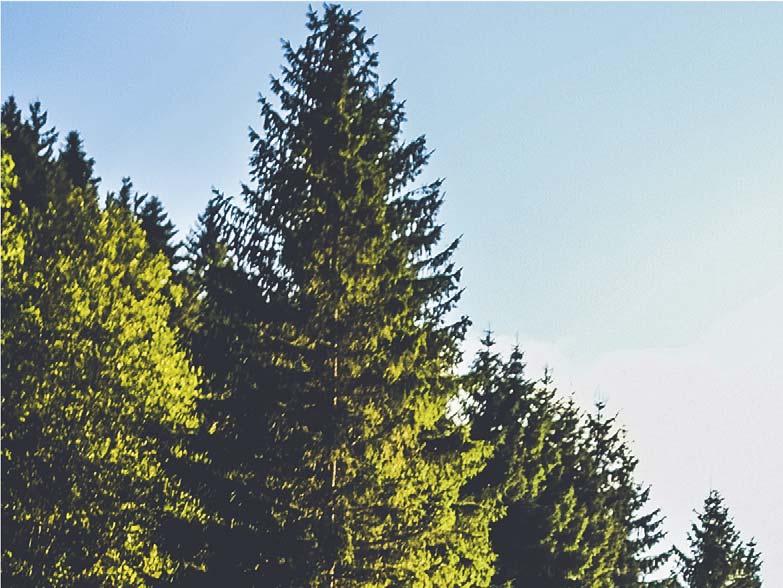
10 minute read
The road to net-zero

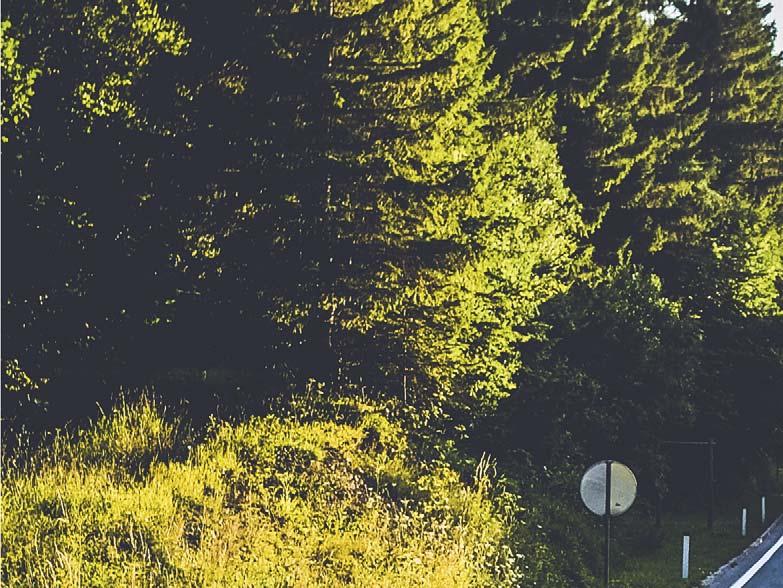
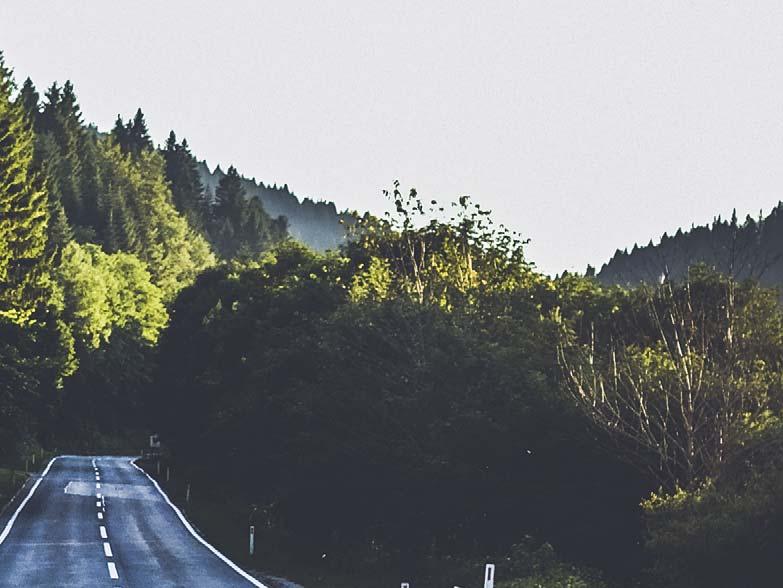

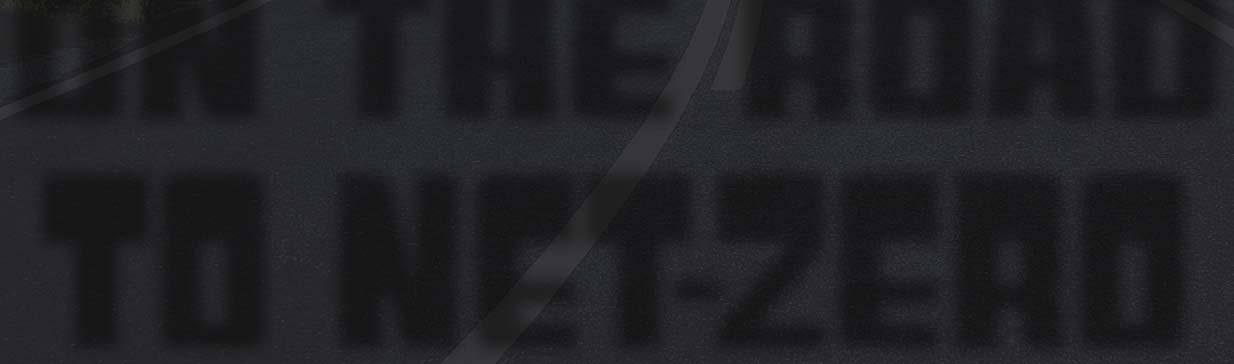
Robert Jolly, Johnson Matthey, UK, outlines how clean hydrogen can play a key role in the energy transition, if it is deployed now.
Momentum to limit global warming continues to build. Individuals, organisations and governments are seeking methods to implement in order to achieve the targets set by the Intergovernmental Panel on Climate Change (IPCC) to keep the global temperature increase below 1.5°C above pre-industrial levels. To limit the global temperature rise to 1.5°C it is essential to reach a net-zero situation for all greenhouse gas (GHG) emissions by 2050.
Whilst there has been growth in discussion, commitments and policy related to net-zero, there is still a signifi cant gap between the commitments made by countries, Nationally Determined Contributions (NDCs) and the 1.5 °C pathway. A predicted gap of 29 GTCO2e/yr
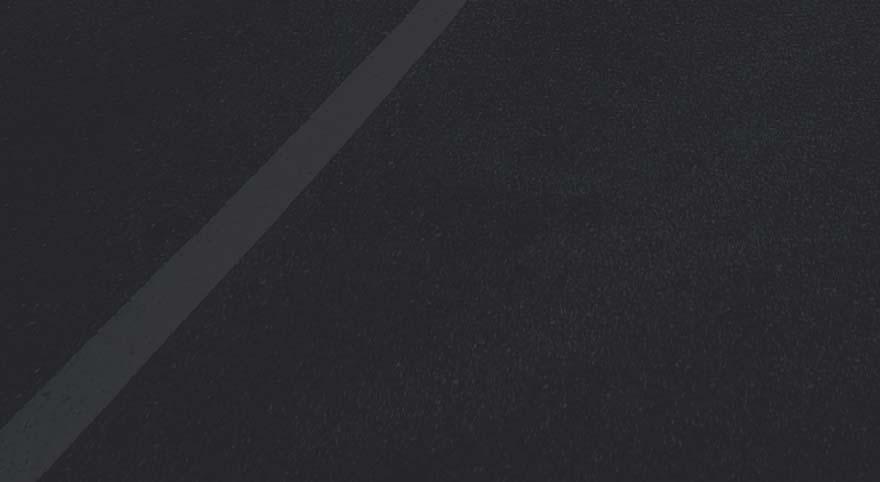

remains by 2030 (Figure 1). To give this context, the difference between the 2010 policy and the NDCs by 2030 is only 11 GTCO2e/yr. This shows the scale of the challenge and that there is much more that needs to be done.
The 1.5°C pathway is achievable, but it requires the deployment of the best low carbon technologies now. Net-zero by 2050 will only be possible if we are on the 1.5°C pathway. The longer it takes to start reducing emissions, the larger the task will be, and there is a point where 1.5°C would not be achievable without a signifi cant period of negative emissions.
Hydrogen’s part to play
Urgently decarbonising the world’s energy systems is essential to meet the 1.5°C goal, and this is where hydrogen has a role to play in providing clean energy for a wide number of applications. The Hydrogen Council identifi ed its potential application in a number of key sectors: power generation (including energy storage), transportation, industrial and chemical processes, and heating buildings.1
Today, hydrogen is primarily used in industrial applications, such as hydroprocessing and chemical feedstocks. However, by 2050 hydrogen is anticipated to become a major energy source across multiple sectors. The expected growth in hydrogen is large, and equates to deploying one 67 kNm3/hr plant each day from now until 2050. To attain the capacity to supply this hydrogen, world scale hydrogen production units will need to be installed, and an acceleration in project development is required to increase the scale of current plants. For existing operators, hydrogen offers a tool to allow decarbonisation of existing assets, securing the future of the business. But it also offers an exciting opportunity to become a new product line providing access to this new energy market. Thinking wider than just decarbonising existing hydrogen capacity is required to truly embrace the opportunity that hydrogen presents.
Figure 1. Predicted emissions gap by 2030. 1 NDC – Nationally Determined Contributions Source: UNEP Emissions Gap Report 2020.
Figure 2. A flowsheet producing H2 using Johnson Matthey’s LCH technology.
Blue hydrogen
One of the primary ways to make low carbon hydrogen is through the reforming of hydrocarbon feedstocks coupled with carbon capture and sequestration (CCS). This method of production is termed ‘blue hydrogen’. Blue hydrogen offers the opportunity to deploy large-scale hydrogen production today, resulting in a signifi cant impact upon GHG emissions. The US Department of Energy (DOE) set a target levelised cost of hydrogen (LCOH) of US$2/kg as the benchmark that would allow wide adoption of hydrogen as an energy source without signifi cantly

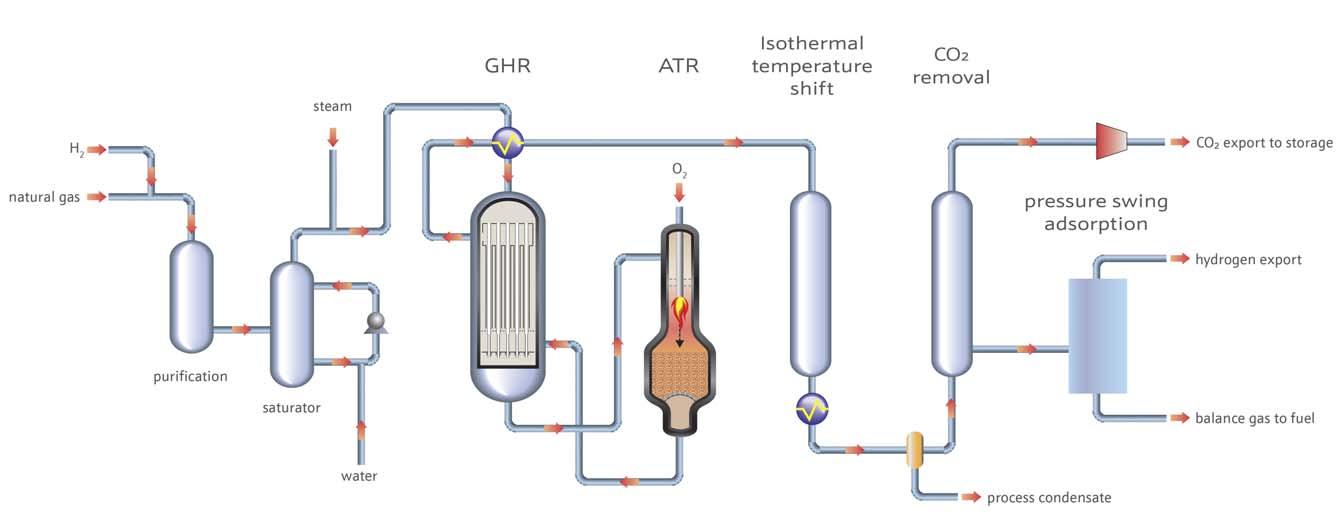
impacting upon economies. To reach this target, technologies that are specifi cally optimised for blue hydrogen production are required.
Focus on emissions
The term ‘blue’ can be used to represent any hydrogen production that includes some decarbonisation. If we return to the net-zero target, it becomes clear that it is essential to focus upon low emission production routes. On a CO2 capture basis, this means striving for the highest rates possible, as any CO2 emission associated with hydrogen production will need to be accounted for through the deployment of alternative technologies. A plant that is achieving 60% carbon capture still leaves a signifi cant challenge to mitigate the 40% remaining emissions, and it also presents a substantial risk of exposure to CO2 pricing infl ation for the operator of the facility.
Blue hydrogen requires a specifi c focus and a holistic approach to tackling the problems. Specifi cally, for blue hydrogen production it is important to aim for high purity H2 and CO2 products, and to maximise feedstock effi ciency while intensifying the process (to enable brownfi eld deployment).
H2 production and CO2 capture cannot be considered as two separate problems in isolation. It is essential to view the process as a whole to fully reach the best solution to the problem.
DYNAMIC SIMULATION SERVICES FOR CENTRIFUGAL AND AXIAL FLOW COMPRESSION SYSTEMS
SCENARIOS COMPSYS™
Normal and emergency (ESD) Machine sequences (series and parallel) Process Valves or other equipment failure events
BENEFITS
proper routing & sizing of control lines & valves of hot by-pass valves process & equipment checks Realistic analysis of controllers of compressors antisurge, performance & load sharing controls operational procedures to reach target operating points
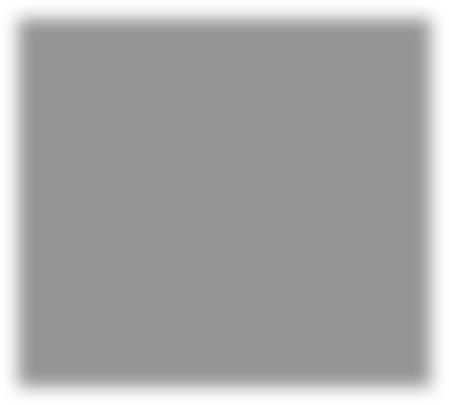
Solution
In focusing on blue hydrogen, Johnson Matthey (JM) has developed its LCHTM process for blue hydrogen production. The LCH technology offer combines JM’s proprietary gas-heated reformer (GHR) and autothermal reformer (ATR) technologies and allows for a higher hydrogen yield and greater energy effi ciency than the standard steam methane reforming (SMR) technology for hydrogen production. The process delivers a high CO2 capture rate (>95%), high effi ciency and low-cost solution. The approach is based on established chemical process engineering, designed to operate at scale, enabling carbon reduction for industry, dispatchable power, domestic heating, and transport.
When compared to a conventional SMR, the LCH technology demonstrated 10% lower natural gas consumption, 10% less CO2 production, and 75% lower capital cost for the CO2 capture system.
Use of the technology de-risks the project by minimising the impact of increasing feedstock costs, increasing costs of CO2 transmission and storage and any governmental scheme for carbon taxation.
Process flowsheet
The effi ciency benefi ts of the LCH technology are achieved by recovering heat at maximum exergy (i.e. the highest possible quality) by coupling a GHR with an ATR (Figure 2). The main difference between the LCH and SMR
PHcorr (kJ/kg)
EXAMPLE: simulation of ESD events to
Dynamic compressor maps
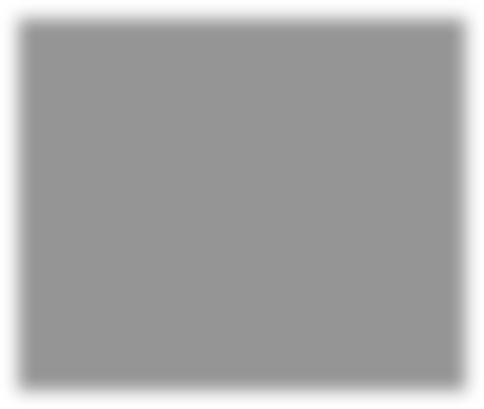
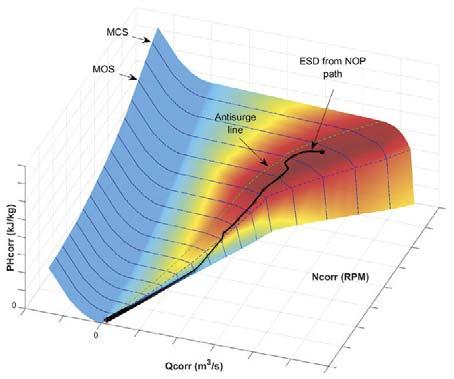
92.6 % of MCS
Cv - 92.1% SLL
Cv - 9.5%
-6.2%
+28.2%
+39.6%
+13.3%
+3.2% +83.5% 91.3 % (@ 0 s)
89.0 % (@ 0.3 s)
86.0% (@ 0.7 s) Valve size optimization
Consulting Simulation services & Software for process plants and machines
Optimized value 0% Selected size +25.4% Qcorr (m3/s)
Table 1. Comparison of LCH to SMR+CCS
Units SMR+CCS LCHTM process
Natural gas energy (lower heating value [LHV]) Hydrogen production MW 432 373
kNm3/hr (million ft3/d) 100 (90) 100 (90)
Hydrogen energy (LHV) MW 300 300
Energy efficiency (LHV) % 69.4 80.5
CO2 emitted ‘000 tpy 77.7 19 CO2 captured ‘000 tpy 700 603 CO2 captured % 90 97 Relative CAPEX % 100 61
Note: these numbers are provided for information and should be considered as indicative. SMR data source: IEAGHG Technical Report 2017-02. LCH CAPEX includes ASU. The LCH process is highly tuneable, allowing project specific optimisation and integration
fl owsheets is that the energy to drive the reaction is provided by introducing oxygen to the ATR as opposed to burning natural gas in the SMR. ATRs are already used in the production of syngas in technologies such as methanol. These plants are very large and demonstrate that the technology is capable of producing hydrogen at large scale.
The heart of the process is the reforming block of GHR-ATR. The confi guration of the reactors allows feedstock effi ciency to be maximisued through effi cient energy transfer. Importantly, all of the carbon dioxide is within the product stream and therefore at high pressure and purity. This means that it can be easily removed using standard industry removal technologies. The ability to apply pre-combustion CO2 removal on a high CO2 partial pressure steam means that CAPEX, OPEX and footprint of the system can be signifi cantly reduced. This increases the ability to deploy the system on existing sites and decreases the LCOH being produced from such a system.
Comparison of LCH to SMR+CCS
In Table 1, the LCH process is shown to offer higher effi ciency, lower CAPEX and lower emitted CO2 when compared to SMR+CCS.
It is important to note that comparing the CO2 capture rates of different technologies can still hide the actual emissions generated from the hydrogen production unit. In Table 1, the SMR+CCS unit was only achieving 90% CO2 capture (signifi cantly increased capital cost to push those rates into the high 90s did not make sense for the study). For comparison, if the SMR+CCS option capture rate was increased to 97%, the emitted CO2 would be 23 000 tpy, which is still 20% larger than the LCH process. This highlights how capture rates can hide the true carbon credentials of a solution. This difference is due to the process effi ciency; in a low carbon world, it is important to maximise effi ciency when converting hydrocarbon energy into hydrogen energy.
Active projects
The LCH process is already being used in the development of a number of projects.
HyNet is looking to develop a full hydrogen economy in a region of the UK, with a first phase producing 80 000 tpy of hydrogen for use in industry, homes and transport. The hydrogen plant at the heart of HyNet will utilise the LCH process, which will be hosted at Essar’s Stanlow Refinery. The initial phase focuses on supplying hydrogen to industrial applications, providing the required base demand to catalyse the development of the CO2 transport and storage and hydrogen infrastructure. The vision is to increase hydrogen production in subsequent phases once demand across various industries develops. The project demonstrates a design and execution that can be replicated elsewhere in the UK and internationally. When fully implemented, HyNet hydrogen will deliver low cost, low carbon hydrogen for key industrial users alongside non-disruptive blending to over 2 million households as part of delivering a net-zero industrial cluster in the region.
The Acorn project places advanced reforming technology at its core and will deliver a replicable process for cost-effi cient hydrogen based around natural gas, whilst capturing and sequestering CO2 emissions. Here, the plan is to blend hydrogen into the natural gas grid for use across Scotland. The fi rst phase is a 55 000 tpy hydrogen plant, and the LCH process has been the basis of the plant design for submission to the UK government’s Department for Business, Energy & Industrial Strategy (BEIS) Hydrogen Supply Competition.
Key advantages
LCH is a high effi ciency process, with low CAPEX. It offers the lowest natural gas usage per unit of hydrogen, maximising the conversion of hydrocarbon energy into hydrogen energy, and it also produces the lowest amount of CO2 per unit of hydrogen. A highly intensifi ed footprint enables the amount of hydrogen per square metre of land to be maximised. The technology is also proven at scale, and has been deployed in both MeOH and NH3 plants for syngas production. This maturity has enabled design of the equipment to maximise reliability and uptime. Finally, all the CO2 within the process stream allows for the implementation of well-proven pre-combustion CO2 removal systems, ensuring all key technologies are mature.
Summary
Limiting global warming to 1.5°C is a big challenge, but it is still achievable if low carbon technologies are deployed today. Clean hydrogen can play a key role in the energy transition and offers a solution that can be deployed into a wide number of industries and applications. JM’s LCH process enables low carbon hydrogen to be produced at scale, today, with leading environmental and economic performance, setting the world on the road to net-zero.
Reference
1. ‘Hydrogen, Scaling Up’, Hydrogen Council, Brussels, Belgium, (November 2017), p. 20.