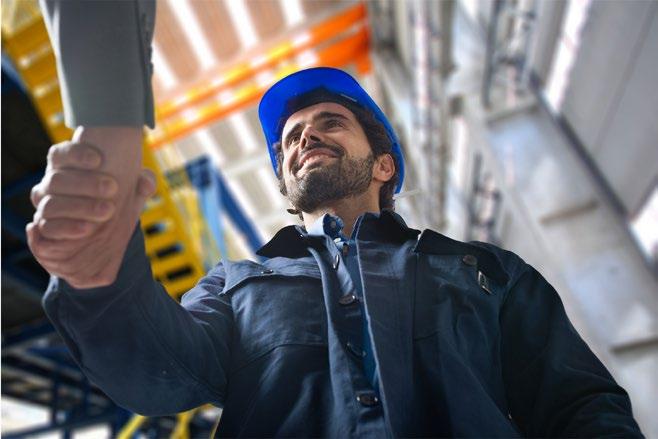
4 minute read
PROSEAL
Proseal’s decade of success with Procare customer support programme
Tray sealing specialist Proseal is celebrating the tenth anniversary of its successful preventative maintenance programme, PRoCARE®, as the company continues to fulfil its longstanding commitment to delivering outstanding customer support.
Launched in 2011, PRoCARE provides comprehensive aftersales service through a series of scheduled inspections and maintenance of equipment in order to minimise unexpected and costly downtime. A decade later, PRoCARE has become so successful that Proseal has established a dedicated department to co-ordinate the programme to ensure continuity of service and speed of response are maintained.
“In today’s fiercely competitive markets and where consumers are expecting new products faster than ever, manufacturers need to be able to rely on their machinery to function at optimum capacity,” explained Daryl Henshaw, Proseal’s Key Accounts Manager. “Loss of production for any reason means a loss of sales, profit, and potentially food. Having proactive preventative maintenance support can help to significantly reduce these risks and prevent unnecessary food waste.”
Proseal’s PRoCARE provides both on-site and remote service and advice that helps to maximise machinery performance and uptime. Recognising that food manufacturing is a year-round operation, the service is available 24/7, 365 days a year.
For major food manufacturer, Bakkavor Group, investing in PRoCARE has played a key part in enhancing the efficiency of its operations. “Given the nature of our industry and where Proseal machinery sits within our group, the continued support of Proseal is key to the success of our business,” confirmed Bakkavor’s Group Engineering Manager, Ben Cooper. “Indeed, the level of aftersales support we receive from Proseal is often used as something of a yardstick for our other suppliers.”
Bakkavor has remained a participant in the PRoCARE programme since its inception. During this time, the company has continued to roll out PRoCARE across six of its largest UK sites, and the number of machines that Proseal is overseeing has increased from around 30 to over 80.
Another indication of the success of the programme is that every Proseal key account customer is a participant, and the PRoCARE division is now carefully managing around 80 active contracts covering over 400 machines. while driving up efficiency: a wellmaintained machine is less likely to breakdown. The feedback has been overwhelmingly positive. Most customers have reported huge reductions in downtime as a result of going from reactive maintenance to proactive PRoCARE.
“Equally important is how we have been able to adapt the service to deal with the specific challenges of the COVID-19 pandemic. Our team were able to put in place stringent procedures and provide PPE to our workforce, which allowed for maintenance visits to continue, underlining our genuine commitment to customer support, whatever the situation.”
Proseal is part of the JBT Corporation family, a leading global technology solutions provider to high-value segments of the food processing industry, committed to providing a service that surpasses customer expectations. PRoCARE service contracts are available across all JBT machinery solutions, built to maximise uptime and financial predictability, with the goal to reduce total cost of ownership.
Automate with PALpack
PALpack are the UK’s leading experts in Palletisers, de-palletisers, AGVs and sack fillers. They design, advise and supply top of the range machinery from European manufacturers. Once delivered, PALpack install and commission these machines and offer service contracts as well as backup and support from their offices and workshop.
Adapting business processes has always been the way to compete, but it’s more important now than ever to future-proof. Automating a repetitive manual process in a production or manufacturing facility means fewer mistakes are made, there’s a faster speed of work and no breaks, plus health and safety is increased. Automation is also scalable, can be integrated into existing systems and will increase your productivity.
PALLETISERS AND DE-PALLETISERS
A critical part of the manufacturing process, palletisers automate the stacking process that can otherwise be labour intensive and expensive, putting undue stress on workers. They’re designed to be configured alongside the other production line facilities. PALpack’s palletisers are capable of assembling pallets, as well as palletising different items simultaneously and are cost-effective to install. De-palletisers are machines that unload items from pallets and are used to transport parts from one line to another during manufacturing.
AUTOMATED GUIDED VEHICLES (AGVS)
AGVs are robotic vehicles used to perform operations that would otherwise be carried out manually, or by forklifts and conveyors. PALpack’s partners at Global AGV recently announced that the payback period for some of its automated guided vehicles is less than one year.
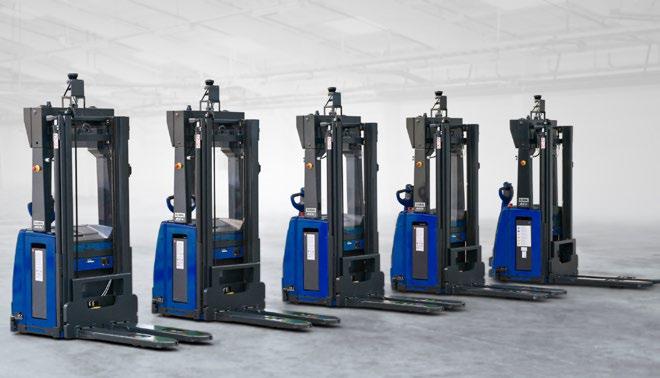
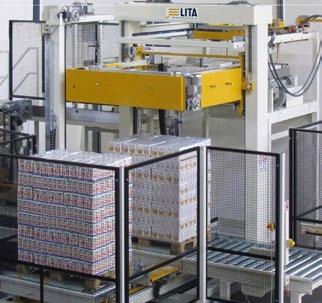
SACK AND BAG FILLING
Bag filling machines automate the material handling, filling, sealing and weighing of packaging bags or sacks with optimal efficiency and accuracy.
SUPER-DEDUCTION INCENTIVE ON AUTOMATION MACHINERY
There’s never been a better time to invest in upgrading your machinery. From April 2021 until March 2023, the UK government is offering 130% capital tax allowance deduction on qualifying firstyear plant and machinery purchases. CONTACT PALPACK
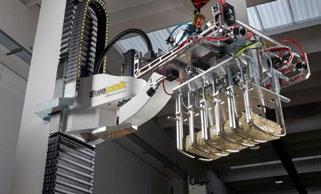
Choose a supplier that is an expert in automation and engineering project management. Beyond the machine they’re selling, they need to understand your space, scope and the wider implications within your manufacturing environment.
PALpack has been improving manufacturer productivity with automation for 25 years. For specialist advice and guidance on the equipment that will best suit your business’ needs, contact PALpack today.
www.palpack.co.uk sales@palpack.co.uk
