
9 minute read
A clear plan of action
Audit proposals therefore need to be exceptionally detailed, including vendor information. It is advisable to choose an equipment vendor that offers service as well; for example, Sentry Equipment offers all service in-house, without outsourcing to another company that could stymie efforts to implement an audit. Choosing a full-service partner allows a plant to seamlessly request and implement an audit with the original equipment vendor.
A valuable SWOT analysis
A sampling audit is a technical review of a sampling system’s strengths, weaknesses, opportunities and threats (SWOT). Audits are conducted by certifi ed sampling experts to identify SWOTs in business areas, sampling units/types and within specifi c samplers. The analysis reviews the following: If any updates, modifications or new systems need to be added. Modifications can include: retrofits of current equipment, replacement of worn lines, installation of new sample coolers, analysers, etc., or adding a secondary cooling system or a magnetite trap. Priority of divisions based on the refinery’s needs. Estimated costs of potential repairs, edits, etc. Risks associated with not taking recommended action(s).
For example, the audit might note that close attention should be paid to the needle assembly on a bottle system, as various samples tend to leave crystal-like deposits that can lead to plugging.
Audits also take into account pressure (PSI), temperature, and processes being audited to make a series of recommendations for the refi nery.
Tailored recommendations
Each audit should be customised to the plant and domains or locations within the plant. No two samplers or processes work the same way, and many sampling areas are often under different types of management, depending on the location within the plant. These elements need to be considered when evaluating the system as a whole.
Prioritised actions
The result of an audit is a comprehensive list of recommended actions that plant operators can take to optimise their sampling systems, from repairing equipment to replacing an entire system. When identifying needs, the sampling expert conducting the audit should use a system for identifying priorities.
For example, Sentry provides comprehensive insight into all samplers within a plant, regardless of manufacturer or brand, providing a maintenance schedule or best practices to ensure the longevity of repairs, modifi cations and replacements.
Table 1. Example of Sentry Equipment’s audit report for a refinery customer
Sampler type Key components
TSI-3 bottle system TSI-31-T-SS sample valve Inspect sample valve for proper function. Replace if cycle positions are not producing desired results This system is not currently functioning. Main line feeding the panel is plugged. Additionally, the N2 system has at minimum a faulty flow meter. If plug is cleared, entire N2 system should be serviced before returning to service
Routine maintenance guidelines Notes
Table 2. Example of a sample station priority matrix
Highest priority Medium priority Lower priority
Little to no existing sample Some existing sample Existing infrastructure is station infrastructure and station infrastructure but mostly working and largely regularly caught, higher risk in very poor condition and compliant with O-029 samples largely not compliant with but needs some minor O-029 improvements to be fully compliant
Samples from bleeders Samples from behind single isolation Sour samples in fresh air High pressure samples Certain bag samples which could be caught through sample stations Samples without essential safety features (boxes, cooling systems, etc.) Stations with broken valves/vents Stations which are totally plugged or inappropriately designed for sample being caught Stations without double isolation or safety purges like purges/vents Stations still mostly usable but with serious flaws Stations which need spring loaded valves Stations with vents not routed far enough away from the collection point Stations with inappropriate thickness of needles Stations missing gauges and flowmetres Stations which do not have constant circulation (if required)
An audit helps optimise plant systems
Running an effi cient refi nery requires real-time data analysis. Gleaning critical insights from sampling equipment is essential to product quality, safety and operational processes.
A properly designed representative sampling system with the right sampling equipment ensures process samples are repeatable and reliable to help refi neries maximise return on investment, better manage loss control, and reduce operating costs.
Matching the equipment to the application
Capturing representative samples and protecting the operator is critical in high-temperature and high-pressure applications commonly found in refi neries. It is therefore essential to match an application to the sampling equipment. A sampling audit can also ensure that the right equipment is matched to the application(s) within a refi nery.
Automatic samplers help to optimise sampling accuracy and repeatability for hydrocarbon liquids such as crude oil, condensates and oil and water mixtures. They isolate the process without interrupting the process line, and offer a variety of different types depending on the application.
An audit will ensure that applications are matched with the correct sampling equipment throughout the course of a refi ning process.
Assess the need for training
While an audit does not specifi cally measure plant personnel’s knowledge of the sampling systems, it can often uncover areas where operators need training, whether on an existing system or a recommended new piece of equipment.
Not only does training ensure new operators get adequate guidance, it also helps experienced operators stay up-to-date on proper operating procedures. An audit can help management clarify where training should occur, from a junior engineer to maintenance personnel.
Training often offers detailed information on application-specifi c equipment so operators can safely collect emission-free samples. This should include: Types of sample systems installed in the refinery. Why each type of sampling system is used. How to use each sampling system. How to conduct sample collection preparation. Common issues with each type of sampling system. General maintenance guidelines. Routine maintenance checklist.
An audit can also help supply plant personnel at all levels with this critical information.
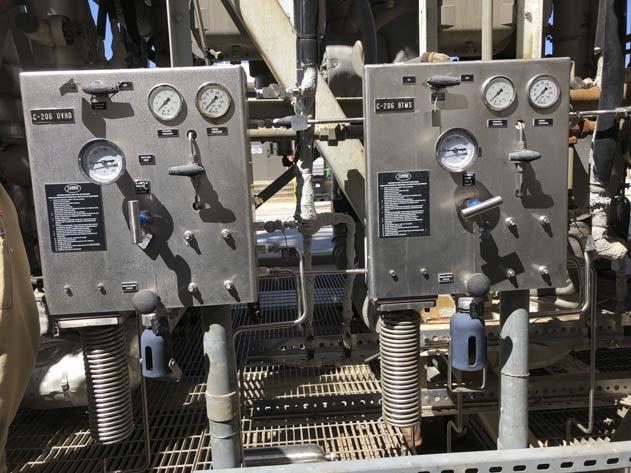
Figure 1. Example of low-emission sampling systems.
Figure 2. Technicians inspecting sampling equipment for audit.
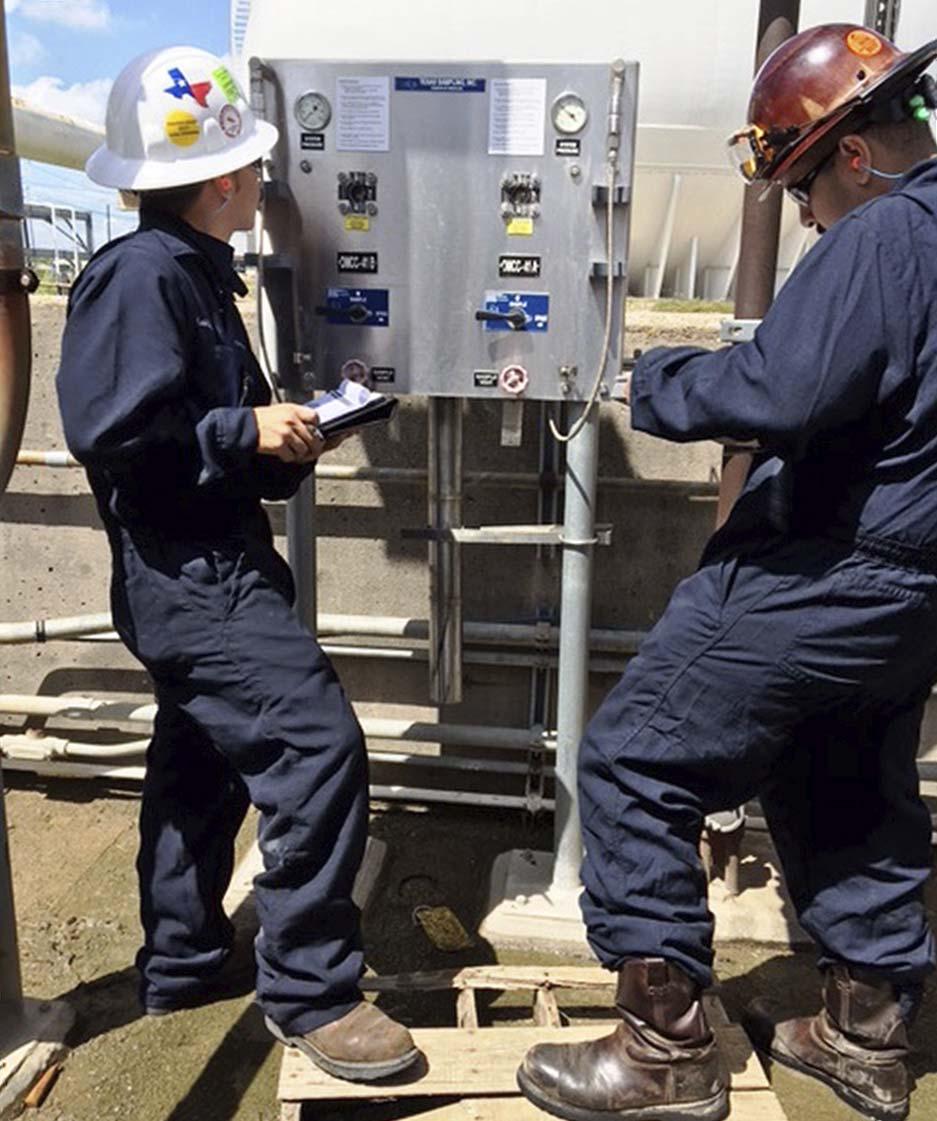
Staying current with the latest regulations
Sampling audits are even more important in light of evolving regulations and guidelines. Not meeting the new and current US Environmental Protection Agency (EPA) regulations can result in large fi nes, as well as damage to the environmental and plant personnel. It is advised to protect processes and prevent these costly risks with representative sampling.
In December 2020, the EPA published its fi nal version of the updated ‘Fuels Regulatory Streamlining’ rule, which will take effect in January 2022. The new rule updates the EPA’s existing gasoline, diesel and other fuel quality programmes to improve overall compliance assurance and maintain environmental performance while reducing compliance costs for the industry and the EPA.
As part of the EPA’s continual effort to ensure that fuel quality standards established under the Clean Air Act (CAA) continue to be met, it streamlines and modernises existing fuel regulations under 40 CFR part 80 fuel quality regulations by transferring them into a new proposed set of regulations in 40 CFR part 1090.
The updated rule takes a wholistic look at the existing part 80 regulations, attempting to consolidate the many different and overlapping regulations into the proposed part 1090 regulations that will better refl ect how fuels, fuel additives and regulated blendstocks are produced, distributed and sold in today’s marketplace.
Any company involved in the production, distribution or sale of transportation fuels, including gasoline and diesel, could be affected by this update.
Under the current EPA Part 80, gasoline manufacturers are required to measure 11 complex model parameters. For the updated part 1090, this has been reduced to just three parameters: sulfur, benzene, and Reid vapour pressure (during summer months only. See the rule for more details). Diesel manufacturers will have to continue to test for sulfur.
Accurate test results depend upon the sample being representative of the entire fuel batch. To achieve this accuracy, it is critical to be sure that the representative sampling system meets these updated sampling requirements. A sampling audit will review a fuel sampling equipment and application to ensure readiness before the EPA Fuels Regulatory Streamlining rule takes effect in 2022.
Conducting a specialised sampling audit can help guide plants in making critical business decisions and implementing high-quality sampling processes.
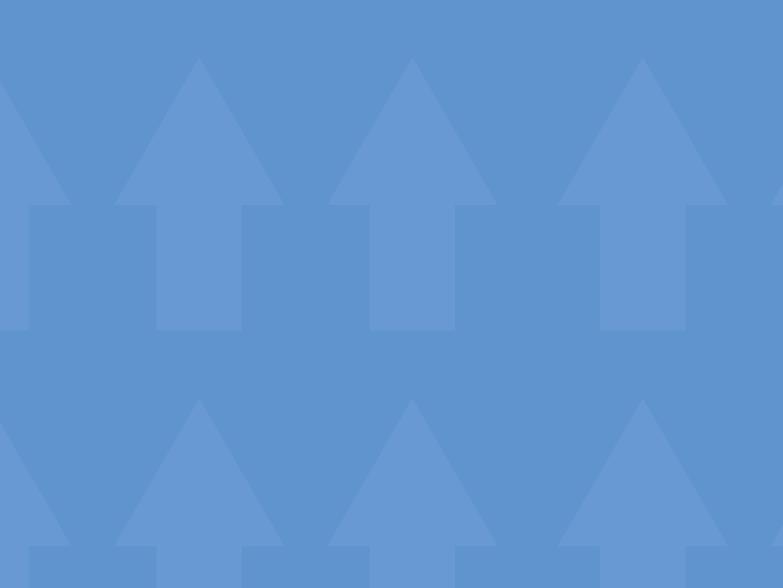
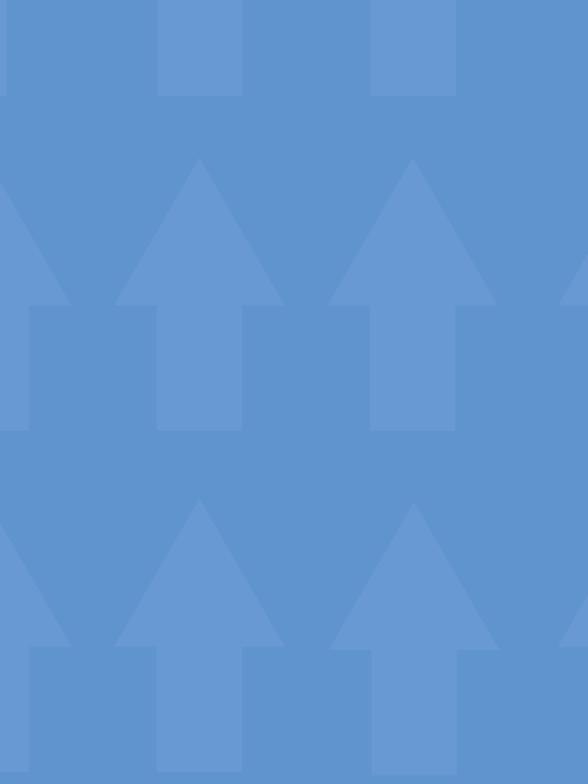
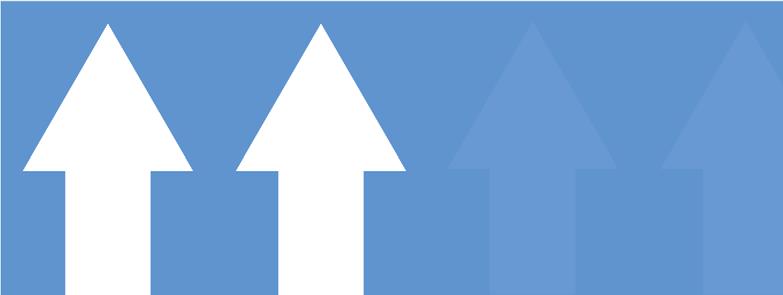
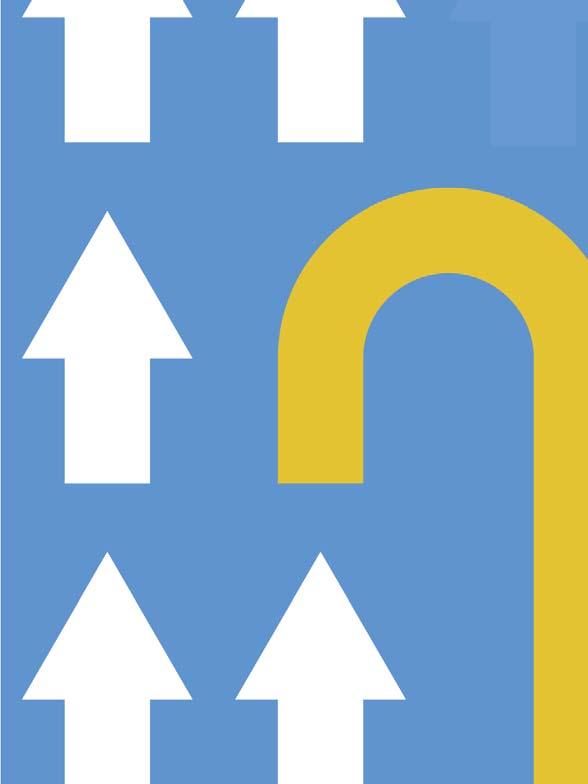

Saeid Aflakian, Merichem Company, USA, presents a new approach to lowering total sulfur in the LPG product stream.
Recent changes in fuel standards complying with the US Environmental Protection Agency’s (EPA) Tier-3 have caused many refi ners to address their compliance methodology for fuel sulfur levels. One area that is often missed is the advancements available in caustic treating. Caustic treating provides a lower CAPEX and OPEX, as well as no reduction in octane, and continues to fi nd a place in the modern refi nery process portfolio. Many caustic treating systems can achieve less than 30 ppm total sulfur in LPG blends by removing acidic sulfur species, such as hydrogen sulfi de, carbonyl sulfi de and light mercaptans. What is not well known is that this same technology can reduce extractable sulfur to less than 3 ppmw (not counting non-acidic inert sulfur species) with the application of new developments in process layout and catalysts. This article will discuss the operation of such a unit at a major Padd 2 refi nery in the US.
The need for ultra-low sulfur (ULS) caustic treating technology
Merichem worked with a major Padd 2 refi nery that produces a high volume of fi nished products such as gasoline with a throughput capacity of approximately 170 000 bpd. Refi nery personnel were evaluating capital scope options and requirements for manufacturing gasoline with 10 ppm sulfur to meet EPA Tier-3 regulations. As a result, they determined that the total sulfur content of their butane/butylene (BB) stream would need to be maintained at less than 10 ppm. To allow for inert sulfur compounds already present in the hydrocarbon feeds, the sum of unextracted acidic sulfur and back-extracted disulfi de oil would need to be 3 ppm or less as sulfur.
Caustic treating removes acidic sulfur species. The alkaline pH of the caustic solution reacts with the sulfur species (most notably mercaptans) to form water-soluble, ionic compounds which preferentially move into the caustic phase. Once separated from the hydrocarbon phase, the aqueous sodium mercaptides are sent to an oxidative regeneration unit where heat, oxygen and catalyst are introduced. The mercaptides react with the oxygen to form mostly insoluble



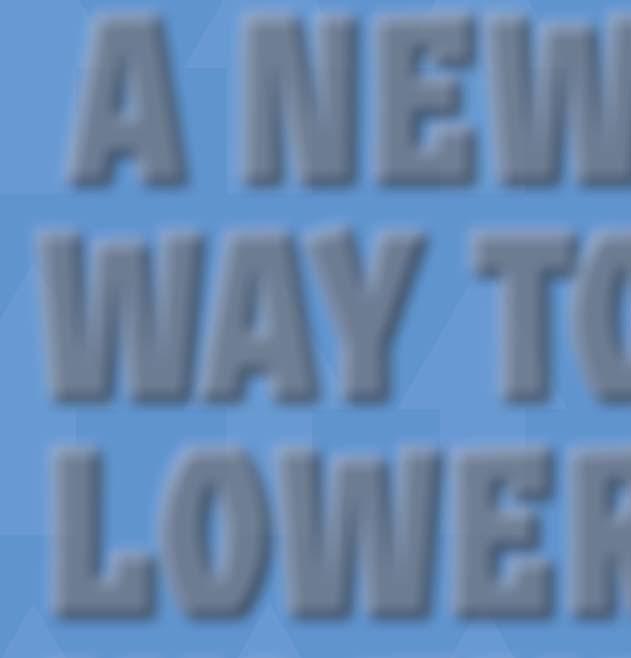

