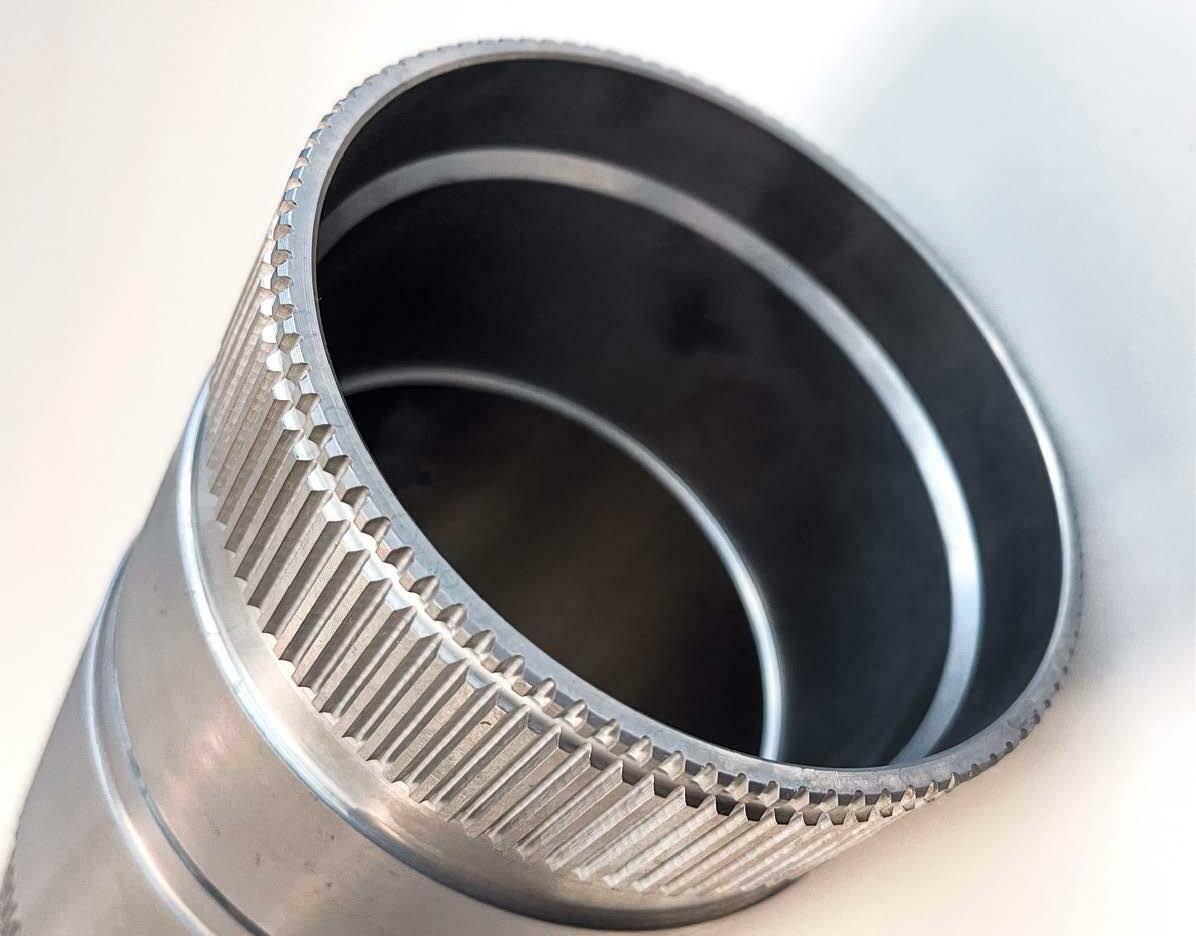
20 minute read
CASE STUDY
The benefits of modified alcohols for cleaning splined shafts before heat treatment
Arcoprofil, specialising in the production of splined shafts for the automotive and agricultural sectors, chose to implement a modified alcohol cleaning system designed and installed by I.T.F., in order to improve part cleanliness, increase production capacity, and reduce water consumption and the cost of disposing of exhaust waste water.
A steel splined shaft made by Arcoprofil (Schio, Vicenza, Italy).
Dettaglio di un profilo scanalato in acciaio realizzato da Arcoprofil di Schio (Vicenza).
I vantaggi degli alcoli modificati per il lavaggio di alberi scanalati pre-trattamento termico
Arcoprofil, società specializzata nella produzione di alberi scanalati per il settore automotive e agricolo, ha scelto di integrare nel proprio stabilimento un impianto di lavaggio con alcoli modificati progettato e installato dall’azienda I.T.F. per migliorare il grado di pulizia dei pezzi, aumentare la capacità produttiva e abbattere il consumo d’acqua e i costi di smaltimento dei reflui deteriorati.
© Arcoprofil
Wear resistance and impact resistance are the main characteristics required from the transmission components that constitute the core of engine drive units, such as for example shafts, gears, armatures, and gearwheels, which are generally made of steel. These mechanical parts are subjected to thermal or thermochemical surface treatments, which, by overheating and rapid cooling, determine the degree of hardness of their surfaces and, consequently, their stress resistance. Arcoprofil (Schio, Vicenza, Italy), a company specialising in the machining of splined shafts for the automotive and agricultural sectors, carries out two types of treatment in order to improve the surface resistance of its products: induction hardening (thermal) and case hardening (thermochemical). “Induction hardening,” explains Giorgio Calli, HSE manager at Arcoprofil, “is a heat treatment process used to increase the hardness degree of steel and its alloys. The metal components we produce are used for motor vehicle transmission units. They can be subjected either to such induction process, where heat is generated directly in the parts, or to the thermochemical treatment of case hardening followed by further oil hardening. These two technologies enable us to optimise the performance of steel by enhancing its characteristics, so that it can withstand any workload. “However, if any oil residue left by our machining operations remains on their surfaces, it can ignite and/or contaminate the coolant. This explains why it is important for us to completely clean our workpieces
© ipcm Resistenza all’usura e agli urti sono le principali caratteristiche richieste per quegli organi di trasmissione generalmente realizzati in acciaio che costituiscono il cuore della trazione del motore, come, per esempio, alberi, ingranaggi, indotti e ruote dentate. Questi componenti meccanici sono sottoposti a trattamenti superficiali termici o termochimici, che, tramite surriscaldamento e rapido raffreddamento del pezzo, determinano il grado di durezza della superficie e, di conseguenza, la resistenza alle forti sollecitazioni del prodotto trattato.
Allo scopo di migliorare il grado di resistenza superficiale dei propri manufatti, Arcoprofil, società di Schio (Vicenza) specializzata nella lavorazione di alberi scanalati per il settore automotive e agricolo, effettua due tipologie di trattamento: quello termico di tempra a induzione e quello termochimico di cementazione. “La tempra a induzione – ci spiega Giorgio
Calli, responsabile Sicurezza in Arcoprofil - è un processo di trattamento termico utilizzato per aumentare il grado di durezza dell’acciaio e delle sue leghe. I componenti metallici da noi realizzati sono utilizzati per la trasmissione del moto per autotrazione e possono essere sottoposti sia a questo processo di induzione, per cui il calore è generato direttamente nel pezzo, sia al trattamento termochimico di cementazione che precede un ulteriore trattamento di tempra in olio. Queste due tecnologie ci consentono di ottimizzare le prestazioni dell’acciaio esaltandone le caratteristiche in modo da poter meglio sopportare i carichi di lavoro. Di contro, se qualche residuo di olio derivante delle lavorazioni meccaniche permane sulla superficie, durante il surriscaldamento può infiammarsi e/o contaminare il liquido di raffreddamento: questo è il motivo che spiega
The machining department. Il reparto di lavorazioni meccaniche.
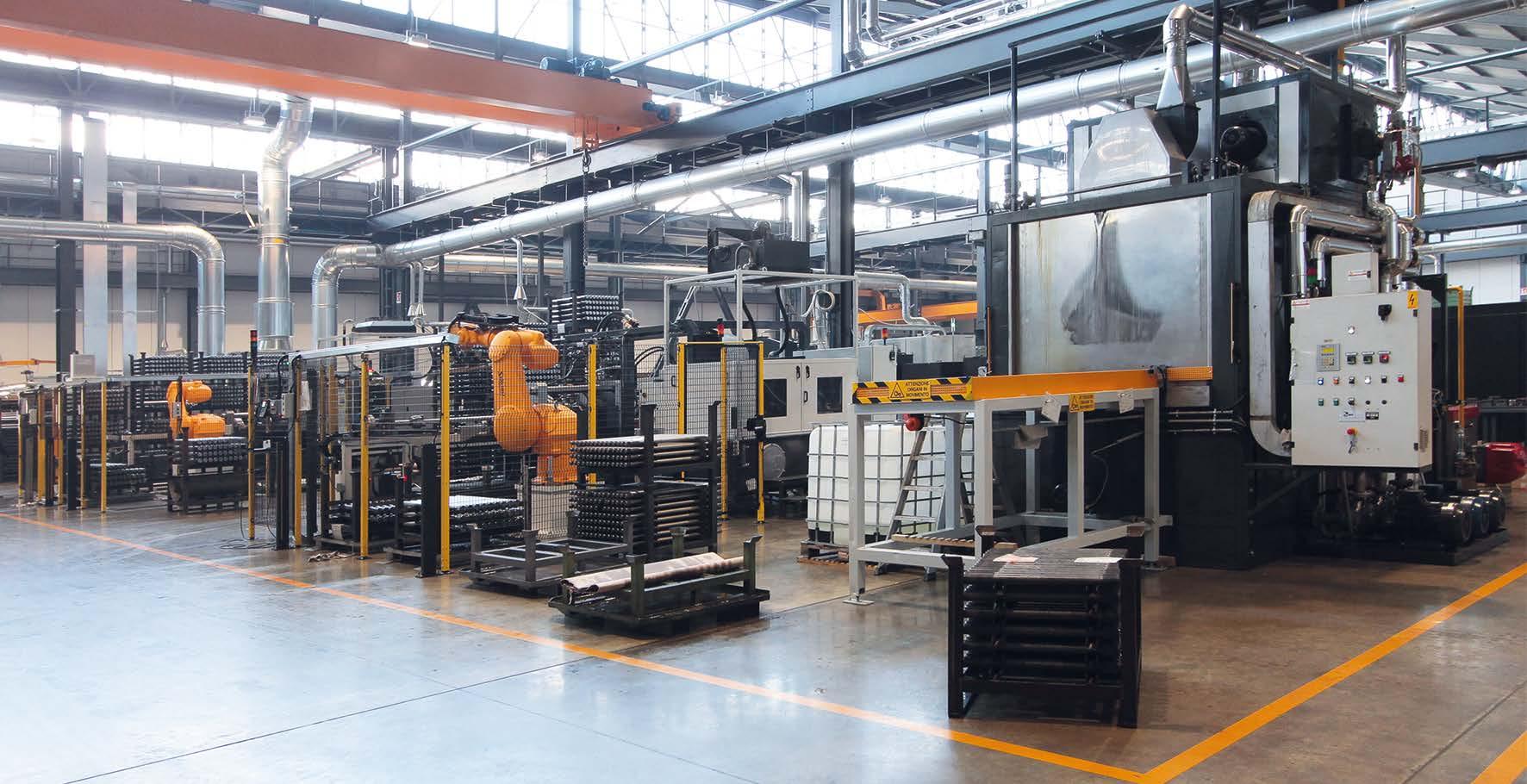
The new shot blasting machine that removes any calamine and other residues after case hardening and oil hardening.
I.T.F.’s modified alcohol cleaning system.
The inside of the cleaning chamber.
La nuova granigliatrice che rimuove calamina e residui dopo cementazione e tempra in olio.
L’impianto di lavaggio ad alcoli modificati di I.T.F..
L’interno della camera di lavaggio.

before the thermal processes and why we decided to equip our factory with a new cleaning system to complement the already existing one, placing it after the cutting, turning, and hobbing stations. For this project, we chose to work with a company with extensive experience in the design and construction of cleaning, deburring, shot peening, and shot blasting plants: I.T.F. (Mesero, Milan, Italy).”
Arcoprofil: fifty years at the forefront of every stage of production
“Arcoprofil,” says general manager Roberto Casolin to describe the foundation and evolution of his company, “was established in the mid-1970s as a company specialising in the cold rolling of splined shafts using the Grob system. Little known in Italy at that time, this technology was developed by the Swiss company from which it takes its name for deforming steel and obtaining splined shafts from solid or hollow semi-finished parts, without any chip removal action. Over fifty years of activity, we have integrated this precision machining process with other technologies: our aim has always been to obtain high quality products by exploiting any plant innovation offered by the market. Today, not only the value of our products, 99% of which are exported abroad (in particular to Germany, Sweden, Brazil, and the USA), but also that of our company, which is certified for quality management (ISO 9001:2015 and IATF 16949), environmental (ISO 14001:2015), and safety (ISO 45001:2018), are recognised worldwide.” quanto importante sia per noi la completa pulizia del pezzo prima dei processi termici e il perché, quindi, abbiamo deciso di attrezzare il nostro stabilimento con un nuovo impianto di lavaggio, da affiancare a quello preesistente, e collocarlo dopo le lavorazioni meccaniche di taglio, tornitura e dentatura. Per questo nuovo impianto abbiamo scelto la collaborazione di un’azienda con una profonda esperienza nella progettazione e costruzione di impianti di lavaggio, sbavatura, pallinatura e granigliatura: I.T.F. di Mesero (Milano)”.
Arcoprofil: cinquant’anni all’avanguardia in ogni fase produttiva
“Arcoprofil” – descrive la nascita e l’evoluzione della sua azienda il general manager Roberto Casolin – “nasce nella metà degli anni ’70 come azienda specializzata nella rullatura a freddo di profili scanalati con il sistema Grob, una tecnologia a quel tempo semisconosciuta in Italia e sviluppata dalla società svizzera da cui prende il nome per la deformazione dell’acciaio allo scopo di ottenere profili scanalati da particolari semilavorati pieni o cavi senza asportazione di trucioli. Nel corso di cinquant’anni di attività a questa lavorazione meccanica di precisione se ne sono affiancate altre: l’obiettivo è sempre stato quello di ottenere un prodotto di qualità garantito dalle innovazioni impiantistiche che il mercato offre. Oggi non solo il valore dei nostri prodotti, esportati per il 99% all’estero - in particolare in Germania, Svezia, Brasile e USA - ma anche quello della nostra azienda, certificata sia per la qualità di gestione (ISO 9001:2015 e IATF 16949), per l’attenzione all’ambiente (ISO 14001:2015) e alla sicurezza (ISO 45001:2018), sono riconosciuti in tutto il mondo”.
© ipcm © ipcm
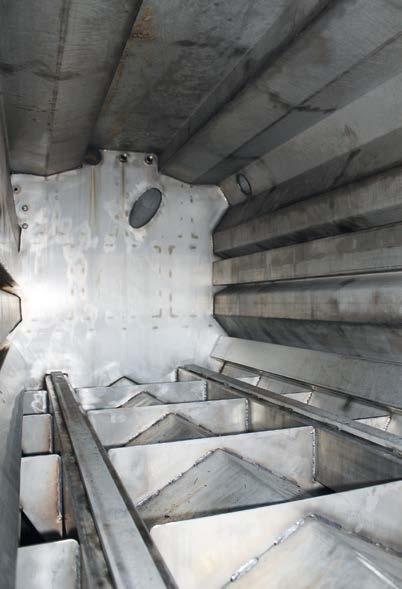
During the early 2000s, the company completed a gradual process of insourcing all production phases in one production site, in a new 11,300 m2-wide building. “Currently,” adds Casolin, “Arcoprofil is able to manage every processing phase in-house, supporting its customers from the design stages to the creation of the finished products, including heat treatment. With our team of 150 specialised operators, we serve the world’s leading manufacturers of heavy vehicles, construction machinery, and tractors, as well as some major manufacturers of axles and mechanical transmissions in the automotive sector.”
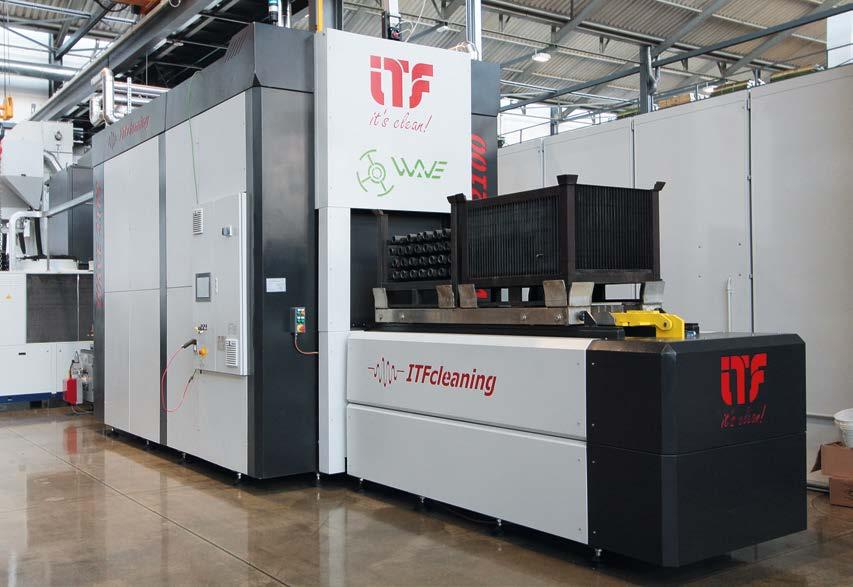
From semi-finished products to mechanical transmission components
The splined shafts’ processing starts with semi-finished products, consisting of bars with diameters ranging from 20 to 250 mm or forgings, depending on customer requirements. The bars are cut by high-speed sawing machines and their faces are machined with centring and facing systems, which prepare the parts for the subsequent machining steps. “The workpieces are then subjected to turning with CNC centres and splining,” indicates Calli, “which is our flagship operation and with which we produce both internal and external splined shafts using different technologies, depending on design specifications and the material used. We can offer four processing methods: shaper cutting and gear hobbing, cold rolling with the Grob system, and Felss frequency modulated axial deformation. “All components coming out of our machining operations are then Nel corso dei primi anni del Duemila, l’azienda ha concluso il progressivo processo di internalizzazione di tutte le fasi produttive in un unico sito costituito dal nuovo capannone da 11300 m2. “Attualmente” – prosegue Casolin – “Arcoprofil è in grado gestire internamente ogni fase di lavorazione, supportando il cliente nella progettazione fino al prodotto finito, inclusi i trattamenti termici. Con il nostro team di 150 addetti specializzati forniamo i più importanti costruttori di veicoli pesanti, macchine movimento terra e trattori mondiali ed alcune aziende leader nella costruzione di assali e trasmissioni meccaniche nel settore automotive”.
Dal semilavorato alla trasmissione meccanica
La lavorazione del profilo scanalato prende avvio da un semilavorato costituito da una barra i cui diametri variano da 20 a 250 mm, o da uno stampato in acciaio, a seconda del tipo di prodotto richiesto dal cliente. Le barre vengono tagliate da segatrici ad alta velocità e le facce lavorate da macchine centro intestatrici, che preparano il pezzo per le successive fasi di lavorazione. “Segue la tornitura con centri CNC e la dentatura – prosegue Calli – che rappresenta il nostro fiore all’occhiello e con cui realizziamo profili scanalati sia interni che esterni ottenuti per mezzo di diverse tecnologie, in base alle specifiche del disegno e al materiale utilizzato. Sono 4 i metodi di lavorazione che possiamo offrire: dentatura a coltello e dentatura a creatore, rullatura a freddo con sistema Grob e deformazione assiale a frequenza modulata Felss. Tutti i componenti in uscita dalle lavorazioni meccaniche sono lavati per rimuovere l’olio residuo prima dei trattamenti termici: la presenza del minimo residuo
© ipcm © ipcm

One of the two large baskets and a basket with carefully arranged profiles entering the cleaning chamber. Una delle due ceste di grandi dimensioni e l’ingresso della cesta con i profili posizionati nella camera di lavaggio.
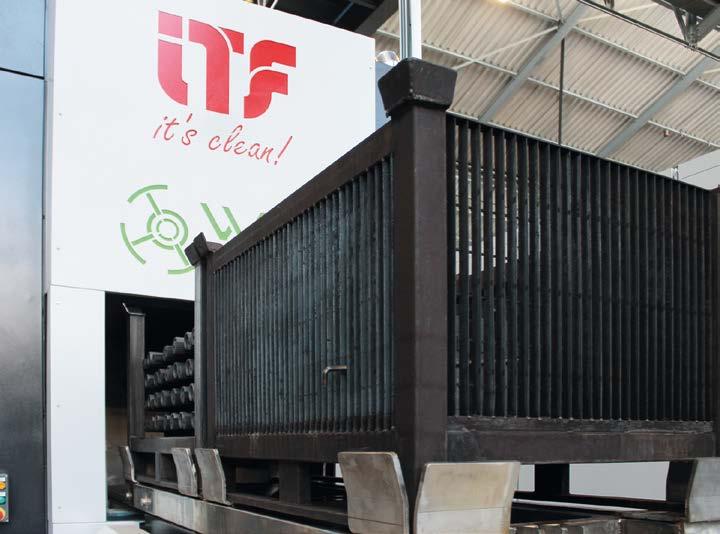
cleaned to remove any residual oil traces before heat treatment. In fact, the presence of the slightest oil residue on their surfaces could compromise the success of this delicate stage of our production cycle. As mentioned, this is followed by the two thermal processes of induction hardening and quencing cooling and case hardening with oil quencing. After this step, further cleaning is necessary before moving on to mechanical cleaning with a shot blasting machine, used for removing any residuals, and to grinding, aimed at achieving the required degree of roughness and surface precision. Finally, some components also require a final cleaning step before getting through quality control at our metrology laboratory, assembly, and shipping.”
Interoperational cleaning with modified alcohols
“Until some time ago,” indicates Calli, “we used a water and detergent washing system, installed in 2010, both for the parts coming out of machining operations and for the products requiring final cleaning after finishing. Recently, however, this plant had become a bottleneck due to an increase in production volumes. Our management, therefore, decided to invest in a new cleaning system to meet two main requirements: optimising our production flow and reducing both the water consumption level and the disposal costs of exhaust water that characterise the other system. Together with I.T.F., we assessed several options and we finally chose a modified alcohol system that guarantees greater cleaning agent stability and zero water consumption. The latter aspect, in particular, led us to opt for a more environmentally di olio sulla superficie potrebbe compromettere il successo di questa delicata fase del nostro ciclo produttivo. Seguono quindi i due processi termici di tempra a induzione con raffreddamento in quench e cementazione con tempra in olio. Dopo questa fase è necessario un lavaggio prima di passare ad una pulizia meccanica con granigliatrice per rimuovere eventuali residui - e la rettifica, per ottenere il grado di rugosità e la precisione superficiale desiderata. Alcuni componenti necessitano anche di un intervento di lavaggio finale, prima di passare al controllo qualità del nostro laboratorio metrologico, al montaggio e alla spedizione”.
“Fino a poco tempo fa” – continua Calli – “utilizzavamo un impianto di lavaggio ad acqua e detergenti del 2010 sia per i prodotti in uscita dalle lavorazioni meccaniche sia per quelli che erano sottoposti al lavaggio finale di post-finitura. Recentemente, a causa dell’aumento del volume di produzione, questo impianto era diventato un collo di bottiglia. La direzione ha quindi deciso di affiancargli un nuovo impianto di lavaggio in grado di soddisfare 2 esigenze: ottimizzare il flusso produttivo e abbattere il consumo di acqua e i costi di smaltimento dei reflui deteriorati che caratterizzano il primo impianto. Con I.T.F. abbiamo valutato più soluzioni impiantistiche e abbiamo scelto un impianto con alcoli modificati in grado di garantire una maggiore stabilità dell’agente di lavaggio e un consumo di acqua pari a zero. In particolare, quest’ultimo
friendly solution.” “Initially,” states Christian Accogli, the CCO of I.T.F., “we presented Arcoprofil with different plant types, from a water and detergent system to a high-pressure deburring machine and a modified alcohol cleaning plant. We also outlined the advantages and disadvantages of each solution. For example, with profiles that can reach dimensions of up to 1,200 mm, choosing a water-based system would mean carefully analysing the size of the chamber (which should be around 2 m3) and of the tanks and the water flow rate required, as well as considering the spoilage factor of the washing solution, which becomes unstable after a short time, unlike modified alcohol. Modified alcohol can also be used as a single degreasing, cleaning, and rinsing agent, whereas a water and detergent system necessarily calls for at least 3 washing agents.”
Building technology that makes the difference
“The system was installed at the beginning of this year,” says Accogli. “It is built in thick AISI 304 stainless steel (DIN AISI 1.403), a material that allows reaching high vacuum levels in the chamber, in order to
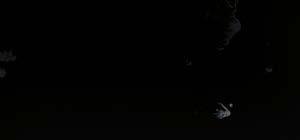
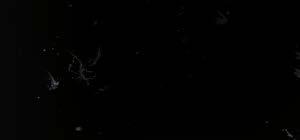
aspetto ha rappresentato l’ago della bilancia che ha fatto decidere per una soluzione dal nostro punto di vista più ecosostenibile”. “Inizialmente – spiega Christian Accogli, CCO di I.T.F. – abbiamo proposto ad Arcoprofil soluzioni impiantistiche diverse, dall’impianto ad acqua e detergenti fino ad un impianto di sbavatura ad alta pressione e a quello di lavaggio con alcoli modificati. Per ciascuna soluzione abbiamo illustrato vantaggi e svantaggi. Per esempio, in presenza di profili che possono raggiungere dimensioni di 1200 mm, scegliere un impianto all’acqua comporterebbe la necessità di analizzare attentamente la grandezza della camera (che dovrebbe corrispondere a circa 2 m3) e delle vasche e la portata dell’acqua necessaria, oltre a considerare il fattore di deperimento della soluzione di lavaggio che dopo poco tempo diventa instabile, contrariamente a quanto accade con l’alcol modificato. Quest’ultimo, inoltre, può essere utilizzato come unico agente di lavaggio per lo sgrassaggio, il lavaggio e il risciacquo, mentre con un impianto all’acqua e detergenti gli agenti di lavaggio devono essere necessariamente almeno 3”.
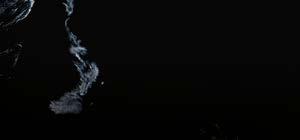
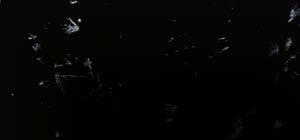
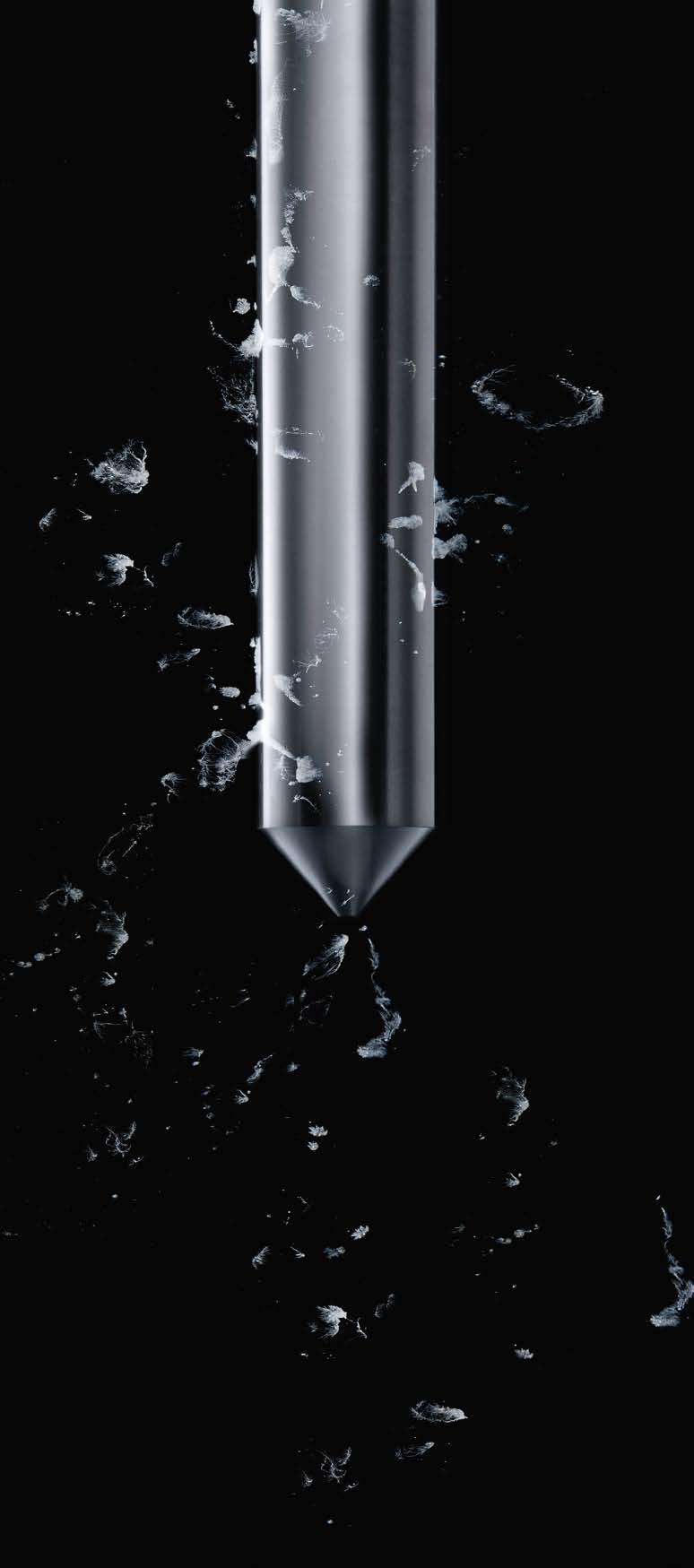
Una tecnologia costruttiva che fa la differenza
“L’impianto installato all’inizio di quest’anno – precisa Accogli – è stato costruito in acciaio inox di alto spessore AISI 304 (DIN AISI 1.403), un materiale che permette di raggiungere in camera alti livelli di vuoto, per evitare di stressare il liquido di lavaggio, e di asciugare i pezzi molto rapidamente. Il nostro concept costruttivo è caratterizzato dall’integrazione della camera di lavoro nel corpo macchina, in modo da evitare la presenza di serbatoi e tubazioni che potrebbero contribuire a dissipare il calore e che, con il passare del tempo, non
The original: Sonopush HDT rod transducer. 360° effect. Robust, durable and suitable for the toughest applications.
© Arcoprofil © Arcoprofil
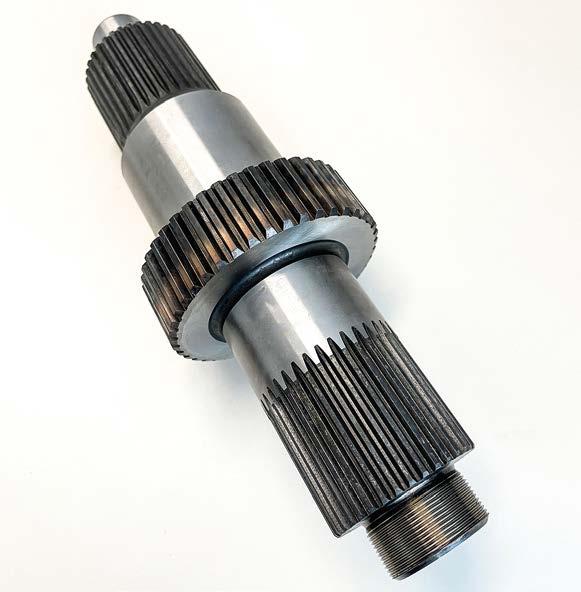
Splined shafts produced by Arcoprofil.
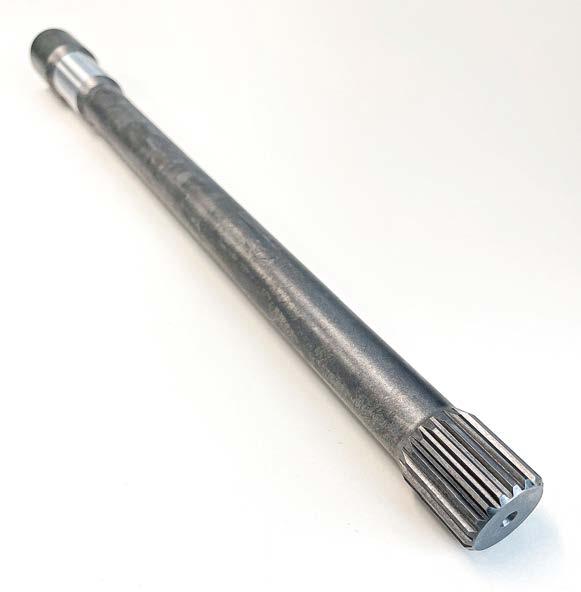
avoid stressing the cleaning liquid, and drying the parts very quickly. Our construction concept is characterised by the integration of the working chamber into the machine body, in order to avoid the presence of tanks and pipes that contribute to heat dissipation and cannot guarantee vacuum tightness over time.” Arcoprofil’s machine, in particular, can handle 2 large-sized baskets with a dimension of 1,000 x 2,200 x 850 mm and it has 2 tanks integrated in the main body: a storage tank for the treatment liquid and an evaporator. “The chamber can process 4,000 litres of product: 2,600 in the upper tank and 1,400 in the lower tank,” indicates Nicola Milani, technical manager at I.T.F.. “The cleaning agent used is DUALENETM 1601 S, a pre-stabilised product suitable for the most challenging applications, especially in the presence of chlorinated substances.” When the splined shafts enter the cleaning chamber, high vacuum is created, followed by flooding from the upper tank so that the parts are completely immersed. “At this point,” adds Milani, “4 batteries always working at maximum power activate ultrasound. This can be adjusted manually, but the vacuum created generally prevents any degasification problems that, on the other hand, arise when using ultrasound at atmospheric pressure. This makes the ultrasound action more effective.” The workpieces remain inside the chamber while ultrasound is active for a pre-set time. “The chamber is then emptied and flooded with hot solvent vapour above 120 °C. Drying takes place by evaporation thanks
Alberi scanalati prodotti da Arcoprofil.
garantiscono la tenuta in regime di sottovuoto”. Nel caso di Arcoprofil, la macchina, in grado di trattare 2 cesti con dimensioni ampie pari a 1000 x 2200 x 850 mm, presenta due vasche integrate nel corpo principale: una vasca di stoccaggio da cui viene prelevato il liquido per il trattamento in camera e un evaporatore. “All’interno la camera può trattare 4000 litri di prodotto: 2600 nella vasca superiore e 1400 in quella inferiore” - afferma Nicola Milani, responsabile tecnico di I.T.F.. “L’agente di lavaggio utilizzato è il DUALENETM 1601 S, un prodotto prestabilizzato utilizzato per le applicazioni più difficili soprattutto in presenza di clorurati”. L’albero scanalato entra nella camera di lavaggio, in cui viene creato un vuoto molto spinto seguito da un allagamento per caduta dalla vasca superiore, per cui il pezzo risulta completamente immerso. “In questa fase vengono attivati gli ultrasuoni – prosegue Milani - da 4 batterie che lavorano sempre alla massima potenza. Gli ultrasuoni si possono regolare manualmente, ma, in genere, grazie al vuoto non sussistono i problemi di degasificazione che emergono, invece, con gli ultrasuoni a pressione atmosferica. In questo modo l’azione degli ultrasuoni risulta più efficace”. Il pezzo rimane all’interno della camera con gli ultrasuoni attivi per il tempo prestabilito. “Successivamente la camera viene svuotata e inondata con vapori di solvente caldo superiore ai 120 °C. L’asciugatura avviene per evaporazione grazie alla creazione di un vuoto molto spinto in 2 fasi: una intermedia intorno ai 50 millibar di pressione e una intorno ai 4-5
to the creation of high vacuum in two phases: an intermediate phase with a pressure of around 50 millibars and a second phase around 4-5 millibars. Thanks to such high vacuum regime, it is possible to evaporate the heat in the chamber and on the parts at a still very high temperature, thus bringing them to complete drying. Vacuum drying prevents airborne particles from re-contaminating the cleaned parts inside the process chamber by creating a hermetically sealed and therefore extremely clean environment, as the chamber is also washed with each work cycle. Finally, preventive deodorisation of the chamber occurs by means of a flow of fresh air that exits the pump and reaches the condensers before being expelled.”
The advantages of total recovery
Distillation within the plant is continuous. “The evaporated and condensed solvent,” notes Milani, “can be recirculated to the upper tank. We have also equipped the machine with an external distillation system for oil recovery. As this is a very large chamber, the distillation system was designed with 4 vacuum pumps, 2 bag filters for chip recovery, 2 emptying pumps, and 4 condensers, of which 2 are used to extract alcohol from the system and the other 2 for drying the chamber. In this way, alcohol is completely recovered and returned to the system, whereas the eluate, consisting of the recovered neat oils and the water extracted from the alcohol bath by the separator, can be disposed of.” Thanks to the integrated module concept, the solvent vapours generated by the distiller are used to supply the chamber with thermal energy. “In order to reduce the thermal power required, we have designed a mixed system: water heated with a methane gas burner is recirculated inside the machine to heat modified alcohol through steel coils. This reduces the thermal energy used to restore the necessary distillation regime, thus lowering electricity consumption and generating a greater quantity of vapour for the final stage of the process.”
Conclusions
Casolin describes the reasons for Arcoprofil’s partnership with I.T.F. as follows: “We chose the solution offered by this company because its technical staff was highly knowledgeable about this system’s potential. Thanks to the new machine’s installation we have noticed an actual improvement in the cleanliness degree of blind holes and, above all, we have reached fast and efficient drying times, which makes all the difference in a mass production flow like ours. Thanks to I.T.F.’s knowhow we optimized the results also on the most complex geometries. We will soon be able to distribute the cleaning operations required on all our products between our two machines, thus eliminating the bottleneck that was our main concern.” millibar all’interno nella camera. Grazie al regime di vuoto così spinto, è possibile far evaporare il calore presente sia nella camera sia sul pezzo con temperatura ancora molto elevata, portandolo così all’asciugatura completa. L’asciugatura in vuoto evita che i corpuscoli presenti nell’aria contaminino nuovamente i pezzi puliti all’interno della camera di processo in un ambiente ermeticamente sigillato e dunque estremamente pulito, dal momento che anche la camera viene lavata a ogni ciclo di lavoro. La fase terminale prevede la deodorazione preventiva della camera attraverso un flusso d’aria fresca che dalla pompa è condotta ai condensatori, prima di essere espulsa”.
I vantaggi del recupero totale
La distillazione all’interno dell’impianto è continua. “Il solvente evaporato e condensato – continua Milani – può essere ricondotto alla vasca superiore. Abbiamo dotato la macchina anche di un sistema di distillazione esterno per il recupero dell’olio. Trattandosi di una camera molto ampia, il sistema di distillazione è stato studiato con 4 pompe a vuoto, 2 filtri a sacco per il recupero dei trucioli, 2 pompe di svuotamento e 4 condensatori, due dei quali sono utilizzati per l’estrazione dell’alcol dal sistema e gli altri 2 per l’asciugatura della camera. In questo modo possiamo ottenere un recupero totale dell’alcol che viene reimmesso nel sistema e lo smaltimento dell’eluato costituito da oli interi che vengono recuperati e dall’acqua estratta dal bagno di alcol dal separatore”. Grazie al concept con modulo integrato, i vapori di solvente generati del distillatore sono sfruttati per dotare la camera di energia termica. “Per ridurre la potenza termica abbiamo studiato un sistema misto: l’acqua riscaldata con un bruciatore a gas metano viene fatta ricircolare all’interno della macchina per riscaldare l’alcol modificato con serpentine in acciaio. In questo modo abbiamo ridotto l’energia termica utilizzata per ripristinare il regime di distillazione necessario, riducendo i consumi elettrici e ottenendo una maggior quantità di vapori per la fase finale del processo e per la loro condensazione”.
Conclusioni
Casolin descrive così i motivi della partnership di I.T.F.: “la scelta è ricaduta sulla soluzione proposta dall’azienda milanese perchè siamo stati convinti dalla preparazione del loro staff tecnico sulle potenzialità dell’impianto. Con l’installazione della nuova macchina abbiamo potuto notare un miglioramento effettivo del grado di pulizia dei fori ciechi e, soprattutto, abbiamo rilevato tempistiche di asciugatura veloci ed efficaci: un elemento che fa la differenza in una produzione massiva come la nostra. Grazie al know how di I.T.F. abbiamo potuto ottimizzare i risultati anche sui componenti dalle geometrie più complesse. Presto potremo distribuire le operazioni di lavaggio di tutti i nostri prodotti tra le due macchine e risolvere quel collo di bottiglia che rappresentava la nostra principale preoccupazione”.