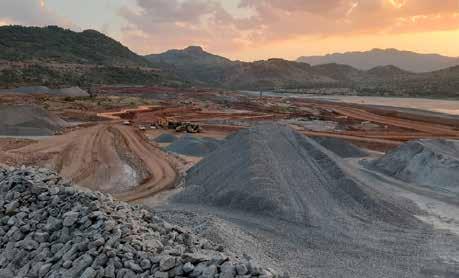
1 minute read
Mareesburg Tailings Storage Facility (Phase 2) by SRK Consulting for Anglo American Platinum, Limpopo
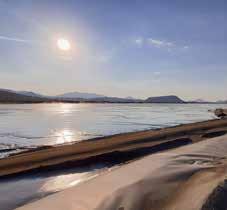
PROJECT TEAM
Advertisement
Client: Anglo American Platinum
Design & Construction Management:
SRK Consulting Contractor: Stefanutti Stocks
Serving the Mototolo Concentrator near Steelpoort in Limpopo, the Mareesburg Tailings Storage Facility (TSF) is Anglo American Platinum’s first TSF to be built on a high-density polyethylene (HDPE) liner.
The locally manufactured dual-textured HDPE liner was used in place of previously imported liners, requiring detailed analysis before acceptance. SRK Consulting (appointed to do the design and construction of the TSF) had to embark upon an extensive research and testing process, while engaging with regulatory bodies.
While it enhanced the environmental performance of the TSL, the inclusion of the HDPE liner also introduced a number of technical challenges that SRK was required to resolve in its design. Among the challenges was the lack of economically accessible clay material to create the layers beneath the HDPE liner, as normally required by environmental regulations. Testing revealed that the permeability characteristics of tailings from the plant were similar in important respects to clay, and this was used instead.
Furthermore, the topography of the TSF site is generally steep, extending from the base of a hill at an elevation of 1 077 metres above mean sea level (mamsl) up the hill to a final proposed elevation of 1 190 mamsl. This variability of the geology affected the founding conditions for the structures and sourcing of construction materials. To ensure stability on this hillside facility, rigorous testing was conducted on the liner strength, by a specialised laboratory abroad. In response to a lack of suitable locally sourced and commercially available material, the project created an alternative granular material from mine waste rock.
The client required an alternative to plastic pipes in the drainage system, leading SRK to design drains and filters of natural material. No commercial sources for such aggregate were locally available. Therefore, the design included the on-site manufacture of the requisite sized aggregate from the mine’s waste rock facility. These drains were selected as a safety risk mitigation, in place of more common plastic drainage systems, due to the concern of their long-term deformation and failure.
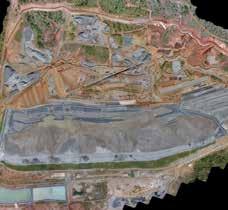
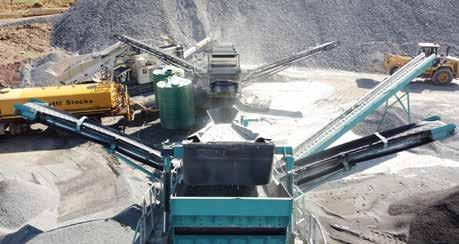