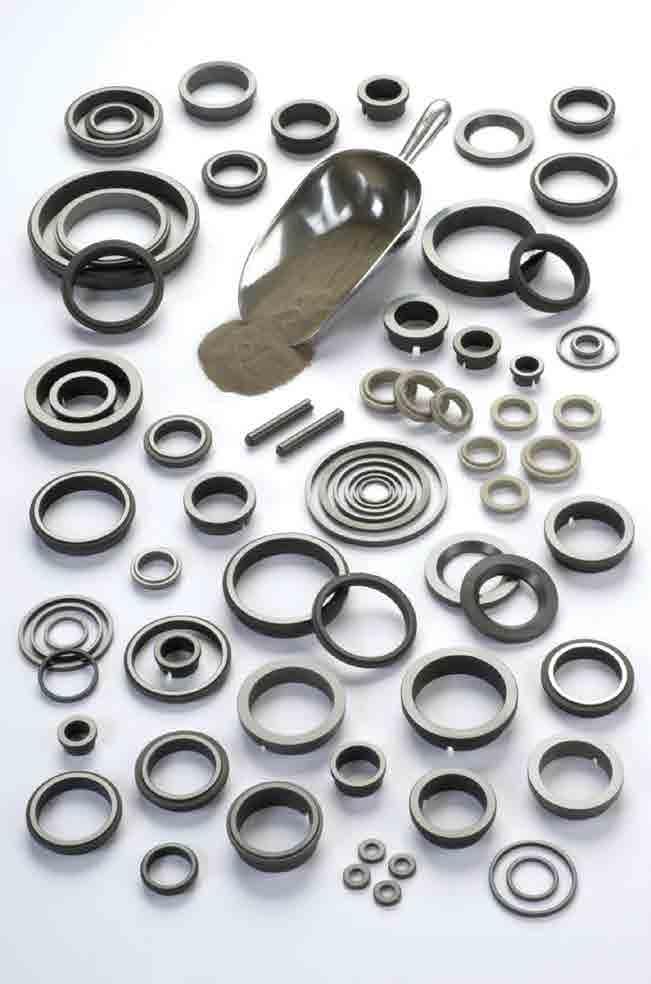
9 minute read
Controlling the power ETI Group
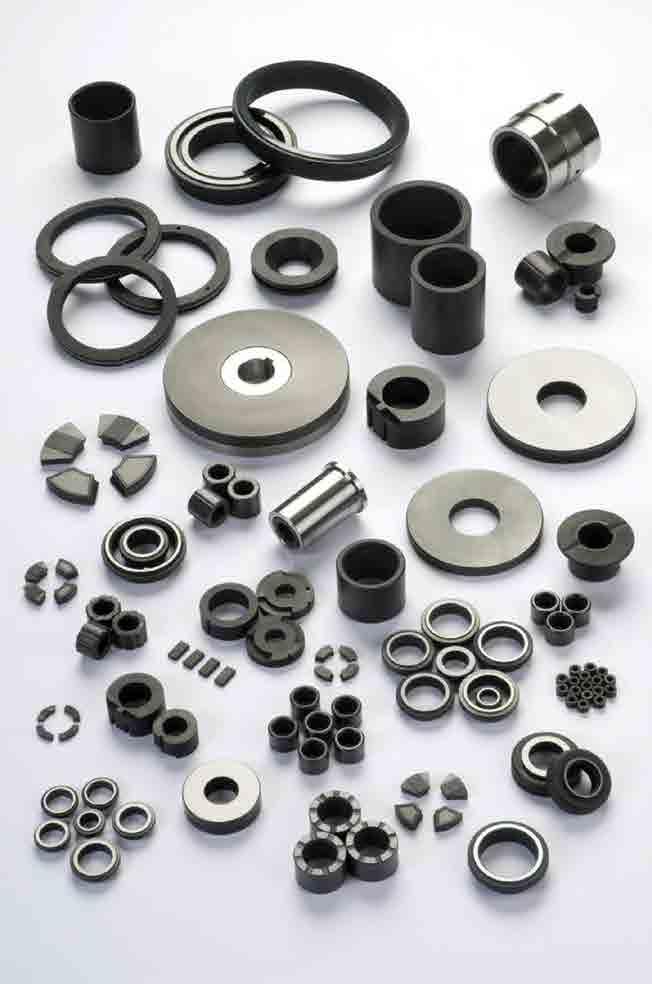
Eurocarbo SpA is based in the Teramo area, in the central Italian region of Abruzzo. Here the company manufactures carbon/ graphite components for mechanical and electrical applications. The range of products is composed of brushes for electrical engines for industrial and consumer purposes, as well as brushes for the automotive sector. Examples of applications using electric engines for consumer purposes include residential automated gates and lifts. In terms of mechanical applications the company produces graphite components for pumps of various types, for the mechanical, chemical and oil and gas industries, as well as for pumps for domestic use (as in the case of residential boilers) and for the food sector (such as those used for espresso coffee machines and for dairy and chocolate production). Products for mechanical applications include rings, bearings and machined carbon. The company holds all relevant certifications with regard to the food and water industries – including TIFQ, NSF and WRAS – as well as being ISO 9001:2008 and ISO 14001:2004 certified.
While partly owned by its management, the majority shareholder of the company is the Milan-based Vidoni family that owns various mechanical seal firms. Eurocarbo supplies the rest of the Roten Group, owned by the Vidoni family, with some of its products such as seal rings. Mr Tizzoni explains, “We are the only group in the mechanical seal sector that is able to produce carbon internally. We also supply advanced ceramic components, specifically silicon carbide, for special applications.
“We have a well-equipped internal R&D department and for the past two years about 10 per cent of our annual turnover has been invested in this area, as well as in machinery and infrastructure (the Vidoni group’s annual turnover is €30 million). We are continuously improving our eco products (products which contain no lead and metals) and have developed an all-carbon range.”
Around 35 per cent of Eurocarbo’s turnover is generated by products for electrical applications, while the remainder comes from products for mechanical applications (with 5 per cent of this accounted for by products for special applications). Production takes place at a single site, which has recently been expanded, so that half of its 30,000m2 area is now occupied by covered facilities in which 130 people are employed. This leaves space for future expansion, which could indeed take place as the company is experiencing a growth trend.
Big and small
Eurocarbo’s clients are pump manufacturers and companies supplying components to the oil sector, as well as firms engaged in
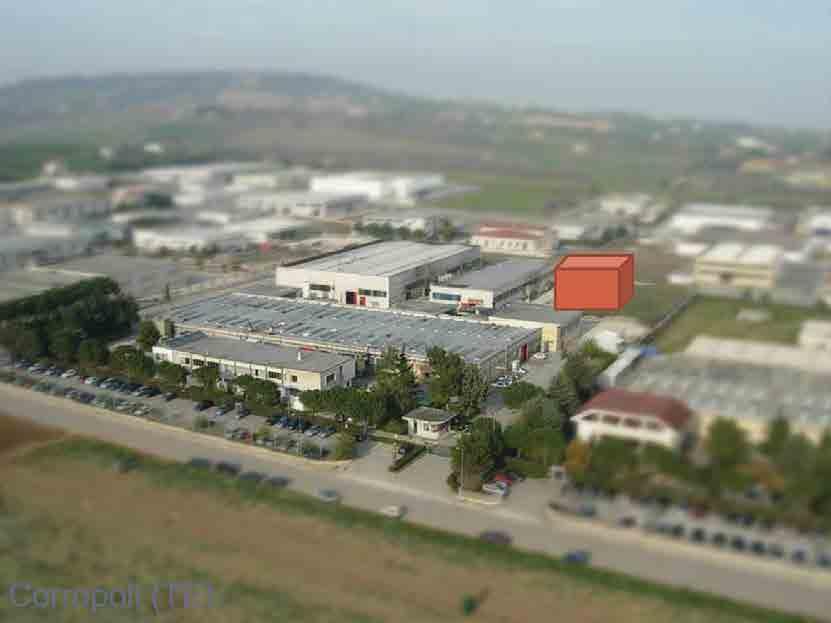
General view of factory New building 2013


Investment 2013: new additional building, improved layout to implement lean production
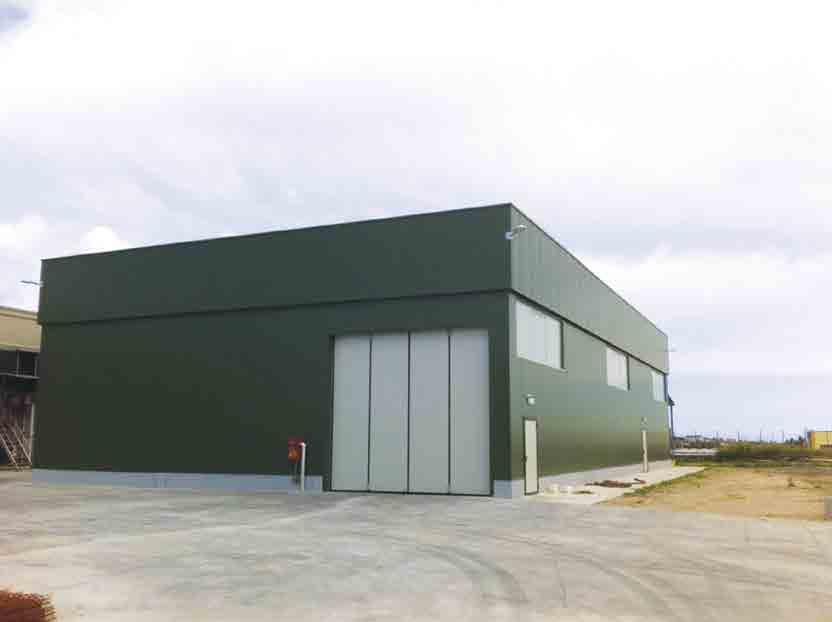
repairs and maintenance. They include both multinationals and smaller companies. In the former category the company’s client lists include names such as the Wilo Group and the Grundfos Group for the mechanical/industrial sector; the Weir Group in the oil industry; Fluid Utec in the food pump field; Turkey based Vansan and Alarko, as well as India-based Saer, in the submersible pumps and agriculture sector. Meanwhile clients from the electrical/ automotive industry – for which Eurocarbo supplies pre-assembled brushes with holders, in addition to other components – includes the globally renowned company Bosch.
Exports are very important for the company, generating 60 per cent of turnover. This mainly comes from western Europe – with Germany and France as the main markets – although there are also other potential markets and contacts in Asia. “We participate in the European version of Achema, the chemical sector trade fair, which takes place every three years. Last May we also took part in Achema Asia, where our stand was very successful, as we are planning to focus much more on the important Chinese market. Italy nevertheless remains an important market for us. Export is even higher for components for electrical applications, where it reaches a 70 per cent share of turnover. This is mainly owing to the business we do with Bosch. We are very used to working in foreign markets and have skilled multilingual staff able to take care of our clients.
“The expansion towards Asia is inevitable, as our clients have relocated much of their production there and we intend to carry on supplying them with our products. The group to which we belong already has a branch in China, near Shanghai, which we currently use as a base. We just intend to expand commercially in China, but have no plans for commencing production there. To start with, the distribution focus in China will be on semifinished products for mechanical applications.
“I believe that, as well as having an efficient organisational structure, one of our strengths as a group, and as a company, is that for us carbon is still our core business, while some of our competitors no longer take this view. This makes us particularly committed to this sector, on which we rely and in which we are investing (as Roten Group, as well as Eurocarbo). With regard to pumps, replacing graphite with other materials is quite problematic, as possible replacement materials are too expensive, so I do believe that graphite will carry on being important in the future. ”
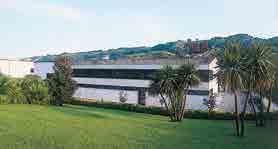
www.tma.it
T.M.A. 2 S.r.l is located in the Valtesino di Grottammare industrial area, near Ascoli Piceno, about 2 km from the Grottammare motorway exit. The company was set up in 1985 by three partners, who had previous experience in the metalwork sector, both as employees and as partners of other companies.
Our company is a high precision mechanical workshop specialised in: - design and manufacturing of blanking and drawing dies; - design and manufacturing of injection moulds for plastic materials; - design and manufacturing of casting dies; - manufacturing of dies for powders, carbons and sintered materials; - manufacturing of mechanical components, industrial machines components and small pre-assembled sets. Positive outlook
In terms of growth, Mr Tizzoni is keen to highlight how Eurocarbo aims to be a real partner for its customers. In addition to expanding into new markets, the company is planning to grow through the acquisition of new clients in existing markets, in Italy as well as abroad.
“As well as our previously mentioned strong points, we also have an excellent relationship with our highly valued staff. I have to say that we work surrounded by a real family atmosphere. Of course, as a medium company based in Italy there are currently issues with banks with regard to getting financed, but we really believe that this situation will soon resolve. We are also lucky, insofar as we do not have cash flow problems, because our clients are very punctual with payments. My future outlook is therefore positive, as we are armed with products whose excellence is widely recognised, alongside offering an outstanding service and competitive prices. As the cherry on top of the cake we are also in a position to make investments.” n
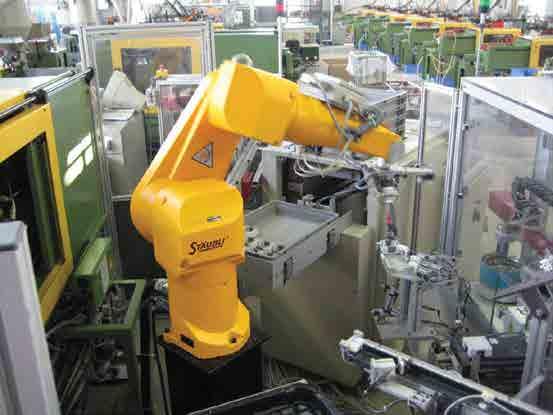
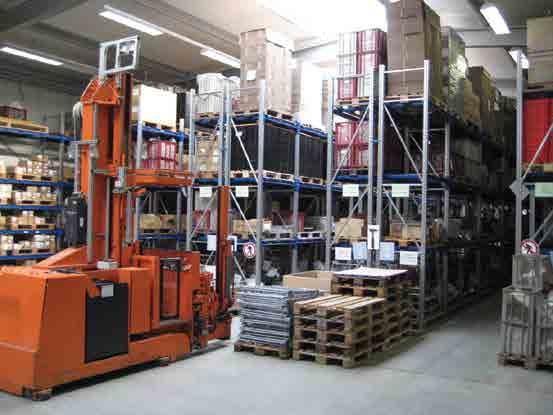
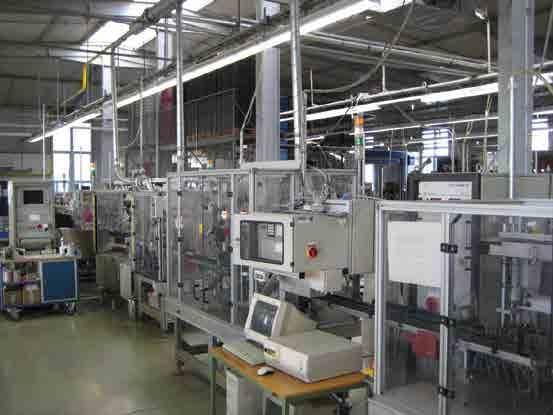
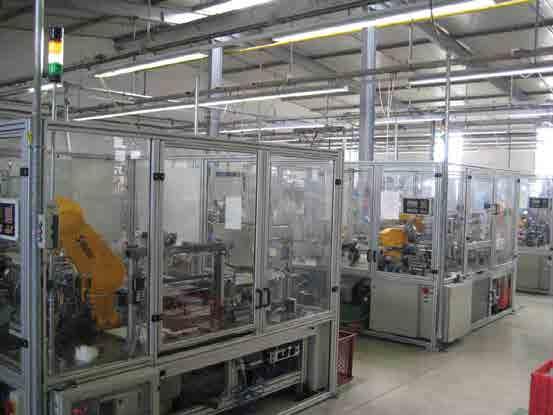
CONTROLLING THE POWER
The ETI Group has a strong production base in 13 countries across the world and branch offices in more than 60 countries. With a reputation as one of the leading producers in the field of fuses and an important niche player in the field of switchgear, the group is today a widely trusted company when it comes to the protection and safety of properties and their users. Vanja Švačko reports.
IN more than half a century’s long his tory, the ETI Group has managed to gain significant experience in innovating products and solutions for the protection of residential, commercial, industrial and power distribution installations. Established in 1950 in the central Slovenian city of Izlake, the company started making ceramic products, setting up its first electro-porcelain Bergman pipe in 1954. It took them only a decade to engage in the manufacturing of electrotechnical products and to become one of the first to offer safety fuses to its customers.
What followed was the development of innovative products such as their first miniature circuit breaker. This initiated the company’s shift towards an electrotechnical range of goods and the beginning of automation upon development of its first assembly line. Integration with the ceramic factory Svit Kamnik in 1981 shaped the form of future production and today this plant is one of the company’s main manufacturers of a large part of the technical ceramic range.
Expansion through subsidiaries
Fifteen years ago ETI embarked upon a new plan of establishing subsidiaries. The first of these were ETI Proplast in Slovenia and ETI Polam in Poland. Today ETI has daughter companies in 11 European countries (such as the former Yugoslav republics, Ukraine, Slovakia, Romania, Lithuania and Germany).
As well as establishing subsidiaries, ETI was also pursuing its expansion policy through various acquisitions, such as a plant in Hildburghausen for the manufacture of miniature circuit breakers and so on.
Today the company has three production sites: apart from the ceramic manufacturer Kamnik, Trbovlje deals with special-purpose fuses, while the facility in Izlake, which is also the company’s headquarters, makes the whole range of products including switchgears, fuses and some of the technical ceramic items. Some of the subsidiaries have autonomous production (Bosnian ETI Sarajevo, Slovakian ETI Elb, Polish ETI Polam, German ETI De and Slovenian ETI Proplast) and are basically in charge of semi-finished
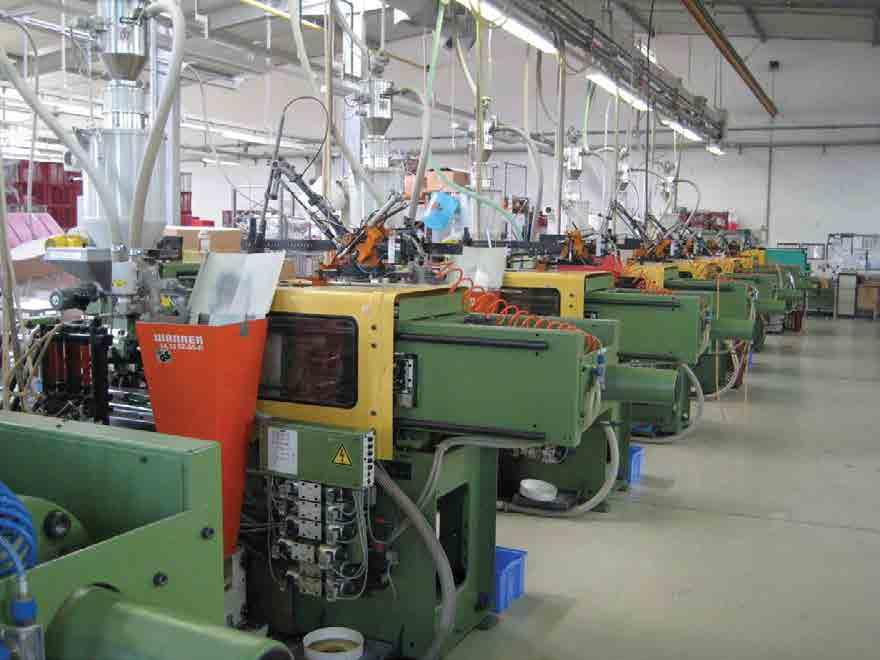
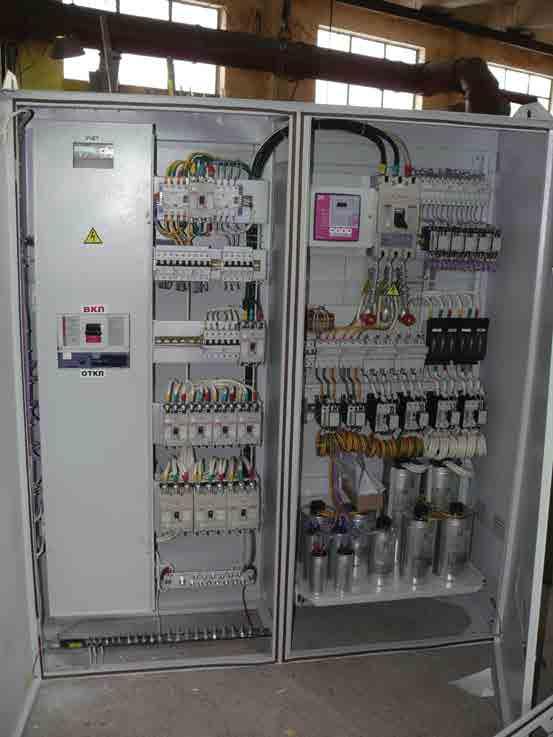

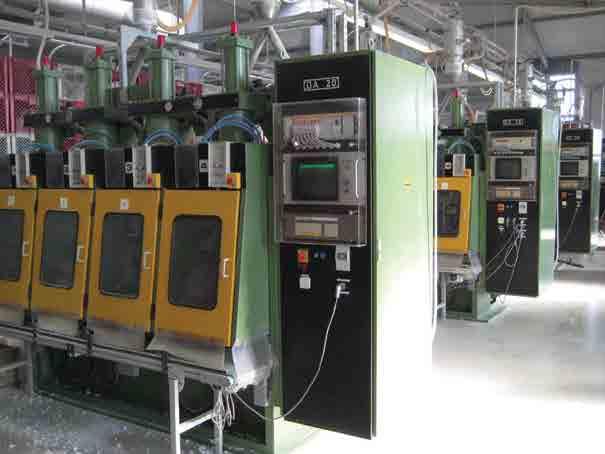
products and the assembly of goods for the Group or for their own needs. This additional manufacturing area consists of 31,154m2 .
ETI thus has a network of manufacturers, more than 1600 employees and a turnover of €95 million.
Product range
The ETI Group specialises in a range of products in four main categories: electrotechnical products, technical ceramic products, tools and equipment and specific plastic products. The first category offers solutions for residential, commercial and industrial installations, solutions for energy installations, protection of semiconductors, protection of photovoltaic systems and other renewable energy sources and special fuses. Within the category of technical ceramic goods the company makes electrotechnical ceramics, household appliances parts, products for the chemical industry and so on. In the tool shop the assembly lines and tools are designed and manufactured for the main production.
Innovating success
ETI’s constant dedication to research and improvement of its products within the frame of international standards has resulted in the company pioneering and innovating in almost all areas of its activities. It is a pioneer in the field of protection of photovoltaic

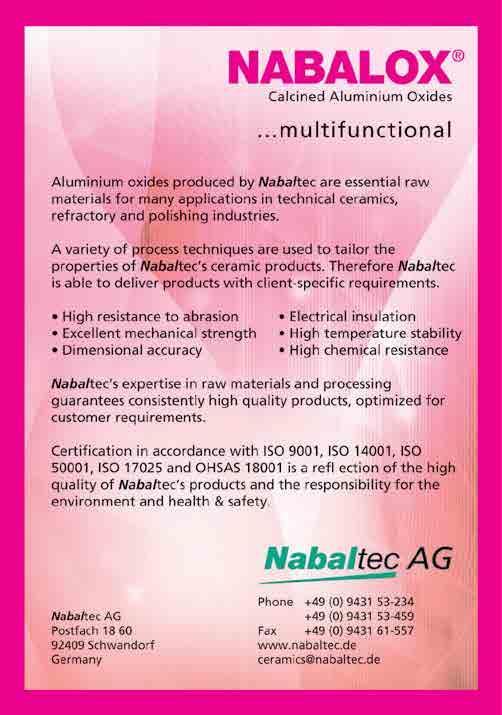
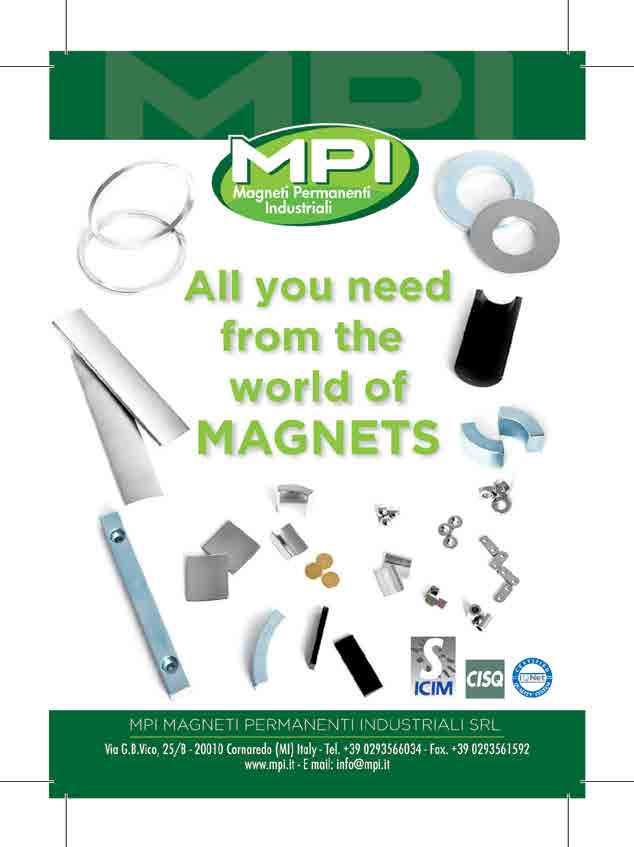