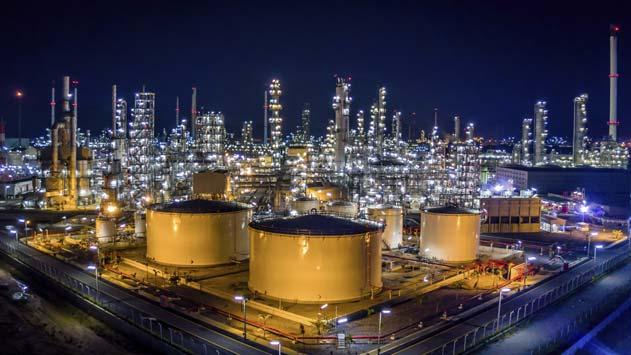
11 minute read
The key to competitiveness
Figure 1. Gas analysis is essential to support operational excellence and competitive performance in many industrial facilities.
Figure 2. A service plan, supported by predictive condition-based monitoring, increases confidence that unplanned downtime can be avoided.
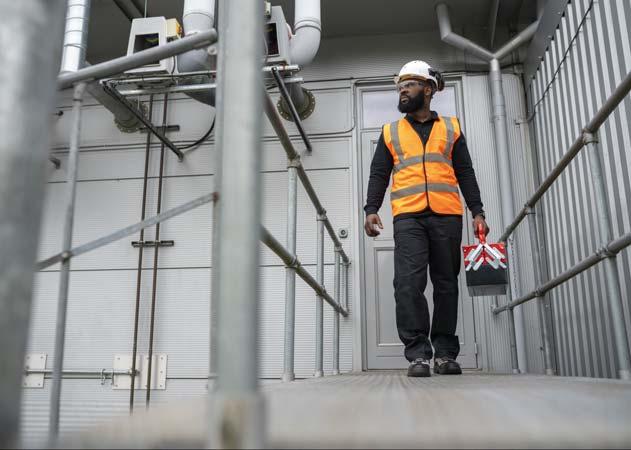
competitiveness, or even survival. These gains in operational excellence often come from incremental, thoughtful and focused digitalisation initiatives; for example, fi nding ways to automate or streamline manual, error-prone or slow activities, and improving situational awareness.
Low-cost sensing, connectivity, data storage and processing can be fully utilised, enabling more informed and responsive operations and maintenance, and creating new levels of optimisation and asset management.
Offline gas analysis and the impact on operational excellence
Gas concentration measurements support the operational excellence objectives of many industrial processes, meaning that if those measurements become unavailable for any reason, operational revenue decreases while operational costs and risks are increased.
An offl ine gas analyser means that the process control system has less information on which to base adjustments, leading to the degradation of control and higher operational costs. A process may be able to continue, thus avoiding a shutdown, but cannot run optimally. The consumption of energy, fuel, and other resources may increase, other assets may be affected, and the operator will incur additional costs to remedy the offl ine analyser.
Take the example of the NOX emission reduction process in combustion power plants (DeNOX), using selective catalytic reduction (SCR). Ammonia (NH3) is injected into the gas fl ow from the combustion process. It reacts with NOX in the fl ue gas, in the presence of a catalyst, to form H2O and N2. Surplus unreacted NH3 (ammonia slip) is wasteful and costly, and often leads to harmful deposits which impact the catalyst and may cause corrosion of air pre-heaters located further downstream.
A gas analyser going offl ine can also impact operational revenue, since the degradation in control capability can take product quality off-spec, reduce product yield or increase product scrappage. Consider semiconductor wafer manufacture, which relies on ultra-pure gases. The smallest impurities can result in major defects, leading to product scrappage.
Operational risks are also increased by an offl ine gas analyser. In the ammonia slip example above, an offl ine analyser means harmful emissions increase, and can affect regulatory compliance.
Accurate gas analysis is essential to maintain safe operation in some processes, such as combustion in control fi red heaters. These are integral to many hydrocarbon processing applications, and depend on the stable, continuous measurement of excess air.
Operating large, fuel-hungry units effi ciently – for example, those on ethylene crackers – requires a delicate balancing act, ensuring effi cient, low-emission operating conditions while remaining on the safe side of a tipping point that leads to potentially explosive low-oxygen, fuel-rich conditions.
Factors that can reduce gas analysis availability
While balancing cost and risk, it is essential to achieve high availability for gas analysis. Nonetheless, there are a number of factors that may lead to reduced availability.
Issues with installation and commissioning can affect tightly planned and coordinated construction, upgrades, and shutdowns, and could delay the startup/restart of production. Delays can cost operators up to hundreds of thousands of dollars each day, with lost revenue and the need to re-schedule dependent works. Late delivery, defective materials, poor installation and limited fi eld access to information are all factors that contribute to such delays.
If an analyser is exposed to unforeseen process and operating conditions, this is often detected by the analyser’s diagnostics, though this is not always the case.
Depending on the conditions encountered, gas measurements may stop while the analyser reports faults or out-of-specifi cation indications to the plant control system – for example, changes to the ambient or sample gas temperature, pressure, or fl ow levels, poor power supply or excessive vibration.
Specifi c gas concentration measurement technologies may also be able to detect additional conditions – for example, tunable diode laser spectroscopy (TDLS) measurements can be compromised by unexpected background gases and high dust or particulate loading in
the process gas stream. Some conditions can damage the gas analysis system and require replacement parts.
Inadequate maintenance is another factor that can lead to performance degradation, and ultimately to an unavailable measurement. Sampling systems and analysers themselves often include fi lters which protect the gas sensors from expected contaminants such as particulates and moisture. These typically need regular cleaning or replacement. Even under standard operating conditions, analyser optics can become obscured over time and will require cleaning.
These maintenance activities – including cleaning or replacing fi lters, cleaning optics or performing periodic validation of measurement accuracy – usually require analysers to be taken offl ine.
Additionally, the incorrect operation of an analyser – accidentally adjusting a critical confi guration, for example – can effectively render the analyser offl ine, or at least make it unreliable. Examples of this include disabling or changing the temperature or pressure compensation confi guration, modifying assigned behaviour of outputs, or even modifying essential measurement details, such as optical path length of an in-situ installation.
The fi nal factor is unexpected component failure, which typically leads to diagnostics identifying the faulty part. The nature of the faulty part dictates the impact this has on the gas measurement and its availability to the control system.
Dealing with unavailability events using current methods
Many of the current methods utilised to deal with unreliability events are manual, ineffi cient, error-prone and not always suffi ciently data-driven. They may involve taking notes and photographs, or capturing limited digital logs on-site, then travelling to an offi ce in order to consult the necessary documents – such as orders, delivery notes, contracts, manuals, drawings, and technical bulletins – then returning to the site or contacting the distributor/supplier for support.
While emails and phone calls can reduce travel time, they are a limited and imprecise way to convey all the necessary information about an issue. It may take a number of communications, supported by site visits, to accumulate the information needed for remote support workers to offer their insight. All the while, the offl ine duration increases.
Even when the problem is identified, expert service team visits do not happen instantly, potentially extending the impact on revenue, while travel and subsistence add costs and introduce new workers onto the site, increasing risk. Additionally, one visit may not be enough – was a diagnosis based on notes, photos and limited data logs enough to ensure the right tools and parts were brought along to provide a fast and accurate first response?
Gas analysers have been intelligent devices for many years and are integrated into control systems. They have, however, been more focused on providing the gas measurement and health indications necessary to provide situational awareness to process control systems and operators.
This means that they have not continuously recorded or exposed all events and data streams to allow a retrospective and contextualised analysis of analyser and process behaviour, as there has not been suffi cient processing and storage capacity or connectivity bandwidth.
By not recording all events and data streams, maintenance activities remain scheduled events, regardless of system conditions, contributing to waste and unnecessary risk.
Experience, or the process of elimination, may also resolve some issues. While inbuilt diagnostics may not clearly identify the problem, experts may infer that a condition exists using other data – for example, excess vibration, poor power supply and some spectral quality issues.
Improving work processes through digital transformation
Digital transformation provides a major opportunity to improve these work processes, but it depends on the combination of increased amounts of real-time and static digital data, along with increased access to it.
If future products and services enable timely access to the right data, for the right people, in the right place, then availability issues and activities could look very different.
Transparency and communication of supply issues could be improved by increasing data collection and tracking from order to delivery, throughout internal processes. The goal is to eliminate supply issues, but if problems arise, early awareness enables sites to take early action to minimise disruption.
Asset management systems are used increasingly by industrial facilities to create digital twins of their facilities and assets, enabling connected workers – carrying out installation, commissioning or maintenance work – to access 2D drawings, 3D models, manuals, technical bulletins and other information at the site via appropriate mobile or wearable devices. Annotated augmented reality capability, enhancing the worker’s view with a digital overlay, can provide visual guidance for the task.
Many of the delays in resolving issues are removed by access to data on this ‘right time, right place’ basis. Equipment suppliers such as Servomex will need to provide product data in appropriate ways to extend these services to gas analysis systems.
While not every facility has advanced asset management or site-wide wi-fi in place, both are increasingly available and are enablers for transforming practices. Gas analysis systems can build upon those services by including a dynamic E-Ink based QR code on every gas analysis system that encode the system’s unique identity, current physical build, fi rmware details and other essential data.
When scanned by a smartphone or tablet app, the QR code enables immediate retrieval of accurate version/built specifi c information from either the advanced asset management system or Servomex systems, to support fast local resolution. For example, available information could
include 2D and 3D drawings, user, service and safety manuals, and technical bulletins.
The app could also offer direct access to technical or application support, providing maximum context to the support operative, minimising the requirement to collect more information.
There is also a further possible application for annotated augmented reality technology, with experts providing visual guidance and over-the-shoulder support to the workforce.
Additional security controls, including well-established methods such as two-factor authentication, can help prevent mis-operation of the analyser, protecting it against ill-considered or unintended changes to critical confi guration.
A service plan increases confi dence that unplanned downtime can be avoided. However, while preventative maintenance is nowhere near as costly as reactive maintenance, it is still not optimal.
If maintenance is carried out only when conditions require it, operational costs can be reduced, revenue less affected and risks lowered. This can be accomplished through predictive condition-based monitoring, which requires signifi cantly more data than process control.
Rather than use the NAMUR NE 107 type diagnostic health indicators currently provided by gas analysers for process control, the data behind those indicators is exposed. Analysis of patterns, trends and correlations can then deliver greater insight into changes over time, and at what moment those changes may impair performance.
Plant operational intelligence systems are becoming increasingly capable of ingesting and cleansing this type of data, then contextualising and analysing it to provide dashboards or notifi cations of critical events to the workforce.
TraditionalFieldbus protocols – such as Modbus – can be used to integrate equipment into these systems; however, since Modbus maps for all types of device are unique and do not conform to a standard profi le, ingestion would need to be confi gured, introducing another cost and productivity overhead. A more plug-and-play approach would be enabled by gas analysers supporting newer connectivity methods, such as Wireless HART or OPC-UA.
With the appropriate device, system and service level security provision, suppliers such as Servomex can leverage additional operational intelligence services to monitor gas analyser assets on the plant operator’s behalf under service level agreements, providing enhanced levels of optimised service response.
Conclusion
The key to the competitiveness – and in some cases survival – of many industrial operations is operational excellence, which can deliver huge benefi ts for safety, reliability, effi ciency, and fi nancial performance.
The expert application of digitally transformed capabilities may enhance these objectives and allow innovative gas analysis suppliers to take advantage of developing technologies that ensure maximum availability of their equipment.


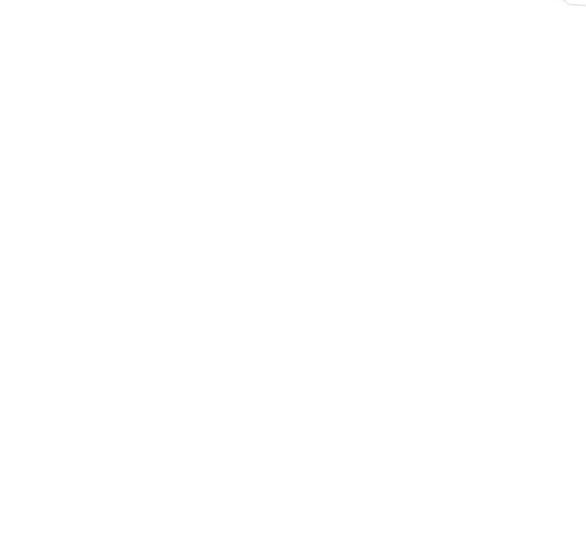
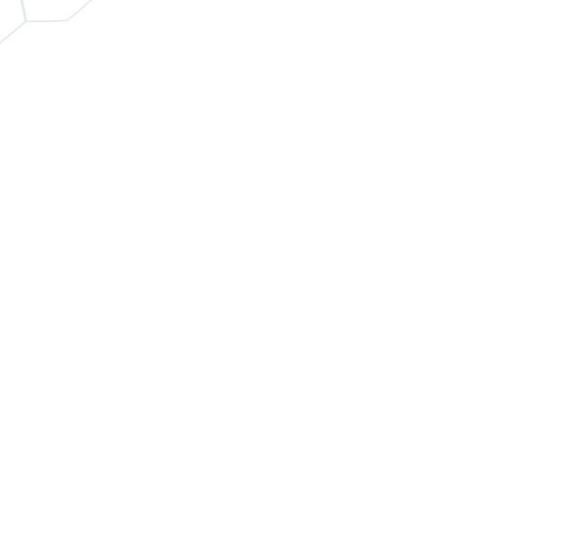

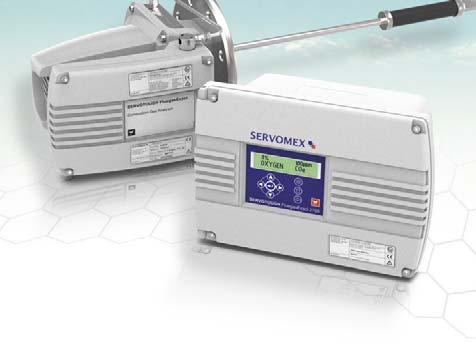
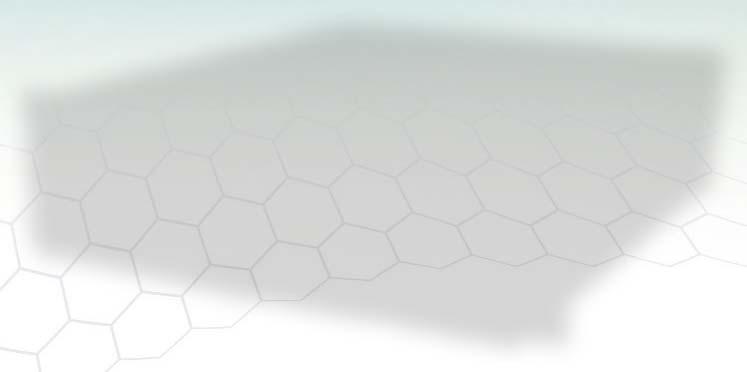


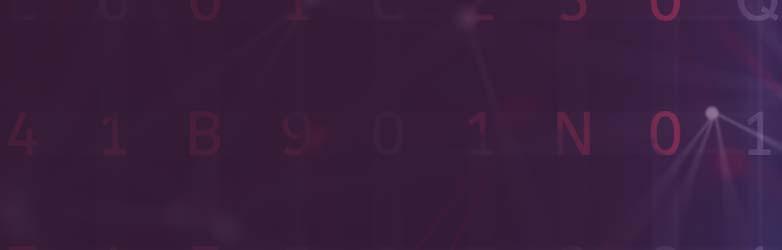
In the first of two parts, Ralph H. Weiland and Nathan A. Hatcher, Optimized Gas Treating Inc., USA, examine two case studies showing disparities between simulation and plant data caused by defective equipment and contaminated solvents.
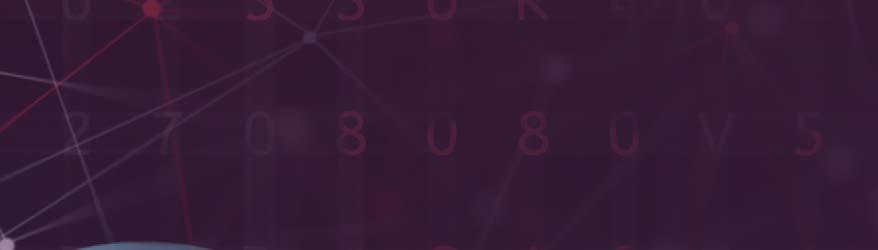

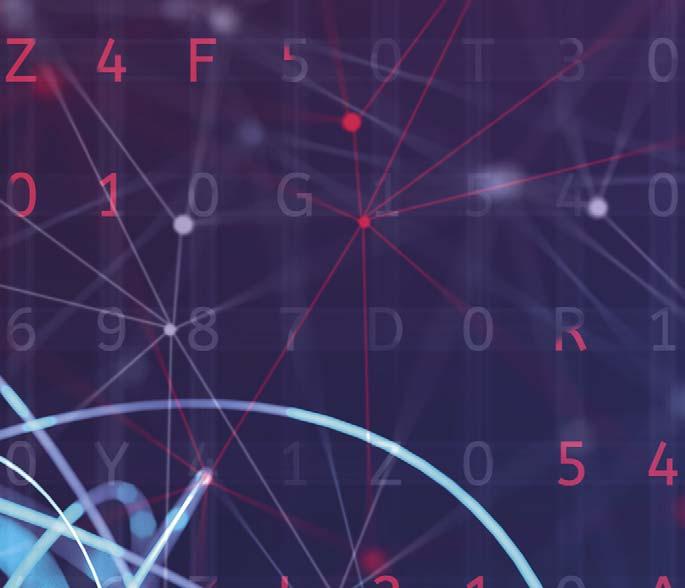
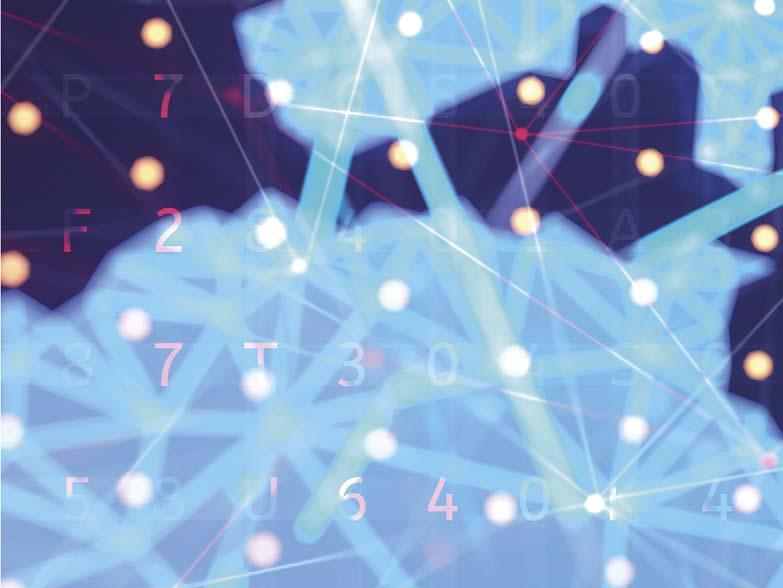
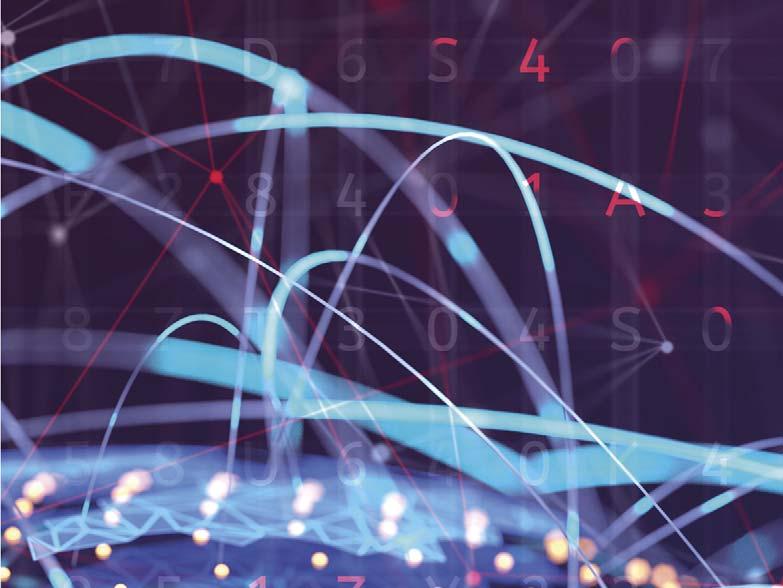
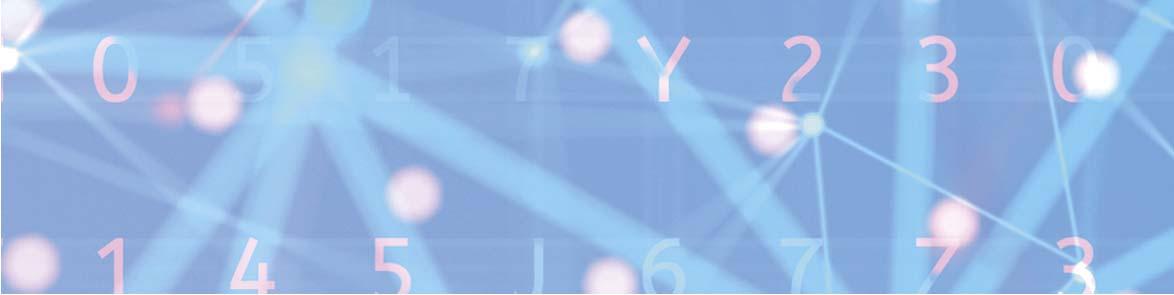
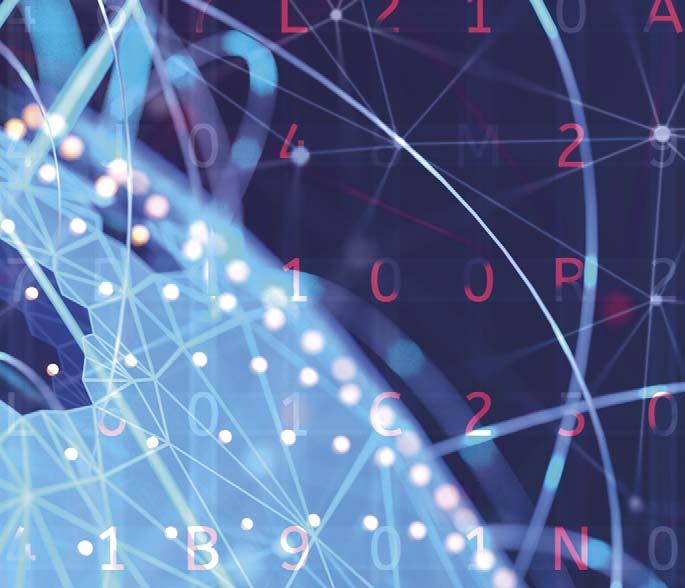
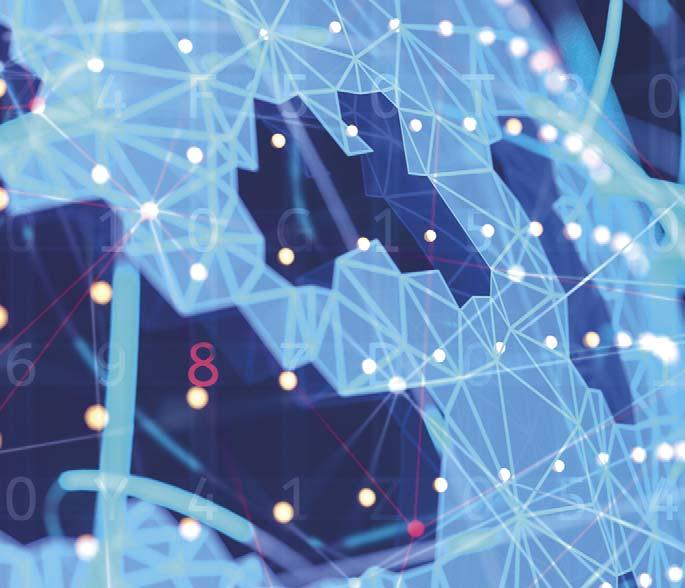
