heat systems and will further increase CAN-ENG’s supply base both in North America and abroad.
WAFIOS has developed a new simple and robust machine for nail production, the WAFIOS HN 4-80, which separates ‘tip scrap’ in a container, eliminating the need for nails to be cleaned in a further work step.
WAFIOS has been supplying its wire nail machines worldwide for decades, however its proven and robust N 31 and N 41 machines had potential for further development. The so called ‘tip scrap’ – small metal splinters – inevitably accumulate when cutting the nail tips, so the nails must then be painstakingly cleaned in a further work step.
This gave the experts at WAFIOS Umformtechnik GmbH the idea of redesigning these nail machines on the basis of numerous discussions with users. The result is the HN 4-80 – a modern and application orientated, yet simple and robust, machine for nail production.
Wire diameters of 1.8mm – 4mm can be processed into pin lengths of 13mm – 80mm. The technical similarities between the HN 4-80 and the old N series make the changeover very easy for the operating personnel, as existing tools can be used. There is also familiarisation with the new system and the machine is purely mechanical, making it robust, reliable and easy to maintain.
The key feature of the new machine is an encapsulated work area, which houses the dust and ‘tip scrap’. The ‘tip scrap’ is then separated from the nails, by falling into a separate container. This helps to save costs as the oil free ‘tip scrap’ can be resold as pure metal scrap.
A leading Turkish bolt manufacturer has installed a Gi-360T high-speed vision inspection system from General Inspection LLC to upgrade its quality control process and highlight a dedication to precision and reliability in production.
The Gi-360T system boasts advanced technology, including four laser beams and eight detector 360° laser gauging, which ensures comprehensive dimensional analysis and precise measurements from every angle. Operating on a Windows 11 platform, the system provides a seamless and user-friendly interface. An integrated velocity gauge also offers accurate length measurements, while the machine’s rail mounted set-up enables a versatile two position bowl configuration, providing ultimate operational flexibility.
A standout feature of this system is the dual-purpose vibratory feeder system that efficiently handles parts with and without heads, significantly reducing changeover time and eliminating the need for multiple machines. The dual metering system ensures smooth and consistent feed of parts into the inspection system, maximising efficiency and minimising downtime.
Additional capabilities of the Gi-360T system include an on-track vision station, with a high-resolution camera, and custom LED illumination for detailed visual inspection of the top of heads and recess features, such as broken punch.
This comprehensive inspection system significantly improves the Turkish bolt manufacturer’s quality control process, customer satisfaction, as well as overall production efficiency, demonstrating its commitment to excellence in manufacturing.
ASAHI OKUMA AT810 (2 machines) 8x100 mm, 200 ppm, 7 5 tons 1992
NATIONAL 34 6 5x55 mm 200 ppm IAC sound enclosure 1985
KLOSE LP200-10 10x200 mm, 90 ppm, 14 tons 1999 unused since 2005
SALVI 243 (4 machines) 5x25 mm, 350ppm, bushing cutoff, sound encl 1990
NATIONAL 500 (3 machines) 14x50 mm 100 ppm Universal Transfer TKO 1986
SACMA SP260 - 10 5x65 mm, 275 ppm, PKO 20 mm, 30 kW 1988
MULTIPRESS MP510S 12x100mm, 50-200ppm, 16 tons 2000
NATIONAL 625 S3 LS 19/16x100 mm, 150 ppm, 24 tons, sound enclosure 1988
CHUN ZU CH20S 20x150mm 35ppm 250 tons load 23 tons 2014 CE
DRAWERS & OTHER MACHINES
RMG 1416 25 4mm, capstan 1300mm, 7 5 m/min, motor 25 HP 2006
STREICHER UNICUT 10 Nut Tapper M3-M12 max part dia 25 mm 4 500 pph 1999
TRANSCO TM20 vibratory bowl 2015 CE WAFIOS FTU 4 3-98 CNC coiling and bending center (2 mach ) 1995 & 1999 CE
By Helmut Fischer GmbH
When choosing the right X-ray fluorescence (XRF) analyser to measure coating thicknesses and analyse materials non-destructively, contact-free, and conveniently, investment costs are always an important aspect. However, it is important to determine the ideal measuring device with the optimum equipment against the background of the given requirements and objectives – not just the most expensive measuring device.
The value of the measurement instrument depends on the complexity of the requirements. In order to find a suitable XRF instrument in relation to a specific measuring task, all possible influencing factors must be taken into account –sample type, sample size, sample geometry, coating thickness range, necessary spot size, measurement mode (coating thickness measurement and/or material analysis), the complexity of the measurement task, number of coatings, as well as the tolerances of the process to be monitored.
All XRF instruments have the same basic design, as Figure One shows. They consist of an X-ray tube for generating X-rays and a detector for detecting fluorescence radiation. These and other components are available in different variants in order to optimally solve the user’s measuring task depending on needs and requirements.
At Fischer, users can choose from the three most essential detector types.”
In general, the detector detects the fluorescence radiation and measures it with the highest accuracy. The detector type determines which measurement tasks can be solved with the XRF instrument. At Fischer, users can choose from the three most essential detector types. These are the proportional counter tube with lower energy resolution but higher count rate; the silicon PIN diode (Si-PIN); and silicon drift detector (SDD) with excellent energy resolution for selective peak evaluation.
The proportional counter tube is the most favourable variant for simple coating thickness measurements in the range of about 0.1µm –50µm, depending on the coating system. It offers a vast active detector area with a slightly curved window, bringing significant advantages when a measuring distance of 20mm – 80mm is required.
Good measurement results can be achieved since a high proportion of fluorescence radiation reaches the detector due to the large detector window. In addition, the proportional counter tube is significantly less sensitive with regard to the accuracy of the specimen alignment to the detector, the measuring distance setting and specimen geometry.
The Si-PIN semiconductor detector offers a higher energy resolution than the proportional counter tube. It can be used for more sophisticated coating thickness measurements, as well as for material analysis. A slightly longer measurement time is required for small measurement spots.
Finally, the SDD is the most powerful detector, realising the measurement of layer thicknesses in the nanometer range and complex multilayer tasks. The SDD also offers the best performance when investigating the elemental composition of materials, with an application range from sodium, in vacuum, to uranium. Especially elements that occur in deficient concentrations are also detected without any problems with the SDD. Detection limits in the parts per million (ppm) range are possible.
Standard and microfocus tubes are available depending on the measurement application, with microfocus tubes enabling
precise results even with small measuring spots and thin layers. The energy spectrum of the primary X-ray radiation with which the elements of the sample are excited is determined, among other things, by the anode material of the X-ray tube. Depending on the element range and detection limit, the appropriate excitation condition must be selected.
Very often, the tungsten anode is used because it produces a particularly intense and versatile spectrum. Depending on the application or measurement requirement, rhodium, molybdenum and chromium anodes are also available.
To define the measuring spot on the sample, the cross section of the primary beam is limited. Generally, the measuring area should be larger than the measuring spot. For optimum precision, the measuring spot should be as large as possible. For cylindrical parts, the specimen diameter should be four times larger than the diameter of the measuring spot. Therefore, additional collimators and capillary optics are available concerning different part geometries and sizes of the measuring area.
Collimators enable a measurement spot size of several millimetres to approximately 100µm, depending on the measurement distance. However, with smaller measuring spots, less primary radiation reaches the sample, which is why the fluorescence signal is strongly attenuated. So called polycapillary optics can remedy this. These consist of structured glass with microscopic cavities that focus a large part of the primary radiation onto a tiny spot – up to 10µm in diameter.
It is recommended to use X-rays that measure in a top down direction as they offer numerous benefits including laser pointer, which allows the operator to position the sample easily, as well as a programmable XY stage that enables multiple samples with multiple points to be measured simultaneously. Moreover, these X-rays are capable of measuring samples that have a height of 80mm and samples that have recesses.
…users from a wide range of industries have the opportunity to select the measuring instrument for solving their specific measuring task.”
The measurement environment determines which elements can be analysed and which detection limits can be achieved. Air is the simplest and most cost-effective measurement environment – suitable for the vast majority of applications.
However, a certain amount of scattering and absorption of the fluorescence signals takes place through the air. This circumstance is almost negligible for elements with a higher atomic number. The absorption is significant for light elements such as aluminium or silicon, resulting in a mostly insufficient signal-to-noise ratio. With the support of a helium purge or a vacuum, the signal-to-noise ratios can be increased, thus optimising the detection limit and measurement precision.
Fischer achieves a high-quality measurement result for many applications with only a few components. During the development of its XRF instruments, special attention is paid to the requirements and objectives in daily practice and a wide variety of variations and combinations of XRF components can be found. Thanks to this bandwidth, users from a wide range of industries have the opportunity to select the measuring instrument that offer the optimum equipment for solving specific measuring tasks.
The University of Strathclyde’s Advanced Forming Research Centre (AFRC), part of the National Manufacturing Institute Scotland (NMIS), has added another internationally recognised accreditation to its name, having attained ISO 17025 for its mechanical testing laboratory.
This achievement underscores the centre’s commitment to continuous improvement and meeting the high-quality standards expected by the businesses it helps to overcome manufacturing challenges, as well as become more competitive.
Awarded by the United Kingdom Accreditation Service (UKAS), the AFRC, which is also part of the High Value Manufacturing Catapult (HVMC) has secured the gold standard for four mechanical testing techniques. ISO 17025 is widely acknowledged as the benchmark of excellence for testing and calibration laboratories, focusing heavily on technical competence.
Notably, the centre has become the first in the UK to be accredited for elevated compression testing up to 1,100°C as per the National Physical Laboratory’s good practice guide. It has also achieved accreditation for its standards in room temperature compression testing, room temperature tensile testing, as well as elevated temperature tensile testing up to 1,000°C.
The latest certification adds to the AFRC’s existing ISO 17025 for residual stress analysis, as well as ISO 9001 and ISO 45001 (18001) for creating and maintaining a quality management system and health and safety standards, respectively.
With numerous years of industry experience, the AFRC’s mechanical testing team demonstrated its technical competency throughout the rigorous benchmarking process. Underpinned by the centre’s leading research, mechanical testing services are available to businesses of all sizes – seeking assistance in checking parts used across a range of sectors from automotive to aerospace.
The XSeeker™ 8000 benchtop computer tomograph from Shimadzu Corporation, a Japan-based specialist in analytical instrumentation and testing equipment, is now available in Europe.
Marking the company’s first foray into the European industrial CT systems sector, building on a rich history of experience in Japan, the XSeeker™ 8000 has been designed for simplicity. It is the smallest, lightest benchtop CT system in its X-ray output class and is equipped with a high output X-ray generator and a high-resolution flat panel detector.
Despite its compact size, the XSeeker™ 8000 is a powerful system with a high X-ray output of 160kV, making it ideal for the analysis of small sized components such as plastic mouldings, aluminium die casts and other metals directly next to the production line, including thick, hard to penetrate parts.
A high image quality and functionality is also ensured with an input resolution equivalent to 5.6 million pixels. With clear image quality, and high throughput, the XSeeker™ 8000 supports applications in a wide range of situations, from detailed observations in product development and quality evaluation to inspections at machining sites.
The system provides high accuracy scanning across a wide 100mm diameter field of view size, as well as being optimised for inspections, offering a three step scanning process and operation at the push of a button – with scanning taking as little as 12 seconds and high-speed reconstruction calculations possible.
In today’s fast paced business environment, companies are always on the lookout for ways to streamline operations and gain a competitive edge. Here Qboid UK, a provider of handheld dimensioning solutions designed to improve the efficiency and profitability of warehouse operations, outlines the benefits of mobile dimensioning and why the technology is gaining momentum in the world of warehousing and logistics.
Mobile dimensioning technology uses advanced dimensional scanning algorithms to capture the dimensions of packages and shipments using a mobile device. The process typically involves taking a series of photographs or scans of the package from different angles, which are then processed by the software application to calculate the dimensions.
Some mobile dimensioning solutions also include built-in augmented reality features, which can help to further improve accuracy and reduce errors. For example, the App may provide visual cues or guidelines to help the user capture the package dimensions more accurately.
Combining the power of mobile devices with advanced dimensional scanning technology – to provide accurate ‘real time’ data on packages and shipments – means mobile dimensioning can transform the way companies manage inventory and logistics. By eliminating the need for manual measurements and calculations, mobile dimensioning can save time, reduce errors and improve efficiency across the entire supply chain. With mobile dimensioning, warehouse operators can quickly and easily capture the dimensions of packages and shipments using their mobile device, without the need for any additional equipment or hardware.
This technology can also help logistics managers optimise warehouse space and improve shipping processes. By accurately measuring the dimensions of packages and shipments, companies can better plan and allocate warehouse space, ensuring that shipments are loaded onto trucks and planes in the most efficient way possible. This can help to reduce shipping costs, improve delivery times and enhance the overall customer experience.
Offering several key advantages over traditional methods of measuring and calculating package dimensions, mobile dimensioing is much faster and more efficient, as well as being more accurate and reliable. Manual measurements are often prone to errors and inconsistencies, especially when it comes to irregularly shaped packages. Mobile dimensioning uses advanced dimensional scanning technology
to ensure measurements are accurate and consistent, regardless of the shape or size of the package.
Finally, mobile dimensioning is more costeffective. Traditional methods of measuring package dimensions often require additional hardware or equipment, which can be expensive to purchase and maintain. Mobile dimensioning, on the other hand, requires nothing more than a mobile device and a software application, making it a much more affordable solution.
The technology can also help to improve efficiency in supply chain management. By providing accurate and ‘real time’ data on package dimensions, logistics managers can better plan and allocate warehouse space, as well as optimise shipping routes and reduce the number of trucks required for each shipment.
This can help to reduce shipping costs, improve delivery times and enhance the overall customer experience. By streamlining the supply chain, and reducing the time and resources required to manage inventory and logistics, companies can become more competitive and better positioned to meet the demands of today’s fast paced business environment. While mobile dimensioning offers many benefits, there are also some challenges that companies may face when adopting this technology. One of the biggest challenges is ensuring the software application is compatible with the company’s existing technology infrastructure.
In addition, there may be a learning curve for warehouse operators who are not familiar with the technology and additional training may be required. Finally, some companies may be hesitant to invest in new technology, especially if they have been using traditional methods of measuring package dimensions for many years.
Despite these challenges, the future of mobile dimensioning in warehousing and logistics looks bright. As more companies adopt this technology, it is likely that the cost of implementation will continue to decrease, making it more accessible to smaller businesses. In addition, advancements in augmented reality and other related technologies may further improve the accuracy and efficiency of mobile dimensioning –making it an even more valuable tool for managing inventory and logistics.
Würth Industrie Service GmbH & Co KG and W. Gessmann GmbH, a supplier of robotics and system solutions, have partnered up to showcase their robotic capabilities and provide future customers the opportunity to have a vending machine supply materials directly to a workstation.
The special solution aims to optimise decentralised material dispensing, reduce the workload on employees and at the same time increase efficiency, flexibility and safety. The GESSbot Gb350, an Autonomous Mobile Robot (AMR) from Gessmann, automates internal transport quickly and cost-effectively, enabling Würth’s ORSY ®mat vending machine to supply materials right up to the workstation.
Thanks to the special sensors that map the surrounding, the robot follows every defined route, travels to workstations and charging stations and makes itself aware of obstacles. In future, it will even be possible to use lifts across several floors. In combination with the digital iDISPLAY and Würth Industrie Service’s own software solution, the mobile GESSbot including ORSY®mat can be navigated from ‘A to B’ easily. Each workstation is equipped with an iDISPLAY, which displays the pre-programmed routes that can be selected and requested by the respective employee.
These are clearly structured and are sorted in the order of incoming orders. It is also possible to request urgent requirements immediately by prioritising the route.
The GESSbot Gb350 itself is also equipped with an integrated display that can communicate with employees in the immediate vicinity. With a possible load capacity of 350kg, and a weight of 150kg, the mobile ORSY ®mat reaches a maximum speed of up to 4.3km per hour –equivalent to half a walking speed – on a maximum gradient of 5%.
Power is easily supplied by the robot, which finds its own way to the charging station, in a timely manner, docks and charges fully automatically. In the series version, the ORSY ®mat will be installed on
an autonomous rack that is supplied inductively via the GESSbot. This means the racks remain mobile and a single GESSbot can transport several vending machines to different locations.
Auxiliary and operating materials such as sanding discs, drills, hand tools or protective gloves have a major impact on procurement due to their irregular requirements – with a wide variety of items, and their shortage, possibly bringing the entire production to a standstill. The key to efficiency is achieved with the reliable ORSY ®mat vending machine solutions.
Today more than 1,800 vending machines, at over 400 customers in 650 different storage locations, are already ensuring more productive materials management. Customers from manufacturing industries can benefit from perfect and organised stocking, automatic replenishment, transparent inventory control and more productive materials management for indirect materials – from tools and technical chemicals to personal protective equipment (PPE).
The system communicates directly with the ERP system of Würth Industrie Service, thus allowing the customers to monitor inventory and material withdrawals in ‘real time’. Different variants of the vending machine models are available in order to fulfil individual customer requirements optimally. Whether it is the ORSY ®mat FP flap vending machine, ORSY ®mat HX helix vending machine, ORSY ®mat RT rotating vending machine, ORSY®mat DR Light drawer vending machine or even the latest developments like the ORSY ®mat WGT weighing system, as well as the ORSY ®mat CHE hazardous materials system – work gets done better with these stocked vending machines.
With the feasibility study of the mobile ORSY ®mat, Würth Industrie Service and Gessmann are making it possible to supply materials right to the workstation. However, the prototype is not only impressive in terms of safety, as high-quality items in particular can be stored securely, it also proves to be an ideal co-worker thanks to its mobile transport from workstation to workstation. The complete transparency of all transactions, withdrawals, and orders, enables an immense reduction in consumption. Customers benefit from maximum savings in their process costs by taking over the requirement assessment, requirement notification, reordering, goods delivery and optional on-site system replenishment.
With over 130 years of experience, REYHER is one of Europe´s leading trading companies for fasteners and fixing technology worldwide.
SCHNORR® is an international leader in engineering and producing safet y washers and disc springs for automotive, aerospace and mechanical applications
Our products and services
More than 130,000 items in stock to ensure highest availability
Expansion of assortment to meet future market demands, e.g. Duplex D 6 and titanium fasteners
Improved e-business solutions, e.g. RIO webshop in different languages and interface systems
Customised packing solutions
F. REYHER Nchfg. GmbH & Co. KG
Haferweg 1 · 22769 Hamburg
+49 40 85363-0 mail@reyher.de reyher.de
Original SCHNORR® safet y washers:
• Highly vibration-resistant
• Twofold effect from one component
• E x tensive range
Original SCHNORR® disc springs:
• Various applications
• Best price -per formance ratio
• Customized solutions
Please contac t us Together we will find your tailor-made solution.
us!
Schnorr GmbH
Stuttgar ter Str. 37
71069 Sindelfingen, Germany
Phone: +49 (0) 7031 302-0
Fax: +49 (0) 7031 382600 mail@schnorr.de www.schnorr.de
06.11.2024
Nothing stands still in the transport sector and that is especially true for railway vehicle design. With over 200km of cables and wiring in an average high-speed train, fastening clips mounted on structural edges are giving engineers more freedom to route parallel cable runs.
With the amount of cable increasing dramatically, the real challenge is how to install cables quickly and easily and hold it securely in place at the lowest cost possible.
HellermannTyton began developing its EdgeClip range in the mid-1990s, primarily for the automotive industry –where considerations of weight and space are of utmost importance. The EdgeClips can guide cables and wires in any routing direction and can be pushed into place easily by hand, which saves time in comparison to riveting metal butts in rail vehicles with tools. The fasteners are also ideal for narrow spaces and applications where drilling holes or using adhesives is not practical. One enormous advantage is that they can be easily pre-assembled on the harness, which saves train manufacturers a lot of time during construction.
“Whereas cables and wires in earlier rail vehicles were mainly to distribute electrical power through the vehicles, today we see data and signal sent back and forth between cars and the locomotive –for passenger comfort but also for more intelligent and efficient operation of the train. At some point you face the question of how to route all this cable once it leaves the ducts and trays in the floor or ceiling – for example, around the doors,” highlights Paul Cocheril, EMEA railway market manager at HellermannTyton. “The traditional method is to use metal butts riveted into place, which is very labour intensive. The butts first have to be installed and often that makes it more difficult to maximise the efficiencies of pre-confection. Metal butts are also relatively heavy, so they add a lot of extra weight to the rail vehicle, without any particular additional structural benefit.”
Paul adds: “Early adopters in the industry are therefore moving away from this approach and are using EdgeClips instead, which are a more
efficient solution. These use existing edges to anchor a cable harness firmly and securely – even where strong vibration is a constant factor.”
The EdgeClip was originally developed as a custom product to meet a specific challenge, but has become a standard product for HellermannTyton .
A more recent development of the EdgeClip is a version that routes two harnesses or cables in parallel, one on each side of a surface edge. “The advantages of parallel routing are very clear. Depending on the weight of a harness, let’s say that the harness or cable has to be fastened approximately every 30cm horizontally, or every 50cm vertically. We’re talking about a significant reduction in process costs and time – potentially up to two thirds – compared with the butt and tie method, to secure the same amount of harness or cable in parallel in a carriage,” underlines Paul.
The metal claws at the heart of the EdgeClip withstand vibration and support the weight. Pre-confected with the harness, all it takes is one simple process step – without the need for any tools – to secure parallel cable runs.
“If you take into account the cost of metal butts and the time spent installing them, the EdgeClip is a highly efficient and economical option. Savings are significant and that can take some of the pressure off overall costs,” comments Paul.
Savings are not just during the initial manufacture of the railway vehicle. The average lifespan of a train is 40 years and as a rule, rail vehicles are modified and refurbished at least once during their lifetime, which includes cable assemblies – these are refurbished about every 20 years.
“What you save on cable assemblies and installation on your average train will be repeated later when the assemblies get their overhaul. This makes using EdgeClips, especially one capable of routing harnesses in parallel, even more attractive. Just imagine the huge increase in long-term cost and time spent on installation when metal butts are used,” adds Paul.
Material characteristics of the EdgeClip and ties make these highly suitable for use in the railway sector. The cable tie is made from heat stabilised polyamide 6.6 (PA66HS), the foot from UV-resistant polyamide 6.6 (PA66W), and the EdgeClip clamp from double tempered and coated steel. They also meet the EU RoHS directive on the restriction of the use of certain hazardous substances in electrical and electronic equipment, and meet DIN EN 45545-2 European norm for fire protection on railway vehicles and hazard level HL2 in requirement set R22, R23.
“EdgeClips have long been an unsung hero in many industrial applications and they’re also now on the way to being the product
of choice for many applications in railway vehicles. Of course the advantages are multiplied when the same fixing point can be used to route parallel cables. EdgeClips may be hidden behind cladding in railway vehicles, but their cost saving potential is very visible on the bottom line,” concludes Paul.
www.hellermanntyton.co.uk
The QwicGrip provides quick and easy installation, offering secure cable organization and strain relief for various cable sizes and types. It minimizes cable damage and safety hazards, ensuring reliable and efficient solar installations. This adaptable solution also reduces installation time and labor costs, making it a cost-effective choice for your solar projects.
The T50REC1-3 Trio fixing tie with multi-way EdgeClip allows for a multitude of combinations for multiple cable routing. Thanks to its 3-loop, you can route your cables at a glance, whether perpendicularor parallel to the edge. This fixing clip is easy to install and can be used both indoors and outdoors.
J. LANFRANCO & Cie offers a wide range of slotted self-locking nuts – ESL, ERM and THU – designed to meet the specific requirements of railway applications.
The ESL, J. LANFRANCO’s flagship all-metal nut, is reusable and suitable for a very large number of railway, passenger vehicle and track applications. The self-locking system is provided by the two overlapping slots located on the upper part of the turret of the nut.
Also available is the THU all-metal, reusable hexagonal nut – with two slots on the same plane in the turret. This also comes in a low version (THM), offering flexibility of application according to specific constraints. Unlike other models, such as the ESL, which have slightly higher self-locking performance, the significant advantage of the THU and THM is that they can be used without specific tools, such as torque wrenches. This avoids dispersion due to the human factor and ensures consistent performance even with used materials.
The choice of the nut depends on the specific constraints of each application. The THU stands out for its ability to maintain its performance. It is particularly suitable for environments subject to extreme stresses, intense vibrations, variations in conditions and wear of equipment. This versatility is particularly advantageous for freight networks, where loads and speeds vary considerably in South America, North America and Australia.
The THU nut has proven its effectiveness in a variety of applications, ranging from metro and TGV infrastructure to secondary freight networks around the world.
Its design and ability to operate without torque accuracy make it an ideal choice for railway infrastructure and other applications under
Strainlabs has qualified for Vossloh connect, a global platform for solutions contributing to the digital transformation of the railway industry, with its smart bolts enabling the remote digital monitoring of critical infrastructure.
Vsevere stress. “We have chosen a constant evolution to meet the technical needs of our customers. We integrate normative updates, improve friction coefficients and select the nuts best suited to each assembly,” highlights J. LANFRANCO & Cie.
www.lanfranco.fr
ossloh connect is an initiative gathering the world’s solutions for the essential digitalisation of the railway sector, with an objective to facilitate train operators and infrastructure managers in finding digital solutions in one place to increase the reliability of train systems; enhance the utilisation of existing tracks; reduce the risk of accidents; and streamline maintenance work.
Strainlabs’ solution for the digital monitoring of critical bolts can be used, for example, in functions such as switches, which are still manually controlled with the same practices used in the 1800s. A large portion of the traffic disruptions impacting railway traffic today are caused by switch failures – issues that could be prevented with Strainlabs’ technology.
Strainlabs offers smart bolts that regularly send out signals with information about their condition. The signals are gathered in a Cloud solution, Strainlabs Analytics, where the information is analysed. The set-up allows simultaneous monitoring of thousands of critical bolts and bolted switches.
Each individual bolt is equipped with a sensor that continuously sends data including preload, temperature, RSSI (information about signal strength), and battery status. If something does not align with the standard values, the system alerts which specific bolt or group of bolts that needs to be addressed. For example, if bolts are becoming loose, overheating, or if there is another problem. This way, operational stops and breakdowns can be avoided. Furthermore, maintenance work is optimised as bolts and switches no longer require manual inspections.
The automation of cable set production for automobiles is gathering speed, with ITW Automotive’s Plastic Fasteners Division supporting the process with a fully automated and fully validated production concept for bonded fasteners. The concept is characterised by a high-level of standardisation, continuous validation of the process chain and numerous cost and process benefits.
The vehicle electrical system is one of the last disciplines in automotive manufacturing that is not manufactured automatically.
The size and complexity, as well as the vast number of varieties and flexible structure of vehicle electrical systems, were previously arguments against robot-assisted manufacturing. In addition, for a very long time, the element of cost was managed by shifting manual cable set production to best cost countries.
However, things are changing. The economic and geopolitical upheavals that have taken place over the last few years have motivated automotive manufacturers and vehicle electrical system suppliers to bring cable set production closer to vehicle production again, in order to boost supply chain resilience. This requires automated systems, as they are only way to limit production costs while increasing process reliability. ITW is able to provide a decisive impetus for this type of automated production with a fully validated production concept for bonded fasteners.
ITW became aware early on that an innovative fastener for automated production can only be successful in combination with a validated production and assembly concept. Adhesive technology works well here, as it is already used across various applications in automotive engineering.
ITW therefore developed a continuous process concept and safeguarded it with comprehensive concept validation, process reliability, and cost efficiency, a top priority. The geometry of the locator was also optimised for automated processing.
ITW then set-up simplified automated prototype production with industrial partners for the proof of concept. Key steps in the fully automated process include separation of the locators delivered as bulk goods into a vibratory bowl; picking up of the locator by the setting head at the end of the in-feeding conveyor; plasma pre-treatment of the adhesive surface; application of the hot adhesive on the curved contact surface; as well as the placing of the locator on the taped wiring harness using a robot.
Even during the early development of the concept, ITW integrated several design details that offer many advantages in the subsequent series process. For example, the locator has two standardised contact surfaces for its vacuum gripper – regardless of the geometry of the connecting element. Various locators can therefore be handled on one cable set, with a single standard setting head, without needing to put a lot of work into modifying the setting head.
In addition, the newly developed locators are suitable for both bonding and winding
with tapes. As a result, cable set manufacturers can combine the ITW locators with manual winding technology in a first step, already in series production, and later either with an automated winding process or as a standalone bonded connection. Furthermore, ITW has selected an adhesive that produces an excellent bonded connection with all relevant winding tape variants. Depending on the materials of the winding tapes, holding forces of up to 600N can be achieved – far above the required values of around 100N – 150N.
As an option, a tab can be attached to the locator to make it easier to replace damaged fixtures. The locator consists of 80% – 100% recycled material and thus improves the customer’s carbon balance.
Flexibility and modularity play a key role for cable set producers. With ITW adhesive technology, automated production lines can easily be expanded with separators, robots, and setting heads, to shorten cycle times or
place additional locator variants on the same wiring harness.
The automated locator production concept also offers additional advantages compared to previous fastener solutions – primarily cable ties and adhesive tapes. Bonding is therefore a relatively simple and fast process with a high-level of reliability and comparatively low investment costs. The small locators and the streamlined setting head can be easily inserted into narrow gaps between the mounting panel and the wiring harness, thereby ensuring good all round access to the wiring harness. Competing concepts require significantly more space here.
Furthermore, a bonded locator can be placed with significantly reduced distance to an interference contour when compared with competing processes. These are also significantly more complex and fragile when handling during bonding.
When applied to the design and development of the wiring harness, ITW states its adhesive technology enables greater design freedom than competing concepts and is significantly cheaper. It also offers a fully validated process and represents a significant step towards automated cable set production. Furthermore, the concept complies with the
basic recommendations of DIN 72036, which several OEMs, cable set manufacturers, and suppliers, have developed as part of ARENA 2036, which will be published soon. ITW has already presented the concept with bonded fasteners to premium OEMs in the south of Germany and is currently working together with one of them on the concept approval. If these tests are successfully completed, cable set manufacturers could integrate ITW
adhesive technology into initial automated production concepts for this premium OEM. ITW can support partners not only with its fasteners suitable for automation and setting head technology, but also with its expertise on the entire production concept in this process. This includes, for example, contact with adhesive and system suppliers. Customers may also choose to just use ITW’s concepts and industrialise them with their own partners.
INDEX® – A PERFECT FIXING has launched a new solar fixing App designed to provide the calculations needed for fixings and installation systems necessary to carry out the installation of solar panels – quickly and accurately.
With just a few simple inputs, the App will provide users with the fixings and installation systems required, with calculations valid for all types of panels and orientations. This includes projects with a height of 1,800mm – 2,300mm, width of 1,000m – 1,150mm and a thickness of 30mm, 35mm or 40mm.
The App is optimised for any type of surface and environment including plain, mixed, Arabic and slate tiles; simple corrugated, sandwich, imitation tile sheet; and concrete, deck, landscaped, gravel flat roofs. It also covers all possible fixings – products for fixing structures, unified assembly solutions, as well as fixings that simplify the management of components and the assembly of the structure at the installation site.
Accessible from any device with an internet connection and, being online, does not require a download to be used. Furthermore, it is available in several languages including Spanish, English, French, German, Portuguese and Italian.
The new patented InterShim™ wave spring design from Rotor Clip has been engineered for high acceleration electric motor applications and features alternating turns between inactive (flat) and active (waved) turns to ensure reliable performance under torsional loads and precise rotational movement.
WCE Marked solar fixings kits
As well as launching its solar App, INDEX solar installation kits have recently obtained CE Marking, guaranteeing the products comply with mandatory European legislation on special requirements. This recognition underlines the commitment to quality and safety in every INDEX® product.
To further assist customers, INDEX ® – A PERFECT FIXING has published a series of videos on its YouTube channel showing examples of solar panel installation on different types of roofs, using a variety fixings and systems – giving users a clear idea of how these products can be used in different environments.
www.indexfix.com
TensionPro has developed a range of highly versatile and reliable hydraulic tensioners, optimised for subsea applications in the offshore oil and gas industry.
The new SUB series is ideal for tightening Norsok/SPO compact flanges, as well as all common sized ANSI, ASME and API flanges.
hile initially developed for Electric Vehicle (EV) applications, Rotor Clip’s Intershim™ wave spring offers benefits that extend far beyond the automotive industry. It is highly customisable, with options open for the number of waves, number of turns, the arrangement of shims/troughs as well as a variety of speciality alloys. The option of either floating ends or bent ends also helps prevent damage to the mating surface during application.
Intershim™’s advanced design addresses physical challenges such as extreme forces and vibrations, making it a versatile solution for highspeed and high stress applications across various industries.
“The development of the new wave spring design represents a significant milestone and underscores our dedication to meeting the evolving needs of our customers. By listening to feedback, and leveraging our expertise, we have engineered a solution that offers unparalleled performance in high acceleration applications. We are proud to introduce this design to the market and look forward to its positive impact on our customers’ operations,” reported Elmar Kampmann, European sales engineering director at Rotor Clip Ltd.
An ergonomic design features a one piece body, anti-slip tool surface, contoured ‘grip’ reaction nuts and a high-vis finish – making it easy for divers to use the tools subsea. A 30mm piston stroke also ensures each bolt tightening operation can be completed in one hit, without having to return the tool to the surface to reset the piston.
Customers can choose between solid or split reaction nut options to suit their application and budget. Both are interchangeable on the SUB series, providing complete flexibility. Split reaction nuts offer speed of use for some applications, while solid reaction nuts provide a fail safe operation for applications with large or unknown bolt misalignment.
The series’ all stainless steel construction ensures long life performance and guarantees simple and efficient maintenance. Pressure tested and with CE Marking, the SUB series is supplied with detailed operating and safety manuals. Special one off designs are available for any thread size, load and diameter requirements. Ancillary subsea equipment, including pumps, hose reels and downline can also be supplied from stock.
We are the specialist in high-quality fasteners made from stainless highgrade steel and special materials. We are used to extreme conditions and face the toughest challenges on a daily basis.
We never lose sight of our aim to give the customer just what they want. And we always offer that little bit extra.
ART. 9015 bi-metal thin sheet screws
with double-thread/fine thread are made of A2 stainless steel and therefore guarantee high corrosion resistance and processing safety. Thanks to the hardened carbon steel tip, the screws are ideal for fastening aluminum and steel components to aluminum or steel profiles – without any pre-drilling!
Available with or without pre-mounted A2 stainless steel sealing washer.
Exclusively at TOBSTEEL the fixing of pre-drilled aluminium components is also covered by the ETA!
So, why not contact us? Call +49 7941 6073-0 Mail info@tobsteel.com Visit www.tobsteel.com
TOBSTEEL GmbH
Rudolf-Diesel-Straße 8 | D-74613 Öhringen
By Ian Parker, freelancer, ianparkerwriter@aol.com
Space is becoming big business worldwide, which means launch rates must increase if they are not to be limited by launch availability. However, launches are still a risky affair and launch failures are not uncommon. For instance, in August a test was being carried out on Unst – an island in the far north of Scotland – by German company Rocket Factory Augsburg and the nine engine test vehicle exploded.
Precise details of the cause will take a while to discover, but the fundamental problem is that rocket engines have to run close to mechanical and thermal failure to make them efficient. The slightest manufacturing or procedural error can lead to an explosion. Many will know about the Space Shuttle Challenger, which exploded in early 1986, killing seven astronauts. A leaking solid rocket booster was the cause.
Re-entry is equally demanding – spacecraft re-entering Earth’s atmosphere do so at around 17,000mph, meaning the frictional heating is huge. Any flaw in the heat shield could also be disastrous.
While most existing or planned launch services are targeting ’run of the mill’ spacecraft customers, Elon Musk’s SpaceX is looking much further ahead – to Mars, possibly via the Moon. The company made 96 successful launches last year of its smaller rockets, putting satellites into Earth’s orbit, but SpaceX’s Super Heavy launcher and Starship space vehicle are aiming much further into space.
Elon Musk has been enthralled with space since he was young, with his love of space stemming from science fiction and science fact. Today, as one of the world’s most successful people, he is about to launch his fifth Starship atop a Super Heavy booster.
So long as no one is hurt or killed, Musk isn’t too worried about launch vehicle explosions. His philosophy is “let’s try it and see”. Failure is a great educator. He also has an unusual attitude to material selection and therefore fasteners.
SpaceX’s Super Heavy launcher and Starship space vehicle are truly remarkable, but do not always use the latest materials and systems because of the drawbacks. They are basically made from steel, not aluminium alloy or composite materials, as you might expect. These were looked at, but the sheer size of the rocket made
While most existing or planned launch services are
targeting
’run of the mill’ spacecraft customers, Elon Musk’s SpaceX is looking much further ahead – to Mars, possibly via the Moon.”
composites impractical – where can you get an oven or autoclave that big?
Aluminium alloy is light but doesn’t tolerate heat very well. That’s why the Space Shuttle had a complex and expensive thermal protection system – with a major bugbear being the cost in its reusability. It was one of the reasons the Space Shuttle was nowhere near as cheap to operate as had been predicted. The spacecraft also lost tiles on launch and re-entry and they had to be replaced at significant cost. Every tile had a unique shape and had to be specially manufactured. Before each launch, each tile had to be pull tested to ensure it wouldn’t come off.
So, SpaceX opted for steel and a simpler heat shield with common tiles. However, the use of steel meant many welds and SpaceX had to do lots of development to get the welding right. There’s an important lesson here, traditional materials can solve your problems, but sometimes they need advanced joining techniques – it can take a while to get them optimised.
Book your entry today!
200+ companies listed
400+ product categories
90,000+ users (last 12 months)
The first Starship looked very rough. Today, it is much smoother with less apparent welds. Will it soon be completely smooth and shiny as in SpaceX promotional pictures and videos? Image is important – even for a space launch company.
Originally, Starship was to be made from carbon fibre reinforced plastic (CFRP) with production beginning in California. This seemed logical since it’s extremely light and strong and most of the workforce was in California. It was therefore surprising when a stainless steel Starship ended up being made in Texas, but there were a number of reasons as to why.
CFRP begins to break down at about 200°C. It would therefore require a very good heat shield to survive the 1,600°C encountered on multiple re-entries. Stainless steel is heavier, but it can stand up to 850°C, so a thinner heat shield is sufficient. Also, CFRP costs about US$150 per kg, whereas stainless steel costs a mere US$3 per kg and that’s a huge difference.
Initially, Starship was made out of rings of 301 stainless steel that was 4.5mm thick. The company that made it built water towers – with no experience of building rockets. The welding standards were poor.
To begin with, flux-core welding was used, in which current is passed through a metal wire forming an arc of about 7,000°C. The tip of the wire melts and falls into the molten steel, filling any cracks or air bubbles. A material around the wire burns and releases a protective gas around the weld – preventing it from oxidising.
However, at this time SpaceX didn’t have a suitable factory and most of the welding was done outside. This resulted in the wind creating poor welds because it blew the protective gas away. The welds were heavily corroded and had cracks and rough edges on the surface. To manage this SpaceX started grinding the welds down, which perhaps surprisingly strengthened them because cracks on the surface can propagate through.
Unfortunately, Starship Mk1 exploded when one of the welds failed, which led to more improvements being made. Thinner grades of 304L stainless were used, which needed much less welding. Also, it was much more resistant to corroding. The company also went to TIP TIG welding, allowing a tighter, deeper weld. This also warped the surrounding metal less. SpaceX also got robotic welding machines, similar to the ones in Tesla factories. Stringers added inside the rocket also stopped it buckling under its own weight.
SpaceX’s steel is cold rolled, which strengthens it by stretching the grains. It also makes it harder. However, welding causes the material to soften. So, SpaceX got a giant planishing machine, which hammers the welds and compresses them till they match the hardness of the surrounding metal. It also improves their look. The company is also now developing its use of laser welding.
Even though stainless steel has good heat resistance, SpaceX’s Starship still needs a thermal protection system and this is made up of a thermal blanket with tiles on top, similar in concept to the ones used on the Space Shuttle, but with far fewer shapes. The problem has been keeping them on. Some are fastened with metal studs and others are bonded on –with SpaceX also experimenting with the adhesives for the tiles.
The tiles are very similar in chemical composition to the ones used on the Space Shuttle (essentially a porous silicon material), but it is not clear at this stage why some are coming off. One theory is the booster, which is filled with cryogenic propellant that causes it to contract. On launch, it produces lots of vibration, and noise, and heats rapidly.
All these things tend to dislodge or crack the tiles. Musk is adding an additional ablative material under all of Starship’s existing heat shield tiles. This will provide extra protection if a tile breaks or falls off.
During the last flight, Starship’s upper stage managed to make it through Earth re-entry despite a weak point between a flap and the main body that nearly destroyed the flap. Even so, Starship managed to complete its landing burn anyway with the flap still actuating.
Musk talked about a change to the entire heat shield of Starship. During a livestream, he said: “We’re going to replace the whole heat shield on the ship. So, the new heat shield tile is about twice as strong as the ones that were on the last flight. We want to put an ablative secondary structure, basically ablative protection behind the tiles, so that if the tiles crack or come loose it doesn’t cook the rocket.”
He continued: “We ran two experiments with tiles on this flight, which people may have noticed because there were missing tiles. They were intentionally missing because we were testing the secondary heat shield material, which is like a silicone felt ablative.”
In pictures taken before the flight, these missing tiles were obvious toward the bottom of the ship. What wasn’t so clear was the addition of the ablative material, which must have performed well in those specific areas considering SpaceX has now added an entire layer behind the tiles of the next ship.
Musk went on to clarify: “It’s not good for reuse but it’s good for saving your butt if a tile cracks or falls off. It’s very tricky to put these tiles on and have them work well because the tiles are ceramics; they are like a coffee cup or a dinner plate. So, you have a whole bunch of dinner plates on a rocket that is shaking. It’s shrinking cryogenically with the propellant and then expanding under pressure and then the tiles are expanding when they get hot. So, there’s a lot of expansion and contraction happening while trying to keep all these brittle tiles from cracking or breaking off.”
He went on to talk about the challenges of making a reusable orbital heat shield, citing the Space Shuttle taking months of work between flights to fix and repair its heat shield. What’s clear from these comments is that they are still struggling a bit with the main heat shield tiles themselves, as far as keeping all of them secure and in one piece throughout the entire launch process. However, the new ablative material, in combination with the rocket’s steel construction, is expected to provide a significant safety barrier if a few tiles fail.
The goal for Starship is rapid reuse; this obviously would not be possible if after each landing the rocket needs repairs to the underlying ablative material, as well as lost tiles replacing. The other specific fix had to do with the seal where plasma initially broke through and damaged the flap. In regard to that change, Musk initially tweeted that they would have this nailed for the next flight and that it didn’t seem to be a very significant alteration.
He said again that they still want to catch the booster on the next flight. Specifically, he was quoted saying: “Unless something comes up that we think is problematic, we will try to bring the booster back and catch it with the giant Mechazilla arms (known as chop sticks).”
Another detail from this livestream, combined with other tweets and comments, suggests that only the one flap was damaged. Whenever mentioning the damage, it was always singular rather than plural. If that is the case and only the flap shown on camera was damaged, it would be an even better sign as the others held up even with the current heat shield system. With heat shields, a tiny weakness can easily become a disaster for the entire vehicle.
Based on everything said, we should expect to see SpaceX get very busy in the coming weeks in preparation for another launch. The launch pad seems to be in great shape, including the water deluge and steel plate protection. This system has now been used for three launches and seems to be holding up nearly perfectly.
In a post-launch report, SpaceX said: “Starship’s fourth flight test launched with ambitious goals, attempting to go farther than any
previous test before and demonstrate capabilities central to the return and reuse of Starship and Super Heavy. The payload for this test was the data.”
Musk made it clear that they got a lot of incredible data from Flight 4, but he pointed out that both the soft landing of the booster and upper stage was about a 20% lucky event, based on their initial expectations. With this came even more data they can apply to the next mission to try even more ambitious things.
Once the catch process is attempted, depending on how that goes, it could become somewhat of a regular occurrence. From there we can hope to see the ship actually returning for an attempted touchdown on land. The faster Starship becomes operational the better.
So, what are the main lessons here? Explore and ignore the naysayers. You don’t have to always use the latest technology. Processes have to offer value for money. Time served materials with new processes can be the best. Also, don’t be scared of trying something that fails. The opposite of success is not failure; the opposite of success is not trying. Failure is part of success and nearly all major successes had lots of failures on the way.
With Super Heavy and Starship, the production welding and the thermal blanket and tile fastening system, whether it be with metal studs or adhesive, are crucial to the vehicle’s survival and re-use. If the fastening systems fail in many places, the vehicle will likely be lost. A few tile losses can be tolerated, but a major weld failure probably not.
With SpaceX’s ambition to launch astronauts on Starship, the chances of a major failure must be as low as possible. The company’s ‘Try it and see’ attitude is producing a huge amount of data, hopefully meaning that any failures happen before astronauts are flown. The company’s attitude is very much ‘Test it in the real conditions’ rather than any simulation.
SpaceX’s approach is the opposite of the careful, plodding, conservative development of other launch vehicles and it seems to work. Perhaps competitors will now follow suit.
As the industrial landscape increasingly shifts towards electrification, the demand for components that meet both conductive and insulating requirements has surged. Here, Arne Schlichting, technical specialist in new mobility at KAMAX Automotive GmbH, delves into the technical challenges and solutions associated with bolted joints in electrified environments.
Bolted joints, essential in assembled machines and vehicles, now face heightened expectations to manage these electrical demands while maintaining their core mechanical functions. In any mechanical assembly, bolted joints serve as the critical link between multiple components, providing the necessary clamp load to ensure a stable and durable connection. However, in electrified systems these joints also have the potential to create unintended electrical pathways.
Thus, the challenge is twofold, firstly ensuring that the bolted joint does not inadvertently conduct electricity where it’s not wanted and secondly protecting the joint itself and the surrounding components from electrical hazards, such as creepage currents and voltage surges.
The primary technical requirements for bolted joints in electrified systems include high clamping force transmission –the joint must provide sufficient force to secure the components reliably; durability under dynamic loads – the joint must withstand vibrations and dynamic stresses, especially in environments subject to movement or impact; space efficiency –the design must be compact to fit within the often limited
Bolted joints, essential in assembled machines and vehicles, now face heightened expectations to manage these electrical demands whilst maintaining their core mechanical functions.”
COST-EFFICIENT COLD-FORMING & PRECISION MACHINING
DESIGN, PROTOTYPING & LAB SERVICES
CONSULTING BY OUR EXPERTS
GLOBAL DELIVERY
ASSEMBLY EXPERTISE
Are you looking for a supplier who is an expert in every field?
Make it easy for yourself, get everything from just one source: us
Our experts analyze your application down to the last detail. We challenge your technical drawing with our decades of experience. We work with you to develop complex geometries and prototypes and conduct laboratory trials and material tests.
When your product is perfectly designed, we produce a cost-efficient tailor-made part: we form it, we machine it, heat-treat it, coat it, overmold it, assemble it, and package it. We then deliver it to you quickly, safely, and locally – anywhere in the world.
And if you want to get more out of it, our application engineers will find a way –without you ever having to deal with more than one source.
www.kamax.com
space available in machinery; and corrosion resistance – the joint must resist environmental degradation, especially in harsh conditions like those found in automotive applications. Other technical requirements include ease of assembly and disassembly – the joint should be designed for straightforward installation and removal without compromising its insulating properties; mechanical injury protection –the design must minimise the risk of injury during handling and maintenance; and finally defined clamping force – precision in clamping force is crucial for maintaining the integrity of the assembly.
With the integration of electric drives, additional electrical insulation requirements must be met by bolted joints, including the prevention of unintended electrical conductivity. The joint must prevent any electrical current from passing between the assembled components unless specifically designed to do so. There must also be protection against voltage surges – the bolted joint should prevent voltage surges from causing damage or creating hazardous conditions. As well as this is creepage current mitigation – the joint must minimise the risk of current leakage along the surface of insulating materials and human protection from electric shock – with the design ensuring the joint is safe to handle, even in a live system.
To effectively address these challenges, it’s essential to consider the different areas of a bolted joint, such as the head with wrench grip. This area must protect against human contact with the joint during assembly and disassembly, ensuring the insulating layer remains intact. The underhead must also be considered as this area experiences significant wear during tightening and must be designed to withstand high pressure while providing effective insulation. As well as this, the shank must have minimal coating thickness to fit within the component’s bore while maintaining adequate insulation. The thread area must also be considered as it transmits significant force and has limited space for coatings, which must provide insulation without compromising the joint’s strength.
For the head area, KAMAX offers bolt heads coated with specially modified polymers, which are designed to protect against accidental human contact with live components, as well as have a high clamp load
The shift towards electric drives imposes new technical challenges on bolted joints, requiring innovations that address both mechanical and electrical requirements.”
with minimal risk of damage to the insulating layer. The bolt heads also have adequate insulation to prevent voltage surges and creepage currents up to 5kV.
For the shank, KAMAX provides advanced powder coating technologies that offer a minimal coating thicknesses of less than 200µm, suitable for tight tolerances with a high insulation strength of 50kV/mm. The technologies also provide high corrosion resistance, withstanding over 720 hours of salt spray testing (NSS per ISO 9227), as well as enhanced chemical resistance – capable of withstanding exposure to acids, alkalis and organic solvents.
The underhead of the bolt is particularly critical as it transmits approximately 50% of the clamp load. KAMAX’s solutions therefore focus on low friction during assembly, ensuring easy and accurate torque application and long-term durability under mechanical and thermal stresses. They also exhibit high insulation properties to prevent electrical failures due to voltage surges or creepage currents.
For bolt threads, KAMAX does not currently offer standard insulating solutions but is equipped to collaborate with customers to develop customised solutions based on existing technologies.
Besides the regular electrified systems, joints in fuel cells play a significant role as those joints have additional requirements. In addition to the clamp load transmission and the insulation, to avoid any electrical short in the fuel cell stack, those joints have to compensate for the high swelling of the fuel cell without increasing the pressure in the cells and their components, such as bipolar plate, membranes and sealings. KAMAX has developed such an element, called STACKFLIX, which fulfils all the three requirements and includes the media flow.
The shift towards electric drives imposes new technical challenges on bolted joints, requiring innovations that address both mechanical and electrical requirements. KAMAX is at the forefront of developing solutions that meet these dual demands, offering robust, reliable, and cost-effective options for a wide range of industrial applications, particularly in the demanding automotive sector. By focusing on insulation, corrosion resistance, and mechanical integrity, KAMAX ensures that its bolted joints deliver superior performance in electrified environments.
For further technical discussions or bespoke solutions, KAMAX’s engineering team is ready to assist, leveraging their extensive experience in both the mechanical and electrical aspects of bolted joint design.
www.kamax.com
Flaig + Hommel GmbH
Verbindungselemente
Heerstraße 1
D-78554 Aldingen
Tel.: +49 (0) 74 24 / 9 62-0 info@flaig-hommel.de www.flaig-hommel.de
YouTube
Hitzebeständig Heat-resistant
Witterungsbeständig Weather-resistant
Wiederverwendbar (ISO 2320) Reusable (ISO 2320)
Vielfältige Varianten various variants Visit us!
Fastener Fair Italy 29.-30. October Booth 703 Milan, Italy InnoTrans 2024 24.-27. ExhibitionSeptember hall 8.2 / Booth 390 Berlin, Germany
Vibrationsbeständig Vibration-resistant
Säurebeständig Acid-resistant
100% Qualitätskontrolle 100% quality control
Through more than one hundred lines of its Unifix drywall screws, Owlett-Jaton offers an extensive range of collated fasteners, encompassing various diameters and lengths, head styles, finishes, thread types, ends and packaging.
Specifically designed to be compatible with auto-feed screw guns and enable fast and efficient installation, the range of collated drywall screws includes fine thread, coarse thread and self-drilling options. Owlett-Jaton underlines the importance of choosing the correct thread type for the application material, as using the incorrect thread type may result in time-consuming and costly damage to both the fastener and the material during use.
For instance, coarse thread drywall screws are ideal for fixing plasterboard sheets to timber studs, often found in domestic applications. The sharp point penetrates the timber, enabling the coarse thread to cut into the timber, producing a very effective result. Fine thread drywall screws are developed specifically for light gauge metal tracks, or studs, typically found in commercial and industrial properties. The sharp point is designed to pierce the sheet metal, thus removing the need for a pilot hole, as well as enable the fine thread to cut into the material and produce a strong grip.
Finally, self-drilling drywall screws incorporate a tip that is designed to penetrate a heavier gauge of metal stud work or tracking, up to 2mm depth, to eliminate the need for a pilot hole. The thread then actively engages with the metal surface, giving a secure finish.
www.owlett-jaton.com
The new 20V MAX XR® brushless cordless 21° plastic collated framing nailer and 30° paper collated framing nailer from DEWALT®, a STANLEY Black & Decker brand, have been designed to minimise downtime between shots by enabling the tool to stay active after the trigger is released.
Each tool delivers powerful performance in a wide range of applications, enabling users to install up to 49m 2 of subflooring and complete up to 30m of wall framing per charge.
The next generation nailers are optionally compatible with newly introduced extended magazines that are constructed from high strength magnesium and hold two strips of nails. Users can align and drive up to 3 ½ inch nails at aggressive angles with the redesigned nose that is engineered for ‘toe-nailing’ applications. With field serviceable springs and a driver blade, the nailers also don’t require delay inducing maintenance.
“Productivity is vital on the jobsite and the new DEWALT nailers will keep pros working at optimal efficiency – with the new flywheel that eliminates ramp-up time between shots in rapid sequential mode,” underlines Tyler Knight, senior product manager at Stanley Black & Decker. “The nailers are lightweight and provide the convenience and mobility of cordless without the hassles of compressor and hose hook-up that extend set-up and breakdown time.”
Suitable for application with steel, wood, plastic or aluminium, Klein Tools Inc, a US-based manufacturer of tools designed specifically for industry professionals worldwide, is offering two premium step drill bit kits for use on jobsites.
Available in two versions – the premium electrician’s quick release step bit set and the premium electrician’s ⅜ inch hex step bit set – the drill bits all feature a coating with an aluminium titanium nitride that, the company highlights, makes them up to 10 times more durable than steamed black oxide coatings.
Laser markings are also imprinted on the bits making them easier to read for fast size identification on the jobsite. As well as this, the bits come equipped in a compact, modular case designed to fit neatly within MODbox™ toolboxes and the MODbox™ case adapter side rail attachment.
In the quick release kit, an impact rated shaft allows for the use of impact drivers and standard drills with the bits. A double spiral flute removes chips, enabling faster cuts and drilling. Additionally, the quick release ¼ inch hex shank provides a firm grip that prevents spin out in the drill. The hex step kit offers a double straight flute design for cleaner cuts and drilling, while the durable 38 inch hex shank provides a firm hold that prevents spin out in the drill.
“Klein Tools constantly looks to adjust its offerings to meet the needs of trade professionals,” says Amina Nunn, product manager at Klein Tools. “With these new step bit sets we’ve designed two options – one for faster cuts and drilling, and one for cleaner cuts and drilling – to ensure that pros can use the bits in a way that works best on their projects. Both sets feature bits coated with aluminium titanium nitride for long life, easy to read markings and cases that fit in Klein’s MODbox™ modular system.”
Specially developed for drilling in reinforced concrete and natural stone, the Rocket 7 hammer drill bit is an ideal solution for construction and industrial applications – offering strength, precision and reliability.
ith its four spiral geometry the drill bit, developed by Germany-based Projahn Präzisionswerkzeuge GmbH, distributes wear evenly – significantly extending the life of the tool while also reducing vibration. The bit also features a solid carbide head, which is firmly bonded to the drill body by a diffusion welding process, to help eliminate the risk of head fractures and ensure safe use even in the most demanding conditions. Additionally, integrated wear marks indicate wear limit according to PGM certification, offering further
“Since we started using the Rocket 7 our work processes have improved significantly. I was particularly impressed with the drilling speed, as we can now do up to 30% more holes per day compared to our old drill,” comments Erwin Janzen, an experienced site manager from Munich, Germany, and professional user of the Rocket 7.
By Dr Bill Eccles, Bolt Science Ltd
Most engineers will likely come across a fatigue failure at some point in their career. Fatigue, which refers to the progressive cracking of a material due to repeated loading and unloading cycles, mainly occurs due to repeated changes in the loading condition and, subsequently, the stress condition.
Afatigue crack will normally form where the highest stress condition is located. For bolts, this is usually at the root of the thread closest to the nut-to-joint interface. The thread root is located at the bottom of the thread and is the region where the stress is significantly greater than the surrounding region – a feature known as a stress concentration. It can take thousands or even millions of load cycles for the crack to propagate through the bolt. Ultimately, the smaller the stress concentration on the joint interface, the better the fatigue life in the bolt.
When bolts fail due to fatigue, it is usually located in the first thread root next to the nut-tojoint interface. The reason why failure occurs here and not in another thread root is due to the high-level of loading on this region – as the load must pass between the joint, the nut and into the bolt. Because the loading takes the stiffest path, more loading passes through the first thread in the nut, a path which is demonstrated in Figure One.
The stress concentration in the thread root region is between 4 and 6 depending upon the pitch and diameter of the thread – meaning the stress can be 4 to 6 times the stress in the central section of the bolt thread.
There are two main reasons why the root of the thread is rounded. Firstly, the rounding reduces the stress concentration and hence facilitates fatigue resistance. Secondly, since most bolt threads are rolled rather than cut, the rounding increases the life of dies used in the rolling process. It is advised that the thread root is fully rounded to facilitate prolonged bolt life (Figure Two).
Tolerances are placed on the root radii which, for metric threads, must be between 0.125p to 0.144p (where p is the thread pitch). Hence for an M6 coarse thread, whose pitch is 1mm, the root radii must be between 0.125mm – 0.144mm. Limiting the radii to a minimum value, limits the stress concentration present.
The type of loading sustained by the joint influences the bolt’s load response. The majority of bolted joints that are shear loaded have clearance holes – where the hole is larger than the bolt thread to provide a radial gap between the bolt and the hole. Such joints rely upon the clamp force generated by tightening the bolt to transmit any shear by friction between the joint plates (Figure Three), as against shear being transmitted between the plates through the bolt shank. These joints are referred to as friction grip joints.
With such a joint, if designed and assembled correctly, the bolt will not experience a load change when the shear force is applied. Therefore, if there is no load change, there is no stress change in the bolt and hence no fatigue. If, however, the bolt is not tightened sufficiently, or the interface friction is low or the loading too high, the friction grip can be overcome and cause a joint slip. Fatigue failure in the thread root due to a shear loaded joint’s friction grip being overcome is a common, if not the most common, cause of bolt fatigue failure.
With an axially loaded joint, the bolt does not sustain the full magnitude of the applied loading, as most of the loading reduces the clamp force. There is a small proportion of the loading, typically between 5% to 20%, that will be sustained by the bolt. If the axial loading varies, this will cause the stress sustained at the thread root to vary and hence cause fatigue. With a properly designed joint, the alternating stress sustained under axial loading is kept below the fatigue endurance limit of the bolt.
In an axially loaded joint, if the bolt was not tightened sufficiently, or the axial loading too high, the clamp force acting on the interface can be overcome. This results in a gap occurring in the joint interface, referred to as joint separation. The bolt would then sustain the full magnitude of the applied loading with potentially a large alternating stress in the thread root. Again, this is a common cause of fatigue failure.
In general, for both a shear and axially loaded joints, increasing the bolt preload will reduce the risk of fatigue failure occurring. Checking that the bolt has been tightened correctly is one of the first steps in a fatigue investigation. If the tightening was as specified, increasing the tightening torque, and increasing the bolt strength, is often second on the list when seeking to resolve a fatigue issue.
The BOLTCALC program by Bolt Science offers joint analysis and complete design checks to determine whether or not fatigue is a possibility in a bolt joint. www.boltscience.com
Locking nuts and washers have vital roles in securing fasteners, helping to prevent loosening due to vibration, thermal expansion or dynamic loads in various industries where safety and reliability are paramount. Here Norm Fasteners highlights the different types of locking nuts and washers it can supply, as well as the applications they can be used in.
Norm Fasteners is able to supply a wide range of locking nuts and washers including:
Prevailing torque nuts with nylon ring – these nuts have a nylon collar that grips the bolt threads and increase friction. This offers reliability, reusability and consistent locking performance, however they are temperature sensitive and therefore less effective in high vibration or high temperature environments.
All metal prevailing torque nut – this nut is deformed from either the sides or the top to maintain a constant torque by gripping the counterpart threads. It is effective in high vibration settings but requires higher installation torque, which may cause thread damage during applications with repeated use.
Jam nuts – these thin nuts are tightened against a standard nut to lock both in place by applying opposing forces. These nuts are simple and cost-effective but require precise installation and can loosen if not properly tightened.
Serrated flange lock nuts – these nuts possess serrations or ripp on the mating surface of the flange with the counter part. The serrations bite into the surface to prevent loosening, distributing the load over a larger area to allow for reliable fastening. However, they can damage the surface coating and are not suitable for soft materials that can easily be damaged by the serrations.
Slotted nuts – also known as castellation nuts, they have slots on one end and are used with a cotter pin that passes through a hole in the bolt – which subsequently locks the nut in place. With a highly secure locking mechanism, these nuts are used in critical applications such as automotive and aerospace. The downside is they require drilling a hole in the bolt,they are expensive and they have a long installation process.
Locking washers – this includes split lock washers, tooth lock washers, flat washers and wedge lock washers. Split lock washers have a helical shape that grips the nut and surface, whereas tooth lock washers, with internal or external teeth, prevent rotation by biting into surfaces. Flat washers distribute loads and can complement other
The future of locking nuts and washers is centred on enhancing performance and adaptability through advances in materials science.”
locking methods, while on the other hand, wedge lock washer pairs have outer serrations to grip surfaces and interlock with mating serrations inside. Lock washers enhance locking capability of standard nuts and are easy to install, while wedge lock washers exhibit a very high vibration and dynamic load resistance that makes them suitable for many industries. However, these washers may cause surface damage during application. In environments that are subject to high vibration, standard washers are less effective than specialised lock nuts.
The future of locking nuts and washers is centred on enhancing performance and adaptability through advances in materials science. New high strength, lightweight materials are expected to improve performance in extreme conditions.
Other trends include emerging smart locking systems that integrate sensors and IoT technology for ‘real time’ monitoring and adjustment. These innovations aim to overcome current limitations like temperature sensitivity and reusability, offering more reliable solutions
EXPRESS SERVICE automated storage 95%products in stock
40.000 REFERENCES standard products screws,bolts,nuts,washers
ONLINE ORDERS 24h delivery service live warehouse stock
Nowadays many sheet metal or thin walled components are so thin that they require nut elements to hold them in place during assembly. That’s why Böllhoff Group has developed the QUICK FLOW® Plus thin sheet screw – so users no longer require these additional elements.
QUICK FLOW ® Plus is a self-tapping fastener designed specifically for use in thin walled components. Self-tapping screws are thread forming fasteners that create the female thread by themselves when being installed. The female thread is created with the forming zone of the male thread, which is usually done by grooving. This process requires the male thread to have higher strength than the workpiece material and for the material to have sufficient ductility. By using self-tapping screws, time-consuming process steps such as thread cutting or cleaning the thread can be omitted.
The distinctive geometry of the tip, in combination with a high case hardness, enables self-tapping fastening without drilling a hole
Plus thin sheet screw, with its specially designed screw tip, creates a hole in the sheet metal during the fastening process and pulls the sheet screws, which means that there is sufficient overlap of the formed thread flanks to create a stable joint.
Another advantage of the QUICK FLOW ® Plus thin sheet screw is a double thread, which additionally increases the surface area of the engaged thread flanks. This double thread enables shorter cycle and process times, resulting in increased efficiency while also allowing for the possibility of automated assembly.
Surface treatments, which are essential in industry, mainly provide protection against corrosion, clamping capability and, in some cases, appearance constraints. J. LANFRANCO & Cie offers three main types of surface treatments - electrolytic coating, zinc flake coatings and hot dip galvanising.
These treatments must in no way modify the characteristics of the fasteners, such as mechanical strength, geometry, hydrogen embrittlement, as well as suitability for assembly – even in the presence of a coating. J. LANFRANCO complies strictly with current regulations, in accordance with RoHS and REACH, to guarantee its products conform to environmental and safety standards.
Electrolytic coating NF EN ISO 4042 is used for nuts in Classes 8 –10. This treatment, which is particularly effective against corrosion, is achieved by coating the surface with a thin layer of electrolytic zinc enriched with nanoparticles. This composition increases corrosion resistance. In addition, a film-former is applied to obtain an improved coefficient of friction of 0.12µ - 0.18µ. For Class 10 nuts, a systematic degassing process is used, adapted to the quality class, to ensure hydrogen embrittlement does not happen.
Also available from J. LANFRANCO are zinc flake NF EN ISO 10683 coatings – used for Class 12 nuts. This kind of treatment offers protection against corrosion and is less likely to induce hydrogen embrittlement than electrolytic coatings. This method involves
the application of several coatings of zinc particles, forming a durable and effective protective coating. Zinc flakes are particularly adapted to industrial sectors requiring increased resistance and long-term reliability.
Finally, hot dip galvanising NF EN ISO 10684 is a different technique used to protect fasteners against corrosion. The process involves immersing parts in a zinc bath, creating a thick coating of zinc. Galvanising remains a suitable option for specific industrial applications requiring maximum protection against corrosive environments.
By controlling all of these surface treatments, J. LANFRANCO is able to meet the specific requirements of its customers, offering tailor-made solutions and guaranteeing precise coefficients of friction. Whether for Class 8, 10 or 12 nuts, J. LANFRANCO is dedicated to supplying surface treatments that comply with the strictest standards – whilst meeting the technical and regulatory requirements of each industrial application.
www.lanfranco.fr
Specially designed to keep screw bits in order, the new SmartHolder set from HAZET aims to always keep things tidy, arranging the most common bits in practical holders and combining them into useful sets.
ith a special mechanism, a row of eight bits folds up for easy access in the sturdy and easy to clean holder and folds back to allow for transport or space saving storage. When closed the magazines are securely locked in place and no bits are lost. The colour coding of the respective screw profiles and the bit sizes printed on the holder ensure consistent order and quick location of the bit required.
Developed and produced in Germany, the SmartHolders contain a choice of 16 short bits in two fold out magazine rows. HAZET-WERK – Hermann Zerver GmbH & Co KG offers a total of six new SmartHolder sets –three with short 25mm bits and three with long 50mm bits, for more flexibility in hard to reach places.
In order to become independent of external testing services, investing towards in-house testing technology can lead to an increase in process reliability and a reduction in maintenance costs. The SmartCheck product family from STAHLWILLE is ideal for mobile, as well as stationary, testing and offers the advantage of direct evaluation.
Three versions are available from STAHLWILLE, the SmartCheck USB for simple and fast data exchange with a PC; SmartCheck DAPTIQ with interface for integration into complex Industry 4.0 environments; and SmartCheck Angle for testing angle wrenches.
The entire SmartCheck product family is characterised by robust construction, precise measurement results and easy operation. The devices can be used in workshops or production halls, as well as in service vehicles. For an optimal viewing angle, not only the display but also the display holder and the base body can be rotated by 180 degrees. In addition to a power supply unit, connected either to the socket or via the USB port, battery operation is also possible. The display and membrane keyboard are also splash-proof and the housing is made of impact resistant plastic.
SmartCheck’s testing torque tools are available in different measuring ranges, from 1Nm – 1,500Nm, as well as offering a version for testing torque screwdrivers. The SmartCheck Angle has a measuring range upto 720 degrees and enables the testing of angle wrenches up to 400Nm.
In addition to the SmartCheck product family, STAHLWILLE also offers the electronic tester 7077 W with small dimensions and flexible mounting options. The device can display the trigger torque and the actual torque applied at the same time, with the data shown on a separate display that is connected to the tester via a spiral cable.
The new grip lock washers from Gala Precision Engineering Ltd have been engineered with unique radial ribs, on both sides, to help prevent loosening under dynamic stress and maintain the integrity of bolted joints in high vibration environments.
eaturing a robust fastening mechanism, as well as radial ribs embedded into the mating surfaces, the grip lock washers ensure the preload force is retained even under heavy dynamic loads – a mechanism that is crucial for applications where stability and reliability are paramount. By helping to prevent the loosening of bolted connections, the new washers also reduce maintenance costs and operational downtime.
To withstand harsh conditions, the new washers are treated with advanced surface coatings such as zinc flake coating and mechanical zinc plating, which provide excellent corrosion resistance, thus extending the lifespan of the washers and ensuring long-term reliability. Additionally, the washers have been tested according to DIN 25201-4 and DIN 65151 standards, a testament to their reliability under dynamic loads. Available from sizes M6 to M30, and suitable for all property classes up to 12.9, the new range is a versatile solution for numerous applications – from heavy machinery and equipment to the construction industry. The washers are an addition to Gala’s extensive range of anti-vibration products including Gallock wedge lock washers, disc springs and other special fastening elements.
www.galagroup.com
Corrosion is a growing concern across industries, with requirements increasing in environments where accelerating factors, such as humidity, heat, and air pollution, are combined. The Neutral Salt Spray Test (NSST) according to ISO 9227 is one of the most established methods to verify corrosion resistance.
The corrosion resistance of all steel wedge-locking washers with zinc flake coating from Nord-Lock Group promise at least 1,000 hours in a salt spray test. However, constructors can expect significantly more hours than that, as Nord-Lock washers consistently surpass 1,000 hours easily during tests. These NSSTs ensure optimum performance over time, even in the most extreme environments.
Corrosion occurs when metals come into contact with humid air or water. Corrosion will eventually weaken steel parts and can potentially impact their function, forcing operators to increase repairs which decreases productivity. It can impact structural integrity and therefore cause accidents. Extreme environments demand more, but regardless, corrosion will occur sooner or later and can jeopardise the whole application, not just the bolted joint.
Understanding exactly how extreme factors such as pollution are impacting applications and using this experience as the basis for product developments is increasingly important. Whatever the environment, Nord-Lock Group collaborates with customers globally to meet needs and specifications, including providing necessary certifications.
“Customers need washers that can withstand extreme environments for a longer period of time. Based on this, we continuously put more focus on increasing the corrosion resistance of our standard products,” explains Anders Knutsson, coating and corrosion expert at Nord-Lock Group.
Although 1,000 hours is the official number released by the Group, this is just the minimum amount of time Nord-Lock steel washers with zinc flake coating by DELTA PROTEKT® can withstand corrosion in a salt spray test. The quality testing the Group does, as part of ensuring its high-quality standards, clearly shows the washers generally endure much longer.
“We have perfected our coating process so that we can guarantee 1,000 hours. But if you look at the results of the salt spray tests that we do every week, the washers on average do endure way longer than that in the salt spray chamber before any signs of corrosion occur,” highlights Anders. According to ISO 12944-6:2018, 1,000 hours in a salt spray chamber corresponds to at least C4 High or C5 Medium conditions.
The Nord-Lock standard range includes Nord-Lock Original Washers and X-Series washers, with standard and enlarged (SP) outer diameter, and Steel Construction (SC) Washers. High corrosion
resistance for such a large range of washers allows customers to secure applications when facing a wide variety of challenges. This is especially helpful when the industry uses galvanised bolts which, combined with Nord-Lock steel washers, provide a very high corrosion resistance for the whole assembly.
Galvanised bolts are used within the wind power industry and according to Sales Manager Brian Troest, pairing them with Nord-Lock steel washers is very beneficial as more and more wind turbines move offshore. “Steel washers are used onshore and offshore, inside the towers and on blade bolts, where they can be exposed to the environment,” highlights Brian.
Galvanised bolts are also often used in construction. If steel washers are used in a polluted environment with galvanised bolts, the combination is very durable against corrosion.
Big cities in Europe and the rest of the world are facing difficulties with a high-level of pollution. In some parts of the world, Asia for instance, corrosion is also propellered by a humid climate. The high-quality of the coating on the Nord-Lock washers fits all ranges of potential climate scenarios that the steel might face.
A stable production with rigorous process controls is the most important way to ensure customers do not encounter problems in the field. Nord-Lock’s testing facilities with state of the art equipment in Europe, the United States and Asia, combined with collaborations with external test centres, enables its customers all over the world to know they can rely on its quality. Nord-Lock Group also performs customer specific tests if a specific assembly needs verification .
Oil and gas applications, power generation, and industrial machinery, must operate in some of the most aggressive conditions on Earth. Nord-Lock washers made of 254 SMO™ are specifically developed to protect bolted joints in saltwater applications. As well as this, washers made from Alloy C-276 are the most reliable for acidic environments.
Nord-Lock Group will continue to provide material and product selection guidance to ensure the best solution for every application.
www.nord-lock.com
The new RIV943 hydropneumatic riveting tool from Rivit features an enhanced motor, making the tool both powerful and flexible, as well as suitable for a wide range of fastening needs.
RIV943 features a one stage operation to enable rivet nuts to be deformed and unscrewed in a single step, as well as a double adjustment force of 32,000N and 10mm stroke, which is adjustable by pressure switch and ring nut – enabling faster and more precise actuation.
Tec-Bond® 240-IN is a water-based threadlocker adhesive from Tectorius® that combines the reliability of epoxy chemistry with solvent-free technology.
Meeting REACH and RoHS compliance standards, the new thread adhesive is suitable for all types of threaded fasteners and performs well in temperatures ranging from -40°C to 175°C. It offers resistance to humidity, and extended storage capabilities, and possesses a room temperature curing formula ensuring the adhesive remains dormant until the fastener is installed.
tesa® is expanding its portfolio with the new tesa® 64295, a transport securing tape manufactured in answer to the increasing demand for more sustainable transport securing solutions.
The tape was specially developed for the secure fastening of loose or moving parts during the transport of household appliances. It offers reliable adhesion and can be disposed of after use together with the packaging material without impacting the recycling process.
E-Z LOK, a manufacturer and master distributor of threaded inserts for metal, plastic and wood, has received ISO 9001 certification.
With a quality management system that conforms to ISO 9001 in place, the company can now meet customer and other stakeholder needs within statutory and regulatory requirements related to products.
With new standards of automation, speed, flexibility, and stability, WEBER Schraubautomaten GmbH is introducing its next generation insertion system – the SBM25.
Fasteners are provided through a feed system that makes it possible to feed the next fastener already in the insertion process, significantly reducing the overall process duration. Standard blind rivet nuts from M4 to M10, as well as blind rivet bolts from M5 to M8, can be used.
Designed for use in the construction of steel building frames and bridges, the 40V max XGT® shear wrench from Makita is capable of delivering up to 250 M22 tightened torque control bolts per charge.
Powered by one 40V Max XGT ® battery, and an efficient brushless motor for maximum fastening performance, the 40V Max XGT ® shear wrench also offers a significant weight reduction of up to 1.59kg less than the previous LXT ® model. The tool also features an electric brake enabling it to be repositioned faster for increased productivity.
www.kaleliler.com.tr/en export@kaleliler.com.tr
3 Star Rivet 191
310 Express 198
A. Agrati SpA 51
Abbey Clamps 15
Achilles Seibert GmbH 11
Acton 195
Advance Spares 197
Albert Pasvahl GmbH + Co 9
Alexander Paal GmbH 7
Ambrovit 1, 13
APM Hexseal 179
Astrotech Steels Private Ltd 137
Atlantic Man 114
BBA Fasteners Srl 111
Bendfast 195
Beneri SpA 107
Berardi Group 163
Berdan Bolt 129
Bonotto Packaging Srl 80
Bontempi Vibo SpA 91
Bossong 97
Bralo 187
Brugola OEB Industriale SpA 87
Bulloneria Del Toce 62
Bülte GmbH
Kunststofferzeugnisse 143
Buora D.P.U. Srl 201
CAMCAR Innovations ( TORX® Ttap) 193
Canali Srl 104
Carlo Salvi 49
CEIA 115
Chavesbao 21
CITT 56
Colombo Giovanni & Figli Srl 89
Colombo Special Fasteners 57
CZ Fasteners Parts Co Ltd 155
Dell’Era Ermanno E Figlio Srl 99
Dell’Era Giuseppe 81
Dimac Srl 55
DIV GRUPA d.o.o 166
Don Quichotte B.V 149
Doss Visual Solution Srl 109
DS Fasteners 204
E.CO Srl 74
EcoClean GmbH 158
Euromac International Sp z.o.o 151
Fast Trade 45
Fastbolt 2
Fastdev Srl 94
Fastener + Fixing Magazine 71
Fastener Fair Global 135
Fastener Fair Italy 121
FastFixSearch.com 181
FastFixTechnology.com 117
Fixi Srl 15
Flaig + Hommel GmbH Verbindungselemente 187
Fong Prean Industrial Co Ltd 203
Fürniss GmbH 151
G&B Fissaggi Srl 85
Gala Precision Engineering 33
Graewe GmbH & Co KG 161
Growermetal SpA 101
Hafren Fasteners Ltd 175
Halfmann Schrauben GmbH 47
HAŠPL a.s. 193
HEICO Befestigungstechnik GmbH 123
Hellermann Tyton GmbH 173
Hisener 4, 5
Hobson Engineering Pty Ltd 147
ETA-CE anchors for structural applications, including C2-C1 categories,for use in high seismic hazard zones.
The CE marking is everywhere. But it’s only now that you’ll find it on one type of securing washers.