#43008019agreementmailPublication INSIDELOGISTICS.CA CANADA’S SUPPLY CHAIN MAGAZINE CanadianINCLUDING:NOWShipper AUGUST 2022 TheAWARDSCHOICESHIPPERS2022bestcarriersinCanada › How two Ontario 3PLs use WMS › Preventing MH injuries › Fleet electrification
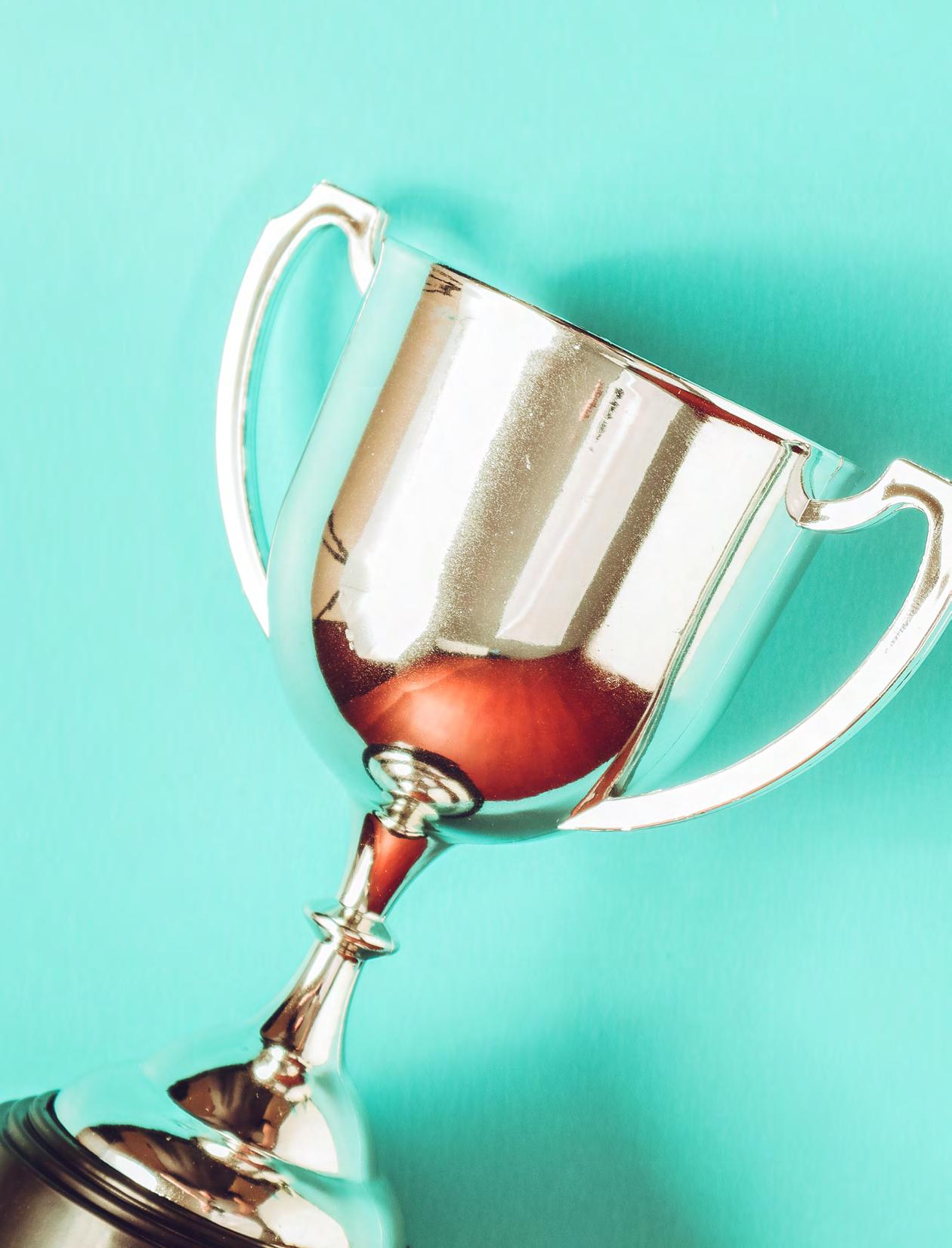
Expanding Our Global Reach www.cargojet.com Canada’s Cargo Airline
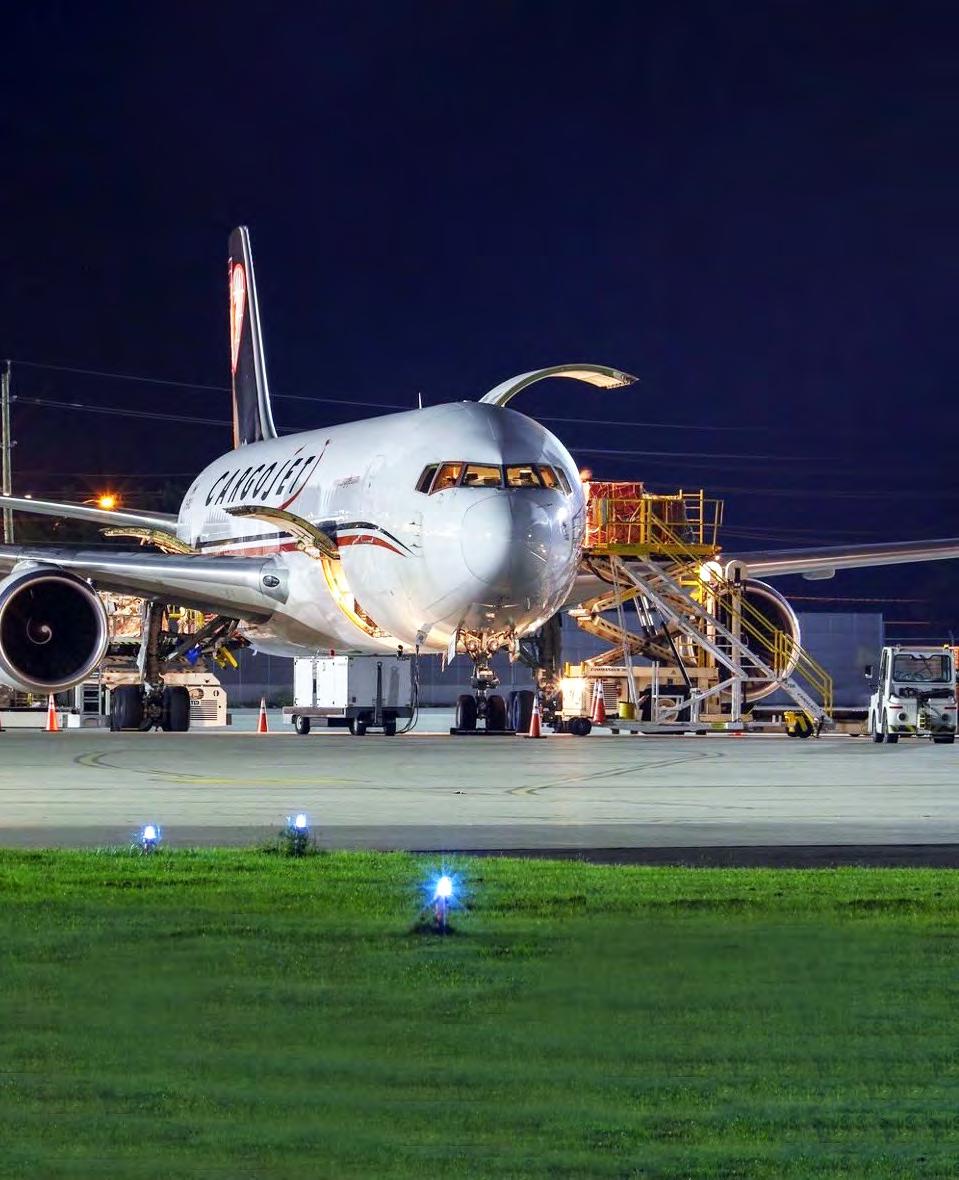
insidelogistics.ca 3 In every issue: 5 Taking Stock Are EVs the answer? 6 Supply Chain Scan News and numbers from around the world 11 Movers + Shakers Appointments and promotions 29 Trade Update Forced labour 30 Safety First Preventing material handling injuries CONTENT S 4 Publisher’s message Meet Turnkey Media Solutions, Inside Logistics’ new owners 14 Digitization Yard management - the overlooked answer to congestion 28 Real-time Visibility See who’s been out and about in the supply chain community 6 cover image: Nattapol_Sritongcom/ Adobe Stock ON THE COVER | PAGE 17 SUPP LY CHAIN SCAN Flying whales | Rivian on the road | EV incentives | Cando sold Young professional award | Walmart’s big reefer AUGUST 20 22 • VOLUME 67 • NUMBER 04 CANAD A ’S SUPP L Y CHAIN MAGAZIN E INCORPORATINGNOWCANADIANSHIPPER 4 2814 12inWMSaction
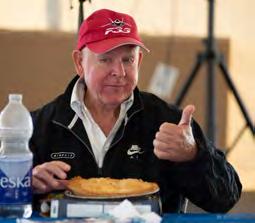

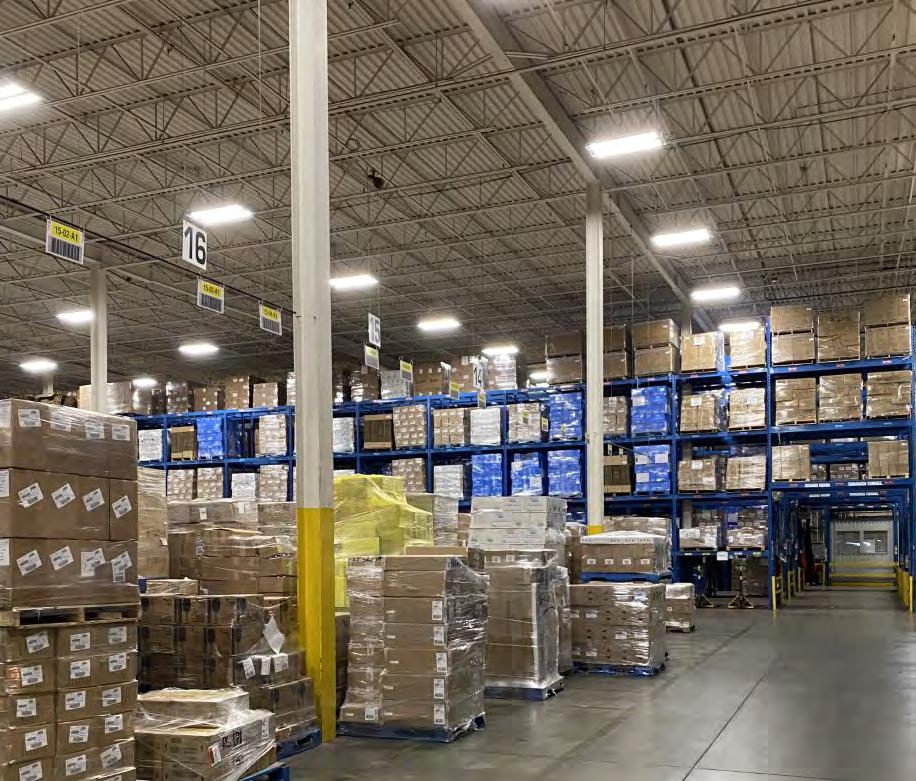
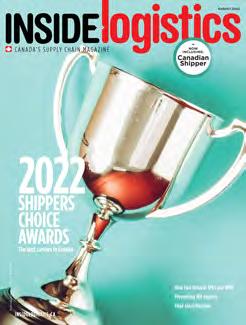
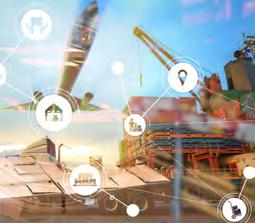
Director of Sales & Partnerships

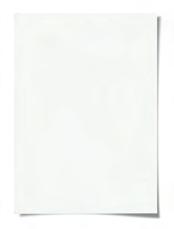
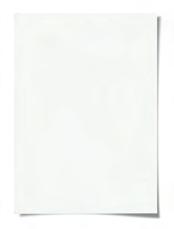
As sales manager on Inside Logistics in 2018 and 2019, I fell in love with the industry and saw my place in it immediately. I found success in this industry, and with the magazine, by following Turnkey Media’s philosophy: serve our readers first by providing the best analysis and most up-to-date information available.
like the pandemic and the growth of e-commerce, this is a market with tons of potential. We aim to capitalize on that and build the magazine into an even bigger and better product.
Turnkey Media Solutions Inc. 416 459 0063
Turnkey Media Solutions Inc. 585 653 6768 peter@turnkey.media
I’m delighted to be making this announcement in the first issue of Inside Logistics under Turnkey Media Solutions management. All of us here look forward to continuing the almost 70-year legacy of this great Canadian title with your continued readership and support.
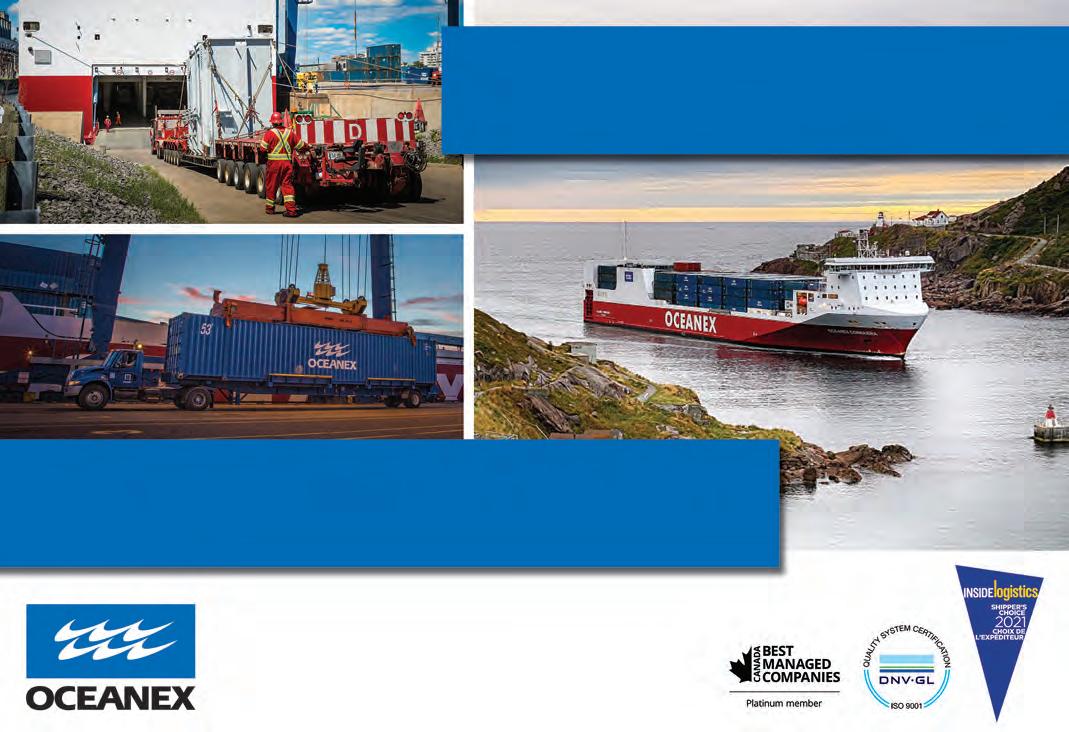
My business partner, Peter Bulmer, and I founded the company in 2019. After building our publishing careers working for other leading publishers in various industries, we decided it was time to work for ourselves.
Peter and I are excited to be your new publishers for Canada’s supply chain industry news source. Whether you are a reader, an advertiser, or just curious about the industry, we’re always here to chat about anything in the magazine, or anything that’s not. We’re looking forward to getting to know you all. My contact details are below, please drop me a note or give me a call – I’d love to hear from you.
HELLO!
We are here to introduce ourselves as the new owners of Inside Logistics. We are Turnkey Media Solutions Inc., an upand-coming, new-generation publishing firm.
We are happy to announce that Emily Atkins, who is celebrating her 20th year with the magazine in 2022, will be continuing to direct the excellent editorial product. Her expertise and industry knowledge will ensure that Inside Logistics is the best source of information and analysis for Canadian supply chain professionals.
Joining the team as art director is Samantha Jackson, who also recently began working on our automotive titles. A creative and professional designer, Samantha is a tremendous asset to the magazine.
We started out purchasing a group of automotive industry titles from Newcom Media. You may be familiar with Jobber News and CARS (Canadian Auto Repair & Service) magazines.
PUBLISHER’S MESSAGE

Delon Rashid Managing Partner

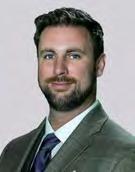
When the opportunity arose to buy Inside Logistics from Newcom, we knew it was a good fit for our company. As Canada’s supply chain magazine, Inside Logistics is well respected, and recognized as the authoritative source of supply chain business information in this country.
Peterdelon@turnkey.mediaBulmer
With the recent evolution in supply chain, thanks to factors
DELON RASHID PETER BULMER
Production and Ad-ops | Tracy tracy@turnkey.mediaStone
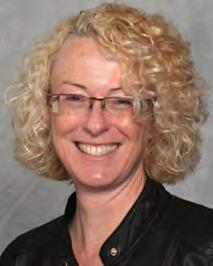
It’s not that EVs won’t be the future – progress is being made every day to improve range and performance. However, I believe that – with the exception of Amazon – they aren’t quite ready for prime time.
Are EVs the future?
Nonetheless, the progress being made towards commercial fleet electri fication is impressive. Manufacturers are turning out excellent, purpose-built vehicles like the Rivian vans for Amazon, or our own home-grown Lion Electric trucks.
AMAZON ROLLS PAGE 10.
On the face of it these are positive developments. Done right, EVs can be run more cheaply than ICE vehicles, and have numerous environmental advantages. But that is based on a couple giant assumptions.
OUT RIVIAN VANS ON
Canada Post Canadian Publications Mail Sales Product Agreement No. 43008019

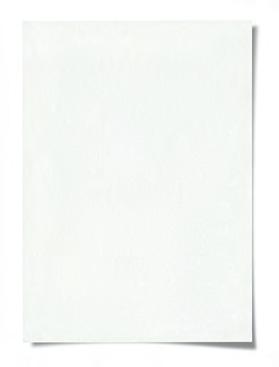
Publisher | Delon Rashid (416) delon@459-0063turnkey.media
From time to time we make our subscription list available to select companies and organizations whose product or service may interest you. If you do not wish your contact information to be made available, please contact us.
ISSN Online0025-53431929-6460
TAKING STOCK
“Return Postage Guaranteed” Send change of address notices, undeliverable copies and subscription orders to: Circulation Dept., Inside Logistics magazine, 48 Lumsden Crescent, Whitby, ON, L1R 1G5
WE HAVE A COUPLE of stories in our news section this issue about electric vehicles. In one, Amazon is rolling out its custom-designed Rivian delivery vans for last-mile deliveries across many US cities. In the other, the Canadian government is offering significant incentives to businesses buying electric work trucks.
To end on a personal note, I want to say how delighted I am to be reunited with Delon Rashid on Inside Logistics. I’m looking forward to continuing to build this magazine with a great new team!
But Canada poses some challenges to electric vehicles. Cold weather deteriorates EV performance, and our vast geography and thinly spread population mean that the urban delivery model is not applicable to sig nificant portions of the population.
Sales | Delon Rashid, (416) 459-0063 peter@Peterdelon@turnkey.mediaBulmer,(585)653-6768turnkey.media
President & Managing Partner | Delon Rashid Head of Sales & Managing Partner | Peter Bulmer
Contributing Writers | Norm Kramer, Christian Sivière, Matthew Wittemeier, David Branson
Video / Audio Engineer | Ashley Mikalauskas, Nicholas Paddison
insidelogistics.ca 5
Corporate Office 48 Lumsden Crescent, Whitby, ON, L1R 1G5
Inside Logistics magazine is published by Turnkey Media Solutions Inc. All rights reserved. Printed in Canada. The contents of this publication may not be reproduced or transmitted in any form, either in part or full, including photocopying and recording, without the written consent of the copyright owner. Nor may any part of this publication be stored in a retrieval system of any nature without prior consent.
The use-case for urban last mile delivery is strong. Shorter routes, defined hours of service, and the ability to return to a depot every night provide good conditions for EVs. Likewise the middle mile is an equally good place to deploy EVs. Fixed, repeatable routes make sense, allowing the planning of charging times and locations.
The first is that companies wanting to adopt EVs will be able to obtain the charging infrastructure they need at a cost that doesn’t make running the EVs prohibitive. What’s seldom mentioned in the push for EV adoption is the cost and complexity of establishing a charging infrastructure for a sizeable fleet. Buying chargers and installing them is one of the last steps. Before that is finding out if the electrical utility can even supply the amount of power needed. When new transformers have to be installed and new conduit run, the bills get hefty. And that’s not even looking deeper into the utility’s larger capacity to handle dozens or hundreds of companies seeking electrification of their fleets.
Inside Logistics magazine (ISSN No.: 0025-5343 (Print); 1929-6460 (Digital) is published six times per year by Turnkey Media Solutions Inc., 48 Lumsden Crescent, Whitby, ON, L1R 1G5
Editor | Emily Atkins (416) emily@turnkey.media262-4106
Creative Director | Samantha Jackson
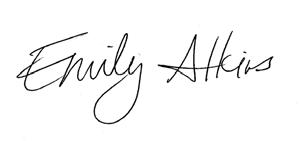
“Flying Whales is taking another step in its growth, where Quebec expertise will enable the development of a new generation of aircraft,” said Pierre Fitzgibbon, Quebec’s minister of econ omy and innovation, and minister responsible for regional economic development.
WALMART’SREEFER
Originally designed to meet the needs of log ging in hard-to-reach areas, the LCA60T’s hov ering, loading and unloading characteristics will provide solutions for heavy-lift logistics chal lenges around the world, with a low environmen talThefootprint.blimp is 200 metres long and 50 metres in diameter. Its 60-ton payload will be contained in a 96- by eight- by seven-metre cargo hold that
11 SUPPLY CHAIN SCAN |
enough in 2023 to be spun off into a subsidiary.”
“The aeronautical program and its developmentimplementationindustrialarewellunderway,andtheactivitiesforthefutureairlineandairportcompanywillbemature
First refrigerated60-foottrailerhitstheroad
EDMONTONHUB
andAppointmentspromotions
FLYING WHALES IS planning to build the LCA60T, a rigid airship for heavy load transport with a carrying capacity of 60 tons.

“Quebec is a world leader in aerospace. We must focus on innovation to keep this strength here and create economic spin-offs here.”
8
6 INSIDE Logistics AUGUST 20 22
9 SHAKERSMOVERS+
This new funding will allow the company and its consortium to finalize the development of the LCA60T aeronautical program in France and Quebec, and to accelerate the work neces sary to launch Flying Whales Services, an oper ating company.
Blimp maker secures funding
It has received 122 million euros in new fund ing from the French government, and other investors, including Investissement Québec. The Quebec government, through Investissement Québec, is already a 25 percent stakeholder in theFlyingproject.Whales was founded in 2012 and is sup ported by a consortium of 40 French and Canadian aeronautical companies.
by Emily Atkins
can be loaded and unloaded during flight. Lift will be provided by unpressurized helium contained in rigid cells, and propulsion will come from seven different zones, enabling vertical take-off and landing. Maximum speed is said to be 100 Currently,kmh. the prototype blimps are operating on hybrid electric power, and will be fully elec tric once operational, the company said. The environmental footprint is also reduced by elim inating the need for ground-based loading and unloading infrastructure.
– Sébastien Bougon, Chairman and CEO of Flying Whales
2,000 acres developedbeingforcargo
Bringing Structure and
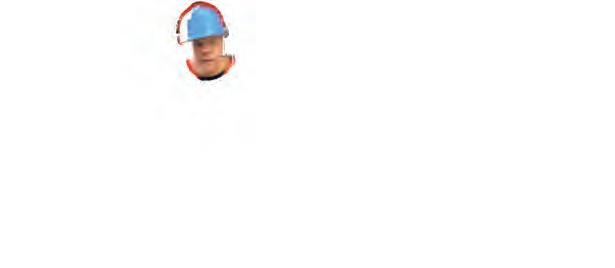
The Incentives for
Alberta Investment Management Corporation buys Cando Rail & Terminals
Cando was founded in 1978 and is headquartered in Brandon, Manitoba. It operates a network of 40-plus industrial railyards, nine owned terminals and one shortline railroad.
Discipline,
Feds unveil EV incentives for commercial vehicles
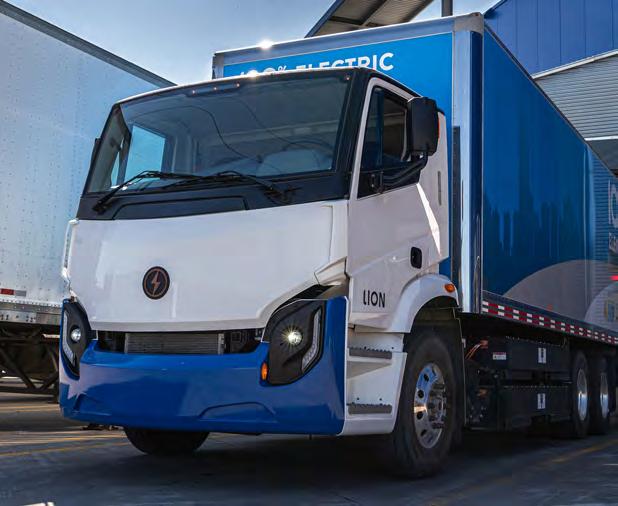
These incentives will apply to the purchase or lease of commercial medium- and heavy-duty zeroemission vehicles such as the Ford e-Transit cargo van, the Karsan e-Jest shuttle, the Lion8 vocational truck, the Volvo VNR-electric tractor truck, and more. Zero emission vocational on-road trucks (e.g., refuse or dump trucks) will be eligible, as would yard/shunt and drayage trucks. Zero-emission shuttle or coach buses will also be eligible. Vehicles that have been converted to electric will not be funded.Businesses and provincial or territorial and municipal governments operating fleets are eligible for up to 10 incentives (or a maximum of $1,000,000) under the program each year.
(iMHZEV) Program began on July 11. Scheduled for four years, the program will help businesses and communities across the country make the switch to zero-emission vehicles with close to $550 million in Battery-electricincentives. vehicles (BEVs), plug-in hybrid electric vehicles (PHEVs), and fuel cell electric vehi cles (FCEVs) are all eligible.
Visibility to the Supply www.rfpathways.comChain RF_P_third square.indd 1 2022-07-04 3:33 PM insidelogistics.ca 7 | SUPPLY CHAIN SCAN
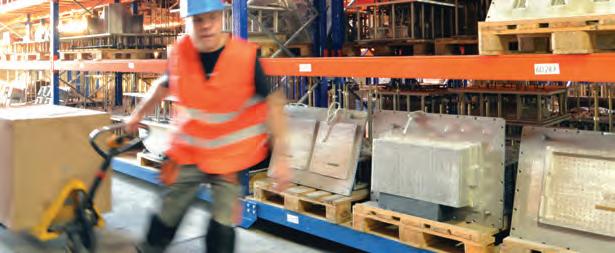
The company has more than 400 active employee shareholders, who collectively own 25 percent of the business. There will be no changes to the company’s operations or management as a result of the transaction.
THE FEDERAL GOVERNMENT has unveiled incentives for the purchase of medium and heavy-duty electric vehicles. Medium- and Heavy-Duty Zero-Emission Vehicles
The program offers purchase incentives for approximately half of the price difference between an electric vehicle and a traditional vehicle. The incentive tops out at $200,000 per vehicle (for a class 7/8 coach), and can be combined with provincial or territorial incentives.
AUTOMATION ASSOCIATES INC. 6705 Tomken Road, Suite 211, Mississauga, Ontario L5T 2J6 905-565-6560
THE ALBERTA INVESTMENT Management Corporation (AIMCo) is acquiring a 100 percent equity stake in Cando Rail & Terminals Ltd. from TorQuest Partners.
Edmonton getting new air cargo hub
8 INSIDE Logistics AUGUST 20 22
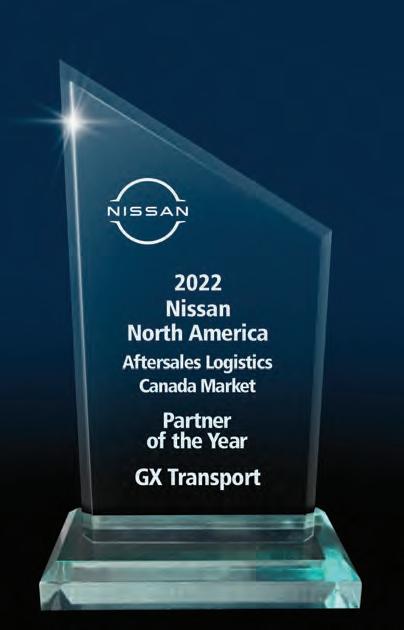
SUPPLY CHAIN SCAN |
nities is a global game changer. It drives the growth of small and medium enter prises in Alberta and the rest of Can ada, which creates jobs and spurs investment.”Ruthalsosaid the federal investment into EIA will help accelerate its plan to position Edmonton as a multi-modal global logistics centre and vital trade corridor for Canada. He added that the new hub will be “transformational” for the Edmonton Metro
acre cargo handling hub will be built at the airport
A NEW CASH infusion will see the development of a new cargo handling zone at Edmonton International Air port (EIA).
A 2,000 acre cargo handling hub will be built at the airport. The federal government has put up $100 million under the National Trade Corridors Fund for the project, which is expected to begin in 2023.
The new handling capacity is expected to expand the airport’s dis tribution reach in Canada as well as the United States and Mexico.
“Cargo and logistics play a major role in our region’s economic growth and development,” said Tom Ruth, president and CEO of Edmonton International Airport.
“Increasing air capacity and market access for exports and trade opportu
2000Region.
Canadian wins regional young forwarder award
FIATA (INTERNATIONAL FEDERATION OF Freight Forwarders Associations) and TT Club have revealed this year’s regional win ners of the Young Logistics Professionals (YLP) Award 2022.
Canadian entrant Karina Daniela Perez Perez won in the Americas region for her dissertation: Resilient Solutions: The Future of Freight Forwarding and Logistics. She works at DSV Air & Sea in the ocean exports department.PerezPerez was selected by CIFFA in January as the Canadian Young Logistics Professional of the Year, after a review of her industry experience and a written dissertation demonstrating her technical knowledge.PerezPerez‘s paper illustrates the trans Continued on Page 9
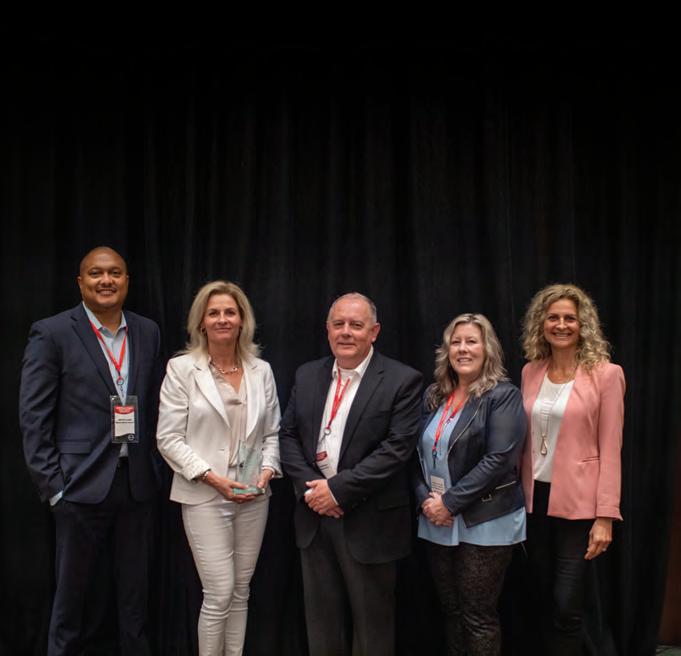
portation of two key products for the Canadian economy, the challenges that freight forwarders must overcome to successfully deliver goods, and the resiliency of the supply chain with a focus on sustainability.
WALMART CANADA’S fleet has expanded to include its first 60-foot multi-temperature refrigerated trailer. It’s also the first of its kind for Walmart in North America.
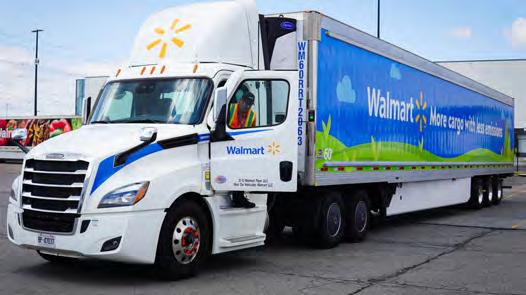
Walmart Canada adds first 60-foot reefer
The custom-built multi-temperature refrigerated trailer allows the retailer to ship more freight to stores in a single trip, resulting in improved efficiency and lower CO2 emissions.
“All four regions were represented by a variety of impressive entries and the judges were struck by the high incidence of projects requiring close consideration of environmental factors and prioritizing sustainability,” said Mike Yarwood, managing director loss prevention, TT Club, and chair of the panel of judges.
The increased capacity and multi-temperature zones allow for better routing and delivery planning. The company says it can now pair certain stops that would not normally ship on the same
Thetrailer.trailer was built by Utility Trailer Manufacturing Company, which adjusted its manufacturing capabilities to make it possible.
“We never tire of reading about the innovative approaches to logistical challenges employed by our youngThisprofessionals.”year,ifconditions allow, the four regional win ners will present their dissertations at the FIATA World Congress in Busan, South Korea, during a dedicated session with the final judging and announcement of the YLP Global Winner 2022.
Karina Daniela Perez Perez
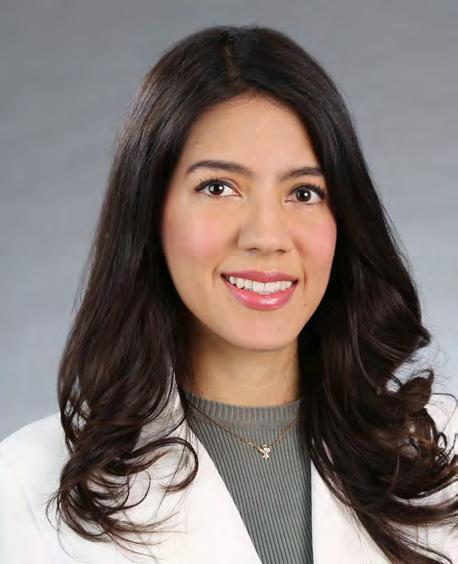
In 2012, Walmart initiated a pilot program with the Ontario Ministry of Transportation to introduce 60-foot trailers to Ontar io’s roads.
The trailer is being used on routes between the company’s Mis sissauga distribution centre and stores in Windsor and Woodstock. It can carry up to 30 pallets of perishable goods – like meat and dry or wet produce – requiring different temperatures. That’s four more than a standard 53-foot trailer.
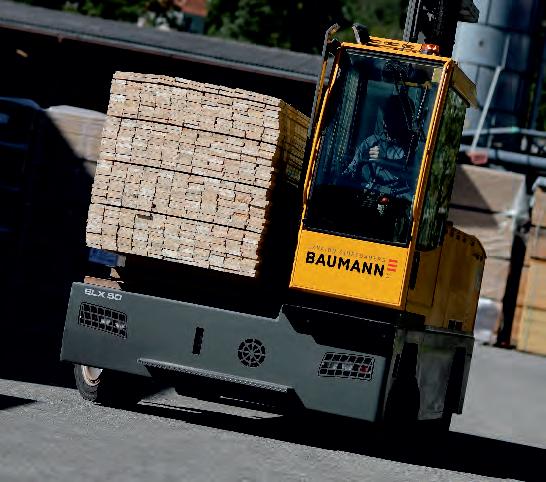
insidelogistics.ca 9 | SUPPLY CHAIN SCAN
“This is a truly custom solution, purpose-built for Walmart Canada to help us bring innovation to the industry and work towards reaching our regeneration goals,” said Brian Sookhai, senior manager, transportation innovation and planning at Walmart Canada.
Recipient of the “Shipper’sChoice”Award2012to2022&“CarrierofChoice”Award
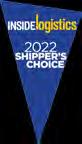
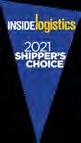
Amazon has been testing deliveries with Rivian pre-production vehicles since 2021, delivering over 430,000 packages and accu mulating over 90,000 miles. Rivian has also completed certifications with the National Highway Traffic Safety Administration, California Air Resources Board, and US Environmental Protection Agency.
Amazon rolls out electric delivery vans
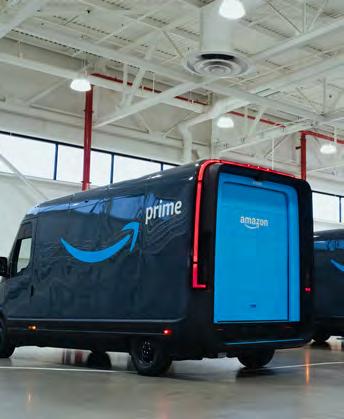
Amazon expects the vehicles will con tribute to its sustainability goals by reduc ing carbon emissions.
Operating from seven terminals in Canada and the USA, we offer swift and reliable truckload service to most of North America. That, combined with our no nonsense commitment to customer service has helped Penner become the transportation provider of choice for customers who need to keep their promises, wherever they need to ship in North America. As a shipper’s “Carrier of Choice”, our promises do get delivered... consistently.
be on the road in more than 100 cities by the end of this year, with 100,000 deployed across the US by 2030.
TERMINAL LOCATIONS Mississauga, ON Winnipeg, MB Saskatoon, SK Regina, SK Calgary, AB Edmonton, AB Vancouver, BC Fargo, ND www.Penner.ca Toll Free 866.729.7134
OUR PROMISES GET DELIVERED penner_insidelogistics_halfpagead_2022.indd 1 2022-07-27 11:39 AM
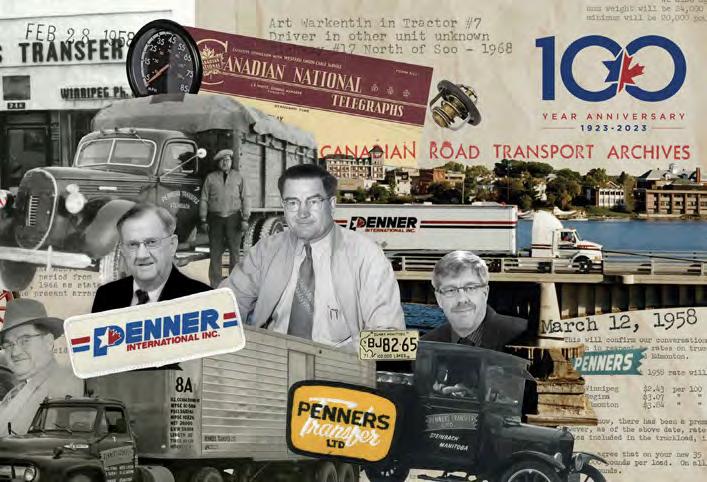
To support the addition of EVs into its fleet, Amazon has added thousands of charging stations at its delivery stations across the US. Amazon has also partnered with the nonprofit CERES, and several other fleet operators to launch the Cor porate Electric Vehicle Alliance, bringing together companies to accelerate the tran sition to electric vehicles.
The vehicles are made at Rivian’s fac tory in Illinois. They incorporate autono mous safety features along with embedded routing and navigation technology that integrates the delivery workflow with the vehicle. They also have special capabilities to speed up the delivery process including automatic door locking and unlocking as the driver approaches or leaves the vehicle, and a powered bulkhead door that opens when drivers reach their delivery location.
10 INSIDE Logistics AUGUST 20 22 SUPPLY CHAIN SCAN | Over 350 Power Units and 800 Trailers Fully EDI capable Up to date Technology Single point of contact 99 years of experience Cross border TL carrier
Starting July 21 the vans hit the road loaded with customer parcels in Baltimore, Chicago, Dallas, Kansas City, Nashville, Phoenix, San Diego, Seattle, and St. Louis, among other cities. The company says it expects thousands of the electric vans will
AMAZON HAS BEGUN putting its custom-designed Rivian electric delivery vans on the road across the United States.
Amazon and Rivian announced the plan to jointly develop the vans back in 2019.
π SHIPPING SUPPLY SPECIALISTS COMPLETE 1-800-295-5510CATALOG uline.ca
Logistec Corporation has appointed Dany Trudel as vice-president and corporate con troller. He succeeds Carl Delisle, who is now the chief financial officer. Fluent in English,
NFP has appointed Evan Garner to its newly created executive leadership team. Based in Montreal, Garner joined NFP’s Complex Risk Solutions Group in 2021. He has 20 years of industry experience.
Kuehne+Nagel has promted Dianna Fiora vanti-Ashikwe to managing director for Can ada. Fioravanti-Ashikwe was most recently as vice-president, sales and marketing, Kueh ne+Nagel Canada. Before this, she was the managing director of Nacora and GFH Canada (K+N subsidiaries). She earned degree in polit ical science from the University of Waterloo and a CIP designation from the Insurance Insti tute of Canada. She is executive co-sponsor and board member of the Canadian Women in Logistics Leadership (WILL) chapter.
French and Spanish, Trudel has over 20 years of experience in the financial field and has led accounting teams at prominent world-class Insurercompanies.
movers + shakers
FedEx Corp. has promoted Brie Carere to be the compa ny’s first chief customer officer. She also was named co-presi dent and co-CEO of FedEx Ser vices, a role she will share with Rob Carter, executive vice-president and chief infor mation officer. Carere joined FedEx in 2001 and most recently served as chief marketing and communications officer. Previously, Carere was vice-president of marketing, customer experience, and corporate communications for
Mitch Whitnack and Robb Sollows have joined Carton Cloud as implementation specialists. Ottawa’s Sollows is an industry veteran of more than 40 years. His previous experience includes positions at Trimble Transportation, Trans Plus and TMW Systems. Vancouver-based Whitnack has five years of experience in logistics and has been responsible for several warehouse man agement software implementations in BC.
insidelogistics.ca 11 | SUPPLY CHAIN SCAN OVER 2,700 TAPE PRODUCTS IN STOCK ORDER BY 6 PM FOR SAME DAY SHIPPINGBIG DADDY BIG MAMA
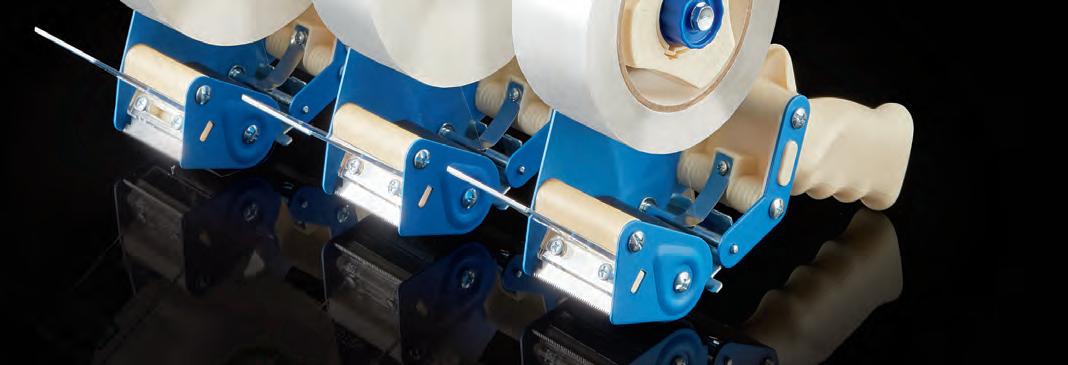
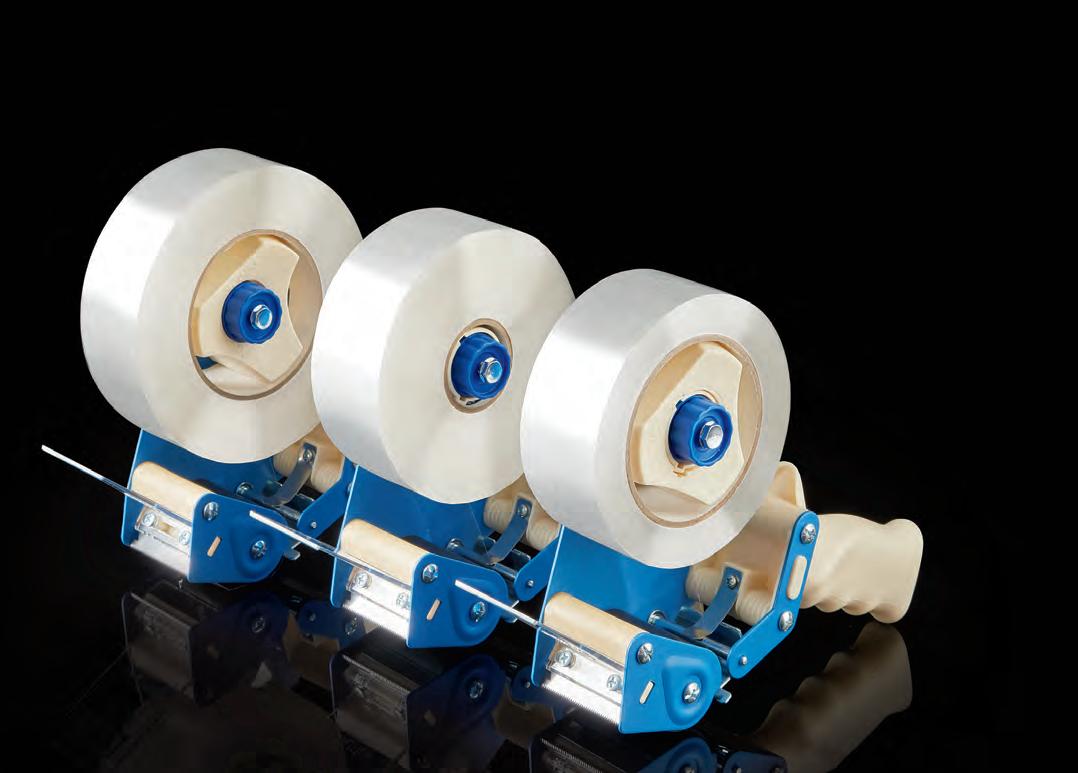
Brie Carere
INDUSTRIAL
PortsToronto has appointed Roelof-Jan (RJ) Steenstra as president and chief executive officer, effective in September. Steenstra comes to PortsToronto from the Fort McMurray Air port Authority where he has served as presi dent and CEO since 2016. He is also currently chair of the policy board of the Canadian Air ports Council (CAC), and a director on Airports Council International – North America (ACI-NA) executive committee. Steenstra steps into the role previously held by Geoffrey Wilson, who is retiring.
FedEx Express Canada. She founded a Women in Leadership community during her time with FedEx in Canada. Originally from Ontario, Carere earned a degree in commerce from McMaster University.
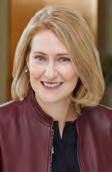
hen you’re in the warehousing and transportation business, getting bigger is not as simple as adding warehouse space and trucks. The experiences of a cou ple logistics service providers in the Greater Toronto Area demonstrate the importance of having the right technology to underpin growth.
For Cavalier, which runs a 200,000-square-foot facility in Bolton, Ontario, north of Pearson airport, the RF Pathways sys tem was an upgrade from a legacy set-up. Their old WMS was an outdated Unix-based green-screen system that required a lot of manual inputs for receiving and inventory control, said the com pany’s warehouse manager, Tony Saunders. It had been in use for about 15 years before it became obvious that an upgrade would be
12 INSIDE Logistics AUGUST 20 22 DIGITIZATION | By Emily Atkins
Cavalier Transportation Services and QRC Logistics have both been growing to meet demand. And the two companies realized they needed to improve their ability to manage inventory if they were going to successfully expand. Separately, they decided to adopt a warehouse management system from Mississauga, Ontar io-based Automation Associates (AA).
Modernizing at Cavalier
“Weneeded.wanted a more modern, Windows-based, user-friendly
After doing a full comparison of the different systems, Cavalier felt that they’d get “more bang for the buck” from AA. “It did all the things we were looking for at a much better price point,” SaundersImplementationsaid. was a year-long process, as the two compa nies worked together to design the software and customize the warehouse with the necessary barcoding. Start-up began with smaller customers being brought online first because they could be launched without shutting down operations. The final initial ization, with larger customers, was done outside of work hours.
system,” he said. “We needed to move to RF (radio frequency) guns and have our warehouse barcoded – aisles, bays, pallet spots etc – for ease of receiving and better inventory control through automation.”Cavalierevaluated the options from numerous WMS vendors in a process that took about a year, before deciding on Automa tion Associates. The smaller, local company made it into the mix against the likes of heavy-hitters Tecsys, Red Prairie, Maves and Great Plains because Cavalier’s founder George Ledson knew the company.
Saunders explained that each customer had to have a profile established within the software with all their SKUs. The pro cess required manually associating all stock with unique license plates, which means physically touching every pallet in inventory.
MANAGINGGROWTH
W
Logistics providers opt for WMS to help accommodate expanding business
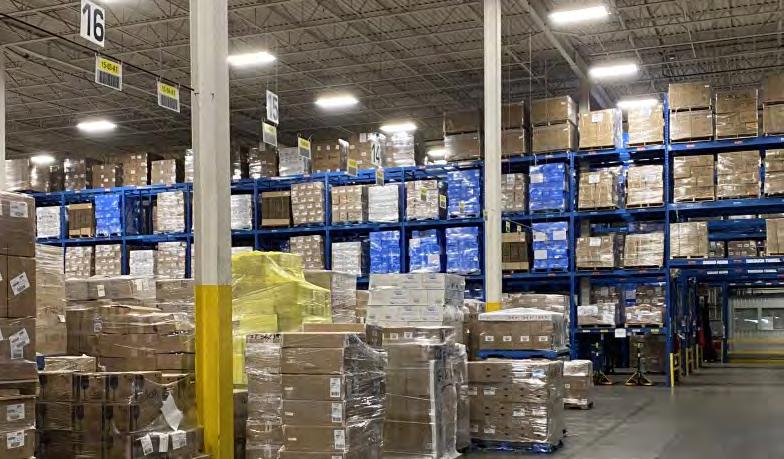
Cavalier’s vice-president and general manager, Brian Ledson, is happy with the way the warehouse performs with RF Pathways. “Tony’s the main man that has to work with it. We just try to give him the, the best tools that we can to operate as efficiently and in the best way we can. As far as I’m concerned, Automation Associates is forthright, they’re timely, and they get me what I need. It’s a good relationship.”
Another deciding factor was the ability to pivot quickly and get things customized for QRC’s customers and pro cesses. RF Pathways’s EDI capabilities also helped to auto mate a lot of data entry and streamline the pick process, DrewImplementationnoted. took eight to 10 weeks. “We did not stop our operations,” Drew said. “We had to stop only for a few hours when we wanted to switch the system to transfer real time inventory into RF Pathways.”
The real proof is in customer satisfaction. Drew recount ed: “Realtime visibility of inventory and their orders has been really appreciated by our customers and we no lon ger get phone calls asking how much inventory is on hand. This means the coordinator can focus on processing orders rather than answering customer calls.”
insidelogistics.ca 13
The largest customer at the time had about 3,000 pal lets in the warehouse, and it took a team of 10 people a full day to register all of them in the system. “We got it done in about seven hours, in one day,” Saunders explained. “With that particular customer, we had to have it completely done so that there would be no downtime. We planned it so that we wouldn’t have any days where we weren’t able to pick.” For the smaller clients, Saunders and his lead hand would stay for four or five hours after shift and add them to keep the operation moving.
QRC’s ten-fold expansion
B2C orders, accounting for an average of 18,000 to 20,000 items that get delivered by courier, LTL or TL, in-house or outside carriers. Picks range from an inner each, to a case, master case or a skid.
consideration was that AA is a local company. Drew said he wanted to be able to lean on them for in-per son training, and “with our company growing at the speed it is, it was very important to not overspend on capital and time required for set up and implementation.”
The bulk of the work was identifying dimensions, weights and pallet ti-hi’s so that clients’ SKUs could be correctly configured. “We received the majority of the information from our clients but some things we had to do on our own, which required a dedicated team just creating SKUs in spreadsheets to be imported,” Drew recounted.
“We are able to provide our customers with a level of ser vice that would not have been possible previously,” he add ed. “Every pallet is fully tracked from the moment it is re ceived, through to the day it is shipped, giving us the ability to provide our customers with the data indicating where each carton is shipped from a specific receipt. Included in the software is a link to an online portal where the custom er can generate a variety of inventory reports.”
Since implementing the system, Cavalier has found they are better able to maximize the space in the warehouse to generate more revenue. Previously, staff had inventory lo cations memorized, so they specialized in certain parts of the warehouse. “They had one account that they were re sponsible for, right from putting it away, to picking the or ders and shipping them out,” Saunders said. “Now, anybody can pick any order in the building without prior knowledge or experience picking a particular customer.” It means la bour can be more efficiently deployed.
If there’s a flaw, Saunders said, it’s the system’s inabili ty to create back-dated inventory reports. But generally, he is impressed with the system and the service from AA. “They’re great to work with. Any time there’s an issue, even if it’s not necessarily their issue, if it’s an issue on our end, they’re quick to jump in and help find a solution,” Saunders said. “I think because they are a bit of a smaller operation they’re able to better service the customers they have.”
Drew said that getting staff up to speed was the most sig nificant challenge in the whole process. “There is always re sistance to change no matter how good a system,” he noted. “But once the team started using it and realized how much easier it was for them, everybody loved it.”
Since going live, the operation has seen dramatic oper ational improvements. Picking accuracy went up from 85 percent to 99.78 percent. Inventory accuracy for every cli ent is approximately 99.2 percent. Order picking time has been reduced by 25 percent. As well, the system allows for better insight into inbound and outbound schedules on a day-to-day basis, while being able to consolidate while re ceiving has helped with space optimization.
Drew noted that QRC assessed multiple vendors before choosing RF Pathways. “RF Pathways came out to be most cost-effective, local, hands-on provider with a great team,” he Asaid.major
With that kind of throughput, the company needed a “ro bust WMS system, that could deliver inventory control and better visibility and management of the floor,” said James Drew, QRC’s president. Its requirements included inventory control; picking and packing accuracy; cycle counting; pickroute optimization; 3PL billing; and customer visibility.
For QRC Logistics based in Halton Hills, Ontario, grow ing into a 300,000 square-foot warehouse that is 10 times bigger than its previous space was the catalyst for needing a new WMS. The operation includes 24-hour pick, pack and ship operations. An average day sees 800 to 1,000 B2B or
“If their cartons and pallets had barcodes, we added them, which helped with the initialization,” Saunders said.

14 INSIDE Logistics AUGUST 20 22 DIGITIZATION
LET’S FACE IT, the global supply chain has not been operating at peak perfor mance for many years. The pandemic just made things worse, highlighted its weaknesses and led to persistent shortages and bottlenecks across all links in the supply chain, from labour and materi al shortages to air, ports, trucks, rail, warehouses and yard constrictions.
all-too-common occurrence even though many companies recognize the potential benefits a YMS can provide. Consequently, they suffer from a host of problems, ranging from difficulty locat ing equipment and inventory, to high costs from dwell and detention fees, to overtime labour costs, and error-prone manualMonitoringoperations.keyperformance indi cators (KPIs) becomes extremely dif ficult, yet it is critical that yard opera tors be able to benchmark key metrics, including gate, carrier, yard jockey, and equipment metrics.
While trailer yards are just one of the elements in global supply chains, they do play a critical role. When they’re backed up and congested, they slow down everything from in- and outbound transportation to order fulfillment.
The handling of in-bound trailers can also be optimized using priority load per formance management. Here, containers with time-critical content arriving on inbound trailers may be designated for im mediate unloading, leaving standard-load trailers to be stored until a dock becomes available. Outbound trailers with priority loads can also be prioritized for discharge from the Additionalfacility.features that may be worth the investment are AI and machine learning enabled systems that can run autonomously and make routine digital decisions.
To mitigate supply chain challenges, optimize resources and improve pro ductivity and customer satisfaction, dis tribution centres have turned to yard management systems (YMS). Delivering digital decision-making support, they offer many benefits.
State of yard management Yard management improvements have been largely neglected. Organizations instead focused on their warehouse and transportation management pro cesses. As a result, yards have stayed inefficient, burdened by manual pro cesses that have yard jockeys following verbal orders conveyed over a radio, and scrambling around searching for trailers or inventory located somewhere in the Thisyard.isan
Transparency and more
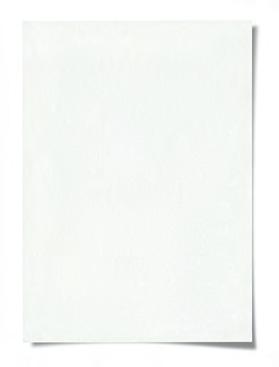
A YMS should have standard, digitized gate processes which help expedite truck check-in and out. Both fully automated and manual processing should be supported, as well as communication within the software when a situation is not consistent with the plan (e.g., the arrival of an unplanned truck). The YMS lets dispatchers manage exceptions within their larger plans and communicate directly to gate staff without requiring a phone call or email.
To provide the greatest value, a YMS should be designed and configured to support standardized processes and data needs. This allows KPIs to be eval uated to further improve operations.
YARD MANAGEMENT – THE OVERLOOKED ANSWER TO CONGESTION CHALLENGES
As a starting point, it should deliver full transparency of on-site trailers and yard resources. By logging every incoming and outgoing asset and their movements while in the yard, the YMS eliminates time wasted by yard jockeys trying to locate a trailer or other equipment. This also improves yard safety by reducing the number of individuals conducting chaotic searches.
Added value and future proofing Additional features go beyond these to deliver the extra added value, which re
duces ROI time from years to months. Regardless of the number of yard trucks, yard vehicle optimization can reduce vehicle travel and deliver fuel savings, decrease maintenance and increase asset lifes pan. For large yards with many trucks, a high-performance yard optimizer can cut the number of needed by a third while still delivering the same service quality. This can also contribute to sustainability initiatives.Dockdoor optimization automates routine dock door decisions, freeing up dispatchers to concentrate on services that contain costs and generate value. Leveraging complete knowledge of dock door parameters and status ensures that the YMS adheres to both fixed and vari able constraints. Real-time information regarding trailers at the dock is fed to facility staff and, using handheld devices, they are able to supply critical information regarding unloading/loading processes to the YMS
An on-time performance feature also delivers value. With this, a YMS system can receive scheduled trailer arrival and discharge times from a transporta tion management system (TMS). Using the schedule, vehicle processing can be optimized by the YMS to maximize the on-time departure of outbound trailers. When a trailer arrives late, but needs to leave first, it can be prioritized for un loading/loading ahead of trailers that can depart later.
MATTHEW WITTEMEIER is a director marketing and sales at INFORM’s terminal and distribution centre logistics division
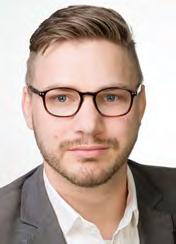
To do this, they’ll need to take the time to understand your business and its unique needs. Ask, “are they more focused on selling themselves or understanding my business?” If it’s the former, move on. If it’s the latter, they’re worth considering.
DAVID BRANSON is vicepresident of managed transporta tion operations, TA Servicess
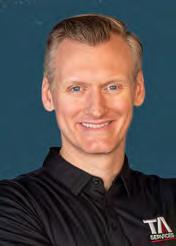
Practical benefits
When properly used, a TMS can give businesses greater supply chain visi bility and improved decision making. When supply chain bottlenecks occur, businesses can know exactly where their products are and identify alter natives to ensure timely delivery. No more wondering where your products are and hoping they make it to their final destination.
Short and long-term ROI Companies using a TMS can begin seeing positive ROI both right away and con tinuously. In the short term, they can cut costs through rate shopping and automate previously manual tasks such as tracking and customer billing.
At its worst, it can be underutilized, turn ing what sounded like a good idea into a costly mistake.
Whenwith?”selecting a 3PL to outsource your transportation management needs to, keep these tips in mind:
Accessing an up-to-date database of carriers and capacity sourcing tools al lows businesses to become more vendor agnostic, choosing to work with the car rier that offers the best prices.
insidelogistics.ca 15 DIGITIZATION
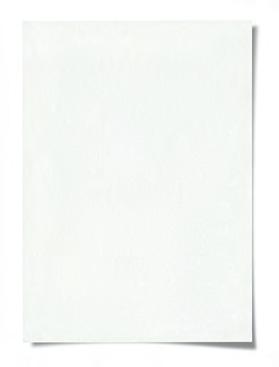
With an end-to-end solution, you’ll gain visibility over your entire supply chain.
Gain the power of a transportation management system without having to manage it
Businesses seeking a smarter supply chain are presented with a dizzying array of TMS options, ranging from piecemeal solutions, to end-to-end, enterprise level systems. If they select one, they then need to either train ex isting employees to run this complex software or hire new employees with specializedHowever,skills.formany companies, out sourcing transportation management functions to a third-party logistics pro vider may be the right solution. This allows businesses to stick to their core competencies and leave transportation management to the experts. These ex perts will not only know the best TMS solutions, but their highly trained teams will also know how to use them, applying their full power for the unique needs of any given business from day one.
TMS takes into consideration shipment characteristics to determine the best routing, and can update if things like weight, freight class, or services change. This allows your company to quickly fac tor these changes into prices.
Selecting a managed TMS provider
AT ITS BEST, a transportation manage ment system (TMS) enables businesses to plan, execute, manage, and optimize the movement of goods in a supply chain.
1 Pick a partner you trust and enjoy working with Make sure this provider is someone you trust and is continuing to evolve their product offering. The ideal third-party logistics (3PL) partnership is for the long term. Picking a partner that you can trust for years to come will allow you to gain maximum value from their expertise, helping your processes get better with age.
Over time, transportation manage ment software allows for continuous improvement. Rather than maintaining data in silos, the centralized data and analytics of a TMS, paired with indus try expertise, can lead to a finely tuned, custom supply chain strategy that will
A TMS offers continuous route opti mization. If using a GPS to route around traffic on a 30-minute commute saves five to 10 minutes, imagine the time saved by implementing advanced route optimization across an international supply chain.
If you’re a large company with the capi tal for an in-house team of IT and trans portation experts, purchasing a TMS solution and hosting it on site could be the right solution for you. However, for many companies, the question should not be “which TMS solution should I purchase?” but rather, “which man aged transportation provider should I partner
2 Make sure your partner offers a truly customized solution
By optimizing routes and allowing for quick, data-driven solutions to evolving problems, businesses can keep custom ers happy with increased reliability. Car rier partners will also appreciate this. Maintaining positive relationships will ensure that your company is a shipper of choice for carriers.
A TMS provides multiple avenues for carrier capacity and dynamic rating. In a fluid market, companies with a clear carrier solution and technology strategy are best equipped to adapt and win. A
save time and money in the long term.
THE PROMISE AND THE PITFALLS OF TMS
3 Ensure the TMS offers an end-to-end solu tion and can integrate with your existing ERP
Fragmented solutions result in inef ficient processes, incomplete data, and ultimately cost your business money.
The digital age has inflamed business owners’ DIY impulses. This leads manu facturers and retailers, with the best of intentions, to enter the complex world of transportation management.
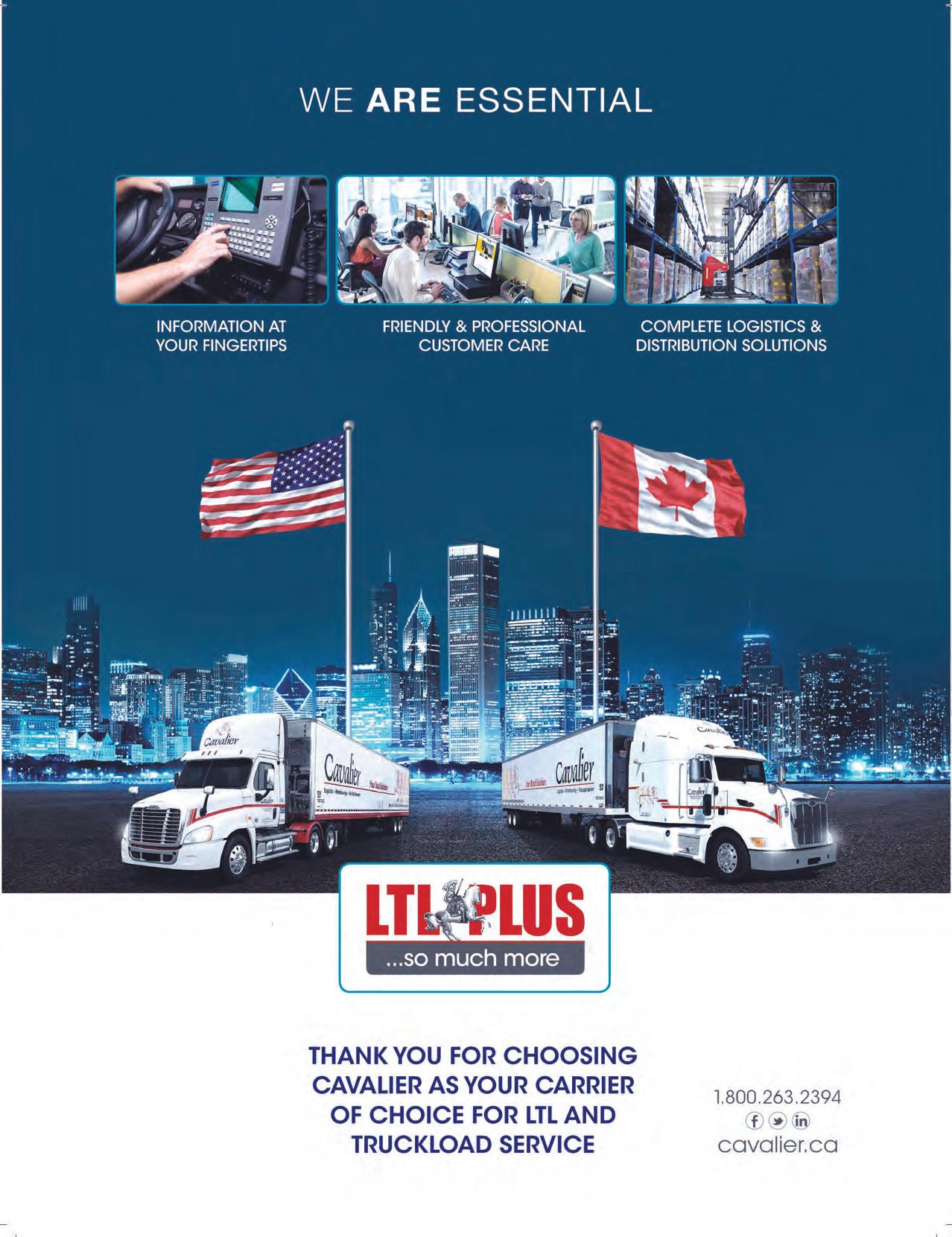

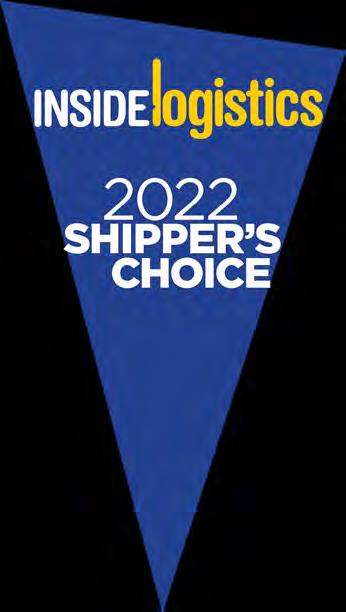
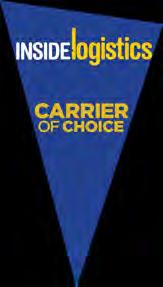
ockAdobeStNattapol_SritongcomImage: SUPERL A TIV E surveyexcellencesurpassareTheCARRIERS2022Shipper’sChoiceAwardspresentedtothecarrierswhotheindustry’sbenchmarksofaccordingtoourannualoftransportationbuyers.
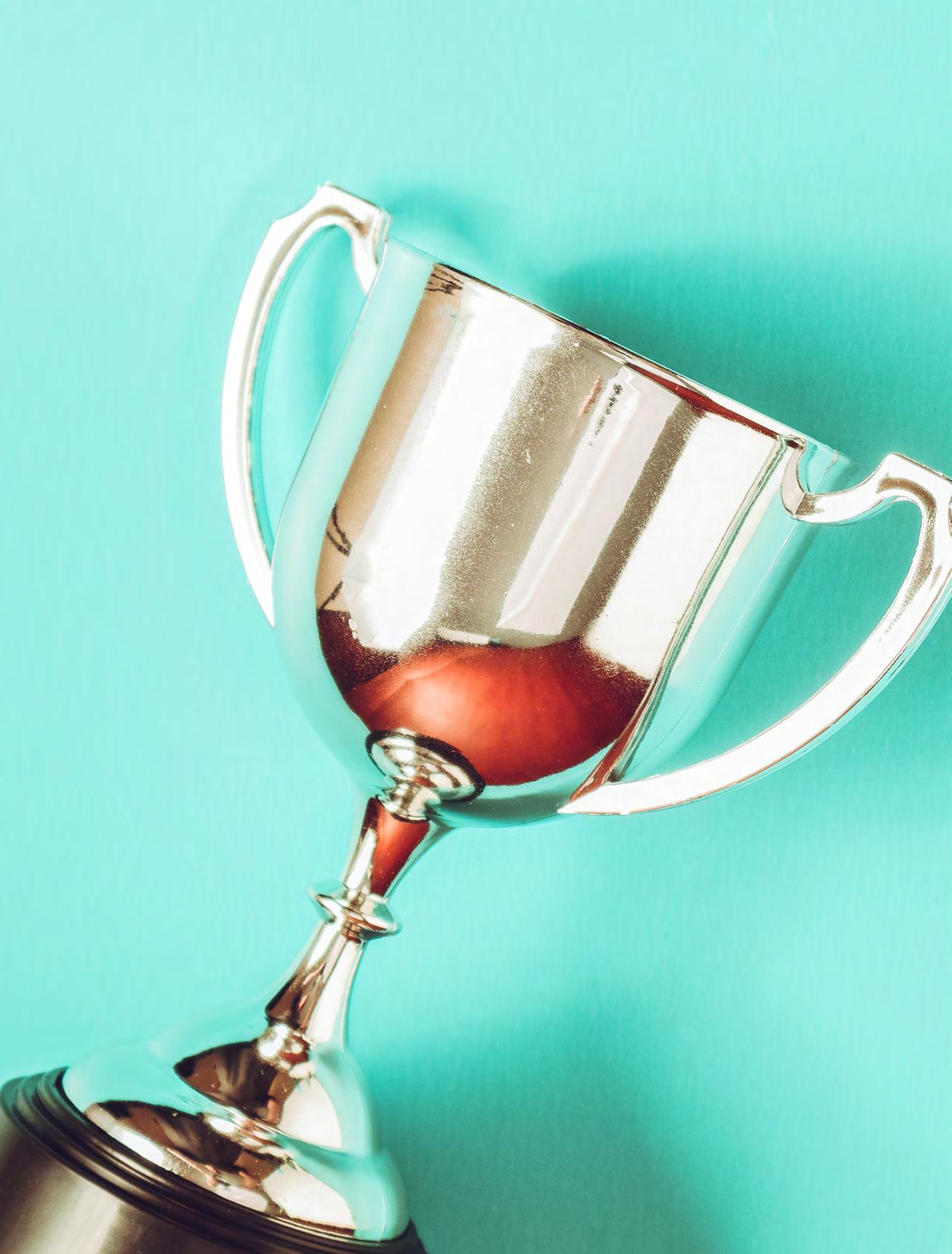
Mode On-time Qu ality of In formation Co mpetitive Cu stomer Le adership Ab ility to Su stainable per formance eq uipment & te chnology pr icing se rvice in problem pr ovide tr ansportation oper ations sol ving va lue-added pr actices ser vices LTL TRUCKING 4. 694 4. 399 4. 213 4. 671 4.713 4. 474 3. 810 4. 032 TL TRUCKING 4. 804 4. 533 4. 221 4. 660 4.716 4. 549 4.110 4. 204 AIR CARRIERS 4. 839 4. 475 4. 565 4. 661 4. 677 4. 500 3. 946 3. 964 OCEAN CARRIERS 4. 528 4. 396 4. 423 4. 679 4. 604 4. 415 4.140 4. 098 RAIL CARRIERS 4.700 4. 474 4. 350 4 .575 4 .550 4. 525 4. 030 4.108 COURIERS 4. 829 4. 373 4. 561 4.704 4. 671 4. 428 3. 827 4 .088 Importance of Performance Criteria
SHIPPER’S CHOICE AWARDS |
he annual Shipper’s Choice Awards measure how well carriers perform against our Benchmarks of Excellence. The scores are established by shippers, 3PL service providers, and freight forwarders from across Canada in our annual survey. These transportation buyers rate each of their top three carriers on a five-point scale against eight key performance indicators, and use another five-point scale to rate the importance of the key performance indicators themselves. The weighted rankings are deter mined by multiplying the two numbers together. These
T
18 INSIDE Logistics AUGUST 20 22
EXPLAINING the scores
weighted rankings are then compared to the Benchmarks of Excellence, which represent averages of the weighted scores for each category’s key performance indicators.Fifteencarriers met or exceeded the bench marks established for the 2022 awards. Six companies earned the coveted Carrier of Choice designations because they have scored above the benchmarks for at least five years in a row (see page 27).
To qualify, carriers need to receive a minimum number of evaluations. To prevent tampering, we watch for multiple submissions by known respondents; look for similar IP addresses; and if carriers have invited customers to submit scores, we compare those email addresses to our own database.
Rail
18 .16 18 .00 16 .45 15 .54 15 .88
16 .11
The methodology
Air
This year 339 respondents – buyers of transportation services, and those who manage shipments handled by freight forwarders or 3PL providers – completed our survey.
TL
WHO ANSWERED THE SURVEY Mode On -time Qu ality of Inf ormation Co mpetitive Cu stomer Le adership Ab ility to Su stainable To tal pe rformance equi pment & te chnology pri cing ser vice in problem pro vide tr ansportation comb ined ope rations sol ving va lue-added pra ctices sc ore ser vices

LTL Trucking 19.75 19.12 17.51 20.15 20.14 18 .42 15 .98 16 .69 147.760 Trucking 21.06 20.22 17.36 19.99 21 .16 19.62 17.56 17.79 15 4.756 Carriers 20.42 19.26 18 .92 18 .91 19.34 18 .00 15 .52 15 .65 146.008
Ocean Carriers 16.98 17.45 17.50 135.971 Carriers .63 12.92 15 .21 130.849 17.06 .43 13 .91 15 .75 137.554
The Shipper’s Choice Awards Survey is undertaken through a continuing partnership with CITT and the Freight Management Association of Canada (FMA), and conducted by an independent research firm.
EXPLAINING THE SCORES Shipper Satisfaction Ratings By Mode 49% respondents339 answered the survey of respondents spend more than 40% of their budget on transportation 36.6% MANUFACTURING 19.8% LOGISTICSTHIRD-PARTY 15.0% RETAIL 10.3% FREIGHT FOWARDING 18.3% OTHER Respondents’ Industry Sector 1 – 20% 38.7% 21 – 40% 12.4% 41 – 60% 15.6% 61 – 80% 14.2% 81 – 100% 19.1% Percentage of budget spent on transportation
15
insidelogistics.ca 19
17.26 17.63 17.15 17.95 16
Couriers 19.93 17.92 18 .66 18 .89
This
Formerly Atlantic Truck Show, largest, most trucking and logistics show. is THE venue where products that
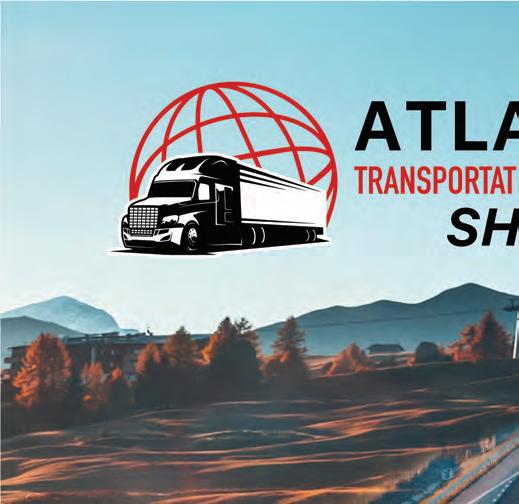
this is Atlantic Canada’s

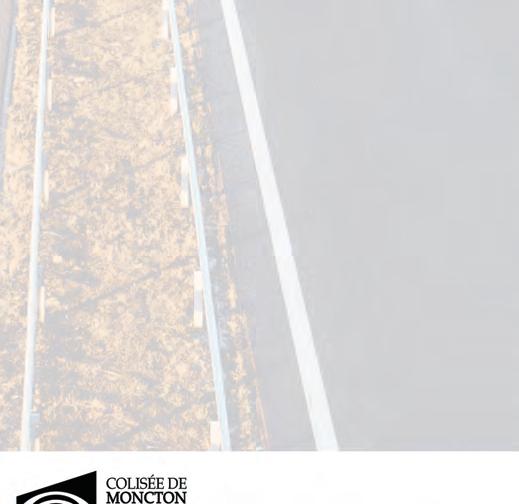
and services
keep the truck, transportation, and logistics industry moving, day in and day out. Fleet managers, buyers, and distributors will all be out in full force, looking to talk with your sales and technical sta to plan their next purchase. NEW This year! LIVE Logistics & Warehousing Operation We will be showcasing the most innovative technology and products, including Warehousing Systems, Racking and Conveyor Systems, Storage Containers, Forklifts, GPS, Loading + Unloading Technology, Inventory Software, Telematics, Refrigeration + Cold-Chain Logistics and the list goes on... Booth spaces are selling quickly - don’t miss out on this exceptional business opportunity to generate new leads, build relationships with customers, and increase your sales! For more information and to secure your exhibit space at this premier event, please contact: Mark Cusack, National Show Manager • mcusack@mpltd.ca • 506.333.1064 Andrew Burns, Exhibit Sales • aburns@mpltd.ca Toll Free: 1.888.454.7469

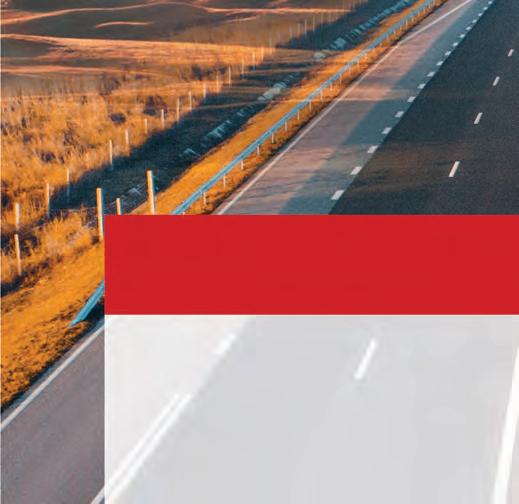
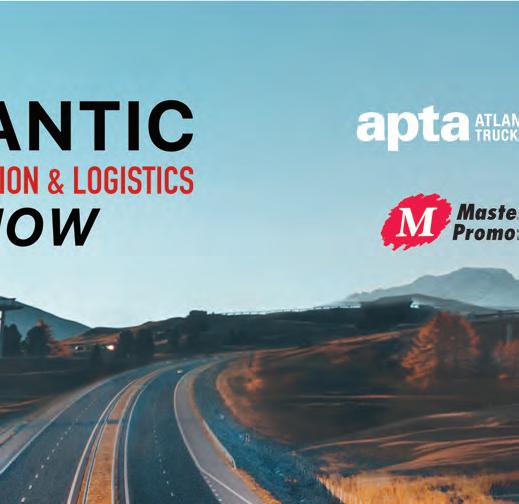
MONCTON, NBwww.ATLS.ca
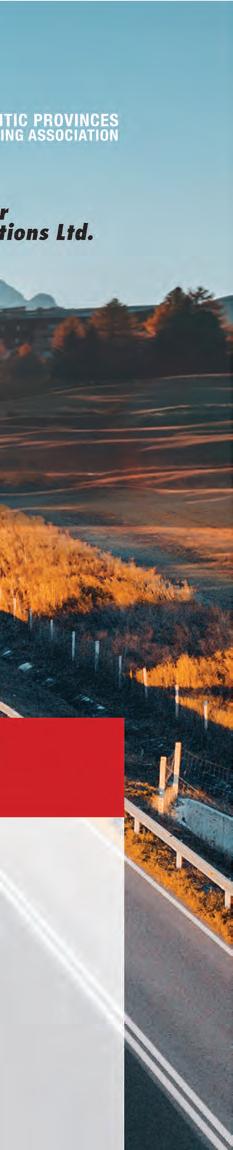
Presented by: Produced by:
the
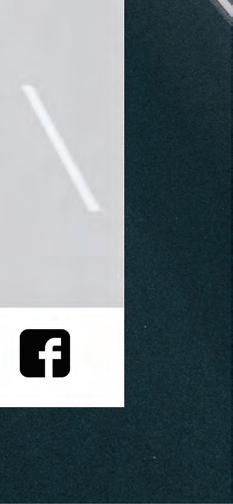
OCTOBER 20-21, 2022 Business
Driving
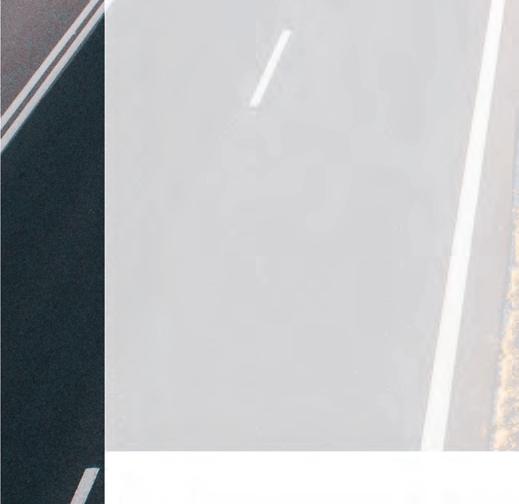
inclusive
buyers source out the
.73 Cavalier Transport 21 .14 18 .13 19 .42 20 .50 21 .69 20 .47 19 .73 19 .34 Maritime Ontario 21 .62 20 .40 19 .70 20 .97 22 .01 20 .47 18 .50 19 .62 Bourassa Transport 21 .20 21 .06 17.38 19 .46 21 .36 20 .34 18 .50 18 .78
iStockfranckreporter,Image: Services On-time
Penner International 22 .10 22 .67 19 .42
TL WINNERS
he TL mode has historically been the toughest for carriers to score above the Benchmark of Excellence. The TL mode had the highest benchmarks in six of the eight KPIs tracked by this year’s Shipper’s Choice Survey: on-time performance, quality of equipment and operations, customer service, leadership in problem solving, ability to provide value-added services, and sustainable transportation practices. Six TL carriers surpassed the Benchmark of Excellence this year. Quality of Inf ormation Co mpetitive Cu stomer Le adership Ab ility to Su stainable pe rformance equi pment & te chnology pri cing ser vice in problem pro vide Tr ansportation ope rations sol ving va lue-added Pr actices ser vices .49 22 .78 23 .32 22 .21 20 .04 20 .28 22 .37 23 .58 21 .84 18 .08 18 .50 21 19 19
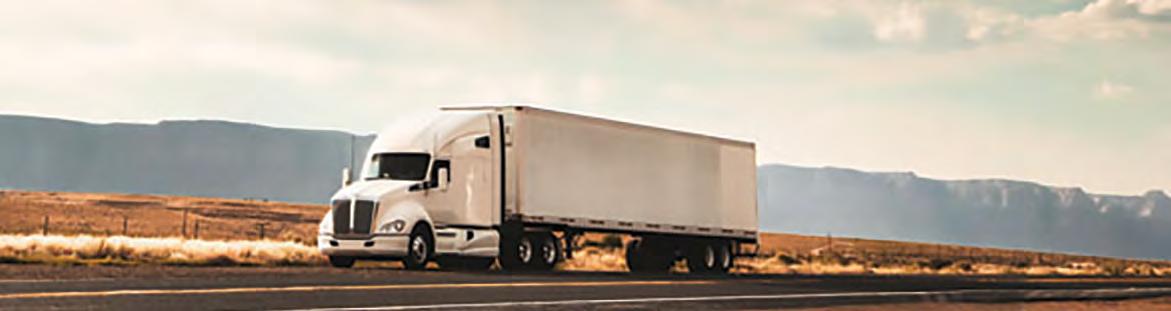
insidelogistics.ca 21 2022 SHIPPER’S CHOICE | continued from pages 18 & 19 Benchmark of Excellence 21.06 20 .22 17.36 19 .99 21 .16 19 .62 17.56 17.79
Hercules 23
All Connect Logistical 22 .42 21 .76 19 .42 22 .30 23 .58
T
21 .66 20 .17
.67
.53
THANK YOU FOR SUPPORT!CONTINUEDYOUR 1.800.409.2269 info@polaristransport.com OF PERFORMANCEWINNINGAWARD CONSECUTIVE

.32
.94
.51
M
Excellence. M-O.COM On-time Quality of Inf ormation Co mpetitive Cu stomer Le adership Ab ility to Su stainable pe rformance equi pment & te chnology pri cing ser vice in problem pro vide Tr ansportation ope rations sol ving va lue-added Pr actices ser vices Benchmark of Excellence 19.75 19.12 17.51 20 .15 20 .14 18 .42 1 5.98 16 .69 Hercules 22 .12 20 .71 19 .56 22 .05 22 .95 21 .08 17.77 18 .92 All
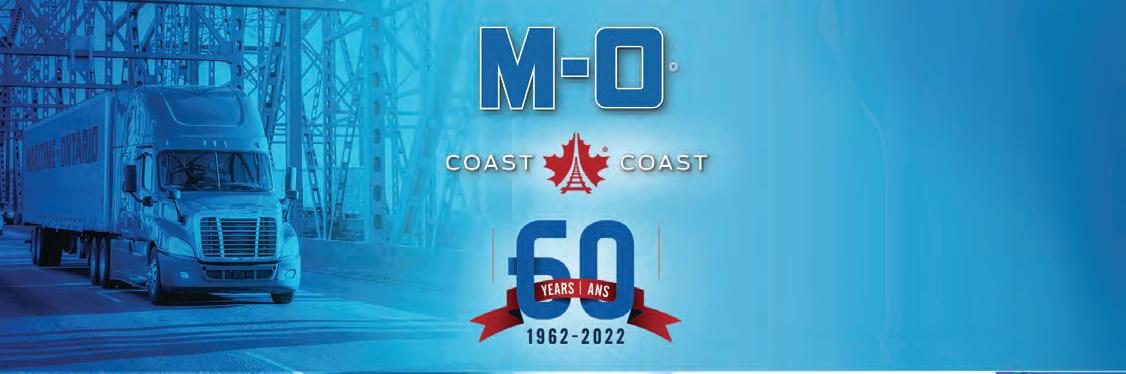
LTL WINNERS
.38
18 .14 Polaris 20 .48
insidelogistics.ca 23 2022 SHIPPER’S CHOICE | continued from page 21

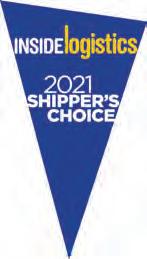
surpassed the
value-added
iStockstockvisual,Image:
anaging so many different shipments sharing space on one trailer and touchpoints between terminals makes the LTL business complicated. The demands from buyers of LTL services are high and carriers have to navigate a tightrope between providing excellent customer service while keeping prices competitive. year’s survey found LTL carriers had the highest benchmark for competitive pricing, and second highest for customer service, leadership in problem-solving, ability to provide services, and sustainable transportation practices. Four LTL carriers Benchmark of Connect Logistical 22 23 21 17.86 19 18 .94 21 21 .05 19 .73 16 .96 17.89 .46 20 .04 18 .51 19 .68 21 .54 20 .55 17.15 17.90
Services 22 .43 20 .96 19 .43
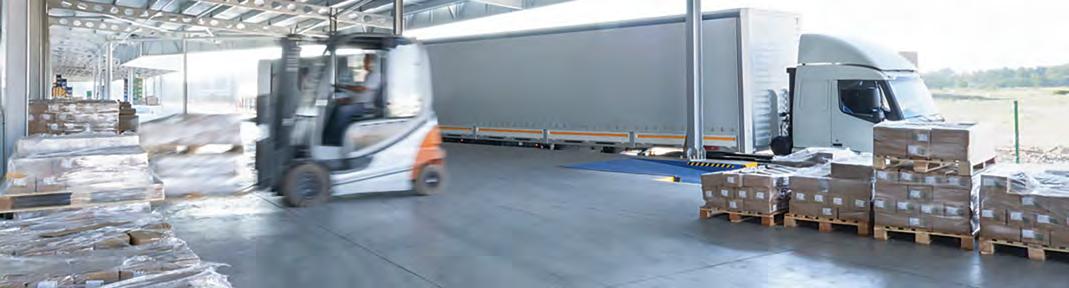
This
.30
Bourassa 21
herculesfreight.com Learn more at youtube.com/user/herculesfreight There comes a time in every traffic manager’s life when they want to start seeing other carriers. That’s us — nice to meet you!
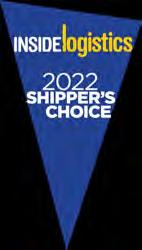

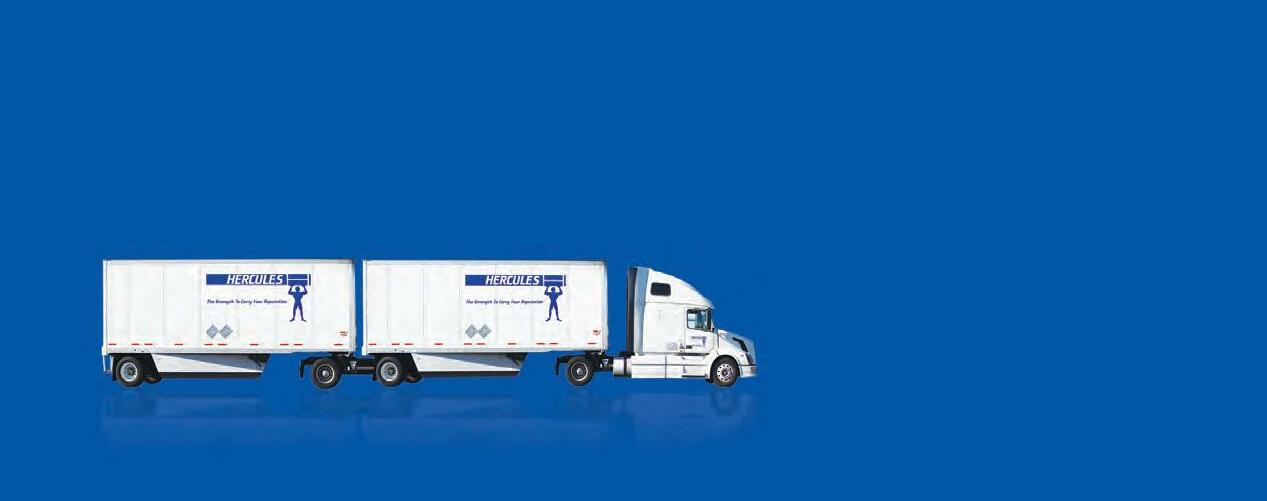
uyers of courier services have high expectations when it comes to shipment tracking and speed of delivery, so it’s no surprise this mode had the second highest benchmark for information technology and that on-time performance was the highest benchmark for the mode. Five courier companies made the benchmark this year.
B
ir carriers have the third highest overall Benchmark of Excellence this year. Buyers of air freight services have particu larly high expectations when it comes to on-time performance, setting the highest individual benchmark in the air category this year. For air carriers information technology was deemed the most important, and this was also the highest score across the modes. Two air freight carriers surpassed the Benchmark of Excellence this year.
insidelogistics.ca 25 2022 SHIPPER’S CHOIC E | continued fro m page 23
COURIER WINNERS
On-time Quality of Inf ormation Co mpetitive Cu stomer Le adership Ab ility to Su stainable pe rformance equi pment & te chnology pri cing ser vice in problem pro vide Tr ansportation ope rations sol ving va lue-added Pr actices ser vices Benchmark of Excellence 20.42 19 .26 18 .92 18 .91 19 .34 18 .00 1 5.52 15 .65 KLM Cargo/ Air France Cargo 22 .99 20 .14 21 .68 19 .81 23 .39 21 .38 17.10 18 .50 Cargo Jet 21 .96 20 .65 19 .67 19 .00 21 .14 19 .98 17.40 16 .89 On-time Quality of Inf ormation Co mpetitive Cu stomer Le adership Ab ility to Su stainable pe rformance equi pment & te chnology pri cing ser vice in problem pro vide Tr ansportation ope rations sol ving va lue-added Pr actices ser vices Benchmark of Excellence 19.93 17.92 18 .66 18 .89 17.06 15 .43 1 3.91 15 .75 Cardinal Courier 24 .15 18 .12 19 .55 22 .85 18 .68 20 .24 18 .18 19 .27 Midland Courier 22 .94 20 .77 21 .66 23 .52 22 .19 21 .03 19 .14 20 .44 Ace Courier 22 .21 20 .12 20 .07 21 .64 20 .55 19 .48 16 .26 19 .42 Fed EX 19 .98 18 .20 18 .64 18 .33 17.15 15 .23 14 .00 16 .35 Dicom/ General Logistics 19 .92 16 .95 18 .24 19 .99 18 .10 15 .18 13 .67 15 .84 Systems (GLS)
AIR FREIGHT WINNERS A
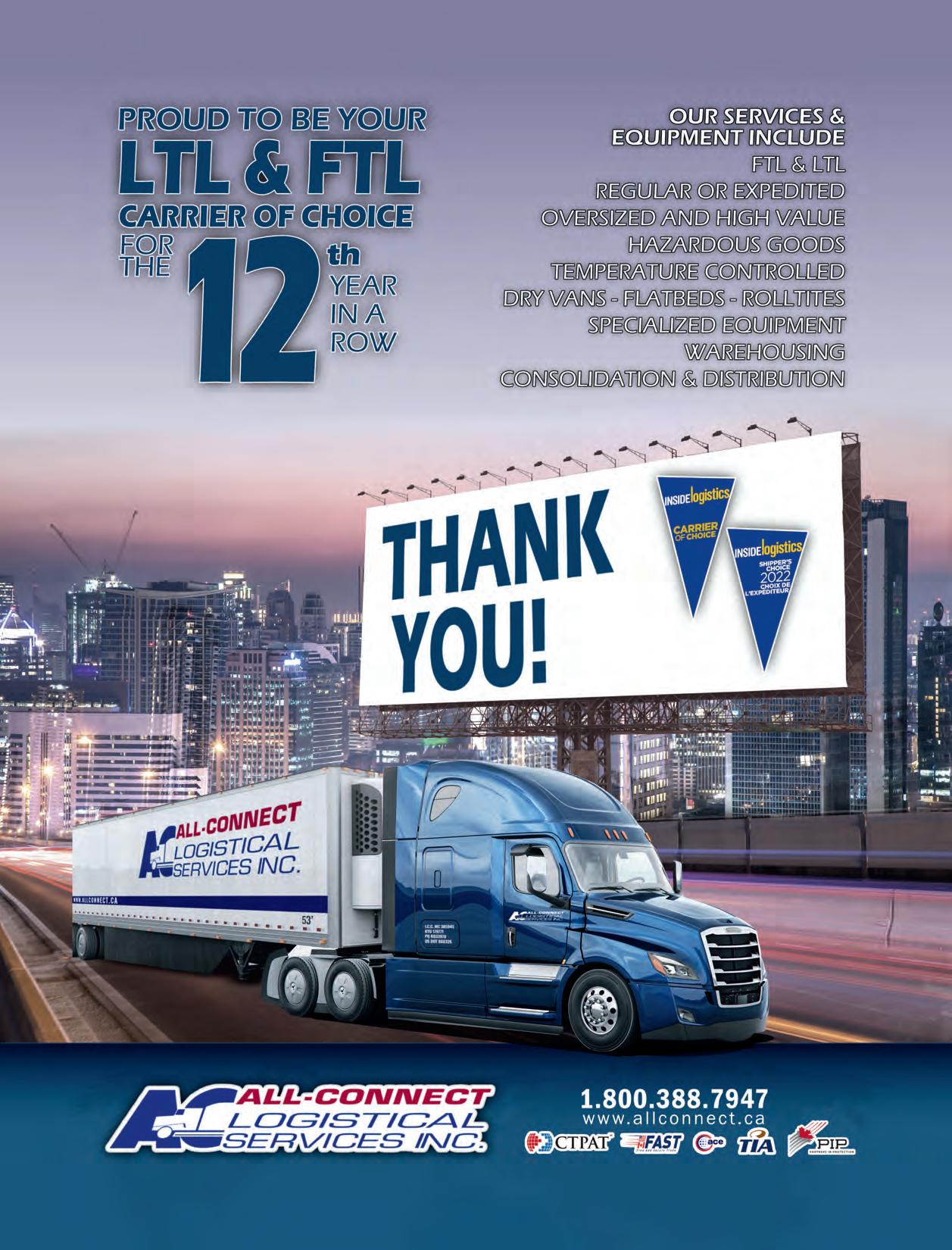
CARRIERS OF CHOICE
C
to the 2022 Carriers of Choice! On-time Quality of I nformation C ompetitive C ustomer L eadership A bility to S ustainable p erformance equ ipment & t echnology pr icing se rvice i n problem pr ovide Transportation operations solving value-added Practices s ervices Benchmark of Excellence 16.98 17.45 17.50 1 8.16 1 8.00 1 6.45 15.54 1 5.88 Orient Overseas Container 1 7.21 1 8.46 2 0.35 2 0.59 1 8.42 1 6.78 1 5.73 1 6.39 Line Hapag(OOCL)Lloyd 1 7.46 1 7.58 1 8.96 1 8.05 1 8.09 1 7.03 1 6.18 1 6.08iStockTryaging,Image:
uyers of ocean freight services have traditionally been very price sensitive and this year’s Shipper’s Choice Survey found their attitude to be no different. Competitive pricing has the highest benchmark among the ocean carrier KPIs. The second highest benchmark for ocean carriers is customer service. Two ocean carriers surpassed the Benchmark of Excellence this year.
arriers are presented with this prestigious award if they have demonstrated the consistency necessary to attain the highest levels of service by surpassing the industry Benchmarks of Excellence for a minimum of five consecutive years. This is a particularly difficult task. Aside from having to maintain consistent excellence in their operations, carriers have to meet a standard that rises every year, while also responding to changing priorities. To remain part of this exclusive fraternity, carriers must requalify each year.
2022 SHIPPER’S CHOIC E | continued fro m page 25 All Connect Logistical Service s HeFCCargojetavalieredExrcules CardinalPolaris Courier Penner MidlandInternationalCourier

Congratulations
insidelogistics.ca 27 O CEAN WINNERS B
28 INSIDE Logistics JUNE 20 22
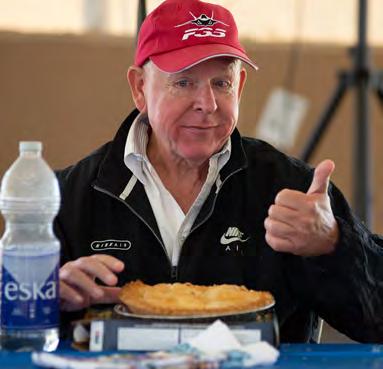

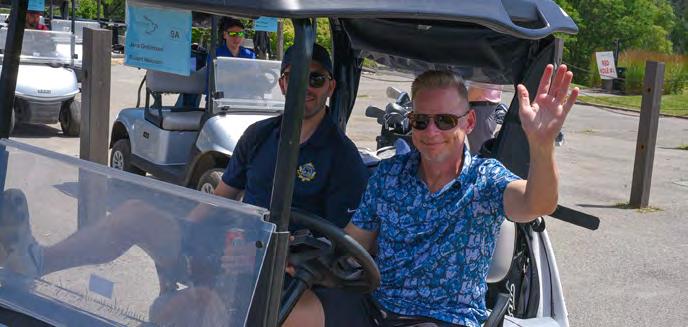
real- time visibilty
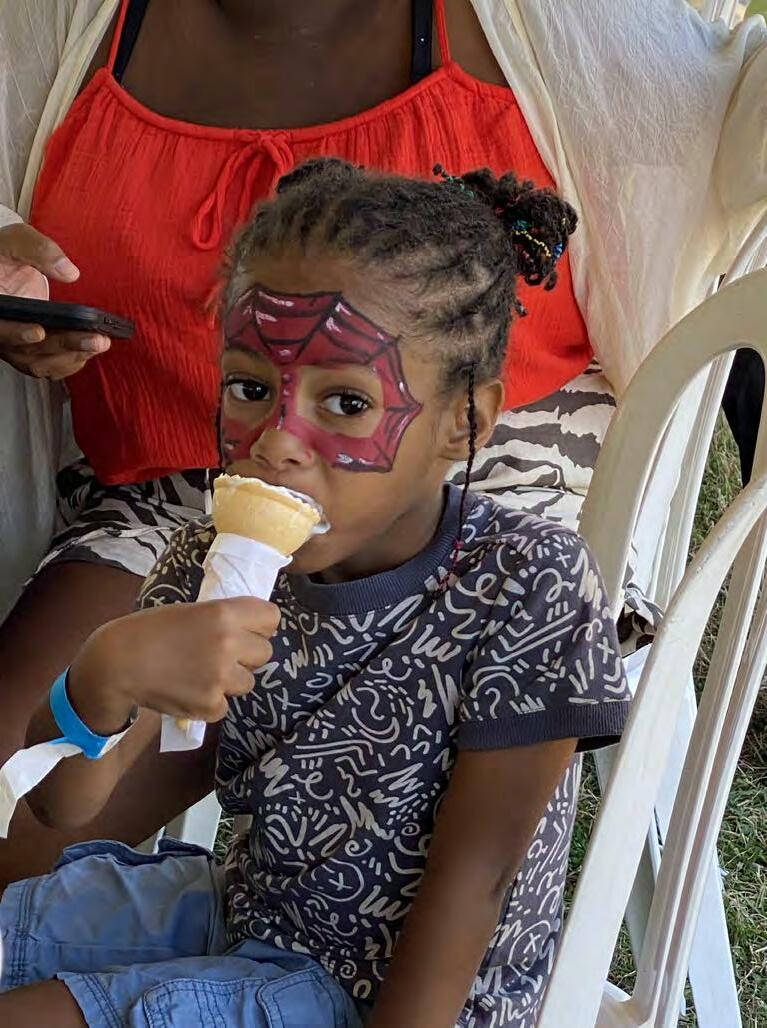
Welcome to our new feature, Real-time Visibility! Here’s your chance to share photos from your latest company event. Whether it’s a celebration, speaker, conference or just shots of action at work, we’d love to see what’s going on in real time at your workplace. So grab your phone, take some snaps and share with us. Send a note to emily@turnkey.media to find out how. This time around we have submissions from the CITT Toronto Area Council from their 2022 golf tournament, and Polaris Trans portation Group’s summer party.
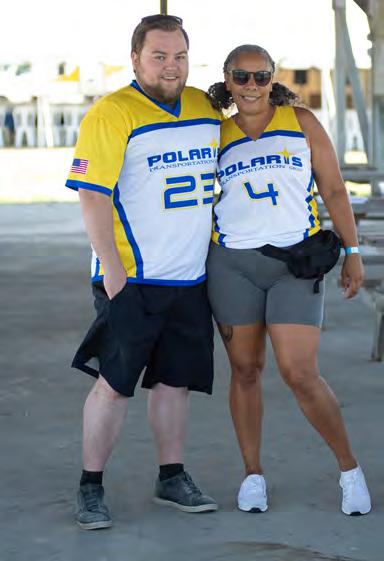
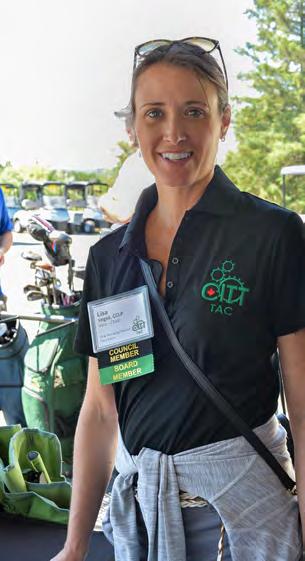
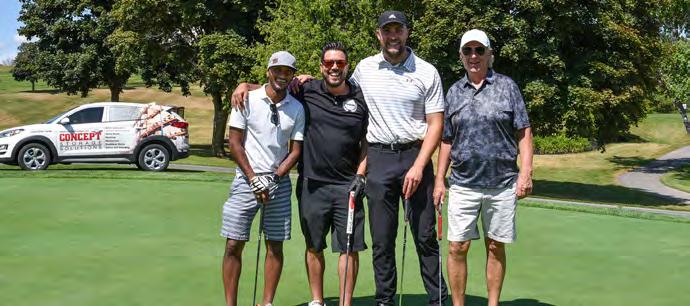
Across the Atlantic in the meantime, the European Union launched a public consultation in June on their proposed regulation that would prohibit making available on the EU market any prod ucts made, extracted or harvested with forced labour, whether they are made in the EU or elsewhere. The EU approach is different from the US. Due to legal differ ences between individual EU countries, the union is not directly targeting the entry of such products, but instead will ban the placing of such products on the European market. This is planned for the third quarter of 2022.
ON JUNE 21 this year, US Customs and Border Protection (CBP) began enforcing the Uyghur Forced Labour Prevention Act (UFLPA). The import of goods made with forced labour has been illegal for some time in the US, and this new Act extends the reach of CBP to block the import of goods made with forced labour.
New rules require greater due diligence
slave labour. Following the implementation of our new North American trade deal in 2020, we amended our Customs Tariff Act to prohibit forced-labour imports, but Canada has yet to stop a single such import.
T R ADE UP D A T E
insidelogistics.ca 29
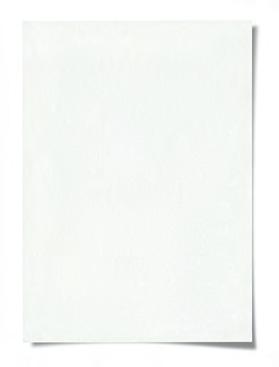
Materials from Xinjiang can be used to make goods outside China as well. Importers must therefore demonstrate documented due diligence with their suppliers and be in a position to prove the absence of forced labour components in their imports. With this, the risks of delays, disruptions and additional costs, including penalties, have increased. This is another example of the extraterritorial reach of US laws.
Sometimes though, there are good news stories and things can get easier. At a meet ing between Canada’s international trade minister and the US trade representative in July, it was announced that Trump-era tar iffs on Canadian-made solar products will be scrapped. These had been imposed in 2018, resulting in an 82-percent drop in our exports of solar products to the US. In Feb ruary, a CUSMA dispute resolution panel found that the US was in violation of its ob ligations under our free trade agreement.
This new law could also remind us that there has been a long-standing US ban on cotton imported from Turkmenistan over findings of state-enforced slave labour in that Central Asian nation, so China is not the only origin to watch. The message to Canadian importers/exporters therefore is: Keep your eyes open!
the situation in Canada also point to a 2018 Australian study called the Global Slavery Index which estimated that $185 billion of goods imported in Canada were at risk of being made by forced labour at some point in the supply chain.
Canada is perceived by our American neighbours as lagging behind. CUSMA has provisions dealing with labour and environmental protection that include banning the entry of goods produced by
As supply chain management gets more complex, we’ll take these good news stories anytime.
Under the new UFLPA, CBP will be able to detain or seize any and all goods that were made, in whole or in part, with inputs from China’s Xinjiang Uyghur re gion, on the presumption that the goods were made using forced labour. Import ers will have 30 days to demonstrate that the goods were either not made using forced labour, or that the goods did not include any inputs from the Xinjiang re gion.Down the road, certain companies lo cated in that region or outside of it will be specifically designated in the Act. This may help importers, but because the prohibition applies to goods made in whole, or in part, and applies to companies that may or may not be located in the Xinjiang province, US importers of products from anywhere in the world are at risk.
This new law also highlights the importance of environmental, social and governance factors and their impact on supply chain
management. Diversification of supply sources is key to successful procurement strategies to mitigate the risks of disruption, but it comes with the need for strong internal complianceRegulatoryprocesses.reviewsnow have to include forced labour, not just from a Canadian perspective but also with full awareness of what’s happening in the US, the first desti nation for our exports. And since the vast majority of our exports are made under the DDP Incoterm (or the UCC term, FOB Destination) and the Canadian exporter becomes the Importer of Record in the US, many Canadian companies are on the hook for this.
In the past, CBP issued “withhold release orders” and “findings” on imports from specific companies and/or specific countries, when there was a reasonable suspicion to detain the goods. The importer would then have 30 days to demonstrate that the product was not made using forced labour.
FORCED LABOUR AND THE SUPPLY CHAIN
In October 2021, the CBSA seized a ship ment of clothing arriving from China at the Port of Montréal, but it was subsequently released after the importer challenged the seizure. By comparison, in 2021, the US seized over 1,400 shipments of goods made with forced labour from China and other countries.Criticsof
CHRISTIAN SIVIÈRE runs Solimpex and is an international trade consultant and christian.siviere@videotron.calecturer.
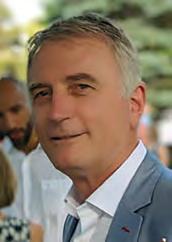
6 Ensure supervisors meet the definition of “competent”. Do they understand the safe ty aspects of their job, such as relevant
1 Maintain up-to-date hazard assessments. It’s a critical element of the RACE (recognize, assess, control, evaluate) process, which helps keep workers safe and promotes competitive ness and profitability. Have you identified and implemented controls for all hazards? Have you documented these controls and communicated your expectations regarding safe operating procedures and behaviours? Have you trained your supervisors to monitor this? Do you have a process for reviewing and updating the hazard assessments?
WHAT DOES MATERIAL handling mean to you?
5 Store materials safely. Are pallets in good condition? Are rack loads stable and securely placed? Is there any risk of loads falling? Avoid hanging loads on the rear beam, where they could compromise the stability of the load behind them.
8 Train employees on manual lifting best practices. It’s not as simple as “Just lift with your legs and keep your back straight”. Employees may be manually unloading boxes from trailers, loading them onto conveyors, moving them from conveyors to pallets, and stacking them for ship ping. Train employees to conduct these movements safely and assign specific tasks to the right person. Is the box a safe weight for them? Are they able to lift it without twisting and bending? Do they know how to plan the lift? Ask for help when necessary? Does the training reflect working conditions and unique situations that may arise?
9 Provide lifting aids, such as such as sus pended lift assist devices and spring-loaded pallets so workers may lift at a safe height and avoid excessive bending and reaching.
It’s much more than picking up a box to build a pallet load. In today’s sophisticated warehouses and distribution centres, product moves through your workspace with precision and grace by means of trucks, conveyors, ladders, pallet wrappers, walkies, lift trucks, automated guided vehicles, robotics, cranes, and steel storage racks. In the process, your people may get caught, struck by or crushed if hazards are not identified and controlled.
PREVENTING MATERIAL HANDLING INJURIES
legislation and standards? Do they know exactly which safe procedures employ ees must follow? Do they monitor and enforce them?
Moving goods is an essential activity – getting injured while doing it isn’t
2 Create a safe environment for moving goods. Minimize or eliminate pedestrian traffic on loading docks. Give equipment operators clear sight lines and paths by eliminating blind spots and obstructions. Avoid plac ing tall loads on corners or at intersections where mobile equipment and pedestrians may meet. Ensure that lighting is functioning and sufficient for the tasks at hand, and that occupancy sensors trigger lighting promptly.
NORM KR AMER, is a Canadian Registered Safet y Professiona l with over 25 year s of experienc e. Nor m provides health and safet y consulting ser vices for Workplace Safet y & Prevention Ser vices ( WSPS) as a warehouse specialist in the GTA region.
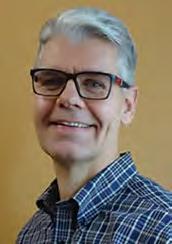
The best defence against material handling injuries is implementing a prevention pro gram. Here are 10 components of an effective program, along with sample considerations for each. Each component plays an essential role in preventing injuries and property loss.
3 Employ proper lockout and tagout procedures for machinery and equipment. A lot of material moves on conveyor systems with rollers, belts, gears, sprockets and other mechanical parts that can seriously injure a person if not properly guarded, or if not locked out
7 Ensure equipment operators are fully trained and experienced. For example, CSA B335, Safety standard for lift trucks, calls for theoretical and practical training, as well as evaluations. Provide new trainees a full eight hours of practical operator training on the equipment they’ll be using, and have them practice manoeuvres that they will be expected to perform on the job. To ensure competency, assess operators’ newly developed skills before they perform work on the warehouse floor.
30 INSIDE Logistics AUGUST 20 22
10 Document everything, including policies and procedures, inspection results, hazard assessments, training, etc. Inspectors may ask to see any of these documents, but going forward having them on hand and accessible will help you identify gaps and opportunities, improve performance, and promote compliance.
SAFE T Y FIRS T
4 Integrate safe operating procedures into your health and safety program. Do your proce dures include equipment manufacturers’ recommendations? Does the joint health and safety committee take them into ac count when conducting inspections? Do you evaluate them periodically?
during maintenance and repairs. Are all your pinch points properly guarded? Do you have proper lockout and tagout pro cedures in place, based on manufacturers’ recommendations, as part of a hazardous energy control program? Have employees been trained on the program and proce dures? Are the procedures monitored and enforced?
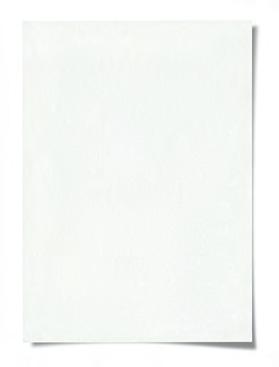
Keep “Your inside Track to Canada’s Supply Chain” Visit InsideLogistics.ca to SUBSCRIBE to the e-newsletter. Delivered every Tuesday and Friday. E-news CANAD A ’S SUPPLY CHAIN MA GAZINE
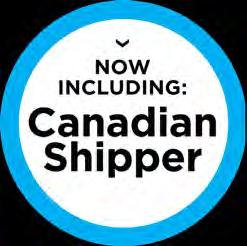


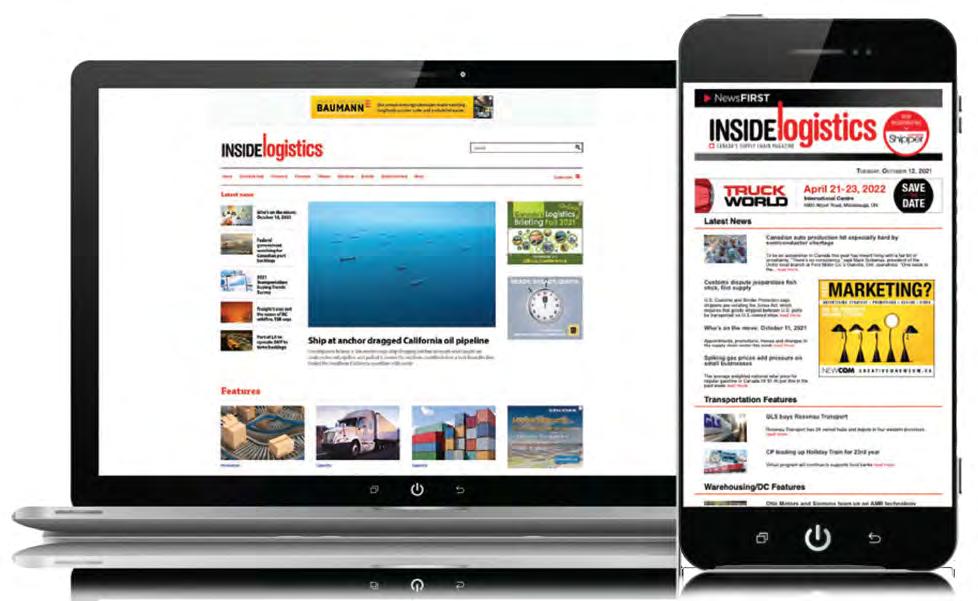
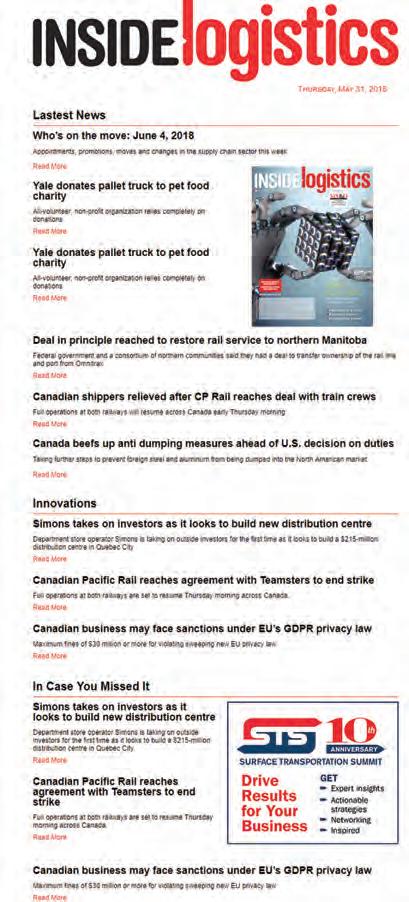
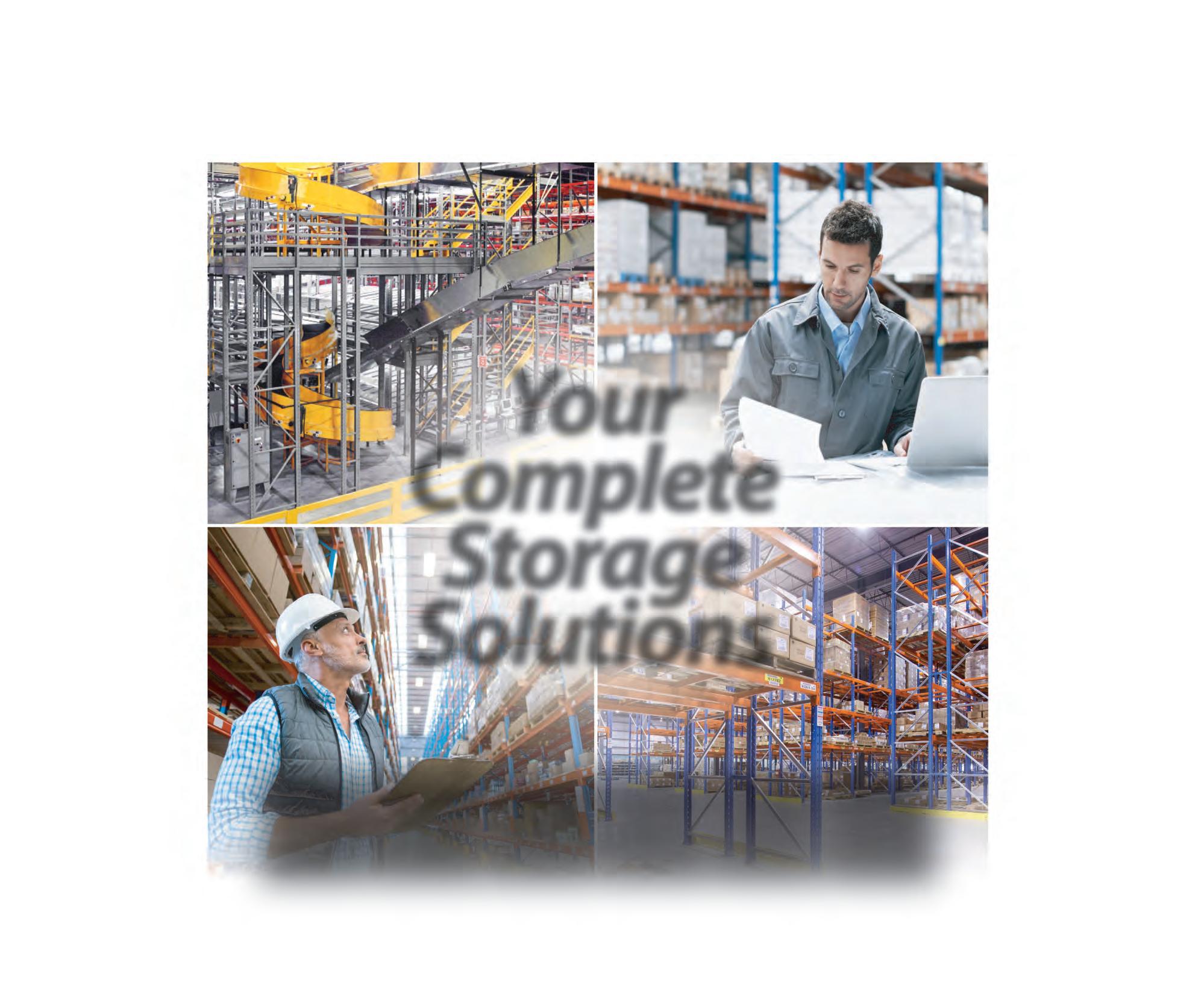