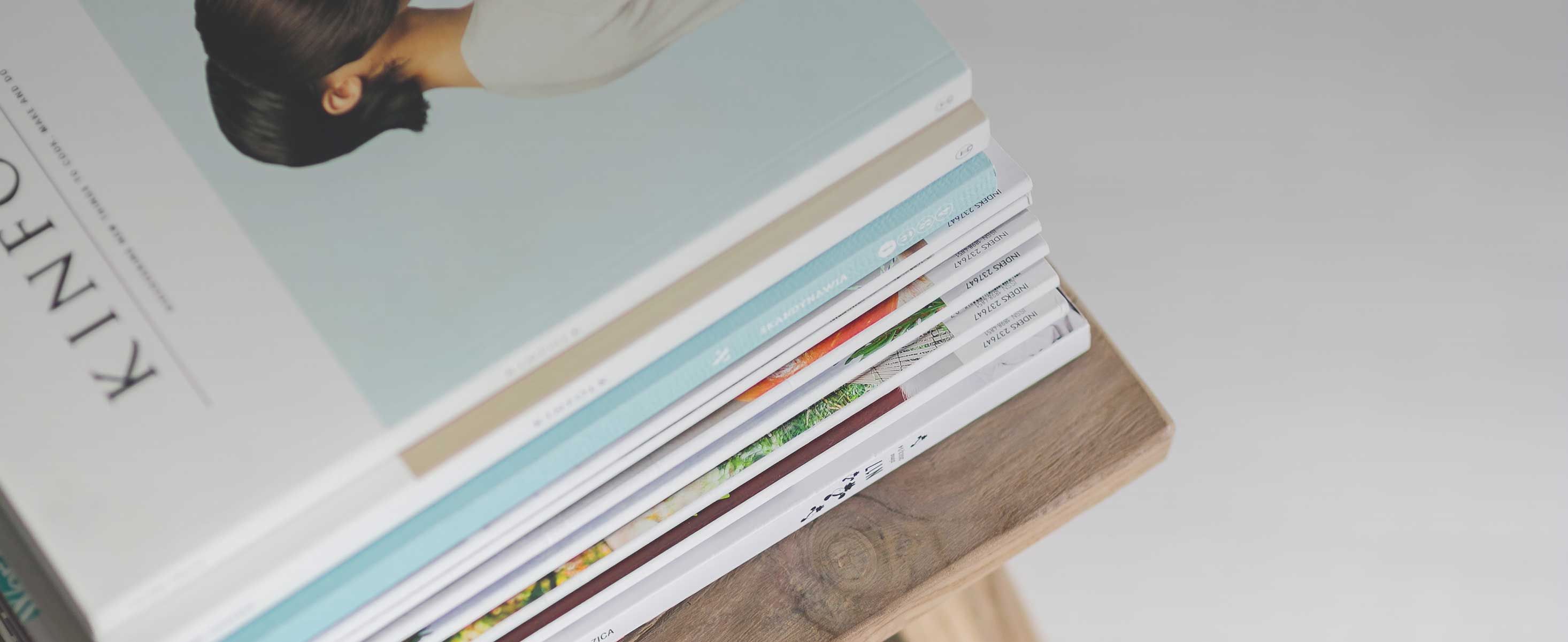
6 minute read
Conclusion
Connexion avec tenon et mortaise traversante 126
c. Conclusion These seals can be prefabricated, brought to the site and assembled. The more precise they are, the more rigid they are. They have long been hand-cut, but today, the development of subtractive manufacturing technologies, such as CNC, allows them to be produced with a high level of fineness. While the preparation is quite complex, the assembly is easier, almost intuitive. The same applies to reuse, the elements are not damaged since no additional physical intervention is required to maintain them. The location of the notches provides a fairly precise direction to the final shape and the flexibility of the nexorades is no longer really considered. However, it is one of the most discreet methods of structural expression. The notch makes the whole thing uniform by giving it a homogeneous thickness over its entire extent. Nevertheless, the incisions, by reducing the size of the section in some places, therefore reduce the structural strength of the part.
Advertisement
From this family comes a whole series of self-locking digital joints, which attempt to fully integrate the connection elements of other types into the design of the parts. There is a huge stake in the development of this kind of link in digital manufacturing, as it opens up the field of possibilities and promotes a strong technical symbiosis. We are witnessing the emergence of an innovative construction language due to the use of these tools.
2.19. Towards an integrated wood-wood joint
In wood construction, half of the budget is allocated to the material, and the other half to installation and connections.78 Consequently, wood construction requires an important planning process, which is also found in carpentry techniques. Integrated joint systems are therefore interesting, because if they require some study, the cost of the joint can be drastically reduced. At the same time, it concerns the purity of the material, which maintains its natural expression. In this case, it is wise to minimize the optimization of this preparation time by seeking innovative approaches. Inspiration for such improvements is often drawn from old assembly methods such as mortise and tenon, dovetail or toothed assemblies, which were common craft techniques in traditional carpentry and cabinet making. Historically during the proliferation of the industry, these seals have been largely replaced by mass-produced metal plate connectors and fasteners. But today, the boon created by algorithms and digital technologies offers new opportunities for mechanical integration and a resurgence of the interest in wood construction. These joints are often made using a digital milling machine and are a new vocabulary in carpentry.79 This recent vocabulary is a reinterpretation of these traditional couplings through the constraints of digital tools. This is all the more important in reciprocal structures, because the principle of spatial composition limits connections to two elements in the same place. As the connections are generally simple, it is possible to make extensive use of this entire connection directory. This phenomenon is further amplified by the relationship between nexorades and computational design. It is sometimes a question of interpreting all the parts of a structure differently and algorithms are essential tools to define all the connection details.
There is even a collection of fifty of these joints developed by Jochen Gros80 and intended, thanks to its open source availability, to support a broad artisanal experimentation that will itself serve as inspiration for pavilions, which in turn will open the way to new construction techniques.
Collection of fity joints aimed for digital fabrication, developped by Jochen Gros127
2.20. Integrating research into practice
It is necessary to question the extent of all these researches and their scope in an architectural reality. While the scientific production relating to reciprocal structures is important, this is not the case for its integration into construction. Computational architecture, by its inherent complexity, is not specifically accessible. In this case, how is such research supposed to end up in the architecture project? Salvator-John Liotta offers two approaches, either the designers develop a research project themselves or they integrate students who have participated in similar projects. This approach is becoming more and more frequent, as there is a growing interest on the part of students in a return to learning through tangible construction, which helps them to move somewhat outside the theoretical environment of the university. Nevertheless, between small experimental projects and their more concrete applications, several constraints arise, particularly from the legal and budgetary point of view. Indeed, the few requirements linked to architectural exploration through a pavilion without a specific function allow a great freedom. Budgets are often covered by individual sponsors and are not subject to this pressure from investors, who tend to regulate the scope of architects’ activities according to economic objectives.81 Nevertheless, it is through this integration of research into practice that a study can become concrete and it is important for architects to consider such initiatives. Digital democratization makes these explorations more and more accessible and less and less economically risky. The integration of a technique developed in a theoretical context into a concrete project is a form of maturation that will allow this technique to have its own autonomy, to spread and gradually improve in architectural design.
90
3. FORM-FINDING AND PROTOTYPES
Research framework
By combining the work on tesselation, connection and optimization, we obtain a complex, but potentially algorithmically solvable device. With the intention of experimenting with what was presented earlier, I have personally undertaken the production of a series of small scale prototypes that will use, as far as my skills obtained during my architectural studies will allow me, the informations gathered during this exploration. My objective was to propose a reciprocal system that would be productible using two-dimensional cutting, in order to maximize its flexibility. It can also limit the need for digital technology to what is available in the laboratory (3D printer, laser cutter, digital milling machine), which are accessible tools for a traditional architectural practice. The project seeks to be in line with the same direction as the Wikihouse, i. e. the production of a configurable object from a standard resource, such as multiplex boards. The algorithm is responsible for transforming a guide surface into a system of connectable elements, without additional elements, while maintaining the material and formal unity. The algorithm is written on Grasshopper for the reasons cited at the beginning of the brief and will explore the various strategies for form-finding developed for reciprocal structures. We will see three of them through as many prototypes: by rotation, by translation and by cells. Not all methods give the same approximations for the eccentricity values and therefore it is necessary to study the specific optimization mode(s) for each approach. The use of planar parts and limited digital manufacturing implies symmetry between its two sides. A laser cutter can only cut a material perpendicular to its surface and if a CNC can dig diagonally, it can only do so on the upper side, the other being glued to the base. To work on both sides, several operations are required. However, a reciprocal structure has very variable contact angles, it is therefore essential to rationalize this by subdividing the guide surface into a series of parts adapted to the format of the boards from which they will be cut, or even to the dimensions of the machines that will carry out this task. It should be kept in mind that this list of methods is not exhaustive, there are many others and as the investigation of the behaviour of these structures continues, new ones will emerge. These methods thus have all their optimization operations, i.e. to ensure that the parts have the right measurements to be adjusted at their various points of contact. However, these optimization methods are not always accessible and the ones presented here are sometimes the result of my own research. In addition, these experiments are based on reciprocal structures that have emerged and been carried out using tesselations.
It is also possible to draw them on the basis of a conformal map that reproduces a two-dimensional three-dimensional reciprocal pattern or with a generative algorithm, which multiplies a rule in a Botom-Up approach. I will therefore explore a Top-Down strategy, from the point of view of an architect who seeks to have advanced control over the form of his project.