July - August 2022miningbusinessafrica.co.za
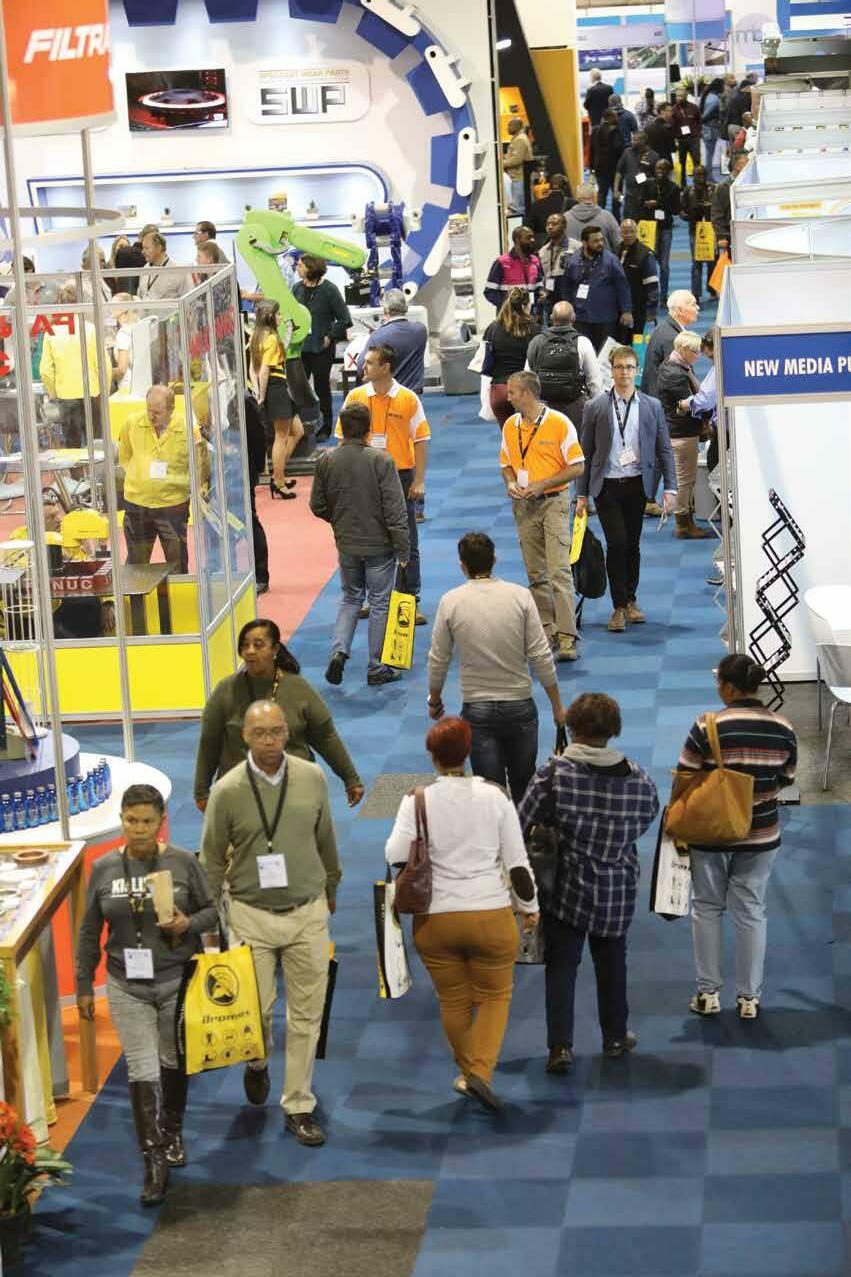
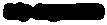

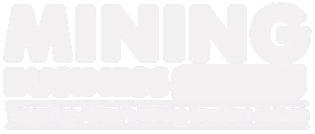
B u i l d i n g a g r e e n h y d r o g e n b u s i n e s s m o d e l U n l o c k i n g g r e e n h y d r o g e n d e v e l o p m e n t ’s p o t e n t i a l i n S o u t h A f r i c a E n a b l i n g r e g u l a t o r y e n v i r o n m e n t f o r t h e d e v e l o p m e n t o f g r e e n h y d r o g e n W h a t i s t h e r o l e o f p u b l i c o r p r i v a t e fi n a n c e i n t h e S o u t h A f r i c a n h y d r o g e n e c o n o m y H y d r o g e n p r o d u c t i o n , s t o r a g e a n d t r a n s p o r t a t i o n - I s S o u t h A f r i c a t h e n e x t g l o b a l p o w e r h o u s e o f p o w e r f u e l s H y d r o g e n a n d d e c a r b o n i s a t i o n - W h a t p a r t c a n h y d r o g e n p l a y i n S o u t h A f r i c a ’s e n e r g y t r a n s i t i o n F u e l o f t h e f u t u r e - H o w f a r c a n h y d r o g e n g o i n f u e l l i n g t h e m a s s t r a n s p o r t a t i o n o f p e o p l e a n d p r o d u c t s W h a t p r o s p e c t w i l l h y d r o g e n’s f u t u r e l o o k l i k e i n S o u t h A f r i c a
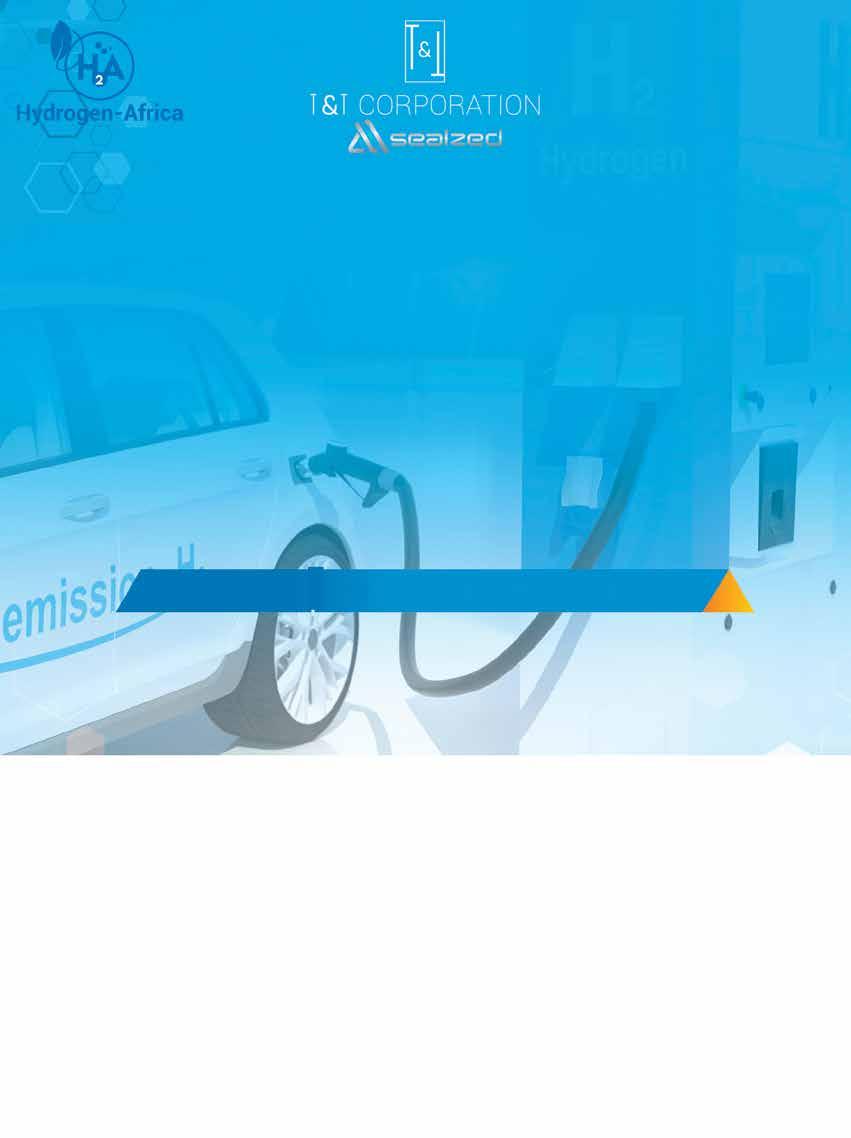
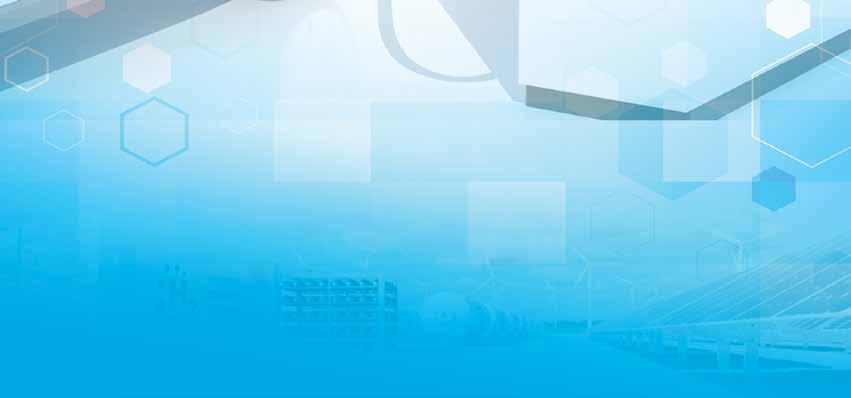
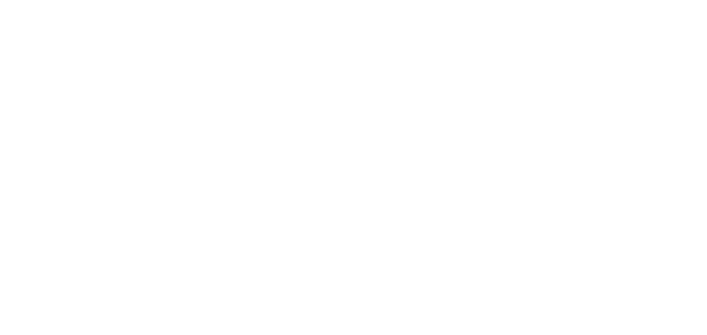
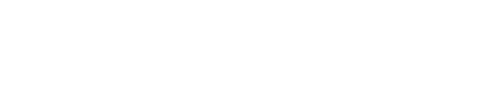


023222 CONTENTS July - August 2022 Media Icon (Pty) Ltd makes every effort to ensure the accuracy of the contents of its publications, but no warranty is made as to such accuracy and no responsibility will be borne by the publisher for the consequences of actions based on information so published. Further, opinions expressed are not necessarily shared by Media Icon (Pty) Ltd. www.miningbusinessafrica.co.za Editor’s Note
editor@miningbusinessafrica.com
Unavoidably, the situation has impacted both projects and operations. At best, the components are beyond the budget, and at worst, the manufacturers or suppliers cannot provide them as and when needed. The former has contributed to an increase in capital expenditure (CAPEX), while the latter resulted in disruptions to production due to unexpected downtime.Remarkably, the common challenge to most mining companies is the single-source supply model, particularly, the overreliance on China, the biggest supplier of mining-related equipment. Understandably, from a cost-savings standpoint, the low cost of production in the country and the Yuan’s low exchange rate in dollar terms had made China a feasible option. The Ukraine-Russia war has compounded the problem. Rising energy prices have simultaneously led to an increase in shipping costs and a rise in equipment prices.
July August 2022miningbusinessafrica.co.za Editor Nick +27editor@miningbusinessafrica.co.zaBarnes100553356 Web/Sub-Editors Jimmy anyangoanita18@gmail.comAnita+Jimmy@miningbusinessafrica.co.zaSwira27100553356Anyango Contributing Writers Chantelle +chantellec@miningbusinessafrica.co.zaC.27100553356 Susan susanm@miningbusinessafrica.co.zaM. Sales and Marketing Winnie ++angien@miningbusinessafrica.co.zaAngeline+27winnie@miningbusinessafrica.co.zaSentabire835306832|+27100553356Ntobeng270783225938270100553356 Accounts Precious +accounts@miningbusinessafrica.co.zaChirunga27100553356 Art Director/Layout Augustine Ombwa Arobia Creative +254austin@arobia.co.keConsultancy772187334 Circulation/Sales +info@miningbusinessafrica.co.za27100553356 Published By Media Icon (Pty) Ltd TEAM Electra Mining Africa 2022 COVER STORY: PG02 Cover Image: Electra Mining Africa Exhibitors, their associates, together with potential and existing clients are excited about the forthcoming Electra Mining Africa 2022. The event is the first “Live, In-person“event after a three-year hiatus when the world shut down to cope with the beginning of the COVID-19 pandemic. 12
Delays in the delivery of critical components and equipment from manufacturers and suppliers located in different regions are hampering mining operations. Initial optimism that the situation in the global supply chain would rapidly get into gear, functioning as efficiently as it was preCOVID-19 has turned out to have been very naive.During hard lockdowns implemented in countries, manufacturers halted operations. This has resulted in huge backlogs of unattended orders from clients globally.
Broader Supplier Base, Minimal Disruptions
Observing the situation, supply chain experts have warned that the situation may not normalise as soon as mining companies might wish. They have suggested that the practical step is for mining companies to consider broadening their equipment suppliers. In this way, the impact of disruptions due to delays or non-delivery on their projects and operations can be minimised.
Nick Barnes

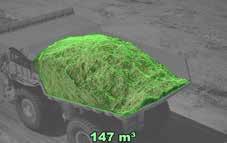
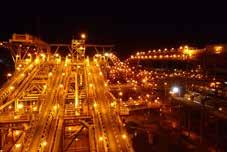





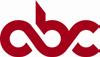
The state-of-the-art mining-specific equipment is on display.
Electra
The economic impact of the Ukraine war
The war in Ukraine has critically threatened the world’s energy supplies, disrupted global supply chains and caused significant price inflation and rising fuel prices. According to Yvonne Mhango, head of African Research at Renaissance Capital, heightened energy prices will be felt most severely in skyrocketing transport and utility costs. Exhibitors, their associates, together with potential and existing clients are excited about the forthcoming Electra Mining Africa 2022. The event is the first “Live, In-person“event after a three-year hiatus when the world shut down to cope with the beginning of the COVID-19 pandemic.
Specialised Exhibitions’ Response: Covid-19 effects The Covid-19 pandemic had disastrous consequences on the exhibitions and events industry, with the impact of the last two years having decimated many of the smaller industry players. However, the core of the industry has survived and the bigger organisers and shows have survived. Exhibitions and events are now successfully re-opening globally and the good news for local industry is that Electra Mining Africa will be going ahead as a live in-person Mining Africa Electra Electrifies Stakeholders
FEATURE
2022 Forthcoming
2 Mining Business Africa | July - August 2022
MBA: The conference and exhibitions sector has been adversely affected by the Covid-19 pandemic, and lately the economic impact of the Ukraine War, events relating to construction and mining being no exception. Despite this situation, what opportunities do ‘Live in-person’ events present to suppliers of various technologies to the mining sector? What about organisations like Specialised Exhibitions?
event this year. Since February, several B2B exhibitions have taken place successfully with excellent results being reported by all involved. In general, there have been fewer people – both exhibitors and visitors – but the quality of both is high. Those involved in shows that have already taken place, such as the KZN Industrial Show, Propak Africa, A-OSH, Securex and Frigair say that while the shows may have been smaller and visitor numbers less, the quality of both is higher. These were world-class shows that provided an excellent platform for buyers and sellers to connect and for business trade to take place.
The event attracts a cross section of stakeholders in Africa’s mining industry
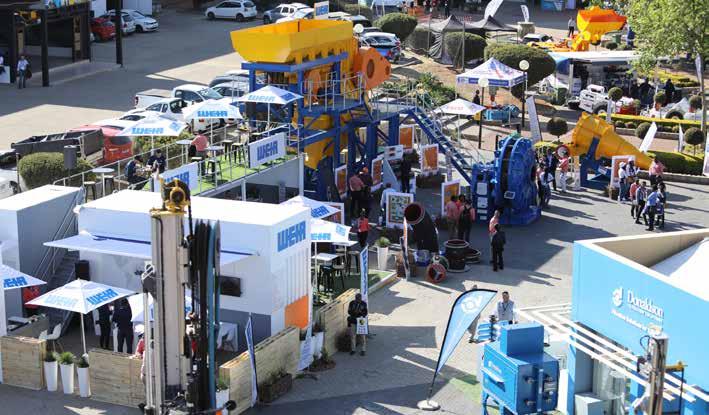
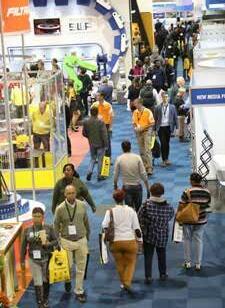
MBA: How has been the response of stakeholders in the mining sector to the Mining Indaba 2022 - the first physical Mining Indaba – after the lull that the COVID-19 pandemic occasioned? Specialised Exhibitions’ Response: According to Hyve, organisers of Investing in African Mining Indaba 2022, the event was a “reunion like no other” with the mining community back together all under one roof. This year’s overarching theme was ‘Evolution
Mining Business Africa | July - August 2022 3 WearCheck, Africa's leading condition monitoring company, is dedicated to saving money for you, our customers. We analyse data from condition monitoring and fluid analysis to schedule maintenance and avoid unexpected machine failure. Accurately predicting maintenance = saving you time and money. Condition Monitoring is at the heart of machine reliability Branches GhanaBotswana Mozambique ZimbabweZambiaUgandaNamibia +267 311 6829 +233 20 896 8484 + 258 843 173 781 +264 81 129 6078 +256 78 529 6994 +260 212 210 161 +263 24 244 6369 + 27 31 700 5460 support@wearcheck.co.za www.wearcheck.co.za South Africa (Head Office) Scan for brochure Testing and Analysis | Lubricant-Enabled Reliability | Asset Reliability Care CMYCYMYCMYMCK WCk Advert AMB 180mmx130mm June 22 Print.pdf 1 2022/06/29 2:55 PM Opportunities for live in-person events for suppliers However, despite this situation, industries have been celebrating being back at in-person trade events in South Africa. Shows offer access to fresh new thinking and provide a platform to showcase the latest cutting-edge machinery, products, consumables, systems and services. Both local visitors and international visitors are visiting the shows; the internationals mainly being from across the west, east, south-central and southern African countries. These events have provided a much-needed platform for buyers and sellers to connect face-to-face again after two years of restrictions due to the Covid-19 pandemic. They provide an opportunity for industry networking to take place again, for the onsite sales of machinery and products or services, to build business partnerships and to launch new products and services.Thetop reasons for visiting include the sourcing of products and solutions, finding out about the latest industry trends and developments, and networking with peers. Trends identified since this year’s re-opening of exhibitions: fewer visitors but the quality of visitors has been excellent; quality visitors from Africa; the exhibitions are smaller but this has allowed for local innovation and technology to shine through; provide a valuable platform for marketing and business/trade; also a good platform to reconnect with existing customers that may not have been seen over the past two years; and seen as a good platform to find and interact with new potential customers, to build awareness and to showcase new products and innovations. Opportunities for organisations, such as Specialised Exhibitions The two-year hiatus of exhibitions and business events highlighted the importance of these events. It was apparent that they were missed and had an important role to play. The exhibition and business events industry believes that they will bounce back stronger than they were before with innovation and technology being embraced to enhance them even further. An initiative of UFI – the Global Association of the Exhibition Industry, the seventh edition of Global Exhibitions Day (GED) took place on 1 June 2022. GED events were held around the world to celebrate and promote the role of faceto-face business events in driving the global economy. Exhibitions have always played a role in bolstering and growing economic sectors –and this year has been no exception. This year’s GED campaign focused on the irreplaceable value of physical exhibitions and face-to-face business events in creating platforms for economic growth and recovery and the vital role they play.










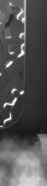



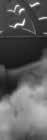



















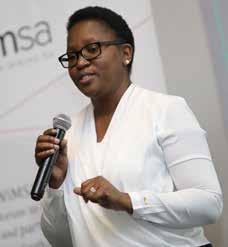
MBA: What about measures to cope with the changes the COVID-19 pandemic has brought? Specialised Exhibitions’ Response: Patrons appreciating equipment on display during the 2018 event
MBA: What specific changes have you introduced to add more value to the event for participants and patrons? Specialised Exhibitions’ Response: Electra Mining Africa will be taking place from 5-9 September at the Expo Centre, Nasrec, in Johannesburg. Specialised Exhibitions, organisers of the show, are promising an exciting interactive event with many activities planned by exhibitors and industry partners, and to also celebrate Electra Mining Africa’s 50th
of African Mining: Investing in the Energy Transition, ESG, and the Economies.”
* The event was initially expected to attract around 4,000 delegates on the back of the Covid-19 pandemic, whereas the final number of delegates was over 6,500 according to Simon Ford, Portfolio Director for the Mining Indaba. The event also hosted three heads of state from South Africa, Botswana and Zambia as well as the Prime Minister from the DRC and forty governmentPresidentministers.CyrilRamaphosa, who addressed delegates on the second morning of the Investing in African Mining Indaba 2022, highlighted that the event was taking place at an important time in the globe’s recovery from the impact of Covid-19, saying that “Across the world, almost every industry is having to adapt to new circumstances, confront new challenges and be prepared to seize new opportunities.”
Day 1: Automation Day | Connecting with the future Day 2: Innovation Day | All that’s new in machinery, products & technology Day 3: Safety Day | A focus on Occupational Health & Safety Day 4: Future Skills Day | Training & Skills Advancement trends Day 5: South African Day | Celebrating 50 years and all things local A business matchmaking programme will enhance the event through the pre-matching of visitors and exhibitors and the making and management of business meetings on-site at the event.
ToForanniversary.example:promotethe
The Lifting Equipment Engineering Association of SA (LEEASA), Women in Mining South Africa (WiMSA), and the Society for Automation Instrumentation Mechatronics and Control (SAIMC) will be running conferences alongside Electra Mining Africa. The new ‘Theme Days’ concept launched at Electra Mining Africa 2018 was enjoyed by both exhibitors and visitors. The ‘every day a theme day’ experience will again be part of this year’s event with Automation Day, Innovation Day, Safety Day, Future Skills Day and South African Day confirmed. The topics for the free-to-attend seminars will align with the theme days.
After a virtual event in 2021, the support from stakeholders in the mining sector to the Mining Indaba 2022 to get back to a physical event in 2022 was exceptional and demonstrated the need and value of these types of events where face-to-face interaction is so important.
4 Mining Business Africa | July - August 2022
FEATURE
*source: www.miningindaba.com
importance of Forklift operations and operators in the Supply Chain & Logistics industry, Lifting Africa and LEEASA (Lifting Equipment Engineering Association of SA) will be hosting a Forklift Driver competition during Electra Mining Africa. The event will provide forklift operators with an opportunity to prove their driving skills, compete with others around Johannesburg, win prize money, as well as achieve recognition as a champion. Entries are open for all operators who have a valid Forklift license and can drive either a reach truck or a counterbalance Forklift Truck in racking. The focus of the competition is on accurate, safe driving skills and knowledge, not on speed. The first round of heats for counterbalanced forklift operation will be an online test to assess entrants’ practical skills, theoretical knowledge, attitude and efficiency. Lifting Africa and LEEASA want to assist in promoting the importance of inspection, safety and training and to reward the safest forklift drivers at Electra MiningElectraAfrica.Mining Africa and co-located shows Elenex Africa, Powerex, Transport Expo and Automation Expo will be supported by a programme of content-rich conferences and free-to-attend seminars with industry experts speaking on a range of topical and important issues. The SA Institution of Mechanical Engineering (SAIMechE) seminars will be live-streamed to enable a wider audience to participate in the learning experience.

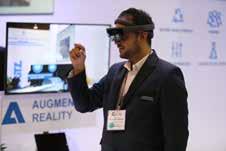

Specialised Exhibitions’ Response: Electra Mining Africa is a much-needed platform for buyers and sellers to connect face-to-face again. It presents an opportunity for industry networking to take place, to build business partnerships and new connections, and for new products and services to be launched. Electra Mining Africa and its line-up of conferences and free-to-attend seminars will be taking place from 5-9 September at the Expo Centre, Nasrec, in Johannesburg. Hundreds of exhibitors are ready to showcase their latest innovations, technology, products and services at Southern Africa’s biggest mining, electrical, automation, manufacturing, power and transport trade exhibition. 550 exhibitors are currently confirmed; more are expected. Industry stakeholders were disappointed that the opportunity to interact face-to-face at Electra Mining Africa in 2020 was not possible, due to the Covid-19 hiatus. It’s an exhibition viewed by industry as one of the most important events on the Exhibitorscalendar. are eager to get back to the faceto-face environment and to the business and trade opportunities that Electra Mining Africa offers. For the past five decades, Electra Mining Africa has built a strong reputation for its ability to effectively connect people and industries, buyers and sellers. As in previous years, many respected Associations and industry organisations will be partnering with Electra Mining Africa.
Face-to-face interaction facilitates the building of relationships and trust; live demonstrations engage the senses, and networking and collaboration between industry professionals can take place. The Global Association of the Exhibition Industry (UFI) advocates for the irreplaceable value of physical exhibitions and face-to-face business events in bringing people together and driving the global economy; there is power in face-to-face events that create platforms for economic growth and recovery. As per the answer above, following global trends, exhibitions are adopting more technology and moving to hybrid events. What is clear from the February 2022 UFI Global Exhibition Barometer Report is that the majority of respondents agree that virtual events will not be replacing physical events.
MBA: Last but not least, what is your message to companies that could be thinking about participating in future Electra Mining events on the values they can get?
Mining Business Africa | July - August 2022 5 Without compromising on the visitors’ ability to effectively interact with the exhibitors, several measures will be in place to ensure that Electra Mining Africa (and all our exhibitions) complies with the government’s regulations for safe social exchanges.Ourindustry is so well regulated and safety is a prerequisite to any event plan. This was the case even before the global pandemic. Exhibition organisers and venues involved are more than capable of putting together a public event that falls within the World Health Organisation and local government COVID-19 regulations.According to the Global Association of the Exhibition Industry (UFI), as the pandemic recedes, the exhibitions industry has made a remarkable comeback thanks to its resilience, innovation, and strength. Exhibition organisers and associations have managed to quickly bring live event platforms back. Indeed, events are seeing levels of attendance similar to those before the pandemic driven by pent-up demand especially from small and medium-sized businesses to meet and do business face-toface.The industry has been united to bring safe, successful events back to life.
Charlene Hefer, Portfolio Director at Specialised Exhibitions, has confirmed that the Society for Automation Instrumentation Mechatronics and Control (SAIMC), the SA Institution of Mechanical Engineering (SAIMechE), Mining Equipment Manufacturers of South Africa (MEMSA), the South African Mineral Processing Equipment Cluster (SAMPEC), South African Capital Equipment Export Council (SACEEC), Southern African Institute of Mining and Metallurgy (SAIMM), Women in Mining South Africa (WiMSA) and the Lifting Equipment Engineering Association of SA (LEEASA) are on board as Companiespartners.exhibiting at Electra Mining Africa will have the opportunity to generate on-site sales and pre-qualified sales leads, connect with quality buyers and decision-makers, build new and existing relationships, launch new products and services to the industry, increase their product and brand awareness, strengthen business growth and invigorate connections with industry.Thousands of local and international purchasing decision-makers and influencers will be attending Electra Mining Africa. With its proven track record for driving sales and increasing sales leads, it’s the ultimate platform to showcase the latest products, services, technologies and innovation; a chance to experience the power of live, face-to-face marketing.
MBA: Can you tell our readers in mining about the relevance of physical events like Electra Mining Africa 2022 in the face of the growing niche of virtual events? Specialised Exhibitions’ Response: Following global trends, exhibitions are adopting more technology and moving to hybrid events. Whereas exhibitions remain a face-to-face, in-person event, technology can make the exhibition experience even more enjoyable, driving many aspects of the exhibition from registration to live stream of events. What is clear from the February 2022 UFI Global Exhibition Barometer Report is that the majority of respondents agree that virtual events will not be replacing physical events. The Report also indicates an optimistic outlook for the exhibition industry; data from the barometer backs this up. Says Monica Lee Muller, President of UFI - The Global Association of the Exhibition Industry: “the Barometer results highlight the accelerating pace of the industry’s recovery in 2022, following the severe impact of COVID still felt on activities in 2021. There is strong anticipation that the sector, primarily driven by physical exhibitions and business events, will bounce back quickly.”
UFI CEO Kai Hattendorf added that “in most parts of the world, this year is seeing the exhibition and business events industry busier than ever. Shows are back and calendars are tight.” He confirms the importance of live in-person events, saying that “business events drive the recovery and re-connection of industries, sectors, and economies”, and their importance cannot be underestimated. Exhibitions that have already taken place this year reinforce the power of face-to-face connection and the value of our services. Exhibitors and visitors are returning to the show floor with urgency and enthusiasm. With the addition of digital and data services complementary to our in-person platforms, we are enhancing and evolving our event experiences to do even more for the markets we serve.
MBA: Can a virtual event for suppliers be as effective as a physical one? Specialised Exhibitions’ Response: Face-to-face interaction has been greatly missed in the exhibitions and events industry. Although online events and virtual exhibitions filled the void and created an environment where buyers and sellers could engage remotely, these fell short of the in-person, face-to-face experience. Exhibitions in the modern world remain incredibly relevant. Even with the growth of the digital age, human beings are gregarious and social by nature, they need personal contact.
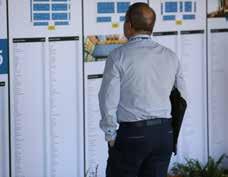
Currently, the demand for various minerals on the global market is increasing. And as you would expect, to make the most of this situation, mining companies are seeking opportunities in various avenues that can enable them to increase productivity in their operations from pit to port. Louis Nortje, the Managing Director of Symplexity, a proudly South African BBBEE Level 1 organisation, suggests that one of the avenues that mining companies should consider exploring, for potential opportunities, is a fully integrated real-time Human Resources and Payroll solution. A solution that manages the most complex environments in a simple and comprehensive manner throughout the employee life-cycle. In particular, he urges them to adopt alternative solutions that can simplify and rationalise their efforts for efficiency and productivity. “Management at mines should ask themselves: How effective is our Human Resource and Payroll system?” To underscore the business case for alternative human resources and payroll management systems, Nortje highlights how the inherent limitations of traditional methods impact mining operations.
6 Mining Business Africa | July - August 2022 Symplexity software has emerged as one of the highly regarded integrated and realtime human resources and payroll solution that can be recommended for industries. FEATURE
Human Resources and Payroll Management for mineworkers
Unfortunately, traditional approaches have limitations in meeting these requirements. Mainly, these include but may not be confined to non-flexible payroll systems, manual calculations, excel-based payroll solutions and disparate multiple system databases which increase the risk of human error. This poses further challenges in managing attendance, leave, and claim payments, among others. Legislative and statutory compliance become problematic which can lead to penalties for non-compliance and potential strike action. Ultimately, the impact on resourcing increases and, subsequently, productivity and efficiency decreases. Based on these limitations, there is a compelling business case for mining companies to switch from the traditional approach of payroll management to alternative methods.
Consistent, Accurate and On-time Payments from a Single Point
Inherent limitations of traditional approaches Ideally, within industries such as mining and construction, payroll systems require complex calculations and the ability to process large volume payroll transactions with ease. In addition, they should have the ability to manage large-scale contractor payments to ensure that consistent, accurate and on-time payments are done through one system.
Organisations that use traditional approaches to attendance and payroll management encounter various challenges in complying with statutory and legislative regulation, updating and managing multiple systems and effectively processing payroll at a click of a button. As an alternative, with multiple interfaces and third-party integration, Symplexity’s software has emerged as one of the highly regarded, integrated and real-time Human Resources and Payroll solutions that can be recommended for complex and non-complex industries and their workforce.
The convenience of Integrated and real-time solutions Integrated and real-time HR and payroll solutions, as an alternative technique, address the limitations of traditional approaches. This is based on evidence gathered from organisations that have adopted them. For instance, with a growing portfolio of successes registered in different sectors,
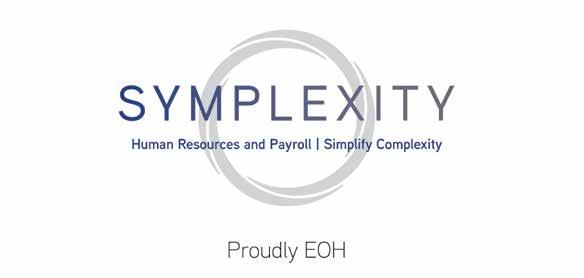
• Accommodation allows for the provision and management of accommodation to mine workers.
In general, the solution includes all functionality required to manage the full life cycle of an employee and includes strategy and planning, recruitment and selection, development and counsel, reward and retain re-deployment and exit management. Convenient options for end-users Nortje explains that, for the convenience of end-users, Symplexity software licence can be acquired through a rental or purchase option. “The software can be hosted in the Cloud in a Data Centre on Data Centre infrastructure and hardware (Shared Environment) or hosted in the Cloud in a Data Centre on Data Centre infrastructure or own hardware. For clients that opt for providing their own IT Infrastructure, the on-premise solution proves to be the favoured model and for clients preferring to outsource IT infrastructure, the SAAS model is more appropriate.”
Customised to client’s needs Scrupulously, several steps are undertaken to ensure that the solution provided is customised to the client’s needs, Nortje points out.
“Understanding the client’s environment, their business challenges and requirements is key to allowing us to provide tailored customised solutions. We follow a deep dive process of understanding the client and their requirement and how this is aligned to their overall business strategy and desired outcomes.
Symplexity is aware that there are times when clients can encounter problems when using the software. Thus, to pre-empt costly downtime, it offers requisite post-installation services to ensure that the software is updated and, most importantly, is delivered as expected. Currently, various support models are available, ranging from a dedicated consultant supporting the client environment through to hourly support. Continuously abreast of changing needs Symplexity leaves no stone unturned to remain adequately resourced to continuously keep abreast of changing requirements in industry-specific human resource and payroll management. True to form, the company concluded a partnership agreement with InfoSlips. InfoSlips is a next-generation interactive employee communication tool enabled through a comprehensive workflowdriven Employee and Manager self-service.
Symplexity provides services to large complex organisations across various sectors. Its growing clientele portfolio includes but is not restricted to the following industries Energy, Construction, Mining, Research and Outsourced Services. Scan the QR code below to discover how Symplexity can simplify your Human Resources and Payroll processes in real time, at the click of a button.
• Multiple interface and third-party integration
Symplexity ticks all the boxes Symplexity software ticks all the boxes of solutions that meet the contemporary needs of a mining company’s employee human resource and payroll management. Specifically, Symplexity Human Resources and Payroll modules cater for the following common needs within mining operations:
• Occupational Health and Safety allows for incident logging and proactive and preventive management
Optimism about prospects On the whole, Symplexity is optimistic about prospects for the growth in demand for reliable Human Resource and Payroll Management solutions from potential clientele in mining, construction, as well as in other sectors. “As organisations are increasing production, they appreciate the importance of reliable and effective human resource and payroll management systems. That is the most credible way in which productivity, and how it impacts the bottom-line, can be gauged,” Nortje concludes.
• Manpower Planning provides the organisation with the ability to plan, execute and monitor its workforce against its budget. The benefit allows for cost containment.
• Time and Attendance of multiple sites with different shift patterns through API integration or allows raw data to be fed directly into the payroll calculation engine.
More to the point, the company’s HR and Payroll specialists are affiliated with the relevant professional bodies which allow each of them to keep abreast of industry standards, changes, and legislative amendments. Furthermore, the company’s other approach involves spending time with clients to understand how their business requirements evolve and how its solution can support this.
• Mining Leave accommodates the various leave types required within the mining industry, with the added benefit of controlling the mine’s leave liability.
• Exit procedure, noting the return of company equipment and security cards.
• Reminder functionality allows the proactive management of contract, passport, work permit and licencing expiries.
• Recruitment allows for the integration of various E-recruitment platforms and community recruiters to access one platform reducing the time and cost of recruitment
Mining Business Africa | July - August 2022 7
Post-installation services
• Compliance and legislative reporting in line with Departments of Mineral Resources and Energy (DME) and Mining Qualifications Authority (MQA), Seta tending to the mines, Social Labour Plan, BBBEE requirements and Skills Development
• Pay cycles provide for various pay cycles applicable within the mining industry.
• Overtime management through workflow approvals allows for managing the process in line with BCEA requirements and industry agreements, ensuring timeous and correct payment
Symplexity software has emerged as one of the highly regarded, integrated and real-time human resources and payroll solution that can be recommended for various industries. Its multiple interfaces and third-party integration, such as time and attendance into the payroll solution, address limitations with ease. “At its core, the Symplexity solution has a payroll calculation engine which allows for the processing of all payroll transactions in real-time, at a click of a button. This allows for a reduction in manual effort and resourcing costs. An additional advantage is greater flexibility and efficiency,” Nortje demonstrates.
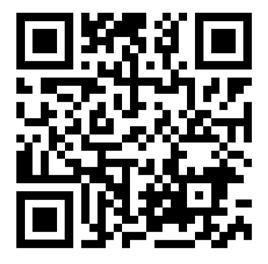
The scale of the impact of absenteeism on the economy may be underestimated. But the reality is that it is far-reaching. Based on present economic conditions, it is an issue worth confronting head-on, rather than wishing away. Presently, the country is facing record youth employment of 67% and unemployment of 34.5% (in the first quarter of 2022, based on StatsIntriguingly,SA). in any discourse on frightening unemployment figures, the focus is biased toward the ‘visible’, the macro-level. However, in the course of this, the critical smaller details – the critical micro-level issues - within organisations may be ignored. Chief of them is productivity, on which employee absenteeism has a considerable impact.
8 Mining Business Africa | July - August 2022 FEATURE
In South Africa, government-aligned labour unions, like-minded bodies and some academics have been pressing for a basic minimum wage, better working conditions and other benefits for employees. Mining companies, as one of the biggest employers, are among businesses that have been pilloried the most for their alleged indifference towards attending to these pressing issues. Arguably, this may hold water. However, on the flip side, what may be overlooked - deliberately or inadvertently - is the burden the implementation of the demands places on employers. Sometimes, a fact that is lost on critics or commentators is that mining houses are first and foremost running businesses, which have to make a return on shareholder investment, and the rest, much as it is presented otherwise, is secondary.Asarule, the provision of improved employee conditions is directly correlated to an increase in productivity. In other words, improved employee conditions and an increase in productivity are mutually inclusive. The significance of this is that productivity affects the bottom line as it impacts upon revenue. For this reason, mining companies have to adopt practices that can help them increase
By reducing absence levels significantly, mining companies can register a rise in productivity, and concurrently profitability. But mining management needs a fundamental attitude shift in their approach to absence management. This is the sage advice from Soma Initiative (Pty) Ltd, providers of Soma iKon™, an absentee management solution.
Absenteeism is not limited to sick leave. Its scope spans all unscheduled leave, including early departures from and late arrivals at work, feigned illness, attending to private affairs during working hours and such “absence”. Thus, from this viewpoint, Lancefield explains that the realm of absentee management covers identifying, monitoring, and significantly, addressing absentee issues within the framework of the law, collective agreements, employment contracts and organisational policy. “Through absentee management, employers are empowered to manage their most vital capital, human capital, and in the process to reduce costs, boost productivity and profitability. Employees too are rewarded as their attendance promises potentially greater financial reward and more importantly, security of job tenure.”
Absence Management for Mining Operations
Citing alarming statistics, Lancefield laments, Members of the South Africa’s mining trade union, AMCU, picketing for better work conditions
Effective employee management
Effective employee absentee management is one of the ways that mining companies can increase productivity. This is the sage advice of Soma Initiative to mining houses in South Africa and the region. This is based on the company’s experience as a provider of a wide range of customised human resources management solutions to diverse industries. Marianne Lancefield, Project Manager for Soma Initiative’s Absentee Management Programme, Soma iKon™, acknowledges that every organisation has a standard way to manage employee absenteeism. However, the level of reliability, and thus effectiveness of the absenteeism management, is questionable. To underscore the importance of employee management in organisations, Lancefield illustrates how the neglected elements at the micro-level (within organisations) can have huge implications at the macro-level (national economy). Based on this, she suggests that there is need for a fundamental shift for mining companies to manage this challenge. At the outset, it is important to define employee absenteeism in this context.
The scope of absenteeism
Effective Absence Management, Increased Profitability (or sustain) productivity. So, what about the employee side of the bargain? One area, easily within the mining houses’ grasp, where new approaches to productivity management can be explored is in managing employee absenteeism, one of the main causes of poor productivity.
Impact of absenteeism
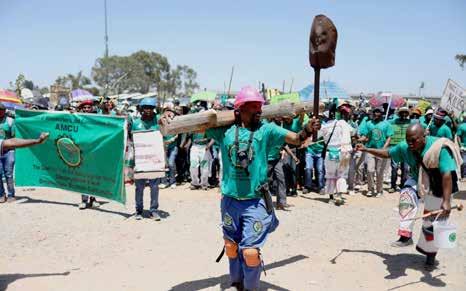
over efficiency
and
Mining Business Africa | July - August 2022 9
profiling
trend and absentee case management •
• Intervention
approach is
Focussed, goal-directed absence management a significant to boost optimal employee
thereof, duration of absence in relation to the diagnosis, patterns of absence, liaison with treating doctors •
consulting
presents
Optimal business performance demands input cost minimization and output benefit maximization. Human capital is an essential input cost that presents unavoidable but manageable threats to company productivity and concomitant financial performance.
of disability claims • Incapacity management • Functional Capacity Evaluation • Work-site
Effective employee management a proactive versus reactive approach to
factual, unbiased, and fair disability assessment reports on the validity or otherwise of disability claims. Employees essentially drive output, and it is them that differentiate one enterprise from another ... Human Capital therefore holds the key to any enterprise’s success or failure ... the so-called “profit lever” ... Managing this “profit lever” effectively is vital to business performance ... 80% of the impact of poor productivity is unseen. Tel: +27 (0) 21 670 6920 Fax: +27 (0) 86 635 4427 Email: info@soma-i.co.za www.soma-i.co.za Such assessments produce objective, accurate, appropriate, and legally robust disability claim recommendations. Assessment is complex and not merely based on medical reporting but comprises a multi-disciplinary assessment process with legal, ethical, and statutory components. Absentee and Sick Leave Management Treating the problem and the cause • Real-time absentee control transforming the cost of absenteeism into significant financial gain • Web- or non-web based, in-house, or outsourced to the Soma Initiative • A cutting-edge ‘Web-based Absentee Management Program’ at low cost • Medical Certificate management - the
• Disability and
Analysis
Productivity
Assessment Protecting the
claims evaluation in controlling costs and
administration • Providing
analyses of processes and methodologies, manual and automated
retirement benefit determination
assessment and management for
demands
Soma Initiative (Pty) Ltd, as market leaders in Absentee, Disability and Productivity Management, advocates that a company’s workforce is the key element of its success and prosperity and that management of the employee is undoubtedly and unequivocally the ultimate value driver.
associated poor
Organisational Productivity
management
Disability underwriting
are determined,
Once these fundamentals appropriate, goal-directed intervention proposed in order to guide future strategic intervention. Pre-empting preventing Health Risk risk
is
• Premium, employee and
Assessment protocol design • Death/disability
As an expert and professional Health Risk Manager with in excess of 25 years’ experience, Soma Initiative is a Level 4 B-BBEE contributor with nationally distributed offices and a large team of professionally qualified staff. The company operates in both the Public and Private sectors being an appointed Health Risk Manager to the South African Government at both National and Provincial level having built its business and national reputation on a simple yet essential principle: top services backed by top knowledge, expertise, and technology.
and
• Operational effectiveness and efficiency consulting analysis relating to human capital designed to ascertain the root causes of compromised employee wellbeing and productivity.
more
Soma Initiative assists self-insured risk This proactive risk determination far beneficial retrospective safeguarding
retirement assets.
than
the identification of individuals requiring intervention.
in the validation or
impairment • Guiding Trustees
is
Soma Initiative manages those human capital-related areas fundamental to company performance: and/or Ill Health Retirement business and the workforce Incapacity both and Benefit the true extent of an employee’s functional limitations associated occupational and Employers repudiation analysis; job evaluation Real-time, web-based independent, validity Proactive Strategic workforce management
organisational performance and productivity, while maintaining
The workforce is everything
Funds • Assisting Trustees/Employers in determining
Disability
•
Employers
undue risk •
funds and schemes in evaluating insurable
and applying appropriate underwriting limitations.
Affecting effectiveness
• Situational
opportunity
health.
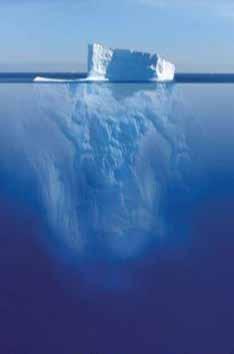
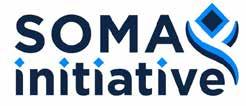
• Automated, real-time reports identifying incidents of culpable and innocent absence
• Medical Certificate management: validation, verification, and capture of medical certificates received by Soma from the client. Medical practitioner liaison for confirmation of accuracy and appropriateness of medical certificate detail, when deemed necessary.
Okun’s Law of Economic Production posits: GDP needs to grow by some 4% in order to reduce unemployment by 1%. Clearly, considering the unemployment rate of 34.5%, there is work cut out . Realistically, there is no ‘quick-fix solution’ to saving jobs, contrary to what trade unions and populist politicians may pontificate. “We can only grow our economy by producing. We can only produce by being at work and working. We need to get the employed ‘working’. Then, perhaps we can produce more jobs for the unemployed,” asserts Lancefield. “Employers can boost their profits by attending to productivity issues. They need to get the workers back to work. They need to manage their absenteeism. If absentee levels are managed, productivity rises and so does profitability. In general, as Soma Initiative, our stance is that if we attend to the absenteeism issue, we can do both: save the jobs we have and create new ones, too.”
10 Mining Business Africa | July - August 2022 “Those fortunate enough to be employed in South Africa cost the nation an estimated R38 billion per annum in direct sick leave costs [Momentum Effective Employee Index, September 2021]. Unscheduled absence in some industries runs at 15% - 15% of the time scheduled to be spent at work, is lost through absence according to Occupational Care South Africa (OCSA). This may be extrapolated into losses of about 36% of annual payroll and 20% of man-days through absenteeism [Mercer: The Total Financial Impact of Employee Absences, OctoberAnother2008].”factor worth pointing out is that against the backdrop of unattended absenteeism is a persistent economic paradox, a dichotomy.
Case study at a mine Soma iKon™ – SOMA’s absence initiative
• Ad hoc telephonic “hotline” consultation facility for backup advice, guidance, and instruction on absence management
• Ad hoc on-site case management or problem consultation provision by specialist Medico-legal Consultants
• Standardized requisite record letters and forms allied to intervention management (return-to-work, leave application, counselling, formal and informal warnings)
Soma iKon™’s scope of critical features that enhance absent management include:
Soma’s offering is flexible and tailored to be client-specific. It has two options – either the client can use Soma iKon™ to manage absence independently or in a consultative alliance with Soma iKon. Generally, the main benefit of Soma iKon™ is that it facilitates focused, goal-directed absence management. For instance, it helps industries manage the common problem of having a technically skilled and knowledgeable employee who lacks requisite people skills and knowledge and human resources management training to manage absenteeism. In this way, it presents a significant opportunity to boost organisation performance and productivity.
Fundamental mindset shift In the end, the rewards of improved absenteeism management are immenseorganisations grow, and they can make further investment in the business in the form of, inter alia, creating further employment, and employee skills development. Evidently, the onus is on organisations to tackle absenteeism – most importantly, there is a need for a fundamental shift at the management level on how best to manage it and the human resources and operations units. Recently the team at Soma Initiative conducted extensive research on the impact of employee absenteeism at a mine in South Africa. The findings indicated that the biggest oversight was the grey area of the responsibilities of both the human resources and operational teams. At the mine, each of these units worked in silos, disparately, inevitably leading to undefined and poorly demarcated areas of responsibility. Unsurprisingly, there was poor management and control of absenteeism; neither team being ultimately responsible for absence management. In addition, there was neither data nor information to enable informed decisions to address the problem. To manage a challenge of this nature, Soma Initiative suggests that mining companies should have access to actionable data and information and should consolidate their approach by creating clearly defined lines of responsibility. Actionable data and information enables timeous management of the workforce as a whole. This particularly applies to mining companies as they comprise 1000s of employees who disseminate in a number of shifts each day into several small operational teams within a number of shafts. And so, rapid, and accurate realtime data and information should be a critical component of daily absence management as is the accessibility of historical data in respect of employees’ behaviour, illnesses, sick leave patterns and trends. In the same vein, the provision of relevant reports and the ability to analyse pertinent data are essential in workforce management. Without such and the willingness of the responsible parties to manage, effective management of absenteeism is doomed. Based on the current challenges that industries face managing employee absenteeism, Soma Initiative (Pty) Ltd has devised a solution. Sophisticated but highly cost-effective, Soma iKon™ is a web-based software application that functions parallel to any time and attendance and/or HR programme and is customised to allow for client-specific data mining and information reporting. There could be a dime a dozen apps that are tailored at helping industries manage employee performance, but what makes Soma iKon™ stand out is that it delivers targeted, employee-specific, management information and instruction.Highlighting standard absentee management programme functionality, Lancefield says, “It is the generation of crucial management information out of raw data by Soma iKon™ which facilitates the effective and efficient, in-house or outsourced, management of inappropriate employee absence.”
On the one hand, on the micro-level, there are profit and productivity pressures, and, on the other hand, on the macro-level, unemployment, and GDP pressures. “We have the unemployed crying out for jobs, and we have the employed not fulfilling their employment contracts,” Lancefield points out. The compelling case for effective absentee management From the abovementioned, given the epic crisis of unemployment, there is a compelling economic case for reducing absenteeism.
• Contravention-specific intervention management instruction
• Automated real-time notification of (imminent) company policy and/or labour legislation contravention by specific employees
• Contracted on-site, Soma-sourced intervention management by shared or dedicated, roving or permanent, specialist Absentee Management Consultants to conduct return-to-work interviews, counselling sessions and to advise and guide on absence management and disciplinary issues where required.
FEATURE
There has been increasing usage of helicopters as a mode of transport in remote mining areas, as well as in carrying out mineral exploration, inspection and material measurement activities. Fleet owners of helicopters who provide services to mining companies are looking forward to participating in lucrative projects in West African countries.
Noticeably, there has been increasing use of helicopters in the past decade, mainly for mining projects in Southern and West Africa. Recently, Mining Business Africa contacted leading services providers of aviation services for information on common purposes that the helicopters serve in mining operations. The companies own and run a fleet of helicopters. Purposes helicopters serve In their responses to the questionnaire the helicopter fleet operators suggest that mining companies need helicopters more or less for the following: • Transport Employees, more especially VIP executives, use helicopters as a convenient means of transport. A helicopter also is regarded as
In terms of business prospects, by and large, helicopter fleet owners are cautiously optimistic. This is given the impact of the war in Ukraine on global economic outlook. There is lingering concern that major economies would be in recession.However, compared with the depression that greeted the declaration of COVID-19 as the pandemic, the atmosphere now can be termed as bullish. Now, there has been a rebound – at least that is the general sentiment in the mining sector. Encouraged by the rise in commodity prices, mining companies have resumed exploration and mining projects that were deferred during lockdowns to cope with the pandemic. This has translated in an uptick in orders for helicopter services from mining companies mainly involved in projects in Southern Africa and West Africa. The companies claim to be mission ready adhering to expected performance and safety standards. This involves personnel involved undergoing training regularly to ensure they are qualified and ready for deployment.
• Emergency medical services by helicopter In case of a health emergency, helicopters are deployed for evacuation. They present the safest and quickest evacuation option in situations urgent intervention is needed. Their use enables a patient to access medical attention within a short time and saves lives.
Helicopters of convenience
Mining Business Africa | July - August 2022 11 FEATURE
the fastest and most cost-effective mode of transport cargo, in most cases, components of parts and equipment would be needed urgently.
• Aerial surveying, aerial observation Helicopters are used in a host of tasks that support exploration projects, such as aerial surveying and aerial observation activities. It can be used for tasks such as volumetric calculations of open pits, topographical surveys, detection of ground deformations, stockpiles and tailings, just to single out a few. A wide variety of instruments, which are permanently mounted on the aircraft, are used to gather a wide range of data. Common instruments used include aerial cameras, light detection and ranging (lidar). Lidar, which uses laser, is an alternative to infrared, radar transmitter, magnetic and gravity sensors ultraviolet and gamma-ray sensors.
Helicopter Services for mining project
Helicopters guarantee the shortest possible reaction and response times in the event of a technical breakdown. In this way, a mine is kept operational as downtime and costly production losses. Additionally, helicopters are used to ferry precious metals and stones from mines to secure locations.
Typically, mining companies are located in remote areas that are difficult to access due to long distances. In developed countries with good road networks, long-distance becomes a challenge when the delivery of cargo or transportation of personnel has to be done within a short time. In Africa, the situation is even worse due to poor or non-existent infrastructure. All the more, on the continent, most mining operations are located in hostile environments with high safety and security risks. Thus, given these circumstances, the use of aviation becomes the most convenient option to support operations.
Cautions Optimism
Helicopters are used in a host of tasks that support mining projects in remote areas
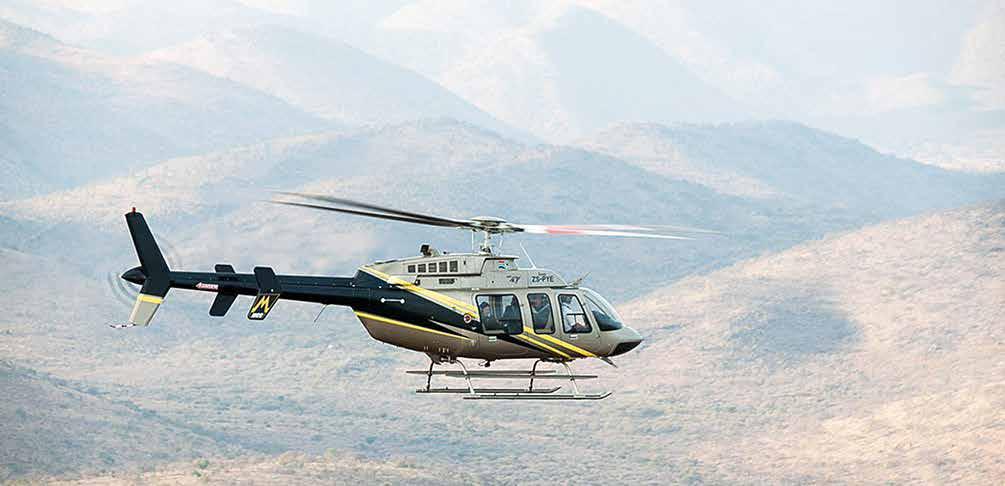
12 Mining Business Africa | July - August 2022
• Thorough consultation Noteworthy, having seen the impact of lighting failure on mining operations, the company undertakes a thorough consultation with the client before embarking on a comprehensive design as standard practice. “To create a customised design for the client, certain parameters have to be established, for instance, indoor or outdoor application, maintenance factors to be used, lux levels required and colour temperature. We also consider whether or not emergency lighting is required,” Grobler expounds.Afterthe parameters have been established, drawings are sent to the design department, in either pdf or dwg format for the design. After the design is completed, a full schedule or BOQ can
• Specialised LEDs and optics for high ambient heat Magnitech has observed that high ambient heat is another destroyer of LED lighting installations. And to manage this challenge, it ensures that specified LEDs, optics, and even wiring, are used.Usually, high ambient temperatures affect the LED PCB by lowering the output and lifetime drastically, or depending on temperature, destroying the PCB completely as the Tj (or junction temperature) of the LED may be exceeded. These units, together with other components such as LED drivers and optics, are only designed to be able to operate up to a maximum temperature as recommended by the supplier. For instance, the higher ambient temperatures can cause the maximum allowable Tc or case temperature on the driver to be exceeded. This decreases the lifetime of the driver. Should the higher ambient temperature be prolonged, the driver can also be destroyed. On Magnitech’s advice on how companies can manage this challenge, Grobler explains: “It is paramount to note that all components within a fixture, for example - optics, can only be subject to certain maximum temperatures as specified by the manufacturer. After that, a threshold is exceeded, and in this case, specialised optics made from materials such as silicon, have to be used.”Magnitech’s hands-on approach Magnitech offers a turnkey solution to its clientele and employs a hands-on approach to ensuring its delivery. The company’s engineering team leaves no stone unturned in guaranteeing that all requirements specified in the order are met – from the lighting design itself through to post installation audits. Although Magnitech is purely a supplier of industrial lighting, the team works closely with all the related parties to ensure a successful and appropriate installation. The critical steps in the process encompass thorough consultation with the client, initial design and product recommendation, manufacturing, delivery, and post-installation audits.
FEATURE Customised LED lighting for mining projects
‘Fit-for-purpose’ Design, Reliable Lighting
Currently, mining companies are eager to earn record-breaking revenue from high global commodity prices. But truth be told, they can realise this only through ensuring that their operations remain safe and productive. Among the tried and tested methods of achieving this is through the use of reliable lighting Procurement based on informed decisions
A situation mining companies should avoid encountering is the failure of lighting, which can result in a huge loss of productivity and an increased exposure of safety risks to workers. That is why procurement of LED lighting solutions should only be based on informed decisions.Thisis what Martin Grobler, Head of Marketing at Magnitech, is telling mining companies. This is based on Magnitech’s 53 years of experience in the provision of lighting solutions for harsh industrial and mining environments within Southern Africa and further afield. Grobler demonstrates how mining companies can forestall common lighting product failure and outlines the hands-on approach the company employs to customise the best possible solution for a respective project.
A suitable fixture that is inherently designed to be ‘fit-forpurpose’ must always be chosen
Forestalling lighting failure From experience, Magnitech has gathered that the most common causes of failures on LED (lighting installations) luminaries are due to spike voltage, heat-related problems and the results of excessive vibration. So, to forestall these costly consequences, the company recommends that a lighting product should tick all the boxes in the following areas: the design, appropriate surge protection and resistance to high ambient temperatures. • ‘Fit-for-purpose’ design Concerning design, first and foremost, a suitable fixture that is inherently designed to be ‘fit-for-purpose’ must always be chosen. “From the outset, the fixture should be designed to withstand the rigours of a harsh mining environment. This includes the overall design of the fixture, the materials used, the construction of the fixture, and the internal components that are chosen. Each element should speak to its intended purposes and environment,” Grobler elaborates.Secondly, the use of appropriate surge protection is paramount. And so, Magnitech ensures that as a quality manufacturer, they take every precaution to ensure that all the internal components of its light fittings, such as LED drivers, are protected against spikes or transient voltages. The company is very particular about the installation of quality replaceable surge protection devices. “The sole purpose of surge protectors, as sacramental components, is to protect, and once it has performed its function and has given the ultimate sacrifice, it must be replaced. The installation itself should also have a suitable surge protection device protecting each line,” Grobler emphasises.
Magnitech’s hands-on approach assures the client of a ‘fit-for-purpose’ LED lighting solution with minimal downtime, and low maintenance requirements. In the long run, with reliable lighting, the momentum of productivity is sustained and the risk of accidents is minimised.
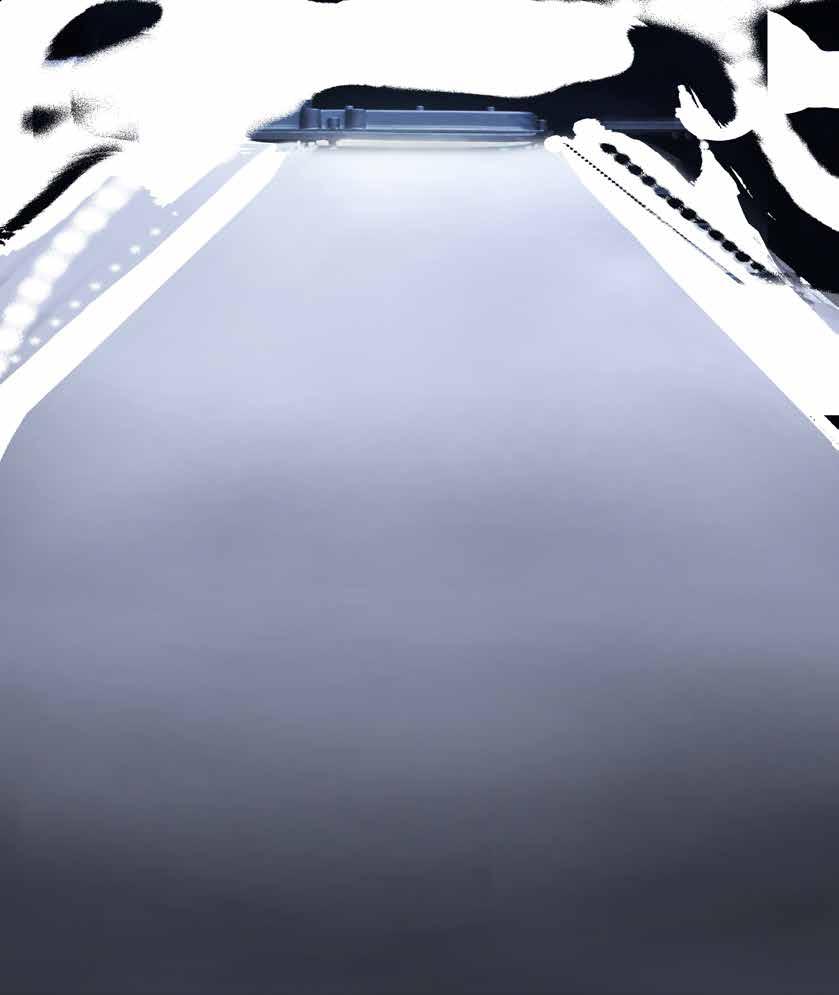
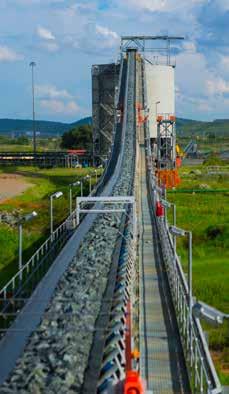
SEPARATE LED COMPARTMENTDRIVER 21 RAEBOR ROAD BENROSE JOHANNESBURG 2094 P.O. BOX 27129 JEPPESTOWN 2043 T: +27 (0)11 618 2720 F: +27 (0)11 614 9603 E: SALES@MAGNITECH.CO.ZAW:MAGNITECH.CO.ZA MAGFLOOD FEATURES & BENEFITS • WORLD LEADING COMPONENTS • UP TO 900W OF POWER • 143 000 LUMENS • L90B10 - 100 000 HOURS • IK08 & IP66 RATED • MARINE GRADE ALUMINIUM BODY • HIGH VIBRATION & CORROSION RESISTANT THE ULTIMATE INDUSTRIAL FLOODLIGHT NEW PRODUCT VARIOUS OPTICS AVAILABLE
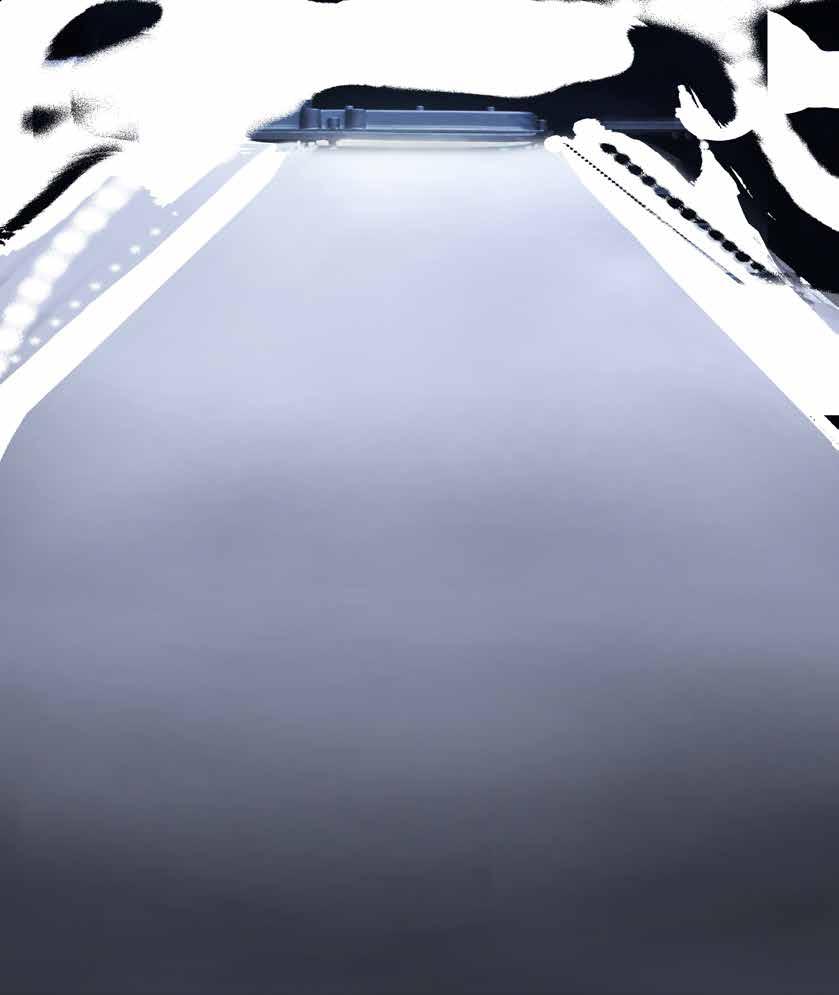
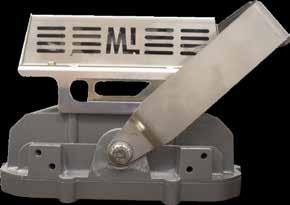
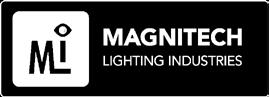

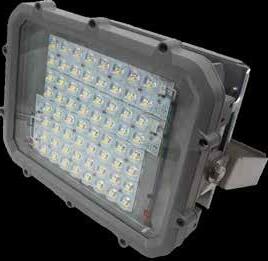

A cardinal rule in the selection of any product that is to be deployed in the mining environment is that its features should be ‘fit-for-purpose’. For mining-specific LED lighting, this is no exception, indicates Grobler. “One should ensure that the fixtures chosen are designed by professionals who truly specialise in the mining environment and understand the complexities and unique challenges of the environment itself.”
• Manufacturing (production) Once a design is approved, the client will place an order, after that, we will produce the fixtures in our ISO9001 and SABS accredited facility, based in Johannesburg, South Africa.
Lapses in product selection result in severe unintended consequences. This is despite the fact that lighting only accounts for between 1 and 2% of the overall Capex expenditure of a mining environment, notes Grobler. “Choosing the incorrect lighting fixtures, or choosing on price alone, can have severe unintended consequences such as increased maintenance costs, downtime for the mine, decreased visibility, (and) Health and Safety Issues and personal liability claims against the responsible person.”
• Delivery and installation Magnitech then delivers the fixtures and lighting solution in line with the client’s delivery schedule, to be installed by the client or their installation contractor.
• Post-installation audits Magnitech then offers post-installation audits to ensure that the (expected) designed light levels are delivered, and that the installation meets not only the clients’ rigorous requirements but its own too.
Informed selection, minimal downtime By and large, to ensure minimal downtime as a result of poor product selection, Magnitech recommends that the client chooses a “fit for purpose” LED light fitting and not just the cheapest that is available. Grobler emphasises that it is important that mines fully comprehend what ‘fit for purpose’ means: “When we refer to ‘fit for purpose’ in the industrial and mining context, we mean the light fittings themselves and all components are carefully designed to ensure suitability for use in this application.
Does the driver have sufficient built-in surge protection? Does it have advanced features such as CLO (or), constant light output? Can the light fitting withstand vibration, and to what degree?
Ultimately, many other features need to be taken into consideration to create a truly ‘fit-forpurpose’ fixture.” Magnitech assures mining companies, as they are embarking on Greenfield and brownfield projects, that it is well-resourced to provide customised LED lighting solutions.
LED lighting at a diamond mine
FEATURE
14 Mining Business Africa | July - August 2022
What constitutes mining-specific LED lighting?
Delivering an LED lighting solution to a power plant Magnitech has been delivering LED lighting solutions to customers’ satisfaction for over 53 years for use in different mining environments. Recognising its extensive experience, a client approached the company for advice on a lighting solution for a power plant in an extremely eco-sensitive area. The design was for a number of barges out in the middle of a lake where gas is being harvested as well as the onboard gas processing plant, including buildings such as scrubbing plants. In particular, this type of installation required the use of specialised Zone 2 Exn nonsparking lighting fixtures, especially on the barges.The MAGLED MINI was chosen for this application. To ensure minimal impact on the environment from a lighting perspective, specialised environmentally-aware 2200K LED PCBs were utilised, so as to minimise the effect on the wildlife and insect populations surrounding the site. The use of the MAGLED MINI was continued throughout the process plant in both standard and Zone rated versions. All emergency lighting was through a backup generator and the light fittings had to be easily identifiable. be presented to the client. The majority of light level requirements that Magnitech follows are specified in SANS 101142020. These are recommended requirements that the lighting designer is required to base their lighting designs on.
• Initial design Typically, a successful installation starts with the initial design, where the company’s experienced team of lighting professionals will work with the client and consultant to understand the needs of the mine itself. A lighting design will be incorporated into the design of the installation. In the process, a multitude of factors are taken into account. These include required lux levels, type of installation, an understanding of the potential dirt and dust build-up over time, and potential harmful gasses and dust in the air as a result of the mining process. In addition, even the topographical and environmental conditions may contribute to additional challenges that must be taken into account.
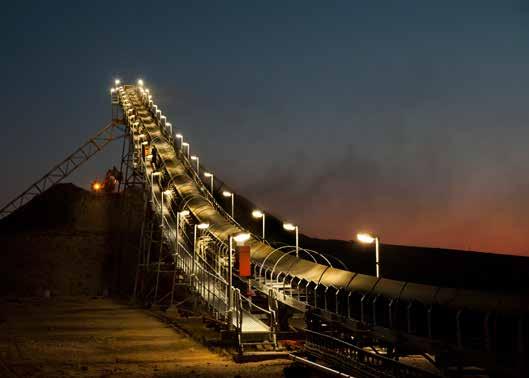
The Council for Geoscience’s review (Derelict and Ownerless Project) indicates that this call is not tantamount to making a mountain out of a molehill. The organisation’s recently released report estimates that there are at least 6,000 derelict and ownerless in South Africa.
“Illegal mining is prevalent where there has been a failure to take adequate measures to close a mine. Illegal miners will go to great lengths to circumvent efforts to prevent access to unused mines, “notes the body. Intervention urgent Make no mistake - abandoned mines are proverbial ticking time bombs that has to be defused pre-emptively before it causes untold damage, as recent community protests have revealed. There is a need for the Departments of Mineral Resources and Energy, in conjunction with the Department of Environmental Affairs (DEA), to intervene.
By Nick Barnes
Conveniently, politicians have been capitalising on its link to undocumented migrants to resonate with the sentiments of the disillusioned electorate.Truthbe told, though, political expedience or not, it is rational to get to the bottom of the matter to establish a lasting solution.
Regulation governing rehabilitation
Many of South Africa’s 6,000 historic abandoned mines and dump sites predate the current legislation governing mine rehabilitation and closure. Consequently, they remain unrehabilitated and will always be a magnet for illegal miners. Markedly, unless legislation is amended to accommodate this reality, illegal mining will remain a persistent challenge.
One of the areas that seem to be overlooked in the raging debate on how illegal mining activities Mine rehabilitation and closure
South TickingAfrica’sTimeBombs
Mining Business Africa | July - August 2022 15 FEATURE
An illegal miner coming out of an abandoned mine Illegal miners digging for a fortune
Conspicuously, rehabilitation and closure of abandoned mines and dumps, where illegal mining activities take place, fall out of the scope of The Mineral and Petroleum Resources Development Act, 2002 (“MPRDA”). This is the primary legislation that governs the mining industry and its activities post-2004. Intriguingly, until 2008 before the amendments, under Section 43 of the MPRDA, the holder of a prospecting right, mining right, retention permit or mining permit was responsible for any environmental liability, pollution or ecological degradation and its management until a closure certificate was issued by the Minister. However, following the 2008 MPRDA amendments, the mining company will remain liable for any latent environmental hazards, even if a closure certificate is issued. Nevertheless, the challenge is that most of the abandoned mines predate the legislation (were operational way before the current legislation came into effect). Then, this removes the task of thoroughly applying rehabilitation from previous owners if they still exist. In other instances, a company that owned the mine may have been liquidated before complying with the statutory obligations for closure.
There have been sporadic protests in communities affected by criminal activities allegedly attributed to illegal mining activities in Gauteng Province, South Africa. The affected communities are faulting undocumented migrants who are involved in illegal mining. Nonetheless, for a while, illegal mining has been a persistent problem meriting urgent attention that has been either overlooked or underestimated or both. It is only now that political parties that are aiming to get into power through the 2024 national elections that illegal mining has been thrust into the limelight.
can be eliminated is the regulation governing mine rehabilitation and closure. And this is where the primary focus should be.
Unrehabilitated mines, persistent risks Due to this situation, mines remain unrehabilitated, exposing communities to health hazards and damage to their property, over and above providing a fertile ground for illegal mining activities to thrive. In a recent report, Human Rights Watch attributes the failure to effect rehabilitation as a major cause of illegal mining.

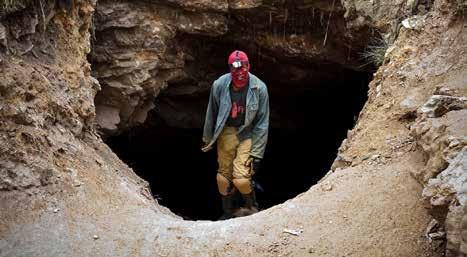
The company resolves complex disputes on construction and engineering projects for clients in different industries. “We can assist the disputing parties to resolve the conflict Arbitration, Litigation and Dispute Resolution Expert Services for African Mining Projects
If left unattended or ineffectively addressed, disputes between different parties can result in failure to meet project expectations, with costly implications, as well as jeopardising future business relationships.
Conventional formal dispute proceedings may work in some cases, but even where they do it is at a colossal cost to the parties involved. Typically, conventional formal dispute proceedings are both very formal, expensive and in most cases lengthy. “The complex procedural formalities allow for little flexibility between the parties and outcomes are outside the control of the parties, being in the hands of the Arbitrator or Judge,” Donovan elaborates. Adopting alternative or independent expert-lead mediations
Exercising prudence in engaging consultants In an economy, where organisations are emerging in every sector claiming to be experts in some fields, Wing tells potential clients in the mining sector to exercise prudence when engaging consulting firms to provide alternative dispute resolution services.“Our advice would be to choose not just a reputable company, such as EVRA, but ensure the Expert chosen is both successfully experienced in formal and alternative dispute matters and an Expert in the matter the dispute relates to.“ Recommending mining companies to EVRA, he highlights: “We take great pride in our track record and reputation. We have several experts who have successfully resolved complex matters for clients, adjudicators and arbitrators by providing impartial, independent, honest and transparent opinions.” EVRA’s panel of Mediators are experienced construction professionals accredited by professional bodies such as the Royal Institution of Chartered Surveyors (RICS) as Commercial and Civil Mediators.
FEATURE
Considering the shortcomings of conventional dispute resolution channels, it is rational to explore Alternative or Independent Expert lead mediations. There are numerous benefits to be had from using conventional methods, which can be summarised into two. Firstly, alternative or Independent Expert lead mediations allow the parties, where possible, to settle disputes in a cost and time-effective way. Additionally, the ADR process has the advantage of putting the parties more in control of the process and final outcomes. “In our experience, as parties can be fully involved in the terms of any settlement, both parties tend to be more satisfied by outcomes within this process,” Donovan highlights the win-win benefit of independent expert-lead mediations. Disputes resolution about reaching a compromise However, both the aggrieved parties should be willing to reach a compromise. For this reason, there has to be a genuine desire by both parties to reach an amicable solution. Notwithstanding that viewpoint, there are situations where that is not possible, EVRA Consulting seeks an alternative, Donovan assures. “When faced with matters where parties are distant from a middle ground our approach would be to break the dispute up into smaller key issues and resolve these individually. This process by its very nature tends to bring parties closer together.”
16 Mining Business Africa | July - August 2022
through the use of specialised communication and negotiating techniques,” Donovan Wing, Operations Director of EVRA Consulting, states, pointing out common problems encountered with conventional dispute resolution and the business case for seeking independent, expertled mediations. Common problems with conventional channels
Where ever there are different parties involved in the planning and implementation of projects, disputes are unavoidable. The main challenge, though, is how to resolve them in the event they arise.
More projects, more disputes Notwithstanding the effects of the Ukraine War, which has occasioned high energy prices, mining companies are bullish about prospects. Electing to look on the brighter side, taking a long-term view, undeterred, they are unveiling projects. In this atmosphere, naturally, there are likely to be more disputes between parties involved in projects. Based on its experience in resolving complex cases for clients globally, EVRA Consulting advises clients to consider utilising alternative dispute resolution services should disputes arise. EVRA Consulting can provide ADR and independent Expert services for quantum, delay and contract management disputes under the most common forms of Contract i.e. FIDIC, NEC3/4 and bespoke Contracts.
There is a colossal cost of utilising conventional channels to settle disputes that may arise between parties involved in projects, both in terms of financial resources and time. Thus, it is always rational to utilise alternative dispute resolution channels that save time and resources, and most importantly, ensure that a healthy business relationship is maintained. Disputes always arise in projects, the question is: How do parties involved address them amicably?
Expert-lead Mediations, Equitable Dispute Resolution Outcomes
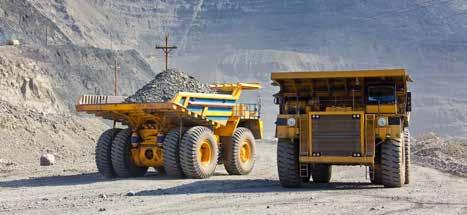
EVRA CONSULTINGHeadOffice Block A, 322 Rivonia Boulevard, Rivonia, Gauteng,
EVRA is Africa’s leading construction consultancy providing Project Controls, 5D BIM, Claims Advisory, Alternative Dispute Resolution and Expert Services across multiple sectors throughout the continent. We further specialize in provide Agile Project Management Services to the financial, insurance, pharmaceutical, information technology and telecoms sectors.
Africa’s consultancy.constructionleading
EVRA Consulting’s vision is to provide quality services, to long term clients, that lead to their desired outcomes. We are an equal opportunities employer that provides a professional environment that is challenging, rewarding and respectful of ideas and individuals. South Africa, +27 11 234
8410 | E: sales@evraconsulting.com | W: IndependentPlanningwww.evraconsulting.comMediationClaimsDraftingBaselineProgrammesandSchedulingDisruptionAnalysisExpertServicesClaimsManagementProgressUpdatingClaimsDefenceProgrammeRepairNegotiationsandSettlementExpertDeterminationClaimsAvoidanceTenderPlanningProjectControlsExtensionoftimeAnalysis EXPERT WITNESS SERVICES IN SUPPORT OF ADJUDICATIONS AND ARBITRATIONS ALTERNATIVE DISPUTE RESOLUTION FORENSIC DELAY ANALYSIS CLAIMS AGILEBIMPROJECTADVISORYCONTROLSAND5DPLANNINGPROJECTMANAGEMENT SERVICES
What differentiates EVRA is our consultants, all of whom have in-depth practical expertise combined with world-class skills. This enables us to deploy the consultants best suited to our client’s requirements. EVRA supports and adds value to our client’s projects from tender stage through to project completion, be this at the natural end of a project or in the unfortunate event of dispute resolution proceedings. Our clients include government agencies, major construction contractors, specialist subcontractors, banks, insurers, telecoms, information technology and law firms.
2128 T:
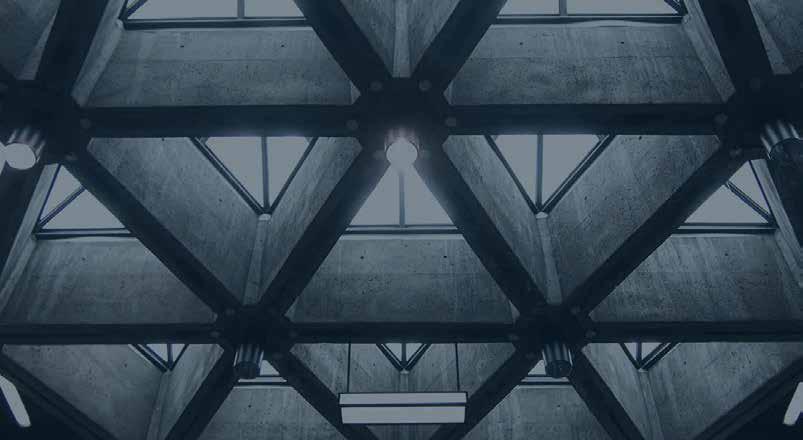
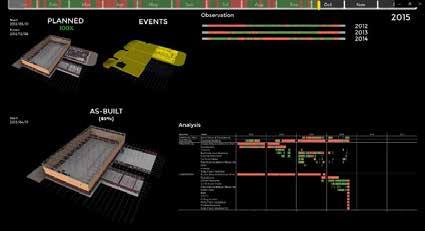
Drones for Surveying, Security & Inspection in Mining Projects
• Security surveillance patrols and asset protection,
FEATURE
Specifically, he highlights three vital areas: the host of fields where drones can add value; legislation governing ownership; steps to make an informed choice in obtaining and maintaining a drone RPAS Operating Certificate (ROC). Fields where Drones can add value
• Thermal inspections on equipment and infrastructure. Unsurprisingly, with so many benefits, the drone has become a tool of choice in any competitive mining operation.
• Geomagnetic surveying for mineral/ resource deposits
• Progress reports and digital twins,
RPAS Consulting is committed to using the extensive know-how it has honed to help organisations in the mining and related sectors navigate through the maze of requirements needed to own and maintain drones for various applications. The company’s speciality is the provision of bespoke drone solutions to clients in diverse fields in South Africa and the region.
• Airborne Light Detection and Ranging (LIDAR) scans,
Thanks to breakthroughs in research and development, the scope of fields where drones can be deployed is broadening. Noticeably, some of the areas where it has had a groundbreaking impact include but are not exclusive to surveying, security and inspection in mining, oil, gas and power generation projects.
While there is an increasing appreciation for the relevance of drones in contemporary industry, understandably, some organisations are put off by the intensity of the paperwork involved. Concerned that organisations could miss out, RPAS Consulting pronounces that it is dedicated to helping mining companies thoroughly understand the complexity of requirements needed to obtain and maintain its own RPAS Operating Certificate (ROC), and to weigh it sensibly against other potentially more cost effective operational and business model options.Operational since 2015, RPAS Consulting, the South African-based outfit, has accumulated tons of experience in the provision of bespoke drone solutions to multiple clientele in South Africa and the region. Bertus Greef, the company’s Managing Director, says that his organisation is keen to impart invaluable knowledge to prospective drone owners.
• Tailing dams’ health,
• Blasting reports and fragmentation analysis,
• Engineering inspections at height,
• Safer surveying practices with denser datasets mean quicker and more accurate data
18 Mining Business Africa | July - August 2022 Drones for Surveying, Security & Inspection in Mining Projects
Legislation Greeff tells potential drone owners in the mining sector to be thoroughly acquainted with legislation that defines terms of ownership and maintenance in South Africa. “Just like in any country in the world, Drones – also known as Remotely Piloted Aircraft Systems (RPAS), Disputes always arise in projects, the question is: How do parties involved address them amicably? Security surveillance
There are a host of areas where drones can add value to mining operations. Some of the most common ones are:
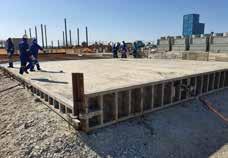

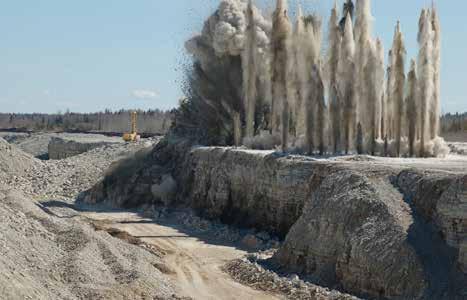
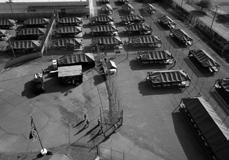
Turnkey Services vs Own Operations In the end, the decision to implement drones as part of any mine’s workflow is not an “if”, but rather a “how and when” decision, Greeff asserts. “At some point, a purchase has to be made. The big question is just how to go about it in a way that makes the most financial and operational sense.“ Greef stresses that it is important for an organisation to make an informed decision on a drone ownership package suitable for its requirements. “If you are a smaller operation, with only two or three pilots, obtaining your ROC could prove an intensive and time-consuming exercise. For specialist applications such as geomagnetical surveys or LIDAR modelling, outsourcing to a key specialist could still be your best option. For general day-to-day surveying and security type applications, it could be rewarding to talk to us about an alternative costeffective solution working with our ROC.“
legally compliant. RPAS
including: • Surveying •
We
their lives
surveillance • Bathometric Surveys • Geo-Magnetic surveys • Aerial LIDAR Scanning • Engineering Inspections at height • Thermal Analysis & Reporting such as Solar Plant panel Bertus Greeff | 082 455 7526 | bertus@rpas.co.za | www.rpas.co.za Services and Solutions RPAS
Part 101
The South African Police Services (SAPS), in conjunction with the Commercial Unmanned Aircraft Association of South Africa (CUAASA), has recently implemented a specific set of CAS Crime Codes to facilitate the criminal prosecution of transgressors of SACAA Part 101, which has serious implications for any manager in case of non-compliance.
in-house service capabilities such as LIDAR, surveying processing capabilities, thermographic reporting, and specialised security services, among others.
business
provide clients with several turnkey solutions to
Unmanned Aerial Vehicles (UAV), or Unmanned Aircraft Systems (UAS), are governed by strict aviation legislation in South Africa. However, this should not be looked at as an unnecessary bureaucratic burden. It is very necessary, since drones share airspace with manned aviation, and could very well result in loss of life if not conducted responsibly.“
companies
Mining Business Africa | July - August 2022 19
South African Civil Aviation Authority (SACAA) CAR Part 101 defines the legalities of operating drones in South Africa. Specifically, for any commercial operation, several certifications need to be in place, the most important being an RPAS Operating Certificate (ROC). A ROC is an active certification, not just a once-off exercise. It requires various post holders such as accountable manager, person responsible for flight operations, person responsible for aircraft, aviation safety manager, quality manager, safety and security manager and RPAS maintenance technician/s. The ROC systems get audited by the SACAA regularly, and the license needs to be renewed every 12 months. The cost of compliance can add up and could very well result in being grounded if all the systems are not properly maintained.
has the following specific SACAA permissions in place: • Multirotor and fixed-wing ratings • Beyond Visual Line of Sight (BVLOS • Night flying • Controlled airspace • Prohibited airspace • Restricted airspace • Up to 1 000 ft AGL • Operating closer than 10 km to airports • Operating over roads, infrastructure, and people • Operating in Inclement weather conditions
Are you planning on implementing a Drone program, but struggle to justify the cost of obtaining and maintaining an ROC? We can assist you to conduct your own legal flight operations with substantial savings. also deliver turnkey services Security Consulting was one of the first to comply with SACAA and obtain a ROC. In since 2015, the company can make easier and be Consulting has Its robust ROC
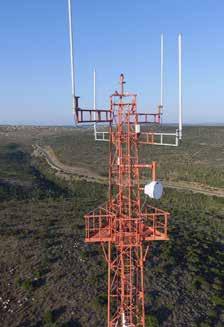
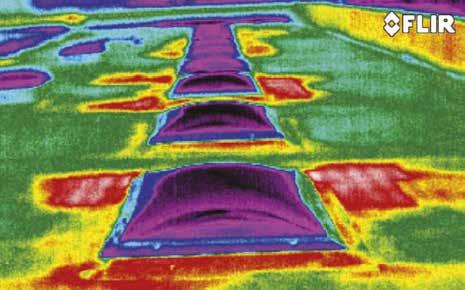
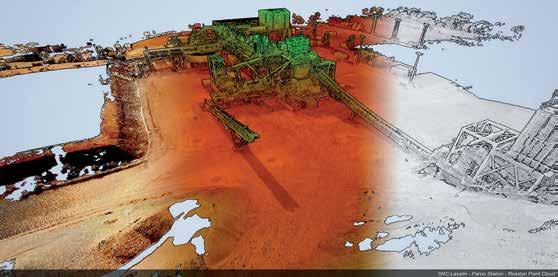

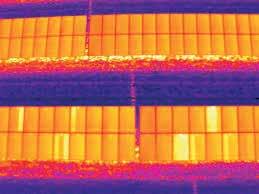
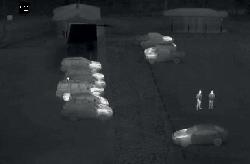
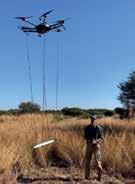
UKP sources parts from the OEMs and wellrecognised factories only and has an in-house Quality Control (QC) centre, and thus promises supply of very high-quality parts. Wide range and large inventory UK P has a wide range of spare parts. From engine to transmission, brake, final drive, chassis, hydraulics, undercarriage, GET and then to accessories and allied parts. UKP has a very strong hold on thousands of top-quality parts. The company also carries a large inventory for immediate supply and assures prompt and efficient services.
Filling the gap
20 Mining Business Africa | July - August 2022
UKP specialises in supply of spare parts for Cat, Komatsu, Hitachi, Liebherr, O & K- Terex & Volvo equipment, Cummins & Perkins engines and Volvo, Scania & MAN trucks. The company is keen to serve large fleet owners with a consistent and cost-effective supply of spare parts. and consolidation from different factories. “The buyer is confident that he is purchasing the right quality of parts at factory prices. The trust for the right part at the right price is cemented,” management assures.
Spare Parts for
The top management of UKP has combined experience of over 150 years in the spare parts industry and has gathered considerable experience and expertise to supply parts which are reliable to the users. Under their guidance, UKP has the pride of having 0% complaint on quality and delivery – this is a commendable feat considering the challenge that comes with meeting the exact demands of clients. Small wonder, UKP has earned the goodwill to be the trusted supplier to many mining giants and large fleet owners across the world.
in African Mining ‘Consistency
FEATURE GLOBAL SUPPLIER OF TOP-QUALITY SPARE PARTS FOR EARTHMOVING, CONSTRUCTION, MINING EQUIPMENT AND GEN SETS T +44
OEM
Viren Mundra of United Kingdom Parts
Combined 150 years of management experience
Strong relations with manufacturers UKP has built strong relations with spare parts-producing OEM factories and can get the original parts of equipment straight from manufacturers. In this way, the benefit of 12 months manufacturer’s warranty is also passed on to the users. To industrial conglomerates, mining giants, construction companies and large fleet owners, UKP offers the most unique service of arranging parts to these users and direct from spare parts factories. “We enjoy strong links with factories and bring the end-users to these factories from where they purchase parts directly at factory prices and thus avoid the hefty margin kept by OEMs and their distributors,” management tells fleet managers in African mining. Additionally, UKP can arrange one-to-one virtual or personal meetings between users and factories and help in the negotiation of price and MOQ. This is over and above, arranging logistics 1753 708788 M +44 77542 33777 E sales@uk-parts.comLTD www.uk-parts.com and Quality Large Fleet Managers of Supply and Enormous Cost Savings’
Considerable cost savings UKP is eager to replicate the success of meeting the specific needs of many large fleet owners who purchase OEM parts directly to potential clientele in Africa. The company guarantees that African fleet owners can reap enormous savings in reduction of operational costs and purchase of parts. This is given that UKP is commercially benefitted by a percentage paid by the buyer on purchase and the business is transparent. “Buyers save substantially” is an assurance by UKP. Currently, skyrocketing oil prices, due to geopolitical events (mainly the Ukraine War), has resulted in record inflation, which has not spared the OEM spare parts. For large fleet operators in African mining, UKP offers the convenience of consistent supply and predictability of cost, bringing in considerable cost savings. For more detail on how fleet managers in African mining can bring down costs in purchase drastically, they can contact: Viren Mundra, Navin Walia or Bilal Raja @ +44 7754233777 & +44 7859886390 or +44 1753 708788 & 708789 and email to: sales@uk-parts. com
UNITED KINGDOM PARTS
United Kingdom Parts Limited (UKP) has observed that during Covid-19 period one of the areas that was most impacted is the supply of spare parts for earth-moving and mining machines. The company informs large fleet owners in African mining about its commitment to meeting the gap for reliable supply of spares.


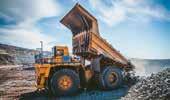
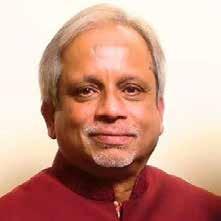
Empirical studies gathered globally indicate increasing awareness among mining companies about the need to revise their approach to truck load measurement. This trend should not be surprising. Truckload measurement is being embraced as one of the numerous channels through which they can achieve efficiencies and reap considerable cost savings
Measurement of material volume in truck trays has been an error-prone and costly process. Handily, the use of 3D laser has revolutionised the task, bringing about efficiency and significant cost savings.
However,simultaneously.thetraditional approaches to weight measurement may have been deemed fit for purpose in the past. However, it is emerging that they could fall short of meeting current expectations. And so, this is necessitating the adoption of alternative techniques of truck load measurement.Thevalidcase for embracing alternative techniques becomes more appreciated when the limitations of traditional truck load measurement are examined. Common challenges with traditional weighing Numerous challenges are encountered when using traditional truck load measurement techniques like a static weighing scale. Based on information from common cases, these include but may not be limited to:
• Variance in the density of material determined by the source of the ore on the rockface and the way the bucket is loaded.
Using the case study of a large mining truck (CAT 797B), the team of researchers involved determined that by overloading a truck by a “mere“ 10 per cent, fuel consumption and costs could escalate by about US$400,000 annually as well as adding add 900mt CO2 emissions per truck.
• The need for costly constant maintenance and calibration
• Bulk density changes cannot be accurately tracked
Groundbreaking discoveries are being made in product research and development (R&D) and enjoying increasing usage in payload management, replacing traditional methods. This has presented widening options for mining companies to use in their payload management. And one of the techniques that have been earning plaudits is 3D volumetric laser measurement.3Dvolumetric laser scanning of bulk material is answering the call for the need for a technology that can help maximise productivity by optimising every load, translating into improved profit. It is a technique that measures all loads and automatically generates 3D scan images.Volumetric Scanning systems use 3D imaging software to measure bulk materials that have been loaded into trucks and rail wagons. While a vehicle passes slowly beneath the scan head, the system can automatically scan the load, record the results, and send them directly to an operator. In 3D laser high precision volumetric bulk material measurement systems, the truck bed is placed underneath the sensor(s) underneath a sensor. The truck is measured in empty condition and when filled. As the truck passes slowly beneath the scan head, the load is scanned, results recorded and sent to the operator. In the end, the benefit of 3D volumetric scanning is that ensures reliable accuracy and performance. Furthermore, there is virtually no impact on moisture content or uneven loads.
• Off-centre loading is a common problem. The worst part is that it causes component wear necessitating replacement costs. Naturally, bearing in mind the inadequacies of traditional weighing, mine operators are pinning their hopes on innovations. Nonetheless, contrary to expectations, the innovations are sometimes erroneously punted as the cure-alls do not eliminate the challenges. For instance, this has been observed with onboard weighing, which cannot be deployed as a complete solution, given their unique shortcomings, mainly:
3D volumetric laser measurement
• Other weighing techniques do not account for the carry back of material being shifted. Shift tallies are not deducted.
• There is no guarantee of getting the actual weight-to-volume ratios of material.
• Cases of heavy trucks moving a dynamic weighing systems scale’s foundation are not uncommon. In most cases, they cause inaccurate measurements. Accordingly, to a review from Payload Management, a subsidiary of Loadtech, this could be in the region of 3 to 5 per cent or even higher.
FEATURE
• The requirement of large trucks to spend time on static weighbridges is timeconsuming. This could lead to the loss of 1 to 2 loads per shift per truck. Simply put, higher cost per tonne hauled.
Mining Business Africa | July - August 2022 21
• Besides the need for constant calibration and maintenance, what makes on-board truck scales all the more expensive (is that every truck requires its own system. This becomes more expensive when a mine has a large fleet of haul trucks.
Three-Dimensional Laser Measurement System for Truck Load Volumes Effective increasedmeasurement,productivity
• An Australian technical paper determined that overloading massively increases fuel costs and CO2 emissions. Titled, Haul truck fuel consumption and CO2 emission under various engine load conditions.
• Moisture composition can make the load materials heavier than they are, consequently its weight.
Volumetric Scanning systems use 3D imaging software to measure bulk materials that have been loaded into trucks and rail wagons (Image credit: LASE)
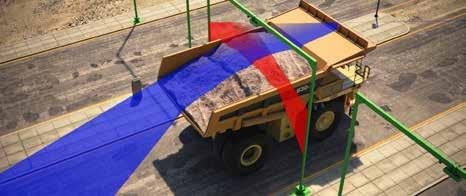
22 Mining Business Africa | July - August 2022
LASE customers use laser-based measurement systems to improve the quality of their products and services as well as to enhance process productivity. Quality and safety is the primary goal of LASE activities! - https://lase-solutions. Forcom/further information on the LaseTVM systems and other mining applications in Africa please get in touch with our South African partner Dwyka Mining Service.
FEATURE
assistance, laser scanners, distance meters and different components for container port industry, mining industry, steel industry and logistic industry.
• Rethabile Letlaladwykamining.africa.rethabilel@ Dwyka Mining Services is an agile mining technology integration partner focused on assisting their clients to adopt and adapt to technological change. Dwyka Mining Services equip their clients with the best global technologies and responsive teams to support proactive decision making in increasingly complex and cost intensive arenas. Dwyka Mining Services source, develop and deploy miningready solutions to deliver end-to-end solutions to extract data from extreme underground environments - https:// dwykamining.africa/ LASE is committed finding suitable solutions to addressing the common problem of measuring the volume of material in haul trucks. And the LaseTVM-3D-M has proved to be just what the mining industry needs.
The truck volume measurement system - LaseTVM-3D-M is a highly accurate 3D laser measurement system for automatic and dynamic volume measurement of trucks of all kind. LaseTVM-3D-M measures the truck load while the truck is driving. The laser scanners are mounted on a frame, gantry or existing infrastructure above the truck lane. Trucks are measured empty and full. The delta between both measurements equals the exact loading volume. Furthermore, the system is able to detect carry back (hold-up detection), material overload, material underload, center of gravity and load spread on the truck bed. The retrofittable application enables instant measurement without conversion factors and eliminates weight and volume manipulation due to moisture and the system speeds
• Jamie van Schoor - jamievs@ dwykamining.africa
LaseTVM’s solves Truck Volume Measurement challenge up processes. LaseTVM-3D-M is available in combination with an RFID reader, a HD camera for documentation and an OCR camera for license plate recognition. All data is captured with just one application. Within a company network for example all measured data like volume, pictures, 3D images, measurement ID’s can be accessed via the “LASE WebGUI” system. For controlling and monitoring purposes current and historic data can be accessed via mobile end device or any PC via the LASE WebPortal”. The system has high versatility and is used for volume measurement of various materials such as stones, sand, ore or wood products. For more than 30 years LASE is developing, producing, and developing laser measurement systems for automation solutions and operator
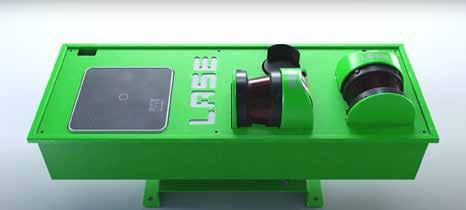

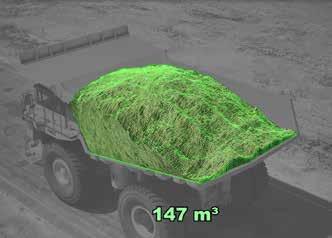
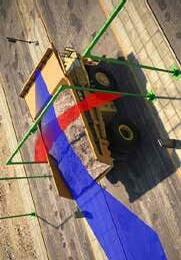
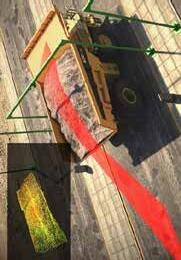
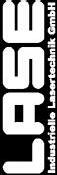

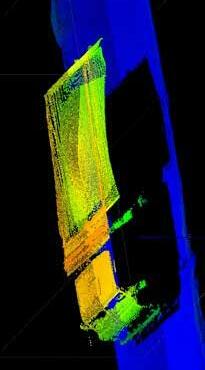
• Increased uptime and processing (improved plant availability);
The use of reliable lining is the tried and tested approach to increasing the availability of semi-autogenous grinding (SAG) mills. For this reason, informed decisions have to be made in the selection of lining material. The importance of suitable lining material is better comprehended when the role of the SAG mill is considered in the entire milling circuit. Why availability of SAG mills SAG mills are a vital cog in the grinding process. Usually, with a larger diameter than length, SAG mills are deployed specifically in a secondary process to reduce large feed size ore (where an industry-standard falls within the range ~300mm down to ~3mm). In contrast, ball mills, which are smaller in diameter than length, are used in primary, secondary or tertiary grinding applications to reduce material from ~20mm to very fine product sizes measured in microns. So, given their specialised role, SAG mills must be available at all times. Any downtime can result in a loss of productivity, which translates into an irretrievable loss of revenue. But, inevitably, due to the materials they handle, SAGs are subjected to severe abrasion and Liners for semi-autogenous grinding (SAG) mills
DynaMax™ Product range. Indisputably, there are very few companies in the world who can lay claim to that. He mentions that when it comes to Mill Liners, the technology has changed very rapidly with respect to Design, Manufacturing and Condition monitoring. Tega is at the forefront of this technological shift: it has been extremely successful in developing, designing, manufacturing, and Installing the Mill liners in big diameter SAG Mills & Ball Mills. This is an incredible achievement since most of these Mills are very aggressive and hard applications. Tega DynaPrime™ Tega’s mark of excellence in wear lining engineering is the Tega DynaPrime™. Tega DynaPrime™ has been engineered to reduce the number of pieces being installed inside the mill, substantially reducing the installation downtime for maximum mill operation uptime. Tega Dynaprime™ Liners are now installed in a twelve-metre Diameter Mill which would probably be one of the biggest SAG mills in the world. Gautam underlines that the most notable aspect of the project is safety. “Tega DynaPrime puts safety above all and has taken measures to render the reline site safe. The option of Bolting from outside and lesser weight of the lining considerably reduces any risk during the installation of the liner.”
Partnerships in Practice Vishal Gautam says the development of mill liners comes from a deep-rooted philosophy of Tega which is “Partnerships in Practice”. “Tega develops partnerships with customers daily with their Quality Product, Service and Turnaround time.”Gautam believes this is a very interesting time for Tega, and regards the growth the company has experienced in the past few years as “something like a dream”. “We look forward to further growth. We are very aggressive in the market. We are looking at a very interesting trend in the market with respect to commodity prices since it’s opening new doors for us.” He concludes: “We walk the Talk. Please watch this space.” Tega’s Mill liners
Key selection considerations When selecting a mill lining system, several
impact, which results in wear and tear of the mill shell.Conveniently, wear lining systems are the first line of defence of the mill shell, offering protection against abrasion and impact. During a product launch in 2021, FLSmidth regional product line and key account management director, Terence Osborn, highlighted the importance of liners reliable liners.“Grinding accounts for about 30% of the operational cost of a concentrator plant. Energy, liners and grinding media are some of several elements that constitute this substantial cost. Furthermore, the milling circuit consumes about 50% of a concentrator’s power demand,“ he said. In the other words, poor selection of liners is bound to fail, exposing the mill shell to wear and tear causingEvidently,downtime.oneof the opportunities to improve the efficiency of milling and grinding is available in the form of reliable lining. There is a need for products that offer a host of tangible benefits. Consequently, the process of selecting lining material has to be thorough.
Selection of suitable linings for semi-autogenous grinding (SAG) mills guarantees the following benefits: considerable reduction in mill downtime; increased uptime and processing (improved plant availability); increased cost savings; and reduced maintenance costs.
•specifically: A considerable reduction in mill downtime;
• The mill liner must be constructed from high wear-resistant materials. As materials technology and design technology have advanced, today many superior alternatives exist to metal linings that have widened options;
Tega Industries Limited is a name synonymous with pioneering achievement in the mineral beneficiation, mining and bulk solids handling industries the world over. Tega currently has six Manufacturing Units in the World and supplies products to more than 90 Countries. It is a dominant player in the World Market of Mill Liners. In Africa, the mother company’s subsidiary, Tega Industries Africa Pty, Ltd, which is based in Brakpan, is under Mr Vishal Gautam who is Tega’s Business Unit Head. Gautam is responsible for Tega’s business Growth in the Continent.Ontheemphasis of Tega Industries Africa’s offering, Gautam explains: “At Tega, we are selling solutions instead of products. We have resolved some very complex engineering problems related to Mills and Mill Liners and that has given us a lot confidence.”
• Reduced maintenance costs
Tega has been manufacturing Mill Liners for more than 40 Years. Today, Tega has a reference base of more than 600 Mills in the world and in Southern Africa alone we have more than 100 Mills Lined with Tega Mill Liners
• Faster, easy and safe installation.
Reliable Liners, Increased Availability
FEATURE
Host of benefits Ultimately, there are a host of guaranteed benefits from the selection of suitable linings,
• Increased cost savings;
• Specific material should have the following characteristics: high hardness, elongation, tensile and tear strength; and
key considerations must be taken into account, mainly:
• Specific information on the needed grinding action, mill size, ore and grinding media characteristics etc;
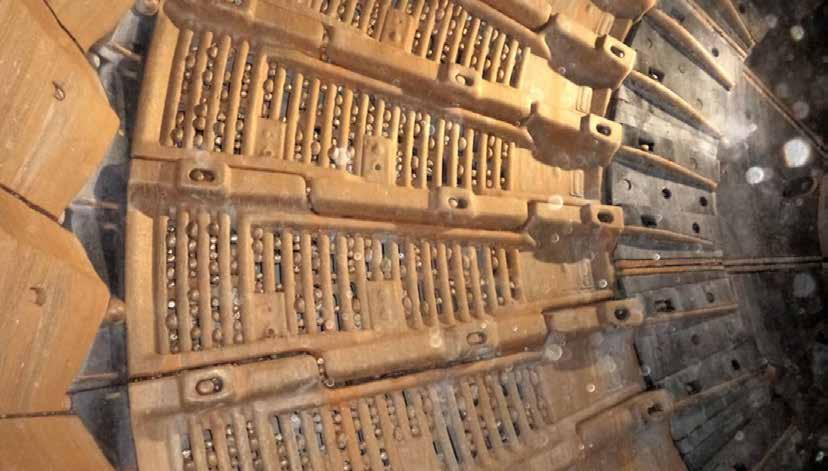
info@tegaindustries.co.za | www.tegaindustries.co.za An ideal liner for high-aspect SAG mills from 34 to 40ft in diameter maximizes availabilitymill unlocks capacitymillResilient design cushions high-energy impacts and liner cracks Unique design ensures better control on lifting angle throughout liner life
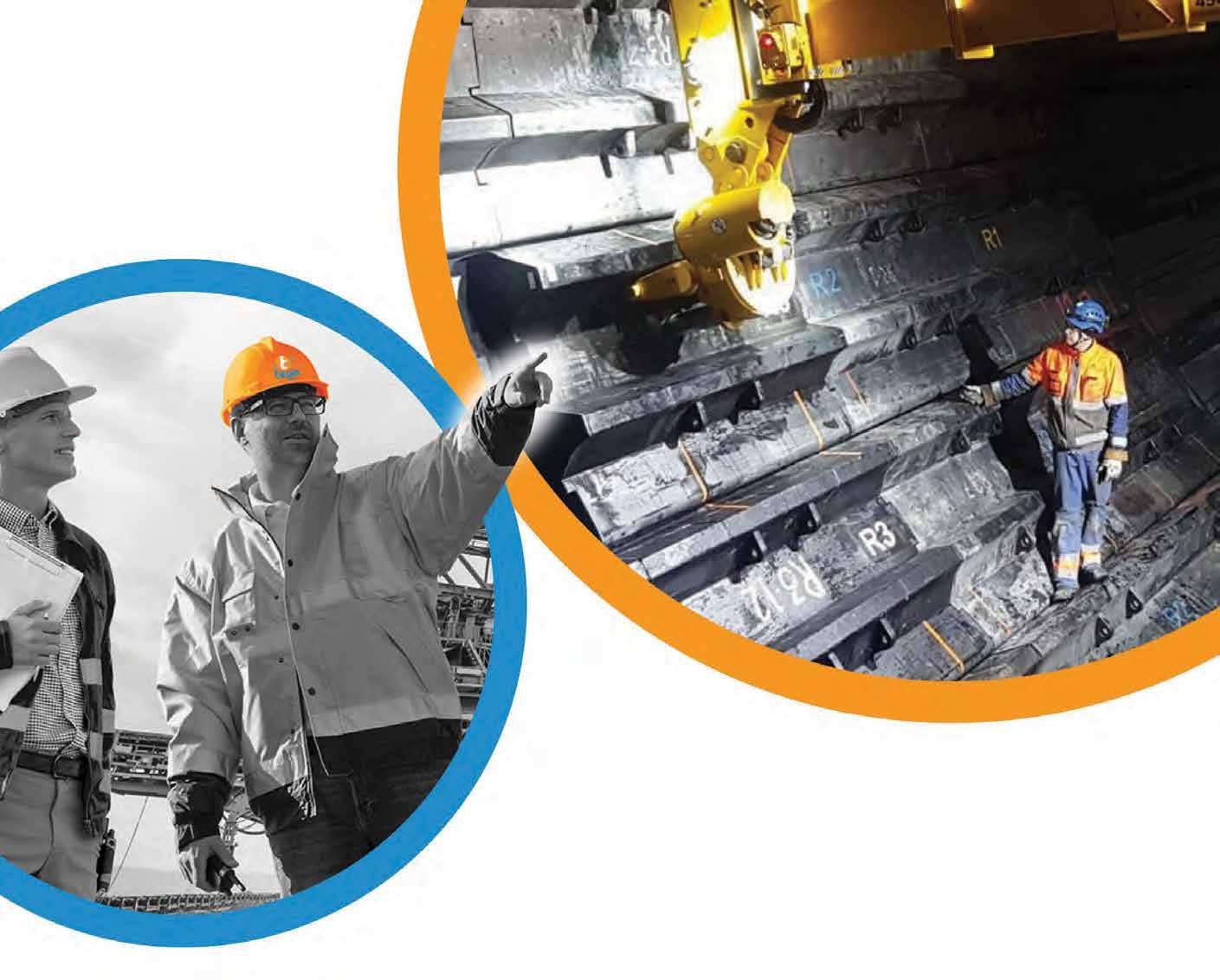
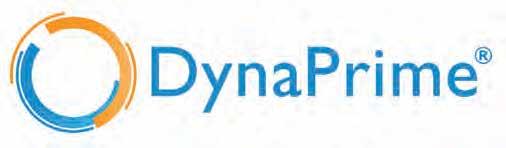

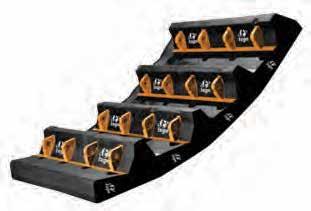

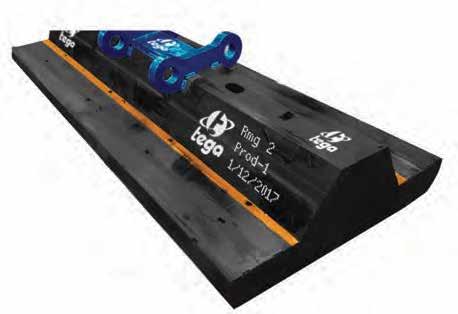
On the other hand, increasing air levels when incomplete combustion is detected can also backfire. This is especially when complex interactions of oxygen and unburned fuel can lead to flammable mixtures igniting further down from the burners.
allow for closer monitoring with greater accuracy and reliability. In the article’s context, he explores how Zirconium Oxide technologies and Tunable Diode Laser (TDL) analysers can be used in monitoring oxygen and fuel mix to reach Stoichiometric combustion levels. The need for accurate and reliable technologies
SERVOTOUGH Fluegas Exact 2700 measures O2 and COe in flue gases, improving combustion efficiency and reducing emissions.
Organisations in mining, power generation, oil and gas, and petrochemical industries have to ensure that their fired heaters achieve efficient combustion. The sure-fire approach that engineers and plant operators employ is getting the appropriate balance in the oxygen–to–fuel ratio, known as Stoichiometric combustion. The cardinal rule is: You can only control what you know. And with respect to fired heaters, the use of gas analysis technologies (gas analysers) has proved effective. At the outset, it has to be acknowledged that cherrypicking suitable gas analysis technologies, with dozens of product brands out there in the market, is akin to searching for a needle in a haystack. Handily, there are huge volumes of literature that process plant engineers can refer to for guidance when choosing technologies relevant to their respective needs. Rhys Jenkins, the Product Manager at Servomex, has compiled a detailed analysis on how to use proven technologies to optimise the process of combustion in fired heaters. His review - A comparison of gas analysis technologies available for efficient and safe combustion in control fired heaters - is rich with relevant information. In a nutshell, he posits that technologies do not provide a ‘one-size-fits-all’ solution, a complete replacement of the available ones, but rather a complementary technique to
• Reduction of excess air to low air, increasing the excess air There can be downsides at both extremes –reducing excess air and increasing air.
• Negative process control conditions
In the pursuit of reducing excess air, unintended consequences could be encountered. Low air could create unsafe operating conditions. This is particularly when products of combustion contain unburned fuel which is wasted and passed into the atmosphere. The review elaborates this point: “Incomplete combustion at less than 10-15% excess air or 2-3% oxygen in the flue gas –pockets of carbon monoxide, hydrogen and methane – result in localised hotspots, as they ignite and produce higher emissions of gases such as methane.”
Given the abovementioned challenge, a point where a balance can be reached should be sought. Notwithstanding the abovementioned risks, there are significant benefits to be had from operating fired heaters at Low Excess Air (LEA) levels. Usually, at that point, the lowest level of fuel is consumed and the products of combustion are cooled the least by the unused excess air. Significant cost savings and environmental emissions requirements At the LEA level, the cumulative gains in fuel cost savings in tens of thousands of dollars from several combustion processes are significant.
Besides, the air-to-fuel ratio, there are negative control conditions that could impact combustion. Mainly, these include: excess heat at the process tubes, which causes damage and leaks; carbon deposits on the process tubes, which decreases efficiency and heat transfer; and, in extreme cases, potentially dangerous combustion events can occur.
The complementary use of Zirconia (zirconium oxide cell technologies) and Tunable Diode Laser (TDL) analysers in some sites can enable fired heaters to achieve efficiency, enhance safety and reduce emissions.
At the outset, by first examining the challenges that incomplete combustion poses to fired heaters it is much easier to comprehend the necessity for adopting proven technologies. Typically, fired heaters notoriously consume large quantities of fuel, produce large quantities of Nox emissions, and pose a potential safety hazard to employees and the plant (potentially dangerous explosion - low-oxygen, fuel-rich conditions). Understanding the delicate process of combustion control Thus, to manage these challenges, an understanding of the basic aspects of the complex and delicate process of combustion control is needed for the correct selection and effective use of the monitoring technologies. Mainly, these are the reduction of excess air and negative process control conditions.
Process analysers for effective combustion in fired-heaters
26 Mining Business Africa | July - August 2022 FEATURE
Striking a balance
Complementary usage of analysers for optimal combustion
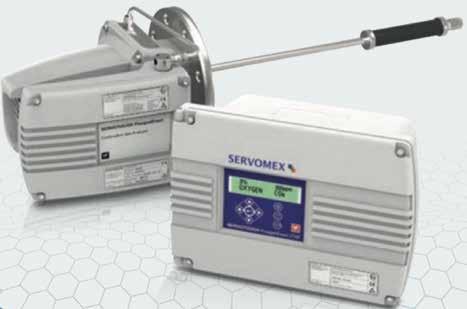
Areas where TDL technologies have the edge • Monitoring carbon monoxide Respected for fast response and specificity, TDL enables carbon monoxide breakthrough to be monitored accurately. Due to this, it can act as a secondary and complementary measurement to the oxygen measurement. In this way, it can enable LEA optimisation as well as introduce a further level of process safety-related diagnostics.
The general advantage of TDL technologies is that they are highly attractive in both maintenance and performance.
Technologies to monitor unused oxygen When exploring suitable means to monitor the level of unused oxygen in fired heaters, one thing to bear in mind is no technology one-sizeall. This is not the least Zirconium oxide cell technologies and Tunable Diode Laser (TDL) analysers. Each of them has distinct merits and demerits. Hence, they can be used as complementary techniques, where applicable. They are available as portable gas analysers and some highly specialist fixed gas analyser applications.
• Purchase and installation costs A TDL does not come cheap. Its purchase and installation costs are between three to five times of a typical zirconia installation. While multiple zirconia analysers can be purchased for an equivalent amount that can be deployed for both an average measurement and the single-point measurements for burner diagnostics.
• Maintenance and performance
• Monitoring carbon monoxide and moisture levels Further, a single TDL monitor for methane optimised measurement can monitor carbon monoxide and moisture levels.
• Operational and maintenance ADL requires the fitting of optical windows between the source and the process, detector and process. Depending on process gas velocity, this makes operation and maintenance prohibitively expensive when compared with zirconia techniques.
• Flameout protection
TDL can provide the catalytic measurement of carbon monoxide combined within the same analyzer as the zirconia oxygen measurement.
Complementary techniques in some sites All in all, for optimal analysis of a fired heater‘s process control to achieve efficiency, enhance safety and reduce emissions Zirconia and TDL technologies can be used on some sites. Some among them are particularly in the following scenarios:
This can result in enhanced, cost-effective diagnostic capabilities for burner efficiency.
• Levels of carbon monoxide and water For oxygen, levels of carbon monoxide and water within the radiant section can be effectively measured by TDL in conjunction with a zirconia analyser.
• Susceptibility to environmental factors TDL is susceptible to environmental factors. These include but may not be isolated to path length variation, window purge gas effects, optical interferences and temperature and pressure changes.
SERVOTOUGH Laser 3 Plus Combustion
Generally, Zirconia analyzers are split into two types: close–coupled extractive analyzers and in–situ analysers. Commonly used in process control are the close-coupled extractive analysers.Aspectroscopic
• Enhanced, cost-effective for burner efficiency
• Reading errors For a WMS instrument, an error of approximately +/– 5% of reading is normal, while for a DAS measurement, the error can be considerably higher.
• For flameout protection and diagnostics For flameout protection and diagnostics, and added combustibles breakthrough analysis, an additional combined CO/methane TDL can be used.
Mining Business Africa | July - August 2022 27 Additionally, controlling air levels just above incomplete combustion enables the production of the cleanest burn, helping plants to meet environmental emissions requirements. In this context, a competent LEA combustion process runs at approximately 2.5-5% excess air or 0.51% oxygen above the point at which unburned fuel in the form of carbon monoxide starts to break through. This can be maintained and controlled at the most efficient running point.
• Zirconia Zirconia measures oxygen on a ‘wet’ basis and has two applications that are worth highlighting. Firstly, the technology enables the sampling and direct analysis of the hot, wet and often corrosive products of combustion. Secondly, as inherent partial pressure measurement, it allows the percentage oxygen measurement to be made independent of temperature and pressure.
• Measurement TDL’s main disadvantage is that, for oxygen analysis, it offers an average path measurement across all burners. On the other hand, as they can sample a single point, zirconia analysers measure a particular section of burners.
absorption measurement technique, TDL consists of a tunable diode laser light source, transmitting optics, an optically accessible absorbing medium, receiving optics and a detector. They are ideal for in–situ cross stack measurements, as there is no physical or mechanical interaction with the process, besides molecularTypically,absorption.across-stack system consists of the laser emitter module and receiver mounted across the process pipeline or flue stack. TDL counts molecules (or number density of molecules) that fall within the beam. Comparison between TDL and Zirconia
In fire heater processes, TDL can be integrated into flameout protection. This is particularly the measurement of methane in natural gas burners. Installing TDL can help in the quick detection of a burner flameout. In this way, it can enable greater flexibility and response to controlling and shutting down processes.
• Safety For LEA operation, the installation of a combustibles sensor combined with the zirconia analyser is a very cost-effective choice to support process safety procedures and site safety regulations.
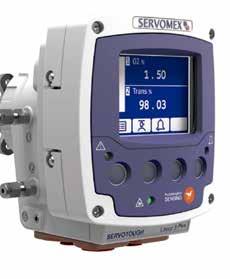
Email: info@e-analytics.co.za Website: www.e-analytics.co.za YEARSYEARS ANNIVERSARY ANNIVERSARY YEARS FEATURE Elemental Analytics
28 Mining Business Africa | July - August 2022 TAKE CONTROL OF YOUR COMBUSTION PROCESS
and
conditions,
The SERVOTOUGH FluegasExact 2700 Operating hazardous challenging the FluegasExact 2700 delivers high-performance analysis of oxygen and combustibles, a cleaner process with lower emissions. 11 918 6994
Oxygen and combustible analysis in one device Extractive design ensures long life of sensors Developed for demanding process environments Flow sensor enables preventative maintenance Learn more at: servomex.com/2700 Tel: +27
Combustion is essential to many industrial processes. Usually taking place in a fired heater, it is often the only way to create the extremely high temperatures required.
The combustion reaction mixes fuel with oxygen (from air), delivering heat energy for use within the process. Typically, this requires a significant amount of fuel, creates potential safety hazards, and generates harmful emissions.Excess fuel can create unsafe conditions that could lead to an explosion, while excess oxygen (O2) will combine with nitrogen and sulfur present in the fuel to produce unwanted emissions, for example oxides of nitrogen (NOx) and sulfur (SOx). The most efficient combustion reaction, therefore, depends on optimizing the ratio between the air and fuel. This requires highly accurate gas analysis of O2 and combustibles (COe).The SERVOTOUGH FluegasExact 2700 gas analyzer is designed by Servomex to long-established as a solution for O2 monitoring in combustion, and delivers reliable, accurate results with a fast response to changing conditions. The addition of a combustibles sensor provides an all-in-one combustion control solution.Additionally, Flowcube technology enables positive flow conditions to be validated, supporting preventative maintenance and lowflow alarms, and the analyzer is hazard rated for ATEX Cat. 3, IECEx Zone 2 & North America Class 1, Division 2. Controlling combustion produces many benefits for plants looking to meet environmental standards requirements. Fuel consumption is reduced, and safety improved. It also results in fewer emissions, a reduction in NOx, SOx and carbon monoxide, and a decrease in the greenhouse gas carbon dioxide. This makes the FluegasExact 2700 an integral part of many clean air strategies.
A combined gas analysis solution for cleaner and more efficient combustion measure O2 and COe in flue gases, improving combustion efficiency and reducing emissions. Developed to operate in some of the hottest and most extreme process environments, it meets the most demanding needs of combustion efficiency applications in the power generation and process industries. Armed with an integral sampling system, it is ideal for use in extremely hot environments, operating in high-temperature processes up to 1750°C (3182°F). This resilience makes it the combustion analyzer of choice for a wide range of processes, including use in process heaters, utility boilers, thermal crackers, incinerators, and furnaces.TheFluegasExact 2700 uses proven Zirconia technology for O2 sensing and a sulfur-resistant combustibles sensor, all in one compact platform. Its close-coupled extractive measurement principle ensures a long sensor life by keeping these sensors outside the harsh process conditions, in a heated enclosure. Zirconia sensing technology has been
in the most
for
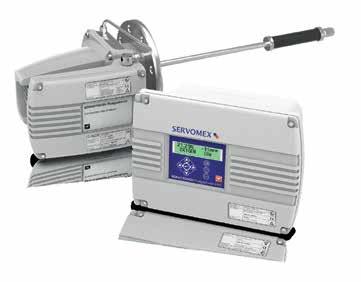
Gas analysis & emissions monitoring Quality assurance of continuous emissions monitoring systems
Mining Business Africa | July - August 2022 29
environmental monitoring and consulting certified USEPA, European EN and UK MCerts equipment sales service and maintenance contracts data management and reporting equipment rentals indoor air quality Telephone: + 27(0)11 444 7809 www.sianalytics.co.za info@sianalytics.co.za
From an EU perspective which Africa tends to follow, EN14181 has now been in operation for the last 10 years and has had far-reaching consequences for regulators, equipment manufactures, test houses and, most importantly, process operators. The standard describes the quality assurance procedures needed to ensure that the Continuous Emission Monitoring System (CEMS) installed to measure emissions to air is capable of meeting the uncertainty requirements on measured values given by legislation.
FEATURE
MEANS BETTER AIR FOR FUTURE GENERATIONS
Leo de Veer, SI Analytics head of client service, points out that challenges arise when handling equipment that requires the use of internal optics, for example. The monitoring equipment can be very sensitive to high dust loads or wet stacks, which as a result, will not perform to the required quality assurance levels. Several technologies can perform similar measurements, for example, extractive vs in-situ vs cross-stack. Once again, de Veer stresses that the most suitable should be selected based on site specific conditions. Engaging an experienced solutions provider At an early stage, given the complexity of the task, it is important for site operators to engage with stack monitoring companies with the necessary experience to assess, recommend and ultimately install, commission and maintain the most suitable stack monitoring equipment.
Choosing the right equipment for stack emission monitoring is a complex process due to various site specific conditions. Decisions that site operators make in-house could prove costly should incorrect equipment be chosen. Engaging an experienced consultant can help site operators in making informed choices when it comes to the early stage of equipment selection. The integrity of data gathered from stack emission monitoring instruments is always subject to intense scrutiny as it not only informs critical internal decision making but regulatory compliance status as well. How does one then get comfort that the instrument reading is accurate and representative of what actually is being emitted?
There are three different Quality Assurance Levels (QAL 1, QAL 2, and QAL 3) : QAL 1 relates to the equipment that must meet certain performance requirements evaluated at testing houses under the Monitoring Certification Scheme (MCERTS). QAL 2 specifies procedures to ensure that the CEMS has been correctly installed, calibrated and verified. QAL 3 requires the plant operator to regularly measure the drift and precison of the CEMS. According to Mark Rowand (Director of SI Analytics), the most challenging aspect when it comes to CEMS selection is that every industrial site is different which requires certain site-specific knowledge as temperature, pressure, humidity and altitude all play important roles. Unfortunately, there is no one size fits all solution and a small omission can have a significant impact on the CEMS readings.
SI Analytics has been a focused environmental monitoring company specialising in stack and ambient emission monitoring throughout subSahara Africa since 2005.
As the world strives to create a cleaner, greener future, there’s a push to find energy sources that do not involve fossil fuels. This cannot happen overnight. SI Analytics believes in an incremental, practical approach to limit emissions through world class monitoring of all relevant sources. By providing our customers with air monitoring instrumentation, SI Analytics is providing them with the tools to join the environmental revolution.
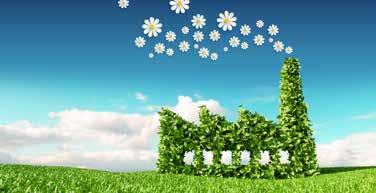

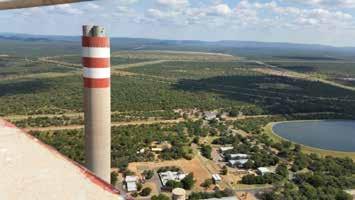
Rack Series: Identical to the HC Range above except for the redesigned modular layout, specifically to simplify transportation to & installation at remote locations. High Voltage Series: For deployment in high-performance demand environments. Developed for integration with ATESS® HPS inverters & subsequently officially approved by them. iESS: Intelligent Energy Storage Systems. Its flagship products are each designed individually to meet exact requirements. Components typically consist of battery storage, inverter(s), local and remote monitoring, air conditioning, fire suppression and access control components which is built into 6m or 12m shipping containers. Noteworthy, BlueNova is currently in the final stages of production of the largest iESS system that it has supplied to date, with a rated continuous power output of 1.2MW and battery capacity of 1.3MWh. This is due to be delivered & installed in Australia. Own BMS (battery management system) which is integrated into all four of the above product ranges. Compact Power Stations: Wallmounted systems that each include battery storage, inverter, output and distribution components. Preconfigured for UPS applications & designed for easy installation in residential and small commercial environments as solutions to loadBMACshedding.(Battery Monitor and Control): This is a multi-purpose electronic module that can be installed for one or more of the following purposes:
BlueNova’s competitive edge
The battery storage arena has seen the entry of several players jostling to get a piece of the market pie, targetting the growing niche of renewables. BlueNova acknowledges that this is good for the end-user. However, it recognises that companies with a competitive edge will excel. The company has always believed that, to remain competitive in the energy sector, it has to differentiate itself by means of continued innovation. This approach to doing business has led to the development and successful rollout over the years of the following: High Current Product Range: Stainless steel enclosed and built with A-grade LiFePO4 cells with a characteristic maximum fade of 20% over a 10-year minimum service life. 10-year warranty included.Battery
• To facilitate serial (CAN) communication between its products and inverters, as well as other peripheral devices by ensuring that sent and received CAN data strings are translated correctly. The firmware of BMAC modules can be updated remotely by design. This is in instances where battery/inverter communication compatibility is suddenly lost because of an inverter firmware update.
• To enable in-depth remote monitoring functionality of battery performance and health variables from any internet-connected location worldwide (requires internetconnected Wi-Fi on site). Remote access to this data not only provides many clients with peace of mind regarding their investments but also enables the company to provide technical support of exceptional Autoquality.ModeChange: A patented algorithm has been developed primarily to ensure that batteries will be charged to maximum capacity automatically in preparation for scheduled load shedding events and/or forecasted bad weather (backup mode). Then, it reverts automatically to standard operation (cycle mode) under favourable conditions to maximise investment returns.Fascinatingly, BlueNova’s Research and Development (R&D) team is currently working on an algorithm for the BMAC that would monitor the load shedding schedule as well as weather forecasts. This will ensure that sufficient battery capacity is always available to our clients under less-than-ideal circumstances.
30 Mining Business Africa | July - August 2022 FEATURE
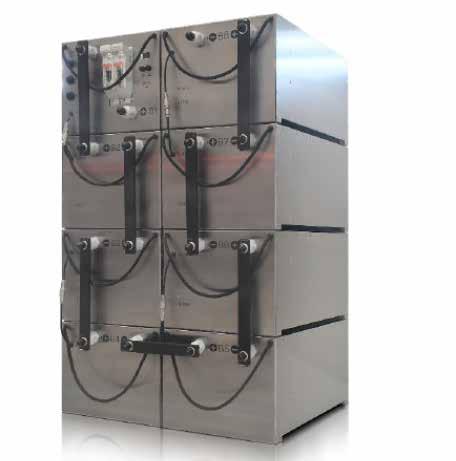
27-28 September 2022 Kampala Serena Hotel, Uganda THE SEVENTH E D IT I O N www.uiogs.com Strategic Partners Held under the auspices of the Ministry of Energy and Mineral Development Uganda 40+ SPEAKERSEXPERT 32 STAKEHOLDERSSENIOR 125 COMPANIES To discuss exclusive early bird o ers, please contact: Faheem Chowdhury Event fchowdhury@energyadvance.orgDirector+971 58 969 5448 Driving the final steps in andcommercialisationproduction Welcoming over 400 attendees from across 125 national and international companies, the 7th Uganda International Oil and Gas Summit (UIOGS 2022) is returning for September 2022, as the o cial platform for oil and gas business in Uganda and the must-attend meeting for all stakeholders in East Africa
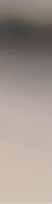
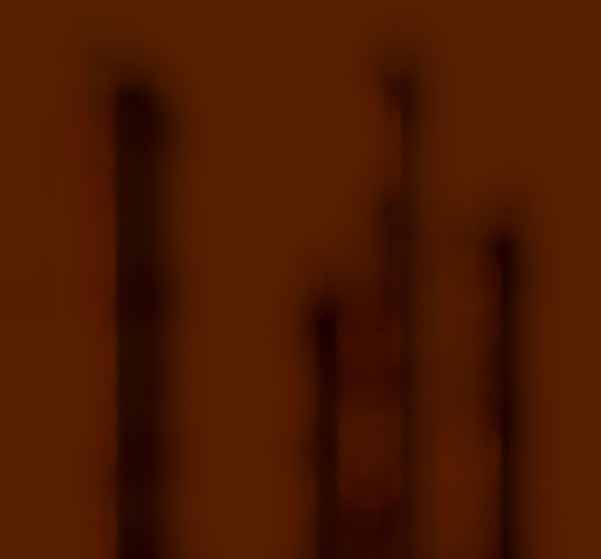
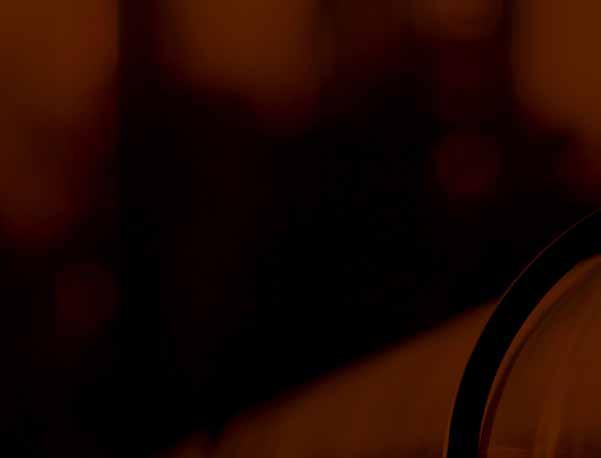
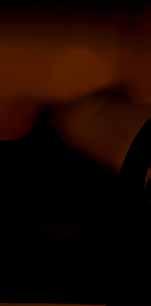

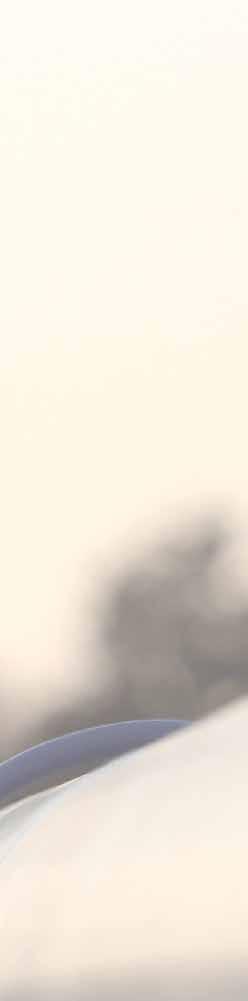

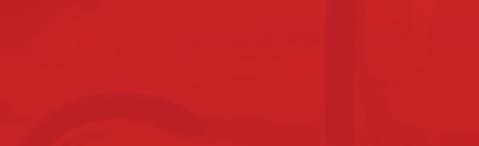
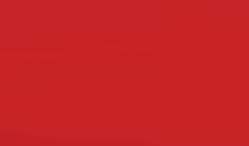

A principal aim of Ctrack is, from the moment the ignition is switched on, to provide as much information as possible on all operational parameters, with the aim of helping to improve efficiencies and reduce fleet operational costs. In Conclusion, Ctrack has industry solutions to track a variety of assets including cars, trucks, trailers, containers, generators, dump trucks, front-end loaders, graders, bulldozers, water bowsers, light- and heavy duty vehicles, which is why Ctrack is a one stop shop for all your mining, yellow metal and asset management needs.
Compliance & Asset Management
Driving Behaviour (Cost Management) Improving the driver behaviour of employees can benefit operations through better kilometres per litre, lower fuel bills, enhanced driver safety
Maximum efficiency and productivity for any mining asset and reduced accident rates as well as less fleet administration and vehicle maintenance costs Ctrack offers a range of solutions to support business with driver performance and management across multiple driver groups and vehicles. These solutions include driver behaviour monitors and indicators that detects vehicle operational parameters, while driver fatigue is managed with the help of front, rear and in-cab Integrationcameras.withfurther peripherals such as breathalysers prevents access to vehicles from intoxicated drivers, and safety requirements such as the failure to wear seatbelts can also be reported. Drivers can also be identified through various mechanisms such as, the Dallas iButton, RF ID Cards, and even virtual driver pins. Driving behaviour monitoring then ensures that the correct person is behind the wheel and that the vehicle is being driven in a satisfactory manner with parameters that keep an eye on factors such as speed, harsh braking, irregular stops, load capacity and many more.
Operations Control
The Live Productivity Dashboard, which forms part of the online software suite, provides a 24-hour timeline of vehicle or asset movement, allowing for quick and easy dissemination and management of vehicles and assets. Users can view the movement of vehicles stationary times, speed (harsh braking, cornering, acceleration), payload, as well as driving times in a single graphical view. Stopping locations and operating times allow managers to identify unauthorised usage of vehicles quickly. With the Live Productivity dashboard management is able to ensure time management, and productivity of assets, ensuring cost reduction through productive fuel usage, overtime management, fraud detection & prevention.
As vehicles age, it becomes difficult to have a holistic view of their individual condition. With Ctrack it is possible to receive daily health checks and odometer/hour metre readings. From here it becomes much easier to schedule vehicle maintenance, keep up with vehicle license renewals and perform accident analysis.
32 Mining Business Africa | July - August 2022 FEATURE Ctrack, South Africa’s leading fleet management and asset monitoring solutions provider, is continuously innovating in order to provide its customers with the latest solutions in an ever-changing environment. Despite recently celebrating their 35th birthday Ctrack continues to seek out cutting edge solutions to provide information and insight on a wide variety of moveable and non-powered assets while providing real-time monitoring. When developing and refining their operation, especially in the tough and stressful mining environment, Ctrack always considers five key focus areas of asset management namely, Safety & Security (Risk Management), Driving Behaviour (Cost Management), Productivity & Efficiency, Operations Control & Compliance and Asset Management. Safety & Security (Risk Management) In any mining operation accident prevention is top priority. Utilising a range of remote monitoring systems to alert control room staff to driver behaviour and asset utilization ensures a safe and productive working environment. The data harvested from these systems makes it possible to upskill operators and ensure the safety of both workforce and assets. Managers can provide direct operator behaviour feedback to their staff using indicators through Ctrack software applications, visible on mobile devices, as well as vehicle in-cab peripherals or electronic data sets. Various camera options, allow live video and replays of incidents on the road, that could support and reduce insurance claims. Engine performance monitoring ensures that the vehicle is driven efficiently by keeping an eye on engine speed and will also alert fleet managers to excessive periods of idling. Further enhancements to safety and security of mining operations include the use of Ctracks unique script capabilities called SMILE. With SMILE, operators can create unique efficiency and risk outputs that create endless opportunities to measure and solve an operator’s critical KPI’s. Managers can set up geo zones with pre-defined speed limits, load limits, safe stop areas, and other customizable parameters. These simple yet effective actions reduce wear and tear on the vehicle, reduce warranty claims, and improves safety.
Ctrack Driver Management tools succeed at providing you with multiple solutions to ensure your operations run effectively, efficiently, safely, and allow operators to manage drivers, asset access, and driver behaviour across multiple vehicles and assets remotely. Productivity & Efficiency Owning and operating vehicles efficiently, no matter the industry is reliant on information. Having the correct information in a tangible format is imperative to making the right decisions. Ctrack’s rich fleet analytics and smart interpretation of data provide the information
needed for critical decision making, from cost savings to future investments. Improved productivity is guaranteed when business owners know how their vehicles are being used. Efficient fleet management will ensure the avoidance of unnecessary costs incurred by factors such as speeding, accidents, fuel consumption and harsh driving. In addition to vehicle locations, Ctracks real-time visibility software, including mobile applications and website dashboards, provide valuable information on drivers, points of interest, ground coverage, upcoming tasks and even a live productivity dashboard. The culmination of real-time visibility, proactive notifications and infographics ensures optimised and efficient asset utilisation and ultimately a more profitable operation.
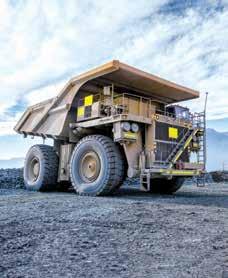
Features Driver Identification & Driving Behaviour Monitoring Engine CollisionMonitoringPerformance(RPM&Idling)AvoidanceSensors Fuel Level & Consumption IrisMonitoringCameraSolution Front-Back-Side Facing Camera Option Onboard TipBreathalyserWeighingSensor Improve your mining operation with dynamic Ctrack Solutions. www.ctrack.co.za | sales@ctrack.co.za | Call Centre: +27 (0)860 333 VisibleAlways444
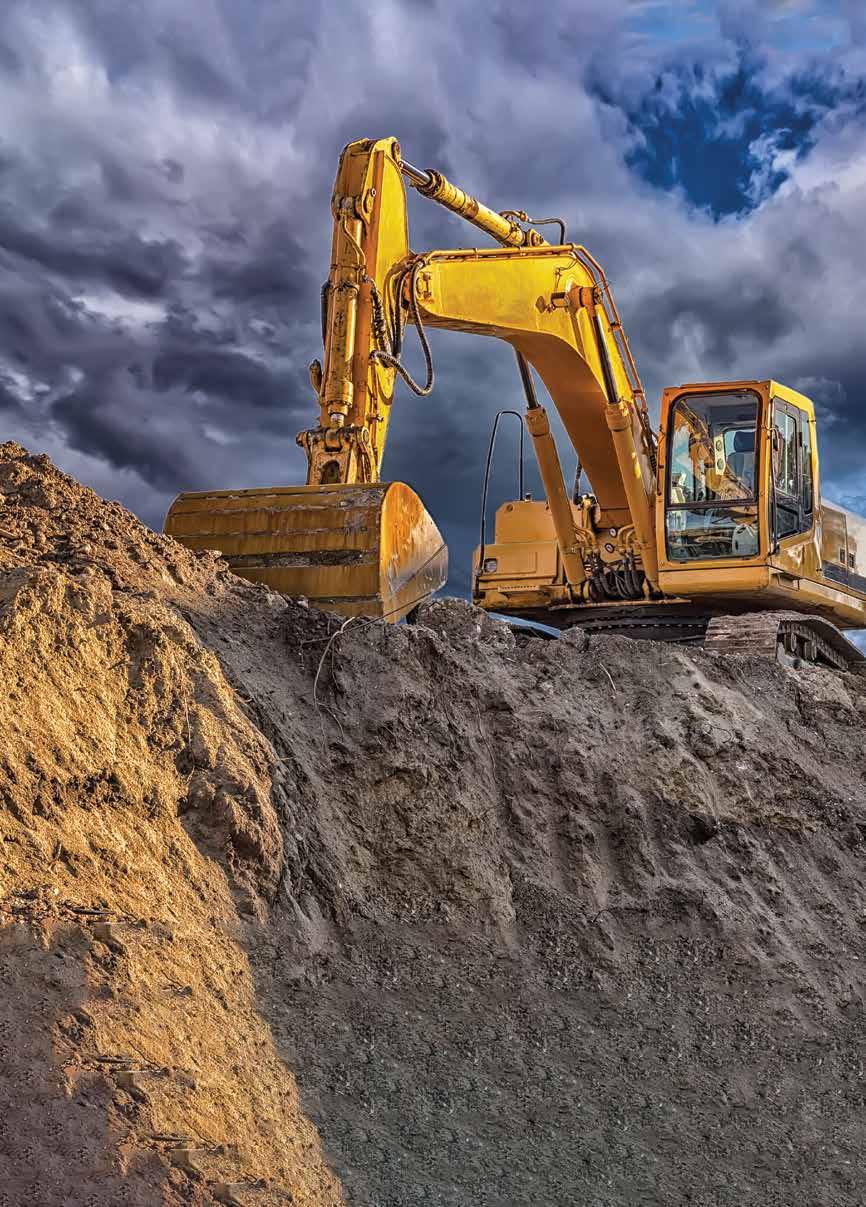
34 Mining Business Africa | July - August 2022
how they can break the glass ceiling without reducing the appointment of women into a numbers game, so to speak? LN: Have more flexible policies to allow women who love their career and their families to manage both. It’s incredible how loyal and dedicated women are when they know that they are valued and that their employer understands the importance of their family commitments and life outside of the firm.
MBA: NSDV seemed to be managing pretty well, now you have brought two additional legal minds on board. What has necessitated the appointment of people with their skill sets? LN: We have been fortunate enough to be busier than ever. I think the market has recognized the value of our integrated professional offering combined with our legal and practical approach to mining-related matters.Animportant business value for us is to attract and retain top-tier talent, and part of maintaining our specialized services is preventing burnout and creating a space where our talented team can maintain a balanced lifestyle.We’re all about sustainable solutions that are good for business and the people we do business with. The busier we get, the more people we will keep appointing.
MBA: You have gone beyond the threshold of 50% women. What is your advice to other legal firms on May - June 2022
LN: I never like to generalize but have observed and experienced that women have a different approach to matters than men. Generally, I find women are more collaborative, more inclusive, and more aware of all stakeholders’ so-called ‘softer elements’ within a transaction. Our male counterparts can be more fixed on the bottom line – the financial upshot or commercials of the transaction. Reaching the bare minimum of 50% representation of women for many organisations remains a tall order. Sometimes, for the few that have achieved this, in reality, it becomes a tick box exercise for the sake of fulfilling compliance requirements. Sadly, many of the women referenced in the statistics would neither be in decision-making positions nor key areas in an organisation’s core business. But blazing a trail, NSDV has achieved a South African milestone –it could be even an African record, now it boasts 70% of the women-led legal team involved in various areas. NSDV is Africa’s first fully integrated law and consultancy firm specialising in mining, construction, energy, and environmental law.
LN: Watch this space!
Lili Nupen - Director at NSV; Nel de Jager - Senior Associate; and Nicole Kruger – Mining and Environmental Law Associate fields questions from Mining Business Africa on the milestone. de Jager and Kruger recently joined the firm to bolster the legal offering.
Going beyond the Glass Ceiling Women’s month feature – Women in Mining FEATURE
Lili Nupen, Director at NSDV
MBA: Are we going to see more additions to the staff complement at NSDV this year?
When you take industries like mining and construction that are known to be maledominated, the ‘softer’ elements are often overlooked. In my experience, this ‘softer’ approach has been welcomed and all stakeholders are seeing the benefit of varying approaches from men and women. It would be great to see this at an operational level within the mining and construction industries too. Where you can see this difference in approach is women’s willingness to collaborate and create relationships with stakeholders and regulators as opposed to merely taking them to court to obtain a favourable outcome.
MBA: Why do you think the legal profession needs more women to be involved in positions of influence specifically in mining, construction, energy, and environmental law?
MBA: How relevant are their skills concerning the vision and mission of NSDV? LN: We purposefully look for talent focused on the mining, environmental, energy, and construction sectors. Nel and Nicole complement our existing skillset perfectly.
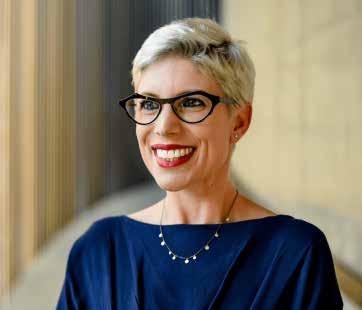
MBA: Where would you like to see NSDV grow in the next five and ten years NdJ: Judging by what the firm has achieved in the past 5 years, I can see NSDV being a formidable player in the market in five years, and in the next ten years I expect NSDV will be a leader in the legal industry.
Nicole Kruger – Mining and Environmental Law Associate MBA: You are joining NSDV at an earlier career point. What makes you think that the timing is right? How does NSDV fit in your growth plans?
Nel de Jager - Senior Associate MBA: Assuming you had other tempting prospects, Why did you opt to be part of NSDV? What struck you about the organisation as the place-tobe? NdJ: Apart from the team of exceptional practitioners, NSDV has a separate team of corporate advisors. I love the integrated and practical approach NSDV has to business solutions, and I’m very excited to join this new type of speciality law firm with its more personable approach.
Nel de Jager - Senior Associate
Mining Business Africa | July - August 2022 35
MBA: What value do you aim to add to the organisation? NK: I hope to contribute to all aspects of the organisation and, in particular, I aim to add value to the Mining and Environmental Law team at NSDV by doing my best daily, being detail oriented, and remaining calm and positive in stressful situations.
NK : I feel that this is a great time in my career to be challenging myself and learn from all different types of people, environments, and work. NSDV encompasses a diverse and dynamic team and provides innovative legal services for its clients. I believe that as an Associate in Mining and Environmental Law team at NSDV, I will experience significant development both personally and professionally, and I already have.
Nel de Jager - Senior Associate
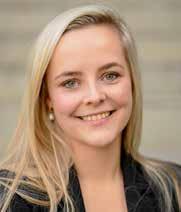
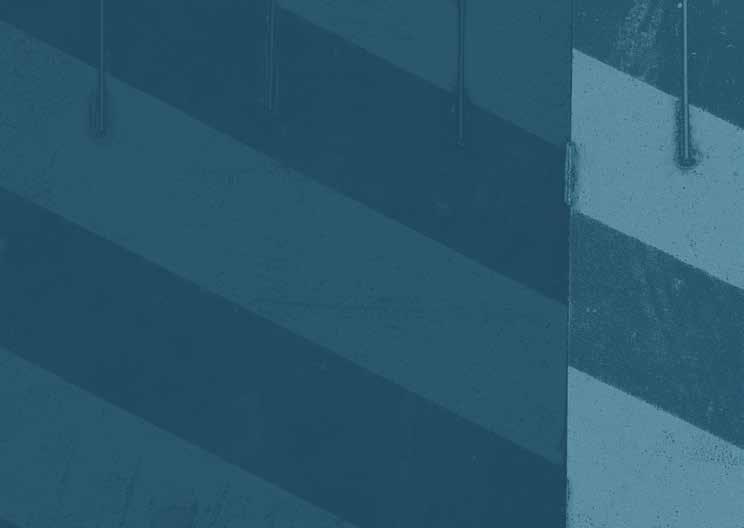
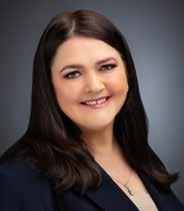
Long-lasting and High-Performance Energy Storage Industrial-scale Lithium-ion Energy Storage Batteries for mining projects FEATURE
BlueNova is a manufacturer and supplier of a wide range of energy storage solutions for clients in different sectors. The company’s A-grade Lithium Iron Phosphate (LiFePO4) product offering is a perfect fit for addressing the demand for reliable energy storage in industries in the region. The chemistry has several advantages over lead acid energy storage batteries.
BlueNova Lithium-Ion Battery BN52V-230-12k LiFeYPO4
36 Mining Business Africa | July - August 2022
Wide capacity range BlueNova supplies A-grade Lithium Iron Phosphate (LiFePO4) batteries ranging in capacity from 104Wh (for powering gate motors and security systems) to 1.3MWh (for powering large office blocks or microgrids). Besides batteries, BlueNova develops devices such as the BMAC (Battery Monitor and Control (BMAC). The BMAC not only facilitates serial (CAN) communication between its batteries and select inverters, but also enables remote monitoring of battery peripherals. This allows the company to provide unparalleled technical support in the industry.The company’s medium to large solutions, as well as BMS electronics, are built at its facilities. Its smaller products are imported. However, BlueNova’s team tests and supports the products in terms of technical support and warranty.
The requirements that the representatives would normally need to confirm to provide a suitable solution include the following:
In general, BlueNova can provide delivery, commissioning and continuous technical support for the systems.
Tailor-made turnkey solutions BlueNova offers tailor-made turnkey solutions to meet the demand for industryscale energy storage coverage. Its iESS (Intelligent Energy Storage Systems) are designed to meet the specific requirements of its owners. iESS systems typically include a battery bank, high voltage inverter(s), air conditioning, fire suppression, access control and remote monitoring electronics. The battery pack includes a ten-year warranty supported by BlueNova and the inverter(s) and other components typically also include warranties from various suppliers. The battery pack includes its own BMS electronics.
Delivering a suitable solution BlueNova undertakes a thorough process to ensure that a client, for instance, a mining company in Africa, has a suitable lithium energy solution for its needs. Its technical sales representatives handle enquiries from customers.
• Usable capacity requirements (including autonomy)
With increasing investment in power generation projects in Africa, there is a simultaneous need for industrial-scale energy storage solutions. To fill this gap, BlueNova has a wide selection of products divided into several product ranges bespoke for the different needs of clients.
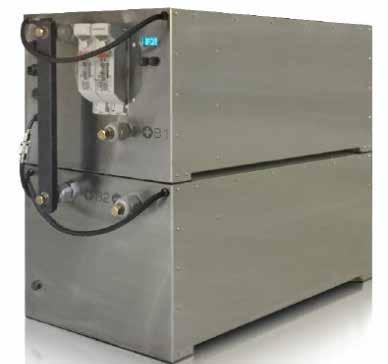
Advantages of BlueNova LiFePO4 over lead acid BlueNova assures customers that its A-grade Lithium Iron Phosphate (LiFePO4) medium to large batteries offer several advantages over conventional lead acid. Mainly, these include but are not isolated to:
Mining Business Africa | July - August 2022 37
• Application of the battery
• Longer Depth of Discharge (DOD) A-grade Lithium Iron Phosphate (LiFePO4) cells fade with a maximum of 20% over the service life. The recommended maximum depth of discharge (DoD) of the batteries is 80%, which ensures a cycle life of 5000 cycles.
• Additional charging sources (solar arrays, generators etc.) that would be included in the system
• Less weight LiFePO4 batteries are much lighter compared to lead acid batteries with equivalent capacities. Its weight is a quarter of a lead acid battery with the equivalent capacity, and the volume is a third of an equivalent lead acid battery. This not only translates to easier installation but also to financial savings associated with transportation fees. Such savings are further multiplied considering that LiFePO4 batteries last much longer than lead acid batteries and would therefore need to be replaced much less often. High charge efficiency The charge efficiency of LiFePO4 batteries is 96% (4% lost), if recharged over two hours. This efficiency improves to 98% (2% lost) if recharged over ten hours. In comparison, the average charge efficiency of lead acid batteries is 67% (33% lost). Lead acid batteries can also not be recharged in two hours. The closer a lead acid battery gets to 100% state of charge (SoC), the slower it charges. Additionally, over-charging a lead acid battery will inevitably shorten its lifespan dramatically and may result in toxic gases being vented from the battery. Lead acid batteries are dangerous under these circumstances and may result in thermal events and subsequent insurance claims.
• Continuous
• Certain applications might require feedback on more than the above. Once requirements and expectations have been established, we propose one or more solutions that can then be discussed further if necessary.
On the other hand, lead batteries can only be discharged to 40-50% DoD, and will then only yield a cycle life of 1800-2500 cycles for premium lead batteries. The BlueNova team states that performing a cost analysis based on these variables will illustrate that the running costs for LiFePO4 batteries is substantially lower than that of premium lead batteries.
• Safest battery LiFePO4 batteries are the safest lithiumbased batteries available (apart from lithium titanante). This is based on findings of rigorous tests conducted worldwide. LiFePO4 batteries have been punctured, crushed and incinerated in tests performed by several independent companies. Fascinatingly, this has never led to a thermal event taking place (unlike with the more dangerous chemistries in the lithium-ion family, such as lithium nickel cobalt oxide found in cell phone & laptopLiFePO4‘sbatteries).safety is further bolstered by the fact that LiFePO4 batteries include battery management system (BMS) electronics, which protect the batteries against over-charge, over-discharge and short-circuit complications. Warranty One of the common concerns of endusers is the lack or limited warranty on critical components of products. Given this, on its part, Bluenova guarantees that most of its products include a 10year warranty entailing local technical support on products that it has developed and supplied itself (incl. electronics). The company warrants that no other local supplier of LiFePO4 batteries can make this claim in its entirety. BlueNova is keen to be involved in industrial projects where there is a need for medium to large-scale battery storage solutions. & peak power
• Inverters and/or chargers to be integrated with
Minimising downtime BlueNova recognises that downtime to a battery storage system can be very costly to a mining company, leading to loss of productivity and revenue. For this reason, it has provisions firmly in place to minimise downtime. BlueNova has established that the best countermeasure to possible downtime is for the battery/battery system to be remotely monitored. In this way, downtime can then be pre-empted and thus avoided. And so, the company offers several remote monitoring solutions that include functionalities that warn users and the technical support team automatically through SMS. For instance, these would be cases where power demand approaches higher than normal levels of capacity is discharged to levels beyond what was previously configured as "safe".
requirements
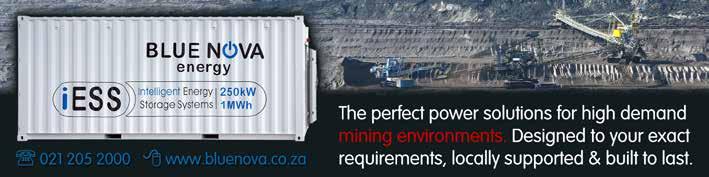
FEATURE
Ensuring a reliable 24/7 electricity supply from grid-to-mine, is one of the challenges currently facing the mining industry. In addition, the high cost of electricity is negatively impacting operating expenses to a level that is affecting the overall viability of mining operations. “Reducing high electricity costs in the mining industry can be easily achieved through PV solar power. While there are currently very few solar projects for mines in South Africa, owing to challenges experienced in the licensing process, there is a positive sentiment as regulatory reform is underway, together with the expected approval of a solarpowered mining project in the coming weeks,” says Svilen Voychev, Managing Director, Valsa Trading. “The challenges experienced by the mining sector in terms of power supply also provides an opportunity to innovate,” says Voychev. One such area is that the implementation of solar results in a reduction in the carbon footprint of the mine. He explains that a mine can achieve many deliverables by building solar projects with excess power capacity than what is required for its operations. This would allow the mine to sell the power to a local utility that may not be able to increase its supply of power due to its own constraints. Further, it might be possible for the mine to supply a neighbouring mine and/or local communities at an appropriate tariff. Owing to the low operation and maintenance costs associated with solar and the long-term life of solar panels, the mine’s solar project could continue to operate after the life of the mine has been reached. “We can provide a turnkey solar solution to replace some, if not all, of a mine’s existing power sources, whether it is a diesel generator or expensive and unreliable electricity from the national or local grid” States Voychev. Valsa conducts a visibility study that takes the needs of the mining operation into consideration. The design and the sizing of the PV system is based on the power profile of the mine and the load requirements. PV solar enables the mining operation to create stable operating conditions that can allow it to operate at full capacity. “Many African mines are located in remote areas without access to a national electricity grid. The use of expensive generator power is often the only power solution. Most of these locations have abundant solar resources and, therefore, solar can be used to replace some of this power. The high output of the solar solutions at these sites (subject to the impact of extremely high temperatures in some locations) increases the viability and lowers the cost per kilowatt as well as the payback period,” Voychev concludes.
38 Mining Business Africa | July - August 2022 PV SOLAR ALLTOOLSPVPVCABLINGCOMBINERBATTERIESMOUNTINGINVERTERSPANELSSTRUCTURESBOXESSOLARKITSSOLARDESIGNSELECTRICALCOMPONENTS Call 011 794 1306 Email info@valsa.co.za www.valsa.co.za
Valsa Trading is a PV Solar system manufacturer and distributor, supplying PV Solar Mounting System Solutions to resellers, installers and clients installing solar systems for businesses and homes across South Africa.
SIMPLE & SOLUTIONSEFFECTIVECOST
PV Solar reduces both Costs and Carbon Footprint in Mining
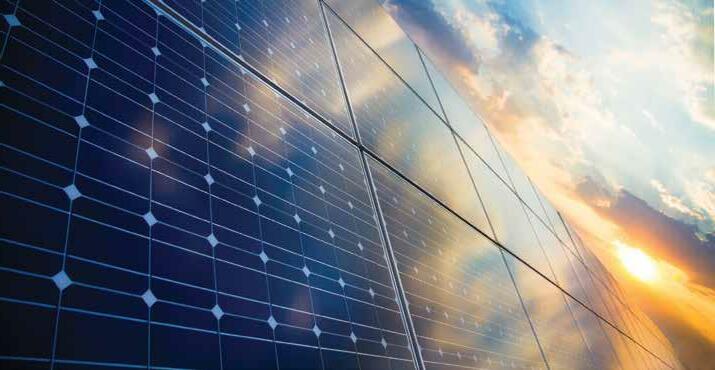
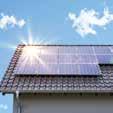
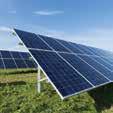

‘In dynamic testing, which is applied to license winders, the law states that physical testing must be conducted within every 200 days in order to comply with safety standards.
‘There are two levels of testing. Level one is where general electrical and mechanical audits are conducted. Level two involves designer audits on OEMs. In level one testing, even though there is no specific law that stipulates the frequency of testing for winders, industry best-practice dictates that they should be tested at least four times a year.
WearCheck’s technical compliance (TC) team comprises six winder inspectors, who have around 140 years’ combined experience between them. It is this team’s responsibility to check that every component in a given machine is working exactly as it is supposed to work.
This safety circuit is required to undergo technical compliance testing every time a level one audit is scheduled. Here, testing is conducted by WearCheck advanced field services technician, Joe Kies, to ensure that it is operating within the required safety regulations. After each audit, WearCheck prepares a report containing all findings and the previous three audit results to establish performance trends.
‘During a typical TC audit, which is normally done during a weekly examination in which around 100 items are tested, the safety circuit is tested for correct operation. The different circuits on each unit must be tested to ensure correct operations. A report is compiled with all findings and includes the previous three audit results so that a trend can be established. Recent repairs done on the machine are highlighted.
Mining Business Africa | July - August 2022 39 Oil, Vibration and Motor Circuit Analysis Solutions the Mining Sector
‘Our TC team is standing by to assist in any way possible to ensure that all moving machinery is audited according to best practice, and that all required safety standards are met. Due to the production-critical nature of our support work, we are on call 24/7/365.’
‘WearCheck’s TC team comprises six winder inspectors, who have around 140 years’ combined experience between them. It is this team’s responsibility to check that every component in a given machine is working exactly as it is supposed to work. For example, on a lighting circuit, all lights must be working perfectly. Or each safety circuit trips exactly when it is supposed to trip.
WearCheck’s advanced field services (AFS) division offers a wide range of specialist monitoring techniques which include rope testing, technical compliance (TC) and non-destructive testing. Here, some of the different TC techniques are discussed. According to Johan Stols, WearCheck’s TC manager, the ultimate goal of the TC division is to ensure that all the components that they monitor comply with stringent, predetermined safety standards. The TC team plays a supporting role to customer operations by reduction of risk using specialised and multidisciplinary services and resources, and they are on call at all hours. The TC customers predominantly operate in the mining sector, but other industries are beginning to realise the value of TC, too. The TC team’s mining customers are generally the deep level mines – coal, gold, platinum etc – where vertical shafts (people movement), incline shafts (goods movement), ropes and many other components are tested. The TC tests generally include level one winder and main fan compressor inspections, compliance level electrical inspections, headgear elevator electrical inspections, lock bell inspections, chairlift electrical inspections, secondary injection testing and conveyor belt compliances.Thesecomponents must undergo regular tests to ensure that they are constantly in a safe operating condition. Inspections are conducted using specialised testing equipment, highly skilled and experienced inspectors, and compliance to rigorous safety standards. In South Africa, TC standards are legislated in many cases, but are also guided by industryrecognised best-practice values. Stols explains further, ‘We add value for our clients by providing quality services, and identifying and mitigating risks associated with safety and production-critical equipment.
WearCheck helps companies comply with technical safety requirements
Repairs are carried out by the engineer’s maintenance team, and then the TC team returns to retest the faulty component.
‘What is important to note, for example, is that each winder has its own unique operating and protection system, which must be adhered to when it is undergoing testing. We make sure that we are acquainted with each component and its maintenance and compliance history.
‘If an error is found, this is reported to the engineer in charge of that particular component.
‘Tracking the compliance status of each component enables the engineer and the maintenance team to keep the component in peak operating condition and avoid nasty accidents or costly downtime.
FEATURE
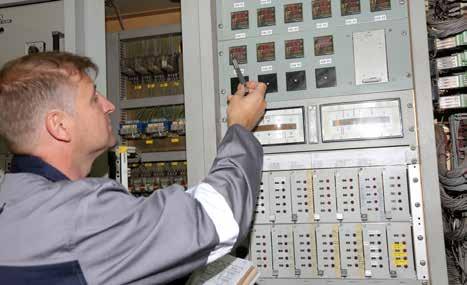
Advertiser’s index Blue Nova NSDV.......................................................................................35Magnitech................................................................................13LASEHydrogenEvraEnergyElementalCTRACK...................................................................................33Energy...................................................................37analytics................................................................28Advance......................................................................31Consulting.......................................................................17Africa....................................................................IFCIndustrielleLasertechnikGmbH................................23 Resources 4 Africa...............................................................IBC RPAS Consulting.....................................................................19 SI WearValsa........................................................................................38UnitedTegaSymplexity...............................................................................06SomaAnalytics..............................................................................30Initiative.........................................................................09Industries........................................................................25KingdomParts.............................................................20Check.............................................................................03 Mining Business Africa (MBA) is Pan-African bi-monthly publication that focuses on latest developments in mining and allied industries in Africa. The publication covers the scope of critical activities from pit to port – mineral exploration (prospecting), mine planning and development, extraction, mineral processing, storage transportation, as well as beneficiation. Mining Business Africa provides the desired mileage for companies looking to promote their products and services to a specific niche clientele in the African Mining Sector. Subscribers are located or at least involved in projects in South Africa, Botswana, Zimbabwe, Zambia, Kenya, Democratic Republic of Congo, Kenya, Tanzania, Ghana and Nigeria. MBA is published by Media Icon, a company manned by personnel with a combined experience of 30 years in the publishing space. TO ADVERTISE | CALL: + 27 10 055 3356 | Email: info@miningbusinessafrica.co.za Becker Varis Ltd. 122 Dell St., Sudbury, Ontario, Canada P3C 2Y1 | www.becker-mining.com The Becker Mining System smartdetect changes the SURFACE COLLISION AVOIDANCE market with leading industrial technology at an affordable cost. info@ca.becker-mining.com
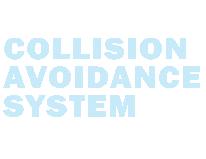


For sponsorship opportunities please contact us on: sponsorship@resources4africa.com +27 (0) 11 463 7799 // +27 (0) 61 421 9492 // registrations@resources4africa.com // www.joburgindaba.com REGISTER TODAY! Joburg Indaba 2022 is proudly sponsored by: Lead MiningPremiumSponsorSponsorsIndustryPartners LEAD SPONSOR 5 -6 October www.joburgindaba.com2022 THE INANDA CLUB, FORREST ROAD, INANDA, JOHANNESBURG & ONLINE
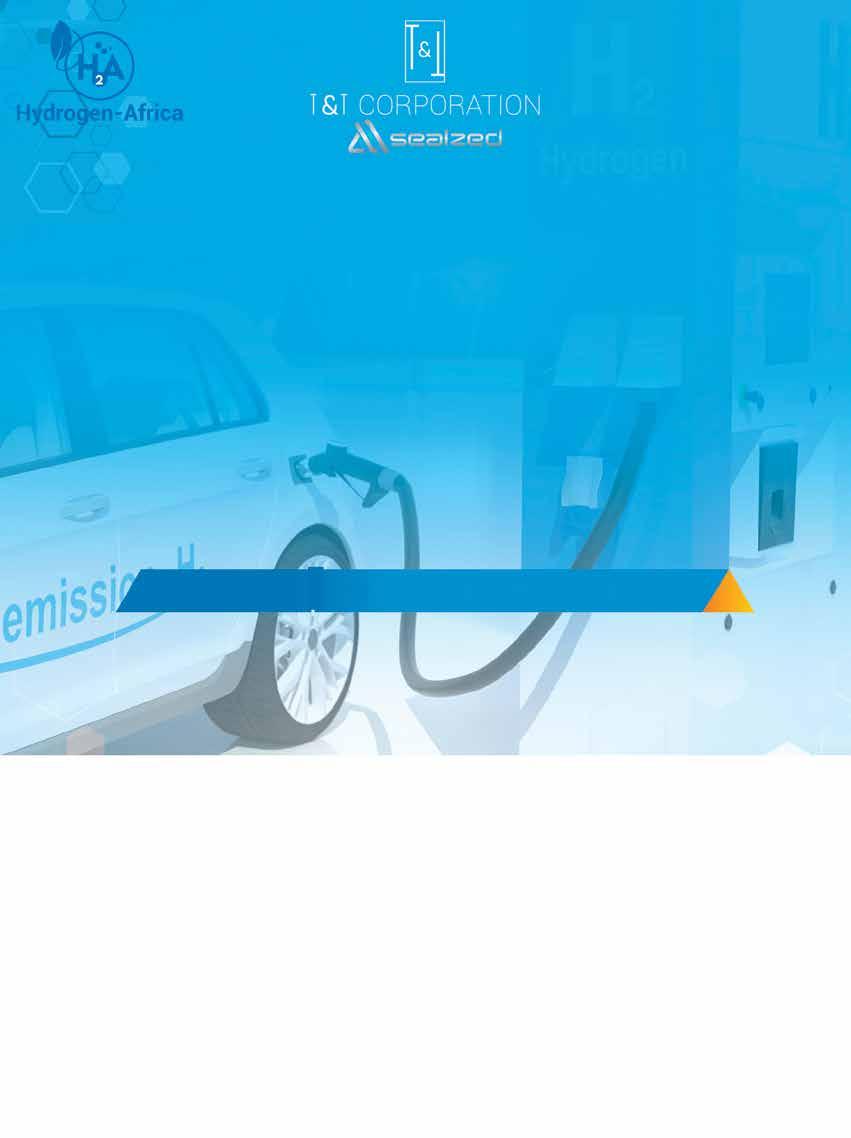
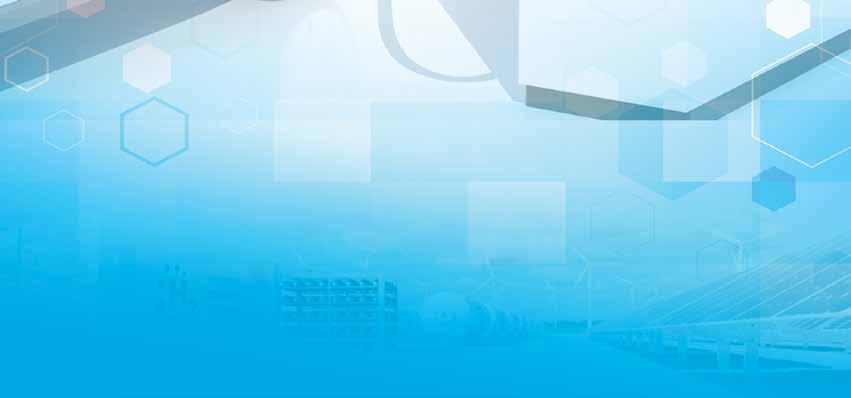


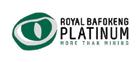
Airwork Africa is an industry leading expert in all facets of flight operations. We provide a high standard of support and full turn key aviation services to a wide range of industries and can configure the aircraft to the customer’s specific requirements. Our capabilities include providing a safe, reliable and class leading product offerings within the following categories: P +27 82 967 0440 E donovan.foley@airworkgroup.com Suite 4, Hangar 38 Wonderboom Airport Linvelt Road, Pretoria PO Box 14 535, Sinoville South Africa 0182 www.airworkgroup.com • Utility helicopters offering survey and external load capabilities • High capacity transportationpassenger • The carriage of security sensitive cargo • The carriage of Dangerous Goods • Full IFR and NVG capabilities • VIP Charter • EMS and Fire Fighting • SACAA Helicopter Operations
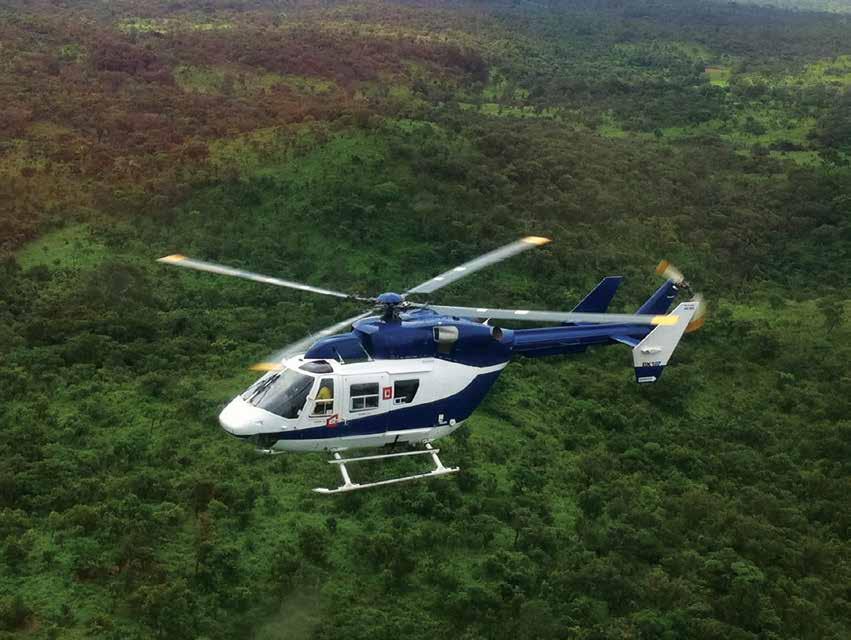