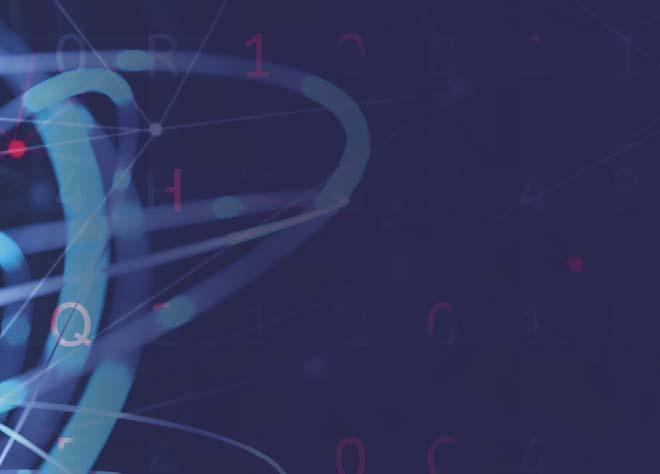
10 minute read
Simulation in a world of trouble: part one

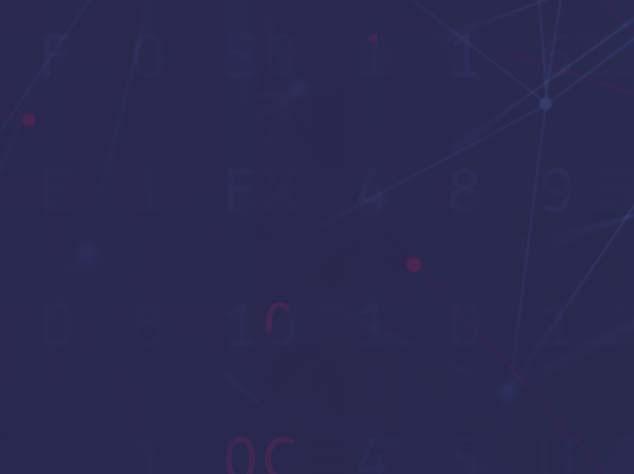
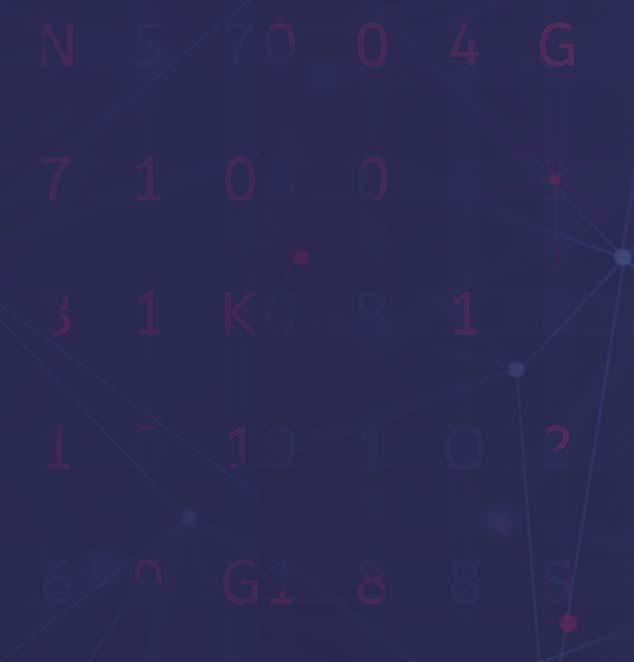

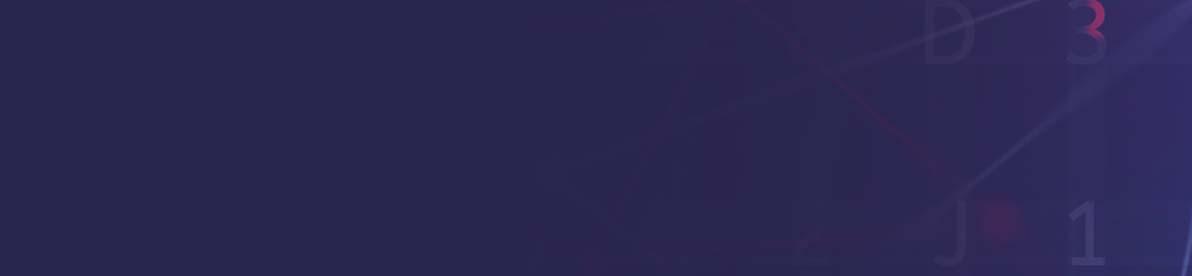

Simulation tools are used extensively in a wide range of activities, from plant design, unit revamps and troubleshooting, to plant optimisation and unit monitoring. Confi dence and trust in a simulator are usually gained by running simulations against measured plant-performance data. But what happens when measurement and simulation do not align? Can we learn anything from such experiences?
In the fi rst installment of this two part article, two case studies are used as examples, each one initiated by disparity between simulation and plant data too large to be attributed to just modeling and measurement errors. Examples are defective equipment and contaminated solvents. In the second part of this article, poor temperature control, and a problem with the model itself will be discussed.
Each case compares simulation results with measured performance metrics, and each one uses a combination of data and simulation to deduce logically a diagnosis and to resolve the issue. In each case there is some gross defi ciency either in a measured parameter, in the integrity of one or more pieces of equipment, in faulty or overly-simplistic thinking, or in the simulator itself.
Case study 1
Following an internals and solvent change out, a pair of fuel gas treaters in a US West Coast refi nery were unable to reach the treated gas H2S level that the simulator they were using (modifi ed ideal stages) said should be achieved. The sulfur emissions from the units were on the cusp of exceeding the permit limit, meaning that corrective action was imperative. A consultant was approached for advice. Because the two treaters are so similar, this article will focus on only one of them.
The treater originally used trays to treat the gas using diethanolamine (DEA) which resulted in gas comfortably below 4 ppmv H2S. To improve throughput, trays were replaced with random packing (#2 Minirings) which lowered pressure drop and increased tower capacity. To take advantage of its lower required energy for solvent regeneration, N-methyldiethanolamine (MDEA) was substituted for DEA. Simulation of post-change-out conditions showed that both treaters were capable of producing treated gas below 1 ppmv of H2S. However, performance tests after the revamp showed the treater was actually achieving only 26 ppmv H2S – far higher than expected – and contributing to the plant now pushing emissions limits.
The consultant surmised that the liquid residence time on the packing was not nearly long enough to achieve treat, and he made the recommendation to put the original 17 trays back into the column. When the switch back was made, a repeat of the performance test surprisingly showed that column performance was unchanged – it was still producing 26 ppmv H2S in the treated gas. The reason this happened is explained below.
When the trayed and packed cases were run in Optimized Gas Treating’s (OMT) ProTreat® mass transfer rate-based simulator using MDEA, the predicted H2S content of the treated gas for both internals types was calculated to be 0.64 ppmv, but the measured value was a factor of 40 higher. This is too large to be anything other than an error either in the basic data fed to the model or in the model itself. What turned out to have been overlooked was the real solvent analysis, i.e. incomplete data was used in the model. It was not realised that heat stable salts (HSS) have a profound effect on treating, primarily by affecting vapour-liquid
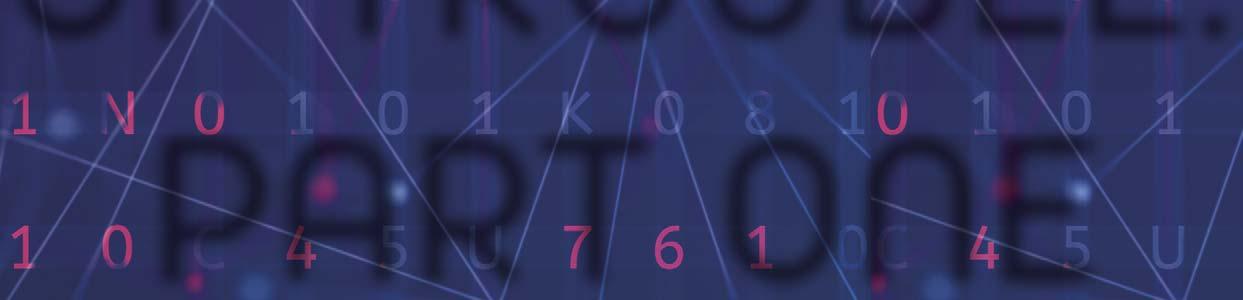

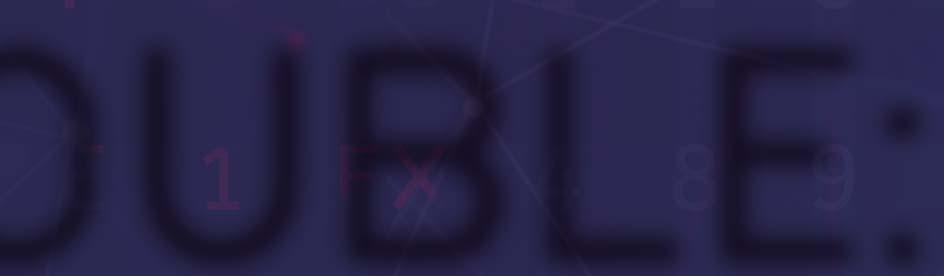

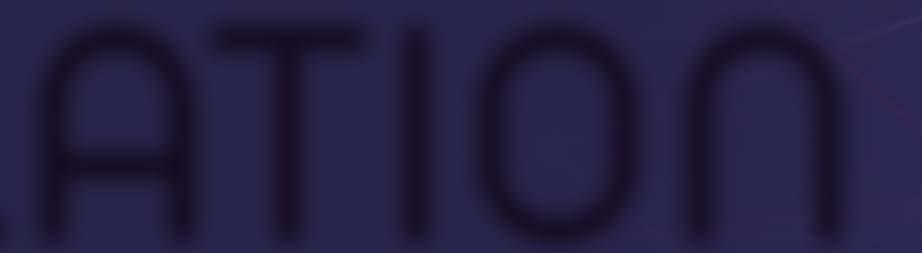
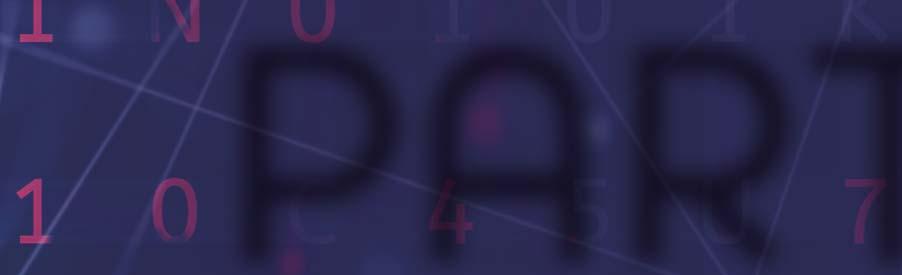
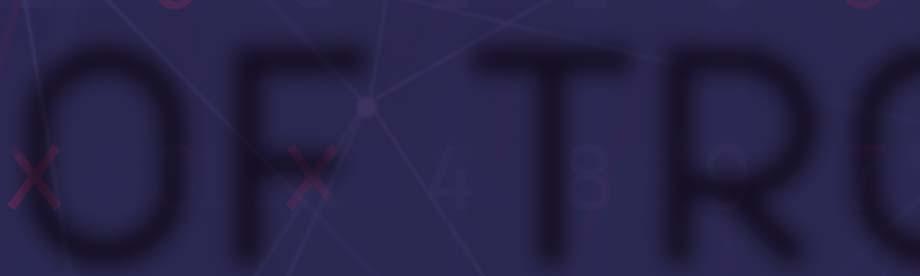
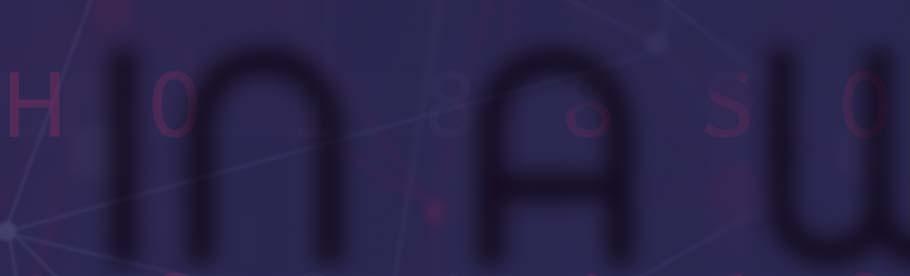
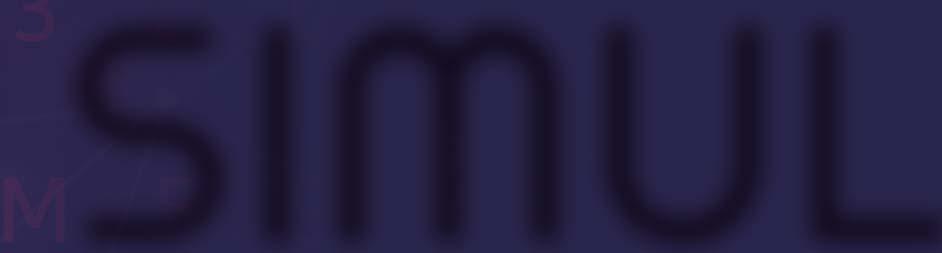

equilibrium over the lean solvent. In this case, it happened that the 38 wt% MDEA solvent contained 2.2 wt% heat stable salts (230 ppmw sulfate; 2580 ppmw acetate; 3225 ppmw thiocyanate; 14 305 ppmw formate; 1675 ppmw chloride). These levels of HSS are fairly typical of amine solvents in refi nery environments, a fact that should be kept in mind when trying to resolve amine treating problems in refi neries. When the simulation was rerun with the measured HSS levels (how the HSSs actually break down into individual salts matters), the ProTreat simulation produced a treated gas with 26 ppmv H2S, in perfect agreement with measured data.
This is an example of faulty, simplistic thinking combined with a lack of understanding of the process chemistry which resulted in presenting the model with incomplete data. In ignorance, the faulty assumption was made that HSS had no infl uence on the process, and was therefore ignored. The lesson from this example is that solvent contaminants can make a huge difference to both a simulation and to real performance. Ignoring this resulted in considerable lost profi t and wasted time performing multiple, expensive revamps to solve a problem that, in reality, had a completely different, unrelated cause.
Case study 2
In this case, a leaking heat exchanger caused simulations to produce wildly different predictions from what was being measured in the plant. The simulator was not wrong; it was just being applied when assumptions about equipment integrity were violated. A great use for a simulator is to point out defective equipment (including fl ow meters).
A refi nery amine unit came out of a turnaround six months prior, and its performance was deteriorating. Revamp work in the turnaround included: The switching of sieve trays to valve trays in the amine regenerator for increased capacity. The increase of H2S to the system by approximately 20 tpd, leading to reboiler duty being increased from 77 to 85 million Btu/hr, the limit of the system. The increase of the DEA solvent strength from 25 wt% to 30 wt% to handle the additional sulfur load.
Pertinent observations made over the time since the turnaround include: The H2S lean loading measured immediately following the turnaround (0.006 mol/mol measured) was higher than prior to the shutdown (0.001 – 0.003 mol/mol), and it had been increasing steadily ever since. It was currently at 0.012 mol/mol (4 – 12 times the pre-turnaround value). Several operators felt the new trays were already fouled. The tray supplier claimed the trays were functioning properly and noted that valve trays are slightly less efficient than sieve trays, the price that must be paid for increased hydraulic capacity.
When a plant fi rst runs into trouble, the engineers and unit operators usually come up with a host of explanations. Speculation runs rampant and almost everyone has their own theory. But troubleshooting must be based on data, not speculation. During the turnaround, no changes were made to the absorber, although changed absorber performance is what fl agged the problem; however, regenerator trays were changed from sieve to valve type. It is OGT’s experience that crossfl ow tray type is important in determining hydraulic performance, but it does not play a great part in deciding treating performance. The most signifi cant observation was the 4 – 10 times increase in lean solvent H2S loading. ProTreat simulator modeling immediately following the turnaround gave an H2S lean loading of 0.0074 mol/mol. When the pre-turnaround conditions were substituted in the simulation, the simulated lean loading dropped from 0.0074 to 0.0052 mol/mol. This compared more favourably with the measurements just before the turnaround of 0.003 mol/mol, and is only 0.0014 higher than the post-turnaround value. Both simulations agreed well with other measured performance parameters (e.g. fl ow rates and temperatures). However, the simulated post-turnaround lean loading of 0.0074 is far lower than the presently measured value of 0.012. Thus, simulation was close to both pre- and immediate post-turnaround measured data but far from the present value. Simulation results return to a fairly close alignment with immediate post-turnaround observations, meaning that the increase in lean loading to 0.012 mol/mol is probably not the result of any of the changes made during the turnaround. Something else must have been happening after the turnaround to explain the source of the extra H2S loading.
The root cause analysis (RCA) team investigating this problem inquired about the maintenance history during the turnaround and learned a key piece of information. After unit cleaning and inspection, the turnaround crew had plugged several leaking tubes in almost every heat exchange bundle in the amine circuit. The only explanation left was a lean/rich heat exchanger leak. Subsequent sampling of the lean amine on both sides of the exchanger confi rmed this diagnosis. The plant was fortunate that tie-in valves were already in place to allow a spare lean/rich exchanger bundle to be tied in while the plant continued to operate. New 316 stainless bundles were installed while a temporary spare exchanger was placed into service, and a costly shutdown was avoided.
Summary
Without simulation, a defect can hide and go uncorrected for a long time. What is worse, using a less-than-rigorous simulator with tuning parameters buried within it can lead to some fruitless and costly adjustments to operating conditions, hardware replacements, misdiagnosis of the true problem, or the resigned acceptance of reduced processing rates and lost revenue.
Troubleshooting is not always as straightforward as the examples here, but it can be made a lot easier when a reliable simulator is used to assess the validity of measured data. It is almost always important in assessing lean loadings to account for the HSS levels, simply because HSS levels can account for the lean loading value itself. In sweetening to low residual acid gas levels, solvent lean loading can determine the treat actually achieved. With a reliable simulator, it is almost always possible to pinpoint the cause(s) of poor performance as the simulator will show what the plant, as-specifi ed, should be doing. It is up to the engineer to use the simulator thoughtfully to fi gure out why expectations are not being met.
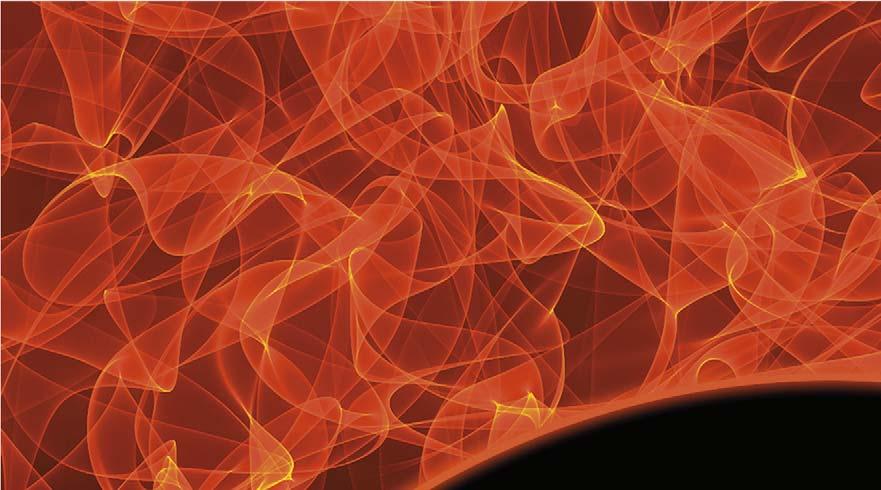
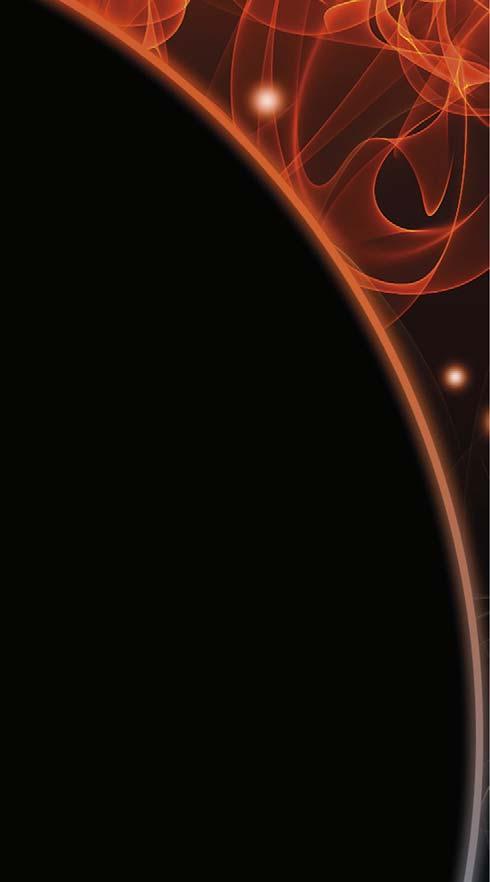
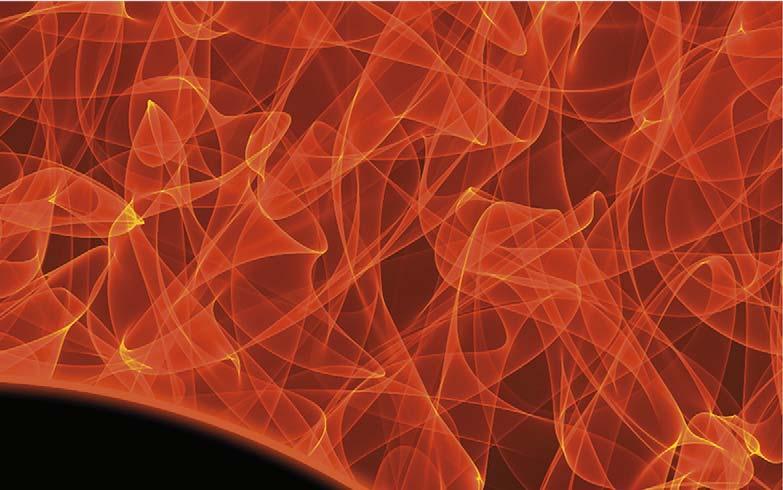
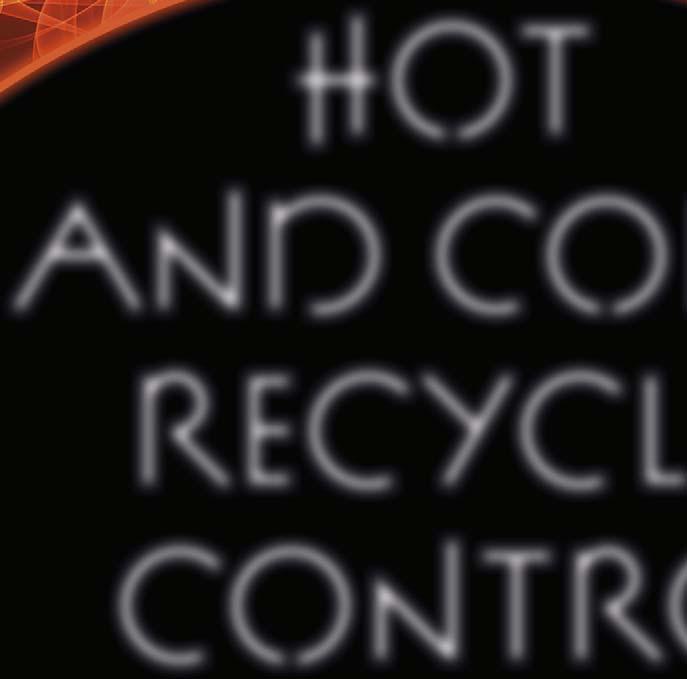
Nabil Abu-Khader, Compressor Controls Corp., UAE, discusses the operation of a two-shaft gas turbine-driven centrifugal compressor with hot and cold recycle lines.
The usual objective of a gas turbine (GT) fuel controller is to vary the fuel fl ow as needed to maintain the desired power turbine speed regardless of load or fuel quality variations. In some applications, that speed set point (SP) is held constant, but it is more commonly varied to achieve a cascade control objective.
Compressor Controls Corp. (CCC) has developed various application software solutions called ‘control applications’ (or just ‘controllers’) to drive, protect, and sequence the entire GT train. This article will demonstrate how a two-shaft GT drives a centrifugal compressor having two recycle lines (hot and cold). It will also show how the train reacts when exceeding design boundaries including centrifugal compressor surge.
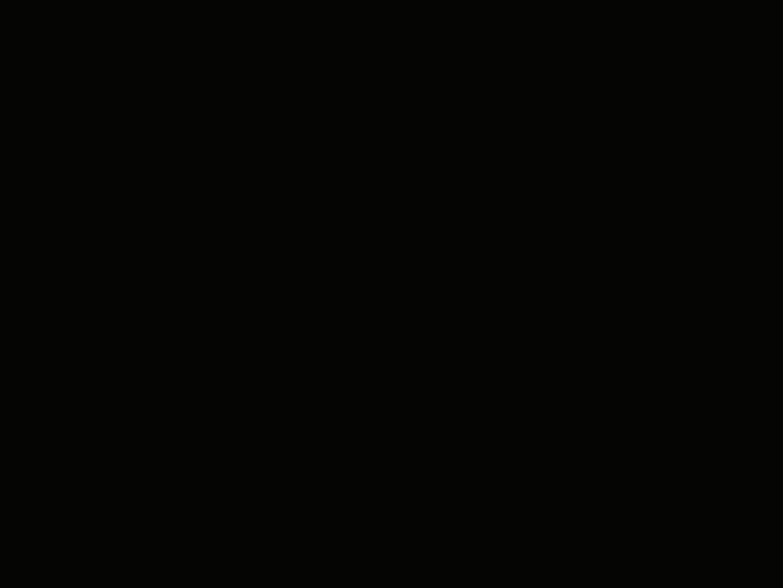
GT integrated control system
For a GT-driven compressor, the control system would combine logic controller (LC), speed indicating controller (here ‘fuel’ or ‘GT controller’ [SIC]), performance indicating controller (PIC/PF), and user-defi ned indicating controller (here ‘antisurge’ [UIC/AS]) control applications. ‘S’ antisurge for cold recycle (SUIC/SAS) control application can also be added for cold recycle requirements. The SP for the GT controller would then be controlled by the
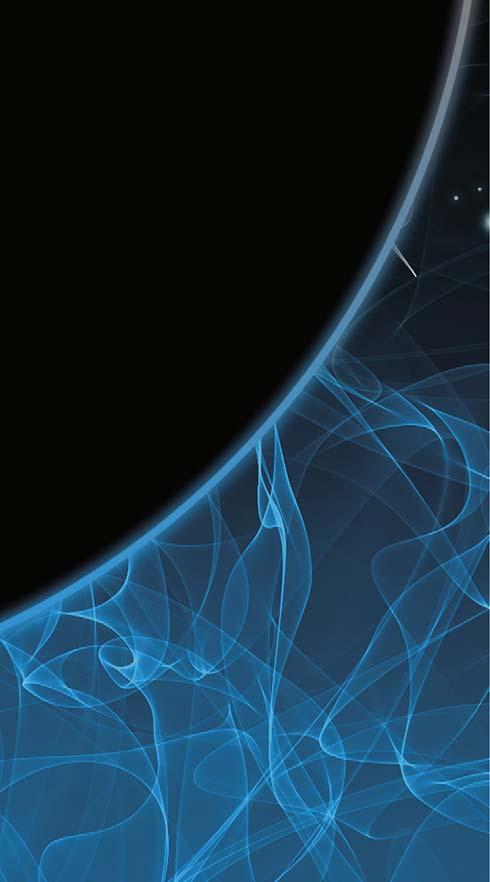
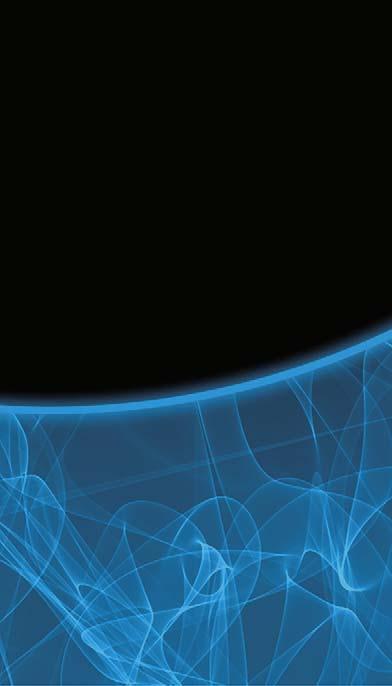
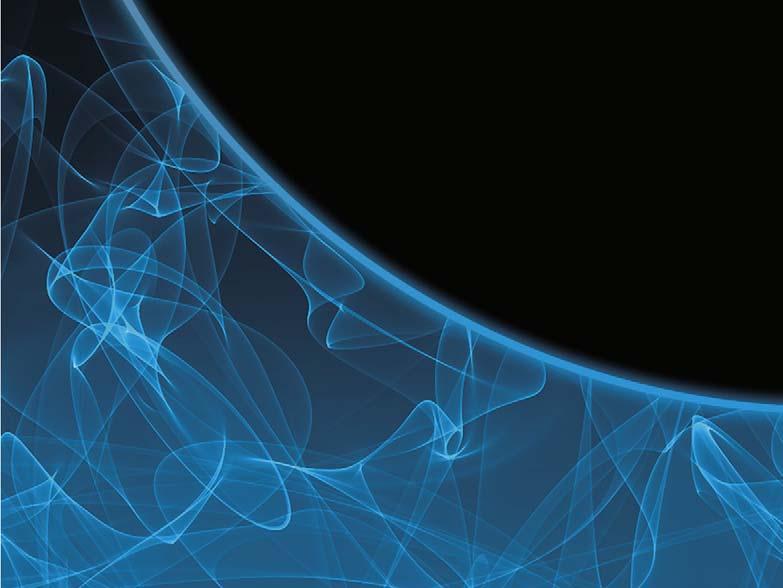