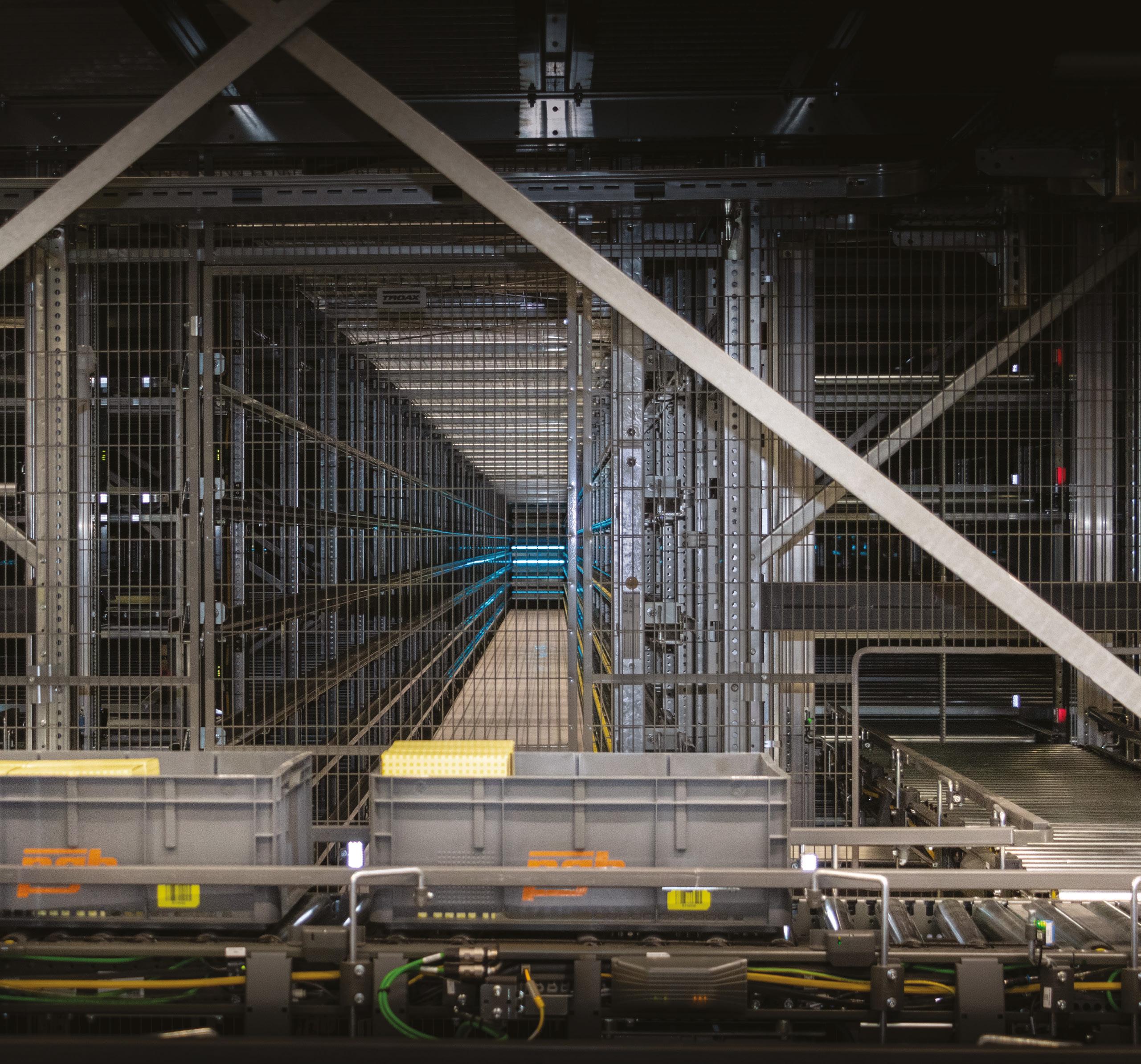
C ome meet us at the Fastener Fair Global! Hall 1, booth 836
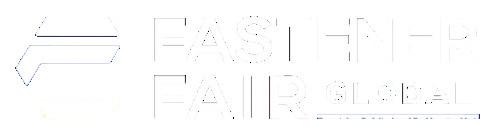
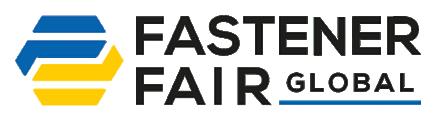
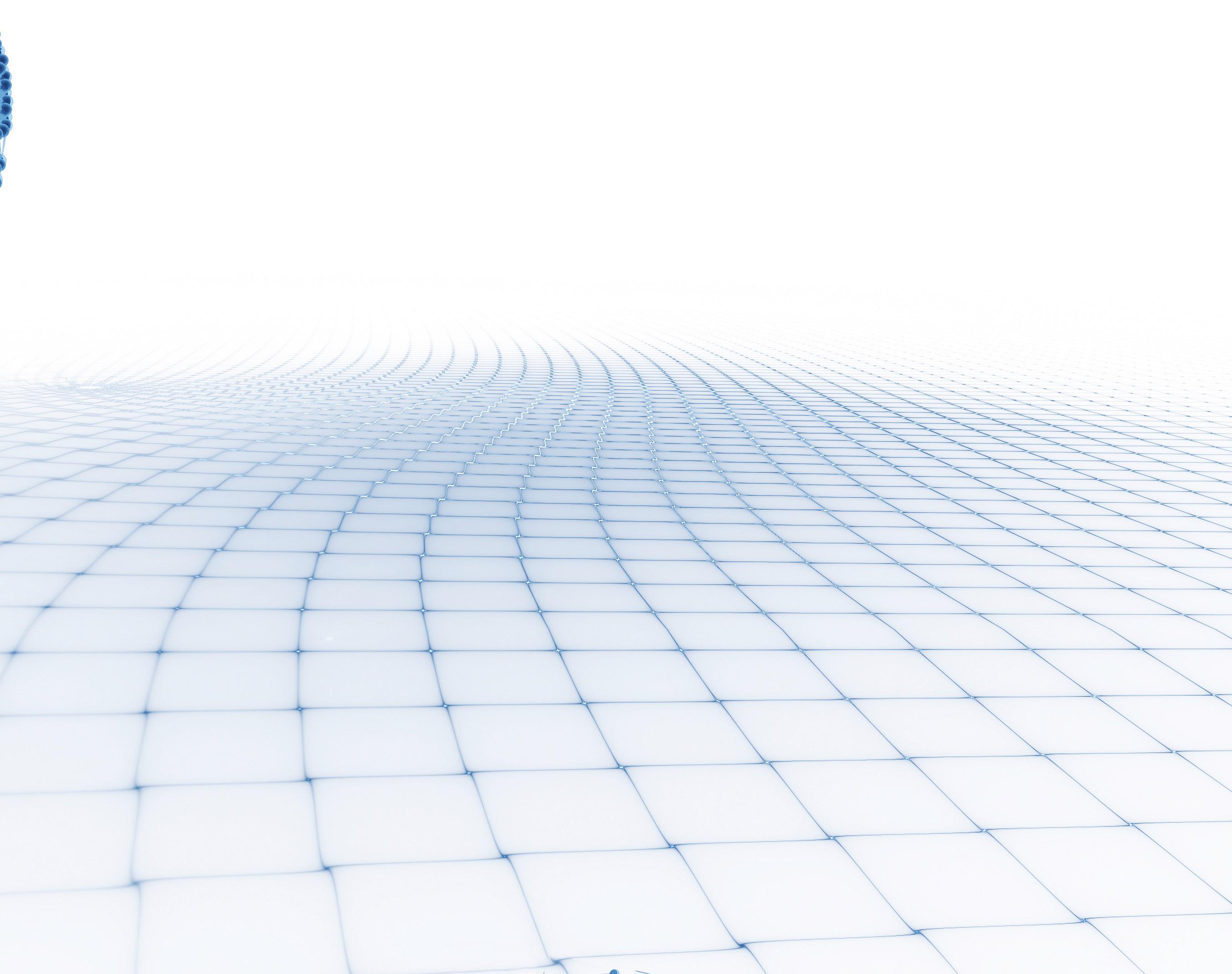
25 - 27 March
Stuttgart, Germany
BOOTH #3-2004
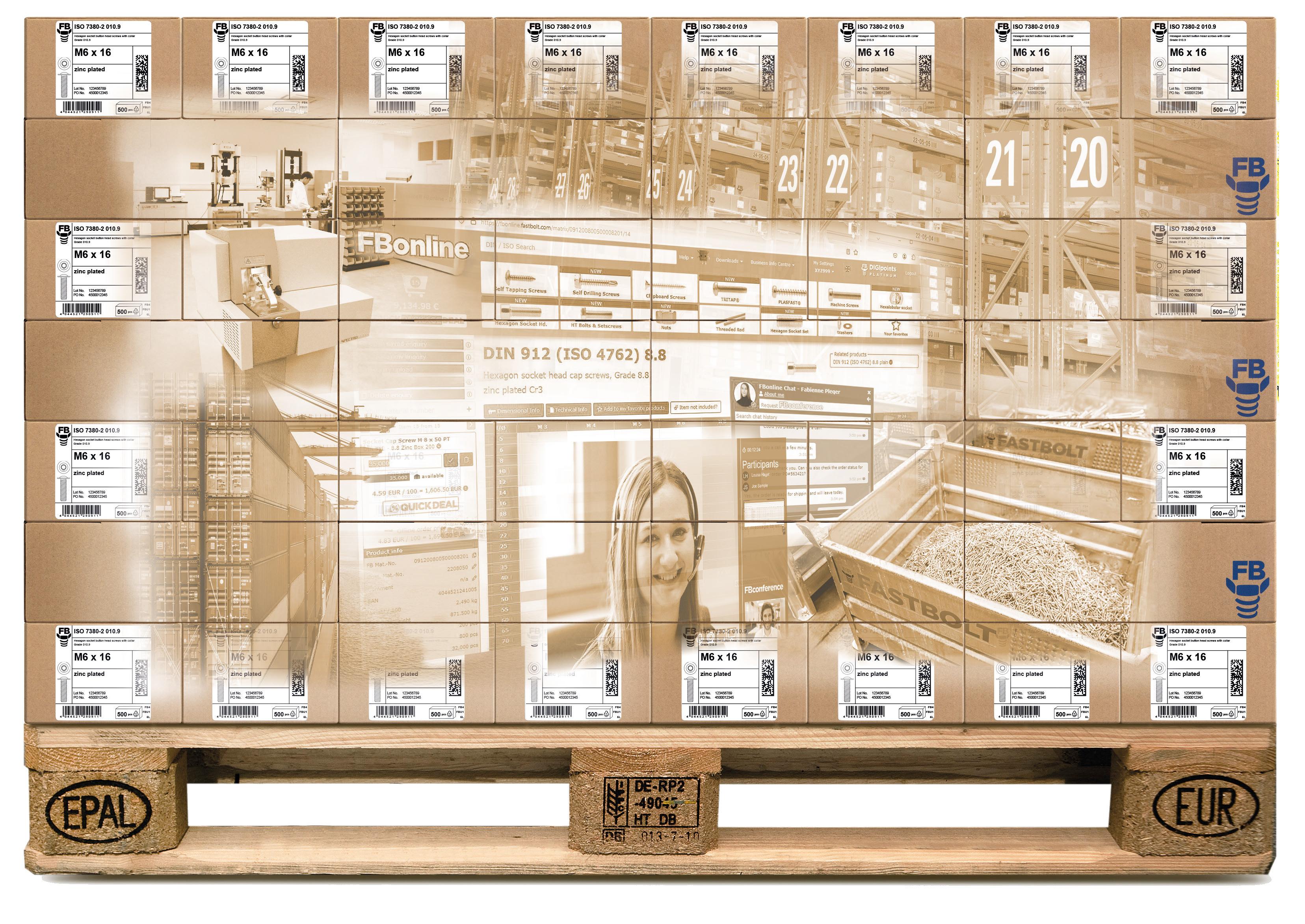
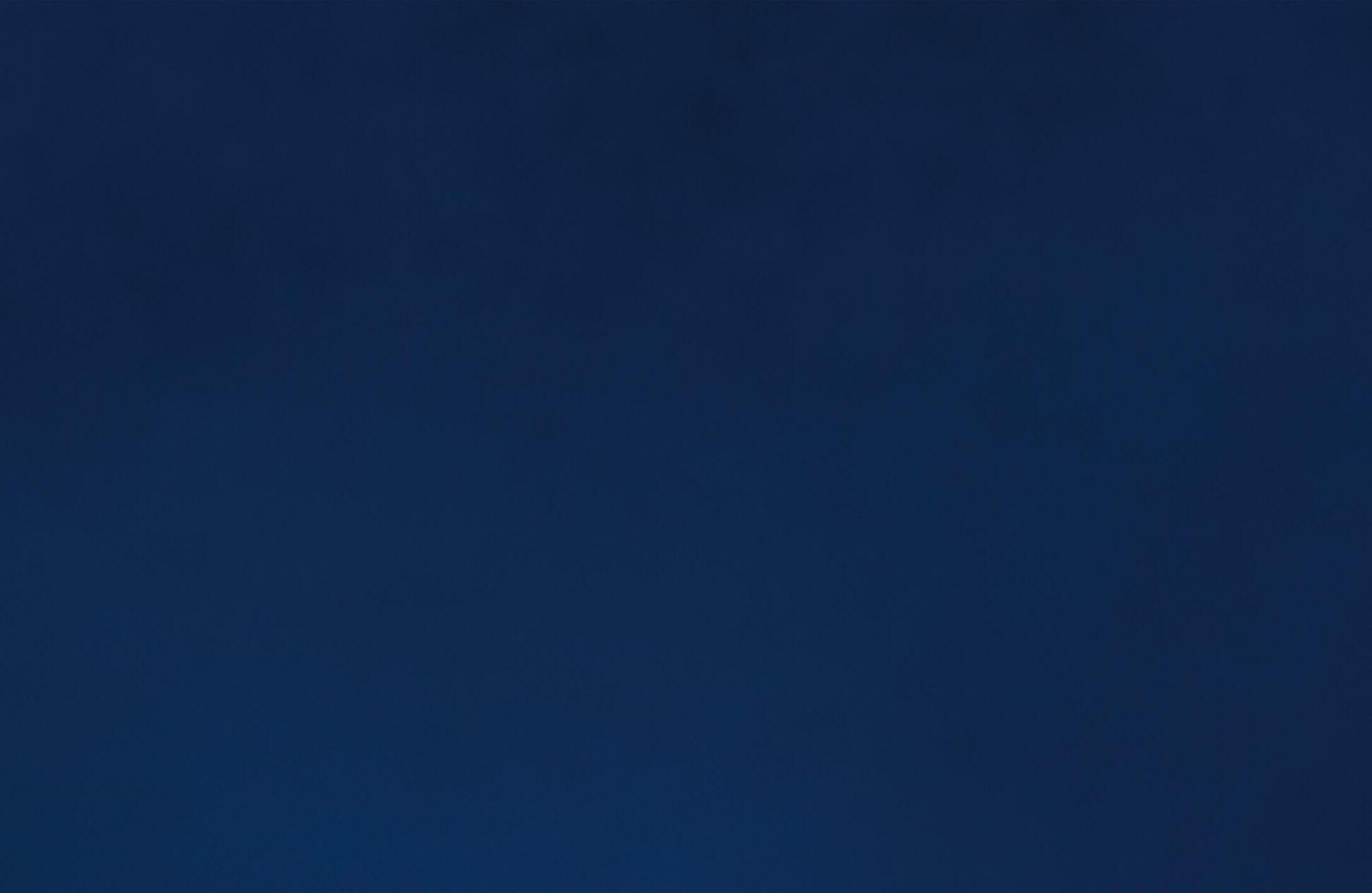
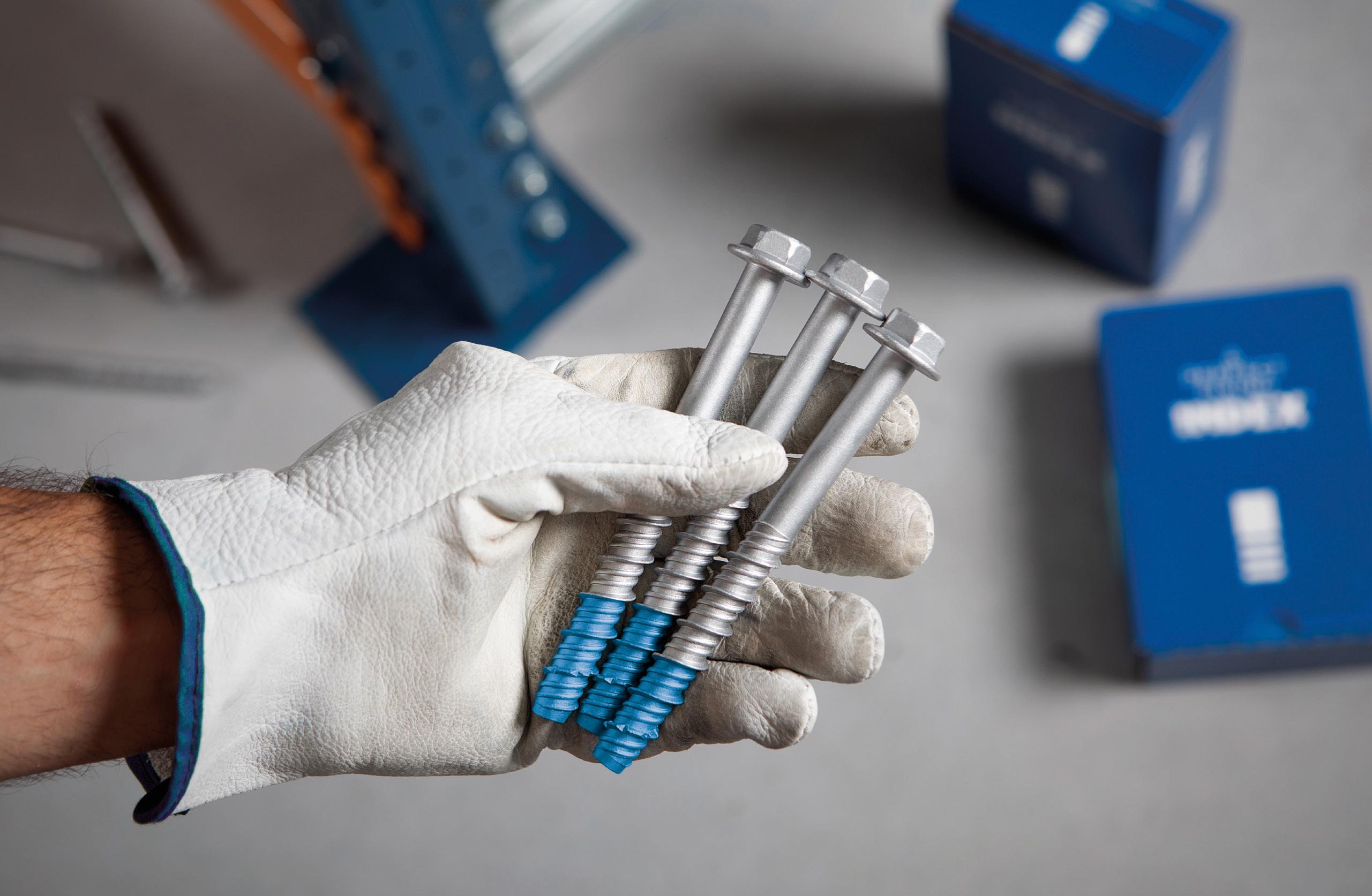
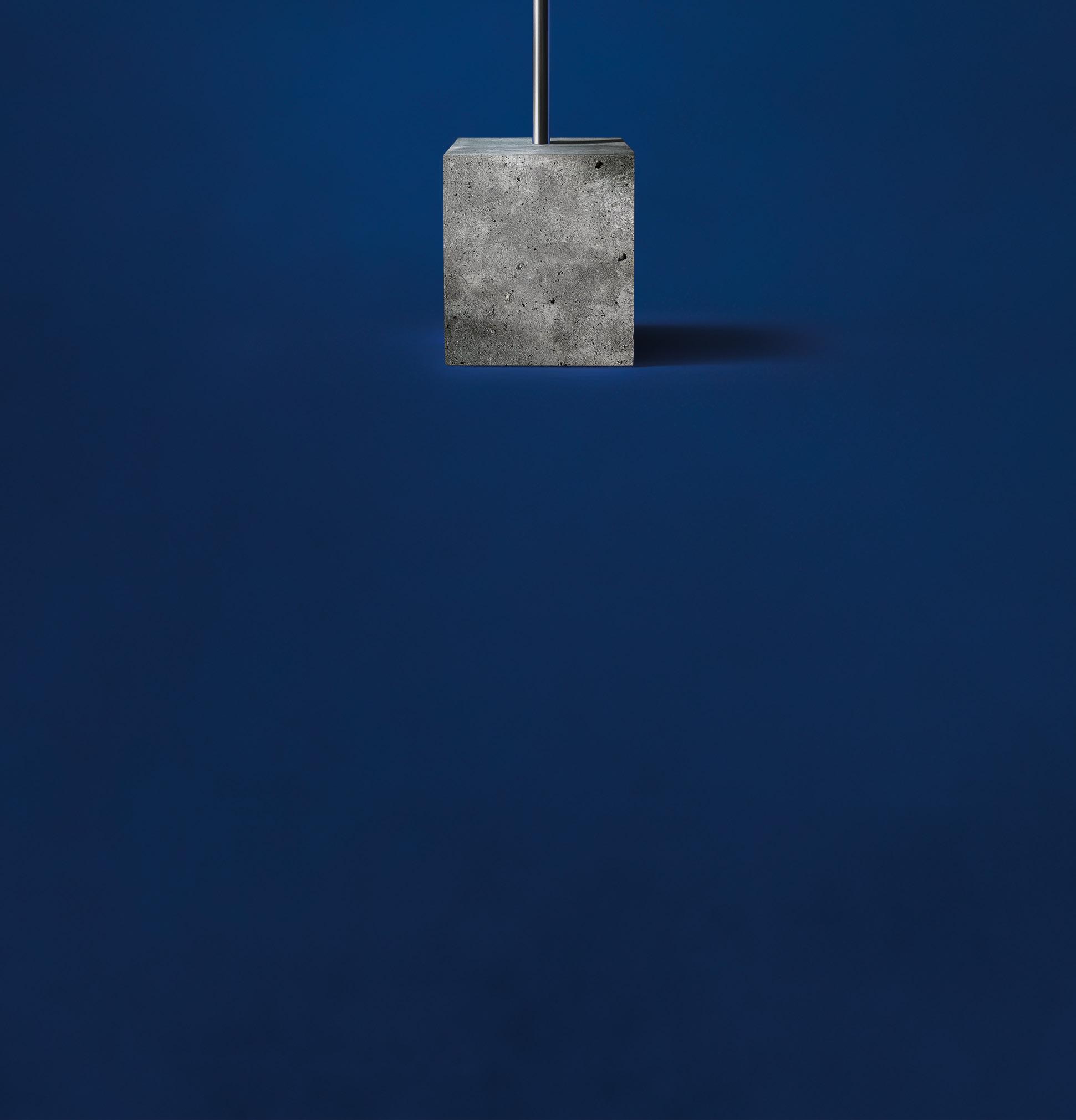
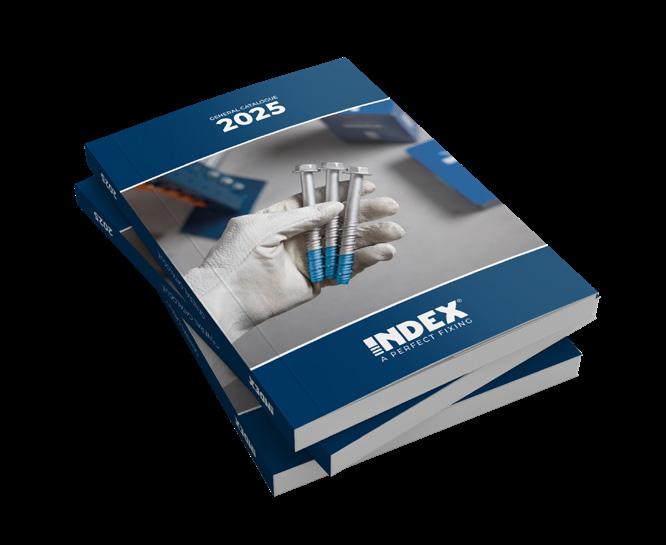
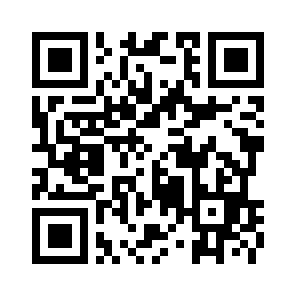
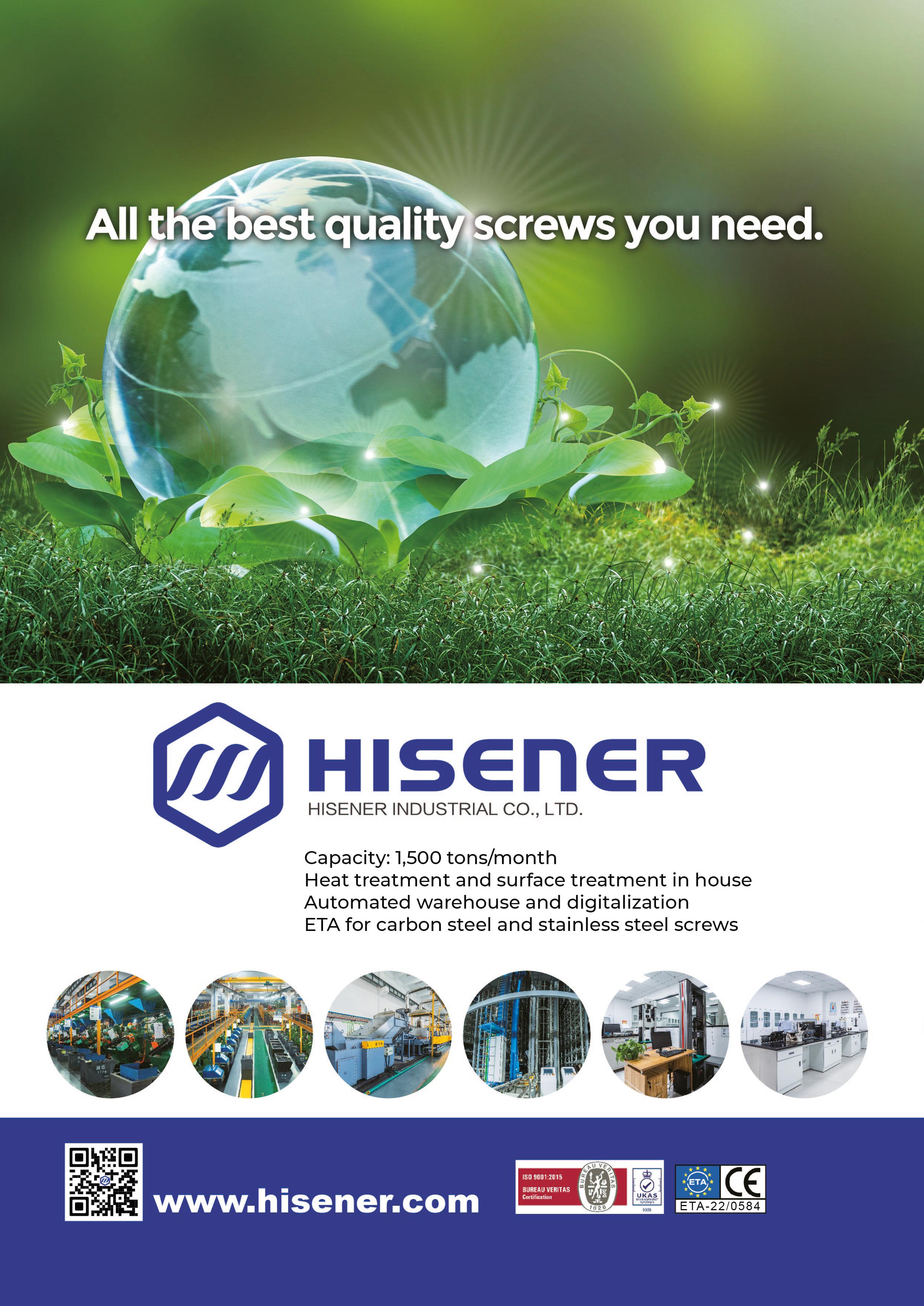
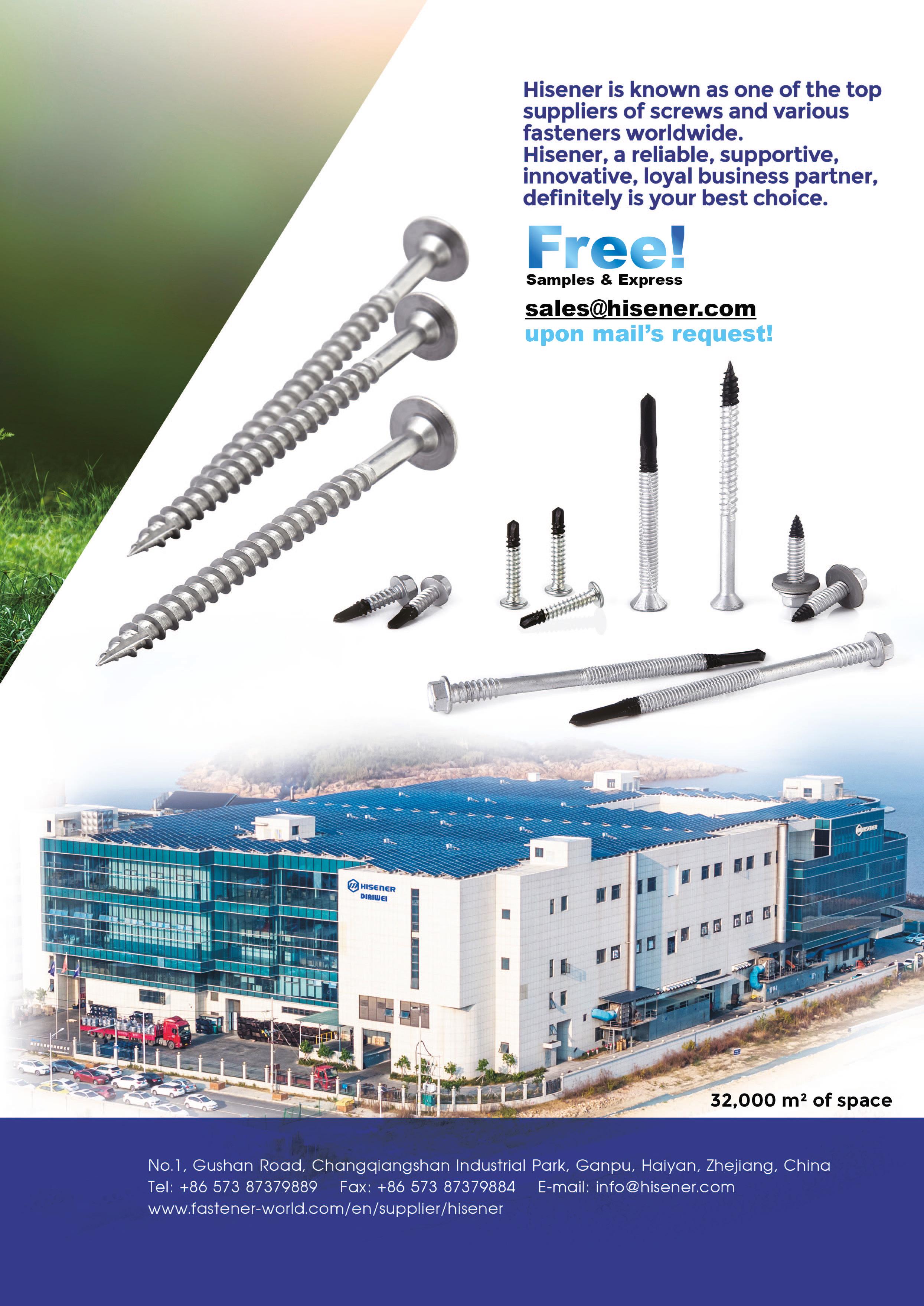
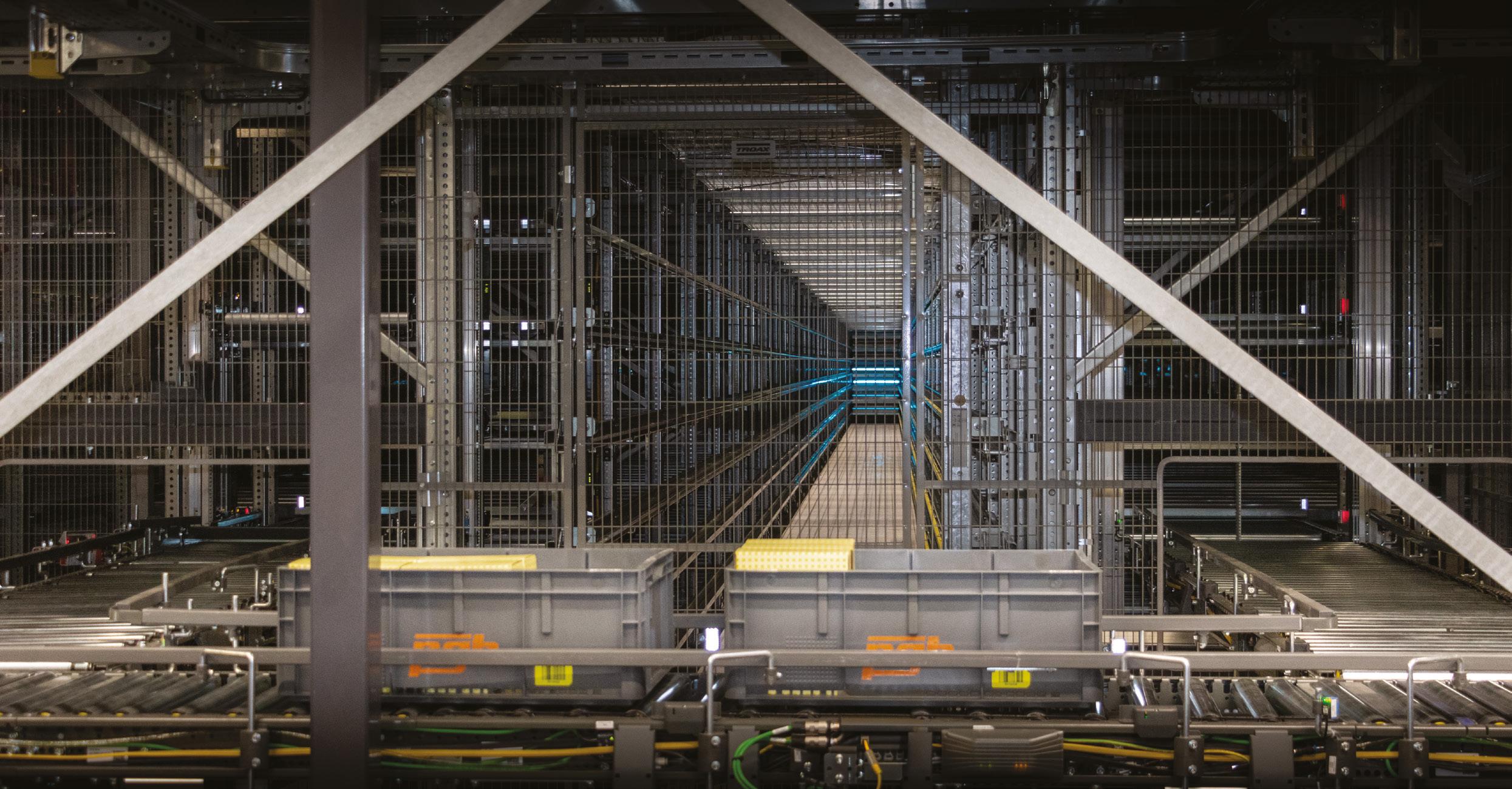
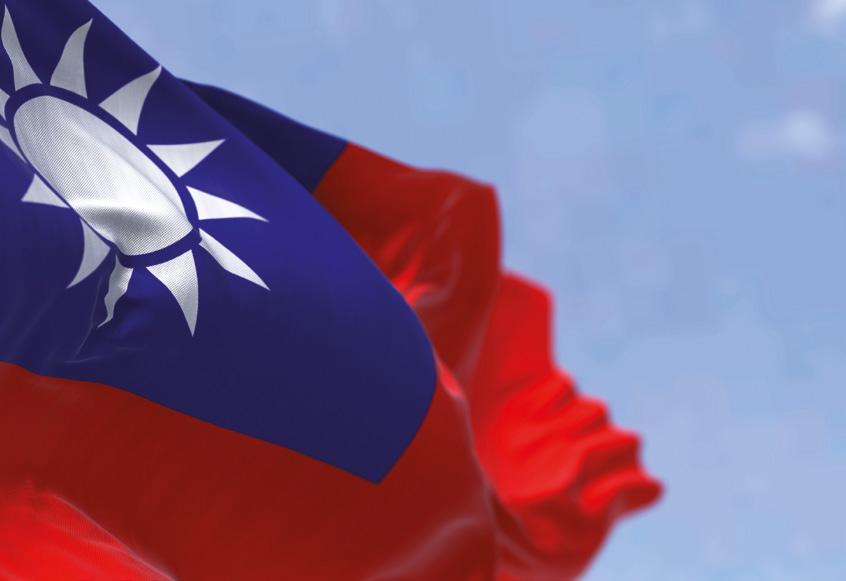
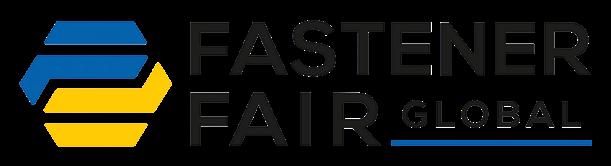
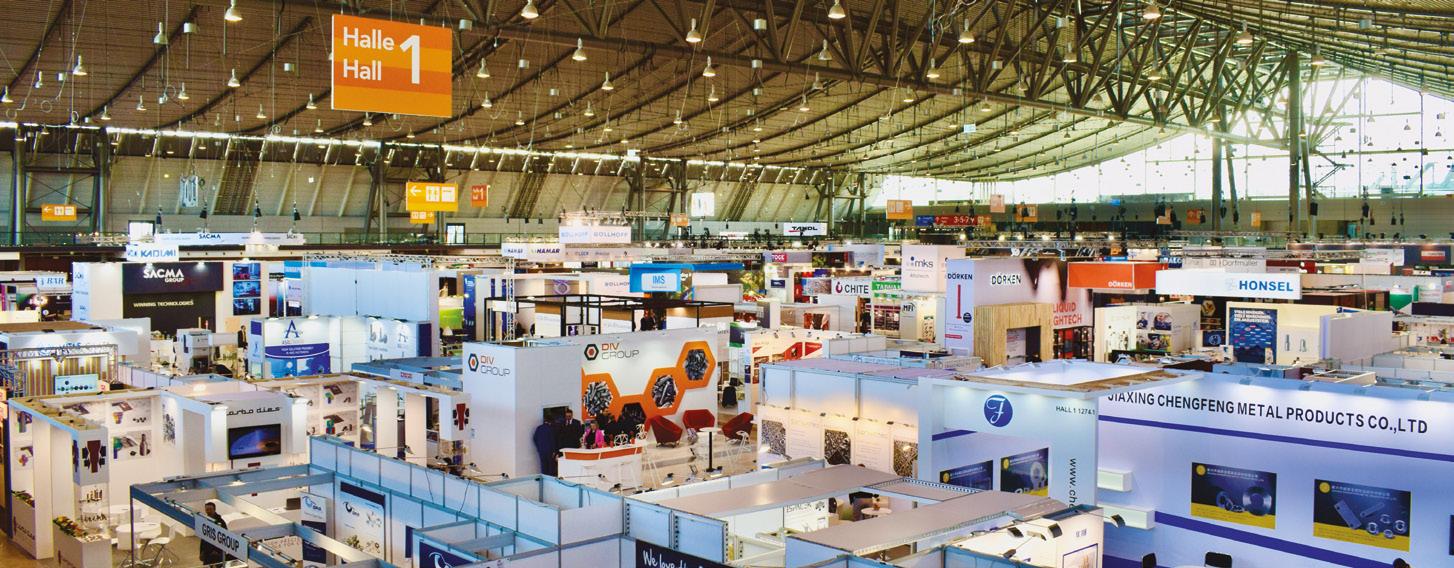


C ome meet us at the Fastener Fair Global! Hall 1, booth 836
25 - 27 March
Stuttgart, Germany
BOOTH #3-2004
Claire Aldridge, editor, Fastener + Fixing Magazine
The new year is a time to celebrate new beginnings, set goals and embrace the potential of the year ahead. So what will 2025 bring you? Opportunities? Challenges? Innovations? As always, this magazine will continue to be with you every step of the way.
ithout our readers and the relationships we’ve forged over the past 27 years, the magazine would not be what it is today. In my new role as Editor, it’s important for me to continue what we do best – talking to you, visiting you, understanding your challenges and goals for the future, as well as making sure we’re keeping you up to date with everything you need to know.
Fastener Innovation’ logo on their stands – so make sure you look out for them.
A company that will have a big presence at the show is pgb-Europe, the focus of this issue’s Cover Story. As one of the leading suppliers and manufacturers of fasteners and anchors, pgb-Europe highlights how it is taking the next step in the development of its sustainable growth plan, through the construction of a new automated shuttle warehouse – with 40,000 storage locations.
How fitting then that 2025 brings with it the 10th Fastener Fair Global show in Stuttgart, taking place from 25 th – 27 th March at Messe Stuttgart in Germany, as a platform for the entire fastener and fixing industry to network and showcase their technologies under one roof. As the show’s official media partner, we have an extensive preview of the companies and products that you can expect to see, as well as a full exhibitor list to help you plan your days. The whole Fastener + Fixing team will be at the show – so please do come by hall 7, stand 4040, to say hello – we’d love to see you.
We’re also once again hosting the Route to Fastener Innovation Competition, which gives visitors a first-hand opportunity to see new products and services that exhibitors have brought to the market since the last show. Entrants to the competition will have a special ‘Route to
In addition, we have a special ‘Made in Taiwan’ feature with articles from Taiwanese manufacturers that focus on the continued developments in products, and services, and in particular how they’re responding to CBAM. We also have an in-depth article from one of our Taiwanese media partners – Fastener World, which gives an insight into the Taiwanese fastener market and some of the challenges manufacturers are facing in an increasingly global and competitive market.
You’ll also find our special features within the magazine including ‘Chemical Anchors + Resins’ in Construction Fixings, ‘Aerospace Fasteners’ in Application Technology, as well as ‘Stainless Steel Fasteners’ and ‘Torque Wrenches’ in Products.
www.fastenerandfixing.com
Published by
Managing Director
Jamie Mitchell jamie.mitchell@verulammedia.com
Content Director
Will Lowry will.lowry@verulammedia.com
Editor Claire Aldridge claire.aldridge@verulammedia.com
Assistant Editor Rebecca England rebecca.england@verulammedia.com
Sales Director Mac Rahman mac.rahman@verulammedia.com
Business Development Manager –Italy
Emiliano Pagliaroli emiliano.pagliaroli@verulammedia.com
Business Development Manager –DACH & Europe
Chantal Ridings chantal.ridings@verulammedia.com
Production & Design Manager Lee Duskwick lee.duskwick@verulammedia.com
Disclaimer
25. - 27. MÄRZ 2025 HALLE 1, STAND 412
Fit bolts, plugs, knurled thumb screws, square head bolts, flat headed screws, hexagon set screws, brass screws and specials.
Fon +49 (0) 40 532 852-0 · info@pasvahl.de
PennEngineering® has announced the appointment of Gerard Quaid as the new managing director of PEM® Europe, effective immediately. Gerard Quaid (Ger) takes on the role with a wealth of experience and a steadfast commitment to continuing the company’s legacy of innovation, operational excellence and customer centric solutions.
Ger comments: “It is a privilege to step into this role. For decades, PEM® has been synonymous with solving customer challenges, empowering employees and delivering consistent value to stakeholders. I am honoured to lead this remarkable organisation and am committed to building on its strong foundations as we navigate the opportunities and challenges ahead.”
Under Quaid’s leadership, PEM ® Europe is committed to solidifying its status as a global leader in self clinch fasteners, connection solutions and insertion technology. The company’s strategic vision emphasises robust growth driven by customer centric innovation and collaboration, operational agility, speed to market and a steadfast dedication to manufacturing excellence and environmental accountability. By fostering a culture of curiosity and professional development
among employees, embracing advanced system selling approaches, and championing sustainable practices, PEM ® Europe is poised to continue delivering exceptional value to its customers while shaping the future of fastening and connection solutions.
PennEngineering ® has embraced digital transformation across its operations, most notably at its Galway manufacturing plant, where the integration of cutting edge technology has improved productivity and operational control. These advancements were recently recognised with the Medium Lean Business of the Year Award by Lean Business Ireland.
Additionally, the company’s new UK and Poland offices and warehouses strengthen its presence across the region, offering comprehensive fastener stock and a dedicated sales team to enhance customer support and streamline logistics.
“As I take on this role, my focus will be on protecting PEM ® ’s legacy while advancing our vision for a future of sustainable success,” adds Ger. “We are where our customers are, and we will continue to prioritise innovation, operational excellence and stakeholder value at every step.”
PEM ® Europe looks forward to an exciting new chapter under Gerard Quaid’s leadership, advancing its mission to deliver reliable, efficient, and tailored solutions, for a dynamic and ever evolving market.
Bufab has acquired VITAL SpA, an Italian distributor of C-parts with net sales of €48 million in 2023, headquartered in Milan, as well as two additional branch offices.
VITAL has been family owned since its foundation in 1975 and is today run by the founder’s sons, who will continue to manage the business. Its customers are primarily located in Italy from industries such as electrical, machinery, rail and construction. In recent years, VITAL has achieved excellent growth and profit, with 57 employees and net sales of €48 million in 2023 and an operating profit margin above Bufab’s 2026 profitability target.
The purchase price paid upon closing of the transaction amounts to €31.9 million on a cash-free/debt-free basis. In addition, a deferred purchase price of circa €11 million will be paid in two instalments in 2025 and 2026. Finally, a performance based additional payment (earn-out) of a maximum €11.2 million may occur in 2025, 2026, 2027 and 2028 conditional on improved operating profit. The acquisition will be financed by Bufab’s existing credit facility.
“I am very happy to announce this acquisition, as we see VITAL as a great opportunity to build up our Italian footprint and increase our service level to the customers. In the future can be used as a platform for add-on acquisitions and drive market consolidation in a highly fragmented market. Furthermore, we see that Bufab and VITAL complement each other well. We will also deepen our presence in Italy and southern Europe by learning from the VITAL team with great and long experience in the region,” says Erik Lundén, president and CEO at Bufab.
“Over the past two years, we have gotten to know Bufab very well and are pleased to have found a partner that is a perfect fit for us. This deal comes at a good time in VITAL’s development and will enable us to accelerate our growth journey. We are pleased that we, the previous owners, can continue as managers, and together with the whole VITAL family we look forward to the cooperation with Bufab,” highlights VITAL previous owners Daniele Pesce, Stefano Pesce and Luca Bernasconi.
RANGE INCLUDES:
THE STANDARD DIN 912 | DIN 931 | DIN 933
HEXAGON HEAD DIN 6921 | ISO 4014 | ISO 4017 | DIN 960 | DIN 961
HEXAGON SOCKET HEAD DIN 7991 | ISO 10642 | DIN 6912 | DIN 7984 | ISO 7380 -1 & -2
THREADED SCREWS WITH HEXALOBULAR SOCKET ISO 14579 | ISO 14580 | ISO 14581 | ISO 14583
HEXAGON SOCKET SET SCREWS DIN 913/ISO 4026 | DIN 914/ISO 4027 | DIN 915/ISO 4028 | DIN 916/ISO 4029
THREAD ROLLING SCREWS DIN 7500 Form CE | DIN 7500 Form M
TAPPING AND DRILLING SCREWS DIN 7504 Form K | DIN 7981 | DIN 7982 |
HEXAGON NUTS DIN 934 | DIN 985 | DIN 980 | DIN 439 | DIN 6923 | ISO 4032 | ISO 7042
WASHERS DIN 125 | ISO 7089
PARALLEL PINS ISO 8734 | DIN 7979 Form D Achilles Seibert GmbH | Philipp-Reis-Straße 3 | D-24558 Henstedt-Ulzburg Phone +49 (0) 41 93 89 55 | sales@achill-fasteners.com
|
|
|
LeankCo SAS, the holding company of CLUFIX, has announced the acquisition of TITANOX Group –strengthening its position in the technical fastening market and underlining its ambition to become a leading global player in the fastener sector.
TITANOX, through its renowned brands such as RIVELIT® (blind rivets) and TITANOX® (self-clinching components), operates in France, Turkey, and China, boasting over 60 years of expertise in fastening technologies. Through high-quality products, and the technical proficiency of its product managers and sales teams, TITANOX has established itself as a key player in the market, supporting design offices in the search for assembly solutions.
The acquisition of TITANOX will enhance LeankCo’s international presence and innovation capabilities, as well as enable it to drive profitable growth through synergies between the two entities. It will also help strengthen LeankCo’s existing markets and help it diversify into strategic sectors connected to climate and energy transition, including decarbonised mobility, clean energy and sustainable construction.
Further benefits for LeankCo include the expansion of its product portfolio by incorporating complementary solutions, such as blind rivets and self-clinching components. Plus, it will enhance its support for global clients, especially those with a focus on the automotive market, by offering more personalised local services and increased expertise.
“This acquisition aligns with a clear strategic vision shared by the management teams of both CLUFIX and TITANOX, as well as majority shareholder Galiena Capital, to transform LeankCo into a global group able to anticipate market evolutions and meet growing demands of
more demanding industries,” explains LeankCo. “By integrating TITANOX we will equip ourselves with the necessary resources to continue innovating and supporting our clients in overcoming technical challenges, while consolidating our growth in rapidly expanding markets.”
Neuenstadt-based FÖRCH Group, supplier of products for workshop supplies, assembly and fasteners for trade and industry, has acquired 100% share capital of its export partner Ziebe Ltd.
Ziebe has been active in the UK market since 2002, specialising in providing the automotive aftermarket with C-parts. The company has 15 employees and generates annual sales of circa GB£1.5 million (€1.7 million). Through this acquisition, FÖRCH will be represented by 23 companies across Europe in 2025.
“Our business continues to operate as usual and will continue to offer excellent service to the trade. We look forward to enhancing our product range and services to optimise the customer experience,” highlights Terry Slade, who will continue to operate as managing director at Ziebe – in partnership with Andreas Pescht, managing director at FÖRCH Group.
Andreas adds: “This acquisition further enhances the FÖRCH parts distribution business and provides a solid platform for continued growth across Europe and in particular provides direct access for an increase in market share of the high potential UK market place.”
Ahlsell Sverige AB has entered into an agreement to acquire all shares in Inseco AB, a provider of industrial fastening products and services for the engineering industry, as well as the power and energy sectors.
Through this acquisition, Ahlsell is strengthening its offering in industrial fastening, gaining increased expertise, a broader product range, various VMI (Vendor Managed Inventory) solutions and enhanced availability in a new geographic area. Additionally, Ahlsell expands its market position and can offer an even more comprehensive service in fastening to industrial customers.
Inseco AB has twelve employees and generates an annual revenue of approximately SEK 50 million (€4.3 million). The company is based in Söderhamn, Sweden.
Ileana, Daniele, Luca
Our lives and our tasks in the company are different, but we are united by the passion we put into our work. Because at Ambrovit it is the people who make the difference. AMBROVIT HAS ALWAYS PLACED PEOPLE AT ITS CORE
With effect from 1 st January 2025, three positions on Würth Group’s boards have been filled with new members – supervisory board, advisory board and executive vice-president of arts and culture.
Prof Reinhold Würth, the prominent leader of the Würth Group for decades, will hand over his position as chairman of the supervisory board to his grandson Benjamin Würth. Benjamin has been working for the company for 25 years and has gained extensive professional experience both at a national and international level. Reinhold Würth will remain honorary chairman of the supervisory board.
Secondly, the advisory board consists of nine members, most of which are non-family members. It has been chaired by Bettina Würth, the daughter of Reinhold Würth, since 2006. Bettina will hand over her position as chair of the advisory board to her nephew Sebastian Würth. Sebastian has been working for the company since 2012 and holds a Master of Arts in Family Entrepreneurship. Bettina is also a member of the supervisory board and will become honorary chairwoman of the advisory board.
Finally, Sylvia Weber, in charge of art and cultural activities, will transfer most of her tasks to Maria Würth, the daughter of Bettina. Maria holds a Master of Arts in Art History from the University of Tübingen and, mentored by Sylvia, has prepared herself for this position since 2018.
LISI AUTOMOTIVE, a subsidiary of the LISI Group, is pursuing its refocusing strategy and has entered into exclusive negotiations with ZeroBaseInvest GmbH with a view to selling its French subsidiary LISI AUTOMOTIVE NOMEL SAS.
ZeroBaseInvest GmbH submitted a firm offer to LISI AUTOMOTIVE with a view to acquiring 100% of the shares in LISI AUTOMOTIVE NOMEL, which specialises in the manufacture of nuts by cold heading and washers by vertical cutting, notably for the automotive and industrial/distribution markets.
This subsidiary, located in La Ferté Fresnel, France, achieved sales of around €35 million in 2024, drawing on significant positions with automotive manufacturers including Stellantis, Renault, VW, Nissan, as well as industrial distributors and manufacturers of screws and cage nuts. LISI AUTOMOTIVE’s subsidiaries will continue to purchase washers and nuts for its customers’ automotive applications.
This acquisition project completes the range of nuts produced by ZeroBaseInvest through its subsidiary ZB M+F, acquired from LISI AUTOMOTIVE FORMER in 2020. This disposal will enable LISI AUTOMOTIVE to continue refocusing its activities on high value-added fastening solutions and mechanical components for its automotive customers.
This transaction is subject to certain conditions and obtaining the usual required authorisations. It should be completed by the end of February 2025.
From 1 st November 2024, the company
SI. COP Etanco Srl, also known as Etanco Italia, will be incorporated into Friulsider SpA.
The merger is one of the natural consequences of the acquisition of the French Etanco Group, by the American multinational company Simpson Strong-Tie, which took place in 2022. It is part of a series of synergies implemented in order to consolidate the Group’s presence in Europe.
Friulsider’s production and logistics spaces have recently been strengthened, to support growth and accommodate the Etanco business unit, optimising flows and management, while the commercial offices and the operational headquarters will remain in Milan to ensure continuity of service to customers.
SI. COP Etanco is the Italian branch of Etanco Group, specialised in the sector of fixings and accessories for ventilated roofs and façades since 1952. The Etanco business, unlike Friulsider, provides a direct sales model and strong support on the design side. The Group serves over 18,000 customers distributed in more than 50 countries worldwide, generating a turnover of €260 million per year.
The British & Irish Association of Fastener Distributors (BIAFD) is introducing a new Technical Group to bring together the expertise of more than 100 specialists from its member companies, to share knowledge and inform on standards development.
BIAFD’s new Technical Group aims to reflect the all too often forgotten fact that fasteners and fixings are technical, engineered products complying to detailed international standards, performing in increasingly demanding and critical applications.
Over the last decade, BIAFD has more than lived up to its commitment to ensure its members are better informed, providing information and support on the seemingly relentless tide of regulatory developments, economic and global factors impacting their businesses. Recent BIAFD meetings have addressed topics including EU and UK trade remedies, volatility in the global container freight market, through to the currently dominant topic of the EU Carbon Border Adjustment Mechanism regulation and its soon to be introduced UK counterpart.
At the 2024 BIAFD Autumn Meeting, Maddy Webb, head of risk and internal audit at Trifast Plc, presented an impassioned case for remembering that fasteners and fixings are technical, engineered products functioning in increasingly complex and demanding applications. She proposed, and BIAFD members wholeheartedly agreed to, a new BIAFD Technical Group, that would bring together the quality, compliance and technical specialists from more than 100 BIAFD members, to provide a forum to discuss and share non-competitive information and expertise.
BIAFD has long been well represented on the British Standards Fastener Committee FME/9. The new Group will disseminate information from BIAFD members of that Committee on standards developments and, equally important, provide a mechanism to deliver feedback to the Committee from hands-on practitioners.
Maddy explains: “Fastener standards are evolving to suit new applications, particularly the development of large diameter bolts for use in power generation, and it is likely that changes in steel processing
will result in changes to heat treatment practices, driven by green steel and carbon footprint reduction. The BIAFD Technical Group has the opportunity to influence the development of technical standards through the BSI Fastener Standards Committee, and to understand these changes and communicate them to their organisations, allowing business risk and opportunities to be evaluated effectively.”
She continues: “In many fastener distribution businesses there is a growing gap between technical teams and commercial teams, with roles increasingly filled by business graduates and software or data tools, where there once might have been a team of engineers and inspectors. In fact, recruitment of technical team members, and providing technical training, is often a significant challenge, so bringing like-minded people together to facilitate discussion and debate is a core objective of the Technical Group.”
BIAFD has already established an email circulation to provide updates to its technical specialists. However, interactivity is a crucial aim of the new Group, so BIAFD now has a rapidly growing discussion forum on LinkedIn, on which specialists from member companies are encouraged to participate.
“As a Group we are right at the beginning of our journey,” says Maddy. “There is real need driving this. As the Group grows, we will establish a programme of speakers, technical and educational presentations, and of course a pub quiz!”
On 29 th November 2024, during the annual general meeting of UDIB (Unione Distributori Italiani Bulloneria) in Palazzo Maccaferri in Bologna, Gian Marco Dalpane was unanimously elected as the association’s new president. The term of office is three years. Dalpane succeeds Riccardo Bonalumi, who did not stand for another term.
Gian Marco Dalpane is managing director and owner at La Bulloneria Emiliana Srl based in the province of Modena. He previously served as UDIB president from 2012 to 2021. Dalpane is also vice-president of the European Fastener Distributor Association (EFDA), of which UDIB is a member.
This is his statement after the election: “I am extremely proud to be able to represent UDIB for the next three years. I will endeavour to do my utmost to ensure security and cooperation for our members at this time of serious economic and legislative uncertainty. At the same time, I will try to maintain a high-level of cooperation with the European organisation EFDA, which represents us so well in Brussels.”
Opened in 1996, TR Italy has announced a significant sustainability achievement at its 6,110m 2 manufacturing facility in Umbria, Italy, with the installation of 1,395 solar panels on its roof.
Along with six inverters, the photovoltaic panels are projected to generate approximately 900,000kWh annually – approximately 25% – 30% of the facility’s electricity – making a substantial step towards reducing TR Italy’s environmental impact. During weekends when energy consumption is lower, TR Italy will also be able to sell surplus energy back to Terna, the operator of Italy’s national grid. This initiative is another example of TR’s commitment to enhancing its global ESG metrics.
Thanks to an innovative financial structure, this investment won’t result in major capital expenditure, as the installation is under a 12 year lease agreement with fixed monthly payments, offering a cost-effective solution that will lead to substantial savings over time.
Stefano Pisoni, managing director at TR Italy, comments: “As a company, we’re always striving to balance innovation with responsibility. This sustainability project is a perfect example of how we can reduce our environmental impact without compromising on the quality of our
products or the service we provide to customers. This installation not only aligns with our long-term goal for energy efficiency, but it also enhances the comfort of our employees. We’re proud to be taking meaningful steps towards a more sustainable future for TR Italy.”
Bulten and ZJK Vietnam Precision Components Co Ltd, part of the Chinese fastener company ZJK Precision Parts (ZJK), have signed a letter of intent to establish operations in Vietnam through a joint venture – to be called Bulten ZJK Vietnam Company Ltd.
Agreements have been signed between the parties with the aim of starting production in Vietnam in 2025. The background to the establishment is an increased demand for domestically produced micro screws among international customers in the consumer electronics industry with manufacturing in India and Vietnam.
In late 2023 Bulten entered into a joint venture with ZJK and Indian Radium Fasteners Private Ltd (Radium) for the manufacture of micro screws and now a similar establishment is planned in Vietnam.
“Bulten’s strategy is to grow within customer groups outside of automotive, which is our largest and most established segment.
In recent years, we have had good development in the consumer electronics segment, especially in Asia, and see this trend continuing. It is against this background that we are now taking the next step and establishing ourselves in Vietnam. This will increase Bulten’s sales volumes and benefit profitability,” says Christina Hallin, interim president and CEO of Bulten.
The new joint venture plans to rent production facilities, which means limited investment costs and risk taking for Bulten. Bulten’s ownership in the planned company will be 51% and ZJK will own the remaining 49%.
Since its creation in 1974 by Jack Lanfranco, J LANFRANCO & Cie has specialised in the field of high-end safety fasteners. In December 2024, the company celebrated 50 years of manufacturing single and double slotted self-locking nuts, as well as its unique expertise in fastener loosening issues in the traditional industrial sector.
Based on a strategic vision, as well as an ability to adapt and focus on innovation, J LANFRANCO continues to meet the needs of an ever changing market. Following the death of Jack Lanfranco in 1983, his sons Patrick and Thierry took over the reins of the company. While Patrick managed the commercial operations from Paris, Thierry supervised the production site in Bourges, known as the cradle of French bar turning.
Their leadership enabled J LANFRANCO & Cie to take crucial steps, including the relocation of a 150m 2 premises located in an urban area to a more suitable industrial site in Bourges in 1990. This new
site was a springboard to increase production volumes and diversify products, while meeting the specific needs of the railway sector. Between 1984 and 1990, the company’s workforce doubled, testifying to this growth dynamic. The first automatic transfer machine, acquired in 1992, expanded production capacities, foreshadowing the company’s development.
International development, supported by a network of international representatives and a regular presence at trade fairs, has also played a decisive role in the company’s success. In 1996, the creation of the Canadian subsidiary in Montreal gave access to the North American market. The same approach in 2011 gave birth to the Brazilian subsidiary in São Francisco do Sul, to cover the South American market. Today, exports represent a significant part of the business, with products sold to the United States, Europe, Asia, Australia and beyond.
While the railway sector remains at the heart of its activity, both in terms of rolling stock and infrastructure J. LANFRANCO & Cie has also been able to diversify. The company has successfully deployed its products in other applications and is now working in sectors as varied as aeronautics, defence, energy and mining, where the reliability of fasteners is paramount.
“As we stand, 50 years on, with nearly 100 employees in the group and a rapidly growing turnover, J LANFRANCO & Cie continues to promote French know-how throughout the world,” comments the company. “It takes commitments to innovation, quality and customer satisfaction to remain the driving force behind a company that, 50 years after its founding, continues to push the boundaries of excellence.”
NORMA Group intends to focus on its core business as a market leader for joining technology, with the initiation of a divestment process for the global business activities of its Water Management business unit.
This step is the result of an in-depth review by the Management Board regarding the further strategic direction of the company. The aim is to strengthen the market position of the remaining Industry Applications, Mobility and New Energy business units.
CEO Guido Grandi comments: “In a persistently difficult market environment, we have reviewed our portfolio and are exploring divestment options for the global Water Management business. In the future, we will concentrate even more strongly on our inherent core business areas including mission critical joining technology for mobility, infrastructure, machinery and other industrial applications. We see high potential for profitable growth, especially in the area of Industry Applications, both organically and through acquisitions.”
The divestment of the water business will enable NORMA Group to free up resources and capacities for further growth in the business units Industry Applications and Mobility & New Energy. These business units have many synergies, including similar or identical product groups that can be manufactured in the same plants. Respective products are metal clamps, pipe couplings, plastic quick connectors, fluid-transport systems and other joining elements.
Paul Raedts has stepped down as CEO of Royal Nedschroef B.V, for personal reasons, but will continue to serve as an advisor to the board of directors.
Rob Janssen will succeed Mr Raedts as CEO, with the leadership transition taking effect on the 1 st November 2024. Rob joined Nedschroef in 2018 and drives the execution of Nedschroef’s strategic projects, aiming for operational excellence and an improved product value stream.
British Steel has attended the inaugural meeting of the new Steel Council, launched by the UK Government, to advise on rebuilding the industry through its upcoming Steel Strategy.
The Council brings together industry figures, experts, trade unions and devolved governments to secure the long-term future of steelmaking in the UK. It will meet regularly and be led by Business Secretary Jonathan Reynolds and Chair of the Materials Processing Institute Jon Bolton.
On its journey to significantly reduce CO 2 emissions, Hilti Group’s ambitious sustainability goals have been validated by the Science Based Targets initiative (SBTi), underscoring its commitment to environmental responsibility.
Hilti committed in 2022 to achieve net zero greenhouse gas emissions across its value chain by 2050. The company has set a near term target of reducing 50% of its Scope 1 and 2 emissions and 30% of its Scope 3 emissions by 2032.
Sika has closed the acquisition of Chema, a producer of tile setting materials, with operations throughout the whole of Peru.
Chema offers a comprehensive range of tile setting materials renowned for their high-quality and ease of application. The acquisition strengthens Sika’s position in the fast growing mortar segment and offers significant cross selling opportunities through an increased distribution channel presence and a complementary manufacturing footprint.
Grupo Celsa has reached an agreement with Sev.en Global Investments, a Czech-based investment group that invests in a variety of sectors, for the sale of 100% of its subsidiaries in the UK and Nordics.
Through this important divestment, the European steel producer continues with the implementation of its plan to reorganise its industrial and financial situation, focusing on its operations in Spain and on the reduction of financial leverage.
On 2 nd December 2024 the acquisition of Dow’s flexible packaging laminating adhesives business to Arkema was finalised.
This acquisition will enable Arkema to significantly expand its portfolio of solutions for flexible packaging and become a key player in this attractive market. With annual sales of around US$250 million (€242 million), Dow’s flexible packaging laminating adhesives business offers a broad range of high-quality solutions.
by John Wolz, editor, GlobalFastenerNews.com
US President-elect Donald Trump pledged to impose a 25% tariff on Mexico and Canada on his first day in office. In response, Mexico’s President Claudia Sheinbaum warned the penalties would cause inflation and unemployment in the USA.
Mexico is the top US trading partner and Canada is close behind. More than US$1.5 trillion (€1.4 trillion) worth of goods are exchanged annually among the three North American nations. Mexico’s top exporters include US-based automakers General Motors and Ford Motor Company, which have built sprawling modern production facilities around the country.
Trump’s latest tariff pledge sent shivers through the US auto industry, which depends heavily on both countries for parts and manufacturing. The prospect of tariffs “is a two alarm fire for the auto industry”, according to Patrick Anderson, CEO of consulting firm Anderson Economic Group. “There is probably not a single assembly plant in Michigan, Ohio, Illinois and Texas that would not immediately be impacted by a 25% tariff.”
The list of vehicles made in Mexico or Canada includes Ram pickups and Chrysler minivans. In addition, General Motors also makes Chevrolet Silverado pickups and electric versions of Equinox and Blazer SUVs in Mexico, where Ford also makes its Maverick pickup.
Separately, Trump also outlined an additional 10% tariff, above any additional tariffs on imports from China. He has previously pledged to end China’s most favoured nation trading status and slap tariffs on Chinese imports in excess of 60% – much higher than those imposed during his first term. Trade between the USA and China amounts to US$600 billion annually.
US fasteners and automotive products suppliers have prepared for months for this outcome. Executives at auto parts retailer AutoZone told investors in October that they were prepared for products they import from India, China and Germany to become more expensive.
“If we get tariffs, we will pass those tariff costs back to the consumer,” comments Philip Daniele, CEO at AutoZone, on a recent earnings call. Likewise, Stanley Black & Decker CEO Donald Allan told investors his company would probably “have to do some surgical price actions” to offset any new tariffs.
Optimas Solutions has integrated a multi sourcing functionality within the company’s SO99+ ToolsGroup platform, enhancing its supply chain resilience and mitigating risks through the automation of its supply base.
Benefits to this newly launched intergration include risk mitigation; enhanced supplier management; increased flexibility and responsiveness; and cost optimisation. “By integrating robust risk mitigation strategies into our operations, we are not only enhancing our responsiveness but also safeguarding our customers against potential disruptions,” highlights Daniel Harms, CEO at Optimas Americas.
The implementation process involved consolidating supplier data through automation and Artificial Intelligence – streamlining the supply network, with testing ensuring the solution met performance, accuracy and reliability standards.
Wood Dale, Illinois-based Optimas Solutions manufactures and distributes fasteners to OEMs through locations in 19 US states, as well as Mexico, Europe and Asia.
by Fastener World Inc www.fastener-world.com
On 7 th October 2024 the Taiwan Ministry of Environment announced a consensus on the carbon price, with a general rate of NT$ 300 per tonne, which will be increased to NT$ 1,200 – NT$ 1,800 in 2030.
Preferential rates may be applied to businesses that propose independent reduction plans, which are NT$ 50 or NT$ 100 depending on specified requirements. In addition, businesses with high carbon leakage risks can multiply the price by the “emission adjustment coefficient” of 0.2, which will result in the minimum carbon price of NT$ 10 per tonne.
The charges are applicable to the electricity, gas supply and manufacturing industries whose annual greenhouse gas emissions exceed 25,000 metric tonnes of carbon dioxide equivalent. In the first phase, there are about 281 companies subject to carbon price collection. The Ministry has calculated and found that if all carbon price levy targets can propose independent reduction plans, carbon emissions will be reduced by 14% in 2030 compared with 2005, while Taiwan’s Nationally Determined Contribution (NDC) target for 2030 is 23% to 25%.
The Ministry stated the next step is to pre-announce a draft bill for carbon price rate, which took effect on New Year’s Day. There will be future measures to increase carbon inventory scope, as well as the levy targets. Calculation based on a preferential rate of NT$ 100 translates to a carbon price income of NT$ 6 billion in 2026, which will be used for practical reduction efforts, adaptation to climate change, administrative implementation and other work. Environment protection advocates issued a statement of criticism, asking that the preferential rates should be phased out after 2030.
Starting in 2025, the Ministry will follow the EU’s practice and require imported similar products to declare emission coefficients. The Ministry will also start planning Taiwan’s own CBAM.
As a result of Chinese low price fasteners, Taiwan’s fastener exports have dropped in terms of weight and price. Recently though, there have been signs of recovery.
According to customs statistics, Taiwan exported 101,000 tonnes of fasteners in September 2024, down 19.4% from 127,000 tonnes in August 2024, but a slight increase from less than 100,000 tonnes in the same month in 2023.
The USA, accounting for 46% of Taiwanese fastener exports, is the largest destination for Taiwanese fasteners with 47,000 tonnes exported in September 2024 – a decrease of 0.31% from 2023. Exports to the 27 EU countries and the UK amounted to 31,862 tonnes – an annual increase of 14.10%, however exports to ASEAN decreased by 10.89% annually.
China previously leveraged its low price to grab orders, but as the USA imposed a 25% high tax rate on Chinese steel and aluminium, China greatly reduced the amount of exports to the USA. In September 2024, Chinese fastener exports to the USA dropped 16.17%, compared to its exports to the EU which increased 17.74% and its exports to ASEAN which increased 4.7%. However, Taiwan’s current fastener export unit price, at US$3.53/kg, is still nearly twice as expensive as China’s, at US$1.9/kg.
Although China exports a higher volume of fasteners over Taiwan, more and more countries are seeking actions against Chinese low priced steel products. According to sources, Indonesian steelmakers are vigorously asking the government to take action on China’s dumping of low priced steel products, meaning China’s low priced fasteners will continue to face considerable challenges.
Taiwan’s China Steel Corporation (CSC) has been implementing carbon reduction, green energy and resource recycling, with its value of carbon emissions per tonne of steel billets now under the EU’s CBAM’s pilot phase at 1.86 tonnes – 15% lower than the default value.
Between 2011 and 2020 Taiwan CSC completed a total of 1,182 carbon reduction projects, with a cumulative annual carbon reduction of 1.45 million tonnes, accounting for approximately 6.5% of Taiwan CSC’s total annual carbon emissions. This translates to an average annual carbon reduction of 0.65%.
Between 2021 and 2023 another 682 carbon reduction projects were completed, including heat recovery in the manufacturing process, improving energy efficiency, replacing old equipment, introducing Artifcial Intelligence and reducing energy consumption. This amounts to an annual carbon reduction of 1.27 million tonnes, with an annual reduction rate of 1.93% – 2.9 times the past average.
The Haiyan Fastening and Locking Technology Association, the only academic organisation in China focusing on fastening and locking technology, was officially established at the Fastener Integrated Innovation Service Hub in Jiaxing City, Zhejiang Province.
During the inaugural conference, the association elected the first leadership team, including chairman, vice chairmen, secretary general, deputy secretary generals and supervisors. Sun Yingbing, chairman of Shanghai Tiancheng, was elected as the first chairman, while Dr Wang Hui, vice general manager of China Components Test, and Yang Junfeng, chairman of CFM, were named vice chairmen.
Currently, the association comprises of nearly 100 members from across the country, including Southwest Jiaotong University, Beijing Institute of Technology, Mingyang Smart Energy Group, Shanghai Electric Wind Power Group Co Ltd, Würth and Tong Ming.
Tenda Technology has announced a joint investment with Tengxing Fastener Co Ltd to establish Tenda Jinyuan (Anhui) Fastener Co Ltd.
By partnering with leading players in the fastener industry, and leveraging its advantages in resources and customers within the stainless steel fastener industry, Tenda aims to enhance the market competitiveness and market share of its products, thereby boosting its profitability.
The Indian Government, in a push for higher quality in industrial fasteners, has introduced the Cross Recessed Screws (Quality Control) Order 2024, under the Bureau of Indian Standards (BIS) Act 2016.
This order requires all screws and fasteners to comply with Indian Standards, which shall bear the Standard Mark, and be certified for conformity assessed under the BIS Conformity Assessment Regulations 2018.
The order avers exemptions for items manufactured domestically for export; imported goods as parts of finished products or components; and certain micro and small units, which are granted time-bound compliance relief. Screws and fasteners without BIS certification cannot be allowed to be imported or sold within India.
OEMs will also be excluded from the order for importing up to 200kg of the same product for research purposes. Such imports, however, shall not be sold commercially and tracked in case of review by the authorities. BIS will be the certification and enforcement authority for this purpose. In case of noncompliance, there will be penalties.
This newly introduced order covers a variety of fasteners, including panhead, countersunk and hexagon washer head screws.
Sterling Tools Ltd, India’s second largest automotive fastener manufacturer, has partnered with China-based Kunshan GLVAC Yuantong New Energy Technology Co Ltd to boost India’s Electric Vehicle (EV) industry.
Through its subsidiary, Sterling Tech-Mobility Ltd, the company aims to establish local production of key High Voltage Direct Current (HVDC) contactors and relays that regulate current flow in electric and hybrid vehicles.
To do this, Sterling Tools plans to invest around INR 40 crore in a new manufacturing facility in Bengaluru to produce HVDC contactors and relays. The initiative supports the Indian government’s ‘Atmanirbhar Bharat’ and ‘Make in India’ policies by reducing import dependency and strengthening India’s EV supply chain.
Sérgio
Although this article is written at the end of 2024, and therefore with incomplete data, the aim is to show a summary of what happened in Brazil within some industrial sectors where a lot of fasteners are consumed, and therefore are very within for the players in the supply chain that involves screws, bolts, nuts, washers, rivets, and others, in addition to technological services, coatings and final application.
The first aspect to focus on is that the production of the domestic steel sector for Q1 and Q3 of 2024 was 25.2 million tonnes of steel, 4.26% higher than the same period in 2023, which in turn closed the year with 32 million tonnes.
To add to this, Brazilian industrial production, including automobiles, motorcycles, home appliances, and electronic products, had very robust performances, reflecting a great end to 2024, and even better predicted for 2025, as long as nothing unexpected happens economically or politically both nationally and internationally.
The challenges of automobiles
Regarding automobile production, Brazil ranked amongst the Top 10 producers in 2023, producing 2,324,838 – with expected growth of 7% for 2024.
Automobile production is a key market for fasteners, with it estimated that each passenger car (not electric) requires 30kg of fasteners, which indicates an apparent annual consumption of around 7.4 million tonnes of screws, bolts, nuts and similar, produced in and outside Brazil. In addition, there is a robust consumption from the aftermarket, currently orbiting 110 million vehicles in circulation in the country.
There are however challenges within the sector, Brazil, and other countries, have still not yet recovered to the levels produced in 2019. In addition, car prices have risen significantly. By comparison, until 2020 in the USA there were 17 car models under US$20,000. Today there are only six.
Added to this, car purchases by young people are falling, who in turn increasingly choose to use public transport and App-based taxis. It is also worth noting that the drop attributed to high prices is significant in Brazil, where the average income is low, currently at US$10,300 per capita, even though it is the 8 th largest global economy in absolute numbers – US$2.173 trillion in 2023.
Unlike the segment of 4-wheeled or more vehicles, the 2-wheeled motorcycle sector is living its golden years. After producing 1.573 million units in 2023, surpassing the 1.511 million in 2014 – prior to the 2015 to 2017 recession, between Q1 and Q3 of 2024 more than 1.323 million were assembled, 11% higher than the same period in 2023. This expansion was apparently driven by the growth of delivery services in the country. Projecting to close 2024 with 1.745 million motorcycles, and multiplying 6kg of fasteners per unit, apparent consumption in assembly lines should be around 10,000 tonnes, excluding the aftermarket involving 32 million motorcycles in circulation in the country.
Between Q1 and Q2 of 2024, sales of home electronic appliances in Brazil increased by 34% compared to the same period in 2023. This is the highest level over the historical series, according to Eletros Associations Manufacturers to Forbes Brazil website. On average, 12.9 million units have been sold per year, specifically washing machines, stoves and refrigerators, and in the recent Q1 and Q2 there were 7.3 million more units, 16% more than the same period in 2023.
Represented by 33 companies, this sector is equivalent to 3% of the national GDP, with 200,000 direct jobs shared among 51 factories in the country.
In short, all these sectors are strong consumers of fasteners, and we have still not taken into account the construction and renovation sector of residential, commercial and industrial properties, which represents around 10% of the GDP, or the oil & gas sector.
There is also the renewable energy sector such as hydroelectric, wind power and solar sectors. Brazil is leading the G20 when it comes to installation of renewables, with approximately 89% of its power being represented by renewables in 2023.
According to Ember Energy, a global energy think tank, the Brazilian renewable energy breakdown is divided as 60% from hydroelectric, 11% of non-renewable, 8% of bioenergy and 21% on wind and solar.
Sources: https://forbes.com.br www.oica.net www.abraciclo.com.br www.anfavea.com.br www.acobrasil.org.br/site/ www.sindipecas.org.br
As one of the leading suppliers and manufacturers of fasteners and anchors, pgb-Europe is taking the next step in its sustainable growth plan, through the construction of a new automated shuttle warehouse –with 40,000 storage locations.
For three generations, pgb-Europe
N.V has specialised in fasteners, from small screws to European certified structural bolts, as well as seismically approved anchors –maintaining a constant stock of around 30,000 items, primarily distributed under the brand names pgb-Fasteners, PFS, HAPAX and SMART.
Founded in 1956, the company has grown into an international player with a central logistic centre in Belgium, a production facility in Poland and a sourcing hub in Shanghai, China. Sales organisations have also been set-up in the Netherlands and France to better meet customers’ specific needs. With the construction of the new automated shuttle warehouse, pgb is deploying the next phase in its sustainable expansion.
Since pgb-Europe moved to its current headquarters in Melle in 1997, its warehouse and logistic processes have constantly evolved using state of the art processes to best meet its customers’ needs. From its inception, the Melle headquarters was a paperless warehouse with small aisle trucks and has grown to be what it is now – all steered by a modern WMS and automatic order picking.
“Our warehouse is the beating heart of our organisation, which is why we are heavily investing in advanced automation
Our warehouse is the beating heart of our organisation, which is why we are heavily investing in advanced automation…”
(Dynaman WMS) and efficiency to ensure every process is as efficient as possible. For instance, in our high bay pallet warehouse goods are stored with automatic cranes and multiple AGVs (Automated Guided Vehicles) handle internal transport. The WMS system is also seamlessly connected to our ERP system (S/4H). This enables us to ensure that each step is traceable, allowing us to map the entire product chain,” highlights Johannes Heye, managing director at pgb-Europe.
He continues: “Every year pgb-Europe processes over 1,000 incoming containers and ships 18,000 tonnes of goods to customers across Europe. This naturally requires a well structured system to keep everything organised, but at the same time we always operate with a customer centric approach to add extra value.”
The construction of the new automated shuttle warehouse is expected to be completed in Q1 of 2025, with 40,000 storage locations (OSR –Order Storage and Retrieval), representing a new level of top tier logistics technology for pgb-Europe. The system uses small autonomous shuttles that quickly move across different rack levels. Products are stored in plastic totes or remain in outer boxes, which are transported by shuttles to and from storage locations and work/pick stations.
Johannes explains: “The significant difference between this new addition from our current miniload system is that the new system operates much faster and more efficiently than the older cranes. Additionally, we can process full outer cartons directly without manual handling and robots will assist with de-palletising. This will drastically increase our processing speed, enabling us to more than double the number of pick lines
Every year pgb-Europe processes over 1,000 incoming containers and ships 18,000 tonnes of goods to customers across Europe.”
per day. Furthermore, it will offer a more ergonomic way of working for our warehouse employees, by eliminating the manual handling of heavy outer cartons.”
pgb-Europe has also successfully acquired two adjacent plots and will be carrying out further expansions of the logistics centre in the short term. In addition, pgb will launch a new shipping area by February 2025, which will feature the construction of four loading docks, along with additional offices and meeting rooms on the upper floors. Once this phase is completed, a second automated pallet warehouse is planned, to provide an additional 12,000 pallet spaces by the end of 2026.
pgb-Europe is not only investing heavily in its internal processes, it is also focusing on other channels to provide a quality service to its customers. Firstly there is the webshop, which provides 24/7 access to pgb’s online product catalogue, which is controlled by a Product Information System (PIM). Customers can also enjoy all kinds of commercial tools and have access to the pgb-ScanApp, which is seamlessly integrated with the webshop. In addition, pgb offers digital connections such as full or partial EDI integration and PunchOut catalogue.
Thanks to these targeted investments, pgb-Europe and its customers can continue to look brightly to the future. “Logistical excellence, combined with digital tools supporting the sales process, ensure that customers can enjoy an excellent service from us,” underlines Johannes. “In this way, we seek to continue our international standing among the top players within the industry.”
www.pgb-europe.com
Here we invited our media partner Fastener World Magazine to give an insight into the Taiwanese fastener market and some of the challenges that Taiwanese manufacturers are facing in an increasingly global and competitive market.
Back in February 2022 when the EU imposed anti-dumping duties on certain iron or steel fasteners from China, Taiwan’s fastener exports experienced an unprecedented boom, reaching over 1.6 million tonnes annually. However, since the end of Covid-19, and especially in recent years – due to stagnant orders from overseas customers, rising manufacturing costs, and unstable geopolitical conditions –Taiwan’s fastener exports have been unable to achieve the highs of pre Covid-19.
With increasing competition from China and emerging markets; the potential impacts from the upcoming CBAM regulation; a stronger focus on developing IT industries in Taiwan; plus pressure from customers for Chinese or Taiwanese suppliers to establish overseas factories; there are a number of significant challenges for many Taiwanese fastener manufacturers. Given these market changes, maintaining a robust global fastener supply chain has become a priority for all stakeholders in Taiwan’s fastener industry.
In a recent interview, Arthur Chiang, president of the Taiwan Fastener Trading Association (TFTA), reported that the Taiwanese fastener industry experienced a production and sales decline of approximately 10% to 30% in 2024. This downturn was attributed to factors such as the Russia-Ukraine war, fluctuations in exchange rates, inflation and rising electricity, as well as oil prices, which have disrupted market recovery. Arthur emphasised that the primary challenges for Taiwanese fastener manufacturers are manufacturing costs and remaining competitive within the market.
He pointed out that while customers may consider switching to lower priced competitors, Taiwanese companies offer superior quality and advanced technology – along with a more stable financial foundation. Therefore, diversifying orders to include Taiwanese companies is a wise choice for sustainable operations and risk management.
While opinions on economic performance vary, and different fastener categories have experienced distinct supply and demand dynamics, making a comprehensive judgement is challenging. Based on export data from the first nine months of 2024, Taiwan exported approximately 936,000 tonnes of fasteners – slightly up from 934,000 tonnes during the same period in 2023. This increase coincided with low priced wire rods being dumped by China and other countries, potentially signalling that the economy has bottomed out and is poised for recovery. Following this trend, the export forecast for 2024 suggest exports would reach around 1.2 million tonnes by the end of the year, which means there is no need for excessive pessimism. If tensions from the Russia-Ukraine war ease next year, and major central banks implement interest rate cuts and quantitative easing policies to stimulate growth, a new wave of global economic recovery may be on the horizon.
The sluggish European economy can be partly attributed to hasty ‘net zero’ carbon policies. European car manufacturers were
compelled to develop electric vehicles but did not anticipate that competitive Chinese electric cars would capture significant market share before their own technology had matured. Furthermore, Germany, Europe’s largest automobile manufacturer, is facing higher energy costs due to the Russia-Ukraine conflict, resulting in decreased demand for fasteners due to sluggish industrial production. Germany is also a crucial partner for Taiwan’s fastener exports, indirectly impacting Taiwanese companies’ orders. Economic cycles fluctuate naturally; thus, it is estimated that current demand stagnation is likely a short term phenomenon.
As 1 st January 2026 approaches, the date when the EU CBAM regulation will formally impose carbon taxes, manufacturers worldwide are beginning to feel pressure from European importers. Fortunately, Taiwanese fastener manufacturers still hold an advantage over other Asian competitors regarding carbon reduction efforts. The president of EFDA noted in a recent interview that Taiwanese manufacturers are ahead in preparing for CBAM requirements, which serves as an important bargaining chip for expanding sales in Europe. However, there are concerns within the industry that achieving the EU’s ‘net zero’ carbon reduction target may increase manufacturing costs by an additional 20% to 30%, further raising fastener prices. Whether this will be beneficial or detrimental for end users remains uncertain. Questions also arise about whether the implementation schedule might be delayed or if carbon taxes could be adjusted based on product types or import quantities.
In Taiwan challenges include labour shortages and high operating costs, due to limited land availability and difficulties obtaining competitively priced materials domestically. Additionally, Taiwan does not benefit from preferential or zero tariffs like ASEAN countries. As a result of these disadvantages, some manufacturers are opting to invest overseas. Whilst large factories, with strong capital, may manage this transition well – by serving local markets alongside exports – the small and medium-sized enterprises face greater challenges.
In addition, although Taiwan’s fastener industry initially outpaced those in China and south-east Asia in development speed, rapid advancements in these regions mean Taiwanese businesses can no longer afford complacency. They now face significant competition both as rivals and potential collaborators in the global market. Over the past three decades, many Taiwanese companies have established factories in Vietnam and other south-east Asian countries where they have thrived. Now even Chinese firms are investing in south-east Asia, seeking new opportunities. This means competition will only intensify.
Chin Tai Sing Precision Manufacturing is an IATF 16949 certified manufacturer with over 20 years’ experience in producing a variety of brass inserts, clinching metal fasteners and CNC components – with the company recently investing in several different machines, and systems, so it can provide customers with additional parts, as well as OEM and ODM services.
Based in Taichung City, Chin Tai Sing Precision Manufacturing (CTSP) has consistently implemented automated machinery and robotics within its production process in order to increase the speed and consistency of production – helping the company’s employees to focus on more complex and value added activities. CTSP has also looked to adopt Artificial Intelligence (AI) and machine learning tools into its production process, with the aim to predict demand, optimise supply chains and improve operational efficiency.
“As Industry 4.0 continues to evolve, automation and the integration of Smart technologies, such as the Internet of Things, AI, and robotics, will become increasingly prevalent in fastener manufacturing,” underlines CTSP. “This will lead to greater efficiency, reduced errors and faster production cycles. That is why we have automated systems with ‘real time’ monitoring and inspection of our products, ensuring they meet strict quality standards. With automated vision systems, and sensors, defects can be detected early, which minimises waste and improves product reliability.”
CTSP continues: “We also plan to enhance our design and production capabilities by leveraging advanced digital tools, such as 3D modelling and digital prototyping. This will help to optimise our prototyping and production processes, enabling us to deliver faster and more accurate solutions, as well as reduce lead times and improve the accuracy of our products – catering to the increasingly complex needs of our customers.”
As part of its production facility, CTSP also has its own quality control department, which enables it to carry out testing throughout its production lines. In addition, the company can offer 100% optical sorting to make sure all parts delivered to customers meet the required standards. “We can provide our customers with all the necessary test reports, including PPAP Level III, IMDS, material/surface treatment test certificates, as well as meeting a host of other requirements,” points out the business. “Thanks to our optical sorting machines, and automatic packing system, we can also provide customers with 0 ppm quality parts.”
Another key aspect of CTSP is its commitment to having engineering experience in its R&D department, so it can work with customers in designing parts – helping to keep costs down, whilst creating innovative solutions. “With industries such as automotive, aerospace and electronics requiring more specialised solutions, the demand for custom designed fasteners and advanced materials (e.g lightweight, corrosion resistant materials) will increase,” reports CTSP. “That is why our R&D team is focused on developing new, high performance materials and creating custom fastener solutions to meet the unique needs of industries.”
Due to its investments in the latest machinery, dedication to quality, and ability to partner with customers on R&D projects, CTSP has established itself as a leading manufacturer when it comes to ‘Made in Taiwan’ parts. “Taiwanese manufacturers are known for their commitment to high-quality standards, strict quality control processes, plus adherence to global certifications,” highlights CTSP.
“‘Made in Taiwan’ has come to be associated with well crafted, durable and precise products, which are highly valued in industries such as electronics, machinery and for automotive components. By working with us, customers know that the products they receive have been designed, engineered and produced in a country known for its strong industrial base, skilled workforce and cutting edge technology.”
The company adds: “As a result of its consistent reputation for quality, ‘Made in Taiwan’ has become a symbol of trust in international markets. It stands as a mark of reliability and many global companies choose Taiwanese manufacturers for their expertise and dependable production capabilities. Taiwanese manufacturing stands out from competitors due to its technological expertise, flexibility, efficiency and commitment to sustainability – making it a trusted choice for global markets.”
This global reputation is underlined by CTSP’s customers being based all around the world, with the company working in 50 different countries, with 40% of customers in Europe, 40% in the USA and approximately 20% in Asia. “While global supply chains continue to grow, there is also an emphasis on strengthening supply chain resilience. Companies will need to diversify their supply sources and ensure their operations are flexible enough to adapt to changes in global trade or market demands and at CTSP we can help them,” states the business. “That is why we are diversifying our supplier base and
investing in more localised production capabilities. We are also incorporating advanced analytics to ensure better forecasting and inventory management, allowing us to respond quickly to market changes. Additionally, we are planning to have a third factory built that will focus on assembly parts –enabling us to offer customers more options.”
CTSP continues: “We can also offer additional sourcing for our customers who are looking for parts that are not in our production range – using our IATF 16949 experience to examine those parts and make sure the necessary quality standards are met.”
A fundamental part of being a global supplier is also being able to meet the growing sustainability requirements of customers, with CTSP committed to reducing its environmental impact by incorporating sustainable materials in its products and adopting energy efficient practices within manufacturing processes. “We aim to meet the growing demand for environmentally conscious solutions in the fastener industry, which is undoubtedly growing,” outlines CTSP. “This includes using eco-friendly materials, reducing waste, as well as optimising energy consumption in production. We are leaders in the Taiwanese fastener sector, known for our innovation, high-quality products and now through our commitment to sustainability. With advancements in automation, Smart manufacturing, and new materials, we have significantly expanded our capabilities – improving both production efficiency and customisation for customers.”
CTSP concludes: “Our aim going forward is to broaden our global presence, reach new markets and forge stronger relationships with international customers. Through continuous investment in research and development, we will also stay ahead of industry trends, providing cutting edge solutions, as well as adapt to the evolving needs of sectors such as automotive, aerospace and renewable energy. We will grow our market share and continue to be recognised as a trusted partner.”
www.ctsp-insert.com.tw
With 38 years of industry experience and advanced R&D capabilities, Fong Prean is known for its patented screws and customised solutions that are tailored to meet specific customer requirements –with the company continuously expanding its product portfolio with new innovations in order to meet future customer needs.
Based in Kaohsiung City, Fong Prean Industrial Co Ltd manufactures a wide range of screws, including drywall screws, woodscrews, decking screws, roofing screws and self-drilling screws – covering specifications from M3 to M10 and lengths up to 400mm.
Since 2021, Fong Prean has been especially focused on further expanding its product portfolio, and increasing market share, with the business introducing several customised screws, including the patented MSword screw, which has been specifically designed for hardwood-to-hardwood applications, without pre-drilling, to help significantly improve work efficiency. Additionally, Fong Prean has launched the MS Sharp-point screw, which it says is ideal for drilling into MDF boards, light gauge steel or aluminium – with versatility for use across various materials and guaranteeing excellent performance.
“We are well known for our patented screws and customised solutions – tailored to meet specific customer requirements,” states Fong Prean. “That is why we are always looking to strengthen our R&D capabilities, focusing on innovative designs and patented products –while offering highly customised solutions to meet evolving market demands. For us, investing in technology and innovation not only enhances our core competitiveness, it enables us to respond quickly to industry challenges – reflecting our commitment to delivering exceptional quality and reliable service for our customers.”
This is underlined by Fong Prean’s investments in upgrading its production equipment, testing instruments and implementing digital systems to optimise manufacturing processes – while also exploring eco-friendly coating technologies and carbon footprint management.
“Investments in technology and innovation are essential for maintaining competitiveness. The steps we have taken have helped us reduce production costs and error rates while ensuring consistent product quality,” points out Fong Prean. “As a business we look to
leverage automation, advanced manufacturing processes, and data analysis, to enhance both production efficiency and quality. That is why our production process integrates strict quality assurance at every stage, from forming and heat treatment to coating and packaging, with multiple inspections conducted throughout, helping to guarantee the high-quality and stability of our products.”
To add to this, and further meet the needs of its customers, Fong Prean has also introduced a carbon data management system to provide precise carbon footprint data, helping its customers meet sustainability goals and regulatory requirements. “These advancements enable us to efficiently support customer needs, address end user challenges, as well as respond rapidly to market changes with competitive solutions,” highlights Fong Prean. “Sustainability is a core focus for us, which is why we have optimised designs to minimise material waste, adopted eco-friendly coatings, as well as promoted environmental education amongst our employees. Thanks to our ability to provide carbon footprint data, we can help customers assess their environmental impact, as well as achieve our own carbon reduction goals – helping us to appeal to environmentally conscious customers worldwide.”
Whilst its primary markets include North America, Europe, and Japan, Fong Prean has also looked to expand into the South American and Australian markets. “We want to provide our innovative, high-quality fastening solutions to a broader customer base,” mentions Fong Prean. “We are also transitioning from being a traditional OEM manufacturer to becoming a strategic partner offering integrated solutions. By providing product design, logistics support, and technical services, we have strengthened our role as a value-added supplier. Working closely with our customers, we can develop fasteners tailored to their specific application needs, ensuring seamless compatibility with new tools and materials – enabling us to deliver efficient and effective solutions.”
Going forward, Fong Prean plans to continue to strengthen its R&D capabilities; expand its patented product portfolio; and develop innovative, efficient fastening solutions to address diverse market demands. “We will continue advancing our digitalisation and automation to enhance production efficiency and product quality. Simultaneously, we will drive sustainable manufacturing, reduce carbon emissions through green technology and contribute to global environmental goals. As our motto states: ‘We live for solving problems’. This is not just our promise but the driving force behind our growth.” www.fongprean.com
Major Industries, the hot and cold forming tooling specialist, has recently made several significant investments in advanced machinery and infrastructure that have enabled the company to expand its capacity and efficiency, enhance its precision and reliability, as well as continue to meet its sustainability goals.
With 40 years of experience, Major Industries is dedicated to helping its customers achieve operational excellence by providing customised die assemblies, inserts, punches, pins and auxiliary tooling. Through its in-depth knowledge of materials and heat treatment processes, combined with cutting edge machinery and rigorous testing, Major Industries can empower its customers to lower their production costs while maintaining high performance.
“Building on our expertise in heat treatment and machining, we have recently made several investments so that we can continue to meet and exceed the needs of our customers,” reports Major Industries Ltd. “We’re committed to staying ahead in the market and supporting our customers with cutting edge precision tooling tailored to their industry needs. That is why we have invested in advanced machinery and infrastructure, so that we can enhance our customers’ production capacity, efficiency and accuracy.”
Major Industries’ investments include the installation of a three axial CNC milling machine and an additional CNC turning machine to boost throughput and reduce lead times. Plus, a new five axial CNC milling machine and a CNC complex milling and turning machine have been added to handle intricate designs with exceptional accuracy. The company has also expanded into hot forming tooling and can now produce tooling for manufacturers in the wind, power and ammunition industries – specialising in fasteners and critical components.
“Investing and innovating in efficiency, quality, cost-effectiveness and sustainability is crucial for us to stay competitive and meet the evolving demands of our customers,” explains Major Industries. “By optimising production processes, and maintaining high-quality standards, we not only reduce costs and waste but also ensure that we deliver reliable, high
performance tooling solutions.
Embracing innovation allows us to adapt to new technologies and continuously improve our offerings, while prioritising sustainability aligned with our environmental goals and customers’ expectations. This holistic approach also ensures long-term growth, strengthens our market position and drives customer satisfaction.”
To add to these investments, Major Industries has also looked to enhance its precision and reliability, with a CNC EDM (Die-Sinking Type) for highly precise and consistent machining. The company also relies on advanced measurement technology, including 3D and 2D high-level measuring devices, as well as a height measuring device –ensuring the highest quality standards.
When it comes to sustainability, Major Industries uses lower power consumption equipment, aligned with decarbonisation goals, as well as a fully integrated MES infrastructure, with IoT connectivity, for ‘real time’ monitoring and improved workflow efficiency, managed from a centralised control room.
offer a seamless, end-to-end manufacturing solution. Our in-house capabilities span from machining and production to high-value investment in heat treatment and PVD coating equipment, ensuring that we control every stage of the process for maximum efficiency and quality,” underlines the business. “By handling everything internally, we meet our customers’ demand for a ‘one stop shop’, simplifying their supply chain and reducing the need for multiple suppliers. This integrated approach streamlines customers’ production, cuts lead times and ensures consistent quality from start to finish.”
The vertical integration also gives Major Industries full control over product quality and traceability, meaning every component is closely monitored throughout the production process – enabling the company to maintain the highest standards and provide its customers with complete transparency. “Our approach to vertical integration has earned us the trust of top automotive fastener suppliers in North America and Europe,” comments Major Industries. “By offering superior products, and unmatched reliability, we help these industry leaders stay competitive in a fast paced market. Furthermore, we have a network of local agents and representatives worldwide, ensuring prompt and personalised service wherever a customer is based.”
Even with such a diverse and loyal customer base, Major Industries is still able to provide expert design advice by reviewing tooling specifications and analysing performance in its advanced metallurgical laboratory. “Our team conducts thorough inspections, material analyses, performance evaluations, and failure mode identification, to
pinpoint the root cause of any issues,” highlights the company. “Once we have a clear understanding, we implement tailored corrective actions, whether it’s refining the design, adjusting materials or improving maintenance procedures. Our goal is to not only resolve the issue but also enhance customer productivity, ensuring long-term, effective solutions that prevent future failures.”
The company can also meet the evolving and growing demands of industries –including automotive, aerospace and renewable energy – when it comes to lightweight, high strength materials, such as titanium, advanced composites, and high grade steel, which need to be designed to withstand harsher conditions and enhance the durability of products. To add to this, there is also the increasing interest in corrosion resistant coatings, eco-friendly materials, and custom fastener designs, to improve performance, reliability and reduce environmental impact.
“The industrial fastener industries in our main territories – USA, UK and Ireland, and Germany – are undergoing significant development, driven by advancements in technology; increasing demand for sustainable products; and the need for
Optimised tooling ensures improved durability, enabling fasteners to perform reliably in demanding environments.”
higher performance in challenging applications,” mentions Major Industries. “High performance tooling enhances the production of fasteners by ensuring tighter tolerances, as well as improving material efficiency by minimising waste and maximising the use of high strength alloys – promoting sustainability and cost-effectiveness.”
Major Industries adds: “Advanced tooling solutions also speed up production cycles and reduce lead times while maintaining quality. Optimised tooling ensures improved durability, enabling fasteners to perform reliably in demanding environments. High performance tooling also plays a crucial role in supporting the
fastener industry’s product development and assists formers with operational efficiency.”
Thanks to its ability to provide performance tooling, Major Industries believes it is poised to be a global leader in precision tooling, driven by its diversification into industries such as wind power, ammunition, and renewable energy, alongside its established markets in automotive, aerospace and construction. “Strategic investments in cutting edge machinery, IoT enabled infrastructure, and advanced measurement tools, will enhance efficiency, precision and sustainability – solidifying our competitive edge,” concludes Major Industries. “Our focus on total cost of ownership, superior tooling performance, and eco-friendly solutions, aligns with global trends in sustainability and high performance manufacturing. By leveraging our expertise in materials, heat treatment, and failure analysis, we will further strengthen customer relationships, expand our market presence and offset challenges, such as pricing pressures and shifts in demand. With continued innovation and operational excellence, we are set to reinforce our position as a leading tooling supplier, as well as go on delivering long-term value to our customers.”
www.majorindustriesltd.com
Ray Fu has recently introduced various types of additional machinery so that it can provide greater capacity for its customers, enabling the manufacturer to increase its range of products and services and further become a ‘one stop shop’ for customers.
Ray Fu Enterprise Co Ltd was established in 2000 as the international sales department (export department) for parent company Chen Nan Iron Co Ltd – a steel wire manufacturer – before turning into a manufacturer and expanding its factory to include fastener production, which today covers 138,000m 2
“Investments in new machinery and capabilities are a must for us,” states Ray Fu. “We strive to provide better service and quality for our customers in order to maintain our competitive edge, which is why it is essential we innovate with the help of new technology.”
Another big part of Ray Fu’s success is the reliable and secure supply of high-quality products it can provide customers. “Our stable quality across all our product ranges can give our customers peace of mind when they purchase from us,” emphasises Ray Fu. “Our R&D team communicates with customers before a new product launch to maximise the product quality and minimise potential setbacks. This helps ensure that when we expand our product portfolio it is based on customers’ requirements and we can be confident the increase in our manufacturing capabilities is better serving a wider range of customers.”
Ray Fu’s product portfolio includes self-drilling screws, self-tapping screws, concrete screws, window screws, automotive screws, as well as socket cap screws (Allen cap screws) from M1.8 to M20, and in lengths from 2mm to 400mm. It can also provide different iron wires for fastener use, such as C1018, C1022, C10B21, 4037 and stainless steel – from a diameter of 1.78mm to 10mm.
Over the years, Ray Fu has also acquired multiple ISO, CE and ETA certifications, which underline the quality of its production and the wide range of products it can supply. For instance, the company’s RF self-tapping screws for timber structures, available in lengths from 60mm up to 600mm, has achieved an ETA certification (ETA – 18/0850). To add to this, in 2022 Ray Fu also achieved the AS9100D aerospace certification, further expanding its market from industrial, automotive and medical into aerospace.
“This certification confirms that we are able to meet the highest quality standards within Europe and means our customers can be confident in the quality of the products they are receiving,” explains Ray Fu. “From the moment an iron coil arrives at our facility, we perform a full inspection at the start and end of each process to ensure the quality of the products. We also have our own in-house TAF laboratory and we use ISO 9001 to ensure the products in-process and after-process adhere to customers’ specifications.”
Ray Fu’s key markets include North America, Europe, the Middle East and Asia. “The current North American market is stable, but the European market has decreased its demand for fastener products. The Middle East and Asia markets are also considered stable and have slightly increased their demand over the past years,” reports Ray Fu. “We remain optimistic for 2025 and hope the different conflicts around the world will end soon. Either way, we will keep supporting our customers with competitive prices and stable quality products.”
Ray Fu adds: “Taiwanese manufacturing for the fastener industry is crucial for markets around the globe. It has and will continue to provide a stable, quality driven source of fasteners and we believe there will be a continued shift of focus within the sector from standard parts to special parts. Our role as a proud Taiwanese business is to provide stable quality products at an even faster rate to our customers worldwide. That is why we work with every customer to find out their specific needs and create various planning schedules so that our product can still adhere to the ‘Just in Time’ model. When customers work with us they get reasonable pricing, stable quality products, great customer service, and quick solutions to meet their needs, which helps differentiate us from the competition.”
www.ray-fu.com
In the last three years Kwantex has actively looked to participate in overseas exhibitions, and visit customers directly, to personally understand market conditions, requirements, and changes, in order to develop new products to meet specific customer and sector needs.
Based in Tainan City, Kwantex Research Inc has used this experience to develop new products, whilst also applying for new patents and certifications around the world. “We are a R&D oriented company, so we invest in developing new products every year,” explains Kwantex. “We believe that only innovation can develop new markets and make a key difference for us as a business. Through the functions and performance of new products, we can help customers increase their market share, as well as ensure we stay competitive within the global market.”
The new products that Kwantex has recently introduced includes the KTX Archimedes’ Secret® Screw, which can be used for all wood applications – including chipboard, decking, wood structures, etc. The KTX Archimedes’ Secret® Screw includes a TTX® Drive with a special six-lobe hook design that helps avoid cam-out and offers superior fit quality with a TTX® bit. It also features Tornado ribs that can cut and press wood fibre and enables the head to sink flatly with no burrs; as well as the option of AS’/XAS’/DAS’/DXAS’ threads that immediately grab, offering low driving torque, anti-split and high pull-out – replacing regular TY-17 and two cuts design.
Other recently introduced products include the KTX-Hidden
point design that can be used without pre-drilling and avoids breakage.
In addition to its new products, Kwantex has also invested in ESG (Environmental, Social and Governance) including the establishment of an environmental management and greenhouse gas investigation team, as well as a sustainable development team, to provide employees with a safe, healthy and friendly environment. In addition, Kwantex has implemented local care, social participation and environmental sustainability (education, culture, assistance and environmental protection).
Kwantex also obtained ISO 14064-1:2018 (Greenhouse Gas Verification Statement) in 2022 and ISO 14067:2018 (Product Carbon Footprint Verification Statement) in 2023. To add to this, Kwantex’s ESG sustainability report was completed at the end of 2024, with the company also committing itself to green electricity in 2025.
“With technological advancements, the fastener industry is promoting ‘net zero’ carbon reduction and power saving technologies, introducing Smart manufacturing, and moving towards high added value,” points out Kwantex. “That is why as a business we have invested in ESG and environmental certification; committed ourselves to promoting green and environmentally friendly products, such as using trivalent chromium or chromium-free; using FSC certified boxes or cartons; as well as adding recycled materials to plastic boxes to respond to environmental protection.”
The company concludes: “We will continue to invest in both new products and sustainability so that we can go on meeting the needs of our key markets of Europe and North America, as well as other customers based around the world. Thanks to our professional R&D capability, we can also work with customers to develop new products or solve problems –according to a customer’s actual application and the types of materials, thicknesses and installation methods involved. We can jointly discuss the options available and provide prototype parts to confirm the feasibility and guarantee the most optimal solutions are offered.”
www.kwantex.com.tw
Joker Industrial has more than 38 years of experience in the manufacture of construction anchors, fasteners, and hardware, with the company taking several key steps in order to keep itself at the forefront of the market when it comes to product development and quality management.
Joker Industrial Co Ltd’s products have long been recognised in the fastener market for their patented designs, which use fewer materials while delivering superior performance – enabling the company to offer unique solutions to its customers. “Our HWA, EASY ANCHOR, SISSY ANCHOR (internal concrete screw), and ETA certified concrete screws, are prime examples of our ability to provide unique solutions to the market,” highlights Joker. “By using our DesignfiX software, with our ETA certified concrete screws, installers can even pre-calculate the required load, which helps to improve installation accuracy, boost efficiency and reduce unnecessary installations.”
In response to the global supply chain impact before, during, and after the Covid-19 pandemic, Joker has also become more determined than ever to enhance its production line intelligence. This has enabled the business to gain ‘real time’ insights into production progress and share information with its customers – granting it greater flexibility in allocating capacity.
“We have been using an ERP system for over 30 years, accumulating extensive data, which helps to continuously monitor and improve our production processes,” reports Joker. “In preparation for the EU’s CBAM requirements, we have also thoroughly organised and calculated our internal data, making it possible to provide carbon emission figures for all our products. We are confident that once the EU provides more details, we will swiftly comply with any new requirements.”
Thanks to Taiwan boasting a mature and fully integrated supply chain, with each manufacturing stage located in close proximity, Joker is able to rapidly work on product development. “While geopolitical factors may introduce some uncertainties, considering the industry’s characteristics, our adaptability, and the trust built over time, choosing us as a long-term strategic business partner remains the most reliable and stable option,” concludes the company.
www.joker-fastener.com
Joker has become more determined than ever to enhance its
By Taiwan External Trade Development Council (TAITRA)
In recent years Taiwan’s fastener industry has shifted from the traditional production of standard fasteners to high-precision, customised products tailored to specific needs. Taiwan’s manufacturers are also actively expanding into specialised sectors, such as renewable energy, aerospace and automotive – showcasing their adaptability to global market changes, technological advances and diverse customer needs.
Today, Taiwan’s fastener industry plays an important role in sectors such as electric vehicles, medical devices and advanced electronics. With growing global demand for high-end customised products, Taiwan is enhancing its competitiveness in these fields.
Like many others, Taiwan’s fastener industry has been deeply impacted by ongoing geopolitical tensions and global uncertainties. These tensions have created uncertainties in global supply chains and raw material costs. Additionally, economic disruptions caused by Covid-19 delayed production schedules. This has led to excess inventory within many industries. Also, inflation continues to rise in countries around the world. As a result, demand has decreased, leading to less orders.
Taiwan companies also face challenges such as rising energy costs, labour shortages, and higher living standards, all contributing to increased production costs. This makes it difficult for Taiwan’s fastener industry to maintain cost competitiveness, especially compared to countries with lower production costs. Moreover, Taiwan’s limited participation in some regional trade agreements also restricts its ability to expand its global market reach.
Another key factor impacting the market and gaining importance is environmental and regulatory pressures, such as carbon emissions. The EU’s Carbon Border Adjustment Mechanism (CBAM) will impact the fastener industry worldwide, including Taiwan. Taiwanese fastener manufacturers must adopt sustainable practices and meet carbon emission regulations to stay competitive in global markets. This regulatory shift will add pressure to an already challenging industry environment.
Despite these challenges, Taiwan’s fastener industry has significant opportunities to grow – by embracing innovation and focusing on high value markets. The shift toward sustainable manufacturing and investments in Smart technologies, such as Artificial Intelligence (AI) and the Internet of Things (IoT), can help companies meet evolving industry demands.
Additionally, Taiwan’s government is providing support to help businesses adapt to environmental regulations, turning challenges like the EU’s CBAM into opportunities for growth and enhanced international competitiveness.
One of the key advantages of Taiwan’s fastener industry is the industrial cluster in Kaohsiung, which supports a strong, integrated supply chain. This concentration enables manufacturers to meet diverse market demands efficiently, from raw material sourcing to precision manufacturing and surface treatments. The proximity of suppliers also helps shorten lead times and ensures flexibility in meeting the specialised needs of global customers.
Taiwan’s fastener manufacturers are also highly agile and can quickly respond to market trends and customer needs. They excel at creating customised, high-quality fasteners for specialised applications – with their commitment to research and development enabling them to stay ahead of global competition.
This means that Taiwan’s fastener industry is well positioned to seize emerging opportunities and tackle global market challenges. As the industry evolves, it will continue to focus on innovation, sustainability, as well as adaptability, to maintain its competitive edge.
A key showcase for Taiwan’s fastener companies is the 2026 Taiwan Fastener Show, held at the Kaohsiung Exhibition Center. Under the theme ‘Green Fastening, Precision Attaining’, the show will highlight cutting edge and innovative products applied in various sectors, including materials, moulds, tools, nuts, bolts, screws and machinery. It will also feature forums and events designed to foster global collaborations and drive industry growth.
Fastener Taiwan 2026 will bring together international professionals and Taiwanese suppliers, creating opportunities for strategic partnerships and global business cooperations. The show dates in 2026 will soon be announced on the official website.
Roseter, a specialist manufacturer within construction fixings, provides fastening screws for sandwich elements, steel, timber, concrete and EPDM – with the company recently looking to increase its number of ETA certified products for sheeting/roofing and exterior wall cladding.
Roseter explains: “Our ability to achieve ETA certification for sheeting/roofing and exterior wall cladding applications signifies that we not only specialise in production but also understand the demands of the end market. A prime example of this was last year, when we collaborated with a customer to develop a new type of solar screw. This innovative product successfully reduced the customer’s installation time and costs. We have also applied for an ETA on this product, which we expect to be issued in the first half of 2025. Moving forward, we will continue to bring even better products to the market and warmly invite customers to partner with us when it comes to customised screw solutions.”
Due to its expertise in the construction sector, Roseter is well positioned to understand what is happening currently within the market. “With the current high interest rate environment, and a weaker PMI, market demand is not as strong as in previous years,” outlines Roseter. “The good news is that the current CPI has dropped to the 2% target, so we believe we are nearing the bottom of the market cycle. Thanks to our ability to provide R&D innovation, as well as small batch flexibility, we are confident that we can help support customers with high-quality certified products as the market grows in the future.”
Roseter is well positioned to understand what is happening currently within the market.”
Roseter adds: “At Roseter we can respond to customer needs quickly and efficiently – supplying products as and when they are needed. This helps minimise product inventory, which in today’s market is a crucial aspect of supply chain management. When added with our innovation capabilities, and wide range of products, we are confident we can continue to grow as a key business within the global supply chain.”
www.roseter.com
In order to maintain its position as a global leader in large-scale diversified tool precision machining, San Shing Fastech Corp has made investment in high precision equipment, and innovation in production technology, as key pillars within its business in order to continue to grow in an ever changing market.
Following its commitment to investment and innovation, San Shing has increased its use of automation equipment, introduced intelligent production systems, as well as planned the integration of AMR robots into its production lines. “The main goal is to increase production capacity, reduce labour costs and improve efficiency,” states San Shing. “This also helps lower production costs, making our prices more competitive, and shortens lead times to meet customers’ urgent order demands.”
San Shing adds: “Diversified operations and innovative development have become nearly universal challenges faced by all manufacturing industries. That is why we place great emphasis on investing in advanced processing equipment, process optimisation and the training of technical personnel. With the continuous upgrading of both hardware and software, as well as the technical team, our tooling factory has successfully taken on cross-disciplinary mould processing challenges. We have also successfully gained validation from users in various fields and secured long-term cooperation orders.”
San Shing specialises in various types of cold and hot forging tools, as well as customised tools for automotive and aerospace fastener industries. “Quality is the life of San Shing, which is why we are committed to complying with ISO standards and have obtained the ISO 9001 certification. In response to market demands, we are also continuously researching new manufacturing technologies across different fields,” underlines San Shing.
By utilising nearly 60 years of production experience, the company can ensure its tool manufacturing expertise is at the very forefront of the industry – fulfiling every customer quality requirement, whilst also offering technical suggestions for improving tool lifespan based on customer production feedback.
“Stable quality ensures a steady production line for our customers. Also, when compared to European manufacturers, we offer a higher cost performance ratio,” states San Shing. “In addition, thanks to
our production experience, and user feedback as our foundation, we are also able to provide potential improvement suggestions when customers encounter tooling related issues. Our professional design and programming team can also help customers identify potential issues in the drawings, preventing them from discovering errors after receiving the tooling, which could delay their production schedules.”
San Shing continues: “We are a proud Taiwanese business and the positive perception of Taiwan greatly benefits us as we expand in the global market. We believe ‘Made in Taiwan’ represents high-quality, integrity, and kindness, which is why when customers seek high-quality products, Taiwan naturally comes to mind. As we earn customers’ trust through quality, we can more easily retain existing clients. When compared to European manufacturers, we offer comparable quality but at more competitive prices. This is why many of Taiwan’s ‘hidden champions’ have a high global market share in their respective industries.”
With its main markets in Europe and the Americas, San Shing has also looked to adapt to the changing requirements of its key markets, in order to stay competitive. “In recent years both regions have been continuously developing the Electric Vehicle (EV) industry –with the European Union even setting a target to ban the sale of new cars emitting carbon dioxide by 2035, leading to increased investments in the EV sector,” reports San Shing. “Car manufacturers and related supply chains are also closely monitoring the unpredictable market trends, attempting to explore new directions arising from things such as sustainability and Artificial Intelligence related issues. There is also the aviation industry, which has finally emerged from the shadow of the Covid-19 pandemic, with demand starting to recover in 2022 and remaining strong in 2023 and robust in 2024, with optimistic market expectations for the coming year.”
San Shing adds: “Due to the impact of the Carbon Border Adjustment Mechanism (CBAM) regulation, Europe has also started to reduce its imports of finished fasteners, with the proportion of local production gradually increasing. As a result, the demand for tools has also risen.”
San Shing concludes: “By maintaining stable quality, continuously investing in high precision equipment, and refining our machining capabilities, we are confident that we will remain an indispensable business partner for our customers. Over the past few decades, our customer base, both long-term and newly developed, has increasingly shifted towards high precision and specialised products, which underlines the quality tooling we can supply customers. We will therefore continue to work with industries such as automotive, aerospace, construction, and hand tools, whilst at the same time looking to expand our tool manufacturing footprint into other diverse application sectors.”
www.sanshing.com.tw
Shin Chun has recently invested in a set of open die re-header/threading machines to support customers who are looking for longer sized screws, which is a trend the Taiwanese screw manufacturer has seen from customers within the market.
With over 20 years’ experience, Shin Chun Enterprise Co Ltd is able to manufacture a wide variety of screws, including drywall screws, chipboard screws, tapping screws, self-drilling screws, concrete screws, machine screws, as well as automotive screws and specials.
Through the investment in the new machinery, Shin Chun has been able to expand its capabilities and can now produce screws up to 12mm outer diameter and up to 800mm long. “We are well known in the market for the good and stable quality of our screws,” states Shin Chun. “We are also able to satisfy customers’ needs by always looking to add new products where possible, as well as by offering a lot of additional services. We welcome customers to tell us what they need and then we look to make it real. We had several customers asking us for longer sized screws, so we decided to invest in the new machines so we can further support customers.”
In order to guarantee the quality of its products, Shin Chun has also taken several steps to ensure its production is of the very highest quality. This is underlined by the company achieving ISO 9001, IATF 16949, ISO 45001, ISO 17025 certifications, as well as several European Technical Assessments.
“We are a very proud Taiwanese manufacturer and have become a key partner for customers around the world. Thanks to our investments in the new longer sized screw machinery, we can further support our customers and we will go on being a loyal and even strong partner that can meet all our customers’ needs,” concludes Shin Chun. www.sce.com.tw
In 2022 Vertex Precision opened a new plant dedicated to open die, 1 die 2 blow, as well as CNC machines – with the aim to increase its production capabilities for advanced fasteners.
Vertex made this investment due to the production of standard fasteners in Taiwan becoming increasingly uncompetitive. The company has therefore looked to shift to high unit price/multiple stage fasteners to meet the needs of the market.
In addition to investments in machines and equipment, another important focus for Vertex Precision Industrial Corp is environmental protection, including software and hardware. Due to the introduction of the Carbon Border Adjustment Mechanism (CBAM) regulation, which will start collecting carbon taxes in 2026, as well as a similar policy in the United States, Vertex Precision has introduced solar power generation, plant energy saving, resource recycling and other devices to reduce carbon emissions in production.
“Through these environmentally friendly investments we can contribute to environmental protection, whilst at the same time enhance the competitiveness of our business on the global market,” explains Vertex Precision.
Vertex Precision is focused on the European market, which represents 65% of its business. However in 2024, Europe’s market was a little slow, with business in the North American market moving faster. In 2024 the company also increased its new product development projects by 24% compared with 2023, which underlines the positive steps the business is taking and why Vertex Precision is optimistic about 2025.
“With the increasing competition from countries such as China, India and Turkey – where production costs are lower –Taiwanese manufacturers have to decide whether they want to compete on price, which can erode profit margins, or focus on innovation and value-added products,” highlights Vertex Precision. “That is why we have invested in our manufacturing capabilities. There are abundant opportunities for Taiwan’s fastener industry, especially with the global emphasis on sustainability and green manufacturing, which opens new avenues for Taiwanese companies to develop eco-friendly products and processes.”
The company adds: “Moreover, Taiwan’s advanced manufacturing technology, and skilled workforce, position it well to transition toward producing high-precision and speciality fasteners for industries such as aerospace, automotive, AI/robotics and renewable energy. A small number of customised products, with high technical content, can help improve R&D capabilities, increase product selling prices, as well as build a global reputation for the Taiwanese market as a high-end fastener market.” www.vertexprecision.com.tw
Since its establishment in 2007, Ye Fong Aluminium Industrial Ltd has consistently provided high-quality aluminium alloy materials, including seamless aluminium tubes, aluminium bars, extrusions profile, aluminium plates and aluminium wire rod – all for various industries including automotive, military and defence, as well as medical and aerospace.
Akey factor in Ye Fong’s ability to stand out from its competitors is its long-term focus on product quality and stability; its flexible product development capabilities; as well as its versatile product portfolio; which has enabled it to become a key supplier to aerospace fastener manufacturers – with customers relying on aluminium alloy materials in the form of straight bars or wire rod for their production needs.
In order to support the aerospace sector, Ye Fong’s production process also strictly adheres to international standards. In addition to rigorous in-house quality control and assurance testing, the company collaborates with globally certified laboratories to conduct third-party quality tests as specified by customers. Furthermore, in response to recent upgrades to its facilities, Ye Fong will soon launch larger sized products and a more tailored product line-up to better meet customers’ needs.
“We are the only aluminium alloy manufacturer in Asia with full process capabilities for aerospace grade aluminium plates, tubes, bars, as well as hot rolled aluminium wire rods,” underlines Ye Fong. “Our aluminium hot rolled wire rod production capability includes all alloys, with a focus on high strength aluminium alloys, including 7075, 7050, 2024, 2011, 2014, 2117, 2017, 6061, 6056, 6082, 5056 and 5052, from 2mm – 30mm diameter for finished wire and 9.5mm –32mm diameter for redraw rod.”
Ye Fong is NADCAP (Heat Treating & Non Destructive Testing), DNV, ABS accredited, as well as AS9100 certified. In addition, the company also has ISO 9001 and ISO 14001 certifications.
“For years we have supplied premium aluminium alloy straight bars to high-end aerospace fastener manufacturers. However, in the fastener manufacturing process, using wire rod is more efficient compared to straight bars. Additionally, aerospace fastener manufacturing is governed by strict standards, requiring the use of hot rolled production wire rod when employing coil materials. Globally, there is currently only one supplier capable of producing hot rolled aluminium alloy wire rod suitable for high-end aerospace fasteners,” highlights the company.
Recognising this gap in the market, Ye Fong used its decades of expertise in aluminium alloy manufacturing, and its commitment to ongoing research and development, to introduce the highly rare hot rolled aluminium alloy wire rod to the market, offering high-end aerospace fastener manufacturers a superior and alternative material solution.
“Investment and innovation are the key factors that enable our company to maintain a leading position in the industry. They are also the primary reasons behind our outstanding reputation in the international aerospace aluminium alloy materials market today,” states Ye Fong. “Another key factor in our success is our ability to offer 100% customised products and to assist customers in developing products within the shortest possible time. Based on the results of each trial sample, we can then adjust the mechanical properties of the aluminium wire rods, helping customers achieve mass production in the shortest timeframe.”
An area in which Ye Fong continues to invest resources is in sustainable development, with the company designating the topic
as one of its key mission objectives for the future. “When it comes to environmental conservation, carbon emission, and sustainable management, we have taken several key steps, such as using low carbon raw materials in production; improving manufacturing processes to save energy; enhancing material strength; and reducing the use of aluminium alloy raw material consumption,” reports Ye Fong. “The global trend of carbon reduction and ‘net zero’ emissions, along with the EU’s introduction of the Carbon Border Adjustment Mechanism (CBAM) regulation, has changed the global economic situation. Environmental awareness is increasing, and this will be a key issue that fastener manufacturers must face in the future. By offering help with this type of topic, we believe we can continue to support customers and grow our standing in the aluminium alloy fastener manufacturing supply chain.”
Ye Fong currently collaborates globally with aluminium alloy fastener manufacturers, providing hot rolled aluminium alloy wire rod and support where necessary. “As a proud Taiwanese business, and supplier of aluminium alloy materials for Taiwan’s fastener industry, we believe we can also help Taiwanese fastener manufacturers move toward the industrial upgrade of high-value-added aluminium alloy fasteners,” adds the company. “By working with us, customers around the world are able to secure resources for the rare hot rolled aluminium wire rods, with quality approval from aerospace fastener manufacturers. We can also offer flexible production specifications, 100% customisation services and competitive pricing. This complete package will help us to continue to grow our market share in the global supply chain of aluminium alloy wire rods, especially targeting the high-end aerospace and lightweight electric vehicle markets.”
www.ye-fong.com
Since the Covid-19 pandemic, Rexlen has embraced transformative strategies to enhance its offerings and support its customers. These efforts include entering new markets, expanding production capabilities and establishing cutting edge facilities. A centerpiece of these advancements is Rexlen’s new cleanliness testing laboratory, specifically designed to meet the growing demands of the automotive industry.
The global economic disruption caused by the 2019 Covid-19 pandemic highlighted the importance of adaptability. While Rexlen Corporation previously focused solely on export sales, the company has since recognised the potential of the domestic market. Leveraging its expertise in secondary processing technologies, the company has successfully served major clients in Taiwan, broadening the application of its fasteners beyond the automotive sector.
Simultaneously, global trade developments, such as the European Commission’s anti-dumping measures and increased tariffs on Chinese goods, prompted Rexlen to explore new opportunities in the Chinese market. The company’s strategy of continuous investment in infrastructure and talent development has positioned it to thrive amidst these challenges.
One of Rexlen’s most significant advancements is the establishment of a certified cleanliness testing laboratory. With the automotive sector increasingly prioritsing stringent cleanliness standards, Rexlen proactively responded by creating a laboratory capable of verifying product cleanliness to meet customer specifications and industry benchmarks.
“We recognised the importance of supporting our customers in ensuring their components meet rising cleanliness requirements,” states Rexlen. “This laboratory enables us to validate that cleaned
As a business we are always looking at how we can develop our products and markets so that we can continue to grow and support customers…”
products comply with both customer and regulatory standards, addressing a critical and growing demand within the industry.”
The laboratory’s cutting edge equipment, and certified processes, empower Rexlen to maintain the highest quality standards, reinforcing its commitment to innovation and customer satisfaction. This initiative complements the company’s TAF-certified laboratory, which has been enhanced with additional inspection equipment, including spectrometers and coordinate measuring machines, to support comprehensive quality control.
With over 47 years of experience in the fastener sector, Rexlen combines technical expertise with advanced manufacturing capabilities. The company offers a wide range of services, including multi-forming cold forging, CNC machining and secondary processing, supported by ISO and TAF accredited laboratories in Taiwan and China.
Rexlen’s specialisation in custom fastener solutions is further bolstered by its Advanced Product Quality Planning (APQP) process, which ensures each production stage meets or exceeds customer requirements. The company’s ability to innovate through cold heading and secondary machining techniques has also enabled it to deliver superior quality products with faster lead times and competitive pricing.
In addition to its manufacturing prowess, Rexlen also provides procurement services for additional components, leveraging its certified inspection facilities to guarantee quality and reliability, whether for in-house products or items sourced externally.
“At Rexlen we are dedicated to delivering innovative, high-quality products and services,” the company concludes. “Our investments in facilities such as the cleanliness testing laboratory reflect our forward-thinking approach and commitment to exceeding customer expectations. With these advancements, we are well positioned to support clients worldwide with the solutions they need.”
www.rexlen.com.tw
Customers entrust Rexlen not only with products it manufactures but also with the procurement of additional items…”
To meet the growing sustainability needs within the fastener market, Sheh Kai has made some key investments within its production and structure so that it continues to be a leading manufacturer of bi-metal screws and bi-metal screw anchors.
Founded in 1992, Sheh Kai Precision Co Ltd offers a first class strategic partnership for customers, in cooperation with the best quality and service when it comes to bi-metal screws, screw anchors and hammer drill bits. “We have been able to become one of the main players within the bi-metal screw sector thanks to our commitment to quality, which is underlined by the numerous certifications we have received for our products, including European Technical Assessments (ETAs), PGM, as well as ICC-ES certification in the USA,” states Sheh Kai.
Alongside quality, a main aspect of meeting market requirements today involves sustainability. “We have made some key investments in the last few years in order to go on supplying high-quality products, whilst at the same time helping us meet sustainability needs,” points out Sheh Kai. “This includes replacing old machinery with more efficient modern machines to improve energy and space efficiency, which greatly benefits us when it comes to the CBAM regulation and production capacity. By upgrading our machinery, we are also ensuring our capacity continues to meet customers’ demands.”
As a publicly listed company in Taiwan, Sheh Kai has published an ESG report, available on its website, which highlights three core elements. Firstly, economic development, which focuses on new applications of core technologies; next up is social progress, which addresses social issues and supporting the physical and mental wellbeing of employees – ensuring legal compliance and more; and finally environmental protection, which involves improving
energy efficiency, reducing carbon emissions, managing waste and promoting recycling.
“Our main market is Europe, so it is vital that we look to help support customers when it comes to the CBAM regulation,” explains Sheh Kai. “Our ESG report shows that as a business we are taking the topic of sustainability seriously and we are putting in place a structure that will enable us to work with customers.”
Sheh Kai continues: “Taiwan is renowned as a major global producer of screws and given the increasingly stringent carbon footprint regulations, as well as the current economic situation, it is essential that as a Taiwanese manufacturer we look to adapt and overcome these challenges. In the future, energy efficiency will be a critical path for the screw industry, and the use of green energy will become increasingly important. That is why sustainability is a part of our plans for gradual improvement moving forward. We are a professional manufacturer and this will never change. However, with the increasing number of tariff barriers, we are looking at all options, even setting up manufacturing facilities in different countries, as we believe manufacturing closer to the market will become an inevitable choice,” states Sheh Kai.
In addition to the requirements of sustainability, Sheh Kai highlights that its key market of Europe is facing additional challenges, with the economy slow and needing to ‘wake up’. “After the overbooking post Covid-19, the demand for fasteners has certainly decreased and the economic situation has been difficult, especially with cheaper priced product competition from China,” underlines Sheh Kai. “That is why as a business we are focusing on higher quality products, so that there is less of a focus on price and more on the features and reliability of a product.”
Sheh Kai adds: “We are a proud Taiwanese manufacturer and our ability to provide first class solutions that are ‘Made in Taiwan’ represents our stable quality, reasonable pricing, trustworthy relationships, and excellent research and development capabilities, enabling us to become a special manufacturer for customers when it comes to bi-metal screws and screw anchors. We are fully committed to this market, which is why we are planning a new factory and implementing automation technologies, such as automated storage and automated handling, along with using AR for employee training in the factory. This will help us to continue to support our customers in the best way possible when it comes to products, quality, service, as well as sustainability and green efficient manufacturing.” www.shehkai.com.tw
Taiwanese tool manufacturer Wan Iuan has confirmed that it is currently working on a new factory, to be completed in 2025, which will include new equipment and machinery to offer further capacity and products to customers, whilst also helping to reduce carbon emissions and labour costs.
Located in Kaohsiung, Wan Iuan Enterprise Co Ltd was set-up in 2001 as a small business with only 20 people. Through the leadership of General Manager Chiou Tsai Ding the company has grown into the leader it is today –supplying punches and dies to global customers, including all kinds of fastener dies and punches in a variety of high-speed steels (Erasteel and Nachi), as well as carbide (CB Ceratizit).
“Our existing factory had reached capacity and to continue to grow as a business we needed to add a new site,” explains Wan Iuan. “We therefore purchased a new factory in 2023, which has been under construction for the last two years and set to be completed by June 2025.”
Wan Iuan confirms that new machinery will be purchased for the new factory, including 5-axis machines and grinding machines, with the option to turn the machines into semi-automated equipment.
“Due to the focus in the market on reducing carbon emissions, we need to purchase new equipment that can help simplify the manufacturing
process, enhance the production speed and reliability, as well as reduce labour costs. By introducing automation within the production line, and all peripheral machinery, we can also help emphasise the quality, convenience, and speed, at which our manufacturing assembly line can operate, which will help us to further support customers,” comments the company.
Wan Iuan’s punches and drives are particularly popular for the production of automotive screws, as well as within the construction hardware sector. “These markets are very important to us and as a business we are always looking at how we can further work with customers in these sectors,” mentions Wan Iuan. “Our company specialises in the production of mechanical parts, mainly in fasteners, and we can provide our customers with tool solutions whilst supporting them to ensure the correct material selection is made for each application.”
Another decisive factor that has enabled Wan Iuan to establish itself within these high-end markets is its commitment to quality.
“The quality of Taiwan’s technology is obvious to all in the world –whether it is fasteners, machinery or any industry,” states Wan Iuan.
“Why is Taiwan’s quality so strong? Because we have a ‘one stop service’ in Taiwan. From upstream to downstream, from order to shipment, the entire production process is complete, with everyone helping each other. We are a very proud Taiwanese manufacturer and we are committed to quality and innovation associated with ‘Made in Taiwan’. As a business we also ensure we have a skilled workforce, use advanced technology, whilst responding to market needs – so that we are a formidable competitor in the global landscape.”
Wan Iuan concludes: “We will continue to provide the products, the quality, and the service, to the necessary delivery dates, to meet the needs of our customers. For those customers that are looking to increase their tool life, and want to work in partnership, they need to speak to us.” www.w-i.com.tw
Here Bettina Mertgen, partner – customs, excise taxes and foreign trade law at Deloitte Legal Rechtsanwaltsgesellschaft GmbH, provides an overview of some key upcoming EU regulations, their challenges, as well as an approach to navigate through this regulatory jungle – both now and in the future.
The European Union has committed to playing a leading role in the transition to a sustainable future through the European Green Deal, which includes several regulatory frameworks introducing obligations for companies.
Firstly, the Corporate Sustainability Due Diligence Directive (CSDDD) is the European approach to a legislative act on due diligence in supply chains. Companies must establish certain due diligence measures regarding basic human rights, such as working conditions, no child labour or slavery, as well as fulfilment of comprehensive obligations regarding environmental protection.
It applies to companies in the EU with 1,000 employees or more and a net annual turnover of more than €450 million worldwide. It also applies to companies located outside of the EU with a net annual turnover of more than €450 million in the EU. The scope is limited to corporations or limited liability companies. While it does not directly apply to smaller companies or other foreign companies, it is likely that they will be affected as being part of a larger company’s supply chain.
The directive results in a considerable expansion of the protected legal interests in the supply chain compared to existing legislation in the EU Member States, such as the Supply Chain Due Diligence Act (SCDDA) currently in force in Germany.
Traditionally, due diligence measures are focused on the company itself and therefore on conditions under its direct control. This changed already with the SCDDA in Germany but will be extended with the CSDDD even further. In the context of the CSDDD, the so called ‘chain of activities’ includes direct suppliers, certain indirect suppliers, and parts of the downstream supply chain, such as the distribution of the products. There are also special due diligence obligations if the company is becoming aware of grievances or violations of the covered rights within its supply chain.
Companies are expected to include the relevant topics into compliance management systems, conduct regular risk analyses, prevent violations, as well as implement remedy measures. They also must establish a complaint procedure and document the situation, as well as the progress in an annual report.
An important aspect in the CSDDD compared to most existing regulatory frameworks is the civil liability of companies for violations. Usually, companies violating any requirements can be fined or subjected to other administrative actions. In addition to potential high fines, companies can now under specific circumstances also be confronted with claims from persons who were affected. This includes full compensation of resulting damages.
EU Member States must transpose the directive into national law within two years after coming into force. The applicable regulations should therefore apply to the first companies in 2028.
Although small companies and companies outside the EU are not addressees of the directive and the implementing national laws, they will be impacted as well when dealing with
EU entities. They will receive requests regarding new contract clauses on the fulfilment of the relevant obligations, as well as regarding the confirmation of being compliant with the respective laws. Therefore, it is highly recommended to set-up a robust compliance system and to gather the relevant information within the supply chain.
The Corporate Sustainability Reporting Directive (CSRD) establishes obligations for companies to make certain ESG data available to the public in an annual report. It applies to large companies meaning that at least two out of the following three thresholds must be exceeded: A €25 million balance sheet total; €50 million net turnover; and 250 average employees.
While the CSRD does not apply to non-EU companies directly, EU companies in scope with a third country ultimate parent will also have to request sustainability data from their ultimate parent if certain revenue thresholds are reached.
Companies in scope must gather sustainability data in different ESG areas and report them annually. The report must be included in the financial statement and must be validated externally. Relevant datapoints to be reported are published by the EU and require a company to disclose information in certain areas
with a financial impact on the company, an impact of the company on the environment, or both. The data is related to data gathered according to the CSDDD and therefore certain synergies can be utilised.
The CSRD applies to the mentioned large companies beginning in business years starting on or after 1 st January 2025, with the first report to be made in 2026. Other timelines apply to companies that are public interest entities, for example because they are listed on a capital market.
Challenges for companies will in many cases be the limited quality of existing sustainability data, and a complicated process of gathering new data. As already mentioned, such companies should ensure a robust data basis and a compliance management system – enabling them to align the different requirements in one central system.
The regulatory background of the EU Taxonomy Regulation is closely related to the CSRD. It aims to classify the business activities of a company according to their environmental performance and to direct investments into more sustainable activities.
It is applicable to all companies that must report on sustainability topics according to the CSRD. Companies must conduct an analysis of their business activities and check any eligible activities against a catalogue of requirements for the specific activity, including the availability of certain certifications or reductions in CO 2 emissions. Depending on the outcome, the activity can be reported as conforming with the EU Taxonomy in a mandatory annual report. Like the CSRD, the EU Taxonomy does not require companies to directly improve their sustainability indicators, but rather to establish transparency about the sustainability of ongoing business activities.
Indicators reported under the CSRD and EU Taxonomy will only become more relevant in the future, when present and upcoming regulations require
…companies violating any requirements can be fined or subjected to other administrative actions…”
financial institutes to increase the share of sustainable investments. Publicly available sustainability data will likely be important indicators for determining if the company can be seen as a sustainable investment in this context.
Carbon Border Adjustment Mechanism (CBAM) aims to compensate for carbon emissions caused by the production of certain goods that are imported into the EU, but produced in third countries, preventing the outsourcing of energy intensive productions into low cost countries ‘carbon leakage’. It is applicable to any company acting as a so called ‘operator’ importing goods, including cement, fertilisers, iron and steel, hydrogen and electricity. The specific goods are determined by tariff codes in the annex to the CBAM regulation and cover certain products relevant for the fastener industry, such as screws, bolts and nuts. Companies importing the goods need to collect the necessary information about the production from their suppliers or producers and register as an importer. They need to report the amount of goods imported and pay a fee in the form of buying a certain amount of so called CBAM certificates. The price for available certificates will be increased in the future to encourage a sustainable transformation. CBAM is in a transitional period since 2023. While the first reports could be based on estimates for certain emission values, future reports must include specific emission data after entering a definitive phase from 2026 and onwards. However, it has turned out that the requirements are so complex and complicated that the suppliers and, consequently, the companies are not yet able to provide this data. It is yet to be seen how the authorities will react if almost no company can provide such data.
There are several upcoming requirements for companies around sustainability topics and there will be even more in the long-term. It is therefore more important than ever to ensure a robust, general and adjustable compliance management system that covers all regulatory requirements now – which is prepared to cover additional requirements in the future. The existence of a solid foundation of sustainability data and information about the own supply chain is a central topic.
However, it must be ensured that this data is centralised rather than used in isolated compliance silos. Even if the effort is substantial, companies can use gathered data to fulfil multiple requirements. They will get a better understanding of the effects of sustainability factors on the own business model within their compliance management system. This does not only support the idea of ESG, but using the gained transparency can help optimise the business set-up as such. Mastering the aforementioned challenges can lead to a more robust business in the future.
For more guidance on these, as well as other regulations, contact Bettina: https://tinyurl.com/23es3zh2
On 1 st October 2024 Pedro Zaldua retired from Talleres Saspi (SASPI) after nearly 40 years, leaving the fastener machinery manufacturer in the capable hands of his sons – Iñigo Zaldua and Mikel Zaldua. Here, we caught up with Mikel to understand what this means for SASPI and its customers, as well as their plans for the future.
In 1961 a small family-owned machinery business, situated in the heart of the Basque country, started serving the Spanish fastener market. Mikel explains: “The original founders of the business looked to grow the company and develop the machinery, but it wasn’t until 1986, when my father took over, that the company really focused on boosting exports and increasing its product range to cover all fastener manufacturers’ needs.”
SASPI’s product range includes flat die thread rolling machines, rolling machines with pointing units, rolling machines with stud selectors, rolling machines with washer assembly, high-speed automatic pointing machines, secondary operation machines, rotary thread rolling machines for nails and washer assembly units.
“My father was a true innovator,” continues Mikel. “He introduced many groundbreaking technologies to thread rolling machines, such as the pioneering touchscreen interface and our patented motorised die pressure adjustment system, which essentially created the ‘CNC’ thread rolling machine. These innovations have been instrumental in defining the SASPI brand. We are proud that SASPI is now one of the market leaders in our field – with SASPI machines operational in countries all around the world.”
In addition to technological innovations within this time, markets have also developed. “The advancements in technology and the increasing connectivity between machines have revolutionised our industry,” comments Mikel. “The fastener market has also undergone a dramatic transformation. The aerospace sector, once a small niche for SASPI, has become a cornerstone of our business and presents significant growth opportunities for the foreseeable future. However, the automotive sector is also on the cusp of significant change and navigating this evolving landscape will be crucial. We are closely monitoring industry trends and investing in technologies that will position SASPI for success in these and other key markets.”
In order to supply these key markets, SASPI works closely with its customers to achieve a flexibility that it says is becoming rare. “Our customer-centric approach, our flexibility, as well as our ability to make quick decisions, enables us to listen closely to our customers and understand their evolving needs. This agility enables us to respond quickly to market demands and maintain a competitive edge,” proudly states Mikel. He adds: “The change in leadership will not alter this commitment to our customers. We will continue to foster the close, family-like relationships we have built, ensuring we understand and address their needs with speed and efficiency. We make it our business to know what our customers or any new
We will continue to foster the close, family-like relationships we have built, ensuring we understand and address customers’ needs with speed and efficiency.”
perspective customers need from their machines, working with them very closely to fulfil all their needs as a quality, reliable partner.”
As part of this commitment, recent investments have included a focus on expanding SASPI’s secondary operation capabilities to enable the company to offer more complete solutions to customers and enhance overall manufacturing processes. These investments will provide significant advantages, such as reduced lead times, increased efficiency and improved overall product quality. SASPI is also actively exploring how Artificial Intelligence (AI) and machine learning can enhance manufacturing processes, improve machine performance, as well as further enhance the customer experience.
“Innovation has always been, and will continue to be, at the heart of SASPI,” concludes Mikel. “It’s not just about keeping up, it’s about driving the industry forward and we will continue to invest in research and development, attend industry events and training programmes, to stay ahead of the curve and integrate the latest technologies into our machines.”
www.saspi.es
Fastener 2000 GmbH is a family run company, now led by the second generation, with one principle at its heart – to offer special goods, drawing parts and non standard parts, in a variety of materials, to wholesalers worldwide.
Fastener 2000 underlines: “Our concept is simple. We offer short delivery times without a minimum order quantity, with high-quality products to wholesalers. We maintain a large stock of products to ensure daily shipping is possible, in order to satisfy our customers’ demands. To further help with this we are constantly investing in improving our logistics processes, as well as making sure our suppliers are of the highest quality available.”
Fastener 2000 supplies screws, hot forged fasteners and parts, cold forged fasteners and parts, special fasteners, as well as turned and machined parts – with a variety of surface treatments available including zinc flake (silver or coloured), as well as HDG and others.
“As the market progresses, so must the fasteners,” comments the company. “As newer innovations and solutions develop across markets, as well as new regulations and specifications coming into force, there is a higher demand for non standard parts. Fastener 2000 is constantly adapting to meet these needs and the challenges associated with them in order to be the best partner for our customers – whatever the challenge or specification. Customers just need to contact us and we will find a solution.”
Fastener 2000 works together with its customers to create drawings to meet these needs, providing hot forged parts for the best quality, further strengthened with an ISO 9001:2015 certification.
In addition to a focus on quality, Fastener 2000 is committed to providing customers with full lot traceability – with lot numbers able to be traced back to the original source. “Since the start of the business back in 2000, our company has a strict guideline for traceability. However, as customer needs’ develop and change, we are now seeing a higher demand for sustainable practices and emissions data. Therefore, as we look to the future, it is important for Fastener 2000 to continue our practice of using as many recyclable materials as possible, whilst also reducing waste on our processes. As part of this commitment, we are constantly looking to modernise our technical equipment, as well as improve and optimise our processes and services – with our delivery, stock and order promises – in order to offer our customers a complete service,” concludes Fastener 2000.
www.fastener2000gmbh.de
Since our foundation in 1932, we are proud to be one of the leading wholesalers of fastening technology. Headquartered in Lotte, Germany, with over 200 dedicated employees, we work every day to keep the world together. Our focus is on high-quality screws, fasteners and solutions that meet the requirements of our customers in various industries. Our modern logistics center in Lotte ensures efficient and on-time delivery. Our vision of „The world in your hands“ embodies our commitment to empowering our customers with reliable fastening solutions while striving to make a meaningful impact on society through sustainable practices and responsible actions.
Never run out of consumables again - our Kanban system makes it possible. To ensure the multi-bin system is seamless, we first determine your actual requirements (forecast) taking into account a safety stock on the shelf. The selected containers contain the quantity of the respective parts required within a delivery cycle - including any consumption peaks.
If a container becomes empty, you use a second one with the same filling quantity. In this way, your business is always optimally supplied without having to build up large stocks.
Discover the benefits of Fuchs+Sanders Kanban RFID - an advanced and efficient method of automatically reordering fasteners. Our Kanban RFID system uses wireless technology to ensure a smooth and intelligent replenishment solution for your business.
With RFID tags on the bins, you can track your material stock in real time and automatically reorder as soon as it falls below the predefined stock level. Our RFID solution detects empty containers and automatically sends an order request to our logistics center so that you can rely on a continuous supply from our product portfolio.
The Fuchs+Sanders Kanban RFID system enables you to optimize your warehousing and simplify the ordering process, allowing you to benefit from improved inventory management, reduced storage costs and seamless integration into your existing processes.
Optimized procurement management saves time and money. With FUSA®-scan, you can digitize your stocks and reorder in no time at all. By scanning the labels on the shelf, the containers or in the scan catalog, you can easily and precisely determine the current demand for an itemor have our staff determine it for you.
The collected data is recorded in the associated software for checking before the individual or collective order is sent to Fuchs+Sanders. The program also creates an order overview in the file format of your choice for your records.
FUSA-scan is: Efficient procurement managementconvenient and self-explanatory. This benefits you as a dealer, trade or manufacturing company.
We have summarized all our services for you in our F+S Connect brochure. Take a look inside:
Fuchs + Sanders Schrauben-Großhandels-GmbH + Co.KG Im Westerfeld 1 · 49504 Lotte · Germany
Tel. +49 5404 9160-0
Fax +49 5404 9160-140 info@fuchssanders.de
Founded in 1979 in Best, the Netherlands, as a distributor of stainless steel fasteners, Nestinox B.V has seen continuous growth over the past 45 years, through the opening of sales offices in both Germany and Belgium, as well as various investments in software and technology – including Artificial Intelligence (AI).
As a supplier of various kinds of stainless steel bolts, stainless steel nuts, stainless steel screws, springs, washers, solar fasteners, concrete anchors, machine bases, security screws, and even maintenance products, Nestinox supplies into industry in the Netherlands, Belgium, Germany and the rest of Europe.
In addition to supplying a wide range of products, Nestinox focuses on adding value to its customers by delivering high-quality products as efficiently as possible, at the lowest possible cost. To do this, the company has recently invested in AI technology to further enhance its internal processes for managing sales orders, as well as for calculating purchase demands.
Robert-Jan Steegman, CFO at Nestinox, highlights: “Nestinox wants to be an extension of our customers’ organisations, which means finding the right solutions through proper communication and an optimised internal process. By streamlining a customers’ order processes, we can
•
•
Nestinox is able to offer specific custom-made solutions according to customer specifications.”
ensure customers are receiving the best service possible and continue to meet the changing customer demands – where customers want high-quality products with no supply chain issues.”
“As Rotterdam is Europe’s most important harbour, especially in containers, Nestinox is able to keep transport costs low, which is of course a huge benefit to our customers,” continues Robert-Jan. “The Netherlands is also the centre of road transport, which means that our customers throughout Europe can count on short lead times. Efficiency is our vision and we strongly believe a high-quality product, with no drop-outs, will win out over a cheap inferior product.”
To further ensure quality, Nestinox has a strict selection of product suppliers, as well as thorough input and output monitoring. The company also supplies its products in robust and tailor-made packaging to ensure fasteners leave the warehouse in robust outer boxes. As well as this, Nestinox offers a private labelling service to meet customers’ requirements. Other additional services include special packaging, powder coating, kitting, as well as delivery per project.
Nestinox is also able to offer specific custom made solutions according to customer specifications. The company highlights: “We truly believe that cooperation is the best connection. Together with our customers we look for tailor-made solutions that can consist of standardised fasteners, but also of a product that is produced according to a drawing or specification – including stamped parts, cold pressed products, turnery, threading and treatments.”
In addition to these added services, corporate social responsibility is a very important focus for Nestinox. Both directly and indirectly Nestinox is contributing to a sustainable future. Internally, the company is making ecologically conscious choices, such as employees driving environmentally friendly vehicles, using green energy, as well as recycling whenever possible.
Indirectly, Nestinox is also contributing to a sustainable future by supplying fasteners for generating solar energy, with some of its key markets including the installation of solar panels, fencing, construction, sun shades, food processing equipment, agricultural installations and the production of bicycles.
Robert-Jan concludes: “Nestinox regards employees, customers and suppliers as partners, working together towards the same goal – to be a partner in stainless steel fasteners.”
With over 3,000 m² of storage space, 5,000 pallet positions, and 15,000 small parts bins, we keep many products in stock – ensuring fast shipping and excellent service.
From 25 th – 27 th March 2025, industry professionals will meet in Stuttgart for the 10th edition of Fastener Fair Global – the international flagship event for the worldwide fastener and fixing industry.
After a record attendance in 2023, visitors can look forward to another event full of networking and business opportunities, with access to top tier suppliers from across the globe. The 2025 show will also see the launch of two focus pavilions, promoting specialist solutions for a fast changing industry.
Nearly three months ahead of the show, more than 900 companies from 44 countries have already confirmed their participation, covering a gross exhibition space of well over 52,000m 2. Visitors can look forward to a line-up presenting the full supply chain for fastener and fixing elements in manufacturing, construction and other industrial applications.
Over three days, there will be numerous opportunities to personally engage with innovation leaders including Albert Pasvahl GmbH, Alexander Paal, Ambrovit SpA, Böllhoff, CHAVESBAO, Eurobolt B.V, Fastbolt Schraubengroßhandel GmbH, INDEX® – A PERFECT FIXING, Inox Mare Srl, Lederer GmbH, Norm Fasteners, Obel Civata, Reyher, SACMA Group, Schäfer + Peters, Tecfi SpA, WASI GmbH, Würth Industrie Service and many more.
Filling four expansive halls, exhibitors will provide a unique cross section of the global fastener and fixing sector, with significant participation from Germany, Italy, China, Taiwan, India, Turkey, the Netherlands, the United Kingdom, Spain and France.
With its unmatched coverage of fastener and fixing products and related equipment, Fastener Fair Global 2025 is expected to attract widespread interest from diverse markets. In 2023, key visitor sectors included metal production, automotive, distribution, construction, mechanical engineering, hardware and DIY retailing, as well as electronics. Nearly three in four visitors came from outside Germany, pointing towards the increasing global reach of the show.
2025 will see the introduction of two special focus pavilions to encourage deeper engagement with emerging trends and innovations and to open new avenues for networking and dialogue.
Launching for the first time in hall 7, the Innovation and Sustainability Pavilion will highlight groundbreaking fastener solutions that deliver high on performance while reducing environmental impact, for example by utilising efficient manufacturing processes, recyclable materials, or lightweight designs. In addition in hall 3, the Hand Tool Pavilion is making its debut, showcasing specialist hand tools designed for advanced, cost efficient, and precise applications in key sectors such as aerospace, defence, energy, shipbuilding, construction and manufacturing.
The popular Route to Fastener Innovation Competition, organised by this Magazine, will also make a return, promoting clever innovations on the market, with the aim to show the benefits of new
fastening products to a wider audience (head to pages 110 – 128 to find out more about the innovative products and services entered this year).
Tangible improvements for users, for example in efficiency, durability, safety, or cost-effectiveness, is what drives the ongoing development of fastener and fixing innovations. By aligning its advancements with the needs of various industries, the fastener and fixing sector acts as a critical enabler of solutions to global issues.
“Our exhibitors are vital strategic partners in driving progress and resilience,“ explains Stephanie Cerri, event director for Fastener Fair Global at RX. “Their innovation power lies in developing customised, high precision fastening solutions, using advanced materials for lightweight or high strength applications; embracing automation, IoT and other Smart technologies; as well as introducing sustainable practices and materials in production processes.”
In fostering this culture of innovation, Fastener Fair Global stands as the keystone event of a progress focused industry, enabling visitors unparalleled access to a wealth of pioneering ideas and solutions.
The official event website provides extensive information, including the latest exhibitor list and online show preview to search for companies, products and services. A one click planning tool also enables visitors to add companies, products and sessions to their personal agenda for downloading, printing or sharing. The show’s travel hub offers useful links and information on travel, visa, and accommodation, including a bespoke HotelMap with hotel offers in Stuttgart.
Fastener Fair Global will be held from 25 th – 27 th March 2025 at Messe Stuttgart, Germany, occupying halls 1, 3, 5 and 7 and will be open from 9:00 to 18:00 on Tuesday and Wednesday, and 9:00 to 16:00 on Thursday.
www.fastenerfairglobal.com
DEUTSCHLAND GMBH & CO KG 1 974
AUGUST FRIEDBERG GMBH 1 212I
AUSTENITE FASTENERS PVT LTD 3 2496
AZTEC INTERNATIONAL S.A 7 3440
BÄCKER GMBH & CO KG 1 474
BAOJI SINO-SWISS TITANIUM CO LTD 7 4177
BARTOLUCCI SRL 1 1294
BEIJING JINZHAOBO HIGH STRENGTH
FASTENER CO LTD 5 3168
BERDAN CIVATA ENERJI IMALAT SAVUNMA
SANAYI VE LABORATUVAR HIZMETLERI TICARET AS 1 931
BEST QUALITY FASTENERS 1 596
BEST QUALITY WIRE CO LTD 5 2540
BETTER FASTENERS (SHANGHAI) CO LIMITED 5 3128
BHAVYA INDUSTRIES 7 4142
BI-MIRTH CORP 5 2731
BIAT GMBH & CO KG 1 120
BILSTEIN & SIEKERMANN GMBH & CO KG 1 212D
BİMELKA METAL SANAYİ VE TİCARET
LİMİTED ŞİRKETİ 7 3626
BIRLIK BAGLANTI ELEMANLARI SAN VE TIC LTD STI 3 2066
BODEGRAVEN METAAL NV 1 1330
BODYCOTE SPECIALIST TECHNOLOGIES GMBH 7 4210
BÖLLHOFF GMBH 1 756
BOLT BAGLANTI ELEMANLARI SAN VE TIC AS 1 446
BOLTUN CORPORATION 5 2888
BONOTTO PACKAGING 7 3630
BONTEMPI VIBO SPA 1 646
BORGH B.V 3 1744
BOSSONG SPA 1 346 BOWON METAL CO LTD 7 3476 BRALO
GURU KIRPA UDYOG 7 3856
GWI GMBH 1 112
H-LOCKER COMPONENTS INC 5 2681
HAFREN SECURITY FASTENERS 3 2290
HAINING HISENER TRADE CO LTD 5 2931
HAIYAN BOOMING FASTENER CO LTD 5 2948
HAIYAN FUJIAN FASTENER CO LTD 5 3058
HAIYAN HANGRUI PACKING CO LTD 5 2944
HAIYAN HUASHENG FASTENERS CO LTD 5 2954
HAIYAN JIAMEI HARDWARE MANUFACTURING AND TECHNOLOGY CO LTD 5 3031
HAIYAN JINNIU FASTENERS CO LTD 5 2938
HAIYAN JINRUN METAL PRODUCTS CO LTD 5 2956
HAIYAN LONGCHENG STANDARD PARTS CO LTD 5 2939
HAIYAN LONGSHENG HARDWARE CO LTD 5 2975
HAIYAN SANMA STANDARD HARDWARE CO LTD 5 3041
HAIYAN SANSHUN TRADE CO LTD 5 2955
HAIYAN SHANGJIA HARDWARE CO LTD 5 3175
HAIYAN TIANQI STANDARD PARTS CO LTD 5 2936
HAIYAN WANCHENG FASTENERS CO LTD 7 4071
HAIYAN WEISHI FASTENERS CO LTD 5 2907
HAIYAN XINGLONG FASTENERS CO LTD 5 2958
HAIYAN YIHUI HARDWARE TECHNOLOGY CO LTD 5 2959
HALFMANN SCHRAUBEN GMBH 1 1322
HAMAR SP J 1 408
HAMIDI EXPORTS 1 1256
HANDAN AOJIA FASTENERS MANUFACTURING CO LTD 7 4186
HANDAN CHANGFA FASTENER
MANUFACTURING CO LTD 5 3181
HANDAN CITY OUCHEN METAL PRODUCTS CO LTD 5 3252
HANDAN HAOSHENG FASTENER CO LTD 5 3159
HANDAN JUDONG FASTENERS CO LTD 5 3188
HANDAN JUER METAL PRODUCTS CO LTD 5 3258
HANDAN MEIJIANLI HARDWARE MANUFACTURING CO LTD 7 4176
HANDAN RUISU FASTENER MANUFACTURING CO LTD 5 3186
HANDAN TEDUN FASTENER GROUP CO LTD 7 4174
HANDAN XIAOJUN FASTENER
CO LTD 5 3184 HANDAN YONGNIAN HONGJI
PARTS CO LTD 5 3185 HANDAN YONGNIAN JIBIAO FASTENER MANUFACTURING CO LTD 7 4184
HANDAN YONGNIAN SHUAIYU FASTENER MANUFACTURING CO LTD 7 4173 HANDAN YONGTE FASTENER MANUFACTURING CO LTD 5 3071 HANGZHOU AILONG METAL PRODUCTS CO LTD 5 2941
HANS SCHRIEVER GMBH & CO KG 1 1122
HAO MOU NUTS MFG. CO LTD 5 2776
HAPARE GMBH 3 2224
HARBIN RAINBOW TECHNOLOGY CO LTD 5 2918
HARITON MACHINERY CO INC 1 1381
HAS FASTENERS VIDA BAĞLANTI
ELEMANLARI AŞ 1 1452
HEADER PLAN CO INC 5 2823
HEBEI FUAO FASTENER
MANUFACTURING CO LTD 5 3260
HEBEI FUYANG METAL PRODUCTS CO LTD 5 3270
HEBEI GOODFIX INDUSTRIAL CO LTD 1 5 190 3189
HEBEI MIJIA LMPORT&EXPORT TRADING CO LTD 7 4185
HEBEI TONGFA GROUP MINGHAO CO LTD 7 4171
HEBEI XILIDE METAL MANUFACTURE CO LTD 7 4180
HEBEI YUETONG FASTENERS
MANUFACTURING CO LTD 5 3280
HECO-SCHRAUBEN GMBH & CO KG 7 3830
HEICO GROUP 1 1222
HELLER TOOLS GMBH 1 1265
HELMUT STEINFELS GMBH & CO KG 1 1374
HERMANN LOHMANN GMBH & CO KG 3 1678
HEROSLAM SAL 1 1284
HISENER INDUSTRIAL CO LTD 5 2932
HIZ BAGLANTI ELEMANLARI SAN VE TIC AS 1 662
HJZ - ZANDVOORT DRAADINDUSTRIE B.V 1 988
HOENDERDAAL FASTENERS B.V 3 1966
HOME SOON ENTERPRISE CO LTD 5 2558
HOMEYU FASTENERS CO LTD 5 2736
HOMN REEN ENTERPRISE CO LTD 5 2644
HSIEN SUN INDUSTRY CO LTD 5 2876
HSIN CHANG HARDWARE INDUSTRIAL CORP 5 2564
HSIUNG JEN INDUSTRIAL CO LTD 5 2756
HU PAO INDUSTRIES CO LTD 5 2658
HUADE HOLDINGS LTD ( VIETNAM ) 5 3008
HUAHUO METAL-TECH CO LTD 5 2964
HUANG JING INDUSTRIAL CO LTD 5 2738
HUGEHIPPO TECHNOLOGIES LLP 7 3862
HUGO BENZING GMBH & CO KG 3 1850
HUIXING INDUSTRY (QINGDAO) CO
JUNTASA
OE SOLUTIONS LTD 3 2090
ORIENTAL MULTIPLE VIETNAM CO LTD 5 2860
ORNIT AGRICULTURE INDUSTRY BUSINESS AND MANAGEMENT ACA LTD 7 3532
ORT ITALIA SRL 7 3730
OTICS FASTENER CO LTD 5 2980
OTTO ROTH GMBH & CO KG 3 2084
P P IMPEX INDIA | BYLDR 5 2700
PANELFISA GROUP 3 1820
PANTHER T & H INDUSTRY CO LTD 5 2522
PATTA INTERNATIONAL LIMITED 1 1274
PEAKSIGHT (SHANGHAI )
TECHNOLOGIES CO LTD 1 462
PECOL SISTEMAS DE FIXAÇÃO S.A 1 1208
PETER SCHRÖDER 1 412
PGB-EUROPE 1 836
PILONI SRL 1 1146
PINGOOD ENTERPRISE CO LTD 7 4080
POOJA FORGE LIMITED 1 1342
PRECISION INDUSTRIAL FASTENERS 7 3760
PRECISION TECHNOLOGY SUPPLIES LTD 3 1596
PRECISO VERBINDUNGSELEMENTE GMBH 3 2244
PRIMAT CURTIS 7 3312
PRINZ VERBINDUNGSELEMENTE GMBH 1 467 PRK TECHNOLOGIES GMBH 1 208
PRO-PATH INDUSTRIAL CO LTD 5 2520
PROFIROLL TECHNOLOGIES GMBH 3 2140
PROJAHN PRÄZISIONSWERKZEUGE GMBH 3 1610
PSE PRECISION SPRING EUROPA SPA 3 2278
PT OZ FASTENER 7 3557
PÜHL GMBH & CO KG 1 622
QIANG XIN STAINLESS STEEL FASTENER CO LTD 5 3250
QIFENG PRECISION INDUSTRY SCI-TECH CORP 5 2902
QINGDAO EASY-FIX HARDWARE & AUTO PARTS CO LTD
•
In today’s interconnected world having a reliable supply chain isn’t just a benefit – it’s a necessity. That’s why Achilles Seibert GmbH (Achill) has established two new warehouses in Vietnam and India, strategically located to ensure efficient logistics and cost-effective operations for customers.
Each warehouse is more than just a storage space – it’s a streamlined inventory management, which enables Achill to sell with import prices and order full containers for its customers.
“Our colleagues in Vietnam and India ensure that products are delivered on time and meet the necessary quality standards,” comments Achill. “They handle sourcing and quality assurance on-site and we welcome all visitors at Fastener Fair Global to come and meet them. Whether its purchasing, sales, or supply chain management, we look forward to engaging with visitors on a wide range of topics.”
Another topic for discussion is Achill’s webshop, with its capabilities demonstrated live at the show. “Time is money and we know that efficiency is key to running a successful business. That’s why we have an intuitive, user-friendly webshop that makes sourcing fasteners a breeze. Whether you’re in the office or on the go, our online platform allows you to check availability and place orders with just a few clicks. Visitors to our booth will be able to discover how our digital solutions can save time, reduce administrative hassle and improve the efficiency of supply chains,” adds Achill.
As the industry evolves, so does Achill’s responsibility to the planet, which is why the company is incorporating CBAM (Carbon Border Adjustment Mechanism) into its operations, setting what it
believes is a new standard for environmental responsibility in the fastening industry.
Achill concludes: “Meeting the CBAM reporting requirements and all associated regulations is enormously time-consuming and complex. We are well prepared in this area, and by purchasing from us, customers can save efforts within their own companies. At Fastener Fair Global, visitors can meet our knowledgeable team, explore our latest product offerings and see how our digital and sustainable innovations are working. Whether you’re an industry expert or new to the world of fasteners, we promise you’ll leave with fresh ideas, valuable insights, as well as connections that matter.”
www.achill-fasteners.com
As experts in the distribution of fasteners and welding, CHAVESBAO will once again be exhibiting at Fastener Fair Global with its wide range of standard fasteners, consisting of more than 14,000 DIN and ISO references, as well as a complete catalogue of welding and customised solutions.
In addition, CHAVESBAO is also able to offer a specialised packaging service with packaging, as well as kits and palletised products that adapt to the needs of projects. The customised packaging and labelling is adapted to meet requirements in specific units per case.
With 16,000m 2 of automated storage facilities, CHAVESBAO’s logistics capacity enables the company to guarantee a 24 hour dispatch service, as well as close and professional advice from its team of 100 people.
“If you are looking for fastening and welding solutions to boost your business, CHAVESBAO is your strategic partner to optimise your processes and achieve your objectives,” underlines the company. “Don’t miss the opportunity to get to know our new products and solutions during Fastener Fair Global.” www.chavesbao.com
By embracing Artificial Intelligence (AI) and redefining its product offerings, Dimac Srl states it is shaping the future of zero-defect manufacturing with its ZED generation machine series, including the MCV4 ZED automatic sorting machine.
Dimac’s ZED generation machines aim to eliminate errors in fastener and metal part production, with a zero-defect commitment, as well as combine Statistical Process Control (SPC), 100% automatic inspection and seamless IT system integration. The machines have also been engineered to help manufacturers achieve stringent quality standards in highly competitive markets.
At the heart of the ZED generation is the MCV4 ZED, an automatic sorting machine designed for the 100% inspection of medium sized fasteners. Key features include simultaneous control of two parts, improving the sorting efficiency; an operator friendly HMI interface with an ergonomic and intuitive design to streamline operations; enhanced reliability with operational memory to safeguard productivity during power interruptions or jams; as well as redefined NDT crack detection and heat treatment inspection technology for superior precision.
Dimac underlines: “The MCV4 ZED doesn’t just speed up the sorting process; it redefines it. Its advanced features drastically reduce human error, ensure seamless operation and enhance overall reliability. The result is a more efficient production process with higher quality outputs, delivering on our promise of zero-defect manufacturing.”
Dimac’s proactive approach to innovation is evident in the company’s adoption of AI integration, which is the development and
deployment of AI-powered algorithms integrated with advanced vision systems. The company has also redesigned modular systems, meaning it has a renewed line-up of 100% automatic inspection and sorting machines that offer superior efficiency and flexibility.
In addition, Dimac is doubling its production facilities in Tortona, Italy, to expand its global commercial network, as well as enhancing its digital presence by launching a brand new modern, user-friendly corporate website.
As a specialist in functional coatings, SurTec will showcase its comprehensive range of solutions at Fastener Fair Global for every possible function that a coating can provide on a bare fastener.
This includes sealing, locking and friction coefficient adjustment. In the field of functional electroplating, SurTec International GmbH provides tailored solutions for corrosion protection, including phosphating and galvanising with zinc and zinc alloys for steel. Its processes cover pre-treatment, coating, and, depending on requirements, passivation and sealing to meet the highest standards.
As part of its portfolio, SurTec places strong emphasis on sustainability, offering cutting edge PFAS-free solutions for future mobility. In addition, the company also offers microencapsulated adhesives for thread locking, including precote® 30 and precote® 80, which is also PFAS free. Additionally, a PFAS-free version of precote® 85, the pre-coating for thread locking, will be available starting 25 th February. These coatings are used, among other things, in the body and chassis of electric vehicles by leading OEMs.
Furthermore, eMobility designs increasingly demanding pre-coatings for sealing applications, with SurTec’s water-based and PFAS-free sealants used in battery packs worldwide. Also available is the SurTec Coat 2000 series, which is ideal for applications such as sealing rings and plain bearings. These innovative solutions demonstrate SurTec’s commitment to helping customers meet the growing demands for sustainable and future-proof mobility, while delivering excellent performance for critical applications.
“Visit Hall 3, stand 1666 to discover the latest advancements in functional coatings and electroplating solutions with our global experts. SurTec combines a comprehensive product portfolio, global reach, and expertise in the coating and finishing of metals and plastics, whilst also offering technical consulting and products for all requirements,” comments the company
Introducing the Atotech CMA Closed Loop System, a game-changing solution for alkaline zinc nickel plating. This revolutionary technology leads the sustainability transition by reducing the disposal and treatment of zinc nickel wastewater by 90%.
Experience exceptional performance and enhanced product quality. Maintain your competitive edge and achieve your sustainability goals faster through higher efficiency, lower energy consumption and savings with the Atotech CMA Closed Loop System.
To find out more about our surface treatment solutions, scan the QR-code to the right.
With a history of exhibiting at Fastener Fair Global – including at the very first show – Don Quichotte B.V will once again be displaying its fasteners and fixings, as well as a warm welcome and famous Dutch hospitality in Stuttgart.
Don Quichotte highlights: “For us Fastener Fair Global is the main event for the fastener sector. We always see a lot of familiar faces, as well as meeting new people and companies. During the show you get a good look and feel for what is happening in the market and in which direction it is heading.”
Since 1921, Don Quichotte has been producing hardened steel nails in Helmond, the Netherlands, which can now be found all over the world. Don Quichotte has established itself as a strong brand for high-quality products against a competitive price on construction sites all over the world.
Next to nails, Don Quichotte also supplies mounting and installation products for the electrical and sanitary sectors. “As a business we are known for our product innovations and our strategy has shifted to products for electrical installation, which might not be the first products that come to mind when visiting Fastener Fair Global,” continues the company. “Of course these, as well as our main fixings and fasteners, will all be on display at our stand, with our international sales team there to answer questions or enquiries – along with an abundance of good coffee and typical Dutch snacks.”
During the show, Don Quichotte will also be highlighting its recent investments in production efficiency, including packaging machines, as well as investments in logistics and more sustainable production and packaging – resulting in less energy waste, energy regeneration and more green energy – with a goal to significantly decrease its carbon footprint every year.
www.don-quichotte.com
For the past 40 years, in the field of induction heating systems, CEIA SpA has been manufacturing high and medium frequency generators that distinguish themselves for high-energy efficiency and minimum operating cost.
Due to its remarkable experience in the field, and continuous and careful technological research, CEIA can guarantee products of excellent quality and security, including its new line of Master Controller V3+ and Optical Pyrometers SLE Slim Line control units.
CEIA systems can be used in different phases of fastener production, including the continuous heating of the steel wire, stainless steel, aluminium, titanium, inconel, or for the warm forming process, for the thread rolling, threadlocking, hardening or forging of bolts or screws. In addition, due to their extremely compact dimensions, CEIA generators can be easily integrated with automatic header machines or automatic thread rolling machines.
To ensure quality, all CEIA systems are certified and calibrated to grant the customer a high-quality control, as well as being able to regulate power automatically. All these important features ensure that CEIA is a quality partner for fastener manufacturers.
Thanks to the web server and integrated data logger, it is also possible for CEIA devices to be interfaced with any PLC or be connected
online to retrieve all the information necessary to the process control, such as heating temperature, power supplied, diagnosis, etc.
www.ceia-power.com
In order to offer customers a wider range and continue to meet market requirements, E.CO Srl is continuing to invest in its fasteners for hybrid and Electric Vehicles (EVs), as well as its new assortments for storage systems, which will be on display at this year’s Fastener Fair Global.
E.CO’s wide range includes clips, buttons, rivets, screws, bushes, bolts, washers, cable ties and other fixing solutions that have been developed in-house – from the design phase to the personalised packing.
“Our constantly evolving range is the result of 70 years of experience and passion, which is moving towards the future to satisfy customers’ needs,” comments the company. “E.CO is a leader in the field of fasteners and specialised in the production of high-quality fixing solutions, designed and developed to fulfil the needs of different customers.”
E.CO fasteners are found in a variety of industries such as automotive, naval, furniture, solar panels, construction, as well as white goods and toys, which have seen large growth in the last few years.
“The E.CO team will be glad to welcome visitors to the fair and support them with our know-how, offering tailored solutions according to specific needs,” concludes the company.
As it enters its 30th year of business, Hafren Security Fasteners is reflecting on nearly three decades of innovation, quality, and dedication, providing the highest levels of security in fastening solutions.
Guided by its mission of stamping out the impact of theft globally, Hafren underlines its position as a trusted name in the fastener industry, offering tamper resistant solutions that prioritise safety, durability and design.
This March, Hafren will showcase its latest advancements in security fastener technology and will demonstrate how its products are addressing the ever evolving challenges in securing assets across industries, from construction and transportation to technology and infrastructure.
The company explains: “Visitors to Fastener Fair Global can expect exclusive and expert consultation on our stand, where they will be encouraged to engage with our knowledgeable team to discuss how our fasteners can offer tailor-made solutions to projects. As we gear up for our 30th anniversary celebrations, we’ll also be providing insights into our journey, as well as what’s next for Hafren Security Fasteners.”
www.hafrenfasteners.com
AGTOS
With more than 10,000 references, visitors to Fastener Fair Global will be able to find out about the new products in INDEX® – A PERFECT FIXING’s new general catalogue, including anchors for direct fixing to concrete, fixing systems for solar panels, as well as the NA nail anchor.
The new catalogue includes innovations in current lines, as well as new ranges and products designed to meet the needs of the construction, renewable energy and agriculture sectors. These include the new TX Bimetal anchor for direct fixing to concrete, with an A4 stainless steel body and carbon steel tip to guarantee strength and maximum durability.
In addition, INDEX® – A PERFECT FIXING is also extending its TH and TF ranges of anchors for direct fixing to concrete.
Other products in the catalogue include a range of fixing systems for solar panels. These steel and aluminium systems come with a 25 year guarantee, as well as CE Marking, having been designed for safe and durable installations on industrial and residential roofs.
Visitors will also be able to discover the new range of NA metal strike-through anchors approved for non-structural applications in cracked and non-cracked concrete indoors; a range of accessories for agricultural work featuring a new family of metric screws; the incorporation of the ISO-7380 Allen; as well as new options including the A4 Bimetal drill screw. www.indexfix.com
As the market continues to develop, customers often need assisting to define and scope complex requirements. That’s why UK-based Francis Kirk has global representatives to visit customers, learn about their products and service needs, as well as provide solutions to best meet their requirements across the globe.
Based in Manchester, Francis Kirk also offers added services to help its customers keep on top of inventory and ordering, such as Vendor Managed Inventory (VMI) that enables the company to take care of managing and replenishing fasteners, fixings and C-Class components – including HELICOIL®, Philidas®, Unbrako, HOLO-KROME and Nord-Lock brands – with no manual intervention.
Francis Kirk explains: “We’re justifiably proud of our extensive fastener range – but it’s not all we do. We’re often asked if we’re simply a distributor, but the reality is we’re much more than that. This is because our mission of optimising the quality, breadth, and accessibility of the fixings, fasteners, and other products and services available, requires more than a standard distributor model.”
Francis Kirk also provides a wide range of components, including C-Class items such as PPE, workwear, cutting tools, hand tools, adhesives and abrasives. The company also handles special requirements or bespoke requests – manufacturing a significant proportion of its offering. “This combination enables us to keep our own costs down and act as a ‘one stop shop’ for our customers – which helps keep their sourcing and overheads low in turn,” comments the company. “With Francis Kirk, customers don’t have to worry where products are coming from, because it’s likely that they’re here already. We have extensive warehousing and logistical operations both in the UK and internationally, so we hold plenty of stock of all our products.”
National Machinery LLC and SMART Machinery Srl will be demonstrating its groundbreaking Smart Planetary RNG machine at Fastener Fair Global in Stuttgart, Germany.
Designed to push the boundaries of rolling technology and maximise effectiveness, SMART states its SMART RNG is built for precision, efficiency and simplicity. Its innovative features include an electronic handwheel and an intuitive graphic interface to make operation effortless.
With just a push of a button via AutoSetup, the machine’s special set-up procedure automatically produces the first part, leaving the operator with the straightforward task of quality assessment. This streamlined process significantly reduces set-up time, increasing productivity.
What sets the SMART RNG apart is its exclusive, maintenance-free design. By eliminating traditional gears, the machine operates quietly and vibration-free, to ensure a smooth and reliable performance. Its synchronisation, with a state of the art linear motor introduction device, delivers unparalleled accuracy to help enable users to produce a wide range of part diameters with extraordinary consistency. SMART RNG’s adaptable configuration and cutting edge technology also combine to deliver a user-friendly and profitable solution.
www.smartmachinery.com
With an extensive portfolio of specialised products, Hapare GmbH is focused on providing customised solutions for thread repair and processing, as well as for securing and sealing connections.
Hapare’s wide selection of thread inserts for the repair and reinforcement of threads, in metal and plastic, are ideal for applications where standard threads fail or where higher load capacities are required. Furthermore, Hapare also offers high-quality threaded pins for precise and reliable connections, capable of withstanding high loads and torsional stress.
In addition to its full range on display at Fastener Fair Global, Hapare will also be displaying a range of H-Coil thread inserts, known for their high stability and resistance. These inserts are especially suited for durable and load-bearing threads in the automotive and mechanical engineering industries. Other inserts on display include specialised inserts with key locking, which provide an additional safety level by preventing unwanted loosening of connections, especially in critical applications where precision and security are essential.
Hapare also supplies WRE rings, which are locking and sealing systems that ensure secure connections by preventing loosening under vibration and movement. WRE rings are used in many industrial sectors where high safety and reliability are critical.
“Visitors to Fastener Fair Global can visit our stand to learn more about our products and their benefits. Our experienced team is ready to provide expert advice and demonstrate how our solutions can optimise manufacturing processes,” explains Hapare.
Through adapting to the dynamically developing construction market and, consequently, to the changing needs of its customers, the Klimas brand will celebrate its 35 th anniversary in 2025, presenting its latest innovations at Fastener Fair Global.
With almost 6,500 products in its portfolio, the Klimas brand has become one of the European leaders in the production of construction fasteners, producing up to 30 million screws a day. This includes the ThermoDrive V2 – a fastener for thermal insulation systems, which has already become known among contractors – that facilitates work on construction sites, especially where there are significant irregularities in the substrate or thermal insulation on the insulated surface. The design of the fastener allows users to not only fasten with one dimension insulation materials of different thicknesses, but also when working with ETICS insulation on ETICS.
“The ThermoDrive V2 is universal, fixing almost all variants of thermal insulation found on walls in Europe,” highlights Paweł Polak, global market development manager at Klimas Wkręt-met. “ThermoDrive V2 also has all the technical parameters at the highest level available in the industry, as well as being very easy to install for any contractor.”
Thermal insulation is a topic that is a part of Klimas’ sustainable development, which is why the brand is intensively developing this branch of production. “The correctly selected product, but also the correct workmanship, results in the durability of the insulation system for years,” explains Pawel.
He continues: “This means not only the absence of failures, but also the absence of point thermal bridges, which consequently generates a lower demand for the thermal energy of the building. At Klimas, we know what producer responsibility means, which is why the highest attention is paid to quality at our plant. The manufacturer’s reliability
is followed by technology, which is why we look to introduce products almost every year. However, these novelties are created in accordance with trends that place ecology high alongside technology.”
Klimas therefore offers a wide range of wood fasteners, used to strengthen structures and indispensable for renovation work. The company also coats many of its screws and mechanical anchors with SQ Ceramic. This proprietary multilayer ceramic coating significantly improves the anti-corrosion properties of the screw, making the fastening much more robust and durable.
These products, as well as mechanical anchors, concrete screws, frame fasteners, light housing fastening systems or fastening systems for hydro and thermal insulation of flat roofs, will all be on display at Fastener Fair Global in Stuttgart in March.
www.klimas.com
With more than 80 years experience in the design and manufacturing of thread rolling tools for the production of fasteners, HEROSLAM SAL will once again be exhibiting at Fastener Fair Global.
As part of its ‘long life thread rolling tools’ motto, HEROSLAM supplies its wide range of thread rolling tools – including flat, cylindrical and planetary dies – to fastener producers around the world. The company produces all its dies from beginning to end at its facilities in Bizkaia, Spain, including heat treatment and coatings, to give the tools an extra quality and guarantee.
“The most prestigious fastener and threaded parts producers around the world rely on HEROSLAM as their main thread rolling tools provider. We establish long-term business relationships with our customers, becoming a partner in thread rolling solutions to help optimise threading processes,” comments HEROSLAM.
The company continues: “Thanks to our extensive background in the field, we offer our customers professional, personalised, technical and commercial assistance, with tailor-made and customised thread rolling solutions.”
During Fastener Fair Global 2025 FM Group will unveil its latest achievements with a particular focus on its expansion into the automotive sector, as well as its new eCommerce platform and FM Academy.
From a small provincial company established in 1978, with just over 5 employees, FM Metal Fasteners Group SpA now has more than 110 employees and specialises in sourcing and distributing standard and custom designed fasteners, serving both the Italian and European markets. As part of its commitment for excellence, FM Group is pursuing certifications such as IATF to align with international standards and strengthen its position within the automotive industry, as well as by meeting the evolving needs of its customers through competitive prices, maintaining the highest standards and delivering efficient logistical solutions.
These logistical solutions include its new B2B eCommerce platform, designed to deliver a streamlined and intuitive purchasing experience. The platform offers access to an extensive product catalogue, simplified ordering processes and personalised technical support tailored to customers’ needs.
To add to this, FM Group has also introduced its FM Academy, an initiative showing the company’s paths to continuous education. FM Academy provides professional and technical training for clients, offering online resources and insights into the fastener industry. The programme is designed to improve skills and optimise production processes for customers.
www.fmspa.com
Brugola OEB will be returning to Stuttgart this March to showcase its nearly century-long expertise, alongside its innovations, as well as the continuous evolution of its brand –with a new, larger stand reflecting its key values of quality, innovation and market focus.
Brugola underlines: “The expansion of our stand is not only a reflection of our growth and dedication to our customers but also an opportunity to provide a more comprehensive experience for visitors to the show.”
The company will be showcasing its range of fasteners for eMobility – a rapidly growing sector requiring increasingly lightweight, durable and sustainable components, as well as its products dedicated to internal combustion engines, reflecting Brugola’s commitment to a power supply that, together with many of its customers, the company still considers fundamental to the future of the automotive sector.
Brugola will also showcase an expanded portfolio of special parts, enabling visitors to discover advanced and customised solutions, which highlight its continued investment in research and development – designed to meet the most complex challenges in terms of performance, reliability and adaptability.
“Even components with complex geometries are manufactured through our cold forming process, thanks to our extensive experience. We are therefore able to offer solutions that would typically require machining operations,” states Brugola. “This approach allows us to deliver products with significant benefits, including higher productivity, superior surface quality and enhanced mechanical properties, all while ensuring substantial cost savings for end customers.”
Amongst these special solutions, Brugola will also be presenting a bolted joint developed in collaboration with Growermetal, which has been designed to prevent corrosion, maintain a consistent energy flow and eliminate the risk of electrical leakage. With its advanced coating penetration, and removal features, this solution ensures extremely low contact resistivity between coated components, and provides significant advantages in terms of efficiency and reliability for battery applications.
www.brugola.com
As a family-owned business in the third generation, R+FK Schulte KG (rfks) is a reliable producer of washers, stamped parts, and screw locking devices, that has established itself as a market leader according to DIN/ISO standards throughout Europe.
All products are 100% manufactured in Plettenberg, Germany, with the aid of more than 45 state of the art stamping machines, as well as the expertise of well trained specialists. At the same time, rfks distributes special parts according to individual customer requirements as a basic capacity.
“Every year we process over 30,000 tonnes of flat steel in all material grades. Our wide customer range includes wholesalers of fasteners, the automotive industry and its suppliers, screw and dowel manufacturers, as well as machine and steel construction companies,” comments Peter Schlütter, sales manager at rfks. “What sets us apart from direct competitors is our versatility and know-how in both worlds. We are at home in DIN/ISO standards as well as customised special parts.”
Through its own tool manufacturing unit and in-house construction, as well as a large raw material stock, plus modern packaging lines and smooth logistics, rfks ensures a comprehensive service thanks to the expertise of its well trained and experienced team members.
For rfks, innovation means the continuous development and improvement of every production process to stay ‘one step ahead’. Peter concludes: “rfks has one clear goal in mind – to achieve the highest possible customer satisfaction. Our daily challenge is the constant development of our technology expertise, which is how rfks succeeds in handling even the most complex orders and fulfiling each demand.”
www.rfks.com
International specialist for fixing and joining solutions, NORMA Group, has extended its portfolio with a full range of pipe support system solutions specifically designed to meet the rigorous demands of modern construction and building services.
Offering safety, stability, and long-term performance, these solutions will be on display at this year’s Fastener Fair Global, and cater to essential applications such as fire protection systems, HVAC, plumbing and temperature control. By delivering adaptable, high-quality components, including pipe fixing components, rail systems, and assembly parts, NORMA enables efficient and sustainable infrastructure across the building industry.
The new pipe support system portfolio offers a versatile and efficient design for quick and easy set-up, reduced labour time and increased overall efficiency. Thanks to its adjustability, the system can accommodate different pipe diameters without the need for multiple tools, which helps lower installation costs. Built from robust materials such as steel, the solutions provide exceptional stability, ensuring pipes remain securely in place – preventing movement or misalignment during assembly or operation. Also designed to withstand high pressures and harsh working environments, the system delivers long-term durability and minimal maintenance requirements, further supporting cost-effectiveness and reliable performance.
As well as the new pipe support system, NORMA Group will be showcasing its entire product portfolio at Fastener Fair Global. NORMA’s experts will also be demonstrating the latest advancements in pipe support systems and discussing how these innovations can add value to construction, infrastructure and industrial applications.
www.norma-connects.com
Remaches Factory Srl serves the needs of European distributors that require immediate access to fastening products directly from the manufacturer, by reducing costs and lead times and, most importantly, consistent product quality.
Remaches’ production facility located in Wuxi, China, spans 30,000m 2 and has a daily production capacity of 12 million pieces, offering a comprehensive range of standard and structural rivets tailored for the European market.
The company explains: “Ensuring consistent product quality is the guiding principle of Remaches Factory. In the fastener manufacturing landscape there are many players but only a few of them have internal laboratories with the most sophisticated equipment.”
Remaches Factory’s laboratory houses advanced metallographic miscroscopes, multimode detectors, optical shielding, durometers, coating thickness meters, as well as neutral salt spray test chambers for strict product quality control.
“Whether we are talking about the automotive or aerospace industry, electronics or railway, the consistency in quality and technical specifications of our products are guaranteed by an effective control system, certified by the most important certification bodies worldwide,” explains Remaches Factory. “We can provide certificates in accordance with the most common standards concerning
raw materials, surface treatments, as well as measurement of product performance.”
The company concludes: “The production of special products according to customers’ design or sample products also enables us to meet even the most sophisticated requirements. Many companies sell fasteners, we provide technical solutions through our top quality fasteners, with a mission to enable our customers to be successful distributors.”
NORMA has set the standard for innovative and reliable connection technology for 75 years. Offering over 40,000 products — from clamps to tailored solutions — everything is provided from a single source. Our expertise, experience, and proven know-how support diverse industries. Trusted by millions worldwide, our solutions ensure efficient, reliable, and future-proof projects. NORMA creates connections that drive industries and deliver quality that lasts. Today and tomorrow.
The origins of Nord-Lock Group can be traced back to 1982, when the company introduced the original wedge-locking washer. Since then, Nord-Lock Group has grown into a global engineering group, consisting of three additional technology brands: Superbolt®, Boltight® and Expander®. Visitors to Fastener Fair Global will get to experience the latest product achievements first-hand, along with a first class technical support service offering.
At the end of 2023, Nord-Lock became the first company to obtain CE Marking for securing washers. Now, Nord-Lock has expanded the range of CE Marked products, with one notable product being the Nord-Lock X-series washer. This innovative product features a conical shape, making it excel at keeping bolted connections tightened and secure even when the mating material expands or contracts due to thermal effects.
Another noteworthy addition is the recently launched wedge-locking washer that comes pre-coated in black, ideal for applications where camouflaging is critical. Just like the original wedge-locking washers, the black washers will never loosen unintentionally; they provide unparalleled corrosion protection; and offer opportunities to streamline operations since no additional paint job is required. Combined with Nord-Lock Group’s global availability and unmatched lead times, the black washer is a valuable addition for critical missions, when there is no time to lose and much on the line.
“Nord-Lock Group goes beyond delivering industry leading bolting solutions by acting as a trusted partner to customers in numerous industries. Meeting face-to-face with existing and potential partners to build strong, reciprocal relationships is something we put a lot of effort into,” comments the company. “When working with Nord-Lock Group, you can rest assured that you will receive the highest quality in both products and business partnerships.”
www.nord-lock.com
In September 2024, as part of a long-term strategy, Güde completed a new logistics hall in Plettenberg, Germany, giving the washer manufacturer 12,500 new storage spaces for mini load carriers to deliver even more flexibly and quickly, as well as enabling the company to focus on its sustainability commitments.
With an emphasis on added services, lean logistics and high-quality products, Güde produces safety washers, wire bended parts, as well as screw and fastening devices. Using custom-made machines and tooling, Güde’s production facility ships up to 140 pallets of products every day to wholesalers and distributors worldwide.
Güde is also pleased to be making a special contribution to the energy transition, with its washers and spring washers used in large solar parks, new electricity highways and in the railway sector. As a further sign to its commitment to sustainability, Güde has also installed a new 600kWp photovoltaic system, which means more
than 60% of the production is now CO₂ free and makes an important contribution to environmental protection.
“We are constantly making sure we have all the latest technology available,” comments Lutz Güde, managing director at Güde GmbH. “This means we can offer full customisation to our customers, in terms of products, quantities, as well as packaging, which we need to stay ‘one step ahead’ of our competitors. Added services have never been more important and we are proud of our ability to adapt to each customer’s individual requirements – especially packaging and labelling.”
www.guede.net
Commonly known as an expert in frame plugs and other fixing systems, TOX-Dübel-Technik GmbH is expanding its portfolio to also position itself as a reliable partner for screws – with the introduction of a new comprehensive range of nine screw categories.
The new screw range covers various types including timber construction, drywall, profile connection, façade, and sealing screws, as well as drywall-to-drywall, decking, adjusting and gypsum fibreboard screws. Specifically designed for professionals, the drywall and gypsum fibreboard screws are also available as collated variants for use with screw guns – ideal for efficient workflows. Available with various material properties, surface finishes, thread types, and drill points to ensure precise adaptation to specific requirements, TOX reports that these screws stand out for their quality and versatility.
TOX has also developed tailored solutions for the sanitary sector to meet the challenges of humid environments. These solutions include the sealing all purpose plug Aqua Stop Pro, now featuring a detachable plug collar and TX screw; the all purpose plug TRI; and other specialised fixings to ensure secure and durable installations – even under heavy loads. These solutions reliably protect against moisture and mould, which could otherwise cause significant damage.
With its expanded range, TOX reinforces its position as a reliable partner for professionals and DIY enthusiasts, setting new standards in fixing technology.
DÖRKEN, a manufacturer of high performance corrosion protection systems, will be presenting its updates on its PFAS-free portfolio this year’s Fastener Fair Global.
The German-based company is addressing the issue of PFAS with its DELTA-PROTEKT® TC 502 GZ topcoat, which features a silver finish – making it ideal for use on numerous metric components and other fasteners. Visitors to Fastener Fair Global can also find out about the results of series trials and projects generated with various PFAS-free prototypes. DÖRKEN will also be presenting the first specification entries with PFAS-free systems.
As well as this, the company will be presenting its zinc flake systems during the show, to help protect components against external influences and the associated signs of corrosion. Thanks to the modular structure of these systems, additional properties such as friction coefficient requirements or different finishes can be added to a basecoat with a topcoat.
DÖRKEN would also like to extend a special invitation to the information event organised by EIFI (European Industrial Fasteners Institute) on the subject of PFAS on the opening day of the trade fair (25 th March) from 16:00 to 19:30 on the exhibition grounds. High-level speakers from the fields of chemistry, users and OEMs will provide
insights with regard to the possible PFAS regulation, as well as DÖRKEN presenting the current status of the possible PFAS restriction and the chemical background.
REYHER has been supporting many industries for decades, with an expert team that has extensive knowledge in specific fastener products. This team is ready to show visitors to Fastener Fair Global how the company understands customers’ needs and how to benefit from REYHER’s quality, reliability and customer focus.
As one of the leading trading companies for fastener and fixing technology in Europe, F REYHER Nchfg GmbH & Co KG offers a comprehensive range of products and customised services, with more than 130,000 items for a wide range of applications permanently in stock – with a delivery availability of over 99%. REYHER also creates customised special parts based on drawings for special
More than 130,000 items in stock to ensure highest availability
Flexible kanban supply
Customised packing solutions
High-level e-business solutions
REYHER test laboratory for reliable product quality
DEGOMETAL states that its know-how in manufacturing rivets, combined with a constant drive for R&D, allows it to meet special requirements for its customers by changing standard features or delivering adapted solutions.
Founded in 1967, DEGOMETAL specialises in rivet production, operating two ISO 9001:2015, NF EN 9100:2018 and AQAP2120 certified plants, which are equipped with advanced cold forming, rolling and assembly machines to enable quick fulfilment of small and large orders.
Its product range includes blind, solid, semi-tubular and tubular rivets, which account for 70% of its turnover. It also manufactures special cold formed and rolled parts, as well as components from turning, stamping and tubular processes. With over 10,000 product references, and a wide array of surface treatments including zinc plating, nickel plating, anodisation and lacquering, DEGOMETAL ensures flexibility, fast shipping and excellent aftersales service.
“Our expertise and customer focused approach have earned the trust of industrial leaders,” comments DEGOMETAL. “As well as this, our commitment to quality, innovative techniques, as well as the ability to deliver customised solutions on time, are key to our success.”
MANASSERO & C Srl will be showcasing some of the new machines available from its second warehouse at this year’s Fastener Fair Global, including an electrically connected SMART NGS flat die thread roller, RMG wire drawers models 500 and 89, as well as a turntable.
Representing a number of machine manufacturers across Europe – with its list of agencies constantly growing – MANASSERO has two warehouses organised into different areas for each type of machine. The first warehouse houses headers, as well as nail headers, while the second warehouse houses thread rollers, wire drawers, pointers and all kinds of ancillary equipment.
“Our aim is to provide the best possible solution for our customers, with new or used machines covering a wide and comprehensive range,” comments the company. “We invite our customers to visit our stand so we can assist them with new or used machines, trade back surplus machines, as well as offer advice on tooling, rebuilding or shipment.”
Optimas Solutions has introduced a significant enhancement to its global supply chain management capabilities with the integration of multi-sourcing functionality within the SO99+ ToolsGroup platform.
This innovative feature marks a pivotal advancement in Optimas’ commitment to delivering unparalleled supply chain resilience, efficiency and flexibility for industrial customers, while also providing robust risk mitigation strategies to safeguard against disruptions.
The integration of multi-sourcing enables Optimas to effectively automate its supply base, enhance its supply chain resilience, whilst also mitigating risks. Key benefits also include enhanced supplier management, increased flexibility and responsiveness, as well as cost optimisation.
“By digitally diversifying our supplier base, we significantly enhance our ability to respond to mitigate risks associated with supply chain disruptions, such as geopolitical events, natural disasters, or supplier insolvencies,” comments Mike Tuffy, CEO at Optimas OE Solutions Ltd. “As a full service distributor managing multiple suppliers, we can strategically allocate awards to maintain consistent product availability, ensuring our customers are never left vulnerable. This proactive approach safeguards business continuity and fortifies our commitment to customer satisfaction.”
The implementation process was carefully structured to ensure a smooth transition and maximise the impact of this powerful new feature. Optimas comprehensively assessed its existing supply chain processes, pinpointing areas where multi-sourcing could provide the most value. Optimas then undertook extensive data research to consolidate supplier information from multiple sources, taking advantage of automation and Artificial Intelligence insights to leverage its complete supply network. Rigorous testing validated the tailored functionality’s performance, accuracy, and reliability, meeting Optimas’ high standards of quality and operational excellence.
MKT Metall-Kunststoff-Technik GmbH & Co KG will be presenting its advanced range of concrete anchors including mechanical and chemical anchor systems –featuring its BZ3 wedge anchor – at this year’s Fastener Fair Global.
Now available in high corrosion resistance (HCR) steel, the BZ3 wedge anchor has also had size M20 added to the range, both of which are reflected in the updated European Technical Assessment (ETA – 20/0117). This ETA also features the application in steel fibre reinforced concrete and increased seismic strength in case of gap filling – where mortar is injected through a special washer to close the annular gap between anchor and fixture.
Moreover, MKT’s BZ3 dynamic anchor for fatigue applications is now also available in stainless steel A4 grade, sizes M10 to M16. MKT reports that the BZ3 dynamic is the first wedge anchor ETA certified for fatigue loading, offering an effective solution for moderate fatigue loads. Next to the BZ3 dynamic, the nail anchor N (M6) and the bonded expansion anchor VMZ dynamic (M12 to M20) complement the product range from dynamic anchors for redundant applications to anchors for very high fatigue loading.
To add to this offering, in its chemical anchor range, MKT now offers general type approvals that cover the compliant installation in facilities for storage, filling and handling of potentially harmful liquids. For this, the epoxy mortar VME plus and hybrid mortar VMH do not require any additional installation steps and can be permanently marked by special washers. Further to these injection systems, MKT has extended the production range of the resin anchor capsule VZ that now also covers sizes for the installation of M24 and M30 rods.
In addition, for these anchor solutions MKT offers training for planners and installers, as well as specialised design software. www.mkt.de Hall 1, Stand 222
MKT is a manufacturer and one of the global market leaders for high quality anchors used in concrete structures. We o er the complete range of mechanical and chemical anchors for professional applications.
Mavita has been producing standard, special screws, bolts and cold stamped items in all types of materials and treatments for over 60 years, building solid and long-lasting partnerships based on competence, fairness and a high-level of quality.
Used across a variety of industries, including household appliances, electrical, solar, furniture, as well as the automotive sector, Mavita’s production range includes screws and bolts from 2mm – 12mm in diameter and in lengths from 4mm – 120mm, in all types of carbon and stainless steel, with the possibility of providing all types of heat, galvanic and anti-unscrewing treatments. The company also cooperates closely with its customers – with 70% of its production range made up of special parts according to customers’ drawings – and has achieved both ISO 9001 and IATF 16949 certifications.
Mavita comments: “Special parts refer to the products that require more deformation in the pressing process and that are realised by the progressive multi-station presses with up to 5 dies. It also refers to the pins with particular geometries or with double threads, as well as the fasteners with various shapes of head, recess, shank and points. In addition pivots, bushings, shafts, stud bolts and pins that perhaps were previously made by turning, we are able to produce by cold pressing, achieving great cost containment for our customers.”
At Fastener Fair Global, Mavita will be showcasing its screws with unlosable washers, available as knurled, wavy, grower, and conical washers, in materials such as steel, stainless steel, nylon and thermoplastic. The company will also be highlighting its commitment
to quality – through SPC checks during production, as well as final mechanical and 100% optoelectronic sorting – using state of the art machines to guarantee a final PPM rate close to zero.
“We invite all visitors to our stand to find the most suitable solution for their fastening needs,” concludes the company. “In Mavita, visitors will find a capable and reliable supplier who wants to build a solid and long-lasting partnership based on fundamental principles such as competence, fairness and a high-level of service and quality.”
www.mavita.it
Stafa Group has invested in a kitting machine to produce kits with paper packaging, as well as LPDE plastic, meaning its packaging is fully recyclable and can be disposed of through the usual paper waste stream.
By using this type of packaging, Stafa is helping customers to improve their ecological footprint and contribute to a better environment, with paper packaging less harmful to the environment.
The company is continuing to seek sustainable solutions to reduce its direct and indirect CO 2 emissions wherever possible, having developed a sustainability strategy and roadmap with many ambitious goals. As a result, along with its partner and manufacturer of tube and flat film, AVI Volendam, Stafa has also succeeded in using LDPE film (LowDensity Polyethylene) consisting of 40% certified recycled material to make bags, which are then automatically filled with fasteners and other components (kitting).
The kitting service offered by Stafa provides complete peace of mind for its customers. “With Stafa, you only need to purchase one item and you no longer need to worry about procurement, handling, transportation, etc, for all the components in the kit,” explains Stafa. “Even if it’s not an item that we supply, our purchasing team can take care of the procurement from a chosen supplier.”
Headquartered in Germany, TOGE is synonymous with precision, durability, and superior engineering, with a comprehensive product range for every application – ensuring professionals can find the ideal fastening solution for any application.
TOGE Dübel GmbH & Co KG supports diverse construction and industrial projects with products including its screw anchors, which come in up to five coatings and quality grades to ensure suitability for various environmental conditions and load requirements.
In addition, TOGE also supplies innovative solutions for modern interior construction, such as the TSM Multiground internal thread screw. Approved for use in concrete and suitable for masonry and wood applications, the TSM Multiground is ideal for fastening ceiling suspensions, cable ducts, pipelines, brackets and claddings.
The company underlines: “TOGE is not only committed to product innovations, but also to sustainability and providing fastening solutions that are fully removable without leaving residue – making them entirely recyclable. This focus on environmental responsibility aligns with modern construction practices – emphasising circular economy principles.”
To further guarantee safety and quality, many TOGE products receive high-quality approvals, tailored to specific applications and conditions. As well as this, TOGE offers customised solutions
with private label packaging, including the transfer of product certifications. This enables business partners to market high-quality fastening products under their own brand while ensuring compliance with stringent industry standards.
Having manufactured and sold more than 2,500 in-line wire drawers for applications with cold headers, as well as straightening and cutting machines, Tecno Impianti has now introduced the SKP38 – an in-line wire drawer capable of drawing a 28mm wire.
The flagship of Tecno Impianti’s SKP series, the in-line wire drawer SKP38 features a newly designed uncoiler with an innovative system for the opening of the coil, as well as a T35 push-pointer for the pointing/threading of the wire into the drawing die. The PR250R feed-head also brings the wire to the cold header in a pre-straightened form.
Other products manufactured by Tecno Impianti for the fastener sector include vertical uncoilers, available in idle or motorised versions, feeding/pre-straightening units, wire pointing machines, vertical and horizontal coil-to-coil wire drawing bull-blocks – designed for big productions of drawn wire, coil compactors, as well as coil tilting units.
experience, we can customise our machines with many different options and accessories, to meet the different needs of each customer. We will be pleased to welcome visitors to our stand at Fastener Fair Global to show and explain our new products and technology for the fastener industry.”
With a long family tradition rooted in water-based products, Italian-based TECNOLOGIC 3® has transitioned from PFAS to water-based products to answer changing customer requirements for an eco-sustainable and ‘reduced impact’ product.
Through innovative chemistry, specific industrial production, and advanced applications, TECNOLOGIC 3® is an undisputed player in the market for reactive and non-reactive coatings for fasteners in the automotive and other industries. TECNOLOGIC 3® underlines that its water-based solutions have the ability to reduce the impact on the environment that the extensive use of solvents is having on the planet. In addition to the environmental benefits gained, the water-based solutions are also physiologically and toxicologically harmless.
“Innovation is a complex system and a result of the combination of technology, human processes, and environmental impact, with the awareness that every industrial action is a relationship, not an isolated act,” comments TECNOLOGIC 3®
This commitment to innovation is possible because of the company’s internal production process, with in-house machinery designed to apply adhesives, sealants and brakings on various materials and temperature ranges. Each product is born and tested in the laboratory, where customisation becomes a method. “Interactions with our customers become a learning opportunity,” comments
TECNOLOGIC 3®. “Our customers’ specific needs inspire process rethinking, as well as open perspectives that go beyond standard product logic.”
An example of this is TECNOLOGIC ® 16, a cold applied coating developed to prevent the adhesion of weld spatter and paint build-up. There is also TECNOLOGIC ® 40, a self-locking agent and hybrid sealant based on water and technologically advanced resins, which is cold applied to specifically prevent surface damages.
www.tecnologic3.it
TR Fastenings (TR), part of the Trifast Plc Group, will be exhibiting once again at Fastener Fair Global, where visitors can explore its latest innovations, and its expert team will be on hand to discuss solutions tailored to individual needs.
TR Fastenings supplies components to over 5,000 companies worldwide, spanning industries such as automotive, medical equipment and smart infrastructure sectors. The focus this year is on TR’s value proposition, showcasing an exceptional blend of manufacturing expertise, supply chain solutions and engineering innovation.
Visitors to TR’s stand can expect innovative animations highlighting key sectors and TR’s comprehensive product range, including proprietary solutions such as the EPW Screw and Plas-Tech 30-20®, designed to meet the highest industry standards, as well as its extensive product range. This range includes self clinch fasteners, fasteners for sheet metal, enclosure hardware, screws and inserts for plastic, cable glands, security fasteners, and plastic and rubber hardware.
TR Germany is a key focus for TR in 2025, reflecting a significant investment in its European warehouse, which has been expanded to 2,000m 2 This strategic move enhances TR Germany’s ability to provide distributors with extensive stockholding for diverse industry demands; excellent freight links across Europe, to ensure fast, reliable delivery; as well as streamlined supply chains, which reduces steps and eases pressure amid global challenges. There is also the added benefit of multilingual teams, offering seamless customer support.
These measures position TR Germany as a centre of excellence, ensuring distributors experience a hassle-free partnership with the confidence that comes from reliable supply chain solutions.
In addition to TR Germany’s advancements, TR Italy has enhanced its manufacturing capabilities, reinforcing its commitment to European production. TR is also focused on sustainability with compliance to CBAM (Carbon Border Adjustment Mechanism), as well as simplifying European supply while supporting global environmental goals.
In order to network with industry experts and form new partnerships, Alexander Paal GmbH will be giving visitors to this year’s Fastener Fair Global the opportunity to see its innovative fastener solutions first-hand and experience their quality and functionality.
On display at the show will be its wide product portfolio, including retaining rings DIN 471 and DIN 472, which are essential fastening elements for securely and precisely positioning components, as well as shim and support washers DIN 988. These precision components are widely used in the machinery and plant engineering industries to precisely adjust distances and tolerances between components, to ensure the functionality and longevity of machines.
Also on its stand will be Paal’s DIN 2093 disc springs. Made from high-quality spring steel and oiled to offer excellent wear resistance and corrosion protection, these high performance spring components can absorb large forces in a compact space.
“We invite visitors to come to our stand with any questions about our high-quality solutions. We look forward to personally welcoming visitors and collaborating to shape the future of fastening technology,” concludes Alexander Paal GmbH.
www.paal.de
From industry to DIY, Hans Schriever GmbH & Co KG (SCHRIEVER) offers a comprehensive range of screws that meet the highest quality standards, specialising in customised solutions such as the SIXFIX and TOBI®-Drive.
For private use in the DIY and craft sector, SCHRIEVER states its SIXFIX multifunctional drive offers exceptional flexibility and precision, making it ideal for demanding applications where reliability is key. Similarly, its S-WOOD screws for wood connections in the DIY sector help to guarantee an optimal connection and durability thanks to their special thread technology.
In addition, the TOBI ®-Drive features a unique geometry to ensure optimum power transmission, reduced tool wear and significantly increased efficiency. This enables users to work faster and more precisely – even in hard to reach places.
Manufactured from its facility in Lüdenscheid, Germany, SCHRIEVER’s speciality is the production of screws according to individual requirements. The company explains: “We are your partner for long-term success. Together we analyse challenges and develop customised solutions that strengthen competitiveness. From the initial idea to the finished screw, we are at your side with our expertise.”
With over 3,000 m² of storage space, 5,000 pallet positions, and 15,000 small parts bins, we keep many products in stock – ensuring fast shipping and excellent service.
One of the key visitor attractions of Fastener Fair Global will be the first-hand opportunity to assess new products and services that exhibitors have brought to the market through the Route to Fastener Innovation competition.
Fastener + Fixing Magazine will once again host the Route to Fastener Innovation competition, with its editorial team reviewing the products and services that have been entered into the competition – awarding the ‘Top 3’ with the accolade of being Fastener Technology Innovators.
Innovations that have been entered into the Route to Fastener Competition were accepted on the following criteria:
1. The product must have been introduced to the market for the first time within the last 24 months leading up to, or launched at, Fastener Fair Global.
2. The product must demonstrate significant and identifiable technical design, material or performance differences from other products already on the market.
3. The product must provide tangible and identifiable advantages for the end user or consumer – for example in efficiency, productivity, safety, strength, durability and cost reduction.
4. The product may be an improvement or upgrade on an existing line but must clearly meet all three of the above conditions.
5. Entries must not infringe the intellectual property rights of any other company.
To find out more about the innovations that have been entered read on – remember to take a note of the stand numbers or look out for the distinctive Route to Fastener Innovation competition 2025 logo that will be displayed on participants’ stands during the show.
On the second day of Fastener Fair Global there will be a special presentation to the winners on the Fastener + Fixing Magazine stand – hall 7, stand 4040.
www.fastenerandfixing.com
In the rapidly evolving Electric Vehicle (EV) sector, the demand for superior electrical connections continues to grow. PennEngineering states its new ECCB™ PEM eConnect® Contact Bushing is revolutionising busbar applications, providing reliable electrical connections between aluminium busbars, as well as copper, PCBs and cable terminals.
Initially, high current pathways in early EVs relied on heavy-duty cables and while these cables offered great flexibility, their performance was limited. As the EV industry advanced, so did the need for higher currents, prompting a shift towards busbars as a more efficient alternative. Early busbars were made of copper, requiring significant material to meet the EV sector’s standards, which not only increased weight but also raised costs.
To address this, companies opted to run busbars warmer and reduce the required amount of copper by half. However, by 2022 the rising cost of copper led EV companies to explore alternative materials, such as aluminium. Despite needing twice the amount of aluminium, its weight was still half that of copper, offering both weight and cost savings. However,
aluminium posed a challenge due to its rapid formation of an insulating oxide layer, complicating electrical connections.
In order to overcome all these challenges, PennEngineering has developed the ECCB™ PEM eConnect® Contact Bushing. This innovative product ensures electrical connections between aluminium busbars, copper, PCBs and cable terminals. Its high surface area knurl design pierces the oxide layer on busbars, creating consistent electrical connections without needing to plate the busbar itself.
Designed for installation into straight punched holes without additional surface preparation, the ECCB™ PEM eConnect® Contact Bushing breaks through aluminium and copper oxide layers for low resistance connections. It is ideal for use in panels with sheet hardness HRB 50/HB 82 or less.
www.pemnet.com
PEM eConnect® fastening technology provides repeatable, consistent electrical joints and superior installation in applications that demand advanced performance.
The unique high surface area knurl design of the ECCB™ Contact Bushing pierces the corrosion layer on busbars creating a consistent electrical current connection without needing to plate the busbar itself. Ideal for making reliable electrical connections between copper or aluminium busbars, PCBs, or cable terminals.
• Innovative design
• Simple installation
• Consistent electrical connections
• Reduced total installed cost
REQUEST SAMPLES
Responding to the industry wide drive towards sustainability, Bossong SpA has introduced the patented FOIL PACK system, which the company highlights uses 80% less plastic, 12% less emissions, as well as 50% less of waste in terms of volume.
For the past three years Bossong has focused on creating this sustainable system, with a special focus on maintaining mechanical performance, level of price, ease of use, as well as environmental characteristics of the product. This is also important due to the challenges of the European Green Deal for all industrial sectors in
As part of this commitment, Bossong has reduced the rigid plastic component of the packaging, with at least 65% of recycled plastic being used in accordance with the target fixed by the PPWR regulation for 2040, as well as removing redundant packaging including the cap.
The FOIL PACK system is suitable for use in combination with a reusable aluminium adaptor, which is compatible with the standard silicon caulking gun – both manual and battery versions. All these improvements and benefits are aimed at reducing resources both in the production, transport and ‘end of life’ phases of the product.
www.bossong.com
Due to its significant technical design, material, and performance, Böllhoff GmbH states its new QUICK FLOW® Plus is a groundbreaking advancement in fastening technology, introduced within the last 24 months.
Plus enables secure joining of thin sheets without pre-drilling or nuts. Its unique screw geometry ensures quick and reliable assembly, significantly boosting efficiency. In addition, Plus is made from high strength, corrosion resistant materials to ensure a longer lifespan and higher reliability, reducing maintenance costs and enhancing safety.
Plus also offers higher load capacity and improved vibration resistance, making it ideal for demanding applications in the automotive and aerospace industries, giving a range of benefits for the end user. These include a quick and easy assembly, which saves times and reduces labour costs; with no need for pre-drilling or thread cutting; as well as a high load capacity and vibration resistance – increasing connection
By employing cutting edge induction hardening technology, GH Induction drives advancements in fastener manufacturing with two key innovations –FEM simulation for precision hardening and additive manufacturing for induction coils.
Finite Element Method (FEM) simulation is used to model the heating process in 3D before testing on actual fasteners. This enables precise predictions of how magnetic fields and temperatures interact during hardening, ensuring uniformity and optimal quality. Additionally, FEM simulation supports the design of complex inductor geometries, enhancing efficiency and reliability in production.
GH Induction also leverages Electron Beam Melting (EBM) to 3D print pure copper induction coils, eliminating brazed points and enhancing durability. This patented process not only extends coil lifespan but also enables the design of complex geometries previously unattainable, unlocking new possibilities in hardening diverse screw profiles.
“By combining these innovations with precise control, energy efficiency and a commitment to sustainability, GH Induction redefines fastener manufacturing, ensuring stronger, greener, and more reliable products, for industries such as automotive and aerospace,” explains GH Induction.
PFAS products that were once widely used in different industrial sectors are now coming under increasing scrutiny due to their long-lasting presence in the environment. NOF METAL COATINGS GROUP has taken this as an opportunity to develop a new PFAS-free top coat range, which includes the PLUS® VLh 2 Silver.
Available worldwide, the PLUS® VLh 2 Silver can be applied to the GEOMET ® waterborne zinc flake base coat and meets REACH regulations, as well as European carmaker demands for a stable coefficient of friction on different bearing surfaces, including steel, aluminium or eCoat.
During tightening, PLUS® VLh 2 Silver helps to adjust and obtain the right coefficient of friction according to ISO 16047, which is required by automotive manufacturers. This new topcoat also performs very well on multiple tightening and high-speed tightening, with no stick slip and a promising release torque of 0.08 at 150°C.
In addition to the improved aesthetics with aluminium pigments in the coating, this new PFAS-free topcoat also includes fluorescent pigments for ease of positive identification. Under daylight, all NOF PFAS-free topcoats will have the same silver appearance, but under UV light, the added pigments enable users to easily identify which topcoat has been applied.
Exposure of GEOMET ® basecoat and new PLUS® VLh 2 Silver coated screw under a UV lamp to observe the
fluorescent blue, green and purple pigments
NOF METAL COATINGS GROUP also offers other silver and black finishes with specific coefficient of friction, all PFAS-free. All these topcoats are applied via industrial processes and are nonelectrolytic to help avoid hydrogen embrittlement, which can cause the cracking of metals.
The new InterShim™ wave spring from Rotor Clip s.r.o has been engineered for high acceleration electric motor applications, featuring alternating turns between inactive (flat) and active (waved) turns to ensure reliable performance under torsional loads and precise rotational movement.
InterShim™’s advanced design changes the turns from inactive to active in alternation, with an inactive turn always followed by an active turn. Every inactive turn between each active turn acts like a shim washer between two spring elements, preventing the wave trough of a higher level active turn from moving onto the wave crest of a lower level active turn – due to displacement or circumferential movement caused by torsional loads.
The turns of the wave spring, arranged with flat or waved shapes, are engineered to smoothly glide against each other. Such a design prevents the wave spring from collapsing, even when subjected to torsional loads that create relative movement between the active turns. Floating ends and bent ends help to prevent damage to the mating surface. InterShim™ is also a highly customisable solution, thanks to the
number of waves; turns, arrangement of shims or troughs; and range of speciality alloys available.
Whilst initially developed for the Electric Vehicle (EV) market, its advanced design addresses physical challenges such as extreme forces and vibrations, making it a versatile solution for high-speed and high stress applications across various industries.
Designed for industrial applications in complex sectors such as automotive, heavy carpentry, industrial automation, and various assemblies, Rivit states its Controlriv GEN3 offers ‘real time’ quality control of fasteners and helps to guarantee absolute precision and reduce costs associated with assembly errors.
Developed through intensive research and development, Controlriv GEN3 is 100% ‘Made in Italy’ and aims to bring considerable economic and time benefits to users. Furthermore, thanks to its versatility, Controlriv GEN3 can operate both in standalone mode and in cluster configurations, with several devices connected together.
The device can monitor the fixing process in ‘real time’, detecting anomalies through an alert system with notifications and colour codes. This ensures rapid intervention and minimises downtime. In addition, the separation of the pneumatic and electronic parts simplifies installation and maintenance, offering greater durability and stability.
Controlriv GEN3 also features accurate measurements, with compressed air pressure controlled within a programmable range – ensuring the correct functioning of the instruments at all times. A handy graphic display also enhances user-friendliness, along with intuitive function keys and USB ports for immediate handling. As well as this, Controlriv GEN3 can be interfaced via cable with Ethernet, Profinet, or cordless WiFi or Bluetooth, with the possibility of remote configuration and data collection.
ThermoDrive V2 from Klimas is a new generation series of universal fasteners for a wide range of ETICS systems, which can be used to fix different thicknesses of insulation up to 40cm.
Combining the advantages of its well known predecessors, the WKTHERM-S series and the ECO-DRIVE series, Klimas states its ThermoDrive V2 fasteners are high-quality, easy to install and achieve the maximum possible values of pull-out load capacity. Another important feature is their versatility of use, as they are suitable for the installation of thermal insulation systems using polystyrene foam, mineral wool or wood wool.
Thanks to their properties and innovative design, ThermoDrive V2 fasteners are ideal for fixing insulation materials to substrates made of concrete, solid ceramic brick, ceramic hollow block, lightweight aggregate elements and cellular concrete, as well as for fixing ETICS systems. Regardless of the chosen installation method, the fasteners can be used to fix different thicknesses of insulation up to more than 40cm.
In addition, the ThermoDrive V2 features a wide range of tolerance to uneven substrates to help ensure effective installation in each application. This significantly improves and speeds up work on the project, as the fasteners can be used across a variety of substrates. As well as this, the design of the 25mm to 65mm anchorage zone helps to guarantee reliable jamming of the fasteners, even in hollow materials with voids inside or thin walls of the internal structure of the masonry element.
Durability and safety of the insulation systems are also increased thanks to the sleeve of the fasteners, which have been designed so that the screwed-in steel pin, enabling the attachment of the insulation layer, is sufficiently isolated. As a result, ThermoDrive V2 is characterised by a minimum point heat transfer coefficient, where the value for ThermoDrive V2 mounted in a recessed manner is 0.001W/K and applies regardless of the thickness of the attached insulation.
www.klimas.com
Through its HS ASPE division, SACMA Group has introduced the T10-VT tapping machine, which combines high efficiency, environmental sustainability, and operator focused ergonomics, to deliver outstanding performance and ease of use.
Capable of running up to 200 parts per minute, SACMA highlights its T10-VT tapping machine is built for high productivity without compromising on quality control. The machine can process parts quickly and efficiently due to its four spindles, enabling the efficient tapping of nuts, rivnuts and various hollow parts, as well as the dual bowl feeders with double exits – complemented by linear feeders, which can carry four parts simultaneously.
T10-VT also features dual tapping heads with synchronised servomotors, mounted on a vertical sliding head and driven by a ball screw drive unit. A conveyor belt with an anti-shock system also enables reliable and damage-free transport of parts.
Other features include an indexing table with four divisions and direct drive rotation to guarantee precise operation; a quick tooling changeover to minimise downtime; as well as an integrated electronic system to monitor tap stress based on spindle motor absorption, ensuring ‘real time’ quality control for up to two parts simultaneously. This system, created in collaboration with Marposs, sensors the force
the
Mounted on a monobloc basement to support the frame, while also containing liquids such as lubricants, hydraulic oils, and coolants, the T10-VT tapping machine has been designed with the operator in mind, as well as to keep the workspace clean and minimise environmental impact. All adjustments are positioned at operator height – from the part feeding system to the operational area and the finished part exit –helping to ensure ease of use and maximising comfort. In addition, the T10-VT is equipped with a soundproof enclosure to ensure a safer and quieter work environment for operators.
www.sacmagroup.com
Adding to its extensive portfolio, Italian manufacturer FAR Srl will be showcasing two new products at Fastener Fair Global – the ALV-IN blind rivet for reliable fastening in difficult to reach areas, as well as the ICT rivet nut for fastening thin sheet metal and soft or fragile materials – including plastics, resins and composites.
Specially designed with reduced dimensions, the ALV-IN rivet is ideal for honeycomb and sandwich panel applications – removing the need for a pre-drilled through hole. An aluminium body also helps to protect soft or fragile materials, including plastics, composite materials, wood or aluminium during use. FAR states the new rivet also ensures a larger contact surface area in comparison to others on the market, further enhancing its reliability.
In addition to standard sizes, the ALV-IN rivet can be customised to specific requirements and can be installed with FAR’s standard range of riveting tools.
Designed with a special geometry, FAR points out that its second innovation, the ICT rivet nut, enables up to 570% more contact than a standard insert of the same size and increases tear resistance significantly. The ICT also exhibits minimal radial stresses during installation, thus eliminating the risk of deformation of the application hole. The special design of the rivet nut makes it an ideal solution for numerous applications and materials.
25 - 27 March 2025 - Stand:1-774
Messe Stuttgart, Germany
www.sacmagroup.com
Our All-In-One Combined Headers and Threaders: Drastically Improving Your Sustainability.
All In One = Optimum Footprint
Energy savings : The installed power required for multiple processes involved in producing screws and bolts such as header, pointer, washing machine, roller, and conveyors exceeds double the power needed by the Sacma combined header, which can perform all these operations in a single machine.
Floor space savings : The All In One solution reduces the required production space by up to 75%, compared to traditional lines that use multiple machines for the same operations.
Clean Factory : By consolidating processes from wire to finished product within a single, sealed machine, we create a simpler and more efficient production system resulting in a cleaner factory environment.
WIP reduction : The need for work-in-progress (WIP) blanks between operations is eliminated, and the removal of inter-process washing further improves the environmental footprint by reducing waste and energy consumption.
Employees care : Health and safety are significantly enhanced by using just one machine. With all operations contained within a single footprint, employees are spared unnecessary travel between multiple machines, reducing exposure to potential risks.
Sustainable supplier : Sacma is one of the most sustainable manufacturers of forming machines in the world having the production of components integrated in its factories ? Come to visit us !
Offering a solution that combines innovation, precision and adaptability in automatic inspection systems, Dimac’s new proprietary Artificial Intelligence (AI) software is redefining fastener quality control.
With the AI software, Dimac Srl enables fastener manufacturers to achieve unprecedented levels of defect detection and classification. Unlike traditional vision systems that rely on pre-set rules, Dimac’s AI software uses neural networks and advanced algorithms to analyse vast datasets of defective and non-defective fasteners.
Through this process, the software ‘learns’ to identify even subtle defects, such as surface irregularities or dimensional anomalies, that may not be apparent through standard inspection techniques. By generating new defect images based on similarity criteria, the system continuously refines its detection capabilities, enabling manufacturers to stay ‘one step ahead’ of evolving quality standards.
A key innovation is the software’s ability to autonomously generate search parameters, enabling it to adapt dynamically to different fastener types and production variables. This flexibility not only enhances detection accuracy but also reduces set-up time, making the software ideal for high-mix, high volume manufacturing environments.
Dimac’s AI software has been successfully integrated into flagship systems including the MCV6 and SPC 360°, where it drives 360° profile analysis and robotic sampling efficiently.
“With its proven ability to push the boundaries of what is possible in automated control and inspection, this software represents not just an advancement, but a new benchmark in industrial innovation,” highlights Dimac.
MKT Metall-Kunststoff-Technik GmbH & Co KG states its new BZ3 dynamic mechanical expansion anchor offers an efficient alternative to injection and undercutting systems in fatigue applications, as well as being one of the first mechanical expansion anchors with an ETA certification (ETA – 20/0017) for fatigue loading.
Available in sizes M10 to M16, the BZ3 dynamic is quick and easy to install and offers very shallow embedment depths, requiring only small concrete thicknesses to anchor into, with the product also capable of installation with small anchor spacings and edge distances. When using a hollow drill bit, no further cleaning of the borehole is required and the exposure of the installer to dust is reduced to a minimum.
BZ3 dynamic can also be pre-set or conveniently installed through the attachment, with a red colour marking, making it easy to visually check the required anchorage depth. This anchor can be immediately loaded after torquing and
is ready to withstand fatigue loads after the mortar, which is injected through the filling washer to close the annular gap between the attachment and the anchor, is hardened. Also suitable for fastening light to medium fatigue loads in cracked and uncracked concrete, the BZ3 anchor is ‘Made in Germany’ under high social and environmental standards, making it a sustainably manufactured
BZ3 dynamic is assessed according to the European Assessment Document (EAD) 330250, the qualification standard for anchors in fatigue applications. Its ETA certification also covers loading for seismic performance categories C1 and C2 and for fire exposure (R30 - R120).
www.mkt.de
Discover our steel construction bolts
HV (EN 14399-4) delivered as set: bolts + nuts + washer in 1 box
HR (EN 14399-3) delivered as assembly in 1 box
SB (EN 15048) in zinc plated and hot-dip galvanised (iso-fit)
TÜV Rheinland certified
As Growermetal prepares to celebrate its 75 th anniversary, the Italian manufacturer of safety washers and fastening solutions is bringing its innovation and research to new levels in 2025 – with the launch of a brand new innovation at Fastener Fair Global.
Details are being held under wraps for now, but the manufacturer is promising a new, innovative product designed to deliver cutting edge solutions and is inviting customers and partners to find out more on its stand.
“Fastener Fair Global serves as a hub for businesses to explore the latest technologies, exchange knowledge and foster collaborations in many industry sectors. Being aware of the market evolution is an essential part in enhancing our services and Fastener Fair Global is the perfect stage to achieve this purpose,” highlights Paolo Cattaneo, CEO at Growermetal.
For decades, Growermetal has been at the forefront of innovation in fastening technologies, building its reputation on delivering safety washers that meet the most complex needs and 2025 is no exception. After the launch of Grower OhmLock® in October 2024, the Italian manufacturer is now presenting a new exclusive design in the Route to Fastener Innovation competition.
“This is our third participation in the competition,” underlines Paolo. “In 2019 we were awarded third place for the Grower TenKeep® safety washer, followed in 2023 with second place for the Grower SpheraTech® preassembled set. Both were great recognition for the excellent work of our R&D team, and we hope our new product will gain positive feedback too.”
During Fastener Fair Global visitors will be able to connect with the Growermetal team, where the company’s full portfolio of fastening solutions will be on display. From the aerospace and automotive industries to renewable energy, electronics, and railway sectors, customers will explore how Growermetal’s expertise and technological advancements can enhance efficiency and reliability in every application.
www.growermetal.com
With an all new design, WAFIOS Umformtechnik states its HN 4-80 machine is a modern, application oriented, simple and robust machine for nail production, featuring an encapsulated work area to separate and collect tip scrap.
While traditional nail machines discharge tip scrap – small metal fragments which have a tendency to accumulate during the process of cutting the nail tips –alongside the finished nails, a process which then requires a separate cleaning step to remove the scrap and other impurities from the end product, the HN 4-80 separates tip scrap from the nails at the part drop out area, collecting the waste material in a separate container.
This newly designed, fully sealed work area, equipped with the knife and press carriages running in sealed round guides, also provides oil free operation. “Both nails and scrap are discharged without oil, eliminating the need for nail washing – therefore increasing productivity while allowing for cost savings, as the oil free scrap can be resold as clean metal waste. This also helps to reduce the cutting carriage of parts, which enables more accurate nail tips and longer tool life,” explains WAFIOS Umformtechnik.
as being compatible with existing tools from older machines – without modification. The new machine also uses similar operating concepts to enable operators to quickly adapt to the new system.
Capable of processing wire diameters from 1.8mm – 4mm into pin lengths ranging from 13mm – 80mm, WAFIOS highlights the HN 4-80 exceeds the working range of established models on the market, as well
“By reducing waste and improving efficiency, the HN 4-80 contributes significantly to the sustainability efforts of nail manufacturers, supporting a cleaner and more cost-effective production process,” concludes WAFIOS Umformtechnik.
Specifically designed to lock in the recess when driving, and to help avoid cam-out, the new patent pending BIT-LOK™ drive system from Phillips Screw Company requires no force to keep the bit in the recess.
One problem has plagued the fastener installation process since their invention – cam-out. Cam-out happens when the driver bit slips out of the recess during driving or the removal operation. Typically, this happens when the torque is high and the resulting damage can be extreme. In some cases, the recess will become too damaged to drive or remove the screw. The driver bit might also accidentally strike and damage the materials that are being fastened – with repairs time consuming and costly.
formed into
Phillips Screw Company has developed a new patent pending technology that locks the bit into the recess when driving or removing. A shelf is forged on each wing of the driver bit and, when inserted into the recess and torque is applied, the shelf lodges under an overhang that has been formed on each drive wall of the recess effectively locking the bit to the screw. Initially this has been demonstrated on a woodscrew using a three winged drive system, however Philips highlights that it intends to deploy the drive system in other designs.
In driving applications, once the fastening has begun, there is no force required to keep the bit in the recess, as the design pulls the drive
along with the screw, minimising the risk of cam-out. In addition, another added benefit of the new system is the ability to drive in tight areas or overhead where it is difficult to push on the driver. This reduced effort for the installer helps to reduce fatigue and injury.
www.phillips-screw.com
www.bbafasteners.com/bctfp
Würth Industrie Service GmbH & Co KG, in collaboration with W Gessmann GmbH, has combined the GESSbot Gb350, an Autonomous Mobile Robot (AMR), with the ORSY ®mat vending machine to provide a mobile vending machine capable of transporting materials in the warehouse – directly to specific workstations.
Würth states this special solution aims to optimise decentralised material dispensing, reduce the workload on employees and at the same time increase efficiency, flexibility and safety. Special sensors in the GESSbot Gb350 map the surroundings, with the AMR capable of following defined routes to workstations and charging stations. If the robot encounters an obstacle, it makes itself noticeable and drives around the blockage.
In combination with the digital iDISPLAY, and Würth Industrie Service’s own software solution, the mobile GESSbot equipped with the ORSY ®mat can be navigated easily. Each workstation can be equipped with an iDISPLAY that shows the pre-programmed routes that employees can request at any time. Once the goods have been removed at the desired workplace, the GESSbot returns the vending machine to the central magazine, where it can be refilled and be readily available for the next user.
With a possible load capacity of 350kg, the GESSbot can be combined with different ORSY ®mat models to better suit each individual warehouse. It can also reach a maximum speed of 4.3km/h on a maximum gradient of 5% – this is equivalent to half a walking speed. Power can be easily supplied to the robot, which finds its own way to the charging station in a timely manner, docks and charges automatically.
Würth highlights: “With the ORSY ®mat, customers can benefit from organised stocking, automatic replenishment, as well as transparent inventory control.”
www.wuerth-industrie.com
Developed as an alternative for contractors taking 20kg coils of stainless banding and clips to site, where they would then spend time cutting banding to length and adding a clip before insulation could be installed, Easi-Bands from GOEBEL UK aim to save labour time and eliminate this time-consuming process, whilst also enhancing safety for contractors.
Cutting bands on-site with sheers also produces sharp edges, making cuts to fingers and hands very common for contractors. Easi-Bands are manufactured using an edge dress band with a rounded end and a clip installed with rounded tabs, making them more ergonomic and userfriendly, reducing the risk of injury to those installing them.
Not only reducing risk of injury to those fitting the bands, the Easi-Bands also feature low profile and smoothed edges with rounded tabs helping to eliminate risk of injury to those maintaining surfaces through cleaning in areas such as food processing and production factories.
Easi-Bands are used to fix insulation cladding in place, both on external in internal applications, and are made from a 304 grade stainless steel with a bright annealed finish to stand the test of time under all conditions.
The main advantages of using Easi-Bands is that they are cut to the required length with a clip welded in place, therefore saving labour time and costs on-site, as they are ready for installation, as well as reducing the amount of waste. The bright annealed finish with a low profile clip also makes them a more aesthetically pleasing finish for applications that are visible for years to come.
The Structus column-splice system from Eurotec offers an innovative solution for the construction of multi-storey buildings using Cross-Laminated Timber (CLT), providing seamless connections between columns across multiple floors, as well as facilitating the creation of point supported floor systems –thus improving the efficiency and stability of timber construction.
quipped with a tube in tube system, Structus’ design combines an inner core with an outer jacket tube – ensuring the inner core achieves its maximum yielding capacity without buckling under compressive forces, while the outer tube provides critical support – increasing the overall stability of the joint. Designed to EC5 standards, Structus is engineered for strength, precision and efficiency.
Another feature of the tube in tube system is its simplicity and precision during installation. The system is self-locking, enabling timber columns to be installed on-site with speed and accuracy, helping to reduce construction time while guaranteeing high and reliable structural performance.
Structus can also support both post and slab as well as post and beam timber framing systems. Its
primary function is to provide a continuous vertical load path between successive timber columns, ensuring that loads are efficiently transferred through the building structure.
To achieve this the connector uses fully threaded screws for the steel-to-wood connections. Recognising that wood fibres are weakest along the end grain, Structus uses a unique approach – screws are inserted at a 30° angle into angled, pre-drilled holes in the steel plates, which are machined using advanced CNC technology. This method significantly increases shear and tensile strength, thus safeguarding the stability and longevity of the joint.
Eurotec GmbH states: “While similar systems exist, Structus is distinguished by its sophisticated operating principles. The combination of the tube in tube core stability and the angled screw applications on the column faces, without any adapters or angular washers, represent a leap forward from traditional 90° end-grain screw methods, which are less efficient and limit overall strength.”
Ideal for outdoor or overhead working areas, as well as jobs where speed, reliability and power are required, the new BT-18N battery operated riveting tool for blind rivet nuts is suitable for a wide range of applications.
With a pulling force of 18,000N, and a capacity to set nuts from M3 to M10, the BT-18N riveter from BRALO S.A features great speed, high durability and reliability, as well as easy maintenance, with a brushless motor and 18V lithium ion battery. Easily programmable and easy to maintain, the BT-18N also comes equipped with easily interchangeable M3 to M10 nosepieces and mandrels.
To enable suitability for a wide range of applications, BT-18N can be adjusted under two parameters. The first, stroke regulation or ‘S’ mode, offers 10 programmable memories for stroke regulation. When working in ‘S’ mode, the riveting machine uses its full pull force, but limits its stroke to the programmed stroke, making it an ideal working mode for in-line production of an application that remains unchanged, for example when the same nut will be riveted on the same material with the same thickness. This not only allows flexibility in the application, but also ensures the rivet nut is optimally positioned every time.
The second parameter is pull force regulation or ‘P’ mode, which also features 10 memories for its regulation. When working in ‘P’ mode, the amount of force used by the tool to rivet the nut is regulated – ideal when the same model of nut is used, but the thickness of the base material is not always the same. Working in this mode, the BT-18N uses a quality control system of the riveting process and warns with an acoustic signal if the nut has not been riveted properly, either by incorrect adjustment, or because the nut is not correctly supported on the base material.
In addition, BT-18N features automatic threading and unscrewing, as well as an auto unscrewing button to avoid jamming. The tool also has a counter that shows the number of nuts placed, which can be reset to zero when the user needs to restart the count.
High-tech professionals gathered at the 23rd edition of the Precision Fair taking place from 13th – 14th November 2024 at the Brabanthallen, ‘s-Hertogenbosch, the Netherlands, to exchange knowledge about high and ultra precision technology.
In addition to a wide range of networking opportunities, knowledge sharing took centre stage in the conference programme, featuring insights into major European projects including the Einstein Telescope and discussions on the latest challenges and developments in high and ultra precision technology.
Over 6,100 professionals met, networked, and exchanged ideas, with over 375 exhibitors showcasing their latest innovations and presenting a wide range of high-tech solutions in precision mechanics, metrology, optics, mechatronic engineering, precision manufacturing, machining and tools, as well as vacuum and cleanroom technology.
“This year, more than ever, we see the entire precision technology value chain seeking new connections, knowledge sharing and joint innovation. Interest from abroad is significant and we are proud to have welcomed a record number of international delegations,” said Bart Kooijmans, programme manager at Mikrocentrum, organisers of the Precision Fair.
During the 2024 Precision Fair several top student teams were showcased on the exhibition floor, and in the pitch programme, to inspire and motivate the next generation. Among the international delegations were the short-pulse laser association from Lithuania with four companies and the Irish Precision Tooling & Machining Association, which attended with twelve companies. Delegations also came from Germany, Spain, Italy, and Canada, including the Canadian
Photonics Association and the Swiss Precision Cluster. The large international participation underscores the growing importance of collaboration within the global precision technology sector.
The next edition of the Precision Fair will be held on 12 th – 13 th November 2025 at the Brabanthallen.
International Hardware Fair Italy returns in 2025 with a packed programme of events focusing on important issues and the most interesting opportunities in the Italian and European hardware market.
Taking place from 8 th – 9 th May 2025, more than 250 exhibitors have already confirmed their participation in Bergamo for two days of conferences and matchmaking. Alice Brambilla, project manager for International Hardware Fair Italy, comments: “The participation of major Italian and international companies confirms that the event responds to a need for profitable in-person networking, in a streamlined two day format packed with initiatives and proposals for the market. The next edition will interpret crucial issues in the industry, offering a broad overview of possible solutions.”
The International Hardware Fair Italy will have a comprehensive programme for buyers from all over Europe, as well as an outdoor area for exhibiting tools and machinery. Key themes for the 2025 fair include service, the evolution of formats and sustainability.
“While home improvement, like all industries, has felt the effects of the digital and climate transition, it still continues to be a sector of great interest for the development of retail chains, eCommerce projects and diversification of products and proposals. In this context, the International Hardware Fair Italy committee is working on the completion of a conference programme offering plenty of food for thought and in-depth analysis to guide its strategies and promote its growth,” concludes organisers.
Setting a record for attendance since the Covid-19 pandemic, more than 150 commodity and speciality tape professionals attended the 67 th Afera Annual Conference themed ‘Taping Our Future’ in Thessaloniki, Greece.
Afera, the European Adhesive Tape Association, welcomed tape professionals from 15 countries across Europe, Asia and the USA. The three day programme featured 15 seminars and three expert panel discussions – offering a unique, transformative journey into the world of commodity and speciality tapes.
Three separately themed working sessions focused on market data and trends, regulatory affairs and sustainability, as well as current tape applications and technology highlights. The Conference Working Programme was preceded by Afera’s biannual committee and flagship sustainability project (AFSP) meetings.
“You are the key players, inquisitive minds, influencers and innovative leaders from the adhesive tape industry,” commented Evert Smit, Afera president. “This event is more than just networking and knowledge sharing. It’s about co-creating, transparency, changing mindsets and meeting the new generation and ultimately making our technologies and businesses future proof.”
During the conference, Afera also launched its new collaborative tool for calculation of the product carbon footprint (PCF) of adhesives and adhesive tapes, called TACK, which the industry collective developed with the German Adhesives Association (IVK) and sustainability consultant Sphera. The launch coincides with Afera’s official commitment to ensuring that PCFs of adhesive tape products are calculated in an aligned manner and with little effort to meet future legal requirements and requests from the supply chain.
Afera’s 68 th Annual Conference will be held on 22 nd – 26th September 2025 at the Hyatt Regency in Thessaloniki, Greece.
From 22nd – 24th October, the 20th international FastTec exhibition of fastening products took place at the Crocus Expo IEC in Moscow, Russia, which was attended by 1,025 professionals across the fastener industry.
Visitors included heads of procurement and supply departments from industrial enterprises and construction companies, wholesale buyers of fastening products, representatives of companies specialising in installation work, as well as sole proprietors.
More than 40 manufacturers and suppliers from Russia, Belarus and China showcased a wide range of fastening products, including construction and industrial fasteners, plumbing and heating fasteners, electrical wiring and installation fasteners, plastic fasteners, automotive fasteners, and furniture fasteners and hardware, as well as consumables.
“There were a lot of visitors at the show, with people approaching and asking questions. We also used the show as a chance to look for new partners which was successful – having signed an agreement with a company ready to test our products,” commented Pavel Bordovsky, production manager at exhibiting company Hort Tade –a supplier of industrial fittings, that presented new products at the show, including fittings for built-in sliding door handles, lock handles for fire resistant cabinets, clamping locks and latches, as well as conveyor accessories.
Russian company Strike also presented its next generation power clamp with an increased clamping force. Alexander Mosalov, CEO, highlighted: “This year at FastTec there were many engineers and designers from the military industrial complex. Our product was well received because it performs excellently in aggressive environments and so we expect to attract significantly more potential clients this year.”
The next FastTec exhibition will take place from 21st – 23 rd October 2025 at Crocus Expo IEC.
SCHNORR® is an international leader in engineering and producing safet y washers and disc springs for automotive, aerospace and mechanical applications
Original SCHNORR® safet y washers:
• Highly vibration-resistant
• Twofold effect from one component
• E x tensive range
Original SCHNORR® disc springs:
• Various applications
• Best price -per formance ratio
• Customized solutions
Please contac t us Together we will find your tailor-made solution.
Schnorr GmbH
Stuttgar ter Str. 37 71069 Sindelfingen, Germany
Phone: +49 (0) 7031 302-0
Fax: +49 (0) 7031 382600
mail@schnorr.de
www.schnorr.de
| #1750
Stuttgart, Germany
25 Mar – 27 Mar 2025
www.fastenerfairglobal.com
The international exhibition for the fastener and fixing industry.
BAU
Munich, Germany
13 Jan – 17 Jan 2025
www.bau-muenchen.com
Trade fair for architecture, materials and systems.
BouwBeurs
Utrecht, Netherlands
3 Feb – 7 Feb 2025
www.bouwbeurs.nl
Trade fair dedicated to the Dutch construction industry.
Southern Manufacturing & Electronics
Farnborough, UK
4 Feb – 6 Feb 2025
www.southern-manufacturing-electronics.com
Industrial exhibition for new technology in machinery, production equipement, as well as tooling and components.
Expo Manufactura
Mexico City, Mexico
11 Feb – 13 Feb 2025
www.expomanufactura.com.mx
International trade fair for manufacturing technology, automation and robotics.
BUDMA - International Construction Fair
Poznań, Poland
11 Feb – 14 Feb 2025
www.budma.pl
The meeting place for manufacturers and distributors in the construction industry.
The Smarter E India
Gujarat, India
12 Feb – 14 Feb 2025
www.thesmartere.in
India’s hub for future energy solutions and technologies.
Schraubtec Stuttgart
Stuttgart, Germany
19 Feb 2025
www.schraubtec.com/stuttgart
The regional trade fair for screw connections.
Asia-Pacific Sourcing
Köln, Germany
11 Mar – 13 Mar 2025
www.asia-pacificsourcing.de
European platform for import and export between the West and Asia.
National Hardware Show
Las Vegas, USA
18 Mar – 20 Mar 2025
www.nationalhardwareshow.com
Connects retailers, dealers, wholesalers, distributors and manufacturers to the marketplace.
BYGGERI
Fredericia, Denmark
18 Mar – 21 Mar 2025
www.byggerimessen.dk
Scandinavia’s trade fair for construction products.
MosBuild
Moscow, Russia
1 Apr – 4 Apr 2025
www.mosbuild.com
Russia’s largest building and finishing materials trade show.
Stainless 2025
Brno, Czech Republic
2 Apr – 3 Apr 2025
www.stainless2025.com
The international trade fair dedicated to stainless steel.
By Barbara Sorgato, secretary general, European Consortium of Anchor Producers
The final text of the new Construction Product Regulation (CPR) is supposed to be published any time now. In the meantime, the European Commission has published an explanatory page on the most important changes of the EOTA route under the new CPR.
Simply put, the procedure for requesting ETAs and adopting EADs is now more streamlined, enhancing coordination between EOTA and the European Commission – with a clearer relationship between harmonised standards and ETAs. I find it a very clear page and believe that the information given will be of great use to those using the EOTA route. Here I report its contents in a broad outline:
1. A manufacturer requests a European Technical Assessment (ETA) for a construction product that is not covered by a harmonised standard. A manufacturer can ask for an ETA for additional characteristics not covered by a product’s harmonised standard.
2. The request is made to a Technical Assessment Body (TAB) for the relevant product area; the list of TABs is given in the New Approach Notified and Designated Organisations (NANDO) database[1]
3. The TAB issues the ETA based on a European Assessment Document (EAD) adopted by the European Organisation for Technical Assessment (EOTA).
4. The main content of the ETA is information on the intended use and performance of a product. The ETA has no expiring date.
5. The European Commission publishes an updated list of references for the final EADs in the Official Journal of the European Union (OJEU). ETAs can be issued prior to the publication of the relevant EADs in the OJEU.
EAD cited under the current CPR ETA based on EAD remain valid
End of validity of EADs from
The first is that not only a single manufacturer, but also a group of manufacturers or an association (but each manufacturer receives an individual ETA upon request) or the Commission itself can request a European Technical Assessment (ETA) for a construction product that: Is neither covered by a harmonised standard nor by a harmonised standard that is in the pipeline (to be delivered in a period shorter than one year).
Has a declared use outside the intended use of the harmonised standard. Has a material that differs from those of the harmonised standard. Needs dedicated assessment methods because the ones given in the harmonised standard are unsuitable for the product.
ETAs also cannot be issued anymore for characteristics not covered by a product standard; they will need to be included in the next revision of the harmonised standard.
The next change is that the request is made to a TAB for the relevant product area. The chosen TAB will check all conditions given above and will inform the manufacturer if the ETA request can or cannot be processed.
The TAB then drafts an EAD, which is adopted by EOTA and submitted to the European Commission for greenlight and publication in the OJEU. An ETA can only be issued if the corresponding EAD has been cited in the OJEU.
Another key change is that the main content of the ETA is no longer just information on the intended use and performance of a product. New EADs must include all essential characteristics related to environmental sustainability (LCA = lifecycle assessment indicators according to EN 15804), with ETAs declaring these characteristics in the following stages: Global Warming Potential (GWP) upon EAD citation.
The core list of LCA-EPD indicators by 2029 (four years after the date of application of the new CPR).
The full list of LCA-EPD indicators by 2031 (six years after the date of application of the new CPR).
There are also specific validity and expiration periods for ETAs and EADs:
EADs are valid for ten years.
EOTA can request a ten year extension from the European Commission in the final year before expiration.
ETAs can be used for five years after an EAD expires.
EADs are withdrawn from the OJEU from the moment a harmonised standard covering the same product is published in the OJEU; the
EAD under the new CPR
End of validity of ETAs from current CPR
Another key change is that the main content of the ETA is no longer just information on the intended use and performance of a product.”
related EAD is withdrawn from the OJEU and the ETA cannot be used anymore as a basis for the CE Marking (but it can be used as technical documentation).
As well as harmonised standards, ETAs will benefit from new market instruments under the CPR, including CE Marking with data carriers; Declarations of Performance and Conformity (DoPC); general product information, instructions for use and safety information; as well as digital product passport (DPP), when implemented.
EADs cited under the outgoing CPR can be used for issuing ETAs until 2030 (five years after the date of application of the new CPR). The related ETAs can be used for CE Marking products until 2035 (ten years after the date of applications of the new CPR), provided the product and intended use are not covered by a harmonised standard. Once a new harmonised standard is applied, it becomes the only way to market a product and the EAD and related ETAs can no longer be used for CE Marking.
Below is the explanatory table given by the European Commission: The text of the European Commission website and the above table are available under this link: https://single-market-economy.ec.europa.eu/sectors/construction/ construction-products-regulation-cpr/voluntary-ce-marking-eota-route_en
References:
[1] https://webgate.ec.europa.eu/single-market-compliance-space/ notified-bodies
By Thomas Bruun, president of the European Organisation for Technical Assessment (EOTA)
In the European construction sector, fixings including screws, bolts, and anchors, are essential for ensuring the stability and safety of buildings – contributing to their structural integrity and infrastructure projects. As the industry moves into a new regulatory framework, under the Construction Product Regulation (CPR), fixings manufacturers face both new challenges and opportunities.
Akey aspect of this transformation is the European Technical Assessment (ETA) route, which remains central to the industry’s ability to access the EU market. With the CPR set to be fully applicable in January 2026, this article examines the CPR’s potential implications for the fixing industry and explores how the ETA route can be harnessed to help manufacturers address future challenges.
The European construction industry is one of the largest economic sectors in the EU, accounting for around 9% of the EU’s Gross Domestic Product (GDP) and providing jobs to millions of people. The sector is characterised by a high number of small and medium-sized enterprises (SMEs) making up over 90% of the construction companies. As the industry evolves, so does the need for innovative solutions.
In this context, construction fixings play a critical role across various construction sectors, whether residential, commercial or infrastructural. Like no other industry, the fixings sector is characterised by constant, incremental innovation. This is one of the main reasons why the fastening industry relies on the ETA route for CE Marking and marketing of their products on the EU single market, and globally.
New market needs drive the development of new European Assessment Documents (EADs), the foundations for an ETA. The ETA, issued by a qualified Technical Assessment Body (TAB), enables manufacturers to respond quickly to customer needs, regulatory changes or project specific requirements.
The ETA route has been a stepping stone for the success of the fixing industry for more than 35 years. Since the 1990s, EOTA, the organisation that unites all TABs across the EU, has been developing specifications for fastening products. Mechanical fixings were the first construction
EADs registered – PAC 33
ETAs issued – PAC 33
EADs registered and ETAs issued for fixing products (PAC 33)
The ETA route has been a stepping stone for the success of the fixings industry for more than 35 years.”
Evolvement of ETAs – all product area codes (PACs)
products to have CE Marking in the EU, undergoing innovations in materials and design constantly over time.
Today, high performance materials such as stainless steel, carbon steel, and alloy combinations, play a crucial role in anchor design. These materials provide corrosion resistance, strength, and longevity, particularly in challenging environmental conditions. Recent design innovations have focused on the development of specialised fixings that address seismic resistance, fire safety and thermal insulation.
Since 2013, EOTA has registered 180 EAD development projects for fixings, which were consolidated into 98 EADs available to the industry. With nearly 5,000 ETAs for fixing products issued to date, the ETA route has provided a respected benchmark for evaluating fixings’ performance worldwide. This robust framework has helped ensure that construction fixings meet safety, reliability and performance criteria in diverse building applications.
The new CPR, which will become fully applicable in January 2026, introduces several important updates that will affect the fixings industry. While the change in the legal framework poses challenges, it also opens the door to significant opportunities for the fixings industry.
The regulatory landscape in Europe is intricate, and construction fixings must comply with diverse building regulations. Ensuring that fixings meet the legal requirements of any relevant European country can be costly and time-consuming. An ETA offers a responsive and agile solution to this challenge.
Under the new CPR, the ETA route remains the central tool for fixings manufacturers seeking to gain access to the ‘single market’. On the positive side, the revised regulation offers new opportunities for cooperation between manufacturers, making it possible for business associations or groups of manufacturers to work together on an EAD, thereby tapping into synergy effects. Additionally, the European Commission can request the development of a new EAD if a general market need is detected.
Regarding transitional rules, EADs cited under the current regulation will usually remain valid for five years, until January 2031. ETAs issued on their basis can be used as a basis for CE Marking for another 5 years, for instance until January 2036. The European Commission has published a detailed overview of the transitional rules and relevant changes to Voluntary CE Marking (EOTA route) on its website[1]
EOTA is currently working with the European Commission to complete the citation of numerous EADs in the Official Journal to make sure the industry can benefit from a broad range of existing EADs during the phasing-in of the new regulation.
While the transition timeline for the ETA route remains extremely ambitious, it gives stakeholders an opportunity to be at the forefront of the new developments the revised CPR will bring; namely
While the changes in the CPR are focused on the EU, there is a growing opportunity for the ETA route to have global reach.”
enhanced sustainability, machine readable EAD formats to integrate with Building Information Modelling (BIM) and Digital Product Passports – ensuring easier access to product data throughout the construction lifecycle.
EADs for mechanical fixings: This includes bolts, screws and anchors. Mechanical fixings are commonly used in steel and concrete applications where a strong, reliable connection is essential.
330232-01-0601 (and related variants)
Mechanical fasteners for use in concrete.
330250-00-0601 Post-installed fasteners in concrete under fatigue cyclic loading.
330924-01-0601 Cast-in anchor bolts.
332001-00-0602
Clamping system for connection of precast concrete members.
EADs for chemical fixings: Typically involving adhesives and resin-based anchors, these fixings are used when mechanical fasteners alone cannot provide the required strength or are unsuitable due to aesthetic reasons.
330076-00-0604
330087-01-0601
330499-02-0602
332402-00-0601
Metal injection anchors for use in masonry.
Systems for post-installed rebar connections with mortar.
Bonded fasteners and bonded expansion fasteners for use in concrete.
Post-installed reinforcing bar (rebar) connections with improved bond-splitting behaviour.
EADs for speciality fixings: For special applications, fixings such as expansion anchors, masonry anchors, and cavity fixings, are used to address specific requirements.
330083-03-0601
330196-00-0604
330965-01-0601
331433-00-0601
Powder-actuated fasteners in concrete for redundant non-structural applications.
Plastic anchors for fixings of ETICS with rendering.
Powder-actuated fasteners for the fixing of ETICS in concrete.
Injected anchors for thermal insulation boards.
The shift towards digitalisation in the construction industry is another key challenge for the fixings sector. With the mandatory
use of machine readable formats for EADs under the new CPR, manufacturers must adapt to digital formats that support BIM and Digital Product Passports. While this transition requires investment in new technologies and data management systems, it also offers the opportunity to streamline the flow of information across the supply chain, improving efficiency and reducing material waste.
EOTA and the fixings industry are closely following the discussions on formats and software to be used and should be able to be among the early adopter when it comes to implementing these new approaches.
With the European Union pushing for greener construction practices under the European Green Deal, sustainability has become a central theme in the European construction industry and the fixings sector is no exception.
While the cost and effort of transitioning to green fixings, such as those made of recyclable materials or produced using low carbon processes, is a challenge, the introduction of sustainability requirements in the ETA route is certain to drive innovation.
The EU’s circular economy agenda also encourages the development of products that are durable, recyclable and easy to disassemble. For fixings manufacturers, this is an opportunity to innovate and become global leaders in the production of sustainable, environmentally responsible solutions.
One of the core priorities for EOTA and the fixings industry is to embed sustainability requirements in the relevant EADs. EOTA and the fixings industry are looking into c-PCRs (complementary Product Category Rules) which will enable linking fixing products into the general Life Cycle Assessment framework used in the EU construction sector.
While the changes in the CPR are focused on the EU, there is a growing opportunity for the ETA route to have global reach. The robustness of the EU legal framework has made it attractive to international markets, and 5% to 7% of ETA requests now come from outside the EU. European fixings manufacturers can expand their market reach by complying with high EU quality benchmarks and positioning their products as internationally recognised and reliable.
The new CPR presents both challenges and opportunities for the fixings industry. While the tight transitional timeline, sustainability and digitalisation will require rapid adaptation, they also provide avenues for innovation, growth and differentiation in a competitive global market. The fixings sector, which has long been known for its resilience and ability to innovate, must now focus on producing more sustainable, digitally integrated products that meet the evolving demands of the construction industry.
The ETA route, as a vital tool for achieving CE Marking and market access, will continue to be a cornerstone for manufacturers navigating these changes. By harnessing its ability to provide custom-made, flexible solutions, the fixings industry can not only stay ahead of regulatory demands, but also contribute to the EU’s broader goals of sustainability and digitalisation in construction, putting it in a good position for global success.
www.eota.eu
References:
[1] https://single-market-economy.ec.europa.eu/sectors/construction/ construction-products-regulation-cpr/voluntary-ce-marking-eota-route_ en#:~:text=The%20outgoing%20and%20the%20new,European%20 technical%20assessment%20(ETA)
In addition to traditional solutions, the portfolio of the Klimas brand features a number of chemical anchors – including the Mount Everest epoxy anchor and Makalu universal chemical anchor. These products provide professionals with even greater strength, a wider range of applications and an extended service life.
Chemical anchors work well wherever the safety of the connection is important. A chemical anchor consists of a threaded rod and a two component injection anchors. During installation, the cleaned hole is partially filled with resin before the anchor rod is applied. The anchor’s ability to bond to the irregular shape of the drilled hole means that they are very effective at transferring loads along the entire length of the joint, using bond forces.
Among the advantages of chemical anchors is that they can be used in various types of substrates, both in cracked and non-cracked concrete, as well as for installation in brick masonry, hollow blocks, silicate blocks and autoclaved concrete. Bonding threaded rods and rebar into the concrete of an existing structure is used not only during the construction of new buildings, but also in the reconstruction, strengthening and reinforcement of structures.
One of the most advanced formulations in the Klimas brand portfolio is the Mount Everest epoxy anchor. Thanks to its properties, it is suitable for use in demanding environments such as the construction of buildings and engineering structures, including tunnels and bridges. This is because with its help, it is possible to make connections in static, quasi-static, as well as seismic loaded structural elements in a concrete base.
“The developed formula of the Mount Everest chemical anchor is designed to provide professional contractors with maximum strength and durability,” underlines Wiktor Paradny, global product manager at Klimas Wkręt-Met. “These properties become particularly important in civil engineering construction, where the required lifetime of an object is 100 years. The durability of our Mount Everest chemical anchors has been confirmed by all tests carried out in accordance with current EAD standards.”
Wiktor comments: “The Makalu chemical anchor is a versatile solution that stands out with three separate ETA certifications. It is the second item in our portfolio with a service life of up to 100 years in concrete base material and is the most frequently selected anchor by our partners.”
Hall 1, Stand
“As a supplier of fastening techniques for the construction industry, we are mindful of our environmental impact,” explains Wiktor. “That’s why Klimas develops products to meet the highest standards when it comes to their durability, but at the same time meet all the requirements for environmentalism.”
Klimas’ wide portfolio also includes the Makalu universal chemical anchor for extreme applications. It is ideal for concrete substrates in the cracked and non-cracked zone, post installed rebar connections, or for use in ceramic, silicate and autoclaved concrete masonry. The chemical anchor is also suitable for use in the installation of substructures of ventilated façades or consoles of curtain walls façades and can be used to reinforce multilayer walls or fixing HVAC installations. Makalu can also be used for fixing heavy steel elements to the concrete base material, balcony railings, machine and equipment pedestals, structural beams, as well as wooden structures.
As part of that commitment, Klimas chemical anchors can be used in buildings with LEED (Leadership in Energy and Environmental Design) certification. This is a holistic green building certification system that does not focus on a single element of a facility, such as energy, water or health, but takes a holistic view of the subject so the elements and systems working together create the best possible building.
Anchors are specialised products, so their use requires a design based on accurate load calculations. Klimas, in addition to a top quality certified product, provides full technical support and dedicated tools for anchorage calculations, in the form of its DesignFiX software.
“The task of the software is to provide maximum support to designers, engineers, and contractors, when designing fastenings according to the requirements of the project. The software is based on an intuitive interface, which enables users to easily enter all data directly on the 3D drawing. The software selects the optimal anchorage depth saving the investor’s money and the contactor’s time needed for installation,” adds Wiktor. “The software provides a choice of different resins, different types and diameters of threaded rods, different grades of steel and anti-corrosion coatings.” www.klimas.com CHEMICAL
G&B Fissaggi is a manufacturer of nylon fixing systems, as well as steel and chemical anchors for a variety of industries including construction. Now, the Italian manufacturer is rapidly expanding its offering with certified performance (CE approved) high-quality products.
This expansion includes the GEBOFIX PRO SISMIK VE-SF CE OPT1, which is a styrene-free vinylester. The anchor is CE Option 1 certified for cracked concrete and seismic category C1 for M10 – M24 bars and has also obtained the seismic zone certification seismic category C2 for M12 – M20 threaded bars. This enables maximum safety for structural applications and very high performance even in critical areas.
The GEBOFIX PRO SISMIK VE-SF CE OPT1 anchor is also approved for use in submerged holes; complies with LEED requirements; has a category A+ for low emission components (VOC); as well as being certified for fire resistance R120. Already available on the market, it is
PRO SISMIK Nordic anchors have an ETA accreditation (ETA - 19/0699) and are approved for application in submerged holes.
Also available from G&B Fissaggi Srl is the chemical anchor XTR Extreme Hybrid CE OPT 1, which is certified for cracked concrete and seismic category C1. The anchor is approved for M8 – M16 threaded rods, as well as seismic category C2 for M12 – M16 threaded rods. In addition, another widely used anchor is the SUPER HYBRID SH-PRO CE OPT 7 innovative hybrid formulation without styrene, which guarantees high performance on concrete and masonry. The anchor is CE certified for application for non-cracked concrete with M8 – M24 threaded rods.
Quality products with a service to match available for next day delivery direct from our branch in Sheffield (UK mainland only).
Bossong has obtained an ETA certification (ETA – 24/0719) on the BCR HYBRID for applications on masonry under seismic action, making the product suitable for use on both concrete, medium-heavy loads, as well as on all types of masonry.
Solid masonry buildings represent a significant part of building heritage. This construction technique, which uses bricks or solid blocks bound with mortar, has been widely adopted in Italy for centuries, thanks to the availability of materials and the excellent structural properties of masonry. From ancient medieval villages to Renaissance palaces, solid masonry has made it possible to create long-lasting and resistant structures, capable of withstanding the passage of time and environmental challenges.
The main challenge for masonry buildings is to resist horizontal loads, such as seismic loads. Unlike typical concrete frame buildings, which have steel reinforcement inside the concrete element, masonry buildings generally have larger load-bearing elements but do not have reinforcement to resist tensile stress.
Precisely for this reason, reinforced walls have come into use today in the design and construction of a new masonry structure, that is, masonry blocks that are reinforced with reinforcement bars that are
then incorporated into the masonry itself with mortar or binder. But what should we do with existing and historic walls? In the case of existing buildings, the interventions that are carried out to reinforce and secure the structure include consolidation and reinforcement interventions. This includes creation of a rigid and collaborating slab in such a way as to have a box type structure functioning under seismic action; creation of rigid curb connected with rigid slab; reinforcement of load-bearing masonry sections using reinforced plaster; reinforcement of the floor with the creation of a new collaborating slab; as well as the reinforcement of load-bearing walls with reinforced plaster.
All these types of interventions require the use of a steel element –adhesion bars that are embedded in the existing element in such a way as to connect the new load-bearing element with the existing one. The products used to anchor the reinforcing bars are obviously chemical anchors. Until recently, for this type of product, the ETA certification was only related to masonry fixings under static action, therefore excluding seismic loads.
Today, however, it is possible to obtain CE Marking and therefore an ETA of a product that contains, in addition to static loads, the seismic performance for solid masonry blocks only. The new version of EAD 330076 has recently been released, which includes the tests necessary for seismic qualification of solid masonry. These tests (total of 20 tests per bar diameter) are divided into shear tests and tensile tests, in a number equal to 10 tests for each type.
All tests are performed in the mortar joint, which is always assumed to be the weak element and in which a crack of 0.5mm is opened, in order to simulate the effect of an earthquake on the brick wall. Finally, half of the tests are performed by applying a static load and half by applying load cycles. The reduction in performance is then evaluated.
Bossong has obtained ETA certification (ETA – 24/0719) on the BCR HYBRID product for applications on masonry under seismic action. This qualification is added to the other ETAs already present on the product for applications in concrete (with seismic qualification C1 and C2) and applications in solid and perforated masonry under static loads. www.bossong.com
Designed to ensure reliable and secure joints in a wide variety of applications, from heavy loads in concrete to masonry applications, INDEX® – A PERFECT FIXING says its full range of chemical anchors are known for their high strength, adaptability to various surfaces and technical certifications, as well as the ability to offer maximum quality and safety.
INDEX® ’s full range of chemical fasteners include the styrene-free chemical anchor range made up of the styrene-free hybrid resin MO-H and MO-HW version. The MO-H hybrid resin is approved for high loads in cracked and non-cracked concrete, masonry and for the installation of post-installed reinforcement. It is also suitable for seismic applications (category C1), for use in contact with drinking water, as well as being certified for fire resistance. The MO-HW version is a styrene-free WINTER hybrid resin designed for low temperatures while also maintaining the MO-H properties.
Another approved chemical anchor for high loads in all types of non-cracked concrete is the vinylester MO-V and the styrene-free vinylester MO-VS version, which are approved for fixing high loads in non-cracked concrete, masonry and post-installed reinforcement. These two anchors can be used in both indoor, outdoor and structural applications, including road fences, posters, machinery, as well as boilers and billboards.
In addition, INDEX® also offers a universal polyester MO-PU, which is approved for medium loads in all types of non-cracked concrete, as well as being suitable for hollow and solid masonry. To add to this there is also the MO-PUP version – a universal stone coloured polyester, as well as a MO-PUS styrene-free polyester approved for medium loads in non-cracked concrete and masonry. Both the MO-PUS and MO-PU can be used in indoor and outdoor applications such as the fixing of stone cladding, rehabilitation of façades, as well as structural applications.
Also available in INDEX®’s wide range of chemical anchors is the polyester plus MO-P+ and MO-PS+; as well as the pure epoxies MOPURE and MOPUR3.
“Chemical anchors are an excellent solution for fastenings in materials such as concrete, masonry, and stone, due to their versatility of use, high resistance, approved certifications, flexibility in applications, as well as the fact they have no surface stresses,” comments INDEX® – A PERFECT FIXING. “At INDEX® quality and innovation go hand in hand, which is highlighted in our wide range of products suitable for a number of different applications.”
www.indexfix.com
Cracks in concrete can appear in buildings for several reasons, including moisture and thermal movement, ground settlement, vibrations or concrete corrosion. These cracks must be adequately repaired to preserve the life of the building. JCP, the specialist fixings division from Owlett-Jaton, offers an excellent crack stitching solution, which is growing in popularity year-on-year.
Crack stitching is a simple concrete crack repair method, which mends, stabilises and reinforces cracked walls and bricks. A mix of materials is used with a stitching bar fitted, which is then grouted around to rejoin and seal cracked components. It eliminates the need to rebuild costly walls and also helps to minimise the likelihood of further cracking.
The JCP crack stitch twist starter kit is a two part component system consisting of A2-304 stainless steel stitching bars and polymer reinforced cement-based anchor grout (a two part non-flammable, non-shrink, thixotropic cementitious grout).
The powder component of the grout is based on a Portland cement mix with high-quality graded silica sands plus a synergistic blend of admixtures. The liquid component is based on a styrene-butadiene co-polymer, which acts as the total gauging liquid. The grout is pumped into place using a mortar cartridge gun, offering an excellent bond to masonry and great compressive strength.
JCP’s crack stitching system is available separately and as a kit. It is a fast and cost-effective, easy to use, non-disruptive, versatile method, which offers a permanent repair. It requires no special skills for installation, making it ideal for small and big repairs and once installed, it is also invisible – helping to restore the appearance of the building.
Full data sheets and installation videos are available online.
HEICO Group’s HEICO-LOCK® wedge lock washers, designed for securing demanding bolted joints particularly in steel construction, as well as in safety critical applications, have now achieved CE Marking.
The CE Marking is a significant milestone for HEICO, opening new opportunities in construction projects that demand the highest levels of quality and safety, as well as confirming the washers meet strict EU requirements for safety, health and environmental protection.
The CE Marking refers to the ETA accreditation (ETA – 20/0075) and applies specifically to HEICO-LOCK® wedge lock washers in sizes M5 – M39, of the types HLS and HLB in steel.
“The CE Marking is another important signal to our customers that they can rely on the quality and safety of our products. Especially in the construction industry, where safety requirements are exceptionally stringent. It is therefore essential to provide solutions that uphold the highest standards,” explains Tobias Grobe, head of sales and marketing at HEICO Group.
www.heico-group.com
Following an agreement with the European Organisation of Technical Assessments, here is a list of recent ETAs published in the last two months on the EOTA website.
It is important to note that existing ETAs may be amended or withdrawn so this list should not be considered definitive. For further information and a full list of valid ETAs visit EOTA’s website. If you have recently received an ETA, and would like to have it included in our table, please email us the full details at editor@verulammedia.com
www.eota.eu
Mechanical fasteners for use in concrete
24/0947 NWBH concrete screw Ningbo
Fire stopping and fire sealing products
24/0966
Tytan Professional B1 Fire Acrylic RAKENNUSKEMIA Oy
24/0975 HENSOTHERM® EM Rudolf Hensel GmbH
24/0988
Tytan Professional B1 Fire Mortar Gypsum RAKENNUSKEMIA Oy
Linear joint and gap seals
24/0967
Tecnicas Expansivas S.L
ETICS with renderings
24/0948
Tytan Professional B1 Fire Acrylic RAKENNUSKEMIA Oy
24/1113 Würth Fugensystem AB Adolf Würth GmbH & Co KG
24/1146 ArmaProtect ABLC/ABLF Armacell GmbH
Three dimensional nailing plates
24/0969 Sherpa Sonus M and L SHERPA Connection Systems GmbH
Anchor plates, together with fischer FAZ II Plus bolt anchors and the fischer InnoLock FES cast-in channels, are being used to anchor façade elements permanently and securely to the Estrel Tower – currently under construction in Berlin, Germany.
Designed by the German-American architecture firm Barkow Leibinger, the Estrel Tower in Berlin-Neukölln, will be the tallest high-rise building in Berlin at 176m when completed. The cladding elements are 2.5m wide and weigh approximately 800kg – 1,000kg, depending on their size.
Secure fixing is crucial for the heavyweight façade elements. Each element is anchored in concrete to a depth of at least 85mm using two anchor plates together with two 173mm long FAZ II Plus 16/50 R bolt anchors from fischer Group. The bolts absorb very high-tensile and transverse forces, as well as being quick and easy to install. With a service life of up to 120 years, the FAZ II Plus guarantees a firm hold even after more than a century.
Another fixing method uses the fully hot dip galvanised fischer InnoLock FES RS-S castin channels. Here, the substructure brackets are fastened on the front side of the column with the M16 x 80mm channel bolt FBC-S-225. The InnoLock rails are already embedded in the concrete flush with the concrete support. The façade installers use the corresponding channel bolts and nuts to attach the add-on parts. To do this, they turn the channel bolt clockwise by approximately 90° and then apply the specified torque. The façade elements are then positively hooked into a recess in the anchor plates.
The wide, robust toothing of the fischer InnoLock channel and channel bolt creates connections that can withstand the highest loads, even in the longitudinal direction of the channel, thanks to proven positive locking. At the same time, the toothed connection and the low tightening torque facilitate and accelerate secure installation. The patented lip geometry also enables high retention values for tensile, transverse and longitudinal loads. Thanks to a sophisticated functional concept, the channel bolt remains securely connected to the anchor channel even under the highest loads.
UK-based Chemique Adhesives has added the new Polyped 3370 low hazard, moisture curing, one component pedestal adhesive to its Polyped access flooring range.
Polyped 3370 is a phthalate-free, single part polyurethane adhesive designed for easy pedestal installation. Its unique formula enables effortless application as it requires no mixing and easily fills voids between substrates, resulting in a strong, yet flexible bond.
The Titen HD® mechanically galvanised washer head screw anchor is now available from CONFAST.
For use in cracked and non-cracked concrete, as well as masonry, this easy to install screw with a washer head design is commonly used where a minimal head profile is necessary. The anchor is offered in sizes suitable for use in applications including installing sill plates.
Cooper Turner Beck Group (CTB) has achieved the Deutsches Institut für Bautechnik (DIBt) certification for its large diameter direct tension fasteners from M36 to M72.
CTB achieved this certification – a process that typically takes three years – in just nine months, demonstrating its technical expertise and dedication to quality. The achievement also underlines that CTB’s fasteners meet stringent safety, durability and environmental standards, aligning with both national and European regulations.
Schmid Schrauben Hainfeld GmbH has presented an Environmental Product Declaration (EPD) for its self-drilling timber construction screws, highlighting its commitment to sustainability and environmental responsibility.
An Environmental Product Declaration (EPD) is a standardised and transparent document that provides comprehensive information about a product’s environmental impact throughout its entire lifecycle. With the introduction of the EPD, Schmid Schrauben takes another step towards greater sustainability and its commitment to developing innovative and environmentally friendly solutions.
With the increasing demand for strong connections in precast construction, Peikko Group has introduced high strength HULCO® anchor bolts for screw connections.
The anchor bolts are used to securely anchor concrete or steel structures or machines in the foundation –usually in foundations, ceilings, columns, or walls. Due to their short anchoring length, they are ideal for use in thin components such as slabs and beams.
For mass timber glulam columns, Simpson Strong-Tie has introduced three new concealed connectors – the MCT™ for column-to-column installations and the MCB™ and MCBS™ for column-to-foundation installations.
Each product offers a concealed connection for architectural aesthetics and fire protection whilst, Simpson underlines, bringing strength, simplicity and versatility to mass timber construction.
Carlo Salvi has announced its transition into Industry 5.0, marking a pivotal evolution that integrates human ingenuity with advanced technologies to redefine the future of industrial production. Thanks to the introduction of the new 5.0 Transition Tax Credit in Italy, Carlo Salvi has been empowered to advance its journey towards more sustainable, efficient and customised production.
Carlo Salvi views Industry 5.0 as a natural extension of its mission, centred on the interaction between humans and machines and sustainable innovation. The new directive provides resources to enhance support for innovative technologies, delivering tangible benefits to clients, such as increased productivity and faster response times.
“This transformation presents an unprecedented opportunity for Carlo Salvi and our clients – giving us the ability to optimise processes, address new challenges in the global market, and reduce environmental impact,” explains John Razza, sales area manager for the Italian market at Carlo Salvi SpA.
Carlo Salvi points out that thanks to the 5.0 Transition Tax Credit, companies can receive up to 45% incentives on investments aimed at energy efficiency and digitalisation, with a maximum cap of €50 million per enterprise. Carlo Salvi has therefore seized this opportunity to modernise its machinery, improve energy consumption management, as well as enhance the sustainability of its production processes. These investments not only lower operational costs but also contribute to eco-friendly production and a significant reduction in emissions.
Another critical aspect of Industry 5.0 is skills development. Employee training is a strategic asset to meet the challenges of the transition and ensure the company remains highly competitive. That is why Carlo Salvi is investing in both workforce training and technological development, to make its machines user-friendly for clients and to assist them in making technical and operational choices.
“The focus on Industry 5.0 has brought a sharper orientation toward technological innovation and data management, with the goal of accelerating digital transformation and optimising production,” states
Carlo Salvi SpA. “This approach enables us to gradually integrate new technologies, minimising production interruptions and maximising benefits for customers. Industry 5.0 thus represents a promise of long-term competitiveness for Carlo Salvi.”
The company adds: “Over the next 5 to 10 years, industrial production will evolve toward unprecedented customer centricity, offering customised products, greater automation and shorter delivery times. This new industrial paradigm will provide Carlo Salvi not only with efficiency but also with a strategic edge to tackle the demands of an increasingly challenging market. This moment signifies an acceleration toward a productive future that places humans, technology and the environment at its core.”
GEFRA believes it is leading the newest development for visual inspection with the introduction of ‘deep learning’ technology into its OPTISORT testing system, which offers users completely new perspectives – especially with complex and varying imaging conditions.
With ‘deep learning’ GEFRA reports that defective parts and good parts can be learned and classified accordingly – with these datasets trained using multi-layer neural network architecture. Based on these templates, the test items can be classified as good or defective parts.
“‘Deep learning’ technology is making machine vision technology for automated visual inspection more accessible and capable,” reports GEFRA GmbH. “It requires a lot of computing power but high performance GPUs have a parallel architecture that is efficient for ‘deep learning’. The easy operation of this application is also ensured by our user-friendly AUTOCONTROL testing software.”
The AUTOCONTROL interactive environment provides the platform for training these models for use in machine vision applications. The AUTOCONTROL testing software delivers all the functionality needed for this task, so an operator can create and label the training image dataset; augment the image dataset, if necessary; as well as train, analyse and test the neural network model.
“Artificial Intelligence, specifically machine learning by way of ‘deep learning’ technology, mimics how the human brain processes visual input but performs this task with the speed and robustness of a computerised system,” highlights GEFRA. “The technology works to ensure quality in manufacturing industries, controlling production costs and enhancing customer satisfaction. The technology still benefits from conventional image processing and analysis to locate regions of interest within images, but speeds up the overall process and make it even more robust.”
Ecoclean has expanded the cost efficient EcoCcompact to include the L and XL model variants to meet the diverse requirements of general industry. The new product family, with three working chamber sizes and batch weights of up to 150kg, enables the capacity and cleaning performance to be adapted precisely to company specific requirements.
The diverse product range of the general industry includes workpieces produced by casting and machining, stamped, bent, pressed and deep drawn parts, hydraulic and pneumatic components, as well as fasteners. Depending on the subsequent process or application, the parts manufactured from different materials must meet different but increasingly stringent particulate and film cleanliness requirements. High throughputs, increased demands on resource efficiency and, in some cases, low margins pose a challenge.
As a result, the cleaning process must ensure cleanliness in-line with requirements in a stable, sustainable manner and at low unit costs. For these tasks, Ecoclean GmbH has expanded the cost efficient EcoCcompact product family with the L and XL model variants. As with its smaller sister, the machines make it easy to switch between hydrocarbons and modified alcohols (semi-polar solvents) during operation without any conversion work.
The two new, compact plug and play solvent systems have working chambers with diameters of 650mm (L version) and 750mm (XL version), enabling batch sizes of 650mm x 470mm x 300mm in the L version and 650mm x 470mm x 400mm in the XL version. The maximum batch weight for both systems is 150kg.
Other features include powerful, frequency controlled flood pumps, which ensure fast filling and emptying of the working chamber. During standard injection flood washing, they also generate a high mechanical cleaning effect. This can be specifically supported by an optionally integrated, frequency-controlled rotary drive for fabric rotation and positioning. Adapted to the cleanliness requirements, the systems can also be equipped with all available process technologies for solvent cleaning, such as ultrasound and PPC.
The increased distillate output of up to 180 l/h, and the continuous oil discharge as standard, also contribute to the high capacity and
performance of the L and XL versions. The vertical integration of the flood tanks also offers advantages. It reduces sump formation and prevents dirt pockets from forming, resulting in a longer service life of the baths and thus a reduction in operating costs.
For needs-based cleaning and preservation, the two flood tanks included in the basic version of all EcoCcompact can be supplemented by a third – fully integrated without increasing the installation area. They each have filtration in the supply and return lines with bag or high performance filters, as well as bypass filtration. Speaking of space requirements, at 4,100mm x 1,900mm x 2,650mm and 4,400mm x 2,100mm x 2,655mm respectively, the new versions are also extremely economical.
The EcoCcompact product family also impresses with its comparatively low energy consumption, which has been achieved through optimised system technology. This includes the fact that the flood tank two and optional third tank are heated with heat recovered from the distillation process.
Adapted to the cleanliness requirements, the systems can also be equipped with all available process technologies for solvent cleaning, such as ultrasound and PPC.”
Like all systems for solvent cleaning, the L and XL versions of the EcoCcompact are characterised by high flexibility in terms of material compatibility. This means that components made of different materials can be cleaned in one system. In addition, they can also be used in regions where the consumption of water as a cleaning medium and/ or the disposal of wastewater from cleaning applications is regulated. A prerequisite is the suitability of the solvent cleaning, which can be verified by Ecoclean through cleaning tests in worldwide test centres.
Buy
Redundant
National Machinery, AsahiSunac, Tanisaka, Hartford, Chun-Zu, Jern Yao, Shimazu, Hatebur, Carlo Salvi, Sacma, Wafios, Sakamura, Ayase, Hilgeland, Malmedie, Peltzer & Ehlers, Kyoei, Bundgens
Walter AG, a leading provider of tooling solutions for the machining industry, is joining Cyber Valley – Europe’s leading centre for excellence in Artificial Intelligence (AI) and modern robotics that is based in Stuttgart and Tübingen, Germany.
Digital and AI-based solutions already form a strategically important element of the Walter portfolio, with the company using its own AI-based applications for development and business processes. The collaboration with Cyber Valley aims to further advance the development and application of AI technologies in the field of metalworking.
Jean-Daniel Fechter, vice-president of IT and digital transformation at Walter AG, comments: “We are very pleased to be working with Cyber Valley. This gives us access to a strong network of leading experts and companies in the field of Artificial Intelligence and modern robotics. This will enable us to expand our knowledge and capabilities in this area, exchange ideas, as well as increase our visibility and understanding of the field.”
Rebecca C. Reisch, CEO of Cyber Valley, adds: “The signing of the Letter of Intent with Walter is an important step for us in strengthening the connection between science and industry at the site, particularly in the manufacturing sector. This collaboration not only expands our networks, but also fosters valuable conversations and innovations that might not otherwise have come about.”
Cyber Valley is a major centre for AI research and advanced robotics. The network, founded by the state of Baden-Württemberg and the Max Planck Society, is dedicated to promoting research, development and application of technologies in the field of intelligent systems and their acceptance in industry and society.
The partnership with Cyber Valley opens new opportunities for Walter to collaborate on advancing the digital transformation in the metal industry. The company also benefits from access to an extensive network of AI experts and organisations.
Anastasios Eltzidis, web solutions manager at Walter, has been a key driver of the initiative with Cyber Valley. He expects the partnership to yield concrete results: “Cyber Valley is based in Tübingen, as well as Stuttgart, so it would be hard to get easier access to so much expertise in AI and automation. We are confident that the partnership will help us to develop innovative solutions for our customers and strengthen our commitment to digital transformation in the metalworking industry.”
Product range
• Flat thread rolling dies
• Flat knurling dies
• Flat form rolling dies
• Circular thread rolls
• Tangential chasers
Licenced Products
• Taptite PRO®
• Taptite 2000®
• Duo Taptite®
• Powerlok®
• High-Torque®
• Taptite II®
• Taptite® CA
• Plastite®
• Screwbolt®
• Mathread®
• Remform®
Rohmann GmbH offers various solutions for the non-destructive testing of fasteners and fixings, with its digital in-line test instrument ELOTEST PL650 enabling the automated structure inspection of screws, bolts, nuts, rivets and punched parts.
Since being founded in 1977 Rohmann GmbH has experienced breathtaking development, with the company able to offer solutions for all aspects of non-destructive material testing by eddy current.
Cables, probes, coils, rotors, eddy current test instruments, and systems, as well as software, are all developed, manufactured and sold from the company location in Frankenthal, Germany – with more than thirty representatives supporting the family-owned company worldwide.
Through the ELOTEST PL650, which features a High Distance Sensor (HDS) and FastSort software, also developed by Rohmann, more than 500 parts per minute can be inspected for defects in structure. The sensor is also designed so that, with the high penetration depth of up to 10mm, it is possible to penetrate a glass plate to carry out sorting checks. Therefore, the sensor can simply be mounted underneath a glass plate, on which the test parts are placed.
“Whether crack detection or material mix-up, the eddy current test instrument ELOTEST PL650 displays the test results of different testing stations, which in the past required several devices along the line,” explains Rohmann. “In doing so, it is convincing by its user friendliness and its unsurpassed signal purity.”
The ELOTEST PL650 has also been supplemented by a 19 inch version (PL650/R) and a compacter 9.5 inch (PL650/RC) remote version for integration into automated systems. The inspection system for small
Crack inspection and sorting with ELOTEST PL650
cylindrical rollers from Stalvoss GmbH & Co KG is a good example of how the ELOTEST PL650 can be used. In this case, the eddy current test instrument is provided with two channels, which make it possible to carry out crack detection and multifrequency sorting testing one after the other and in one inspection cycle. An EC15 rotor, with an adjustable RDE rotating head, carries out the inspection for cracks. Two coils, working on the principle of exterior comparison, are provided for the multifrequency sorting test and the FastSort software evaluates the recorded data. In addition to the eddy current component from Rohmann, a camera is used for the inspection of the lateral surface. The inspection system is provided with a total of three sorting gates. The good parts are moved on to the outlet and deposited as bulk material, while the rejects are discarded into separate containers. Another solution from Rohmann is the small ELOTEST IS3 in-line instrument, which is a simple one channel solution that can be integrated in semi-automated systems for standardised sorting tasks or the inspection from cracks and grinding burns – with the corresponding accessories such as sensors or feed-through coils making it possible to achieve a high inspection speed.
In the fast paced world of fasteners and fixings, precision is non-negotiable. Every bolt, screw or rivet must meet exacting standards to ensure reliability and safety across industries. That is why VICIVISION UK is dedicated to supporting manufacturers in achieving unparalleled quality and efficiency.
VICIVISION UK specialises in non contact optical measurement systems that revolutionise how manufacturers inspect cylindrical components. Unlike traditional methods, VICIVISION systems offer ultra accurate, repeatable results in a fraction of the time, helping businesses reduce downtime and eliminate costly errors.
For the fastener and fixing sector, where dimensions such as thread pitch, shaft diameter and overall length are critical, VICIVISION delivers unmatched performance. The company’s advanced technology captures precise measurements of complex geometries, providing instant feedback directly on the shopfloor. This allows manufacturers to maintain consistent quality, meet stringent industry standards and keep production moving seamlessly.
One standout feature of VICIVISION’s optical systems is their ability to measure multiple dimensions simultaneously. This
eliminates the need for multiple gauges or tools, streamlining processes and reducing human error. Additionally, the systems are user-friendly, requiring minimal training for operators and integrate seamlessly with existing production workflows.
The benefits for fastener and fixing manufacturers are clear, VICIVISION’s solutions ensure compliance with ISO and DIN standards, enhance product reliability and improve customer satisfaction. By identifying potential issues early, manufacturers can also minimise waste, save time and improve profitability.
“As demand for high precision components continues to grow, the ability to deliver superior quality while optimising efficiency has never been more important. We provide the tools to meet these demands, empowering businesses to stay competitive in a challenging market,” states VICIVISION UK. “For fastener and fixing manufacturers seeking a cutting edge approach to measurement, we offer the precision, speed and reliability required to excel.”
Despite the ever improving and advancing technologies in fastener manufacturing, the risk of poor manufacturing still cannot, and probably never can, be completely removed. Owlett-Jaton has therefore adopted a long-standing procedure of rigorous product testing, carried out specifically at the point of arrival.
Along-standing procedure of product testing ensures that any poorly manufactured fasteners are contained before they are processed by the Goods In department. In turn, this practice prevents contamination from filtering throughthe supply chain – right down to the person or machine applying the fasteners.
Part of the overall process is the dedicated Quality Assurance department carrying out routine dimensional testing. Approximately 60% of inbound fasteners are checked – a large job when it’s considered that Owlett-Jaton receives approximately 80,000kg of stock every day. It is worth noting that this approach is not a legal requirement, has no accreditation dependency, is not a box ticking exercise, but rather a mindset for Owlett-Jaton to want to do the right thing by customers and beyond.
Standard dimensional testing includes using calliper gauges, ring and plug gauges – both with ‘go’ and ‘no-go’ functions, and if required, the Keyence IM-7000 series image dimension measurement systems. A rolling, random programme is generated for the QA inspection team
to carry out routine and regular testing, with all captured data recorded for future reference.
National and international standards to drawings are used for verifying including DIN, ISO, BS and SAE. Dimensions such as Across Flats (AFs), depth of head/nut, thread integrity, length of thread and product, are just some of the dimensions that are scrutinised.
All equipment is routinely sent off-site and independently tested, calibrated, and certified by a dedicated accredited calibration company, to ensure it remains accurate at all times.
In the rare instances where a fastener failure is identified, the entire consignment is immediately quarantined and stored safely, avoiding any contamination. A PCR (Purchasing Concern Report) is raised, clearly identifying product information, batch and lot numbers, quantities, as well as the failure in question. The supplier is notified, enabling them to address the issue appropriately. The stock is either disposed of locally or returned to the manufacturer; and replacement stock is issued. www.owlett-jaton.com
Here Fischer Instrumentation (GB) Ltd looks at the different ways to achieve valid measurement values and optimise measurement performance when it comes to the measurement of coating thicknesses, using reliable measuring methods and relevant devices to specific applications.
Acoating thickness gauge provides precise and correct measurement results if it has been adequately normalised and calibrated. While normalisation represents an adjustment of the coating thickness gauge to the base material, calibration describes a process in which the measured value is compared with the actual known value – usually of a standard with certified thickness. If these values differ, the device must be adjusted accordingly. In practice, a measurement task often cannot be solved in a textbook manner. Instead, the circumstances must be considered, with the measurement method most suitable for the present situation selected. The coating thickness gauge must therefore be specifically adjusted to the existing measurement task.
The process for the normalisation and calibration of a handheld coating thickness gauge requires several steps. First, measurements are taken five to ten times on an uncoated base material. Then, the coating thickness gauge knows the zero point of the coating and is thus normalised. Next, a certified calibration foil of known thickness is measured five to ten times on the uncoated workpiece. Afterwards, the target value of the foil is entered in the coating thickness gauge. The film thickness should correspond as closely as possible to the coating on the workpiece. If the layer on the workpiece does not extend over a more extensive thickness range, measuring one foil is sufficient for a successful calibration. If this procedure is followed, it is ensured that precise, accurate and, above all, correct measurement results are achieved. However, the prerequisite is that the base material is uncoated and homogeneous.
If it is known that the measurement result lies within an even, if no uncoated material is available, a measuring device can be calibrated –if you know how it works. Specific range, measurement precision and accuracy can be
optimised by corrective calibration. Also, in this case, uncoated material is mandatory. In addition to the base material, one or two foils can be selected for the corrective calibration. If this procedure is performed under the given conditions, a significantly better measurement performance is achieved within the calibration range. On the other hand, measurements outside this range result in less precise readings.
The magic word is offset. This setting is used if a middle layer of known thickness is given and the thickness value of a second layer is to be measured. The procedure is as follows, first normalisation is performed on the uncoated base material. After, the first or middle layer is applied and its thickness is measured. This measured value – the so called offset value – is set in the menu of the handheld gauge. The second coating process follows. During the second coating thickness measurement, the previously entered offset value is subtracted directly from the total thickness value (the sum of the first and second coating thickness). Thus, the exact thickness value of the second layer is obtained immediately, without any other calculations being necessary.
If there is no uncoated workpiece available when normalising and calibrating a coating thickness gauge, some Fischer coating thickness gauges offer the feature ‘calibration on coating’. This feature is available when using the magnetic induction method with Fe probes. First, the coated workpiece is measured. Next, a foil of known thickness is added and measured. Based on these values, the first measured value can be determined by interpolation. The best results can be achieved if the coating on the material is close to zero. Whilst interpolation does not offer the high measurement performance of calibration, sufficiently good measurement accuracy and precision is often achieved in practice.
At Fischer Instrumentation we can solve highly complex metrological challenges and help customers achieve the optimum measurement performance. We supply highquality gauges combined with the knowledge and experience on the suitable measurement methods we have gathered in the last 68 years. Handheld Fischer coating thickness gauges offer the features to achieve accurate, precise and correct measurement results, regardless of the conditions – using corrective calibration, offset, calibration on coating, as well as many other features.”
wide range of tailored special fasteners from M2.5 to M30 with L. max up to 240mm. Made in Italy. For the world.
By Gabriel Rozenberg, CEO and co-founder of CBAMBOO
There is a vast meteor hurtling through space, heading directly for Europe. On the side of the meteor is a sign that reads... ‘CBAM’. That is how important and how much of an impact we at CBAMBOO believe this technical regulation can have on the EU market.
With that in mind, we started working on software for the Carbon Border Adjustment Mechanism (CBAM) regulation at the start of 2023, when information on the CBAM regulatory system was scarce. At that time, it was hard for me and my business partner to even to figure out who our customers should be. However, two years later, if someone asks me which industry CBAM is hitting harder than any other, my answer is simple – fasteners.
You probably already know why fastener distributors are so badly affected. There are two key issues. The first is the challenge of compliance. The EU’s CBAM is a hybrid rule, it’s a carbon regulation, a reshaping of the supply chain and a new kind of tax, all in one highly complex package. So, there’s a challenge for any manufacturing company to figure out its CBAM obligations – theoretically, pretty much any importer of metals and other primary goods is affected.
However, fastener businesses are especially impacted because CBAM requires primary data from each supplier of imports, with an information flow that ultimately must be chased back to the original manufacturer of the products. Fastener companies have complex supply chains, typically involving thousands of companies, each of whom must be drawn into the web of disclosure and reporting.
The second challenge is no less of a concern. In less than a year, CBAM will become a real tax, with importers having to pay for every tonne of CO 2 associated with their imports. In other words, the higher the total
volume of imported metal goods that a company brings into the EU, the bigger their tax bill. It’s perfectly normal for distributors to import tens or hundreds of thousands of tonnes of CN Code 7318 fasteners into the EU each quarter – but with carbon prices of around €70/tonne and likely to rise, that means CBAM bills will be millions of euros each quarter.
Few industries are hurt as much as fasteners. Manufacturers of complex goods typically have much lower import volumes, even though they may have as many orders of larger magnitude companies.
Phil Matten, policy advisor of the British and Irish Association of Fastener Distributors (BIAFD), wrote in the September - October edition of Fastener + Fixing Magazine that “there is widespread bafflement about how to comply…” and warned that many businesses are still “in denial” of the challenges. The European Fastener Distributor Association (EFDA) has also been working strenuously to support the industry through CBAM. Despite that, Alexander Kolodzik, secretary general at EFDA, wrote in November - December edition of Fastener + Fixing Magazine that “it remains extremely difficult to obtain the required information from all suppliers”.
This is where CBAMBOO can make all the difference.
Our customers have ‘CBAM headaches’ and it is our job to make them go away. How do we achieve this? It starts with an innovative
software suite that we built from the ground up to precisely match the CBAM legislation – the CBAMBOO platform. The platform makes it easy for suppliers to provide data that is both compliant and complete. Alongside the software, our clients have access to our in-house customer support, delivered by a team with deep subject matter expertise. Key features of the CBAMBOO platform that can help importers save time on their CBAM reports include:
Imports analysis: Starting with a list of customers’ imports, the CBAMBOO platform automatically analyses which goods are subject to CBAM.
Supplier outreach: First, importers link goods to supplier companies; then the CBAMBOO platform reaches out by email to their contacts at those suppliers. Suppliers, also known as third country operators, can sign up to the platform and create installation data for their customers at no charge.
Audit trails and record keeping: Emails are sent to suppliers automatically and repeatedly over time, to ensure that there is a full audit trail. This means you can easily prove to the European Commission that you have made all efforts to get CBAM data, as required by the latest rules. Unless they are deleted, generated CBAM reports are kept permanently on the platform for future audits.
CBAM reports that match the EU’s Transitional Registry: CBAM reports are generated on the CBAMBOO platform in the XML format required for easy uploading to the CBAM Transitional Registry. In the past quarters, we have frequently seen the European Commission making technical adjustments to the Registry, which require us to rewrite the XML generator code. We constantly track these changes to ensure that our customers’ CBAM reports match up with the latest requirements, giving them peace of mind. Unlimited everything: One simple annual subscription covers the entire company, all subsidiaries and unlimited supplier links –perfect for fastener businesses with complex supply chains.
The results are tangible. In October 2024, the first reporting period in which actual emissions values were required by the EU, most suppliers around the world were barely aware of CBAM. Resistance to sending any information about their production processes was high. However, at CBAMBOO our customers were able to build a near-complete picture of their CBAM exposure. One customer used the platform to reach out to 40 suppliers, educate them about the new obligations and compile and audit their emissions information. Responsiveness was strong, 94% of their EU imports by weight were matched by CBAM data, sourced directly from the supplier.
The CBAMBOO platform helps save our clients from chasing up suppliers and shuffling spreadsheets. Onboarding suppliers is a time consuming challenge – we give you that time back by handling much of the chasing ourselves, using a mix of automated tools and personal outreach. The platform is also easy to implement, requiring no integrations to get started. We can get businesses up and running on CBAMBOO with minimal effort.
At the same time, the CBAMBOO platform is the best system available for non-EU suppliers to create CBAM data. Unlike the EU’s dreaded CBAM template, or any other Excel-based solution, the platform is visual, user-friendly and quick to master.
Carbon Flow: Instead of filling in cells in an endless workbook, suppliers draw their production diagram and add emissions data in an intuitive interface that we call ‘Carbon Flow’. This breakthrough approach to CBAM has been core to the CBAMBOO platform since day one.
Direct links to precursors and customers: The big problem with all spreadsheet-based solutions for CBAM is that suppliers need to get data from their own suppliers (known as precursors) before
The CBAMBOO platform includes a Carbon Flow tool that shows the production diagram of the supplier – making it easier to add emission data
they can send out their own data – something that often means nothing gets sent at all. CBAMBOO solves this ‘chicken and egg’ problem by dynamically linking each company’s data together. Once precursor information is updated, the supplier’s data will be updated automatically and seamlessly.
Did we mention it’s free? Basic access to the CBAMBOO platform for non-EU operators is free of charge, enabling suppliers to start compiling their CBAM data for customers straight away. Go to cbamboo.com/signup to get started.
At CBAMBOO, CBAM is what we do. In the past year we have assembled a group of experts with diverse skills who collectively have deep understanding of the disciplines needed to get on top of CBAM. CBAMBOO team members have backgrounds in sustainability, supply chain management, metal manufacturing, trade and customs, financial analysis and data science.
With January 2026’s Definitive Period approaching, we’re already developing solutions for tax estimation, data verification, declarant authorisation and CBAM certificate purchasing – all needs that your business will face. Choose CBAMBOO as your partner to master these new requirements and stay ahead of future changes.
If your fastener business is facing CBAM challenges, we’d love to hear from you. You can also book a demo at your convenience at cbamboo.com/demo. You can follow us on LinkedIn, and visit cbamboo.com , to learn more. Finally, you can meet us in person at Fastener Fair Global in Stuttgart, in hall 7, stand 3350, near the Innovation and Sustainability Pavilion – the first time we’ve set-up a stand at a trade conference, and a sign of how serious we are about the fastener industry. Come and meet our team and see how CBAMBOO can solve the CBAM puzzle for your business. www.cbamboo.com
Parts traceability is an essential aspect of business operations. Whether ensuring quality or meeting compliance requirements, maintaining accurate documentation is crucial. Yet many businesses still grapple with outdated systems, manual processes and fragmented communication when managing quality certifications. SmartCert offers a streamlined solution that empowers businesses of all sizes to enhance traceability and efficiency.
Lyndon Lattie, co-founder and CEO of Aramid Technologies and creator of SmartCert, spent over 20 years in aerospace and electronics and recognised the opportunity for a universal solution to quality certifications (certs). SmartCert provides a centralised platform to simplify cert processes. Whether you’re a supplier, distributor, or manufacturer, the platform makes it easy to verify, manage, create and share documentation. By digitising certs and making them available in the Cloud, SmartCert eliminates the inefficiencies of paper-based systems, ensuring certs are always accessible and accurate.
One of SmartCert’s key advantages is its ability to enhance operational efficiencies and drive cost savings by streamlining the receipt and approval of certs before parts are shipped. This pre-shipment
review process ensures required documents meet requirements, significantly reducing delays and quarantined parts.
“Approving certs ahead of shipment gives teams confidence that everything is in order before parts arrive,” explains Lyndon. “This proactive approach minimises operational disruptions and maintains quality and compliance standards, ultimately leading to substantial cost savings by preventing costly errors and rework.”
In addition to linking certs to products, SmartCert also enables businesses to instantly identify critical part details, such as country of origin and rare earth minerals. This feature is particularly valuable for companies that are required to comply with international trade regulations or want to provide transparency to their customers. By identifying the origin of each part, businesses can ensure compliance, reduce the risk of bad actors and fraudulent parts, as well as build trust with customers.
“We’re enhancing visibility in the sub-tier supply chain and highlighting vendor fulfilment practices to power data informed decisions. This transparency empowers businesses to identify potential risks and opportunities, enabling more efficient and strategic supply chain management,” highlights Lyndon.
SmartCert also fosters secure collaboration across teams and with external partners. Access to certs and related documentation is restricted to authorised users, ensuring that sensitive information remains protected. Suppliers can easily share certs with customers, enabling a streamlined review and approval process with just a few clicks. The platform also keeps all communication in one place, reducing back and forth emails and ensuring version control.
“Centralised and secure communication is essential for traceability and efficiency,” notes Lyndon. “SmartCert ensures that everyone involved in the process stays connected and informed, while maintaining strict access controls.”
As well as this, SmartCert’s ability to connect certs directly to the products they represent further enhances traceability. Using QR codes, businesses can access cert information instantly, whether in the warehouse or on a jobsite. This feature saves time, reduces errors and ensures documentation is always available.
Lyndon adds: “By linking certs to products, we provide full visibility and accountability at every stage of the process. It’s about simplifying workflows and ensuring the right information is always available to the people who need it.”
From raw material to manufacturing and distribution, SmartCert supports businesses in achieving compliance and improving operational efficiency. By eliminating manual processes, and providing a back to birth traceability, the platform helps organisations meet the demands of today’s markets without adding complexity.
Lyndon concludes: “At SmartCert, we’re solving problems for today while preparing businesses for the future. Our platform is flexible enough to fit into existing workflows and powerful enough to drive real results.”
The Massachusetts Institute of Technology Center for Transportation & Logistics (MIT CTL) and Mecalux S.A have started a five year collaborative project to expedite the integration of self-learning Artificial Intelligence (AI) in logistics.
Through MIT’s Intelligent Logistics Systems Lab, the two institutions will explore new applications of AI models with significant potential for businesses and society.
“The objective of our collaboration with Mecalux is to foster disruptive innovation and achieve two highly impactful use cases where AI transforms industry decision making. We will train complex self-learning machine learning models to ultimately reduce costs, lower carbon footprints and improve service quality for customers,” says Dr Matthias Winkenbach, director of research at MIT CTL and the Intelligent Logistics Systems Lab.
In the first year of this project, the teams at the Intelligent Logistics Systems Lab and Mecalux will develop two key research areas to accelerate innovation. The first will focus on increasing the productivity of autonomous warehouse robots. Using advanced simulation, optimisation, and machine learning techniques, researchers will develop a ‘swarm intelligence’ system enabling multiple robots to operate as a single entity, making collective decisions.
“We aim to create a new generation of autonomous robots that learn from human behaviour to foster greater collaboration and efficiency in warehouses,” adds Dr Winkenbach. The second research area will centre on training self-learning AI models. The Intelligent Logistics Systems Lab will design systems capable of learning from demand patterns and anticipating new customer purchasing habits.
“Current distribution systems fail to account for the full complexity of logistics networks and often make strong simplifying assumptions. This project seeks to help companies operating large networks of
warehouses, distribution centres and stores automatically determine the most efficient way to fulfil each order – taking into account the ‘real time’ status of the distribution network,” concludes Dr Winkenbach.
Würth International AG, based in Chur, Switzerland, has commissioned Kardex Mlog to refurbish a high bay warehouse at its logistics centre in Landquart. The project will focus on the two stacker cranes supplied by Kardex Mlog, which have been operating reliably since 2008.
Some of the machine components of the stacker cranes have now been discontinued by the manufacturer and can no longer be sourced. To ensure plant availability in the future, the goal is to sustainably upgrade to state of the art machines. The project will be carried out and completed within a very short timeframe between October and December 2025.
The two stacker cranes of type ecoMAN RE-1200 are approximately 22m tall and can each carry loads of 1,000kg. The load handling device is a telescopic fork for single deep storage and retrieval. The refurbishment of the machines includes reprofiling the rails, renewing the control and drive technology, as well as replacing the conductor line.
The installed Siemens controls of type S7-315-2PN/DP were discontinued as of 2020. These will be replaced by on-board, programmable logic controllers (PLC) of type S7-1515 F. In addition, decentral input and output modules of type ET200SP from Siemens will be installed. These Profinet-compatible assemblies record the lift carriage sensors and forward all signals onto the higher-level PLC.
To optimise the drive behaviour of the stacker cranes, the drive controls are also being updated. The same applies to the gear motors, which have also been discontinued. With the replacement of the drive technology in both the chassis and lift units alongside the telescopic forks, the machines will be state of the art.
Kardex Mlog, with head office in Neuenstadt am Kocher, Germany, is a specialist in integrated material flow systems and high bay warehouses. The company has more than 50 years of experience in the planning, implementation and maintenance of fully automated logistics solutions.
AEROSPACE FEATURE
Nord-Lock Group has collaborated with the aerospace industry for many years, providing safe and reliable solutions to secure critical bolted connections including Nord-Lock wedge-locking washers and NLX washers, which offer an ideal solution even in the most demanding environments.
DHall 3, Stand 2204
uring launch and decoupling in space, vessels must be mechanically prepared to withstand significant levels of vibration and dynamic loads. That is why Spanish aerospace company PLD Space S.L, which develops launch vehicles as well as offering suborbital and orbital commercial launch services dedicated to small payloads and satellites, therefore turned to Nord-Lock for its wedge-locking washers.
These washers come in pairs, with cams facing each other and serrations gripping the mating surface. When the cams lock into each other, it is geometry, not friction – which is the common force used in conventional bolting – that prevents bolts from self-loosening due to vibration. Based on their geometric principle, Nord-Lock wedge-locking washers automatically increase the clamp force when needed. Therefore, when bolted connections are installed properly with Nord-Lock wedge-locking washers, they will never unintentionally loosen.
Another aerospace solution from Nord-Lock is its NLX washer, ideal for facing the challenges related to sudden changing extreme temperatures. During any given space mission, vessels and equipment will face extreme temperatures on both ends of the spectrum – extremely high during take-off and extreme cold once the vessel has entered the outer atmosphere. It is imperative for equipment to provide the desired functionality at all times, regardless of the temperature.
AEROSPACE FEATURE
Extreme temperatures can temporarily affect the properties of materials, causing them to expand or contract – this is something that any manufacturer of space equipment must consider when deciding on a fastening solution. A bolted connection that performs well under operating conditions at ground level may experience completely different conditions in space. The NLX washer features a conical shape, which gives it a unique functionality to compensate against settlements.
www.nord-lock.com
Master Bond’s latest epoxy EP3HT-LO is a single component heat cured epoxy with an unlimited working life at room temperature. This system passes ASTM E595 tests for NASA low outgassing, making it well suited for use in the aerospace, electronic, microelectronic and optical industries.
EP3HT-LO features a good strength profile, with a lap shear strength of 1,600 psi –1,800 psi, a tensile strength of 5,000 psi – 6,000 psi and a tensile modulus of 250,000 psi – 300,000 psi. Additionally, the formula withstands 1,000 hours of 85°C/85% RH exposure.
The epoxy offers reliable electrical insulation properties with a dielectric constant of 3.9 at 60Hz and a volume resistivity of greater than 1014 ohm-cm, at room temperature. EP3HT-LO can withstand a variety of chemicals such as water, oils, fuels, acids and bases. It also exhibits high temperature resistance, with the material serviceable from -60°F to 400°F (-51°C to 204°C).
As a one part compound, EP3HT-LO offers convenient handling and processing and cures with heat, quickly polymerising in as little as 5 – 10 minutes at 300°F (148.8°C). This epoxy bonds well to metals, glass, composites, ceramics and many plastics. The epoxy is available for use in ½ pints, pints, quarts, gallons and syringes and has a shelf life of six months at ambient temperatures in original, unopened containers.
Available across Europe, Blueshift Materials underlines its newly launched AeroZero® tape series, features lightweight, easy to use tapes that deliver high-levels of protection in extreme temperatures from -200°C to over 2,000°C.
Blueshift mentions its functional tapes are ideal for any application where exposure to transient and cycled temperatures can impact the integrity and performance of the product, such as the conditions often found in the aerospace industry, but also in battery systems, consumer electronics and medical devices.
Available in a range of widths, between 5mm to 100mm, as well as a range of thicknesses, AeroZero® tapes are especially valuable for designs where weight and space constraints limit design freedom thanks to their unique customisation options, enabling tailored solutions for customers.
Tim Burbey, president of Blueshift Materials Inc, highlights: “Our expertise in mission critical industries such as space and commercial aerospace demonstrates the tape’s high performance. However, the benefits of our technology extends far beyond those sectors.”
He continues: “We’re now applying our insights to offer AeroZero® tapes to engineers and OEMs making a range of products, especially for use in designs that have space limitations, cycled temperatures
or are looking for an easy to wrap thermal protection system. Our high performance tapes help protect both product integrity and brand reputation.”
Tasked with the challenge of designing and developing a brand new and complex component for a global Electric Vehicle (EV) manufacturer, TR Fastenings used its extensive experience and know-how to produce a unique fastening solution for the vehicle’s central console.
As the EV market grows worldwide, automotive designers and engineers, together with manufacturers, are completely rethinking the design of EVs in order to provide consumers with the most advanced, high-tech specifications they now expect, without compromising on passenger comfort and user experience in any way. In this instance, TR’s customer required a bespoke spring and spool product for the sliding central console, with three different versions designed specifically for installation in the tray, cup holder and lid.
The challenging aspect of the application was the need to execute a precise speed and timeframe of the open and close mechanism, only achievable through advanced fastener technology. To create a smooth and continuous motion of the central console mechanism, TR had to match the spring performance with a suitable damper to ensure the console travelled smoothly and at a continuous speed, both in a stationary vehicle or when driving over a bumpy road.
As nothing like this was currently available in the market, TR brought its expert teams together from global locations, facilitating a high-level of collaboration and technical expertise to develop this highly specialised component. Teams from TR USA and TR Sweden worked closely with several global manufacturers to design and assemble the final spring and spool product.
The spring and spool assembly translates linear motion into rotation – an assembly
As nothing like this was currently available in the market, TR brought its expert teams together from global locations… to develop this highly specialised component.”
that was tailored to the application to fulfil its function smoothly and without noise. In order to do this, the spool was specifically designed to align with the geometry of the spring. The spool was manufactured from a specific polymer to improve control and lubricity, as well as low static and dynamic sliding friction against the mating surfaces.
Utilising years of experience in developing complex parts and working closely with customers and their drawings, TR was able to meet the specific challenges of this application. The company was also able to support the customer with cost efficiencies thanks to a reduced size of the spool decreasing material costs and speeding up installation time.
Patrik Ringdahl, project engineer at TR commented: “Finding the right solution is my passion and working alongside our customer on this project was an incredible opportunity to bring that to life. Leveraging our experience and global supplier network, we designed a solution that not only met the customers’ precise needs but also provided enhanced functionality and durability. This approach means our customer benefits from a reliable, high performance component, supporting their commitment to quality and innovation. Growing with our customers to create functional, forward thinking solutions is what drives our teams at TR, every day.”
With its desire to expand into the field of pneumatic systems for commercial vehicles, ARaymond has launched its new AIRYOSA™ line of connectors, fasteners and tubes to be used as part of key vehicle systems such as braking and suspensions.
Gerald Vincent, ARaymond global commercial vehicles market coordinator explains: “The AIRYOSA™ line-up breaks new ground for ARaymond and we’re excited about the path forward in the pneumatics sector. We are proud to release a new and complete set of products and solutions in this market, leveraging our long-standing expertise in fluid handling for commercial vehicles. These products will provide improved safety, ergonomics and sustainability during the assembly process and the vehicle’s lifetime.”
Key benefits of the AIRYOSA™ product line for commercial vehicles include improved ergonomics as the AIRYOSA™ Quick Connectors (QC) are designed to reduce insertion force by approximately 30%. With more than 110 end piece connections and 130 tube insertions to complete per vehicle – these components can save on installation time, reduce risk of misassembly and preserve worker health.
AIRYOSA™ products also offer advantages with lightweighting and compact assembly, with the company highlighting its pneumatic products are designed to deliver a 17% reduction in weight. This will lower overall vehicle weight and support the sustainability goals of OEMs. Standard tools can be used for disassembly and an eco-friendly design made with bio-based materials enables a more than 50% reduction in CO 2 emissions during manufacturing processes.
In addition wear resistant features enable easy maintenance even after extended service in harsh environments. Also, with all connectors, tubes and fastening solutions coming from one place, ARaymond can be a single source supplier in the pneumatics field, including the option for customised parts and solutions.
“We can now provide commercial vehicle customers with a wide range of products for the design and assembly of their pneumatic systems, including connectors, tubes and fasteners. We are excited to start working with our long-term commercial vehicle OEM partners on new pneumatic projects,” underlines Vincent.
NORMA Group has won a major order from a US-based global manufacturer of home appliances to supply almost three million dishwashers with custom-made metal TORRO clamps annually, starting in Q4 of 2024.
The new order aligns with NORMA Group’s efforts to expand its business within industry applications, with the aim to generate a larger share of sales in this area in the medium term.
NORMA’s TORRO worm drive clamp has been manufactured at the Group’s headquarters in Maintal, Germany, for more than four decades and is characterised by a high belt tensile force and an even distribution of the clamping force. A new combination of the clamp band developed and manufactured in Europe and a screw based on the Anglo-American dimensional system was designed for the order.
“This order is a good example of our strategy to build up additional business directly with manufacturers of machines and appliances from various industries in addition to our established sales channel via distributors. With our development capacities and our global production network, we can deliver customised solutions for our customers worldwide,” states Guido Grandi, CEO at NORMA Group. www.norma-connects.com
Fibrous components, as well as woven or non-woven textile structures in car interiors, pose a fastening challenge. Whether it is the floor panelling of a car or the roof liner, connecting these parts safely or securely anchoring them with a fastening element can be difficult. Bossard Germany says its LiteWWeight® Lotus, part of its MultiMaterial-Welding technology, offers a reliable solution.
LiteWWeight ® Lotus is a fast and secure connection concept that has been specially developed to offer high strength and deep integration into the fibre matrix. With the added advantage of onesided access when installing, LiteWWeight® Lotus can simplify the assembly process and allow for a wider range of design options. The fastener can be integrated directly into an injection moulded part, as well as leaving no marks on the back, even with thin and sensitive materials, ensuring a clean and professional finish to the application.
“The right joining technology is an issue that is still often only considered late in the design and construction process,” reports Christian Busch, business development manager at Bossard Germany. “Looking at the connection technology at an early stage and choosing the right solution can not only avoid expensive detours with
unnecessary susceptibility to errors and scrap but can also optimise processes and ensure the most cost-effective production.”
A particular challenge in lightweighting is fastening elements, which is where Bossard’s MultiMaterial-Welding technology comes into play. The aim of this technology is to optimise production processes, save effort, time and cost with very short cycle times –all without making concessions in terms of quality, resilience and reliability.
In order to meet customer specific requirements, Bossard offers six solutions within its MultiMaterial-Welding technology. Firstly, the LiteWWeight® Pin provides fast and strong fixation on sandwich structures. The LiteWWeight® zEPP is then a standard
solution for a wide expanded polypropylene (EPP) density spectrum. Also in the range is the LiteWWeight® Double Pin, which can reliably connect lightweight sandwich panels made from aramid, polypropylene and other materials. When fastening thermoplastics, the InWWerse® Fastener can be used with or without reinforcement, as well as the InWWerse® Disc that enables quick and secure joining of conventional, non-weldable plastic components. The LiteWWeight® Lotus completes the product family.
Light metals such as aluminium play an important role in reducing the weight of a car body. However, joining them to steel is a challenge due to the very different melting points and coefficients of thermal expansion of the two materials. The SWOPtec process offers a flexible solution and ARNOLD UMFORMTECHNIK is looking to develop the process further.
SWOPtec (Steel Welded Opposed Plug) is a joining process for joining aluminium with steel materials, with its core competencies lying in the production of the joining element.
The focus for SWOPtec applications is on the automotive industry, both OEMs and their suppliers. The process, which was originally developed and patented by Benteler Automobiltechnik GmbH, can be used for a wide range of applications and is suitable for all component joints where aluminium is to be joined to steel.
Dr.Ing Vitalij Janzen has been working at ARNOLD UMFORMTECHNIK GmbH & Co Kg in the field of research and development for five years and is now responsible for developing SWOPtec further. He explains: “The initial impetus came from Benteler Automobiltechnik, with the company approaching ARNOLD in 2018. A process solution was developed and presented in mid 2019. However, the original SWOPtec fastener was not able to meet all of ARNOLD’s customers’ requirements. Further developments and areas of application followed, with the first series application in several model series launched at the Hyundai Motor Company in Korea.”
In principle, the SWOPtec process is used to join aluminium components – cast aluminium, extruded aluminium or sheet aluminium components – to steel components using spot welding technology. SWOPtec is a two stage process. In the first stage, the connecting element is punched in and then the component assembled with fasteners is fed to the core line and welded in the second stage.
With SWOPtec, the customer can act very flexibly. Both steel-steel connections and steel-aluminium components can be manufactured on one production line, meaning a large number of model variants can be produced with the same welding systems.
ARNOLD UMFORMTECHNIK is constantly developing the process with various feeding concepts being worked on, as well as the geometry of the swop elements continuously being adapted.
Cost-efficient production of your fasteners, complex cold-form parts, assemblies, and precision parts
Prototyping, lab services and test runs
Global delivery based on reliable supply chains
Installation into your application
Application engineering consulting by our experts
Multiple suppliers, different competencies at different sources and not enough reliability?
Make it easy for yourself: with us, you get everything from a just one source. We analyze your application down to the last detail with our experts. We challenge your technical drawing with our decades of experience. We work with you to develop complex geometries and prototypes, carry out laboratory trials and material tests.
When it is perfectly designed, we produce your part cost-optimized: we form it, heat-treat it, coat it, overmold it, assemble it, and package it. We then deliver it to you quickly, safely, and locally - no matter where in the world.
So that you can install it at the end and make your application better. And if you want to get even more out of it, our application engineers will find a way. Without you ever having to deal with more than one source
www.kamax.com
Driven by market demand, Hisener is expanding its product portfolio, while also working towards a sustainable goal, by putting stainless steel screws and bi-metal screws at the forefront of its development projects.
Recognising a growing demand for stainless steel products in its customer base, Hisener Industrial Co Ltd inaugurated its new 32,000m 2 automated Smart factory in 2022 where a dedicated workshop was added to broaden the production of stainless steel items. By expanding its original production of woodscrews and pre-packed items, Hisener aims to create a win-win niche market with its customers by adding more high value and cost-effective products to its supply capacity, a move which can also satisfy the customers’ desire for one stop procurement.
Using high-quality 304/316/410 series of stainless steels in production, Hisener offers screws, bi-metal screws, threaded rods, bolts, nuts, washers, anchors, riggings and pins as well as solar photovoltaic bracket fittings. Specifically, the company’s stainless steel deck screws and stainless steel wood structural screws
have obtained CE Marking and an ETA certification (ETA - 22/0584), thus ensuring product reliability in specific applications.
These bi-metal screws manufactured from stainless steel and alloy steel, which were
performance of the bi-metal screws has seen many customers from the building and home improvement, solar energy and mechanical equipment industries choose Hisener products for their fastening solutions.
The most attractive quality of stainless steel products is, of course, their ability to perform well in harsh climates and corrosive environments, which is why Hisener ensures the highest quality through extensive testing of its products. “The test data of our products must be 100% compliant with the industry standards. Not only do we use salt spray and Kesternich testing equipment to test our products 24 hours a day, but we also rigorously inspect each batch to ensure they meet the corrosion resistance requirements,” says Simon Liang, general manager at Hisener Industrial Co Ltd.
In addition to its fully fledged processing technology, Hisener is also able to meet high-quality performance and cost control, both of which are its major advantages. Simon, who often participates in international exhibitions to communicate with customers face-to-face, has a deep understanding of what Hisener’s customers really need. He believes that in this economic downturn, the best value is to provide customers with the most cost-effective products.
“Talent and capital are the key to design and R&D. In the future, we will invest more efforts in R&D and actively look for high-quality talents to join our team in order to create quality products with better customer experience. We have never set a limit on the promotion and sales of our products. Wherever there is a demand, there is a Hisener team there. We
believe that everyone needs good products with high price performance ratios. Hisener will continue to do a good job in every product and provide better service for every customer,” concludes Simon.
www.hisener.com
To reflect its recent growth and focus on future development, UK-based supplier of stainless steel fasteners, Apex Stainless Fasteners has opened a new 7,000m 2 warehouse facility in Wednesbury, replacing its long-standing Bilston warehouse, which closes its doors after 30 years of operation.
Apex’s new warehouse facility is equipped with innovative packing and conveyer belt systems, bespoke shelving solutions, with future plans of an on-site quality laboratory. The site also features plenty of new office space to accommodate growth, as well as modern facilities and staff amenities. The Wednesbury site is also Apex’s first site to adopt its refreshed visual identity, with signage installed showcasing the business’s new logo. This rebranding project represents Apex’s forward-looking vision – a sleek and modern design crafted with a digital first mindset.
David Vahter, managing director at Apex Stainless Fasteners Ltd comments: “Bilston served us well over 30 years but we have now outgrown it and new facilities were needed. The new facilities, thoughtfully refurbished to a high standard, reflect our commitment to growth and operational excellence. The move was made possible thanks to the dedication of our staff and the support of our external partners and represents a cornerstone of the company’s future, ensuring we are well positioned for many years to come.”
Another key milestone for Apex is its new webshop, set to debut in early 2025. It follows the successful ERP change in 2023 that enabled the transition to paperless sales and orders, laying the foundations for the company’s venture into eCommerce and digital services, demonstrating its commitment to securing a sustainable future while accelerating growth. www.apexstainless.com
The new 20V MAX XR® ¾ inch, ½ inch high torque impact wrenches and 20V MAX XR® ¼ inch quiet hydraulic impact driver from DEWALT®, a Stanley Black & Decker brand, are enabling users to meet max torque for heavy-duty applications, whilst also exhibiting quiet operation in noise sensitive work environments.
Joining DEWALT ®’s well known XR® portfolio of 20V MAX power tools, the new 20V MAX XR® ¾ inch high torque impact wrench provides up to 102% more torque for use in tough applications, whilst the 20V MAX XR® ½ inch high torque impact wrench provides up to 28% more torque, when paired with the XR POWERSTACK™ oil resistant 5Ah battery in heavy-duty fastening applications.
Both tools feature glass filled nylon housings to help protect against oils and solvents, as well as a PRECISION WRENCH ™ mode, which helps prevent overtightening and fastener run off. In addition, there is also a four mode push button switch to easily change speeds and LED brightness.
“DEWALT ® ’s latest fastening solutions not only meet the standards of the XR® line-up, but are industry leading with advanced engineering and design features,” says Bill Harman, vice-president of product management at DEWALT ®. “In its 100th year, DEWALT ® continues its commitment to user focused
noise and optimised ergonomics to drive productivity.”
Another addition to the brand is the 20V MAX XR® ¼ inch quiet hydraulic impact driver – DEWALT ® ’s quietest impact driver designed for noise sensitive environments with up to 57% quieter operation. Ideal for framing, cabinetry and other applications in tight areas, DEWALT ® highlights its impact driver delivers up to 40% faster driving with consistent performance in demanding applications and cold temperatures.
With its B-RAD Xtreme torque wrench, RAD Torque Systems has been recognised with the 2024 Pro Tool Innovation Award, celebrating the most groundbreaking tools in the industry.
This year’s competition saw over 100 manufacturers submit nearly 400 products across a number of categories, with RAD winning in the innovative auto and metal – wrenches –torque category.
Judges commented: “The B-RAD Xtreme bills itself as a powerful cordless torque wrench and we have no reason to doubt it. The tool delivers an impressive 15,000Nm of torque from a compact, ergonomic design. Resembling a cordless drill, the B-RAD X offers both speed and precision with an accuracy of 4% of the target torque. Its broad operational range and rapid performance in single speed
gearbox configurations make it ideal for a wide array of demanding industrial tasks.”
They continued: “Innovation comes in many forms and award winners push boundaries, often introducing features no one has ever seen before. The work of teams and individuals who dare to think outside the box is evident throughout the Pro Tool Innovation Awards.”
Dan Provost, founder and president of RAD Torque Systems, added: “It’s an honour to be recognised for innovation once again. The B-RAD X is a testament to our team’s dedication to developing cutting edge torque solutions that deliver both power and precision.”
In applications where a simple spanner used to be sufficient and as customer requirements continue to increase, more bolted joints are requiring the use of a torque wrench or complex precision tool. Here, STAHLWILLE explains why careful handling and the right grip are essential when using a torque wrench.
Atorque wrench is not as robust as a spanner, its interior contains sophisticated mechanics and modern versions even feature electronics. Torque wrenches should always be handled carefully to ensure the tool can reliably measure the applied torque and trigger correctly. It is therefore best to transport a torque wrench in the case or tool box to ensure optimum protection.
Secondly, “don’t overdo it”. A bolted connection is not just defective if the bolt head is sheared off. If a tightening torque is specified, even a slight overrun can result in the connection not meeting the specification. This is why it is so important not to continue applying force after the wrench has triggered – reaction time after the trigger signal is key. Slower reaction to the torque wrench signal
means more force is applied to the screw head unnecessarily, risking a poor connection.
Finally, users must observe the gripping position. It is essential that users hold the torque wrench in the correct position to measure the torque correctly. This is because the torque is calculated from the applied force and force loading point. A force loading point refers to the distance between the user’s hand and the bolting position and, for this reason, many torque wrenches have a marking for the gripping position.
With STAHLWILLE torque wrenches, the ergonomic shape of the handle also prevents incorrect operation. In addition some STAHLWILLE electronic torque wrenches also feature force loading point compensation, meaning the torque wrench automatically corrects minor deviations.
Bahco, an SNA Europe Group brand, offers an extensive range of Bluetooth® digital torque and angle tools including its digital torque and angle Bluetooth® screwdriver, as well as the digital torque and angle slim Bluetooth® wrench, which can now be paired with the new Bahco Connect App.
When paired with the Bahco Connect App, tool users are able to enjoy enhanced efficiency, traceability, as well as control over torque and angle measurements. This easy to use App, available for Android, Windows and iOS, permits two-way data transfer, allows users to create an infinite number of pre-set libraries and jobs, records measurements, as well as links relevant traceable data for future reference and audits. It is these features that help to eliminate errors and simplify daily torque control operations, reduce operating time and providing complete control over critical fastening operations.
Bahco Connect App measures prevailing torque and calculates the average torque needed for continuous movement through the full turn of a nut or screw, ideal for lock nuts. Percentage values for minimum and maximum torque and angles can be specified when creating pre-sets and recorded in the log thanks to enhanced data logging capabilities, while new filters and paging options improve data analysis.
The aluminium mini torque wrench from Torque-Tech Precision Co Ltd has been awarded the 2025 Taiwan Excellence Award – a symbol of superior innovation and craftsmanship within the Taiwanese industry.
Judged by over 100 experts, the Taiwan Excellence Award evaluates products on four key pillars – innovation, design, quality and marketing. Conforming to its original design concept of lightweight and professional application, the mini torque wrench has been manufactured from 6061 aluminium alloy, combined with an anodised surface treatment to create a sleek and professional finish.
Additionally, the tool offers a variety of colours to match its diverse applications, as well as a front direction plate featuring a sun wheel pattern, which effectively prevents slipping and adds aesthetic appeal during operation. With an adjustment handle featuring anti-slip stripes and a simple design, this tool provides both user comfort and an attractive appearance.
“We are honoured to be recognised in the 33 rd Taiwan Excellence Award. This achievement highlights our commitment to delivering cutting edge and high-quality torque tools and we will continue to innovate and raise the bar in precision torque solutions for global markets,” states the company.
Wiha’s speedE® PocketDrive electric screwdriver, designed for universal screwdriving applications, has been awarded the German Design Award 2025 in gold.
Awarded by the German Design Council, the German Design Award is a prestigious award, the gold award only given to a maximum of two products in each category – a testament to the quality of the speedE® PocketDrive.
PocketDrive is the youngest member of Wiha’s speedE® family and combines sophisticated design with versatile functions. Its ergonomic shape with flat handle elements, which serve as practical anti-roll protection, enables comfortable handling – even in overhead applications or in confined spaces.
Two selectable material protection levels offer precise and powerful screw connections, while the LED ring illuminates the work area without shadows. A magnetic bit holder, including 30 bits, offers maximum flexibility for a wide variety of screwdriving tasks. Thanks to the USB-C interface, the battery can be charged quickly, meaning the PocketDrive is always ready for use. An integrated motor protection also means the tool can be used for manual screwdriving.
Sven Wilde, marketing manager at Wiha Werkzeuge GmbH, outlines: “This gold award is an extraordinary honour for the entire Wiha team. It reflects our commitment to developing tools that are functionally and visually impressive and that offer real benefits for users with their overall concept. The speedE® PocketDrive is the perfect example of how well thought-out design and practicality can go hand in hand. This recognition shows us that our innovative strength is valued on a broad level – from the jury to the users. This makes us proud and motivates us to continue working on solutions that make our customers’ everyday work easier.”
Recently introduced by DELO Industrial Adhesives, the DELO-DOT RE is a new retraction valve that helps to ensure a quality bond, as well as dispense adhesive droplets as small as 0.09µl.
Using compressed air, the pneumatic retraction valve features heightened precision and control thanks to the retraction mechanism. This mechanism works after dispensing the adhesive, rather than ceasing air compression, the needle ‘retracts’, pulling back slightly to reverse the flow of adhesive which, in turn, creates a vacuum effect, curtailing the adhesive flow and preventing drips.
Measuring 33mm x 25mm x 112mm, the system can be easily integrated into almost any production line, requiring only an additional 18mm to accommodate for its width. A weight of less than 100g also helps minimise the impact on existing systems. Tool-free cartridge replacement is also possible via the spring loaded reinforcement clips located on the actuator component. In addition, to enhance performance of the system, any part of the valve which comes in contact with fluid is entirely encapsulated and can be easily replaced.
The versatility of DELO-DOT RE means it can be utilised across many application fields. In semiconductor potting, as well as active alignment processes for cameras, dispensing directly from the cartridge is often preferred. Here, the valve’s retraction mechanism provides higher yields by reducing waste through drips while enhancing control during dispensing.
In order to offer the right tool for the right solution, the GEDORE red tool series now features a 43 piece torsion bit set, available in various designs and lengths which includes the practical ratchet screwdriver and a range of adapters and sockets.
Available from GEDORE Werkzeugfabrik GmbH & Co KG, the torsion bit set includes a magnetic ratchet bit screwdriver that can be converted into a pistol grip by the press of a button. Such features make it easy to work with greater force even in confined working areas and make the screwdriver an extremely practical tool.
In addition to the ratchet screwdriver, ¼ inch torsion bits are included in slotted, PH, PZ, TORX ® and hexagon socket profiles in various lengths from 25mm – 50mm and 90mm.
The torsion zone ensures a high load capacity and minimises wear on the bits –extending their service life and ensuring optimum adaptation to hard materials such as wood and metal. In addition, the bits show their full potential especially when driven by cordless screwdrivers, for which they are also designed.
The set is complemented by magnetic sockets in 8mm, 10mm and 13mm spanner widths as well as a practical ¼ inch quick change adapter and two drive adapters in ¼ inch and ⅜ inch sizes. It offers a wide range of possible applications and makes the torsion bit set a flexible partner for different requirements.
In addition, safe storage is ensured with a sturdy plastic case with high-quality metal clasps, as well as different inserts to enable quick and easy access to the tools required.
To guarantee optimum setting processes, the new range of RIVKLE® NEO B battery powered tools from Böllhoff – NEO B107 and NEO B109 – feature electro-hydraulic technology combining performance and reliability making them more compact and easier to handle, as well as being suitable for mass production use.
The RIVKLE ® brand of tools represents Böllhoff blind rivet nuts and stud technology and is a versatile solution for the creation of an internal thread or external thread on thin-walled components. These solutions require access to the application from one side only and allow two or more plates of different materials to be joined together. B107 and B109 give users full control over the setting process to validate the conformity of each installation.
charge levels, error codes, as well as access to setting forces and parameters.
In addition, the NEO B109 can be connected to a computer and managed using the NEOSOFT application. NEOSOFT helps users in their day-to-day work enabling them to control and customise control processes with the ergonomic interface, with options to change various parameters per application.
Capable of setting 32 RIVKLE ® rivet nuts per minute, the optimised design of the two tools offer compact tool dimensions along with two distributed motors for better tool balance. The redesigned anti-pinch trigger ensures force is not exceeded during application, with the tools also featuring an automatic unscrewing button and a comfortable ergonomic handle. Compatible with Böllhoff mandrels and anvils, the mandrel screwing axis has been optimised for ultimate repeatability. The digital display gives users an easy overview of battery
The alarm section enables users to view the history of errors that have occurred on the tool, such as tool stroke, motor, lack of oil or an error with the battery, regardless if these errors were acknowledged or not.
NEOSOFT also features a ‘quick settings’ option, a viewwhich allows direct selection of a pre-registered programme and the option of locking the tool to a defined programme. With the ability to create and modify up to 10 programmes, users can observe the variations in all applications.
With a unique design, the new fastener model ‘A Profile Fastener’ from Norm Civata San ve Tic AS enables fast, low torque threading in assembly processes without causing deformation in wood or metal plates. The fastener has recently been granted a patent (TR2019/08453) by the Turkish Patent and Trademark Office.
Manufactured to address the problems encountered when joining materials such as wood, metal, or profiles with gaps between them, this new solution ensures maximum safety through precise centring and fixation during installation. Problems such as deformation caused by conventional screws when connecting materials, axis misalignment and the need for hole preparation, can therefore be minimised.
Featuring a drill bit design, the screw can drill its own path without the need for pre-drilling, thus offering savings on costs and assembly time. The screw also prevents axis misalignment within the material, ensuring a stable and accurate connection. With a reusable design thanks to minimised damage during assembly, the fastener also enables chips generated during drilling to be expelled through channels on the screw. www.normfasteners.com
CAMCAR Innovations™ has partnered with Hess Industries Ltd, the owner of Clinch Solutions™ and provider of clinch tooling systems for stamped parts, to provide an enhanced experience for customers who want to improve product functionality while improving installation quality and productivity.
CAMCAR offers extensive expertise with clinch fasteners through its well known Strux® family, including the latest Strux SM ™ and Strux HM ™ studs and nuts which, CAMCAR outlines, offers customers functionality with lower installed costs than competitor’s clinch or weld fasteners.
In addition, Clinch Solutions™ provides a high-level of customer service, offering technical solutions tailored to individual customer needs, as well as a committment to providing cost-effective solutions, delivering quality equipment and tools on time.
The company comments: “CAMCAR’s product expertise and Strux® clinch fasteners combined with Clinch Solutions™’s innovative in-die approach will form a collaboration offering superior support and tailored solutions that meet the evolving needs of customers.”
www.camcar.com
In this article, Dr Bill Eccles of Bolt Science Ltd, discusses the role of bolt preload in friction grip joints, as well as how the coefficient of friction can have an impact on bolted joints.
In mechanical engineering, most bolted joints have clearance holes. That is, the hole is a larger diameter than the bolt’s thread diameter. A larger hole is employed for manufacturing reasons so that the parts can be economically made and assembled.
Prior to the bolt being tightened, any shear loading would cause the joint plates to slip resulting in wear issues, amongst others.”
Many bolted joints have to sustain a shear loading as illustrated in Figure One. Prior to the bolt being tightened, any shear loading would cause the joint plates to slip resulting in wear issues, amongst others. By tightening, a preload is induced into the bolt that is reacted by a clamp force acting on the joint. The clamp force in conjunction with the friction that is present between the plates generates a friction grip that resists the shear force. If friction grip is maintained, the plates will not slip, and the shear force passes through the plates themselves rather than the bolt. To prevent slip, the critical parameters are the magnitude of the bolt preload and the value of the static coefficient of friction on the joint interface. In structural engineering, the term slip coefficient is frequently used instead of the coefficient of friction in this regard.
The amount of clamp force needed to resist joint slip is sensitive to the value of the static coefficient of friction. If the shear force was, for example, 5kN, and the coefficient of friction between the plates is µ = 0.2 (a typical value used for dry cold rolled steel on steel), the bolt must provide a minimum clamp force of 5 / 0.2 = 25kN. If say, the friction coefficient was 0.5, the clamp force needed would be reduced to 10kN (that is, 5 / 0.5). If joint slip occurs on a tightened bolt, self-loosening, fatigue and wear of the bolt shank and hole surface can result. Accordingly, the friction between the joint plates is of crucial importance in ensuring the integrity of the majority of friction grip shear loaded joints.
Values for the coefficient of friction between joint plates based upon a purely literature search can vary widely. VDI 2230 on bolted joint analysis, a respected source of information on bolting, gives the coefficient of friction between steel on steel as being between 0.1 and 0.3. This changes to 0.15 to 0.4 if the steel is cleaned. If 0.1 is used in the calculation instead of 0.3, three times the clamp force would be needed to prevent slip. Overestimating the value of the friction coefficient of the joint surfaces have been a cause of bolt loosening and fatigue issues.
To prevent self-loosening, the use of some form of locking device, or method, is frequently used. Since the cause of a bolt self-loosening is usually joint slip, the locking approach works if such joint slip only occasionally happens. If joint slip occurs under normal day-to-day loading, bolt fatigue and wear issues can be anticipated if an effective bolt locking device is used. Bolt fatigue occurs since it is the joint interface that slips first whilst the bolt head still has friction grip and remains stationary. This causes the bolt to sustain repeated bending when slip occurs. This bending is the source of an alternating stress in the bolt that causes fatigue.
Experience indicates that for joints that repeatedly experience slip, adding a locking washer or nut can be regarded as only a short-term measure to resolve the issue. Some weeks or months later, in such situations, the loosening problem previously experienced is substituted for a bolt fatigue issue. There is no long-term substitute to designing the joint so that there is sufficient clamp force to prevent joint
slip from occurring. Bolt Science offers training and software to allow a joint to be successfully designed considering factors such as preload scatter and relaxation loss. If the joint is designed and assembled such that joint slip doesn’t occur, a locking device is unnecessary.
Contamination of the joint interface surfaces with oil or grease can significantly lower the friction value. Friction grip surfaces should be clean and dry. Such contamination has been the source of loosening issues. For example, in one instance that an issue arose, fitters were placing grease on the inside face of wheels when servicing commercial vehicles since they thought, rightly, that this would make the wheels easier to remove. However, it also reduced the friction grip resulting in the slipping of the wheel on the hub. Braking and acceleration forces are transmitted through the wheel – hub interface joint by friction grip. The repeated joint slip resulted in the wheel bolts self-loosening.
However, there are ways in which the coefficient of friction can be increased (Figure Two). Having a proven approach that will increase the interface friction is very useful and can be a way of resolving a service problem or minimising the bolt size needed in a shear loaded application. Such approaches can include thermal spray coating of the plate surfaces, use of diamond impregnated shims, as well as the use of shims with an engineered surface designed to increase friction.
www.boltscience.com
To prevent self-loosening, the use of some form of locking device, or method, is frequently used.”
Rivit Srl is adding new tie rods, designed to fasten Rivbolt rivet nuts with male threads, to its 700 Series of battery operated power tools for blind rivets.
Ideal for mechanical engineering, metalworking, electronics, automotive and heating industries, these tie rods are compatible with the RIV730 and RIV740 battery tools and enable Rivbolts to create a reliable seal and offer an alternative to a screw and bolt in a removable application. Rivbolts can be cylindrical, hexagonal, semi-hexagonal or knurled cylindrical, depending on the fastening requirement.
Made from steel and available in various sizes, the new tie rods are easy to install and remove ensuring strength and maximum reliabilty.
To further aid the operator, the RIV730 and RIV740 cordless riveting tools are equipped with a soft, ergonomic handle to facilitate grip, powerful brushless motors, an LED light system, as well as a panel that allows the operator to adjust and select the best function according to the application. These models are equipped with a 10mm stroke – with the RIV730 designed for M3 to M8 rivet nuts and the RIV740 suitable for M3 to M12 rivet nuts.
Developed for medical device applications, Master Bond’s EP21LSCL-2Med is a two component non-cytotoxic epoxy for bonding, sealing, coating and potting. Equipped with a high resistance to yellowing, this compound is especially suited when optical clarity is required.
While most epoxies yellow over time, especially when they are exposed to heat and intense UV light, EP21LSCL-2Med has been designed to resist yellowing to a greater extent than conventional systems. This unique feature makes the epoxy ideal for imaging applications or other medical devices where optical clarity is needed.
Offering a refractive index of 1.57, the epoxy has a high glass transition temperature of 110°C – 120°C and a service temperature range of -52°C to 177°C.
In addition, the EP21LSCL-2Med has a 100:20 mix ratio by weight as well as a low mixed viscosity of 600 cps – 900 cps at room temperature. A moderate heat cured epoxy, the product also features a long gel time of 6 – 8 hours at room temperature and will cure at room temperature, followed by a post cure of 3 – 5 hours at 60°C – 80°C.
EP21LSCL-2Med adheres well to many substrates including but not limited to metals, composites, glass, ceramics and plastics, offering a tensile strength of 8,000 psi – 9,000 psi alongside a tensile modulus of 325,000 psi – 375,000 psi. This system can also resist various sterilisation methods such as steam sterilisation, liquid sterilants, anti-bacterial agents and Ethylene Oxide.
Shelf life of the EP21LSCL-2Med is six months in its original, unopened containers and is available in kits ranging from ½ pints to 5 gallon pails, as well as speciality packaging in pre-mixed and frozen syringes requiring storage at -40°C.
Static mixing nozzles are vital for dispensing and are used for mixing or blending two part adhesives, potting compounds, and other protective materials, where products are packaged in cartridges or used in metering and mixing equipment.
Intertronics outlines the key design features and characteristics of mixing nozzles include the mixer’s element shape and style, mix ratio, inner diameter, the number of elements, connection interface and nozzle termination.
ZEEKR, a new Electric Vehicle (EV) brand from Geely, a Chinese automotive company, turned to Southco in search of a custom fastening solution to be implemented in an integrated foldable table for its new ZEEKR 009 model.
Southco engineers formulated a hinging solution which enables constant resistance, silent operation even under vibration or dynamic loads, as well as facilitating smooth 180° operation without requiring any adjustments.
E-Z LOK has revealed its intention to build a portfolio of both pull-out and torque out test data for its range of metal, plastic and wood inserts.
Available on the E-Z LOK website, the data will be housed under the ‘Resources’ section with links for specific product groups. Additionally, the company will create PDFs of the testing data on a product group basis.
Laser Tools has added a 15 piece VDE insulated socket set to its range of EV and hybrid insulated tools and safety equipment, designed for reliability.
VDE certified and manufactured to IEC 60900 standards, the set features 15 fully insulated ⅜ inch drive sockets, a 200mm long 45 tooth ratchet, as well as two extension bars. The set is supplied in a heavy-duty plastic case with a routed foam tray to securely hold tools in place.
With the MDR series featuring two clamping nut types – MCA and MDA –JAKOB Antriebstechnik offers a universally applicable power clamping nut with a lateral operating hexagon and through-hole thread.
In connection with variable length T-slot screws or clamping bolts, the through-thread enables a flexible application with different clamping heights or tool thicknesses. Compact dimensions also allow for use in limited access areas and a robust material design helps to ensure high-quality.
In automated environments, quality control relies on continuous measurement and test data monitoring. To address this, norelem has introduced a new line of modular clamping systems for metrology.
Providing a flexible, modular solution that adapts to the evolving needs of various industries, norelem’s systems are designed to use minimal clamping force, making them ideal for quick and efficient set-ups.
Rapid are a proud British Manufacturer of fasteners and turned parts. We manufacture a comprehensive range of standard threaded fasteners in various materials, including steel, stainless steel, brass, and specialty alloys such as INCONEL, DUPLEX, and SUPER DUPLEX.
Our team of experienced fastener engineers are experts in producing custom, precision components tailored to your specifications and technical drawings.
In-house bespoke manufacturing 48 machines across three sites
Full certification Nationwide delivery
SPECIALISTS IN U-BOLTS, ACCREDITED TO ISO 9001: 2015 QUALITY MANAGEMENT SYSTEM.
We have a vast array of stock itemsmanufactured in-house - to BS3974 & Light Pattern. Available in HDSG, BZP and 316 (A4) Stainless Steel We also stock a range of N-Bolts and can manufacture a variety of other bolts including:
Hook-Bolts, J Bolts, Sq. U-bolts, Sq. Hook Bolts, L-Bolts and C- Bolts.
STANDARD & BESPOKE SIZES, IN METRIC OR IMPERIAL
MANUFACTURING SIZE RANGE:
• M6 – M24 (Metric Coarse)
• 5/16” – 3/4” (Imperial – BSW & UNC)
• Drawn Mild Steel Rod (Gr 4.6)
• ASTM A193 B7/ A320 L7 (Gr 8 –High Tensile)
• 316 (A4) & 304 (A2) Stainless Steels
3 Star Rivet 131
310 Express 100
Abbey Clamps 15
Achilles Seibert GmbH 11
Acton 182
Advance Spares 167
AGTOS GmbH 86
Albert Pasvahl GmbH + Co 9
Alexander Paal GmbH 69, 109
Ambrovit SpA 13
Apex 183
APM Hexseal 177
Aramid Technologies, INC (SmartCert) 168
ASF Fischer B.V 129
Astrotech Steels Private Ltd 149
Atotech Deutschland GmbH & Co KG 81
Bäcker GmbH & Co KG 101
BBA Fasteners Srl 125
Beijing Jinzhaobo High Strength Fastener Co Ltd 171
Bendfast 198
Berardi Group 151
Bodegraven Metaal N.V 169
Bossong 113
Bralo S.A 129
Brighton Best International 87
Brugola OEB Industriale SpA 93
BTS GmbH 76
Buora D.P.U. Srl 133
CAMCAR Innovations™ (TORX® Ttap) 191
CBAMBOO 165
CEIA 85
Cetin Civata 23
Chavesbao 21
Chin Tai Sing Precision Manufactory 35, 36
Colombo Special Fasteners 163
Don Quichotte B.V 82
DS Fasteners 182
Eurobolt B.V 97
Eurofast 99
Fastbolt 2
Fastener + Fixing Magazine 159
Fastener 2000 GmbH 66
FastFixSearch.com 195
Huge Range of Metric & Imperial Blanks
Grades 4.6, 8.8, 10.9, 12.9; R, S, T, V, SAE8
UK’s largest stocks of BSF & BSW
Special Head Shapes
Most Materials including Exotics
Excellent Prices & Delivery
Over 150 years’ experience in UK
FastFixTechnology.com 175
Fastener Fair Global 75
Fixi Srl 15
FM Metal Fasteners Group SpA 91
Fong Prean Industrial Co Ltd 41
Fuchs+Sanders GmbH + Co KG 67
Fuerniss GmbH 127
G & B Fissaggi Srl 143
Gala Precision Engineering 7
Graewe GmbH & Co KG 157
Grand Metal 169
Growermetal 123
Guede GmbH 97
Hafren Fasteners Ltd 85
Haiyan Jiamei Hardware Manufacturing And Tech Co 31
Halfmann Schrauben GmbH 70, 135
Hariton Machinery Company Inc 157
HECO-Schrauben GmbH & Co KG 105
HEICO Befestigungstechnik GmbH 127
Heller Tools GmbH 115
Hisener 4, 5
Index 3
Industrias Deu 185
Jiangsu Yongyi Fastener Co 27
ETA-CE anchors for structural applications, including C2-C1 categories,for use in high seismic hazard zones.
New wave, big hair, shoulder pads — not everything from the 1980s was designed to last forever. On the other hand, Nord-Lock invented the original wedge-lock washers that have been trusted to secure bolted joints ever since we began innovating the technology in 1982.
By using geometry instead of friction, Nord-Lock washers prevent bolts and nuts from loosening unintentionally. Engineers ask for them by name, and they’re a standard-bearer for safety in construction and industry. So, as the world changes through the decades, remember that a Nord-Lock washer is made to last.