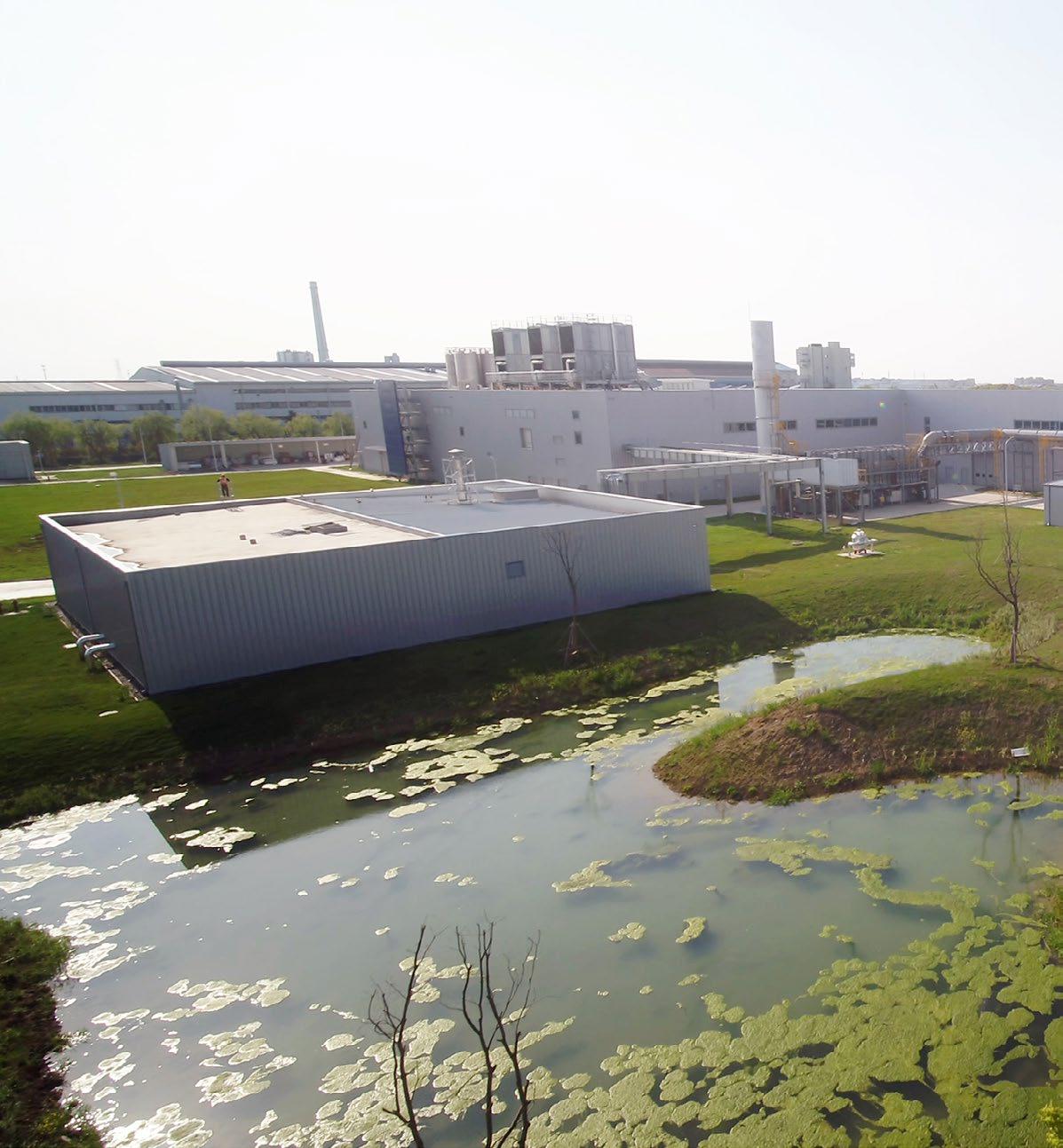
24 minute read
SIG
State-of-the-art facility demonstrates SIG’s engineering excellence and sustainability leadership
SIG’s second state-of-the-art production plant for aseptic carton packaging in China is now up and running. Despite challenges posed by the pandemic, the large-scale project has been successfully implemented, once again demonstrating SIG’s ongoing commitment to engineering excellence and sustainability leadership.
The new plant is located close to SIG’s existing production facility at the Suzhou Industrial Park (SIP), which allows for shared resources in both production and operations. The new facility is also close to SIG’s Asia Pacific Tech Center, with industry-leading innovation capabilities that bring a flow of new concepts and solutions to SIG customers. Having the Tech Centre nearby ensures SIG can keep pace with, and anticipate, new trends.
Samuel Sigrist, CEO of SIG: “The Asia Pacific region continues to be one of the major growth engines for aseptic carton packaging. The expansion of our production network will enable us to further strengthen our position in the growing Chinese market. It also means we can respond more quickly to the needs of our customers to provide holistic solutions to the food and beverage industry.”
By building a second production plant in China, SIG is committed to serving the Chinese market by providing high-quality products and services

to customers across the Asia Pacific region. The entire production process in the new plant is managed intelligently, which significantly improves operational and production efficiency. The smart manufacturing system covers extrusion, printing, creasing, cutting and sealing.
Samuel Sigrist continues: “SIG has built up a strong customer base across the Asia Pacific region, providing outstanding innovation capability and end-to-end solutions for differentiated products, smarter factories and connected packs. Our close partnership with the two largest Chinese dairies, and other food and beverage companies, will continue to grow and develop.”
By 2024, the new plant will cover an area of 120,000 square metres and is expected to have an annual production capacity of 8 billion carton packs. It has been designed and built to have the lowest possible carbon emissions, with an artistic combination of classical Chinese garden and modern elements. Photovoltaic panels on the roofs can provide 1.5 million kWh of solar energy and collected rainwater is also reused after treatment to save around 28,000 tonnes of tap water per annum. In addition to energy-saving lighting devices, special lighting systems are installed to significantly reduce electricity consumption. The new plant’s best-in-class environmental, safety and operation performance has already been recognised with a prestigious international industry certification: LEED (Leadership in Energy and Environmental Design) gold certification for building design and construction. LEED is a green building certification programme created by the U.S. Green Building Council which is used worldwide. SIG’s new packaging plant was the first plant in China’s aseptic packaging industry to be built in strict accordance with the LEED gold certification standard.
Watch our video
For insights into trends that drive the food and beverage industry and inspire us to innovate, visit our SIGnals blog: https://www.sig.biz/signals/en
Spray lubrication for baked goods production: plant manufacturer Sugden invests in technotrans solution
Technotrans SE is further expanding its activities in the food industry. Sugden Ltd, one of the leading manufacturers of production lines for bakery products, is investing in the high-precision spray lubrication system spray.xact food. The first technotrans units will be used as mobile versions in the British plant manufacturer’s pancake and Multi-Plant Lines. Thanks to the low-mist, compressed-air-free application of release agent, Sugden users save resources, improve their product quality and prevent unwanted oil residues in the production environment. The technotrans system is to be installed in other Sugden plants in the future, including those for Vanderpol Waffle production.
“Our goal was to completely eliminate the use of compressed air when applying release agents to our heated plate systems. In this way, we offer our customers even more process reliability and control. With the help of the technotrans solution, we have succeeded in doing just that. In addition, product quality increases and line operators save resources,” says George Jackson, Sales Manager at Sugden. The company develops and manufactures customized industrial baking systems - for English muffins, crumpets and pancakes, among others. In these systems, products are cooked directly on a hot plate to which a release agent is applied. When looking for a new and, above all, easy-to-integrate spray lubrication solution, the company opted for a system from technotrans after only a few test runs.
The challenge in this baking process is, on the one hand, that the release agent is viscous, which makes precise application difficult. On the other hand, conventional, compressed air-driven solutions often produce aerosols that can be inhaled by employees without the use of extraction equipment and can accumulate in the production environment. With the help of spray.xact food from technotrans, Sugden prevents these problems. The temperature-controlled valves ensure optimum viscosity of the release agent to be applied, which ensures a precise spray pattern. There is no need for an extraction system, as spray.xact food spray lubrication does not produce any unwanted mist.
OPTIMALLY ADAPTED TO THE BAKING PROCESS Stuart Packer, New Business Development Manager at technotrans, also emphasizes the flexibility and adaptability of the system. “With spray.xact food, customers are able to adjust all relevant parameters from speed to spray quantity according to their needs. Each spray valve can be individually programmed in the process.” technotrans transfers this flexibility to the design of the unit. For the Sugdens project, a mobile version was developed that is mounted on a trolley system and can be moved freely. George Jackson also praises the partnership with technotrans: “The cooperation was fantastic. The teams in Germany and here in the UK have been extremely helpful in running product trials and giving us valuable information back to help us in design and application.” Due to the Covid 19 constraints, most of the coordination from project planning to go-live took place virtually. Despite these limitations, Jackson says the project proceeded in a focused and efficient manner. “The exchange with the technotrans team and the successful implementation of our requirements quickly convinced us, so the decision was really easy for us.”
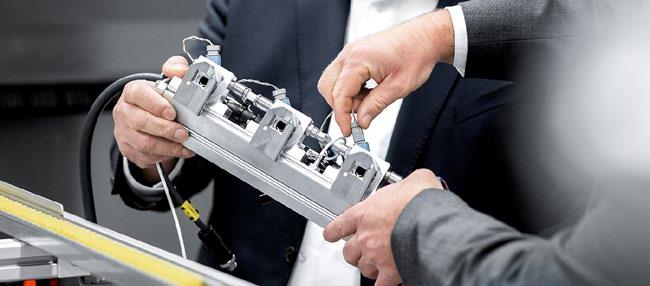
Sugden would like to continue the collaboration in the future. The manufacturer plans to integrate the spray.xact food system on further pancake and Multi-Plant Lines, as well as well as on the Vanderpol Waffle Lines the company is currently designing and manufacturing.
For more information see: www.technotrans.de
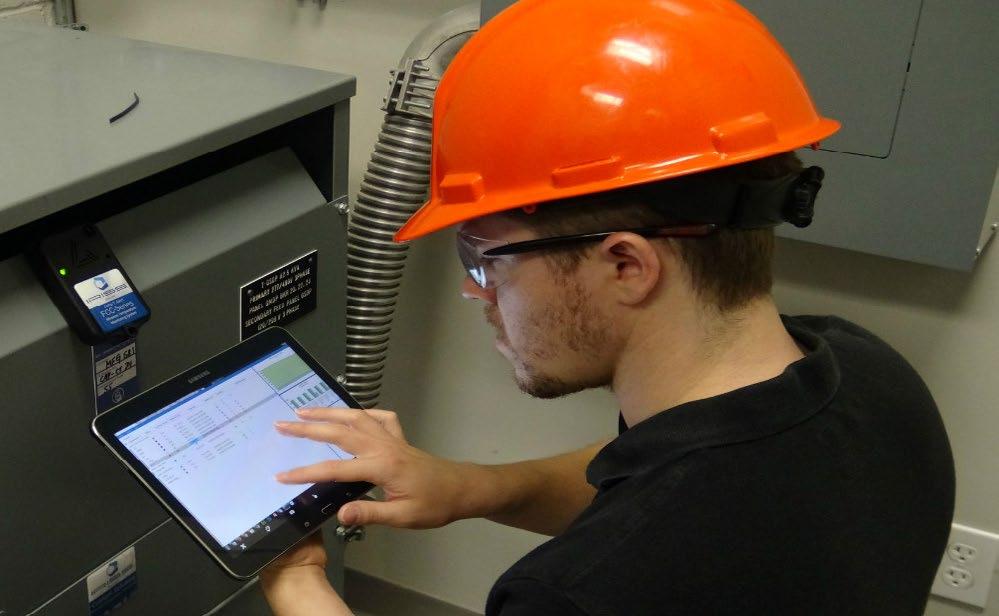
Industrial Reliability & Safety in 3 Steps
By Michael Riccio, CRL, CAT-1 IRT Global Marketing Manager, IRISS Inc.
The critical importance of electrical power to every aspect of our world cannot be exaggerated. It must be generated and distributed effectively to end-users, and any disruption in that process means loss of operations, money, and in extreme cases, life. Therefore, the reliability of electrical power creation and distribution must be continually safeguarded and improved. This does not happen by chance or through reactionary-maintenance tasks, and it must be focused on from the early design stages and continue through the life of the assets tasked with these functions.
Adopting a “Monitor, Inspect, & Manage” approach is a proactive way to avoid the concerns at hand by maximizing the value of workforce time and skill. Scalability is no longer an issue when, instead of going through the time and cost of expanding their workforce, they can apply condition-based reliability technologies to maximize their available workforce skills and availability. These Reliability Technologies can be specified with the specification engineer and Original Equipment Manufacturer at the initial design/build stage or retrofitted into existing equipment through a simple and inexpensive process.
MONITOR
With the use of a monitoring system on transformers and throughout substation electrical equipment, asset conditions can be continually collected, trended, and assessed. Monitors feed data through a gateway to software and apps, allowing the information to be continuously accessed from workstations and mobile devices. When the new equipment arrives from the manufacturer with these monitors built-in, customized parameters can be set for the specific operating and environmental conditions the asset is exposed to that keep it within a “safe zone” to maximize functional reliability. When the asset condition data exceeds the custom parameters, alarms can notify electrical technicians of a possible issue that may require inspection. Keeping human interaction with equipment to only instances where confirmation inspections of potential faults are deemed necessary minimizes workers’ risk and eliminates the humanerror threat to asset functionality.
INSPECT
Once the wireless monitoring system notifies technicians of a possible issue with a transformer or other piece of electrical equipment, the use of pre-
installed inspection windows on the asset allows a safe, efficient method of inspecting and assessing any possible issue during an energized condition. Once solely designed for thermographic inspections using infrared cameras, advancements in manufacturing have led to the inclusion of ports that allow for ultrasound and partial discharge technologies to be incorporated into the inspection. Visual, infrared, and ultrasound inspections can be done simultaneously by a single employee.
Additionally, this design protects inspectors from arc flash/electrocution risk, removes the need for bulky and expensive PPE, and allows the inspection to be accomplished more efficiently. Not only does this represent a significant process improvement driven by original design, but it also falls in line with the most recent NFPA 70E updates and continues to protect critical assets from human interaction/mistakes that may cause failure.
MANAGE
The data collected during inspection can be stored through intelligent asset management tags attached to the pre-installed inspection windows. From the asset location, information can be transmitted into a dashboard system accessible from workstations and mobile devices.
Customizable routes can be established before, and condition reports generated after data analysis to further increase efficiency. These designed aspects allow managers to assess operations and decide how best to increase Mean Time Between Failure (MTBF).

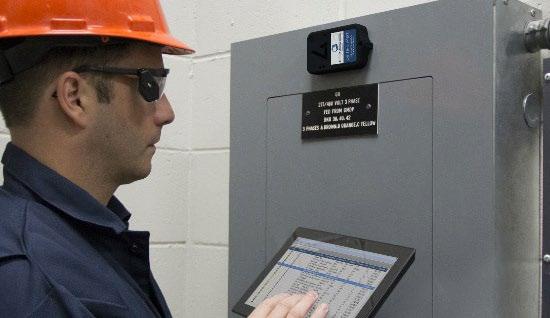
PROPER TRAINING
One major issue facing the industrial world is a coming wave of retirements from the workforce, with fewer new workers entering the industry than the pending need created by this exodus. As the electrical industry expands worldwide, creating the need for a larger workforce, the problem is multiplied. The only way to succeed is to capitalize on reliability technologies designed into the system that allows the industry to do more with less.
While Designing for Safety & Reliability from the equipment-side should drive the overall process toward continuous improvements, the proper tools are only as useful as the hands wielding them. Hardware and software designed/ specified by the engineer and constructed by the OEM are ineffective if the people responsible for their oversight are not adequately trained.
Shifting to an engineered reliability system for the electrical maintenance team means training new and veteran staff alike. With “Monitor, Inspect, Manage,” the use of technology allows single individuals to accomplish inspection tasks with minimal training. Specialized skill sets of electricalfocused staff can be used for actual necessary maintenance/repair activities.
CONCLUSIONS
From the inception of equipment design and manufacture, all possible measures to ensure asset reliability should be specified and implemented. These measures should prove themselves to be learnable, repeatable, and continued throughout any workforce changes to cement the successful practices into the very culture of the role requirements.
Transformers and other critical electrical power assets being monitored remotely cut down on technicians’ routine tasks focused on engineering and electrical operations by providing around-the-clock coverage. When an alarm notification is received, correctly designed and installed inspection windows allow an individual technician to easily do visual, infrared, and ultrasound, and partial discharge assessments of the energized equipment. The data collected on the asset can then be stored, trended, and analyzed through the management software. This process increases the Mean Time Between Failure (MTBF) by allowing for planned shutdown and maintenance only when it is necessary.
www.iriss.com
Experience global know-how locally: New products from Minebea Intec at PPMA this September
After most of last year’s trade fairs were cancelled due to COVID, Minebea Intec has broadly positioned itself for this year’s upcoming events: The leading provider of weighing and inspection solutions presents new products and powerful software tools that increase the efficiency and output of production plants. The first UK trade fair to take place for the industry since the pandemic will be PPMA this September.
NEW LABELLING SOLUTIONS PORTFOLIO: FOUR FUNCTIONS IN ONE DEVICE
PPMA is taking place 28-30 September in the heart of the Midlands at the NEC, where a range of exhibitors will present products related to packaging and processing. In the exhibition halls in Birmingham, the two new price labelling solutions WPL-S and WPL-A from Minebea Intec will be on show for the first time.
With the manual price labelling system WPL-S and the automatic variant WPL-A, Minebea Intec is opening up a new portfolio for applications in the weighing and labelling of products. Both labelling solutions offer the ideal complete package for customers in the food industry: weighing, price labelling, labelling and product traceability in just one device. However, it is not only new products that will be presented at the show - some of the manufacturer’s products have received a major upgrade.
ACCURATE HIGH-SPEED WEIGHING
In production, maximum output with high quality is one of the top priorities: highspeed weighing is therefore currently an exciting topic in the industry. Minebea Intec has given its checkweighers with EMFC technology a turbo upgrade and 10 FDPP - www.fdpp.co.uk
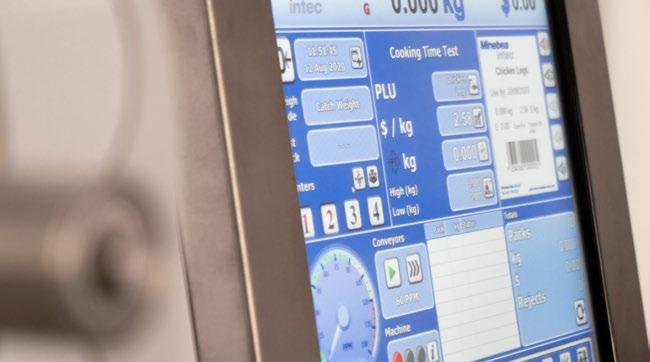
equipped them with a new load cell. The inspection solutions have received MID approval for belt speeds of up to 3 metres per second. This means that up to 600 products per minute can be accurately and reliably weighed. With the new load cells, the minimum weight has also been lowered: products of just 5 grams can be weighed accurately and reliably.
SPC@ENTERPRISE SOFTWARE: FOR ADDED EFFICIENCY
In addition to the optimal weighing solution, Minebea Intec also offers the right software to optimise efficiency and production capacities: Among other things, SPC@Enterprise, a software package for statistical process control and average weight control, will be presented at the trade fair.
SPC@Enterprise is currently available in version 4.0 and includes all the necessary options for prepacked goods and statistical process control, such as the collection of random samples as well as automatic checks throughout the entire process. By networking a wide range of devices and systems, the user has the option of statistically evaluating the collected data from the checkweighing of finished products as well as other measured values from the overall process, reacting with suitable measures and thus increasing the efficiency of his production.
DIGITAL OFFER: FREE OF CHARGE AND AVAILABLE AROUND THE CLOCK
In addition to physical trade fairs, the new Minebea Intec digital contact options remain. Interested parties will find a wide selection of free offers on the website. Minebea Intec offers two options for consultation and research on weighing and inspection solutions: interested parties can either book an appointment in the Virtual Showroom, where experts provide advise and answer questions. Alternatively, there are several online calculators to choose from which can be used to calculate the return on investment, for example. The webinars are the perfect compliment: in just 45 minutes, participants gain an insight into various issues relating to weighing and inspection solutions. Missed webinars can also be viewed afterwards at the participants convenience.
PhoenixTM solution to HACCP Cook & Chill CCP Validation
As part of any Food processors HACCP program, validation of cook and chill processes is a critical and significant task, taking time, effort, and resources.
PhoenixTM have developed a thruprocess temperature monitoring technology specifically for this task, designed to meet the challenges of the food processing market. Ideal for the validation process for any new cook regime, new product, or annual process certification. Whether performing an oven survey “oven mapping to identify cold spots” or validating the cook under production conditions, the thru-process profiling solution gives you the accuracy, efficiency, and reliability you need to satisfy your HACCP demands.
As its name suggests, thru-process profiling is the method by which product and or process temperature is monitored throughout the complete cook / chill process. The data logger making the physical temperature measurement, with multiple thermocouples, travels safely with the product through the process. Protection from process conditions such as heat, steam, water, and oil is provided by a suitably designed thermal barrier. The thermal barrier provides robust protection to the data logger to prevent damage but also ensure that it maintains a safe operating temperature to give accurate temperature readings. Monitoring of continuous conveyorised linear and spiral ovens and semi-continuous or rotational batch cooks is feasible where the use of external recorders with trailing thermocouples is tedious, completely impractical, and possibly unsafe . Employing the thru-process principal, process monitoring can be performed under true production conditions without compromising line productivity . At the heart of the thru-process monitoring system is the PhoenixTM data logger. The PhoenixTM NT data logger range has been designed specifically for the challenges of monitoring food processing applications with an IP67 case design protecting from moisture. Type K or Type T data logger options allow accurate measurement of both cook and chill processes (Type T measurement range -200 °C to 400 °C). Data logger and thermocouple correction factors can be applied to the recorded data logger data to maximise measurement accuracy. PhoenixTM offer a range of thermal barriers to suit the process type, duration, and temperatures. Even if a standard thermal barrier cannot meet the process requirements, PhoenixTM can often custom design a unique solution to suit.
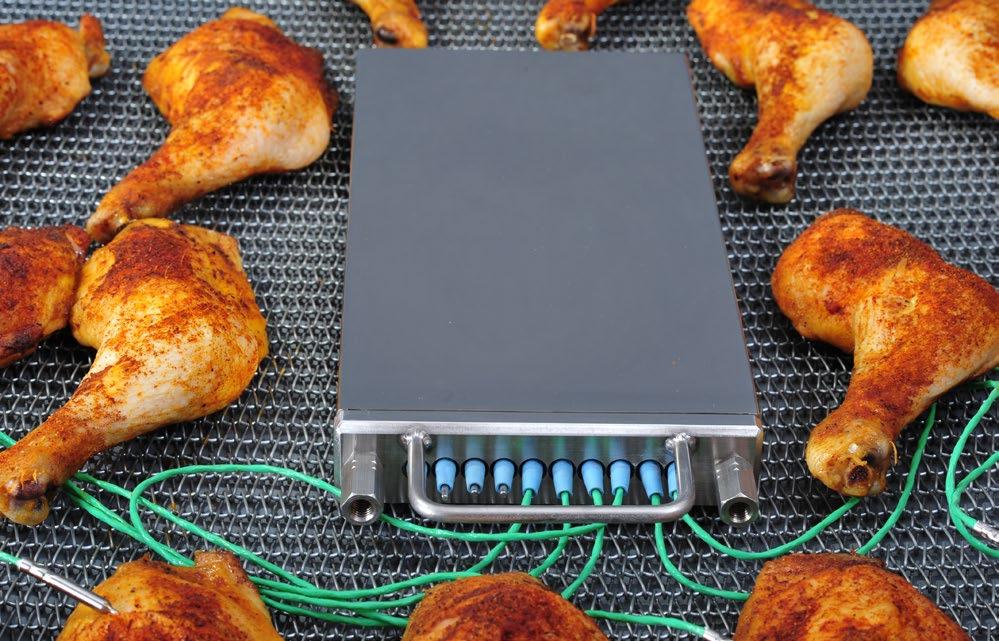
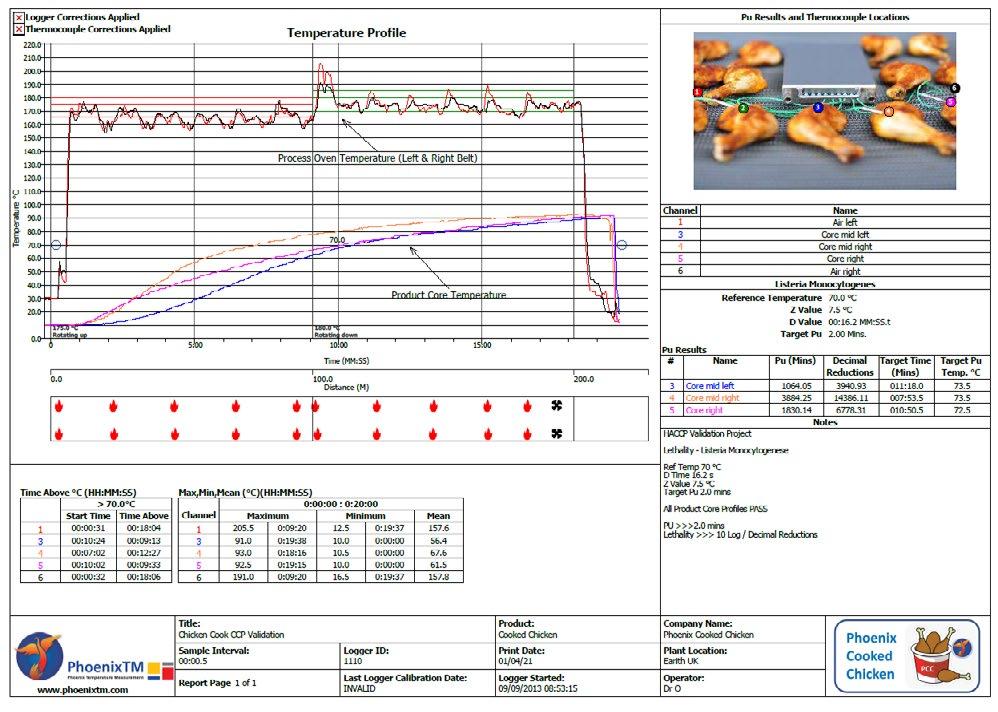
Monitoring core temperatures of food products can be a challenge and getting it right or wrong can have a significant influence on the data collected and therefore any decisions or conclusions made. PhoenixTM offer a range of different designs of thermocouple to suit different product types and sizes. The needle thermocouples ensure you can measure the true core/cold spot of the product accurately and repeatably. Fitted with standard miniature thermocouple sockets, the data logger is also compatible with other generic commercially available thermocouple designs.
Employing the thru-process temperature monitoring principle provides the food technologist with a complete temperature profile of the cook process from start to finish. This information is like the Cook DNA giving full details of the product and or process temperature which is invaluable to allowing validation of the Cook CCP. From a temperature profile it is possible to accurately quantify product safety (pasteurisation) knowing both the temperature, and time at temperature, of the product. Employing the thruprocess temperature monitoring principle provides the food technologist with a complete temperature profile of the cook process from start to finish.
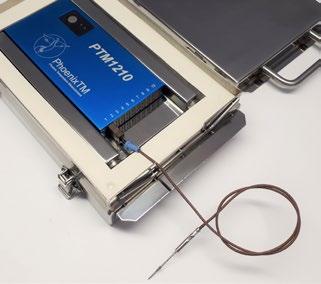
From the profile graph you can see instantaneously the variation in product temperature at any point in the process either at different locations on the product (whole chicken) or different product positions within the cooker, cooking rack or across a mesh belt. The PhoenixTM Thermal View Food Software provides a comprehensive suite of analysis tools to convert the raw profile temperature data into useful process information. The analysis tools include the ability to calculate Fo/Pu values for the process against target micro-organisms. For a typical chicken cook process the lethality parameters for Listeria Monocytogenes (Tref 70 °C, Dt 16.2 s and Z value 7.5 °C) can be input to automatically and accurately calculate for each monitoring point the number of decimal reductions of the pathogen achieved during cook to meet CCP limits.
The information gathered, further to process validation, can be used to allow informed process problem solving and optimisation to maximise product quality, yield, process productivity and efficiency.
Contact PhoenixTM to help Find, Fix and Forget your Food Cook Problems!
Smart Solutions from AutoCoding Systems
AutoCoding Systems was acquired by JBT Corporation in February of this year and now not only enjoys the support of a major US company, but also has the opportunity to work jointly on packaging line applications with their sister company, Proseal.
As a global provider of automation solutions to factory production and packaging areas, AutoCoding Systems has developed a suite of modular software products to facilitate processes such as device integration, data collection and integrity, packaging verification, code deployment and code inspection.
Food and beverage suppliers are under increasing pressure to meet increased production schedules whilst maintaining the highest standards in product quality and safety. This can be achieved with increased automation, removing the human element of the packaging line set-up thereby reducing the risk of errors.
The core AutoCoding product deploys secure set-up and message data to packaging line devices, including coders, barcode scanners and inspection equipment, irrespective of brand. By automating these time-consuming processes, downtime during job set-up and changeovers is greatly reduced and the risk of coding and packaging errors minimised.


Over the years, AutoCoding Systems has expanded functionality with the addition of value-add modules offering greater scope for the collection of data. For example, the Paperless Quality module automates both in-line and off-line routine quality checks. The AutoCoding line terminal can be configured to individual requirements creating various methods for capturing data which can then be used for reporting purposes. QA checks can be mandated at the beginning, during and end of a production run with details of all checks consolidated into the AutoCoding audit log. This not only creates an unbroken audit trail of QA checks, but also results in a reduction of physical paper records that must be retained and subsequently stored.
AutoCoding Systems’ latest innovation in automatic print inspection is 4Sight. Checking the presence, legibility and location of printed codes is often challenging, particularly at high speeds.
The 4Sight software resides on the SICK camera, communicating directly with the printing equipment. It works with all brands of printers and understands the intended message for printing. The solution can be set to differing levels of inspection from print presence to full OCR and users can configure acceptable print tolerances depending on the application, thereby reducing the number of nuisance stops.
Other modules include Inspection Reporting to monitor the performance of, and collect data from, multiple checkweighers, metal detectors and x-ray equipment whilst the Line Performance Reporting module captures real-time manufacturing data which can then be visualised in customisable reports to display accurate packaging line / device / product performance data.
Manufacturing, construction, and engineering are a big part of our economy
But those workers also face a greater likelihood of serious work injuries than other workers.
IN 2019/20 the HSE reported that 111 workers were killed in workplace accidents and 69,206 non-fatal injuries were reported by employers.
Machinery accidents cost employees billions every year and on average employees who are injured usually have to take weeks off work or may never return.
WOULD YOU TAKE THAT CHANCE?
Lockout Tagout is an essential tool in the control of hazardous energy, in a wide range of industry sectors to prevent accidents.
What are hazardous energy sources?
Hazardous energy sources include electrical, mechanical, hydraulic, pneumatic, chemical, thermal, or other sources in machines and equipment.
The unexpected start-up or release of stored energy is immensely dangerous for any employee/operative in close proximity to the machine.
Which form of energy is lock out tag out used to control?
Lock out tag out is a hazardous energy control system used to ensure that machines and equipment are totally isolated from all energy sources. Locks are used to secure switches and valves in the OFF or SAFE position.
Lock out tag out is still the best-known practice for this protection and should be utilized any time the machine or equipment is being cleaned, maintained, and inspected. As well as for company shutdowns, turnarounds, power outages and more.
What is the difference between lock out and tag out?
Lock out means to place a lock on a device that prevents energy release. Tagout means to place a tag on a switch or other shut off device that warns not to start that piece of equipment.

WHAT ARE THE 10 STEPS OF LOCK OUT TAG OUT?
Lock out tag out can easily be implemented by following this simple 10 step process,
1. Prepare 2. Notify 3. Turnoff 4. Isolate 5. Lock/s Application
Recognising the importance of a lock out tag out system is the first step towards implementing an effective safety process. It is not the whole solution, but it can clearly contribute, below are our simple lockout/tagout tips to follow • Clearly identify padlocks and tags either personally or departmentally. • Allow time & apply actions to relieve any stored/residual energies. • Ensure Lockout equipment is suitable for the intended task.
• Develop a written programme, with process & procedures with all details that MUST be followed.
• Any new machines must have a written programme/procedure developed against it. • All new & existing staff are to be trained and made aware of LOTOTO, it’s dangers and how to implement safely. According to the standard operating procedure (ongoing activity). • The only person to remove a lock is the one who applied it. • Implement and review the Lockout
Tagout process and procedures annually. Update and improve where required. • You must Try-Out every time.
Confirming the success of the isolation before proceeding with the task.
STAY ALERT AND DON’T GET HURT!
It goes without saying that industrial equipment can be dangerous, that’s why safety measures, process, products,
and personal protective equipment are used when using them. But machinery can also present hazards when it is not in operation and that’s why lockout/tagout is governed by strict regulations UK wide, such as
• HASAW 1974
• Electricity at work Regs 1989 • PUWER Regs 1998 – Reg 19 for isolation from Sources of Energy • Quarry Regs 1999 • OSHA 1910.147 – Control of
Hazardous Energy - osha.gov
The purpose of these regulations is to prevent injury and fatality. Contact with moving machinery and isolation (including stored energy) is still in the fatal 6, identified high consequence hazards.
Employers must develop, implement, and enforce an energy control program in line with regulations. As well and providing the correct Lockout Tagout equipment to fulfill the procedures in place.
RISK ASSESSMENT
Lockout Tagout is a process designed to reduce/eliminate risk, when performing high risk tasks. A risk assessment should be conducted each time a task occurs with potential risk. The machine/ task specific written energy control procedures will ensure every task has the risk assessed before any action commences. Potentially a one-off task outside of the norm can arise, meaning any works on said task should have a risk assessment conducted by a qualified & authorized representative to control this project. A newly written energy control program should be completed in case of a future re-occurrence.
LOCKOUT TAGOUT SAFETY CHECKS
Audits and visual inspections should be regularly carried out by a competent person, following the specific guidance outlined through regulations and company process/procedures. At least annually, a full audit and site survey should be completed to ensure that all equipment is of high quality, in good working order & in the required volumes to complete tasks. Additionally, the audit should cover and fulfill any newly updated/improved regulations.
It’s also worth noting, any new piece of machinery on site which will require isolation and its energy controlled. Should have a standalone machine specific energy control program written against it (working closely with the manufactures guidelines on its energy sources and moving parts) and trained out to all affected employees. All new employees should be trained to the level of every operative on site with CONCLUSION
Lockout Tagout is not an optional activity! The responsibility to govern this within establishments begins at the top. To instill the culture, behavior, and awareness to a high standard throughout.
Major industries are adopting the LOTOTO process due to the awareness and associated real-life risks. It is now being recognised as best practice for safety management in quarries, oil & gas, heavy manufacturing, food processing plants and more. Sectors such as renewable energy, waste and large retail companies are beginning to apply company-wide procedures utilising LOTOTO to ensure employee and operative safety with a structured and controlled procedural method.
We’ve got a lot of work to do to lockout machines better and control hazardous energy more effectively. Lockout/tagout is not the whole solution it should be combined with effective lockout training.
At Spectrum Industrial we can help by conducting a lockout/tagout survey to help you identify what you need, you can download our eBook to find out what is involved in a lockout/tagout survey.
Or click here to contact us.
Remember, “Short cuts, may cut a lift short!”.
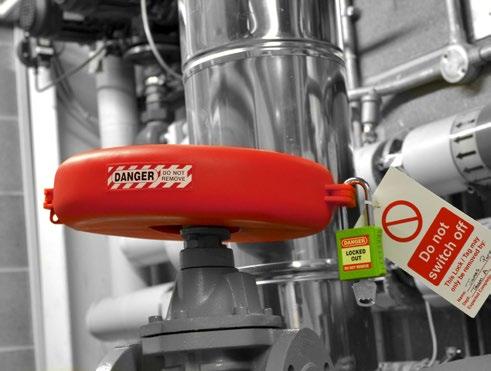
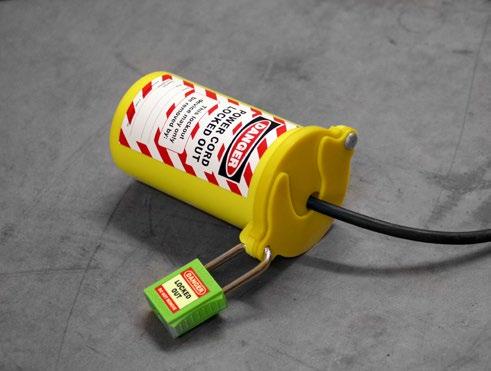