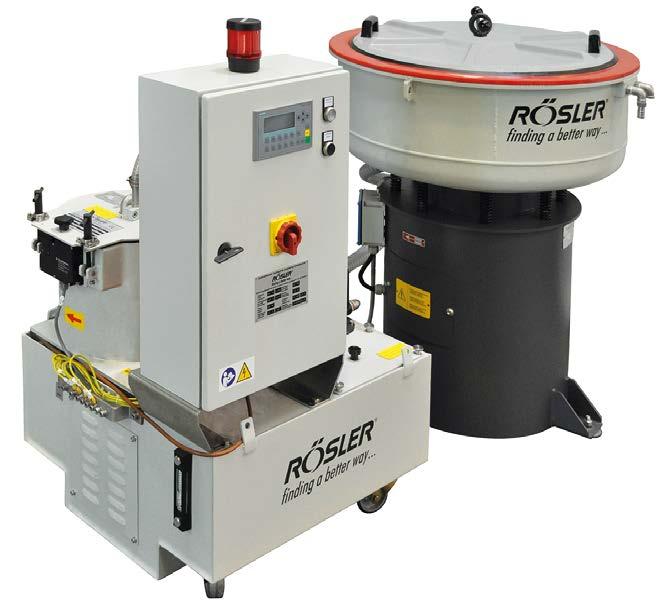
15 minute read
HIGHLIGHT OF THE MONTH
© Rösler
Purification centrifuge from the RZ 60 M-V-KB series connected with MINI 120. Centrifuga di depurazione della serie RZ 60 M-V-KB collegata a MINI 120.
© Rösler
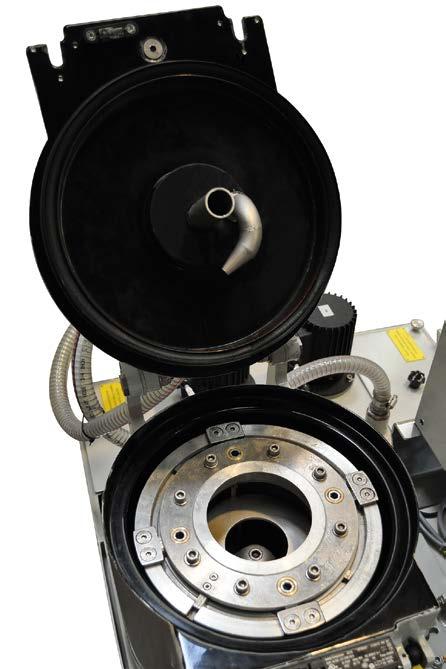
The RZ 60 M-V-KB centrifuge with its tank open. La centrifuga RZ 60 M-V-KB con il serbatoio aperto.
In semi-automatic centrifuges, the sludge formed can be easily eliminated through a basket inserted in the drum, whereas in fully automatic centrifugal systems it is removed automatically. Depending on the type of plant, several units can be linked to one purification centrifuge.
Rösler centrifuges: efficient purification of process liquids
In order to meet market requirements, Rösler has developed 3 types of purification centrifuges in different sizes, guaranteeing not only excellent results, but also significant cost savings. The powerful centrifugal filters, available for two-phase (liquid and solid) or three-phase (two liquids and one solid) separation, can be used for a variety of tasks and they are easily adaptable to any specific application.
RZ 60 M-V-KB purification centrifuges
The powerful RZ 60 M-V-KB is the smallest centrifuge in the range Nelle centrifughe semiautomatiche può essere facilmente rimosso con un cestello inserito nel tamburo rotante. Nei sistemi centrifughi completamente automatici i fanghi sono staccati automaticamente dal tamburo. A seconda della tipologia di impianto, più unità possono essere gestite da un’unica centrifuga di depurazione.
Le centrifughe di Rösler: depurazione efficiente dei liquidi di processo
Per soddisfare le esigenze di mercato, Rösler ha sviluppato 3 tipologie di centrifughe di depurazione di diverso formato, in grado di garantire non solo risultati di depurazione eccellenti, ma anche un notevole risparmio economico. I potenti filtri centrifughi, disponibili per la separazione a due (liquido e solido) o tre fasi (2 liquidi e un solido), possono essere utilizzati per svariate operazioni di depurazione e sono facilmente adattabili anche ad applicazioni specifiche.
Centrifughe di depurazione RZ 60 M-V-KB
La potente RZ 60 M-V-KB è la centrifuga più piccola e si adatta
and it is perfectly suited for applications with limited capacity. It is extremely compact and flexible and its two-stage process makes it easy to separate solids from liquids. This semi-automatic centrifuge treats up to 300 litres of waste water per hour and ensures low noise and excellent performance.
RZ 120 purification centrifuges
The RZ 120 M system is the most powerful semi-automatic centrifuge available on the market. In addition to its high capacity, it also offers another significant advantage, namely its three-phase separation operation, which allows two liquids and a suspended solid to be separated from each other so that they can be reused or disposed of individually. Of course, a two-phase separation process is also possible. In order to guarantee maximum flexibility over time, this system is also available in a mobile version.
RZ 150 purification centrifuges
When particularly high volumes need to be processed, the Rösler RZ 150 A automatic centrifuge is the ideal solution. Manual emptying is no longer necessary thanks to automatic sludge extraction.
Scan or click the QR code to see how Rösler’s purification centrifuges work: perfettamente ad applicazioni con capacità limitata. Grazie alle sue dimensioni, risulta estremamente compatta e flessibile e il suo processo a due fasi permette di separare facilmente i solidi dai liquidi. Questa centrifuga semi-automatica tratta fino a 300 litri/ora di reflui ed è caratterizzata da rumore ridotto e da ottime prestazioni.
Centrifughe di depurazione RZ 120
La RZ 120 M è la centrifuga semi–automatica più potente disponibile sul mercato. Oltre all’elevata capacità, offre anche un altro importante vantaggio: la separazione a tre fasi, che permette di separare due liquidi e un solido in sospensione gli uni dagli altri, così da riutilizzarli oppure smaltirli singolarmente. Naturalmente, è possibile effettuare anche un processo di separazione a due fasi. Per garantire massima flessibilità nel tempo, questo impianto è disponibile anche in versione mobile.
Centrifughe di depurazione RZ 150
Quando è necessario trattare volumi particolarmente elevati, la centrifuga automatica Rösler RZ 150 A è la soluzione ideale. Grazie all’estrazione automatica dei fanghi, non è più necessario lo svuotamento manuale.
Scansiona o clicca il QR code per vedere il funzionamento delle centrifughe di depurazione di Rösler:
Closed loop water recirculation systems
Rösler’s waste water purification and treatment plants can be connected to any mass finishing machine. This guarantees significant savings, as many vibratory finishing processes such as deburring, smoothing, radiusing, and polishing consist of wet operations: the water and cleaning agents used, therefore, are contaminated with metal and abrasive residues. Such process water can be completely recycled through a closed loop system, and the resulting savings in water and chemicals ultimately lead to a significant reduction in costs. The purification plant’s functioning is based on a special centrifuge with an acceleration factor of up to 2000 rpm and on environmentally friendly chemicals developed by Rösler itself. Rösler’s process water recirculation systems can be adapted to any mass finishing application and they are available as both semi-automatic and fully automatic centrifuges.
I sistemi di ricircolo dell’acqua a circuito chiuso
Gli impianti Rösler per la depurazione e il trattamento delle acque reflue possono essere collegati a qualsiasi macchina di finitura di massa. Questo permette un risparmio economico non indifferente, poiché molti processi di vibrofinitura come la sbavatura, la levigatura, la raggiatura e la lucidatura sono effettuati a umido. L’acqua e gli agenti di pulitura rimangono così contaminati dai residui di metallo e di abrasivi usati per il trattamento. L’acqua di processo può essere completamente riciclata attraverso un sistema a circuito chiuso e il conseguente risparmio di acqua e di composti chimici comporta una significativa riduzione dei costi. L’impianto di purificazione è basato su una speciale centrifuga con un fattore di accelerazione che può raggiungere i 2000 giri/min, e su prodotti chimici sviluppati da Rösler nel pieno rispetto dell’ambiente. Gli impianti di Rösler per il ricircolo delle acque di processo possono essere adattati a qualsiasi applicazione di finitura di massa. Sono disponibili centrifughe semi-automatiche o completamente automatiche.
© Rösler
Purification centrifuge from the Z800 HA-TF series. Centrifuga di depurazione della serie Z800 HA-TF.
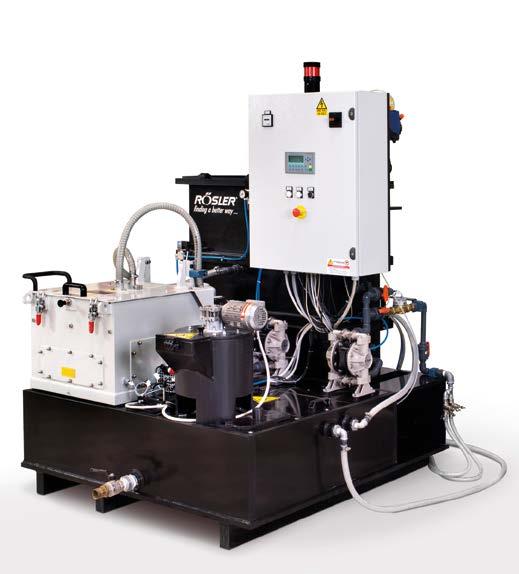
© Rösler
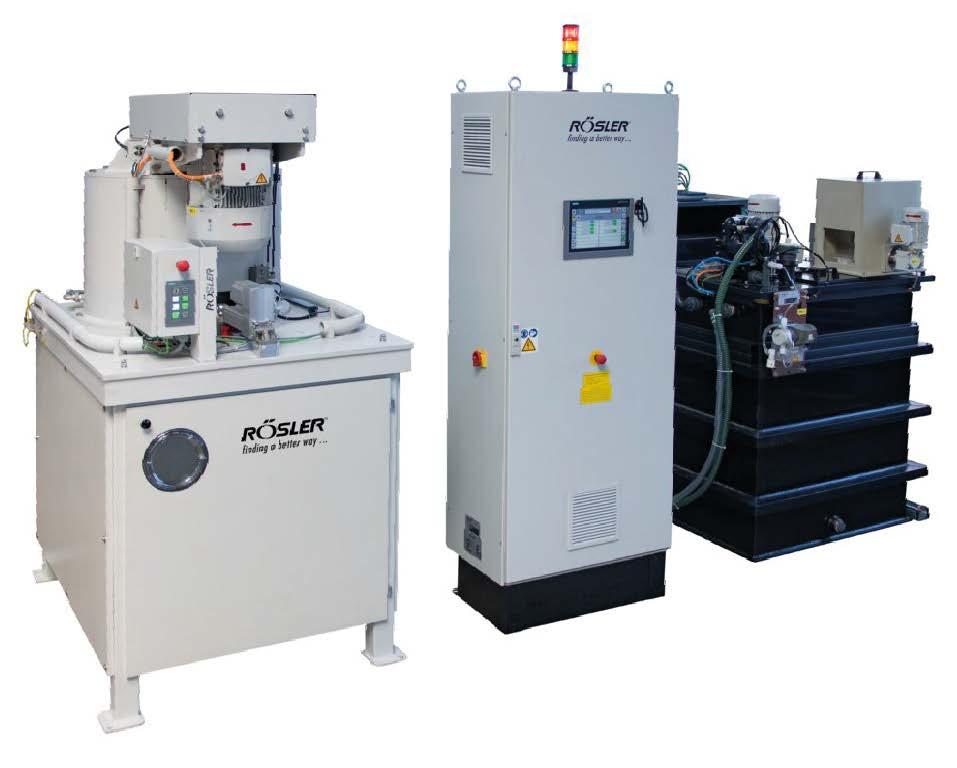
Purification centrifuge from the RZ 150 A series. Centrifuga di depurazione della serie RZ 150 A.
Z800 process water recirculation systems
This series of centrifuges with manually replaced baskets stands out for its exceptional separation performance level, but also for its space-saving installation in the immediate vicinity of mass finishing machines. The centrifuge itself, the plant controls, and the tanks for process water and clean water are installed in a highly functional complete unit, the core of which is exactly the centrifuge developed and built by Rösler.
Z1000 process water recirculation systems
Various applications require large quantities of solid materials or large volumes of water to be centrifuged in a very short time. Plants requiring manual replacement of sludge baskets can often not be integrated into these processes. The ASS series process water recirculation systems, with automatic sludge extraction, can be used in these cases. Their peculiarity is the automatic removal of solid particles in a 300-litre sludge trolley below the centrifuge. At the end of each cycle, the rotor is washed to remove any remaining dirt and to prevent any imbalance in the following cleaning cycle and, therefore, short-term wear of the bearings. A standard-mounted
Sistemi per il ricircolo delle acque di processo Z800
Questa serie di centrifughe a cestelli a sostituzione manuale si contraddistingue, oltre che per le eccezionali prestazioni di separazione, per la collocazione salvaspazio nelle immediate vicinanze delle macchine di finitura di massa. La centrifuga, i comandi dell’impianto e i serbatoi per l’acqua di processo e l’acqua pulita sono installati in una unità completa estremamente funzionale, il cui cuore è la centrifuga sviluppata e costruita da Rösler.
Sistemi per il ricircolo delle acque di processo Z1000
Svariate applicazioni richiedono di centrifugare grandi quantità di materiali solidi oppure grossi volumi d’acqua in tempi molto brevi. Gli impianti che prevedono una sostituzione manuale dei cestelli per i fanghi spesso non sono integrabili in questi processi. Per questo motivo, vengono impiegati gli impianti per il ricircolo delle acque di processo della serie ASS, con estrazione automatica del fango. La particolarità di questi sistemi è la rimozione automatica delle particelle solide all’interno di un carrello per fanghi da 300 litri posto al di sotto della centrifuga. Alla fine del ciclo, il rotore viene lavato per rimuovere l’eventuale sporco restante e per evitare uno squilibrio nel ciclo di pulizia successivo, e quindi l’usura dei cuscinetti a
device that can shut down the system if necessary also monitors such imbalance.
Scan or click the QR code to see how Rösler’s water recirculation systems work: breve termine. Tale squilibrio è monitorato tramite un dispositivo montato di serie in grado, se necessario, di spegnere l’impianto.
Scansiona o clicca il QR code per vedere il funzionamento dei sistemi per il ricircolo delle acque di Rösler:
Conclusions
Environmental protection has always been one of the cornerstones of Rösler’s corporate philosophy. This is why the Rösler Group has developed its efficient water purification and recirculation systems, which, thanks to their centrifugal filtering technology, can reduce water consumption by up to 90%.
Conclusioni
L’attenzione rivolta alla protezione ambientale è da sempre uno dei cardini della filosofia aziendale di Rösler. Questo è il motivo che ha spinto il Gruppo Rösler a sviluppare sistemi di depurazione e di ricircolo delle acque efficienti, in grado, grazie alla loro tecnologia centrifuga di filtraggio, di ridurre il consumo di acqua fino del 90%.
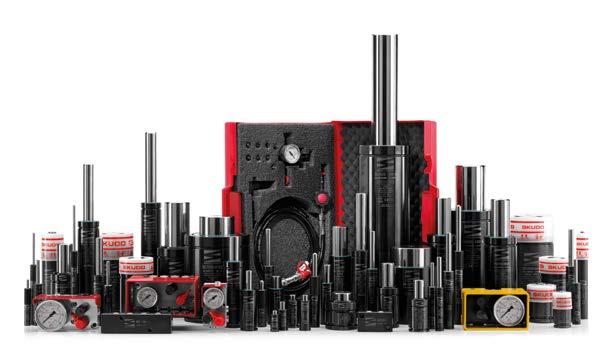
Special Springs’s nitrogen cylinders and wire die springs. I cilindri ad azoto e le molle a filo di Special Springs.
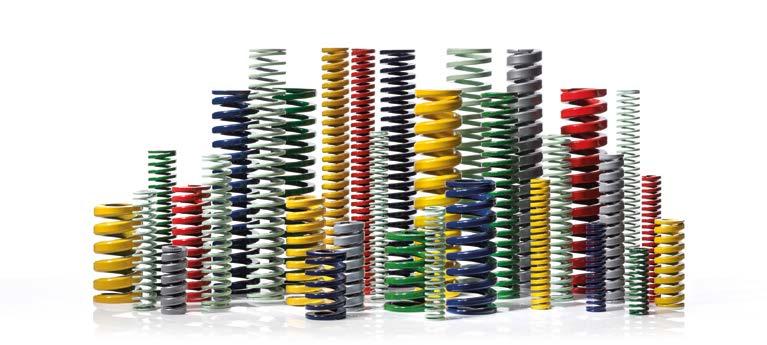
High-quality ultrasonic cleaning with halogenated solvents to remove processing oils: the innovative choice of Special Springs
Automated quality control of nitrogen cylinders makes it possible to deliver components with perfect surfaces, but the cleaning phase must not leave any residue to avoid a high scrap or unapproved parts rate. This is why Meg supplied Special Springs with a plant to fully degrease its parts by ultrasonic cleaning with halogenated solvents.
Automated quality control makes it possible to quickly inspect all surfaces and deliver perfect components, but it is necessary to clean all workpieces thoroughly and remove all residual machining oils, in order for them to be approved. Special Springs worked for several months with Meg (San Martino di Lupari, Padua, Italy), a firm specialising in innovative industrial cleaning solutions, in order to find the right process for its nitrogen cylinders, which are an evolution of classic wire due springs, also manufactured by the company – in particular, cylinders can replace them in certain types of moulds because they are able to withstand different loads, but they require high-quality cleaning to remove machining residues and to be approved by quality control systems. After several laboratory tests, Special Springs chose an automatic ultrasonic degreaser with halogenated solvents supplied that Meg has designed specifically for its needs, which enables it to treat its cylinders in 7 minutes and automatically send them to the robotic quality control station.
Lavaggio di alta qualità a ultrasuoni con solventi alogenati per eliminare tutti gli oli di lavorazione: l’innovativa scelta di Special Springs
Il controllo automatizzato della qualità di tutti i cilindri ad azoto permette di consegnare ai clienti componenti dalla superficie perfetta, ma è necessario che la fase di lavaggio non lasci nemmeno un residuo per evitare un alto volume di scarti o controlli non idonei. Meg ha perciò fornito a Special Springs un impianto per sgrassare completamente i pezzi tramite un lavaggio a ultrasuoni con solventi alogenati.
Il controllo automatizzato della qualità consente di ispezionare rapidamente tutte le superfici e consegnare ai clienti esclusivamente i componenti perfetti, ma è necessario lavare ottimamente qualsiasi particolare ed eliminare tutti gli oli di lavorazione residui affinché questi impianti possano approvare i pezzi. Special Springs ha collaborato per molti mesi con Meg, azienda di San Martino di Lupari (PD) specializzata in innovative soluzioni di lavaggio industriale, al fine di trovare il giusto processo di lavaggio per i propri cilindri ad azoto, che rappresentano un’evoluzione rispetto alle classiche molle a filo – realizzate anch’esse dall’azienda. I cilindri le possono infatti sostituire in determinate tipologie di stampi perché sono in grado di reggere carichi diversi, ma richiedono un lavaggio dalla qualità elevata per eliminare i residui delle lavorazioni ed essere approvati dagli impianti di controllo qualità. Dopo alcuni test in laboratorio, Special Springs ha scelto una sgrassatrice automatica ad ultrasuoni con solventi alogenati che Meg ha progettato appositamente per le sue specifiche esigenze e che le ha permesso di trattare i propri cilindri in 7 minuti e convogliarli automaticamente verso l’isola robotizzata di controllo della qualità.
Special Springs: constantly seeking innovation and expansion
Special Springs was founded in 1968 by brothers Augusto and Luciano Cappeller, who are still at the helm of the company as its president and vice-president respectively. In addition to the production of wire die springs, in the 1990s it began manufacturing nitrogen cylinders in its Rosà (Vicenza) factory, which expanded over the years to handle different types and ranges of products and their accessories. In 2012, the company moved to a single production site in Romano D’Ezzelino (Vicenza), which was further expanded in 2016 to integrate cataphoretic coating for wire die springs. In fact, each type of spring needs to be painted in its own distinctive colour (green, blue, red, yellow, or silver) symbolising the load it can support. Meanwhile, Special Springs has also expanded abroad, opening a subsidiary in India in 2005 for the assembly of gas cylinders and a manufacturing subsidiary in North America in 2011, joining Turkish group GSB Oilless in 2014 and acquiring machining company Unic in 2020. Its products are mainly intended for Tier 1 manufacturers in the automotive sector. With a storage site in South America, it is able to serve four continents very quickly.
From raw materials to finished and assembled products
Currently, Special Springs manufactures various types of wire die springs and gas cylinders and it also performs customised machining to specific requirements. The production of springs starts with silicon steel wire being rolled according to particular geometries and then cold-formed and wound using lathes. At this point in the process, the wire, which has taken on the shape of a spring, is hardened and heat-treated to give it the necessary strength. Finally, the spring is roll flattened, shot peened, pressed, and subjected to cataphoretic coating. The production of nitrogen cylinders, on the other hand, is more complex. “The cylinders we manufacture with CNC machine tools are very different in size, as they can have a diameter of between 12 and 195 millimetres and a height of between 50 and 495 millimetres. Therefore, the production phase also varies depending on their specific requirements,” explains Loris Scalco, the research and development manager of Special Springs. Subsequent processing consists of turning with a bar pusher or a gantry loader and finishing. These cylinders consist of three parts: the body and the bushing (caseback) are static parts, while the rod is mobile. Consequently, the rods need to be cleaned after finishing to prevent machining oils and residual swarf from impairing their proper functioning.
The importance of the cleaning phase and of the subsequent quality controls
Therefore, after the different production phases, the rods are cleaned with the 2S 88/24-P-FP/T AC + TA60/2 machine designed and built by
Special Springs: alla costante ricerca di innovazione ed espansione
Special Springs fu fondata nel 1968 dai fratelli Augusto e Luciano Cappeller, che sono ancora oggi alla guida dell’azienda in qualità di, rispettivamente, presidente e vice-presidente. Oltre alla produzione di molle a filo, negli anni ’90 iniziò anche la produzione di cilindri ad azoto nello stabilimento di Rosà (VI), che si è espansa nel corso degli anni includendo diverse tipologie e gamme con relativi accessori. Nel 2012 l’azienda si è trasferita in un unico sito produttivo a Romano D’Ezzelino che è stato ulteriormente ampliato nel 2016 per includere la verniciatura per cataforesi delle molle a filo. Ogni tipologia di molla necessita infatti di un proprio colore distintivo (verde, blu, rosso, giallo e argento) indicativo del carico che riesce a supportare. Special Springs si è inoltre espansa anche all’estero, aprendo una filiale in India nel 2005 per l’assemblaggio di cilindri a gas e una filiale produttiva in nord America nel 2011, entrando a far parte del gruppo turco GSB Oilles nel 2014 e acquisendo l’azienda di lavorazioni meccaniche Unic nel 2020. I manufatti sono principalmente destinati ai produttori tier 1 del settore automotive e, avendo a disposizione inoltre un centro di stoccaggio in Sud America, Special Springs è in grado di servire quattro continenti in tempi molto rapidi.
Dalla materia prima al prodotto finito e assemblato
Attualmente Special Springs produce diverse tipologie di molle a filo e cilindri a gas ed effettua anche lavorazioni personalizzate su specifica richiesta del cliente. Nella produzione di molle, il filo di acciaio al silicio è inizialmente laminato seguendo particolari geometrie e successivamente profilato e avvolto a freddo da torni. A questo punto del processo il filo, che ha assunto le sembianze di una molla, è temprato e sottoposto a trattamenti termici per conferire la necessaria resistenza. Infine, la molla è spianata, pallinata, pressata e verniciata in cataforesi. La produzione di cilindri ad azoto è invece più complessa. “I cilindri che produciamo con macchine utensili a controllo numerico sono molto diversi per dimensioni, dato che possono avere un diametro compreso tra i 12 e i 195 millimetri e un’altezza compresa tra i 50 e i 495 millimetri. Pertanto anche la fase produttiva varia in base alle esigenze”, spiega Loris Scalco, responsabile ricerca e sviluppo per Special Springs. Le successive lavorazioni consistono nella tornitura con spingi-barra o caricatore a portale e nella finitura. Questi cilindri sono composti da tre parti: il corpo e la boccola (o fondello) sono parti statiche, mentre lo stelo è mobile. Di conseguenza, gli steli necessitano di essere lavati dopo la finitura, al fine di evitare che gli oli di lavorazione e i trucioli residui ne compromettano il corretto funzionamento.
L’importanza del lavaggio e del successivo controllo qualitativo
Dopo i differenti processi produttivi, gli steli sono quindi lavati con la macchina 2S 88/24-P-FP/T AC + TA60/2 progettata e realizzata da