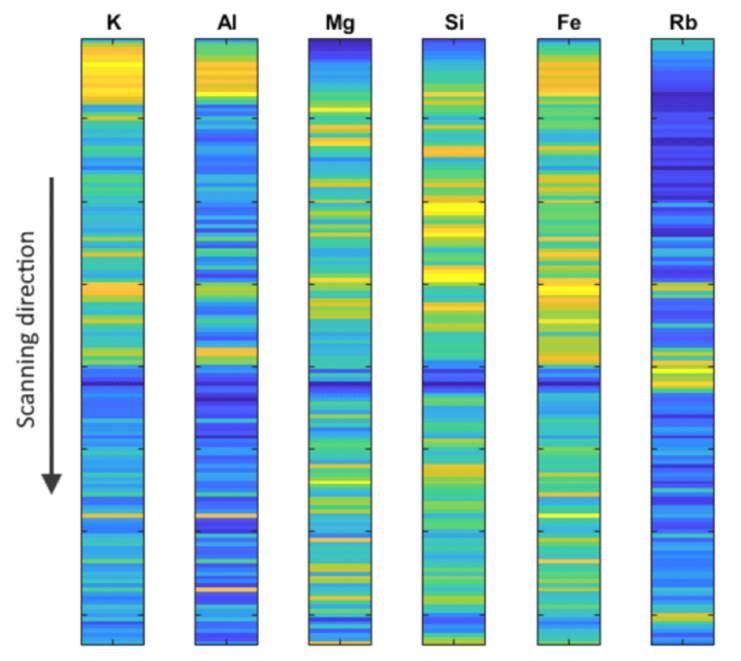
6 minute read
LIBS CHEMICAL SENSING APPLICATIONS IN THE MINING AND MINERALS INDUSTRY
The mining industry is faced with an increasing scarcity of natural resources. At the same me, the global demand for resources keeps growing and the requirement to reduce the environmental footprint of mining becomes more important. This creates the need to develop innovave soluons that increase the efficiency and sustainability of mining natural resources.
Mining operaons deal with huge quanes of excavated material with varying mineral concentraons and economic value. Increased knowledge about the composion of this material provides opportunies to improve decision making for stockpiling, sorng, and mineral processing. However, no systems currently exist that can be used to measure the chemical composion of large material quanes in real-me. LIBS chemical sensor technology provides a soluon, because no sample preparaon is required and measurements can be performed at relavely high speeds.
Advertisement
At SPECTRAL Industries we work together with the mining industry to develop LIBS-based sensor applicaons for the mining environment. Examples of applicaons are inline conveyor belt analysis, scanning exposed rock surfaces (see Figure 1) and scanning drill chips from blasthole drilling. Addionally, we also work on applicaons that improve the exploraon for new mineral deposits such as the scanning of drill cores (see Figure 2). We develop the best LIBS sensor for a specific applicaon using our in-depth experse of lasers, spectrometers and data processing.
One of the major challenges of using LIBS for characterizing the mineral quanty in rocks is the heterogeneity of this material. Rocks are composed of many different minerals with various grain sizes. Each mineral consists of several different elements and for some minerals the relave quanty of these elements can vary. Depending on the size of the mineral grains, a single LIBS measurement can represent one or several minerals. Development of advanced data processing techniques is therefore required in order to provide quantave composional informaon that meets the required accuracy. Addionally, calibraons need to be tailored to the geological seng of a specific mineral deposit to take all the variaon between rock types and mineralogy into account.
The results obtained using LIBS chemical sensing on ore samples from acve mining operaons show that LIBS can be used to provide the informaon that is needed to improve the efficiency and sustainability of future mining.
SPECTRAL Industries is a new chemical sensor developer and manufacturer, with a focus on applicaons in the mining and minerals industry. SPECTRAL's chemical sensors are robust, mobile & fast: they can be applied on (fast) moving raw material. The sensor features our unique IRIS spectrometer with world-class signal-to-noise (S/N) rao, rugged pulse laser source and highly efficient opcs. The design allows for flexible integraon into industrial equipment and can be mounted in any orientaon. Suitable for a wide range of environmental condions, it offers low maintenance cost and improves processes by delivering real-me informaon. SPECTRAL delivers its unique sensor systems for the following applicaons: • Drill core scanning • Rock surface mapping • Drill cungs analysis • Ore, concentrate and slag characterizaon • Muck pile characterizaon
The LIBX sensor can be applied for automated ore sorng, that separates valuable from non-valuable rocks to prevent unnecessary cost for processing worthless ore and maximize return on investment. The technology is highly scalable as the hardware is suitable for any type of ore and materials.
Example of part of the output of a drill core scan (warmer colors are higher concentrations)
maas@spectral-i.com

Airless Tyres for Underground Mining
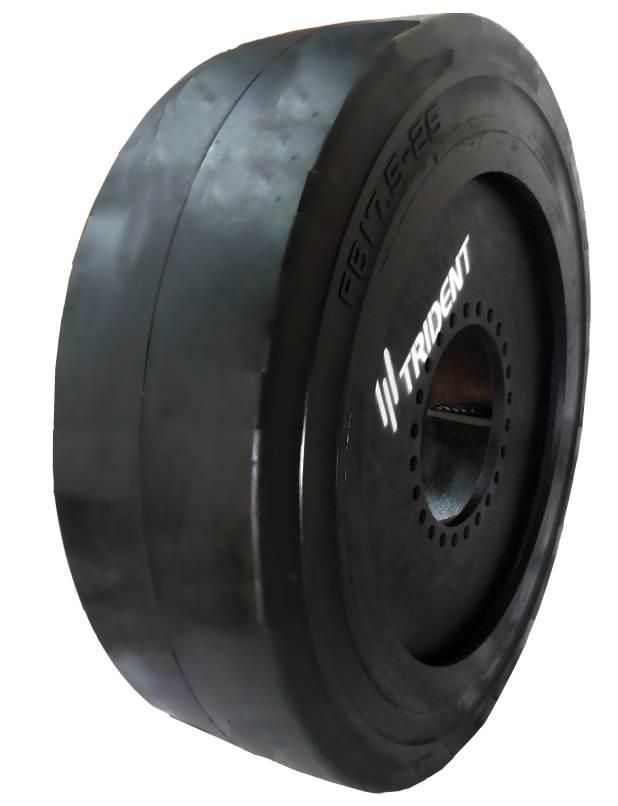
Tyres used in underground mining are replaced frequently as they are prone to punctures, sidewall damage and fast tyre wear due to harsh underfoot condions, ght working spaces, high loads & overall severe operang environment. The frequent repair & related downme results in increased operang costs and safety risks. Tyre related costs are esmated to be among the top five operang costs for mining equipment. It is therefore imperave for mine operators to explore opons such as Airless Tyres that have the following advantages over pneumac tyres: · Airless – hence are 100% puncture proof · Increased Safety – There is no risk of tyre blowouts · Extended Limp-in Capability – machine doesn't get stuck inside a mine · Reduced Tyre Maintenance – Periodic inflaon pressure checks are eliminated There are 2 major prevalent alternaves for airless tyres i.e. Solid Tyres and Foam-filled Pneumac Tyres. Solid tyres are generally used for high load, short haul and low speed applicaons whereas Foam-filled tyres are suitable for longer haul cycles, higher speeds and where ride comfort is required. It is important for users to select the right product based on their applicaon, equipment and operang condions to reduce cost per hour (CPH) and bring down total cost of ownership (TCO).
1/ Solid Tyres:
Solid tyres have a full rubber construcon and thus are airless & puncture proof, have an extra deep tread for long, uninterrupted service, with specially designed sidewall apertures for shock absorpon. However, these are not suitable for speeds beyond 25 kmph & have a firm ride. Solid tyres are available in a range of paerns like to suit various operang condions & can also be supplied as ready to fit.
Solid tyres are suitable for equipment operang at low speeds such as: · Load Haul Dumpers (LHDs) · Jumbo Drills / Roof Bolters · Shield Haulers · Shule Cars / Ram Cars · Ulity Vehicles
In addion to the advantages of airless tyres menoned above, the solid tyres are: · Highly damage resistant · Have a Long Life – typically 2-4 mes that of foam filled pneumac tyres · Ready to use
2/ Foam-Filled Tyres:
Tyre Filling (or Foam Filling) is a process in which a pneumac tyre is injected &
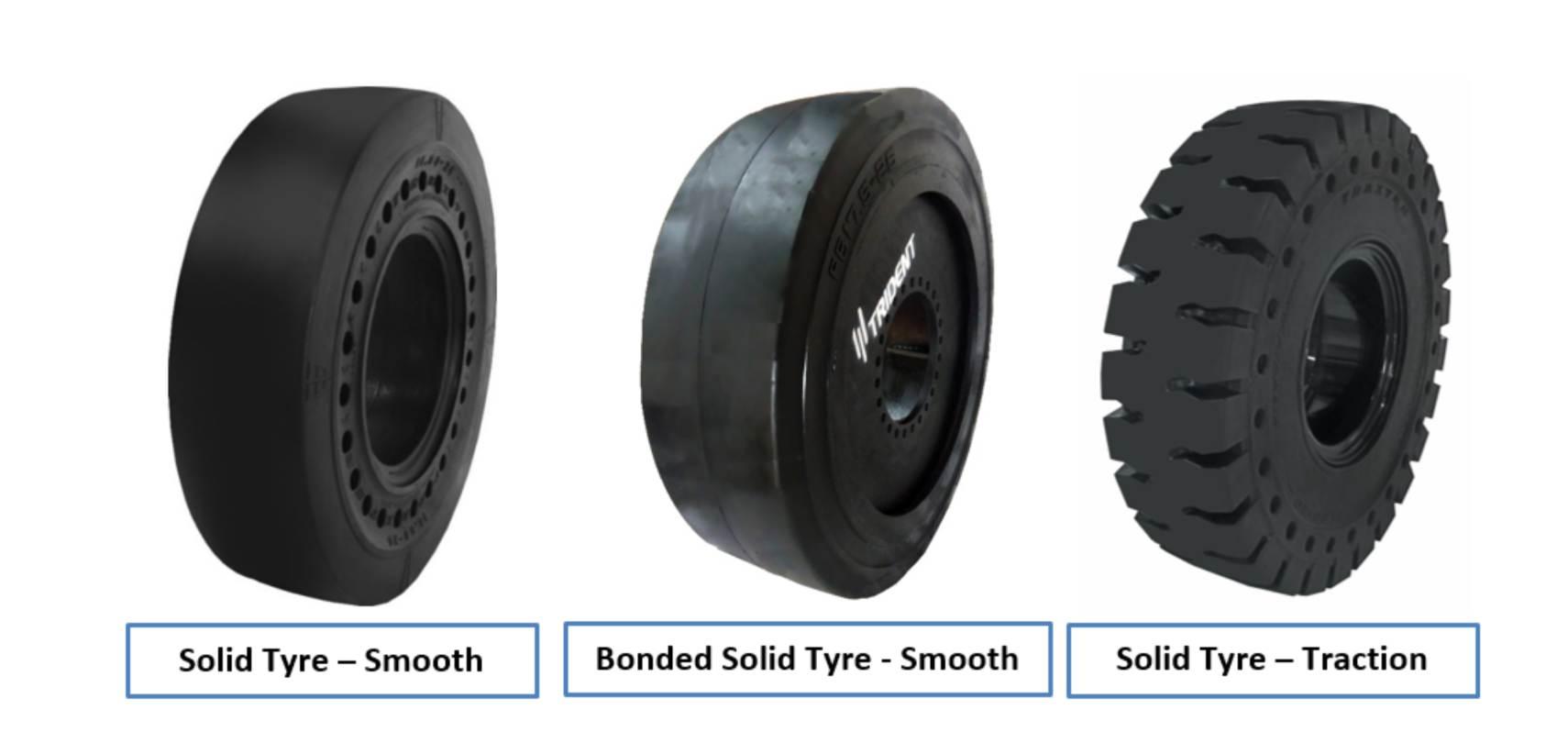

pressurized with a two or three component urethane polymer in a precise proporon using a special metering pump. The polyurethane cures into a resilient and synthec rubber core replacing the air in the tyre. The resultant filled tyre is thus rendered puncture proof and maintains the required pressure throughout its service life. Foamfilled tyres have a full footprint & are capable of carrying their rated load at all mes. Tyre Fill Compounds are available in different grades based on applicaon.
Foam filled tyres are recommended for vehicles that operate at speeds upto 50 kmph & for machines for which solid tyres are not suitable e.g. · Low Profile Dump Trucks (LPDT's) · Personnel Carriers
While these can also be used on LHD's, Shule Cars, Ulity Vehicles etc. it needs to be borne in mind that although foam filled tyres are airless & puncture proof they may sll suffer irreparable damage & may have to replaced prematurely.
Equipment owners should evaluate various parameters (see table 1) and select the right airless tyre depending on their equipment and applicaon for lowest operang costs & opmum capital efficiency About Trident: Trident has developed applicaon specific, outcome orientated products and soluons to assist machine owners & mine operators get the best out of their equipment in the most demanding condions. Our products are distributed in over 25 countries which include the Americas, Europe, Africa, the Middle East and Asia-Pacific.
For further informaon please visit www.trident-intl.com or write to ankit@trident-intl.com
Foam-filled Tyre
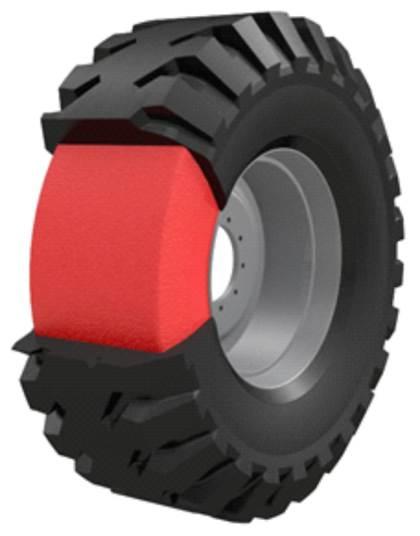
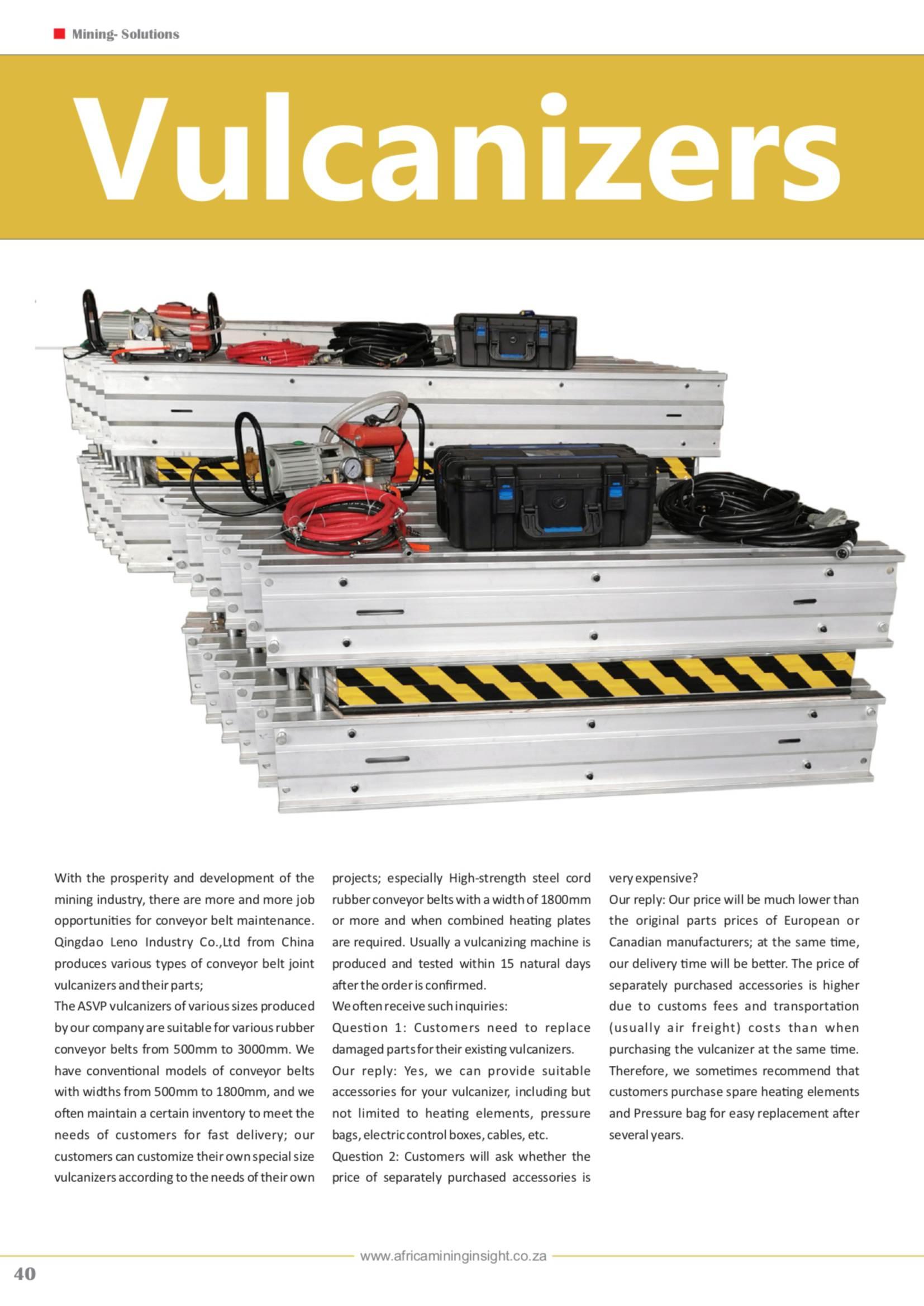
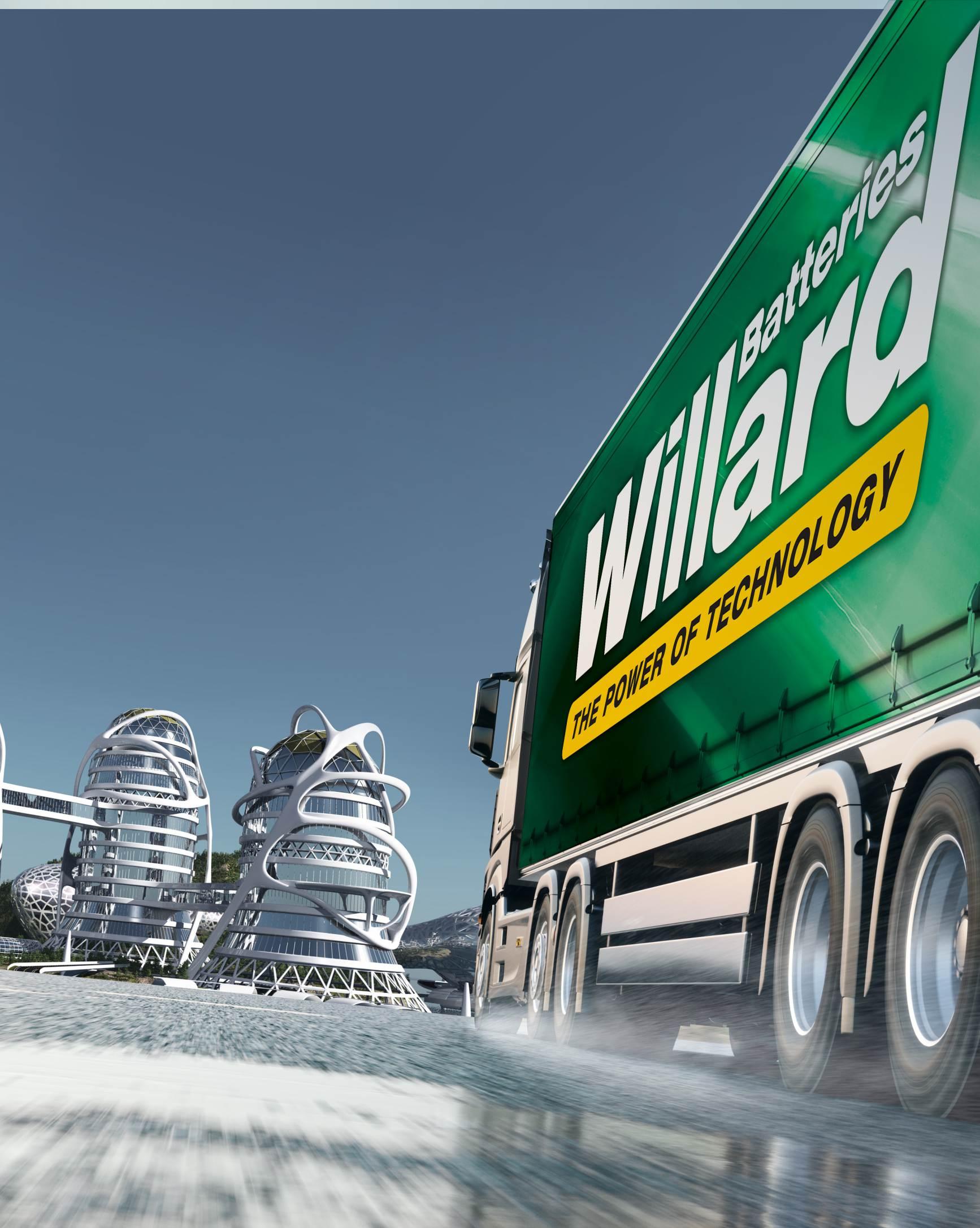
