CRUSHING IT IN MONTREAL
JOBSITES IN PICTURES
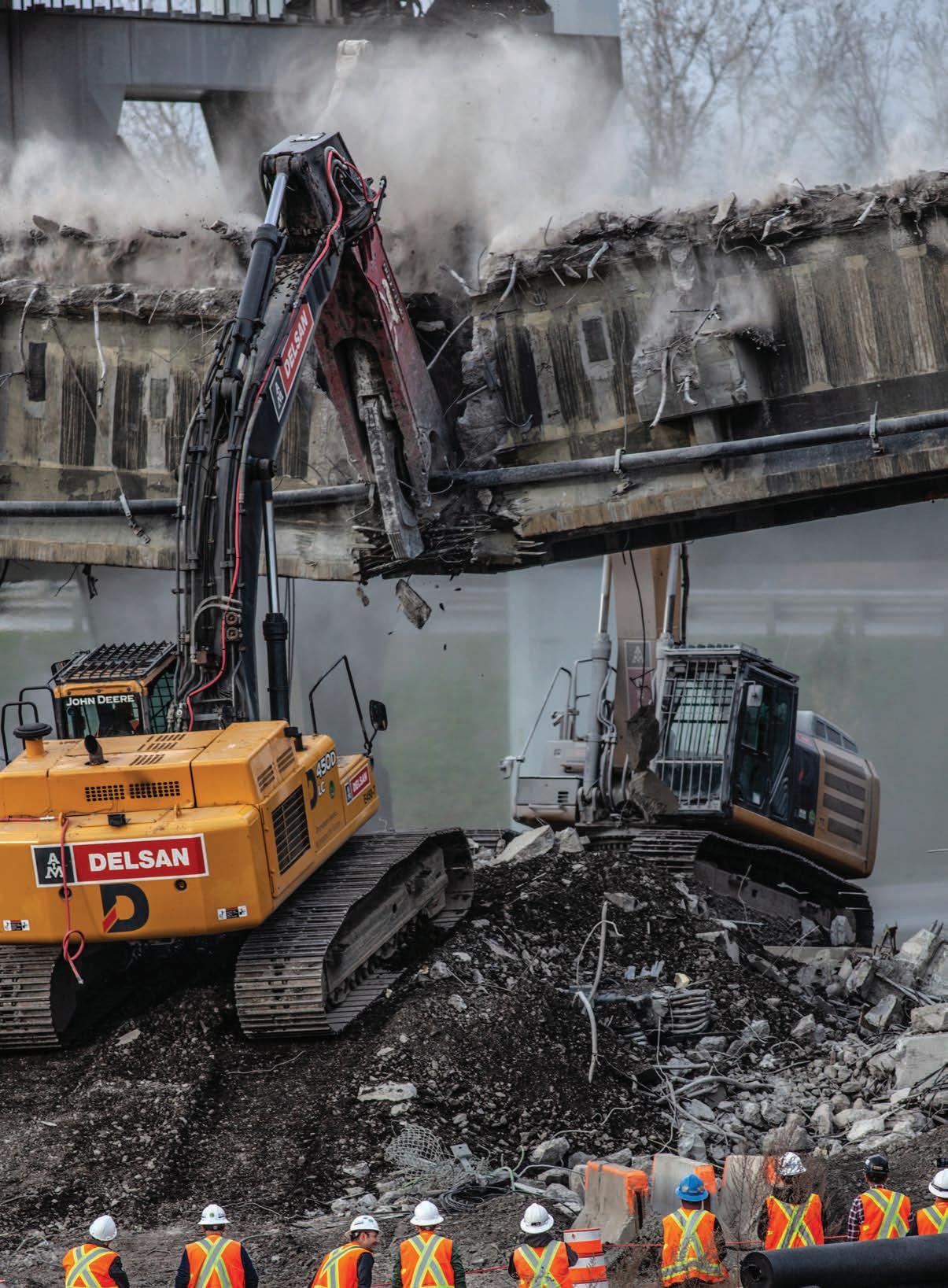
EQUIPMENT: BULLISH ON MOVING EARTH
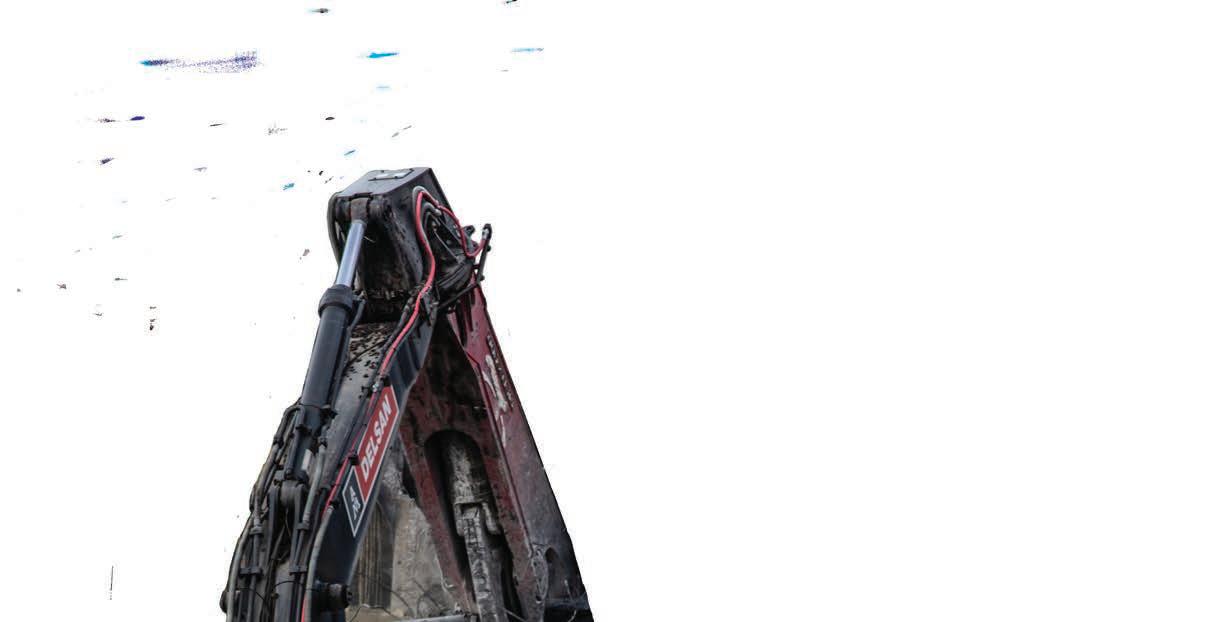
COLLABORATIVE PRACTICES TO REDUCE RISK
PUTTING A POLISH ON CONCRETE FLOORS

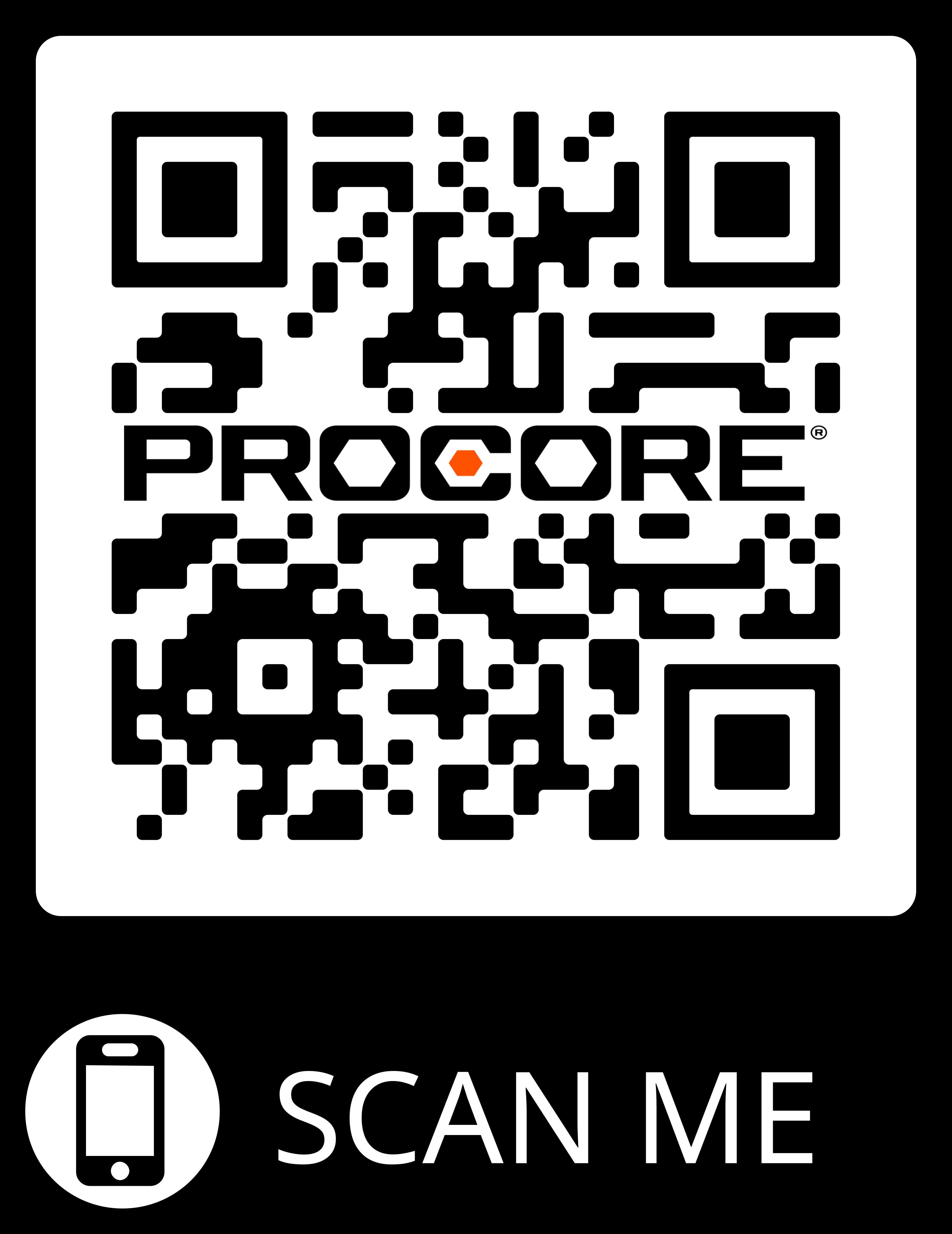
MINIMIZE RISK. MAXIMIZE PROFITS.
EQUIPMENT: BULLISH ON MOVING EARTH
COLLABORATIVE PRACTICES TO REDUCE RISK
PUTTING A POLISH ON CONCRETE FLOORS
MINIMIZE RISK. MAXIMIZE PROFITS.
Set your sites on Procore.
Annual awards put a spotlight on the best of Ontario’s concrete construction projects.
44
Strong attendance and high interest January’s World of Concrete show had an energy not seen since before the pandemic.
The photo contest edition is one of the issues that I most look forward to each year. I love getting out to tour construction sites and buildings — usually working from the basements and mechanical rooms and walking through the service corridors that don’t make the glossy sales brochures. Seeing shots like those in our contest (starting on page 23) is pretty much the next best thing.
Over the years, I have developed an appreciation for what so many users of structures rarely stop to consider. As you well know, it takes teams of highly skilled professionals to build the roads that we all use, the hospitals and water systems that keep us healthy and safe, and the buildings in which we live and work — but I’m not telling you anything that you don’t already know.
Of course, even construction professionals don’t always stop to consider how complicated these projects are, nor how many steps are involved in the creation of these facilities and structures that so many take for granted — and very often we are too busy to step back to take a look at the setting and all the activity that’s buzzing on and around a jobsite.
I guess that’s one of the big tell-tale signs of a professional — they are there to get a job done, and they are great at making the difficult look easy, or at least easier. This photo issue is a chance for us to salute some of what you do, and we thank you for sharing.
On-Site’s annual Canadian Construction Photo Contest provides us a chance to spotlight some of the “behind the scenes” activities that are part of your world. And in sharing these images there is a hope that more people will see (and appreciate) the skills, hours and hard
work that is put in to by the members of our construction community.
In the case of our winning shot this year, while it is showing the demolition of a bridge, even demolition is part of our construction world as core city infrastructure is rebuilt and renewed. Improvements and renewal keep crews busy, and improve the lives of users of these new roads and structures.
One of the ways we recognize each year’s photo contest winner is with a donation to a charity of their choice, and I really liked the choice of charity that the winning photographer selected — Fondation CHU Sainte-Justine Foundation.
Hospital foundations help support not only their communities, but also the projects that so many of our readers work on as these institutions are built, renovated, expanded, and so forth. That’s a nice full circle that becomes noticeable when you take time to step back and appreciate some of the connections in this world.
Speaking of connections, we will be looking to make some as we travel to some of the industry shows and events this year, including the CONEXPO show in Las Vegas, and watch your inbox for invites to some of our upcoming webinars and special events — we are deep into planning for 2023. And don’t forget to include some photography in your 2023 plans as well. The next edition of our photo contest will be here before we know it.
Until next time, stay safe and do great work.
Adam Freill / Editor afreill@annexbusinessmedia.comOn the digital frontier that is opening up as companies explore VDC model capabilities:
“These capabilities are only beginning to find use cases in construction, but compared with what’s possible, contractors are only scratching the surface. Looking at details about materials, for example, a company can measure and track the environmental footprint of a project, fine-tune allocation of resources, or factor supply chain constraints into a project schedule.”
On reducing risk through collaboration in delivery models: “Many in the construction sector have used the term “siloed” to describe the current state of the industry, and these new collaborative delivery models propose to de-silo the industry through collaboration.”
On using software to address labour shortages in the construction sector:
“The difficulty of predicting and planning labour is a strain throughout the industry. Adding pursuits in your planning can help avoid surprise complications and immediately help you mitigate shortages.”
On posting security to vacate liens:
“Lien legislation creates a process by which the lien may be discharged, contract funds continue to flow, and the lien claim be resolved without compromising the protections afforded to the lien claimant.”
www.on-sitemag.com
READER SERVICE
Print and digital subscription inquiries or changes, please contact
Angelita Potal
Email: apotal@annexbusinessmedia.com
Tel: (416) 510-5113
Fax: (416) 510-6875
Mail: 111 Gordon Baker Road, Suite 400, Toronto, ON M2H 3R1
PUBLISHER | Peter Leonard (416) 510-6847 pLeonard@on-sitemag.com
EDITOR | Adam Freill (416) 510-6821 afreill@annexbusinessmedia.com
MEDIA DESIGNER | Lisa Zambri lzambri@annexbusinessmedia.com
ASSOCIATE PUBLISHER | David Skene (416) 510-6884 dskene@on-sitemag.com
ACCOUNT COORDINATOR | Kim Rossiter (416) 510-6794 krossiter@on-sitemag.com
AUDIENCE DEVELOPMENT MANAGER | Urszula Grzyb (416) 510-5180 ugrzyb@annexbusinessmedia.com
PRESIDENT/COO | Scott Jamieson sjamieson@annexbusinessmedia.com
Established in 1957, On-Site is published by Annex Business Media 111 Gordon Baker Road, Suite 400, Toronto, ON M2H 3R1
Publications Mail Agreement No. 40065710
ISSN: 1910-118X (Print)
ISSN 2371-8544 (Online)
SUBSCRIPTION RATES Canada $49.50 per year, United States $113.00 per year, Other foreign $136.50, Single Copy Canada $13.50. On-Site is published 7 times per year except for occasional combined, expanded or premium issues, which count as two subscription issues. Occasionally, On-Site will mail information on behalf of industry-related groups whose products and services we believe may be of interest to you. If you prefer not to receive this information, please contact our circulation department in any of the four ways listed above.
Annex Business Media Privacy Officer privacy@annexbusinessmedia.com
Tel: 800-668-2374
Content copyright ©2023 by Annex Business Media may not be reprinted without permission.
On-Site receives unsolicited materials (including letters to the editor, press releases, promotional items and images) from time to time. On-Site, its affiliates and assignees may use, reproduce, publish, re-publish, distribute, store and archive such unsolicited submissions in whole or in part in any form or medium whatsoever, without compensation of any sort.
DISCLAIMER This publication is for informational purposes only The content and “expert” advice presented are not intended as a substitute for informed professional engineering advice. You should not act on information contained in this publication without seeking specific advice from qualified engineering professionals.
It won’t surprise the panelists from Procore’s Canadian Construction Forecast 2023 if the construction sector outpaces the slowing growth expected in Canada’s general economy this year.
The panelists at the breakfast event, which took place at the Fairmont Royal York hotel in Toronto on January 31, outlined what their research is indicating as they discussed factors driving construction forward in Canada, as well as potential downside risks such as geopolitical and economic trends that may play out as the year unfolds.
Harshil Gupta, regional product marketing manager for Procore, was moderator for the panel discussion, and provided some insights into the Canada’s economy and its construction sector, in particular, before leading the panel through several industry-related questions.
“This is a historically tight labour market,” said Gupta, as he shared findings from several Canadian organizations, inlcuding the Business development Bank of Canada (BDC), which he said expects to see the Canadian gross domestic product (GDP) grow by a modest 0.5 per cent in 2023.
“They would like us to think of this as economic stagnation rather than recession,” he explained.
Mary Van Buren, president of the Canadian Construction Association cited her association’s own economic reporting for 2023, which indicates an expected slowdown in the second quarter on the residential side of construction.
Van Buren said that sentiment and optimism remains high in the industry, however, and stated that factors like decaying infrastructure in Canada and the push to update and “green” civil infrastructure and buildings across the country will create opportunity for the construc-
tion industry.
Immigration will also have a positive impact on high-rise residential construction, said Adam Freill, editor at On-Site Magazine. Freill expects the increased number of newcomers to Canada in 2022 and 2023 to be a positive catalyst for the multi-unit residential segment of construction in the coming years.
Alex Carrick, chief economist at ConstructConnect, considered the geopolitical factors that will affect the industry, “I think the talk of recession is overblown,” said Carrick, “There was a 2.1 per cent increase in GDP in the U.S. in 2022 and the unemployment rates are low in both Canada and the U.S.”
Carrick stated that the global push toward Net-Zero 2050 is as important as the industrial revolution because the entire world is moving away from a dependence on fossil fuels. With this global push, Carrick says mega-construction projects have started in Canada and the U.S. as the countries look to build hydrogen plants, electric-vehicle manufacturing plants, chip-making plants and battery plants like the over $5 billion battery-manufacturing plant by Stellantis and LG Energy Solution in Windsor, Ont.
Among the factors that could have a negative impact on the industry were labour and supply chain shortages.
“Our contractors are feeling the pain of shortages. They’ve had to decline proj-
ects because of labour shortages and it’s impacting Canada’s ability to grow,” said Van Burren.
“Labour has always been in the top three issues impacting our industry,” said Freill, who added that technology like software to manage projects and paperwork can help mitigate some of the issues. “It’s about doing more with what we do have, and technology can help us do that.”
Each panelist mentioned the positive impact technology can have in the industry.
Carrick expects automation to continue trending higher in the industry and suggested modular building and 3-D printing of components as advances that can help the industry. Van Burren mentioned that exoskeletons can also help mitigate the wear-and-tear on labourers’ bodies and can allow more types of people to enter construction.
Beyond technology, Van Burren put some of the ownness of solving the industry’s labour-shortage issue on the federal government: “We need to change the point system for immigration. We need to let in more skilled labourers.”
Looking ahead, Van Burren said she is looking forward to more predictability in the coming year. She would like to see a stabilizing workforce and GDP and expects the government to commit to long-term (25-year) infrastructure plans.
Procore panel presents modestly optimistic outlook for 2023From left: Harshil Gupta of Procore, Adam Freill of On-Site Magazine, Alex Carrick of ConstructConnect, and Mary Van Buren of the Canadian Construction Association. PHOTO BY DANIEL REALE-CHIN
EllisDon has launched its Fit Your Frame campaign. The program aims to provide construction safety vests to women and gender-nonconforming persons whose frame and body type are not best served by traditional safety vest offerings.
“Traditional safety vests are not built to fit women or gender-nonconforming persons, and we wanted to change that,” said Jennifer Khan, the company’s vice-president of inclusive diversity.
“Every day, EllisDon is working towards more inclusive measures on our sites and in our offices; I hope that this will continue to ripple throughout the industry so that everyone, and I mean everyone, feels welcome,” she added.
The construction company has partnered with Md Bespoke, a Black-owned Canadian custom clothing manufacturer
that will produce vests that will uphold the quality and function of traditional safety vests, but with additional fitting and size options.
“It is so important to feel like you belong in a workplace, and I know from personal experience what that can do mentally to you when you feel like you do not belong,” said Tess Durrant, chief operating officer at Safety BeSpoke.
Lafarge Canada and TransAlta Corporation are going to repurpose landfilled fly ash to replace cement in concrete. The fly ash is a waste product from TransAlta’s Canadian coal-fired electricity operations west of Edmonton, which ended in 2021.
“Driving innovative and sustainable initiatives is a key part of our business in Alberta and across Western Canada,” said Brad Kohl, president and CEO of Lafarge Canada (West). “There is great potential in repurposing materials across the construction value chain. Transforming landfilled material, such as fly ash, into a usable product for construction, is a win-win solution for all of us.”
“Our role in this project demonstrates TransAlta’s commitment to supporting innovative solutions for our customers that reduce their environmental footprints and meet their ESG goals,” said Blain van Melle, executive vice-president, Alberta Business, at TransAlta Corporation. “Using fly ash to make concrete creates a valuable opportunity to recycle one of the largest waste streams in North America. It’s a great complement to the zero-emissions electricity we are currently providing to Lafarge from our wind platform in Alberta.”
Landfilled fly ash must first go through a beneficiation process to be used in concrete. The project will use Ash-TEK Ponded Ash Beneficiation System (PABS) technology, which has consistently produced high quality ash during trials and has a low-carbon footprint and an economical operating cost.
Lafarge will deploy this unique approach to the process,
Fit Your Frame is led by EllisDon’s inclusive diversity leadership group 2gether and is geared towards reflecting all forms of gender expression. The campaign, which has launched, will continue nationwide throughout all EllisDon’s area offices and sites with vests will be distributed to EllisDon employees.
To order vests, send an email inquiry to contact@safetybespoke.com.
Alberta fly ash to replace cement in concrete.
removing moisture from the ash, milling it, and removing excess carbon, ensuring that it meets regulatory standards and market expectations. Geocycle, a provider of sustainable waste management services worldwide, and Lafarge’s subsidiary in Canada, will also join the initiative.
“Landfilled fly ash sometimes has too much carbon, which affects how much air there is in the concrete. Once we can treat and separate that carbon, then the fly ash is ready to be used in place of cement,” commented Sophie Wu of Geocycle. The fly as can be used to replace up to 25 per cent of the cement, in a standard replacement, she explained.
“We recognize that seizing opportunities to optimize cement is a key part of our CO2 reduction strategy,” said Kohl. “Thinking outside the box is a part of how we do business.”
The crowning of the Cat Global Operator Challenge (GOC) champion is one step closer. North America’s eastern and western regional champions have been determined.
From a field of 35 dealer-event winners from across North America John Schiedeck of Schiedeck Construction and Matt Ferris of Kinkaid Civil Construction emerged victorious to earn spots in the championship at ConExpo in Las Vegas this March.
Held on Caterpillar grounds in Clayton, N.C., operators from Canada, the U.S.and Puerto Rico competed in eastern and western regional semi-finals. All competitors completed the same three events using Cat equipment and technology.
“Our challenge team went to great lengths to ensure a level playing field for all participants, so no one had an advantage,” said Matt Smith, global marketing manager for Caterpillar. “They even tarped
the large excavator challenge area so the rain we had the night before the eastern semi-finals to ensure that didn’t affect any section of that challenge event.”
One event had operators use a Cat 315 excavator with Cat Grade with 2D technology to dig a 20-foot trench with depth changes and pipes to avoid.
“I like the excavator,” commented Ryan Totton of Gulf Operators in New Brunswick, representing Toromont Cat. “You can do almost anything with it.”
The regional GOC semi-finals were a culmination of months of competitions held worldwide at the dealer level.
“We experienced amazing participation in this year’s challenge,” said Jessica Nunley, global marketing manager for Caterpillar. “From more than 10,000 registrants, 3,500 machine operators competed in the first round at the dealer level, and only 84 of the best operators in the world made it to the regional semi-finals.”
In addition to the overall winners advancing to the finals, the following participants were recognized by Caterpillar with awards.
Second place – Ryan Totton, Gulf Operators/Toromont Cat
Third place – Robert Donnellan, CAC Industries Inc./HO Penn
Trench Run winner – John Schiedeck, Schiedeck Construction/Holt Cat
Locked and Loaded winner – Tom Gardocki (Dirt Ninja), New Era Excavation LLC/Milton Cat
Backhoe Bonanza winner – John
Schiedeck, Schiedeck Construction/Holt Cat
Second place – Steve Newman, Newman Equipment Rentals/Quinn Company
Third place – David Gruhot, D&G Excavating/Ziegler Cat
Trench Run winner – Ben Dunbar, Windley Contracting LTD./Finning Canada
Locked and Loaded winner – Daniel Ludtke, Elite Dirtwerz/Holt of California
Backhoe Bonanza winner – Steve Newman, Newman Equipment Rentals/ Quinn Company
The Co-operators new head office has earned Zero Carbon Building – Design Standard certification from the Canada Green Building Council (CAGBC). The building, which is currently being built in Guelph, Ont., by Cooper Construction, is scheduled to open in the summer of 2024
The 226,000 sq. ft facility will feature an all-electric design that will eliminate direct carbon emissions from any on-site source, meaning no retrofits or decarbonization plan will be required as the organization progresses toward its net-zero targets.
The insurance firm says that the building has been designed to be highly energy-efficient and to minimize indirect annual carbon emissions from electricity. It will offset any remaining emissions through high-quality carbon offsets or carbon-free renewable energy.
“Achieving the Zero Carbon Building – Design Standard certification for our national headquarters is a strong reflection of our values and vision to catalyze sustainability in our society,” said Shawn Fitzgerald, vice-president workplace services at Co-operators. “This building is a compelling demonstration of imagination and innovation that will be required as we build for a more sustainable future in Canada.”
Features of the new building include a 282-kW rooftop solar array, automatic tinting windows, a tight building envelope design, a heat recovery and redistribution system throughout the building, and LED lighting equipped with occupancy and daylight harvesting sensors.
Investment in building construction was down in November, but not in the non-residential sector where the three core components – industrial, commercial and institutional – combined to post a slim increase, reaching $5.5 billion. A significant drop in Alberta pushed the combined residential and non-residential figure to $20.4 billion for the month. Ontario accounted for most of the non-residential growth.
The industrial component was up almost one per cent on the month, at $1.1 billion, a 25.5 per cent rise year over year. Commercial construction edged up to $3.1 billion in November. Institutional construction investment remained flat for the month, remaining at $1.4 billion, a value it has consistently stayed close to after reaching its historic peak in April.
Investment in residential building construction saw a third consecutive decline as the single-family home component continued to fall. The drop brought the single-family component back down to levels last seen in December of 2021. The multi-unit component remained relatively unchanged to slightly positive, however, coming in at $7.1 billion.
The total value of building permits in Canada reached $11 billion in November, reports Statistics Canada. That was a rise of 14.1 per cent from a month earlier, with growth coming as a rebound after a pair of months of losses. The rebound was tied heavily to significant gains posted in Ontario.
The multi-unit component drove residential sector growth, where combined permit values reached $7.1 billion. Permits for multi-family dwellings were up 19 per cent thanks largely to 21 permits for new condominiums and apartments in Ontario with values over $10 million. The single-family dwelling component advanced as well, but by a more modest seven per cent.
Ontario played a major role in the growth of non-residential sector permits as well. The total permit value in the sector rose almost 15 per cent to reach $3.9 billion in November.
Permits in the institutional component were up 41 per cent, with much of that gain linked to a new courthouse planned for development in Toronto. That project is valued at just over $500 million. The value of permits in the industrial component followed a strong October with a second consecutive healthy month, jumping 32.4 per cent thanks to projects like a $425 million manufacturing plant in Toronto. The lone drop could be found for construction intentions in the commercial component, where permit values edged down a slight 0.6 per cent.
RESIDENTIAL +7.1% Multi Family +19.0% COMMERCIAL -0.6% INDUSTRIAL +32.4%
INSTITUTIONAL +40.6%
Following a decrease in employment in November, the number of people working in Canada’s construction sector rose by 35,000 in December. The 2.3 per cent increase was led by significant gains in Ontario and Alberta. On a year-over-year basis, employment in construction was up by 84,000 in December, a jump of almost six per cent.
Overall, Canadian employment figures rose by a half-per cent, or 104,000 positions, for the month as the national unemployment rate dropped by 0.1 per cent to reach five per cent. That was just above the record low of 4.9 per cent that was observed in June and July of 2022. Total hours worked were little changed on a monthly basis in December, and up roughly one-and-a-half per cent compared with 12 months earlier.
Total Employment in Canada
19,770,000
Unemployment Rate 5.0%
Construction Employment
1,544,300
OEMs continue to add high-tech features and make structural changes to their bulldozers as they aim to enhance performance and reduce costs. In short, dozers are becoming increasingly powerful, productive and connected, while cabs are safer and more comfortable than ever.
For all that, some common vehicle trends, such as electrification and automation, remain a challenge when it comes to dozers. This has less to do with technology than with concerns about safety and practicality within the construction sector.
Driverless trucks are used to haul loads in some mines, but these vehicles operate in controlled environments away from the public. Putting automated dozers on worksites in population centres raises a fear of malfunctioning machines plowing into homes, schools and roads, which is
difficult to overcome. Driverless dozers would need to demonstrate flawless performance and a perfect safety record to gain mainstream acceptance at worksites in populated areas.
Dozer electrification also poses challenges. While the concept isn’t new — Caterpillar unveiled the Cat D6 XE, which the company described as “the world’s first high drive electric drive dozer” back in 2019 — charging concerns persist.
“While electrification of utility equipment has its advantages due to ease of transport to energy sources, larger equipment poses a challenge because of the demanding duty cycles and availability of power sources in remote locations,” states Rafal Bukowski, product specialist, for HST Dozers at Komatsu. “At Komatsu, we are focused on finding solutions that both meet our customers goals and our carbon
neutrality goals, which means looking at various solutions depending on the size of the equipment and application.”
For all that, no one in construction should dismiss the notion of driverless or large-sized electric-battery dozers. Pundits from decades past, after all, never would have predicted that remote monitoring and digital file sharing would become common dozer features.
“‘Autonomy’ and ‘electric’ are words that are swarming around the construction industry. At John Deere we are focused on making our machines smarter, safer, and more sustainable to keep the construction industry moving forward. Autonomy and electric will obviously play a large part in that, and there will likely be steps in-between to get us there,” notes Matt Goedert, solutions marketing manager at John Deere.
well as tomorrow.
As you plan your CONEXPO-CON/AGG journey, make sure to visit Wacker Neuson in the West Hall, Booth #43501. We’ll be sharing the latest products and innovations designed to deliver all it takes for the challenges you face.
March 14-18, 2023
Booth #43501
Over the past two years, John Deere has made multiple productivity-enhancing upgrades to its dozer lineup.
Blade offerings, undercarriages, and exterior hoses have all been upgraded on large 950K and 1050K dozers, for example. Both machines now feature an extended life undercarriage option that uses a proprietary coating it says doubles the working life of standard track chain bushings. The 1050K was fitted with a suspended double-bogie undercarriage frame that provides a more comfortable ride on rough terrain.
“These updates centred around making the machine more productive and reducing potential for downtime. Along with increased productivity, operators are enjoying the smoother ride of the updated 1050 undercarriage,” says Goedert.
John Deere has also expanded the number of dozers fitted with Slope Control, an entry-level solution that makes it easier to grade smooth planar surfaces in applications like road building. Slope Control is now optional on John Deere’s 450, 550, 650, 700, 750 and 850-size dozers, while a “SmartGrade Ready” feature is also available on the latter four models.
SmartGrade Ready “gives customers flexibility. If they want to upgrade to SmartGrade down the road, the harnessing
is already installed on the machine making it a faster turnaround time to install the upgraded technology,” explains Goedert.
Another solution, SmartGrade Remote Support, is now standard on the company’s 650, 700, 750, and 850 dozers. With features such as Remote Display Access (RDA) and Wireless Data Transfer (WDT), SmartGrade Remote Support “allows users to remotely troubleshoot issues to reduce downtime and transfer files to/from the machine,” explains Goedert.
Case Construction Equipment recently unveiled the Minotaur DL550 compact dozer loader, an industry first-machine that the company says is, “Part dozer. Part loader. All beast.”
The DL550 “delivers true dozing performance and true compact track loader performance … You can use it in the dozer configuration with the integrated C-frame and six-way blade,” states Jeff
Jacobsmeyer, product manager at CASE Construction Equipment.
Putting dozer and loader capabilities in a single compact machine reduces both worksite congestion and costs for owners, he adds.
Weighing 18,600 pounds, the DL550 is easy to transport, and is suited to jobsites with limited space. Powered by a 114 hp engine, the DL550 boasts adjustable electro-hydraulic controls like Case’s full-size dozers, a true-positive pressure cab to keep out dirt, dust, and noise, and the company’s popular “Blade Shake” feature.
Activated by a joystick button, Blade Shake “hydraulically shakes the blade when you come to the end of a push and it sheds the dirt and material stuck to the blade so that you’ve got a clean blade on the next push,” states Jacobsmeyer.
The DL550 comes standard with Case Universal Machine Control for precision grading, Case SiteWatch telematics and the SiteConnect Module.
“With standard telematics, you can remotely monitor machine performance and activity. With the SiteConnect Module, you can remotely check machine codes, and service needs and upload software updates,” explains Jacobsmeyer.
Bobcat offers a handy dozer blade attachment for select company skidsteer loaders, compact track loaders and telehandlers.
“While applications can vary, the dozer
blade attachment can turn a loader into a mini-crawler for optimal performance on construction and landscaping jobsites,” says Keith Huff, product specialist at Bobcat.
The six-way adjustable blade angles at plus or minus 30 degrees and can oscillate 10 degrees as well. Blades range from 80 to 96 inches in size, while adjustable skid shoes mounted on the attachment control and guide blade depth.
Suitable applications include backfilling around foundations, creating runoff grades, and leveling, piling, or grading loose gravel, dirt, and sand.
“The dozer blade attachment is an excellent option for owners or rental companies that want the functionality of a dozer without the need for a dedicated machine,” adds Huff.
When Komatsu introduced the D71-24 in early 2020, the company boasted that its new, mid-sized crawler dozer featured the most powerful hydrostatic transmission in
its size class. It’s a claim that still holds true today, says Bukowski.
“The D71 is a 237 hp machine … It is the strongest machine in its size class with regards to performance,” he states.
The D71-24 has a six-way power angle tilt (PAT) blade pitch system, and is well-
suited for grading, side-cutting and pushing. The D71i-24 version of this crawler dozer (the “i” stands for “intelligent”) features Komatsu’s proprietary, performance-enhancing intelligent Machine Control (iMC) 2.0.
Introduced at CONEXPO-CON/AGG
‘Autonomy’ and ‘electric’ are words that are swarming around the construction industry.
2020, and now on all intelligent Komatsu dozers, iMC 2.0 is an “evolutionary form of technology” that offers “significant productivity and efficiency improvements compared to conventional grading,” says Bukowski.
Since iMC 2.0 is factory installed, “the customer can purchase the machine and pretty much be ready to go. They don’t need to buy any aftermarket [products] or add-ons,” he continues.
The iMC 2.0 solution contains a slew of features, including Proactive Dozing Control which can boost productivity by 60 per cent compared to other Komatsu models.
Proactive Dozing Control “allows the machine to see where it’s going to make its next move. So, as you are running the dozer, it tracks the ground underneath it … This machine can track over and map where it went last and can tell you, ‘You need to cut from this location,’ or ‘You have to fill this location,’” states Bukowski.
The Lift Layer Control feature, mean-
while, enables operators “to essentially double their production from previous models” by maintaining consistent lift thickness and automatically spreading lift, he adds.
Also new from Komatsu is a 2D laser kit for intelligent dozers featuring a Topcon laser receiver. The kit allows operators to use 2D applications “inside buildings, under bridges, closer to power lines—locations where GPS and GNSS connectivity is either poor or nonexistent,” says Bukowski.
In 2022, DEVELON introduced its first dozer in North America, the DD100, competing in the 140-hp and under category. The company reports that the DD100 dozer is at the top of its class for operating weight and horsepower, adding that the machine is ideal for residential and light commercial construction and fine grading tasks.
“The under 140-horsepower size class presents the biggest opportunity for
DEVELON, based on North American dozer sales volume,” says engineering manager Moo Young Park.
Customers can choose from two blade options, a standard 2.9 cubic yard blade or an optional 3.4 cubic yard capacity blade. The blade moves freely to lift, tilt and angle, and offers two-way mechanical adjustments to change the blade pitch to control how steeply the blade will dig into the ground. Operators can adjust the blade pitch from 54 to 58 degrees. Also available is a blade shake button for operators to quickly remove materials stuck to the blade.
DEVELON plans to offer a larger model, the DD130, in North America as well. The company says it expects the 13-metric-ton model to launch in 2023 and be on display at this year’s CONEXPO-CON/AGG in Las Vegas.
Nate Hendley is a freelance writer and author, and is a regular contributor to On-Site Magazine.
MTWO is a construction enterprise cloud solution that connects all project stakeholders, processes, and data in one integrated platform. The robust solution is highly configurable with 100+ modules that address every phase of the building lifecycle and an open API that seamlessly integrates with other business-critical solutions.
MTWO delivers full project control, cost transparency, real-time intelligent data, and unparalleled collaboration and efficiency.
Download our risk management white paper to learn more about how you can utilize technology and implement other strategies to help mitigate risk and set your business up for sustainable long-term growth.
The labour shortage in construction isn’t a surprise for contractors anymore. Although the pandemic certainly intensified the impact of shortages, the construction sector has been coping with fewer and fewer recruits for more than a decade, but with an aging labour pool and a huge demand for workers, the shortage has reached new levels. Being strategic with planning your workforce is more important than ever before.
Unfortunately, inefficient manual processes that silo data and make it hard to collaborate can amplify the difficulties experienced while trying to combat labour shortages. A recent survey of contractors indicated that workforce allocations tend to focus on the coming two-month period, or less, and almost half said that they don’t have adequate time to hire when a project needs it.
These statistics tell us that workforce planning is a reactive part of the construction process, leaving ops teams and HR scrambling to fill gaps, causing project delays due to workforce limitations, and hires that may not be the best fit for a company.
Being proactive and using technology to plan workforce needs months, or even years, in advance can prevent these problems.
A common mistake contractors make with labour is only planning for awarded projects. Including pursuits and projects that are likely to be awarded in planning can provide insight into potential staffing complications, however. In that survey of contractors, 86 per cent reported they have bid on projects only to find they did not have the necessary labour to complete the job. The difficulty of predicting and planning labour is a strain throughout the industry. Adding pursuits in your planning can help avoid surprise complications.
Another benefit to planning pursuits is an improved bid-to-win ratio. Since a lot of resources go into each project bid, having a lower ratio is ideal. Planning labour for pursuits can help improve a bid-to-win ratio, since pre-bid discussions will be informed of the company’s labour capacity and its ability to take on new jobs.
As the planning process around capacity insights improves, winning bids happens more often and the cost of losing bids declines, helping the company grow sustainably and stay proactive with hiring and upskilling internally.
Modern tools are available to strategically allocate resources to maximize workforce planning and productivity.
SIMIC
Having a recruitment strategy informed by your workforce planning can also help combat labour shortages. The more that human resources and recruitment teams can anticipate hiring needs, the more likely they are to find a quality candidate that’s a good fit for your company.
Investing in systems that can provide insight on when people are coming off jobs, when jobs are starting, and what the workforce demands for pursuit projects will likely be is the best way to provide the necessary foresight for your recruitment teams.
This foresight can help you avoid rushed hires and help you develop a solid recruitment strategy. This plan includes the job description, publishing the job, working with recruiters and job boards, conducting interviews and screening applicants.
Recruiting quality candidates proactively mitigates against the steep cost of turnover in construction. Keep in mind that the cost to replace an employee for specialized jobs like superintendents and project managers can be 200 per cent, or more.
It’s imperative that a good recruitment strategy is in place not only to help combat the labour shortage, but also the costs of employee turnover.
Labour shortages aren’t always about the sheer volume of people needed to complete a job, either. It could mean that there’s a shortage of skilled labour, which is the
trend right now. Solving this skills gap problem should include the development of your current workforce.
Contractors need the ability to track experience, certifications, career trajectory and education for current employees. With the current systems in place, data is siloed with limited transparency into it. The result is that employees aren’t developing as they should because they’re being used to fill gaps reactively.
With more insight into the development of the workforce your managers are able to allocate people into jobs where they’re gaining skills, ultimately futureproofing your workforce.
For example, a contractor may have a mason who’s expressed interest in becoming a superintendent. By tracking their skills and helping them get the necessary certifications, the mason could fill a superintendent gap that opens up as a new project begins.
Doing this effectively requires contractors to begin looking at their workforce long-term and step back from the reactive daily management of projects. To accomplish this, a common-data strategy is needed, in which the whole company can access insights on projects and people. With the current tools in their arsenal, it’s difficult to do this because they weren’t designed to provide dynamic insight on constantly shifting variables.
Digital workforce management tools for construction, or even non-vertical specific tools, can help general contractors develop this common data strategy for their workforce by collecting people and project data in one place.
There are many similarities between lean construction and sustainability. At a fundamental level, both systems view processes and production from a similar lens: the lens of value.
Lean construction aims to maximize value to the customer, improve flow, and eliminate waste. The customer is defined as any stakeholder receiving finished work from the previous step in a process, and value is what they need, when they need it, at the quality and quantity that they expect. Waste is defined as any task that does not add value.
The commonly used definition of sustainable development, as defined by the Brundtland Commission, is, “Development that meets the needs of the present without compromising the ability of future generations to meet their own needs.”
Both concepts are focused on the needs of all stakeholders within a system. That focus provides value to both the current and downstream stakeholders. There are three main tools to maximize sustainability through lean.
Originally, the seven wastes were created within the Toyota Production System with a focus of reducing time. As we start focusing on the system from a sustainability lens, we can see that these wastes also eliminate an eighth waste, wasted materials.
The four main contributors of construction and demolition waste are residual, design defects, material handling, and installation errors. Each of these streams can be greatly reduced.
For example, material handling would be reduced with an understanding of defects, inventory and transportation. There is a direct relationship between how long materials are stored on site and the damages that can occur.
When materials are stored on site (inventory) they are exposed to risks for environmental damages, and human error damages (defects). Furthermore, every time the material is moved (transportation) we risk damaging or losing it.
Therefore, it is important to have a material management strategy on a construction site to ensure that material is delivered with a just-in-time approach, and that it is stored in a safe, organized and dedicated location.
Both lean and sustainability require people to work and think differently. People are forced to consider the impacts of choices beyond their silo to ensure the system is optimized for the greatest value. At Chandos we observed that our projects delivered through Integrated Project Delivery (IPD), a delivery method focused on
collaboration, achieved the highest levels of sustainability.
For example, our Drayton Valley Aquatic Centre project in Alberta was able to achieve several sustainability highlights throughout construction due to collaboration and the client’s goal of building a project with net zero energy consumption.
During excavation and land clearing, the project team discussed how they could sustainably remove nearly 5,000 tonnes of clay. Through these discussions the client indicated that they had a berm project that could use the clay. Instead of hauling this material to a temporary stockpile at the local landfill, we were able to directly haul it to this other project, greatly reducing environmental impact.
The second highlight, which was only achievable through the IPD delivery method, was the installation of the rooftop solar panels. The team worked together to install the solar panels as early as possible in the construction schedule. With the system running six months ahead of the project completion, it could be used to power the construction activities.
Not only were we able to use renewable energy to power all construction operations on site, but we are also able to sell extra power generated so that it can be used by the local community. To-date, this has resulted in the project eliminating nearly 109 tonnes of CO2 and delivering thousands in savings.
There is a common saying that a person can’t improve what is not measured, and I like to add that people also don’t improve what they don’t see. Making information visible is critical to success.
When people know the goals for the organization and their projects, the strategies that they can implement to achieve those goals, and have an understanding of their progress over time, they will be empowered to improve and achieve those goals.
When Chandos made its Net Zero 2040 commitment, we didn’t have all the answers. We knew where we were and where we wanted to be, but we didn’t know how to achieve this target. So, we made as much information visible to our employees as we possibly could, provided some starter solutions, outlined the different challenges, and then we let our people run with the ball.
Lean is about truly showing respect for people. It provides the framework, tools, and a way of thinking that people can use to make small continuous improvements.
In his role as a lean and sustainability specialist, Jack Statham advises project teams on how to reduce carbon and waste across the lifecycle of a project.
Much as lean concepts can be used to deliver ever-greater value, they can also be applied to sustainability goals to develop a roadmap to success.
You can’t manage what you can’t see.
Timescapes uses high-quality construction timelapse imagery and powerful visual AI to protect against dispute claims, remotely track and manage construction progress, and inform and engage project stakeholders across all your construction projects.
Track site activity for better visibility, control, and risk management
Monitor heavy equipment usage to create efficiencies
Share visual progress updates with project stakeholder
timescapes.co
Timescapes provides the flexibility to be able to check in on our sites remotely, removing friction from our teams to view and review project progress.”
Hammad Chaudhry | National Director, Digital Project Delivery Services | EllisDon
Timescapes is proud to sponsor On-Site’s annual Canadian Construction Photo Contest. The contest celebrates special moments in construction captured in 2022, and we’re delighted to have had an opportunity to help judge the shortlisted images from jobsites across Canada.
In today’s challenging economic environment, construction professionals are under more pressure than ever to lower costs, reduce schedule delays, mitigate risk, and build trust with project stakeholders — from developers and owners to contractors and employees — at every stage of the project.
Visual project data — or visual intelligence — is an important addition to our digital construction toolbox. It fills in many of the knowledge gaps that we’ve previously encountered on our construction projects.
At a time when construction is leaner than ever, visual intelligence is an incredible tool to help us manage risk, save time and costs on in-person site visits, and create resource efficiencies.
As we help present this year’s photo contest, we hope you enjoy the photoes that have been selected to showcase the incredible power of visual imagery in construction.
Wishing you all a successful year in 2023,
Chester Boyes CEO | TimescapesCapturing the demolition of the last main concrete structure of the original Champlain Bridge in Montreal has earned photographer Pierre Seager and his client the Nouvel Horizon St-Laurent s.e.n.c (NHSL) consortium, formed by Pomerleau and Delsan-A.I.M. Environmental Services, top honours in the 2022 Canadian Construction Photo Contest, as presented by On-Site Magazine and our sponsor, Timescapes.
From a field of almost 200 images and emerging from the shortlist of the honourable mention images that appear in the pages that follow, the action of the excavators, framed by the vested workers on the site, made this image a judges’ favourite, and the overall winner of On-Site’s 2022 Canadian Construction Photo Contest.
Bridges are iconic structures in
Montreal, and until it was closed to traffic when the new Samuel De Champlain Bridge opened in 2019, the original Champlain Bridge was one of the busiest in Canada handling roughly 50 million crossings per year. The bridge crossed the Saint Lawrence River, connecting the Island of Montreal to its south shore suburbs.
Using more than 20 high-reach excavators, the NHSL consortium has been dismantling the bridge in a multi-year project. The main concrete structure of the original Champlain bridge incorporated pre-stressed concrete beams that supported a pre-stressed concrete deck paved with asphalt. More than 10,000 tons of concrete and other materials were recuperated during this particular 50-hour operation, which Seager was on hand to capture last November.
In recognition of Pierre’s great shot,
On-Site has made a donation in his name to Fondation CHU Sainte-Justine Foundation.
As with previous years, this was not an easy contest to judge. In addition to the winner and finalists presented here, there were numerous other images that could have easily landed in these pages, and some that might find their way into future editions of the magazine. To all who submitted images, we’d like to thank you for sharing these moments from your jobsites. It’s heartening to see so much great work, and some impressive scenery, from Canada’s construction sector.
And keep snapping photos as 2023 unfolds. The next Canadian Construction Photo Contest will launch in December, and you can’t enter a photo that was not captured, so keep those cameras, drones and smartphones rolling!
Happy, and safe, shooting.
Company: Nouvel Horizon St-Laurent s.e.n.c (NHSL)
Photographer: Pierre Seager
Location: Montreal
If this year’s crop of images is any indicator, there’s a lot of great work happening on jobsites from coast to coast to coast, which made it very difficult to narrow down all the submissions to a list of finalists and a single winner. Despite having to leave some amazing photos on the cutting room floor, including shots featuring the northern lights, trestle bridges, and more, the shots on these pages are the ones that captured the eyes of our judges. Congratulations to the following honourable mention winners.
EBC has teamed with Bessac Canada to construct a series of shafts, connecting tunnels and collector system for the City of Toronto. Part of the city’s basement flooding protection program, the project provides conveyance and in-line storage tunnels and will connect to future storm sewer separation connections. In June, Ovidiu Petre-Simen spotted a unique perspective to capture this shot, which he has titled Tunnel Launching Shaft.
Company: Pitt Meadows Plumbing and Mechanical Systems
Photographer: Take Off Photography Location: Vancouver
Company: EBC
Photographer: Ovidiu Petre-Simen, Assistant Project Manager, EBC Location: Toronto
Pitt Meadows Plumbing and Mechanical Systems was installing 40-foot lengths of 30-inch diameter piping into the Oakridge district energy utility project in Vancouver the week before Christmas. This photo was taken using a drone while some of the final pieces of pipe were being lifted into place. Pipework goes down the centre of the towers, descending down 22 floors to connect to the central plant that will heat and cool the development.
Company: Kicking Horse Canyon Phase 4 Project
(Sub-contractor: RECo Canada)
Photo courtesy of: Kicking Horse Canyon Phase 4 Project
Location: Golden, B.C.
Upgrading the roads in Kicking Horse Canyon comes with phenomenal views of the Rocky Mountains, as well as one steep drop-off, as can be seen in this photo of the work being done this past October.
Sparks on the waterfront: Photographer Jeff Cooke captured workers building the NSCC Sydney Waterfront Campus Development. The new facility will feature a pedway crossing and will have state-of-the-art learning spaces and community spaces. It will also include four buildings that will be used by 1,400 students and 200 staff.
Company: Ellis Don Atlantic
Photographer: Jeff Cooke / Cooked Photography
Location: Halifax
The dismantling of the original Champlain Bridge bridge’s steel structure by the NHSL team generated a few sparks in the foreground and deeper in the shot as well. It was the perfect opportunity for photographer Pierre Seager to use a long exposure to craft this interesting night-time shot.
Company: Nouvel Horizon St-Laurent s.e.n.c (NHSL)
Photographer: Pierre Seager
Location: Montreal
Kinetic Construction installed three totem poles during the build of the Canadian Coast Guard Base Hardy Bay, including this 16-foot pole. The totem poles were designed and carved by local Kwakiutl First Nations artists. The installation was carried out by Kinetic Construction with support from a crane operator from Hardy Building Supply. The two 16-foot totem poles were installed at the entrance of the building, while a 30-foot pole was placed near the building, facing the ocean.
Company: Kinetic Construction Ltd.
Photographer: Jenn Mudge
Location: Port Hardy, B.C.
The replacement of a “beehive” warehouse roof by Graham Construction this past July required machines with long reaches, which provide an interesting contrast to the ceiling pattern captured through the lens of Michael Laursen.
Company: Graham Construction
Photographer: Michael Laursen
Location: Belle Plaine, Sask.
Company: Powell Contracting
Photographer: Philip Castleton Location: Milton, Ont.
A crew from Powell Contracting installs temporary construction barriers and energy attenuators to protect both construction crews and road users on a July day. The energy attenuators are used at the ends of the barriers for protection.
Company: Strabag Inc.
Photographer: Klaus Skruba
Location: Toronto
The tunnel foreman pauses after an exhausting July day assembling the bulkheads for the arch formwork for the lining of the 330 m long, 3.4 m internal diameter sewer extension tunnel at Toronto’s Ashbridges Bay Treatment Plant Integrated Pumping Station. The work is part of a $120-million Integrated Pumping station project.
Capturing a view of progress on the Bow River Bridge Project, at night, in Calgary. The twinning of the bridge is expanding the transportation infrastructure in the city.
Company: Flatiron Construction
Photographer: Nick McGrath
Location: Calgary
The entire construction industry has a big job ahead of it as we move through 2023: figuring out how to navigate economic uncertainty while continuing to thrive in an increasingly competitive market.
Lessons from the major upheaval in 2008 taught many how financial flexibility and quick decision-making were keys to survival. When the global construction industry started to point negative, some equipment owners held off from making fleet right-sizing decisions. Unfortunately, waiting to see if the markets would turn around quickly would prove costly.
Fast-forward more than a decade and we now know the importance of making smart, agile equipment decisions. We’d like to think we’re better prepared this time around, but the challenge of knowing where to start remains.
Better informed planning begins with an understanding of market conditions, and how existing fleet inventory correlates with upcoming project demands. Working with the right equipment dealer can help you craft the best solution for your fleet management strategy, and not repeat mistakes from 2008.
While the road ahead has the potential to be a bumpy one, there are ways equipment owners can prepare their businesses to weather the storm. The first is right-sizing the fleet using a combination of equipment rentals, sales and purchases to ensure there is balance between capital and operating expenses.
The second is maintenance and repair. Balancing scheduled and required investments in machine conditions and uptime help ensure maximum profitability and market value. A third is giving yourself the flexibility to manage the sometimes-difficult decisions that may become necessary.
Deciding on the right ownership mix is a combined effort between fleet owners, their financial advisors, vendors and dealers. A full-service dealer can be a critical part of this partnership. The right dealer can offer transparent advice on market values, machine condition and required maintenance, and ownership solutions. Conversations between the team can include harvesting equity from owned machines, adding used machines, rental purchase options (RPOs) and leases.
A benefit of replacing part of your fleet with used equipment is that you can better moderate cash flow and overall expenditures. Used equipment often maintains its value better on a balance sheet while still getting the job done.
When it comes to calculating depreciation, there’s no blanket approach. There are tools that can give estimates, but actual valuation is dependent on several factors, including condition, maintenance history, market trends, and supply and demand curves. Your dealer will be able to help determine value and overall market conditions, if you are thinking about selling.
With ongoing supply chain issues and manufacturing delays, new equipment can also come with long wait times. It’s often easier to find the right used equipment for upcoming projects and then resell it when
you have completed the work. An added bonus is that dealers are often able to source equipment from other locations to meet needs.
Reputable equipment dealers aren’t just out to sell used equipment. Many will also purchase old equipment in exchange for cash, which can help to support a business as it grows or even help with immediate cashflow if a need arises.
Just as a dealer can help by validating used equipment purchases, they can also help with the equipment’s maintenance schedule. Deferring maintenance or repairs can save money in the short run but this tactic can cost dearly when trying to sell or trade a machine.
Warranties are also an important part of any large purchase, and used equipment is no exception. Full-service dealers can offer warranties and even certify the condition on some machines. Increasingly, used equipment trends are following those of used car trends with “Certified Used” becoming an attractive feature for buyers.
No matter what 2023 brings us, having the right fleet strategy mix in place will help a company react quickly when needed. We can’t always predict what business will look like in the future, but having flexibility when market conditions are unpredictable is important. That starts by partnering with a reputable equipment dealer who can support you and your company through economic ups and downs.
INDUSTRY RECOGNITION IN ONTARIO
IN THIS ISSUE:
Acting on climate change has become an international priority, and the heavy construction sector is among the biggest contributors to CO2 emissions worldwide. As Canada’s largest general contractor, PCL Construction is leveraging Milwaukee Tool’s battery-powered MX FUEL™ Equipment System on the Cascade Power Project to lessen environmental impact, improve safety and efficiency on the jobsite, and reduce operating and maintenance costs.
Once commercial operations commence in 2023, this combined cycle power plant is expected to lead the transition from coal-fired power to clean electricity in Alberta.
“Our goal is to have the leading-edge technology to complete the project successfully and on schedule,” says Brian Waritsky, warehouse manager at PCL Construction. “With
MX FUEL™, we’re giving our tradespeople the ability to execute their work more effectively.”
As the construction sector searches for innovative ways to meet sustainable development goals, battery-powered technology provides one of the biggest opportunities to reduce harmful jobsite emissions that pose risks to end users and the environment.
“I’ve been on sites this size and larger where you can tell that the generators and compressors have been running all night, especially on those frigid Canadian winter mornings,” says Ken Hanley, general superintendent at PCL Construction. “Last winter, we didn’t experience that here.”
PCL Construction has been transitioning over to MX FUEL™ since discovering the
system delivered reliability and durability for heavy use on industrial projects without the hassles and hazards associated with gas and pneumatic equipment.
The company’s largest investment has been in the MX FUEL™ ROCKET™ Tower Light/ Charger with over two hundred units in their fleet. The tower light emits zero emissions, has a wheel-based design and weighs in at only 108 pounds, so moving it is a one-person job. For comparison, a diesel light tower requires refuelling, spill containment, and a forklift to place the unit because it weighs about 1,600 pounds.
“When we ran the data from 2019 to June 2022, our estimated fuel burn for diesel-powered light towers was 250,000 litres over this time period,” says Scott Sharun, senior procurement and equipment manager with PCL Construction. “If we remove one diesel light tower for a winter, we reduce emissions by an estimated 9.6 tonnes of carbon output per diesel light tower. That’s a game changer.”
The MX FUEL™ Equipment System eliminates exposure to the emissions, fumes and noise pollution of gas tools, especially when you factor in idling time. Battery-powered tools start with the press of a button and there’s no need for spill kits, spill trays and fire extinguishers.
“MX FUEL™ produces zero emissions inside buildings and eliminates the hazards associated with air lines and cords, both of which are huge safety improvements on our jobsites,”
says Roger Keglowitsch, chief operating officer for heavy industrial at PCL Construction.
Since some builds are vertical, getting lighting and heavy gas-powered equipment onto higher floors can also be challenging. The lightweight and cordless MX FUEL™ Equipment System removes limitations on jobsites where mobility is critical.
“Previously, your productivity only went to the end of an extension cord or to the elevation an air hose could reach,” says Waritsky. “MX FUEL™ allows our workers to be far more productive in more areas while mitigating safety concerns.”
PCL Construction is 100 per cent employee-owned, which drives accountability and engages every employee in the pursuit of more environmentally responsible construction practices. Transitioning to battery-powered tools has helped to reduce costs and waste, thereby aligning the company’s sustainability
goals with financial performance.
Gas and pneumatic tools involve more moving parts, increasing the chances of damage and reducing the tool’s lifespan. On top of that, it’s hard to find field mechanics who can service and repair small gas engine units for sites operating 24 hours per day, 7 days per week, and this impacts the site’s ability to stay operational and productive.
“We were replacing a lot of cords and parts with our older equipment,” says Sharun. “We’ve seen a significant reduction in service and labour costs with our MX FUEL™ fleet because there’s no risk of over-throttling, cords and hoses are gone, fouled plugs and burnedout mufflers are gone; and all the issues around fuel in winter on small combustion engines. Providing limited downtime and service requirements increases utilization as we aren’t waiting for parts or repairs.”
On top of that, because MX FUEL™ is ONEKEY™ compatible, PCL Construction has been able to geo-fence a project site and easily track
asset location to reduce loss by remotely disabling batteries when they wander off site.
Every project in PCL Industrial in Canada has access to or is currently using MX FUEL™. “We’re hungry for all the innovations that come with battery power,” says Sharun. “We want out of gas and diesel, and we want out of cords.”
According to Sharun, the ability to quickly deploy MX FUEL™ results in an operating site by lunchtime. Meanwhile, those using gas are still unwrapping skids, running cords everywhere and trying to figure out where to put their fuel tanks.
Tradespeople are also getting harder to attract, Hanley adds, so it’s important to show that you’re evolving and using the latest and greatest gear. “MX FUEL™ has allowed us to do that,” he says. “We’re able to make the best technology available for them to do their job and that makes them want to work for our company.”
For more information about MX FUEL™, visit milwaukeetool.ca/mxfuel.
Project Profile
Project: Greenfield combined cycle 900 MW power plant
Location: 16 kilometres south of Edson, Alberta
Jobsite size: 11 hectares (27 acres)
Approximate workforce: 1,080 people at peak
Construction started: September 2020
Total construction costs: $1.3 billion CAD
The MX FUEL™ CARRY-ON™ 3600W/1800W Power Supply (MXF002-2XC) delivers portable power on demand with no noise and no emissions. The MX FUEL™ 14” Cut-Off Saw (MXF314-2XC) can cut 72 pieces of #5 rebar per charge with zero emissions. The MX FUEL™ ROCKET™ Tower Light/Charger (MXF041-1XC) provides up to 27,000 lumens of lighting for both indoor and outdoor tasks.Concrete polishing produces floors that are extremely durable, easyto-clean and provide a polished look that many clients are looking for in their buildings.
With applications ranging from large, commercial buildings like warehouses where a client’s main focus may be durability, to commercial gyms where the desire for polish is mainly aesthetic, there are many reasons a client might choose a polished-concrete floor, so it is important to work with the building owner to understand what they want, and what can be delivered, when it comes to polished concrete surfaces.
Communication can help avoid pitfalls, since the multi-step process used to create these surfaces involves navigating variables in the concrete, and ensuring that you and your client are on the same page.
There are certain aesthetic expectations that customers tend to have when it comes to polished concrete, but between the architect bidding the project and the end-user, the reality of what can be achieved with a polished concrete floor may get lost in translation. If the only discussion about the finished floors has been between the architect and their customer, there is a risk of vision and deliverable misalignment.
Managing expectations starts with making sure the end customer understands the process. Creating polished concrete
floors begins with grinding the surface of the concrete using diamond tooling as an abrasive. Although the process produces a smooth surface, there can be a considerable variation in the end deliverable.
“The first question a contractor should ask is, are you looking for a very consistent, monolithic looking floor?” says Randy Wheelis, product training specialist for Bartell Global.
Polishing concrete is a beautification process, but like people, Wheelis explains that all concrete has personality. Through the process of grinding, densifying and polishing, Wheelis says that the personality of the floor will be brought to the forefront.
“By polishing the concrete, you reveal what is already there,” he explains. “Your customer needs to understand that any imperfection in the concrete like cracks, spalling marks, etc., those are going to be visible when you are done.”
Many customers are looking for the unique look that each polished-concrete floor retains, embracing how its cracks and imperfections create a truly one-of-a-kind project, but Wheelis advises that customers still need to be made aware of this lack of uniformity. “As long as your customer knows that they will not get a standard monolithic look, as a professional, you can proceed,” he says.
Paul Bravo, president of Bravo Cement Contracting, has worked on a variety of
projects for clients, ranging from schools to commercial warehouses. He says part of managing expectations is being upfront and properly illustrating the different finishes possible with this technique.
“When it comes to new-construction projects, there can be confusion between the architect hiring a concrete polishing contractor and the end-user who wants to achieve something very specific with their floors,” says Bravo.
Within his client base, there are three finishes that customers tend to ask for: a cream finish, a salt and pepper finish, and an aggregate finish. Bravo finds that architects are usually referring to the level of aggregate exposure when they ask for any of those finishes.
For some, the concept of a polished floor means that aggregate in the concrete will be exposed through the process of grinding. Bravo explains that a cream finish won’t expose any aggregate, however, adding that it is possible to achieve a finish that is closer to a monolithic look.
A salt-and-pepper finish exposes aggregates like sand and the occasional larger stone, while a full-aggregate exposure is closer to a terrazzo look, with large pieces exposed throughout the floor. The amount of aggregate exposure that can be achieved depends on the diamond grit used to polish the concrete. A coarse-grit diamond disc, which can execute a deeper cut into the concrete, will get the polisher closer to achieving an appearance similar to terrazzo.
Polished concrete floors are one smooth option that is not only durable, it’s eye catching as well.
Wheelis also abides by a certain set of definitions that help dispel some of the miscommunication that can happen with concrete and polished-concrete literacy. As with Bravo, is aim is for clients and contractors to share the same definition of what each finish is, and how it can be achieved.
Wheelis classifies finishes into four categories, ranging from a cream finish, a salt and pepper finish, and then two aggregate looks: a medium or a large aggregate exposure. With each level of exposure, Wheelis says the cut made in the concrete will be deeper.
“But even between these categories, you may find some larger aggregates in a salt and pepper look in random areas because, remember, you will never achieve that completely monolithic look,” he says.
For his clients, Bravo recommends the full-aggregate exposure. That look, he says, can be more forgiving, given the depth that the contractor is cutting into the surface. Lately, Bravo has noticed a trend with school boards asking for polished concrete,
and opting for a cream or salt-and-pepper finish. In schools, he says that look is often hard to achieve because of the unequal lay of the floor.
“You also need to keep in mind that these finishes cannot be achieved on all floors,” he says. “Cream finishes and finishes with little aggregate exposure require very flat surfaces if you want to get an even look.”
Both Bravo and Wheelis note a trend toward a cream finish for concrete floors. That is a look that it can be hard to achieve, and might not be possible, in some cases.
“If I have a client who is requesting a cream finish, I have to make sure that they know that they might get a bit of aggregate if there’s a high spot in the floor, because we often can’t do anything about high spots and concrete,” says Wheelis.
“What often happens is the contracting company will polish the floor, give the client a cream finish, and it will not look as uniform as they expected,” says Bravo, explaining that the limits of the finish
can lead to a dissatisfied building owner, which illustrates the need for proper communication.
To achieve the desired level of exposure, abrasives are a must. Wheelis explains that polishing to a salt-and-pepper- or heavy-aggregate exposure usually begins with a 40-grit metal bond diamond. Diamond grit can range from as low as six grit to as high as 300 grit. Some manufacturers even offer higher grit levels than that. His company, Bartell, carries four profiles, ranging from 16- to 150-grit.
The company’s 16-grit profile is its most aggressive, and is recommended for removing coatings like epoxy or glue. Wheelis says a 40-grit profile provides an average scratch, which he recommends for rough concrete, thin coating materials or to expose aggregate. For new concrete, he says 80-grit is a popular choice.
The abrasives are used in succession, each removing the previous grit’s scratch pattern as the machine operator works towards a smooth, scratch-free surface.
Once the grinding is finished, it is time to add a liquid densifier. Wheelis explains that his choice of a chemical densifier is sodium silicate because of its proven effectiveness for over 70 years, but there are many densifier options, including lithium silicates.
A densifier creates a reaction between the lime in the concrete and a chemical that fills in the small spaces in the concrete, which is porus. The result is a dense floor that should holds up to impact.
“I think people tend to forget that densifying is a chemical process. Densifiers harden over time to make the concrete durable. It hardens right away, but because it’s causing a chemical reaction, that can take more than nine months for the chemical reaction to make the concrete as hard as it will be in the end,” says Wheelis.
Once the concrete densifier has cured appropriately, the client can select a final surface gloss, ranging from almost no gloss all the way to a reflective shine. Burnish-
ing, the process of using a high-speed burnisher to heat, melt and shine a chemical product to the concrete surface is the start of building the shine.
This is another key area where Bravo recommends checking in with your customer, or asking the architect who bid the job to, to gauge what the customer wants to achieve with their polished floor.
Wheelis says that gloss meters are often used as a scale to measure the amount of light reflecting off the floor. He ranks a floors’ amount of gloss into four levels. Level one has little-to-no sheen, and registers as “no reading” on the scale. Level two provides the customer with a low-to-medium sheen and matte or satin appearance with slight reflection and registers at a 40-to-50 reading on the scale.
Level three has a medium-to-high sheen, where an observer can identify an object, but the image is not sharp. This registers at a 50-to-60 reading. Level four delivers a highly polished sheen with a high amount of light reflection and a gloss
reading of between 60 and 80.
Being able to present architects with a chart can ensure that all parties are again on the same page as the client selects the level of final polishing for their concrete.
“Architects are often the ones specifying the level of aggregate that the client wants, and what they want to achieve with their floors, but most of the time, what it takes to make sure that a client is going to end up with a product they’re satisfied with is a conversation between the concrete polishing company and the client, directly,” says Bravo.
Bravo suggests doing a site walkthrough or having a conversation with the client prior to tender, since different aggregate exposures, gloss finishes and protectants can require different processes, amounts of work, and therefore more money.
“Beyond that, it is always critical to do a test area to show the customer – the end-user – what the floor is going to look like,” adds Wheelis.
The Ontario Concrete Awards have been recognizing the exceptional work of owners, designers, contractors, and suppliers in Ontario’s construction industry since 2001. A celebration of creative projects and applications of the most used construction material in the world, this year’s awards feature a variety of commercial, residential and infrastructure projects.
1. Structural Engineering: Cast-in-Place
Name: Enwave Well Project
Details: Enwave constructed a large Thermal Energy Storage (TES) system as part of The Well development in Toronto. There was only 3,200 m³ of concrete in total but approximately 2,400 m³ was poured using a stationary pump at street level down approximately 70 ft to the bottom of P7 and then distributed to various discharge points around the perimeter of the tank.
Location: Toronto, Ontario
Owner: Enwave Engineer: Stantec
General Contractor: C&M McNally
Material Supplier: St. Marys CBM
Additional Participants: Master Builders Solutions
2. Structural Engineering: Precast
Name: Lodestar Structure’s Precast Concrete Modular Building System
Details: Lodestar Structures is a family of Precast Concrete Modular Building components designed for rapid and sustainable construction for residential and commercial applications.
Location: Kingston, Ontario
Owner: Anchor Concrete Products Ltd.
Architect: Anchor Concrete Products Ltd.
Engineer: Anchor Concrete Products Ltd.
General Contractor: Anchor Concrete Products Ltd.
Material Supplier: Anchor Concrete Products Ltd.
3. Specialty Innovation Technology
Name: TrueCure (at Garden District Condos)
Details: CBM’s TrueCure system takes the guesswork out of determining in-place concrete strength development. It does so by curing test cylinders to the natural hydration curve of the in-place concrete.
Location: Toronto, Ontario
Owner: The Sher Corporation
Structural Engineer: Jablonsky, Ast and Partners
General Contractor: SKYGRiD Construction
Material Supplier: St. Marys CBM
Additional Participants: EXACT Technology
4. Material Development & Innovation
Name: EvoBuild
Details: ANC Modular approached Hanson Ready Mix while in patent design development of a volumetric modular void form system. This system allows developers to
Macro Synthetic Fibers for Concrete
Fibrillated Micro Synthetic Fibers for Concrete Monofilament Micro Synthetic Fibers for Concrete
Macro Synthetic Fibers for High-Ductility Concrete
Macro Synthetic Fibers for Shotcrete Applications
High-Performance Monofilament Micro Synthetic Fibers for Concrete
Functionality is the main requirement for concrete flooring in industrial and commercial environments. In addition to a very high aesthetic quality, MAPEI products provide excellent flatness and dimensional stability, partially or completely eliminating the need for traditional metal reinforcement and contraction joints.
For more details, visit www.mapei.ca or contact 1-800-361-9309.
have a concrete superstructure without the need to use conventional forming methods.
Location: Ontario
Owner: ANC Modular Inc.
Engineer: J.H. Cohoon Engineering
General Contractor: ANC Modular Inc.
Concrete Contractor: ANC Modular Inc.
Material Supplier: Hanson Ready Mix
Additional Participants: Sika Canada Inc.
5. Sustainability: Pre-Cast
Name: Roxborough Apartments
Details: Roxborough Park is built to passive house standard and is comprised of 103 one & two-bedroom units ranging from 500 to 1,000 sq. ft.
Location: Hamilton, Ontario
Owner: CityHousing Hamilton
Architect: KNYMH Inc.
Passive House Consultant: JMV Consulting
Construction Manager: Legacy Constructors Inc.
Material Supplier: Stubbe’s Precast
Additional Participants: LANHACK Steelcon Inc.
Sika Canada Inc.
6. Mid- to High-Rise Residential: Precast
Name: Gaslight Condos
Details: One of the goals with the Gaslight
condominiums in Galt was to produce a similar feature style to the historic buildings surrounding it, while giving it a newer, appealing, eye-catching look.
Location: Cambridge, Ontario
Owners: HIP Developments
Stubbe’s Precast
Engineers: MTE Consultants
Rizz Engineering Inc.
Architect: ABA Architects Inc.
GC: Melloul-Blamey Construction Inc.
Precast Supplier: Stubbe’s Precast
Additional Participants: Sika Canada Inc.
7. Mid- to High-Rise Res.: Cast-in-Place
Name: Oak & Co
Details: This multi-tower high-rise residential building includes a tower that consists of a 1,200 m³ raft slab pour that used two pumps and had six suspended transfer slabs. Approximately 52,000 m³ of concrete delivered to site from three different production facilities.
Location: Oakville, Ontario
Owner: Cortel Group
Record: Zeidler Architecture
Record: RJC Engineers
General Contractor: Expo City Management
Material Supplier: Dufferin Concrete (A CRH Company)
Additional Participants: Euclid Canada
MCF Highrise
8. Architectural Hardscape
Name: Canada Summer Games Building and Park
Details: Lafarge was contacted by Aquicon to supply concrete for the construction of a legacy facility at the Canada Summer Games Building and Park, this included foundations, slabs, steel gray coloured concrete for polished floors, and the exterior hardscape concrete.
Location: Thorold, Ontario
Owner: Canada Games Host Society / Canada Games Council
Architect: MJMA / Raimondo & Associates
Engineer: Blackwell Structural Engineers
General Contractor: Aquicon Construction
Hardscape Contractor: UCC Group Inc.
Material Supplier: Lafarge Canada Inc.
Additional Participants: Euclid Canada
Tri-Con
Master Builders Solutions
9. Infrastructure: Cast-in-Place
Name: Bramalea GO Station
Details: The Bramalea GO Station redesign creates a cohesive and efficient transportation centre. The extensive use
of durable concrete products in various forms and finishes in the facility’s design delivers aesthetic appeal and enhanced permanency.
Location: Brampton, Ontario
Owner: Metrolinx
Architect: IBI Group Architects (Canada)
Engineer: RJC Engineers
GC: Kenaidan Contracting Ltd.
Material Supplier: Innocon Inc.
Additional Participants: Belmont Concrete Finishing Co. Ltd.
Fermar Paving Ltd.
Master Builders Solutions
Pre-Con
The Downsview Group
10. Infrastructure: Precast
Name: Duchesnay Creek Bridge, MTO Project 2018-5106
Details: The Duchesnay Creek Bridge replacement was built using laminated, high quality Douglas Fir girders and a bridge deck constructed with 28 precast deck panels.
Location: North Bay, Ontario
Owner: Ontario Ministry of Transportation, Northeastern Region
Engineer of Record: LEA Consulting Ltd.
General Contractor: Nipissing Miller
General Partnership
Material Supplier: Miller Northern Precast
Additional Participants: Sika Canada Inc.
11. Sustainability: Cast-in-Place
Name: 360 West Condos
Details: The units at 360 West Phase 1 are constructed using Insulated Concrete Forms formwork utilizing full height concrete construction from the footings all the way up to the roof lines in order to provide strong and energy efficient buildings.
Location: Tillsonburg, Ontario
Owner: 360 Developments
Architect: Ernst Construction & Design
Engineer: Strik Baldinelli Moniz Ltd.
General Contractor: Braunz Construction
Material Supplier: Lafarge Canada
Additional Participants: Master Builders Solutions
12. Architectural Merit
U of T Schwartz Reisman Innovation Centre (SRIC)
Details: The 15-storey research and innovation centre has monolithic panels that span floor to floor. A CNC machine was used to produce the custom forms to achieve the desired angles and slopes of
the precast panels.
Location: Toronto, Ontario
Owner: University of Toronto
Architect: Teeple Architects Inc.
Engineer: Cole Engineering Group
General Contractor: EllisDon
Material Supplier: TKL Group Inc.
Additional Participants: Euclid Canada
13. Institutional Building
Name: The Nicol Building
Details: The thought, time, and planning that went into the design, manufacture, storage and installation of special architectural panels resulted in an eye-catching 115,000 sq. ft. building.
Location: Ottawa, Ontario
Owner: Carleton University
Architect: Hariri Pontarini Architects
Engineer: Thornton Tomasetti Canada Inc.
General Contractor: HEIN
Material Supplier: Central Precast
Additional Participants: Euclid Canada
14. Specialty Concrete Construction
Name: Boulevard Lake Dam Rehabilitation
Details: The rehabilitation of the Boulevard Lake Dam included the widening of the bridge deck over the dam, the addition of an architectural viewing platform, architectural lighting and stainless steel railings.
Location: Thunder Bay, Ontario
Owner: City of Thunder Bay
Engineer: TBT Engineering Limited
GC: Concrete Walls, PDR Contracting
Material Supplier: Canada Concrete Corporation
Additional Participants: Euclid Canada Miller Precast
Concrete professionals kicked the year off with a highly attended World of Concrete show, the world’s largest trade show for the concrete and masonry sectors. This 49th edition of the annual event, held once again in January at the Las Vegas Conven-
“The 2023 edition of World of Concrete far exceeded our expectations. The crowded show floor and packed educational sessions proves how essential meeting face to face is, that it remains important now more than ever to have a space to connect, to learn, to share across the concrete, masonry and construction industries as a vital contributor to our economy,” stated Jackie James, vice-president of the show. “In-person attendance is on its way back to pre-pandemic levels and
improvements, and a massive range of original manufactured equipment from excavators to wireless concrete sensors. Also generating some significant interest was the display of modern materials like eco-driven autoclaved aerated concrete.
At this year’s edition of the Spec Mix Bricklayer 500, Michael Schlund and his tender Arron Kowalski laid 759 bricks in one hour to take the title of World’s Best Bricklayer. Schlund walked away with a new Ford F250 4x4 Super Duty truck, an Essick Pro12 Mixer, and more than $15,000 in cash and prizes for his efforts.
This year, World of Concrete also offered more than 160 technical sessions, including hands-on training, safety expertise and business development. Noted new additions to the 2023 education program were eight concrete basics and leadership courses presented in Spanish, a revamped three-hour comprehensive concrete repair track, and new workshops focusing specifically on women in construction.
tion Center (LVCC), put a focus on product innovations, new technologies and technical discussions.
Registrations for this year’s show, which was presented by Informa Markets, topped 48,000, generating heavy foot traffic on the show floor as trades professionals from more than 120 countries were in attendance.
the World of Concrete event leads global trends in construction.”
Notable highlights from the indoor and outdoor product displays, demonstrations and competitions included the first ever mobile 3-D robotic concrete printer and AI site map printer, top-of-the-line work trucks with electric batteries and aerodynamic
“World of Concrete is proud to support laborers in education and connection providing opportunity to advance the industry toward enhanced sustainability, efficiency and safety, and continuing growth,” stated Kevin Thornton, senior vice-president of construction at Informa Markets.
World of Concrete will return to Las Vegas in 2024 for its 50th anniversary show. The event is slated for January 23 to 25 with education sessions kicking off on January 22.
World of Concrete show had throngs of attendees providing an energy not seen since before the pandemic.
GOMACO offers the full range of concrete slipform pavers, curb and gutter machines, trimmers, placer/spreaders, texture/ cure machines and bridge/canal finishing equipment. GOMACO equipment features our exclusive and proprietary G+® control system, created in-house by our software engineers from the wants and needs of contractors paving in the field. At the heart of GOMACO equipment is our passion for concrete and our commitment to our customers. We look forward to visiting with you about your upcoming paving projects and your concrete paving equipment needs. Our worldwide distributor network and our corporate team always stand ready to serve and assist you.
Attended by more than 125,000 visitors and held every three years at the Las Vegas Convention Center (LVCC), the CONEXPO-CON/AGG show is one of the largest trade shows in North America, and is by far the largest for the construction industry. And this year’s show is shaping up to be the biggest yet.
“The addition of the new West Hall and Diamond Lot at the Las Vegas Convention Center gave us, and our exhibitors, a number of new opportunities to show how we are taking the construction industry to the next level,” said show director Dana Wuesthoff. “Now at 2.8 million square feet of exhibits, there’s more for construction pros to see than ever before.”
The show, which will be almost five per cent bigger than its record-setting 2020 edition, will feature 1,800 exhibitors and more than 175 education sessions during its run from March 14 to 18.
Although it will be the largest CONEXPO ever, recent additions to the LVCC will make it easier than ever to get
around the grounds. Opened to convention center traffic in 2021, and located beneath the entire LVCC campus, is the Convention Center Loop, an underground transportation system designed by Elon Musk’s The Boring Company. The system of Tesla vehicles transports convention attendees throughout the campus in under two minutes, free of charge.
“We are excited to welcome CONEXPO-CON/AGG back to Las Vegas for another record-setting event,” said Brian Yost, chief operating officer of the Las Vegas Convention and Visitors Authority (LVCVA), which owns and operates the LVCC.
“The addition of the West Hall and the Convention Center Loop will only further enhance the ‘Only Vegas’ experience for
Technology and sustainability two big attractions as the North American construction industry’s largest show ramps up for Vegas.
attendees and exhibitors.”
Construction pros are ready for the show to return as well. As of December, attendee registration was running at nearly double the pace it was for the same month ahead of the 2020 show.
“This is the event that construction professionals, especially those making company-level decisions, and those needing professional development hours, can’t miss,” said show chair and Caterpillar senior vice-president Phil Kelliher. “Seeing the new equipment and techniques on a screen doesn’t compare to seeing it all in person. At the show, you can see the equipment, ask questions of the manufacturers themselves, and really understand what the equipment and education can do for your career and business.”
A core theme that will be visible in the offerings from many of the exhibitors is sustainability.
“The construction industry and CONEXPO-CON/AGG are evolving in many ways to adapt and showcase sustainable technologies, products and practices supporting a more sustainable world,” said Wuesthoff. “More than ever, show attendees will see sustainability in action, from electric and hydrogen powered construction equipment, to more recyclable materials and waste reduction opportunities, to changes we’re making to the show to better support sustainability.”
In addition to the sustainable technologies, products and practices on display across the show floor, event organizers have also given sustainability its own education track in its seminar offerings.
With more than a dozen sessions
planned, speakers will address such subjects as reducing the carbon footprint of concrete, getting and managing electric construction equipment, asphalt and concrete recycling, carbon neutrality, and a “Sustainability 101” session for those just starting their sustainability journies.
CONEXPO-CON/AGG show organizers are also committed to reducing the environmental impact of the show itself, and have partnered with vendors dedicated to sustainable practices and reducing waste, while helping exhibitors choose more sustainable options. They will also be measuring the show’s total 2023 environmental impact to identify potential areas for future improvements.
In a statement leading up to the event, show organizers explained that sustainability efforts at CONEXPO-CON/AGG reflect the focus on sustainability within the entire construction industry, explaining that many construction companies have realized that clients are demanding sustainable building practices on projects, so contractors themselves are recognizing benefits from moving to more sustainable equipment and practices.
Principal sponsors of the event are the Association of Equipment Manufacturers (AEM), the National Ready Mixed Concrete Association (NRMCA), and the National Stone, Sand & Gravel Association (NSSGA). The show sponsor is the Associated General Contractors of America (AGC), with AEM producing the show.
For more information about CONEXPO-CON/AGG, or to register with a 20 per cent discount using code MEDIA20 by March 13, visit www.conexpoconagg.com.
New meeting area to feature lively discussion and a place to recharge with friends, old and new.
Dave Turin of Discovery’s Gold Rushand Dave Turin’s Lost Mine and Aaron Witt, founder of BuildWitt, will be headlining conversation in the Community Zone, a new addition to the show.
The Community Zone is an area in the Festival Lot of the show where construction pros can gather to network, grab some refreshments, and participate in different events.
“It’s good to come back to CONEXPO-CON/AGG,” said Turin. “I learn so much every time I come, and I’m proud to lend my own experience and story to the thousands of construction pros that come each time.”
Turin last joined Witt at CONEXPO-CON/AGG 2020 for an episode of the BuildWitt podcast. This time, they’ll open the Community Zone with an enthusiastic, informative, and entertaining talk, followed by a question-and-answer session open to everyone at the show.
“Dave is such a great voice for the construction and mining industries,” said Witt. “His story, having grown up in his family’s quarry business, and then turning to full-time mining, and all the equipment involved in both businesses, has given him a lot of unique experience I can’t wait to help share.”
“The Community Zone is the kind of area attendees have been asking for,” said show director Dana Wuesthoff. “It’s a place for construction pros to recharge their devices and recharge themselves, all while still being able to continue learning and enjoying their experience.”
Turin and Witt will be in the Community Zone Tuesday, March 14, from 1 to 2 p.m. In addition to the session with Turin and Witt, conversations with other special guests are scheduled for Thursday and Friday, and the Community Zone will feature live music, influencer meetups, and a concession area every day of the show.
Blueprints, the blue-coloured project drawings, disappeared decades ago, but the term blueprint has survived as a general descriptor for detailed plans of action. That updated definition aptly applies to current VDC models which can now accommodate an unlimited variety of images, specifications, descriptions, verifications, and other elements.
“There’s only so much you can put on a construction drawing,” says Ben Ferrer, national director of virtual design and construction at Turner Construction. “But now that you’re in a digital environment, the sky is the limit on the amount of detail and data that you can put into a model.”
These capabilities are only beginning to find use cases in construction, but compared with what’s possible, contractors are only scratching the surface. Looking at details about materials, for example, a company can measure and track the environmental footprint of a project, fine-tune allocation of resources, or factor supply chain constraints into a project schedule.
“The data we’re using fits into two different buckets,” says Daniel Doherty, manager of integrated construction technology at PCL Construction. “One is data formatted for specific applications such as drone flight data, 3-D scan data, or virtual coordination. The other bucket is data that we’ve always had but never fully utilized, for example, asset data, labour distribution, weather information, and trade-specific productivity. These might have been tracked in some way in the past, but never correlated with each other fully. This is why we’re eagerly awaiting the realm of AI.”
Focusing on areas where contractors specialize is one way of getting a solid return on investment for expanding the model.
“The way we’re approaching this is to start with something
“All of a sudden, we’ve gone from a couple of software touch points for the project manager or site superintendent to easily a dozen or more,” says Hammad Chaudhry, national director of digital project delivery, digital and data engineering for EllisDon. “We have so many more ancillary tools coming up that you end up with a conundrum of hundreds of different applications, each with its own data. So, as we’ve seen with other industries, the evolution is towards integration of these data sources in a way that reduces duplication and inefficiency, and the number of touch points for people that rely on the data.”
The model has to not only be accessible, but also be clearly valuable.
“Our first point of view is that we have to make sure that field teams can easily access and navigate those models,” says Julian Clayton, vice-president, product – general contractors at Procore Technologies, “because a lot of the times just visualizing that model can drastically improve productivity and reduce rework.”
One of the most powerful accelerators of technology is the universal adoption of standards that support interoperability and collaboration, and greatly improve the economies of scale for digitizing business processes. Canada lags behind many countries in mandating such standards for government projects.
“When it comes to digital constructuction and BIM and VDC processes, Canada is pretty much a free-for-all in the sense that there’s no driving force right now,” says Steve Rollo, national BIM and VDC manager at Graham Construction and Engineering LP.
As Rollo points out, there’s an international group of companies and associations promoting the Open BIM standard.
“This is a global data discussion in the sense that data is consistent no matter where you are in the world,” says Rollo. “The leader in this is the U.K., where you can’t bid on projects anymore without a certain level of VDC. They’ve been very successful with that, and I think that in Canada, we’re missing an opportunity.”
that’s predictable, repeatable, and well understood,” says Matt Lawrence, director of engineering technology services at Kiewit. “We do a lot of solar projects, and we know what all the components look like. So, we’re able to take drone images, process that using AI, and automatically feed real-time progress information into our project control software.”
One of the toughest challenges is ensuring that the model remains easily accessible by people who depend on it for realtime updates.
“We’ve seen a major shift in the U.K. because of government policy,” says Chaudhry. “Canada has made a lot of progress too, in terms of competing on the global stage, and even without government policy we are able to lead, but if government policy were at the same level as the U.K., it would help bring forth a digital- and data-first approach to procurement.”
Until recently, virtual design and construction (VDC) was primarily about replacing paper drawings with 3-D digital images. That’s changing as contractors begin to digitize their business processes.
“But now that you’re in a digital environment, the sky is the limit on the amount of detail and data that you can put into a model.”
Break new ground, win more work and complete it more profitably with a unified platform for heavy construction estimating, operational workflows and business insight.
HEAR SHANNON’S SUCCESS STORY AND MORE AT B2WSOFTWARE.COM/SHANNON
We’re more agile, efficient and connected with the B2W platform.
Risk allocation has been a hot topic within the construction sector for as long as I’ve been in the industry. Over the past decade this issue has climbed the ranks of the hot topic list and is now often cited as a top three issue within the construction industry. And it is a top issue globally.
The overarching position is that owners are foisting too much risk to construction contractors and design consultants, often through a design-build delivery model.
Studies conducted over the past 10 years clearly show that the delivery models (and contracts) currently being used in much of the world’s construction projects are not delivering when it comes to budget, schedule and expected benefits.
A recent Harvard Business Review article by Bent Flyvbjerg and Dan Gardner looked at a study of 16,000 major projects. Only 8.5 per cent were done on-time and on-budget. Only a half-percent of all these projects delivered the expected benefit.
Basically, 99.5 per cent of all projects failed to deliver the expected outcome of the owner. Granted, the construction industry deals with more unknown unknowns than most industries, but when 99.5 per cent of construction industry clients feel they did not receive what they had expected, there is room for improvement.
What is being done to improve customer satisfaction within the construction sector? One hot topic is the growing use of new delivery models, including models with a much greater degree of collaboration between the three key stakeholders to the construction project: the owner, the contractor, and the designer.
The use of a more collaborative, all-stakeholder early involvement delivery model (and contract) is a great idea, however, there is one problem: These models are not being adopted at a very rapid pace globally. The overwhelming majority of project delivery models use either a bid-build or design-build framework, which are the two main delivery models that drive lower collaboration .
What can be done to grow the use of more collaborative delivery models? One key is for the owner community to educate themselves about the delivery models to grow comfortable with them. Education takes time, however, and perhaps a better path is to see if any of the collaborative practices housed within the other models can be applied to traditional delivery models.
The idea is to use select practices or clauses from these collaborative models to allow an owner to “dip their toe” into the collaborative project delivery model pool.
To that end, the following are some of the top practices/clauses that could conceptually be ported to the more traditional delivery models which should allow the owner a more measured approach to experimenting with collaboration within their contracts:
1. Collaborative Behavioural Assessments: In the bid stage, use these collaborative behavioural assessments of potential bidders, borrowed from alliance contracts, to determine which team will work best with the owner.
2. Co-locating of Stakeholders: Require key stakeholders to the contract to physically work together as the project is being carried out. Physical proximity breeds collaboration.
3. Contingency Sharing: Open contingencies up to major construction stakeholders using the concepts of “skin in the game” or a “carrot in the game” to drive better collaboration and alignment.
4. Conflict Avoidance Procedures: Put procedures in place that avoid conflict and bring out the issues in a solutions-oriented manner.
5. Alternative Dispute Resolution: Use the power of less adversarial dispute resolution techniques.
These are just five examples of practices or clauses that could be used in traditional contractual models to allow owners to “test drive” collaborative practices within their contracts. There are many others. All construction stakeholders should be encouraged to seek out the entire inventory of collaborative practices and clauses that can be brought to projects.
Early signs from the insurance sector indicate that these collaborative practices are reducing insured losses and, by capturing and collating other performance metrics, owners could compile the necessary evidence to more fulsomely embrace collaborative contracting practices.
David Bowcott is the managing director, construction, at NFP Corp. Please send comments to editor@on-sitemag.com.
Arecent Alberta Court of Appeal decision, Tempo Alberta Electrical Contractors Co. Ltd. v. Man-Shield (Alta) Construction Inc., continues the debate started by the Supreme Court of Canada in Stuart Olson Dominion Construction Ltd. v. Structal Heavy Steel regarding posting security to vacate liens and discharging trust obligations under builders’ lien legislation.
In the Tempo case, the Alberta Court of Appeal decided that security paid into court to discharge a lien, pursuant to section 48 of Alberta’s lien legislation — now Alberta’s Prompt Payment and Construction Lien Act (PPCLA) — may be substituted for a different form of security, provided there is no resulting prejudice to the lien holder. However, the court also determined that cash paid into court as security may not be substituted with other security, such as a lien bond, where those funds are impressed with a statutory trust.
Posting security into court to discharge builders’ liens is a key function of lien legislation across the country. The registration of a lien on title to a project stays the hand of the paymaster, which can bring a project to a halt, expose those continuing to work to increased risk of non-payment, and create cash flow challenges. To mitigate these consequences, lien legislation creates a process by which the lien may be discharged, contract funds continue to flow, and the lien claim be resolved without compromising the protections afforded to the lien claimant.
Where security is posted for the amount the lien claim, plus costs, the security will stand in place of the land and the registered lien will be discharged from title. It is typical to post a lien bond, rather than cash, as security to discharge a lien to maximize operational cash flows. Once the lien has been discharged, the owner can resume making payment.
The PPCLA is, however, silent on the ability to substitute cash for security (or vice-versa). On that point, the Alberta Court of Appeal concluded that the PPCLA permits substitution of the form of security, absent demonstrable prejudice to the lienholder.
However, the nature of a lien bond is such that if the lien is ultimately determined to be invalid, the claim against the lien bond is extinguished. Unlike a lien bond, where cash has been paid into court, the funds paid into court may also be impressed with a trust and a trust claim could still be made against the funds even if the lien claim is found to be invalid.
Whether a trust actually exists may vary by province, as the statutory trust provisions differ. For example, in Alberta, the trust provisions are only engaged when the owner makes a payment after a certificate of substantial performance is issued. Regardless, because a lien bond would not respond to a breach of trust claim, replacing funds that are impressed with a statutory trust with a lien bond could arguably put the trust funds at risk.
In Tempo, the Alberta Court of Appeal focused on this issue when deciding the lower courts erred and that the application for the substitution of the security ought to have been dismissed.
Though each case must be considered on its facts and the specific wording of the applicable lien legislation, similar judicial activism has appeared in similar Manitoba cases and is present in the Supreme Court of Canada’s reasoning in the Structal case.
Notably, lien statutes across the country have mechanisms to post security for lien claims and not trust claims. In Tempo, the cash paid into court by the owner was to stand in place of the lands to discharge a builder’s lien, not as security for the subcontractor’s trust claim (which had not even been advanced). Nonetheless, the Alberta Court of Appeal determined that the cash paid into court had been impressed with a statutory trust and therefore should not have been substituted with a lien bond. This was despite the fact that the lien claimant would suffer no prejudice to its lien claim, which suggests that the court came to this conclusion based on prejudice that the substitution of security would have on a statutory breach of trust claim.
The Tempo decision provides clarity with respect to a party’s ability to substitute security under the PPCLA and may provide guidance to other jurisdictions. However, the decision is also another example of an emerging trend in Canada where courts demonstrate a willingness to protect the rights of trust claimants under lien legislation and may arguably be creating a security for trust claims where none expressly exists.
Trish Morrison, partner and national business leader, and Theron Davis, senior associate, are construction lawyers at Borden Ladner Gervais LLP. This article provides an overview and is not intended to be exhaustive of the subject matter contained therein. Although care has been taken to ensure accuracy, this article should not be relied upon as legal advice.