
10 minute read
The ins and outs of corrosion studies
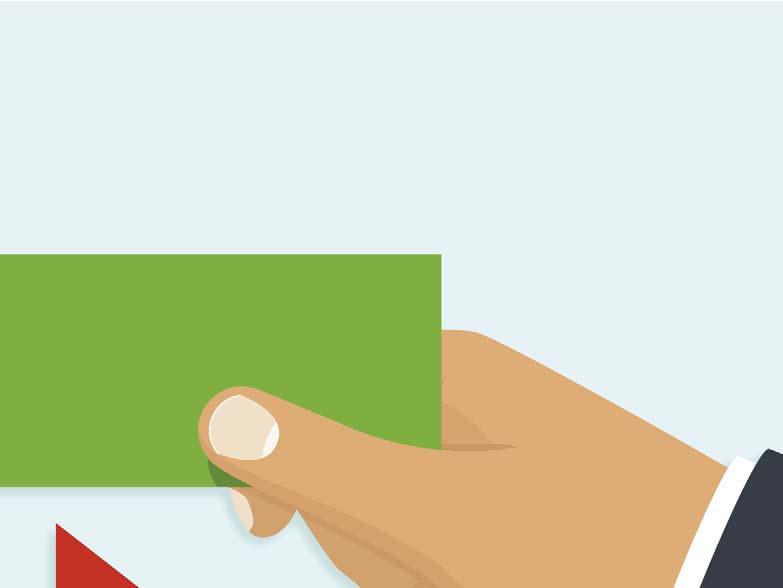
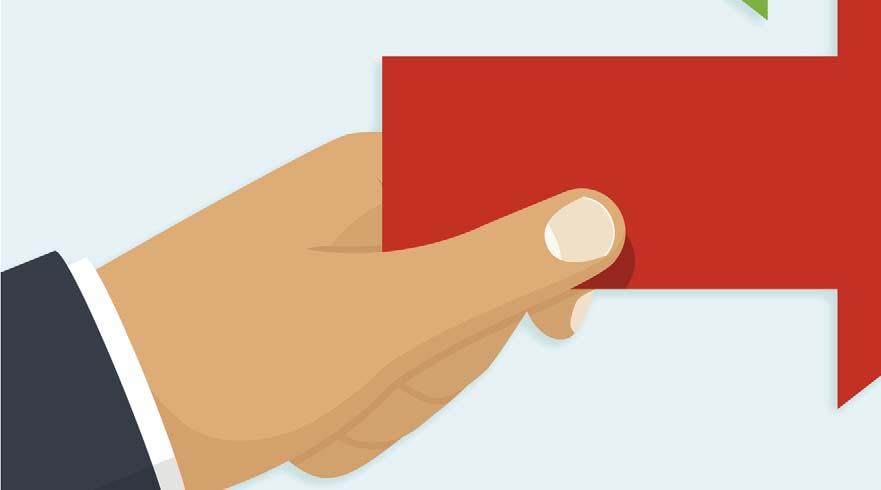
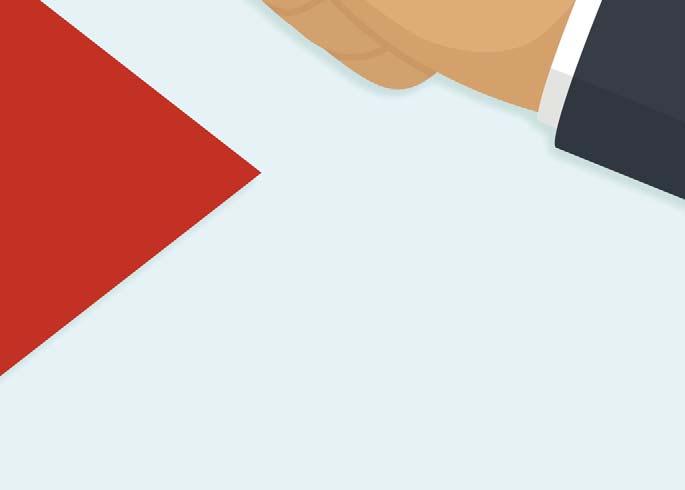
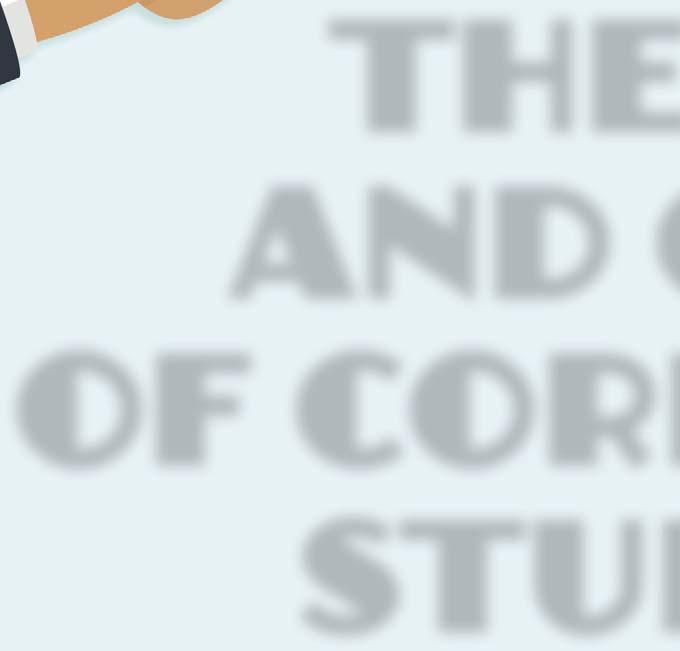
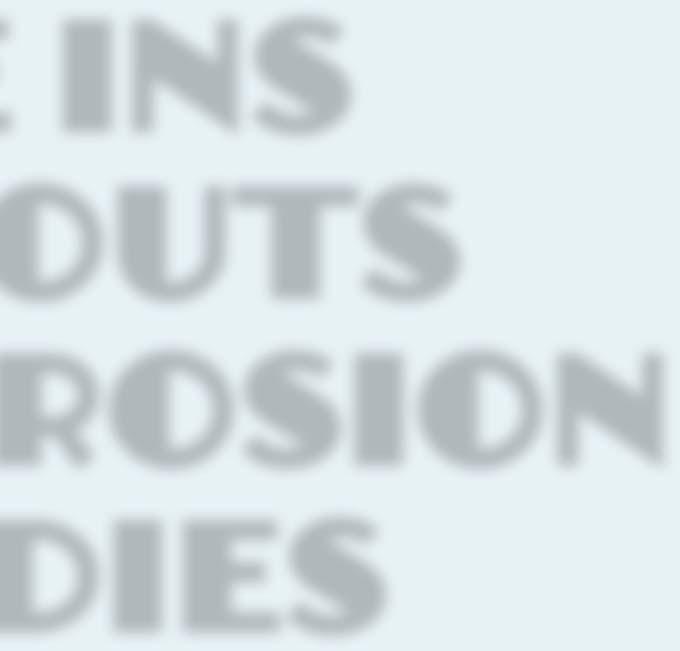
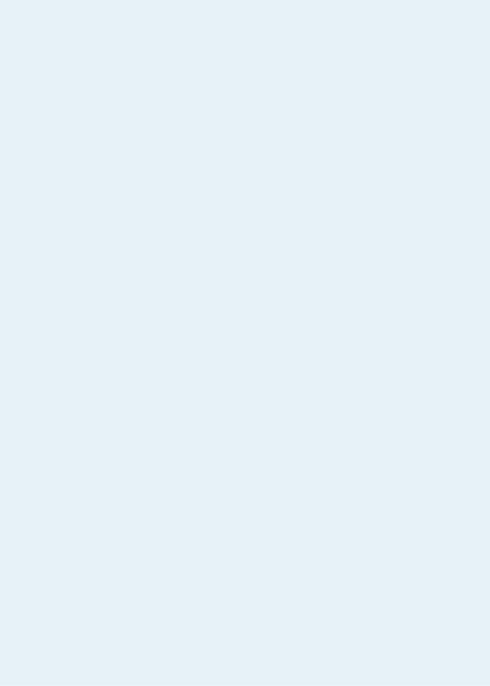
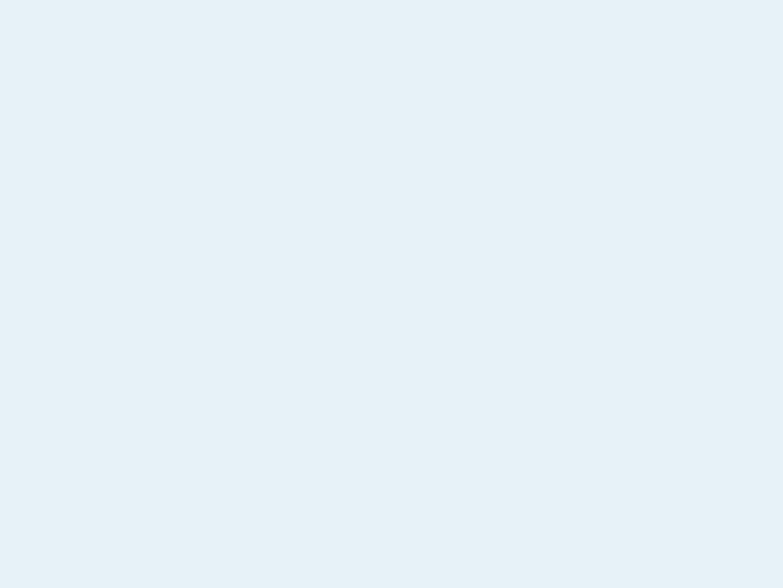
Jim McVay, MISTRAS Group, USA,
explains how corrosion studies can be used to determine potential damage mechanisms, corrosion types, and corrosion rate/potential to inform risk assessment and inspection planning.
Corrosion studies – also known as degradation mechanism reviews (DMRs) – examine the process, design, materials, and history of a process unit. They are now relatively common exercises in operating facilities, necessary for the suffi ciently well-grounded and dynamic inspection programmes needed in today’s operating environments. API RP 970 (Corrosion Control Documents) helps, but it has omissions in areas that responsible operators need to address. Standardised criteria for consistent determinations of environmental cracking mechanism vulnerabilities is but one example; rigour of data review and analyses is another.
The execution of a corrosion study is complex. It requires a multi-disciplined team of inspection and engineering subject
matter experts (SMEs) with advanced knowledge of mechanical, corrosion, reliability, and materials engineering disciplines. With such a wide range of competencies required, operators can benefi t by partnering with a third-party service provider to ensure corrosion studies are executed accurately and effectively.
This article will discuss good practices and possible pitfalls in executing corrosion studies, along with possible practices that can be implemented to optimise these efforts.
Key participants in corrosion studies
Carrying out comprehensive corrosion studies requires a team of dedicated and well-versed professionals who know how to perform their respective responsibilities. Key participants in corrosion studies include: Inspection/process supervisors. Corrosion experts. Operations. Process engineering. On-site/internal corrosion/metallurgical engineering. Inspectors/inspection planners.
Other experts can be helpful as well, such as process SMEs, maintenance, and chemical vendor representatives. MISTRAS Group provides experts for each of these specialties, allowing proper damage mechanisms and defects to be evaluated.
In-depth look at process corrosion study process
The process of executing a corrosion study is involved, but is ultimately extremely useful for the operational well-being of process units. The process is viewed in steps: Selection of corrosion expert and corrosion team company personnel resourcing to support the intended study. If the right people cannot commit necessary effort to the study, it is advisable to do it another time. Determination of work processes, schedules and required deliverables. Information/data gathering: this part of the process is driven by the corrosion expert personnel. The owner is responsible for responsiveness and the quality of data provided. Corrosion review meeting: the corrosion expert facilitates a corrosion review meeting. Full plant attendance and participation is ideal. Corrosion report: a corrosion study report is prepared.
It features the basis, findings, and recommendations for mitigations and process controls. The corrosion study report should be thoroughly reviewed by the corrosion review team as a whole and accepted by the owner for the purpose of ultimately well-informed inspection programming.
Critical plant information that should be reviewed includes the following: Applicable operations manuals and procedures. Past, current, and future degradation-related operating data requested by the corrosion expert. Current process hazard analysis (PHA) reports. Simplified process flow diagrams (PFDs). Piping and instrumentation diagrams (P&IDs). Equipment design and materials of construction. All applicable management of change (MOC) completed since the last corrosion study. All available information on damage mechanism related incidents from the owner’s incident management database and industry sources (e.g. American Fuels and
Petrochemical Manufacturers [AFPM] incident portal). Inspection histories. Any available corrosion control documents (including material flow diagrams). Leak repair locations and histories. Exchanger bundle replacement histories (if applicable). Any special accelerated corrosion inspection programmes. Refinery dead leg lists and dead leg inspection programme history. Condition monitoring location (CML) corrosion rate data and analysis and other corrosion rate information (corrosion coupon analysis, corrosion probe data, etc.). Previous applicable corrosion studies.
Special attention in the form of special tasks and checks should be attended to in an effort to ensure the quality of the corrosion study. Process management, verifi cation and quality of all data reviewed, corrosion review team composition, damage mechanisms considered, and corrosion study report content are among the topics that could be addressed. Other quality related topics are discussed below. Assembling and using a checklist to keep track of determined quality-related tasks and checks through a corrosion study is also a valuable tip. Organising quality-related tasks and checks tasks is a good idea to stay on top of the study. Useful categories to include in a checklist are: Task category. Required elements. Task responsible person. Corrosion engineer and/or owner inspection supervisor assessment of compliance (if applicable). Objective evidence of compliance to study requirements. Owner/supervisor approval. Additional comments.
Corrosion report deliverables
The corrosion expert typically writes a fi nal corrosion report, comprised of a summary of the corrosion study activities. Consideration should be given to require a unit premise document and process summary which may be supplemented by a critical asset level process data spreadsheet containing information such as representative fl uid/phase, operating temperature, operating pressure, toxics and toxic percentages identifi ed for each unique process.
Applicable degradation mechanism descriptions should be included in the report. All PHAs and MOCs reviewed should be documented. The report should include all

Figure 1. Since different inspection results can result in different CML data, corrosion studies help to more accurately determine the amount of corrosive CMLs, enabling plants to more effectively plan their inspection and maintenance strategies.
injection and mixing points, dissimilar metal weld locations, and vulnerable piping systems and circuits. Expected corrosion rates for each asset should be presented and, if requested, external corrosion rates should be included.
For a comprehensive characterisation of corrosion, applicable environmental cracking, and other damage mechanisms, the affected assets, expected corrosion rates or ‘potential/probability’ assignments for each damage mechanism as applicable, as well as possible locations of damage on each asset, should be identifi ed. Integrity operating window (IOW) tables that support determinations of the corrosion studies and assist with effective mitigation could be included as well. Other technical recommendations, such as material upgrades, are benefi cial to the report too.
Quality control/quality assurance factors
Accuracy and completeness of corrosion studies are critical to the effectiveness of fi xed equipment inspection programmes. Active involvement by refi nery inspection, process, and/or operations personnel supporting the corrosion expert helps to ensure the corrosion studies are technically correct and adequately support mechanical integrity (MI) programme requirements.
The inspection supervisor should review and approve all completed corrosion study reports for completeness and compliance with company standards and expectations. All other corrosion review team members for each study should also review the completed corrosion review and approve reports for accuracy based on their knowledge and expertise. Traditionally, approvals require a documented signature so that quality assurance is guaranteed.
A corrosion expert (often from a third-party contractor) can verify knowledge of process and degradation mechanisms and how determinations will be utilised. They should establish standards from degradation mechanism assignment to ensure repeatability and compliance to ‘Recognized And Generally Accepted Good Engineering Practices’ (RAGAGEP).
Verifying the completeness and accuracy of all process safety management (PSM) related-information used in the study is important. PSM information includes PFDs, P&IDs, material fl ow balance sheets, and material fl ow diagrams (MFDs).
The inspection supervisor should also verify the accuracy and completeness of inspection data in the inspection programme and in other records used in the corrosion study. This data could appear in original fabrication records, inspection reports, thickness data, repair records, and more.
Common pitfalls of less managed reviews
There are various ways in which pitfalls can occur during a corrosion study and lead to less-managed reviews, which can cause greater issues down the line and affect operations once the review is complete and subsequent operational activities take place.
A lack of technical and/or institutional knowledge amongst plant personnel is a common pitfall. A corrosion engineer may have little familiarity with their current company’s inspection and corrosion control standards or programming procedures and software. The company may have no peer review and corrosion study services. Owner process data gatherers may require more experienced support to get the right data in the right amount.
Critical corrosion review process omissions are another pitfall. No review of critical internal documents like MOCs or past corrosion studies and no review or consideration of industry incidents is a red fl ag. It is not a good idea for little direct plant data review or to leave process reviews only at PFD level. It is imperative that there is adequate owner team support in data gathering or team meetings. Inadequate capturing of corrosion study meeting discussions is a faulty habit that can lead to a non-fully realised review.
Expected corrosion rate assignments can also be an issue. The corrosion engineer may not review and consider plant non-destructive examination (NDE) data and analysis due to initially writing it off as ineffective. Inconsistencies in determined corrosion and the corrosion engineer choosing arbitrary corrosion rates to ‘drive inspection’, with little understanding of impact on risk analysis and inspection planning, can lead to ineffi ciencies and improper review.
For degradation mechanism assignments, a corrosion engineer may not consider all potential degradations mechanisms in API 571 or other applicable standards. Criteria for when to assign or not can be inconsistent, arbitrary and not necessarily in line with RAGAGEP standards. Determinations may be made with little or no actual process data, relying on known past practices. This leads to imprecise guidance on assigned degradation mechanisms. An engineer’s consideration of past inspection data may also not adequately consider quality/effectiveness.
Comprehensive and accurate fi nal reports are essential to the corrosion study process as a whole. Errors in the fi nal report may be attributed to inadequate documentation in several critical areas, such as unit premise, alternative operating regimes considered, and team meeting discussions. The report format not being aligned or otherwise conducive for ready extraction of necessary data for inspection analysis and planning purposes should be avoided. Technical recommendations not clearly presented and in a separate section contributes to a poorly organised report. Of course, a fi nal report should be thoroughly reviewed and approved by the owner.
Special topics
There are a few special topics to be mindful of when dissecting corrosion study practices. These aspects of the review help to ensure that reviews are conducted as effi ciently and successfully as possible.
For the corrosion expert, all requests should be clear and documented. All operating regimes should be considered, as direct process measurements should always be used rather than judgement or estimates. Wherever possible, modelling could also be pursued for determining or validating the most critical process parameters used in the study.
Expected corrosion rate determinations should consider available actual NDE data and analysis of said data. The impact on inspection risk assessment and planning should always be considered when making determinations.
For corrosion study assignments, it is ideal to consider using measured vs modelled critical data wherever possible. Standardising degradation mechanism assignment thresholds can keep tasks organised, and considering likely effectiveness of historic inspections when factoring them into degradation mechanism assignment determinations is useful.
Dissimilar metal welds (DMWs) are important to be mindful of. Establish clear guidance for determining degradation potential at locations depending on metallurgies involved and service conditions. It is important to be mindful of thermal and environmental cracking, as well as galvanic corrosion, at these locations. The plant needs to be able to compile a complete and accurate list of all DMWs locations for consideration.
Study up for the best results
As corrosion studies can be an involved and daunting task, plants can benefi t by working with a third-party provider, such as MISTRAS, to effi ciently execute the review. Teamwork, effective communication, and diligent organisation of tasks can truly be the deciding factor of a successful, well-executed and less-managed corrosion study. The effort that is put into reviews is ultimately what operators can expect the quality of the fi nal product to be. When completed properly, corrosion studies are an undeniably essential piece of information to have for risk assessment and inspection planning efforts.
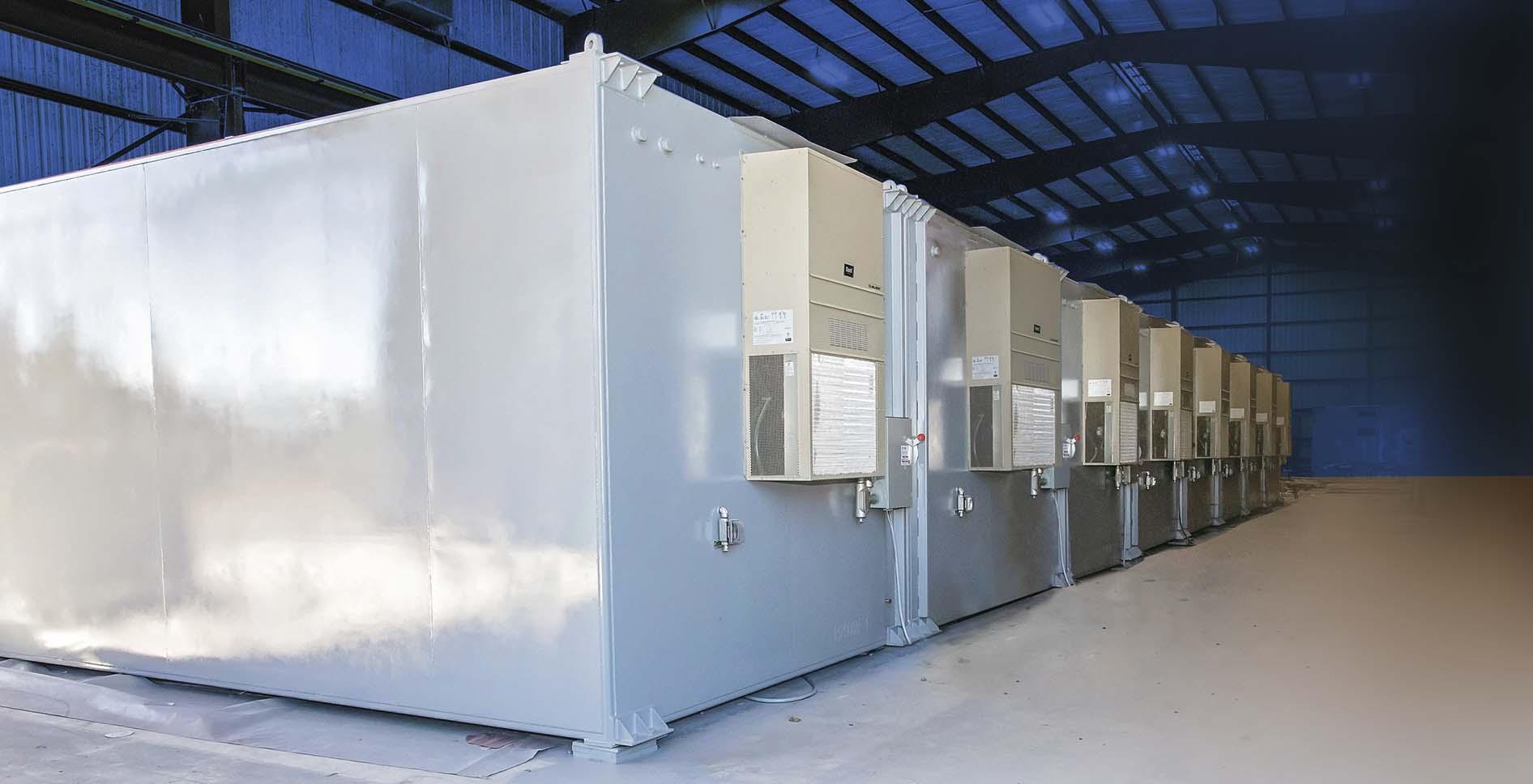
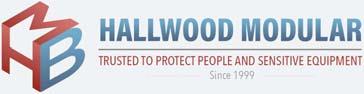
