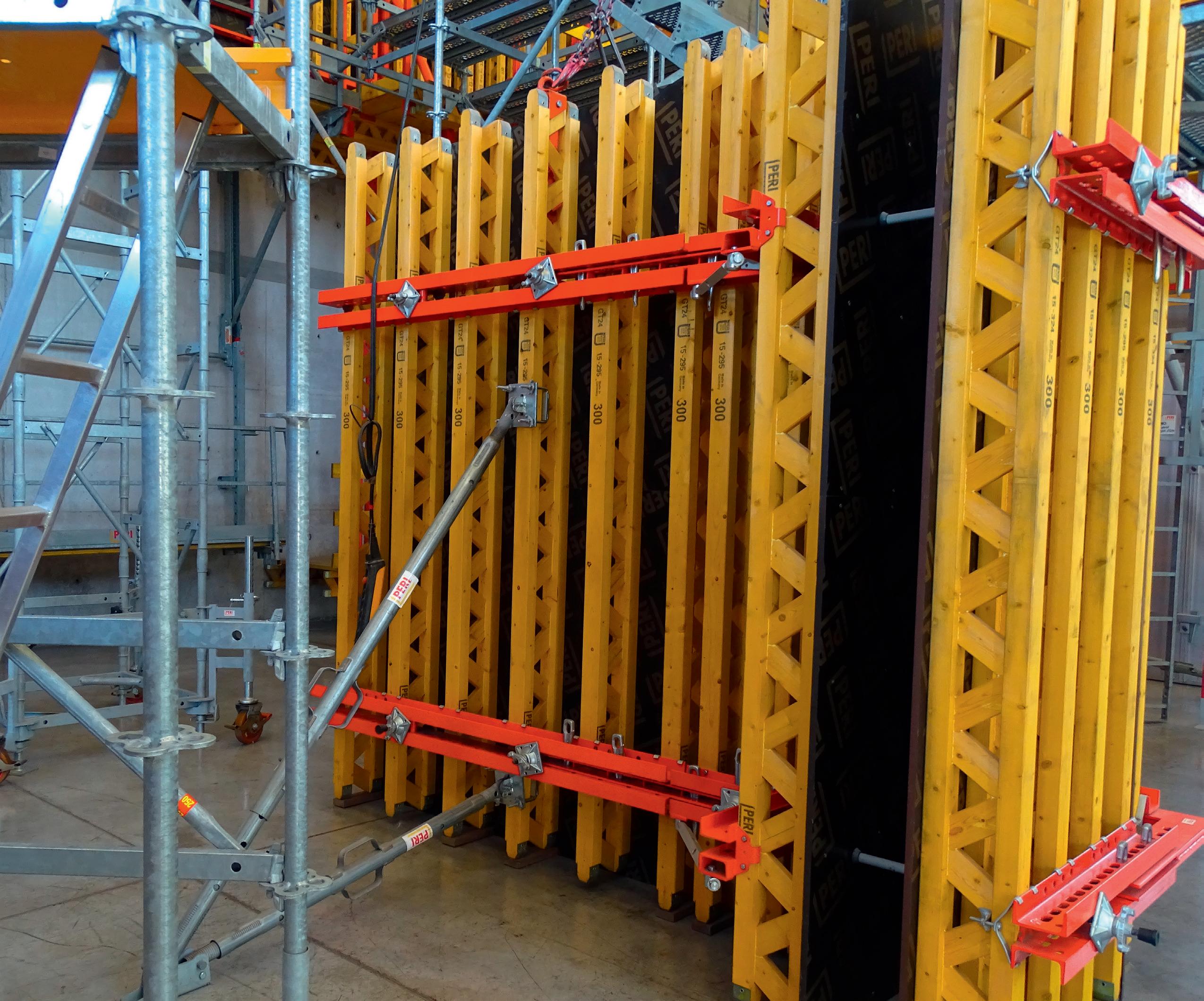
17 minute read
MAQUINARIAS
ENCOFRADOS EN LA CONSTRUCCIÓN CON HORMIGÓN
SISTEMAS DE ENCOFRADOS PARA LA CONSTRUCCIÓN
Advertisement
DANDO FORMA AL HORMIGÓN
Todos los proyectos constructivos, sean obras civiles, habitaciona les, de corte industrial o incluso, aquellos ligados a la actividad minera, poseen dos elementos en común. El primero de ellos, es que el hormigón, como materialidad de obra, responde prácticamente a todos los requerimien tos que contemplen dichos proyectos. De la mano con esto, es que al hor migón necesariamente hay que darle forma estructural, ya sea muro, losa u otro elemento. Para ello, son necesarios los moldajes o encofrados, elementos transversales a todo tipo de obra.
El moldaje es un elemento de cons trucción transitorio, cuya finalidad es contener al hormigón y darle forma mientras éste fragua y se rigidiza para adquirir la figura dada por el molde. Una vez que ocurre este proceso, el moldaje se retira y queda el hormigón con la for ma permanente.
En Chile, los encofrados más utiliza dos hasta mediados de la década del noventa, que es cuando se comienzan a traer equipos que apuntaban a indus trializar este proceso, eran aquellos de fabricación artesanal con material lige ro. Este tipo de moldes, fabricados en la misma obra, presentan problemas como formas irregulares, pérdida de material (hormigón) y su durabilidad, en general, era muy baja. Esto implicaba un costo extra para la obra, destinado precisa mente para rectificar las imperfecciones producto de este tipo de moldes.
Con la irrupción de moldajes de carac terísticas más industrializadas en cuanto a su diseño y más robustos en sus ma terialidades, se consiguieron mejorar los plazos de las obras, elevar la calidad de las terminaciones e incorporar otros atributos que con moldajes artesanales eran muy complejos de conseguir, como es el caso de dejar hormigón a la vista. Además, también mejoraron los están dares de seguridad en obra, al tratarse de encofrados producidos en serie y no fabricados in situ, en el mismo lugar de la obra.
Bastidor metálico y placa fenólica: el nuevo estándar
Desde el instante de su irrupción, a fines de la década del noventa, los mol dajes metálicos con placa fenólica se han convertido en uno de los más uti lizados en el sector, ya sea para obras
civiles como para proyectos habitacionales. Los distintos sistemas que abarca esta denominación tienen todos carac terísticas industriales. Vale decir, estos se fabrican en serie en una planta y por lo mismo, el equipo viene con las dimen siones ya fijadas para las prestaciones que se requieren, sean muros, columnas, losas u otras estructuras de característi cas especiales en su forma.
Así, en términos de sus materiales, los sistemas de moldajes se dividen en cua tro tipos: metálicos, mixtos, de material ligero o de otras materialidades.
En el caso de nuestro país, al superar la fabricación artesanal del encofrado con material ligero, se opta por elemen tos como el acero y el aluminio, entre otros, para entregar mayor durabilidad al sistema, al tiempo que mejora las terminaciones que tendrá el hormigón una vez se descimbre el molde. Junto con ello, también se adoptan bastidores metálicos con placa fenólica para el con tacto con el hormigón.
Al respecto, Paula Rissi, product manager de PERI, comenta que para empresas dedicadas al moldaje, esos elementos son el “piso que maneja hoy
El moldaje es un elemento de construcción transitorio, cuya finalidad es contener al hormigón y darle forma mientras éste fragua y se rigidiza para adquirir la figura dada por el molde. Una vez que ocurre este proceso, el moldaje se retira y queda el hormigón con la forma permanente.
por hoy la industria dedicada al montaje: bastidor metálico con placa fenólica”.
La placa fenólica, explica Vicente Fuenzalida, ingeniero civil y ejecutivo comercial de encofrados PERI, se com pone de “un terciado que viene con un film fenólico incorporado para generar una buena reacción con la humedad del hormigón, que pueda absorberla y así, provoca un efecto de impermeabiliza ción destinado a proteger al terciado”. De esta forma, se asegura que la placa, que es la cara de contacto con el hormi gón, rinda usos continuos para efectos de la productividad de la obra, agrega Fuenzalida.
Junto con esto, el representante de PERI cuenta que la placa fenólica po see distintos grosores, dependiendo del sistema al que se encuentren incorpora dos. ¿Qué implica esto? Según explica Fuenzalida, a mayor grosor, “la placa es de mejor calidad, lo que permite que tenga mayor cantidad de usos, por una parte, y que también, la calidad de la terminación sea mejor”. En el caso de PERI, estas piezas van desde los 15 milí metros hasta los 21milímetros de grosor. La placa fenólica se une al bastidor metálico por medio de un sistema de pernos que la anclan al bastidor y en general, se necesitan dos operarios que vayan apretando los pernos en ambas

caras del sistema, para luego cerrarlo. En ese aspecto, comenta Fuenzalida, algunos sistemas de moldaje con placa fenólica más avanzados, con mayor gra do de industrialización, utilizan un solo trabajador. “Se usa un cono para unir los paneles. Entonces, ese cono, cuando los unes, queda enganchado, se aperna, el trabajador da la vuelta y lo aprieta des de el otro lado”, especifica.
Los moldajes metálicos con placa fe nólica pueden subdividirse en aquellos que pueden ser transportados por los propios operarios y los que necesitan de grúa para ser trasladados. Para esto, se cuenta la robustez de sus bastidores metálicos. En ese sentido, Vicente Fuen zalida revela que, por ejemplo, el panel más grande del sistema TRÍO de la firma, cuyas dimensiones son de 3,30 metros de ancho de panel por 2,40 metros de alto, pesa “alrededor de 330 kilogramos, por lo que se debe mover con grúa”.
En la otra vereda, existen moldajes metálicos con placa fenólica que están diseñados para evitar el uso de equipos para su transporte. Esto se logra al redu cir las dimensiones del bastidor metálico (y de la placa fenólica), lo que se tradu ce en una importante pérdida de peso. “Lo que buscan ese tipo de sistemas –comenta Fuenzalida– es que la obra no dependa de la grúa. Por lo mismo, en trega mayor flexibilidad, ya que en vez de coordinar dos equipos, uno con el moldaje y otro que transporte materia les, se utiliza uno solo”. En este sentido, dice, en PERI, el sistema DÓMINO está diseñado bajo esas características. “En el fondo, lo tratamos como un sistema semi-manual”, aclara.
El profesional detalla que el panel más pesado del sistema DÓMINO pesa 80 kilogramos y que el del sistema LIWA –“similar a DÓMINO pero con bastidor más delgado”, subraya– tiene un peso de 60 kilos, por lo que “entre dos per sonas, se puede mover perfectamente”, asegura.
Finalmente, en cuanto a usos, la vida útil de la placa fenólica varía desde los 120 usos a los 80. Eso, según Vicente Fuenzalida, se supedita al proyecto don de se utilice este sistema y del grosor del terciado que compone la placa.
Moldajes dedicados a diferentes estructuras
Además de clasificarse de acuerdo a su materialidad (metálico con placa fenólica, metálico o de material ligero), cada sistema de encofrado también puede dividirse de acuerdo a la estruc tura para que va a utilizarse: muro, losa, columna, trepante y, en el caso que el moldaje permita hormigonar de una sola vez losa-muro, se habla de un monolí -
tico.
Ya sea para muro o losa –sin conside rar el sistema monolítico– los distintos encofrados de bastidor metálico con placa fenólica pueden ser utilizados para moldear al hormigón y dar con la estruc tura deseada. En el caso de los moldajes basados en bastidor metálico, si bien las dimensiones vienen establecidas desde fábrica, los bastidores multiperforados, comenta Vicente Fuenzalida, “permi ten ajustar el cierre del muro sin que necesariamente coincida donde cae la perforación de cierre. En definitiva, tie nes una mayor flexibilidad a la hora de modular el muro, lo que se traduce en menos compensaciones de material li gero y por ende, menos costo para la obra”.
En la misma línea de la flexibilidad a la hora de modular muros, existe un sistema de placa fenólica con vigas de material ligero exclusivo de PERI, que permite moldear muros sin las limitantes que plantean los bastidores metálicos, cuyas dimensiones de alto vienen defi nidas desde su fabricación.
Este sistema, cuenta Vicente Fuenza lida, permite flexibilidad en cuanto a la modulación de los muros. Esto, explica lo realizas gracias a que “las vigas de material ligero van amarradas entre sí con correas metálicas y la placa fenólica se atornilla a estas vigas. La combina ción de estos elementos te permite, por ejemplo, moldear un muro con medi das especiales. Por ello decimos que este sistema, llamado VARIO, es nuestro moldaje arquitectónico”, asegura el eje cutivo.
Asimismo, en la misma línea de en cofrados con vigas y placa fenólica, también existe otro variante que implica que las correas metálicas puedan ajus tar la curvatura de la placa y así, moldear muros curvos. “Se necesita un radio de un metro, como mínimo, para poder ajustar la curvatura de la placa.”, comen ta Fuenzalida, mientras que Paula Rissi agrega que, dado el radio de curvatura que entrega este sistema de encofrado, “se podría ajustar un muro curvo con un diámetro de dos metros”.
Para estructuras como pilares, pueden utilizarse tanto los sistemas de encofra do fenólicos compuestos por bastidor metálico o aquellos más flexibles, cuyo armazón son las vigas reticuladas de material ligero. En los primeros, se tra ta de bastidores “multiperforados, que cuentan con dimensiones que van des de los 90 a los 120 centímetros y que pueden formar pilares cuadrados o rec tangulares de 20 por 20 centímetros hasta 75 por 75 centímetros”, explica el ingeniero civil.
Agrega que, en el caso de aquellos moldajes que permiten formas curvas, se pueden modular pilares “haciendo unos cortes a la placa, cosa que quede como un pilar y luego, se unen las pla cas”.
En el caso de los encofrados para losas, Vicente Fuenzalida explica que estos se dividen dependiendo de la al tura de la losa. “En la mayoría de las obras –comenta– utilizamos el sistema denominado MULTPLEX, que permite trabajar alturas de hasta cinco metros. Este se compone de puntales de acero denominados PEP que van sobre unos trípodes metálicos, los que estabilizan un entramado de vigas principales de material ligero y sobre eso, se posiciona la placa fenólica para el hormigonado”.
Para alturas superiores o de mayor peso, el ejecutivo de PERI comenta que se utiliza este mismo sistema, pero con una variación: en vez de puntales de acero, se utilizan unos de aluminio. “Estos se pueden unir en altura, permi tiendo la construcción de torretas. La altura máxima que se alcanza con este sistema es de 6,25 metros”, dice Fuen zalida y agrega que “con este sistema, se pueden realizar dos uniones en altura, lo que significa que se puede hormigo nar una losa a un máximo de 12,5 metros
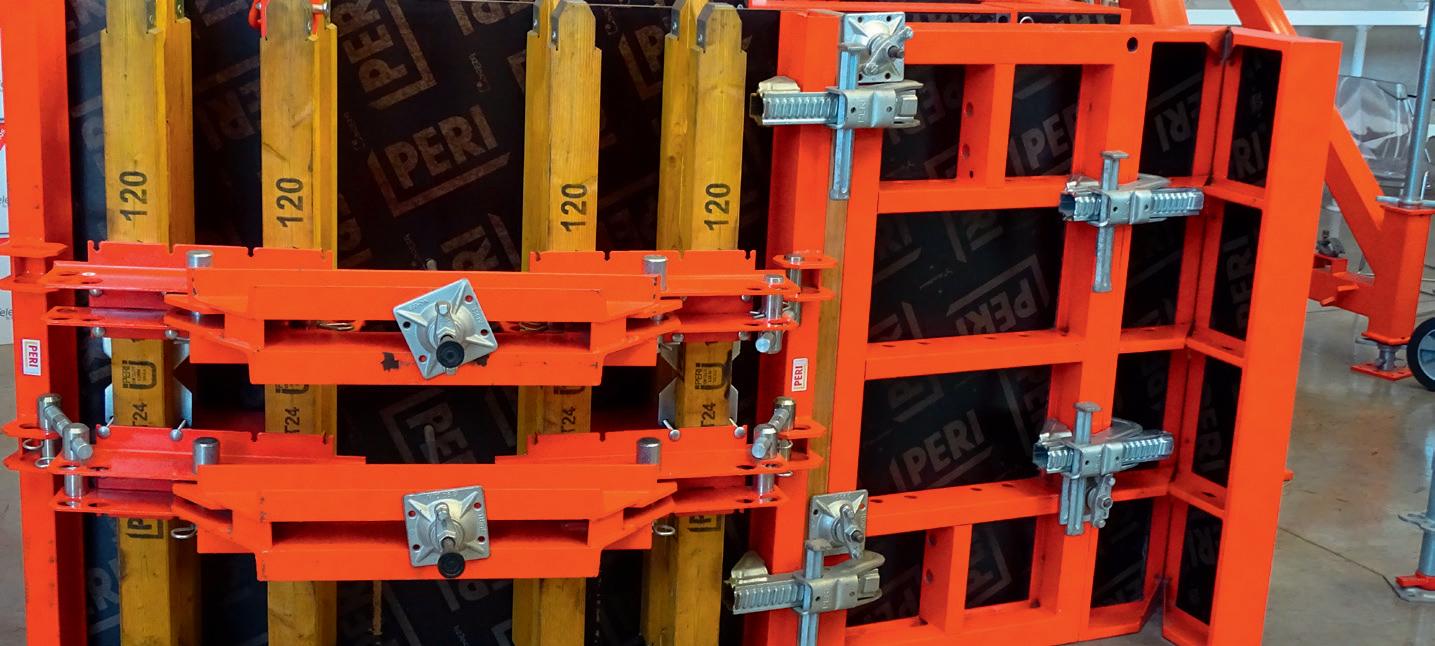
de alto”.
Existe otro sistema de moldaje de losa que utiliza bastidor de aluminio. “Este sistema funciona con los mismos punta les PEP y tienen una placa fenólica que va directo al bastidor. De esta manera, se puede hormigonar de inmediato la losa”, dice Vicente Fuenzalida.
Dentro de esta categorización se in cluyen los sistemas trepantes. “Estos sistemas –comenta Fuenzalida– son un complemento para el muro porque se trata de una plataforma que se arma para poder modular y hormigonar estas estructuras”. En ese sentido, explica el ejecutivo de PERI, “el sistema de trepas permite trabajar en muros donde no tie nes apoyo para trabajar. Por ejemplo, el muro de la culata que queda por afuera del edificio, no tienes como trabajarlo a menos que sea en un andamio. Las tre pas permiten trabajar eso”.
“PERI desarrolló un sistema de tre pas que básicamente son escuadras que anclas a los muros y generan una plataforma. Entonces, sobre la trepa, se monta el muro”, dice el ingeniero. Existen dos sistemas de anclaje para la trepa. Uno, se compone de “un cono que que va con una barra y que a la vez, viene con una contraplaca que se deja embebida en el hormigón al momento de hormigonarlo”. Una vez hecho esto, cuando se descimbra, se recupera todo el sistema, explica Fuenzalida.
El otro sistema, en vez de un cono, “va con un perno pasado. Cuando se hormi gona el muro, se deja una camisa, una perforación en el muro de la dimensión del perno. Este se pasa y en la cabe za del perno, se fija la escuadra”, dice. Agrega que también existen platafor -
La gran ventaja que ofrece este sistema en comparación con los de placa fenólica, es su peso. “El panel más pesado es de 24 kilos”, asegura el ejecutivo de PERI, con lo que se transforma en un “producto 100% manoportable”. Además, posee pocas piezas –las que son del mismo material de los paneles– y de acuerdo a Carrasco, “se trata de un sistema muy intuitivo, que cualquier operario puede montar”
mas plegables, cuyo funcionamiento es similar a la escuadra con perno pasado, pero sólo que ésta se plega.
Finalmente, existen los sistemas au totrepantes. “En el caso de PERI, lo recomendamos para alturas sobre los 30 pisos”, subraya Fuenzalida y comen ta que estos se componen de “pistones hidráulicos, que van con unos rieles que se fijan en el muro y gracias a la fuerza de los pistones, las trepas suben cada 50 centímetros. Los rieles tienen el lar go de 3 pisos, lo que significa que es la última trepa la que va subiendo el riel porque si no, no tienes como seguir su biendo al siguiente nivel”.
Moldajes de plástico y monolíticos
Además de los encofrados con placa fenólica, sean estos de metal o de ma
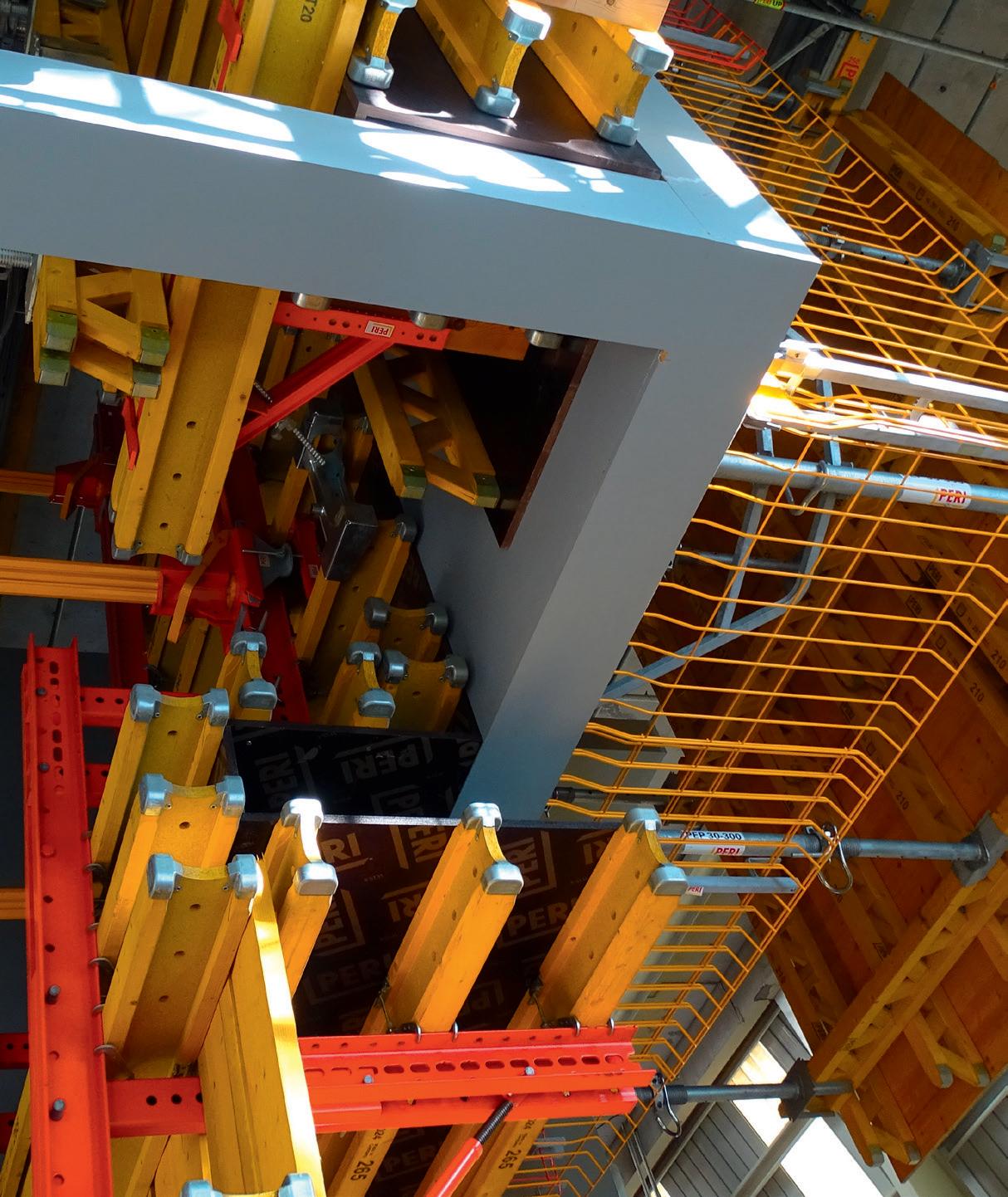
terial ligero, existen innovaciones en cuanto a las materialidades que me recen destacarse. Desde hace unos 5 años, en PERI incorporaron sistemas de moldajes fabricados con polipropileno de alta resistencia, los que están enfoca dos a “proyectos de menor envergadura. Estamos pensando en una persona que construye una o dos casas de hormigón, algún edificio chico de 3 pisos y don de también tiene una disponibilidad de recursos más limitada”, explica Felipe Carrasco, gerente de componentes y tableros de la firma alemana.
La gran ventaja que ofrece este sis tema en comparación con los de placa fenólica, es su peso. “El panel más pesa do es de 24 kilos”, asegura el ejecutivo de PERI, con lo que se transforma en un “producto 100% manoportable”. Ade más, posee pocas piezas –las que son del mismo material de los paneles– y de acuerdo a Carrasco, “se trata de un sistema muy intuitivo, que cualquier operario puede montar”.
Además, el encofrado de plástico puede utilizarse para modular varias estructuras. En ese sentido, el panel estándar del sistema de moldaje de poli propileno de PERI es de 135 centímetros de alto, “entonces con dos paneles en altura, ya podrías hormigonar perfecta mente cualquier muro”, dice Carrasco. Asimismo, con esas dimensiones, el eje cutivo comenta que se pueden moldear fundaciones u otras estructuras, com portándose de la misma forma en que lo haría un moldaje de losa fenólica.
Para el caso del moldaje monolítico de aluminio, más allá de su peso porque también son manoportables, se trata de un sistema que busca ser “repetitivo y que poder utilizarse en muchas postu ras”, explica Matías Cárcamo, gerente general de Socomaq. El ejecutivo agre ga que si bien este tipo de moldajes se utilizan para hormigonar losas y muros con un solo encofrado, también pueden utilizarse para escaleras.
Al ser completamente metálicos, este tipo de moldajes cuenta con un reves timiento que provoca que “la lechada de ese hormigón termine de cubrir to das las microporosidades que tiene el aluminio y con eso, el moldaje ya queda curado”, comenta Paula Rissi.
Aditivos para concreto: Uso y interacción con el cemento
Los aditivos son productos químicos añadidos al mortero o concreto, para modificar una o más propiedades de las mezclas cementantes, son parte integral de mezclas debido a las diversas ventajas que proporcionan a sus propiedades de ingeniería en los estados fresco y endurecido. El incremento de dosis de los aditivos incrementa la fluidez de la mezcla, como lo ilustrado en la Figura 1 policarboxilato (Figura de GCP Applied Technologies)
Los lignosulfonatos fueron los primeros aditivos reductores de agua o plastificantes comerciales introducidos a principios de la década de 1960, el modo de repulsión de los aditivos lignosulfonato es por acción electrostática, como se ve en la Figura 3.
Figura 1: Efecto del incremento de dosis de aditivo policarboxilato en una pasta de material cementante.

Las diferentes moléculas de aditivos dispersantes causan diferentes efectos de dispersión y dependen del tipo de cemento. Los aditivos basados en policarboxilatos son más eficientes que los basados en naftaleno sulfonatos, que a su vez son más eficientes que los aditivos basados en lignosulfonatos, como se muestra en la Figura 2, en una representación esquemática de pruebas de revenimiento.
Figura 2: Representación esquemática de una prueba de revenimiento con diferentes agentes dispersantes (Romano et al, 2012)
Las partículas de cemento tienen una tendencia natural a aglomerarse cuando se mezclan con agua debido a su polaridad y la fuerza de atracción de Van Der Waals entre estas partículas de cemento. El agua queda atrapada entre ellos, lo que reduce la fluidez/ tensión de fluencia del hormigón (Uchikawa, 1997). Los aditivos confieren varios efectos al concreto, la cadena principal del policarboxilato se deposita / adsorbe en la superficie de las partículas del cemento, mientras que las cadenas laterales se extienden desde la superficie, separando las partículas lo que reduce las fuerzas interparticulares responsables por la tensión de fluencia del concreto o de la pasta. El aditivo causa una repulsión estérica entre las partículas de cemento, una barrera física junto con un efecto de fuerzas repulsivas que resulta en la dispersión de las partículas y libera agua para fluidizar la mezcla, como se demuestra en la Figura 3 (Jolicoeur y Simard, 1998). Los superplastificantes interactúan en la superficie o se combinan químicamente con las fases de cemento o los componentes de cemento hidratado (Ramachadran, 1995).
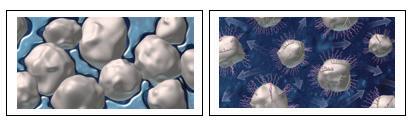
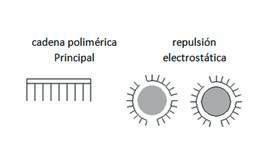
Figura 3. Ilustración del efecto de repulsión electrostática del lignosulfonato
Las investigaciones realizadas a principios de la década de 1960 en Japón y Alemania llevaron al desarrollo de los superplastificantes, que pueden proporcionar una gran reducción de agua (hasta un 40%) o gran fluidez al concreto (baja tensión de fluencia y baja viscosidad plástica). Los condensados de formaldehído-sulfonatos de naftaleno (NSFC) y melamina (MSFC) fueron los primeros tipos de aditivos superplastificantes, y resultaron en una mejora importante en la durabilidad del concreto por haber permitido la producción y el lanzamiento de concretos con baja relación agua / cemento menor que 0,40). Tales tecnologías fueron adoptadas por la industria del concreto con aceptación relativamente alta.
(a) (b)
Figura 4 - Monómero de la melamina sulfonato (a) y del naftaleno sulfonato (b) (Rixan,1999)
A finales de la década de 1980, una nueva familia de superplastificantes a base de poliéteres de policarboxilato-poliéteres (PCE) fue desarrollada en Japón. A partir de la década de 1990, los policarboxilatos-poliéteres se convirtieron en una importante tecnología de superplastificantes, a menudo sustituyendo el NSFC y el MSFC en muchas aplicaciones. La estructura química genérica de los PCEs se muestra en la Figura 5.
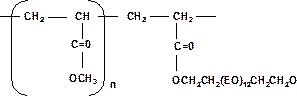
SOMOS LO QUE NECESITAS

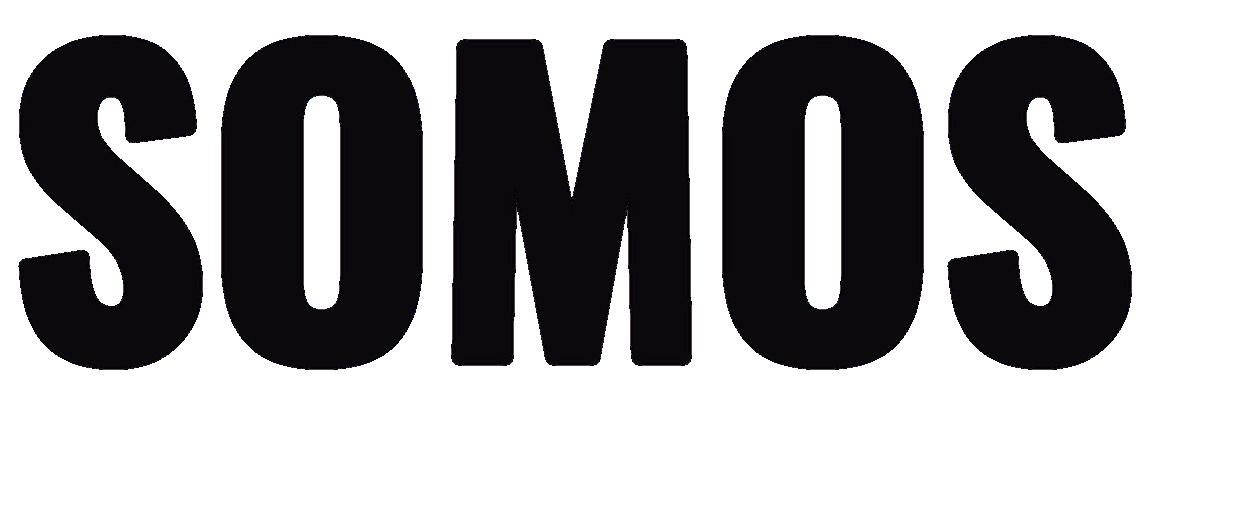
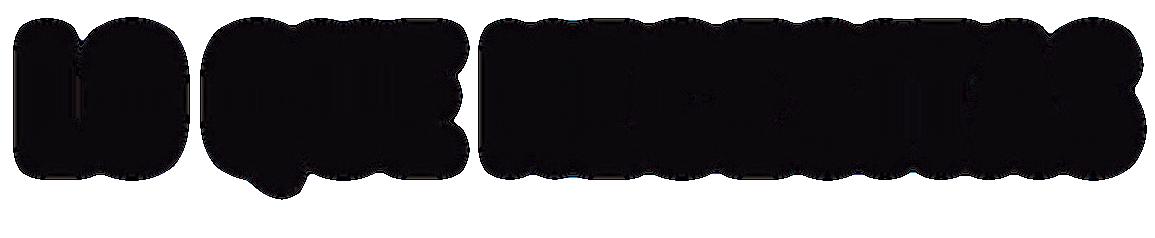


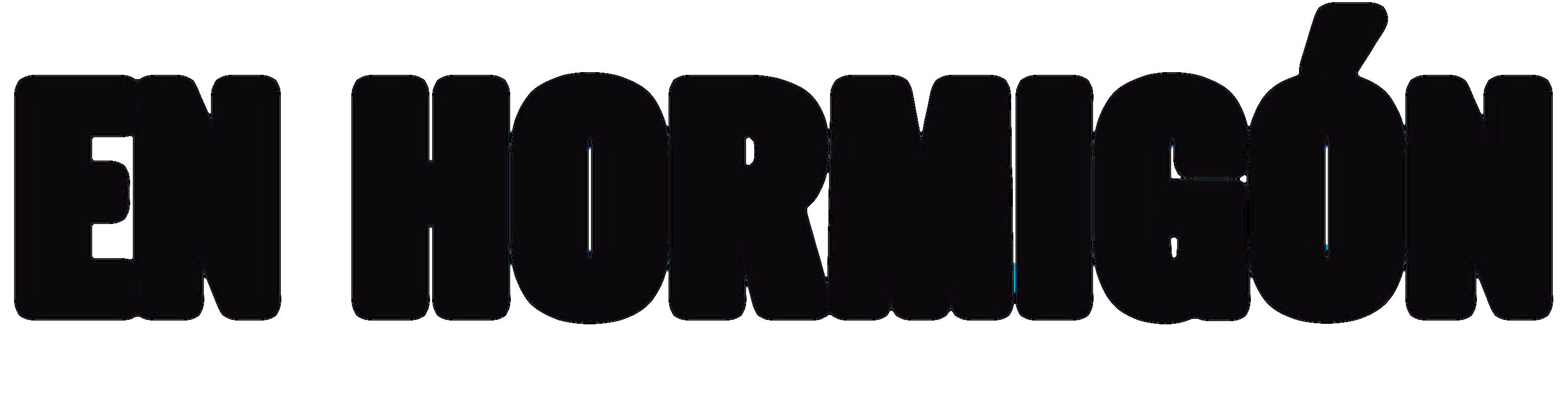



PROFESIONALES EN HORMIGÓN
PROFESIONALES EN HORMIGÓN



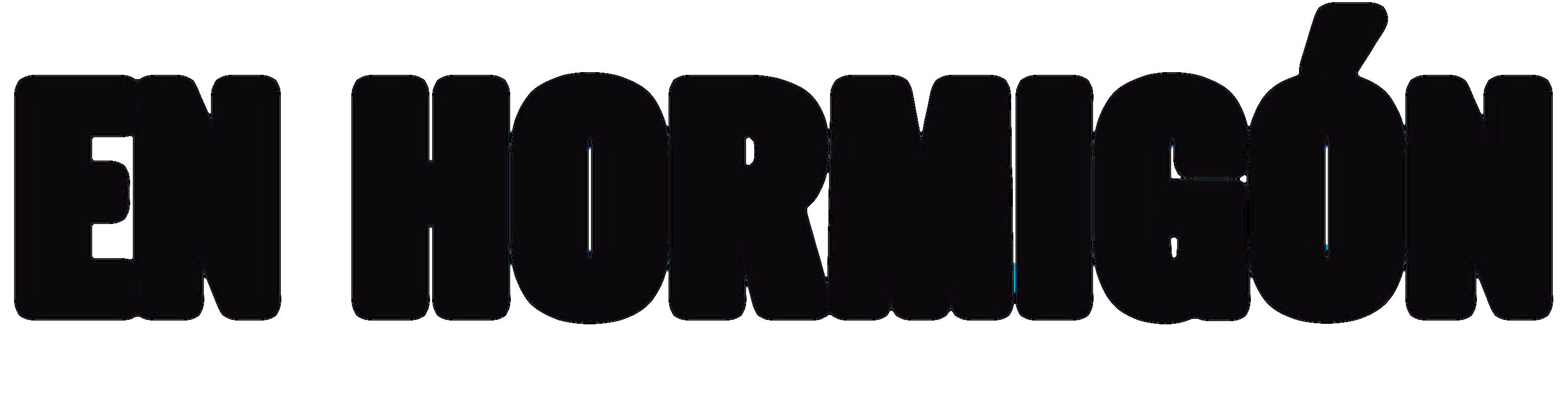
