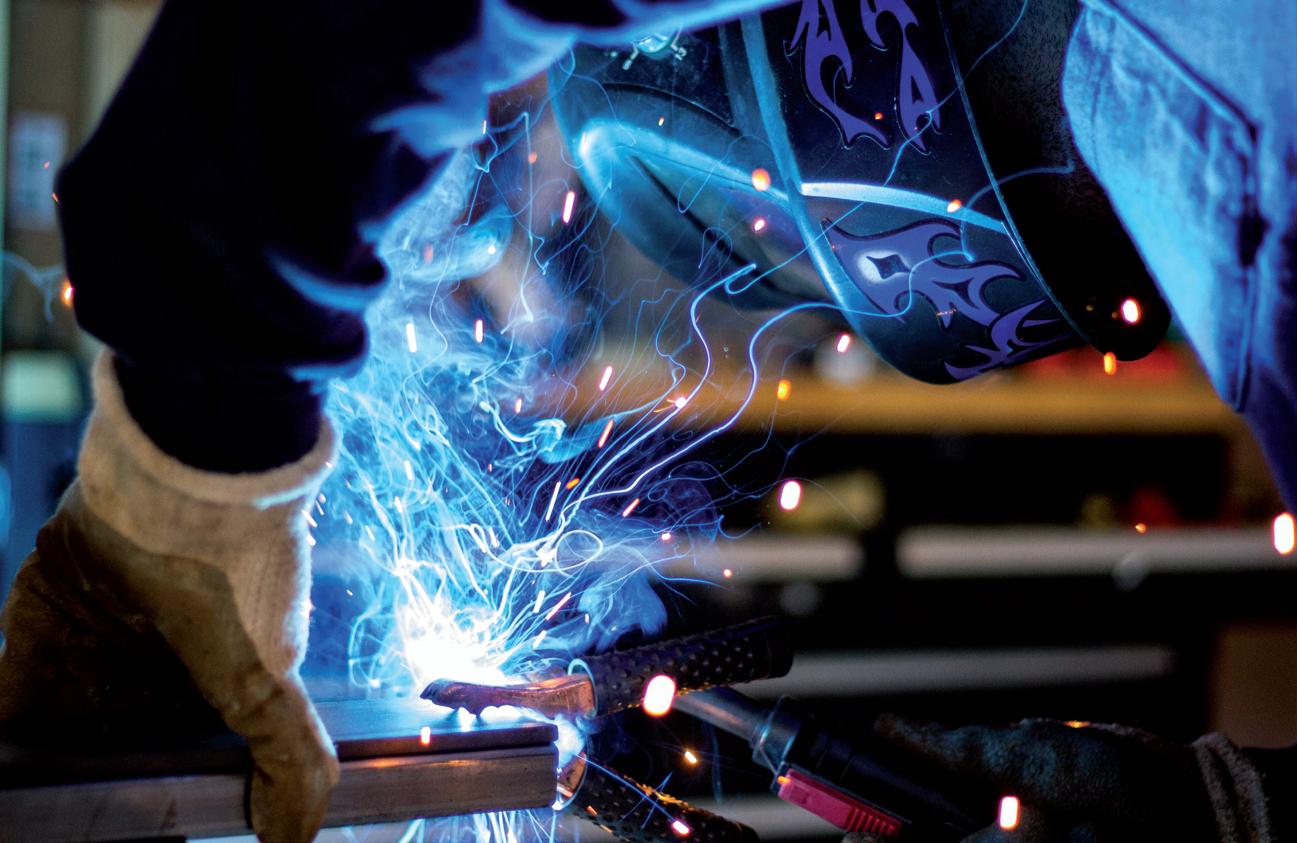
4 minute read
LA STARTUP DELLA FABBRICA INTELLIGENTE DIVENTA GRANDE
Miraitek4.0 compie cinque anni ed è ormai una realtà consolidata nell’ambito dell’Industria 4.0. Un progetto visionario ma allo stesso tempo molto concreto, che ha già superato gli obiettivi iniziali.
Ha compiuto cinque anni da poco, ma nonostante la giovane età è ormai parte del panorama dell’innovazione del manifatturiero. Fondata nel 2018 come spin-off del Politecnico di Milano, Miraitek4.0 ha l’obiettivo di integrare soluzioni di Industrial IoT (Internet of Things industriale) per la digitalizzazione della fabbrica. “Lo spirito era ed è ancora oggi quello di mettere insieme intelligenze che arrivano da mondi diversi, come università, ricerca, industria, innovazione, con un approccio non da informatici ma da utenti”, dice Marco Taisch, cofondatore di Miraitek4.0, “mettendoli poi in comunicazione e cooperazione con altri soggetti imprenditoriali (come ad esempio Cosberg) che consentissero di avere in casa una buona palestra in cui allenarsi. La formula si è rivelata vincente, perché ha creato valore per tutti e sta aiutando molte fabbriche a consumare meno risorse e a essere quindi più sostenibili”. Nella pratica, Miraitek4.0 realizza progetti, consulenze e attività di assessment, e integra una suite di servizi confezionati base alle esigenze del cliente, il quale viene supportato lungo tutto il processo di digitalizzazione. La piattaforma software di Industrial IoT sviluppata fornisce tutte le informazioni utili per la gestione della fabbrica: dal semplice monitoraggio dei flussi al dettaglio sui consumi energetici, fino alla pianificazione della manutenzione e alla gestione della qualità. La società si pone, quindi, come partner del futuro per le imprese, sviluppando soluzioni 4.0 che consentono di raccogliere e analizzare i dati, così da ottimizzare la produzione e ridurre eventuali inefficienze e criticità.
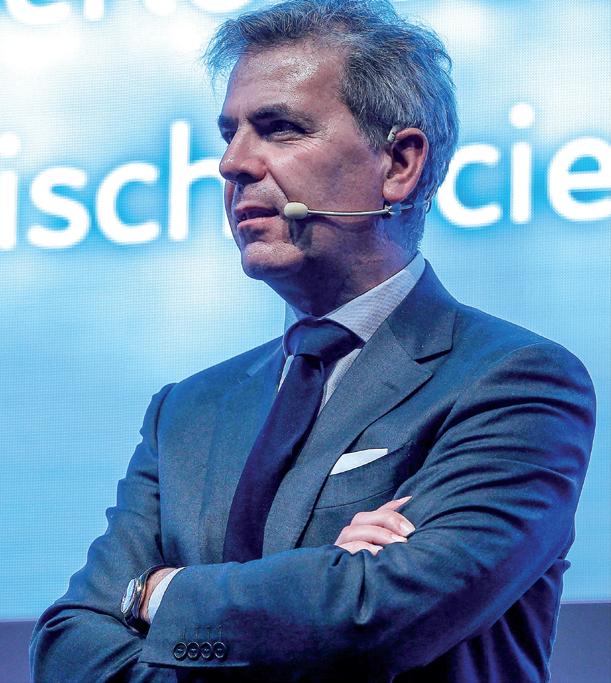
“Lo scorso anno abbiamo chiuso con un fatturato di 770mila euro”, prosegue Taisch, “un risultato che va oltre il budget previsto. Abbiamo operato soprattutto su due mercati. Il primo è quello dei produttori di macchine (beni strumentali), come ad esempio Cavanna, per i quali il nostro ruolo è duplice: non solo fornire la piattaforma IoT ma supportarli nel percorso verso la servitizzazione. E poi c’è il secondo mercato, quello delle fabbriche che possiedono macchine da collegare. Al nostro interno convivono le due anime IT e OT; grazie al connubio di questi due mondi aiutiamo i nostri clienti a fare un salto in termini di crescita, per cui l’IoT diventa l’abili-
Vantaggi E Rischi Della Digitalizzazione
Sensori, reti wireless, oggetti connessi, robotica, Automatic Guided Vehicle (Agv), stampa 3D, software per la gestione della produzione e delle attività di magazzino, per la simulazione di modelli e la progettazione (digital twin), per l’analisi dei dati e per l’automazione basata su intelligenza artificiale, senza dimenticare le soluzioni di cybersicurezza specifiche per il settore: sono alcune delle tecnologie qualificanti della cosiddetta “industria 4.0”. Secondo le stime di MarketsandMarkets Research, il mercato mondiale dei prodotti e servizi per la manifattura smart nel 2020 valeva 97,6 miliardi di dollari e, con un tasso composto di crescita annuale del 18,5%, arriverà a movimentare 228,3 miliardi nel 2027. Parte della spinta arriverà dalle tecnologie disponibili, in particolare quelle per l’analisi dei dati in tempo reale e per la manutenzione predittiva. Un ruolo propulsore spetta anche ai fondi pubblici che, a livello nazionale e internazionale, saranno messi in campo per favorire l’attività di ricerca e sviluppo, la nascita di startup e l’adozione del modello 4.0 da parte delle imprese industriali. Paesi come il Regno Unito, gli Stati Uniti e il Canada, in particolare, hanno stanziato investimenti per spingere il settore della stampa 3D. MarketsandMarkets sottolinea che, in linea di massima, servono budget importanti e competenze evolute per adottare reti 5G private, veicoli Agv, macchinari dotati di sensori e altre tecnologie per la digitalizzazione delle industrie. Gli ambiti coinvolti in questa trasformazione spaziano dall’automobilistico all’agroalimentare, dall’industria chimica alla meccanica, dal settore dell’oil&gas al farmaceutico, senza dimenticare edilizia, produzione di semiconduttori, aerospaziale e difesa. Tra le diverse tecnologie che compongono il mercato, cresceranno oltre la media le soluzioni per i digital twin, che permettono di creare simulazioni tridimensionali e interattive per attività di progettazione, collaudo, manutenzione e altro ancora. Su base geografica, invece, la crescita maggiore nel medio periodo sarà osservata nella regione Asia Pacifico. La digitalizzazione dei processi industriali comporta notevoli vantaggi, a partire dalla possibilità di tracciare, prevedere, correggere e potenziare le attività di fabbrica, interlogistica e logistica. Dall’analisi dei dati, come noto, possono derivare insight utilizzabili per scopi immediati e tattici (tagliare i costi, ridurre i tempi di produzione) o strategici (riposizionamento, apertura di nuovi mercati). Tuttavia è altrettanto risaputo che il passaggio al 4.0 comporti anche un innalzamento dei rischi: in quanto “connessi” e digitalizzati, i sistemi sono potenzialmente esposti ad attacchi e incidenti informatici. Hackeraggi, furto di dati, ricatti ransomware e DDoS (Distributed Denial-of-Service) sono alcune delle possibilità e in questi anni in prima pagina non sono mancati casi eclatanti di disservizi e blocchi, conseguenti sia ad attività di cybercrimine a scopo di lucro sia ad azioni di cyberguerrilla politicamente connotate.
tatore per cambiare il modello di business e andare a intercettare fonti di fatturato che altrimenti non sarebbero alla portata. In pratica le aiutiamo a trasformarsi, un’attività che è nel Dna di Miraitek. Se proprio vogliamo trovare un’altra chiave di lettura, Miraitek è nata perché ci siamo accorti che nel processo di trasformazione digitale mancavano i dati”. Mirai4Machine, in particolare, è una soluzione software IoT che si rivolge alle aziende manifatturiere e ai costruttori di macchinari industriali e che permette di monitorare in tempo reale e da remoto le pre- stazioni produttive dei sistemi, dei reparti e degli stabilimenti, inclusi guasti, allarmi e fermi macchina.
La piattaforma consente inoltre di analizzare i dati storici per ottenere gli indici di funzionamento e migliorare i processi di produzione.
Ad oggi la società annovera 180 installazioni in 14 Paesi del mondo (tra cui una in Australia, dove le operazioni sono state condotte sempre da remoto), più di 130 impianti industriali connessi, 500 stazioni e 55.000 data point. “Di fatto oggi la piattaforma è un piccolo Mes”, conclude Taisch (l’acronimo sta per Manufacturing
Execution System), “anche perché stiamo allargando le caratteristiche tecnologiche del nostro prodotto. Tra poco brevetteremo un sistema di raccolta dati sull’edge, proseguendo quindi nello sviluppo del prodotto. Dal un punto di vista delle soluzioni, un altro tema importante è quello della sostenibilità, della circolarità e della riduzione dei consumi energetici: stiamo aiutando i nostri i clienti a diventare più sostenibili, sempre con un approccio data-centrico, cioè con il monitoraggio efficace di quello che succede nella fabbrica”.
Emilio Mango