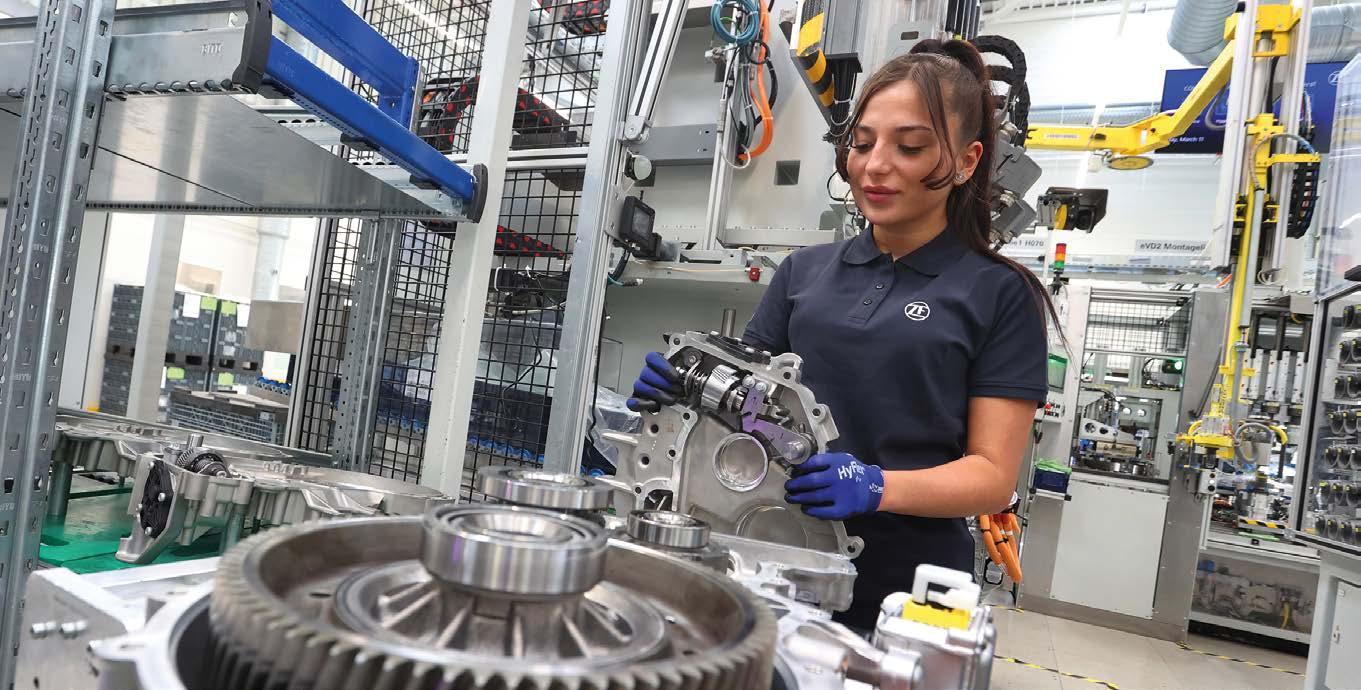
11 minute read
CASE STUDY
Electric drive stators reliably cleaned - simply with air
There was some skepticism as to whether the cleanliness specifications for e-drive stators in hybrid vehicles could be reliably met using only air as a cleaning medium. The dry cleaning system designed by Ecoclean for this specific task has by now proven successful in three-shift operation. The fully-automated cleaning process not only ensures a significant improvement in cleaning quality, but also substantial cost savings. As a result, the cleaning system pays for itself in less than nine months.
ZF Friedrichshafen AG, headquartered in Friedrichshafen (Germany), is a globally active technology group that develops and supplies systems for passenger cars, commercial vehicles and industrial technology. In the four technology domains of Vehicle Motion Control, Integrated Safety, Automated Driving and Electric Mobility, the company offers a wide range of products and software solutions for established vehicle manufacturers as well as for emerging providers of transportation and mobility services. ZF electrifies vehicles of various categories and contributes with its products to reducing emissions and protecting the climate.
© ZF Friedrichshafen AG
Differential and intermediate shaft mounting at the factory in Schweinfurt.
Montaggio di alberi differenziali e intermedi nello stabilimento di Schweinfurt.
Statori di azionamento elettrico lavati in modo affidabile – semplicemente con l’aria
C’era un certo scetticismo sul fatto che le specifiche di pulizia per gli statori e-drive dei veicoli ibridi potessero essere soddisfatte in modo affidabile utilizzando solo aria. Il sistema di lavaggio a secco progettato da Ecoclean per questo specifico scopo si è dimostrato efficiente su 3 turni di lavoro. Il processo completamente automatico non solo garantisce un miglioramento significativo nella qualità del lavaggio, bensì anche un risparmio dei costi. Il sistema si ammortizza così in meno di nove mesi.
ZF Friedrichshafen AG, con sede a Friedrichshafen (Germania), è un gruppo tecnologico attivo a livello globale che sviluppa e fornisce sistemi per autovetture, veicoli commerciali e tecnologie industriali. Nelle quattro sfere tecnologiche – Controllo Movimento Veicolo, Sicurezza Integrata, Guida Automatica e Mobilità Elettrica – l’azienda offre un’ampia gamma di prodotti e software per affermati produttori di veicoli, nonché per fornitori emergenti di servizi di trasporto e mobilità. ZF elettrifica veicoli di vario tipo e contribuisce con i suoi prodotti a ridurre le emissioni e a proteggere il clima.
The automated dry cleaning process with compressed air reliably meets cleanliness specifications and enables cost savings of around 70 percent to be made over manual cleaning - a major contribution to a speedy return on investment.
Il processo di lavaggio a secco automatico con aria compressa soddisfa in modo affidabile i requisiti di pulizia e consente un risparmio sui costi di circa il 70% rispetto al lavaggio manuale – un contributo importante per un ammortamento rapido.

The Schweinfurt site is the group’s lead plant and centre of excellence for electromobility.
Improved efficiency through automated process
Electric motors for hybrid and fully electric passenger cars have been manufactured at the plant in Lower Franconia for almost ten years. Initially, these were only produced in small series, and the stators were cleaned manually after final assembly. “Through various measures, such as a full visual inspection immediately after cleaning and regular cleanliness analyses in our lab, we have ensured that only parts meeting cleanliness specifications leave the plant. In some cases, however, this called for time-consuming and cost-intensive reworking,” reports Admir Kajevic, Production Engineer in the Electric Mobility Manufacturing Engineering division at ZF Schweinfurt. The sharp rise in demand for hybrid and electric vehicles in recent years has led to a significant increase in production capacity for electric motors. Consequently, manually cleaning stators for hybrid vehicles required considerably more personnel, so the decision was made to automate this process. “We first talked to various cleaning system manufacturers closer to home who offered us solutions with CO2 and wet-chemical processes. It was a colleague from the head office in Friedrichshafen who drew our attention to the Ecoclean Monschau’s dry cleaning process using compressed air. However, our management and employees were skeptical at first and were unsure whether the cleanliness specifications of ‘no particles larger than 600 micrometers’ in the critical areas of the stators could be reliably met using only compressed air,” recalls Admir Kajevic.
Won over by cleaning result and fast amortization time
Ecoclean provided the necessary proof by carrying out feasibility studies in the Technology Center at its Monschau site. For the test set-up, La sede di Schweinfurt è lo stabilimento principale del gruppo e centro di eccellenza per l’elettromobilità.
Migliore efficienza grazie a un processo automatico
Nello stabilimento della Bassa Franconia vengono prodotti motori elettrici per autovetture ibride e completamente elettriche da quasi dieci anni. Inizialmente erano prodotti solo in piccole serie, poiché gli statori venivano puliti manualmente dopo l’assemblaggio finale. “Attraverso accorgimenti come la completa ispezione visiva subito dopo il lavaggio e le regolari analisi sulla pulizia presso il nostro laboratorio, abbiamo sempre garantito che solo i componenti che rispettavano le specifiche lasciassero lo stabilimento. In alcuni casi, tuttavia, ciò richiedeva rilavorazioni costose e lunghe”, riferisce Admir Kajevic, Production Engineer della divisione Electric Mobility Manufacturing Engineering di ZF Schweinfurt. Il forte aumento della domanda di veicoli ibridi ed elettrici negli ultimi anni ha portato a un significativo aumento della capacità produttiva di motori elettrici. Di conseguenza, il lavaggio manuale degli statori per veicoli ibridi richiedeva molto più personale e si è quindi deciso di automatizzare questo processo. “Per prima cosa abbiamo parlato con vari produttori di sistemi di lavaggio più vicini a noi, che ci hanno proposto soluzioni con CO2 e processi a umido. È stato un collega della sede centrale di Friedrichshafen ad attirare la nostra attenzione sul processo a secco della Ecoclean di Monschau, che utilizza aria compressa. Tuttavia, i nostri dirigenti e dipendenti erano inizialmente scettici e non erano sicuri che la specifica ‘nessuna particella maggiore di 600 micrometri’ nelle aree critiche degli statori potesse essere soddisfatta utilizzando solo aria compressa”, ricorda Admir Kajevic.
Conquistati dai risultati e dal rapido ammortamento
Ecoclean ha fornito le prove necessarie effettuando studi di fattibilità nel Centro Tecnologico della sua sede di Monschau. Per l’impostazione
The gripper of the linear axis gantry (right) places the stator in the processing chamber of the dry cleaning system, which is equipped with specially adapted air tools. The cleaning step is performed in a cycle time 30 percent shorter than final assembly.
La pinza del sistema a portale ad asse lineare (destra) posiziona lo statore nella camera di lavaggio del sistema, dotata di utensili pneumatici appositamente adattati. Il lavaggio dura il 30% in meno rispetto all’assemblaggio finale.
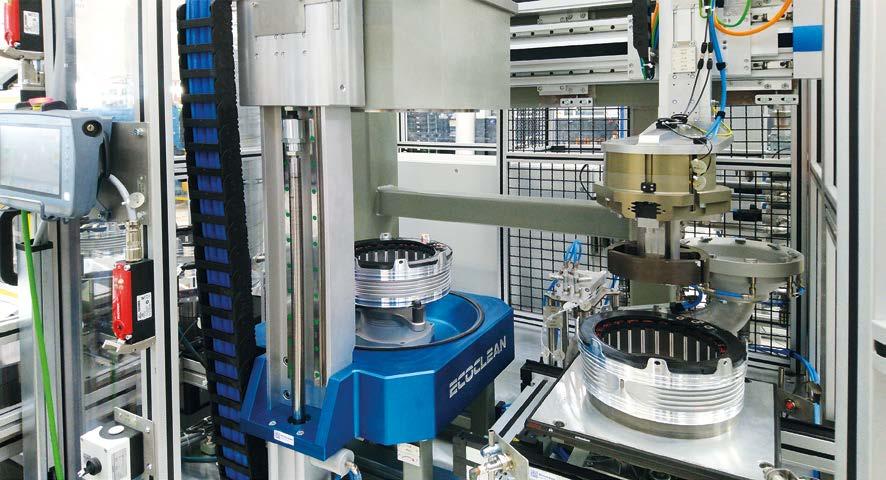
Ecoclean engineers developed air knives and a rotating device precisely adapted to the contours of the 300 mm-diameter stators. Integrated nozzles specifically designed for the part treated can be used to apply an additional, targeted jet of air in order to remove feather burrs around a clipped-in plastic ring, for instance. The air tools were manufactured by 3D printing, which meant that they could be customized quickly and cost-effectively. “We assessed the cleanliness of the stators cleaned in the trials. Already at this stage in development, the superior cleaning result - which is much more consistent than with manual cleaning - surprised us,” explains the production engineer. “Other key factors that influenced our decision to opt for the compressed-air dry cleaning system were Ecoclean’s professionalism and the payback time we calculated. It showed that a ROI would be achieved in less than eight and a half months.”
Reliable cleaning process with capacity reserves
The stators to be cleaned are placed on workpiece carriers by a robot after final assembly. These are then advanced into the cleaning system by a transfer conveyor. The stator is then picked up and placed in the processing chamber by a gantry system. Once this chamber is closed, the cleaning process begins. Compared to the upstream process, the cycle time specified for cleaning is around 30 percent shorter. “This shorter cycle time requirement gives us a reserve capacity for cleaning which will come in handy when we accelerate final assembly,” notes Admir Kajevic. To prevent parts from becoming recontaminated, a specially-designed air extraction system generates a constant airflow that continuously removes detached particles from the processing chamber. Parallel to the cleaning process, a blower cleans the gripper of the gantry system in a dedicated blow-off station. This ensures that no particles are transferred by the gripper to the cleaned stator as it is removed from the processing del test gli ingegneri di Ecoclean hanno sviluppato lame d’aria e un dispositivo rotante adattato con precisione al diametro di 300 mm degli statori. Degli ugelli integrati progettati appositamente per i pezzi trattati possono essere utilizzati per applicare un getto d’aria aggiuntivo e mirato al fine di rimuovere, per esempio, le bave attorno ad un anello di plastica agganciato. Gli utensili ad aria sono stati prodotti con stampa 3D, ciò significa che possono essere personalizzati in modo rapido ed economico. “Abbiamo valutato la pulizia degli statori durante i test. Già in questa fase dello sviluppo l’eccellente risultato – molto più uniforme rispetto al lavaggio manuale – ci ha sorpreso”, spiega l’ingegnere di produzione. “Altri fattori chiave che hanno influenzato la nostra decisione di optare per il sistema ad aria compressa sono stati la professionalità di Ecoclean e i tempi di ammortamento calcolati. Il ROI sarebbe stato raggiunto in meno di otto mesi e mezzo”.
Processo di lavaggio affidabile con riserve di capacità
Dopo l’assemblaggio finale gli statori da lavare vengono posizionati da un robot sui portapezzi. Questi avanzano poi nel sistema di lavaggio grazie a un convogliatore. Lo statore viene quindi prelevato e posizionato nella camera di lavaggio da un sistema a portale. Una volta chiusa la camera il processo di lavaggio ha inizio. Rispetto al processo a monte, il tempo ciclo specificato per il lavaggio è più breve di circa il 30%. “Questo ciclo più breve ci consente di avere una capacità residua, che torna utile quando acceleriamo l’assemblaggio finale”, precisa Admir Kajevic. Per prevenire la ricontaminazione dei manufatti un sistema di estrazione dell’aria appositamente progettato genera un flusso di aria costante che rimuove continuamente le particelle distaccate dalla camera di processo. Parallelamente al processo di lavaggio, un soffiatore pulisce la pinza del sistema a portale in una stazione di soffiaggio dedicata. Ciò garantisce che nessuna particella venga trasferita dalla pinza allo statore pulito
chamber. After cleaning, the part is placed on a clean goods carrier and forwarded to an integrated final inspection workstation. Here, a worker performs a visual inspection in which the entire workpiece carrier is lifted out, enabling the part to also be inspected from underneath. The next step is the packing station. The compressed-air dry cleaning system has been in use at ZF Schweinfurt in three-shift series operation since June 2021 and continues to meet all expectations. “Compared to manual cleaning, the automated process gives us significantly improved and much more consistent results. This is confirmed by the cleanliness analyses we perform once a shift based on a procedure described in VDA 19. We have also been able to reduce cleaning costs by around 70 percent,” says the production engineer.
High economic efficiency arouses interest
News about the good cleaning results, high cost savings and fast ROI have spread within the ZF Group. It is not surprising that Admir Kajevic is being contacted repeatedly to provide information about his experiences with the compressed air dry cleaning system. His satisfaction with the solution has already led to numerous inquiries at Ecoclean. mentre questo esce dalla camera. Dopo il lavaggio, il componente viene posizionato su un portapezzi pulito e inoltrato ad una postazione di ispezione finale integrata. Qui, un operatore esegue un’ispezione visiva durante la quale il portapezzi viene sollevato per poter ispezionare il componente anche da sotto. La fase successiva è l’imballaggio. Il sistema di lavaggio ad aria compressa è in uso presso ZF Schweinfurt su tre turni dal giugno 2021 e continua a soddisfare tutte le aspettative. “Rispetto al lavaggio manuale il processo automatico dà risultati decisamente migliori e molto più uniformi. Questo è confermato dalle analisi che effettuiamo una volta per turno in base ad una procedura descritta nello standard VDA 19. Siamo anche stati in grado di ridurre i costi di lavaggio di circa il 70%”, afferma l’ingegnere di produzione.
L’elevata efficienza economica suscita interesse
All’interno del Gruppo ZF si è diffusa la notizia dei buoni risultati di lavaggio, dell’elevato risparmio e del rapido ROI. Non sorprende che Admir Kajevic venga contattato ripetutamente per fornire informazioni sulla sua esperienza con il sistema ad aria compressa. La sua soddisfazione ha già fruttato numerose richieste ad Ecoclean.
© ZF Friedrichshafen AG More Information
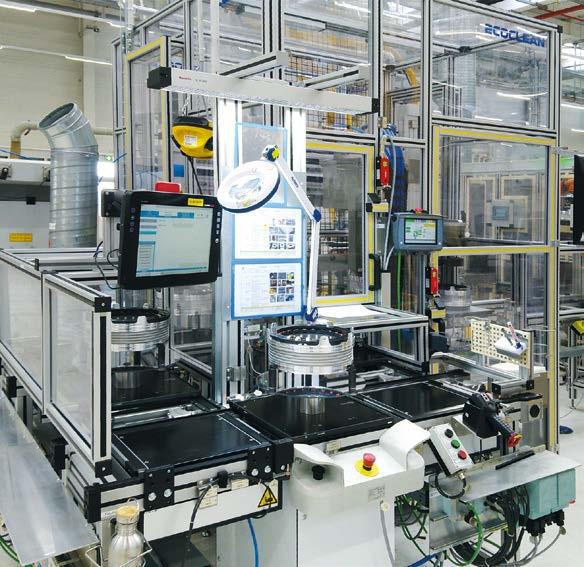
Clean Workpieces.
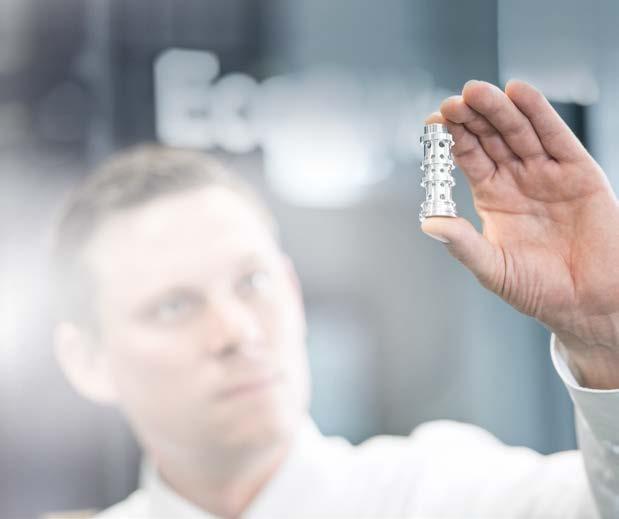
Economical and Sustainable.
www.ecoclean-group.net
A workstation for the final inspection of the cleaned stators is integrated into the dry cleaning system. Not only here, but also the cleanliness analyses in the laboratory, which are carried out once per shift, confirm the superior cleaning results. Nel sistema è integrata una stazione per l’ispezione finale degli statori puliti. Gli eccellenti livelli di pulizia sono confermati non solo qui, ma anche durante le analisi eseguite in laboratorio una volta per turno.
Solvent Cleaning Aqueous Cleaning Ultrasonic Cleaning
High-pressure Waterjet Deburring Surface Processing & Selective Cleaning