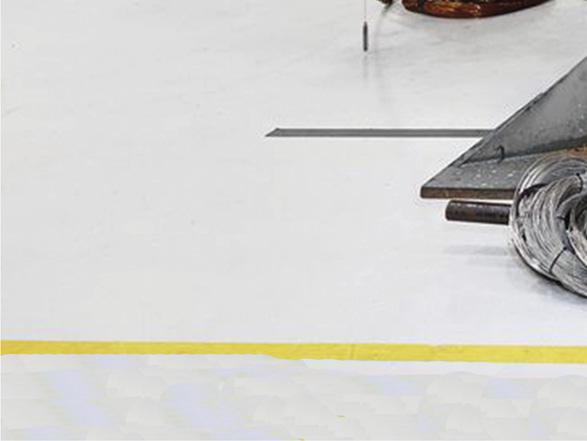
8 minute read
Igniting innovation

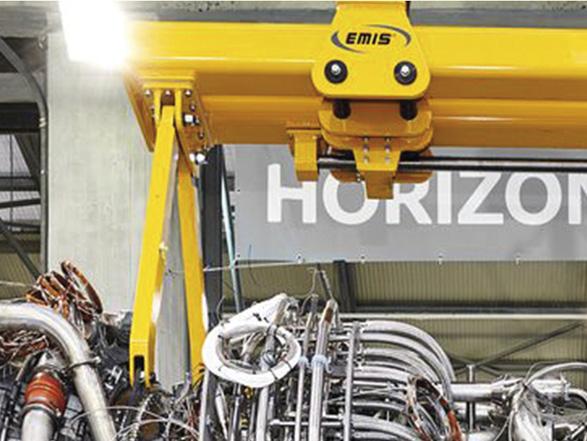

Figure 1. The LM9000 is an aeroderivative turbine design.
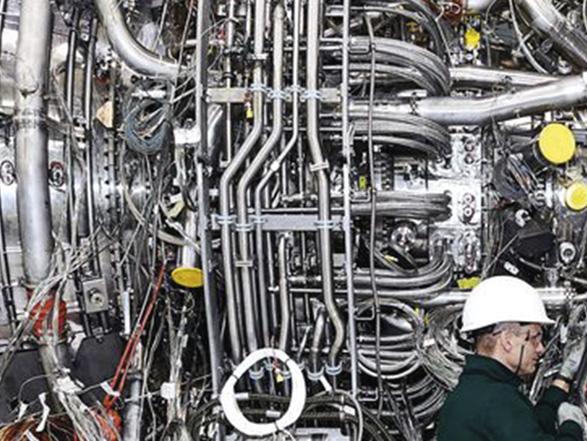
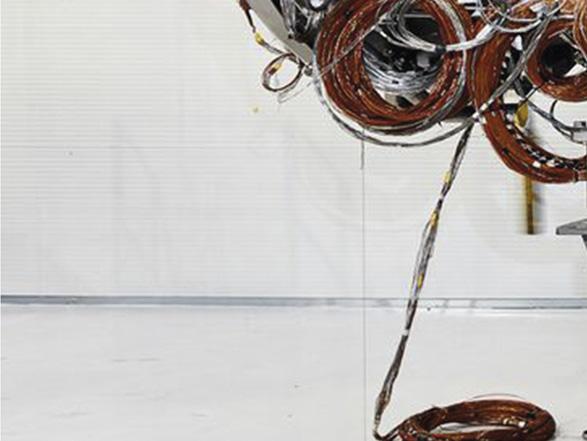
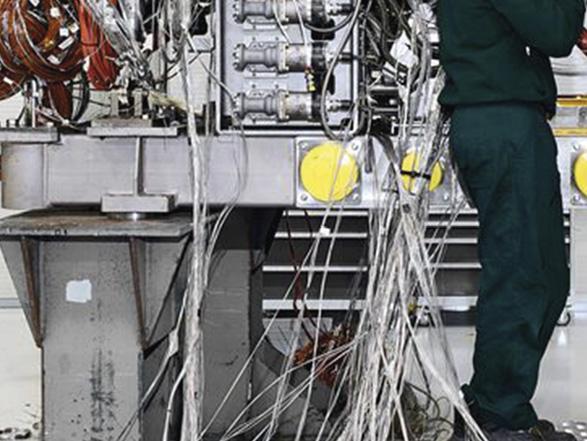
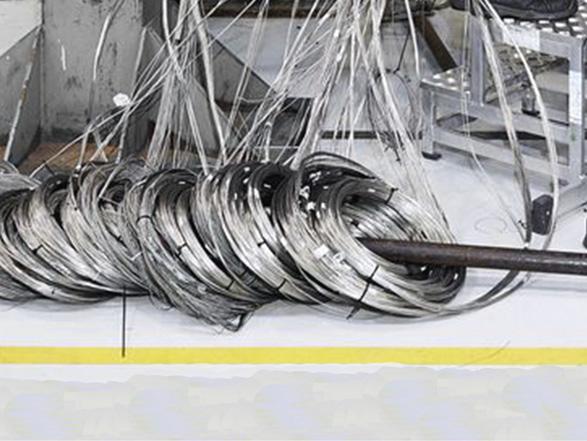
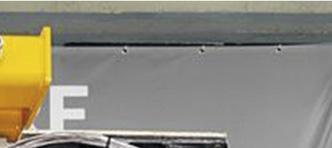

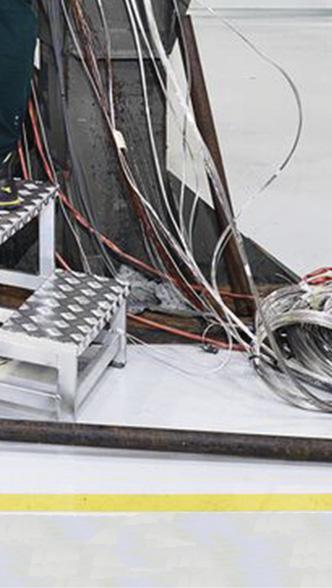
Tommaso Olivieri and Daniele Marcucci, Baker Hughes, Italy, share how continuous improvement and innovation can lead to lower emissions in LNG plants.
The LNG industry is under constant pressure to reduce the greenhouse gas (GHG) emissions associated with each step of the value chain, while also maintaining LNG affordability to meet increasing energy demand. The world is at a critical inflection point with calls to accelerate the energy transition, such as the International Energy Agency’s recently released roadmap, ‘Net Zero by 2050’.
Although the IEA report projects a significant drop of natural gas demand in these coming crucial decades, natural gas will remain a major source of energy, especially for regions where gas has yet to supplant more carbon intensive coal, so it is of the utmost importance to produce and supply it in a more efficient, decarbonised way. Fuels are not the problem – needless emissions are.
Focusing on LNG production, it is clear that real opportunities currently exist to lower costs, improve efficiency, and reduce GHG emissions. This requires installing emissions reduction technology into existing plants and designing the plants of the future using emissions reduction as one of the guiding principles.
Now is a momentous time of introspection, re-evaluation, and reinvention in many aspects of society and especially in the global energy industry. For Baker Hughes’ part in the LNG realm, the company is delivering an efficient turbine in a notably high-power range and making a measurable and meaningful difference today.
Market-driven solutions
Baker Hughes has proven expertise supporting LNG customers, with 100+ trains and more than 400 million tpy of installations powered by Baker Hughes technology. In recent months, the company has been collaborating with customers all around the world who aim to reduce emissions from their operations on both existing and new projects. Its customers are setting net zero targets for 2050 and Baker Hughes has aligned with them on achieving intermediate successes as well as implementing major improvements today. Three trends are clearly emerging: Technology efficiency: Highly efficient gas turbines and compressors serve parallel purposes – lower emissions and lower costs.

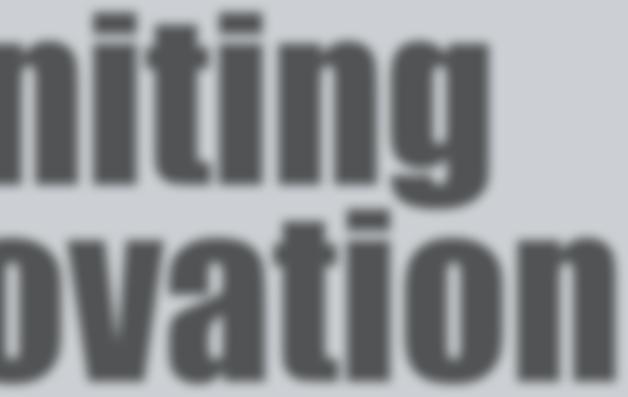
Integrated solutions: Integrating renewable energies, hydrogen, and carbon capture technologies can provide a huge benefit to the carbon intensity of LNG production.
Baker Huges is currently collaborating with some customers to explore each one of these solutions. Capital efficiency: Modularisation of equipment enables total cost reduction and project risk minimisation. This is directly linked to emissions reduction since it can make decarbonised
LNG production cost competitive with traditional LNG.
At the core of these solutions is a particularly powerful machine which Baker Hughes recently developed to bring forth a substantial efficiency increase: the LM9000.
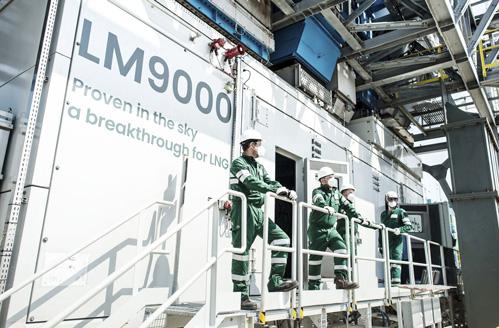
Figure 2. The LM9000 turbine is housed in modular installations.
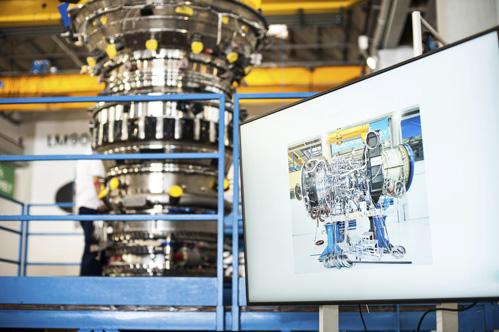
Figure 3. At its heart, the LM9000 is a 73+ MW driver designed to reduce emissions with high-powered efficiency.
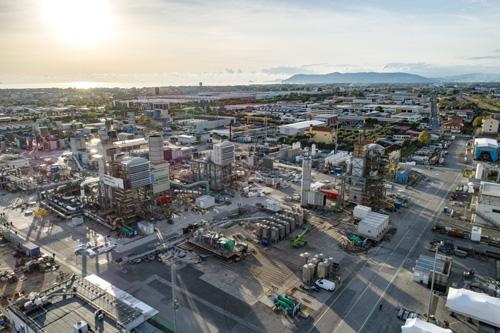
Figure 4. The Baker Hughes turbomachinery testing facility in Massa, Italy. Many engineers are focused on energy transition technologies, including lower-carbon LNG operations, carbon capture, utilisation and storage, and advanced hydrogen solutions.
Carbon reduction by design
The latest aeroderivative gas turbine from Baker Hughes, the LM9000, is a 73 MW+ driver that has been developed with LNG customers in mind and with a strong focus on reducing the carbon footprint of the liquefaction plant.
Aero technologies achieve very high simple-cycle efficiency to reduce direct CO2 emissions because the same power can be achieved using less fuel. Some architectural features, such as the completely new free power turbine, have been introduced to provide greater operational flexibility.
The turbine design also ensures successful start-ups with no need to vent process gases in the centrifugal compressors, thus further reducing the environmental impact of this driver. As for other emissions, this gas turbine is among the best of available technologies with values below 15 ppm for NOx and 25 ppm for CO2 at ISO condition.
The high-power density of this gas turbine brings a reduced footprint compared to traditional LNG plants that also makes it ideal for offshore. With this small footprint and innovative module design for fast and easy maintenance – the engine swap can be performed in less than 24 hours – the LM9000 is designed to be an ideal gas turbine for all mechanical drive and power generation applications.
Energy Renaissance
Key to Baker Hughes’ development effort was the building of a new testing facility on the Tuscan coast, an hour’s drive from the company’s offices in Florence, Italy. The facility housed a prototype engine running over 3000 special instruments to fully validate the product and verify all the major technical features, including performance and operability. This very same facility is also used for all the production factory acceptance tests (FATs).
The facility is located in Massa, Italy, between the Apennines and the Tyrrhenian Sea – a location where Michelangelo used to go and pick the right marble for the masterpieces that are still enjoyed today. Baker Hughes operates its testing much like da Vinci approached his inventions, with curiosita and dimostrazione, which is a commitment to testing knowledge. The inventor also believed in embracing uncertainty and as Baker Hughes geared up to test the enhancements to the LM9000, there was a sense of controlled uncertainty before it realised its success. Each crucial step of the energy transition is taken with these Eureka moments.
Assembling a global engineering team for the LM9000 turbine test was limited by COVID-19 travel restrictions during 2020. With Italy in full lockdown, the business continuity planning became creative.
The team stepped up and set up, in record time, a virtual testing framework with a bare minimum crew present and over 100 technicians connected from all over the world. This approach set a newly adopted standard for remote testing that the company has also used for customer testing, including at the Calcasieu Pass LNG project in Louisiana, US, and for the LM9000 test for the Arctic LNG 2 project in Russia.
Arctic LNG 2
In December 2018, NOVATEK selected Baker Hughes to supply LM9000 aeroderivative gas turbines for the Arctic LNG 2 project. A successful remote prototype test completion in May 2020 paved the way for the LM9000’s use in NOVATEK’s other new LNG projects.
The test confirmed this GT as the most powerful and efficient aeroderivative gas turbine in its class – with more than 44% simple-cycle efficiency and a power output 15% higher than industry peers. This efficiency is key to driving lower carbon intensity and, together with lower NOx emissions (40% lower than competing technology), makes for a more environmentally sensitive solution. In 4Q20, three string tests, with a complete field configuration, both in mechanical drive and power generation were successfully run in Massa.
Baker Hughes’ scope of work for Arctic LNG 2 includes the supply of turbomachinery equipment for power generation and three liquefaction trains on gravity-based structures (GBS) that will produce 6.6 million tpy of LNG each, for a total production of 19.8 million tpy.
Looking ahead
The LM9000 testing was a success and it is already in production, but the company cannot rest on its laurels. The energy transition requires collaboration for further innovations, not just in LNG, but in cleaner, more efficient power generation; the deployment of a variety of carbon capture utilisation and storage solutions; the development of the hydrogen economy; and massive expansions in renewable power, including for electrolysers to produce green hydrogen. The availability of the LM9000 today to reduce LNG train emissions shows meaningful progress for climate goals can be made now. The company hopes that this trailblazing effort will inspire other significant developments across the energy spectrum on the path to net zero.
The energy transition is well underway and is being advanced from within the industry as energy providers demand more and better technologies today. The biggest engine of change in the world is the collective brain trust of energy engineers who truly want to build a sustainable future now.

Figure 5. The LM9000 gas turbine was tested at full speed and full load at the Baker Hughes turbomachinery testing facility in Massa, Italy.

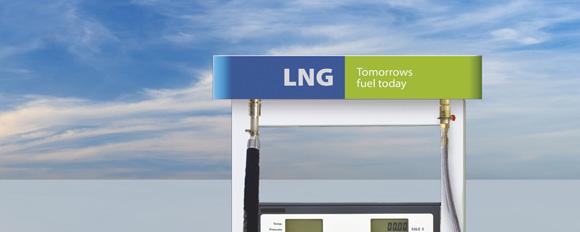
FUELING LNG INNOVATION
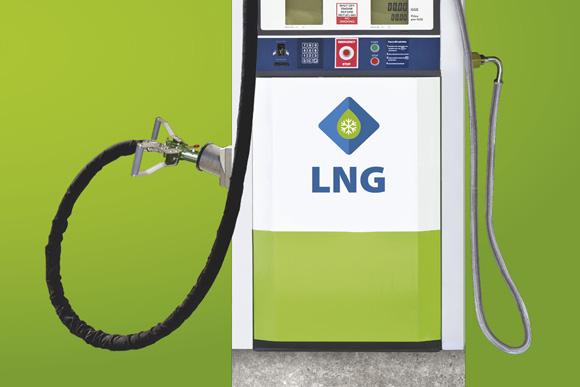
From the dispenser to the vehicle, RegO® innovation delivers unmatched safety, ease-of-use, and performance — and lowers your cost of ownership.

RegO® CryoMac® 4: patented nozzle safety feature is certified & recognized in the market as a major fail-safe advantage for the operator.
REGO 100% TESTED
CRYOMAC® M LNG FUELING NOZZLES
BREAKAWAY COUPLING VENT SIDE COUPLING FUELING ELING HOSES OSES QDV VENT QDV VENTQ QDVVENT See the complete line at regoproducts.com/lng rego-europe.de/products/lng

