
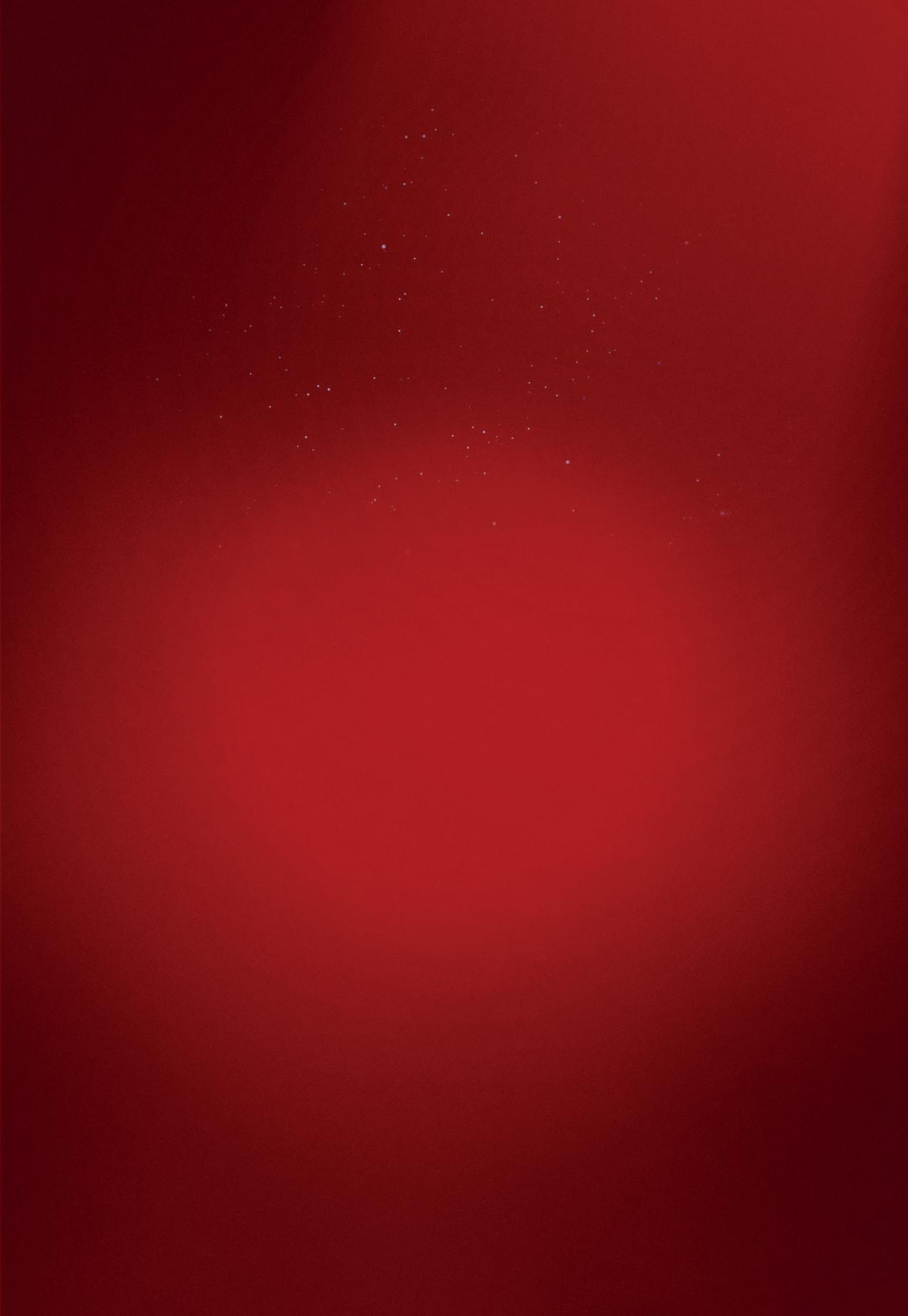
Full offering
- Full range vehicles with the most advanced technologies
- Highly customized product driven by market needs and optimized Total Cost of Ownership
High capillarity of aftersales
- Repair and Maintenance contracts and competitive warranty conditions
- Origin 100% IVECO Parts and a widespread network coverage
European technology
- High quality complete line-up in terms of tonnage, power, torque, safety, ergonomics
- High performance and robust trucks for extreme Off-road conditions
Customer centricity
- Comfort, ergonomics and the latest safety technology to make on board easier
- Driver Style Evaluation tool on Heavy ON-road range and optimized vehicle design to improve customer profitability
At Almajdouie Logistics, our dedicated team provides tailored solutions that prioritize safety, drawing on our extensive industry experience.
With a commitment to excellence and customer satisfaction, our innovative services are designed to meet clients' unique needs. This dedication to exceeding expectations has earned us their continued trust.
Our organization specializes in delivering comprehensive solutions for mega projects across Saudi Arabia, the Middle East, and the Far East. With a strong commitment to sustainability, we actively participate in national renewable energy initiatives.
SIGNATURE MEDIA FZ LLE
P. O. Box 49784, Dubai, UAE
Tel: 04 3795678
Email: info@signaturemediame.com
Exclusive Sales Agent
Signature Media LLC
P.O. Box 49784, Dubai, UAE
Publisher: Jason Verhoven jason@signaturemediame.com
Editor: Abigail Mathias abigail@signaturemediame.com
Art Director: Johnson Machado johnson@signaturemediame.com
Production Manager: Roy Varghese roy@signaturemediame.com
In current times, Material Handling involves the movement, storage, protection, and control of various materials throughout manufacturing, warehousing, distribution, and disposal processes. This month, we closely examine some of the key trends shaping this vital aspect of the industry.
For starters we bring you the future of logistics. The lead story showcases the ingenuity of SSI Schaefer, a global leader providing cutting-edge intralogistics automation solutions. The company’s commitment and expertise are evident in its steps to support the Middle East and Africa region with the integration of advanced technologies and strategic infrastructure, instilling confidence in the region’s logistics expertise.
The rising cost of commercial space is a challenge not only in the region, yet it is pushing businesses to maximize their existing footprints worldwide. This aspect is brought to light by entrepreneurs like Addverb and Landmark Group’s Kuwait fulfilment centre, who have come together to shape the future of retail logistics with ingenuity and precision.
While the industry’s focus remains on enhancing efficiency, reducing costs, and adapting to changing market demands, putting people first, is also an aim of international logistic companies. Recently recognised as a ‘Great Place to Work,’ in the mid-size category, we offer an exclusive interview with Shubhendu Das, Managing Director of Hellmann Worldwide Logistics, India. He highlights the values of the company incorporated in day-to-day operations.
Printed and Distributed by Masar Printing and Publishing L.L.C., Part of Dubai Media Incorporated Dubai, UAE
Contributor’s opinions do not necessarily reflect those of the publisher or editor and while every precaution has been taken to ensure that the information contained in this magazine is accurate and timely, no liability is accepted by them for errors or omissions, however caused. Articles and information contained in this publication are the copyright of Signature Media FZ LLE & SIGNATURE MEDIA LLC and cannot be reproduced in any form without written permission.
We bring you an intimate conversation with, Fatima Ait Bendawad, DHL Global Humanitarian Logistics Competence Centre Head, DHL Humanitarian Logistics, for her take on the complexities of issues and how she navigates the system to reach critically needed material aid and relief goods to those who desperately need it.
We also look at Saudia Cargo, which has launched its newest campaign. In keeping with the company’s swift and reliable shipping services to multiple destinations across China. The initiative underscores Saudia Cargo’s commitment to empowering Saudi exports and also aligns with Saudi Arabia’s Vision 2030.
Slimstock offers an engaging perspective on Excel and asks if it is holding data driven business back when it comes to real time collaboration.
This issue also has an exclusive academic discussion on the future of supply chain management with Dr. Bachir Sentissi, Executive Director of Atracio Solutions, Middle East and Jason Verhoven, Publisher, Global Supply Chain
Our regular selection of the latest news, international logistics events, business analyses, commentaries, professional contributions, OpinionEditorials (OpEds), and useful content, all of which are well encapsulated to offer you an issue that you won’t want to put down.
Wishing you a pleasant read.
Abigail Mathias Editor, Global Supply Chain abigail@signaturemediame.com
www.globalsupplychainme.com
40 GWC – Qatar’s leading warehouse company
Shaping
Addverb and Landmark Group elevate retail operations across the Gulf Cooperation Council.
Exclusive interview with Fatima Ait Bendawad, DHL Humanitarian Logistics.
A market leader in logistics services. 42 OpEd-IATA on regional air freight Cargo levels on ‘Solid Ground’ - Director General.
Is it time to move on from redundant data solutions or do they offer more?
What makes this international conglomerate a ‘Great Place to Work’.
Port and terminal operator handles over 10 million TEUS at Hamad Port.
Promises to be a landmark gathering for the global logistics and supply chain sector.
An engaging dialogue between Dr. Bachir Sentissi and Jason Verhoven.
GSA in
and Oman as Middle East operations expand.
Power of customization and automation in software development.
Up to date news of the industry.
Addressing the challenges and finding solutions that would transform the middle east & africa (mea) region into a worldclass logistics hub.
As industries worldwide embrace technological advancements, the MEA region stands at the cusp of a transformative era in warehousing and intralogistics. Automation, whether it was once a futuristic concept or a ‘wish list’ of big corporations, is now a proven and critical driver of efficiency, productivity, and innovation. Over the past few years, the region has witnessed a dynamic transformation in its logistics and warehousing sectors, driven by significant economic reforms, infrastructure development, and a surge in e-commerce activities.
Gulf Supply Chain investigates how SSI Schaefer is at the threshold of this development.
Developing markets in the Middle East, such as Saudi Arabia and the United Arab Emirates, have made significant strides in transforming their logistics sector, driven by the Saudi Vision 2030 initiative. Investments exceeding USD 106.6 billion have also bolstered logistics infrastructure, making the Kingdom a pivotal logistics hub in the region according to Aawsat. United Arab Emirates, the UAE continues to innovate in logistics, with major projects like the Al Mafraq-Al Ghuwaifat road upgrade and Dubai South development.
“Driven by the Saudi Vision 2030 initiative, Investments exceeding USD 106.6 billion have bolstered logistics infrastructure, making the Kingdom a pivotal logistics hub in the region.”
At the heart of this revolution is SSI Schaefer, a global leader in providing cutting-edge intralogistics automation solutions. The company’s commitment and expertise are evident in its steps to support the region with the integration of advanced technologies and strategic infrastructure, instilling confidence in the region’s logistics prowess.
In this article, we draw the limelight to three explosive industries: e-commerce, pharmaceutical, and food & beverage warehousing logistics. These industries
face similar hurdles, and it’s crucial that we find collective solutions to intensify business operations during peak seasons. How should organizations tame this monstrous period while managing customers’ expectations and the expense of employees’ health and costs?
“Surge and more surges”— as the time of the year approaches the last quarter of 2024, this season marks the seasonal and festive season globally, where all retailers and their employees, regardless of industries, prepare to attempt to tame the monstrous season. With a higher volume of orders, diverse SKU varieties, and increasing consumer expectations for fast and reliable
deliveries, employees are stretching their late nights and energy to focus on picking the accurate orders that are viable and to meet their industries’ regulatory standards.
Warehouses need to handle a vast array of SKUs efficiently, and automation systems such as high-bay warehouses and shuttle solution systems might excel in managing these complexities by providing quick and accurate storage and retrieval of items. Since these systems, in combination with manual or automatic picking technologies, can significantly reduce errors, increase operational efficiency, and improve order fulfillment times, which are crucial for maintaining customer satisfaction in a
competitive market, why are companies not rushing to automate?
Initial Costs and the Uncertainty of Returns of Investment:
The upfront costs of realizing automation can be significant and it might pose a significant barrier for many businesses. However, viewing it as a strategic investment with substantial long-term benefits can make a difference. How the potential return on investment (ROI) and the steps to make informed decisions must begin by conducting a thorough cost-benefit analysis, considering factors such as labour concerns and savings,
error reduction, and increased operational efficiency and speed.
SSI Schaefer provides a thorough costbenefit analysis for clients. By evaluating the specific needs and current operational challenges of a business, SSI Schaefer can assist in identifying how automation solutions can bring substantial savings in labor costs, reduce errors in picking and handling operations, and thereby increase overall warehouse operation efficiency. Such analysis typically includes:
- Labor Savings: An appropriate level of automation can significantly reduce the need for manual labour, leading to longterm savings on wages, reduce reliance on a limited labour pool, and provide other employee benefits. Identifying the most labor-intensive part of the material flow process to start with is essential.
- Error Reduction: Automating processes enables continuous operations, crucial for meeting high consumer demand and ensuring timely deliveries. These systems enhance order processing accuracy and reduce errors. Integrating with a warehouse management system (WMS) such as SSI Schaefer’s proprietary software WAMAS optimizes resource allocation and overall efficiency. Such assessment is more than just automating tasks; identifying problematic bottlenecks and legacy systems constraints would keep the investment realistic and prevent the need to ‘upgrade’ for the sake of technology novelty.
- Integration with Existing Systems: Many warehouses operate with existing systems and technologies that have been in place for years. Integrating new automation hardware and software with existing systems might pose a significant challenge and concern to employees working with legacy systems. Overcoming this hurdle is crucial for the success of seamless integration with current systems and operational infrastructure. The human aspect of the issue cannot be ignored.
Businesses should prioritize compatibility and invest in flexible automation solutions that seamlessly integrate with their current infrastructure. SSI Schaefer excels in integrating new automation systems with existing warehouse operations. The thorough assessments conducted by the team ensure a smooth transition and the planning implementations that align with current processes.
Customized automation solutions tailored to each business’s unique requirements aren’t just about understanding specific pain points and operational goals. A bespoke approach ensures that every dollar invested brings measurable improvements in productivity and efficiency. Since every business has its unique needs, the approach to customizing solutions to fit seamlessly within the existing infrastructure works best for businesses who prepare well in advance such as conducting data mining and research into historical and fulfillment inventory patterns.
One of the strengths of “innovative solutioning” is the ability to scale the warehouse space whenever and wherever needed. Businesses can start with a smaller, more affordable system and expand it as needed. This approach allows businesses to manage initial costs more effectively while still benefiting from automation. SSI Schaefer’s broad range of flexible solutions grows with the business, ensuring that the investment continues to provide value as the company expands.
SSI Schaefer leverages cutting-edge technology to deliver superior performance; the wide range of solutions driven by AI, robotics, and IoT can certainly ensure that automation systems are not only efficient but also future proof. The latest SSI Piece Picking is an example of the nextgeneration Picking Robots launched by SSI Schaefer this fall. Taking piece picking to the next level, the solution won first place in the 2024 IFOY (International Intralogistics and Forklift Truck of the Year Award) Award –‘Stationary Robots’ Category.
The award-winning SSI Piece Picking features AI-based object recognition and innovative gripper technology. The use of compact suction cups instead of fingershaped grippers allows for fast and gentle handling of small parts. With the help of machine learning, the system continuously improves and builds a comprehensive knowledge database. The pick-and-place method ensures particularly gentle handling, achieving optimal utilization of storage space. The compact design of the cell allows for easy transport in a shipping container. WAMAS Piece Picking, as part of the WAMAS portfolio, provides efficient material flow control and seamless integration into existing WMS systems without extensive TeachIn processes.
- Robot’s control scanning manages to read more than 99% of the products on the first try. The patent-pending picking point optimization automatically shifts the gripping point, ensuring barcodes are unobscured so they can be scanned immediately.
High Performance:
- The portal robot uses compact suction knobs instead of finger-shaped grippers. That allows it to reach every corner of a container and grip even the smallest part. The speed adjusts individually to the specific product to save valuable time. With SSI Piece Picking, you can pick up to 1,200 small parts per hour.
Pick and Place
- Delicate pharmaceutical products or expensive luxury cosmetics dream solution. With a pick-and-place approach, the picking robot places each item as close as possible to the bottom of the container or the storage location above the items already in the container. This not only guarantees especially gentle product handling, but also ensures precise placement to optimize the filling level.
Smart Technology
- AI-based object recognition with integrated scanning and weighing function guarantees error-free product verification. If something unexpected happens, the
smart solution knows exactly what to do: Automatic error correction solves problems like unreadable barcodes right in the robot cell, reducing the need for manual interventions to the absolute minimum.
- Whether the packaging is cubical, cylindrical, tube-shaped, or blister packs –the application is effective in a wide range of product assortments across different industries. Furthermore, it improves with every pick: Machine learning allows SSI Piece Picking to accumulate and process experiences.
As the MEA continues to push the boundaries of logistics innovation and infrastructure development, automation is poised to play an important role in transformation. These are some trends that are expected to shape the future of warehouse logistics:
- Advanced Robotics and AI: The synergy between robotics and artificial intelligence (AI) is set to augment the capabilities of automated systems. Such integration will allow the logistics operation to handle complex tasks with greater efficiency and boost overall productivity.
- IoT Integration: The Internet of Things (IoT) will possibly be the key to connecting various components of the supply chain. By providing real-time data and insights, IoT hat will help improve the decision-making process.
- Sustainability: With a growing focus on sustainable practices, automating the warehouse systems will contribute by monitoring and enhancing energy usage and reducing waste. Regardless of the size of the business footprint, every organization holds the key to aligning itself with global sustainability goals.
- Cybersecurity: As warehouses become more automated and interconnected, robust cybersecurity measures will be essential to protect against cyber threats and maintain the integrity of operations and data.
“Any
- Whether the packaging is cubical, cylindrical, tube-shaped, or blister packs – the application is effective in a wide range of product assortments across different industries.”
SSI Schaefer offers a wide range of maintenance and customer service support and training, easing the transition for employees and minimizing the learning curves. To supplement businesses in leveraging the full potential of adopting technology, SSI Schaefer emphasizes the importance of robust cybersecurity measures, these include secure communication channels, regular software updates, and employee training on best practices to mitigate cyber risks. With a solid proven track record backed by numerous case studies and client testimonials, SSI Schaefer is the partner of choice in the automation journey for many businesses. For more information, contact SSI Schaefer: www.ssi-schaefer.com
While Excel can often be a reliable tool to manage data, we analyse why it may be often times become redundant. Data overload, lack of scalability and sometimes the need for manual updates can slow things down. Global Supply Chain investigates this through the expertise of Slimstock.
For decades, Excel has been the backbone of supply chain management, relied upon by countless businesses for its simplicity and versatility. However, as supply chains become more complex and demand greater precision, the limitations of Excel are becoming harder to ignore. In a world where agility and accuracy are critical, relying on Excel for supply chain planning can put your business at a significant disadvantage.
In this article, we will explore the key challenges that arise when using Excel for supply chain planning. We’ll deep dive into issues such as data overload, the risk of errors, and the difficulties in achieving real-time collaboration. We will also discuss how the lack of integration and automation in Excel can lead to inefficiencies that ultimately hold your supply chain back. By understanding these limitations, you’ll see why transitioning to more advanced, specialized tools is not just beneficial—it’s
essential for staying competitive in today’s fast-paced market.
As your business grows, so does the complexity of your supply chain. Managing multiple SKUs, tracking inventory across various locations, and coordinating with
numerous suppliers requires a tool that can handle vast amounts of data efficiently. Excel, while capable in small-scale scenarios, quickly becomes overwhelmed when faced with the demands of a modern supply chain. The manual processes inherent in Excel make it difficult to scale operations, leading to bottlenecks and inefficiencies.
One of the most significant drawbacks of using Excel for supply chain planning is the high risk of errors. Studies have shown that nearly 90% of spreadsheets contain mistakes. In the context of supply chain management, even a small error can have far-reaching consequences—resulting in stockouts, overstock situations, or misinformed strategic decisions. The manual data entry and complex formulas often used in Excel increase the likelihood of these errors, making it a risky choice for critical supply chain operations.
In today’s interconnected world, supply chain management often involves multiple stakeholders spread across different locations. Effective collaboration is crucial, but Excel’s limitations in real-time data sharing can create significant barriers. Without real-time updates, teams are forced to work with outdated information, leading to miscommunication and delays in decision-making. This lag can be detrimental in situations where quick responses are essential to maintaining the flow of goods and meeting customer demands.
Supply chains today rely on a complex ecosystem of tools and technologies. From ERP systems to demand planning software, the ability to integrate data from multiple sources is vital for accurate planning and execution. Excel, however, struggles with integration, often requiring time-consuming manual data transfers that can introduce
errors and delay critical processes. In contrast, specialized supply chain planning software is designed to seamlessly integrate with other systems, providing a holistic view of your operations and enabling more informed decision-making.
Automation is transforming supply chain management, enabling businesses to streamline operations, reduce manual workloads, and improve accuracy. However, Excel’s limited automation capabilities mean that many tasks still require manual input, which is both time-consuming and prone to error. This lack of automation not only hampers efficiency but also prevents businesses from fully leveraging the benefits
of modern supply chain technologies, such as predictive analytics and AI-driven decision support.
Supply chain planning involves more than just tracking inventory levels; it requires the ability to forecast demand, optimize production schedules, and manage supplier relationships. Excel’s basic functions can’t handle the complexities of these tasks, particularly as your business grows. Specialized supply chain planning tools, on the other hand, are equipped with advanced algorithms and analytics that can model complex scenarios, identify potential risks, and suggest optimal strategies for mitigating them.
Specialized supply chain planning software offers a level of visibility and control that Excel simply cannot match. These tools provide real-time insights into inventory levels, demand trends, and supplier performance, enabling businesses to make more informed decisions. With features like dynamic dashboards and customizable reports, supply chain managers can monitor key metrics and respond to changes swiftly, ensuring that the supply chain remains agile and responsive to market demands.
By automating data collection and analysis, supply chain planning software significantly reduces the risk of errors that are common
in Excel. These tools are designed to handle large datasets and complex calculations with precision, ensuring that the information you rely on is accurate and up-to-date. This improved accuracy not only enhances day-to-day operations but also reduces the risk of costly mistakes that can disrupt the supply chain.
Collaboration is at the heart of effective supply chain management. Specialized planning tools facilitate real-time collaboration among teams, regardless of location. By providing a single source of truth, these platforms ensure that all stakeholders have access to the same information, reducing the risk of miscommunication and enabling faster, more coordinated decision-making. This streamlined communication is essential for maintaining the efficiency and resilience of the supply chain.
Excel has long been a trusted tool for supply chain planning, but its limitations are becoming more apparent in today’s complex and fast-paced business environment. From data overload and error-prone processes to challenges in collaboration and integration, the drawbacks of Excel can no longer be ignored.
Transitioning to specialized supply chain planning software is not just a step towards improved efficiency—it’s a critical move for businesses aiming to stay competitive. By embracing advanced tools that offer better visibility, accuracy, and collaboration, companies can optimize their supply chains, reduce risks, and drive growth in an increasingly competitive market.
Slimstock’s supply chain management software provides the advanced capabilities needed to meet these challenges head-on. With real-time data insights, robust analytics, and seamless integration with existing systems, Slimstock empowers businesses to make informed decisions and maintain a competitive edge.
For those serious about optimizing their supply chain, the time to move beyond Excel is now. Learn more about us on www.slimstock.com
Exclusive interview with Shubhendu Das, Managing Director of Hellmann Worldwide Logistics, India
GSC: How do you feel about being recognised as a Great Place to Work (GPTW) in the mid-size category?
We are participating for the first time for this prestigious certification, and I am pleased that we have been recognised as the ‘Best Workplace in the Industry (Transportation & Logistics)’ in India. This is a proud moment for all of us. I always believed in a “People First approach”. If we take care of our team, they will take care of the organisation’s sustainable growth professionally. This accomplishment is a clear reflection of our team’s collective efforts and I feel proud of Team India.
GSC: How does the company support employee growth and development?
Our working eco system revolves on two main pillars - purpose and pride. The pillars are governed by our strong four Organizational Values- Caring, Reliable, Entrepreneurship and Forward thinking. Every employee believes in our core values, and they make this a part of the DNA.
We ensure that our employees are aware of how important their contribution is in our organisation and therefore encourage them to excel in their respective domain. We support them with structured training and mentoring. We introduce various platforms for constructive feedback, innovation and exchange of good ideas to make things better. Recognition and fairness play an important part for every employee’s growth and development.
GSC: What does work-life balance look like here?
At Hellmann India, we firmly believe that work-life balance is not just an option, but a necessity for our employees to
perform at their best. We strive to create an environment where our team can excel both professionally and personally with enthusiasm.
Our Human Resource (HR) best practices are designed with a strong emphasis on employee well-being.
“Kid’s day out, “is held in office and is a great initiative. It is a day where the children of our staff understand what their mother and father do in office. We also have dedicated health camps, sports and active participation on Corporate Social Responsibility (CSR) activities. These initiatives are part of our commitment, fostering a balanced life resulting in a positive environment in our workplace.
GSC: How does the organisation promote diversity and inclusion?
We have a strong belief in diversity and inclusion. Our focus on ‘Woman Power’ and inclusion of all among different parts of society. We create an environment of “equals.” In fact our HR policies focuses on open communication and fairness. We foster a more inclusive and empathetic workplace culture and this starts from our hiring process, internal mentoring, group collaboration and many other initiatives which lead to a sense of overall belonging.
“I always believed in a “People First approach”. If we take care of our team, they will take care of the organisation’s sustainable growth professionally.”
GSC: What kind of recognition programs are in place for employees?
We believe in putting “People first, “which means that employees feel valued for their good contribution for the success of the organisation. Such an environment cannot be created artificially and needs a genuine approach both from head and heart. We drive a high-performance culture and a competitive eco system. This helps employees achieve exceptional performances resulting in their career development within India and in our global network.
We have many internal recognition programs but the one which we all look forward is the ‘Annual Award night.’ It is a gala event which is attended by our regional and global management teams, and we reward individuals and individual teams for their exceptional contribution. It is a must for all employees to shine on this night which is compared to the ‘Oscars’ ceremony.
GSC: How do you gather feedback from customers to improve products or services?
We keep it simple. Meeting customers “face to face” at all levels on a regular basis is more important to us. Personally, I meet most of our top customers and take their feedback. This helps the organisation to be more disciplined as my team knows that anything which is not up to the expectation of the customer, the escalation will directly come to me. VUCA (volatility, uncertainty, complexity, ambiguity) is the new normal. In such a situation to be closer to the customer, helps us make things better.
GSC: What processes are in place to ensure timely responses to customer inquiries?
We have a strong escalation matrix. At Hellmann we offer timely responses and quality communication -- it is a part of every employee’s job profile. If one misses for any reason, the customer has all the information to initiate escalation.
“We have the ambition to be in the top five in Indian market in next five years through organic and inorganic growth. The growth story will include sustainability, inclusivity, diversity and strong CSR activities to give back to society.”
GSC: How does the company prioritize customer needs in its decision-making?
We are a “customer centric” organisation. The customer’s needs are of high priority as this brings opportunities on the table to get a new customer or grow with the existing customer. The needs are well understood through data and collaboration resulting in designing an innovative solution.
GSC: What metrics do you use to measure customer satisfaction?
We have internal and external measurement tools to understand customer satisfaction. These tools are through survey both direct meeting/interview and through online questionnaires either done by our ‘project team’ or through external agencies. Some metrics such as CSAT & CES are used in our measurements as well.
GSC: Can you share a success story where your team went above and beyond for a customer?
We have had many such achievements, over the years, however, the one which always comes to mind was during COVID -19 where our team went all out risking their
lives to keep the operation continuity and support customers who were stranded as others failed.
GSC: What does Hellmann Worldwide plan to take its India operations a set further towards achieving sustainable development goals?
We have big plans in India. Today we are one of the youngest MNC logistics company in India but have the best results in the mid-size segment. We have the ambition to be in the top five in Indian market in next five years through organic and inorganic growth. The growth story will include sustainability, inclusivity, diversity and strong CSR activities to give back to society.
GSC: How do you embed the ‘Hellmann Promise’ into your employees’ work culture? What does the Hellmann Promise mean to you personally?
In India, the Hellmann Promise is an integral part of our work culture. It serves as the foundation of our daily tasks and communications, inspiring our workforce to manifest principles in their professional
conduct. This cultural adherence aids our employees in personifying the Hellmann Promise’s values in their day-to-day duties, promoting dedication, honesty, and superior performance. Regular training programs, workshops, and team bonding exercises, strengthen these values and make them an integral part of our work philosophy. Employees are motivated to recount instances where they have demonstrated these values in their professional life.
Personally, the Hellmann Promise means everything to me. My leadership style revolves around the four values (mentioned earlier) and the leadership principle. When it is part of my DNA, decision making is professional, easier and fair.
GSC: What is the legacy you want to leave behind as Managing Director of Hellmann Worldwide.
To make Hellmann India as a most successful and admired company in the Indian market and in Hellmann Worldwide through good governance and fairness. Leaders need to be tough but should also be good human beings. I hope to always, ‘lead by example.’
What is data-driven logistics and how does it stabilize the warehouse automation operation for you?
With the WAMAS Control Center, this isn’t just a hypothetical scenario— it’s a real possibility. Data-driven logistics involves using data and analytics to optimize various aspects of the supply chain, including inventory management, transportation, and warehouse operations.
Tailored to meet the specific demands of industries from fashion to pharmaceuticals, WAMAS provides warehouses with actionable insights that enable you to optimize operations, improve efficiency, and adapt to changing market conditions, thereby stabilizing warehouse automation operations.
Discover how WAMAS can transform your warehouse into a model of efficiency and
Receive proactive notifications for faults and maintenance, boosting operational efficiency. Customize dashboards to turn complex data into clear, actionable insights. Drive maximum efficiency and cost savings, leading to unmatched customer satisfaction.
Our magazine brings you an engaging dialogue between Dr. Bachir Sentissi, Executive Director at Atracio Solutions Middle East and Jason Verhoven, Publisher, Global Supply Chain.
The future of supply chain management is set to be shaped by several key trends and innovations. For instance, Environmental, Social, and Governance (ESG) factors are becoming crucial. The use of robots and automation is also increasing. Recent global events have highlighted the need for supply chains to be resilient and agile. Companies are investing in technologies and strategies that allow them to quickly adapt to disruptions and changing market demands. Global Supply Chain brings you an engaging dialogue between Dr. Bachir Sentissi (BS), Co-Founder of Atracio Solutions Middle East and Jason Verhoven (JV) of Global Supply Chain.
JV – Atracio recently opened its Business Unit in UAE, what drives this decision to focus on wider Middle East region? BS – Many Middle Eastern countries are diversifying their economies away from oil dependence. Initiatives like Saudi Arabia’s Vision 2030 and the UAE’s diversification strategies are driving investments in infrastructure, technology, and logistics, enhancing supply chain resilience.
The region is investing heavily in infrastructure to position itself as a global logistics hub. Major projects include new ports, railways, and airports, which are set to improve connectivity and efficiency. Investments in smart city projects are also contributing to better supply chain management by integrating technology into urban planning and logistics.
The MEA region is specifically going through huge changes at different levels, and we saw this as a catalyst to expand and support the Digital Transformation agendas of Businesses in the region. There is a growing focus on building more
resilient supply chains to handle disruptions, such as those experienced during the COVID-19 pandemic. Adoption of advanced technologies like artificial intelligence, BI and Internet of Things -RFID in particularis increasing. These technologies are enhancing supply chain visibility, efficiency, and security.
There is an increasing emphasis on sustainability and environmental responsibility within supply chains. Companies are focusing on reducing their carbon footprint and adhering to global sustainability standards.
The rise of e-commerce is accelerating demand for more sophisticated supply
chain solutions, including faster delivery systems and better inventory management.
So, if we look at it holistically, there are lot of positive factors supporting our ambition to add value to regional businesses –Investment in Technology to enhance Supply Chain resilience, Diversification of regional economies, E-commerce growth, Development of Logistics Hubs and Smart Cities, Drive to focus on Sustainability and reduce waste
JV – Tell us a little bit more about the capabilities and functionalities of Atracio platform?
BS – Atracio is a Cloud-based, integrated
platform for warehouse, fleet, and asset management. Thanks to its native IoT and AI capabilities, Atracio is helping companies from a variety of sectors and regions to catalyze their digitalisation initiatives.
Atracio consolidates the collection and processing of all goods’ and information flows within organizations, meeting their specific business needs and ensuring consideration for future developments. Atracio features native identification by RAIN RFID technology, allowing its users to immediately benefit from the unique business advantages of this technology to automate tracking, identification, and inventory management of your assets, goods, equipment, and spare parts.
Atracio’s connected mobile application, which can be used on dedicated mobile devices or on regular smartphones, allows its users handle their business processes on-the-go and boost the performance and productivity of their field teams.
With Atracio, we can enhance the quality and speed of our customers decision-making through increased visibility of all their key performance indicators. Atracio’s Analytix module allows in-depth data analysis, identifying trends and opportunities, and making informed decisions to promote business growth and profitability.
JV – You mentioned “adding value to regional businesses” – how would you define that?
BS – Atracio supports E2E Supply Chain Scope but I would highlight two very concrete examples of Return on Investment in RFID and Fleet Management, where we assume we can make a big difference in MEA region specifically
The return on investment (ROI) for Radio Frequency Identification (RFID) technology can vary widely depending on the industry, application, and specific implementation. However, RFID generally offers several key benefits that contribute to its ROI:
1. Improved Inventory Accuracy: RFID can significantly reduce errors in inventory tracking, leading to better stock management and fewer stockouts or overstock situations. This often translates to increased sales and reduced holding costs.
2. Increased Efficiency: Automated data collection with RFID speeds up processes such as check-in/check-out, sorting, and shipping. This can lead to labor cost savings and faster turnaround times.
3. Enhanced Visibility and Tracking: RFID provides real-time visibility into the location and movement of goods. This can improve supply chain management and reduce losses due to theft or misplacement.
4. Better Data Quality: RFID reduces manual data entry errors and improves the accuracy of information, which can enhance decision-making and operational planning.
5. Improved Customer Service: With better inventory management and tracking, businesses can provide more reliable
service to customers, potentially leading to increased customer satisfaction and loyalty.
6. Reduced Shrinkage: In retail environments, RFID can help reduce theft and loss by enabling more accurate tracking and real-time alerts.
The functional benefits above generally translate into significant gains that contribute directly to financial performance. For example:
1. RFID can reduce inventory management costs by 20-30%.
2. Improved inventory accuracy can lead to a sales increase of 1-5%.
3. Retailers often see an ROI of 3-5 times their initial investment within the first year.
4. Improved efficiency and reduced cycle times can lead to a 10-15% increase in production throughput.
We have the required expertise of successfully delivering RFID implementations in sectors like Fashion, Retail, F&B, Telecommunications, Xperience Management etc.
Regarding Fleet Management, the ROI is even quicker as implementation time is relatively faster and we can deliver these kinds of implementations very quickly. For ex: if a business has a fleet of 300 vehicles, we are talking about weeks and not months. When it comes to value-add, these are some of the benefits I can easily highlight from our experience and benchmarks
• Benefit: Fleet management systems can optimize routes, reduce idling, and monitor fuel consumption.
• Quantified ROI: Companies often see fuel savings of 10-15%. For example, if a fleet spends $500,000 annually on fuel, a 10% savings translates to $50,000 in reduced fuel costs.
• Benefit: Preventive maintenance alerts help avoid costly breakdowns and extend vehicle life.
• Quantified ROI: Maintenance costs can be reduced by 10-20%. If annual maintenance costs are $200,000, a 15% reduction saves $30,000.
• Benefit: Enhanced route planning and real-time tracking reduce downtime and improve efficiency.
• Quantified ROI: Productivity improvements can lead to a 5-10% increase in deliveries or services. If a company handles 1,000 deliveries per month, a 7% increase translates to 70 additional deliveries.
JV – According to you, what are the key challenges that Supply Chains are facing today?
BS – In my humble opinion, it depends a lot on which part of the world we are talking about and also if you are an export dependent country with strong manufacturing component or import focused consumption-based economy. But in the end, the interconnectedness of the supply chains today means when China catches the cold, the entire world sneezes.
To answer your question, I would say Ambiguity due to Lack of Visibility for quick and efficient decision making, Uncertainty due changing Geo-Political equations, Volatility due to Environmental imbalance, Complexity due to change in customer expectations, technological disruptions and evolving regulations.
JV – And how can we address these challenges?
BS – Businesses will need to have a holistic
approach to their Transformation agendas if they need to mitigate the risks that these challenges engender. Throwing dollars on Technology will not bring the expected results if we fail to address the Governance, Talent, Process part of the Organisation.
JV – Can you elaborate more on the “holistic approach” you mentioned?
BS – For example – let’s say a Business is investing in technologies such as IoT sensors, GPS tracking, and RFID to gain real-time visibility into it’s supply chain and implement integrated systems that provide end-to-end tracking and data sharing. In this case, they would also need to focus on:
1. Training and Change Management: Ensure that your workforce is trained to use new technologies effectively and implement change management strategies to facilitate smooth transitions and adoption.
2. Incremental Adoption: Implement new technologies in phases to manage costs and minimize disruption. One approach can be to start with pilot projects to test and refine technology before full-scale deployment.
3. Cybersecurity Measures: Invest in robust cybersecurity measures to protect your supply chain data. These can be through
regularly updating security protocols and conduct vulnerability assessments.
4. Strategic Partnerships: Build strong relationships with key partners and stakeholders to enhance collaboration and coordination across the supply chain.
JV – I saved the best question for the last – tell us a little about yourself, what makes you wake up with excitement every morning and what keeps you awake at night?
BS – I know the logistics and transportation sectors very well thanks to my 25 years of involvement on both sides of the Atlantic. I have always been excited and intrigued by the potential benefits that the information and telecommunication new technologies can bring to these sectors. It is not a surprise therefore that my Doctorate thesis was on the prerequisites of successful adoption of IoT in the supply chain sector.
We are currently witnessing the dawn of new era where AI, connected devices and Cloud computing are revolutionising how the supply chain industry is run. This will allow everyone to digitally track, manage and optimize their supply chain, so that they can enjoy a good night sleep -- me included. www.atracio.com
Falcon Autotech is a global intralogistics automation solutions company. With over 10 years of experience, Falcon has worked with some of the most innovative brands in E-Commerce, CEP, Fashion, Food/FMCG, Auto and Pharmaceutical Industries.
CONTACT US:
Email: salesenquiry@falconautoonline.com
Website: www.falconautotech.com
Addverb’s comprehensive suite of automation technologies spans a wide array of applications crucial for modern supply chain management. Together with Landmark’s expertise, this strategic alliance is poised to shape the future of retail logistics with ingenuity and precision.
Blending advanced robotics and industry expertise, Addverb and Landmark Group elevate retail operations and customer satisfaction across the Gulf Cooperation Council. They stand at the forefront, leading the charge with advanced robotics and deep industry expertise, redefining the very essence of customer satisfaction. Through seamless integration and visionary leadership, this partnership has set a new benchmark in operational efficiency, promising a future where every retail experience is elevated and every order fulfilled with precision and speed.
In today’s dynamic retail and e-commerce arena, automation has transcended from being a mere convenience to becoming an indispensable necessity. At the forefront of this technological revolution stands Addverb, a global leader renowned for its pioneering advancements in robotics and automation solutions. Addverb’s mission is clear: to empower businesses with state-of-the-art systems that not only streamline intralogistics operations but also positions them for sustained success in an increasingly competitive market landscape. Addverb’s comprehensive suite of
automation technologies spans a wide array of applications crucial for modern supply chain management. From Automated Guided Vehicles (AGVs) and Autonomous Mobile Robots (AMRs) to Sorting Robots, our advanced automation systems cover a wide range of needs. Each designed to meet the diverse needs of businesses across various sectors. The core strength of Addverb lies in its relentless pursuit of innovation and commitment to excellence. By integrating cutting-edge technologies, Addverb enables companies to optimise their supply chain processes, reduce
operational costs, and improve overall productivity.
Nestled in the vibrant heart of Dubai, the Landmark Group stands as a beacon of innovation and excellence in the realm of retail and hospitality. Since its inception in 1973, this multinational conglomerate has flourished into a powerhouse, spanning across the Middle East, Africa, the Indian subcontinent, and Southeast
Asia. Renowned for its expansive portfolio, the Landmark Group proudly owns and operates a myriad of distinguished brands in fashion, footwear, home furnishings, electronics, and leisure. With a steadfast commitment to delivering quality, the group has garnered acclaim for its extensive retail footprint and unwavering dedication to consumer satisfaction. Embracing the future with foresight and as a part of their ongoing efforts to enhance customer satisfaction and operational efficiency, Landmark Group identified their fulfillment Centre in Kuwait as a pivotal site for transformation. The goal was clear, to weave advanced automation seamlessly into operations, enabling the handling of diverse products while elevating overall efficiency. Harnessing its advanced robotics and automation skills, Addverb was central to this development. Addverb brought to the table a transformative vision that, when combined with Landmark Group’s extensive
industry acumen and expansive operational capabilities, set the stage for a significant evolution. This collaboration stemmed from a unified vision to pioneer a future-ready fulfilment centre capable of effortlessly adapting to the ever-changing landscape of retail. Together, both the companies have embarked on a journey to transform standards in logistics, leveraging innovation to enhance efficiency and elevate the retail experience to new heights. This partnership represents not just a convergence of technologies, but a strategic alliance poised to shape the future of retail logistics with ingenuity and precision.
Underscoring the transformative impact of Addverb’s automation solutions on Landmark Group’s Pawan Kaura, Head of E-commerce Operations, Landmark Group said, “Creating an adaptive and agile supply chain is part of our supply chain vision. We are happy to collaborate with Addverb to elevate our Kuwait fulfilment centre operations. The
integration of warehouse automation not only enhances our operational efficiency but also ensures that our customers receive their orders accurately and promptly. This investment in automation aligns with our commitment to delivering unparalleled service and experiences.”
Pieter Feenstra, CEO of Addverb EMEA, also reflects on this strategic partnership with Landmark Group, stating, “Partnering with the Landmark Group, a distinguished and influential player in the field, fills us with immense pride. This synergy not only reinforces our commitment to delivering state-of-the-art automation solutions but also amplifies our dedication to efficiency, reliability, and accuracy. Landmark Group, a key player with an illustrious track record, brings a wealth of expertise and a legacy of excellence to this strategic partnership. This collaboration is a testament to the trust and confidence that industry giants place in Addverb.”
“Creating an adaptive and agile supply chain is part of our supply chain vision. The integration of warehouse automation not only enhances our operational efficiency but also ensures that our customers receive their orders accurately and promptly.”
Addverb’s innovative automation solution for Landmark Group’s Kuwait Fulfilment Centre represents a paradigm shift in logistics, where precision and efficiency converge to redefine industry benchmarks. At its core are two advanced technologies: Zippy and Quadron, seamlessly integrated through Addverb’s Warehouse Execution System (WES) to orchestrate logistical operations—from the moment an order is placed to its swift dispatch.
Zippy, the high-speed robotic sorter capable of processing an impressive 1,000 sorts per hour, exemplifies efficiency and accuracy in the sorting process. As products glide seamlessly into the system via automated conveyors, Zippy springs into action with rapid scans and precise categorizations. This ensures that non-bulky items are swiftly directed into designated order totes, minimizing errors and maximizing throughput. The meticulous functioning of Zippy guarantees that each order progresses seamlessly through the fulfilment process without delay. Complementing Zippy’s finesse is Quadron, the agile carton shuttle system, which swiftly ferries sorted totes to the outbound
“Operating at a rate of up to 100 crates per hour, Quadron optimises the flow of goods, effectively eliminating bottlenecks and enhancing overall operational fluidity within the warehouse.”
conveyor system. Operating at a rate of up to 100 crates per hour, Quadron optimises the flow of goods, effectively eliminating bottlenecks and enhancing overall operational fluidity within the warehouse.
However, the true innovation lies in the synchronized actions managed by Addverb’s Warehouse Execution System— Concinity. This software platform focuses on real-time execution and control of warehouse operations, facilitating seamless communication and coordination between Zippy, Quadron, and various subsystems within the warehouse.
Additionally, by harnessing the transformative potential of robotics and AI-driven automation, Addverb equips Landmark Group to navigate the complexities of global commerce with
agility and confidence, setting a new standard for operational excellence and customer-centricity.
As technology and tradition converge, this collaboration charts a path towards a future where operational efficiency is not just a goal but a strategic imperative. This partnership paves the way towards a future where operational efficiency becomes more than just a target—it becomes a critical necessity. With each precisely sorted tote and flawlessly executed logistical procedure, Addverb and Landmark Group redefine industry benchmarks, ensuring that every order fulfilled is synonymous with excellence. This collaboration aims not only to streamline operations but also to set a new standard for precision and reliability in retail logistics.
Empowering Your Chemical Supply Chain Beyond Boundaries...
The primary aim of humanitarian logistics is to support relief efforts by alleviating suffering and maintaining human dignity during a crisis.
Fatima Ait Bendawad, DHL Global Humanitarian Logistics Competence Centre Head, DHL Humanitarian Logistics unravels to Global Supply Chain, how it boosts efficiency.
GSC: How is Humanitarian Logistics similar and different from other more conventional Logistics?
While grounded in the same principles of managing the flow of goods and information, humanitarian logistics and conventional logistics are distinct in their objectives, operational environments, and challenges. Both fields prioritize efficiency and employ advanced technologies for transport and inventory management, aiming to ensure timely and accurate delivery.
However, the primary aim of humanitarian logistics is to support relief efforts by alleviating suffering and maintaining human dignity during crises. When natural disasters like earthquakes or floods occur, it becomes clear that transport logistics can achieve so much more than just supplying people with essential goods—humanitarian logistics can save lives in an emergency.
Operations often unfold in challenging conditions with compromised infrastructure and volatile environments characterized by natural disasters, conflicts, and other humanitarian emergencies necessitating rapid, flexible responses and the ability to operate under resource constraints.
Moreover, the stakeholder environment in humanitarian logistics is notably complex, involving coordination among international agencies, NGOs, and local governments, which contrasts with the more straightforward supplier-customer dynamics in conventional business logistics.
This complexity necessitates a unique set of strategies to manage resources and deliver aid effectively under pressing circumstances and innovative solutions and adaptive strategies to overcome challenges. Humanitarian logistics often faces funding constraints, resource shortages, and unpredictable demand patterns, emphasizing the importance of adaptability, resilience, and a strong humanitarian mandate
GSC: What are the challenges you face in humanitarian logistics, and how does DHL Global Forwarding address them? In 2024, the demand for humanitarian assistance is substantial, with nearly 300
million people globally in need, according to the United Nations Office for the Coordination of Humanitarian Affairs (OCHA).
The delivery of aid in such scenarios is fraught with challenges, from damaged or inadequate infrastructure and complex supply chains to regulatory hurdles. Essential transport routes are often compromised in crisis zones, where roads may be destroyed or obstructed, requiring logistics providers to devise alternative delivery methods, including airdrops when necessary. Furthermore, ensuring that the right supplies reach the right people at the right time is a critical yet challenging task due to the dynamic nature of crises, which can alter needs and logistical requirements rapidly.
DHL Global Humanitarian Logistics Competence Center overcomes these challenges by leveraging its global network and expertise in last-mile delivery to reach even the most remote and inaccessible areas. In DHL Global Humanitarian Logistics Competence Center we implement robust security protocols, conduct thorough risk assessments, and coordinate closely with local authorities and security experts to help mitigate security risks. Additionally, DHL integrates advanced technologies for sophisticated tracking and routing, enhancing the efficiency and adaptability of supply chain management. This ensures that aid reaches the right places at the right times, even as situations on the ground rapidly change.
Furthermore, DHL’s deep understanding of international and local regulatory environments enables them to handle sensitive items like medicines and chemicals efficiently. Our expertise ensures compliance with regulations, avoiding delays and facilitating the smooth delivery of urgently needed aid. These strategies collectively streamline the process, ensuring that humanitarian aid is both timely and effective.
GSC: What are your strengths and capabilities that make DHL unique in this sector?
At DHL, our strategic capabilities in humanitarian logistics are exemplified by our Global Competence Center for
Humanitarian Logistics based in Dubai’s Humanitarian, the largest humanitarian hub worldwide. Drawing from decades of experience in humanitarian logistics and a passionate humanitarian team we have honed our expertise to ensure the seamless transportation and delivery of essential relief goods, even in challenging environments. Our center serves as a pivotal hub for coordinating operations across all United Nations agencies, NGOs, Suppliers, donors, manufacturers, and governmental entities. We ensure that essential relief goods products are delivered seamlessly across global crisis zones.
Leveraging our extensive global footprint and specialized regional knowledge, we meticulously optimize delivery schedules and routes, crucial for timely and effective responses to humanitarian crises and development programs.
In this scenario, we excel in managing the intricate process of distributing medicines to address neglected tropical diseases across 120 diverse locations. We navigate the logistical challenges with precision and expertise. Our meticulous planning, coupled with our extensive experience in managing complex supply chains, ensures the timely and reliable delivery of life-saving medicines to communities in need, contributing to the eradication of neglected tropical diseases worldwide.
Our effectiveness in humanitarian efforts is also bolstered by our GoHelp program, which includes disaster preparedness
initiatives such as Get Airports Ready for Disaster (GARD) to ensure airports are equipped to handle crises. Additionally, our Disaster Response Teams (DRTs), which can be deployed within 72 hours, consist of 900+ trained volunteers ready to manage logistics operations at airports, facilitating the swift movement of aid and maintaining clear lines of communication with various organizations.
Moreover, in times of major disasters, our offices transform into bustling hubs of activity, capable of mobilizing up to 300 tonnes of aid in a single day. Our logistical capabilities extend to using ‘speedballs’—emergency supplies packed in polypropylene bags and delivered via helicopter airdrops to locations unreachable by road.
Our integrated approach to disaster management—spanning preparedness, response, and recovery—reflects a comprehensive strategy that utilizes our global presence and logistical expertise. This robust infrastructure and readiness to act enable us to make significant contributions to society and the environment, particularly in responding effectively and efficiently to global humanitarian crises.
GSC: Can you tell us about DHL’s humanitarian support programs?
DHL’s humanitarian support programs, particularly our GoHelp initiative, exemplify our commitment to leveraging logistics expertise in global relief efforts. Identifying a critical gap in humanitarian logistics, we
collaborated with UN agencies and NGOs to enhance disaster relief, especially at congested airports during natural disasters.
Since 2004, DHL has deployed logistics experts to disaster-stricken airports worldwide, utilizing our vast global network to ensure rapid, efficient aid delivery. Our presence in 220 countries, combined with the world’s largest transportation network, enables us to swiftly deliver medical supplies and essential aid.
In addition to GoHelp, our GoTeach program enhances our social impact by empowering young people, especially those from disadvantaged backgrounds, to improve their employment prospects. Through partnerships with organizations like SOS Children’s Villages and Teach For All, GoTeach connects our employees with youth worldwide, offering mentorship and insights into the working world.
Our approach to humanitarian support and youth empowerment emphasizes our commitment to community resilience and economic stability.
GSC: What are your activities in nonemergency situations?
DHL’s role in humanitarian logistics significantly contributes to the
development program of the humanitarian organizations for the achievement of Sustainable Development Goals -SDG 2023. DHL fosters partnerships with governments, non-profit organizations, international agencies, and other stakeholders to address humanitarian challenges collectively. Through collaborative efforts, we leverage our logistical capabilities to support development programs aimed at achieving SDG 2023 and other related goals. By facilitating coordination and cooperation among diverse stakeholders, we maximize the impact of humanitarian interventions and contribute to sustainable development.
As an example, DHL facilitates the transportation and distribution of medicines and equipment to underserved communities. By ensuring timely access to healthcare resources, we support efforts to improve health outcomes, combat NTD, Malaria, TB, and HIV, and promote well-being; along with public health, we transport water purification systems, sanitation supplies, and equipment to areas affected by waterborne diseases or lacking access to clean water. By ensuring the timely delivery of these essentials, we contribute to improving water quality, sanitation, and hygiene practices, thereby
enhancing public health and supporting the elimination of diseases.
Through our logistical expertise, DHL facilitates the distribution of agricultural inputs such as seeds, fertilizers, and equipment to farmers in rural areas. We also transport educational materials, school supplies, and equipment to communities in need, enabling access to quality education in underserved areas.
DHL plays a crucial role in the transportation and distribution of food aid, nutritional supplements, and emergency relief supplies to communities affected by food insecurity or humanitarian crises. By ensuring the efficient delivery of food assistance, we help alleviate hunger and address malnutrition.
In each of these areas, we leverage our global network, logistical capabilities, and partnerships to support development programs, humanitarian initiatives, and emergency response efforts worldwide. By facilitating the movement of essential resources and supplies, we contribute to building resilient communities, promoting sustainable development, and achieving the United Nations’ Sustainable Development Goals.
In non-emergency situations, DHL Group
actively engages in long-term community development initiatives alongside our daily operations. We extend our support beyond crisis response, focusing on sustainable development and building resilience within local communities.
In addition, DHL initiatives under the ‘GO’ family—such as GoTeach and GoTrade—exemplify this commitment. GoTeach addresses educational barriers and employment opportunities for youth, particularly those from disadvantaged backgrounds. GoTrade aims to facilitate international trade by improving logistics and market access for developing countries.
We strongly believe in the power of volunteerism and have made it a part of our corporate culture. By providing volunteer opportunities to our diverse workforce of around 600,000 people worldwide, we aim to utilize their unique skills and interests to make a positive impact on communities. This collaborative approach not only enhances our workplace environment but also fosters a shared sense of purpose and empathy.
Together, these efforts reflect our dedication to exceed our responsibility as a global leader in logistics. We aim to
unite our employees in a common cause, leveraging their varied talents to make a meaningful difference on a larger scale. Our commitment to connecting people and improving lives is unwavering.
GSC: How do you see the role of logistics evolving in the humanitarian sector, particularly with emerging challenges such as climate change and global health crises?
As we face the growing challenges of climate change and global health crises, the role of logistics in the humanitarian sector is becoming increasingly crucial. Rapid and severe weather events demand logistics operations that are not only swift but also predictive. By utilizing advanced analytics and forecasting tools, logistics can proactively position supplies near vulnerable areas, enhancing the speed and effectiveness of responses.
The complexities of delivering medical supplies during health crises have also grown. This demands robust logistics capable of handling sensitive products, such as vaccines, that require cold chain solutions. The integration of sustainable
practices is another evolution, with efforts to reduce carbon footprints, use renewable energy, and deploy eco-friendly materials, reflecting a commitment to both efficiency and environmental stewardship.
Strengthening local and regional logistics capacities is essential for quick, appropriate responses that also support local economies and resilience. Moreover, embracing technology—like drones for delivery and IoT for inventory management—enhances operational transparency and efficiency.
Collaborative efforts across sectors are vital, as partnerships can pool resources, share expertise, and drive innovative solutions tailored to specific challenges. The future of humanitarian logistics lies in its ability to adapt swiftly, embrace technology, and foster sustainable, community-centered solutions.
GSC: Final thoughts on enhancing the way supply chain operates?
At DHL, our purpose is clear: to connect people and improve lives. This guiding principle underscores our commitment to humanitarian logistics and sustainable development through programs GoHelp, GoTeach, Gotrade, and GoGreen Initiative. Recognizing the profound impact of our global network and logistical capabilities, we strive to make a positive difference in the world by leveraging our expertise to support communities in need and promote environmental stewardship.
In our dedication to humanitarian logistics, we recognize the vital role of efficient supply chains in delivering life-saving aid to those affected by disasters, conflicts, and other emergencies. Through strategic partnerships, innovative technologies, and agile response mechanisms, we ensure the timely and effective delivery of essential relief supplies, helping to alleviate suffering and rebuild communities in crisis.
In essence, our commitment to humanitarian logistics and sustainable development reflects our belief that business success should go hand in hand with social and environmental responsibility. Through our actions, we seek to create lasting positive impact, connecting people, improving lives, and building a more sustainable world for all.
QTerminals, a prominent port and terminal operator, has proudly announced a significant milestone in its operations at Hamad Port.
In August 2024, the company successfully surpassed the handling of 10 million Twenty-foot Equivalent Units (TEUs) since the port began operations in 2016. This achievement not only highlights Hamad Port’s vital role in the global maritime logistics sector but also underscores its rapid growth and ongoing success within the industry.
Hamad Port, since its inception, has quickly become a crucial hub for international shipping, serving the needs of major global shipping lines. The port’s advanced infrastructure and QTerminals’ commitment to providing top-tier services have positioned it as a trusted partner within the shipping community, a trust that has been instrumental in reaching this impressive milestone.
Reflecting on this achievement, Jesper Pedersen, Managing Director of Hamad
Port, expressed optimism about the future. “This milestone is a testament to our dedication and the growing trust our partners place in us. We believe this success will attract even more mainline and feeder services, solidifying Hamad Port’s status as a key player in global maritime logistics. Our heartfelt thanks go to the QTerminals team for their unwavering commitment and exceptional performance. We are eager to continue building on this success.”
In addition to surpassing the 10 million TEU mark, QTerminals has also recently set new records at Hamad Port, displaying its operational excellence. Last month, the port handled the vessel MSC ELISA XIII, setting a new berth productivity record of 234.26 Berth Moves Per Hour (BMPH), surpassing the previous record of 220.38 BMPH. This achievement was accompanied by the highest volume of cargo handled in a single month, further demonstrating the port’s growing capacity and efficiency.
QTerminals’ success at Hamad Port is a reflection of the company’s broader commitment to excellence in port management and operations. The company’s strategic investments in technology, infrastructure, and human capital have been key drivers of its growth. QTerminals continues to enhance its service offerings and expand its capabilities, not just at Hamad Port but across its global operations.
QTerminals is a joint venture between Mwani Qatar (51%) and Milaha (49%). The company is responsible for managing the operations at Hamad Port, which includes container, general cargo, RORO, livestock, and offshore supply services. QTerminals plays a vital role in facilitating Qatar’s imports and exports, and its operations are integral to the country’s trade and economic diversification efforts.
As QTerminals looks to the future, it remains focused on further enhancing its operational capabilities and expanding its global footprint. The company is committed to maintaining the highest standards of service, ensuring that Hamad Port continues to be a preferred destination for international shipping lines.
This milestone of handling over 10 million TEUs is not just a numerical achievement but a reflection of QTerminals’ strategic vision and the relentless efforts of its workforce. As Hamad Port continues to grow in stature and capability, it is poised to play an even more significant role in global maritime logistics, driving economic growth and connecting Qatar with markets around the world.
QTerminals’ success is a testament to the strength of its partnerships, the dedication of its team, and its unwavering commitment to excellence. As the company celebrates this remarkable achievement, it also looks forward to a future filled with even greater accomplishments in the global maritime industry.
Companies have jointly operated charter flights across East Africa and the Horn of Africa supporting humanitarian efforts in Sudan, Somalia, and Yemen.
As part of a major restructuring, Network Airline Services (NAS), the global GSA company of Network Aviation Group (NAG), has signed an agreement with Kenyan carrier Safe Air to provide cargo sales and marketing for the carrier in Oman and the UAE.
Safe Air operates regular cargo services between Nairobi and Juba in South Sudan, and Mogadishu in Somalia. Recently, it has also launched a weekly service to Port Sudan and Djibouti.
Established in 2007, the company offers both passenger and cargo flights across Africa and the Middle East from its base in Nairobi, Kenya. Network Aviation Group’s Sales Director, Andy King, was at the contract signing in Kenya, along with Safe Air representatives.
An official release by Network Aviation Group states, “The companies have jointly operated charter flights across East Africa and the Horn of Africa supporting humanitarian efforts in Sudan, Somalia, and Yemen. Network has offices in Dubai and Muscat, and will also support Safe globally from the companies’ offices in Europe and USA.”
This appointment marks Network’s first GSA representation of the K3 airline.
Saudia Cargo has unveiled its latest campaign, ‘Landing in China in 24’ designed to highlight the company’s swift and reliable shipping services to multiple destinations across China. This initiative underscores Saudia Cargo’s commitment to empowering Saudi exports and ensuring they gain a strong foothold in the competitive Chinese market, opening doors to substantial growth and expansion opportunities.
The new campaign is closely aligned with Saudi Arabia’s Vision 2030, which emphasizes the growth of non-oil exports and the diversification of the Kingdom’s revenue streams. Saudia Cargo is dedicated to offering advanced logistics solutions that not only bolster Saudi exports but also expand their reach in global markets. The ‘Landing in China in 24’ campaign highlights the company’s dedication to optimizing export operations, showcasing its superior logistical and technological capabilities in efficiently managing global shipping demands.
In 2023, the value of Saudi exports to China was 16.1 billion SAR, representing 17% of total exports.
Additionally, the campaign aims to deepen trade ties between Saudi Arabia and China by positioning Saudi products prominently in one of the world’s most vital markets, thereby driving economic growth. The ‘Landing in China in 24’ is in close collaboration with the ‘Made in Saudi’ initiative, championed by the Saudi Export Development Authority, which focuses on enhancing the global recognition and quality of Saudi products.
Marwan Niazi, Vice President of Commercial at Saudia Cargo, stated: “Through this campaign, we aim to enhance our shipping capabilities and broaden our export scope to the Chinese markets by optimizing export operations and providing advanced logistic services that align with the growing global market demands and commercial connections. We have focused on facilitating the access of Saudi products to the Chinese markets and showcasing our logistical capabilities and operational efficiency.”
“The campaign has generated substantial engagement across social media platforms from partners and related sectors, including the National Competitiveness Center, the National Livestock and Fisheries Development Program, the Saudi Export Development Authority, and the General Authority of Foreign Trade. This demonstrates the widespread interest and support for the campaign,” Niazi stated.
China is Saudi Arabia’s main merchandise trading partner. In 2023, the value of Saudi exports to China was 16.1 billion SAR, representing 17% of total exports. This highlights the continuous upwards trend supporting the opening of new commercial channels and destinations in China.
Saudi Cargo operates 18 weekly cargo flights to Hong Kong, Guangzhou, Shanghai & Shenzhen, Additionally, the company offers an extra ten weekly flights on Saudia Airlines passenger aircraft from Guangzhou and Beijing to further enhance cargo capacity.
Saudia Cargo stands as a leading national cargo carrier, headquartered in the Kingdom of Saudi Arabia. Leveraging the strategic advantage of the country’s location, it serves as a highly efficient aerial bridge connecting the East and the West, seamlessly bridging continents. Our extensive reach encompasses approximately 100 airport destinations and 250 customer destinations across four continents, establishing us as a pivotal player in the global air cargo industry. Spanning over seven decades and a commitment to a ‘humanfirst’ approach, Saudia Cargo has consistently upheld its esteemed reputation as one of the world’s most dynamic cargo carriers. This reputation is underpinned by a rich history of innovation and resilience.
Maritime Law in the United Arab Emirates has undergone significant reform with the enactment of Federal Decree-Law No. 43 of 2023, effective March 2024. This landmark legislation aims to modernize and streamline regulatory frameworks, addressing key aspects such as ship registration and ship arrest to bolster the UAE’s position as a maritime hub.
Key Amendments:
Ship Registration:
The new legislation introduces a centralized ship register under the Ministry of Energy and Infrastructure, marking a departure from the previous decentralized system overseen by the Maritime Inspection Department. This reform expands eligibility criteria for UAE flag registration, now accommodating chartered vessels and those under construction, thereby enhancing the registry’s inclusivity and operational efficiency. This centralization is expected to significantly reduce bureaucratic hurdles, making the process of ship registration more transparent and efficient. Furthermore, by expanding the eligibility for registration, the UAE aims to attract a broader array of maritime stakeholders, thereby boosting the nation’s maritime fleet and enhancing its global competitiveness.
Ship Arrest:
Federal Decree-Law No. 43 of 2023 enhances provisions for precautionary arrest in maritime disputes, broadening the scope of recoverable marine debts. Notable amendments include increased grounds for arrest related to damages, salvage operations, environmental liabilities, and contractual disputes. This expansion ensures that parties involved in maritime commerce can secure their interests more effectively. Furthermore, the legislation introduces stricter requirements for petitioners, mandating financial security for crew and vessel maintenance costs to prevent undue hardship during arrest proceedings. This measure is designed to balance the interests of creditors and those of the vessel’s crew and operators, ensuring that the maritime workforce is protected, and vessels remain operational during legal disputes.
The amendments underscore the UAE’s proactive approach to harmonizing maritime legislation with international standards, fostering a conducive environment for maritime commerce and legal certainty. By aligning with global best practices, the UAE aims to enhance its attractiveness as a maritime hub, offering a robust legal framework that supports the growth and sustainability of maritime businesses. This alignment with international standards is crucial as it provides foreign investors and maritime operators with the confidence that the UAE’s maritime regulations are on par with those in other leading maritime nations. Additionally, these reforms are expected to stimulate investment in the UAE’s maritime infrastructure, as the enhanced legal framework provides greater clarity and security for maritime operations. This could lead to increased activity in shipbuilding, repairs, and other maritime services, further cementing the UAE’s position as a key player in the global maritime industry.
Advocate Joy Thattil is the Managing Partner of Callidus Legal, renowned in the Legal and Consultancy sectors, having offices in Dubai, Singapore & India. Born and educated in Cochin, he graduated in Law from the Government Law College, Ernakulam, and joined the Bar Council of Kerala in 1996. Since 2007, he has served as a Notary Public appointed by the Government of India.
Adv. Thattil specialized in International Maritime Law at the University of Southampton, U.K., and has represented clients globally in complex maritime cases. He has presented papers on International Maritime Law in the USA, Canada, and the UK, and has been a Guest Faculty member at premier institutes in India and abroad. He is the Secretary General of the Dubai Shipping Agents Association (DSAA).
The amendments underscore the UAE’s proactive approach to harmonizing maritime legislation with international standards, fostering a conducive environment for maritime commerce and legal certainty. As stakeholders navigate these regulatory changes, ongoing implementation and stakeholder engagement will be crucial in realizing the full potential of the revised maritime law framework. Active participation from all relevant sectors, including legal professionals, shipowners, and maritime service providers, will be essential to ensure that the benefits of these reforms are fully realized. Continuous dialogue and feedback mechanisms will help identify and address any challenges that arise during the implementation phase, ensuring that the UAE’s maritime sector remains dynamic and resilient.
Gulf Warehousing Company Q.P.S.C (GWC) – one of the fastest-growing businesses in the MENA region, has announced its financial results for the first half (H1) of 2024 (sixmonth period ending on 30 June 2024), the company reported total revenues of QR748.3mn, and a net profit of QR100.4mn, while earnings per share stood at QR0.171 for the same period.
Shaikh Mohammed Bin Hamad Bin Jassim Bin Jaber Al Thani, GWC chairman, said: “The financial results for the first half of this year underscore the strength of GWC’s financial position and its ability to maximize profits. The company is actively implementing a strategic plan to improve its performance and solidify its position as the leading provider of logistics and supply chain solutions in Qatar. GWC aims at increasing shareholder value and providing a comprehensive range of high-quality logistics solutions and services, while
• Sheikh Abdulla Bin Fahad: Exploring investment opportunities to diversify our business model
• Sheikh Mohammed Bin Hamad: implementing a strategy to solidify market leadership in logistics services
• Ranjeev Menon: Innovation, sustainability, and digital transformation focus
“GWC has constructed over 4 million square meters of world-class logistics infrastructure. These hubs serve both local and international clients across various sectors, including aviation, telecommunications, fine art, and records, on a 3PL and 4PL basis.”
continuing to achieve further milestones”.
Sheikh Abdulla Bin Fahad Bin Jassim bin Jaber Al-Thani, GWC Managing Director, said: “In terms of international operations, GWC actively expands its presence in regional and global markets through global network and subsidiaries. This strategy positions us to seize new opportunities, strengthen our market position, and diversify revenue streams by offering specialized and integrated supply chain and logistics services to clients in various industries. Additionally, the company is seeking new arenas to enter as part of its business diversification strategies, allowing for new, well-studied business opportunities to be a part of its revenue streams”.
Ranjeev Menon, GWC Group CEO, said: “We seek to expand into new sectors and markets, build long-term relationships with partners, develop human capital, while focusing on innovation, sustainability,
and digital transformation. We are also committed to effectively managing our investment portfolio to solidify our leadership in integrated supply chain solutions. As the largest private sector developer of logistics hubs in the region, GWC has constructed over 4 million square meters of worldclass logistics infrastructure. These hubs serve both local and international clients across various sectors, including aviation, telecommunications, fine art, and records, on a 3PL and 4PL basis. We continually bid on new projects and management agreements, with specialized hubs catering to vital industries like oil and gas in Ras Laffan and Messaieed industrial cities”.
The launch of GWC Energy, a wholly owned subsidiary of GWC Group, represents a pivotal step in leveraging growth opportunities in the energy sector, especially with the ongoing North Field Expansion Project, the largest gas
project under construction in the world. Moreover, the launch of Al Wukair Logistics Park’s second phase is a key milestone in the company’s strategy to enhance performance and support micro, small, and medium-sized enterprises. This initiative aligns with Qatar National Vision 2030, stimulates economic growth, and fosters entrepreneurship and growth opportunities for start-ups.
GWC remains at the forefront as the premier provider of warehousing and distribution solutions across diverse industries. The company’s comprehensive services cater to entrepreneurs, MSMEs, and MNCs, as it manages billions of customer documents throughout their lifecycle in advanced storage facilities, provides land, air, and sea freight services, along with customs clearance, project logistics, and international moving and relocations. Additionally, GWC manages the State of Qatar’s largest fleet, boasting over 1,600 trucks, trailers, and specialized vehicles, while also providing marine services, facilitated through established subsidiaries, include shipping agency services, liner representation, port agency services, cruise ship hosting, and husbandry services. As the Authorized Service Contractor (ASC) for UPS in Qatar, GWC strategically expands the courier giant’s market share through the utilization of its logistics infrastructure.
The International Air Transport Association (IATA) has released data for June 2024 global air cargo markets showing continuing strong annual growth in demand. The results contributed to an exceptional first half-year performance for air cargo, with volumes exceeding 2023, 2022, and even the record-breaking 2021 levels. Global Supply Chain investigates.
In what can be perceived as a good turn, total demand, measured in cargo tonne-kilometers (CTKs), rose by 14.1% compared to June 2023 levels ( 15.6% for international operations). This is the seventh consecutive month of double-digit year-on-year growth.
Capacity, measured in available cargo tonne-kilometers (ACTKs), increased by 8.8% compared to June 2023 ( 10.8% for international operations).
“Air cargo demand surged in June. Strong growth across all regions and major trade lanes combined for a recordbreaking first-half performance in terms of CTKs. Maritime shipping constraints and a booming e-commerce sector are among the strongest growth drivers. Meanwhile, the sector has remained largely impervious to ongoing political and economic challenges, and the US customs crackdown on e-commerce deliveries from China. Air cargo looks to be on solid ground to continue its strong performance into the second half of 2024,” said Willie Walsh, IATA’s Director General.
Several factors in the operating environment should be noted:
In June this year, the Purchasing Managers Index (PMI) for global manufacturing output indicated expansion ( 52.3 ) while the new export orders PMI registered a small contraction, falling below the critical 50-point benchmark to 49.3.
WALSH, IATA’s Director General
Global cross-border trade expanded 0.1% month-on-month in May while industrial production stayed level compared to the previous month.
Inflation was a mixed picture in June. In the EU and Japan, inflation rates stayed roughly constant compared to the previous month at 2.6% and 2.8% respectively, while dropping in the US to 3.0%. In contrast, China’s inflation rate remained near zero ( 0.3%) reflecting weak domestic demand amid high unemployment, slow income growth, and a crisis in the real estate sector, a trend that has persisted since 2023.
Previously the total demand, measured in cargo tonne-kilometers (CTKs), rose 11.1% compared with April 2023 levels (11.6% for international operations). Capacity, measured in available cargo tonne-kilometers (ACTKs), increased 7.1% compared with April 2023 ( 10.2% for international operations).
“Air cargo demand started Q2 with a solid 11.1% increase. While many economic uncertainties remain, it appears that the roots of air cargo’s strong performance are deepening. In recent months, air cargo demand grew even when the Purchasing Managers Index (PMI) was indicating the potential for contraction. With the PMI now indicating growth, the prospects for continued strong demand are even more robust,” said Willie Walsh, IATA’s Director General.
Riyadh, the vibrant capital of Saudi Arabia, is set to host the muchanticipated Global Logistics Forum 2024 from October 12 to 14. This event, held under the esteemed patronage of Custodian of the Two Holy Mosques King Salman bin Abdulaziz Al Saud, promises to be a landmark gathering for the global logistics and supply chain sector. The forum will take place at the King Abdullah Financial District, a venue selected due to the international significance of such an event.
Minister of Transport Saleh Al-Jasser, in a recent statement, highlighted the transformative ambitions of the forum.
“Our aim is to reshape the global map of logistics,” said Al-Jasser. “This forum will serve as a vital platform for international collaboration, bringing together key stakeholders to drive innovation and growth in the logistics sector.” The minister emphasized that the event, supported by
King Salman’s patronage, is aligned with the Kingdom’s broader vision of pioneering reforms and economic diversification.
The forum is expected to attract over 10,000 participants, including heads of state, ministers, industry leaders, experts, and innovators from around the world.
This impressive turnout underscores the event’s significance in the global logistics landscape, where the exchange of ideas and expertise will be paramount.
A central theme of the Global Logistics Forum 2024 is the need for the logistics sector to adapt to the rapidly changing global environment, particularly in the context of climate change. The forum will provide a collaborative platform for stakeholders to discuss and develop strategies for sustainable logistics practices. Through dynamic discussion sessions, interactive workshops, and exhibitions, participants will explore innovative solutions to address the challenges posed by climate
The Global Logistics Forum 2024 in Riyadh is set to be a transformative event, bringing together the brightest minds in logistics to tackle the challenges of the future. With its strategic location, modern infrastructure, and commitment to innovation, Riyadh is poised to become a global hub for logistics, driving growth and sustainability in the sector.
The Global Logistics Forum 2024 is not just an event; it is a milestone in the ongoing journey to reshape the global logistics landscape.
www.glforum.org
change and other global disruptions.
One of the key highlights of the event will be the unveiling of Saudi Arabia’s logistics centres comprehensive plan, announced by Crown Prince and Prime Minister Mohammed bin Salman in mid-2023. This ambitious initiative aims to establish over 100 million square meters of logistics centres across the Kingdom, enhancing infrastructure, diversifying the economy, and positioning Saudi Arabia as a global logistics hub. “This master plan is a bold step forward in our journey to become a world leader in logistics,” noted Al-Jasser.
Riyadh’s strategic location at the crossroads of Asia, Europe, and Africa makes it an ideal host for a forum of this scale. The city’s modern infrastructure, coupled with its rich cultural heritage, provides a unique setting for the event. Participants will have the opportunity to not only engage in highlevel discussions but also to experience the dynamic energy of one of the world’s most rapidly developing cities.
Saudi Arabia’s recent rise by 17 places in the Logistics Performance Index is a testament to the Kingdom’s commitment to advancing its logistics capabilities. The Global Logistics Forum 2024 will further highlight these achievements, showcasing the progress made under the National Transport and Logistics Strategy.
The forum is more than just a gathering of industry experts; it is a platform for future leaders to shape the direction of global logistics. By fostering relationships with global leaders and exploring groundbreaking collaborations, participants will play a crucial role in influencing future logistics trends. “We see this forum as a springboard for the next generation of logistics innovations,” said Al-Jasser. “The discussions and partnerships formed here will have a lasting impact on the industry.”
Benefits of having Automatic transmission.
• The optional automatic transmission knows the best gear to engage in any situation and allows for quicker yet efficient and optimal cruising speeds. That means more trips per day and a boost to overall productivity.
• Direct coupling “lock up” function for enhanced fuel efficiency and performance.
Wide range of choices to keep every type of business on schedule.
• 3 GVW ranges from 19 – 10.4 Tones.
• Up to 21 different basic configurations.
• 8 & 5ltr engines with 180hp – 280hp.
• Euro 5 emission levels.
As globalisation accelerates, businesses are now more exposed to new markets, heightened competition, and unforeseen risks. This shift is particularly evident in the supply chain and logistics sector, where industry players are now placing a greater emphasis on efficiency and precision. In today’s world, the industry demands meticulously coordinated operations at every stage, from procurement to the final delivery of goods.
Evolving industry requirements and business processes have raised the need to integrate advanced technologies and automation management. In the present scenario, state-of-the-art supply chain and logistics software plays a pivotal role in streamlining every process and enhancing productivity. However, amid the complexities of each market, off-the-shelf software solutions often fail to mitigate unique requirements. This underscores the vital need for integrating customised software solutions in the industry.
As the regional industry gains traction on the global stage, it is crucial to consider the dynamics of various markets to maintain a competitive edge. For instance, the Middle East and Africa Freight and Logistics Market size is anticipated to reach USD 222.63 billion by 2029 from USD 163.57 billion in
2024, marking a CAGR greater than 6.36 per cent during the period. This growth also sheds light on the need for adaptive and customised software solutions to meet diverse needs of the expanding market.
The concept of customisation in software development for the supply chain and logistics industry is not about merely including features and functionalities. Developers should thoroughly understand the intricacies of each business operation, the challenges faced and goals to be attained. Software solutions that are designed on the basis of thorough background studies to address certain pain points are proven to be flexible and scalable, as against off-the-shelf solutions.
Customised software solutions provide the supply chain and logistics sector with the opportunity to seamlessly integrate their operations into existing systems
and technologies. Currently, warehouse automation is becoming increasingly prevalent in the industry as competitive pressure and customer demands for quality and delivery time rise. Amid this, embracing customised solutions gives a competitive advantage to industry players, given the inevitable need for interoperability in the evolving field of supply chain and logistics. In this environment, where multiple systems must collaborate in real-time, bespoke solutions empower businesses to navigate seamlessly through the intricacies of their operations.
The bespoke solutions aid supply chain and logistics companies to gain deeper insights into evolving market trends, customer behaviour, demand forecasts and operational performance. It further enables businesses to adapt to changing market conditions and emerging trends.
Another key benefit of customisation is the ability to address industry-specific regulations and compliance requirements. Similarly, embracing automation can benefit companies in ensuring optimal service quality, meeting customer expectations in delivery time, providing value-added services and reducing the difficulties of demanding tasks in warehouses. The supply chain and logistics industry operates in a highly regulated ecosystem with stringent guidelines for safety, security and environmental sustainability and adopting these solutions helps seamlessly mitigate the risk of non-compliance and potential penalties.
To ensure a seamless and efficient functioning of the industry, these customised and automated solutions can be integrated with legacy systems, IoT devices, warehouse management systems,
transportation management systems and other third-party applications. It further offers a unified ecosystem that streamlines operations and enhances visibility across the supply chain as well as empowers businesses to implement advanced analytics and predictive algorithms tailored to their distinguished needs.
In this regard, Savoye’s ODATiO 3MS (WMS, TMS, OMS) software solution has been grabbing attention since its launch in the Middle Eastern market. The agile and flexible supply chain solution, combining warehouse and transport management systems, has been designed to address the need for global logistics companies to adapt to the ever-evolving demands of the market for an automated environment. The solution’s warehouse management system is compatible with both automated and robotic environments, featuring
the ability to manage and schedule all logistics operations in a unified manner. It empowers businesses to customise and robotise the systems based on their unique requirements, preferences, and diverse industry profiles.
In the supply chain and logistics sector, the significance of customised software solutions cannot be emphasised enough. In the rapidly evolving landscape of supply chain management, businesses can benefit by leveraging bespoke software solutions. Such solutions have the potential to elevate efficiency, agility and innovation, fundamentally transforming the optimisation of supply chain processes for businesses. Whether enhancing warehouse operations or ensuring optimal customer satisfaction, these solutions act as catalysts propelling sustainable growth for industry players.
n Turkish Cargo, the air cargo brand of Turkish Airlines, has received the IATA Smart Facility Operational Capacity Certification. This prestigious certification, received for the SMARTIST Terminal, confirms that Turkish Cargo’s operational procedures comply with IATA Regulations (IATA Cargo Handling Manual, Dangerous Goods Regulations, ULD Regulations, Temperature Control Regulations, Live Animals Regulations and Perishable Cargo Regulations).
At SMARTIST, one of the state-ofthe-art cargo facilities in the world, cargo is stored and transferred using a computer-controlled Automated Storage and Retrieval System (ASRS), eliminating the need for an operator or forklift. Additionally, ULD storage processes are automated through the ULD Storage System. These smart storage management systems not only expedite operational processes by allocating the workforce to more value-added tasks but also minimize potential risks and reduce costs.
Commenting on the certification, Ali Türk, the Chief Cargo Officer of Turkish Airlines, said; “With a focus on maximizing customer satisfaction, Turkish Cargo aims to become the industry leader by 2033. This vision guides all our investments and business processes. The IATA Smart Facility Operational Capacity Certification is a significant endorsement of our brand, as it not only verifies that SMARTIST meets international quality
standards but also demonstrates that our digital solutions, smart systems, operations, and human resources are all aligned with our future goals.”
“We are pleased to announce that Turkish Cargo has achieved IATA’s Smart Facility Operational Capacity (SFOC) Certification for its SMARTIST
Terminal. This certification highlights Turkish Cargo’s commitment to operational excellence, ensuring that all types of cargo are handled seamlessly, securely, and in full compliance with global standards. The SMARTIST Terminal sets a high bar for cargo facilities worldwide, and SFOC Certification reinforces Turkish Cargo’s vision of leading through maximizing customer satisfaction,” said Brendan Sullivan, IATA’s Global Head of Cargo.
The IATA SFOC Certification is granted following detailed examinations conducted by independent auditors according to IATA standards. This prestigious certification demonstrates the compliance of handling and storage processes, from the acceptance of all special and general cargo to their loading onto the aircraft, with global standards. As a result, it enhances the operational efficiency and competitive strength of the facilities, ultimately boosting customer satisfaction.
n The AD Ports Group, subsidiary Noatum, has acquired a majority stake in Safina BV, a maritime agency and cargo services provider in Egypt and across the Middle East.
This strategic move marks a significant milestone for Noatum Maritime as it strengthens its foothold in the Mediterranean and Middle East regions.
AD Ports Group has a presence in over 50 countries and an extensive portfolio that includes 33 terminals. The recent acquisition of Safina aligns with the company’s broader expansion strategy, following its recent entry into the Turkish market and the signing of concession agreements by AD Ports Group for the management of cruise and Ro-Ro terminals in Egypt’s key ports, including Safaga, Hurghada, Sharm El Sheikh, and Sokhna.
With over four decades of experience, Sainfa is a prominent player in Egypt’s maritime industry, providing comprehensive agency services to the metals, minerals, and fertilisers sectors.
The company operates from six strategic locations, including its Cairo headquarters, and services 15 Egyptian ports, covering both the Mediterranean and Red Sea regions.
Terry Gidlow, CEO of Noatum Maritime, says, “The move enhances our
presence in key markets and enables us to strengthen our service offering across Egypt, the Middle East, and North Africa.” Safina will be rebranded as Noatum Maritime Egypt. The company’s founders will retain a minority stake and continue to support its growth under the new brand.
n J&T Global Express Limited, a leading global logistics service provider, has officially launched its J&T SPEED delivery service in Saudi Arabia. This new service aims to offer a more efficient, convenient, and reliable parcel delivery experience, catering to the increasing demand for such services in the region, particularly among individual customers and businesses.
The rise of the global digital economy has significantly accelerated the movement of goods, driven by the growth of e-commerce and new business models. This surge in demand for parcel delivery services is especially pronounced in Saudi Arabia and the broader Middle East. The introduction of J&T SPEED represents a pivotal advancement for J&T Express, reflecting the company’s commitment to enhancing service quality and customer experience. This launch not only strengthens J&T Express’s position in the Middle East market but also
highlights its ability to innovate within the logistics industry.
J&T SPEED is designed with user convenience in mind, offering multiple channels for order placement. Customers can effortlessly send parcels via the official app or website. Leveraging J&T Express’s extensive logistics network
and its wealth of operational experience, J&T SPEED delivers packages with remarkable speed. According to company data, the average delivery time for J&T SPEED is just 58 hours. Deliveries from Riyadh to Jeddah can be completed in as little as 20 hours, while intra-city deliveries are achievable in just 14 hours.
n Teleport, an integrated logistics provider, and Etihad Cargo have partnered together to inject cargo capacity and frequency on their respective cargo network between Southeast Asia and the Middle East, with plans to increase frequency in the near future. This move is against a backdrop of growing airfreight demand and trade between the two regions.
Trade between the Gulf nations and emerging Asian nations continue to show high growth momentum, surging 35% from US$383bil in 2021 to US$516bil in 2022, and is expected to reach US$757bil by 2030, outstripping growth rate with Western nations such as the US, UK and the Euro Area. At the same time, air freight demand continues to pose double digit growth across all regions, having risen 14.1% as of June 2024.
Since signing the partnership in May this year, Teleport has deployed its freighters for Etihad to ship machines, raw materials, phones and chip sets among others, from Ho Chi Minh to
Kuala Lumpur twice a week, with onward connection via Etihad’s capacity to Abu Dhabi and beyond. This partnership also enables both parties to maximise the available passenger belly capacity especially out of leisure hubs such as Bali and Phuket, by leveraging on each other’s network strength. Etihad will deepen its connectivity in Southeast Asia on the back of Teleport’s extensive network in the region, while Teleport leverages on Etihad’s strong global network to expand its network reach into the Middle East, Europe, Americas and the African regions. By the end of this year, the partnership is expected to see 1600 tonnes of cargo moved between the two destinations with potential for an increase in flight frequency and new routes.
Stanislas Brun, Vice President of Cargo at Etihad Cargo said,“We continue to anchor our strategy on key partnerships that will enable us to better serve our customer needs while supporting global trade. This recent partnership with Teleport is important to enhance our
connectivity to Southeast Asia, and we are confident that through the integration of their freighter operations and our capacity, we are able to continue to grow and build a more efficient and robust network that better serves both regions, and quickly. The market environment is highly favourable to grow our presence here today, and with a strong air partner like Teleport.”
Jagedeswaran Nadrajah, Head of Air Partners at Teleport, commented “The integration of Etihad’s global network with our largest Southeast Asia network has opened up a more dynamic way to connect cargo between these two regions - leveraging on the strengths of both our networks. This is valuable to both our existing and new customers trading between two important regions. This sort of synergy is testament to what Teleport has been building through its Air Partners programme as a win-win solution for all Teleport Air Partners, where we can continue to build and grow, and never fly empty.”
n Federal Express Corporation has upgraded its shipping services in Beijing and Tianjin by optimizing its air cargo network to enhance service efficiency in these cities. This improvement better connects local customers to markets in Asia, Europe, the Middle East, and Africa.
With immediate effect FedEx has reduced transit time for inbound shipments for Beijing and Tianjin by one day. The cutoff time for same-day outbound shipments has also been extended to 4:30 p.m. in Beijing and 3:30 p.m. in Tianjin, offering customers more time and greater flexibility. Additionally, FedEx has increased its weekly capacity in these cities to meet the growing import and export needs of local customers. This upgrade provides more efficient shipping services for customers using FedEx International Priority® service for outbound shipments, and both FedEx International Economy® and FedEx International Priority® services for inbound shipments.
“FedEx remains committed to optimizing its air transport network in China to provide more flexible and valuable
solutions for local customers,” said PohYian Koh, Senior Vice President of FedEx and President of FedEx China. “Supported by our air cargo partner, these upgraded international shipping services in Beijing
and Tianjin will enhance the connection between the Beijing-Tianjin and markets in Asia, Europe, the Middle East, and Africa. They will also help accelerate foreign trade in the region and support the stable growth of global trade.”
As the Beijing-Tianjin-Hebei region continues to develop, its logistics ecosystem plays an increasingly critical role in unimpeded domestic and international economic flow, supporting the sustainable growth of foreign trade. This year marks the 10th anniversary of the Beijing-TianjinHebei coordinated development strategy, celebrating a decade of building an economic powerhouse for China’s opening up. The total value of foreign trade has increased from RMB 3.74 trillion in 2014 to RMB 5.03 trillion in 2023, up 34.4%.[1] In the first half of this year, the region saw its import and export value increase by 4.6% year-over-year to RMB 2.54 trillion, a record high level for the same period in history. [2]
This year also marks the 40th anniversary of FedEx operations in China. Since 1984, FedEx has been committed to expanding its logistics network and service portfolio to support the development of China’s supply chain. Last month, FedEx launched two new flights to the United States from Qingdao and Xiamen and plans to establish international gateway facilities at each location.
The newest freighter in the Lufthansa Cargo fleet has also been given its name “Hola Argentina!” within the “Say hello around the world.”
n Lufthansa Cargo recently welcomed its 18th B777 freighter at Frankfurt Airport. The long-haul freighter was transferred directly from the Boeing factory in Everett, USA, to the cargo airline’s largest hub. The event took place on 17th August 2024.
“We are delighted to welcome another efficient freighter to our fleet. This will allow us to provide our customers with additional capacity, continue to grow in the air freight market and enable global business. This means that we can align our network even more closely with our customers’ needs and also offer solutions to market changes at short notice. In addition, the B777F remains the most efficient and modern freighter in its class. Our latest aircraft is therefore another important investment in our modern long-haul fleet and contributing in making air cargo more sustainable,” explains Ashwin Bhat, CEO of Lufthansa Cargo.
The newest freighter in the Lufthansa Cargo fleet has also been given its name “Hola Argentina!” within the “Say hello around the world.”
As one of the leading air freighters, Lufthansa Cargo utilizes the belly capacities of Lufthansa, Discover, Brussels, Austrian Airlines and SunExpress. This enables the Lufthansa Group’s logistics expert to offer its freight customers the transportation of their shipments with up to 7,000 flights a week to over 350 destinations worldwide.
Lufthansa Cargo currently operates a full B777F fleet of 12 of its aircraft
on long-haul routes. In addition, six B777 freighters are operated by AeroLogic, a joint venture between DHL and Lufthansa Cargo. The global network is additionally supplemented by a total of four A321 freighters on short and medium-haul routes. From this summer, these will not only operate to and from Frankfurt, but will also connect the Munich hub directly to the freighter network.
n Maersk, a global shipping major headquartered in Denmark, has announced that it has joined hands with Saudi General Ports Authority of Saudi Arabia (Mawani) for opening of its largest logistics park in the Middle East at Jeddah Islamic Port.
The 225,000 sq m facility, which is the largest single-site logistics & services facility in the region, has built at an investment of $250 million, said Maersk in a statement.
The new logistics park will contribute to service and development in supporting economic activity in the kingdom and providing highly efficient logistics services to support the movement of trade and export to foreign markets and enhance the work of supply chains and logistics, it stated.
An eco-friendly complex, it will draw up to 70% of the electricity from 32,000 solar panels installed over 64,000 sq m. on
the rooftop. The Maersk Logistics Park will use electric equipment and electric trucks within the facility, have low electricityconsumption LED lighting optimised with light sensors, etc.
The inauguration ceremony was held in the presence of Engineer Saleh bin Nasser Al-Jasser, the Minister of Transport and Logistics Services, Chairman of the Board of Directors of the General Ports Authority;
Omar bin Talal Hariri, the Chairman of the Authority, Vincent Clerc, the CEO of AP Moller – Maersk, Richard Morgan, the Managing Director of Maersk Indian Subcontinent, Middle East and Africa; Mohammad Shihab, the Managing Director at Maersk Saudi Arabia; Ahmed Kudous, the Head of Supply Chain Personal Care Middle East and Turkey and Head of Customer Operations GCC, Unilever.
This new enhancement is testament to the airline’s commitment to simplify cargo booking services through digital transformation.
n Qatar Airways Cargo has launched the “My Allotments” feature on its website within the Digital Lounge portal, setting a new standard in cargo booking efficiency and intuitiveness.
The allotment dashboard signifies a big leap in the airline’s digital transformation journey. As the world’s largest air cargo carrier, Qatar Airways Cargo is leading the industry, providing customers with a personalised allotment view and instant confirmation of their bookings while at the same time allowing customers to directly book allotments via the Digital Lounge platform. The feature will also help in preventing overbooking by allowing customers to easily track available inventory and optimised pre-planning of
allotment shipments.
Customers can book their allotments quickly and complete their bookings with just a few clicks. Additionally, the Digital Lounge portal offers a personalised experience, by showing upcoming allotments, so customers can book, with real-time updates on the remaining capacity available on the flight. These enhancements align with Qatar Airways Cargo’s continuous upgrades to the Digital Lounge since its launch, including auto-confirmation for bookings, 24/7 helpdesk, advanced tracking and tracing and making the entire booking journey for its customers efficient and seamless.
Mark Drusch, Chief Officer Cargo at Qatar Airways Cargo commented: “The ‘My
Allotments’ feature in our Digital Lounge booking portal is proof of Qatar Airways Cargo’s commitment to leading the industry in technology, innovation and customercentricity. This platform not only streamlines the booking process for our clients but also embodies our dedication and drive towards digitalisation and providing realtime solutions that enhance efficiency and planning. We are proud to set a new standard in the cargo industry, focusing on the requirements and feedback of our customers to continuously improve their cargo booking experience.”
Qatar Airways Cargo encourages its customers to take advantage of the multiple benefits of online booking by signing up to Digital Lounge today.
International Benefits:
+ The FIATA member certificate
+ Use of the Fiata logo
+ Entry in the FIATA members directory & networking events
+ Advertising in the FIATA members directory, review and information (FIATA e-Flash)
+ Special Rates for FIATA publication and articles
+ Access to secretariat›s assistance
+ FIATA arbitration code
+ Use of FIATA documents
+ FIATA worldwide member connectivity
+ Talent Connect Worldwide, E-Learning
+ Discountes rates in participating in global and regional conferences
+ Asssistance in case of legal advocacy
+ Discounts for cargo/logistic events and exhibition stands
+ Discount training for NAFL members
+ Training/Certification for regional/international courses
+ Insurance at discounted rates (cargo/liability/medical)
+ Complimentary internship, Skill upgrade and Mentoring & Innovation ideas
+ Discounted supplier rates for industry products
n The UAE’S leading port authority, AD Ports Group has issued a white paper titled “Digitalisation for Enhanced Efficiency: Leveraging Data for Smart Ports”as a valuable resource for understanding the dynamics of digital transformation in the maritime sector and its critical role in enhancing global trade efficiency.
An in-depth analysis of the transformative impact of digital technologies on port operations that outlines strategic approaches to harnessing data for increased operational efficiency, sustainability, and competitiveness is also presented in the white paper. Furthermore, it discussed the challenges and successes of digitalisation across various global ports, with a focus on Asia, Africa, and South America, regions that have seen significant advancements in port technology.
It highlighted how deploying cuttingedge technologies and data-driven strategies has been instrumental in reshaping traditional port operations to meet modern demands.
Dr. Noura Al Dhaheri, CEO of Digital
Cluster and Maqta Gateway at AD Ports Group, said,“When applied to ports, big data and digital-twin technology is set to transform a wide range of operations. This technology can store different streams of information from ports, logistics, sensors and positioning networks; and process that information in real time, which allows ports to create multidimensional models that help
optimise port supply chains, reducing delays and congestion at the facilities and increasing the efficiency of the different stakeholders involved.”
Key insights from the white paper include a detailed examination of the technological innovations driving the evolution of traditional ports into smart ports, including IoT, AI, and blockchain technologies.
n Mace has been appointed as delivery partner by King Salman International Airport Development Company (KSIADC) to oversee the planning and construction for its airport development programme in Riyadh, Saudi Arabia.
Mace, the global consultants and construction experts, working alongside KSIADC that is owned by Saudi’s Public Investment Fund (PIF), will lead the full range of delivery partner services for the six-runway airport. This will incorporate project and programme management, PMO and planning, construction management, cost and commercial management, procurement, logistics, health and safety strategy, and sustainability, environmental and carbon-advisory services.
Mace’s integrated team will focus on optimising planning and construction schedules to enable the phased completion of one of the world’s largest airports. The new major aviation hub is set to be ready to host people travelling for Riyadh Expo 2030 and FIFA World Cup 2034™ and will
play a key role in Saudi Arabia’s economic diversification under Vision 2030.
KSIADC appointed Mace because of the firm’s experience leading major global aviation programmes – including Heathrow Airport in the UK, Schiphol Airport in the Netherlands, Keflavik International Airport in Iceland, and Hamad International Airport in Qatar – as well as its reputation as a leading delivery partner, and extensive giga-project portfolio in the Middle East. The appointment was sealed at an official ceremony in Riyadh,
where Marco Mejia, Acting CEO for KSIADC, and Christopher Seymour, Managing Director of Middle East and Africa at Mace Consult, signed the contract.
Davendra Dabasia, Chief Executive Officer of Mace Consult, said: “King Salman International Airport is a game-changing infrastructure programme. The scale of ambition for the programme’s physical build, as well as its commitment to sustainability, innovation and economic development, is unmatched.
n Huizhou, China - BSL New Energy Technology Co., Ltd. (Brand: BSLBATT® ), an innovative high-tech company that designs and manufactures smart lithium-ion batteries (50% more efficient than similar products on the market) for industrial forklifts used in the warehousing and distribution industries, has partnered with PF, a major European cold storage customer, to launch the largest fleet of lithiumbattery-powered Crown forklift in the cold storage industry, with a deployed capacity of approximately 6.6 megawatthours (MWh).
“Lithium-battery systems eliminate time-consuming and expensive maintenance and provide longer life at extreme temperatures, especially in cold environments. As the company converts all existing and future material handling equipment to lithium batteries, the fleet
“As the company converts all existing and future material handling equipment to lithium batteries, the fleet will run better, longer, and consume less power.”
will run better, longer, and consume less power.”
As one of the largest public cold storage companies in the world, PF has 30 facilities in Italy, France, and Spain. Many upcoming facilities are under construction. The company’s warehouses are below -30 degrees Celsius and face
unique challenges that lead-acid batteries cannot solve. Specifically, lead-acid battery systems lose power and operating efficiency over a shorter cycle life, resulting in increased operating costs and performance degradation of up to 60%.
Tracy Shen, Sales Manager of the Power Division at BSL BatteryIndustrial, said: “PF customers have seen immediate benefits from switching from lead-acid battery systems to lithium-ion systems. Lithium-ion systems eliminate time-consuming and expensive maintenance and maintain a longer service life at extreme temperatures, especially in cold environments. As the company strives to convert all existing and future material handling equipment to lithium-ion batteries, the fleet will operate better, longer, and consume less power.”
n Cargo comes to the rescue yet again. IAG Cargo, the cargo division of International Airlines Group, whose brands include British Airways, Iberia, Aer Lingus and Vueling, has delivered critical aid to Grenada in the aftermath of Hurricane Beryl.
The cargo division of International Airlines Group, whose brands include British Airways, Iberia, Aer Lingus and Vueling, has worked with organisations including the Grenada Overseas Association Manchester and All Saints Parish Church Bedford, alongside the Grenada High Commission in the UK to transport aid to the Caribbean island following the disaster on 1 July.
In early August, critical items were flown on a British Airways 777 to Maurice Bishop International Airport, including first aid kits, water purification systems, bedding, non-perishable food items and hygiene supplies.
Chief commercial officer, John Cheetham, said: “IAG Cargo is committed to swift action during humanitarian crises. Leveraging our global network, we are proud to collaborate with charities to
deliver essential aid to Grenada and I’m thankful to our team who have worked to support this effort.”
High Commissioner for Grenada, Her Excellency Rachér Croney thanked all involved in the effort, adding: “Without the efforts of Grenadians in the diaspora answering the call and rising to the
challenge this could not have been possible and we certainly could not have done it without the partnerships and philanthropic contributions of international organisations such as IAG Cargo. We are thankful for their assistance and generosity during our time of need.”
n DB Schenker has expanded the number of airlines it has digital connectivity to for online bookings through a new partnership with cargo.one.
The forwarder has in recent months been creating API connections with a series of its airline partners as it looks to create efficiencies in the booking process.
DB Schenker recently announced it had formed a partnership with online booking portal cargo.one that would give it digital access to the capacity of 50 airlines. The connectivity between DB Schenker and cargo. one is based on API calls from DB Schenker’s transport management system for availability and pricing of capacities, as well as booking and booking confirmations. Those calls are triggered and fed back to the transport management system in DB Schenker.
The forwarder said that when it digitally responds to a quote request from a customer it will inquire with a larger number of airlines – four times as many, on average.
The carrier previously created API connections with nine airlines: Cargolux (November 2022), Qatar Airways Cargo (May 2023), Lufthansa Cargo (June 2023), Air France KLM Martinair Cargo (August 2023), American Airlines Cargo (November 2023), Cathay Cargo (December 2023), Emirates SkyCargo (April
2024), Avianca Cargo (May 2024).
“Around 75% of DB Schenker’s global airfreight volume is carried on our top 20 carriers. We had already set up direct API interfaces with a significant proportion. Now we are connected to almost all of them,” said DB Schenker spokesperson Mario Arnold.
10 – 11 December 2024
Dubai World Trade Centre
Secure your spot at Dubai's premier logistics & mobility event
Launch Edition
Collocated with: Meet 2,000+ Visitors Join our Mainstage Conferences Network with 125+ Speakers
n Ethiopian Airlines Group has signed a contract with Dar Al-Handasah Consultants to build a ‘Mega Airport City’ at Abusera in Bishoftu City that will include over 100,000sq m of cargo and support facilities.
The site, 40 km from the existing Addis Ababa Bole International Airport, lies about 20 km south east of the city centre on the main A1 road to the south. According to Ethiopian Airlines, the Mega Airport City will have a capacity of 110m passengers each year, four times the current capacity of the existing gateway.
The first phase is scheduled to be completed in 2029, with a capacity to handle 60m passengers, itself almost three times the number of passengers handled at Africa’s busiest airport in 2022.
Crucially, the new gateway will also have the advantage of a lower elevation compared to the current hub which is among the highest major airports in the world and hence presents operational challenges, including reduced aircraft payloads.
Dar Al-Handasah specialises in design, planning, engineering, and management
n Aramex, a leading global provider of comprehensive logistics and transportation solutions, is taking its sustainability efforts to the next level with the appointment of Manosij Ganguli as Group Chief Sustainability Officer. This strategic move highlights Aramex’s commitment to not only maintaining but also elevating its position as a regional leader in sustainability.
Manosij Ganguli joins Aramex with a distinguished background in global decarbonization efforts, having previously served at the Energy Transitions Commission and Mission Possible Partnership (MPP) in London and as the Global Program Director at BP. Both at MPP and at BP, Manosij spearheaded transformative programs across continents. His extensive experience and track record of translating ambitious sustainability goals into actionable
services, and is part of the Sidar group that has delivered projects in over 300 airports worldwide, including Bole International and Dubai International.
The architecture of the new airport will incorporate elements of the country’s heritage “to establish a new emblematic structure for the
strategies make him a valuable addition to our team.
In his new role, Manosij will spearhead Aramex’s sustainability agenda, ensuring that the logistics provider continues to innovate and implement best practices in environmental stewardship. The new appointment aligns with Aramex’s well-established history of integrating sustainability into its operations. From reducing carbon emissions through innovative last-mile delivery solutions to implementing energy-efficient technologies across its global network, the company has consistently prioritised the environment alongside its growth.
The company’s comprehensive approach to sustainability is underpinned by evidence-based strategies that address the needs of all consumers, businesses and stakeholders.
nation”, said Ethiopian Airlines.
Group chief executive Mesfin Tasew added: “With its exceptional capacity and world-class facilities, this new airport promises to elevate African aviation and strengthen partnerships, marking a significant advancement for the region’s air travel infrastructure.”
Aramex has consistently demonstrated its commitment through proactive measures, including investments in renewable energy, carbon footprint reduction programmes, sustainable packaging solutions, implementation of zero and low emissions delivery vehicles and the development of eco-friendly logistics hubs.