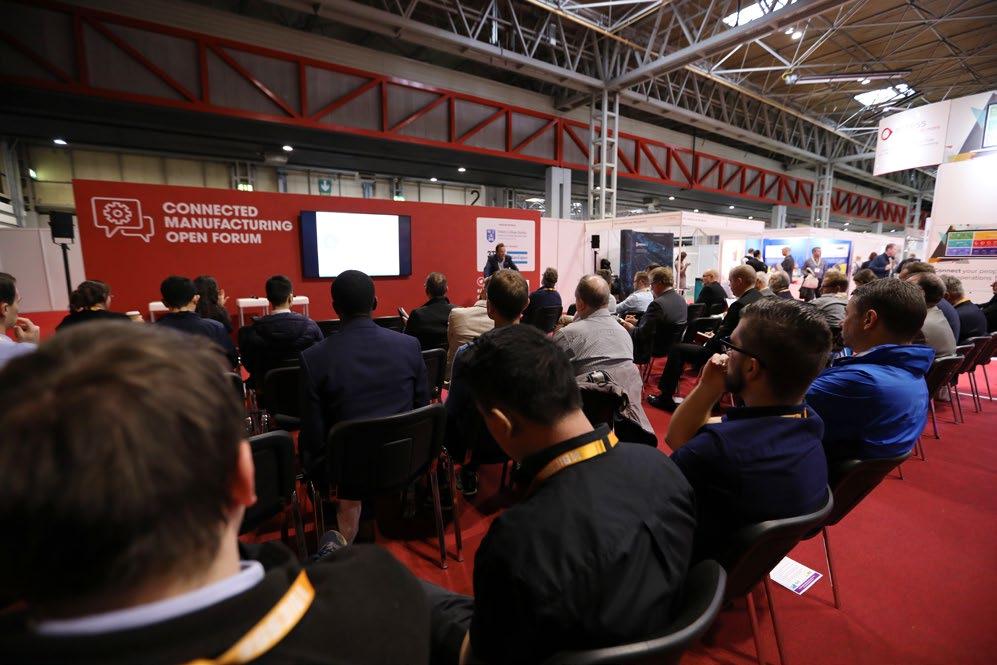
7 minute read
ADVANCED ENGINEERING
Advanced Engineering is back with a bang in 2021
The UK’s largest annual gathering of engineering professionals, Advanced Engineering, will return to the NEC, Birmingham on November 3 and 4, 2021. Here, the UK’s talented and vast engineering industry can meet again for the first time in almost two years to do business, make new connections and discover innovation.
This year, there will be seven show zones — aerospace, composites, automotive, performance metals, connected manufacturing, medical devices and, new for 2021, space and satellite. Also, for the first time, Advanced Engineering UK’s sister show, Lab Innovations, will take place in the same hall. Advanced Engineering UK hopes that having so many sectors under one roof will enable crossindustry collaboration and the formation of new business relationships after 18 months of limited interactions.
There will be four forums held during the two-day show, featuring some of the leading voices from engineering and manufacturing. A huge topic at the aerospace forum this year is decarbonising aviation. During the show, there will be presentations on electrification, zero-carbon aviation and hydrogen propulsion from the Aerospace Technology Institute, Rolls-Royce, Ampaire, ZeroAvia and ID TechEx. Supply chain management is a concern for many companies this year, so Advanced Engineering UK will welcome talks from Airbus UK and ADS on supplier expectations and supply chain excellence. morning dedicated to space and satellite engineering, with talks from the UK Space Agency, Skyrora, D-Orbit UK and the Space Applications Catapult.
At the automotive forum, electrification and sustainability will also feature as major themes, with talks from JCB, Ford, the Advanced Manufacturing Research Centre (AMRC), Jaguar Land Rover and many more.
On the composites stage, visitors can find out more about what digitalisation means for composite manufacturing, the 3D printing of composite parts and how composites are enabling the UK’s move towards its net-zero carbon emissions targets. Composites UK CEO, David Bailey will return along with the National Composites Centre’s Head of Digital Engineering, Marc Funnell. BAE
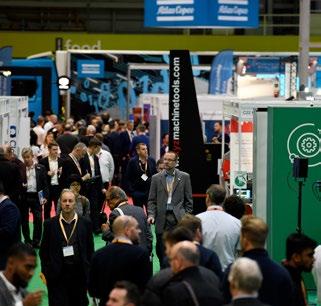
Systems and Transport for London will also take to the stage.
During the connected manufacturing forum, Ian Gardner, Industry 4.0 and Oracle Specialist at IBM and Stephen Phipson, CEO of Make UK, will deliver keynote speeches. They’ll be supported by speakers from the Connected Places Catapult, Brunel University London and IoT North, to name a few.
As well as its impressive speaker programme, Advanced Engineering UK will be supported by some of the world’s key industry associations, such as The Institution of Engineering and Technology (IET), Composites UK, Make UK, the Institution of Mechanical Engineers, GAMBICA, BARA and the Department for International Trade, all of whom now feature as trade body partners.
Advanced Engineering UK is the go-to show for anyone wanting to meet the world’s leading engineering companies, plus the UK’s most innovative startups, thanks to the return of the show’s Enabling Innovation zone, supported by Innovate UK. Here, ten chosen start-ups will have the opportunity to showcase their ground-breaking product or technology, before presenting it to a panel of esteemed judges for the chance of winning a stand at next year’s show.
The show already has several exciting features confirmed, including an original prototype of the ExoMars rover, created by Airbus Defence and Space. The rover, commonly known as Bruno, is semiautonomous and equipped with all the same technology as the final rover, including the sensors, actuators and cameras that allow the rover to see in 3D while navigating Mars. Advanced Engineering UK’s new show zone dedicated entirely to space and satellite innovation will be Bruno’s landing site for the show, and can be found in the existing Aero Engineering floor.
Also on display will be RS Electric Boat’s Pulse 63. The boat’s power source is a battery pack derived from the automotive industry, which harnesses a RIM drive unit rather than a traditional propeller, increasing the boat’s efficiency and offering a lightweight power solution. The boat is zero emission and the most sustainable laminate of any RIB in the industry. More features will be announced in the coming weeks.
Advanced Engineering offers a great opportunity to meet suppliers, partners and generate business leads for the first time in over a year. Already, the show’s exhibitor space is 90 per cent sold out – a sign that our industry is eager to come together again. In 2019, over 10,000 professionals from the manufacturing sector attended Advanced Engineering. 70 per cent of visitors reported that they planned to place orders as a result of the relationships formed and an impressive 93 per cent of exhibitors reported that they achieved their objectives at the show.
This year, Advanced Engineering UK is also relaunching AE Connect, a digital platform that is used to schedule meetings ahead of the show. In 2019, the platform was used to schedule 588 meetings, which generated an average order value of £200,000 per meeting held. After 18 months of limited inperson meetings, it’s understandable that businesses might not have as many connections as they usually would by this time of year. AE Connect allows both exhibitors and visitors to make the most of their time at the show by filling their diaries with valuable meetings beforehand.
“Advanced Engineering UK marks the return to face-to-face business, which the UK has been craving since March 2020,” explained Alison Willis, Director at Easyfairs, the organizer of Advanced Engineering. “The show offers the UK’s engineering industry the chance to get together again, do business and discover the innovative technologies and products that have been created in the past year.”
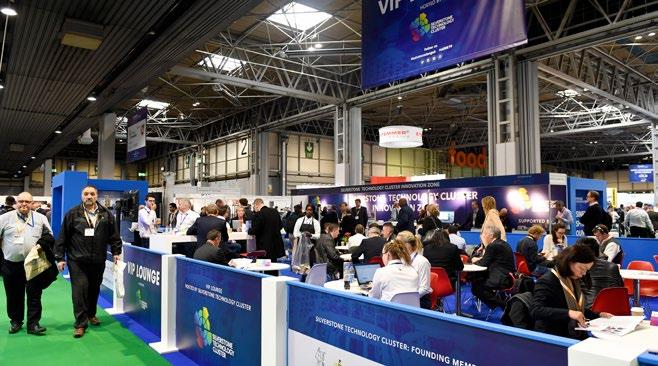
Are you ready to meet some of the UK’s top innovators in engineering? Register to attend Advanced Engineering 2021 on November 3–4 via the exhibition’s website, www.advancedengineeringuk.com. FDPP - www.fdpp.co.uk 91
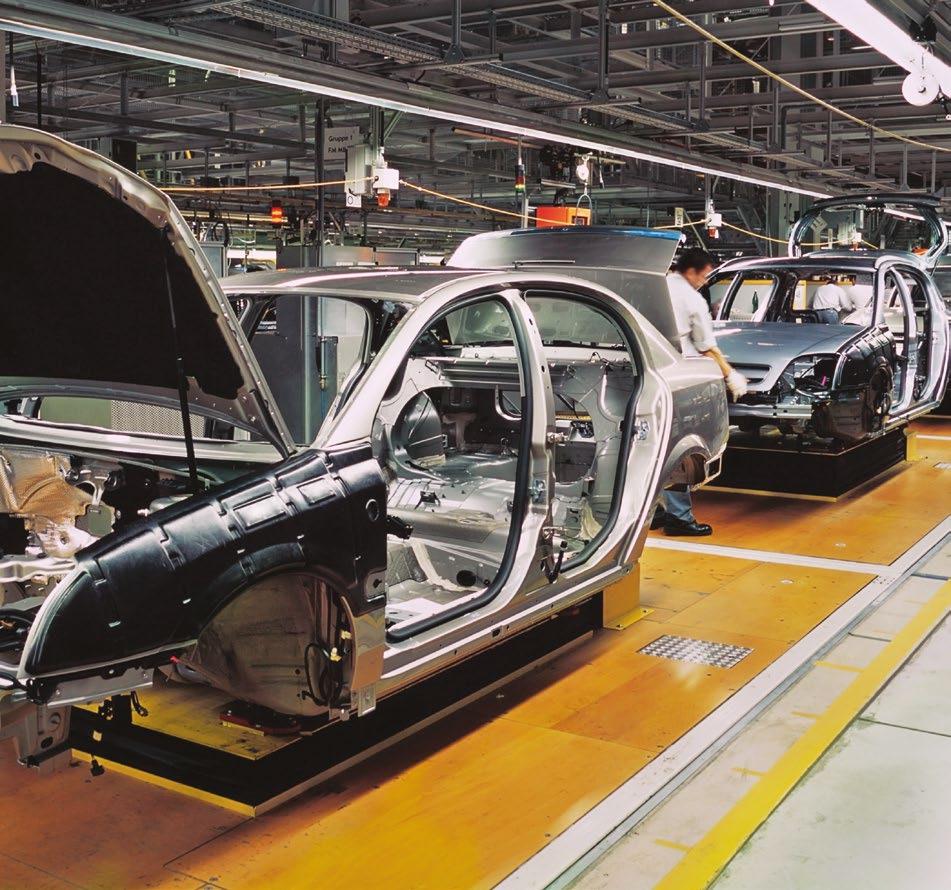
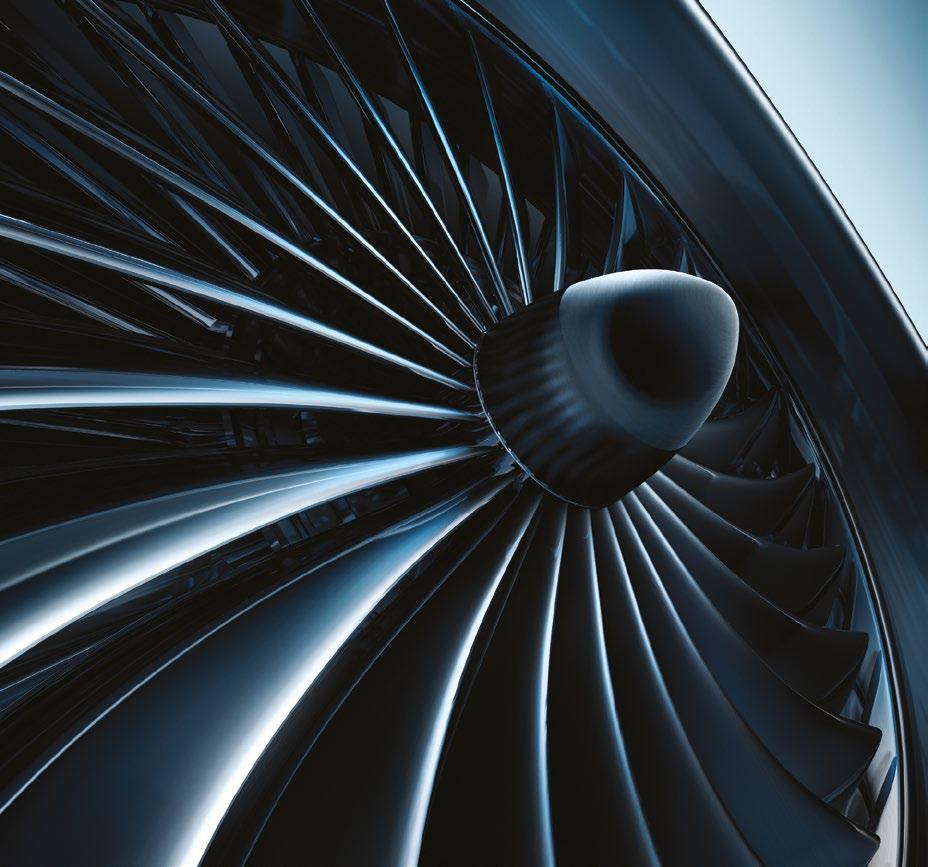
Are You Still Inserting Documents and Marketing Material into Shipments Manually? Read How a Small Investment Can Save Your Business $500,000 Annually
PSI Engineering is the global expert in pack station automation. We manufacture and integrate automation solutions for the last 100 feet of the order fulfillment line. With applications in any industry that packs and ships product, we can provide solutions for all your pack station needs.
Case Study: A rapidly growing online grocery delivery company and their consultant were working to open new fulfillment centers designed and optimized to fulfill orders quickly and efficiently. The Company is committed to delivering fresh, locally-sourced products to customers at reasonable prices and therefore need to ensure orders are accurately and rapidly processed to keep operating costs low.
Included in every order is a thank you card, a referral card (with a personalized promo code), and a flyer advertising promotions or new products. These inserts vary in size from 6.5”x7.5” to 8.5”x14”. For new customers, a welcome brochure was also included with their first order.
At existing facilities, document printing and insertion is completed by a team of 10 operators at individual packing tables where they manually pick preprinted materials, print the promo code on the referral card, and insert the right documents and marketing material into orders. This manual process results in a high error rate where the wrong code gets sent to the wrong customer or the wrong advertisement is inserted. Finally, since the amount of material required varied, there was often too much or not enough material available.
Working with PSI, the Customer and Consultant decided that the packing tables were to be converted to a single pack line with a straight run conveyor and three in-line PSI Print Feeders (one document type per machine). As the carton containing the order moves along the conveyor, the barcode is scanned prompting the Print Feeder to print the appropriate promotional flyer, referral card with personalized promo code, and personalized thank you card and inserts it into the order. One PSI LC In-Feeder was installed downstream of the Print Feeders to include a welcome brochure if the order was for a new customer.
Introducing this automated pack line eliminated document insertion errors which got the orders out the door twice as fast. The Company now saves $500,000 annually on labour costs by reducing the staff required to complete this transaction.

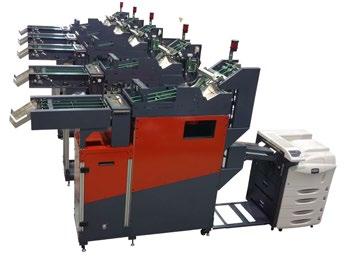

info@psiengineering.com www.psiengineering.com
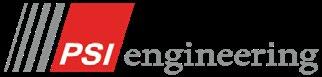