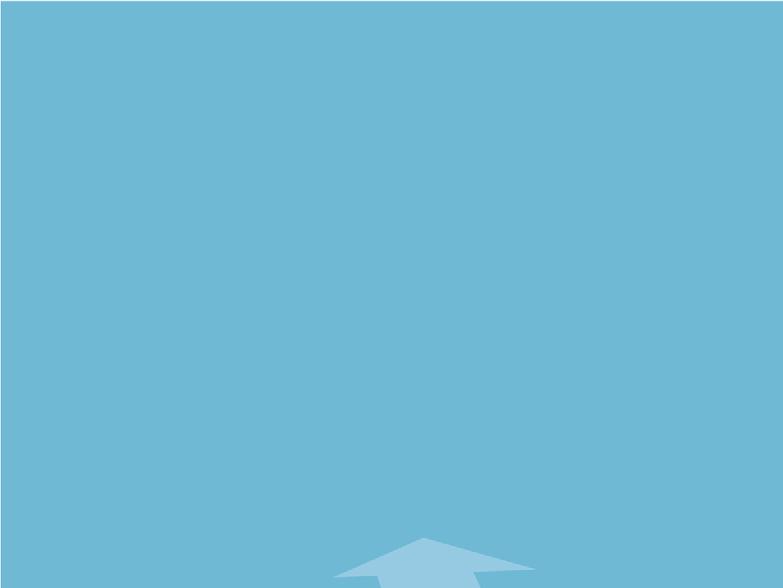
10 minute read
Blue routes
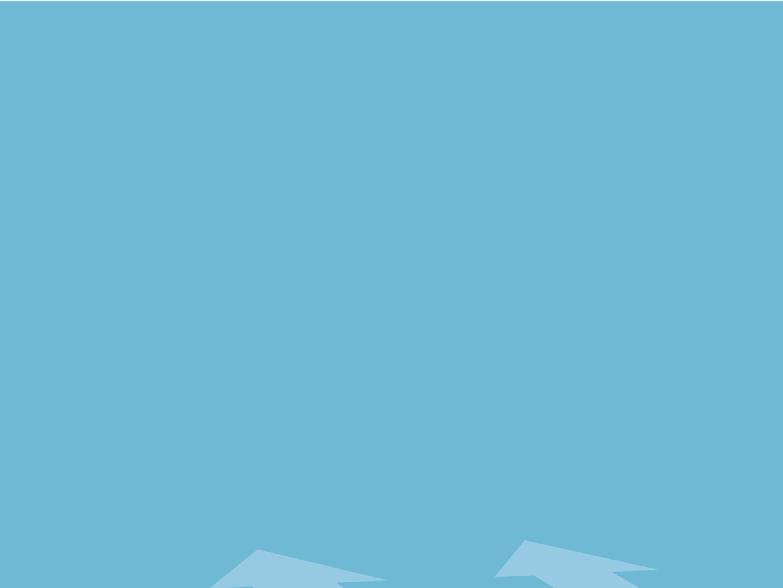
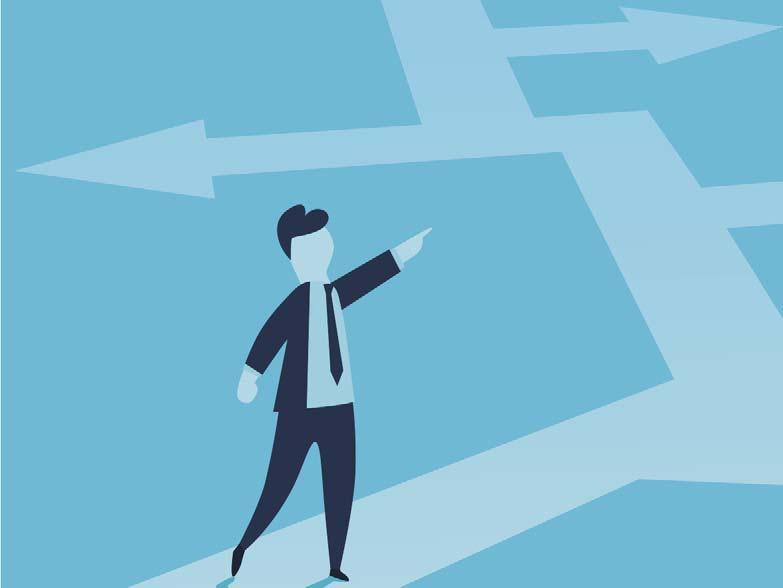
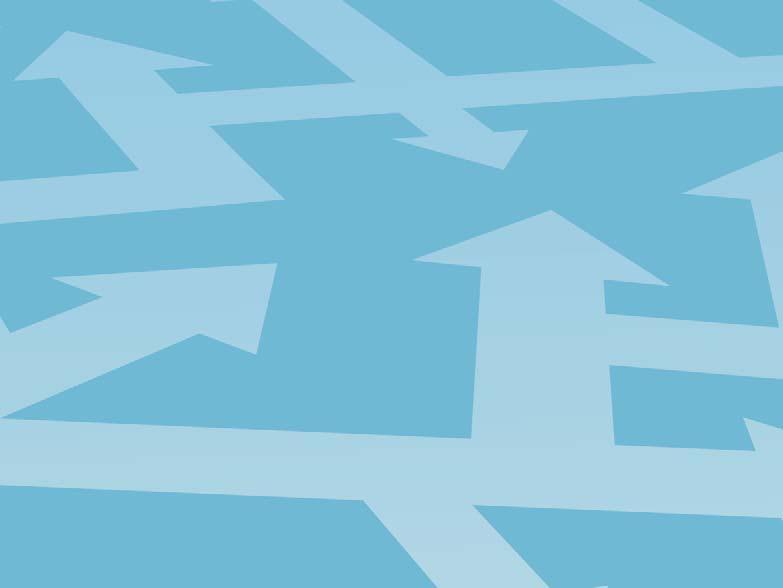
Elias Xanthoulis, Andrew Board, Attila Racz and Tobias Roelofs, Comprimo, part of Worley, look at typical routes to blue hydrogen production, and how to maximise CO2 removal at high thermal efficiency in blue hydrogen facilities.


The need for decarbonisation of existing industrial operations drives the need for higher volumes of hydrogen production in many areas of the world. As the promise of large-scale green hydrogen is still some time away, reforming of natural gas, as currently applied in many installations, will continue to play a key role in the transition towards meeting the Paris Agreement goals. Adding CO2 capture to existing reforming installations and new greenfi eld natural gas reforming hydrogen production installations is a fi rst step in reducing carbon emissions but warrants the question: at what capital and operational costs? The predominant operating cost in a reforming unit is due to the natural gas. In addition, the pricing of CO2 emissions in the EU-ETS has reached an all-time high1 contributing to current and future OPEX while validating the economic need for carbon capture. The different process line-ups in blue hydrogen production determine the height of the initial investment while the extent of carbon removal varies. This article seeks to provide an answer to the question above by assessing the main blue hydrogen line-up options, by focusing on the most important techno-economic parameters of the processes, namely thermal effi ciency and their respective carbon capture rates achievable, to produce the required hydrogen purity.
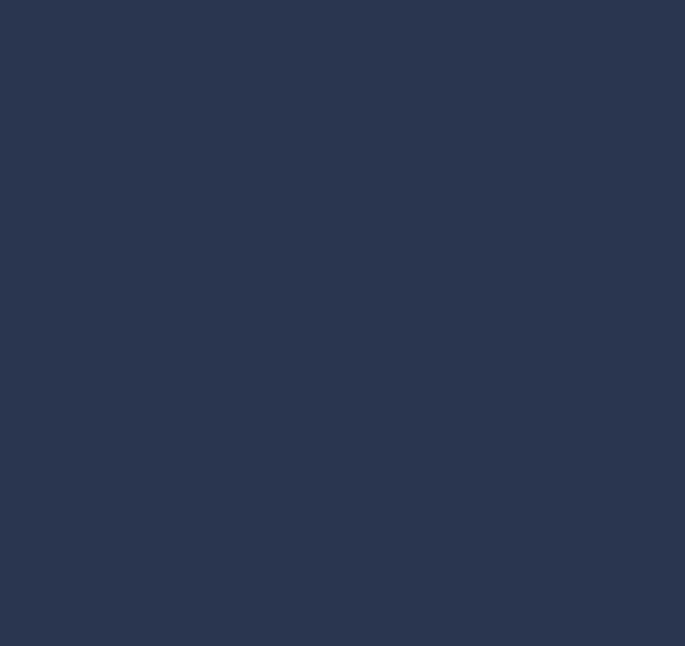
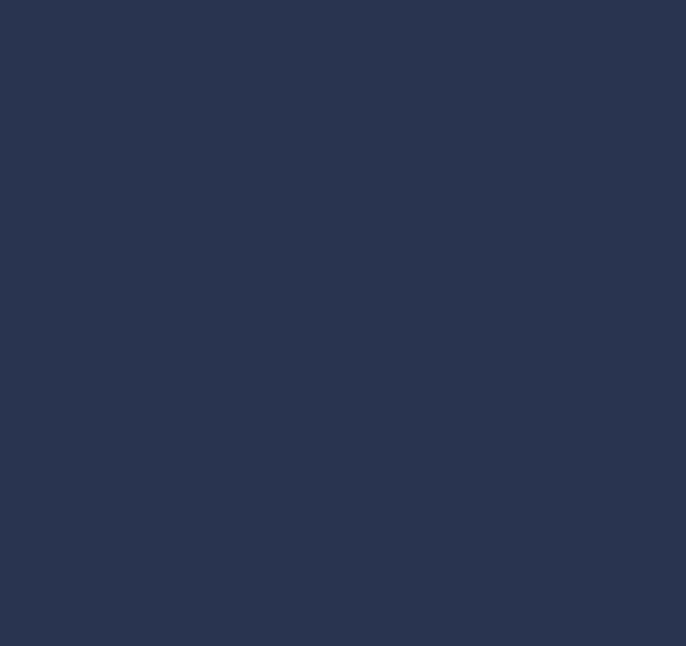
Characteristics of a blue hydrogen plant
A blue hydrogen facility has three signifi cant design parameters: Carbon capture – requirement of a minimum of 90 to 95% total carbon capture (95%+ is rapidly becoming the benchmark). Thermal efficiency – requirement for high thermal efficiency targeting 75 to 80% (HHV basis, including power required), especially when natural gas cost is a significant factor, which is nearly always the case. Hydrogen quality – ensuring high quality industrial hydrogen production, such as meeting the ISO 14687
Hydrogen Fuel Quality, which requires H2 of a minimum of 98 mol% purity, and strict specification of level of impurities such as CO (CO <1ppmv).
The hydrogen purity specifi cation can be achieved via a pressure swing adsorption (PSA) or methanation purifi cation step in which the design is actually governed not by the hydrogen purity but by the CO product specifi cation. Specifi c to the PSA is the loss in the tail gas of approximately 6 to 8% of the feed to a PSA. The tail gas contains approximately 70 vol% hydrogen and it needs to be utilised as fuel gas in the
fi red heater burners or elsewhere. A methanator step could be more cost-effective, however methanation requires dewpointing to remove water to the required specifi cation to prevent condensation in the downstream hydrogen pipeline, whereas PSA will reject water with the tailgas. A methanator is considered a more effi cient option compared to a PSA, as more calorifi c content is retained within the product gas, but this depends on fi nal product quality requirements.
There are two broad reforming methods of producing blue hydrogen: the conventional approach using steam methane reforming (SMR), and the oxygen-based approach, which lends itself to a number of commercially available processes, such as combined reforming, autothermal reforming (ATR), heat exchange reforming, and partial oxidation (POx).
All of the these methods are catalytic processes with the exception of partial oxidation.
The carbon capture rate also plays a role in later operations as the price of CO2 emissions will gradually increase, with recent EU-ETS prices exceeding expectations already. Therefore, maximising removal rates is both an environmental and economic driver. CO2 capture can be accomplished via: absorption in a solvent (physical or chemical), cryogenic based removal, and the use of membranes or solid adsorbents. In general, CO2 is compressed and/or liquefi ed for transport or usage. The use of commercially available amine-based solvents is the most common and mature technology option. Variations in performance are mainly derived from the use of proprietary and more formulated solvents. This includes lower energy consumption in the regeneration section or increased loading capacity reducing the overall circulation fl ow rate. Other upcoming technologies include the use of membranes and solid adsorbents. Membranes could be advantageous through a lower energy demand, installation cost and plot space requirement in the case of high concentrations of CO2. Solid adsorbents are typically regenerable (thermal/pressure) and could outcompete the energy demand of amine-based systems in the future. For all technologies, developments are still ongoing and relative rates of adoption could change in the future. In blue hydrogen line-ups, the option of pre- or post-combustion capture plays a large role in the extent of carbon removal.
Typical blue hydrogen routes
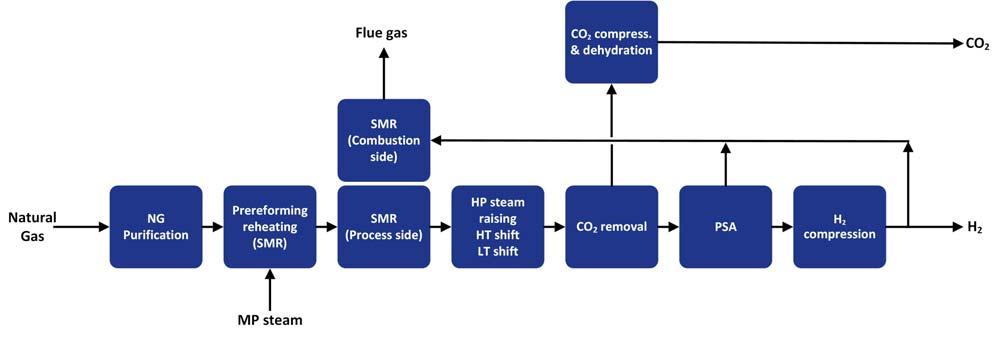
Reforming of natural gas is an endothermic process requiring fuel provision for the reaction heat. Conventionally, this heat is provided by using natural gas as the fuel, the combustion of which results in signifi cant quantities of CO2 produced. One of the fundamental considerations is the source of this energy/fuel. Instead of utilising natural gas, product hydrogen can be used instead. Figures 1 and 2 show an SMR path to blue hydrogen using hydrogen or natural gas as the fuel source. The main advantage of the SMR route is the fact that expensive-to-produce oxygen is not required as a feedstock. However, the process produces more CO2 per kg of feed gas than oxygen fed reforming routes. This requires carbon capture, limiting the effi ciency of the process if high CO2 capture targets are to be realised. Attempting to limit the CO2 production by using product hydrogen as the fuel gas decreases production effi ciency and limits achievable carbon capture rates to just over 80%. On the other hand, using natural gas as the fuel to the reformer in order to remedy this requires the addition of post-combustion capture on the combustion side of the SMR. This fl owsheet option can achieve CO2 capture targets of 95%, but at the expense of reduced thermal effi ciencies Figure 1. Typical SMR flow scheme with pre-combustion CO2 capture. (well below 75%). An ATR process provides an option of reforming hydrogen, with an overall lower CO2 production footprint. However, it requires a costly air separation unit (ASU) to provide the oxygen feedstock. A number of options exist to optimise the ATR fl owsheet (as shown in Figure 3): Optimisation of the reformer operating conditions while still meeting the carbon Figure 2. Typical SMR flow scheme with post-combustion CO2 capture. capture criteria for the project.
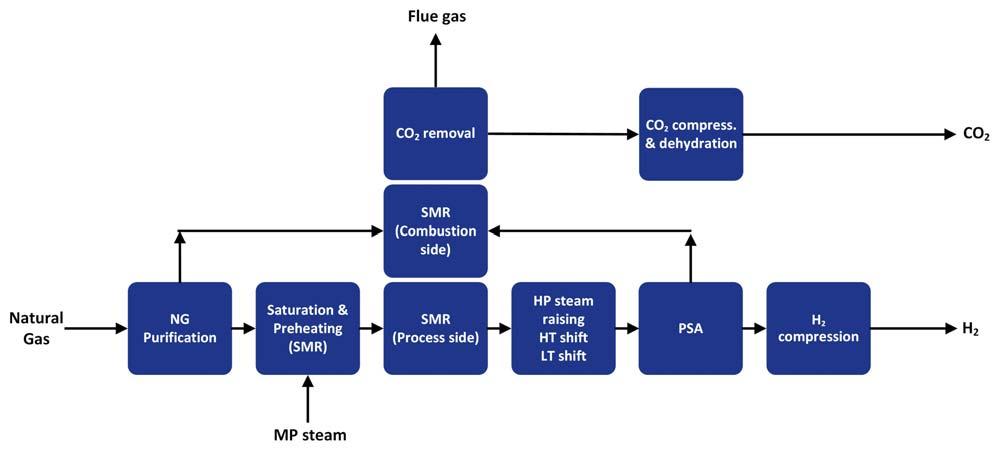
Optimisation of the steam system to minimise fuel consumption. Optimisation of the pre-combustion carbon capture (solvent based) flowsheet to reduce thermal demand.
Implementing the above unit operations has shown to achieve CO2 capture targets above 95%, while maintaining thermal hydrogen production effi ciencies approaching 80% (on an HHV basis).
A single ATR train can achieve up to 400 kNm3/hr of hydrogen production (dependent on confi guration), which is considered to be advantageous. This is a signifi cant production capacity if one considers that most installed conventional grey hydrogen production plants rarely exceed 200 kNm3/hr.
An option to minimise the expense of oxygen production is to have a combined reforming process, which utilises a combination of ATR and SMR, thereby requiring less oxygen. This fl owsheet, suitable for the larger hydrogen production capacities, does have effi ciency advantages over the SMR scheme. The scheme would be able to achieve 95% as the syngas methane slip is controlled by the ATR. However, the cost to achieve the required performance can make this option unattractive compared to the other reforming options.
Another option is to combine the ATR with heat exchange reforming (parallel or series arrangement), which increases overall thermal effi ciency by removing the SMR component. However, it introduces a heat exchange arrangement, which limits the capacity of a single unit due to fabrication limits on the size of the heat exchange reformer. The major advantage of this scheme (as shown in Figure 4), especially the series arrangement, is the capability of capture rates in excess of 97%, at high thermal effi ciencies of 80% (HHV), hence offering a technically optimum solution. However, especially for the higher capacity options considered for some of the developments (where two or more trains of heat exchange reformers would be needed), the additional gas-heated reformer (GHR) contributes and elevates overall costs. This confi guration has limited commercial references. POx offers a non-catalytic route to blue hydrogen,
Figure 3. Typical ATR flow scheme with pre-combustion CO2 capture.
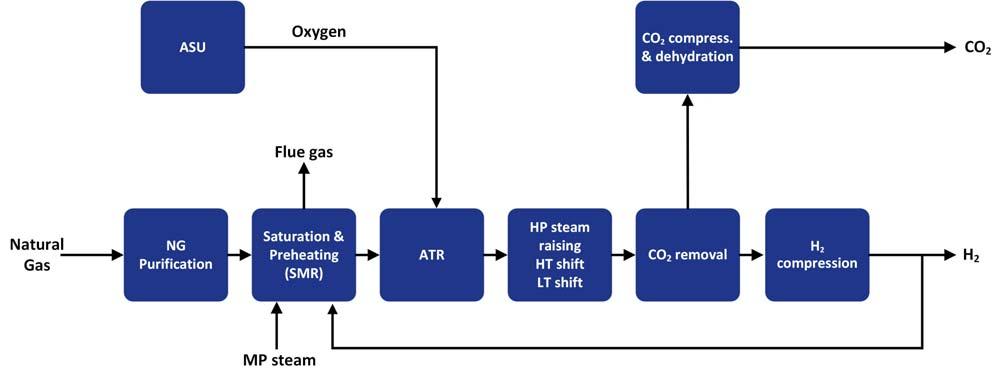
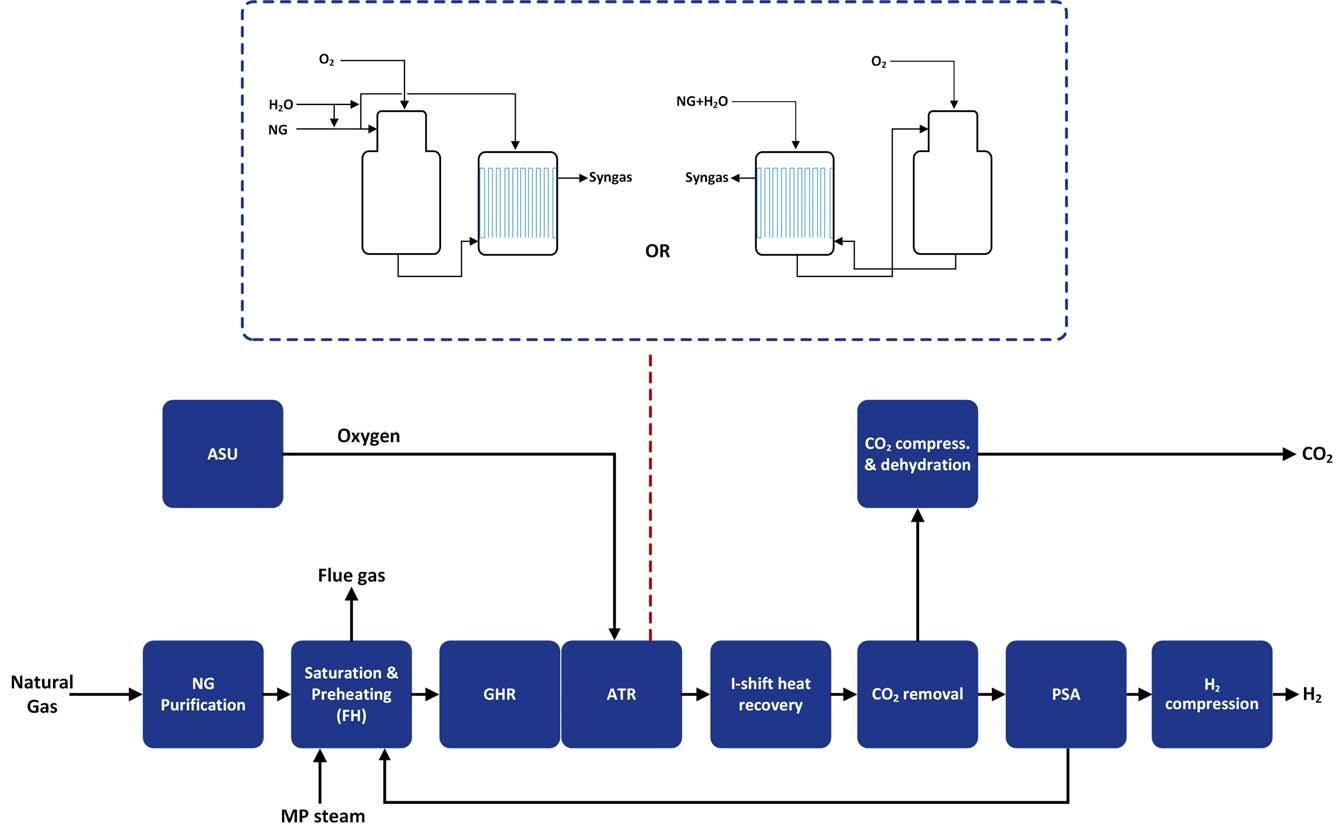
Figure 4. Heat exchange reforming scheme.
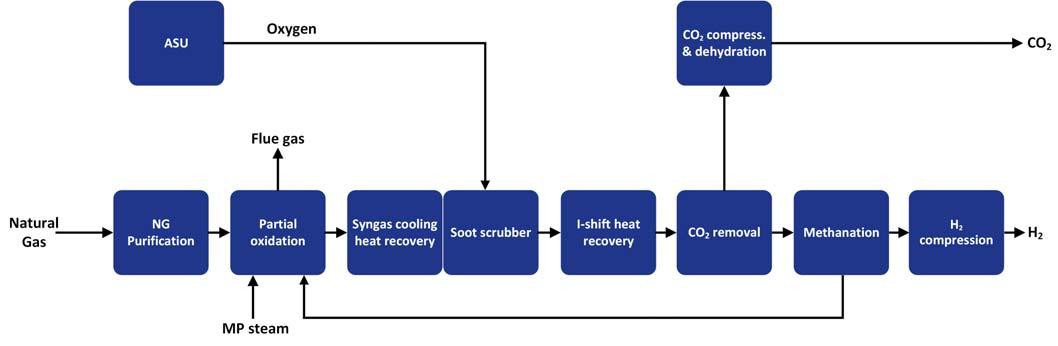
Figure 5. Typical POx flow scheme (non-catalytic).
Conclusion
achieving 95%+ CO2 capture targets. The process requires a higher oxygen feed, increasing the size of the ASU. It displays a higher tolerance to feedstock impurities, which potentially would deactivate reforming catalysts if not removed. Scrubbing systems are nonetheless typically required downstream of POx reforming to ensure that the CO shift process unit’s catalyst and equipment is protected, as indicated in Figure 5. This negates some of the advantages offered by the non-catalytic reforming route. Additionally, more severe operating conditions (much higher operating temperatures) of this process could have an impact on plant availability, which would need to be taken into consideration for this route to blue hydrogen.
Overall assessment of blue hydrogen routes
Worley assesses reformer fl ow sheets and performs optimisation studies for a number of customers in this fi eld. For large scale blue hydrogen greenfi eld facilities, which need to meet high carbon capture rates (95%+) combined with high thermal effi ciency, an oxygen-based catalytic reforming approach is the most thermally and techno-economically effi cient path.
When smaller capacities are considered and (naturally) when retrofi ts to existing hydrogen generation systems are required, an SMR blue hydrogen option becomes a viable
alternative as it offers a lower CAPEX option and no ASU requirement. The breakpoint in this capacity, where SMR becomes a viable alternative, depends on a number of parameters and is very specifi c to each project. Worley’s experience has Table 1. Technical assessment comparison of blue hydrogen technologies shown that SMR or a Description SMR H2 fired SMR natural combination of SMR gas fired with ATR (combined reforming) would not achieve the carbon capture targets currently being set by the industry, which is particularly true for most greenfi eld blue hydrogen (large) projects in Europe and the UK. The reforming would be expensive, especially at the capacities considered, and post-combustion capture is required as an additional step to achieve the higher CO2 capture targets. For smaller capacities (below 100 kNm3/hr) and for existing facility retrofi ts (conversion to blue hydrogen), this route is a viable alternative. ATR and GHR technology can meet the high energy effi ciency criteria at the 95%+ capture rate, with ATRs being more suited to the larger capacity projects. This article has shown that an optimised ATR fl ow scheme can be achieved by carrying out a number of process parameter changes. The CO2 capture rate achieved by the series coupled GHR confi guration is the highest of all the reforming confi gurations considered and it can be achieved at thermal effi ciencies exceeding 80% (HHV based). Although this is a promising technology, it does have the drawback of limited commercial references. Non-catalytic POD, although not as techno-economically effi cient as the catalytic approach, does offer the advantage of allowing for feed gas at lower purity, however reformer downstream catalytic processing (CO shift) still requires syngas clean-up steps at the exit of reforming, which negates some of this advantage.
Reference
1. BULI, N., ABNETT, K., and TWIDALE, S., ‘EU carbon price hits record 50 euros per tonne on route to climate target’, Reuters, (4 May 2021), https://www.reuters.com/business/energy/eu-carbon-price-tops-50euros-first-time-2021-05-04/
Combined reforming ATR HE reforming (GHR)
H2 capacity (single train)
Downfired high capacity approaching 400 kNm3/h Others low <200 kNm3/h Downfired high capacity approaching 400 kNm3/h Others low <200 kNm3/h 400 kNm3/h Approximately 400 kNm3/h Approximately 200 kNm3/h (single ATR with two GHRs) Carbon capture rate
70 – 85% 85 – 95% Maximum 95% 95 – 97% 97+% Efficiency (HHV including power import)
~75% <75% 75% 75 – 79.5% 80.5% Cost High1 High High Low Low Power import Low High Low Low High 1 High CAPEX at large capacities