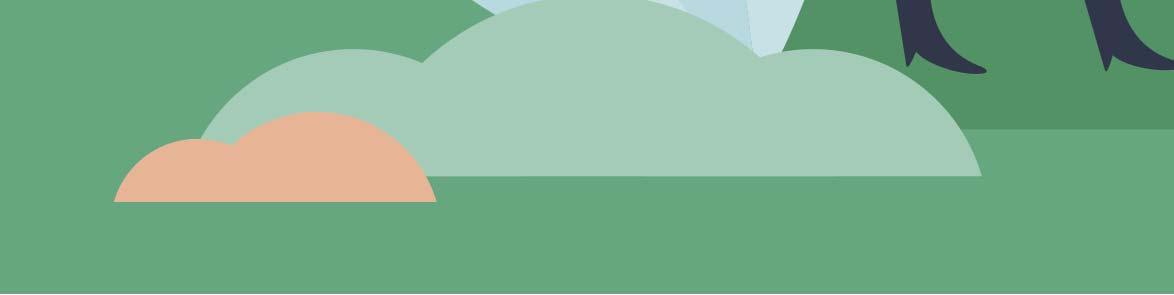
9 minute read
Integrated Systems: The Next Step To Zero Emissions Mining Solutions
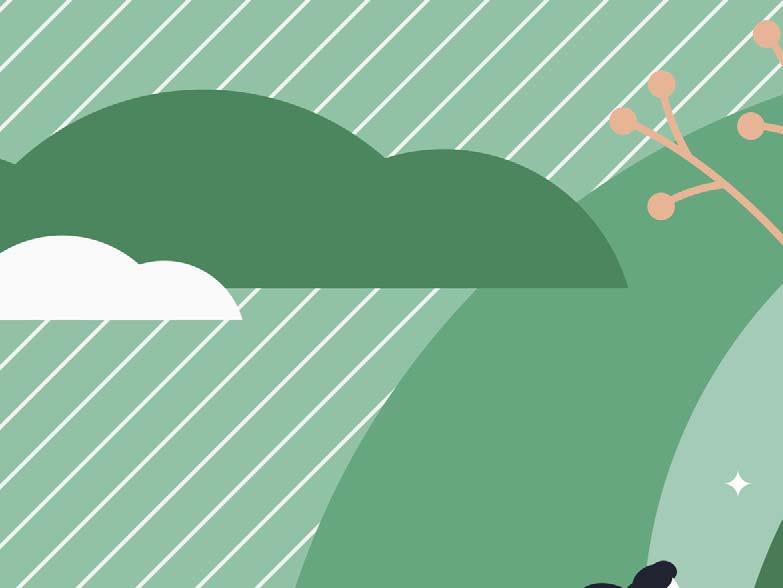
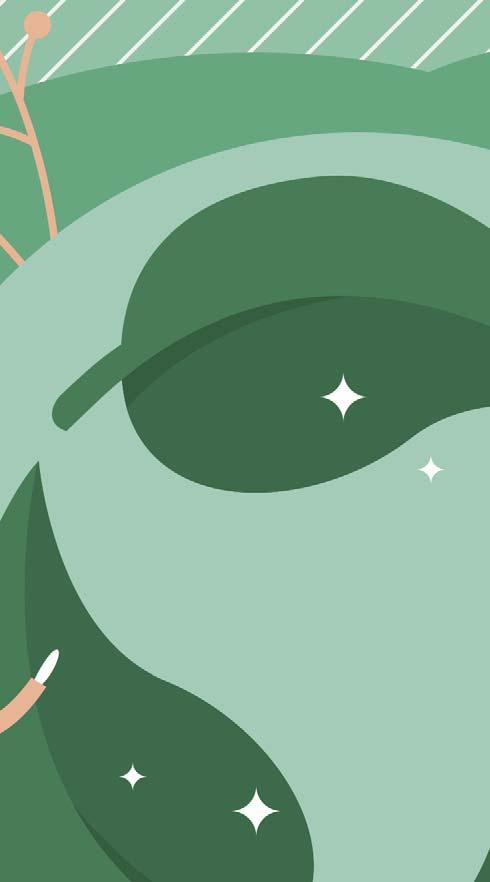
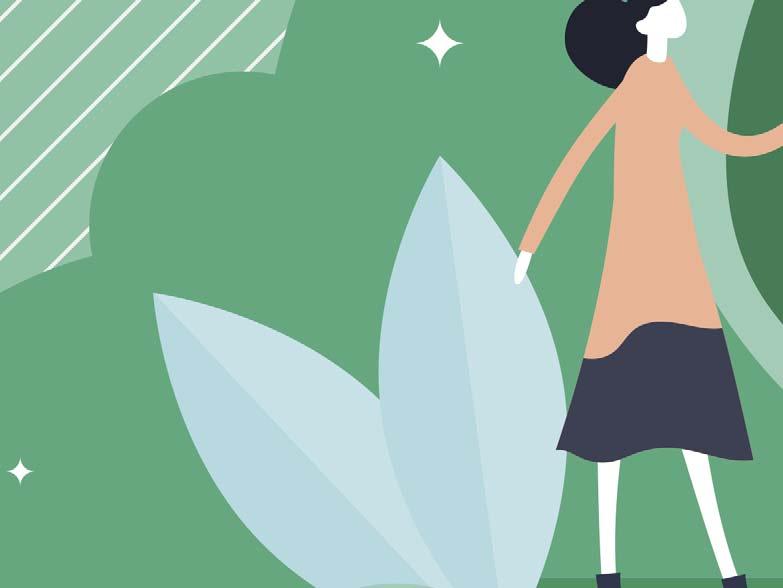
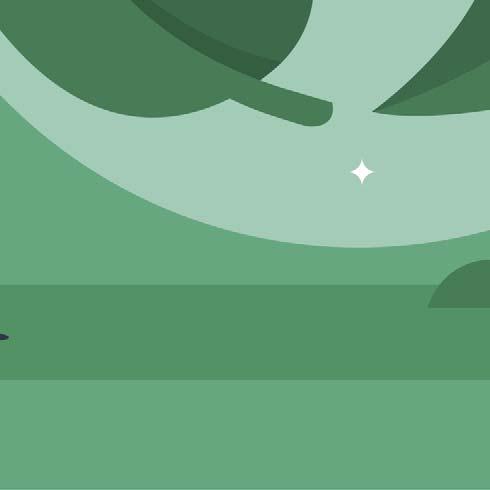
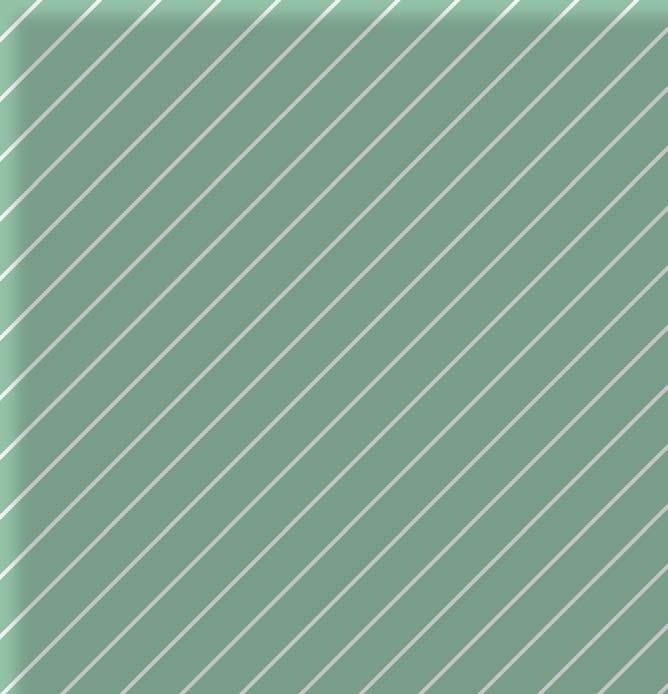
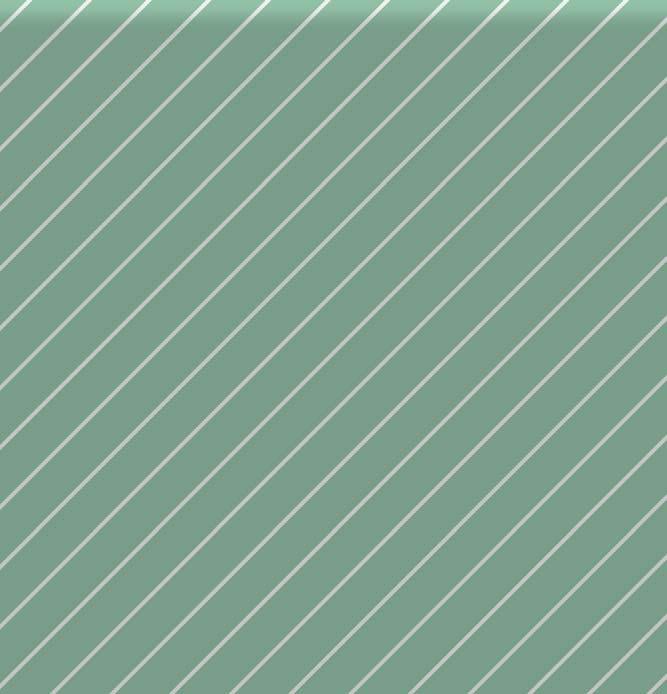


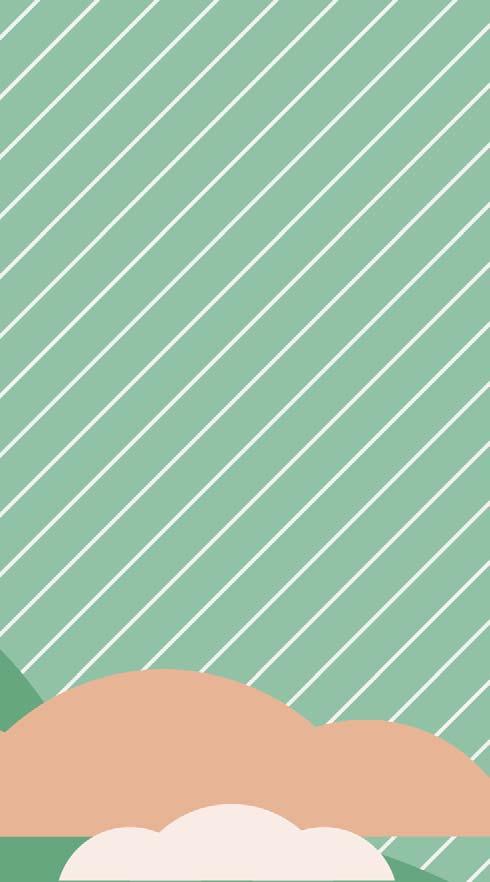
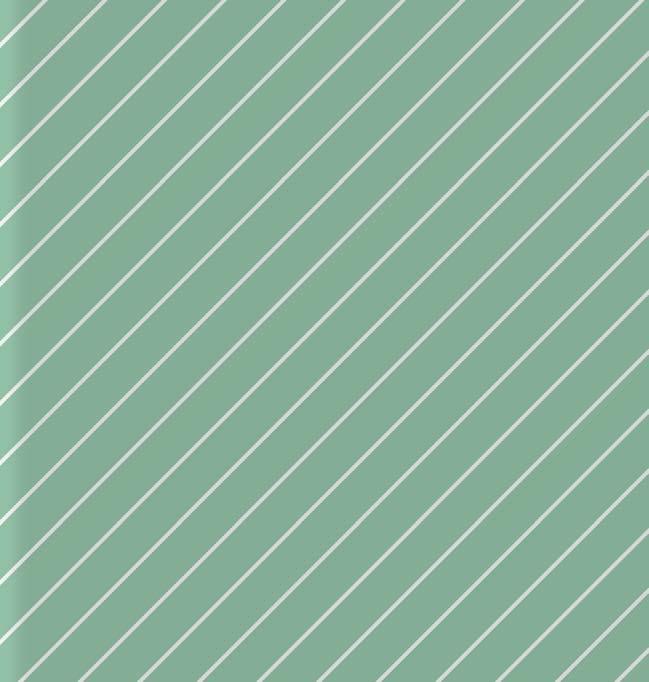

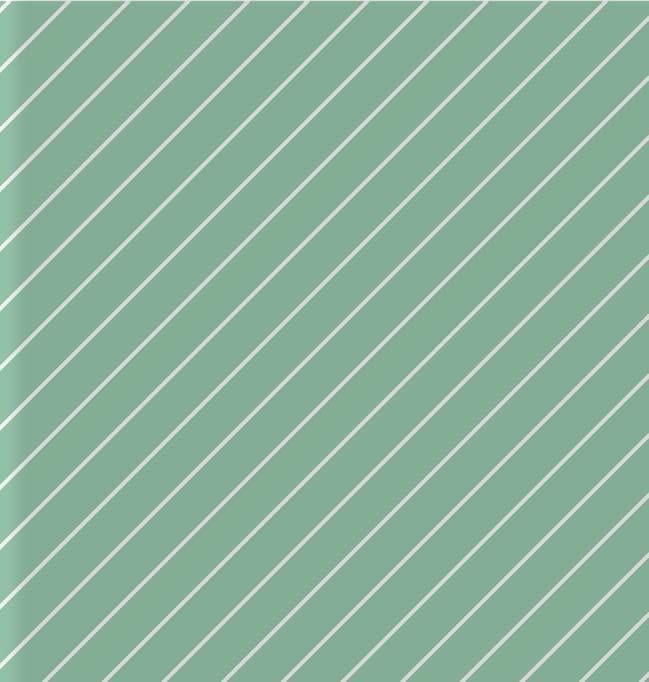
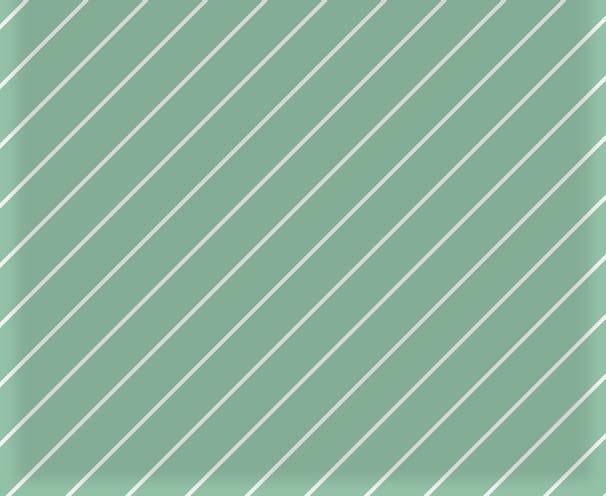
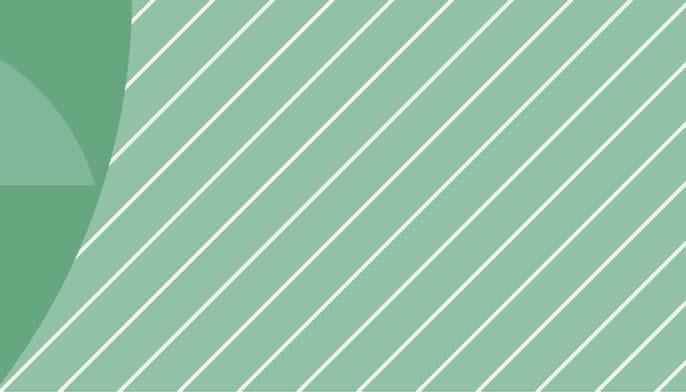

As determination towards green initiatives grows within the mining industry, Elliott Duck, Mincon Inc., USA, outlines how companies can change the way manufacturers and mines think about operating effi ciencies and equipment solutions.
Net-zero emission initiatives, lower carbon footprint action plans, and a push toward sustainability have become a necessity with regards to the future growth of the global mining industry. A strong focus on actioning these initiatives will be a key determining factor for the new competitive leaders of the industry, and the success of reaching its emissions goals.
In the July/August issue of Global Mining Review, Philippe Baudry of RPMGlobal, said that sustainability for mines is now viewed as “an ethical norm and an important part of the businesses’ social license to operate, the challenge for the mining industry to move to a greener future is an opportunity to reset the industry’s reputation within the broader public.” This could also be extended to manufacturers and equipment suppliers, as they will ultimately determine the progress of these initiatives by developing eff icient and sustainable technologies and tools to accomplish the work. This is an opportunity for manufacturers to step up their focus on eff icient and green technologies, and, ultimately, solutions. Mincon is helping change the way manufacturers and mines think about these solutions through ‘integrated systems’.
What is an integrated system?
The term developed from a reference to Mincon’s Drill Mast Attachments – drilling systems that integrate with a customer’s existing fleet of carrier machines, typically skid steers or excavators. It has since become a far more meaningful term for Mincon, as it has focused on developing new methods and processes within its own organisation, steering itself towards eff iciency and sustainability. These methods and internal processes have become ‘integrated systems’ in terms of how they think and how they drive the development of their products. As this grew, Mincon found that its customers also saw value in their focus on eff iciency and sustainability, and began to adopt its ‘integrated systems’ thinking into how they made decisions on equipment solutions and service support contracts, recognising the importance of integrating the systems and processes that drive eff iciency within their companies. The adoption of such thinking by mine operations and purchasing managers, as well as manufacturers within the mining industry, may well determine the speed at which sustainability goals are reached, and help to drive the development of new technologies sooner.
This is where the loop is closed. Mines have the power to bring about this thinking within manufacturers.
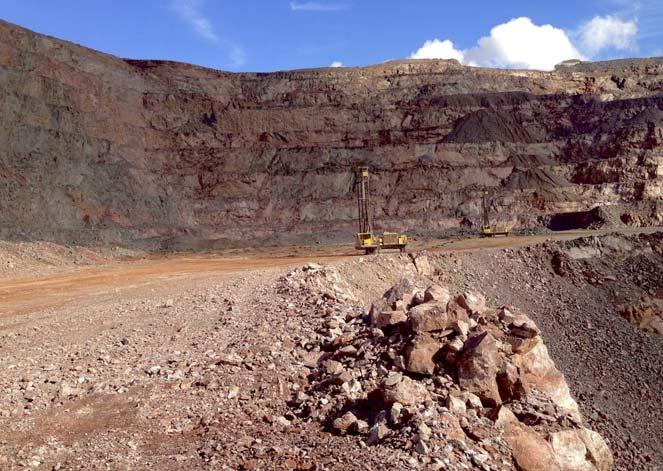
Figure 1. Mining through hard rock requires power; eff iciency is key to lowering emissions.
Integrating effi ciency into solutions
Mincon Group plc’s pursuit for more eff icient drilling solutions is one of the key advantages for TDC-based supply and service contracts, where it continuously refines designs for its rigs, drill masts, down-the-hole (DTH), reverse circulation, and rotary drilling tools. Its determination for eff iciency also extends to its customers as the company looks to build partnerships where it works closely to help the customers businesses grow and develop into eff ective and eff icient challengers in their respective markets.
It is a substantial undertaking and the company’s Technology Steering Group is continually working toward a stronger, greener future for the industry. The group comprises its most experienced and dedicated people across a variety of disciplines, from metallurgy and technical analysis, to product design and manufacturing. Mincon says this internal working group evaluates the latest materials technologies, drilling percussion concepts and manufacturing methods, in order to further develop both new and existing products.
The company has also invested heavily in a dedicated research and development (R&D) facility. This introduces eff iciency into its production, as the R&D facility can accommodate production of special parts for new products – reducing disruptions in the commercial production line. Mincon's R&D facility is the birthplace of a number of new technologies, including its hydraulic DTH system that is being commercialised in 2021.
Where it starts
If mine operations make it a goal to support the growing and emerging manufacturers that focus heavily on eff iciency and developing solutions for green initiatives, this could have a dramatic eff ect on the success of the industry’s goals for net-zero emissions by 2050, or even sooner.
This eff ect has been clearly seen in the coff ee industry, as consumers’ strong support of sustainable and ethically sourced coff ee transformed supply chains and participation from growers. As consumers, mine operators and purchasing managers have the ability to drive change by supporting the manufacturers and suppliers that will help them develop sustainable and green eff iciencies into their operations and equipment solutions now, and in years to come. Green-goal or eff iciency focused partnerships are based on a united eff ort to gain feedback from every aspect of a mine’s operations, in order to build processes and solutions that contribute to the development of eff icient and sustainable (economically viable/cost eff ective) solutions. This goes beyond the typical sale of a piece of equipment, and gets manufacturers more involved with the growth and development of innovative solutions (i.e. equipment, methods, and processes), in partnership with mines directly.
The total-drilling-cost model
To increase overall project eff iciency, many mines have actively pursued a new operating model where the equipment/service provider is bound by a service-level agreement to not only supply the equipment solutions, but also develop a continuous improvement plan to guarantee a specified level of productivity or face penalties. This total-drilling-cost (TDC) model, as an example, focuses on overall production rates and not just cost-per-metre drilled, which could remain the same for 50, 10 m-deep bores regardless of whether it takes one shift (or three) to complete them. Service providers entering into these TDC-based contracts are now evaluated on product life in addition to productivity over time – a more stringent performance requirement over cost-per-metre alone.
An eff iciency-based approach ultimately makes mines more successful in their operations and involves service providers and manufacturers more directly in their success, driving the development of new eff iciencies. This is another proof-of-concept that shows the success of a mine’s operations requiring more than just equipment from a supplier. The TDC model has become an integrated system of eff iciency for many mines.
Building today’s solutions for the future
Mincon Group plc’s pursuit of eff iciency has now been embodied in its new Rock Drill range of products, which off er the drilling and mining industry a next step toward sustainable operations, by helping mines build eff icient equipment solutions into their green-action-plans. This is accomplished in several ways with the range of products, from the drill solutions options themselves down to the engineering and design methodologies used to develop them. The company’s unique approach could change the way manufacturers build equipment in the future.
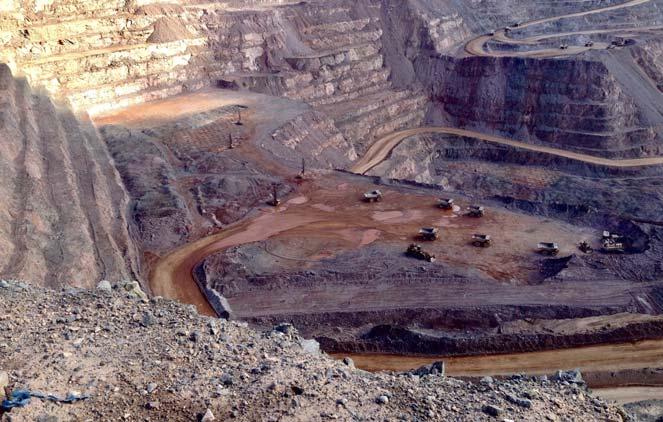
Figure 2. Mining operations are expansive, integrated systems can significant reduce costs.
Figure 3. Eff icient power can reduce drill size, cost, and lower maintenance requirements.
Figure 4. Innovations in technology drive drilling eff iciencies, the SpiralFlush casing advancing system is a prime example of this.
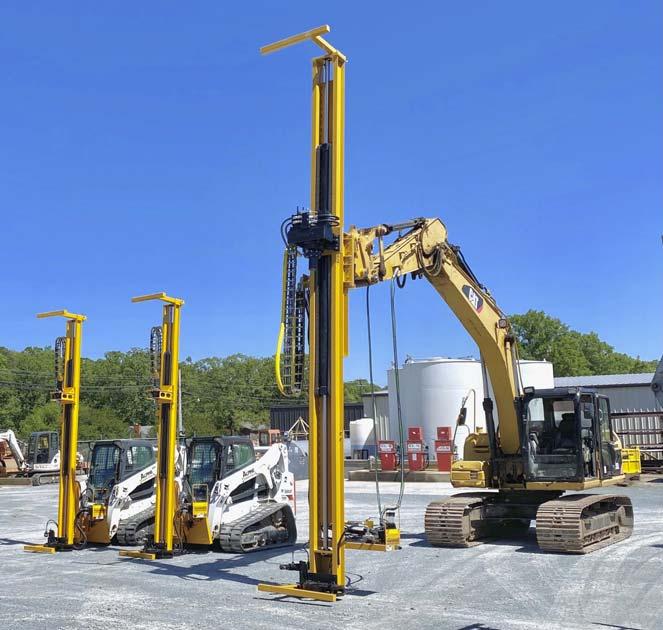
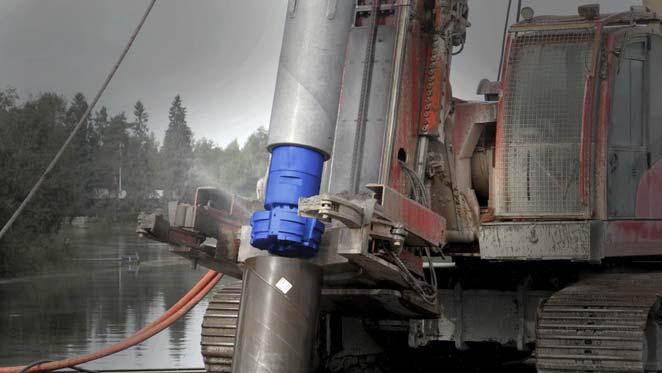
The business-end of effi ciency
Drill Mast Attachments off er the business-end of the drilling rig without adding an additional diesel engine to the end user’s carbon footprint. These drilling solutions can be deployed quickly with lower manufacturing time, lower steel requirements, lower cost to the end user, and are easily integrated with existing or rented carrier machines, such as skid steers or excavators.
Effi cient methodologies
The engineering team that developed the Rock Drill range of products started out as drillers, and through this experience they developed a strong aversion to downtime from waiting for propriety parts or overly technical service requirements. This is where their unique approach has made a diff erence.
The design methodology was to innovate simplicity into the product line. Simplicity meant that the drill rigs and drill mast attachments had to be built stronger for a longer service life. It also resulted in intuitive, easy-to-operate controls and minimal maintenance requirements from fewer wearing parts and less downtime. Instead of proprietary spare parts, reliable off -the-shelf components were used to reduce service downtime and lower maintenance costs and diff iculty for end users. The results are drill solutions that last in operation well beyond standard industry service life, and that can be maintained cost eff ectively by the end user without having to depend on the manufacturer for service or support.
Developing future solutions
By extending the focus of their business into drilling rigs and mast attachment systems, Mincon has gained flexibility in their engineering and development processes. The company can now develop more eff icient solutions across their product lines. Complete drilling systems that work cohesively as a single unit to off er more metres drilled per-litre of fuel, optimising drill unit functions for tooling technology eff iciency.
Conclusion
Mining has the foundation to build on, with examples of integrated systems working in the industry and others. The challenge for the mining industry to move to a green future is an opportunity for manufacturers, service suppliers, and mining operations to work together to push the boundaries of change and development as a team. When mining operations insist on this, it will drive manufacturers to develop the new methods, processes, and equipment solutions the industry needs to reach its sustainability goals.
So what opportunities are there? Be the one who drives eff iciency and the development of integrating more eff icient systems. Start the conversation with manufacturers and service provides to see how they can help action new eff iciencies. It is going to be the future of the mining industry. The leaders of that future will be those who start today.