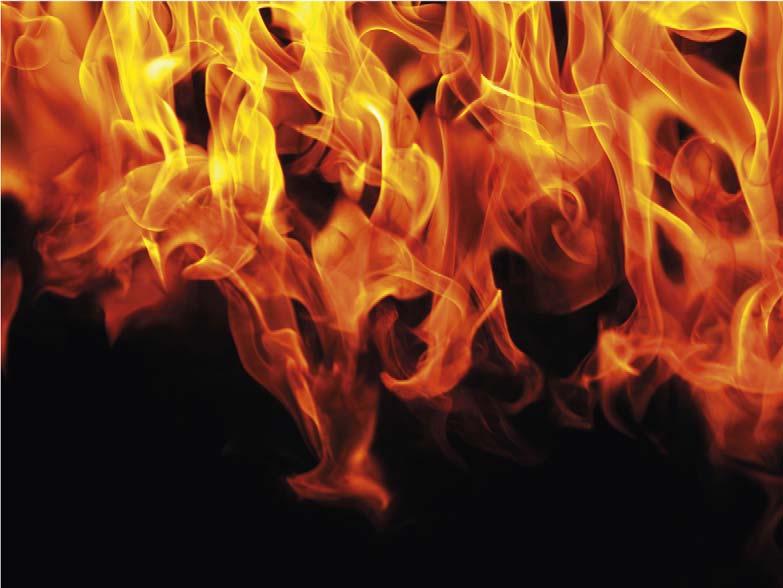
8 minute read
Fighting Mine Fires
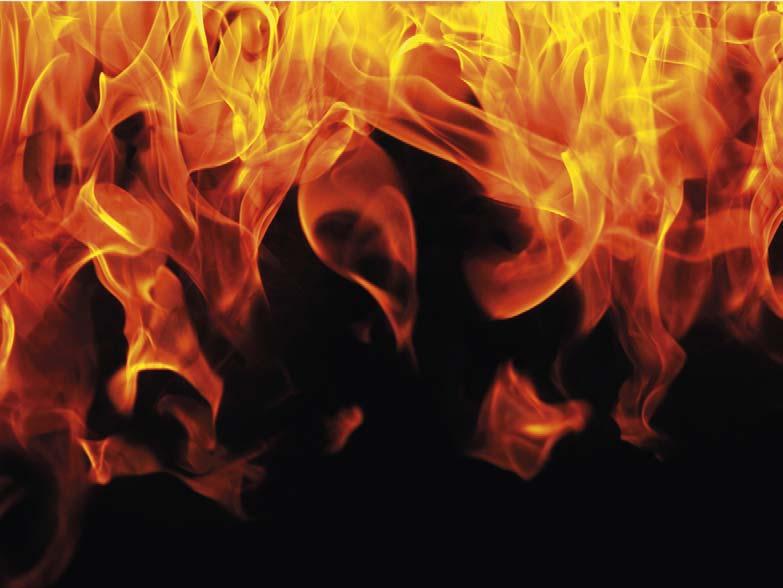

Alan Bailes, Weber Mining & Tunnelling S.A.S, Australia, discusses recent advances in safety, using remote seals for the confi nement of cavities in an Australian coal mine as an example.
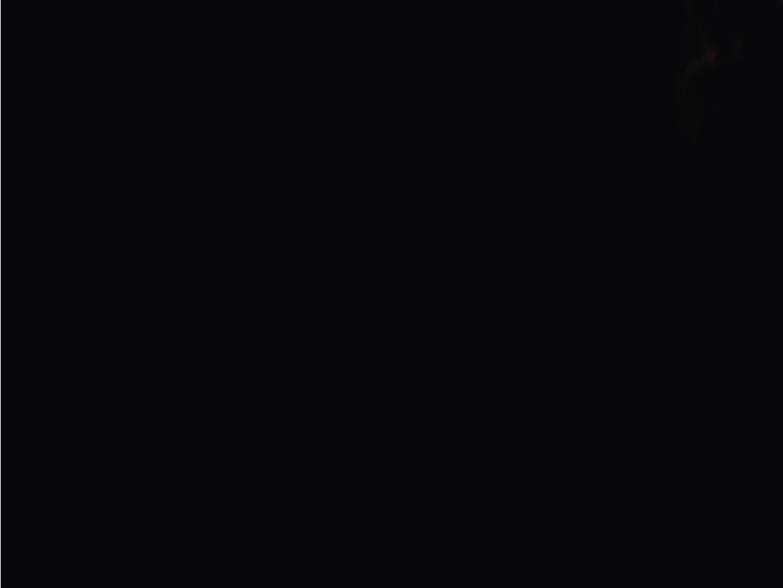
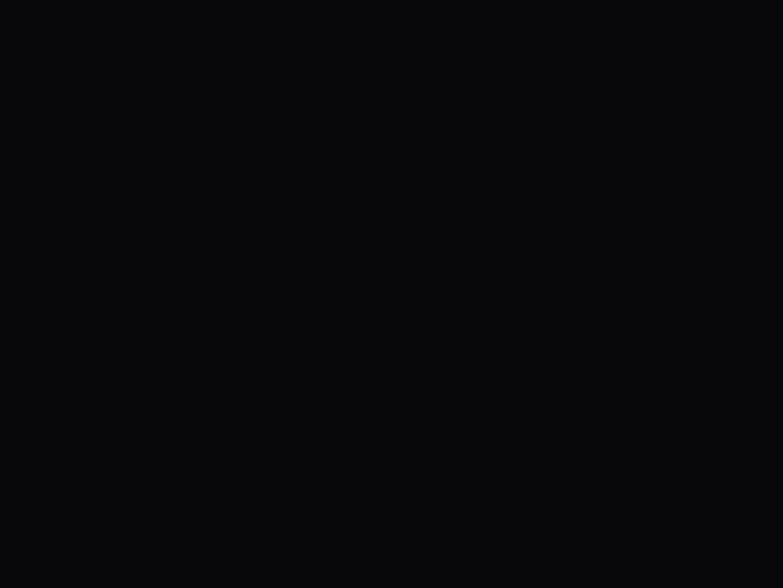
Mine fires are fought indirectly when access to the fire zone is impossible, as a result of: safety restrictions, blocked underground access, a limited supply of available firefighting materials, or a fire zone that is too large for available underground personnel. This approach involves sealing the mine or construction area off , using in-mine temporary seals as ventilation-control structures to isolate the fire area. These in-mine seals can be constructed from within the mine, or remotely through boreholes. Sealing the mine or isolating the fire or heating event area is designed to control or extinguish the fire by reducing the oxygen concentration in the mine atmosphere to a level that will not support combustion.
Rocsil® LS1 foam has a history of being used in underground coal mines around the world. The product is commonly used to provide confinement in open void areas (cavities) above longwall shields and roadways, improving safety for coal mine workers. The foam is an eff ective solution in recovering collapsed roadways and enabling longwalls to retreat more eff iciently when experiencing poor mining conditions.
For remote sealing, specially designed equipment eff ectively delivers the foam product into mine roadways or shaft s without the need for labour to be deployed underground, or when exclusion zones are in place on the surface. Once the critical mine event is under control,
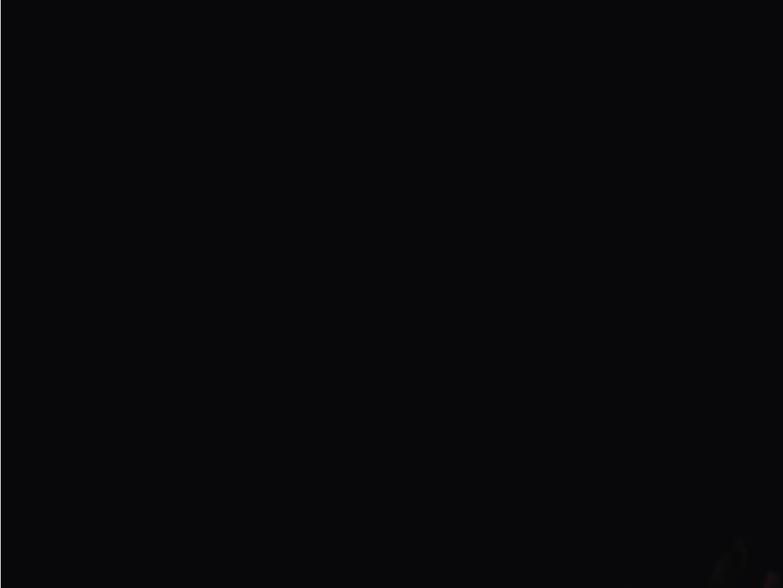
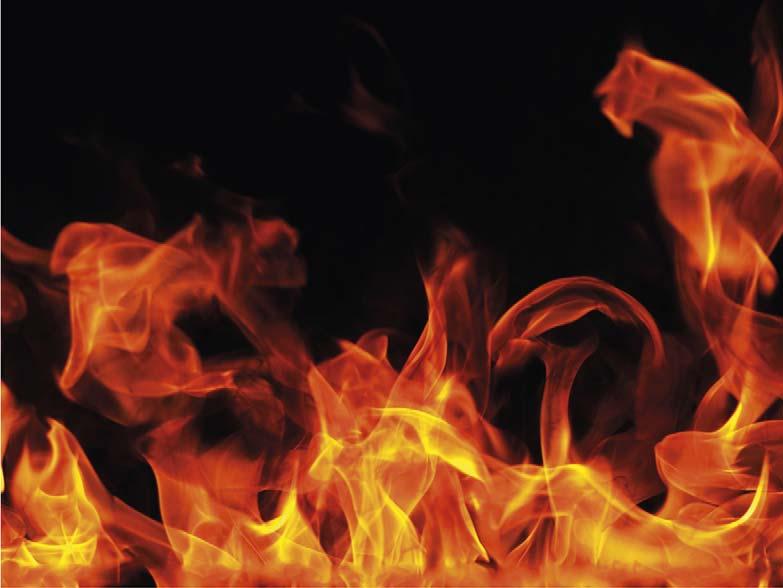
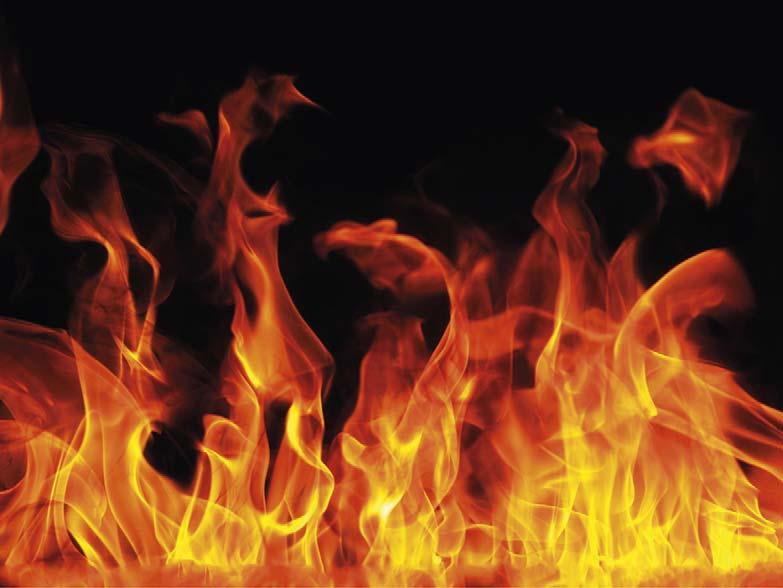
the plug can be easily removed to facilitate safe re-entry into the mine. The remote Rocsil LS1 foam plug seal system is a current industry benchmark available to deal with underground explosions, heating, or fire events in a safe, cost-eff ective, and rapid way.
Rocsil is pumped from the surface until it expands to the roof and ribs forming an airtight barrier (Figure 1).
This article reviews the use of remote seals to control fires and heating events as current best practice in Australian coal mining, describing the current industry benchmark of foam seals. Rocsil HD20, a recent innovation delivering overpressure blast remote seals, is discussed, with case studies provided.
The benefi ts of remote seals
The remote seals system provides a major advantage in removing mine workers from exposure to a high-risk situation. The remote sealing system allows for a Rocsil foam plug to be pumped from a place of safety, sealing the mine entry or roadway in the event of an emergency. These foam plugs can be installed to the specification required by the mine, now rated up to 50 psi.
In the Australian coal mining industry, Weber Mining works with its selected applicator; Wilson Mining Services. Wilson specialises in engineering the delivery of resin injection systems and has a wealth of experience in using Rocsil to create remote seals.
The companies also work together to ensure stringent quality controls ensure the foam conforms with Weber specifications. Ratio and density are maintained by advanced ratio/flow monitors and Wilson Mining’s team of chemical applicators. QC testing reports of the sampled product are then verified by the engineer, along with the camera footage, to analyse and provide an ‘as built’ certificate for the rated seals.
A Rocsil Foam Maxi standard pump with bulk IBC product packaging is used. This system improves pumping rates, reduces manual handling and has the added benefit of being a closed-circuit system, which reduces the likelihood of mine workers being exposed to chemicals. Using this system, product, equipment, and crews can quickly be mobilised to site.
Preventative applications provide the most favourable option for clients with current Australian mining regulations requiring in-situ provision of remote sealing of mine operations. Using the Wilson system, this can be achieved by placing a mixing gun and two flexible hoses at an accessible point in the roof of selected roadways. The product can be applied from surface to seam using a high-volume delivery pump attached to the pre-installed hoses. The Rocsil product pods are connected in the event of a potential incident from a safe location.
The Wilson Mining pre-installed remote emergency sealing system provides a significant time reduction in the event of a mine fire or explosion, allowing remote Rocsil Foam plug seals to be installed in pre-determined best suited locations, along with gas monitoring systems in fixed positions.
The system is designed to mine site requirements and has been installed in many Australian coal mines as part of their emergency sealing plans.
Advantages of the pre-installed remote Rocsil seal system include: Mine sealing plan designed and engineered for optimal outcome. Pre-determined safe installation locations. 70% faster installation than reactive drill and remote sealing methods. Pre-installed gas monitoring on inbye side of plug location. Hosing and remote heads pre-run and fixed in-situ. Rocsil quantities known and understood. Suitable for highwall portals entry, conveyor drifts, materials drifts, and shafts. Low cost solution for guaranteed sealing.
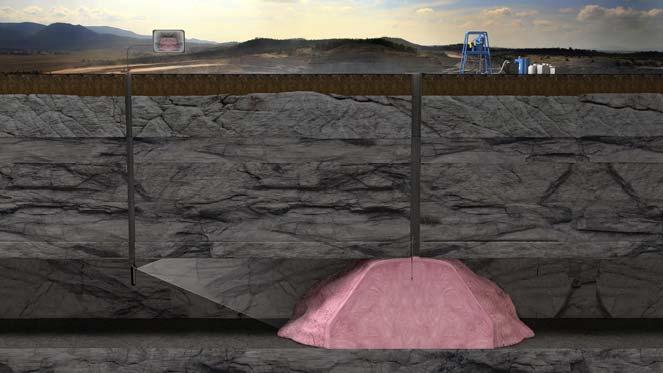
Figure 1. Diagram of a typical Rocsil surface to seam remote seal.
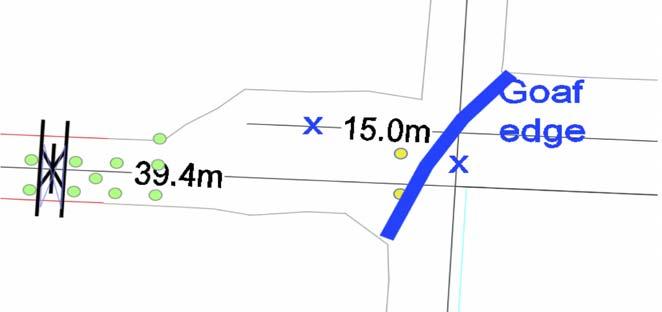
Figure 2. New South Wales case study application diagram.
Rated surface to seam vent plugs
Rocsil LS1 is a proven solution to create ventilation plugs of various sizes in underground coal mines – preventing oxygen ingress into the goaf areas of a longwall, gases being released from the goaf, or installation of plug seals in roadways to prevent injury or damage from an overpressure event.
It is an eff icient product capable of expansion rates up to 35 times its original volume. Rocsil Foam LS1 has a fast reaction and curing time (1 – 1.5 minutes) and obtains an average density of 45 kg/m3. Engineering test work was performed on Rocsil Foam LS1 to design a mine rated plug seal which could be installed via the surface to seam (S2S) method. A maximum of a 30 psi rated plug seal was achieved.
Demand for a higher strength plug seal
The Rocsil HD20 product was developed by Weber Mining in conjunction with Wilson Mining as a response to demand for
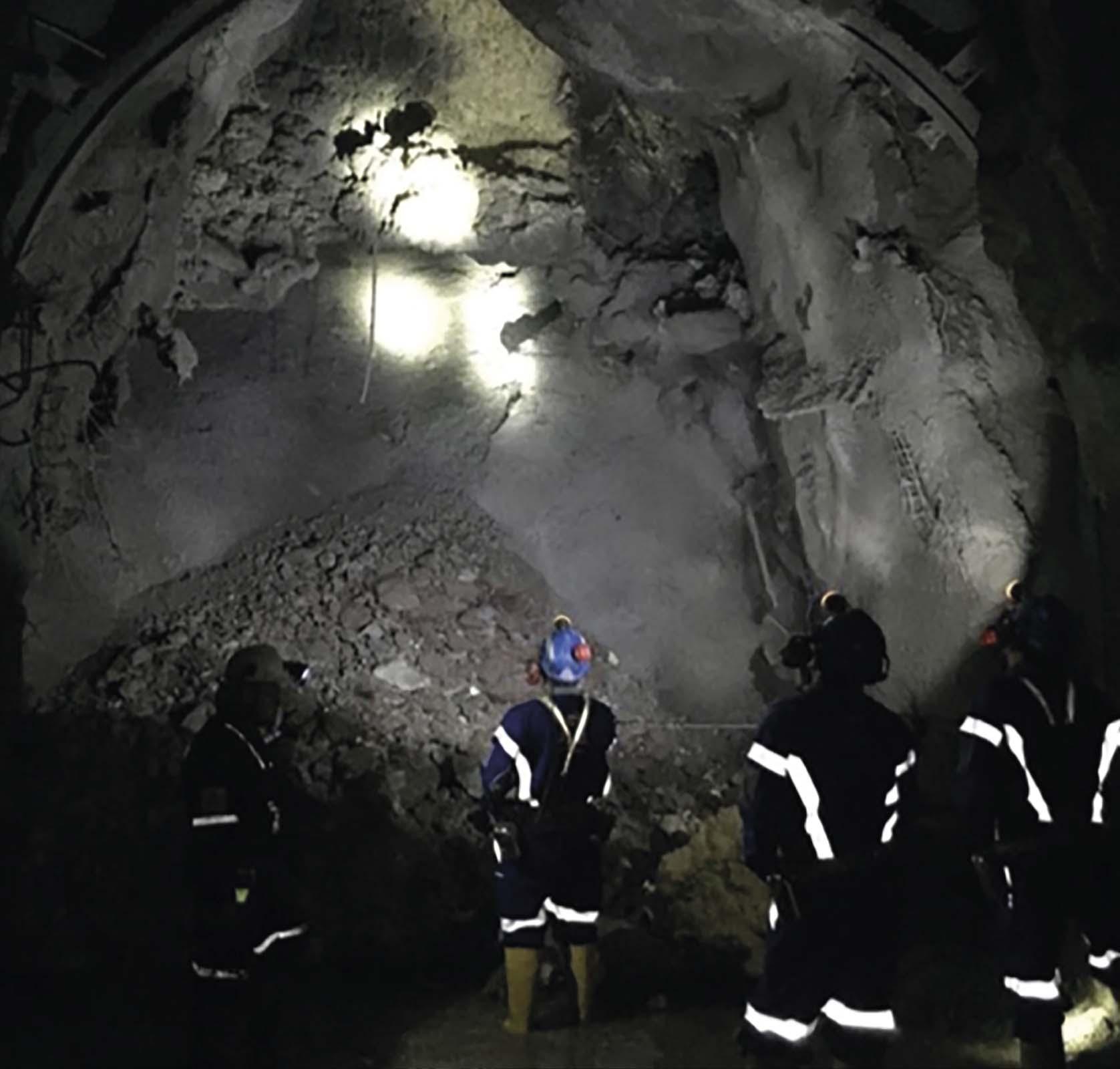
a higher strength plug seal. These high strength mine seals are typically utilised to protect against overpressure (blast) events in underground mines
The Rocsil HD20 product was developed specifically to achieve a mine plug seal rated to a 50 psi overpressure loading. Following the product development and confirmation using FME analysis, the company was able to engineer a design to obtain a 50 psi rated plug seal using Rocsil HD20. The product gives a 60% increase in overpressure loading, compared to the 30 psi achieved previously including a safety factor of 1.1.
Some key Rocsil HD20 product properties include: Slower set time of 2.5 minutes, allowing for increased permeation. Density of the foam increased to an average 60.6 kg/m3 . Increased compressive strength to 97.3 kPa at 10% deformation.
Using Rocsil HD20 oft en allows design parameters to be greatly reduced, saving infrastructure costs and negating the requirement for additional drilling to install boreholes.
Case study: New South Wales
S2S injection in a longwall goaf behind a seal area required control of oxygen egressing into the area of concern.
Situation
An Australian mine required support with controlling oxygen egress through the rib around an installed seal in a goaf area (Figure 2).
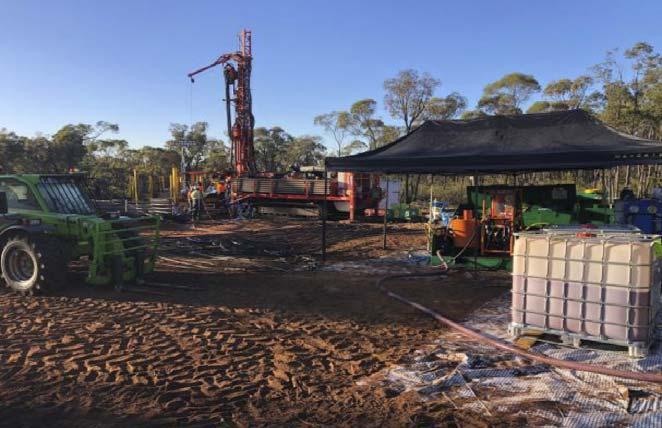
Figure 3. New South Wales case study, topside operations.
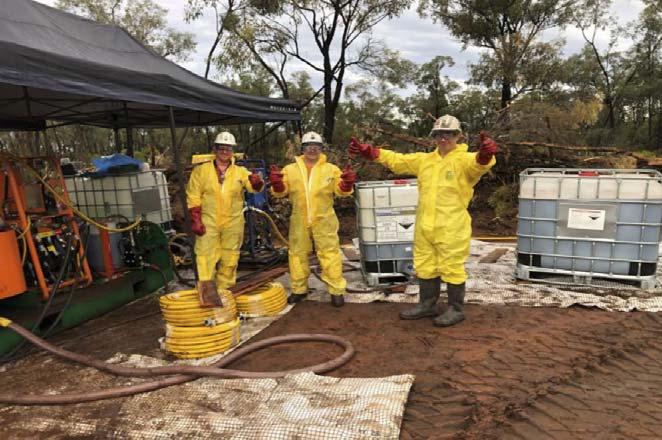
Figure 4. The end of the New South Wales project. Method
The injection was executed via a 330 m borehole with a drill rig lowering the remote head and hoses to provide a goaf plug to seal off the area. The first 400 m3 of product pumped was Rocsil HD20. In order to ensure maximum penetration through the goaf floor, loose rock fill followed with 450 m3 of standard Rocsil LS1 to fill the void above and to close off the area path (Figure 3).
Results
The results included the following: Continuous injection of 850 m3 was pumped in under 22 hours from start to finish. 44 250 kg of Rocsil applied in total: 24 000 kg of
Rocsil HD20 and 20 250 kg of Rocsil LS1. The customer was satisfied with the injection outcome and the resulting seal (Figure 4).
Case study: Australian mine
Australian mine S2S injection of underground roadway in an emergency situation.
Situation
An Australian mine required an emergency remote Rocsil S2S application aft er a mine explosion event.
Method
Chemical applicators, equipment, and Rocsil HD20 product was deployed to the site within hours of the event. Engineering on the final seal installation of the roadways was developed with and agreed to by the mine and the regulator.
A S2S injection was executed via a 380 m deep x 12 in. borehole, with a drill rig lowering the remote head into position in the roadways. The average plug size was 300 m3 of Rocsil HD20. 11 plugs were pumped to seal off all roadways into the longwall. The injection was guided by a camera, from adjustment holes drilled for the camera view. Over a number of weeks, the plugs were installed under direction from the mine and the regulator.
Results
All plugs were installed successfully with approximately 190 000 kgs of Rocsil HD20 pumped to seal off the longwall. 50 psi plugs were achieved. Mine personnel have since worked through a full re-entry plan and are now back underground working on a start-up plan. The customer is satisfied with the injection outcome and the quick response time.
The application of Rocsil and the latest innovation of Rocsil HD20 in creating remote seals represented a significant advance in mine safety.
References
1. ALSTON, N., SCHMITTER, J. L., ALCOTT, A., and FRY, R., ‘Recent case studies using the remote ROCSIL® FOAM plug system’, in AZIZ, N. and
KININMONTH, B. (eds.), Proceedings of the 2020 Coal Operators'
Conference, Mining Engineering, University of Wollongong, (2020). 2. TREVITS, M.A. and MCCARTNEY, C., ‘Use of Rocsil® foam to remotely construct mine seals National Institute for Occupational Safety and
Health (NIOSH)’, (2008).