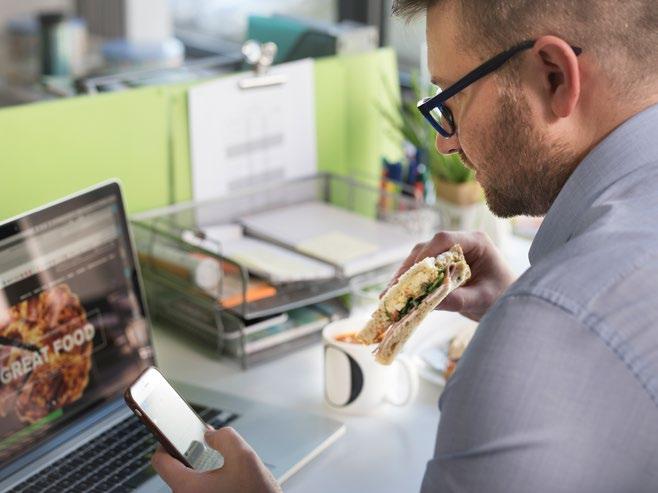
22 minute read
GREENCORE
Fully-recyclable sandwich packaging to be trialled in UK supermarkets
Greencore Group plc (‘Greencore’ or the ‘Group’), a leading UK manufacturer of convenience foods, is delighted to announce that, in partnership with the Coop and Sainsbury’s, it will soon commence ‘test and learn’ trials of an all fibre plastic free recyclable sandwich skillet in stores across the UK.
The packaging, developed in conjunction with ProAmpac and believed to be the first of its type in the world, marks the culmination of 18 months of research and development by Greencore. The skillet will have a plastic-free window and be made entirely from paper-based material; crucially, due to the precise level of moisture resistance the skillet provides, it will see products have the exact same shelf life as if they were they packaged in a traditional skillet.
Data shows that consumers currently find it challenging to separate the plastic film from the packaging of a typical sandwich skillet, meaning that recycling rates are nowhere near as high as they could be. The new skillet’s all-paper construction will make the process much easier for consumers. Subject to successful trials, which commence in September 2021, and the proposition meeting all parties’ performance criteria, roll-out of the new packaging will begin later in the year. In time, Greencore expects to make these new packaging techniques available to the wider UK market.
Development of the fully-recyclable skillet sees Greencore deliver on one of the key commitments outlined in its 2020 Sustainability Report. The Sustainability Report also contains a range of pledges across the areas of sourcing, manufacturing, and community engagement. Further commitments include:
• All surplus product will be donated to local communities by 2022 • A deforestation-free supply chain by 2025
• All raw materials will be sustainably sourced by 2030 • Product development will be equally split between animal protein versus plantrich alternatives by 2030.
It is estimated that some 600 million pre-packed sandwiches are consumed in the UK every year, or just over 1,100 every minute. Should the fully-recyclable skillet ultimately be adopted as industry best practice, the potential for significant reductions in plastic usage and in improved recycling rates is immense.
Andy Wright, Head of Sustainability at Greencore, commented:
“Consumers are increasingly aware not just of the importance of their own health but also of the impact their food has on the health of the planet. Developing a fully recyclable sandwich skillet is one of the key ways we can reduce waste and help our customers do their bit to protect the environment.
“This is not a problem we can solve alone, though. The complexities of the challenges we face require collective action, inside and outside our industry, and Greencore is pleased to have such supportive customers who share our enthusiasm for making great food for all, that’s accessible, healthy and sustainable.”
Breige Donaghy, Director of Delicious Food, Co-op, said:
“We’ve worked closely with Greencore from the start on the development of the compostable sandwich packaging and implemented the first trial of its use in our pop-up store at Glastonbury Festival in 2019 with great success.
“The trial aligns with Co-op’s ambition to reduce the use of virgin plastic and how we’ve also worked to ensure that all of our own-brand packaging is now fully recyclable. We’re looking forward to seeing the new packaging on shelves this autumn and are confident it will resonate with our members and customers.”
For further information go to www.greencore.com or follow Greencore on social media.
Machinery Moves, Installation, Relocation and Technical Lifting project expertise for the Food, Beverage, Distilling & Brewing Process Sectors
Based in project offices throughout the United Kingdom, the RRS Group is an experienced machinery relocation and installation contractor with significant knowledge in the food and beverage process sectors.
Our expertise includes installation and relocation services for projects on tanks, process lines, filling, mixing and bottling lines, packaging systems, distilling process equipment, conveying lines, canning and sealing, plastics, card and corrugated packaging and all associated utilities plant moves.
The RRS Group has decades of experience in project planning, health and safety, quality and commercial awareness to meet all sizes of budgets whether a single machine move or a large capex turnkey installation project under CDM Regulations. Our engineered solutions, project management, skilled site personnel and lifting and installation plant/ equipment are the core ingredients to our successfully delivered site projects. We welcome discussions on budget proposals and future project ideas as well as planned projects or last minute requirements
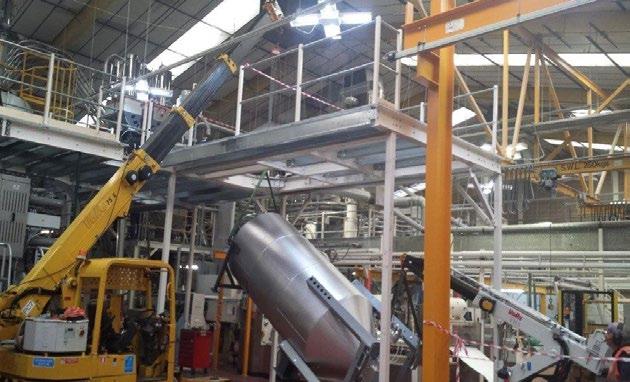
E: info@rapidrs.co.uk T: Projects HQ : 023 92669714 W: www.rapidrs.co.uk
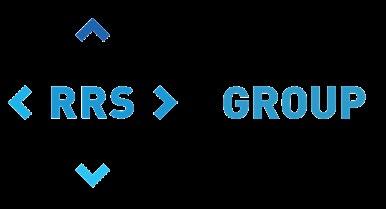
Precision Laser Converting Equipment For Packaging

Production level automated folding carton cutting and creasing systems using CartonsInMinutes®
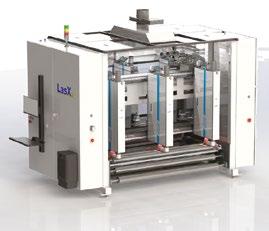
Flexible laser scoring and perforating equipment for easy open and breathable features
Roll-to-roll or roll-to-part converting systems
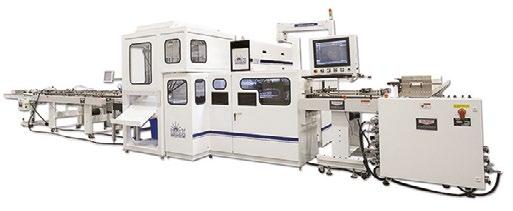
Sheet-fed laser finishing with automated robotic part handling Introducing a brand NEW wide-web equipment series to meet your flexible packaging needs.
2021
Meet LaserSharp® FreshFocus.
Competitvely priced | shorter lead time: Powered by LasX technology
Sheet-fed laser cutting systems to cut complex designs
Partnership between TLM Laser and LasX Europe serving the United Kingdom market
Eliminate Manual Handling, Reduce Risk and Improve Safety with a North Ridge Mobile Pump Kit
Manual handling is one of the most common methods utilised for the transferring of ingredients and waste within wholesale food manufacture. With over 30% of injuries reported to HSE being a direct result of manual handling - when the budget is simply not available to have a fully automated food production system; handling different products in a safe sanitary manner can often prove quite difficult.
Ensuring a production process meets all the current hygienic and food safety regulations is one of the main challenges facing any wholesale food business however one of the most often missed opportunities are investments into automating part of production to improve safety, reduce risk and wastage, increase accuracy or eliminate manual handling. The North Ridge bespoke food grade pump kits are often a solution to this.
CUSTOMER’S REQUIREMENT
When a traditional family run bakery established for over 50 years required a fully hygienic, easy to clean method to transfer Fruit Jams, Toffee Sauce, Fruit curds and Whipped cream they approached us to see if we could help. The variety of products posed a real challenge to ensure components did not wear prematurely, that damage could not be easily performed to the pump and that the customer had a low maintenance solution.
Some of the products were manually dispensed from cooking kettles at high temperatures into their current process at an average temperature of 100 - 110 °C, whilst other fluids which were incredibly viscous, were stored within refrigerators prior to use and needed pumping from cold to maintain hygiene. The customer wanted a bespoke multipurpose solution for their processes, which was sanitary grade, easy to clean, capable of handling all the products in question without manual handling, and suitable for high viscosities and temperatures up to 120 °C.
The unit also had to have a gentle pumping action due to the shear sensitivity of the whipped cream. High temperature liquids can have a negative impact on seals shortening their lifespan, cause issues at pump suction ports and reduce overall pump lifespan if careful consideration is not taken during pump selection.
Their current procedure involved manually transferring sauces via totes and buckets, however the customer wanted to improve their process to automate food transfer, reduce the likelihood of burns or accidents, and eliminate manual lifting and tipping of containers. They needed a custom costeffective unit that operates similar to a semi-automatic liquid filling machine.
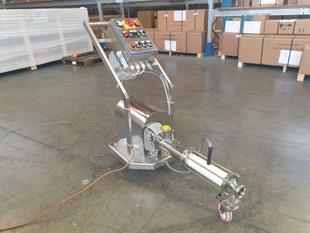
OUR MOBILE AUTOMATED PUMP SOLUTION
We supplied a completely bespoke mobile pump system with an integrated control panel. The pump is 3A sanitary certified, suitable for CIP (cleaningin-place) and SIP (sterilization-inplace) and designed without dead zones where product can build up preventing bacterial growth and cross contamination when handling different liquids. We also ensured the exterior of the unit was easy to clean during spray down by fitting a stainless-steel shroud covering both motor and gearbox. Besides having an integrated inverter for varying flow, the control panel has several other safety and operation features, to enable Start/Stop, reversing of the unit, alarm for motor overload and temperature control sensor to prevent damage from dry running.
The inverter can also be controlled via an App where operators can also view the status of the pump, reduce speed which is essential with some fluids such as Whipped Cream and further avoids the repeated contact of controls by multiple personnel.
PROJECT OUTCOME
Thank to our pump kit the customer improved their production efficiency dramatically, which in the food industry translates as an increase in profitability. The layout enabled users to operate the unit with very little training due to the simplicity of design but also built-in protection ensures the unit cannot be damaged through misuse. Social distancing has been easy to maintain through the use of remote controls, and as processes are automated less personnel are present within confined areas.
If you would like to talk to someone about automating a food transfer application contact us on 01773 302 660, or visit our website at www. northridgepumps.com to see our previous case studies.
We’re pump We’re pump specialists, so you specialists, so you don’t need to be don’t need to be

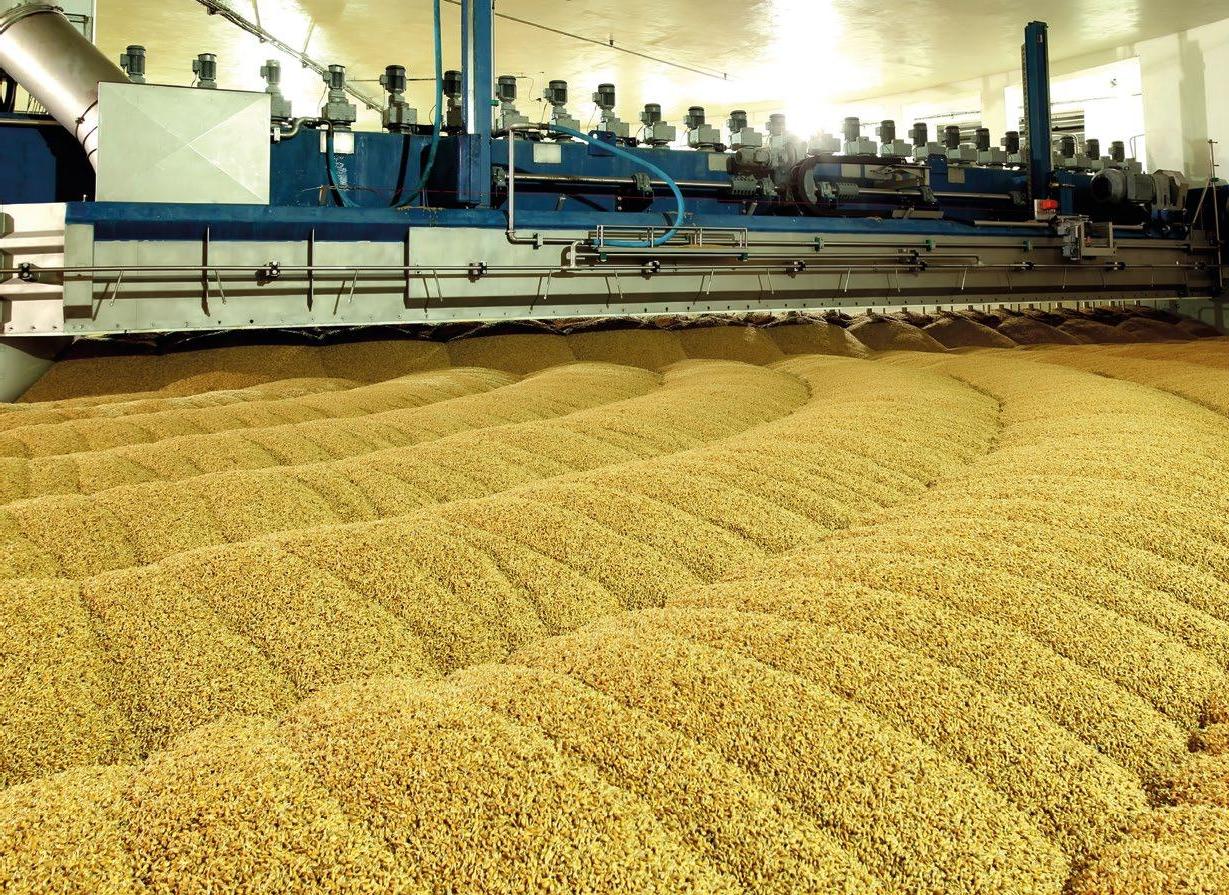
Sanitary Pumps Sanitary Pumps Engineered for Your Process Engineered for Your Process
Optimise performance with specialist support Optimise performance with specialist support
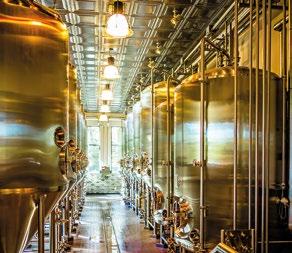
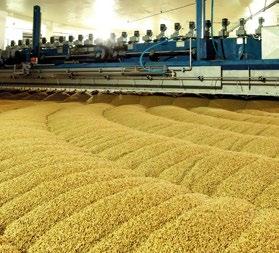
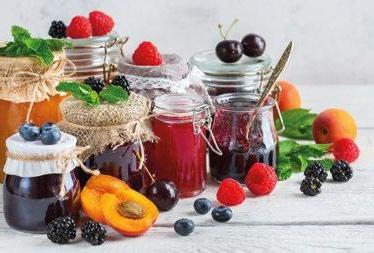
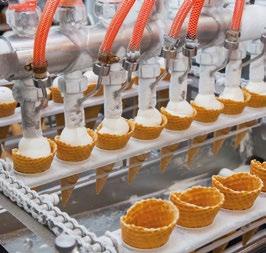
Whether you’re dealing with clogging, separation, downtime, or other issue - Whether you’re dealing with clogging, separation, downtime, or other issue - it’s costly. Time wasted troubleshooting and lower production mean missed it’s costly. Time wasted troubleshooting and lower production mean missed targets and less profit. A sanitary pump is the solution but choosing the right targets and less profit. A sanitary pump is the solution but choosing the right one feels like stepping into a minefield. You know what you need it to do but one feels like stepping into a minefield. You know what you need it to do but with so many options, it’s difficult to know which is best for your process and with so many options, it’s difficult to know which is best for your process and parameters. parameters.
++ Accelerated stator wear Accelerated stator wear ++ Clogging Clogging ++ Changes to fluid consistency Changes to fluid consistency ++ Clean-in-place and sterilise-in-place hygiene issues Clean-in-place and sterilise-in-place hygiene issues ++ Crushing of sensitive products Crushing of sensitive products ++ Inconsistency in finished product Inconsistency in finished product ++ Inaccurate transfer of flavourings or ingredients Inaccurate transfer of flavourings or ingredients ++ Liquid separation Liquid separation ++ Seal wear or failure Seal wear or failure We’ve been engineering sanitary pumps We’ve been engineering sanitary pumps for sectors such as distilling, brewing, food for sectors such as distilling, brewing, food manufacturing/processing, and more, for manufacturing/processing, and more, for 20+ years. We understand industry-specific 20+ years. We understand industry-specific processes and know what it takes to optimise processes and know what it takes to optimise performance through better-suited pump performance through better-suited pump design - giving you complete peace of mind. design - giving you complete peace of mind.
EXPERT GUIDANCE: EXPERT GUIDANCE:
Our expert engineers understand your process Our expert engineers understand your process and guide you through the options, so you and guide you through the options, so you can confidently select the most suitable can confidently select the most suitable sanitary pump. sanitary pump.
EXAMPLE PRODUCTS: EXAMPLE PRODUCTS:
++ Abrasive mixtures Abrasive mixtures ++ Creams, milk & ice cream Creams, milk & ice cream ++ Edible oils & fats Edible oils & fats ++ Fish & meat Fish & meat ++ Fruits eg. cooked apples, Fruits eg. cooked apples, plums, berries, grapes plums, berries, grapes ++ Grains & seeds Grains & seeds ++ Pastes & purees Pastes & purees ++ Syrups, juices & alcohols Syrups, juices & alcohols ++ Vegetables & peelings Vegetables & peelings ++ Waste eg. trimmings, Waste eg. trimmings, packaging & offcuts packaging & offcuts ++ Sheer sensitive liquids Sheer sensitive liquids ++ Solid laden or viscous Solid laden or viscous mixtures mixtures
Panasonic Minas A6 Multi Servo Drive system: European design, Japanese technology
Panasonic’s new MINAS A6 Multi 400V servo drive system has been specially developed for the European market. It has a slim, 50mm wide, book size format and each servo driver can control two axes allowing space requirements in the cabinet to be reduced by up to 64% compared with standard drives.
Integrating the MINAS A6 Multi into an EtherCAT interface network is easy and is complimented by 18 integrated safety functions meaning the MINAS A6 Multi complies with SIL / PLe safety guidelines.
The systems modular design means multiple drives can be connected to a single power supply and linked with a simple and reliable DC Bus Link system.
Low, Middle and High inertia motors are extremely compact where length and weight are reduced by up to 15% over a standard motors and are currently available in the range of 400W up to 5kW with power levels as high as 22kW soon to be introduced.
All motors offer IP67 protection with robust, rotatable connectors complying with IEC, CENELEC, and IEEE standards. The 23 bit encoder offers high resolution in both absolute and incremental mode with battery less absolute operation supported.
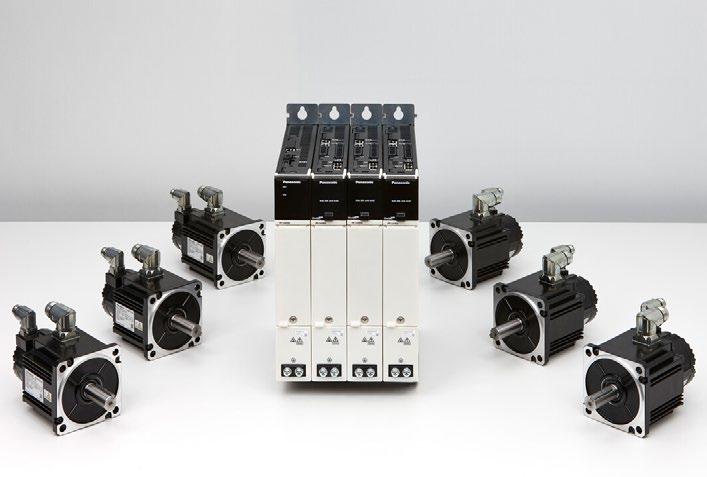
For more information contact Bob.Norfield@eu.panasonic.com
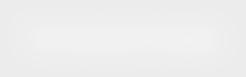
The new bar code reader.
Perfect performance on the conveyor line.
Our new BCL 200i bar code reader is specialized for guided container and tray identifi cation. Its especially compact design is optimally tailored for stationary use in confi ned spaces. Integrated industrial interfaces and simple confi guration offer you perfect performance at the best price.
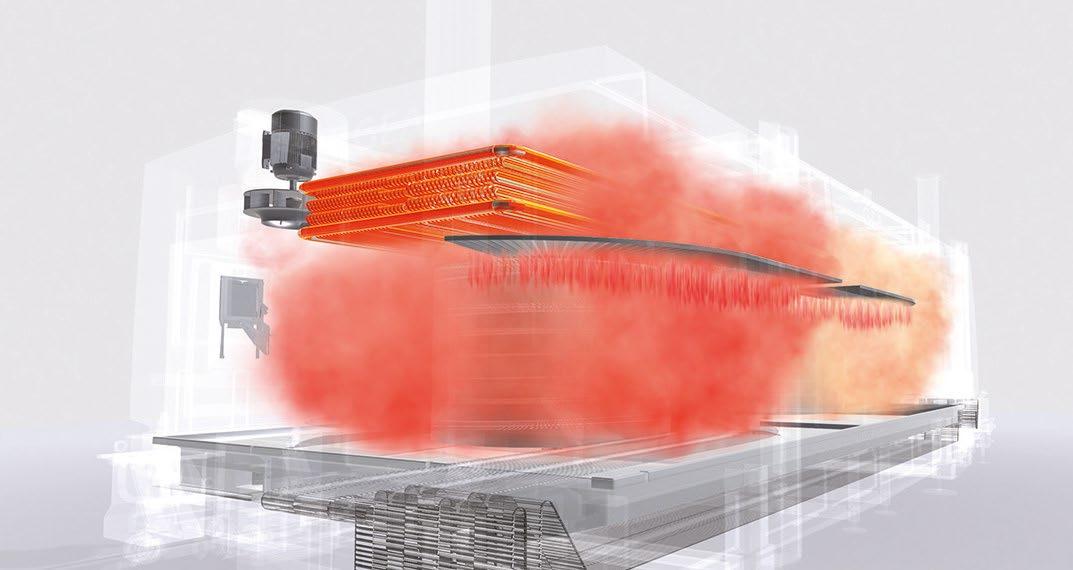
Precise performance cooking for outstanding results
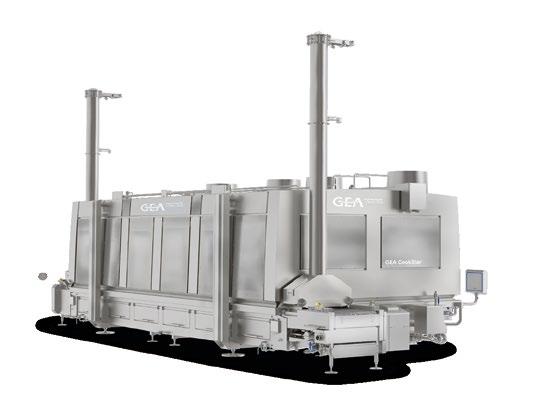
Industrial cooking technology has come a long way since GEA introduced the world’s first two-zone spiral oven in 1992. The latest model, the CookStar 1000 Gen 3, provides powerful new technology for the mass production of roasted, breaded and smoked products.
The CookStar cooks powerfully yet accurately, maximizing yields using smart technology that continuously adapts, maintaining the optimum oven conditions for each product. Its three-zone cooking method controls the flow of air through the oven for consistent browning, and an enhanced impingement zone allows a higher air volume for greater efficiency.
The CookStar’s ability to accurately control the cooking parameters is making this latest model the increasingly popular choice for industrial cooking. The CookStar 1000 Gen 3 is the only spiral cooker on the market which can dry, steam, cook, roast and smoke products in a single machine.
Capturing the authentic flavors of the perfect joint or roast chicken requires the right timing, airflow, dewpoint and temperature. In most commercial ovens, the optimum setting for any individual product is a compromise: a high dewpoint improves yield but prevents browning; while a lower dewpoint browns the meat but dries it out. However the CookStar 1000 comes with built in smart climate and exhaust systems allowing increased flexibility and sustainability. Intelligent exhaust systems monitor the environment within the oven, adjusting the volume of air as needed to maintain the precise conditions required for optimum cooking. Using energy exactly as and when it is needed, this technology reduces heat and steam losses, reducing power consumption.
Operating at a high dew point, the first phase uses steam to cook quickly and gently, keeping the meat succulent. Then the impingement zone blasts the product with hot, dry air, preparing the surface for roasting without drying out the core. The final phase, with a much lower dew point, completes the process, cooking products to perfection.
The dewpoint within the CookStar’s two cooking towers can be managed precisely by injecting steam or opening fresh air gates, and each cooking tower can operate independently, so different products can be cooked simultaneously using the same equipment.
For smoked products, freshly generated smoke from condensate can be included in the airflow of the CookStar, combining the smoking and cooking processes, reducing process time and the need for manual intervention associated with traditional smoking methods.
GEA’s CookStar 1000 Gen 3 offers food processors even more flexibility. Its intelligent systems allow greater control, high productivity, sustainability, reliability and consistency of outcome.
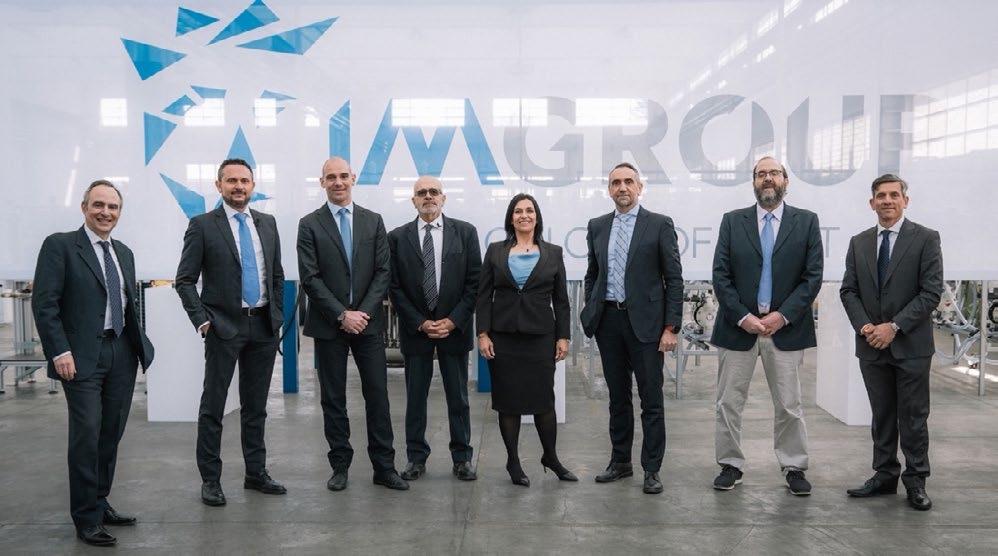
From left to right IM GROUP members: Silvio Cimenti, Global Director of Branding and Marcom; Gianluca Incerti, Global Commercial Director; Christophe Rizzo, CEO EMEA/AMERICAS; Remo Careglio, Area Sales Manager (retired): Valentina Cigna, President and Global HR Director; Roberto Guerra, CEO Asia Pacific; Francesco Nesti, Global Director of Software & Automation; Enrico Mattiazzi, Global Director of Engineering, Production and Supply Chain
Inkmaker group rebrands as IM group
Inkmaker Group has announced it will officially be known as IM GROUP. The launch, filmed on location at Inkmaker’s headquarters in Turin, Italy (now also headquarters to IM GROUP), was screened for private viewing on Youtube to coincide with World Earth Day to emphasise its commitment towards sustainability.
The decision to rebrand Inkmaker Group as IM GROUP aligns with the group’s vision, of evolving its technology to expand in its fields and adapt, the advantages of its products, to new markets.
“Since October 2019, Inkmaker has made significant investments, on the acquisitions of the businesses of Rexson and Valtech, in UK; Tecnopails, in Italy; and most recently Swesa, in Germany. The driving strategy behind these acquisitions was to create a reliable complete supply chain—serving predominantly, but not only, the ink, paint and coatings industry—to sustain our core businesses,” explained Christophe Rizzo, CEO EMEA/Americas, IM GROUP.
This meant restructuring the group’s brands into various specialities, yet to still function as one strong force, hence the need to rebrand the existing Inkmaker Group brand, to have an identity of its own, as an autonomous holding brand positioned as a “Total Solutions Provider”. As Rizzo highlighted, “this is the evolution of Inkmaker Group, which is essentially that of Inkmaker.”
Gianluca Incerti, Global Commercial Director, IM GROUP explained that this was one of the key reasons for forming IM GROUP. “Our strategy is to create “areas of excellence” dedicating each of our brands to a specific expertise. In this way each brand still works individually, with its existing clients in its own markets, and when required shares that expertise—offering Total Solutions— when for example, working on large turn-key plant engineering projects. This guarantees resource optimisation and high flexibility to manage projects of all sizes,”
With the restructure of IM GROUP’s brands—Inkmaker will focus on ink dispensing and software design; Rexson will be predominantly for paint as well as liquid ink, Vale-Tech will focus on
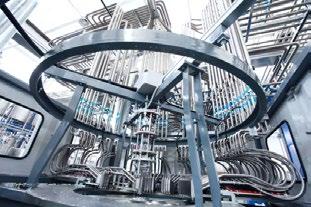
narrow-web and paste-ink dispensing; Swesa mainly for; food, pharmaceutical, corrugated packaging, cosmetics and more; Teko will remain in POS Tinting and R&D Training and; Tecnopails for Filling Solutions.
The new identity—inspired from the Inkmaker logo—was designed by the group’s inhouse corporate communications division, THINK. “The focal point of IM GROUP’s new logo is a symbol of a face created from a series of triangles, that like the many brands and skills of our Group, converge to form a strong whole—a distinct ‘human identity’—depicting a technological engineering leader with a ‘human touch’. The face is embellished with a crown, representing the Group’s determination to maintain its leading position in the industries it serves,” explained Silvio Cimenti, Global Director of Branding, Marketing and Communications, IM Group, “The Colour of Trust”— the Group’s credo— is a result of its core values of being Truthful, Responsible, Understanding, Safe and Tailormade to ultimately position the group, as the leader you can T R U S T.”
Great attention was given to the name “IM”, acronyms deriving from the name “Inkmaker”, which are steeped in history as Valentina Cigna, Global Director of HR and President of IM GROUP outlined, “they recall not only Inkmaker—as the founder of the group—but also those who, in 1987 founded Inkmaker; Carlo Musso, Luciano Longobardi and— especially for me—my father, Giuliano Cigna. He would have been very proud of this moment.”
The move comes at a time of great evolution, on all fronts for the group, and in all of its locations globally. The global organisation is rapidly gaining market share across South-east Asia especially in Philippines and Vietnam and as Roberto Guerra, CEO Asia Pacific, IM GROUP highlighted, “The big one for us is of course China, due to our larger premises, we can now double the number of standard machines we ship monthly, from an average of 5 or 6 units to 10 to 12. More importantly, this permits us to build more complex units, which is where IM GROUP’s R&D is investing a lot of resources. Smart factory and Industry 4.0 are driving our growth and when you build complete production lines for a paint and ink company it’s important to have enough space to work in total safety.”
Safety at the workplace has always been a high priority for the group, along with technology, but it is also evolving the way in which its products are impacting the environment and the carbon footprint they leave.
“This was the reason for choosing to launch IM GROUP, on “World Earth day”, to make a global statement of our commitment in furthering our social responsibility and sustainable practices. To action this, IM GROUP is partnering with international consultants to create a roadmap to reduce our eco-impact and to align our ethical principles for a safe work environment with those of the United Nations’ Global Compact.” concluded Valentina Cigna, Global Director of HR & President of IM GROUP.
“Due to its acquisitions, Inkmaker grew by 25% globally. Taking into account the current challenges the pandemic has caused; this is still on track with our vision. Now having the holding brand, IM GROUP—to steer all our speciality brands—we foresee all our brands to grow exponentially.” Concluded Rizzo.
For those of who missed the launch, it can be viewed by clicking this link: https:// im-group.com/our-business.html
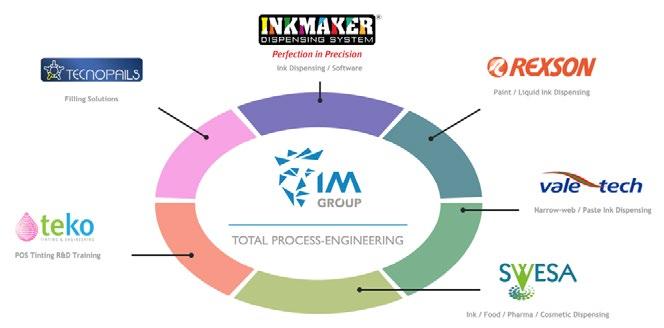
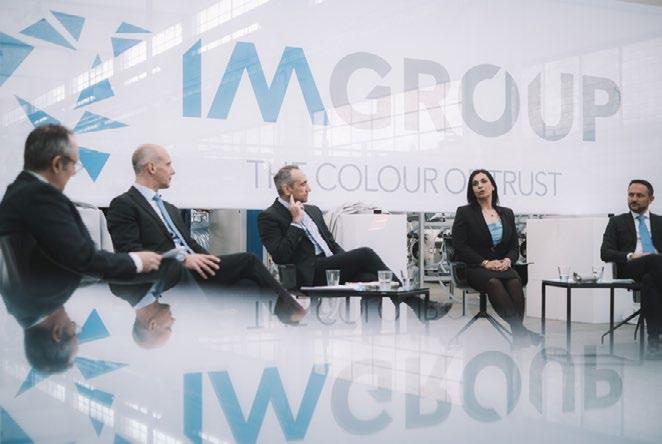
Gentle pumping of critical fluids with Roto’s progressive cavity pumps & AODD pumps
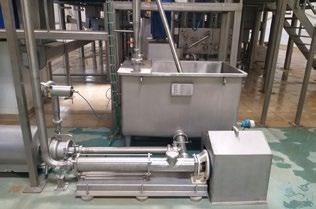
ROTO PROGRESSIVE CAVITY PUMP TRANSFERRING HONEY
Applications in Food, Beverages, Pharma and Cosmetics industries require pumps that can transfer hygenic, shear sensitive, abrasive and highly viscous media with zero contamination. Roto’s food range progressive cavity pumps are made of stainless steel with the smooth surface finish to avoid contamination. These pumps are designed in a way that eliminates all retaining pockets.
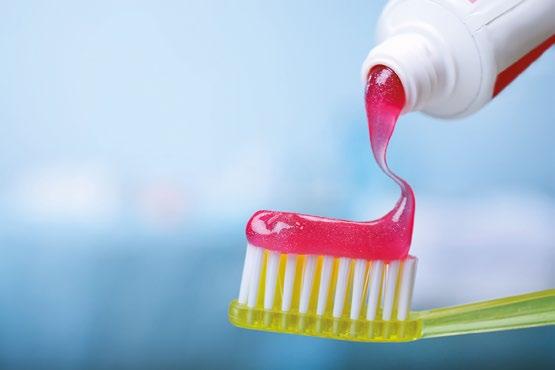
These pumps offer a distinctive edge over other positive displacement pumps as it can be customized in wide throat (standard hopper & oversized hopper) design which helps in transferring nonflowable fluids such as syrups, shampoo, wine must, ketchup, yogurt, dough, meat, vegetables, etc.
PRODUCT RANGE FOR FOOD & BEVERAGE INDUSTRY
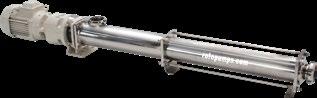
DM Series Progressive Cavity Pump Capacity – Up to 86 m3/hr Pressure – Up to 24 bar
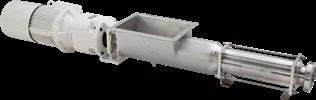
WM Series Progressive Cavity Pump Capacity – Up to 86 m3/hr Pressure – Up to 24 bar 78 FDPP - www.fdpp.co.uk
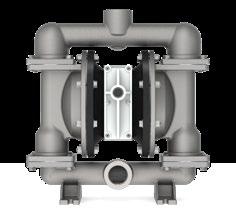
RAODD Pump in SS 316 MOC Capacity – Up to 60 m3/hr Pressure – Up to 10 bar
CLEANING –IN –PLACE (CIP) TECHNOLOGY
Cleaning is an important aspect while designing food grade pumps. Roto’s CIP feature enable pump operators to clean the pump by running a cleaning agent i.e. caustic, acid or simply water to avoid any contamination with ease. The rotor and stators are designed to be compatible with media as well as cleaning agent. These pumps are equipped with the appropriate drain or bypass system.
ROTO PUMPS UK| 15 YEARS OF DELIVERING POSITIVE DISPLACEMENT PUMPING SOLUTIONS
2004, Roto Pumps Ltd. established a branch in the UK with warehouse and assembly infrastructure to provide positive displacement pump solutions to various industries across Europe. New Market had its own challenges which can slow any new company’s progress. But Roto Pumps Ltd. was not new; it had a rich experience of over four decades with a maximum number of screw pump installations in critical applications across the globe.
To gain a strong foothold in the European Market, Roto Pumps focused on providing customized engineered pump packages, strong service support and ensuring ready availability with optimum stock levels of Pumps & spares. Also, Roto Pumps UK has established an intensive network of distributors and channel partners.
15 years of experience in the European market, Roto Pumps has demonstrated its expertise in application engineering i.e. understanding of complex pumping requirements, handling critical media, optimizing pump life cycle cost.
KEY CAPABILITIES OF ROTO PUMPS UK
• 15 years of strong presence in Europe • Robust supply chain network • Strong sales & service support team in the UK
• Readily available pump & spare parts
Stocks
• Cost-effective & customized engineered packages.
We at Roto Pumps believe in customer delight; we have a team of experienced application & sales engineers in the UK who completely take care of customer’s concern right from receiving inquiry to providing prompt after-sales support.
Dave Bent Roto Pumps Ltd. UK Unit 1, St Elizabeth Park, Grey Street, Denton Manchester UK, M34 3RU Tel: +44 ( 0 ) 161 477 5511 Mobile: + 44 ( 0 ) 7778 637343 E-Mail: davebent@rotopumps.co.uk
www.rotopumps.co.uk
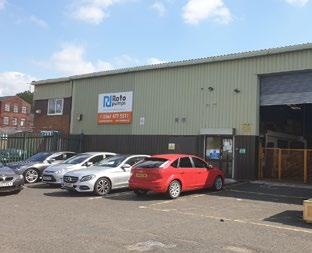