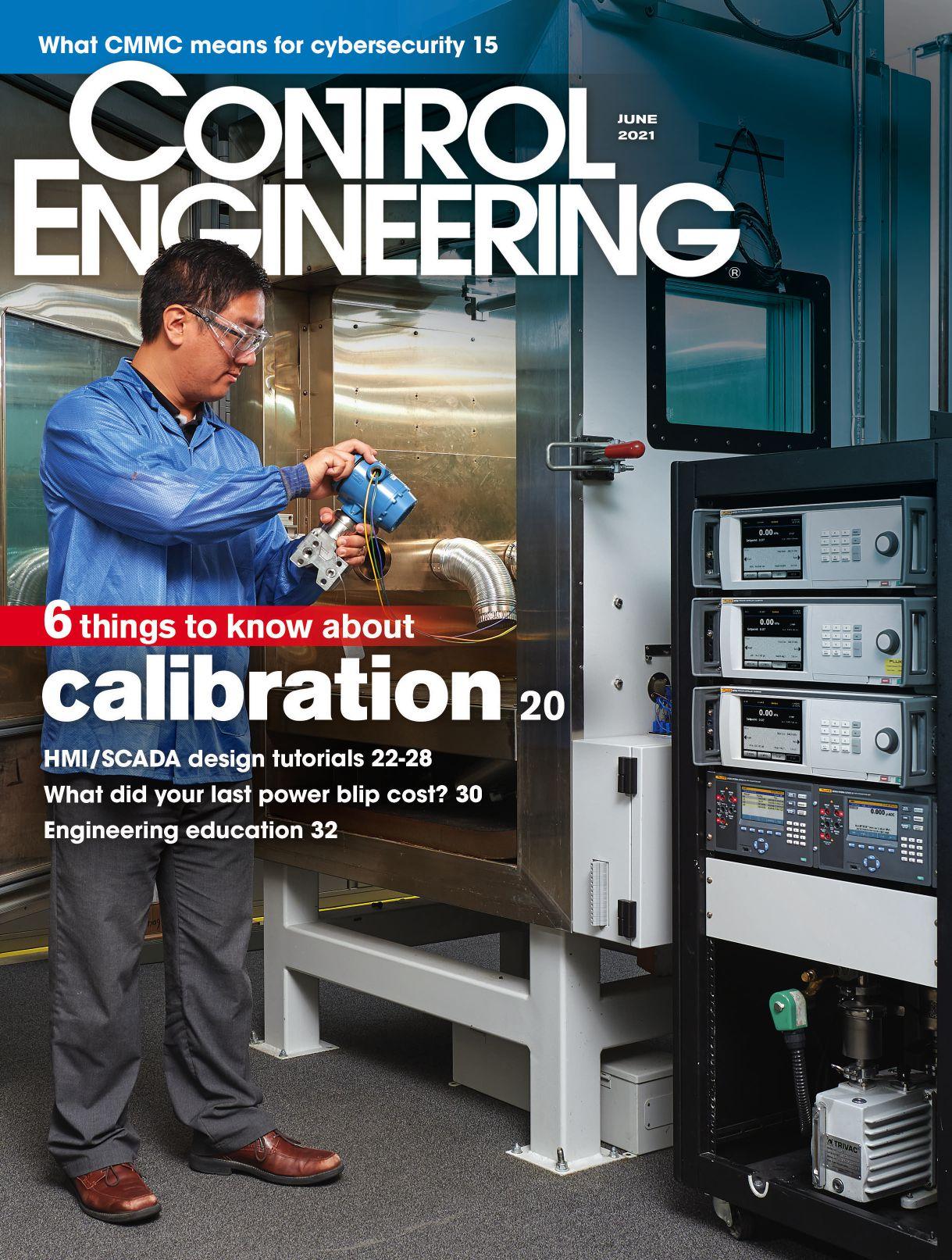































C-more Micro HMI Panels
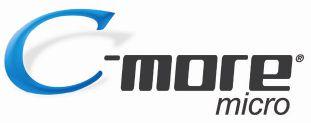
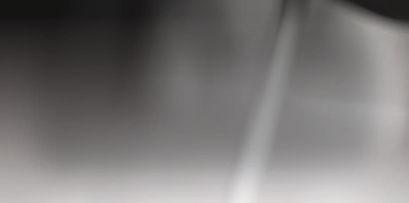
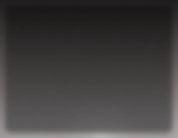
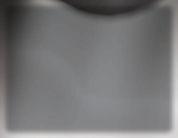

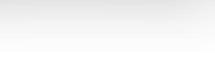
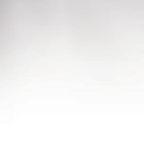
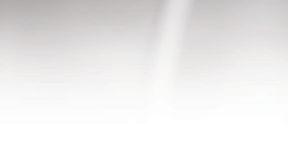
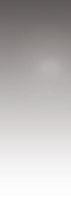
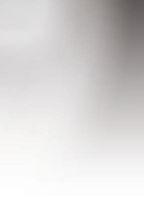

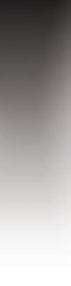
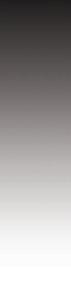
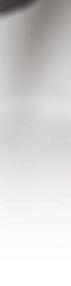
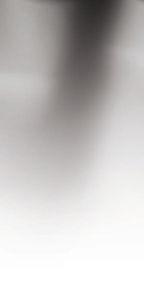

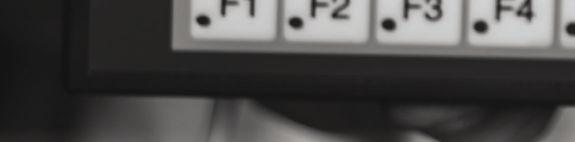
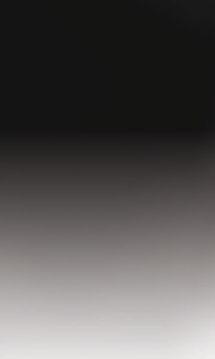

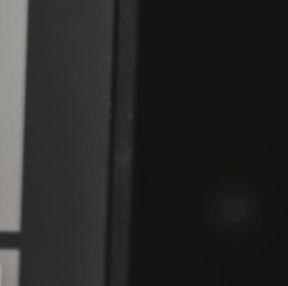

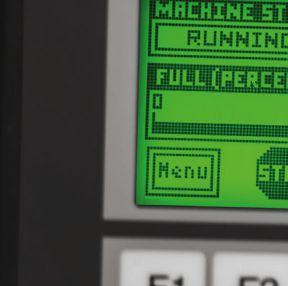
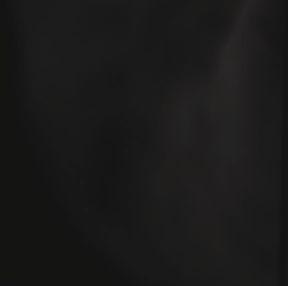
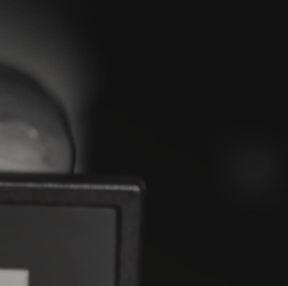

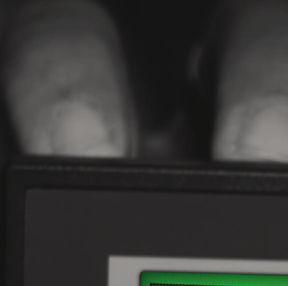
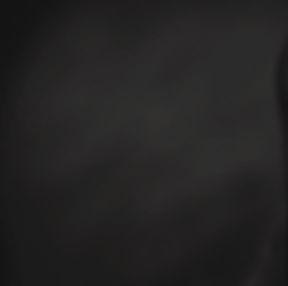


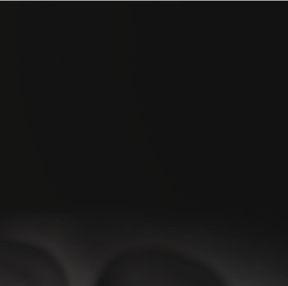
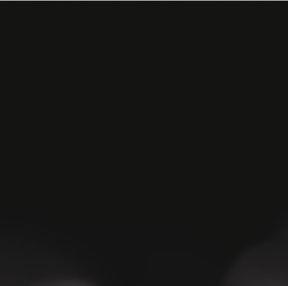
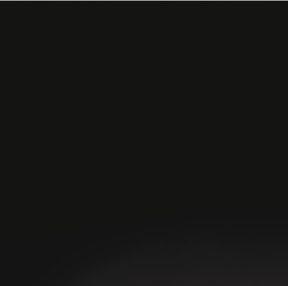
RHINO power supplies provide the efficiency, affordability and most importantly the durability needed for industrial applications. With a wide variety of form factors, power ratings, and output voltages (up to 48VDC), along with the industry’s best prices, RHINO power supplies are the most practical solution for your DC power needs. The RHINO PRO family of power supplies iss the best choice when you need a high-performance power supply or additional features such as an LED display or automatic power boost.
Automatic Power Boost ensures continuous operation when a large inrush current is detected starting at $93.00
Also Available:
Value Series Power Supplies starting at $34.00
Ruggedized Power Supplies (Class1 Div. 2 Hazloc) starting at $249.00
Additional 1-Phase AC/DC Power Supplies starting at $19.00
3-Phase AC/DC Power Supplies starting at $63.00
DC-DC Converters starting at $75.00 DC Specialty Modules Redundancy, buffer and battery control modules starting at $31.00
You get everything you need to know about the health and performance of your motors, such as vibration, bearing condition and speed, securely out, while the IECEx, ATEX and NEC 500 certified IP66/67 stainless steel and reinforced PBT case lets nothing in, be it water, dust or corrosive chemicals.
The new high-performance ABB Ability™ Smart Sensor for hazardous areas.
61 | PRODUCT EXCLUSIVE: Rugged, superspeed USB 3.1 hub extends temperature options
Ultrasonic flow measuring system, Smart function kit, Metrology system for metal layer detection, Machine safety lighting guards, Tunable diode laser spectrometer, Connectors for 5G networks
More New Products for Engineers: www.controleng.com/NPE.
63 | Four ways to production resiliency in food processing
Food processing operations need to be resilient during the COVID-19 pandemic and can achieve this by improving collaboration and enforcing consistency.
• Control Engineering Career and Salary Survey, 2021
• Safety instrumented systems: Diversity in flow measurement
• How companies are winning top engineering candidates in a post-pandemic world
• How MEMS sensors are changing for automotive applications
• Career, salary survey 2021: Advice Keep up with emerging trends: subscribe. www.controleng.com/newsletters.
Attend CFE Media and Technology’s Virtual Training Week on-demand with 17 sessions on motors and drives, safety and security, critical power considerations, effective maintenance strategies and digital transformation and advanced manufacturing. https://cfeedu.cfemedia.com/learning-paths/cfe-mediatechnology-virtual-training-week
Digital transformation is a hot buzzword in manufacturing today, but what does it mean? What does it mean for manufacturers and what effect will it have for the present and future?
This helpful eBook offers several examples of the many digital transformation is taking hold in manufacturing. Learn about five ways digital transformation metrics give manufacturers more flexibility, how to address future obsolescence in embedded computer systems, and predict product quality with analytics. Learn more and register to download at www.controleng.com/ebooks.
How system integrators make remote automation work, Migrating legacy PLCs to modern PLCs, Replacing seven SCADA systems with one and More advice in a Supplement to Control Engineering and Plant Engineering www.controleng.com/GSIR
Control Engineering digital edition
Download an article or issue PDF. Tablet and digital editions provide links to more article images, text and resources online. www.controleng.com/magazine
controleng.com provides new, relevant automation, controls, and instrumentation content daily, access to databases for new products and system integrators, and online training.
Mobile collaborative robot growth buoyed by changing market, https://www.controleng.com/articles/mobile-collaborative-robot-growth-buoyed-by-changing-market/ Semiconductor industry has a resilient supply chain, https://www.controleng.com/articles/semiconductor-industry-has-a-resilient-supply-chain/
Top 5 Control Engineering articles April 26 to May 2, 2021, https://www.controleng.com/articles/top-5-control-engineering-articles-april-26-to-may-2-2021/ Control Engineering hot topics, April 2021, https://www.controleng.com/articles/control-engineering-hot-topics-april-2021/
Safety instrumented systems: Diversity in flow measurement, https://www.controleng.com/articles/safety-instrumented-systems-diversity-in-flow-measurement/
OPC UA: wider controller communications with TSN, APL, https://www.controleng.com/articles/opc-ua-wider-controller-communications-with-tsn-apl/ Benefits of PLC-controlled robots, https://www.controleng.com/articles/benefits-of-plc-controlled-robots/ Robots learning to grasp friction, https://www.controleng.com/articles/robots-learning-to-grasp-friction/
Connected distribution center takes control of intralogistics challenges, https://www.controleng.com/articles/connected-distribution-center-takes-control-of-intralogistics-challenges/
Neural nets used to rethink material design for batteries, more, https://www.controleng.com/articles/neural-nets-used-to-rethink-material-design-for-batteries-more/ Control loops benefit more than control systems, https://www.controleng.com/articles/control-loops-benefit-more-than-control-systems/
Five technologies that can help manufacturers evolve after COVID-19, https://www.controleng.com/articles/five-technologies-that-can-help-manufacturers-evolve-after-covid-19/ Automation built for resiliency, https://www.controleng.com/articles/automation-built-for-resiliency/ Robot sensor market growth expected, https://www.controleng.com/articles/robot-sensor-market-growth-expected/ Mobile access to production data through customized applications, https://www.controleng.com/articles/mobile-access-to-production-data-through-customized-applications/ Robot sales have strong start for 2021, https://www.controleng.com/articles/robot-sales-have-strong-start-for-2021/ Overcome patch, management vulnerabilities for OT, https://www.controleng.com/articles/overcome-patch-management-vulnerabilities-in-an-ot-environment/ Securing cloud data is a challenge for many companies, https://www.controleng.com/articles/securing-cloud-data-is-a-challenge-for-many-companies/ HMIs work in rugged, low-temperature outdoor applications, https://www.controleng.com/articles/hmis-work-in-rugged-low-temperature-outdoor-applications/ Direct laser writing method leads to advanced printing, https://www.controleng.com/articles/direct-laser-writing-method-leads-to-advanced-printing/ Laser-induced graphene process creates micron-scale patterns, https://www.controleng.com/articles/laser-induced-graphene-process-creates-micron-scale-patterns/ Omlox benefits for manufacturers, https://www.controleng.com/articles/omlox-benefits-for-manufacturers/ System integrators are a good investment, https://www.controleng.com/articles/system-integrators-are-a-good-investment/ TSN market to reach $1 billion by 2026, https://www.controleng.com/articles/tsn-market-to-reach-1-billion-by-2026/
Top 5 Control Engineering articles May 3-9, 2021, https://www.controleng.com/articles/top-5-control-engineering-articles-may-3-9-2021/ Metal-free, recyclable peptide battery developed, https://www.controleng.com/articles/metal-free-recyclable-peptide-battery-developed/ Safety assessments for robots and robotics, https://www.controleng.com/articles/safety-assessments-for-robots-and-robotics/
Benefits of virtual factory acceptance test systems, https://www.controleng.com/articles/benefits-of-virtual-factory-acceptance-test-systems/ Turning toxic sewage sludge into renewable energy, https://www.controleng.com/articles/turning-toxic-sewage-sludge-into-renewable-energy/ Mitigation, technologies for power system harmonics, https://www.controleng.com/articles/mitigation-technologies-for-power-system-harmonics/ Six steps for preventing a cybersecurity attack, https://www.controleng.com/articles/six-steps-for-preventing-a-cybersecurity-attack/ Computing device simulates human learning, https://www.controleng.com/articles/computing-device-simulates-human-learning/
Choosing between TAP and SPAN ports for ICS security, https://www.controleng.com/articles/choosing-between-tap-and-span-ports-for-an-ics-security-solution/ Technique induces magnetism in nanoscale materials, https://www.controleng.com/articles/technique-induces-magnetism-in-nanoscale-materials/ Graphene used to make encrypted keys harder to hack, https://www.controleng.com/articles/graphene-used-to-make-encrypted-keys-harder-to-hack/ Nature helps sustainable industrial networks, https://www.controleng.com/articles/how-natures-characteristics-can-help-build-sustainable-industrial-networks/ Algorithm helps robots collaborate on difficult tasks, https://www.controleng.com/articles/algorithm-helps-robots-collaborate-on-difficult-tasks/ Top 5 Control Engineering articles May 10-16, 2021, https://www.controleng.com/articles/top-5-control-engineering-articles-may-10-16-2021/
WHEN PAIRED WITH Smartia’s AI platform, Dialog Semiconductor’s SmartServer can coexist with existing operational or building management systems (BMS), enhancing both by creating a feedback loop that ties them together. Using Dialog Semiconductor’s IoT Access Protocol (IAP) open API, the SmartServer interfaces to the Smartia MAIO cloud platform using the MQTT protocol running over a 4G cellular radio link. Data calls and control signals are routed back to the PLCs in the chillers via Smartia’s VPN client, which runs on the SmartServer IoT.
Digitalization improves systems engineering, manufacturing automation: Manufacturers collaborate across disciplines with an integrated system that links product requirements, existing devices and components. Each change is instantly visible to everyone. Courtesy: Dassault Systèmes
On pages 6 and 7 are articles posted in May 2021, in case you missed something. Links are live in the digital edtion, at www.controleng.com/magazine.
Is your IoT network putting you at risk of cyberattack?, https://www.controleng.com/articles/is-your-iot-network-putting-you-at-risk-of-cyberattack/ Control Engineering Career and Salary Survey, 2021, https://www.controleng.com/articles/control-engineering-career-and-salary-survey-2021/ Career, salary survey 2021: Advice, https://www.controleng.com/articles/career-salary-survey-2021-advice/
How companies are winning top engineering candidates in a post-pandemic world, https://www.controleng.com/articles/how-companies-are-winning-top-engineering-candidates-in-a-post-pandemic-world/
Benefits of OT system management for cybersecurity plans, https://www.controleng.com/articles/benefits-of-ot-system-management-for-cybersecurity-plans/ Tank gauging systems increase safety, optimization, https://www.controleng.com/articles/tank-gauging-systems-increase-safety-optimization/ Securing smart manufacturing and workforce confidence, https://www.controleng.com/articles/securing-smart-manufacturing-and-workforce-confidence/ How single-pair Ethernet benefits IIoT architecture, https://www.controleng.com/articles/how-single-pair-ethernet-benefits-iiot-architecture/ Six steps for cyberattack incident response planning, https://www.controleng.com/articles/six-steps-for-cyberattack-incident-response-planning/
Turning “magic” material into versatile electronic devices, https://www.controleng.com/articles/turning-magic-material-into-versatile-electronic-devices/ 3D-printed jelly developed for biomedical, soft robotics, https://www.controleng.com/articles/3d-printed-jelly-developed-for-biomedical-soft-robotics/ National measurement system benefits for flow measurement, https://www.controleng.com/articles/national-measurement-system-benefits-for-flow-measurement/ Expanding the horizons of TSN technology, https://www.controleng.com/articles/expanding-the-horizons-of-tsn-technology/
Top 5 Control Engineering articles May 17-23, 2021, https://www.controleng.com/articles/top-5-control-engineering-articles-may-17-23-2021/
Secure networks connect controls, https://www.controleng.com/articles/deployment-of-secure-networks-connect-control-engineering-solutions/ AI-driven insights at the industrial edge (See image, caption, on page 6), https://www.controleng.com/articles/ai-driven-insights-at-the-industrial-edge/ Robotic finger uses tactile sensing to find buried items, https://www.controleng.com/articles/robotic-finger-uses-tactile-sensing-to-find-buried-items/ Six steps to an effective cybersecurity plan, https://www.controleng.com/articles/six-steps-to-an-effective-cybersecurity-plan/ Digitalization improves systems engineering, manufacturing automation (See image and caption above.) https://www.controleng.com/articles/digitalization-improves-systems-engineering-manufacturing-automation/
The importance of ICS security, https://www.controleng.com/articles/the-importance-of-ics-security/ Matching feed water pump designs with gas fired power plants advances, https://www.controleng.com/articles/matching-feed-water-pump-designs-with-gas-fired-power-plants-advances/ IIoT in the real world, https://www.controleng.com/articles/iiot-in-the-real-world/
Andra Keay,
Andra Keay, Silicon Valley RoboticsDon’t give up at hiring a diverse team for robotics and engineering companies. Get inspired.
‘Recruitment should reflect area demographics.’
hiring is the most overlooked aspect of company success. Hiring members of underrepresented groups offers economic and social value, but it’s not easy. Get inspired by seven tips to increase engineering workforce diversity.
Get rid of negative ideas that hold companies back. Do you think women are unavailable? Do you think women are not interested in the work, or are not as capable as the average white male? All evidence says the opposite. Although robotics is not a very diverse industry, over the last year, the Silicon Valley Robotics Online Job Fair averaged 33.3% female job applicants with 10% applicants of color, close to the goal of matching local demographics. Qualified, smart women apply where job descriptions, qualifications, recruitment and workplace culture are fixed.
apply if you’re asking for “rockstars” or “ninjas.” Timed technical interviews and personality tests are discredited and work to exclude underrepresented groups.
Showcasing the social and communicative aspects of a job are more likely to attract interest from a diverse group of applicants. It helps to reevaluate assumptions about position qualifications across the company. Diverse applicants have likely attended less well-known colleges, or had years in different work (parenting) or in adjacent industries. They have not followed the same career paths as the average white man. Don’t exclude them by searching the same ways.
Most have seen studies showing women tend to apply for jobs when they have 100% of the listed skills; men will apply when they tick 50% or fewer of the boxes. In interviews, women are asked to prove they have all the skills whereas men are accepted as showing potential. Interviewers need to refocus equally.
INSIGHTSM
Dispel the “pipeline” myth. Think instead about what prevents women from applying for positions at the same rate as men. What’s preventing them from progressing through the hiring process, and what prevents retention? Women leave the workplace at two to three times the rate of white men. Fix the recruitment process and company culture. An ideal recruitment pipeline should reflect area demographics. Measure and adjust each stage.
It’s not easy to hire and retain a diverse engineering workforce. Qualified, smart women in engineering are out there, which means that usually companies are the problem.
What are you doing to improve engineering workforce diversity?
See more on each tip and links for more about how to hire more women engineers. www.svrobo.org www.controleng.com/ system-integration/ workforce-development/ www.controleng.com/robotics Control Engineering Career and Salary Survey, 2021
Start with where you recruit: A company’s own “friends of friends” network is the single most useful hiring resource unless you’re looking for diversity. The same applies to alumni networks. Have you tried using affinity networks such as Women in Engineering, or women’s colleges? Have you asked women and underrepresented groups to apply in the job ad? Show awareness of diversity issues.
It also helps if the wording of ads is less biased towards men. Services like Textio can show how ad wording is perceived and how to make it more successful. Women are generally unlikely to
Inequality in assessment continues in the workplace, leading to women (and underrepresented minorities) being paid less and progressing more slowly up the career ladder. Women are pushed out of fast-track opportunities for various invalid reasons, and penalized in workplace assessments as not showing leadership material. Have you considered making pay bands and remuneration more transparent? Negotiations often has not favored women or minorities. Showcase a company culture that celebrates diversity, mentors and promotes diverse people to top positions.
The sooner a company addresses diversity, the easier it is to succeed. If you only have 10 people, then every new hire can make a significant difference to the demographic ratio and company culture. Once you have hundreds of staff, you’ve incurred a “diversity debt,” and culture will be difficult to change and companies may struggle with churn.
Don’t give up; get better. Diversity hiring provides increased innovation potential. Better hiring practices deliver a competitive market advantage. ce
Andra Keay is managing director, Silicon Valley Robotics, a CFE Media content partner. Edited by Mark T. Hoske, content manager, Control Engineering, CFE Media and Technology, mhoske@cfemedia.com.
EZ Remote IO leaves your PLC intact but reduces your IO cost to 1/3rd.
EZ connectivity to EtherNet/IP, Modbus TCP/IP
Easiest Drag-n-Drop Free Configuration Software
different I/O modules,
Analog, PWM, Thermocouple, RTD
Indoors & Outdoors, Sunlight readable, Intelligent marquee models to monitor PLC network tags including EtherNet/IP and DH+
EZ to add to any PLC/ Network No change in PLC program whatsoever!
#1 U.S. Supplier of LED
Nisha
Industrial entry management helps protect workers against COVID-19, other infectious diseases.
KEYWORDS: COVID-19, critical infrastructure, entry management
Entry management programs can reduce worker risk and streamline on-site operations. An entry management program helps companies formalize and standardize procedures, processes and tools that help secure staff.
ONLINE
www.controleng.com/ manufacturer-healthwellness.
CONSIDER THIS
How can your facility improve entry?
During periods of global uncertainty, industrial facility owners, managers and operations specialists must take steps to create a more protected and healthier workplace for employees, contractors and visitors. Digital technologies are helping with sensors, analytics, visualization and reporting. Industrial site professionals need effective solutions to prepare for occupant re-entry amid growing health concerns and changing regulatory requirements. Technologies for worker identity verification, contract tracing, real-time location tracking and other functions can help mange entry to industrial sites.
How can industrial organizations oversee the wellbeing of individuals entering and leaving their facilities? This includes industrial employees returning to work, contractors and visitors coming on site, engineering, procurement and construction (EPC) and expansion projects, production shutdowns and plant turnarounds. Without real-time entry enforcement capabilities, operators rely on manual efforts and processes, which are often time-consuming and may lead to increased health concerns and reputational risks.
According to the U.S. Center for Disease Control (CDC) recommendations, industrial facilities should consider developing and implementing a comprehensive screening and monitoring strategy aimed at preventing the introduction of infec-
Figure: A new breed of entry management “portal” can be used to establish a workflow process allowing for site pre-entry registration and efficient entry point screening.
Courtesy: Honeywell
Process Solutions
tious diseases into the plant or site. A new breed of entry management “portal” can be used to establish a workflow process allowing for site pre-entry registration and efficient entry point screening. The portal enables plant security staff to associate pre-arrival details with contact tracing and social distancing elements. These portable facilities are designed for fast and easy installation and can be deployed to meet specific site requirements.
Entry management portals combine industry-leading technologies to support a protected plant entry and help improve the owner’s business continuity, vigilance and response. Delivered pre-loaded with digitized workforce management software, the portal may be equipped to provide pre- and post-entry management, identity verification, digital badge holder issuance, social distancing/contract tracing, real-time location tracking, digital video surveillance, elevated body temperature measurement via thermal cameras and entry visualization and reporting.
Administrators benefit from a customizable approval workflow process and flexible request support for temporary or permanent site access. They can customize clearance procedures to address specific business or facility needs, check access rights, log recent activity and pending tasks with one system.
As part of deployment of the entry management portals, in stage one, mobile units can be stationed outside plant ingress/egress points to conduct entry verification and rapid testing as needed. During stage two, business continuity and response solutions can be leveraged to manage pre-entry and build a secure profile that automates identity and screening verification. Finally, in stage three, ultra-wideband digital badges are issued to registrants to track site capacity and contract tracing patterns in real time.
Benefits include rapid deployment, with minimal infrastructure requirements, efficient pre-entry workflow for individuals accessing the controlled zone, compliant and streamlined entry process reducing queuing and the loss of productive time, accurate onsite location tracking, social distancing and contact tracing capabilities and more confidence in providing a protected environment.
ce
Nisha Lathif, global marketing manager, Honeywell Process Solutions. Edited by Chris Vavra, web content manager, Control Engineering, CFE Media and Technology, cvavra@cfemedia.com.
www.beckhoff.com/power-supply
low heat loss ensures long lifespan and high reliability optimized convection cooling delivers high efficiency rating of up to 96.3% ideal for motion applications through high back EMF immunity universally deployable 24/48 V DC models in compact housings able to start demanding loads with short-term overload capacity of 150% usable in many industries with corresponding approvals
input #7 at www.controleng.com/information
Hale,
Manufacturing resilience in the COVID-19 pandemic is leading to the need for more cybersecurity.
It is becoming more important to talk about the booming levels of digitalization occurring in the manufacturing automation sector, and rightly so, the increased connectivity and the hike in efficiencies continue to grow at a huge rate.
When talking about those increased levels of connectivity, what often is understood and never talked about is how cybersecurity needs to be the backbone of the endeavor. Part of that sense of assurance comes from the resilient nature of the manufacturing enterprise, which has come to light in the COVID-19 era.
Another disruption, Tricoire said, is the world will become massively more electric. But it will be a different kind of electric.
“It is not the same electricity; it is about solar energy, decentralized microgrids, net-zero buildings, and electric vehicles,” he said. “By combining those two disruptions, the future will be smart and green.” To reach that level of sustainability, the industry has to grasp four elements to achieve a stronger environment.
Manufacturing has been resilient and strong during the COVID-19 pandemic.
“Think about the critical networks of our cities, the water networks, the electrical networks, think about the core chains of food, of pharmaceuticals, we were there to support the reliability and the continuity of service of those processes,” said Jean-Pascal Tricoire, chairman and chief executive of Schneider Electric during the Schneider Electric virtual Innovation Summit North America 2020. “And the one thing we have learned is that resilience comes from the automation of processes that can keep going locally without human intervention and that comes from digital monitoring of installations. If your installation is plugged in and if it’s under monitoring of analytics, of AI, then you are in a much better position to understand what is going on and prevent any breakdown. What we have learned also is that one is as resilient as the weakest point in their processes. Resilience is the sum of resiliency and actually is a multiplication of the resilience of the grid, of the power system, of the building system, of the IT system and of the process.”
Cybersecurity is an important, but not always talked about, aspect of manufacturing’s resiliency.
Digitalization is a transformative – and disruptive – part of how manufacturing is changing for the better.
See additional stories about resiliency and automation at www.controleng.com.
What steps are you taking to prepare for manufacturing’s future?
As we are adapting to this work from home environment, digitalization is growing by leaps and bounds and it is making it possible to collaborate remotely to increase agility and ensure operations continue to move forward.
Digital really started 30 years ago when the internet started to take off and it dramatically changed the way we live and work together, Tricoire said. We are now in the second phase of the digital revolution which is the Internet of Things (IoT) connecting us to machines and connecting machines to machines. Big Data and artificial intelligence are major innovations helping move the industry forward.
“We get there by massively leveraging digital efficiency; digital technology to reach a much better efficiency in every building and every city and every manufacturing facility,” Tricoire said. “As digital brings levels of efficiency to a much lower cost point, then we can increase the rate of retrofit in existing installations. The problem is with the existing stock of buildings and manufacturing facilities, we need to digitize the existing installations to make sure everything we do is much more efficient.”
The second element of the equation is circularity, he said. We have to develop a more circular economy, so we save on resources. The third point is everything will be massively more electrical, Tricoire said. In the next 20 years there will be a much larger investment in electricity. The final point, he added, is the electricity will not be the same, it will be green electricity.
“We are facing many crises at the moment,” Tricoire said. “Everybody is talking about COVID-19 and a recession and we are losing site that we are facing climate change. Climate change remains one of the big problems of our generation. We are the first generation to know about climate change, but we may be the last generation to be able to change the course of climate change because this phenomenon is accelerating and needs us to change the trajectory.”
If it isn’t already, digitalization will be the way of the world. It must be secure, and the companies that take advantage of the efficiencies and advantages will be able to achieve great dividends.
ce
Gregory Hale is the editor and founder of Industrial Safety and Security Source (ISSSource.com). This article originally appeared on ISSSource’s website. Edited by Chris Vavra, web content manager, Control Engineering, CFE Media and Technology, cvavra@cfemedia.com.
Robots have gotten quite good at identifying objects, as long as they’re out in the open. Discerning buried items in granular material like sand is a taller order. To do that, a robot would need fingers that were slender enough to penetrate the sand, mobile enough to wriggle free when sand grains jam, and sensitive enough to feel the detailed shape of the buried object.
MIT researchers have now designed a sharp-tipped robot finger equipped with tactile sensing to meet the challenge of identifying buried objects. In experiments, the aptly-named Digger Finger was able to dig through granular media such as sand and rice, and it correctly
For the Digger Finger, the researchers slimmed down their GelSight sensor in two main ways. First, they changed the shape to be a slender cylinder with a beveled tip. Next, they ditched two-thirds of the LED lights, using a combination of blue LEDs and colored fluorescent paint. “That saved a lot of complexity and space,” said co-researcher Nancy Ouyang, a PhD student at Harvard University. “That’s how we were able to get it into such a compact form.”
The final product featured a device whose tactile sensing membrane was about 2 square centimeters, similar to the tip of a finger.
The researchers say the robot might one day perform various subterranean duties, such as finding buried cables or disarming buried bombs.’
sensed the shapes of submerged items it encountered. The researchers say the robot might one day perform various subterranean duties, such as finding buried cables or disarming buried bombs.
Seeking to identify objects buried in granular material (sand, gravel, and other types of loosely packed particles) isn’t a brand new quest. Previously, researchers have used technologies that sense the subterranean from above, such as Ground Penetrating Radar or ultrasonic vibrations. But these techniques provide only a hazy view of submerged objects. They might struggle to differentiate rock from bone.
“So, the idea is to make a finger that has a good sense of touch and can distinguish between the various things it’s feeling,” said Edward Adelson, a professor of vision science at MIT’s Computer Science and Artificial Intelligence Laboratory (CSAIL). “That would be helpful if you’re trying to find and disable buried bombs, for example.” Making that idea a reality meant clearing a number of hurdles.
The team’s first challenge was a matter of form: The robotic finger had to be slender and sharp-tipped.
With size sorted out, the researchers turned their attention to motion, mounting the finger on a robot arm and digging through fine-grained sand and coarsegrained rice. Granular media have a tendency to jam when numerous particles become locked in place. That makes it difficult to penetrate. So, the team added vibration to the Digger Finger’s capabilities and put it through a battery of tests.
“We wanted to see how mechanical vibrations aid in digging deeper and getting through jams,” said Radhen Patel, a postdoc at CSAIL. “We ran the vibrating motor at different operating voltages, which changes the amplitude and frequency of the vibrations.” They found that rapid vibrations helped “fluidize” the media, clearing jams and allowing for deeper burrowing — though this fluidizing effect was harder to achieve in sand than in rice.
They also tested various twisting motions in both the rice and sand. Sometimes, grains of each type of media would get stuck between the DiggerFinger’s tactile membrane and the buried object it was trying to sense. When
this happened with rice, the trapped grains were large enough to completely obscure the shape of the object, though the occlusion could usually be cleared with a little robotic wiggling. Trapped sand was harder to clear, though the grains’ small size meant the Digger Finger could still sense the general contours of target object.
Adelson says the Digger Finger is part of a program extending the domains in which robotic touch can be used. Humans use their fingers amidst complex environments, whether fishing for a key in a pants pocket or feeling for a tumor during surgery. “As we get better at artificial touch, we want to be able to use it in situations when you’re surrounded by all kinds of distracting information,” Adelson said. “We want to be able to distinguish between the stuff that’s important and the stuff that’s not.” ce
Edited by Chris Vavra, web content manager, Control Engineering, CFE Media and Technology, cvavra@cfemedia.com.
Top 5 Control Engineering articles
May 17-23, 2021
Featured articles included the Career and Salary Survey, IIoT automation, retaining engineering employees, PLC-controlled robots and ac induction motor advice.
National measurement system benefits for flow measurement
Flow measurement accuracy in the energy sector makes traceability, supporting documentary standards and regulations vital.
3D-printed jelly developed for biomedical, soft robotics
3D-printable gels with improved and highly controlled properties could benefit biomedical and soft robotics applications.
Choosing between TAP and SPAN ports for an ICS cybersecurity solution
This may help security for aging networks.
‘
threats have never been higher, and it shows no signs of slowing anytime soon. The Department of Defense (DoD) is rolling out the Cybersecurity Maturity Model Certification (CMMC) to help standardize cybersecurity processes for defense contractors and DoD vendors. The CMMC model itself is created, managed and mandated by the Department of Defense (DoD).
purpose is to validate the security of the DoD’s 300,000 vendors throughout its supply chain and includes five levels of certifications. The CMMCAccreditation Board (CMMC-AB) establishes and oversees a qualified, trained and high-fidelity community of assessors that can deliver consistent and informative assessments to participating organizations against a defined set of controls and best practices within the CMMC program. CFE Media senior editor Gary Cohen talks with Ryan Heidorn about what this means for manufacturing.
As we continue to battle the pandemic, every organization has been affected in some form. We have adapted and changed how we do business, getting more creative. From home workstations to changing meetings, we have found solutions to problems and ways to implement new best practices in our firm moving forward.
Working in a remote environment has adjusted how we communicate and collaborate in myriad ways. A benefit has been the ability to more easily “right-seat” a junior staff member or a senior leader being mentored for a next role. We have easily brought employees to client, project, or operational meetings that might not have been feasible due to travel time and/or travel costs. It has become a simple to include an employee on the virtual meeting invitation and allow participation, providing a professional development opportunity. This includes asking a colleague to meet a new client, learn more about a project or task, shadow someone to understand how to facilitate a discussion, or learn the behind-the-scenes process of annual budgeting or proposals.
With a virtual setting, we are on an even playing field when sharing knowledge. Traditionally, sharing a lesson learned or best practice most commonly meant sharing with those that are physically nearby when experiencing that “aha” moment. With fewer people “nearby” anymore, it’s as easy to share a webinar or email or chat with one person as it is with 10, 50, or more people, helping the team. Technology documents the lesson so it is searchable.
Mentoring and coaching within the organization have certainly seen some change, but there are many silver linings. Employees have been able to interact with and learn from mentors even more in a virtual environment. At times, it could be difficult to track someone down while physically in the office, but now they can reach out with a call or a chat message at any time of day because that is now how we track down others. Mentors have also made a point to schedule regular check-ins, making them more consistent and meaningful in fostering the growth and development of less experienced employees.
growing need for a variety of expertise has allowed us to become more unified and put a variety of skills to use. The virtual environment has made the ability to share knowledge across disciplines more accessible.
management director at Dewberry, a
content partner.
Get the most digitally: Since February, Control Engineering has included an online index in the table of contents, including, digitization, DCS migration, and AI edge computing. See 4 tips below.
Control Engineering articles in print often are longer online. Some articles won’t fit on paper, including articles on design tools and digitalization, distributed control system (DCS) migration, and a case study on artificial intelligence (AI) in edge computing. Below, also see four tips for getting the most from the Control Engineering digital edition.
Digitalizationofsystems engineering helps transform existing processes and restructure for automation, increase product connectivity, meet new rules and regulations and optimize operations for uncertainties. Mark TenEyck is director of sales, Catia, Dassault Systèmes and president, International Council on Systems Engineering, Los Angeles chapter.
ers can be leveraged create a uniform fabric of data and automation that ties together control systems, Internet of Things (IoT) devices and artificial intelligence (AI) engines. Case study shows up to 30% reduction in maintenance and call out costs and as much as 30% energy savings. Dialog Semiconductor article is edited by Chris Vavra, web content manager, Control Engineering, CFE Media and Technology.
3010 Highland Parkway, Suite 325, Downers Grove, IL 60515. 630-571-4070, Fax 630-214-4504
Mark T. Hoske, Content Manager 630-571-4070, x2227, MHoske@CFEMedia.com
Jack Smith, Content Manager 630-571-4070, x2230, JSmith@CFEMedia.com
Kevin Parker, Senior Contributing Editor, IIoT, OGE 630-571-4070, x2228, KParker@CFEMedia.com
Emily Guenther, Director of Interactive Media 630-571-4070, x2229, eguenther@CFEMedia.com
Amanda Pelliccione, Director of Research 978-302-3463, APelliccione@CFEMedia.com
Gary Cohen, Senior Editor GCohen@CFEMedia.com
Chris Vavra, Web Content Manager CVavra@CFEMedia.com
Suzanne Gill, Control Engineering Europe suzanne.gill@imlgroup.co.uk
Ekaterina Kosareva, Control Engineering Russia ekaterina.kosareva@fsmedia.ru
Agata Abramczyk, Control Engineering Poland agata.abramczyk@trademedia.pl
Lukáš Smelík, Control Engineering Czech Republic lukas.smelik@trademedia.cz
Aileen Jin, Control Engineering China aileenjin@cechina.cn
Mark T. Hoske, Content ManagerDownload an Adobe PDF version of the issue or article, and the digital edition software bookmarks, highlights, searches, scrolls and zooms.
1. Headlines link to online versions of the article that often contain more images, graphics and text, with contain live links to relate resources. See ONLINE side text in the article to learn more.
To help with upgrades to legacy DCS, Control Engineering offered a March 24 webcast for professional development hour (PDH) credit, “Effective process control system migration.” More information follows, along with a link to webcast, archived for one year. Lynn Njaa is business development manager, DCSNext process automation consultant, at Maverick Technologies, a CFE Media content partner.
AI-driven insights at the industrial edge Edge technology such as smart serv-
More fits online than between the front and back covers.
Paper’s nice but can it do this?
www.controleng.com/magazine
®
2. Table of contents since February has included more than a page of online links. Browse the newsletters, learning resources and articles and click into what you didn’t know you needed.
3. Reader studies show affinity for the advertising pages in Control Engineering as much as the articles. Click into live links in the ads and in the ad index (in back) to see, learn, get specifications, and place an order.
4. Next to the cover, see related resources after clicking into the digital edition from the email subscribers receive or at www.controleng.com/magazine. May Control Engineering digital edition also has eBook article collections on PLCs, Digital Transformation, System Integration, and IIoT Cloud, as well as a link to the Industrial Cybersecurity Pulse site and Oil & Gas Engineering supplement and useful cover story on adventures in self-service analytics.
Think again: Control Engineering is more than what’s between the cover and back page.
ce
www.controleng.com/EAB
Doug Bell, president, InterConnecting Automation, www.interconnectingautomation.com
David Bishop, chairman and a founder Matrix Technologies, www.matrixti.com
Daniel E. Capano, senior project manager, Gannett Fleming Engineers and Architects, www.gannettfleming.com
Frank Lamb, founder and owner Automation Consulting LLC, www.automationllc.com
Joe Martin, president and founder Martin Control Systems, www.martincsi.com
Rick Pierro, president and co-founder
Superior Controls, www.superiorcontrols.com
Mark Voigtmann, partner, automation practice lead Faegre Baker Daniels, www.FaegreBD.com
Content For Engineers. That’s what CFE Media stands for, and what CFE Media is all about –engineers sharing with their peers. We welcome content submissions for all interested parties in engineering. We will use those materials online, on our website, in print and in newsletters to keep engineers informed about the products, solutions and industry trends.
www.controleng.com/contribute explains how to submit press releases, products, images, feature articles, case studies, white papers, and other media.
* Content should focus on helping engineers solve problems. Articles that are commercial or are critical of other products or organizations will be rejected.
(Technology discussions and comparative tables may be accepted if non-promotional and if contributor corroborates information with sources cited.)
* If the content meets criteria noted in guidelines, expect to see it first on our Websites. Content for our e-newsletters comes from content already available on our Websites. All content for print also will be online. All content that appears in our print magazines will appear as space permits, and we will indicate in print if more content from that article is available online.
* Deadlines for feature articles for the print magazines are at least two months in advance of the publication date. It is best to discuss all feature articles with the appropriate content manager prior to submission.
Learn more at: www.controleng.com/contribute
If you’re a system integrator with demonstrable industry success, Control Engineering and Plant Engineering urge you to enter the 2022 System Integrator of the Year competition.
Past System Integrator of the Year winners—Class of 2021, Class of 2020, and Class of 2019—are not eligible to enter the 2022 System Integrator of the Year program.
The chosen System Integrator of the Year winners will receive worldwide recognition from Control Engineering and Plant Engineering The winners also will be featured as the cover story of the Global System Integrator Report, distributed in December 2021.
Control Engineering and Plant Engineering’s panel of judges will conscientiously evaluate all entries. Three general criteria will be considered for the selection of the System Integrator of the Year:
Business skills
Technical competence
Customer satisfaction
Reasons for calibration
scheduled
Manufacturingprocessesrequire hundreds of incredibly precise devices to keep operations running reliably. To keep these devices running ceaselessly and up to specifications, they require regular inspections, repairs, and calibration. Whether it’s the timing, flow, temperature, or pressure that needs to be calibrated, these products are often sent to a calibration lab, or a calibration engineer is brought into the plant to recalibrate the asset.
There are a variety of reasons to calibrate an asset; those often include:
• New instruments installation
• Repair or modification
• Scheduled calibration
or modifications
on preventive
• Ensure accuracy
• Ensure smooth functioning equipment
• Stabilize after exposure to adverse conditions
• Environmental changes (such as weather).
To minimize plant downtime, here are six things automation and control engineers need to know about calibration.
For the same reasons electrical assets are checked during a preventive maintenance route, a few areas of instrumentation assets need checking because they can make the item seem to be uncalibrated. Sometimes when a product seems to be running a bit off, it’s because it needs to be cleaned or maintained. Check the fans and filters. Depending on the machine, they need to be cleaned monthly or quarterly.
Allowing these parts to collect dirt and dust can stop an asset from being able to perform within its designated specifications. So, for example, a part may still be perfectly calibrated, but the fan isn’t cooling it enough to run at peak performance.
Calibrations are often certified for a certain amount of time, but the product’s accuracy can decline after that date. It’s important to follow the schedule the calibration lab sets up for each product.
When sending equipment to a calibration lab, send it early whenever possible. Calibration labs get busy, things can get backed up and shipping times can be unpredictable. The best way to ensure a product is calibrated and back on the line in time to stop any plant delays is to get it sent in early.
The calibration schedule usually depends on:
• Type of instrument
• How the instrument is used
How often the instrument is used
The environment it’s used in
Level of accuracy needed.
When sending in a product for calibration, or bringing a calibration engineer into a plant, provide information about the product. If it’s being calibrated because accuracy is declining or something isn’t working correctly, inform the lab of what issues are present. Include information about the decline and how long the issue has been present.
Context, in addition to how the product is used, can help inform what tests are done to ensure the product’s accuracy.
It also can be helpful to inform the lab of how the test engineers use the equipment. Not every application is used as expected and sharing pertinent information with the calibration lab will ensure better services and optimal performance of the test hardware.
Product calibrations aren’t guarantees everything is perfect. A calibration lab has specific specifications to test on each product to calibrate it. That means the calibration is tested per the manufacturer’s specifications and not at each test point possible.
If the product is used at the ends of its uncertainties, then the basic manufacturer suggested calibration may not be enough. Ask for a specific calibration point based on how the product is used. That will offer high confidence the calibration is accurate for the application’s needs.
Giving the calibration engineer details and a place from which to start the test will help mitigate the uncertainties around the tests the plant is using a product for.
If the product is shipped out for calibration, run a few sanity checks when it returns to ensure it wasn’t damaged during transportation from the calibration lab.
Packages get dropped or treated roughly sometimes, which can interfere with calibration. It’s important to ensure everything is working accurately before using the device in the production line again.
If an issue is observed or it doesn’t seem to be properly calibrated, this provides an opportunity to speak with the lab before further problems are created.
Measurement system analysis (MSA) is a great way to figure out if there is an issue. MSA is a method of determining the variation within a measurement process.
The Fluke Calibration 8558A 8.5-digit multimeter offers 5 megasamples-per-second high resolution digitizing for system automation in labs and manufacturing test environments.
Thismathematicalmethodcan be used to certify the measurements and controls being used by evaluating accuracy, precision, and stability. Whether to ensure an instrument is calibrated when it returns from the lab, or before sending it out, recognize if an asset is properly calibrated. If an emergency happens, it offers test engineers a chance to understand what’s going on before sending to a calibration lab.
Understanding and knowing how to perform MSA creates a chance for engineers to have better control of the products, leading to better results down the line. ce
Jorge Mas Roman is an electrical and RF sales engineer for Fluke Calibration. Edited by Mark T. Hoske, content manager, Control Engineering, CFE Media and Technology, mhoske@cfemedia.com.
Instrumentation calibration may be needed at installation, modification, scheduled intervals, environmental factors and other reasons.
Automation and controls engineers should consider preventive and predictive maintenance when considering instrumentation calibration.
Instrumentation documentation helps ensure calibration is performed appropriately.
CONSIDER THIS Does plant uptime and product quality require more attention to instrumentation calibration?
ONLINE www.controleng.com/ process-manufacturing/ diagnostics-asset-management/
ANSWERSM
‘Basic manufacturer calibration may not be enough. Ask for a specific calibration point based on how the product is used, so the calibration fits the application’s needs.’
skill levels,
Whendesigninghardwareand software for human-machine interface (HMI) and supervisory control and data acquisition (SCADA), there’s a lot more to it than just the basics. Understanding the core principles and pertinent standards are crucial, but there are many related factors that should also be considered. These include a company’s standards, user abilities, skill levels, process needs, future plans and integration with other systems. If a company’s planning involves looking at the bigger picture, a finished product will be the better for it. Several best practices can help.
An important first step is to identify your own company’s standards. Industry or regulatory standards are important, but companies can realize benefits from having their own standards as well.
“Companies looking at improving their systems should think about identifying internal standards,”
stakeholders, and other
advice and seven SCADA
said Kent Melville, application engineering manager for Inductive Automation, maker of the Ignition industrial application platform. “If organizations take the time to define their own standards, they’ll ensure they’re using the protocols they really want to put in place, the type of hardware they want to put in place, and so on.”
Having company standards makes it easier for an organization to stick to its plans and not be swayed into bad decisions. Melville said it can be difficult to maintain standards sometimes, because a lot of work gets done through vendors. Installing proprietary equipment and software can make it cost-prohibitive for companies to make changes later on. And because different proprietary systems don’t talk to each other, companies don’t always know how things will be affected if a change is needed.
“People really need to take ownership of their systems, and not let things be dictated by vendors,” said Melville. “To maintain your own standards for PLCs, protocols, data structures, and more, it often comes down to two options. One, you can pick a proprietary solution, where the manufacturer provides everything. Or you can work with companies that support open standards. With this open approach, even if you’re talking about different companies, all their products communicate with each other and work well together.”
If working with a system integrator, clarifying standards up front will make the overall goals easier to understand. “We’ve seen the full spectrum of standards,” said Davin McDougall, business unit leader for Brock Solutions, an integrator that’s implemented projects around the world in a variety of industries. “We’ve seen no standards, poor standards — which can be worse than no standards — all the way up to world-class standards. When you get the standards right, we refer to them as ‘accel-
Working with open standards provides a lot more control of the process.
erators.’ Everyone wants to embrace and invest in accelerators, because they’ll help things go faster.”
McDougall described a project in which standards played a key role and greatly benefitted the customer. “Their operating model relies on the implementation of practical and effective standards throughout their organization,” he said. “Within the controls, for instance, you’ll find standard add-on instructions, user-defined data types, tag naming conventions, program structures, and a list of general setup parameters. They’ve standardized on hardware and infrastructure as well, albeit with a combination of vendors, for best in-class solutions. Within the SCADA domain, HMI templates, connectivity, screen headers/footers, general navigation, fonts, and font sizes are all standardized. So no matter where you are within the enterprise, a single-speed motor is controlled the same way, by the same code, and looks the same to the operator. And for the maintenance tech, troubleshooting a faulted single-speed motor is the same process anywhere in the enterprise.”
When considering process needs, it’s important to look beyond the specific line or whatever else a project might be focused on. It’s best to see it holistically. “When putting controls in place, it’s really good to take a page out of IT’s book,” Melville said. “IT puts a lot of emphasis on requirements-gathering and making sure all stakeholders are involved. The stakeholders would include anyone affected by the project — operators, integrators, supervisors, the IT team that must support it, and C-level executives who want to see metrics. Everyone with a stake in the process should be involved in defining the requirements. However, you need to give the proper weight to each group’s input. For example, the operator who uses the system every day should have significant weight in the discussion.”
McDougall also sees great value in getting input from stakeholders. “I think it’s important to have stakeholder engagement throughout the project,” he said. “All stakeholders need to be involved when it comes to requirements-gathering, designing, building, testing, commissioning, and sustaining these projects. And ‘all stakeholders’ often includes engineering, IT,
Consider the needs of all stakeholders before designing for HMI/ SCADA.
quality, maintenance, operations, finance, and partners like the systems integrator and technology vendors. As soon as you forget a stakeholder, the risk profile on the project goes up significantly.”
Questions to ask yourself also include: How will people interact with this system? And what’s their experience level?
“On the plant floor, it’s usually about the operator who’s seeing the system on a fixed screen, and they need the info quickly,” Melville said. “And it might be a guy who’s been doing this work for 20 years. That person’s going to need something that’s familiar. If the new system is too different from what he’s used to, he may not learn it properly, or he may become frustrated. You’re walking a fine line, because you want to use new technologies, but you don’t want things to be so different that they alienate people.”
Also, companies need to look at the variety of “user stories” within the organization. “For the operator who needs to quickly identify whether something is running within parameters or not, you’re probably wanting to use high-performance graphics,” Melville said. “With that approach, things running normally are in grayscale, and you’re using brighter colors for things that demand immediate attention, to show things that are out of spec. And you also have to think about the operator’s capabilities, and what the job allows him or her to do. In other words, how much time does he or she have to study these SCADA screens? That’s a factor that should be considered. For supervisors or C-level people on the business side, the user story is different. There, people aren’t necessarily limited to just a quick glance. They can take the time to analyze the data in some depth, so they can make decisions from the information. It can be more complex and have more detail than what the plant-floor operator might need. So every group is different, and if you only design things for one stakeholder, you won’t end up giving everyone what they need.”
Company standards help with SCADA design. Consider mobile-responsive HMI and SCADA designs to integrate with needed systems.
Ask seven SCADA system integration/design questions.
Are your SCADA designs optimized in a standard designed to meet agreeupon needs?
ONLINE
www.controleng.com/ info-management/hmi-oi/
Different displays and sets of data should be provided to different groups of users.
Melville also said companies may want to employ mobile-responsive design. For example, executives may want to see data on a mobile device. It’s harder to adapt a desktop design to a mobile device than it is to design for a mobile device first. If you need to design HMI for mobile, it’s best to know that in advance.
“And in general, when you’re looking at your user interface, you want things to be intuitive, and you want to be able to move fast,” Melville said. “Try to avoid using ‘tips,’ keyboard shortcuts, right-clicking on certain parts of the screen, and things like that. You don’t want hidden functionality. You want people to be able to learn it quickly. And if you use hidden functionality, it can become tribal knowledge, and new people aren’t going to know about it. And as people retire, the knowledge is lost.”
Think about how the system needs to be integrated with other systems. If the company is using open standards, integration is much easier. If you’re pushing data to the cloud, or doing a report for a government agency, you can do that because your data is centralized. You want a system where it all works together, and data can be shared. A big part of keeping things open is having real-time data. It’s really helpful to use modern tools and techniques, like application program interfaces (APIs,) OPC UA, and storing into an open database format that can be queried.
The ability to easily access data will also help with the relationship between operational technology (OT) and information technology (IT). As IT sees modern scalable approaches to OT problems, it can be easier to get funding to maintain standards, because they see it benefits the entire organization. Companies can do more initiatives with IT involved. IT can be the champion, and get corporate budgets for projects, rather than working within constrained OT budgets.
As part of the discussion around integrating with other systems, you need to ask:
Operators’ experience and skill levels should be factored into the equation.
1. Who will need this data?
2. From where do they need to access it?
3. Are things read-only or read-write?
4. Do you need a demilitarized zone (DMZ) to enhance cybersecurity?
5. Are people using a virtual private network (VPN)?
6. Do you need to avoid sharing data externally because you’re in a regulated industry?
7. Is your mobile app something that can be used from anywhere, or can people only use it if they’re connected to the local Wi-Fi network at the plant?
When creating an organization’s standards, companies can’t expect them to be applicable in the same form 10 years from now. Technology changes rapidly, so companies need to evolve with those changes.
“It’s a good idea to establish a group of stakeholders that meet regularly to discuss standards,” Melville said. “The group should meet at least once a year to review its standards, and make changes as needed. And of course, changes can be costly, so your team needs to study needs and possibilities. Put some real thought into it to arrive at the best course of action. Picking technologies that will be supported long-term, will result in fewer changes to be made in the future.”
Having that big-picture view, and working within standards, can lead to more successful projects. “Having a clear set of company standards saves time on future projects,” Melville said. “It prevents you from having to re-invent the wheel every time. You can hit the ground running on new projects because you have a solid foundation in place.” ce
Jim Meyers is communications manager at Inductive Automation. Edited by Mark T. Hoske, content manager, Control Engineering, CFE Media and Technology, mhoske@cfemedia.com.
Advances in Industrial Internet of Things (IIoT) technologies and software
give plant managers
into assets’ health and performance.
Traditional asset monitoring is about to undergo a major overhaul. Advances in Industrial Internet of Things (IIoT) technologies and software analytics are empowering plant managers with valuable insights into the health and performance of their most critical assets. Software applications can assist with reducing emissions and energy losses in a facility by tracking the energy consumption of applicable assets and alerting personnel as needed.
In fired systems, like steam lines and heat exchangers, better energy management would mean decreasing steam loss events and inefficiencies caused by fouling. Release events of pressure relief valves (PRVs) can be tracked and recorded, so operators know when an event occurred and for how long. In the past, traditional wired monitoring methods made tracking the health and performance of these assets expensive. Now, wireless instrumentation combined with easyto-deploy software analytics, user-friendly applications and specialty dashboards enable plant managers
to track energy-intensive assets while reducing costs, emissions and wasted production time.
Many industries depend on steam systems to power their processes, from energy to chemical processing to food and beverage, and, therefore, saving energy in every possible way is an integral part of maximizing process and profits. Certain assets that require a lot of fuel to operate are culprits of such inefficiencies and waste. When steam is wasted due to a failed steam trap, not only is energy lost, but heating fuel is wasted, and product quality may be impacted. Real-time asset monitoring offers the insight to reduce the energy costs associated with operating such systems and in turn is a significant piece of the optimization puzzle.
Other assets, like heat exchangers, become less efficient over time due to the build-up of deposits on the heat exchange surface, a condition called fouling. When this happens, the unit needs to be cleaned and serviced to restore full performance, but in the meantime, the downtime requires time and more energy to properly transfer heat. Traditional asset monitoring practices cannot identify how much energy is wasted before the next planned maintenance occurs. Nor can they determine how inefficiencies affect production capacity before an operator is alerted.
Legacy monitoring systems required expensive wiring and infrastructure to enable each connected device, and installation often required a full shutdown because the instrument had to be inserted into the process line. These demands resulted in the upfront installation costs of wired monitoring systems often outweighing the potential savings. This was especially true for assets in harder-to-reach or outlying locations.
Modern wireless solutions do not require these expensive upfront investments in infrastructure or shutdowns for installation. Wireless measurement devices offer non-intrusive, external mounting without compromising the data delivered. Wireless acoustic transmitters, for example, use a thermocouple and
an ultrasonic sensor to take acoustic and temperature measurements, which can be analyzed to determine the state steam traps and pressure relief valves.
Raw data, from an analytical perspective, is only as useful as our ability to understand and interpret it. Industrial analytics software, like the one referenced in Figure 1, can be installed and connected to WirelessHART gateways to interpret process data. [WirelessHART is a FieldComm protocol.] This allows users instant and continuous access to information on assets that might normally be inspected by a manual operator. User-friendly applications within these software platforms collect and compile real-time data and visualize it into straightforward graphs with an expandable view that makes it possible to drill down to each asset. As the adoption of this type of wireless monitoring grows, so too will the applications provided by software developers. Each new use case can encourage the development of a new modular software application that can be added to the dashboard, showing the status of critical and secondary processes.
Several applications exemplify the easy-to-use data visualization of potential energy losses and emissions in a connected plant environment.
Some of the most critical assets within a pressurized system are pressure relief valves. They protect process and equipment by releasing pressurized flow from a system when the pressure reaches a certain set point. Useful for preventing process upsets and equipment failure, these valves are another asset that is often monitored manually or inefficiently due to the high costs of wiring sensors to their remote locations.
Leaking and releasing valves waste product and can limit production by not allowing the process to run at its optimum pressure. Many plants have several pressure relief devices that vent to one common flare system, which goes directly into the atmosphere. If multiple relief valves vent to one common flare, it’s difficult to know how many of them are in a release state. How is it possible to measure that energy and emissions loss?
Wireless acoustic solutions enable continuous, realtime monitoring of critical PRVs. The data is sent to the software application, which will alert operators to leaks and malfunctions. Built-in sustainability algorithms track energy consumption and emissions and allow plant managers to compare data against performance benchmarks and goals.
Primary purpose of steam traps is capturing condensate in steam lines. Steam lines have many uses, but are primarily used to heat a process or power equipment. A failed trap releases steam to the atmosphere, wasting energy and degrading product quality.
Adding non-intrusive wireless sensing devices
Figure 2: Determine the online health status of a steam trap by verifying if a trap is in failure mode by viewing trends and emissions and energy loss on a per trap basis while tracking impact against key performance objectives.
to each steam trap gives operators a view into their steam system and can alert them if any traps are in a blow-through or cold state. Software applications can show operators the total lost energy costs from leaking steam traps and calculate emissions for recording and reporting. Failed steam traps energy losses can add up and cost millions of dollars a year depending on the number of steam traps in a facility. Unknowingly exceeding emissions standards also can mean paying fines. Manual checks are imprecise, and third-party services can be expensive.
Pervasive sensing applications alleviate, steam trap blind spots. An application can compile data, variables and settings into a dashboard. This increased awareness means operators can find and repair or replace failed traps extensive losses.
Heat exchangers transfer heat from heating fluid to process fluid. With continuous monitoring on heat exchangers, data is put to the best possible use. A simple software dashboard has all the data intelligence needed to make sure maintenance resources aren’t wasted servicing heat exchangers that do not require maintenance and catch the ones that do before fouling results in unplanned production losses. Cutting production costs like this can save millions of dollars in a typical, medium-sized refinery. Lost energy costs are built into the software analytics for heat exchangers, so it’s clear how much energy is being spent on heat exchangers in a critical state. ce
Logan Woolery is part of Emerson’s Digital Transformation business and has product management responsibility for the Plantweb Insight analytics software. Edited by Mark T. Hoske, content manager, Control Engineering, CFE Media and Technology, mhoske@cfemedia.com.
KEYWORDS: HMI, dashboard, asset management, IIoT Poorly managed plant emissions and energy applications can result in inefficiencies and increased energy costs. Non-intrusive wireless technology for improved asset monitoring capability. Easy-to-use industrial data visualization helps asset management in the Industrial Internet of Things era.
Change the future: Can you see what industrial assets are about to fail and avoid that beforehand?
More about Industrial emissions, regulatory future www.controleng.com/ iiot-industrie-4-0/ asset-management/
Don’t let early success with operational technology (OT) connectivity stall technology innovations now for Industrial Internet of Things (IIoT) and industrial digital transformation (DX). Advanced process control system designs incorporate interoperability, modularity, standards, scalability and portability.
Starting 40-plus years ago, with the world’s first distributed control system (DCS), process automation systems have consisted of self-contained control and visualization components. Supervisory control and data acquisition (SCADA) systems often were used for assets such as pipeline systems and wellheads.
Both architectures collect data from process instruments and respond by sending actions to actuators, and both can control multiple loops simultaneously to handle complex processes. As programmable logic controllers (PLCs) gained sophistication, they also began to serve as small-scale controllers.
Early on, operators had to reside in a centralized control room or command center because humanmachine interfaces (HMIs) did not support remote access. Any information provided to personnel other than operators was delivered via reports, which often had a significant time lag.
Over time, proprietary hardware and software gave way to commercial off-the-shelf (COTS) equipment, primarily PCs, providing new mechanisms for industrial connectivity. With that connectivity, process automation systems could interface with corporate networks at the facility, extending to the Internet. Data access and even actual control from any location became possible. Isolated DCS or SCADA systems (Figure 1 left) became part of a larger real-time network (Figure 1 right), which could eventually connect to anything. This helps provide a contextual framework for considering what comes next.
Forward-looking companies concerned about implementing industrial DX strategies must consider
Figure 1: Early process control systems (left) were isolated and built on proprietary equipment. Once they were connected to much larger networks (right), they became more complex and gained broad capabilities. Starting 40-plus years ago when Yokogawa introduced the world’s first distributed control system (DCS), process automation systems have consisted of self-contained control and visualization components.
Courtesy: Yokogawa
Traditional distributed control system and supervisory control and data acquisition system designs can be improved with industrial digital transformation.
Figure 2: With the growth of DX, and convergence of IT and OT, the traditional Purdue Model layers are becoming far less distinct. Open platforms can support both DCS and SCADA environments. Courtesy: Yokogawa
how their DCS and SCADA platforms fit into the larger picture. What will these systems look like to perform their traditional functions in a more complex environment where the layers of the automation pyramid are blurring (Figure 2) and losing distinctiveness?
With IT and OT convergence and virtualization technologies, many engineering and software applications are moving to the cloud. Integrating cloud technologies allows process control systems to perform edge computing and serve as data sources for the IIoT. Cloud-based environments can integrate data from multiple sources and improve data availability to support analytics and decision making. Taking advantage of cloud-based environments, IIoT, and edge computing requires process manufacturers to modernize aging DCS and SCADA platforms. A DX benefit is a more open and secure system architecture and design.
NAMUR Open Architecture (NOA) and Open Process Automation Forum (OPAF) are driving open architecture initiatives (Figure 3) in industrial automation by moving away from proprietary architectures. Both describe how vendor-neutral systems can use state-of-the-art equipment and functions, avoiding vendor lock-in. Key concepts of OPAF include interoperability, modularity, conformity to standards, compliance with security standards, scalability and portability. Within NOA, an independent domain called monitoring and optimization (M+O) is prepared separately from the existing system. It collects data directly from robots and drones as well as new sensors for corrosion, sound, vibration and other maintenance-related variables. Data in the existing system is imported via OPC UA so advanced control, analytics and diagnostics can be realized in the field.
DCS and SCADA systems, driven by DX developments, are changing and evolving and the journey is only starting. This presents challenges to process manufacturers, especially when considering a diffi-
cult decision to launch a major system upgrade. No manufacturer should be satisfied with the idea of the same capabilities running on newer hardware.
Any new system will be more modular, allowing sections to be upgraded or replaced as necessary when new capabilities are added. This is only a start. Industrial automation will add capabilities that can only be imagined now. A DCS will have selflearning abilities to better understand the processes under its control. It will develop the ability to execute complex control functions such as procedures (startup, grade change, etc.) automatically with minimal, or even no, operator intervention. Plants will reduce accidents and downtime resulting from human errors while achieving optimal operation.
Greater system connectivity will support integrated operations centers, along with dynamic operator guidance facilitated by high-quality alarm systems. These developments will help manufacturers achieve new, higher levels of system optimization and safety. Dynamic digital twin simulators allows operators and managers to evaluate changes to operating conditions by predicting process behaviors in advance.
These capabilities will use open systems to support IIoT and cloud-based operations—including OPC UA and message queuing telemetry transport (MQTT)—along with other IT connectivity protocols, such as simple network management protocol (SNMP) and internet control message protocol (ICMP).
ce
Kevin Finnan is a digital transformation and industry marketing consultant at Yokogawa Corporation of America. Wataru Nakagawa is a system product content marketing manager for Yokogawa Electric Corp. Edited by Mark T. Hoske, content manager, Control Engineering , CFE Media and Technology, mhoske@cfemedia.com.
KEYWORDS: Process control system, industrial digital transformation Commercial technologies help industrial operations
IT, OT, virtualization, cloud for IIoT Modernizing industrial control systems with open architectures
Are you overlooking industrial digital transformation innovations because “we’ve already done that”?
This article online has more on industrial control security, project help. www.controleng.com/ info-management/hmi-oi/
‘A DCS will learn processes under its control.’
Industrial Internet of Things (IIoT) relies on fast and accurate communications. Critical control systems cannot afford a momentary power interruption that could cause an industrial PC or controller to crash. Uninterruptible power supplies (UPSs) can add reliability. Knowing UPS basics helps when matching a UPS to an application.
What types of loads will the UPS be powering – ac or dc? Legacy systems tend to run on ac power, so retrofits of old systems will likely require ac power, as well. In the past 20 years, the growth of the industrial PC (IPC) market has shifted to dc power sources. Consider the power and runtime requirements. Realistically calculate the proper UPS sizing and establish realistic expectations.
If a sustained power failure occurs, the UPS ensures a safe and orderly shutdown of the control platform to avoid data loss, system crashes or malfunctions. When designing the system, select a battery sized to allow for some runtime before the PC is told to shut off or if the main power feed is returned in a reasonable time. Oversized battery systems can take a long time to recharge.
Most UPS manufacturers use a few industrystandardized types. Some manufacturers will only offer one type of technology, such as valve regulated lead acid (VRLA). Others will offer a variety, such as VRLA, wide-temperature VRLA and lithium iron phosphate (Li-ion). Different batter-
ies differ in performance and usable service life.
Ideally, a UPS will offer multiple points of health into the battery system, so operators can take preventive measures before the battery fails. Look at how the UPS communicates data; most use LEDs, and a few provide dry contact outputs with a fixed threshold point. Newer UPS systems provide these and integrate data into the control platform communicating over industrial Ethernet protocols.
In control systems that operate on ac voltage, an ac UPS makes the most sense. Offline and standby topology are inexpensive and are the most common ac UPSs. Under normal conditions, an offline UPS passes the mains power from the input to the output without interaction other than the battery charging circuit in parallel to the mains circuit. If the mains power fails, the UPS will switch from the mains circuit to the battery circuit. The transfer time from when the UPS loses mains until it produces battery power cannot exceed 10 milliseconds (ms). The 10 ms transfer usually does not affect downstream devices, but protects systems sensitive to voltage fluctuations.
There are two subsets of ac UPS: modified (simulated) sine-wave output devices and pure sine-wave output devices. Each generates ac output differently.
Modified sine-wave devices take voltage from the battery bank and, in the simplest form, try to create a rough likeness to a sinusoidal wave. While this type of UPS is relatively low cost, it comes with some disadvantages. The massive steps in voltage can damage the input circuits of the downstream devices. These massive steps also create a high number of switching transients from the UPS’ output. This can lead to premature failure of small PC and PLC power supplies.
Figure 1: With the widespread implementation of IIoT and big data in industrial applications, reliable power is more important than ever. Choosing the right UPS system for an application can prevent the problems and costs that a power interruption can cause. Images courtesy: Phoenix Contact
A pure sine-wave UPS produces the same sinusoidal waveform output that would replicate the waveform from the 120/230 V mains power feed. The pure sine-wave UPS is the better choice for sensitive control equipment like programmable logic controllers (PLCs), distributed control systems (DCSs) and IPCs. More circuitry is needed, but control devices powered by a UPS last longer, lowering total cost of ownership.
Mission-critical applications require a more advanced UPS, known as double conversion or online UPS. Such a UPS is never in standby mode. The battery circuit is actively connected to the system. If the mains power feed is interrupted, there is no interrup-
Critical control systems need uninterruptible power supplies (UPS) to prevent momentary power interruptions that may cause a controller crash. Choose wisely.
tion or voltage sag on the output, resulting in seamless battery operation. The online system has a built-in level of filtration and regulation. During normal operation, it converts incoming power from ac to dc and back with an inverter. Isolation protects against voltage fluctuations and minor input power disturbances. These have a higher price tag and larger housing.
The drawback of an ac UPS is everything downstream is ac-powered and relies on that UPS. A control cabinet application might require a very large ac UPS to power all downstream devices. If the ac UPS fails, so will the downstream devices. A distributed dc UPS can save cost and space. Most control cabinets are based on dc voltage. An ac UPS backs up and supports everything at the point of entry. With a dc UPS, the backup occurs after the ac/dc power supply.
Loads can be split into buffered and unbuffered loads. The unbuffered loads are the devices that can lose powe r during a loss of mains voltage and not cause a system failure. The ac/dc power supply can directly power these loads. The dc UPS would power the devices that perform vital functions, or the buffered loads. This can significantly reduce the load to the dc UPS. Amperage reduction equates to a smaller UPS size and battery capacity.
DC UPS technology is simpler than ac UPS designs. DC products do not require ac-to-dc converters or dc-to-ac inverters. All voltages in the UPS remain at nominal safety extra low voltage (SELV) levels of 24 Vdc. This is more efficient for the power supply and the battery bank. Using extra dc/dc converters for other dc voltages uses more current in the conversion and becomes parasitic on the system. On higher-functioning UPS systems, the only dc conversion that occurs is in the battery charging circuit. A dc UPS system allows load priority. This prioritizes powering the load connected to the UPS. When a UPS supplies the load in mains mode and is charging the battery bank, the UPS will monitor the load current. If the load current and charge current combined would overload the main ac/dc power supply, the UPS will automatically reduce the charge current, preventing an overload. A dc UPS often is physically smaller than ac because of simpler circuitry.
Some modular dc UPS systems come with builtin diagnostics. Real-time knowledge allows battery replacement before failure, instead of guessing.
Batteries are the backbone a UPS system. When the power goes out, batteries keep things going. So how can you make sure a battery is not the UPS weak link? Common battery types for industrial UPS applications include VRLA, wide-temperature range (WTR) VRLA and lithium-based variants.
The standard VRLA battery is the most common, is low cost and balances cost and capacity, but it lacks durability. Standard batteries have a nominal opera-
Figure 2: An offline UPS under normal conditions passes mains power from the input to the output without interaction other than the battery charging circuit in parallel to the mains circuit.
Figure 3: In an online or “double conversion” topology, the UPS is never in standby mode.
tional temperature of 0 to 40°C. They perform best in a room with a steady temperature of about 27°C. While they are common in controlled environments, many industrial applications range from -40 to 70°C, which reduces the lifespan of VRLA batteries.
WTR-VRLA batteries can be operated from -25 to 60°C. They have a slightly longer service life than the standard VRLA. They often are used in outdoor applications. Chemistry differs from standard VRLA, and WTR-VRLA is usually larger and higher priced. VRLA and WTR-VRLA batteries can operate for about 250 to 300 charge cycles before failing, so a VRLA may last six months, and a WTR-VRLA may last one and a half to two years. Lithium battery lifespan and temperature range are similar to WTRVRLA batteries. Lithium batteries have up to 7,000 charge cycles for more service life. A lithium battery may cost three times as much as a WTR-VRLA, but with better performance.
An IIoT industrial world is more connected, and many devices are smarter. With networking and connectivity, UPS performance data is accessible with connection to industrial Ethernet network, giving the end user visibility into battery performance where the UPS is installed.
ce
Ken Allwine is associate product marketing manager - power supplies, Phoenix Contact. Edited by Mark T. Hoske, content manager, Control Engineering, CFE Media and Technology, mhoske@cfemedia.com.
KEYWORDS: UPS, power reliability
Define UPS application requirements prior to UPS selection.
Decentralized ac and distributed dc UPS designs are available.
Consider battery performance and communications.
What percentage of outages could be prevented with reliable power?
More details on each section and a table comparing industrial battery technologies. www.controleng.com/ system-integration/energy-power
Engineering fields are facing a major skills gap that isn’t going away. Engineers provide an economic backbone. A university changes the message.
Many of Wisconsin’s most notable companies have grown from family businesses founded decades ago into multibillion-dollar companies with an international reach – and engineers drive the innovations that underlie their progress, global competitiveness and economic success.
“Engineers are a multiplier in the workforce,” said Todd Kelsey, CEO of Plexus, a global company specializing in highly complex design, manufacturing, supply chain and aftermarket services based in Neenah, Wisc. “They create things, and by creating things, they create jobs. Engineering is critical to make our economy grow.”
Beyond manufactured goods, engineers also play a major role in virtually every aspect of daily life. Engineers design transportation systems, buildings, water supplies, and energy infrastructure. Engineers enable all aspects of digital infrastructure, from smartphones to 5G wireless networks to the cloud – and create systems to keep data secure. In healthcare, engineers pioneer solutions for diagnosing and treating disease or improving the way in which patients receive care.
KEYWORDS: workforce development, STEM, engineering education Engineers play a major role in virtually every aspect of life. Industry demand for engineers is outpacing the supply of graduates.
The University of Wisconsin Madison is looking to expand enrollment and upgrade facilities.
With this article online, see additional college and university stories at www.controleng. com. Also look at the Control Engineering 2021 Career and Salary Survey, published in May, for more information about engineers today. https://cfeedu.cfemedia.com/ www.controleng.com/ online-courses/ www.controleng.com/webcasts/ https://cfeedu.cfemedia.com/ pages/virtual-training-week
What inspired you to be an engineer and what advice would you give to an aspiring engineer?
University of Wisconsin-Madison’s College of Engineering enrolls 4,500 undergraduate and 1,500 graduate students annually; each year, approximately 1,500 students earn engineering degrees.
Even with that, industry demand for engineers is outpacing the supply. “We can’t grow our company without continuing to innovate and develop new technologies, and we need more UWMadison engineers coming in to help us do that,” said John Pfeifer, president and CEO of Oshkosh Corp.
As of April 2021, there were nearly 9,400 full-time engineering jobs posted in Handshake, UW-Madison’s online career management system, and Wisconsin occupational employment projections show a 7.77% increase in engineering jobs from 2018 to 2028.
Plexus is among those employers seeking to grow its engineering work-
The College of Engineering’s rigorous curriculum helps students become innovative problemsolvers, while hands-on design and capstone courses allow them to apply their engineering training to real challenges. Courtesy: University of Wisconsin-Madison
force, which in Wisconsin includes 350 engineers. “Over the last five years, we’ve hired well over 100 engineers,” Kelsey said.
Admission to the College of Engineering is extremely competitive, said Robertson. “Each year, some-7,000 talented students apply to UW-Madison with a desire to become engineering undergraduates,” he said. “Our college can admit only about 1,000. That capacity is limited by the space and the facilities we have available, as well as the number of faculty and staff we have to educate our students.”
With an ambitious plan to enroll 1,400 additional students each year – bringing the total annual number of engineering graduates to more than 2,000 – Robertson said the UW-Madison College of Engineering needs to follow suit.
“We need to grow not only to meet student and employer demand, but also to remain attractive to them. If we want to continue to recruit the best talent – and that means at the faculty, staff and student level – we need facilities that are comparable to our peers,” he said.
ce
Renee Meiller is director of communications,University of Wisconsin-Madison. Edited by Chris Vavra, web content manager, Control Engineering, CFE Media and Technology, cvavra@cfemedia.com.
Industrial Internet of Things serves as backbone for Industry 4.0, smart manufacturing, artificial intelligence, machine learning, augmented reality, virtual reality, digital twins, digital thread, big data, analytics, cloud and edge computing.
When discussing Industry 4.0 or smart manufacturing, the conversation will get to the Industrial Internet of Things (IIoT). The IIoT has become nearly synonymous with smart manufacturing; many people believe the IIoT is all there is to smart manufacturing.
Of course, this isn’t true. Many technologies are driving smart manufacturing, including artificial intelligence (AI), machine learning, augmented reality (AR), virtual reality (VR), digital twins, the digital thread, big data, analytics, and cloud and edge computing, to name just some. The IIoT is becoming ubiquitous in smart manufacturing because it serves as the backbone and foundation for all other smart manufacturing solutions. It’s not going too far to say the IIoT is smart manufacturing glue. Here’s why.
As the backbone, the IIoT facilitates real-time machine-to-machine (M2M) communications. This is the essence of smart manufacturing – smart machines communicating with one another in a flat, peer-to-peer environment, coordinating their activities as they execute the manufacturing processes in a totally autonomous fashion. This is also the basic definition of smart manufacturing and the IIoT backbone makes the rest of smart manufacturing possible.
As part of this backbone function, the IIoT also facilitates communications between sensors, devices, machines, and controllers – that is, essentially anything and everything that’s part of the IIoT. The IIoT collects data from all these disparate sources in real time and provides the data to those devices, controllers, systems, and the people that need it. But even beyond the data, the IIoT also collects the context for the data, so there’s a complete picture of the data and what was happening when data was collected.
Intelligent agents are an emerging IIoT solution to take communications, data, and data context to the next level. Think of intelligent agents as objects containing data and data context, with some artificial intelligence mixed in, that act and react autonomously based on IIoT events. Some refer to intelligent agents
as smart objects or smart AI objects, but they are very powerful, combining data, data context, and AI.
An intelligent agent might be used to collect some critical data, and data context, and get it to another system or person when a specific event occurs. An intelligent agent might be used to react to the event, making a correction or adjustment autonomously in real time when the event occurs. Or an intelligent agent might be used to act in advance of an event occurring, making an adjustment autonomously in real time to prevent the event from occurring and keep the manufacturing process running smoothly.
The idea of edge computing has been around for a long time. Edge computing brings data, data context, and intelligence closer to where it’s needed. It’s about closing the loop much closer and much faster. To make this possible, the IIoT supports edge computing where it’s needed and allows edge devices to access more data and data context, supporting edge devices with more intelligence.
Some edge devices might collect data and data context for the cloud or might support better orchestration among devices, machines, and controllers. Other edge devices might lose the loop on events closer to actual events. All these edge devices are possible through the IIoT. The IIoT allows AI and machine learning to be deployed in edge devices. Such devices can take different shapes and do many different things. Because the IIoT provides the data, and the data context, edge AI is possible for the first time. Typical application for edge AI is machine learning and analytics to predict and prevent anomalies in real time very close to the machine or machines. It’s possible through the IIoT, its data and data context.
Augmented reality and virtual reality are sometimes considered stand-alone applications, which doesn’t make sense as they need significant amounts of data
KEYWORDS: Industrial Internet of Things, Smart manufacturing Industrial Internet of Things supports Industry 4.0 and smart manufacturing.
IIoT technologies may include including artificial intelligence (AI), machine learning, augmented reality (AR), virtual reality (VR), digital twins and the digital thread.
IIoT also can include industrial Big Data, analytics, and cloud and edge computing.
CONSIDER THIS Have you reimagined manufacturing operations using IIoT and smart manufacturing technologies?
ONLINE www.controleng.com/ iiot-industrie-4-0
Don’t be puzzled by smart manufacturing and Industry 4.0. It includes many elements that operations may already be using, such as digital twin, cloud, edge computing, machine learning (ML), artificial intelligence (AI), analytics, industrial Big Data and others. Courtesy: Control Engineering
to even work. The IIoT is the data collection backbone that provides large amounts of data and the data context in real time to AR and VR solutions so they can do their job. Without that data, AR and VR don’t work.
Item identification is critical in just about every manufacturing operation conceivable. It might be barcodes or radio-frequency identification (RFID) or one of a variety of other technologies. Regardless, identification of products, sub-products, parts, assemblies, materials, tools, and a whole host of other items is critical to manufacturing.
An identification may not be enough all by itself. All the information included with that identification is also critical – what order the material is tagged for; where the item came from; where it’s supposed to go next; what quality assurance issues the product has or hasn’t had as it was being manufactured; and so on. Backing up that identification with the data and data context of the item from one end to the other is where the IIoT comes into play and is what makes item identification so valuable.
Digital twins are becoming a key technology in the world of smart manufacturing. The physical twin may be almost any asset, essentially anything that can produce a digital stream of data in real time. The key to the digital twin is it’s connected to its physical counterpart, getting continuous real-time data stream from the physical twin and become its digital replica.
The digital twin orchestrates the physical twin, so
it’s in sync with the rest of the manufacturing process. It’s also used to optimize the efficiency, effectiveness, and capability of the physical twin to ensure the manufacturing process flows smoothly and delivers what it needs to deliver. In addition, it’s used to view the physical twin’s inner workings and then troubleshoot it to ensure continued operation. Digital twins require vast amounts of real-time data from their physical counterparts. The IIoT delivers this data.
The concept of the digital thread has been around for a while. In smart manufacturing, it’s often defined as the streams of data used to create digital twins. But the digital thread is much, much more than that. It’s all about getting the right information from the plant floor, organizing it into a complete picture, and then making sure the right people see it at the right time, in real time.
The digital thread captures and documents everything that happens inside the manufacturing facility electronically instead of on paper. Acquiring this data makes it possible to analyze manufacturing operations, track manufacturing history, and support process and product genealogy. It also makes everything about the manufacturing operations much easier to manage and supports historical analyses, production run comparisons, and golden batch approaches.
Ultimately, the digital thread is not merely about how materials move through the manufacturing process but also about how they are transformed along the way to the finished products. It captures information about the materials and the lot genealogy as well as what goes into manufacturing the product including equipment, labor and processes. This transformation process is what manufacturing is all about, and significant business value can be derived from the flow of data coming from the digital thread. The flow of this data is only possible through the IIoT.
Manufacturing execution systems (MES) have been around for a long time. While they’ve always been about execution of manufacturing operations, they are expanding and growing to now be more about orchestrating and optimizing entire manufacturing lines and facilities, and even between facilities. For an MES to perform these orchestration and optimization functions, it needs lots of data and data context, all in real time.
The IIoT provides that real-time data and data context to the MES, which then mixes with the data from the enterprise resource planning (ERP) system, quality management system (QMS), product lifecycle management (PLM), and from a variety of other sources. All to create a complete picture of the overall manufacturing status and objectives to determine what corrections need to be made to
orchestrate the operations as well as adjustments that need to be made to better optimize the operations. All of which is only possible through the IIoT and its data and data context in real time.
Often implemented in the form of dashboards, enterprise manufacturing intelligence (EMI) is one of the core tenets of smart manufacturing. It provides real-time data to people on the plant floor so they know what’s going on in the manufacturing operations, where they are in the process and what’s happening upstream and downstream. It gives a complete picture of the manufacturing operations in real time, including data on production, materials, orders, equipment, status, quality, inventory, performance, throughput, and a whole lot more. Data in real time is only possible through the IIoT.
Analytics is core tenet of smart manufacturing designed to get the right data to the people who need it. Few smart manufacturing solutions don’t include analytics. The most common analytics included are descriptive and diagnostic, which answer the questions, “What happened?” and “Why did it happen?” These analytics require large amounts of data, in real
time and historical. The IIoT provides descriptive and diagnostic analytics with the data people need to do their jobs. There’s more to analytics – there’s also predictive and prescriptive analytics, which are intended to answer the questions, “What is going to happen?” and “What should I do about it?” These analytics require even more data – particularly historical data. Such analytics aren’t possible without the IIoT’s data and the data context for smart manufacturing.
The IIoT has become synonymous with smart manufacturing. Smart manufacturing is smart, and works, because of the IIoT. AI, ML, AR, VR, digital twins, digital threads, edge computing and analytics rely on the IIoT. IIoT is becoming ubiquitous in smart manufacturing, the backbone and foundation that holds smart manufacturing together. ce
John Clemons is a senior consultant at Maverick Technologies, a Rockwell Automation company. Maverick Technologies is a CFE Media content partner. Edited by Mark T. Hoske, content manager, Control Engineering, CFE Media and Technology, mhoske@cfemedia.com.
‘
Predictive and prescriptive analytics answer the questions, “What is going to happen?” and “What should I do about it?”’
Lessons can be learned from prior cybersecurity efforts. Are you aware of the eight ways to mitigate the Aurora vulnerability? In 2007, the Department of Homeland Security, working with the Idaho National Laboratory, demonstrated that a cyberattack could cause real-world physical damage. It had been known cyberattacks could destroy computer equipment by creating anomalous behavior in hard drives and by overclocking microprocessors; the goal of this test was to determine if manipulating control components could damage or destroy large infrastructure, such as a 2.25 MW, 27-ton diesel generator. The test proved it could be done and revealed a difficult-to-mitigate vulnerability. This is known as the “Aurora vulnerability.”
Connecting an unsynchronized generator to a working power grid is dangerous and will damaged or destroy, a generator. What if a threat actor with knowledge of the workings of generating systems were to gain access to protective systems, either physically or virtually? This was the basis for a proof-of-concept test done at the sprawling Idaho National Laboratories, which is run by the Department of Energy.
domly open and close the generator breaker.
Prior to initiating the test, the generator was synchronized to the grid and operating as expected. The start of the test checked the protective systems for synchronism; then disconnected the generator from the grid. Being unloaded, the generator naturally accelerated. Then the circuit breaker was closed, tying the generator back into the grid. The generator was violently forced back into synchronization by the force of the grid; the force of the other connected generators and devices pulled the small mass of the test generator back to synchronism with the 60 Hz grid frequency.
The malicious code that had corrupted the protective system’s functions was less than 130 kb, which is about 30 lines of code. The opening and closing of the generator breaker had lasted for only a few microseconds, or about 15 cycles. The code was executed three more times, causing violent shaking of the generator; after the second hit, pieces began to fly off. The large rubber connector that joins the generator to the engine was rapidly deteriorating from the extreme torque exerted on the machine. The generator began to smoke; its windings had begun to fuse and melt from the high current spikes from the OOPs.
KEYWORDS:
Industrial cybersecurity, ICS
2007 Aurora generator test by INL showed vulnerabilities.
Eight ways to mitigate risk include audits, monitoring and encryption.
See more tips, video in the online version of this article. www.industrialcybersecuritypulse. com/throwback-attack-lessons-fromthe-aurora-vulnerability
CONSIDER THIS
Are these “past” cybersecurity remedies still remediated?
The lab has its own large power grid and generating capacity. A large diesel generator was acquired from surplus, and a facility was built to house it. A new substation was built, replicating those seen in common practice and including the protective relay systems often used in this type of installation.
To facilitate the main goal of the test, vibration monitoring, overspeed and synchronism trips were disabled. The goal was to produce what is called out-of-phase synchronization (OOPS) by opening and closing the generator’s circuit breaker while it is running and connected to the grid. Protective systems isolate a malfunctioning generator should it malfunction. For the test, the synchronism and phase imbalance protective relays were reprogrammed to ran-
After third and fourth execution of the code, the engine and generator tore themselves apart. Generator windings were melted and burned. The engine shaft had twisted and struck the inside of the crankcase. The generator was scrap metal. The test lasted 3 minutes. The generator was destroyed in less than a minute.
Mitigating this vulnerability is similar, if not identical, to protecting any other industrial control system (ICS). These measures require an investment in time and money. If executed properly, they can severely reduce risk. Levels of defensive measures, referred to as defense in depth, frustrate determined attackers by physically blocking, or obfuscating, misdirecting and blocking their efforts. Eventually, bad actors move on to easier targets.
Proper security measures can mitigate risk of the
Aurora vulnerability. Eight baseline measures follow.
1. Audit communication systems. It is important to know how the control network is setup and where any possible breaches can occur. Think like a hacker – they operate like burglars who walk down the street and check doorknobs – shut down any unused ports or extraneous communication channels. The point of the audit is to determine what systems and what staff have access to critical systems communication networks, including SCADA. Know what communication channels are actually in use and which can be eliminated.
2. Institute algorithms that monitor and supervise protective relay and breaker operation. Unusual opening and closing of the relays or breaker may follow a recognizable pattern and can be detected and mitigated before an attack is executed.
3. Encrypt and protect communication channels. Use a firewall with virtual private network (VPN) capability for any outside access requirements. Institute a secure and encrypted (and unadvertised) backup communications channel for use if the primary channel is compromised.
4. Eliminate any cross connections with office or corporate networks. There should be no connection between SCADA or energy management system networks and the facility’s office network, which is likely connected to the internet. This is a grave vulnerability because of attacks that start with a “phishing” email; 85% of all attacks start with a phishing email. Also, attacks can be “inside jobs” by malicious or disgruntled employees.
5. Password policies should be established and enforced. Change default passwords on protective relays. Use long and strong passwords and hierarchical access controls. Require periodic password changes. Use multi-factor authentication (MFA) for critical system access. Treat each system as a unique security domain. Do not use the same password for all systems.
6. Institute a policy of least privilege for all staff to limit access to critical systems. Consider schematics, product manuals, diagrams, flowcharts and any other detailed system information as confidential and limit access to those staff on a need-to-know basis. Compartmentalize system knowledge and the security methods used to secure each domain.
7. Check incoming equipment against the vendor’s specifications. This helps users determine if a supply chain attack has occurred. Work with the vendor to institute methods that can determine if the device or software was tampered with between
the factory and the customer.
8. Audit and strengthen physical security. Threat actors who can infiltrate a facility and physically access equipment can perpetrate an enormous amount of damage on a facility. Humans are the weakest link in cybersecurity. Automate as much of the process as possible, including the starting, synching and connecting of generating equipment. Initiation of these processes can be substantially automated. Modern protective systems perform their functions well with reliability levels exceeding a humans – they are not distracted or annoyed.
In 2009, the first purpose-built digital weapon was used to destroy a third of the uranium enrichment centrifuges at the air gapped Natanz laboratory in Iran. The Stuxnet worm, developed by the NSA and Israeli cyber-warriors, was smuggled into the facility on a contractor’s laptop. The worm infected the centrifuge control systems by specifically targeting the programmable logic controllers (PLCs) that controlled them. This was the first known use of a digital weapon to destroy physical equipment in real world.
In 2016, Russia’s GRU (military intelligence agency) perpetrated an attack on the Ukrainian power grid. The attack started with a phishing email, which unleashed a script that quickly compromised the grid, mostly through unsecured or poorly secured communications channels. The attack caused widespread outages and collateral damage. An often overlooked item was the destruction the attack caused: the worm targeted key pieces of equipment such as PLCs and PCs used for process control and power generation. Several generators were damaged or destroyed using Auroratype attacks; transformers and substations were damaged using similar techniques.
The Aurora vulnerability sent shockwaves through the cybersecurity and power industries after it was revealed in 2009 in a Freedom of Information Act (FOIA) request regarding a different Project Aurora.
The vulnerability can be mitigated, and much progress has been made since 2007 in the protection of critical systems. Many legacy systems still exist, and operators succumb to the belief this is a solution in search of a problem. The problem exists, and the means and methods for preventing it exist. With the chaos that a large and prolonged blackout would produce, the issue requires a sober examination of the facts and for responsible parties to act.
Daniel E. Capano is senior project manager, Gannett Fleming Engineers and Architects, a CFE Media content partner, and is on the Control Engineering Editorial Advisory Board. Edited by Chris Vavra, web content manager, Control Engineering, CFE Media and Technology, cvavra@cfemedia.com.
‘The problem exists, and the means and methods for preventing it exist.’
The i550 protec is exceptionally tough. Its NEMA 4X (IP66) protection rating makes it suitable for even the most demanding applications. Whether dusty or wet, indoors or outdoors – it can handle it all. The housing protects the technology – and performance remains excellent no matter the conditions. Offering a compact design, it’s also the first decentralized drive in the market with IO-Link Device Interface.
PLC-controlled robots, companies were given the opportunity to manage a robotic automation solution with a unified point-of-control between industrial robots and controllers.
For several years, manufacturers were faced with a dilemma when launching a new robot application into their production environment. Most robot original equipment manufacturers (OEMs) required the operator to be knowledgeable in the core robot language in order to program and maintain the robot for the application in question. Support staff would need to be highly proficient in every manufacturer’s specific language and logic a facility had in use.
In these cases, what’s the most prudent course of action to take to implement their new automation solution? Train existing staff? Search out and hire qualified labor? Employ the services of an experienced systems integrator? The expense of finding individuals with multiple skill sets is high, but so is the alternative of employing more people in order to cover the range of knowledge required.
tion solution with a single, unified point-of-control between industrial robots and programmable logic controllers (PLCs). Most manufacturing operations already employ engineers familiar with PLC programming and taking advantage of that existing knowledge to onboard and maintain new robot equipment removes the need to reinvent the wheel. Taking advantage of current staff with experience in PLC programming and general robot programming knowledge reduces the need to outsource via new hires or enlisting the service of a third-party systems integrator.
KEYWORDS: robotics,
programmable logic controller (PLC)
Programmable logic controller (PLC) robot control allows manufacturers to control their operation with only one programming language.
Robot controllers have advanced features such as integrated vision and advanced motion.
PLC-controlled robots are best suited for assessing the need at a large manufacturing facility.
See additional stories about robotics at www.controleng.com.
How can PLC-controlled robots improve your facility?
• Training internal staff on a new robot core language can add unnecessary cost to a capital project and push back the timeline for implementation.
• For complex systems, supporting multiple different robot languages can turn into a logistical and managerial nightmare.
• Finding qualified labor is difficult, especially in less populated areas where many manufacturing facilities operate.
• Luring talented prospects to remote areas has turned into a dicey proposal in today’s environment.
With the development of PLC-controlled robots, companies were given the opportunity to manage a robotic automa-
For the end user, the most important advantage of PLC robot control is only one programming language is often needed to support the entire solution. In many of these situations, the manufacturing facility already has a knowledgeable PLC staff, as this is the standard type and language used for their production, process equipment, and machinery. They can handle the majority of automation support for the integrated cell through the PLC human-machine interface (HMI). Adopting the existing controls system for robots includes the added benefit of simplified troubleshooting and maintenance as well.
Turning to an automation environment controlled via PLCs also gives manufacturers the freedom to choose the robot OEMs that best fill their needs. No longer are end users pigeon-holed into buying from a single OEM to avoid the extra hassle of training staff on yet another robot language. Robot automation can be more appropriately selected due to the characteristics and capabilities of specific models.
When considering options, manufacturers should take advantage of the latest technology. Robot controllers have advanced motion, safety capabilities, integrated vision, collision detection, force sensing, and other advanced capabilities. However, in most cases these advanced robot functions are available for programming through the PLC.
Additionally, many industrial robot applications are simple material handling operations, such as picking, packing and palletizing. These applications can easily be programmed in the function block style found in the PLC environment. If the application in question is primarily a material handling operation, it may be the most sensible course of action to put the teach pendant down and head to the nearest HMI.
PLC-controlled robots are not a magic bullet for manufacturers. Switching from robot controllers to PLC logic-controlled robots will not offer any better or reduced robot performance. This particular solution is geared more toward assessing the need for a larger technical staff at the end user’s facility. By limiting the need for very specific robot manufacturer experience, a company can be more efficient in its staff management.
For example, a company may want to retain a certain skill set among their staff but will not need to staff that skill set for all working shift coverage. More advanced needs for special circumstances will still reside amongst the team but is not necessary for the everyday maintenance of the system.
Integrators with experience installing systems fully controlled via PLC logic can assist in upgrading current cells to help cut down on the support costs of a more complex system. Designing new solutions with the PLC and HMI controls architec-
ture to enable the operator’s ability to support and attend to the cell purely through the HMI can prevent the need to ever pick up a robot teach pendant.
Eliminating the cost and time associated with training new or existing operators can create a quicker return on investment and make upgrading existing equipment or integrating a new robotic automation solution a less complex and more realistic opportunity. ce
This article originally appeared on Applied Manufacturing Technologies’ (AMT) website. AMT is a CFE Media content partner. Edited by Chris Vavra, web content manager, Control Engineering, CFE Media and Technology, cvavra@cfemedia.com.
Then stop using complicated controllers for precision motion. You shouldn’t need a Ph.D. in control systems to program your controller. With Automation1, you can now reduce your set up time — in many cases, from days down to minutes — thanks to a user-friendly, intuitive interface and machine setup wizard. Automation1 is the most user-friendly precision motion control platform available.
PLC controlled robots are not a magic bullet, but can provide cost savings to manufacturers by limiting the specialized a traditionally needed to manage robotic automation. Courtesy: Applied Manufacturing Technologies (AMT)[
More answers regarding servo system tuning follow the April 15 webcast.
Tuning the servo system to performance specifications can be among the most troubling tasks in machine building.
It’s not always about what three numbers should go into the proportionalintegrated-derivative (PID) controller. In an April 15 webcast, “How to Tune Servo Systems: Force Control (Part 4),” Joseph Profeta, Ph.D., director, Control Systems Group, Aerotech, covered how to tune the force loop tools to meet system specifications and create an arbitrary force trajectory, limitations of a force loop around the position loop and current loop, how to command arbitrary force trajectories, and how to minimize bump.
More ANSWERSM
KEYWORDS: Motion control, loop tuning, force control
How to tune servo systems: Force control, Part 4 webcast offers more answers to listener questions.
Tuning answers cover servo stability, sensors, compensation. Temperature can affect precision motion control.
What other servo tuning questions do you have?
ONLINE
www.controleng.com/webcasts/past Webcast series on Tuning Servo Systems
Part 1 – The Basics of Frequency Response
Part 2 – Feedforward & Nonlinearities
Part 3 – Digital Control: Sample Rate and Resolution
Part 4 – Force Control
Diagram at right shows a frequency domain control problem, from a series of webcasts on “How to Tune Servo Systems.”
Courtesy: Aerotech
Profeta answered questions in the live webcast about force control in servo system tuning. More answers are below.
Q: Why is tuning so difficult to attain smooth performance, linear servo, pick and place, at speed?
A: It is possible with pick and place that the linear servo stability is affected by the load change on the axis. Using gain scheduling for different loads is one strategy to use.
Q: How do I tune a servo motor?
A: Depending on servo loop structure, start with low proportional gains. In a stable system, assess stability with the loop gain frequency response and by adjusting gains. The first webinar in the series has a demo.
Q: Is there concern with ringing in the transients?
A: This is application-dependent. Some force applications cannot tolerate overshoot. In this case, tune the system such that it is critically damped to have no overshoot in a step response. If you are able to contour the force command, this also can reduce the transient oscillations.
Q: What effects might you see with precision rotary stages subject to temperature transients?
Can thermisters mitigate this?
A: Say the environment were to slowly fluctuate between 10 and 35°. The temperature variations will cause the mechanical system to grow or shrink. This can include the feedback device depending on what feedback is used and how it is mounted. If the feedback is growing and shrinking with the mechanics, the control loop will be unable to correct for temperature variation. System temperature measurements can add a correction. Some controllers have a linear interpolation algorithm for this purpose.
Q: Why do we use two integrals in force loop when the force loop is wrapped around the position loop?
A: This is used in applications to control the height of an axis above a target when ramp commands are needed. It is not used in the force loop.
Q: Have you considered optical sensor as position feedback in the loop?
A: Yes. This can work well if the sensor is linear and high resolution enough.
Q: After touch, is there force loop compensation?
A: The webinar showed two modes. Touchdown in position mode where no force compensation takes place until the force loop is turned on and touchdown in force mode where compensation is active during and after touchdown. ce
Edited by Mark T. Hoske, content manager, Control Engineering, CFE Media and Technology, mhoske@cfemedia.com.
Our enclosures are UL listed and NEMA rated (4X & 6P), manufactured in aluminum, fiberglass and of course polycarbonate! With a solution for virtually any location, Fibox has you covered with a thousand off-the-shelf, ready-to-ship variations ranging in size from 2 x 2 to 32 x 24 inches.
also offers precision CNC machining on premises before shipping.
Fibox was the first to specialize in injection molded polycarbonate. This highimpact, radio translucent, high-performance thermoplastic is easier to work with than fiberglass or metal. It has a broad temperature range, superior resistance to corrosion, and UV. In short, Fibox’s WiFi friendly polycarbonate will not dent, rust, crack or bloom like steel or fiberglass.
Save time, money, and aggravation with enclosures custom-tailored to your exact needs.
Fibox also was the first to utilize Formed-In-Place gasketing, ensuring a perfectly laid gasket and a dry, dust-free (NEMA 4X) environment. Fibox’s ARCA-JIC series ushered in a new era in enclosure technology. This spirit of innovation continues with the first genuine plastic enclosing alternative to steel boxes: the ARCA-IEC The ARCA - IEC measures 32 x 24 x 12 inches, making it the roomiest polycarbonate cabinet on the block!
With a history of firsts, it’s easy to see why Fibox is the leader in enclosing innovations.
Contact Fibox to learn more: 410.760.9696 www.fiboxusa.com | sales@fiboxusa.com
Hammond Manufacturing offers a broad range of industrial and commercial electrical enclosures. Their focus on providing industry leading service to support their quality enclosures includes extensive inventory for immediate delivery, coast-to-coast field sales support and an easy to use enclosure website, www.hammondmfg.com.
Hammond Manufacturing offers several series of watertight polycarbonate and ABS plastic enclosures available from stock. Ideally suited for mounting printed circuit boards or DIN rail mounted components, with several series offering optional subpanels.
Gasketed lids with two-piece “tongue & groove” construction provides protection against access of oil, dust and
water. Polycarbonate versions are cUL and UL508A listed and are designed to meet NEMA Type 4, 4X, 6, 6P, 12 and 13 ratings – exceeding IP ratings up to and including IP68. Replaceable gasket is one piece made from high temperature, U.L. listed silicone.
Optional mounting accessories include external feet as well as pole mounting brackets. Modifications are also available to customize any enclosure with holes, cutouts and screen printing.
For CAD files and detailed specifications visit: hammfg.com/electronics/small-case/industrial
Contact sales@hammfg.com | Phone: 716-630-7030 | www.hammondmfg.com
Cybersecurity: The Conversation We’re All Having
are increasingly aware of cybersecurity’s importance, especially those operating via cloud and edge-computing models. The subject has introduced anxiety for business leaders and consumers alike, with few having full confidence about safe monitoring and control in a digital, data-driven age.
Sealevel’s SeaI/O family of modular I/O devices are established, industry-leading solutions for distributed control and data acquisition. And as large-scale industrial Ethernet use expands, our Ethernet variants are advancing to include network security to protect against cybersecurity risks. Companies can take advantage of the selectable connectivity and robust I/O they’ve come to rely on with an added layer of security for reliable operations.
Sealevel offers over 350 core products, available in nearly every configuration you can imagine. Our async and sync solutions along with our digital and analog I/O modules enable the transfer, monitoring and control of signals: faster and more reliably than ever before. And with IIoT hardware and software, we’re changing and improving industries through remote monitoring and predictive maintenance with a fortified commitment to security.
American made. Long-term availability. Lifetime warranty. Standard.
ABB provides solutions for efficient production, safe and reliable operations, and digital remote condition monitoring across most industrial plant equipment and systems.
Sensor monitors the health of your low voltage motors, bearings, gear reducers and pumps by gathering data on vibration, temperature and other parameters that can be used to gain meaningful information on condition and performance, enabling users to identify inefficiencies within their system and to reduce risks related to operation and maintenance. Maintenance can now be planned according to actual needs rather than based on generic schedules. This extends equipment lifetime, cuts maintenance costs, and reduces or prevents unplanned downtime due to breakdowns.
EC Titanium: High performance. Flexible solution.
As energy regulations require higher total system efficiency, achieve IE5 efficiency in smaller spaces and with less maintenance by relying on the Baldor-Reliance® EC Titanium™ integrated motor drive. The EC Titanium is a highly efficient integrated motor drive that combines synchronous reluctance and permanent magnet technologies for a sustainable, wirelessly connected solution that improves your bottom line. This sustainable, IE5 solution runs out of the box, minimizes installation costs and increases facility safety.
ABB offers a full line of food safe products that include stainless steel NEMA and IEC motors, mounted ball bearings and gear reducers. The entire line is designed with food safety guidelines in mind, ensuring they will operate reliably no matter the conditions.
The company provides online tutorial videos through their web store at www.automationdirect.com as well as their YouTube channel. They also provide FREE online PLC training to anyone interested in learning about industrial controls. A Customer Forum utilized by tens of thousands of automation professionals provides peer support on technical and application questions.
Company headquarters located just north of Atlanta, GA
A well-recognized name in the industrial automation market, AutomationDirect provides quality products with FREE award-winning in-house sales and technical support. AutomationDirect provides customers with quick order and delivery through an online store and toll-free number. Prices on most products are well below the industry average and a 30-day money-back guarantee is offered on nearly all items.
With close to 30,000 part listings, new products include the 2020 Product of the Year Grand Award Winner ProductivityOpen Arduino-compatible controller, CLICK PLUS PLCs, and DURApulse GS20 AC drives. These products represent many years of design and development by AutomationDirect’s own engineering team as well as their strategic partners. The company also offers motors, sensors, pushbuttons, enclosures, circuit protection, cut-to-length cable, pneumatic supplies and more.
The state-of-the-art headquarters facility near Atlanta is designed throughout for maximum performance. The majority of items are instock and ready for fast shipping; orders over $49 ship for FREE. Some exclusions apply.
AutomationDirect’s customer support team has been rated top-notch by its customers and has received numerous industry accolades/awards for providing the best service and support on various products. To ensure their service and support remains superior, they continuously survey customers and have consistently outranked other suppliers.
Orders ship quickly from our state-of-the-art warehouse
For an in-depth look at products offered, visit: www.automationdirect.com.
Discover the revolutionary possibilities of XPlanar ® , the planar motor system from Beckhoff. Learn how your machinery and processes can be transformed with levitating movers, flying product movement, 6 degrees of freedom and a nearly limitless array of tile paths for total flexibility in manufacturing.
XPlanar gives you the freedom to intelligently adapt to constantly changing workflows and shatter all conventional thinking about automated production. Most importantly, XPlanar can help you secure an unbeatable competitive advantage and achieve the impossible.
Developed in-house and manufactured by Beckhoff, XPlanar is available for purchase today and is ready to revolutionize your application with flying motion technology. XPlanar movers float and fly freely above planar tiles arranged in customizable layouts that enable extremely flexible, precise and highly dynamic applications. For machine builders and manufacturers, this results in unprecedented flexibility and throughput with simplification in machine and plant designs. We can say this because we know. Beckhoff customers are using XPlanar in the field today to transform their operations.
The XPlanar system combines the individual arrangement of planar tiles with multi-dimensional positioning capability of the planar movers floating above them. Easy to use software tools include graphical path planning, automated jerk, pitch and yaw control, collision avoidance and 6 degrees of motion freedom. The movers enable jerk-free and contact-free motion in two dimensions at up to 2 m/s with 1 g acceleration and 50 μm positioning repeatability – completing movements without any noise or friction.
XPlanar is completely integrated into the standard TwinCAT programming environment and runtime. For communication, XPlanar systems are networked via the standard EtherCAT G protocol, which itself is fully compatible with the entire 100 Mbit/s EtherCAT ecosystem.
Flying motion. Fully integrated. Available today. Break free with XPlanar.
times
Decreasing update downtime using the IIoT No matter if you are controlling warehouse logistic systems, machines, mobile equipment or an automated industrial building, all these automation systems need one thing: updates of the control application to add new features, improve performance, adapt to changing requirements.
Earlier, this was a time-consuming and costly process that could take the whole system offline. CODESYS customer, Gebhardt, shows how Digital Twins in the cloud and a cloud-based controller management can speed up the process of updating a large number of PLCs to the point where it’s just a few mouse clicks.
Read the full story here: https://us.store.codesys.com/codesys-us-customer-success-stories
Reducing update times by 600%
What an alternative technology would have to fulfil is to require little to no effort to maintain the required infrastructure. The solution: the CODESYS Automation Server.
What used to take the engineers 2 hours could now be done in a mere 20 minutes. The Automation Server shaved off nearly 85% of the time it takes to update, an increase in speed of 600%! In addition, NO engineer is required to be on site at the customer’s warehouse! The whole update process with the CODESYS Automation Server can be easily done online.
With the Automation Server, Gebhardt can roll out updates of their applications with little effort and also simplified their source code management significantly by letting the Automation Server handle it. Versioning and tracking which source code is running on which controller is easier and more transparent than ever.
The Automation Server stores a copy of every version of the code that is ever deployed, remembers that this specific version is deployed on a specific controller (where it is deployed), and makes all this information readily available.
Utilizing the Internet for remote commissioning provides convenience and significant cost savings, but accessing machines at job sites can be difficult because firewalls block messages that originate from the Internet. The EIGR series of IP routers and the RemoteVPN service provide a complete remote access solution that allows system integrators to access the job site securely.
The EIGR series of IP routers include gigabit ports for faster speeds and higher data throughput, as well as built-in LTE cellular capabilities. When used with the RemoteVPN service, systems integrators can remotely access systems from the convenience of their home or office. A cloud-based VPN server hosted by Contemporary Controls provides the critical connection between two VPN clients—one installed on the systems integrator’s PC and the other permanently installed on Contemporary Controls’ EIPR/EIGR VPN router located at the remote location. Using this approach, two secure
location. this two secure VPN tunnels are created with no concern for intervening firewalls.
The use of RemoteVPN service, along with the VPN eliminates the need
the EIPR/EIGR VPN routers, eliminates the need for a Static Public IP address providing considerable saving. Multiple port forwarding entry setup is also eliminated and the masquerade feature allows access to devices where it is not possible to change the gateway IP address—either because the setting is used for a separate subnet or is missing on older devices. All the traffic is tunneled through the VPN over a single port and is encrypted.
Using the EIGR-C Cellular IP router and RemoteVPN results in a remote access solution is fast and secure. It allows systems integrators to commission and troubleshoot job sites without the need to be at the customer’s facility or negotiate with the customer’s IT department. Multiple remote sites can be accessed simultaneously using the RemoteVPN service.
The workplace has changed significantly during the last year in response to the pandemic. Automation has enabled contact tracing, social distancing, and additional new protocols to create a safe environment where pre-pandemic workloads can be maintained while still protecting the workforce.
The use of LoRaWAN badges protects both workforces and work flow. Each badge is assigned to an employee and records to a cloud-based platform when it is in close proximity to another badge. When an employee is diagnosed with COVID, data can quickly be pulled from their badge to identify other workers who were in close proximity to the infected employee.
Automation has also improved safety in common spaces such as break rooms and meetings rooms by monitoring headcounts to maintain social distancing. An occupancy monitoring system wirelessly and actively maintains a total headcount using photo-eye sensors that count persons entering and exiting a room. The sensors send a count to a controller, which then signals at the door entry if it is safe to enter the room.
Touchless technology enables employees to communicate compliance to new safety procedures. An RGB switch notifies a factory line worker when it is time to clean their work area. Once the task is complete, the employee simply waves a hand over the switch which changes color to indicate that the workstation has been cleaned and signals a coordinator that the work has been done.
To help prevent the spread of COVID in their expansive warehouse, Digi-Key designed and installed a UV light tunnel on their conveyor system that every tote passes through multiple times each day. The tunnel irradiates the entire tote with UV light as it passes through, protecting both employees and customers from the virus.
COVID has had a significant impact on each of our lives. The lessons we learn from this fight must be remembered so we are prepared to protect employees, workflow, and customers during the next public health emergency.
Eric Halvorson, Partnership Marketing ManagerStrategic ProgramsVeracity Industrial Networks’ (www.veracity.io), in partnership with Dynics, Interstates Control Systems, and Schweitzer Engineering Laboratories, began envisioning a product that would address reliability, visibility, data traffic control and deny-by-default security. From Veracity staff’s R&D and extensive experience, we’re providing cutting edge software defined networking (SDN) for OT environments. The product is called the Veracity SDN Controller and it addresses the demanding needs of OT Network Security.
ICS networks control processes including factory floor automation, food processing, water and waste systems and electric power distribution. ICS networks differ significantly from information technology networks and, unfortunately, most existing Ethernet networking-related technologies are based in IT practices. ICS-Defender and the Veracity SDN Controller are designed and developed by teams which are OT centric, many having started their careers in the industrial space.
The Veracity SDN Controller is architectural networking that separates network configuration (control plane) from the switch (data plane) allowing micro-segmentation of traffic within the ICS network. ICS designers and operators gain significant control and visibility into their networks with the Veracity SDN controller.
The beauty of our popular perimeter security product, Dynics’ ICS-Defender, is that it provides exceptional security for today’s traditional networks, and can migrate to support SDN networks deployed tomorrow. It’s important to protect and future-proof the investment our customers make in Dynics Security Solutions today when moving to our SDN solution in the future. All of this using standard IEEE 802.3 Ethernet.
DeltaV version 14 takes the traditional approach to commissioning and reduces it from 2.3 hours per device to 30 seconds per device.
Traditional commissioning of an automation system relies on a multitude of factors— design and installation of physical I/O and field equipment, on-time equipment delivery, cabling installation, personnel availability, and more— any of which can cause delays that cost millions of dollars and impact on-time delivery of capital projects.
Emerson’s DeltaV ™ Version 14 distributed control system (DCS) and safety instrumented system (SIS) offer a smarter approach to drastically reduce time and effort in commissioning.
Smart Commissioning helps take device commissioning off the critical path. With Smart Commissioning, you can manage the entire workflow for commissioning HART devices and enable one-click commissioning for all your field devices.
One-click commissioning
DeltaV Device Commissioner helps you quickly and easily perform all commissioning activities for HART devices for DeltaV DCS, DeltaV SIS, and AMS Device Manager. Once commissioning policies and templates have been set, a single click commissions multiple devices simultaneously.
With Emerson’s Smart Commissioning, tasks that used to take two hours or more can now be completed in five minutes or less. Moreover, DeltaV Device Commissioner gives you one concise location to manage those commissioning activities, including progress notification and automatic generation of documentation. By drastically reducing scheduling dependencies between project can help you shorten your project timelines.
PTUs are full scale, working process skids with on-line instrumentation and controls. Customers gain a hands-on experience with the types of operation, diagnostics and troubleshooting found in real-life process plants. This goes beyond what classroom-only style training can provide. These “mini process plants” feature Endress+Hauser instruments integrated with the PlantPAx process automation system from Rockwell Automation.
The Southside of Houston, right off the beltway in Pearland’s lower Kirby District, was the perfect location for Endress+Hauser to invest $38.5M into building its 112,000 square-foot campus. The company officially broke ground in 2019 and completed the build in the fall of 2020. The campus offers areas for calibration and repair, as well as a training center that features a stateof-the-art PTU (Process Training Unit). The campus is also unique as it serves as the home of the Endress+Hauser team and a few of its production centers as well as its sales and service representative — Vector Controls and Automation Group — all in one place supporting customers in the Gulf region.
“We continue to make investments that enable growth and further expansion in the US market,” said Matthias Altendorf, CEO of the Endress+Hauser Group. “The campus investment will strengthen cooperation and relationships with our sales representatives, strategic partnerships and our customers. We are excited to continue expanding our presence and business in the Gulf region and look forward to growth in Pearland.”
Endress+Hauser offers accredited calibration services consistent with global standards for nearly all physical, analytical and mechanical parameters— whether performed in a production center, in a service center or on-site at a customer’s location.
With more than one million instruments calibrated each year, the company provides these services for instruments of its own manufacture as well as those of other suppliers. Endress+Hauser covers all critical aspects of calibration and can perform and advise on all aspects, from in-situ testing to fully accredited factory calibration.
EZTouch EZ7 Series: EZAutomation is introducing a brand new EZTouch, the EZ7 Series, where the Front Module housing the Display and the Touchscreen is detachable from the back, connected with just an HDMI cable. No cutout is needed, just a small ¾” hole for the cable. Front is metal, NEMA 4/4X. Same strong specs: LED display 400 NITs for 75K hours @ 55 deg. C. 7”, 8”, 10”, 12” models. Backend CPU is common to all sizes. Plant user can replace a defective/ damaged Touchscreen or Display in less than 5 minutes. New 12” model is priced quite attractively. Quite often, plants want to increase the size of their screen over a period of time. This innovation makes it possible to do so at a minimal cost. EZ7 has full capability to talk to DH+ networks.
EZTouch.mini.PLC: has an extremely compact profile and is the most powerful, yet cost effective all-in-one HMI & PLC unit, ideal for small to medium size machines. The 3.5” or 5.7” TFT color HMI touchscreen with advanced programmable logic controller comes equipped with 27 I/O points including 12 Digital Inputs, one configurable Quadrature High speed counter input, eight Digital short circuit proof Outputs, four 5A NONC Relay Outputs with built-in Snubbers, two 12-bit Analog Inputs, and one 12-bit Analog Voltage Output!
EZTouchPLC & EZTouchRackPLC: EZAutomation being the first company to come out with an advanced HMI and a fully modular PLC packaged in one in 2005, called the EZTouch. PLC, is expanding this line to add 306 new models, with 6 to 15” displays, up to 112 modular IOs all contained in same unit, and communication to all networks including DH+, ModBus+, CCLink, Profibus, and all Ethernet protocols.
EZ Programmable Power Supply: EZ PPS is a darling of plant personnel. 12 or 24 DC small footprint DIN mount UL approved power supply with Voltage and Current Readout, is loved by one and all because it is such a great aid to troubleshoot your DC power distribution system. No need to disconnect wires and insert Volt and Amp meters to figure out what component is drawing too much current. Right now it is available up to 10 Amp output.
Ignition IIoT - This end-to-end IIoT solution lets you easily connect to and push data from thousands of devices across numerous sites through a central MQTT infrastructure to both industrial and business applications.
Ignition MES - Collect all your industrial data, connect to any SCADA or ERP system, and build virtually any MES application. Use Ignition to track production, eliminate downtime, schedule work orders, manage recipes, and more.
The Ignition industrial application platform combines unlimited licensing, instant web-based deployment, and the industry-leading toolset for supervisory control and data acquisition (SCADA) — all on one open, scalable universal platform. Ignition is The New SCADA because it solves the major pain points of old SCADA. Now your business can easily control processes, and track, display, and analyze all its data, without limits.
In addition to SCADA, Ignition is a great solution for the Industrial Internet of Things (IIoT), manufacturing execution systems (MES), human-machine interfaces (HMI), alarming, reporting, and edge computing.
Ignition HMI - Rapidly develop high-performance HMIs that optimize operator efficiency. Ignition makes working with HMIs easy, and updates are fast and painless.
Ignition Alarming - Build advanced alarming systems with drag-and-drop ease. Fast to install, easy to use, and infinitely scalable, Ignition is an unbeatable alarming solution at an incredible price.
Ignition Reporting - Easily create dynamic, database-driven industrial reports for a low price. Easily pull together all your data and create any kind of industrial report in any major format and automatically deliver it to anyone.
Ignition Edge - Ignition Edge is a line of lightweight, limited, low-cost Ignition solutions made for embedding into edge-of-network field and OEM devices. Now you can extend data collection, visualization, and system management out to the edge of your network more easily and affordably.
As a global specialist in Motion Centric Automation, Lenze offers you innovative products, drive solutions, complete automation systems, and engineering tools and services from one single source. We support you throughout the entire machine development process, and partner with you to provide the best future-proof machine automation solutions.
Lenze X4 Remote – an integrated solution for cloud-based remote services.
With Lenze X4 Remote, we offer an integrated and ready-to-use solution which is so simple that any machine manufacturer can set it up and configure it independently. Easily add value to your service, reduce downtime, and increase productivity. Make your company fit for the future by accessing all your most valuable insights in one place. Offer remote maintenance, monitor your machines, set up alerts, and create meaningful data dashboards – all with a few clicks.
i950 – the multi-talented servo inverter. The i950 servo inverter is a match for any operational scenario thanks to its three different modes of operation. It can be freely programmed or serve as an actuating drive under a CiA402 motion control, but the most common mode of operation is with the use of Lenze’s integrated FAST technology applications. With FAST, Lenze’s modular software system, preconfigured and tested technology applications can be used immediately with the i950 and adapted to the respective machine task via parameterization.
Compact i550 frequency inverter – a new solution for decentralized applications. Well-protected with IP66 (NEMA 4X), and wellconnected with many popular industrial fieldbuses, the i550 protec sets out to conquer a wide range of decentralized drive tasks. Even outside the control cabinet, the available space in machines and systems is quite limited. With the i550 protec, Lenze is launching an exceptionally compact device in comparison to others on the market. The design of the IP66 (NEMA 4X) devices ensures maximum protection against adverse environmental conditions such as high temperatures, dust, dirt or water jets during cleaning operations. It is particularly suitable for large-scale machines, distributed applications in material flow or apparatus engineering, or wherever control cabinet space is expensive.
PI North America is a non-profit, member-supported automation organization for industrial networking, specifically PROFIBUS, PROFINET, IO-Link, and omlox. It is dedicated to supporting the factory automation and process control industries in achieving beneficial results using these technologies. PI North America also assists device manufacturers in the development and marketing of PROFIBUS, PROFINET, IO-Link, and omlox products. Members of PI North America include vendors of hardware, software, and systems as well as endusers and operators, scientific institutes, universities, distributors, and system integrators.
To date, more than 60,000,000 PROFIBUS devices have been installed. PROFIBUS is the worldwide standard when it comes to networks in industrial automation. With a majority share of the fieldbus market, PROFIBUS has grown to become the unequivocal leader in this industry.
Via a single cable, PROFIBUS links controllers or control systems with decentralized field devices (sensors and actuators) on the field level and enables consistent data exchange with higher ranking communication systems. The consistency of PROFIBUS is enabled by utilizing a single, standardized, applicationindependent communication protocol which supports fieldbus solutions both in factory and process automation as well as in motion control and safety-related tasks.
The total number of PROFINET devices installed now exceeds 40,000,000. PROFINET, the all-encompassing Industrial Ethernet for advanced manufacturing, is the standard for industrial networking in automation. It connects devices, systems, and cells, facilitating faster, safer, less costly, and higher quality manufacturing. It easily integrates existing systems and equipment while bringing the richness of Ethernet down to the factory floor. Here are some advantages of working with PROFINET at the I/O level:
Freely scalable open architectures
Reliable and high-performance network
Maintenance and servicing from anywhere
Lower costs for production/quality data monitoring
Comprehensive diagnostics built into the protocol
Increased uptime with bumpless redundancy
16101 N 82nd Street, Suite 3B
AZ 85260 |
480-483-2456
PI North America – supporting the world’s most used fieldbus and Industrial Ethernet
Radwell International’s Asset Recovery program is an exceptional resource for your company. We offer cash for parts and products you don’t need. In many cases, selling your excess inventory to Radwell gives you the opportunity of adding dollars to your bottom line.
With extensive knowledge of what’s being used –and discontinued – in the industry, Radwell stocks and sells new and certified preowned industrial automation, MRO, pneumatic, motion, electronic, hydraulic, HVAC and electrical control equipment for plant floor and facilities maintenance machinery.
The process is easy. Call Radwell for a free recycling bin, gather and box your surplus, then call Radwell for free pick-up. Need more information? Radwell has highly trained and experienced asset recovery and surplus team members ready to help you make your business thrive.
Organizations that need to off-load equipment are able to do so; organizations that still need to buy that equipment can easily find and purchase certified equipment; and less e-waste ends up in landfills. Asset Recovery is a win-win for everyone!
• Lowering warehousing costs
• Reducing Aging inventory
• Reducing slow moving inventory
• Increasing warehouse space
• It increases cash flow with no labor costs
• Eliminates used overstock inventory
It is important to note that any equipment being sold to or sourced by Radwell International must meet the highest standards of functionality and use. However, not all equipment sold to Radwell via the Asset Recovery program has to be brand-new. Radwell has a team of in-house engineers and technicians who can refurbish equipment to a like-new state, granting it the Radwell Certified PreOwned stamp of approval, which comes with Radwell’s two-year warranty.
The types of equipment Radwell most often purchases and upcycles includes industrial automation equipment, PLCs, drives, motors, electronic parts, circuit boards, meters, sensors and all types of industrial controls. However, if your company has other types of surplus inventory that you’re looking to offload, please feel free to contact us at 800-884-5500 ext. 824.
To learn more about Radwell International’s Asset Recovery Program visit https://info.radwell.com/en/asset-recovery-program
Our team of (MAXOLUTIONS) automation engineers provides the expertise, project planning, software, commissioning, and worldwide support for your most challenging motion control projects. They can serve as a valuable extension of your engineering team, reducing the stress and demanding workload.
Our experts provide a solution of perfectly matched SEW components that work together seamlessly — because we designed them that way!
MOVIGEAR is the mechatronic drive system that combines the gear unit, IE4 motor, and electronics in one compact unit. Recent updates include fully integrated Ethernet/IP communications and digital motor integration. This advanced single-cable technology carries power, feedback information, and control signals along a single hybrid cable between decentralized devices. MOVI-C modular automation system is a one-software, one-hardware, automation platform that combines fully integrated components, control electronics and software.
SEW-EURODRIVE now offers a full complement of drive maintenance and management services. Our CDM ® Maintenance Management service provides a 24/7 online portal as well as a complete overview of your drive components, the condition of your units, drive usage, and service details. Plus, our new on-site Pick-Up Box Service will free up your maintenance team for other tasks. Just place your drives that need repair in the supplied box and we’ll handle the pick-up and return of your units.
Engineering excellence and customer responsiveness distinguish SEW-EURODRIVE, a leading manufacturer of integrated power transmission and motion control systems. SEW-EURODRIVE sets the global standard for high performance and rugged reliability in the toughest operating conditions. With global headquarters in Germany, its U.S. operations include a state-of-the-art manufacturing center, five regional assembly plants, more than 63 technical sales offices and hundreds of distributors and support specialists. This enables SEW-EURODRIVE to provide local manufacturing, service and support, coast-to-coast and around the world.
The optimal use of data is becoming increasingly important for industry. Many companies have already recognized this fact and are analyzing machine and plant data on industrial PCs using their own software. Although this method delivers a great deal of valuable knowledge, it’s resource-intensive and requires frequent manual updates to ensure that the software, operating system, and cybersecurity are always secure and up to date.
Cloud or edge? Thanks to Industrial Edge, there’s no question. You can choose whatever you need.
With Industrial Edge, everything is easier, more flexible, and more. You enjoy all the benefits of edge and cloud computing – optimally tailored to your company’s specific requirements. Industrial Edge allows you to analyze all the data at the machine or preprocess it quickly and instantly. The optimized data points can then be transferred more quickly to the cloud where, for example, you have access to more computing power and larger storage capacities. Among other things, this permits a precise analysis of data over longer periods of time. Based on your application, you decide whether and how you want to use the cloud in addition to Industrial Edge.
With Industrial Edge, you can implement applications and solutions that far exceed the functions of a traditional controller. Whether as a direct part of the controller or with industrial PCs, Industrial Edge offers a flexible and innovative platform with long-term availability that accompanies you throughout the digital transformation of your company.
Thanks to tailored software, Siemens’ SINUMERIK Edge offers you a machine-level platform for apps that digitally support and optimize production. The analysis of high-frequency CNC data is practically feedback-free for the CNC.
Edge Computing – more than a hype?
Get to know the world of Siemens Digital Industries in our Talking Digital Industries podcast. Listen to Siemens podcast on your podcast app or on Spotify and take deep dive into edge computing.
For more information, please contact our Customer Support Center. Phone: 1-800-241-4453 | E-mail: fa.marketing.us@siemens.com | usa.siemens.com/industrial-edge input #34 at www.controleng.com/information
Sealevel Systems Inc. announces the Rugged SuperSpeed 7-Port USB 3.1 Hub, which features a rugged, industrial-grade, metal housing, robust ESD protection, USB 3.1 compliance and backwards compatibility with legacy USB data rates. It is designed to meet the advanced requirements for connecting multiple USB peripherals in extreme environments while achieving SuperSpeed operation. It provides up to 5 Gb/s data rate to the host, operates in -40°C to 85°C, has individual port power management, includes 15kV ESD protections on USB 3.0 data lines and 8kV ESD protections on USB 2.0 data lines, provides up to 1500mA available on all ports simultaneously, has input power protections and includes 2-meter USB 3.0 type A to USB 3.0 type B device cable. The USB 3.1 hub is fully compatible with standard USB cables but includes SeaLatch USB type B connectors. A high-retention thumbscrew prevents accidental cable disconnection, which makes it ideal for high shock and vibration applications. The USB hub supports the full bandwidth of USB 3.1, allowing connection of legacy peripherals alongside newer devices without disruption.
Systems Inc., www.sealevel.com
The compact pipeline systems found in many process plants usually have numerous fittings and pipe bends. Disturbed flow profiles occur downstream of such obstacles and can impair the accuracy of a flowmeter. Prosonic Flow P 500 is the world’s first ultrasonic flowmeter able to detect and automatically compensate for effects of flow disturbance on the measuring signal via calculation. This makes it possible, for example, to maintain a consistent (specified) accuracy, even with a significant reduction in inlet runs, for example from 15 pipe diameters (DN) all the way down to 2 pipe diameters (DN). This capability provides maximum flexibility for planners and operators, particularly in situations where they need to equip or retrofit a plant with clamp-on flowmeters. Endress+Hauser, www.us.endress.com Input #201 at www.controleng.com/information
The Smart Function Kit for Handling is a complete, fully integrated plug-and-produce mechatronics system for Cartesian handling solutions. Developed by the linear motion technology experts at Bosch Rexroth, this smart, multi-axis system drastically reduces engineering costs and allows commissioning within a few clicks. The Smart Function for Handling is ideal for a wide range of applications, including pick-and-place tasks in logistics, machine assembly, packaging technology and assembly processes. The plug-and-produce design speeds up the commissioning process to save time and reduce costs, from configuration to operation. Easy to select and size, the Smart Function Kit for Handling allows users to move from configuration to online ordering in a seamless process that reduces the potential for error.
Rexroth,
The kSA XRF metrology system measures the layer thickness of metal films and dielectric films that are too thin for reliable optical measurements. It provides inline measurements for films on many substrates and applications, including glass and solar panels. The system is comprised of an X-ray tube with a high voltage generator and an X-ray detector system. The system identifies the spectral peaks for the X-ray emission spectrum and collects the peak intensities for further processing. The tool measures the appropriate atomic species based on the customer’s coating formula and measurement needs. k-Space can integrate this tool into existing QC systems and add alarms to flag thickness issues in real time. k-Space, www.k-space.com Input #203 at www.controleng.com/information
The Visorguard-LED provides machine operators with super bright illumination of the working field. The Visorguard-LED’s unique Continuous LED strip lighting is integrated as part of the safety shield providing 6000K natural white light. Auto-Diffuse lighting produces no LED light hot spots. Flexbar’s Visorguard-LED system is water and coolant proof and installs in minutes on CNC mills, conventional mills, drill presses and more. The adjustable Flexbar arm permits setting of the Visorguard shield at the correct height and angle for each setup, then locks rigid. The special wing-shaped shield flips up to load a part and down for machining. A special spring-loaded shaft allows the shield to stay put with no spring back.
Flexbar Machine Corp., www.flexbar.com
The TDLS8100 is a tunable diode laser spectrometer that only requires a single-flange installation. An in-situ measurement with a probe removes the need for sample extraction and conditioning. It can be used in many aggressive process conditions. The probe’s 0.5-m measurement area provides some averaging improvement compared with traditional point-sensor technologies.
Yokogawa Corp. of America, www.yokogawa.com
Input #205 at www.controleng.com/information
#204 at www.controleng.com/information
Binder’s M16 connectors are designed to meet the data speeds, high frequencies, and tight space requirements for 5G wireless networks. Binder’s M16 connectors can now accommodate up to 24 contacts and transmit data at speeds up to 10Gbit/s. The connectors are compliant with AISG C485 standards, providing international protection for selected outdoor installations. The connectors are rated up to IP68 when connected, providing reliable performance in harsh outdoor environments. Binder USA, www.binder-usa.com Input #206 at www.controleng.com/information
Food processing operations need to be resilient during the COVID-19 pandemic and can achieve this by improving collaboration and enforcing consistency.
COVID-19 has put supply chains under the microscope and accelerated the need to build in production resilience. Resilience in food processing sector involves three levels of hierarchy.
• Sector-level resilience: Demand for fluid milk in the dairy sector of the food and beverage industry fell due to school and restaurants closures.
• Supply chain-level resilience: Supply sources have been disrupted. Migrant workers couldn’t travel to help with harvests. Transportation networks were disrupted reducing raw materials, cutting capacity.
• Production-level resilience: Even with raw material inputs, some companies could not adapt factory lines quickly enough to reconfigure bulk lines to support consumer packaging.
Four areas can help food processing operations boost resilience:
1. Improve collaboration across people and systems: A key factor for future manufacturing operations improvements is the effective collaboration of people and systems in a digital, automated and integrated fashion. The element that can bring these together in industrial operations is business process management (BPM) technology integrated with a manufacturing IT platform to connect with plant floor processes, people, data and systems.
The digital transformation of operational processes using a business process management system can capture and transform best practices into electronic workflows, connect assets and systems, establish systematic people and system collaboration, and empower a mobile and next-generation workforce. Enforcing consistency of operational procedures and the automation of workflows with electronic records of manufacturing execution activities and data, preserves investments in existing plant systems and offers significant operational efficiency improvements.
2. Rethink multi-site manufacturing operations transformation: Many manufacturing businesses have grown by mergers or acquisitions to become national, multinational or global organizations. These companies are equipped with multiple production plants across regions for producing the same, similar or variations of products. These multi-site enterprises also are changing to a broader transformative view of manufacturing to make use of new significant ROI opportunities unique on a business-wide basis: Busi-
ness-wide scorecards and consistent KPIs for transparency in cost, capacity and inventory across the enterprise; operational excellence, lean and continuous improvement cultures that need to collaborate and share best practices; a consistent, documented approach to regulatory compliance to minimize risks; a connected enterprise for visualization and accessibility of information anywhere and anytime to increase business agility and speed innovation and reduces cost of ownership. Having fewer applications can facilitate IT and operational standards.
3. Standardize processes, key performance indicators (KPIs) and plant integration: The primary enabler of an effective multi-site manufacturing operations transformation is the enterprise-wide standardization of operational processes, enabled through digital transformation. Such IT harmonization is the foundation to digitally model, integrate, execute, and govern operational processes and related information flow consistently across multiple plants.
4. Adapt and maintain operational excellence: Businesses have the opportunity to adapt and maintain operational excellence in volatile times through digital transformation. The current crisis is accelerating cloud and the use of data in increasingly sophisticated ways to provide visibility and certainty into operations. The adoption of analytics drives digital transformation, as businesses seek greater data-driven insights. Data acts as a source of truth that focusses teams on the critical factors that determine business resilience. Connectivity is key, and a solution should have built-in connectivity to existing plant floor systems, devices and equipment automation. It is vital to ensure an easy-to-use, accessible user interface for a processbased approach to manufacturing operations management. ce
Sree Hameed is global marketing manager for food, beverage and consumer goods industry at Aveva. This article originally appeared on Control Engineering Europe’s website. Edited by Chris Vavra, web content manager, Control Engineering, CFE Media and Technology, cvavra@cfemedia.com.
‘Current crisis is accelerating cloud and the use of data in increasingly sophisticated ways to provide visibility.’
KEYWORDS: Key performance
indicators, food processing
Context is important when it comes to production resilience in food manufacturing.
Companies should improve collaboration and maintain operational excellence.
Standard processes can enhance benefits in operations.
ONLINE www.controleng.com/ iiot-industrie-4-0
CONSIDER THIS
What other ways could companies assurance resilience in their food processing operations?
. .10 . . . .www .fiboxusa .com
HAMMOND MANUFACTURING . .7 . . . . .5 . . . .www .hammondmfg .com
Lenze . . . . . . . . . . . . . . . . . .39 . . . . .14 . . . .www .Lenze .com
RADWELL INTERNATIONAL, INC .17 . . . . .11 . . . .www .Radwell .com
Sealevel Systems Inc . . . . . . . . .15 . . . . .9 . . . .www .sealevel .com
SEW-EURODRIVE, Inc . . . . . . . . .C4 . . . . .36 . . . .www .seweurodrive .com
WAGO Corp . . . . . . . . . . . . . . .35, 37 . .12, 13 . . .www .wago .us
Inside Machines
Aerotech Inc . . . . . . . . . . . . . .M2 . . . . .15 . . . .www .aerotech .com
REQUEST MORE INFORMATION about products and advertisers in this issue by using the http://controleng.com/information link and reader service number located near each. If you’re reading the digital edition, the link will be live. When you contact a company directly, please let them know you read about them in Control Engineering.
ContentStream
Patrick Lynch,
Director of Content Marketing Solutions
630-571-4070 x2210
PLynch@CFEMedia.com
AR, IL, IN, IA, KS, KY, LA, MN, MO, MS, NE, ND, OK, OH, SD, TX, WI, Central Canada
Robert Levinger 630-571-4070 x2218
RLevinger@cfetechnology.com
AK, AZ, CA, CO, HI, ID, MT, NV, NM, OR, UT, WA, WY, Western Canada
Aaron Maassen
816-797-9969
AMaassen@CFEMedia.com
CT, DE, MD, ME, MA, NC, NH, NY, NJ, PA, RI, SC, VA, VT, WV, DC, Eastern Canada
Julie Timbol (978) 929-9495
JTimbol@CFEMedia.com
Jim Langhenry, Co-Founder/Publisher, CFE Media JLanghenry@CFEMedia.com
Steve Rourke, Co-Founder, CFE Media SRourke@CFEMedia.com
Courtney Murphy, Marketing Services Manager 630-229-3057 CMurphy@cfemedia.com
McKenzie Burns, Marketing and Events Manager mburns@cfemedia.com
Brian Gross, Marketing Consultant, Global SI Database 630-571-4070, x2217, BGross@CFEMedia.com
Michael Smith, Creative Director 630-779-8910, MSmith@CFEMedia.com
Paul Brouch, Director of Operations PBrouch@CFEMedia.com
Michael Rotz, Print Production Manager 717-766-0211 x4207, Fax: 717-506-7238 mike.rotz@frycomm.com
Maria Bartell, Account Director, Infogroup Targeting Solutions 847-378-2275, maria.bartell@infogroup.com
Rick Ellis, Audience Management Director 303-246-1250, REllis@CFEMedia.com
Letters to the editor: Please
MHoske@CFEMedia.com
include name,
Information: For a Media
fax 630-214-4504.
go to www.controleng.com/mediainfo.
Marketing consultants: See ad index.
Custom reprints, electronic: Shelby Pelon, Wright’s Media, 281-419-5725 x138, cfemedia@wrightsmedia.com
Tired of working nights and weekends on motion control projects? It’s time to contact an automation specialist at SEW-EURODRIVE to help solve your design challenges.
Using the latest innovation, we provide complete package from start to finish including, project planning, design, software, components, commissioning, and worldwide support.
Go home . . . we got this!