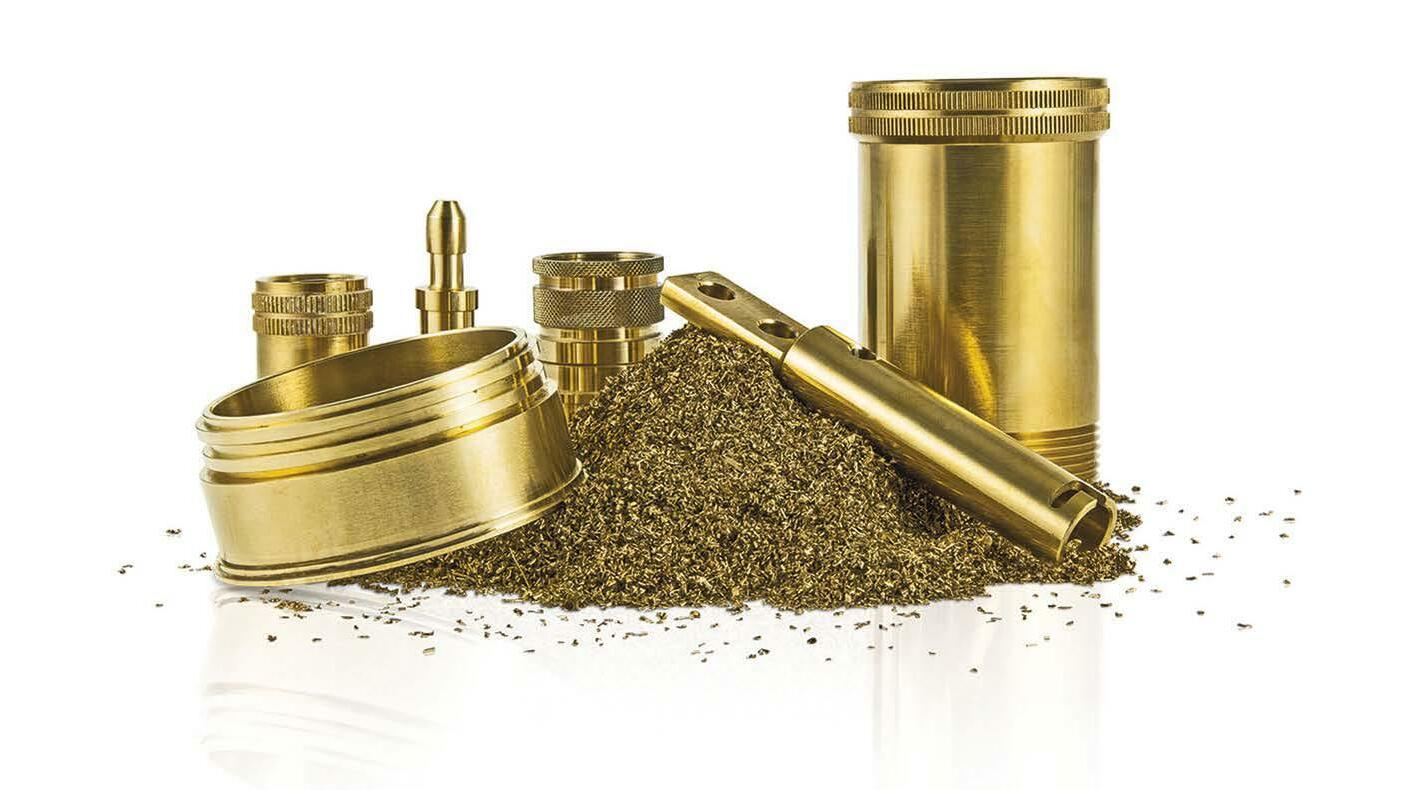
15 minute read
CASE STUDY
Turning with neat oil and cleaning with modified alcohols: Bacchetta’s combination for subcontracting excellence in the precision small parts industry
Striving for excellence often means deciding to invest a large part of one’s own resources in production solutions that may be financially demanding but at the same time guarantee high quality results. This is the path taken by company Bacchetta Giuseppe, which has been specialising in the contract production of precision small parts for almost sixty years now and which has chosen to use only neat cutting oil for its turning operations. This decision has involved a careful assessment of the most effective cleaning technology, which ended with the selection of Cemastir’s L.UN.A. modified alcohol plant.
Bacchetta Giuseppe Srl has been active for almost sixty years in the contract production of turned small metal parts.
Bacchetta Giuseppe Srl opera da quasi sessant’anni nel settore della sub-fornitura di minuterie metalliche tornite di precisione.
Tornitura con olio intero e lavaggio con alcoli modificati: il binomio di Bacchetta per la subfornitura d’eccellenza di minuterie di precisione
Scegliere l’eccellenza significa in molti casi decidere di investire gran parte delle proprie risorse in soluzioni produttive più impegnative in termini economici che però garantiscono risultati di qualità: questa è la strada percorsa dall’azienda Bacchetta Giuseppe, specializzata da quasi 60 anni nella subfornitura di minuterie di precisione che ha scelto di utilizzare esclusivamente l’olio da taglio intero per le proprie lavorazioni di tornitura. Una decisione che ha comportato un’attenta analisi della tecnologia di lavaggio più efficace, identificata in quella dell’impianto ad alcoli modificati L.UN.A. di Cemastir.
© Bacchetta Giuseppe Srl
In the geographic area that is home to one of Italy’s most important industrial districts, that of tapware, namely the Verbano-Cusio province in the Piedmont region, there is a company that specialises in the contract production of precision metal parts and that has been able to set itself apart from other local manufacturers by differentiating its production, intended for different sectors in addition to that of tapware, and by investing in state-of-the-art plant equipment meeting high quality standards. This is Bacchetta Giuseppe Srl, founded in 1963 by the man who gave it its name and currently led by his son Carlo.
“We have been active for almost sixty years in contract production of turned small metal parts. We have always had a customer-oriented approach, aiming for excellence in service and quality: our agile, dynamic organisational structure guarantees a direct and constant contact with our customers, so that we can meet all their needs while creating solid and long-term partnerships. All these elements have allowed us to differentiate our company’s offer from the local one.”
Based in Gattico-Veruno, in the province of Novara, in an area that has become famous for its numerous tapware turning contractors,
Bacchetta Giuseppe is “a rare bird”, as its owner calls it, both in terms of the cutting-edge production processes it carries out within its factory, adapted to the parameters of Industry 4.0, and in terms of the very demanding customers it serves. Since the beginning of the 1990s, Bacchetta Giuseppe focused with high levels of investment on the upgrading of its production plants, in terms of both machine technology and quality control. It has been ISO 9000 certified since 1995. “In 2018, we further renovated our plant equipment with a view to smart manufacturing, implementing latest-generation machinery and installing an MES system to manage our whole workflow, from the reception of customer requests to the shipment of end products.
All 24 CNC lathes are connected to our network, which enables us to monitor job progress and analyse production data and product quality in real time. The experience we have gained over the years in the machining of various types of materials, from stainless steel and brass to aluminium and copper, makes us a multi-faceted company, capable of meeting the needs of various industrial sectors (including electronics, pneumatics, oil hydraulics, fittings, tapware, and automotive) that require turned precision parts, which we produce exclusively to customer drawings. Our core business is the production of electronic components, such as circular connectors used in the automotive, railway, aeronautics, and telecommunications sectors, which we distribute both nationally and internationally, particularly in
Germany and the United States.”
A winning combination
“Our numerous machines,” adds Bacchetta, “enable us to process different types of materials to manufacture components with Nel territorio che ospita uno dei distretti industriali italiani più importanti, quello della rubinetteria del Verbano-Cusio piemontese, c’è un’azienda specializzata nella subfornitura di minuterie metalliche di precisione che ha saputo distinguersi dalle manifatture locali grazie alla differenziazione della propria produzione destinata a settori diversi, oltre a quello della rubinetteria, e alla scelta di investire in una dotazione impiantistica all’avanguardia che garantisca elevati standard di qualità: Bacchetta
Giuseppe Srl, fondata nel 1963 da colui che le ha dato il nome e guidata oggi dal figlio Carlo. “La nostra azienda opera da quasi sessant’anni nel settore della sub-fornitura di minuterie metalliche tornite di precisione. Sin dalla sua fondazione abbiamo sviluppato un approccio orientato al cliente, puntando all’eccellenza nel servizio e nella qualità: la nostra struttura organizzativa agile e dinamica ci permette un confronto diretto e costante con i nostri committenti per soddisfare ogni loro esigenza, creando partnership solide e di lungo periodo. L’insieme di tutti questi elementi ci ha permesso di differenziare la nostra proposta da quella locale”.
Situata a Gattico-Veruno in provincia di Novara, in un territorio diventato famoso per la concentrazione di aziende dedicate alla tornitura in conto terzi di componenti per rubinetteria, Bacchetta Giuseppe rappresenta “una mosca bianca” - questa la definizione del suo titolare - sia per la tipologia di produzione all’avanguardia che effettua all’interno dello stabilimento adattato ai canoni dell’Industria 4.0 sia per la tipologia di clienti molto esigenti a cui si rivolge. Sin dall’inizio degli anni Novanta, Bacchetta Giuseppe si è concentrata con notevoli investimenti nel rinnovamento dei propri impianti produttivi, sia per il livello tecnologico dei macchinari sia per il controllo qualità. L’azienda è certificata ISO 9000 dal lontano 1995.
“Nel 2018 l’azienda ha ulteriormente rinnovato i propri impianti in ottica di smart manufacturing, implementando il parco macchine con macchinari di ultima generazione e installando un sistema MES per la gestione dalla richiesta dell’offerta fino alla spedizione del prodotto finito al cliente. Tutti i 24 torni CNC sono collegati in rete e ciò ci permette il monitoraggio dell’avanzamento delle commesse e un’analisi in tempo reale dei dati di produzione e della qualità dei prodotti stessi. L’esperienza che abbiamo acquisito negli anni nella lavorazione di svariati tipi di materiali, dall’acciaio inox all’ottone, dall’alluminio al rame, fa di noi un’azienda poliedrica in grado di soddisfare le esigenze di svariati settori industriali - elettronica, pneumatica, oleodinamica, raccorderia, rubinetteria, automotive - che richiedono particolari torniti di precisione da noi realizzati esclusivamente su disegno del cliente. Core business dell’azienda è la produzione di componenti per elettronica, come per esempio i connettori circolari, impiegati nei settori automobilistico, ferroviario, aeronautico e delle telecomunicazioni con una distribuzione sia su territorio nazionale sia internazionale, in particolare in Germania e Stati Uniti”.
Il binomio vincente
“L’ampio parco macchine – prosegue Bacchetta – ci permette di lavorare diverse tipologie di materiali per realizzare componenti a partire dal
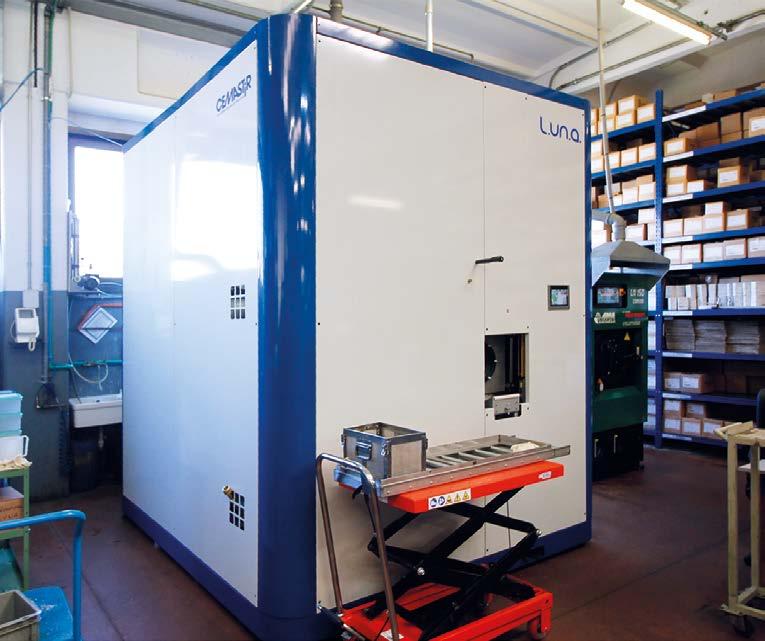
© ipcm © ipcm
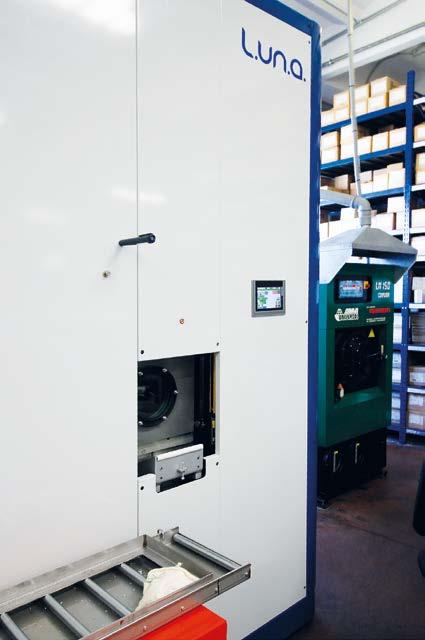
Cemastir’s L.UN.A. modified alcohol cleaning plant and the loading/unloading area of the new plant and. On the right in the background, the old Delfino cleaning machine. L’impianto di lavaggio ad alcoli modificati L.UN.A. di Cemastir e un dettaglio della zona di carico/scarico del nuovo impianto. A destra sullo sfondo, la vecchia lavatrice Delfino.
diameters of 2 to 75 mm starting from bars and of 2 to 5 mm starting from wire. We decided to carry out all our machining operations using neat cutting oil, because we consider the value of our machines, which represent the heart of our production department, to be too important to be compromised by employing other types of products. Although more expensive neat oil offers numerous advantages, including greater lubrication efficiency and better preservation of machine tools, which require 80% less maintenance. This rigorous decision obviously has had an impact on the choice of the most suitable cleaning technology for our turned parts, an operation that our company has always carried out – a further proof of the attention we have always paid to the quality of our products.” The upgrading of Bacchetta Giuseppe’s cleaning systems has gradually followed the technological developments in this field, switching from the trichloroethylene tanks used in the 1960s to increasingly complex systems, up until the latest technological innovation offered by Cemastir, a company specialising in the design and installation of cleaning systems that, in June 2010, took over Amalind, the owner of the Delfino brand and one of Bacchetta’s long-standing suppliers. “When we decided to replace one of the Delfino cleaning machines, diametro 2 a 75 mm da barra e dal diametro 2 a 5 mm da filo. Per scelta aziendale eseguiamo tutte le lavorazioni meccaniche con olio da taglio intero, perché riteniamo che il valore dei nostri macchinari che rappresentano il cuore della nostra produzione sia troppo importante per poter essere compromesso dall’utilizzo di altri prodotti. A fronte di un costo più elevato, l’olio intero presenta tuttavia notevoli vantaggi, tra cui una maggiore efficacia di lubrificazione e una migliore conservazione della macchina utensile, che non necessita di particolari interventi di manutenzione, ridotti dell’80%. Questa decisione rigorosa ha avuto ovviamente conseguenze sulla scelta della tecnologia di lavaggio più adatta per la pulizia dei pezzi torniti, un’operazione che la nostra azienda effettua da sempre a conferma dell’attenzione che da sempre rivolgiamo alla qualità dei nostri prodotti.” L’aggiornamento dei sistemi di lavaggio nell’azienda novarese è proseguito seguendo il progresso della tecnologia e passando dalle vasche di trielina degli anni Sessanta a impianti sempre più complessi fino ad arrivare all’ultima innovazione tecnologica proposta da Cemastir, azienda specializzata nella progettazione e installazione di impianti di lavaggio che nel giugno 2010 ha rilevato Amalind, la proprietaria del marchio Delfino e fornitrice storica di Bacchetta.
which are still in working order but require very long treatment times, we chose to rely on Cemastir not only because their solution was perfectly suited to our needs in terms of performance for an ecological question - very important for us - and for safety of the working environment, but also to maintain continuity in terms of plant engineering and, above all, cleaning quality. This is why we chose a L.UN.A. system.”
L.UN.A.’s technical features
The cleaning technology was not called into question. “The aim was to achieve excellent cleaning results even in the most difficult-to-reach areas, such as bores that can be as small as 0.25 mm in diameter, with a system ensuring a safe working environment, so modified alcohols were immediately the most convincing option.” “The plant,” explains Gianfranco Fiori, the Sales Manager of Cemastir, “is characterised by a compact concept that allows placing it even in limited spaces, with all accessories integrated. It represents the evolution of the Delfino technology, with the advantages of an innovative system that reduces the cycle times from the 45 minutes required by the Delfino machines to the 12 to 15 minutes required by L.UN.A., that is, about one third of the previous times, while also limiting solvent consumption and the amount of sludge to be disposed of. In addition, thanks to two distillers working simultaneously, the machine can work without any downtime for maintenance. Another
© ipcm “Quando abbiamo deciso di sostituire una delle lavatrici Delfino, ancora funzionanti ma che richiedono tempistiche di lavaggio molto lunghe, abbiamo chiesto la collaborazione di Cemastir non solo per la proposta perfettamente attinente alle nostre esigenze in termini di prestazioni per una questione ecologica - molto importante per noi - e di rispetto dell’ambiente di lavoro, ma anche per mantenere una continuità impiantistica che ci consentisse di proseguire il discorso di qualità relativo al lavaggio che avevamo intrapreso tanti anni fa: abbiamo così scelto L.UN.A.”.
Le caratteristiche di L.UN.A.
La scelta della tecnologia di lavaggio non era in discussione. “L’obiettivo era quello di ottenere risultati di pulizia elevati anche nelle parti più complicate da raggiungere – come per esempio i fori che possono avere un diametro anche di 0,25 mm – con un sistema che garantisse la sicurezza dell’ambiente di lavoro, quindi gli alcoli modificati hanno rappresentato da subito l’opzione più convincente”. “L’impianto – interviene Gianfranco Fiori, Sales Manager di Cemastir – è caratterizzato da un concept compatto, che ne consente la collocazione anche in aree di capannone dove lo spazio è ridotto, e dall’integrazione di tutti gli accessori al suo interno. Rappresenta l’evoluzione della tecnologia Delfino con i vantaggi di un sistema innovativo che permette la riduzione dei tempi ciclo dai 45 min delle lavatrici Delfino ai 12-15 min di L.UN.A, corrispondenti a circa un terzo delle tempistiche precedenti, del consumo di solventi e delle morchie da smaltire. Inoltre, grazie a due distillatori che lavorano simultaneamente, la macchina può lavorare senza interruzioni
© ipcm
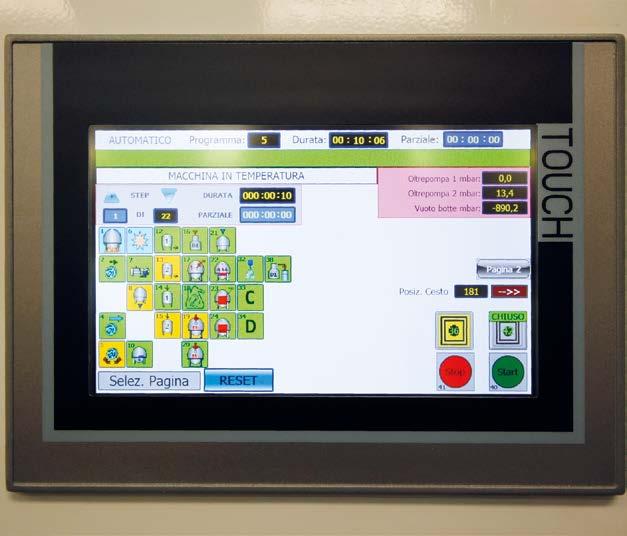
A standard-sized basket. Il cestello con dimensioni standard. The touch screen. Il touch screen.
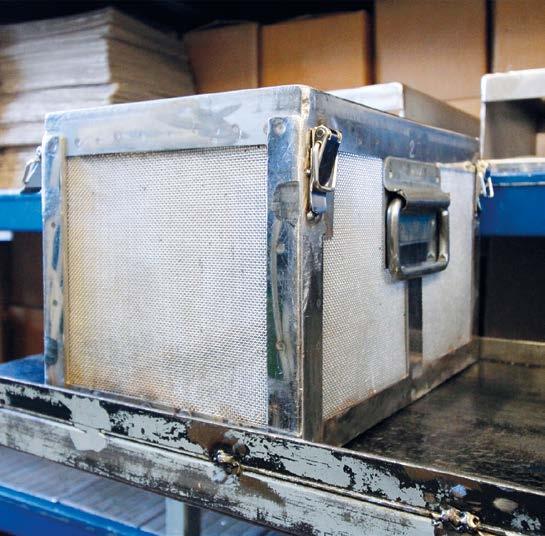
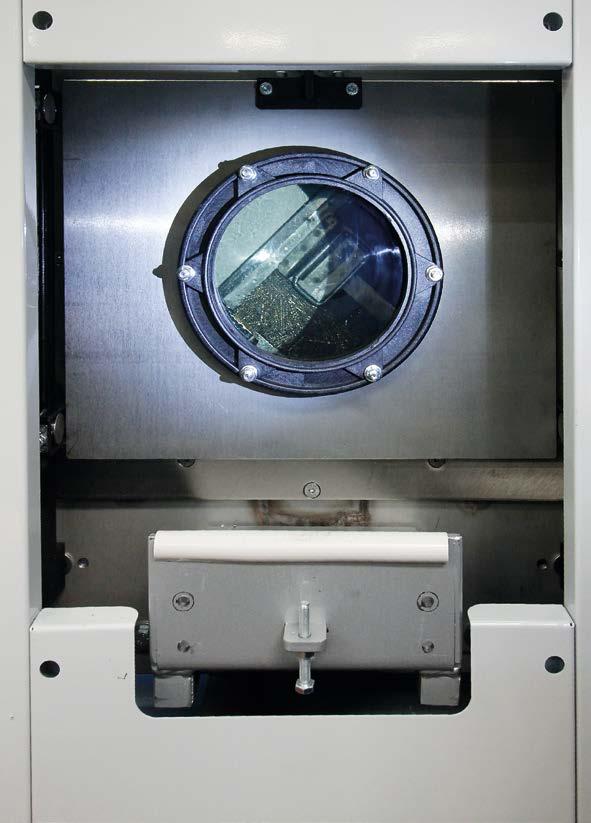
© ipcm
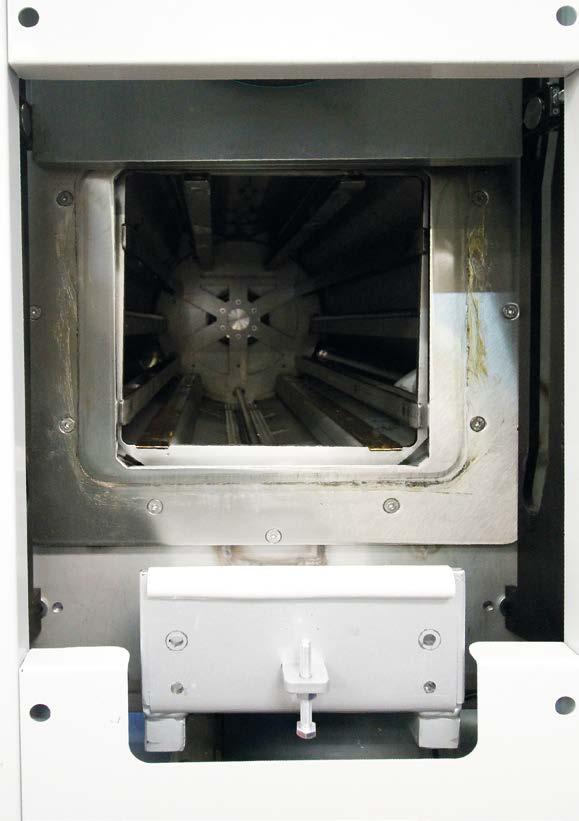
The inside of the cleaning chamber and the basket tilting in the chamber during one of the cleaning phases. Interno della camera di lavaggio e basculamento del cestello in camera durante una delle fasi di lavaggio.
© ipcm
important feature is its highly efficient internal condensation system, which means that it does not need any auxiliary cooling systems.” dovute alla manutenzione. Un’altra caratteristica importante è il sistema interno di condensazione ad altissima efficienza, grazie a cui l’impianto non necessita di sistemi di raffreddamento ausiliari”.
The cleaning cycle
The standard cleaning cycle starts with a pre-cleaning spraying phase, which removes more than 90% of neat oil from the surfaces. The modified alcohol used is immediately conveyed to the distiller to separate it from the oil. This is followed by complete immersion and activation of ultrasound, degreasing with solvent vapours conveyed inside the chamber, and final drying with a high vacuum level obtained by bringing the pressure inside the chamber below 5 millibars, in order to allow the solvent’s total evaporation and subsequent recovery. “The oil recovered by distillation,” indicates Fiori, “contains a negligible amount of alcohol, namely below 1%, and it could therefore also be
Il ciclo di lavaggio
Il ciclo di lavaggio standard prevede un prelavaggio a spruzzo con cui si elimina oltre il 90% dell’olio intero dalla superficie. L’alcol modificato utilizzato viene da subito convogliato nel distillatore per separarlo dall’olio. Segue una seconda fase di immersione completa e attivazione degli ultrasuoni, uno sgrassaggio con i vapori di solvente convogliati all’interno della camera e l’asciugatura finale con un grado di vuoto spinto ottenuto portando la pressione all’interno della camera di lavaggio al di sotto dei 5 millibar per consentire la totale evaporazione del solvente e il suo successivo recupero. “L’olio recuperato tramite distillazione – precisa Fiori - contiene una quantità di alcol trascurabile al di sotto dell’1% e potrebbe
reused in production.” At the end of the cycle, the parts are completely dry and they can be handled immediately. “The possibility of selecting the type of cleaning process depending on the part to be treated via a user-friendly touch screen,” notes Bacchetta, “has simplified the work of our two operators. Indeed, the movement of the two baskets (full rotation, tilting, or static) and the duration of the different cleaning phases can be programmed according to pre-set recipes.”
Future developments
“Another aspect not to be underestimated,” states Bacchetta, “is the aesthetics of the machine, with very clean and linear design, which would deserve a stand-alone location in the new hall that we have designed and that we will soon build to extend our current operating area and provide more space for our production department, while improving and optimising the working environment and the raw materials warehouse. We have also looked into the possibility of adding an automatic loading and unloading system, for which Cemastir’s cleaning plant has been already pre-arranged – but, given the variety of components we produce we do not intend to develop it at the moment. On the other hand, one aspect we are very interested in is the configuration of L.UN.A. in line with the Industry 4.0 parameters. During these months, we have been able to assess the performance and the cleanliness degree achieved with L.UN.A. and we are very satisfied with it. Therefore, we can conclude that the decision to use high-performance products, such as neat cutting oil and modified alcohols for its removal, is definitely our trump card for continuing on the road to excellence.”
© ipcm quindi anche essere reintrodotto nel ciclo produttivo”. Al termine del ciclo i pezzi sono completamente asciutti e subito manipolabili. “La possibilità di selezionare il tipo di lavaggio prescelto in base alla tipologia dei pezzi da lavare tramite un touch screen intuibile – continua Bacchetta – ha semplificato il lavoro dei nostri 2 operatori addetti al lavaggio. Qui sono programmabili secondo ricette preimpostate la movimentazione dei 2 cestelli (rotazione completa, basculante o statica) e la durata delle diverse fasi di lavaggio”.
La strada futura
“Un altro aspetto da non sottovalutare” – conclude Bacchetta – “è l’estetica della macchina caratterizzata da un design molto pulito e lineare che meriterebbe una collocazione indipendente nel nuovo capannone che abbiamo progettato, di prossima realizzazione, per ampliare l’attuale area operativa e offrire maggiore spazio al reparto di produzione, migliorando e ottimizzando l’ambiente lavorativo e un magazzino materie prime più efficiente. Abbiamo valutato anche la possibilità di un sistema di carico e scarico automatico, per cui l’impianto di lavaggio Cemastir è già predisposto, ma che, considerata la varietà dei prodotti da noi realizzati per ora non intendiamo applicare. Invece, una funzione che ci interessa molto è la configurazione di L.UN.A. in ottica Industry 4.0. In questi mesi abbiamo potuto valutare le performance e il grado di pulizia ottenuto e per noi si è rivelato molto soddisfacente per cui possiamo concludere che la decisione di utilizzare prodotti ad alto rendimento come l’olio da taglio intero e gli alcoli modificati per la sua rimozione superficiale sono le nostre carte vincenti per continuare sulla strada dell’eccellenza”.
Freshly cleaned parts are immediately dry and easy to handle. I pezzi appena lavati risultano subito asciutti e manipolabili.
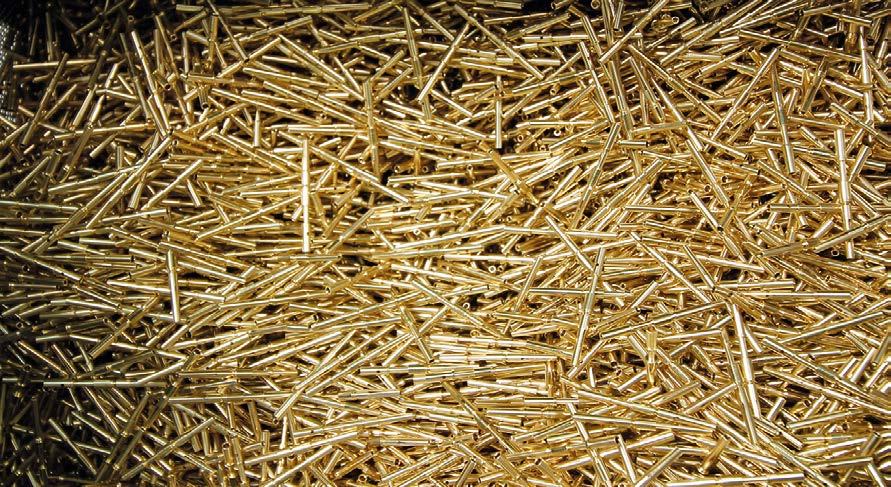