
11 minute read
A more sustainable future
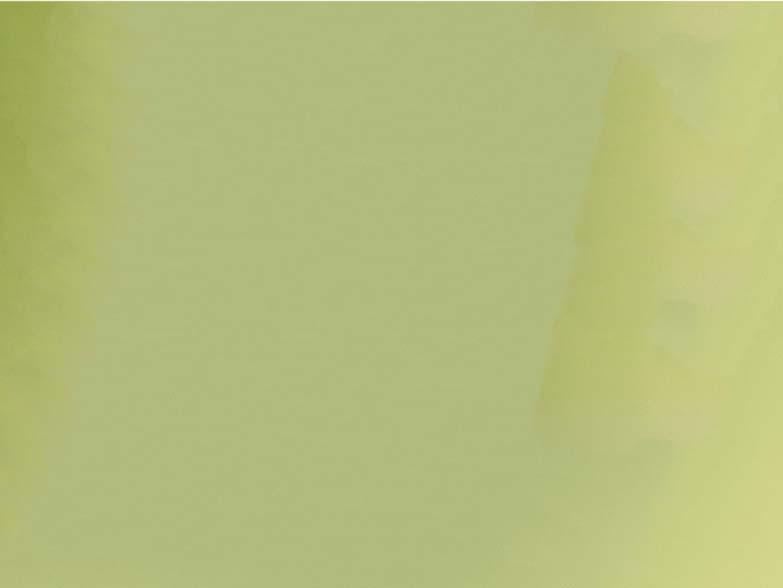

William Vickers, Ionix Advanced Technologies, UK,
explains the contribution that corrosion monitoring technology can make towards increased industry sustainability.


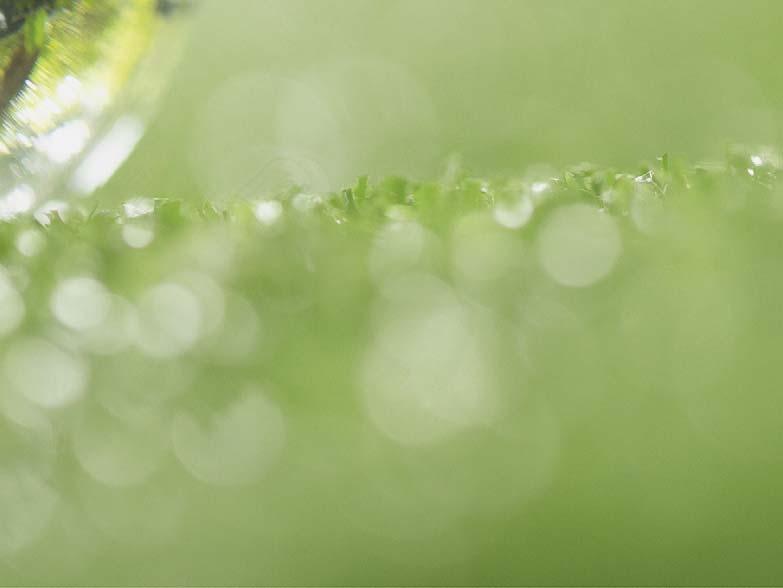

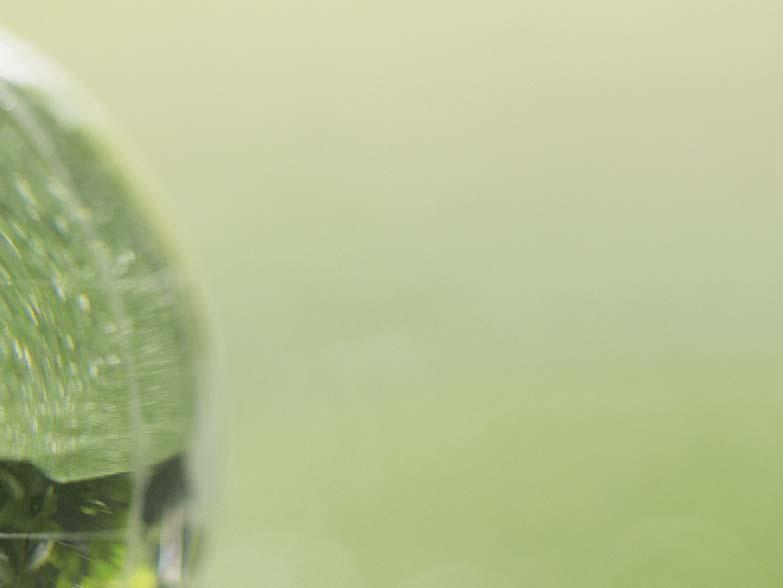
Downstream refi nery operators face an existential challenge with a range of critical pressures facing the industry. With the drive towards a low carbon future, the coming period requires refi nery operators to adapt their business strategy and operations if they want to secure their future. On top of everything, the ongoing effects of the COVID-19 pandemic bring both business and operational challenges to maintain the safety and health of the business operations and staff. All of these challenges require operators to put sustainability front and centre of their strategy, and to look at all aspects of their long-term operations in order to meet emissions targets, minimise the risk of unplanned outage, maximise production availability and rates, and reduce operational risk. Industrial plant digitalisation is spreading across a wide range of sectors, including oil and gas, energy and nuclear, and process industries. Plant digitalisation is increasingly seen as a key element to enable long-term sustainability of a refi nery or upstream operation, with a range of monitoring applications including corrosion monitoring driving towards digitalisation. Automating thickness measurements can allow for an increase in the data collection frequency providing up-to-date measurements to feed into both asset integrity programmes and to guide process control and productivity optimisation. This approach can underpin long-term sustainability by
enabling businesses to meet their environmental and safety obligations whilst delivering improved economics.
Production challenges
There is a mandated requirement for oil and petrochemical operators to continuously test and monitor the health and condition of their infrastructure. This is increasingly important as the lifespan of these assets continues to lengthen over time, driven by reduced investment in new capacity in some regions, while demand for refi nery products is likely to remain volatile as economic activity around the world recovers from the economic effects of the COVID-19 pandemic. Energy demands are increasing globally and the transition from current to future low carbon energy sources will remain a complex process.
Economic pressures dictate that refi ners must be able process lower priced and varied feedstocks to optimise their profi tability, while meeting increasingly demanding emissions targets. Changing market and user demands will require high levels of fl exibility from the refi nery, while these varied feedstocks bring with them increased corrosion risks that must be managed.
The high costs and associated risks of plant-infrastructure failures, coupled with increasing asset lifespan, is creating a growing need for permanently installed and continuous sensing in these industry sectors. Industry is demanding change as it seeks to reduce operating and employee risk, and drive down costs while gaining higher quality data on the performance of critical assets.
Effective corrosion monitoring is especially important for high value refi nery assets where service life can be extended and/or maintenance be deferred.
While conventional inspection approaches have and will continue to be important in the management of corrosion, these complex challenges are driving refi neries to move towards the preferred use of continuous monitoring of their assets combined with proactive maintenance.
Introduction to automated ultrasonic testing
Traditionally, the thickness measurements which are used on a downstream plant or in upstream operations are generated manually by non-destructive testing (NDT) inspectors and are prone to errors and inaccuracies due to the challenge of fully matching calibration/reference material to the asset, variations in equipment and exact inspection locations, and natural human variations in implementing methods and procedures. For this reason, manual ultrasonic testing (UT) measurements are generally considered to be accurate to a maximum of ±0.1 mm and most commonly are only accepted to be accurate to ±0.5 mm.
To enhance precision, combined with the need to reduce the presence and cost of people working on site, manual UT measurements are taken at relatively low collection frequencies to ensure changes in wall thickness are detected. Even so, it is not uncommon for thickness measurements to be seemingly thicker than one taken 5 years earlier due to very low rates of corrosion/erosion and measurement error leading to incorrect calculation of wall loss rates and reduced value of the measurement.
Automating thickness measurements can allow for an increase in the data collection frequency from years to hours, providing up-to-date measurements to feed into both asset integrity programmes but also, importantly, to guide process control and productivity optimisation. Automating thickness measurements bring reduced errors associated with manual measurements by utilising fi xed, installed monitoring sensors and automated measurement calculations using advanced algorithms. This allows the precision of the measurements to be increased to 0.010 – 0.025 mm, allowing smaller changes in wall thickness to be detected.
An increase in precision combined with an increased frequency of data collection allows for statistical analysis of the data and determination of wall loss trends. Trending of thickness data points collected every 12 – 24 hours can allow for corrosion rates as low as 0.020 mm/yr to be detected. It also allows for short- and long-term corrosion rates, as described by API 510, to be calculated from almost live data, allowing for changes in corrosion rate to be detected after only a few weeks, and allowing corrosion rates to be used for process control and optimisation. As a result, automated UT monitoring technology and the powerful data it generates delivers major benefi ts to plant operators, including increased plant up-time, optimised plant economics and profi tability, and reduced operating costs by enabling preventative maintenance. The main barriers to wider adoption of UT monitoring remain the perceived high cost of installation of the solution and the challenges of installation and operation. Next generation UT monitoring solutions will provide lower cost solutions with rapid returns on investment, coupled with live on-line installation and easy operation.
Case studies
The following cases illustrate the investment that major operators are making in corrosion monitoring as a long-term approach to improving the effi ciency and sustainability of their operations. The examples illustrate different scenarios and associated benefi ts for refi ners faced with particular business challenges.
Case study 1: refinery-wide installation – optimising plant economics
A recent refi nery-wide installation of a HotSenseTM corrosion monitoring system shows its major contribution to overall refi nery economics in a fast-changing operating and business environment.
One of the key benefi ts of installed ultrasonic probes combined with automated monitoring nodes is the ability to detect change in wall loss rates. In this case, the refi ner was seeking a system which was stable and predictable and did not pose a signifi cant challenge to the asset managers who can run the plant with a clear
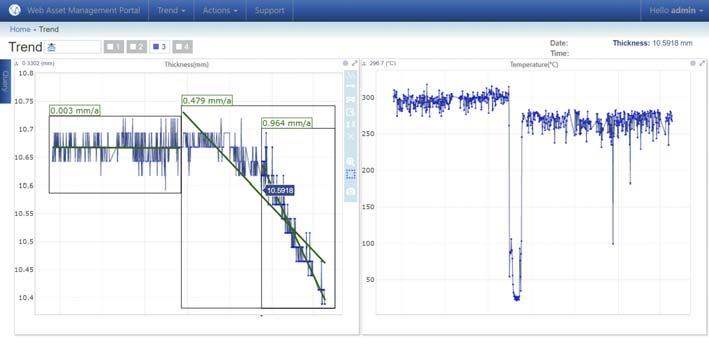
Figure 1. Real-time thickness measurements collected using Ionix HotSense and an ultrasonic monitoring system. A sudden acceleration in wall loss is successfully detected after a reduction in process temperature.
Figure 2. Ionix HotSense ultrasonic sensors and an automated monitoring system installed on a live high temperature plant and integrated into an existing process control sensor network.
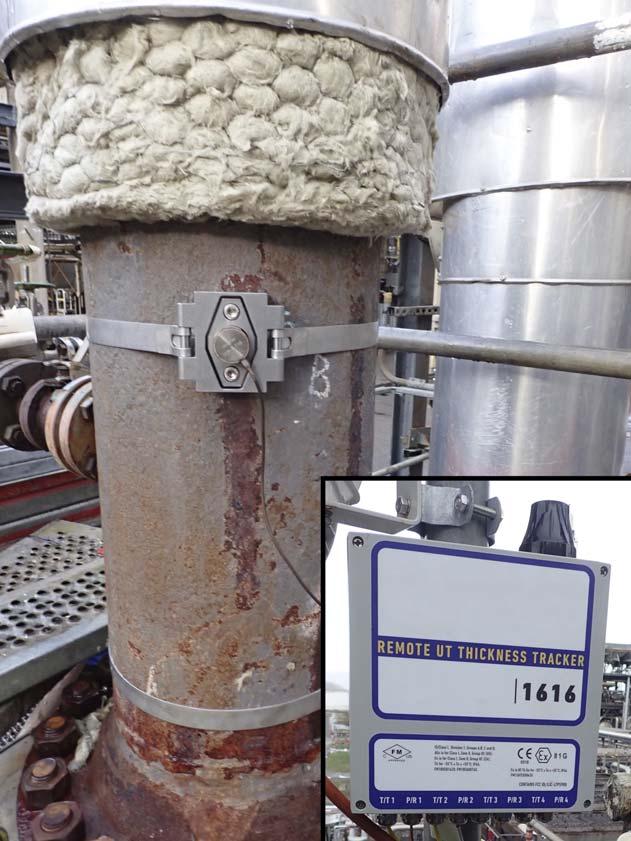
plan for its inspection schedule and ultimate retirement and replacement. However, the move towards a more sustainable oil and gas production and refi ning industry requires changes to be made in the crude slates, products and processing conditions such as operating furnaces at lower temperatures. What is more, these changes need to be made at a higher frequency than previously experienced as fuel demands and emissions targets are reviewed and revised.
The COVID-19 pandemic has also shown how demand for fuels can change rapidly. These rapidly changing production conditions require constant review of the integrity of assets with safe Integrity Operating
Windows (IOWs) being re-defi ned every time a process is required to operate outside of previous confi nes. Generating the data required for the IOWs via manual NDT methods would not be practical for the refi ner due to the low frequency of data collection and low precision of measurements leading to decisions being made on data collected over many years preventing short-term changes from being detected. Installing automated, fi xed UT monitoring on the other hand allowed for the critical high wall loss rates to be detected over a period of weeks. Combined with data from other sensors such as temperature probes, electrical resistance (ER) probes and corrosion coupons, wall loss rates can be correlated with process conditions to allow for the determination of new IOWs and operation of the plant which maximise production whilst ensuring asset lifetime is in-line with replacement and turnaround schedules. Figure 1 shows an example output from the automated UT monitoring system where the measured wall thickness and temperature is shown. It can be seen that the system has been able to detect a sudden acceleration in wall loss soon after a reduction in the processing temperature. This change in actual wall loss rate, not estimated from a coupon or ER probe, would not have been detected using standard NDT monitoring methods, especially at these high process temperatures.
The other key benefi t to the operator of the increased monitoring frequency of automated UT systems is that changes in wall loss rate could be detected early prior to the requirement for an unplanned shutdown for repair/replacement and more importantly before a loss of containment. Corrosion is estimated to be responsible for 25 – 30% of all shutdowns,1 costing £3.4 billion/yr in the US alone.2 With fl aring during shutdowns and restarts combined with loss of containment being major contributors to emissions, implementing a preventative maintenance programme off the back of an online UT monitoring is a cost-effective way for the refi ner to hit emission reduction targets.
Case study 2: targeted monitoring – increasing productivity and enhancing safety
In another example, a European refi nery had identifi ed a number of high temperature locations which were showing increased corrosion and required increased monitoring, with no prospect of conventional inspection without a full plant shutdown. The customer sought an automated system which could provide automated, on-stream wall thickness measurements with data being used by both asset integrity and process control teams.
The customer had an active WirelessHART network which was feeding data from a range of process and safety sensors directly to their process optimisation software within the plant control room. The automated UT system needed to integrate with the host WirelessHART network and feed data to the control systems. The data also needed to be accessible to the plant asset integrity team who sat outside of the plant
fence. All of this needed to be achieved without the installation of any additional IT infrastructure and without adding additional cybersecurity protection measures. All of the installation locations required a minimum ATEX Zone 1 certified solution and would need to operate at between 150 – 380°C.
In this case, HotSense intrinsically safe UT sensors were deployed with a WirelessHART monitoring node, in the areas of concern during normal plant operation, and integrated into the existing plant-wide WirelessHart operating system (see Figure 2). The system performs all the thickness calculations in the field and presents the process variables to a wireless gateway, which are passed directly into the host control and historian systems.
As a result, at low incremental cost, this investment allowed continuous monitoring of the areas of high risk on the plant, and by avoiding shutdown during installation and ongoing operation served to increase plant productivity and reduce operating costs.
Conclusion
Shifting fuel and energy demands are placing pressure on the refining industry to output a changing product portfolio and do so at reduced operational costs to ensure sustainability of the industry. At the same time, environmental and legislative pressure to reduce carbon emissions are adding further challenges to plant operators.
The change in process conditions presents a particular asset integrity challenge as IOWs must be frequently updated based on limited data whilst ensuring the highest levels of safety and plant availability. A shift towards the use of automated inspection methods, such as ultrasonic inspection for wall thickness and corrosion monitoring, enables plants to monitor the effect of process and feedstock change on assets and optimises processes and interventions accordingly.
WirelessHART enabled automated systems allow data to be collected from all plant assets, including remote locations, and aggregated at a centralised location for analysis. The data collected from such systems can be critical in maximising plant availability and detecting the potential for loss of containment or unplanned shutdown that would otherwise be missed by traditional manual methods.
References
1. GE, Corrosion & Erosion – Inspection solutions for detection, sizing & monitoring, 2010. 2. NACE Cost of Corrosion Study, 2002.
Page Number | Advertiser 38| ABC 25| American Petroleum Institute (API) 59| Ariel Corp. 57| Atlas Copco Gas and Process
OFC & 13| Chart Industries 61| Cook Compression 55| Elliott Group 04| Eurotecnica OBC| Filtration Technology Corp. (FTC) 02| Haldor Topsoe IFC| Hitard Engineering 63| Howden 19| HTAC | HGT 67| ILTA 33| Johnson Matthey 79| LARTC
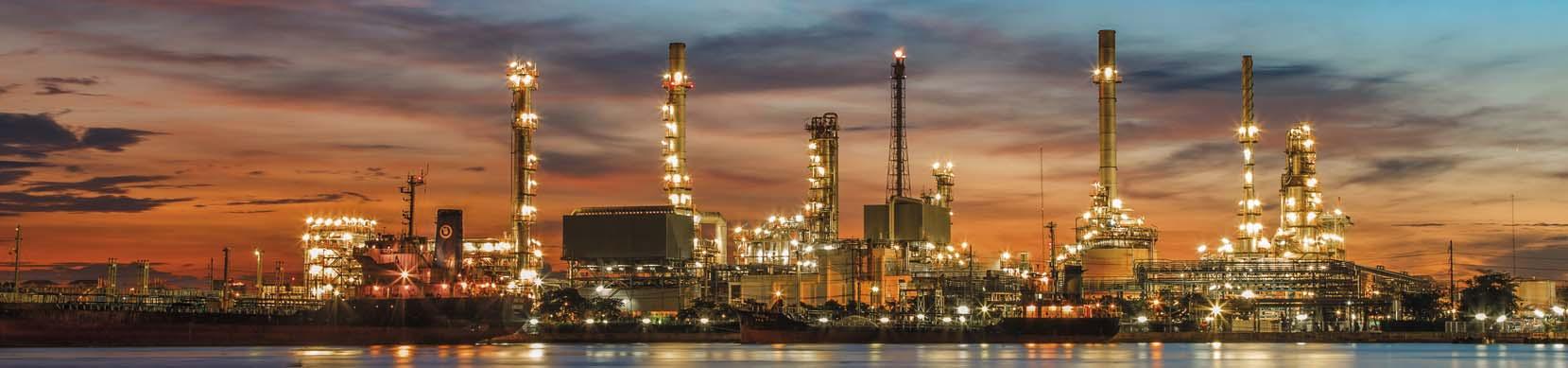
AD INDEX
41| Merichem Company 53 | Mitsubishi Heavy Industries Compressor International 64| Neo Monitors 08 - 09| NEUMAN & ESSER 69| Owens Corning 22, 44 & 77| Palladian Publications IBC| Paqell 27| RIKEN KEIKI Co. Ltd 31| S.A.T.E. 73| Servomex 07| Siemens 74| Sulphur + Sulphuric Acid 2021 37| Union Tech 15| Uniper 44| Valve World Expo Americas 77| World Petroleum Congress