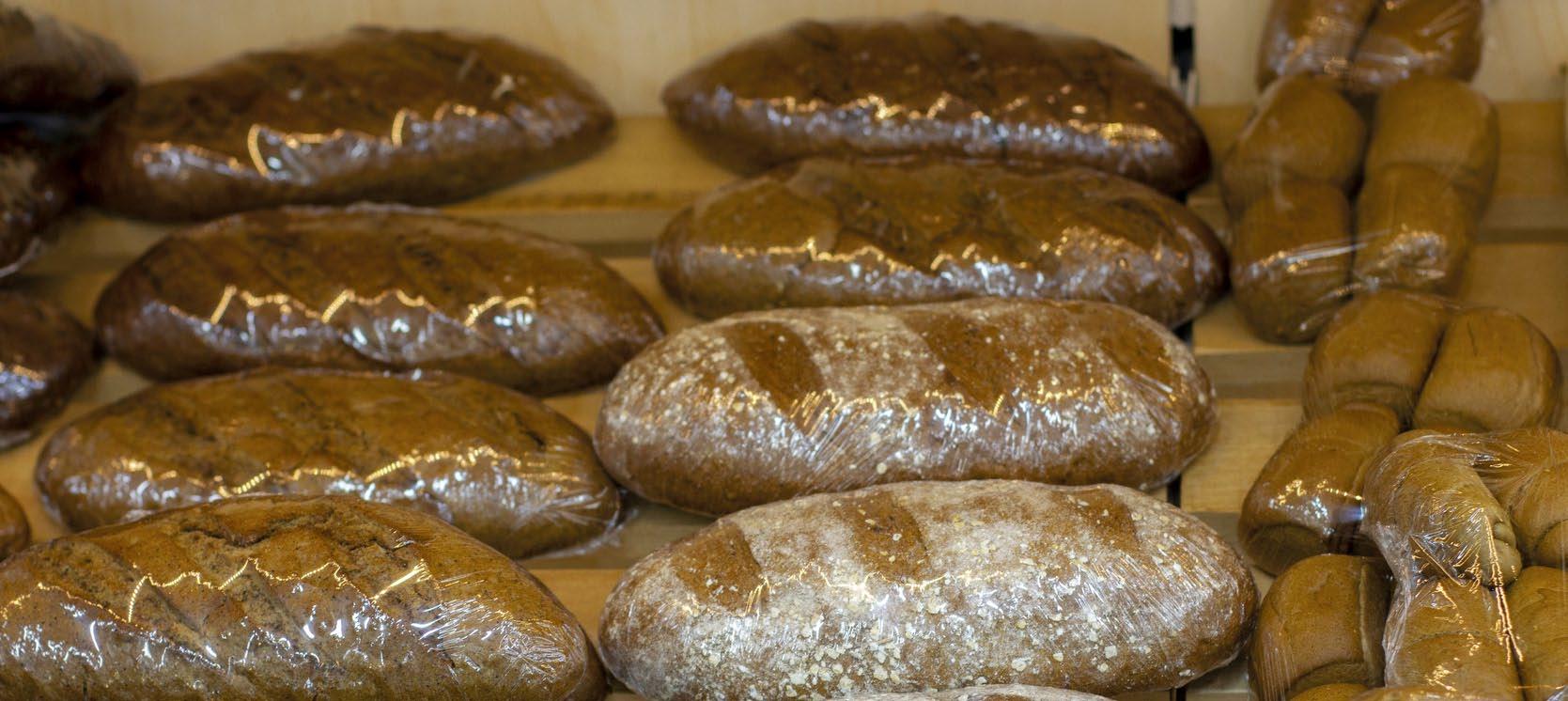
20 minute read
dr Ewa Mucha-Szajek mgr inż. Tomasz Borowy mgr Milena Jasiurkowska
dr Ewa Mucha-Szajek prof. WSHiG mgr inż. Tomasz Borowy mgr Milena Jasiurkowska Wyższa Szkoła Hotelarstwa i Gastronomii w Poznaniu
Nowe i obiecujące interaktywne technologie opakowaniowe
Advertisement
Opakowania aktywne to takie, w których produkt, opakowanie i otoczenie wzajemnie na siebie oddziałują. Ich zadaniem jest ukierunkowane oddziaływanie na produkt, w celu zapewnienia jego wyższej jakości, a także do przedłużenia okresu trwałości i przydatności do spożycia. W odróżnieniu od opakowań tradycyjnych, aktywne materiały opakowaniowe wchodzą w reakcje z wewnętrzną atmosferą i produktem, powodując przedłużenie jego trwałości. Szczególną grupę wśród opakowań interaktywnych stanowią opakowania inteligentne (inteligent packaging), nazywane również sprytnymi (smart packaging), które zawdzięczają swoją nazwę posiadanej funkcji pomiaru określonego czynnika i sygnalizowania wyniku. Działanie tych opakowań związane jest z użyciem interaktywnych wskaźników, najczęściej barwnych, umożliwiających ocenę jakości produktu żywnościowego.
Przemysł spożywczy ze względu na swą dynamikę rozwoju w zakresie tworzenia różnych produktów wykreował w ostatnich latach zupełnie nowe potrzeby w zakresie produkcji opakowań. Powoduje i powodować powinien w najbliższym czasie zwiększony popyt na różnego rodzaju opakowania z tworzyw sztucznych. Są to opakowania wypierające często w coraz szerszym stopniu tradycyjne opakowania z papieru, tektury, blachy czy szkła, których główną funkcją jest chronić produkt, ułatwiać przemieszczanie, magazynowanie oraz oddziaływanie na percepcję konsumenta. Zwiększony popyt na tego rodzaju opakowania jest uzasadniony ze względów nie tylko ekonomicznych, ale i funkcjonalnych. Wraz ze wzrostem zainteresowania producentów żywności nowymi rozwiązaniami w temacie tworzenia nowych rozwiązań dla tworzyw sztucznych spowodowane jest większymi wymaganiami ze strony konsumentów, którzy oczekują od opakowania szeregu funkcji. Producenci opakowań poszukują zatem rozwiązań, które zapewnią lepsze właściwości materiałów opakowaniowych, takie jak: odpowiednia barierowość w stosunku do gazów, ochrona przed promieniowaniem UV, wydłużenie okresu przechowywania, transparentność i w końcu ekologiczność. Kiedyś pakowano prawie wszystko w papier, który nie był dobrym zabezpieczeniem żywności podczas przechowywania. Dzisiaj znane są właściwości tworzyw, które pozwalają na dostosowania konkretnego tworzywa sztucznego do odpowiedniego produktu spożywczego, czy surowca w zależności w jakiej formie ma być przechowywany, transportowany czy eksponowany w ladzie chłodniczej. Dobór odpowiedniego materiału i formy opakowania dla konkretnego produktu spożywczego zależy od wielu czynników. Najważniejsze wśród nich są czynniki związane bezpośrednio z właściwościami fizykochemicznymi pakowanego produktu. Należą do nich np.
skład chemiczny, stan fizyczny w jakim występuje produkt, jego tekstura, porowatość, a także czas przechowywania i warunki w jakich będzie przebywał do momentu spożycia przez konsumenta. Bardzo istotna jest również znajomość procesów (mechanizmów) i czynników stymulujących przemiany fizyczne, chemiczne, biochemiczne i biologiczne zachodzące w produkcie spożywczym podczas przechowywania, powodujące ograniczenie jego przydatności do spożycia. Przy projektowaniu właściwego opakowania muszą być brane pod uwagę również parametry procesu technologicznego podczas pakowania na linii produkcyjnej, np. temperatura lub ciśnienie. Opakowanie musi także uwzględniać sposób i warunki, w jakich produkt będzie transportowany do odbiorców. W tym przypadku chodzi przede wszystkim o przewidywanie potencjalnych narażeń mechanicznych, oddziałujących na opakowanie i zawarty w nim produkt żywnościowy. Opakowanie aktywne powstało, by spełniać wysokie wymagania konsumentów związane m.in. z przedłużeniem okresu ważności produktu, polepszeniem jego właściwości organoleptycznych oraz ochroną. Aby móc spełnić te zadania, opakowania aktywne zawierają szereg specyficznych dodatków. Zaprezentowane poniżej przykłady aktualnie stosowanych opakowań aktywnych dowodzą, że technologia wprowadzania aktywnych substancji w struktury polimerowe została już opanowana. Jest to technologia rozwijająca się, obejmująca wiele praktycznych współczesnych i przyszłościowych zastosowań w skali całego globu. Wyzwaniem, jakie stoi przed specjalistami z tego zakresu, jest uczynienie opakowań nowego typu bardziej przyjaznymi dla konsumenta i oczywiście środowiska. Stosowanie tak szerokiej gamy opakowań bezpośrednich do produktów spożywczych podyktowane jest ciągłym poszukiwaniem nowych rozwiązań, chęcią zaskoczenia odbiorcy i bycia oryginalnym oraz pierwszym na rynku. O użyteczności opakowań zadecydowały ich zalety, tj. duża uniwersalność dostosowania do różnych wymagań względem produktów. Jednocześnie stwarzają wiele możliwości wprowadzania nowych rozwiązań konstrukcji opakowań zarówno z punktu widzenia technicznego, jak i potrzeb marketingowych. Coraz większy nacisk kładzie się na wdrażanie produkcji opakowań zapewniających wygodniejsze użytkowanie produktów oraz w jak najmniejszym stopniu obciążających środowisko naturalne. Krajowe firmy opakowaniowe projektują i produkują opakowania oraz opracowują systemy pakowania, stosując materiały opakowaniowe i technologie produkcji zgodnie z normami międzynarodowymi lub dostosowane do przepisów, które obowiązują w skali międzynarodowej, w tym również w Unii Europejskiej. A kierując się zdaniem klientów, który wyznacza trendy funkcjonalności opakowań, powstają nowsze, bardziej dostosowane do życia codziennego dzisiejszego konsumenta. Głównym celem usuwania tlenu z opakowania jest hamowanie rozwoju pleśni w produktach spożywczych, zachowanie ich typowego aromatu, zapobieganie zmianom barwy, a także przeciwdziałanie jełczeniu. W przypadku wielu produktów, obecność nawet bardzo małych ilości tlenu (rzędu kilku mg/kg) może znacznie obniżyć ich jakość na skutek zmian smaku i zapachu, czy rozkładu niektórych witamin. Ilość tlenu dostępnego dla reakcji chemicznych i innych procesów jest w zamkniętym opakowaniu zwykle niewielka, i ograniczona. W celu zupełnego wyeliminowania tlenu z zapakowanego produktu stosowane są pochłaniacze. Na świecie stosowane są różnego rodzaju pochłaniacze, m.in.: proszki żelazowe, utleniacze glukozowe, związki podsiarczynowe, substancje organiczne typu redukcyjnego i inne. Obecnie produkowane są w formie saszetek, nalepek, zamknięć lub polimerów bezpośrednio wprowadzanych w strukturę materiału opakowaniowego. Produkty różnią się między sobą pod względem szybkości pochłaniania tlenu oraz warunków potrzebnych do aktywacji. Umożliwia to dobór właściwego pochłaniacza do konkretnych potrzeb. Istnieje wiele handlowo dostępnych opakowań aktywnych przeznaczonych do eliminacji tlenu z otoczenia produktu, wśród których do najważniejszych należą: - folia organiczna o nazwie „Longlife”, która może być umieszczona w opakowaniu w postaci saszetki lub włączona do materiału opakowaniowego z tworzywa sztucznego.
Mechanizm działania folii pochłaniającej tlen, używanej do aktywnego pakowania żywności przedstawiony jest na rysunku 1.
- laminat „Bioka Oxygen Absorber”, składa się z kilku warstw, pomiędzy które wbudowany jest enzymatyczny system pochłaniający tlen.
Laminat jest przezroczystym, termozgrzewalnym materiałem, który może być zadrukowany.
Opakowania z systemem obniżającym wilgotność (redukcja aw) i pochłaniające nadmiar wody
Najbardziej obiecującym rozwiązaniem tego typu opakowań są polimerowe struktury z mikrokanalikami służącymi do transportu dyfundujących cząstek wilgoci. Na powierzchni mikrokanalików umieszcza się środki osuszające. Polimery te mogą być fizycznie związane z innymi materiałami lub też włączone w wielowarstwową strukturę w trakcie procesu produkcji danego opakowania. Przykładem mogą być opakowania złożone z warstwy zewnętrznej (np.: polietylenu lub polipropylenu), stanowiącej barierę dla wilgoci z zewnątrz oraz aktywnej warstwy wewnętrznej (z mikrokanalikami) otrzymywanej z glikolu polietylenowego. W opakowaniach nieprzepuszczalnych lub słabo przepuszczalnych gromadzenie się wody może być spowodowane oddychaniem świeżych produktów, w przypadku produktów o dużej wilgotności, fluktuacjami temperatury, wreszcie wyciekiem soków komórkowych. Kontrola ilości wody wewnątrz opakowania jest potrzebna w celu ograniczenia wzrostu bakterii i grzybów strzępkowych, zapobiegania powstawaniu nieestetycznych mgieł (mleczny płyn w opakowaniu). W opakowaniach umieszcza się w zależności od ilości wody, saszetki, wkładki lub całe powłoki wiążące wodę. Jeśli ilość wody, która wymaga usunięcia jest niewielka, jak w przypadku mleka w proszku, kawy instant w opakowaniach umieszcza się zwykle saszetki pochłaniające wilgoć. Jako substancje czynne stosuje się między innymi: żel silikonowy, tlenek lub chlorek wapnia, sita molekularne, minerały ilaste takie jak montmorylonit. Jeśli zachodzi potrzeba usuwania większych ilości
wody, stosowane są całe powłoki wykonane z laminatów formowanych z odpowiednich kopolimerów i żywic poliuretanowych i poliakrylowych. Aktualnie prowadzone są oczywiście liczne badania nad wynalezieniem odpowiedniej bazy technologicznej dla aktywnych folii polimerowych. Takie folie powinny być odpowiednio mocne, nieprzepuszczalne (ograniczające dostęp tlenu) oraz powinny koniecznie zawierać odpowiednią ilość aktywnych składników z wysoką mobilnością dyfuzyjną i zdolnością do uwalniania się z folii. Ze względu na bardzo dobre właściwości, kluczową rolę przy tego rodzaju zastosowaniach mógłby odgrywać polichlorek winylu, jednakże jego toksyczność skłania producentów do użycia zdrowszych odpowiedników na bazie statystycznego kopolimeru etylenu i alkoholu winylowego, np.: żywica evalTM.
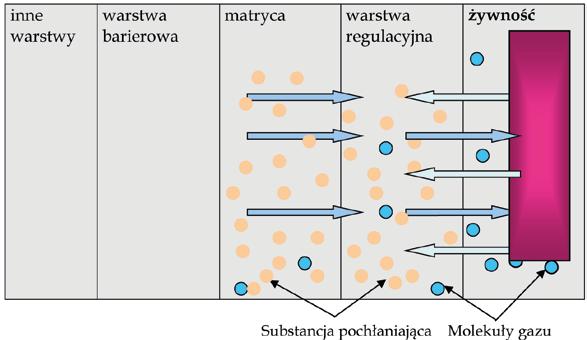
Rysunek 1. Folia pochłaniająca tlen używana do aktywnego pakowania żywności
Zastosowanie substancji antymikrobiologicznych
Aktywne opakowania zdolne do uwalniania substancji przeciwdrobnoustrojowych mogą efektywnie opóźniać rozwój niektórych mikroorganizmów i przedłużać trwałość produktów mlecznych. Konieczne jest przede wszystkim zahamowanie wzrostu bakterii chorobotwórczych i pleśni wytwarzających mikotoksyny (mykotoksyny), niezbędne jest również opóźnienie rozwoju bakterii powodujących procesy psucia. Opakowania przeciwdrobnoustrojowe mogą zawierać sorbiniany, benzoesany, propioniany lub bakteriocyny, które po uwolnieniu z saszetki lub folii hamują rozwój drobnoustrojów, mogących stanowić zagrożenie dla bezpieczeństwa zdrowotnego i jakości produktu. Często stosowaną substancją aktywną jest etanol lub inny alkohol, którego zastosowanie ma na celu zahamowanie wzrostu pleśni. Obecnie prowadzonych jest wiele badań ukierunkowanych na projektowanie opakowań zawierających naturalne składniki o działaniu przeciwbakteryjnym. Naturalnymi środkami stosowanymi w opakowaniach antymikrobiologicznych są substancje ekstrahowane z gorczycy, bakteriocyny, chitozan, polifenole, olejki eteryczne z oregano, bazylii, cynamonu i czosnku. W opakowaniach o właściwościach przeciwbakteryjnych stosowane są również systemy oparte o dobrze znane właściwości przeciwbakteryjne jonów srebra, które hamują wiele enzymów metabolicznych komórki drobnoustroju. Wielowarstwowa struktura materiałów opakowaniowych do żywności zawierających związki przeciwdrobnoustrojowe sprzyja kontrolowanemu ich uwalnianiu. Folie tego typu mogą składać się z następujących części: - matrycy zawierającej aktywny związek; - warstwy regulacyjnej o znanej dyfuzyjności kontrolującej szybkość migracji aktywnych związków w kierunku powierzchni produktu; - warstwy barierowej zapobiegającej migracji aktywnych związków w kierunku na zewnątrz opakowania, a także mającej odpowiednie właściwości barierowe względem wilgoci i tlenu.
Mechanizm działania folii uwalniającej substancje przeciwdrobnoustrojowe przedstawiony został na rysunku 2.
Kontrola smaku i zapachu
W trakcie przechowywania żywności następują jej zmiany organoleptyczne, które nie zawsze świadczą o zepsuciu
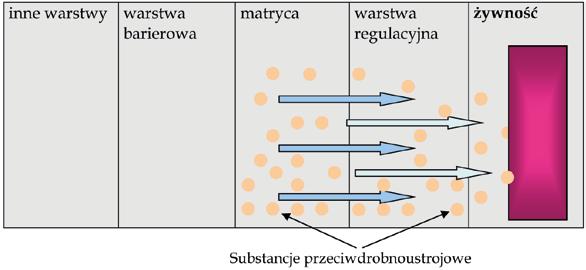
Rysunek 2. Folia uwalniająca substancje przeciwdrobnoustrojowe stosowane do aktywnego pakowania żywności
Regulatory wilgotności
W przypadku żywności wrażliwej na wilgoć, nadmiar wody w opakowaniach może powodować niepożądane skutki, tj. zbrylanie proszku, rozmiękanie chrupkich produktów oraz nawilżanie lub zlepianie higroskopijnych produktów. Zbyt duża utrata wody z żywności jest również niekorzystna i może doprowadzić do wysuszenia produktów, a tym samym przyspieszenia niepożądanych reakcji, tj. nieenzymatycznego i enzymatycznego brązowienia, degradacji witamin czy utleniania tłuszczu. Regulatory wilgotności służą do kontrolowania wskaźnika oksydacji tłuszczu oraz aktywności wody. W ten sposób można ograniczyć rozwój mikroorganizmów przez zmniejszenie dostępności wody potrzebnej do ich rozwoju. Substancjami czynnymi chłonącymi wodę są zazwyczaj chlorek sodu lub wapnia, skrobie modyfikowane, kopolimery skrobi, poliakrylowe sole, żel krzemionkowy, zeolity i włókna celulozy. Przy pakowaniu produktów świeżych stosowane są torebki z absorbentami wilgoci, które są wbudowywane między warstwy folii przepuszczalnej dla pary wodnej. Mogą być również stosowane inne substancje, tj. roztwory glukozy w owinięciach. Owinięcie złożone jest z dwóch warstw, wewnętrzna jest przepuszczalna dla pary wodnej, natomiast zewnętrzna jej nie przepuszcza. Przestrzeń między warstwami jest wypełniona roztworem glukozy. W przypadku dużej wilgotności względnej powietrza w opakowaniu, woda znajdująca się w produkcie przenika przez warstwę wewnętrzną owinięcia do roztworu glukozy. Gdy wilgotność względna powietrza jest niska, woda przenika w postaci pary z roztworu glukozy do wnętrza opakowania. Poziom wilgotności względnej, przy której następuje migracja wody pomiędzy roztworem glukozy a wnętrzem opakowania jest determinowany przez stężenie roztworu glukozy. Zaletą jego jest możliwość wielokrotnego wykorzystania, nawet do 10 razy po uprzednim umyciu i osuszeniu. produktu, ale po otworzeniu opakowania mogą być one źle odbierane przez konsumentów. Natomiast należy pamiętać, że opakowania aktywne nie mogą być stosowane w celu ukrycia oznak psucia się żywności, ponieważ może to stanowić niebezpieczeństwo dla zdrowia konsumentów. Pochłaniacze zapachu i smaku są dostępne na rynku w postaci folii, saszetek, taśm, etykiet lub tacek. Zwykle są umieszczone wewnątrz opakowania lub są włączone do materiału opakowaniowego. W celu neutralizacji lub usunięcia niepożądanych substancji zapachowych z opakowania wykorzystuje się systemy „Odour and Taste Control” (kontrola zapachu i smaku) lub „Interactive Packaging”. System „Odour and Taste Control” polega na wprowadzeniu sit molekularnych o średnicy porów co najmniej 5,5 nm, do materiału opakowaniowego, które wiążą składniki lotne. Natomiast system „Interactive Packaging” polega na zastosowaniu substancji chemicznych dopuszczonych do kontaktu z żywnością do materiałów opakowaniowych, które neutralizują niepożądane zapachy. System ten znalazł zastosowanie w przypadku serów, produktów mleczarskich, przekąsek. Oprócz pochłaniaczy można również stosować, równie skuteczne, emitery zapachów. Ich działanie polega na zamaskowaniu nieprzyjemnych substancji zapachowych lub wzmacnianiu naturalnego zapachu zapakowanego produktu. Emiterami są zwykle substancje charakteryzujące się wysoką odpornością termiczną. Są one stosowane jako dodatki do tworzyw sztucznych m.in. polipropylenu, polietylenu, poliestru, poliamidu oraz polichlorku winylu. Mogą również występować w postaci proszków, tabletek, granulek i etykiet.
W ostatnich latach obserwuje się duże zainteresowanie nowymi koncepcjami rozwiązań konstrukcyjnych i materiałowych opakowań spożywczych. Najważniejszą funkcją tych opakowań jest ochrona produktu przed zanieczyszczeniem mikrobiologicznym i chemicznym, bezpośrednim kontaktem z tlenem atmosferycznym, parą wodną i światłem. Inteligentne pakowanie polega na monitorowaniu warunków, w jakich znajduje się zapakowana żywność w celu dostarczenia informacji o jej jakości podczas transportu i magazynowania. Takie opakowanie spełnia następujące inteligentne funkcje: wykrywanie, zapisywanie, śledzenie, a przede wszystkim zastosowanie naukowej logiki w celu ułatwienia podejmowania decyzji dotyczących przedłużenia trwałości produktu, poprawy jego jakości, dostarczenia informacji i ostrzeżenia przed możliwymi zagrożeniami. Inteligentne opakowania nie oddziałują bezpośrednio na pakowaną żywność, czyli nie zostają uwalniane składniki do opakowania, w którym znajduje się produkt spożywczy, a jedynie dostarczają odpowiednio klientowi, sprzedawcy czy producentowi informacji o stanie, w jakim się znajduje dany produkt. Rozwinęły się one jako odpowiedź na preferencje konsumentów poszukujących produktów żywnościowych nieznacznie utrwalonych, świeżych, smacznych, wygodnych i o wydłużonym okresie przydatności do spożycia (produkty mleczne, pieczywo). Ponadto zmiany w sprzedaży detalicznej, takie jak np. globalizacja rynków i związana z tym dystrybucja towarów na duże odległości, przyczyniły się do zmian w koncepcji opakowań, tj. między innymi do wydłużenia czasu przydatności do spożycia, przy jednoczesnym zapewnieniu bezpieczeństwa i jakości zapakowanej żywności. Działanie opakowań inteligentnych związane jest z użyciem interaktywnych wskaźników, najczęściej barwnych, umożliwiających ocenę jakości produktu spożywczego (np. serów twarogowych, podpuszczkowych, gotowych kanapek). Ostrzegając, opakowania te wskazują kiedy żywność jest przechowywana w nieodpowiedniej temperaturze lub gdy uległa zepsuciu. Wyróżnia się dwa rodzaje opakowań inteligentnych: jedne bazują na pomiarze warunków na zewnątrz opakowania, a drugie mierzą bezpośrednio jakość żywności, czyli warunki panujące wewnątrz opakowania. Na rynkach światowych znane są obecnie następujące rodzaje opakowań interaktywnych: - integratory czasu i temperatury (TTI); - wskaźniki świeżości; - wskaźniki nieszczelności. Temperatura jest jednym z najważniejszych czynników decydujących o pojawieniu się w produktach spożywczych niekorzystnych zmian fizykochemicznych i drobnoustrojów. W żywności przechowywanej w temperaturze wyższej aniżeli jest to zalecane zachodzi gwałtowne zwiększenie się flory bakteryjnej. Zwykle produkt ulega zepsuciu przed upływem terminu jego przydatności do spożycia. Wskaźniki integratora czasu i temperatury (TTI), stosowane są w celu nieustannego monitorowania aktualnej temperatury produktu oraz jego środowiska (rys. 3). Zasada działania TTI polega na nieodwracalnej zmianie jego właściwości pod wpływem działania temperatury wyższej od wartości zadanej lub w wyniku efektu cieplnego, skumulowanego w czasie przechowywania i transportu. Następstwem tej zmiany jest proporcjonalny do jej natężenia efekt wizualny, wyrażający się najczęściej przebarwieniem pola etykiety. Jest to szczególnie istotne w przypadku mrożonek i produktów chłodzonych (margaryny, przetwory mleczne, mięsne), pozwalają one m.in. zarejestrować fakt przejściowego rozmrożenia produktu, przez co wskaźnik zmienia swoją barwę, informując nas o wymianie środowiska.
a.
b.
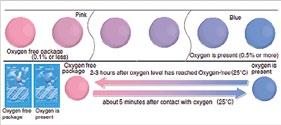

Rysunek 1. Torebki absorbujące tlen z opakowania (a.) i wskaźnik Ageless Eye (b.) tzw. „starzejące się oko”
Drugi typ TTI umożliwia monitorowanie wszelkich odstępstw od optymalnej temperatury w całym okresie dystrybucyjnym, jednocześnie sumując ich natężenie i czas występowania. Sygnał integratora pośrednio informuje o skróceniu bezpiecznego dla jakości okresu przechowywania. Wskaźniki czasu i temperatury, aby były skutecznym narzędziem służącym do monitorowania żywności, muszą spełniać określone wymagania między innymi takie jak: łatwość aktywacji, precyzja i dokładność pomiaru. Wskazania muszą być nieodwołalne, odtwarzalne i za-
leżne od zmian zachodzących w żywności, muszą też być czytelne i nie mogą wprowadzać w błąd użytkownika. Wskaźniki czasu i temperatury, od momentu aktywacji, wizualizują historię czasowo-temperaturową produktu mlecznego poprzez zmianę barwy lub przemieszczenie się barwnika. Barwa wskaźnika ulega zmianie w momencie, gdy opakowanie osiągnie uprzednio założoną pojemność cieplną.
Obecnie na świecie najbardziej znane są trzy rodzaje integratorów: • Life LineTM, w których zachodzi chemiczna polimeryzacja powodująca zmianę wyglądu okrągłego okna na etykiecie (tzw. bawolego oka), wskutek postępującego od centrum ciemnienia. Wskaźnik ten jest popularnym wskaźnikiem sprawdzającym świeżość produktów.
Składa się z polimeru znajdującego się wewnątrz koła otoczonego pierścieniem wzorcowym. Ciemniejsza barwa polimeru w części centralnej informuje konsumenta, że produkt nie nadaje się do spożycia bez względu na datę ważności, która jest umieszczona na opakowaniu.
• 3M Monitor Mark, który sygnalizuje zmianę za pomocą barwnego pierścienia (lub paska) przesuwającego się na białym tle. Jest to efekt fizycznej dyfuzji roztworu o zmienionej chemicznie barwie. Podczas przechowywania w odpowiednich (zalecanych przez producenta) warunkach wskaźnik jest biały. Wskaźnik tego rodzaju sygnalizuje moment przekroczenia przez produkt temperatury wyższej niż jest to zalecane dla zachowania przez niego odpowiedniej jakości. O przekroczeniu progu temperatury właściwej dla produktu świadczy czerwony lub niebieski kolor wskaźnika. Wskaźniki pokazują także, jak długo produkt znajdował się poza wymaganym zakresem temperatury. Różnią się natomiast między sobą zakresem temperatury, w jakim produkty mogą być przechowywane oraz czasem ich działania od momentu aktywacji.
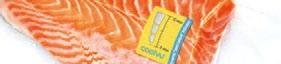
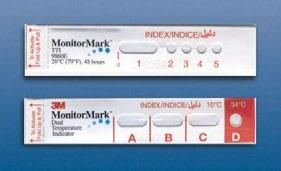
• Etykieta Vitsab (Visual Indicator Tag System AB), której działanie opiera się na enzymatycznej hydrolizie tłuszczów, prowadzącej do zmiany barwy sygnalizatora. Aktywacja wskaźnika następuje przez zniszczenie przegrody pomiędzy dwoma elementami, czyli pomiędzy płynem zawierającym lipolityczny enzym (lipazy), a jego lipidowym substratem i wskaźnikiem pH. Wraz ze zmianą pH dodany do systemu barwnik zmienia zabarwienie z zielonego na jaskrawożółtą, czy też pomarańczowo-czerwoną. Jest wskaźnikiem dostarczającym pełnej informacji o wszelkich zmianach i odstępstwach od optymalnych warunków temperaturowych w całym cyklu dystrybucyjnym.
Wskaźniki TTI są już obecnie stosowane w wielu krajach Europy do pakowania żywności wymagającej chłodzenia, zarówno w transporcie, jak i w witrynach sklepowych. Samoprzylepne etykiety można spotkać m.in. na opakowaniach ze świeżymi kanapkami, sałatkami, przetworami mlecznymi, mięsnymi. Drugą grupę opakowań inteligentnych stanowią wskaźniki świeżości, które różnią się głównie tym od TTI, że jakość produktu sygnalizują przez bezpośrednie reagowanie na zmianę składu atmosfery panującej w wewnętrznej przestrzeni opakowania (np. w przypadku pakowania sera podpuszczkowego w MAP, mięsa czy wędlin) lub na zmiany zachodzące na powierzchni samego produktu. Działanie opiera się zazwyczaj na wykrywaniu obecności metabolitów mikroorganizmów, takich jak: dwutlenek węgla, dwutlenek siarki, amoniak, aminy, siarkowodór, kwasy organiczne, etanol, toksyny i enzymy. W metodzie tej stosuje się głównie elektroniczne i optyczne detektory, a także barwne związki tworzące się w reakcji z substancją wchłanianą z wnętrza opakowania. Wśród proponowanych rozwiązań, najszersze zastosowanie znalazły etykiety Fresh Tag. Zawierają one wkładkę z tworzywa sztucznego z zamocowanym w jej wnętrzu pierścieniem (od strony opakowania). Pierścień zawiera opatentowaną substancję chemiczną, będącą w bezpośrednim kontakcie z gazami dyfundującymi z wnętrza opakowania i tworzy barwną reakcję z lotnymi aminami obecnymi w gazie. Wraz ze wzrostem stężenia amin, jaskrawożółta plama ulega przesunięciu na termometrycznej skali pierścienia, określając aktualną jakość produktu spożywczego. Powstały również systemy reagujące na różnego rodzaju bakterie np.: Salmonella, Campylobacter czy Escherichia coli. Kolejną grupę opakowań inteligentnych stanowią wskaźniki nieszczelności. W opakowaniu, które jest nieszczelne zmniejsza się zabezpieczające oddziaływanie zmodyfikowanej atmosfery na produkt i wzrasta niebezpieczeństwo mikrobiologicznego zanieczyszczenia poprzez zwiększoną podatność produktu na niebezpieczne dla zdrowia człowieka drobnoustroje. Wskaźniki pomiaru zawartości tlenu i ditlenku węgla (CO2) w opakowaniu, przykładowo: Ageless Eye oraz TellTab Oxygen Indicator, jako wskaźniki nieszczelności, mogą być użyte do monitorowania jakości m.in. produktów spożywczych (m.in. sery twarogowe, podpuszczkowe). Zasada działania tego rodzaju wskaźników oparta jest na zmianie ich koloru w wyniku reakcji chemicznej lub enzymatycznej. Wskaźnik w warunkach beztlenowych ma barwę różową, a przy dostępie tlenu w przeciągu kilku minut ulega zmianie i zmienia zabarwienie na niebieskie. Najczęściej stosowanym redukującoutleniającym barwnikiem we wskaźnikach nieszczelności w odniesieniu do tlenu jest niebieski metylen. Wskaźniki te muszą kontaktować się ze środowiskiem gazu wewnątrz opakowania i stąd pozostają w bezpośrednim kontakcie z żywnością. Jednak reakcje są odwracalne przy zmianie warunków na beztlenowe.
Wskaźniki jakości pozwalają na monitorowanie warunków, w jakich dane opakowanie oraz zawarty w nim produkt znajdowały się podczas przechowywania, transportu, sprzedaży detalicznej i przechowywania w domu konsumenta. Wskaźniki świeżości sygnalizują zmiany jakości produktu np. bezpośrednio po zmianie składu atmosfery wewnątrz opakowania. Idealny wskaźnik powinien wskazywać zarówno nieprawidłowości powstałe na etapie produkcji, jak i utratę „świeżości” opakowanych produktów w dalszych etapach dystrybucji i użytkowania. Głównym elementem wskaźnika jest substancja, która w obecność metabolitów zmienia barwę np. w wyniku tworzenia barwnych kompleksów lub zmienia swoje właściwości optyczne. Do identyfikacji zmian mogą być również wykorzystywane detektory elektroniczne. Idea działania opiera się na reakcji substancji aktywnej z wydzielającymi się podczas starzenia opakowanych produktów lotnymi metabolitami np. ditlenku węgla, amin, amoniaku, siarkowodoru. Lotne produkty rozkładu np. siarkowodoru mogą być wykrywane przez wskaźniki oparte na typowych reakcjach chemicznych, natomiast do wykrywania produktów nielotnych wykorzystuje się reakcje enzymatyczne. Do pierwszej grupy należą np. indykatory oparte na reakcji mioglobiny z siarkowodorem. W wyniku reakcji zmienia się zakres promieniowania absorbowanego przez mioglobinę, w wyniku czego wskaźnik w obecności siarkowodoru zmienia zabarwienie z brązowego na czerwone. Wskaźniki z mioglobiną jako substancją czynną zalecano do śledzenia zmian jakości mikrobiologicznej drobiu w opakowaniach z atmosferą modyfikowaną. Wskazano też na dobrą korelację pomiędzy informacjami uzyskanymi za pomocą wskaźników a wynikami badań sensorycznych i mikrobiologicznych. Ciekawym pomysłem inteligentnego opakowania są konstrukcje sygnalizujące rozpoczynające się w opakowaniu procesy gnilne. Obecnie na etapie badań są czujniki, które zmianą barwy informowałyby o pojawieniu się nawet bardzo niewielkich ilości amin powstających w wyniku rozkładu białka. Opracowywane są także indykatory, reagujące na pojawienie się w produkcie choćby śladowych ilości toksyn wytwarzanych przez mikroorganizmy. Innym przykładem specyficznych indykatorów wzrostu bakteryjnego, użytecznych w opakowaniach inteligentnych, są systemy indukujące i wykrywające wybrane enzymy zewnątrzkomórkowe. Takie rozwiązanie nie było jeszcze praktycznie wykorzystane, chociaż doczekało się już patentu. Niezależnie od tego, jaka będzie ostateczna forma opakowań przyszłości, jedna rzecz jest pewna „tak długo, jak ludzie będą chcieli przewozić i magazynować żywność, zawsze będzie potrzeba stosowania opakowań”. Omawiane systemy, przeznaczone do kontroli jałowości żywności w hermetycznych opakowaniach, wykorzystują na przykład wykrywanie specyficznej proteazy. Opracowano też czujniki sterylności z przeznaczeniem do opakowań z odżywkami mlecznymi dla niemowląt, oparte na wykrywaniu amylazy.
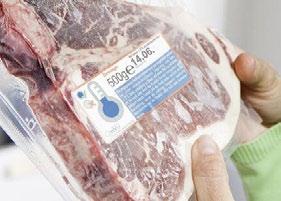
Podsumowanie
Wykorzystanie nowoczesnych rozwiązań w przemyśle opakowaniowym może prowadzić do ograniczenia zużycia ilości konserwantów, poprawy cech sensorycznych żywności i zapewnienia jej bezpieczeństwa mikrobiologicznego. Według prognoz ekspertów, powstające generacje opakowań inteligentnych stanowią przyszłość opakowalnictwa żywności. Powszechna jest również opinia, że opakowania aktywne i inteligentne w połączeniu z pakowaniem w kontrolowanej i modyfikowanej atmosferze mogą w przyszłości wywrzeć znaczący wpływ na rozwój przemysłu mleczarskiego. Zatem wraz z rozwojem technologii, które pozwalają na obniżanie kosztów produkcji oraz dzięki zmianom legislacyjnym, należy spodziewać się szerszego upowszechnienia opakowań inteligentnych. •
Atmosfera chroniąca żywność
Naciśnij i przejdź na naszą stronę www
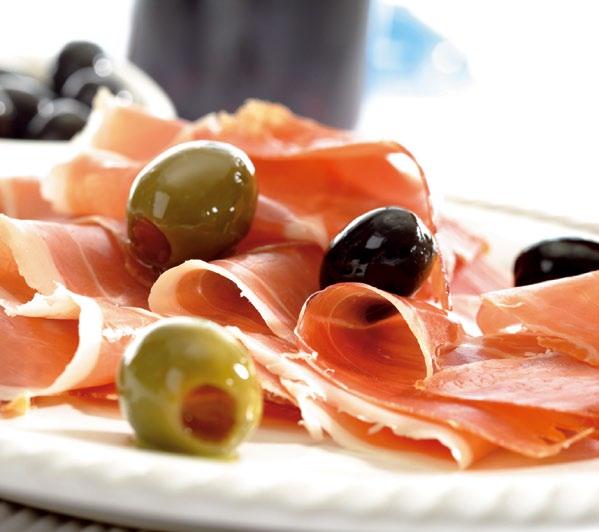
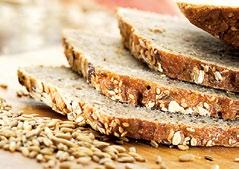
Gourmet® to linia gazów ochronnych takich jak azot, dwutlenek węgla i tlen oraz ich mieszaniny, stworzona przez Messer dla przemysłu spożywczego. Korzyści stosowania gazów osłonowych Gourmet® w procesie pakowania żywności, w skrócie nazywanej MAP: • wydłużona trwałość produktów spożywczych oraz dłuższy okres przydatności do spożycia • lepsza stabilność mikrobiologiczna w porównaniu do pakowania próżniowego • zachowanie naturalnego kształtu i koloru produktu • eliminacja procesu utleniania • zabezpieczenie przed wysychaniem produktów • zwiększenie efektywności prowadzonych procesów produkcyjnych. Ogromna różnorodność produktów spożywczych nie pozwala stosować atmosfery ochronnej o jednakowym składzie dlatego zachęcamy do kontaktu z naszymi specjalistami z obszaru aplikacji spożywczych, którzy służą doradztwem w zakresie doboru optymalnych gazów spożywczych oraz zwiększenia efektywności prowadzonych w Państwa zakładach procesów produkcyjnych.
Messer Polska Sp. z o.o. ul. Maciejkowicka 30 41-503 Chorzów tel. +48 32 77 26 000 fax +48 32 77 26 115 messer@messer.pl www.messer.pl
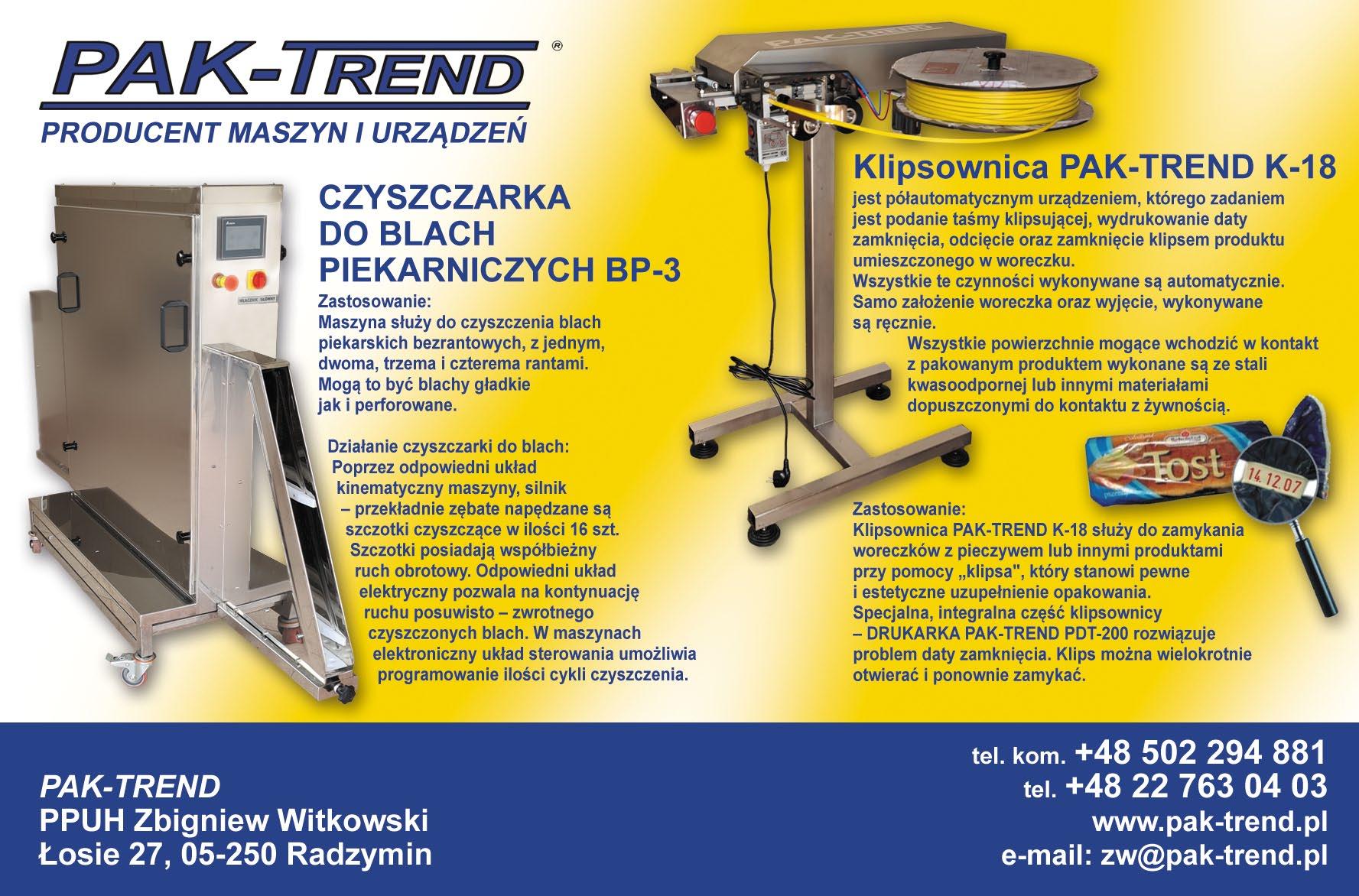
Naciśnij i przejdź na naszą stronę www
FR 400 to maszyna w pełni sterowana elektronicznie.
Oznacza to, że każdy element ruchomy jest sterowany i napędzany niezależnie. Została zaprojektowana z myślą o współpracy z liniami pakującymi o średniej oraz wysokiej prędkości produkcji. Wydajność do 400 opakowań na minutę. Model ten może być wyposażony w różne typy podajników oraz automatyczne systemy załadunku zaprojektowane głównie dla wyrobów piekarskich oraz cukierniczych. Maszyna posiada system odrzucania pustych oraz błędnie zgrzanych opakowań oraz automatyczną zmianę rolki folii.
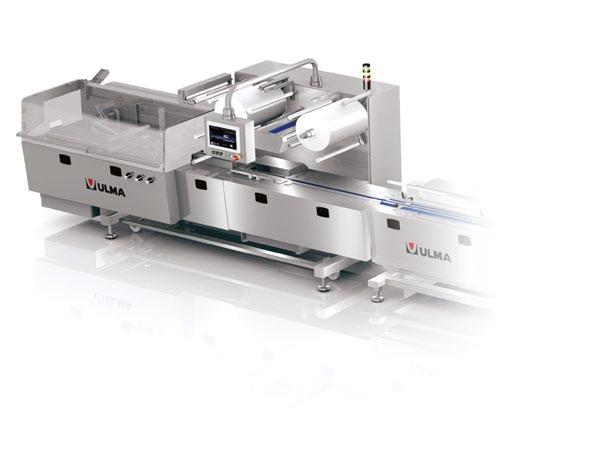
ULMA FR BOE
To specjalnie zaprojektowana maszyna do pakowania produktów delikatnych i kruchych tj. wafelki czy herbatniki. Posiada uniwersalny system do załadunku grupy produktów o różnych kształtach i wymiarach. Produkty pakowane są w opakowania typu „Flow - pack”. W wersji elektronicznej w przeciwieństwie do mechanicznej każdy element ruchomy jest napędzany osobnym silnikiem. Rozwiązanie takie skutkuje łatwością przestawienia maszyny na inny produkt oraz opcjonalnie umożliwia użycie funkcji: „brak produktu - brak opakowania”, „produkt przesunięty – podwójne opakowanie”.
ULMA Packaging Poska Sp. z.o.o.
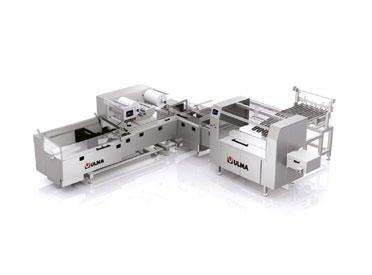
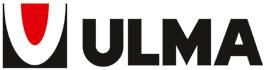
biuro@ulmapackaging.pl www.ulmapackaging.pl
Naciśnij i przejdź na naszą stronę www
Kliknij, by zobaczyć film
R E K L A M A
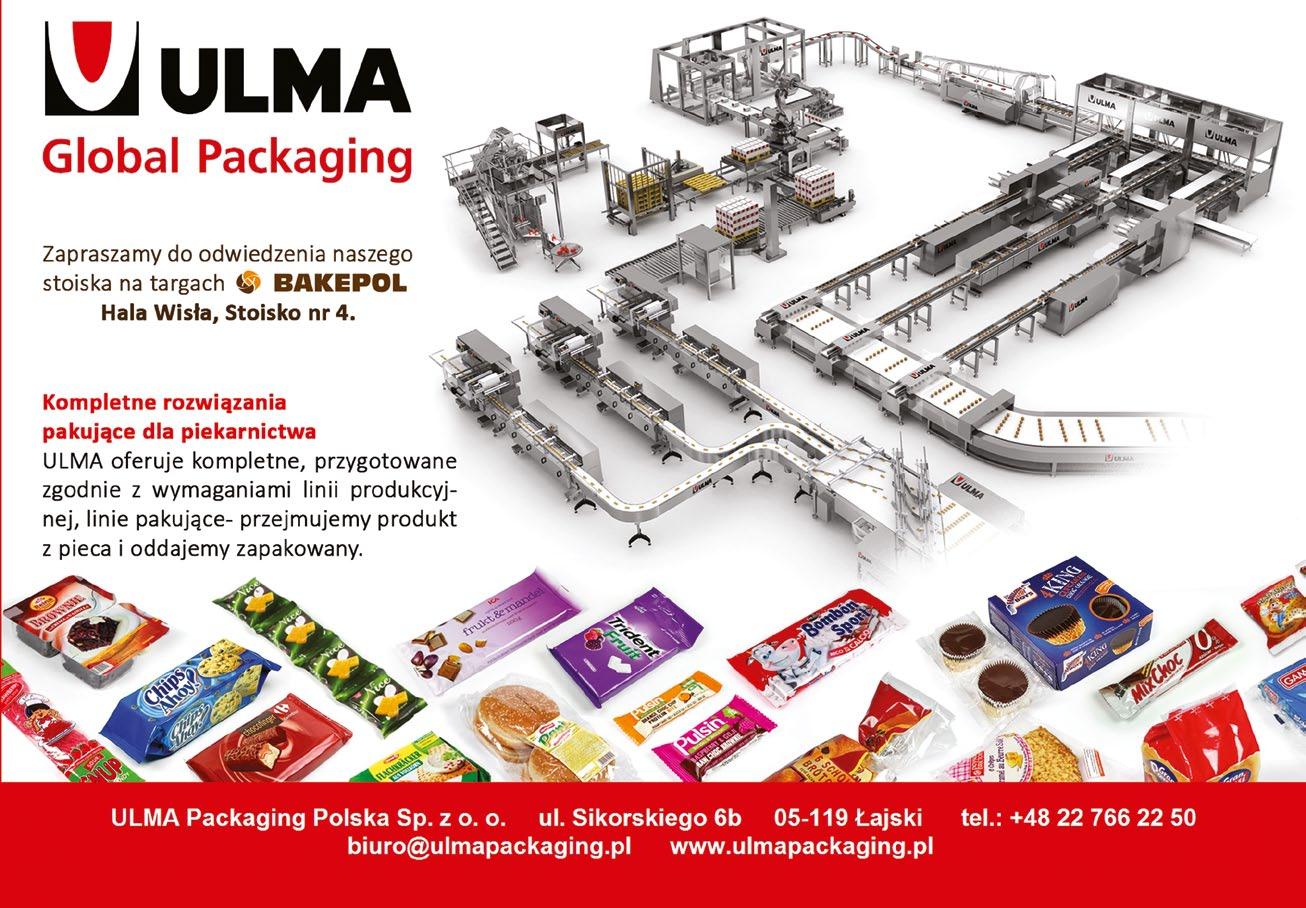