
11 minute read
A clean air strategy
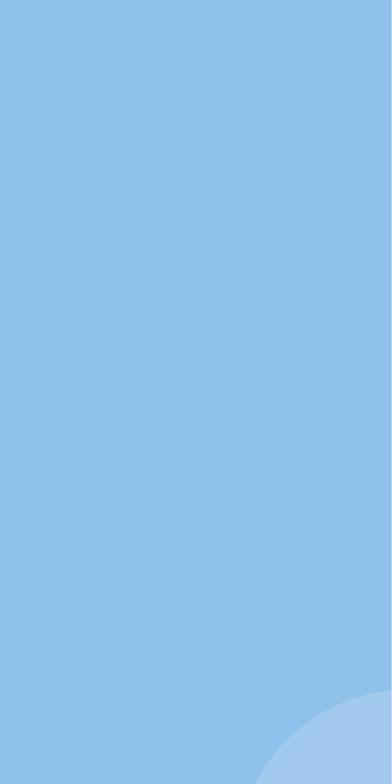


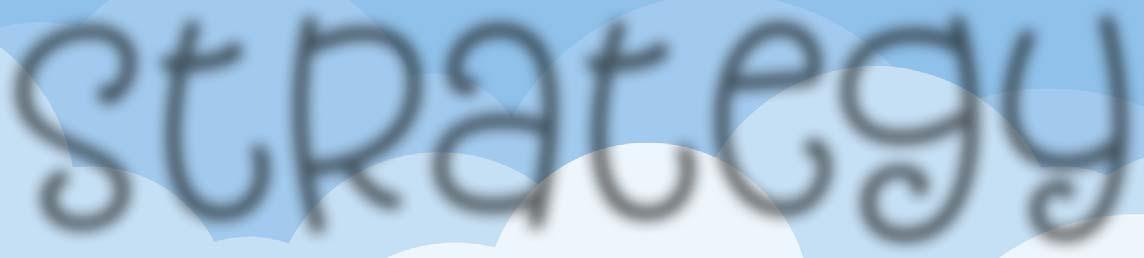
Matt Halsey, Servomex, UK, explains how hydrocarbon processing plants and refineries can implement cleaner air strategies using gas analysis.
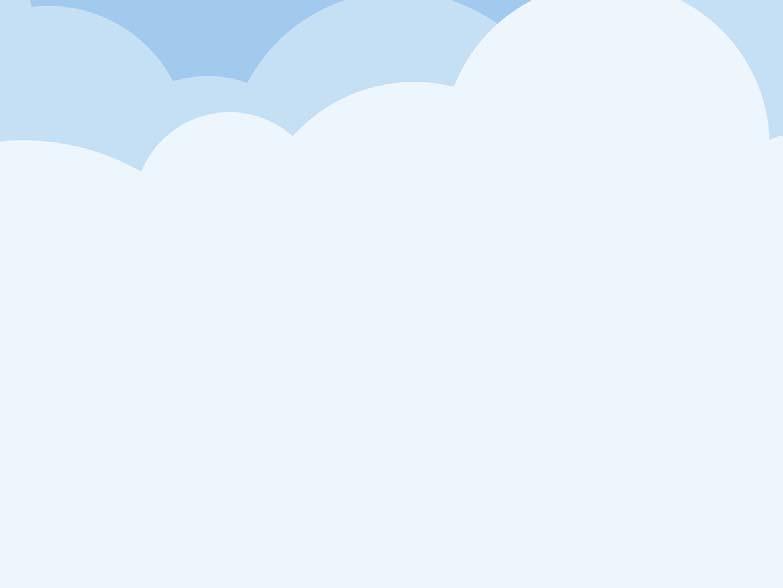
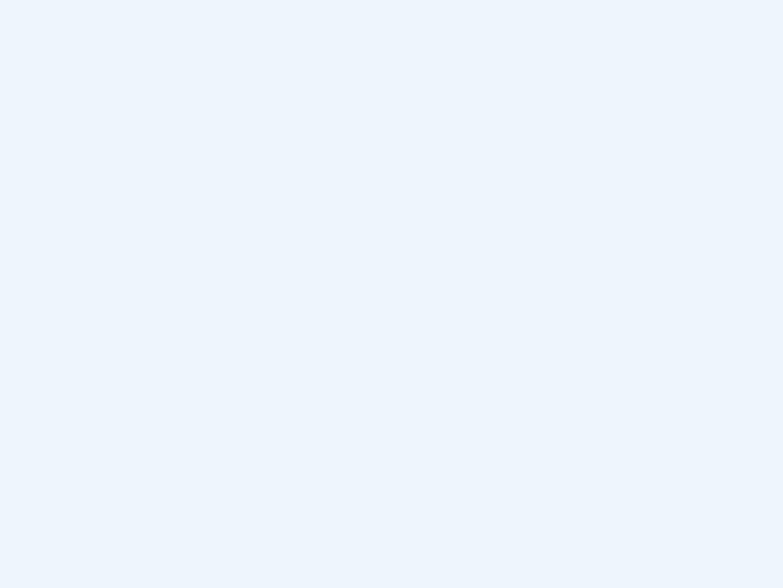
Increasingly stringent environmental regulations, along with international action to reduce the impact on climate, such as the 2016 Paris Agreement, have made plant operators more aware of their contribution towards greenhouse gas emissions. Gas analysis systems provide an effective solution for plants looking to reduce their emissions and operate in an ecologically responsible way. Servomex operates a clean air strategy that focuses on three key process areas: combustion effi ciency, gas clean-up, and emissions monitoring. Analytical solutions for these areas will support plants in their clean air goals, while also optimising processes to deliver reduced fuel consumption and higher yields.
Stage one: effective combustion control
There are no realistic alternatives to combustion when it comes to creating the high temperatures needed for many hydrocarbon processing applications. Achieving an effi cient reaction is therefore key.
The reaction of oxygen (from air) with fuel typically generates harmful emissions, while also using a signifi cant amount of fuel and creating potential safety hazards. Obtaining an effi cient reaction means optimising the ratio between the air and fuel.
Before gas analyser technology was developed, fi red heaters were typically run in high excess air conditions. This avoided the creation of unsafe conditions that could lead to an explosion, but was ineffi cient and increased the level of fuel consumption.
Additionally, excess oxygen (O2) will combine with nitrogen and sulfur in the fuel to produce unwanted emissions such as oxides of nitrogen (NOX) and sulfur (SOX).
By accurately measuring O2 and combustibles such as carbon monoxide (CO), plant operators are better able to balance the air-to-fuel ratio, controlling the combustion reaction.
This produces a number of benefi ts, particularly where plants are looking to improve environmental standards. It reduces fuel consumption, resulting in fewer emissions, lower NO x, SOX, and CO generation, and a decrease in the greenhouse gas carbon dioxide (CO2).
As a solution for monitoring O2 in combustion, Zirconia sensing is a long-established technology. It delivers reliable, accurate results with a fast response to changing conditions.
A combustibles sensor can be added easily, and at modest cost, to provide an all-in-one combustion control solution, such as in Servomex’s SERVOTOUGH FluegasExact 2700 combustion analyser.
The more recent development of tunable diode laser (TDL) technology provides an even faster measurement, particularly for carbon monoxide. This also takes an average result across the measurement path, rather than measure a single point. However, TDL sensing is highly specifi c to the gas being measured, so separate analysers are required for O2 and CO.
For this application, Servomex’s SERVOTOUGH Laser 3 Plus Combustion TDL analyser can be confi gured to measure either O2 or CO. It can also be confi gured to jointly measure CO and CH4, providing a rapid-response measurement for safety in natural gas fi red heaters and boilers.
Stage two: process gas clean-up
The second phase in the aforementioned clean air strategy is to support the removal of harmful substances from process gases which might otherwise be emitted by the plant. Examples of these applications include DeNOX (ammonia slip) treatment and fl ue gas desulfurisation.
Process efficiency Ammonia slip
Gas analysis is used in many applications to support greater process effi ciency in the same manner as optimising combustion. An effi cient process reaction generates fewer harmful emissions, so this also plays its part in cleaner air.
For example, one of the largest air emissions sources in a refi nery is the fl uid catalytic cracking unit (FCCU). In a typical FCCU, a process control oxygen measurement is required in the regenerator off-gas, where low O2 causes incomplete combustion of the catalyst coke while excess O2 reduces catalyst life.
Measuring the CO and CO2 in the same off-gas helps calculate catalyst coke formation, enabling catalyst regeneration effi ciency to be determined. Excess O2 and CO levels are monitored in the regenerator fl ue gas, while ammonia (NH3) ‘slip’ is measured at the selective catalytic reduction (SCR) outlet to control the DeNOX process.
Each process point requires the application of appropriate gas analysis technology. The off-gas measurements for O2 and NH3 slip benefi t from the use of TDL open-path measurements (as provided by the Laser 3 Plus), which reduce issues with catalyst particulates experienced by in-situ or simple extractive systems.
Close-coupled extractive systems are reliable and cost-effective when measuring O2 and combustibles (COe) in fl ue gas, while the SERVOTOUGH SpectraExact 2500 is suited for the off-gas CO and CO2 measurements.
Ammonia (NH3) or urea is used to suppress the harmful emissions of NOX from combustion, through either a SCR or selective non-catalytic reduction (SNCR) process.
These methods require accurate NH3 dosing to reduce NOX levels – if insuffi cient NH3 is used, then NOX emissions are not adequately suppressed, while excess NH3 causes the eventual formation of ammonium bisulfate (ABS), a white powder that can plug the catalyst in SCR processes, damaging equipment and reducing the value of the fl y ash by-product.
Therefore, it is vital that plants manage DeNOX processes by controlling the level of ammonia slip to between 2 – 3 ppm of NH3. NH3 can be monitored by extractive sampling. However, this is diffi cult, since the sample must be kept above 290˚C (554˚F) to prevent the formation of ABS and sulfuric acid.
Inlet NOX concentration, fuel composition and catalyst performance can also affect the measurement, while Infrared-based extractive systems may also be impacted by signal interferences from gases formed by the process, and by high levels of dust. A more effective solution is a TDL analyser installed directly into the process ducts. This provides a signal that is averaged across the duct, for a more accurate NH3 reading despite uneven fl ow conditions.
Figure 1. Using the Laser 3 Plus TDL analyser in ammonia slip applications. Flue gas desulfurisation
A fl ue gas desulfurisation (FGD) system is designed to remove sulfur compounds (SOX, chiefl y SO2) from exhaust gases. It is typically used by fossil-fuel power plants and operators in other SO x-emitting processes, such as waste incineration.
The most common method sees the fl ue gas sprayed with a wet slurry of lime, which reacts with SOX and scrubs up to 95% of the SO2 content from the gas. Gas analysers measure the SO2 content after treatment to ensure that remaining sulfur compounds meet regulatory limits.
Gas analysis in this process is challenging, as gases containing SOx can be corrosive, and
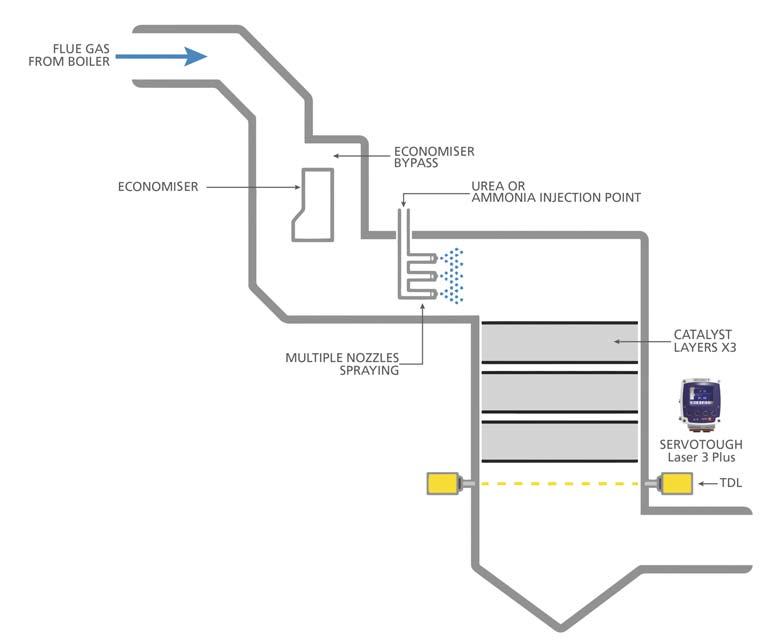
treatment temperatures are usually kept high to prevent moisture content from damaging equipment. The most effective and accurate measurement for SO2 in this application is provided by non-contact, photometric sensing technology.
Servomex’s SERVOPRO 4900 Multigas uses infrared gas fi lter correlation (Gfx) technology to measure SO2 in this application. This allows accurate, real-time measurements at very low levels, without interference from background gases.
Gfx technology also supports sulfur recovery units (SRUs), which recover sulfur from streams containing H2S.
Stage three: emissions monitoring
Monitoring fl ue gas emissions helps protect the environment and determine the effi ciency of the process. It also demonstrates that plant operators are complying with the necessary regulations.
Greenhouse gases – CO2, CH4, and nitrous oxide (N2O) – and key pollutants such as NOX, SOX, and CO, must be measured in order to achieve a clean air strategy and meet regulatory requirements.
To measure all the necessary components of the fl ue gas, and ensure compliance, a continuous emissions monitoring system (CEMS) is required.
This system must be capable of offering the highest sensitivity and accuracy when dealing with multiple measurements for pollutants and greenhouse gases.
Multi-component gas analysers are suitable for this application, and depending on the process can either deliver all the necessary measurements in one device or form a key part of an integrated, comprehensive CEMS.
For example, a single 4900 Multigas can monitor four gases simultaneously, measuring from a choice of O2, CO2, CO, SO2, NO, CH4 and N2O, so multiple analysers can easily cover the pollutants of interest.
Any gas analysis system must also meet MCERTS and QAL1 certifi cations to comply with regulatory criteria.
Carbon capture and storage (CCS)
The capture and storage of CO2 – rather than releasing it into the atmosphere – not only results in a cleaner environment, but also allows the CO2 to be used in other processes. It falls within two phases of the clean air strategy, as it encompasses elements of both gas cleaning and emissions monitoring.
Three methods exist for CCS: post-combustion, oxyfuel, and pre-combustion. Post-combustion CCS is when CO2 is removed from the fl ue gas after fossil fuels have been burned. Oxyfuel CCS produces a fl ue gas consisting almost entirely of CO2 and steam by reacting the fuel source with almost pure O2, so fl ue gas can be stored/sequestered without signifi cant pretreatment. Both methods can be retrofi tted to existing plants or used in new ones.
Pre-combustion CCS, performed before the fuel is burned, converts the fuel into a mixture of hydrogen and CO2. This is diffi cult to retrofi t and so is better suited to newly built facilities.

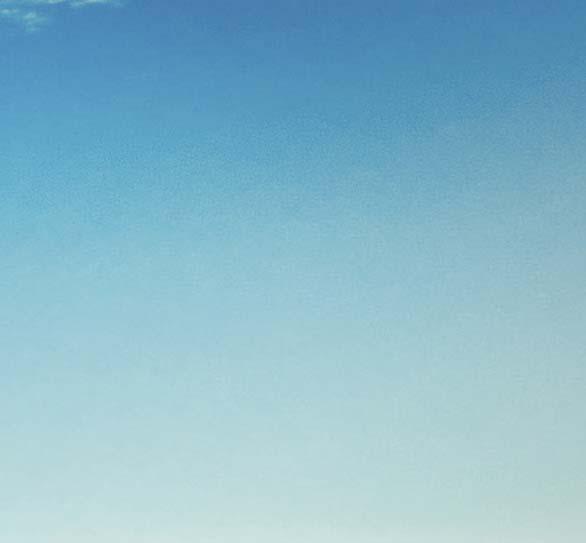

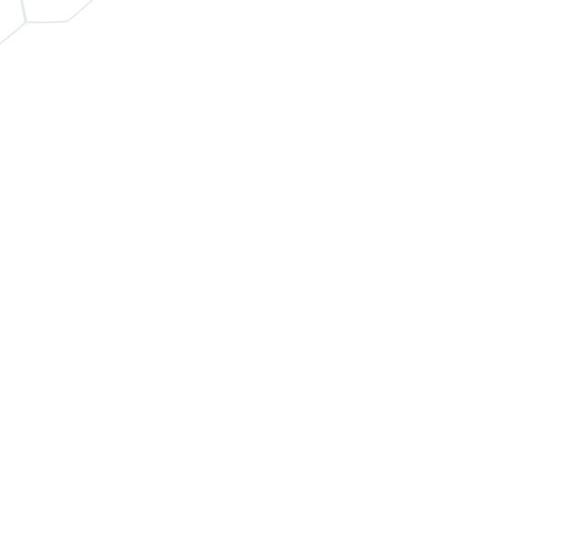
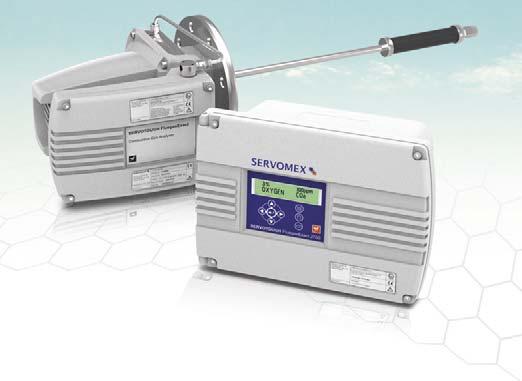
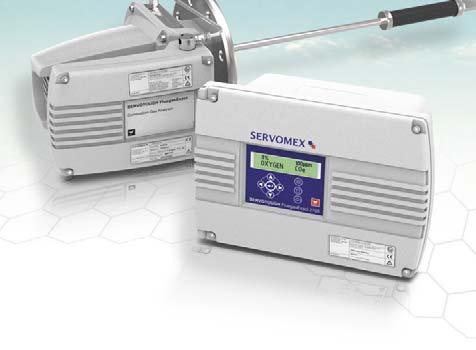
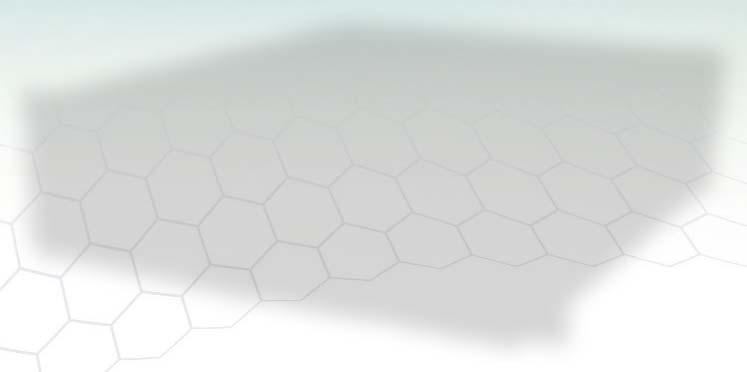
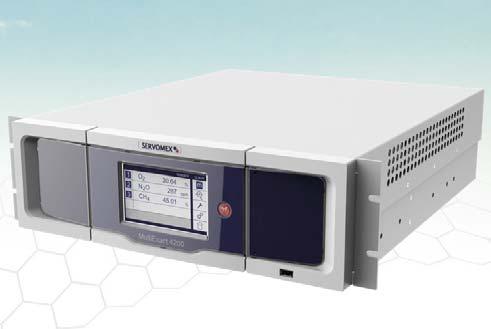
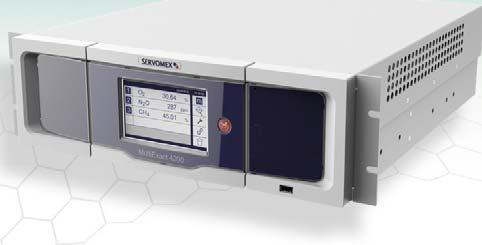
Whichever method is used, once the CO2 is captured it is then compressed into a liquid and transported for storage.
Requiring accurate gas analysis, industrial-level CCS is likely to expand in coming years as countries look to meet Paris Agreement carbon reduction targets.
The SERVOTOUGH SpectraExact 2500 photometric analyser can be used for this application. It is capable of single or multi-component gas monitoring in corrosive, toxic, or fl ammable streams, using Infrared and Gfx sensing to measure CO2 at percentage and ppm levels.
In addition to measuring the fl ue gas to ensure CO2 removal, it is also capable of assessing the purity of the removed CO2 prior to it going to storage.
Cleaner energy sources
As part of their emissions reduction plans, many operators are moving to cleaner energy sources, such as hydrogen. At the same time, plants that produce hydrogen are ramping up output to meet this increased demand.
Hydrogen gas (H2) burns much more cleanly than CH4, as it does not contain carbon, so CO2 is not formed as a combustion by-product. Gas analysis again plays a major role, as the purity of the hydrogen directly affects its quality as a fuel.
Depending on the manufacturing method, the most common contaminants will be O2, CO, and CO2, which can all be monitored by the MultiExact 4200, Servomex’s multi-component analyser, using a mixture of paramagnetic, infrared, and Gfx technology.
Whatever cleaner energy sources emerge in the future, it is certain that gas analysis technology will have an important part in the process.
A cleaner future
Gas analysis is essential to cleaner plant and refi nery operations, whether it is in ensuring more effi cient processes, supporting the safe removal of pollutants, or monitoring the remaining emissions to the atmosphere.
It also supports emerging trends in the industry, such as the desire for greater process optimisation, the move towards cleaner fuels, and the achievement of higher product yields.
For such a wide range of goals, an equally wide range of sensing technologies is required. Partnering with an expert gas analysis supplier is vital; by offering a diverse selection of technologies, and the expertise to support them, such suppliers can ensure the best-fi t and most cost-effective solution for each application.
Service support is another key consideration – forging a service contract that maintains gas analysis systems at peak performance means the refi nery or plant keeps operating as cleanly as possible. Servomex’s Service Network, for example, offers customisable service packages depending on the level of support required.
Each of the phases outlined in this article is a vital component of any cleaner air strategy. By combining all three, plants and refi neries can fully address the impact of their operations on the environment, playing an important part in creating a world with cleaner air.
37th

Oil | Gas | Fertilizers | Metallurgy | Industrial Sulphur + Sulphuric Acid 2021
Virtual Conference & Exhibition
1-4 November 2021
SPONSORS:
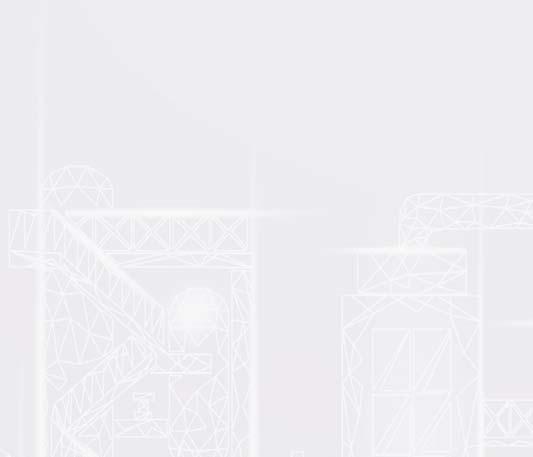
CRU’s Sulphur + Sulphuric Acid will run as a fully virtual event again in 2021 – connecting you with an even wider audience of sulphur and acid industry professionals from around the globe. Drawing on the success of the 2020 virtual event you can expect expanded content streams, enhanced networking opportunities and much more – all from the convenience of your
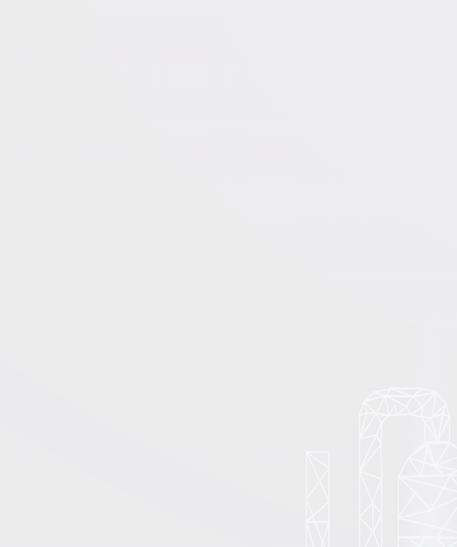
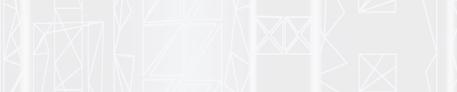
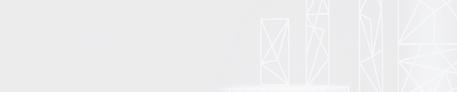