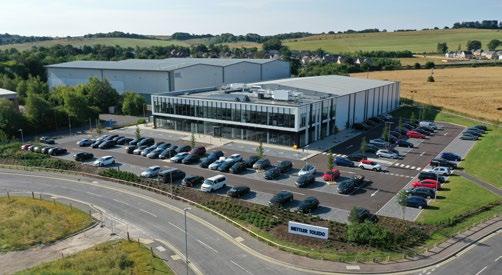
8 minute read
METTLER-TOLEDO
Mettler-Toledo announces Open House at new Global Centre of Excellence, helping customers improve product safety and profitability
Food and pharmaceutical manufacturers and copackers can attend the Product Inspection Open House at the new Global Headquarters for x-ray in person or virtually, participating in a range of seminars, technology demonstrations and consultation sessions.
Royston, Hertfordshire, UK, 1st September 2021 – Mettler-Toledo Product Inspection will showcase new product inspection technologies, offer opportunities for face-to-face and virtual consultations, and deliver educational seminar content, at an Open House event which will officially open the new Global Centre of Excellence for x-ray in Royston, Hertfordshire.
Mettler-Toledo Product Inspection’s new x-ray manufacturing facility in Royston, Hertfordshire sets the business up for continued expansion over the next decade and more. Set across a 1.4-hectare site, it expands the company’s UK manufacturing footprint by more than 80%, enabling multiple development projects to be handled simultaneously. The facility will also help to expand the customer experience, with new factory acceptance testing rooms and a production observation area.
The COVID-safe event will take place over 6th and 7th October 2021, giving brand owners, manufacturers and contract packers in food and pharmaceuticals the opportunity to experience the latest innovations and best practice in x-ray, metal detection, checkweighing and vision inspection, as well as discussing their specific product inspection needs and challenges with a Mettler-Toledo expert. can book a free personalised 1-2-1 consultation, either virtually or in-person, enabling their teams to tap into MettlerToledo’s expert knowledge of areas such as compliance, product safety and digitalisation.
Mettler-Toledo’s latest product innovations will take centre stage, with 1-2-1 customised live demonstrations of a new metal detection system, a new x-ray inspection machine as well as the latest C33 Series checkweighers with FlashCell™ load cells and demonstrations of our vision inspection solutions and ProdX™ data management software.
The event will also include two educational seminars, both running at 8am and 2pm (BST) on their respective days:
Wednesday 6th October - How Product Inspection Innovations Improve Food Safety and Automate Quality Processes for Contract Packers – co-hosted with ECPA, featuring Ton Knipscheer of the European Co-Packers Association (ECPA); Rob Rogers, Senior Advisor Food Safety & Regulation and Niall McRory, Global Key Account Manager both from MettlerToledo Product Inspection.
Thursday 7th October – Good Inspection Practice: 6 Steps to Preventing Physical Contamination – co-hosted with BRCGS, featuring John Figgins, Senior Technical Manager from the BRCGS; Ian Robertshaw, Global Key Account Manager and Adam Green, Market Manager both from Mettler-Toledo Product Inspection.
“We are really excited to officially open and showcase our new Global Centre of Excellence for x-ray inspection at our Product Inspection Open House event. The new Global Headquarters has been specifically designed to become MettlerToledo’s main hub for x-ray research and development plus manufacturing x-ray innovations. The significant investment we have made into developing the x-ray business is part of our strategic business development plans and is in response to customer demands for us to continually design x-ray inspection technologies to improve packaged product safety,” said Niall McRory, Global Key Account Manager at Mettler-Toledo Product Inspection.
“Meeting customers and prospects faceto-face has obviously been difficult over the last year and a half, and we are very much looking forward to interacting with them again at our October Open House event, either in person at our new Global Centre of Excellence or virtually,” continued Niall McRory. “We’ve got a lot of gamechanging new innovations to show them, as well as some inspirational educational opportunities to share. The challenges of product safety and operational efficiency remain front and centre for every manufacturer, and that’s where our focus will be during this event. Whether they are in food or pharma, there will be something for every customer and prospect at the Open House, so we hope they will mark the dates in their diaries.
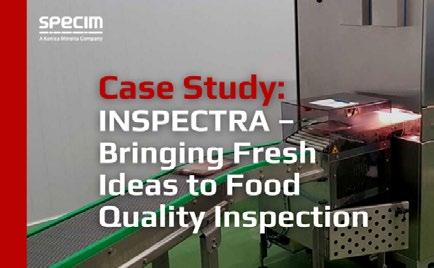
INSPECTRA – Bringing Fresh Ideas to Food Quality Inspection

Inndeo, a Spanish company founded in 2016, uses Specim’s hyperspectral imaging technology to improve the quality inspection processes in the food industry by increasing automation. With this new technology, they can detect contamination and defects in the production lines and characterise different food quality parameters.
Click here to learn more about: • Replacing manual labour and old equipment with sensor fusion • Advancing from detecting defects and contamination to quality parameters • Further applications
Specim Hyperspectral Cameras for the Food Industry
Applications Include:
■ Meat, fish and poultry ■ Dried food – nuts and cereals ■ Fruits berries and vegetables ■ Food packaging ■ Heat seal inspection ■ Seed and grain
SPECIM DISTRIBUTOR IN THE UK AND IRELAND: Quantum Design UK and Ireland Ltd
Tel: +44 (0)1372 378822 Email: info@qd-uki.co.uk
FX Series:
Small, fast & affordable
FEATURES:
■ Spectral range: ■ FX10 400-1000 nm ■ FX17 900-1700 nm ■ High spatial resolution of 640 pixels ■ High image speed: ■ 527 FPS (full range) for GigE version ■ 670 FPS (full range) for CameraLink version ■ Free wavelength selection from 224 bands within the camera coverage
For more information visit qd-uki.co.uk/imaging-cameras
Norsk Kylling Designs Future of Food with Infor
Infor have announced that Norway-based poultry producer Norsk Kylling has selected the Infor EAM enterprise asset management solution. Already live at its Støren-based operations, the solution will be extended to a new 40,000-square-meter state-of-theart factory in Orkanger to support higher equipment availability, reduced costs and tighter inventory management for the food company. Working with Infor partner Prevas, Infor EAM is expected to go live upon facility completion in spring 2021.
Learn more about Infor EAM: https://www.infor.com/en-gb/ products/eam
Norsk Kylling manages its entire value chain for chicken production, from brood and hatcher egg production, to hatchery, broiler production and processing, as well as owning the Solvinge chicken brand. Its new facility will represent best practices and innovation in food production, encompassing the highest animal welfare and environmental standards, and supporting the circular economy.
Against this backdrop, digital capabilities and automation were intrinsic to the new facility’s design. Having selected an ERP platform for greater control over production and the value chain, Norsk Kylling set out a requirement for a maintenance system which could limit waste and reduce costs.
“Excesive downtime can have far-reaching consequences in our business, so opting for a solution that can help ensure high availability of equipment and productivity across the factory is paramount,” comments Ulf Jensen, Norsk Kylling technical manager. “In addition to cost savings, a comprehensive view of equipment status, and higher availability, Infor EAM will also give us greater control over spare parts and stock. We have more than 3,000 units in the plant register and up to 15,000 parts in the article register, therefore the automatic ordering capability within Infor EAM will help us to optimise availability without incurring unnecessary costs.”
“The right digital capabilities are absolutely paramount for modern food producers, particularly those in categories that are managing tight shelf lives and significant waste,” comments Infor’s Johan Made, executive VP for the Nordics.

How an ERP Can Help Your Business Successfully Transition to More Sustainable Packaging Options
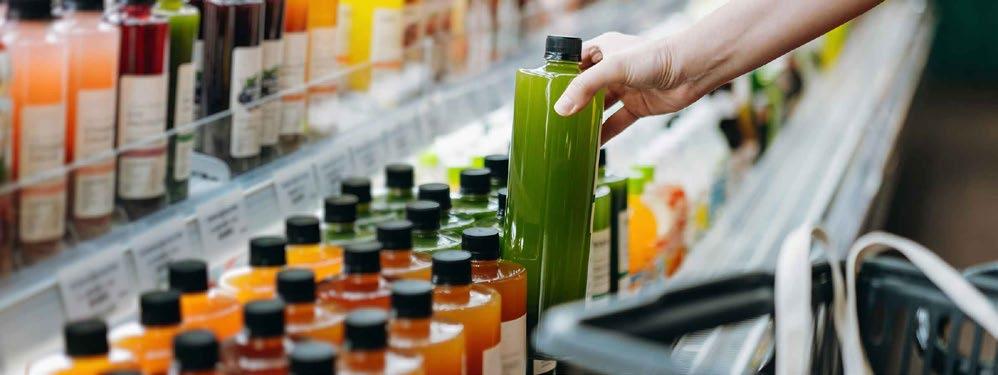
Over recent years, the push for sustainable packaging for the food and drink industry, driven by consumer demand, has led to food manufacturers, processors and packaging companies rethinking how they package their products.
With 67% of consumers globally thinking that it is important that products come in recyclable packaging, and 54% saying it is an active consideration when shopping, utilising sustainable alternatives to single-use plastics is a key concern for those who work in food and drink packaging.
There are many options available when it comes to looking for sustainability in packaging including: utilising paper packaging, reducing packaging volume, introducing refillable packaging, and incorporating recycled plastics into packaging.
However, evolving current practices doesn’t come without challenges, but this is where complete visibility of data and processes in one place can be extremely beneficial for businesses who are looking to implement these changes.
An ERP (enterprise resource planning) solution provides your business with the perfect foundation to help you integrate new packaging materials and technologies in the most cost-effective way. The Food and Beverage ERP solution designed by Aptean, is an integrated software platform which brings together all aspects of your business, and technology stack, providing you with accurate and consistent data exactly when you need it.
ABOUT APTEAN
As a leading provider of industry-specific software, Aptean’s Food & Beverage ERP is designed to meet the particular needs of the food and drink industry. Our ERP provides you with full control of your growing business while also retaining all the flexibility you require to respond dynamically to any new trends in the fastmoving food industry, from the increasing popularity of plant-based foods to the demand for sustainable packaging. More than 1,000 food and beverage customers already use Aptean’s solutions, built on the Microsoft Dynamics 365 platform, allowing them to unlock the benefits of a reliable and scalable platform to underpin their business, and its growth plans.
With over 20 years’ experience in the UK market, we have helped many companies to transform their business to continue to remain competitive and ensure that they are delivering best practice for today’s priorities.
Join Aptean on October 5th for our 2021 Food and Beverage Global Symposium to discover more about how we can help your business to scale and succeed.
Website: www.aptean.com Email: info@aptean.com
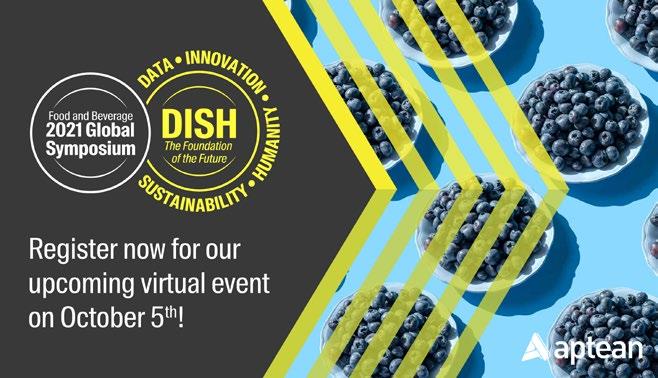