
16 minute read
TOPIC VEILIGHEID Veiligheid begint op de werkvloer
Veilig werken begint op de werkvloer
Veel van de geldende veiligheidsprotocollen, procedures en voorschriften zijn van bovenaf opgelegd. Dat wil niet altijd zeggen dat ze allemaal even e ectief op de werkvloer belanden. Daarom draait branchevereniging voor de industriële dienstverleners VOMI de zaken eens om en kijkt bottom-up hoe werknemers ervoor zorgen dat ze hun werk veilig uitvoeren.
Advertisement
David van Baarle
Het succes van de Nederlandse procesindustrie is zeker niet alleen te danken aan de asset owners. Want al die installaties zouden niet kunnen draaien zonder de inzet van talloze dienstverleners die de assets onderhouden, testen, reviseren, uitbouwen, vernieuwen of bijvoorbeeld aansluiten. Het zal dan ook geen verbazing wekken dat die dienstverleners, ook wel contractors genoemd, op hun eigen specialistische vlak zeer veel kennis en kunde in huis hebben. In de continue zoektocht naar effi ciency-verbetering spelen contractors een steeds belangrijkere rol. Want waarom zou een asset owner de kennis van die hands-on specialisten niet inzetten om assets te optimaliseren, procedures te verbeteren en de veiligheid te verhogen? Dat is precies de gedachtegang van branchevereniging VOMI. VOMI-directeur Peter Hecker en de kersverse voorzitter Ivo van Vliet willen de onontgonnen kennis van de contractors inzetten om de industrie effi ciënter en veiliger te maken.
Kleine incidenten
De verwevenheid tussen industrie en aannemers is groot, stelt Hecker. ‘Sommige werknemers zitten jaren op dezelfde industriële site en doen in betrokkenheid en ervaring niet onder voor de eigen werknemers van een bedrijf. Anderen switchen tussen verschillende sites en nemen hun ervaring bij de ene opdrachtgever mee naar de volgende. Inmiddels vertegenwoordigt VOMI zo’n 32 van dit soort bedrijven. Je kunt je bijna niet voorstellen hoeveel kennis we daarmee in huis hebben over professionele dienstverlening, optimalisering en veiligheid. Daarnaast weten onze leden alles van de arbeidsmarkt, hoe je mensen opleidt, traint, boeit en bindt. We willen die kennis inzetten om industriële projecten te optimaliseren. We deelden al ons optimalisatiemodel met opdrachtgevers via een handboek, masterclass en een infographic over de negen misvattingen van eff ectiviteit.’ In diezelfde gedachtegang, pakte de branchevereniging het thema veiligheid op. Want hoewel de procesindustrie de afgelopen jaren minder ongelukken registreerde, heeft de helft van de (bijna) ongelukken die nog wel plaatsvinden te maken met onderhoud. En die werkzaamheden worden vaak uitgevoerd door contractors. Van Vliet, die dagelijks leiding geeft aan Equans West Industrie, ziet dan ook een belangrijke verantwoordelijkheid voor de VOMI-achterban. ‘Gezien het aantal jaarlijkse werkuren op chemische sites, is de veiligheidsscore van de Nederlandse procesindustrie best goed. Maar dat wil niet zeggen dat het niet beter kan, want we zien toch nog dagelijks dingen niet goed gaan. Ook kleine incidenten zijn een teken dat er iets mis is met de procedures, het kennisniveau of het veiligheidsbewustzijn van mensen. Gelukkig hebben we professionele technici in huis die escalatie in de regel kunnen voorkomen, maar liever zetten ze die kennis in om incidenten voor te zijn.’
Bottom-up
Inmiddels zijn de goede intenties omgezet in een offi ciële safety deal met de naam VOMI Veilig. De branchevereniging kreeg een subsidiebedrag van RVO voor de eerste verkenning van een veiligheidscampagne. Met als doel de veiligheidscultuur en ketenverantwoordelijkheid te vergroten. Uiteindelijk moet dat leiden tot veilige bedrijventerreinen en industrieclusters. Dat daarmee het algemene kennisniveau van de industrie stijgt, is een mooie bijvangst. Ook hier geldt weer dat VOMI de kennis van de werkvloer wil gebruiken om het veiligheidsbewustzijn en de veiligheidscultuur te vergroten. Hecker: ‘Veel van de geldende veiligheidsprotocollen, procedures en voorschriften zijn van bovenaf opgelegd. Dat wil niet altijd zeggen dat ze allemaal even eff ectief op de werkvloer belanden. Daarom wilden we de zaken eens omdraaien en bottom-up kijken hoe werknemers
VOMI wil de kennis van de werkvloer gebruiken om het veiligheidsbewustzijn en de veiligheidscultuur te vergroten.
ervoor zorgen dat ze hun werk veilig uitvoeren. Hoe bereiden ze zich voor, hoe overleggen ze met hun collega’s en hoe corrigeren ze collega’s of wellicht opdrachtgevers? Durven mensen wel gevaarlijk gedrag te melden of het werk stil te leggen als ze denken dat het niet veilig is? Allemaal vragen die we graag aan de werknemers zelf willen stellen.’ Om de antwoorden boven tafel te krijgen, start de branchevereniging het project met twintig pilots bij
opdrachtgevers als Dow, Shell, Huntsman, BASF en Vopak. En met als contractors onder meer Equans, Kaefer, Van der Panne, Mourik, Mammoet, TMS, Travhydro, Brand, Bilfinger, Croonwolter&Dros, Visser& Smit Hanab, Verwater en Bukom. ‘We vormen kleine groepjes van vijf tot tien man sterk die met een veiligheidscoach vrijuit kunnen spreken over datgene wat ze in de praktijk tegenkomen op het gebied van veiligheid. Daarna breiden we de groep uit met directieleden van de contractor om vervolgens ook de opdrachtgever of asset owner bij de discussie te betrekken.’
IVO VAN VLIET VOORZITTER VOMI
Gezond verstand
Uiteindelijk moet uit die gesprekken de meest veilige werkwijze wordt vastgelegd op de betreffende locatie. Vervolgens worden de ervaringen generiek gemaakt en gedeeld met de sector, waar ook weer de samenwerking van de contractor met de opdrachtgever tot uiting komt. Bij voorkeur is de aanpak via VOMI Veilig complementair aan het veiligheidssysteem van de opdrachtgever. Van Vliet: ‘Bij een grote brand of explosie trekt de industrie daar op sectorniveau lering uit. Die aanpak leidde ertoe dat zich steeds minder van dat soort grote incidenten voordoen. Dat wil niet zeggen dat je dan klaar bent, maar dat de aandacht naar de kleinere incidenten verschuift. Want ook daarvan leren we.’ De meeste grote incidenten zijn een gevolg van een reeks kleinere incidenten, miscommunicatie en misperceptie. ‘Willen we de ketenveiligheid verhogen, dan moeten we juist die kleine incidenten en near misses bespreekbaar maken. Heel vaak zien mensen een ongeluk aankomen en kunnen ze nog op tijd ingrijpen. Of, wat helaas ook gebeurt, houden ze kleine incidenten onder de pet. Daar kunnen valide argumenten voor gelden. Wellicht voelt men tijdsdruk, zijn ze bang voor gezichtsverlies of voor een reprimande van de opdrachtgever.

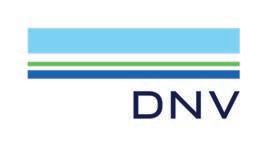
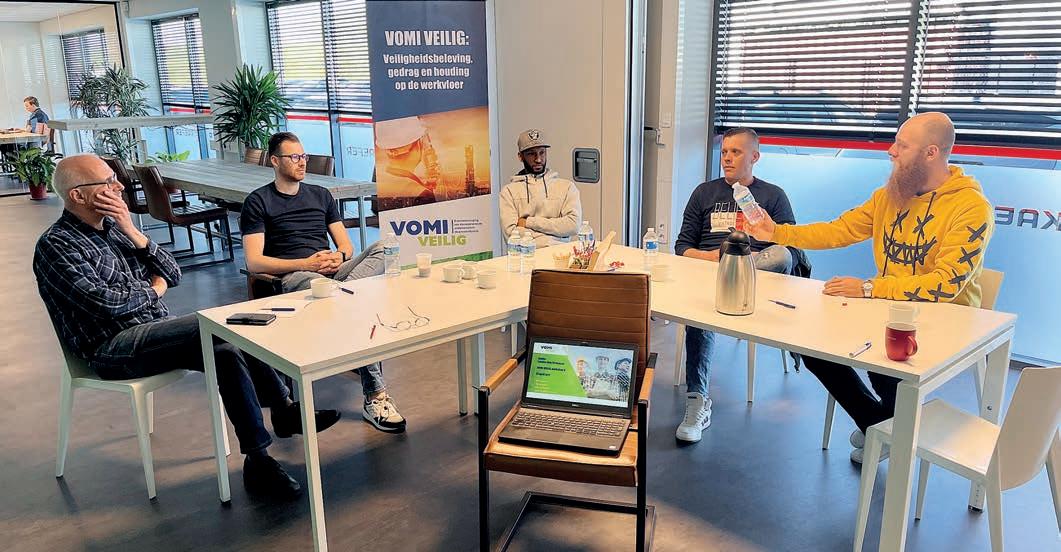
Kleine groepjes van vijf tot tien man kunnen met een veiligheidscoach vrijuit spreken over datgene wat ze in de praktijk tegenkomen op het gebied van veiligheid.
En als er inderdaad tijdsdruk is, zullen werknemers ook niet de tijd nemen om met collega’s de dag te evalueren en na te gaan of ze een project wel echt veilig hebben aangepakt. Toch is juist dat nodig.’ Om veiligheid echt te kunnen borgen in de hele keten, moet de werkvloer de dialoog durven aangaan met collega’s die het werk uitvoeren, maar ook met de opdrachtgever, stelt Van Vliet. ‘Uiteindelijk gaat veiligheid ook om vertrouwen. Vertrouwt een opdrachtgever dat een dienstverlener er alles aan doet om zijn werk zo efficiënt en veilig mogelijk uit te voeren? Veel procedures zijn gestuurd door controle en sluiten daardoor niet altijd aan op de dagelijkse praktijk. Het kan best zo zijn dat een werknemer de procedures negeert en toch veilig werkt. Misschien werkt diegene zelfs wel veel veiliger. Leg zijn werkwijze dan vast en gebruik het als best practice voor vergelijkbare projecten. Daarbij is het belangrijker dat iemand weet waarom hij bepaalde voorzorgsmaatregelen moet nemen, dan dat het hem wordt opgelegd. Het gevaar bij een overvloed aan regels en procedures is dat men het gezond verstand negeert en alleen nog maar bezig is met afvinklijstjes.’
Tijdsdruk
Inmiddels zijn de eerste gesprekken geweest en Hecker ziet dat de aanpak nu al nieuwe inzichten oplevert. ‘We kozen er bewust voor de gesprekken on site te houden. Daar voeren de technici tenslotte hun werk uit. De coaches bespreken een aantal kernthema’s en gebruiken diverse werkvormen om boven water te krijgen wat er echt leeft binnen de groepen. We zien enthousiaste reacties en mensen zijn positief verrast dat hun inbreng serieus wordt genomen. Wat als eerste opvalt, is dat vooral tijdsdruk een issue is. Met name doordat vertragingen vaak ver in de keten doorlopen. Dan wordt het zeer lastig voor werknemers om de afweging te maken tussen tempo maken en veilig werken.’ ‘Ook communicatie horen we vaak terugkomen als aandachtspunt. Het aantal nationaliteiten op de sites is alleen maar toegenomen waardoor men elkaar minder goed verstaat en begrijpt. Dat heeft niet alleen met taal te maken, maar ook met cultuur. In Nederland durven we de baas vaak wel van
weerwoord te dienen, maar in veel culturen is dat niet gepast.’ Het succes van de pilots laat zien dat VOMI voorziet in een behoefte bij de werknemers van de contractors om hun bijdrage te leveren aan de veiligheidscultuur van hun opdrachtgevers. Hecker verwacht daarom de methodiek te continueren. ‘We zullen de resultaten van de pilots met de opdrachtgevers én contractors delen om ervan te leren. Maar met veiligheid ben je nooit klaar. Dit moet het startpunt zijn van een methodiek die de kennis en de veiligheidsbeleving van de werkvloer ontsluit en vertaalt naar een veilige en plezierige werkomgeving. We stellen de VOMI Veilig systematiek na het project ter beschikking aan de sector. We willen de evaluatie van alle ervaringen dan graag delen tijdens een slotmanifestatie aan het einde van het jaar.’
PETER HECKER DIRECTEUR VOMI
Robotica maakt steigerbouw effi ciënter en veiliger
Er is in de industrie een groeiend tekort aan technisch personeel. Bovendien kiezen maar weinig technici voor het vak steigerbouw en is het werk vaak zwaar en repetitief. Daarom heeft start-up Kewazo de Liftbot ontwikkeld, een robotoplossing voor de steigerbouw. ‘Met onze robot besparen industriële dienstverleners als Altrad Services of Bilfi nger gemiddeld 44 procent aan manuren’, stelt Jonas Lerchenmüller.
Kewazo wil met geavanceerde technologie veiligere, effi ciëntere en kosteneffectieve werkplekken creëren. ‘Dit doen we momenteel onder meer met onze Liftbot’, vertelt Jonas Lerchenmüller, business development manager van Kewazo. Liftbot is een compacte robot die in twintig minuten op elke standaard modulaire steiger kan worden geïnstalleerd. Het compacte formaat en de snelle installatie maken de robot geschikt voor een breed scala aan steigerprojecten in de bouw, industriële installaties en scheepswerven, terwij l hij ook eenvoudig over de locatie kan worden verplaatst naar waar hij nodig is. ‘Onze Liftbot transporteert nu automatisch steigerdelen bij projecten zoals tanks of kolommen die traditioneel volledig manueel worden gebouwd. De robot werkt daarbij draadloos en heeft een batterij capaciteit die voldoende is om een hele dag lang steigerelementen op hoogte te brengen. Tot honderd kilogram per loop.’
Veilige materiaalstroom
Honderd kilogram laadvermogen lij kt in eerste instantie weinig, maar het levert meer voordelen op dan je op het eerste gezicht zou denken, vertelt Lerchenmüller. ‘Meer dan vij ftig proefprojecten hebben bewezen dat met toepassing van Liftbot bij na elk soort project met slechts drie steigerbouwers kan worden uitgevoerd: twee medewerkers bovenin en één beneden. Deze laatste laadt de steigerdelen in de robot. Onetouchtechnologie zendt de robot automatisch naar zij n bestemming met een snelheid van 42 meter per minuut. Zo kan het systeem in twee minuten worden volgeladen en op hoogte worden gebracht. Twee steigerbouwers halen het materiaal eruit waarna ze het meteen kunnen assembleren.’ Ondertussen keert de Liftbot automatisch terug naar beneden om weer te worden volgeladen. Dit proces leidt tot een constante materiaalstroom. Er is nooit te veel materiaal in één keer bovenin ter plaatse zodat de steigerbouwers het overzicht goed kunnen bewaren. ‘Daarnaast verlaagt het kleine aantal benodigde werknemers de kans op ongevallen, terwij l de robot ook de ergonomie van de steigerbouwers
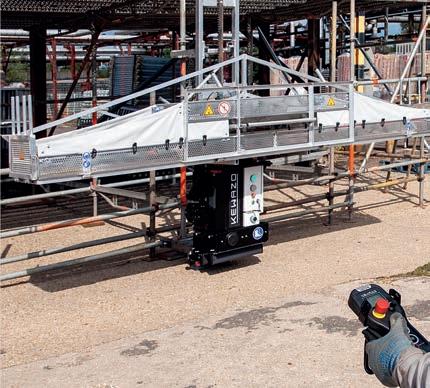

Kewazo is in 2018 opgericht met de visie om bouwactiviteiten op locatie te digitaliseren met robotica en data-analyse. Het bedrij f combineert kennis en ervaring op het gebied van constructierobotica, civiele techniek, programmeren en business. Tegenwoordig is Kewazo een van de toonaangevende start-ups voor bouwrobotica ter wereld, met meer dan twintig medewerkers. Kij k voor meer informatie op www.kewazo.com
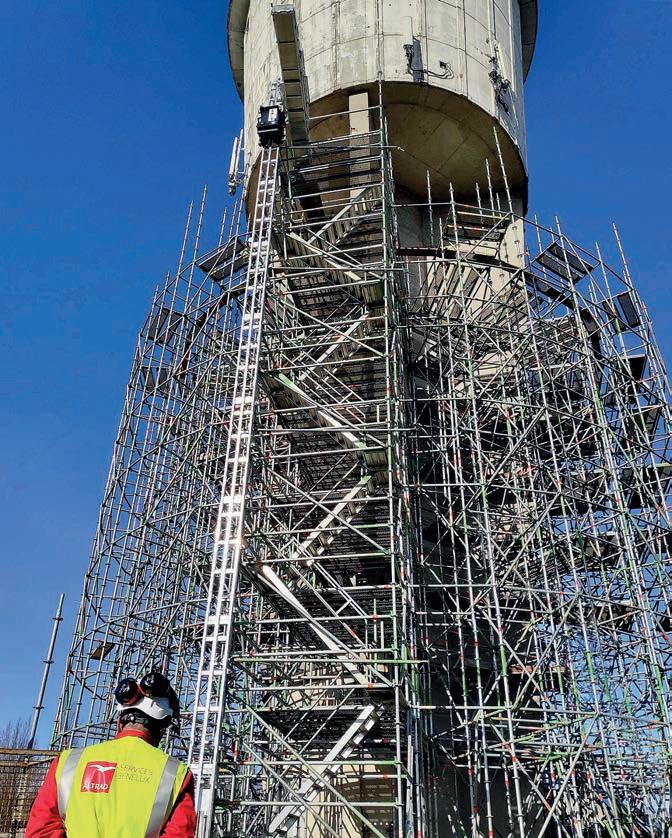
Het compacte formaat en de snelle installatie maken de robot geschikt voor een breed scala aan steigerprojecten.
verbetert. De fysieke belasting voor steigerbouwers is enorm. Ze vervoeren maar liefst vijf ton steigermateriaal per dag wat op korte of lange termijn kan leiden tot schade aan hun lichaam. De Liftbot kan dit voorkomen’, stelt Lerchenmüller. ‘Kortom, dankzij de robot neemt de efficiëntie en veiligheid toe.’
Benelux
In eerste instantie richtte Kewazo zich op de Duitse markt, maar inmiddels heeft het ook voet aan de grond gezet in de Benelux. ‘Midden 2021 voerden we bij industrieel dienstverlener Altrad een pilot uit op een locatie in België, waar het systeem uitvoerig werd getest. Onmiddellijk werd de meerwaarde duidelijk ten opzichte van de traditionele steigerbouwoplossingen. Na deze pilot heeft het bedrijf besloten om een exemplaar aan te schaffen. Afgelopen februari werd de Liftbot in een lopend project geïntegreerd. Onze robot ontlast de steigerbouwers waardoor ze zich meer kunnen focussen op het bedenken van constructies en planningen.’ Ondertussen ontwikkelt Kewazo weer nieuwe concepten om veiligere, efficiëntere en kosteneffectieve werkplekken te creëren. ‘Zo ontwikkelen we momenteel een gamification concept waarbij teams met elkaar kunnen vergelijken hoeveel elementen ze hoe snel
hebben verplaatst. De best presterende teams krijgen prijzen, in de vorm van cadeau of waardebonnen. We zien dit als een kans om motiverende prikkels te geven voor uitstekende prestaties. Dit alles terwijl de veiligheid gewaarborgd blijft.’
Dataplatform
De hardware van de Liftbot is slechts één aspect dat werd ontwikkeld. Een tweede is het data analytics platform Kewazo Onsite. ‘Liftbot verzamelt operationele gegevens zoals de actuele steigerhoogte en de getransporteerde tonnen via een array van sensoren. Deze gegevens worden in realteam geanalyseerd en weergegeven op Kewazo Onsite en bieden volledige transparantie van de activiteiten op de bouwplaats voor bouwmanagers en bedrijfseigenaren. Ook is een vergelijking met andere projecten op andere locaties mogelijk.
Hierdoor is geautomatiseerde projectplanning mogelijk en wordt de kostenefficiëntie inzichtelijk.’ Een derde pijler die de startup biedt, is Kewazo Care, een pakket van training, engineering services en projectondersteuning. Dit omvat jaarlijkse en noodonderhoudsdiensten voor Liftbot, zoals klantondersteuning bij specifieke projecten om de meest efficiënte prestaties te garanderen
Jonas Lerchenmüller business development manager Kewazo
Als volwaardige speler werkt Bang&Clean al vele jaren wereldwijd met haar PressureWave systeem in onder andere de afvalbranche en grote energiecentrales. De technologie kan echter op veel meer plekken worden ingezet voor veilige reiniging.
Afvalenergiecentrales, biomassacentrales en gasgestookte installaties spelen een belangrijke rol in de energietransitie. De circulaire energiebronnen kennen echter één groot nadeel; ze zijn gevoelig voor anorganische vervuilingen. Deze hechten zich aan de bundelpakketten die de warmte van de ovens moeten omzetten in stoom. Daardoor neemt het rendement dermate af dat de energiebedrijven hun centrales regelmatig stilleggen om de vervuiling te verwijderen. Dat moest anders, vond een afvalverbrander in regio Rijnmond jaren geleden. De speurtocht naar een veilig, effectiever en kostenbesparend alternatief eindigde bij het Zwitserse Bang&Clean Technologies. ‘Normaal gesproken moet zo’n oven handmatig worden gereinigd’, zegt quality manager Raoul Hopman van Bang & Clean. ‘Dat betekent een oven uitzetten, laten afkoelen en stellingen bouwen om vervolgens mensen handmatig de reiniging uit te laten voeren. Dit is niet alleen onveilig, maar levert ook productieverlies op.’ Het gepatenteerde reinigingssysteem van Bang&Clean verwijdert met druk en geluidsgolven blokkades en aangehechte vervuiling in onder meer verbrandingsovens terwijl deze in bedrijf zijn. Dus zonder productieuitval, tijdverlies en kosten voor af en opstoken. Het bedrijf garandeert hierdoor een hogere beschikbaarheid van de installatie en daarmee een directe kostenbesparing.

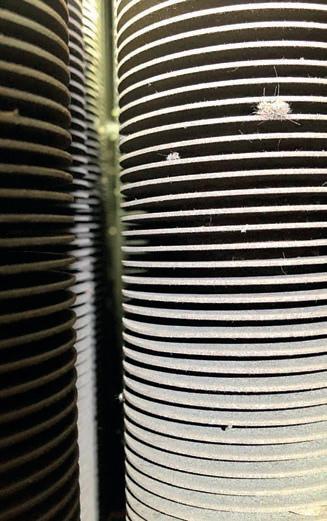
Katalysator
Managing director Jerry Goud vertelt dat Bang&Clean Technologies anderhalf jaar geleden besloot de licentie in eigen beheer te nemen. Zijn team bedient het grootste deel van de biomassa, afvalenergie en gascentrales in de Benelux. ‘Als bedrijf zijn we jong, maar we hebben twintig jaar ervaring met deze techniek. In de afvalbranche zijn we dan ook al min of meer de standaard keuze geworden voor het verwijderen van anorganische vervuiling. We weten echter dat ook de petrochemische industrie kan profiteren van drukgolftechniek.’ Een mooi voorbeeld hiervan is de katalysatorwissel die het bedrijf ondersteunde in de reactor van een Italiaans chemiebedrijf. ‘De katalysator wordt daar op den duur zo hard dat mensen in speciale, gekoelde pakken moeten afdalen in de reactor om het
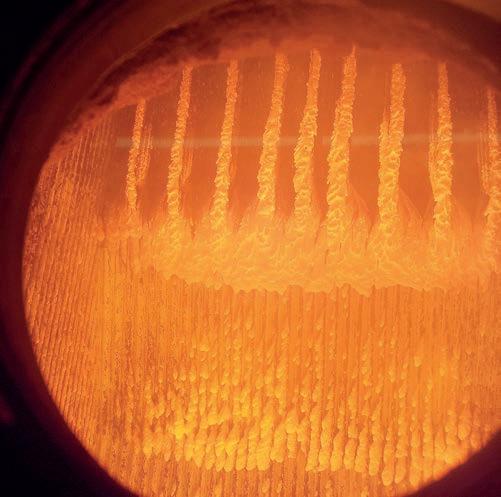
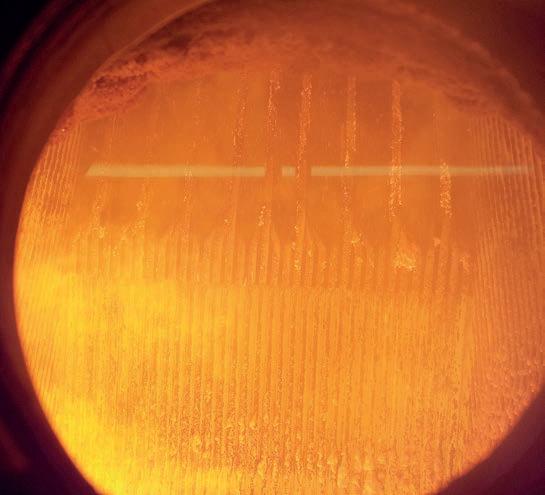
eruit te bikken. Ook daar lukte het om via gedoseerde detonaties het materiaal zo los te maken dat het er daarna vanzelf uitviel. Daarmee brachten we de wissel van veertien dagen handmatig werk terug naar drie dagen met onze PressureWave technologie. En dat terwijl de reactor inert werd gehouden met stikstof.’
Gasgestookte installaties
Ook gasgestookte installaties kunnen volgen Hopman profiteren van de efficiënte reinigingsmethode. ‘Gasgestookte installaties hebben nog wel eens last van corrosie, met name roestvorming tussen de vinnen, en vervuiling van zwavel. Daardoor kan de warmtegeleiding behoorlijk afnemen en levert de turbine een hogere tegendruk. Veel bedrijven denken er niet eens aan om dit probleem aan te pakken, maar de kosten van de ingreep zijn vele malen lager dan het verlies van de productie. Dat is zeker in deze tijden met hoge gasprijzen geen verkeerde investering.’
Jerry Goud managing director Bang&Clean Technologies
Veilig
Veiligheid speelt vanzelfsprekend een belangrijke rol in de industrie. PressureWave technologie voorkomt onveilige situaties door vuil veilig en tijdig te verwijderen. Goud: ‘Een verstopte efilter kan gevaarlijk zijn omdat het stof voor kortsluiting kan zorgen. Dit is relatief eenvoudig te voorkomen door het stof tijdig te verwijderen met een aantal detonaties.’ Natuurlijk kunnen bedrijven ook volledig handmatig reinigen, maar veel bedrijven willen liever zo weinig mogelijk mensen in besloten ruimtes laten werken, weet Goud. ‘Met deze drukgolftechniek verkort je de doorlooptijd van het handmatig reinigen en daarmee ook de belasting op de mens. Dat neemt natuurlijk niet weg dat je moet weten wat je doet. ‘Wie een gasmengsel wil laten detoneren in een werkende oven van 1.200 graden Celsius moet wel op de hoogte zijn van potentiële risico’s. Als de onderdruk in de installatie is weggevallen, kan je alsnog een gevaarlijke situatie krijgen. Onze experts weten niet alleen hoeveel drukgolven waar het beste resultaat opleveren, maar ook hoe ze dat veilig kunnen uitvoeren.’ Dat het bedrijf veilig werkt, blijkt uit de veiligheidsprijs die het won bij een van haar opdrachtgevers. ‘Ze waardeerden met name de manier waarop we met veiligheid omgaan. Je werkt toch vaak in het hart van een bedrijf, dus willen ze terecht weten wat de risico’s zijn en welke maatregelen we nemen om die te voorkomen. Die informatie delen we graag.’
De PressureWave reinigingsmethode is primair geschikt voor complexe installaties waarin producten worden verbrand en stoom wordt gewonnen. De druk en geluidsgolven verwijderen de rendement verlagende vervuiling in warmteoverdrachtkamers. TNO onderzocht het systeem op effectiviteit en ontwikkelde een berekeningsmethode waarmee de techniek heel nauwkeurig en veilig is af te stemmen op verschillende soorten installaties en omgevingen. Daardoor is de kans op schade uitgesloten, anders dan bij andere beschikbare technieken. Deze techniek wordt inmiddels wereldwijd toegepast en heeft nog nergens schade toegebracht aan installaties of personeel.